fuel type DATSUN PICK-UP 1977 User Guide
[x] Cancel search | Manufacturer: DATSUN, Model Year: 1977, Model line: PICK-UP, Model: DATSUN PICK-UP 1977Pages: 537, PDF Size: 35.48 MB
Page 111 of 537
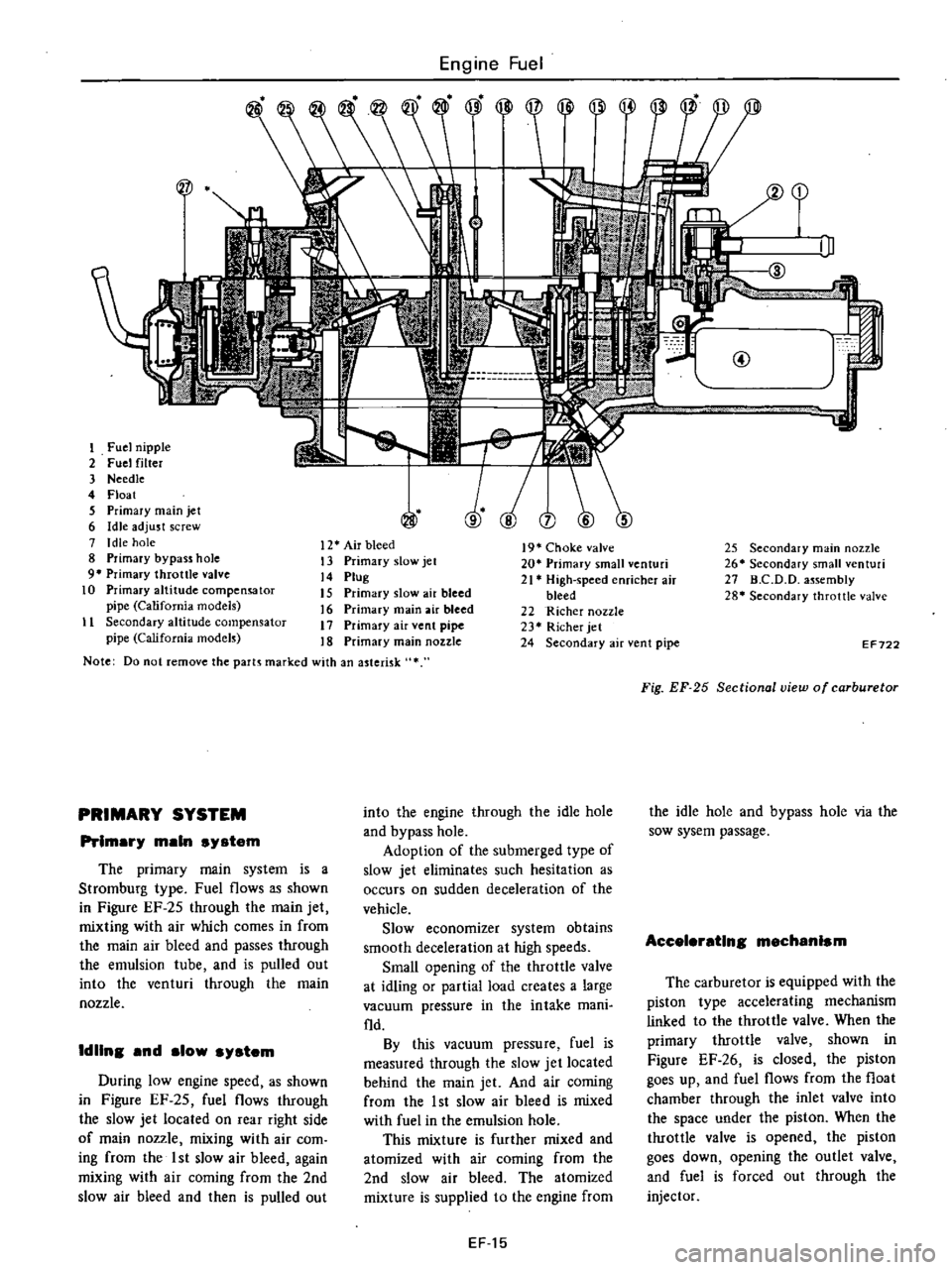
tZrJ
I
Fuel
nipple
2
Fuel
filter
3
Needle
4
Float
S
Primary
main
jet
6
Idle
adjust
screw
7
I
die
hole
8
Primary
bypass
hole
9
Primary
throttle
valve
10
Primary
altitude
compensator
pipe
California
models
11
Secondary
altitude
compensator
pipe
California
models
Engine
Fuel
jli@
I
12
Air
bleed
13
Primary
slow
jet
14
Plug
15
Primary
slow
air
bleed
6
Primary
main
air
bleed
17
Primary
air
vent
pipe
8
Primary
main
nOlzle
Note
Do
not
remove
the
parts
marked
with
an
asterisk
PRIMARY
SYSTEM
Prlmar
main
s
stem
The
primary
main
system
is
a
Stromburg
type
Fuel
flows
as
shown
in
Figure
EF
25
through
the
main
jet
mixting
with
air
which
comes
in
from
the
main
air
bleed
and
passes
through
the
emulsion
tube
and
is
pulled
out
into
the
venturi
through
the
main
nozzle
IdUns
and
slow
s
stem
During
low
engine
speed
as
shown
in
Figure
EF
25
fuel
flows
through
the
slow
jet
located
on
rear
right
side
of
main
nozzle
mixing
with
air
com
ing
from
the
1st
slow
air
bleed
again
mixing
with
air
coming
from
the
2nd
slow
air
bleed
and
then
is
pulled
out
I
III
@
19
Choke
valve
20
Primary
small
venturi
21
High
speed
enricher
air
bleed
22
Richer
nozzle
23
Richer
jet
24
Secondary
air
vent
pipe
into
the
engine
through
the
idle
hole
and
bypass
hole
Adoption
of
the
submerged
type
of
slow
jet
eliminates
such
hesitation
as
occurs
on
sudden
deceleration
of
the
vehicle
Slow
economizer
system
obtains
smooth
deceleration
at
high
speeds
Small
opening
of
the
throttle
valve
at
idling
or
partial
load
creates
a
large
vacuum
pressure
in
the
intake
mani
fld
By
this
vacuum
pressure
fuel
is
measured
through
the
slow
jet
located
behind
the
main
jet
And
air
coming
from
the
1st
slow
air
bleed
is
mixed
with
fuel
in
the
emulsion
hole
This
mixture
is
further
mixed
and
atomized
with
air
coming
from
the
2nd
slow
air
bleed
The
atomized
mixture
is
supplied
to
the
engine
from
EF15
25
Secondary
main
nozzle
26
Secondary
small
enturi
27
D
C
D
D
a
sembly
28
Secondary
throttle
valve
EF722
Fig
EF
25
Sectional
view
of
carburetor
the
idle
hole
and
bypass
hole
via
the
sow
sysem
passage
Accele
atlns
mechanism
The
carburetor
is
equipped
with
the
piston
type
accelerating
mechanism
linked
to
the
throttle
valve
When
the
primary
throttle
valve
shown
in
Figure
EF
26
is
closed
the
piston
goes
up
and
fuel
flows
from
the
float
chamber
through
the
inlet
valve
into
the
space
under
the
piston
When
the
throttle
valve
is
opened
the
piston
goes
down
opening
the
outlet
valve
and
fuel
is
forced
out
through
the
injector
Page 112 of 537
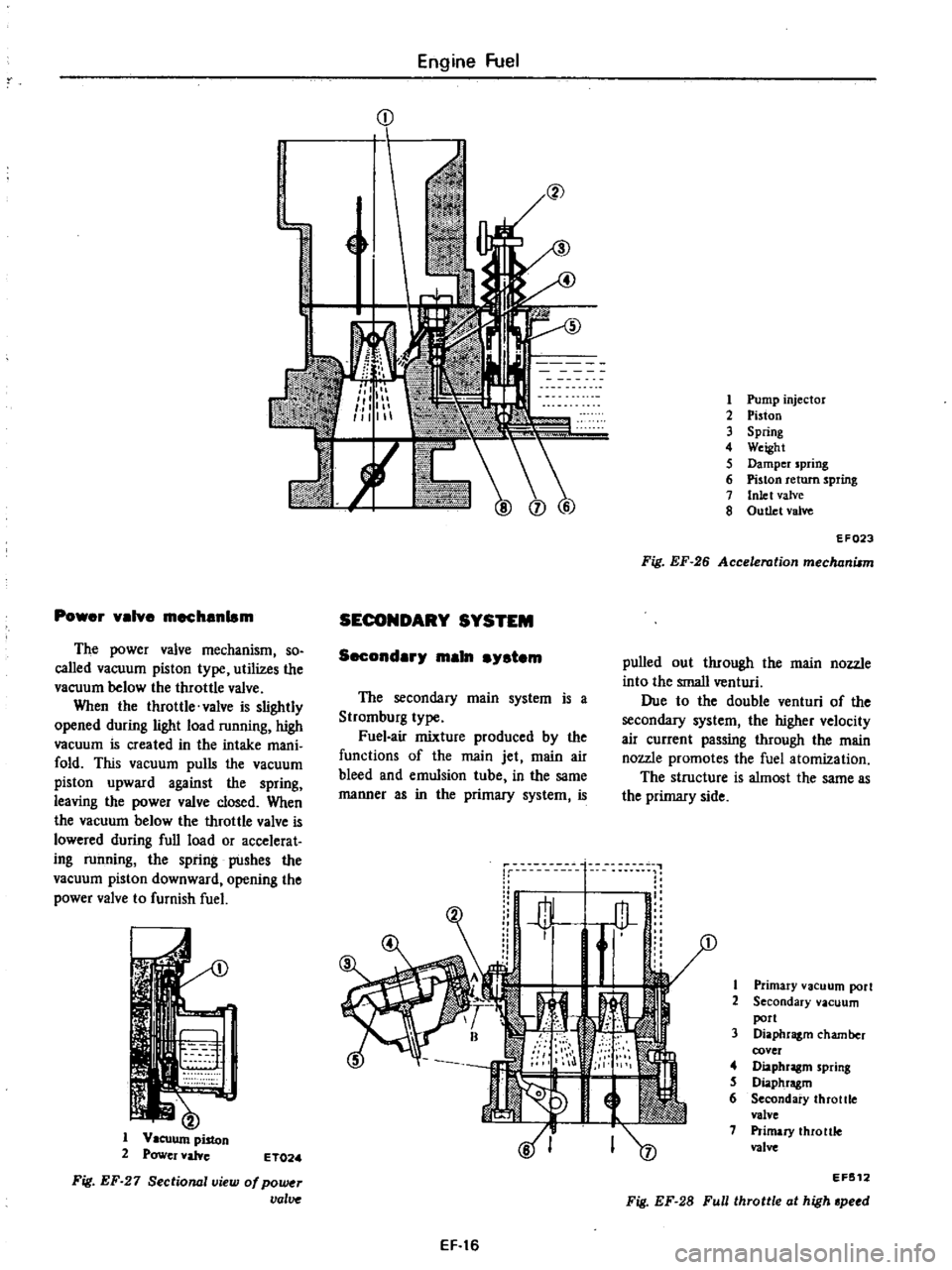
Engine
Fuel
1
L
if
1
Pump
injector
2
Piston
3
Spring
4
Weight
5
Damper
spring
6
Piston
return
spring
7
Inlet
valve
8
Outlet
valve
EF023
Fig
EF
26
Acceleration
