DODGE NEON 1999 Service Repair Manual
Manufacturer: DODGE, Model Year: 1999, Model line: NEON, Model: DODGE NEON 1999Pages: 1200, PDF Size: 35.29 MB
Page 1151 of 1200
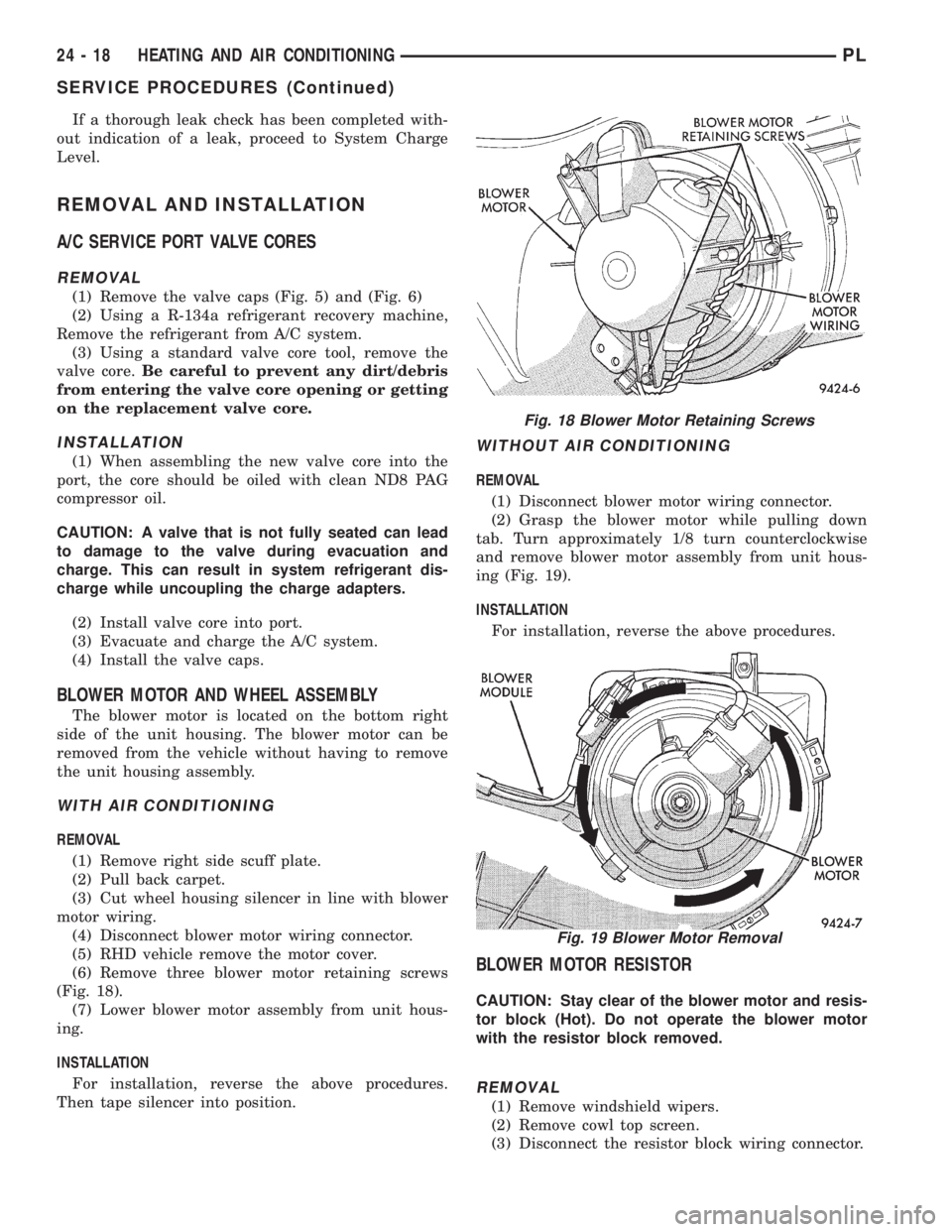
If a thorough leak check has been completed with-
out indication of a leak, proceed to System Charge
Level.
REMOVAL AND INSTALLATION
A/C SERVICE PORT VALVE CORES
REMOVAL
(1) Remove the valve caps (Fig. 5) and (Fig. 6)
(2) Using a R-134a refrigerant recovery machine,
Remove the refrigerant from A/C system.
(3) Using a standard valve core tool, remove the
valve core.Be careful to prevent any dirt/debris
from entering the valve core opening or getting
on the replacement valve core.
INSTALLATION
(1) When assembling the new valve core into the
port, the core should be oiled with clean ND8 PAG
compressor oil.