mechanism
Power
valve
mechanism
SECONDARY
SYSTEM
The
power
valve
mechanism
so
called
vacuum
piston
type
utilizes
the
vacuum
below
the
throttle
valve
When
the
throttle
valve
is
slightly
opened
during
light
load
running
high
vacuum
is
created
in
the
intake
mani
fold
This
vacuum
pulls
the
vacuum
piston
upward
against
the
spring
leaving
the
power
valve
closed
When
the
vacuum
below
the
throttle
valve
is
lowered
during
full
load
or
accelerat
ing
running
the
spring
pushes
the
vacuum
piston
downward
opening
the
power
valve
to
furnish
fuel
Secondary
main
lIYlltem
pulled
out
through
the
main
nozzle
into
the
small
venturi
Due
to
the
double
venturi
of
the
secondary
system
the
higher
velocity
air
current
passing
through
the
main
nozzle
promotes
the
fuel
atomization
The
structure
is
almost
the
same
as
the
primary
side
The
secondary
main
system
is
a
Stromburg
type
Fuel
air
mixture
produced
by
the
functions
of
the
main
jet
main
air
bleed
and
emulsion
tube
in
the
same
manner
as
in
the
primary
system
is
11
1
I
1
1
Primary
vacuum
port
2
Secondary
vacuum
port
3
Diaphragm
chamber
cover
of
Diaphragm
spring
S
Diaphragm
6
Secondary
throttle
valve
7
Primary
theo
nle
valve
lWll
I
1
11
l
v
1
Vacuum
piston
2
Power
valve
ET02
a
EF
512
Fig
EF
27
Sectional
view
of
po
r
valve
Fig
EF
28
Full
throttle
al
high
peed
EF
16
Page 114 of 537
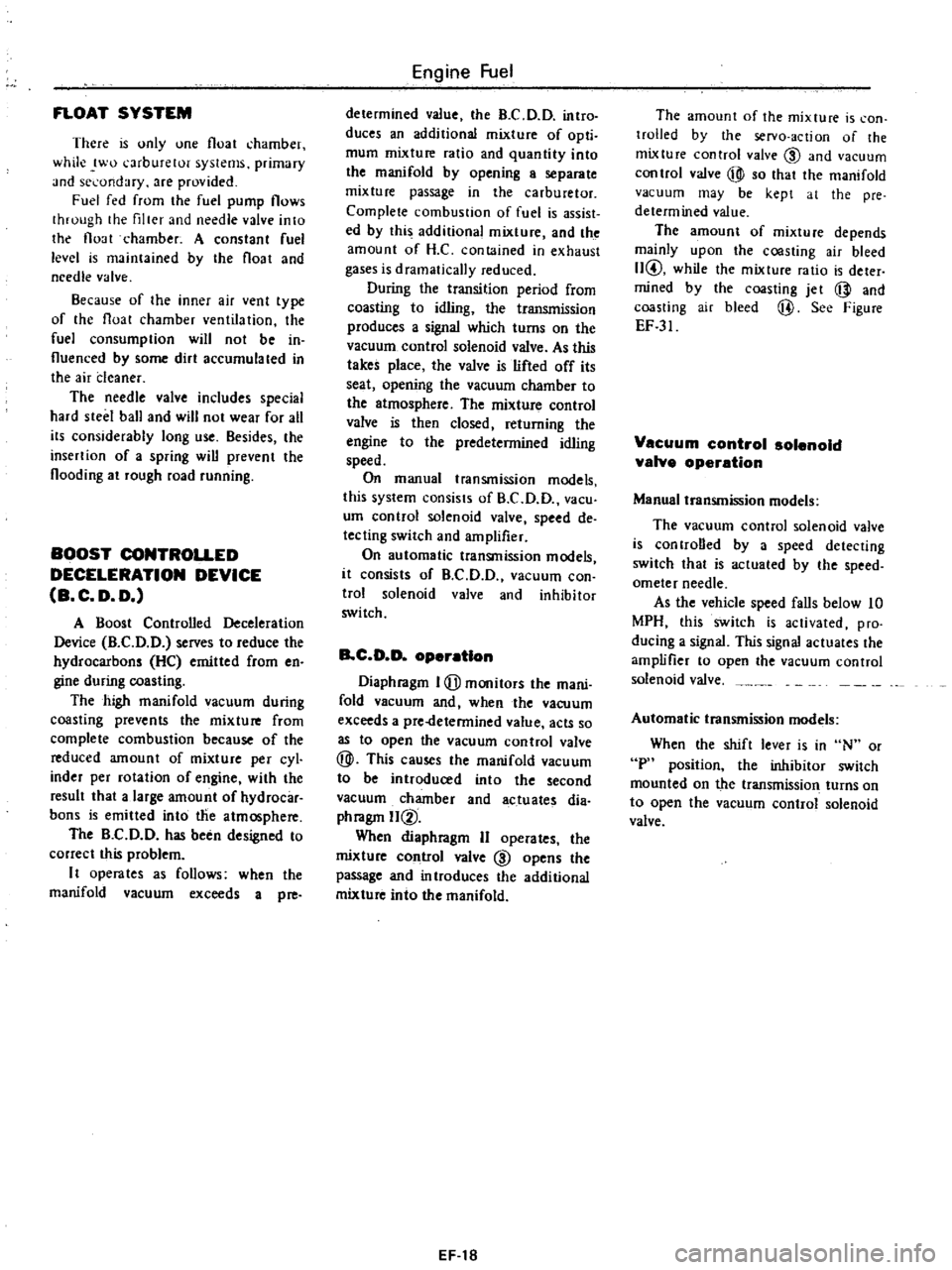
FLOAT
SYSTEM
There
IS
only
one
float
chamber
while
two
l
arburetor
systems
primary
Jnd
st
l
ondary
are
provided
Fuel
fed
from
the
fuel
pump
flows
through
the
filler
and
needle
valve
into
the
flo
t
chamber
A
constant
fuel
level
is
maintained
by
the
float
and
needle
valve
Because
of
the
inner
air
vent
type
of
the
float
chamber
ventilation
the
fuel
consumption
will
not
be
in
fluenced
by
some
dirt
accumulated
in
the
air
deaner
The
needle
valve
includes
special
hard
steel
ball
and
will
not
wear
for
all
its
considerably
long
use
Besides
the
inserrion
of
a
spring
wiU
prevent
the
flooding
at
rough
road
running
BOOST
CONTROLLED
DECELERATION
DEVICE
B
C
D
D
A
Boost
Controlled
Deceleration
Device
B
C
D
D
serves
to
reduce
the
hydrocarbons
He
emitted
from
en
gine
during
coasting
The
high
manifold
vacuum
during
coasting
prevents
the
mixture
from
complete
combustion
because
of
the
reduced
amount
of
mixture
per
cyl
inder
per
rotation
of
engine
with
the
result
that
a
large
amount
of
hydrocar
bons
is
emitted
into
tile
atmosphere
The
B
C
D
D
has
been
designed
to
correct
this
problem
It
opern
tes
as
follows
when
the
manifold
vacuum
exceeds
a
pre
Engine
Fuel
determined
value
the
B
C
D
D
intro
duces
an
additional
mixture
of
opti
mum
mixture
ratio
and
quantity
into
the
manifold
by
opening
a
separate
mixture
passage
in
the
carburetor
Complete
combustion
of
fuel
is
assist
ed
by
this
additional
mixture
and
the
amount
of
H
C
contained
in
exhaust
gases
is
dramatically
reduced
During
the
transition
period
from
coasting
to
idling
the
transmission
produces
a
signal
which
turns
on
the
vacuum
control
solenoid
valve
As
this
takes
place
the
valve
is
lifted
off
its
seat
opening
the
vacuum
chamber
to
the
atmosphere
The
mixture
control
valve
is
then
closed
returning
the
engine
to
the
predetermined
idling
speed
On
manual
transmission
models
this
system
consists
of
B
C
D
D
vacuo
urn
control
solenoid
valve
speed
de
tecting
switch
and
amplifier
On
automatic
transmission
models
it
consists
of
B
C
D
D
vacuum
con
trol
solenoid
valve
and
inhibitor
switch
B
C
D
D
operation
Diaphragm
I
Qj
monitors
the
mani
fold
vacuum
and
when
the
vacuum
exceeds
a
pre
fetermined
value
acts
so
as
to
open
the
vacuum
control
valve
@
This
causes
the
manifold
vacu
urn
to
be
introduced
into
the
second
vacuum
chamber
and
actuates
dia
phragm
ll@
When
diaphrngm
II
operates
the
mixture
control
valve
@
opens
the
passage
and
introduces
the
additional
mixture
into
the
manifold
EF
18
The
amount
of
the
mixture
is
con
trolled
by
the
servo
action
of
the
mixture
control
valve
CID
and
vacuum
control
valve
@
so
that
the
manifold
vacuum
may
be
kept
at
the
pre
determined
value
The
amount
of
mixture
depends
mainly
upon
the
coasting
air
bleed
II@
while
the
mixture
ratio
is
deter
mined
by
the
coasting
jet
@
and
coasting
air
bleed
@
See
Figure
EF
31
Vacuum
control
solenoid
valve
operation
Manual
transmission
models
The
vacuum
control
solenoid
valve
is
con
troDed
by
a
speed
detecting
switch
that
is
actuated
by
the
speed
ometer
needle
As
the
vehicle
speed
falls
below
10
MPH
this
switch
is
activated
pro
ducing
a
signal
This
signal
actuates
the
amplifier
to
open
the
vacuum
control
solenoid
valve
Automatic
transmission
models
When
the
shift
lever
is
in
N
or
P
position
the
inhibitor
switch
mounted
on
the
transmission
turns
on
to
open
the
vacuum
control
solenoid
valve
Page 122 of 537
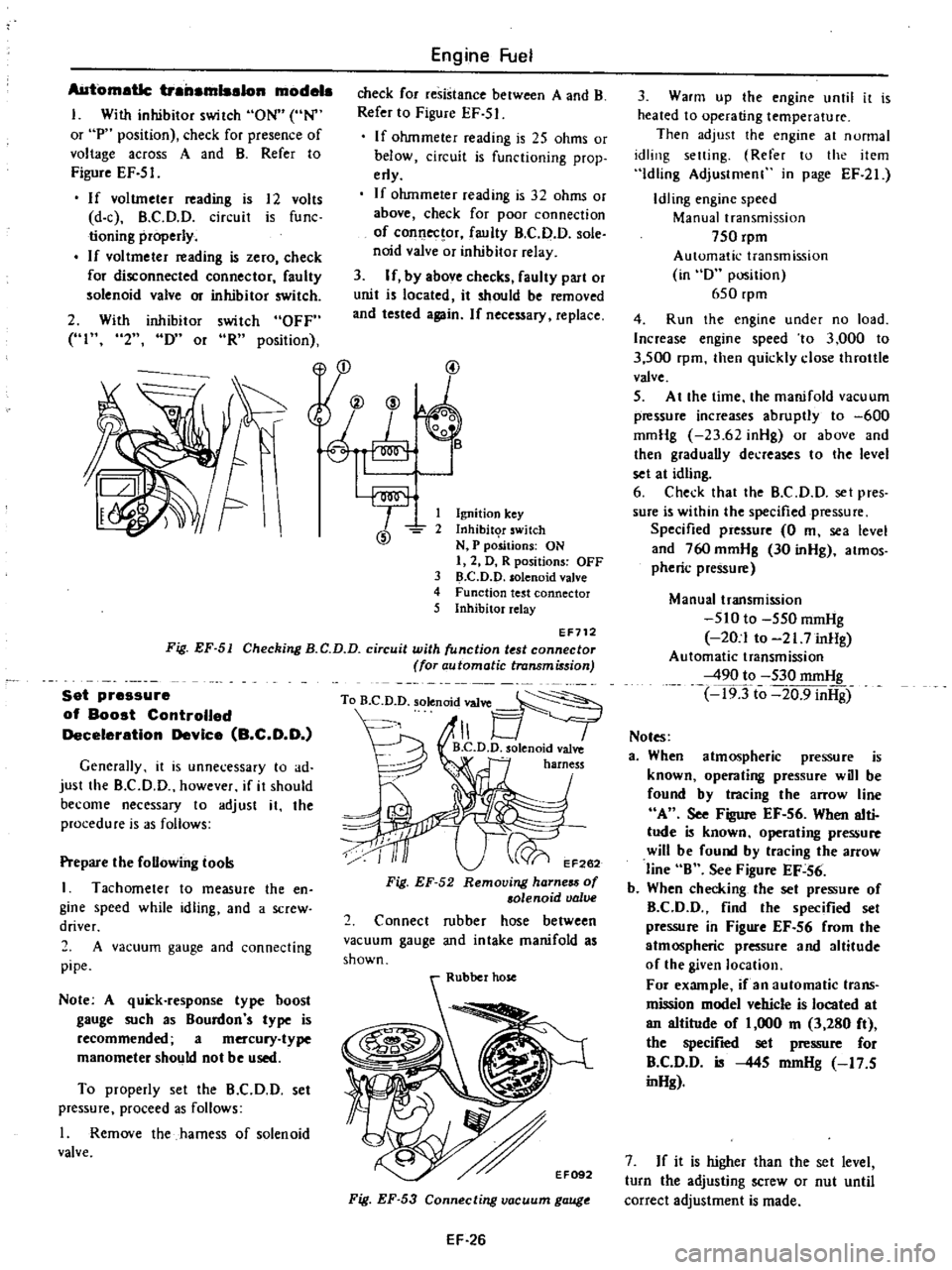
AUtomatic
trailamlsalon
modela
I
With
inhibitor
switch
ON
UN
or
P
position
check
for
presence
of
voltage
across
A
and
B
Refer
to
Figure
EF
51
If
voltmeter
ading
is
12
volts
d
c
B
C
D
O
circuit
is
func
tioning
properly
If
vol
tmeter
ading
is
zero
check
for
disconnected
connector
faulty
solenoid
valve
m
inhibitor
switch
2
With
inhibitor
switch
OFF
HI
2
IY
or
oR
position
Engine
Fuel
check
for
resistance
between
A
and
B
Refer
to
Figure
EF
51
If
ohmmeter
reading
is
25
ohms
or
below
circuit
is
functioning
prop
erly
If
ohmmeter
reading
is
32
ohms
or
above
check
for
poor
connection
of
connec
or
faulty
B
C
D
D
sole
noid
valve
or
inhibitor
relay
3
If
by
above
checks
faulty
part
or
unit
is
located
it
should
be
moved
and
tested
again
If
necessary
replace
yu
@
@
1
Ignition
key
2
Inhibit
T
switch
N
P
positions
ON
I
2
D
R
positions
OFF
3
D
C
D
D
solenoid
valve
4
Function
test
connector
5
Inhibitor
relay
EF712
Fig
EF
51
Checking
B
C
D
D
circuit
with
unction
t
st
connector
for
automatic
transmi
sion
Set
pressure
of
Boost
Controlled
Deceleration
Device
B
C
D
O
Generally
it
is
unnecessary
to
ad
just
the