CAUTION: A valve that is not fully seated can lead
to damage to the valve during evacuation and
charge. This can result in system refrigerant dis-
charge while uncoupling the charge adapters.
(2) Install valve core into port.
(3) Evacuate and charge the A/C system.
(4) Install the valve caps.
BLOWER MOTOR AND WHEEL ASSEMBLY
The blower motor is located on the bottom right
side of the unit housing. The blower motor can be
removed from the vehicle without having to remove
the unit housing assembly.
WITH AIR CONDITIONING
REMOVAL
(1) Remove right side scuff plate.
(2) Pull back carpet.
(3) Cut wheel housing silencer in line with blower
motor wiring.
(4) Disconnect blower motor wiring connector.
(5) RHD vehicle remove the motor cover.
(6) Remove three blower motor retaining screws
(Fig. 18).
(7) Lower blower motor assembly from unit hous-
ing.
INSTALLATION
For installation, reverse the above procedures.
Then tape silencer into position.
WITHOUT AIR CONDITIONING
REMOVAL
(1) Disconnect blower motor wiring connector.
(2) Grasp the blower motor while pulling down
tab. Turn approximately 1/8 turn counterclockwise
and remove blower motor assembly from unit hous-
ing (Fig. 19).
INSTALLATION
For installation, reverse the above procedures.
BLOWER MOTOR RESISTOR
CAUTION: Stay clear of the blower motor and resis-
tor block (Hot). Do not operate the blower motor
with the resistor block removed.
REMOVAL
(1) Remove windshield wipers.
(2) Remove cowl top screen.
(3) Disconnect the resistor block wiring connector.
Fig. 18 Blower Motor Retaining Screws
Fig. 19 Blower Motor Removal
24 - 18 HEATING AND AIR CONDITIONINGPL
SERVICE PROCEDURES (Continued)
Page 1152 of 1200
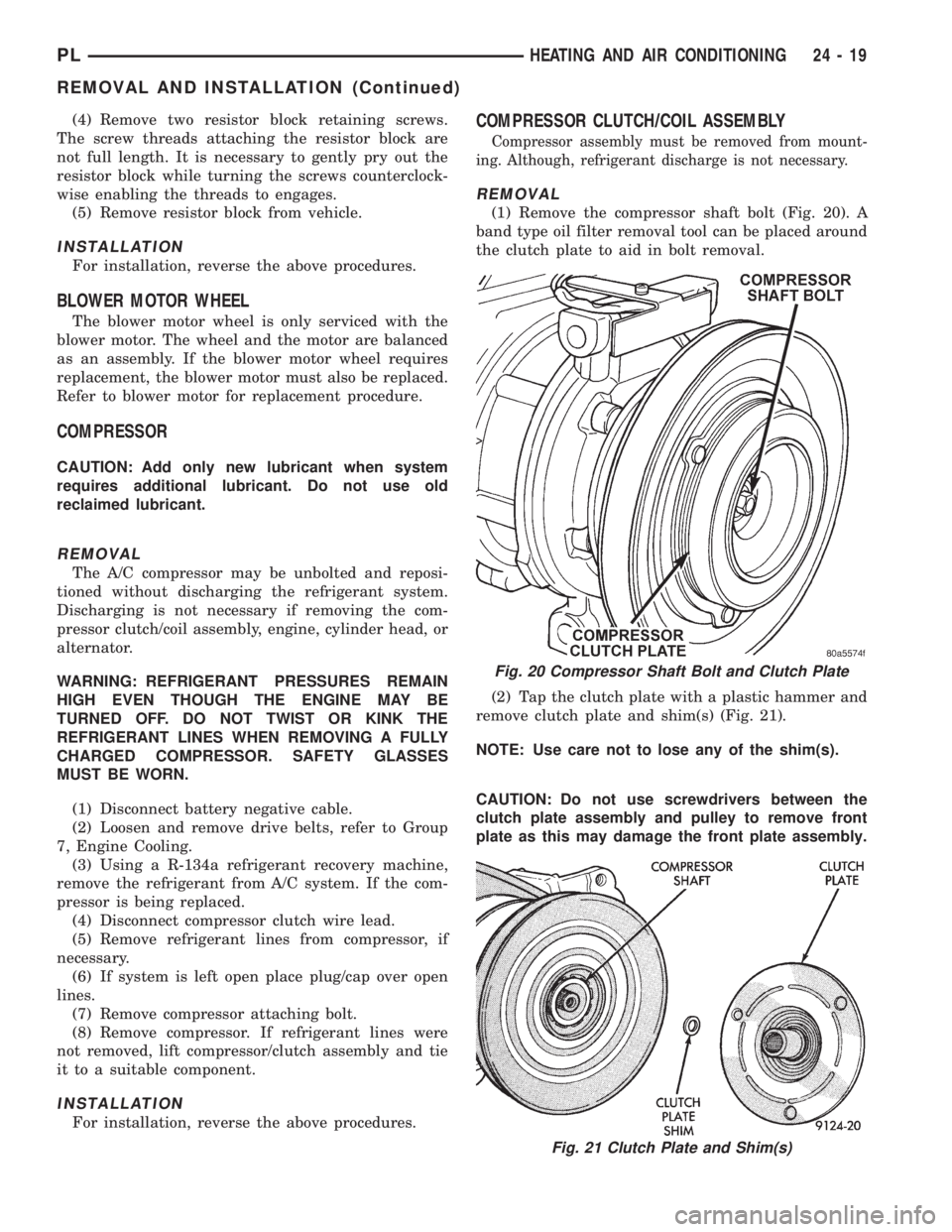
(4) Remove two resistor block retaining screws.