B
CD
D
however
if
it
should
become
necessary
to
adjust
it
the
procedure
is
3S
follows
Prepare
the
foUowing
tool
I
Tachometer
to
measure
the
en
gine
speed
while
idling
and
a
screw
driver
2
A
vacuum
gauge
and
connecting
pipe
Note
A
quick
response
type
hoost
gauge
such
as
Bourdon
s
type
is
recommended
a
mercury
type
manometer
should
not
be
used
To
properly
set
the
B
C
D
D
set
pressure
proceed
as
follows
I
Remove
the
harness
of
solenoid
valve
To
B
D
D
solenoid
valve
1
B
C
D
D
olenoid
valve
harness
EF262
Fig
EF
52
Removing
harness
of
solenoid
valve
2
Connect
rubber
hose
between
vacuum
gauge
and
intake
manifold
as
shown
Fig
EF
53
Connecting
vacuum
gauge
EF
26
3
Warm
up
the
engine
until
it
is
heated
to
operating
temperature
Then
adjust
the
engine
at
nunnal
idling
setting
Refer
to
the
item
Idling
Adjustmenl
in
page
EF
21
Idling
engine
speed
Manual
transmission
750
rpm
Automatic
transmission
in
D
position
650
rpm
4
Run
the
engine
under
no
load
Increase
engine
speed
to
3
000
to
3
500
rpm
then
quickly
close
throttle
valve
5
At
the
time
the
manifold
vacuum
p
ssure
increases
abruptly
to
600
mmHg
23
62
inHg
or
above
and
then
graduaUy
decreases
to
the
level
set
at
idling
6
Check
that
the
B
C
D
D
set
pres
sure
is
within
the
specified
pressure
Specified
pressure
0
m
sea
level
and
760
mmHg
30
inHg
atmos
pheric
pressu
Manual
transmission
510
to
550
mmHg
20
1
to
21
7
inHg
Automatic
transmission
490
to
530
mmHg
19Tto
20
9
inHg
Notes
a
When
atmospheric
pressure
is
known
operating
pressure
will
be
found
by
tracing
the
arrow
line
A
See
Figure
EF
56
When
alti
tude
is
known
operating
pressure
will
be
found
by
tracing
the
arrow
line
B
See
Figu
EF
56
b
When
checking
the
set
pressu
of
B
CD
D
find
the
specified
set
pressu
in
Figure
EF
56
from
the
atmospheric
pressure
and
altitude
of
the
given
location
For
example
if
an
automatic
trans
mission
model
vehicle
is
located
at
an
altitude
of
1
000
m
3
280
ft
the
specified
set
p
ssu
for
B
C
D
D
is
445
mmHg
17
5
inHg
7
If
it
is
higher
than
the
set
level
turn
the
adjusting
screw
or
nut
until
correct
adjustment
is
made
Page 131 of 537
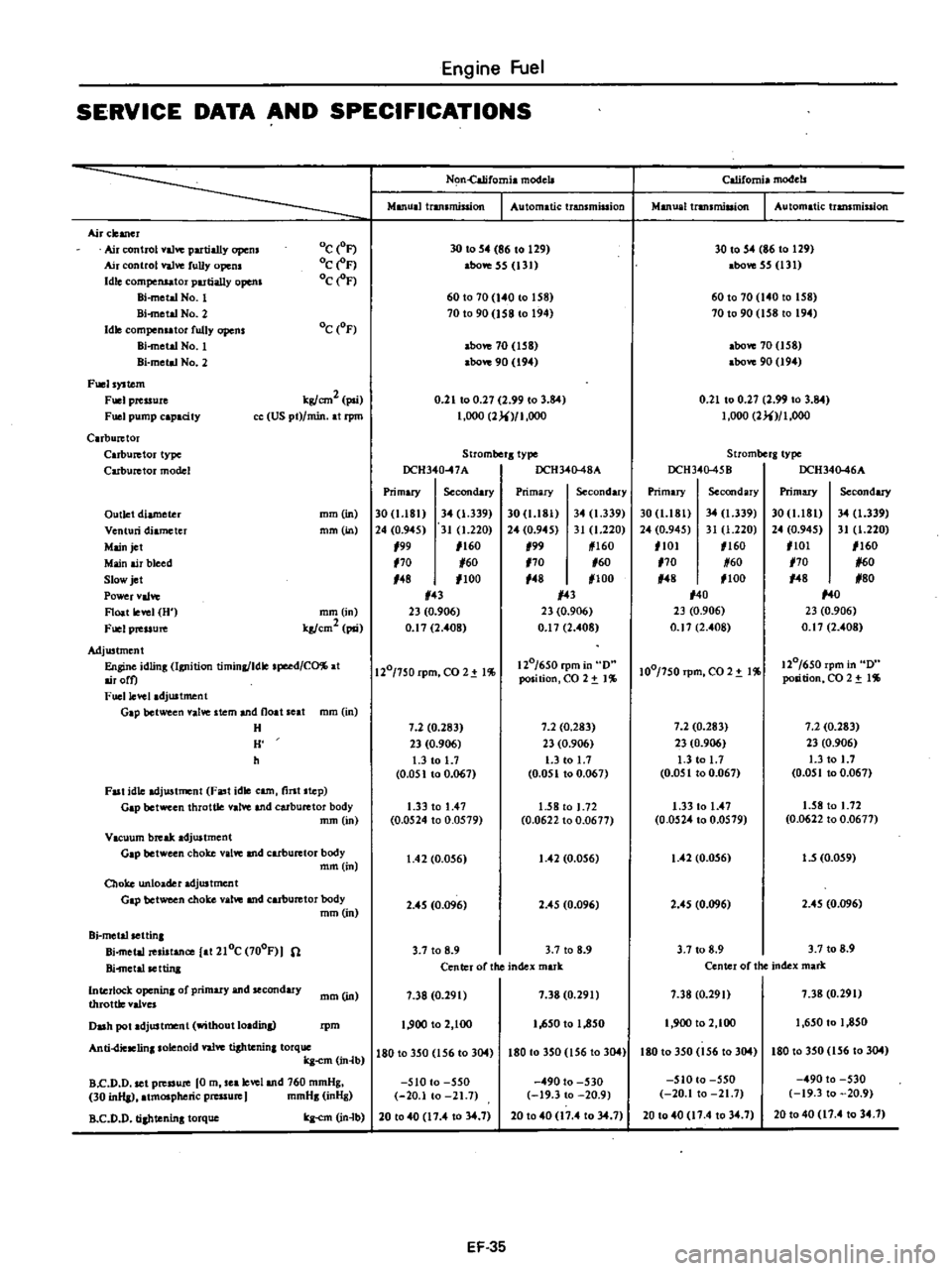
Engine
Fuel
SERVICE
DATA
AND
SPECIFICATIONS
Airclelllcr
Ail
control
val
partially
opem
Air
ntrol
valve
fuUy
opens
Idle
ompensatoI
partially
opens
Hi
mettiNo
l
Bi
metal
No
2
Idle
ompen
tor
fully
opens
Bi
metal
No
1
Hi
metd
No
2
Fuels
Stem
Fuel
prtuure
Fuel
pump
apacHy
C
rbu
tor
C
rbu
tor
type
Carburetor
model
Oc
oF
oCe
F
oCe
F
Oc
OF
kpJcm2
poi
US
pt
min
at
rpm
Outlet
diameter
Venturi
diameter
Main
jet
Main
air
bleed
Slow
jet
Power
val
Float
level
U
fuel
preuure
rom
in
mm
in
mm
in
kg
cm2
psi
Adjustment
Engine
idling
Ignition
timing
Idle
speed
CO
at
mloro
Fuel
level
adjustment
Gap
between
Ive
stem
and
noat
at
mm
in
H
H
h
Fast
idle
adjwtmcnt
Fast
idle
earn
tint
step
Gap
between
throttle
IYe
and
carburetor
body
mm
in
Vacuum
break
adjustment
Gap
between
choke
alve
and
carburetor
body
mm
in
Choke
unloadel
adjusttncnt
Gap
between
choke
alw
and
carburetor
body
rom
in
Bi
metalsettinl
Bi
metal
resistance
at
2Ioe
700F
n
Bi
metalsettina
lnterloc
k
opcnina
of
primary
and
secondary
throtUc
valves
mmOn
Duh
pot
adjustment
without
loadin
I
m
Anti
diclClinasolenoid
valV
C
tiahtenina
torque
ka
m
in
lb
a
c
D
D
set
p
JSure
0
m
sea
level
and
760
mmHg
30
inlla
atmospheric
pressure
J
mmHa
inHg
R
C
D
D
tiahteninl
torque
kg
m
n
b
Nl
n
California
modell
Manual
transmiSsion
I
Automatic
transmission
California
modeb
Manual
transmission
I
Automatic
transmission
30
to
54
86
to
129
above
55
131
30
to
54
86
to
129
above
55
131
60
to
70
140
to
158
70
to
90
158
to
194
60
to
70
140
to
158
70
to
90
158
to
194
above
70
158
above
90
194
above
70
158
above
90
194
0
21
to
0
27
2
99
to
3
84
t
OOO
2
i
I
OOO
0
21
to
0
27
2
99
to
3
84
1
000
2
i
I
OOO
Strombcra
type
OCH340
7A
DCH340
48A
Stromt
rg
type
DCH34Q
45B
DCH340
46A
Primary
Secondary
Primary
Secondary
Primary
Secondary
Primary
Secondary
30
I8t
340
339
30
1
181
34
1
339
30
1
181
34
1
339
30
1
181
34
1
339
24
0
945
310
220
24
0
945
31
1
220
24
0
945
31
1
220
24
0
945
31
1
220
199
1160
199
1160
1101
1160
101
1160
170
160
170
160
170
60
170
1
60
148
1100
148
1100
148
1100
148
180
143
143
140
140
23
0
906
23
0
906
23
0
906
23
0
906
0
17
2
408
0
17
2
40B
0
17
2
408
0
17
2
408
1201750
rpm
CO
2
1
120
650
rpm
0
100
750rpm
C02
t
1
120
650
rpm
0
position
CO
2
t
1
position
CO
2
t
1
7
2
0
283
7
2
0
283
7
2
0
283
7
2
0
283
23
0
906
23
0
906
23
0
906
23
0
906
1
3
to
1
7
1
3
to
1
7
1
3
to
1
7
1
3
to
1
7
0
051
to
0
067
0
051
to
0
067
0
051
to
0
067
0
051
to
0
067
1
33
to
1
47
1
58
to
1
72
1
33
to
1
47
1
58
to
1
72
0
0524
to
0
0579
0
0622
to
0
0677
0
0524
to
0
0579
0
0622
to
0
0677
1
42
0
056
1
42
0
056
1
42
0
056
1
5
0
059
2
45
0
096
2
45
0
096
2
4
0
096
2
45
0
096
3
7
to
8
9
3
7
to
8
9
3
7
to
B
9
3
7
to
8
9
Center
of
the
ndex
mark
Center
of
the
index
mark
7
38
0
291
7
38
0
291
7
38
0
290
7
38
0
291
1
900
to
2
100
1
650
to
1
850
1
900
to
2
100
1
650
to
1
850
180
to
350
156
to
304
180
to
350
156
to
304
180
to
350
156
to
304
180
to
350
156
to
304
510
to
550
490
to
530
510
to
550
490
to
530
20
1
to
21
7
19
3
to
20
9
20
1
to
21
7
19
3
to
20
9
20
to
40
17
4
to
34
1
20
to
40
11
4
to
34
7
20
to
40
17
4
to
34
7
20
to
40
17
4
to
34
1
EF
35
Page 214 of 537
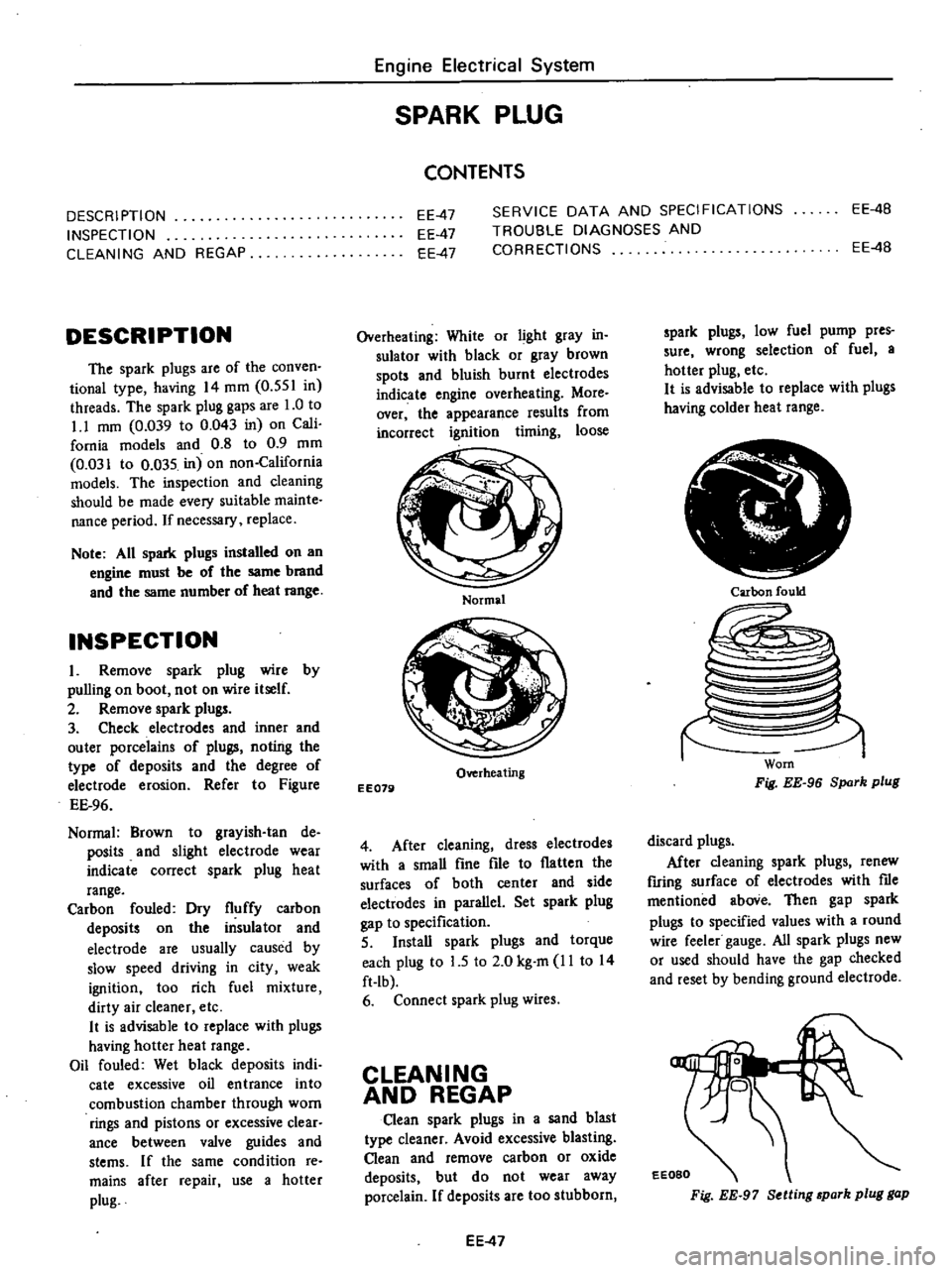
DESCRIPTION
INSPECTION
CLEANING
AND
REGAP
DESCRIPTION
The
spark
plugs
are
of
the
conven
tional
type
having
14
mm
0
551
in
threads
The
spark
plug
gaps
are
1
0
to
1
1
mm
0
039
to
0
043
in
on
Cali
fomia
models
and
0
8
to
0
9
mm
0
031
to
0
035
in
on
non
California
models
The
inspection
and
cleaning
should
be
made
every
suitable
mainte
nance
period
If
necessary
replace
Note
All
spark
plugs
installed
on
an
engine
must
be
of
the
same
brand
and
the
same
number
of
heat
range
INSPECTION
L
Remove
spark
plug
wire
by
pulling
on
boot
not
on
wire
itself
2
Remove
spark
plugs
3
Check
electrodes
and
inner