The screw threads attaching the resistor block are
not full length. It is necessary to gently pry out the
resistor block while turning the screws counterclock-
wise enabling the threads to engages.
(5) Remove resistor block from vehicle.
INSTALLATION
For installation, reverse the above procedures.
BLOWER MOTOR WHEEL
The blower motor wheel is only serviced with the
blower motor. The wheel and the motor are balanced
as an assembly. If the blower motor wheel requires
replacement, the blower motor must also be replaced.
Refer to blower motor for replacement procedure.
COMPRESSOR
CAUTION: Add only new lubricant when system
requires additional lubricant. Do not use old
reclaimed lubricant.
REMOVAL
The A/C compressor may be unbolted and reposi-
tioned without discharging the refrigerant system.
Discharging is not necessary if removing the com-
pressor clutch/coil assembly, engine, cylinder head, or
alternator.
WARNING: REFRIGERANT PRESSURES REMAIN
HIGH EVEN THOUGH THE ENGINE MAY BE
TURNED OFF. DO NOT TWIST OR KINK THE
REFRIGERANT LINES WHEN REMOVING A FULLY
CHARGED COMPRESSOR. SAFETY GLASSES
MUST BE WORN.
(1) Disconnect battery negative cable.
(2) Loosen and remove drive belts, refer to Group
7, Engine Cooling.
(3) Using a R-134a refrigerant recovery machine,
remove the refrigerant from A/C system. If the com-
pressor is being replaced.
(4) Disconnect compressor clutch wire lead.
(5) Remove refrigerant lines from compressor, if
necessary.
(6) If system is left open place plug/cap over open
lines.
(7) Remove compressor attaching bolt.
(8) Remove compressor. If refrigerant lines were
not removed, lift compressor/clutch assembly and tie
it to a suitable component.
INSTALLATION
For installation, reverse the above procedures.
COMPRESSOR CLUTCH/COIL ASSEMBLY
Compressor assembly must be removed from mount-
ing. Although, refrigerant discharge is not necessary.
REMOVAL
(1) Remove the compressor shaft bolt (Fig. 20). A
band type oil filter removal tool can be placed around
the clutch plate to aid in bolt removal.
(2) Tap the clutch plate with a plastic hammer and
remove clutch plate and shim(s) (Fig. 21).
NOTE: Use care not to lose any of the shim(s).
CAUTION: Do not use screwdrivers between the
clutch plate assembly and pulley to remove front
plate as this may damage the front plate assembly.