and
outer
porcelains
of
plugs
noting
the
type
of
deposits
and
the
degree
of
electrode
erosion
Refer
to
Figure
EE
96
Normal
Brown
to
grayish
tan
de
posits
and
slight
electrode
wear
indicate
correct
spark
plug
heat
range
Carbon
fouled
Dry
fluffy
carbon
deposits
on
the
insulator
and
electrode
are
usually
caused
by
slow
speed
driving
in
city
weak
ignition
too
rich
fuel
mixture
dirty
air
cleaner
etc
It
is
advisable
to
replace
with
plugs
having
hotter
heat
range
Oil
fouled
Wet
black
deposits
indi
cate
excessive
oil
entrance
into
combustion
chamber
through
worn
rings
and
pistons
or
excessive
clear
ance
between
valve
guides
and
stems
If
the
same
condition
re
mains
after
repair
use
a
hotter
plug
Engine
Electrical
System
SPARK
PLUG
CONTENTS
EE
4B
EE
47
EE
47
EE
47
SERVICE
DATA
AND
SPECIFICATIONS
TROUBLE
DIAGNOSES
AND
CORRECTIONS
EE
4B
Overheating
White
or
light
gray
in
sulator
with
black
or
gray
brown
spots
and
bluish
burnt
electrodes
indicate
engine
overheating
More
over
the
appearance
results
from
incorrect
ignition
timing
loose
Normal
Overheating
EE079
4
After
cleaning
dress
electrodes
with
a
smaU
fine
file
to
flatten
the
surfaces
of
both
center
and
side
electwdes
in
parallel
Set
spark
plug
gap
to
specification
5
InstaU
spark
plugs
and
torque
each
plug
to
L5
to
2
0
kg
m
11
to
14
ft
Ib
6
Connect
spark
plug
wires
CLEANING
AND
REGAP
Clean
spark
plugs
in
a
sand
blast
type
cleaner
Avoid
excessive
blasting
Clean
and
remove
carbon
or
oxide
deposits
but
do
not
wear
away
porcelain
If
deposits
are
too
stubborn
EE
47
spark
plugs
low
fuel
pump
pres
sure
wrong
selection
of
fuel
a
hotter
plug
etc
It
is
advisable
to
replace
with
plugs
having
colder
heat
range
Ir
i
Carbon
fould
Worn
Fig
EE
96
Spark
plug
discard
plugs
After
cleaning
spark
plugs
renew
firing
surface
of
electrodes
with
me
mentioned
aboVe
Then
gap
spark
plugs
to
specified
values
with
a
round
wire
feeler
gauge
All
spark
plugs
new
or
used
should
have
the
gap
checked
and
reset
by
bending
ground
electrode
EEOBO
Fig
EE
97
Setting
park
plug
gap
Page 215 of 537
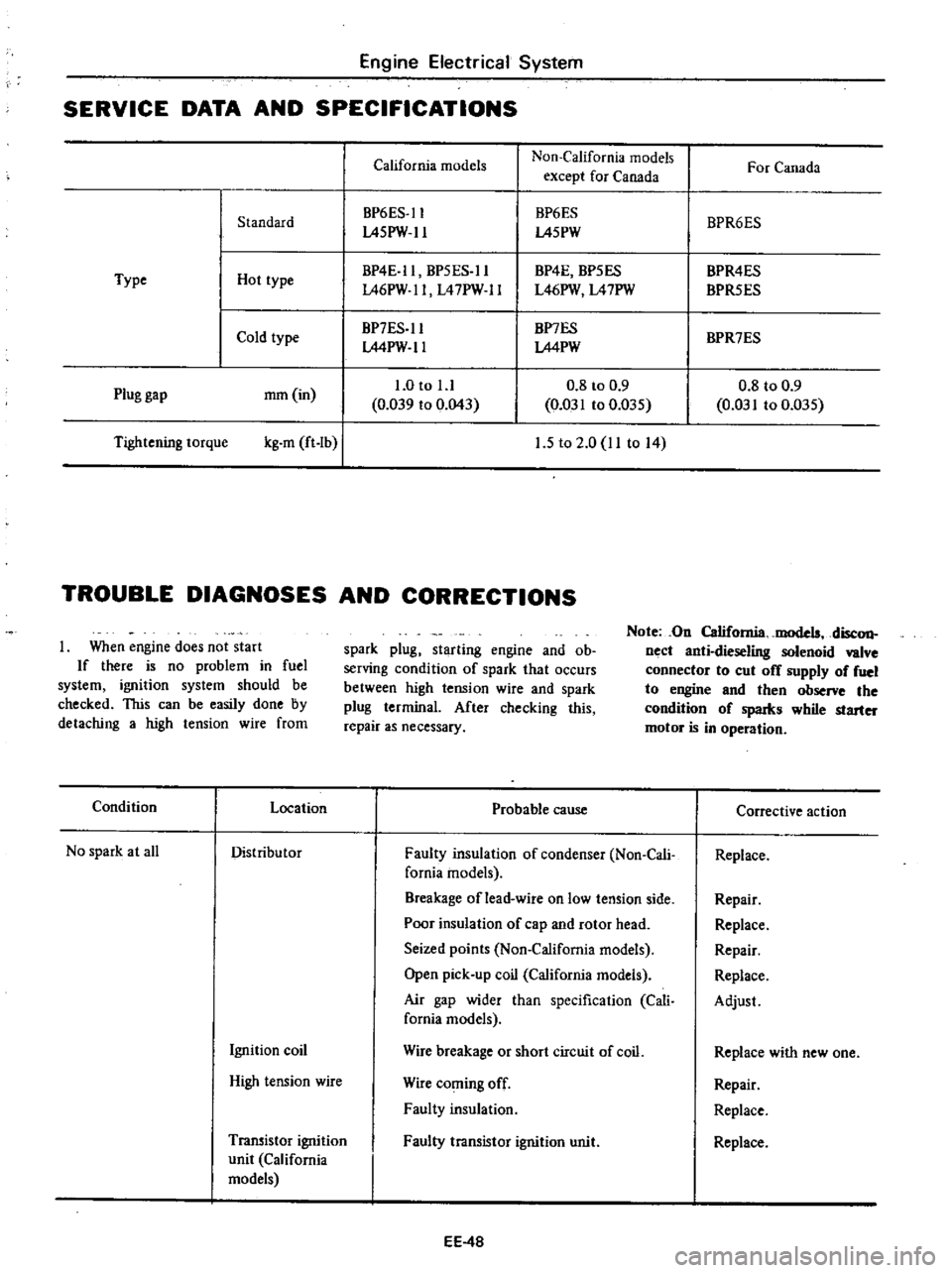
Engine
Electrical
System
SERVICE
DATA
AND
SPECIFICATIONS
California
models
Non
California
models
For
Canada
except
for
Canada
BP6ES
ll
BP6ES
BPR6ES
Standard
L45PW
ll
L45PW
BP4E
ll
BP5ES
ll
BP4E
BP5ES
BPR4ES
Type
Hot
type
L46PW
ll
L47PW
ll
L46PW
L47PW
BPR5ES
Cold
type
BP7ES
ll
BP7ES
BPR7ES
LMPW
ll
LMPW
1
0
to
l
l
0
8
to
0
9
0
8
to
0
9
Plug
gap
mm
in
0
039
to
0
043
0
031
to
0
D35
0
031
to
0
035
Tightening
torque
kg
m
ft
Ib
I
1
5
to
2
0
11
to
14
TROUBLE
DIAGNOSES
AND
CORRECTIONS
When
engine
does
not
start
If
there
is
no
problem
in
fuel
system
ignition
system
should
be
checked
This
can
be
easily
done
by
detaching
a
high
tension
wire
from
spark
plug
starting
engine
and
ob
serving
condition
of
spark
that
occurs
between
high
tension
wire
and
spark
plug
terminal
After
checking
this
repair
as
necessary
Note
On
California
models
disc
on
nect
anti
dieseling
solenoid
valve
connector
to
cut
off
supply
of
fuel
to
engine
and
then
observe
the
condition
of
spaIks
while
starter
motor
is
in
operation
Condition
Location
Probable
cause
Corrective
action
No
spark
at
all
Distributor
Faulty
insulation
of
condenser
Non
Cali
Replace
fomia
models
Breakage
of
lead
wire
on
low
tension
side
Repair
Poor
insulation
of
cap
and
rotor
head
Replace
Seized
points
Non
California
models
Repair
Open
pick
up
coil
California
models
Replace
Air
gap
wider
than
specification
Cali
Adjust
fornia
models
Ignition
coil
Wire
breakage
or
short
circuit
of
coil
Replace
with
new
one
High
tension
wire
Wire
coming
off
Repair
Faulty
insulation
Replace
Transistor
ignition
Faulty
transistor
ignition
unit
Replace
unit
California
models
EE
4B
Page 417 of 537
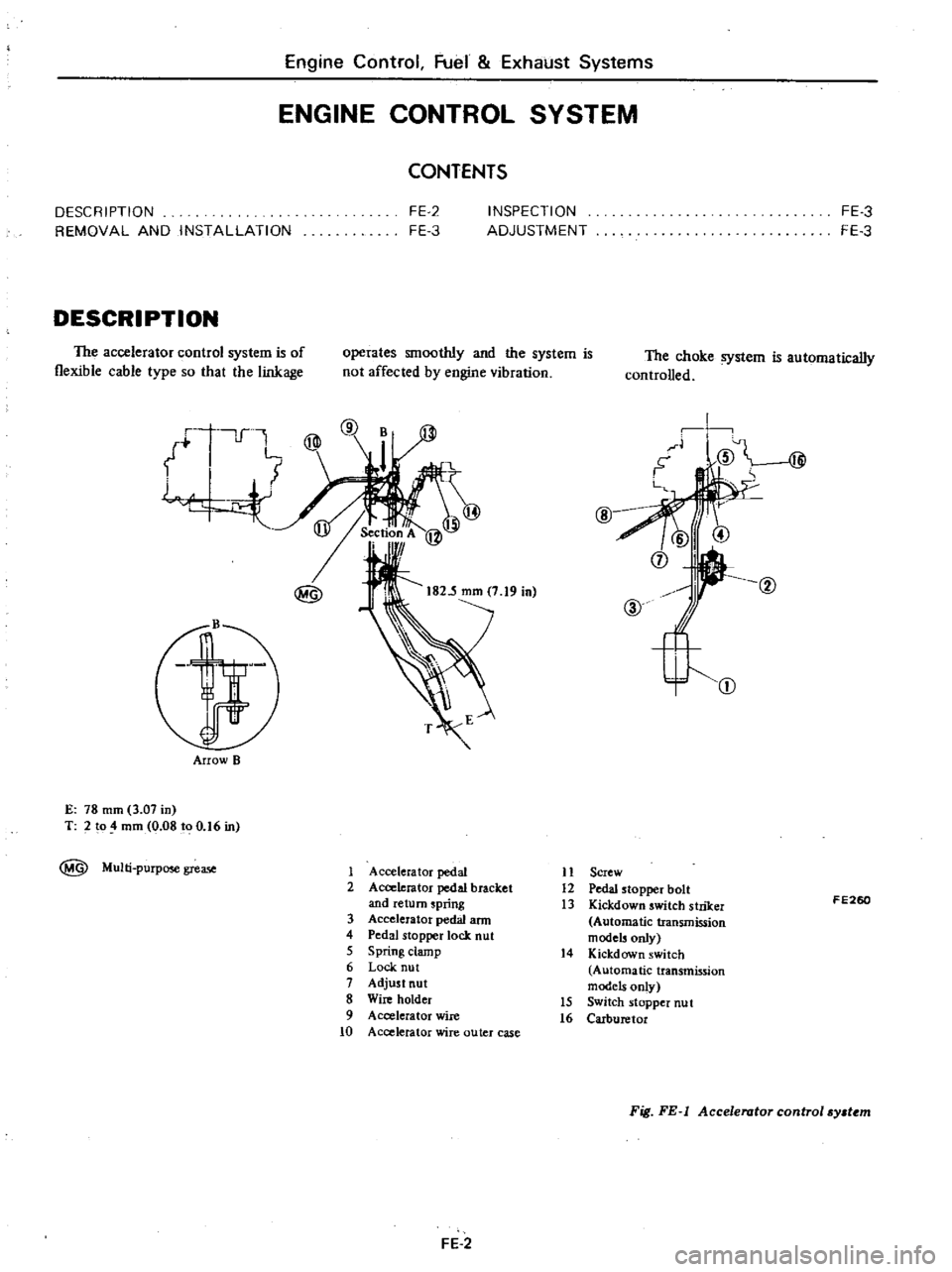
Engine
Control
Fuel
Exhaust
Systems
ENGINE
CONTROL
SYSTEM
CONTENTS
DESCRIPTION
REMOVAL
AND
INSTAllATION
INSPECTION
ADJUSTMENT
FE
2
FE
3
DESCRIPTION
The
accelerator
control
system
is
of
flexible
cable
type
so
that
the
linkage
operates
smoothly
and
the
system
is
not
affected
by
engine
vibration
u
l
f
L
4
@
Arrow
B
E
78
mm
3
07
in
T
2
to
4
mm
0
08
to
0
16
in
MUlti
purpose
grease
FE
3
FE
3
The
choke
system
is
automatically
controlled
i
p
@
I
@
@
CV
j
I
Accelerator
pedal
II
Screw
2
Accelerator
pedal
bracket
12
Pedal
stopper
bolt
and
return
spring
13
Kickdown
switch
striker
3
Accelerator
pedal
arm
Automatic
transmission
4
Pedal
stopper
lock
nut
models
only
5
S
pring
clamp
14
Kickdown
switch
6
Lock
nut
Automatic
transmission
7
Adjust
nut
models
only
8
Wire
holder
15
Switch
stopper
nu
t
9
Accelerator
wire
16
Carburetor
10
Accelerator
wire
outer
case
FE
2
FE260
Fig
FE
l
Accelerator
control
sy
t
m
Page 420 of 537
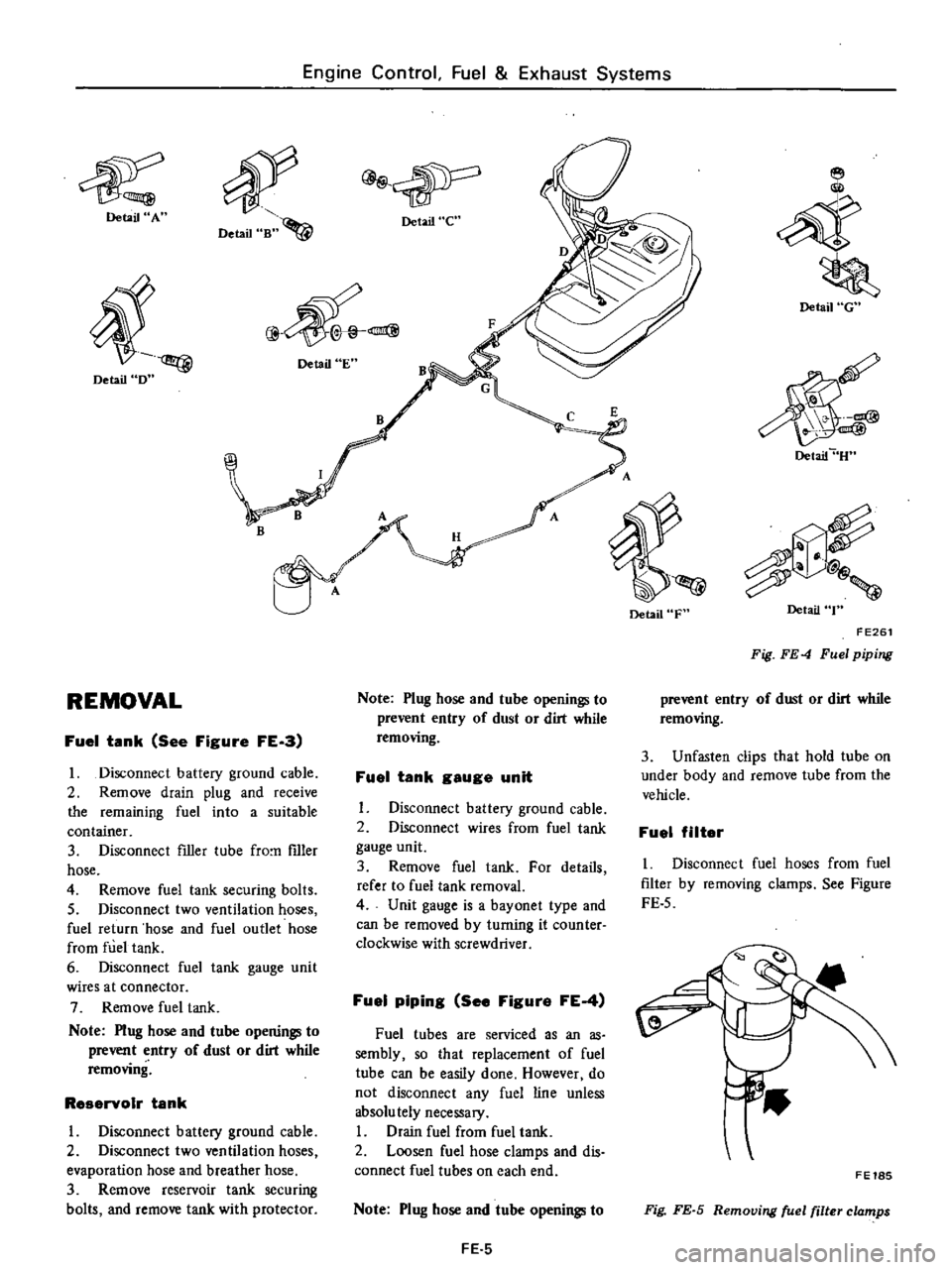
Detail
A
Detail
D
REMOVAL
Engine
Control
Fuel
Exhaust
Systems
Detail
Bn
4
Detail
e
@
Detail
E
B
Fuel
tank
See
Figure
FE
a
I
Disconnect
battery
ground
cable
2
Remove
drain
plug
and
receive
the
remaining
fuel
into
a
suitable
container
3
Disconnect
filler
tube
fro
filler
hose
4
Remove
fuel
tank
securing
bolts
5
Disconnect
two
ventilation
hoses
fuel
return
hose
and
fuel
outlet
hose
from
fuel
tank
6
Disconnect
fuel
tank
gauge
unit
wires
at
connector
7
Remove
fuel
tank
Note
Plug
hose
and
tube
opening
l
to
prevent
entry
of
dust
or
dirt
while
removing
ReservoIr
tank
1
Disconnect
battery
ground
cable
2
Disconnect
two
ventilation
hoses
evaporation
hose
and
breather
hose
3
Remove
reservoir
tank
securing
bolts
and
remove
tank
with
protector
Note
Plug
hose
and
tube
opening
l
to
prevent
entry
of
dust
or
dirt
while
removing
Fuel
tank
gauge
unit
Disconnect
battery
ground
cable
2
Disconnect
wires
from
fuel
tank
gauge
unit
3
Remove
fuel
tank
For
details
refer
to
fuel
tank
removal
4
Unit
gauge
is
a
bayonet
type
and
can
be
removed
by
turning
it
counter
clockwise
with
screwdriver
Fuel
piping
See
Figure
FE
4
Fuel
tubes
are
serviced
as
an
as
sembly
so
that
replacement
of
fuel
tube
can
be
easily
done
However
do
not
disconnect
any
fuel
line
unless
absolu
tely
necessary
I
Drain
fuel
from
fuel
tank
2
Loosen
fuel
hose
clamps
and
dis
connect
fuel
tubes
on
each
end
Note
Plug
hose
and
tube
openings
to
FE
5
Detail
F
Detail
G
Detail
U
Detail
T
FE261
Fig
FE
4
Fuel
piping
prevent
entry
of
dust
or
dirt
while
removing
3
Unfasten
clips
that
hold
tube
on
under
body
and
remove
tube
from
the
vehicle
Fuel
filter
I
Disconnect
fuel
hoses
from
fuel
filter
by
removing
clamps
See
Figure
FE
5
FE18S
Fig
FE
S
Removing
fuel
filter
clamps
Page 421 of 537
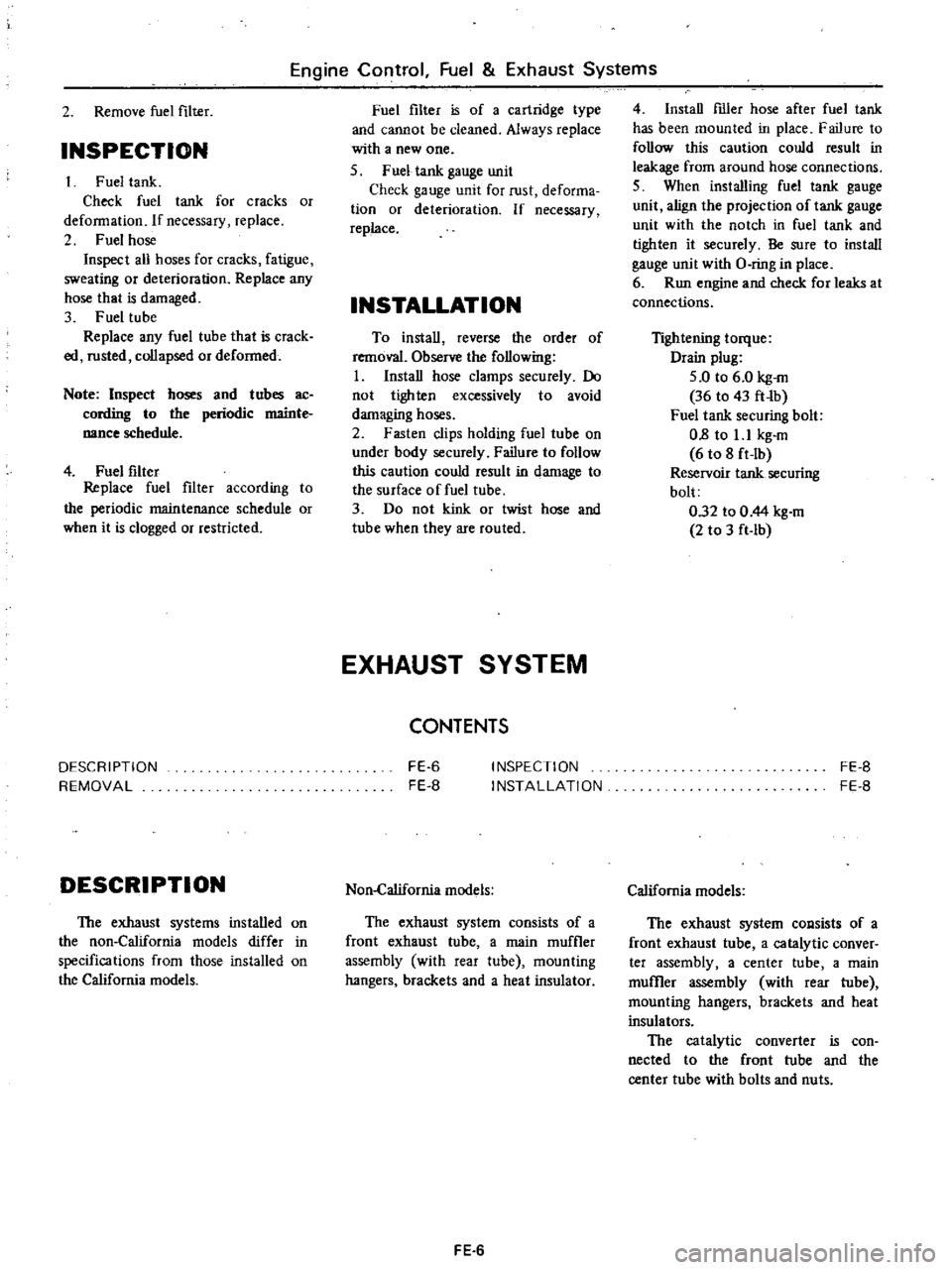
Engine
Control
Fuel
Exhaust
Systems
2
Remove
fuel
filter
INSPECTION
Fuel
tanle
Check
fuel
tank
for
cracks
or
deformation
If
necessary
replace
2
Fuel
hose
Inspect
all
hoses
for
cracks
fatigue
sweating
or
deterioration
Replace
any
hose
that
is
damaged
3
Fuel
tube
Replace
any
fuel
tube
that
is
crack
ed
rusted
collapsed
or
deformed
Note
Inspect
hoses
and
tubes
ac
cording
to
the
periodic
mainte
nance
schedule
4
Fuel
filter
Replace
fuel
filter
according
to
the
periodic
maintenance
schedule
or
when
it
is
clogged
or
restricted
DESCRIPTION
REMOVAL
DESCRIPTION
The
exhaust
systems
installed
on
the
non
California
models
differ
in
specifications
from
those
installed
on
the
California
models
Fuel
filter
is
of
a
cartridge
type
and
cannot
be
cleaned
Always
replace
with
a
new
one
5
Fuel
tank
gauge
unit
Check
gauge
unit
for
rust
deforma
tion
or
deterioration
If
necessary
replace
INSTALLATION
To
install
reverse
the
order
of
removal
Observe
the
following
I
Install
hose
clamps
securely
Do
not
tighten
excessively
to
avoid
damaging
hoses
2
Fasten
clips
holding
fuel
tube
on
under
body
securely
Failure
to
follow
this
caution
could
result
in
damage
to
the
surface
of
fuel
tube
3
Do
not
kink
or
twist
hose
and
tube
when
they
are
routed
EXHAUST
SYSTEM
CONTENTS
FE
6
FE
8
INSPECTION
INSTAllATION
Non
California
models
The
exhaust
system
consists
of
a
front
exhaust
tube
a
main
muffler
assembly
with
rear
tube
mounting
hangers
brackets
and
a
heat
insulator
FE
6
4
Install
fIller
hose
after
fuel
tank
has
been
mounted
in
place
Failure
to
follow
this
caution
could
result
in
leakage
from
around
hose
connections
5
When
installing
fuel
tank
gauge
unit
align
the
projection
of
tank
gauge
unit
with
the
notch
in
fuel
tank
and
tighten
it
securely
Be
sure
to
install
gauge
unit
with
O
ring
in
place
6
Run
engine
and
check
for
leaks
at
connections
Tightening
torque
Drain
plug
5
0
to
6
0
kg
m
36
to
43
ft
Ib
Fuel
tank
securing
bolt
0
8
to
1
I
kg
m
6
to
8
ft
Ib
Reservoir
tank
securing
bolt
032
to
0
44
kg
m
2
to
3
ft
Ib
FE
8
FE
8
California
models
The
exhaust
system
cOllsists
of
a
front
exhaust
tube
a
catalytic
conver
ter
assembly
a
center
tube
a
main
muffler
assembly
with
rear
tube
mounting
hangers
brackets
and
heat
insulators
The
catalytic
converter
is
COD
nected
to
the
front
tube
and
the
center
tube
with
bolts
and
nuts