Fig. 20 Compressor Shaft Bolt and Clutch Plate
Fig. 21 Clutch Plate and Shim(s)
PLHEATING AND AIR CONDITIONING 24 - 19
REMOVAL AND INSTALLATION (Continued)
Page 1153 of 1200
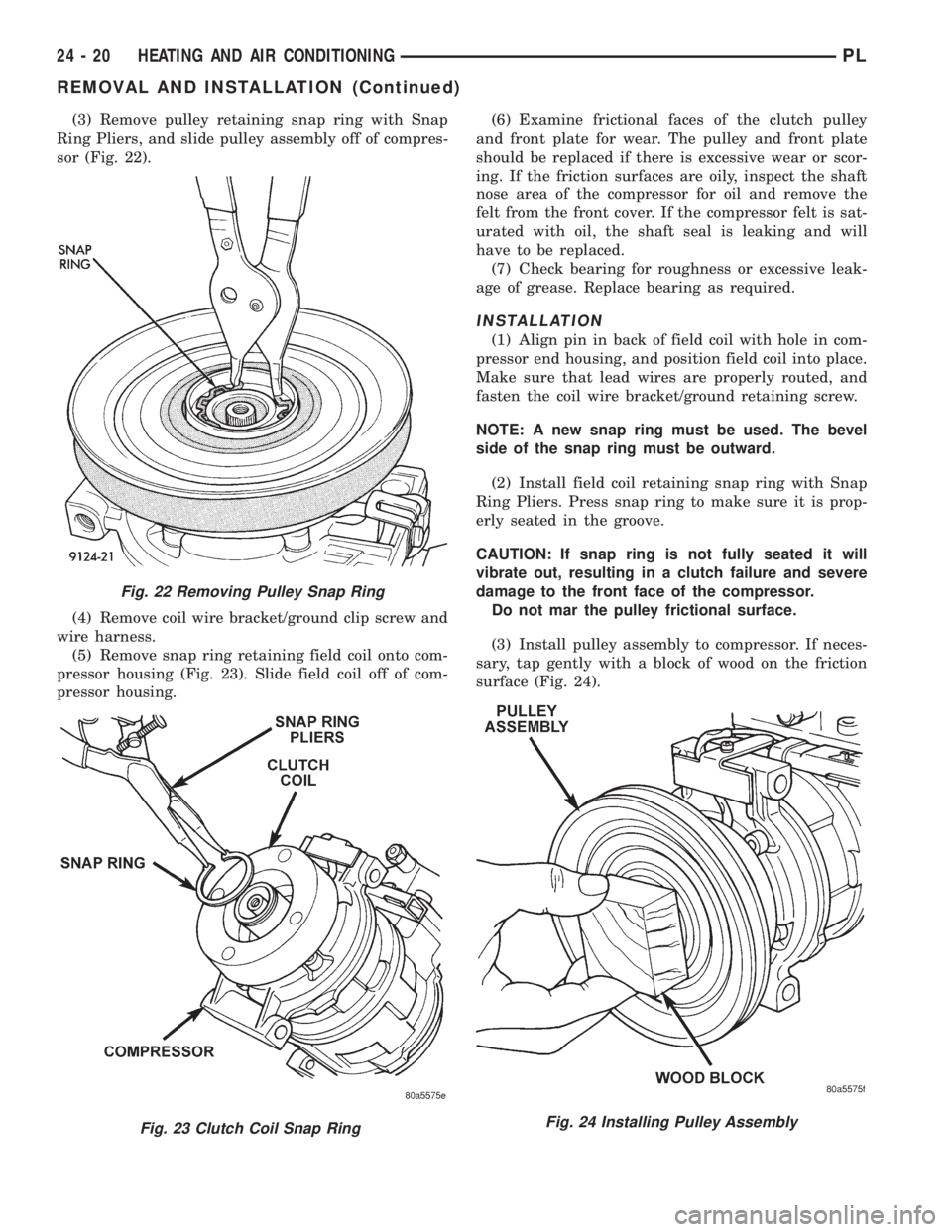
(3) Remove pulley retaining snap ring with Snap
Ring Pliers, and slide pulley assembly off of compres-
sor (Fig. 22).
(4) Remove coil wire bracket/ground clip screw and
wire harness.
(5) Remove snap ring retaining field coil onto com-
pressor housing (Fig. 23). Slide field coil off of com-
pressor housing.(6) Examine frictional faces of the clutch pulley
and front plate for wear. The pulley and front plate
should be replaced if there is excessive wear or scor-
ing. If the friction surfaces are oily, inspect the shaft
nose area of the compressor for oil and remove the
felt from the front cover. If the compressor felt is sat-
urated with oil, the shaft seal is leaking and will
have to be replaced.
(7) Check bearing for roughness or excessive leak-
age of grease. Replace bearing as required.
INSTALLATION
(1) Align pin in back of field coil with hole in com-
pressor end housing, and position field coil into place.
Make sure that lead wires are properly routed, and
fasten the coil wire bracket/ground retaining screw.
NOTE: A new snap ring must be used. The bevel
side of the snap ring must be outward.
(2) Install field coil retaining snap ring with Snap
Ring Pliers. Press snap ring to make sure it is prop-
erly seated in the groove.
CAUTION: If snap ring is not fully seated it will
vibrate out, resulting in a clutch failure and severe
damage to the front face of the compressor.
Do not mar the pulley frictional surface.
(3) Install pulley assembly to compressor. If neces-
sary, tap gently with a block of wood on the friction
surface (Fig. 24).
Fig. 22 Removing Pulley Snap Ring
Fig. 23 Clutch Coil Snap RingFig. 24 Installing Pulley Assembly
24 - 20 HEATING AND AIR CONDITIONINGPL
REMOVAL AND INSTALLATION (Continued)
Page 1154 of 1200
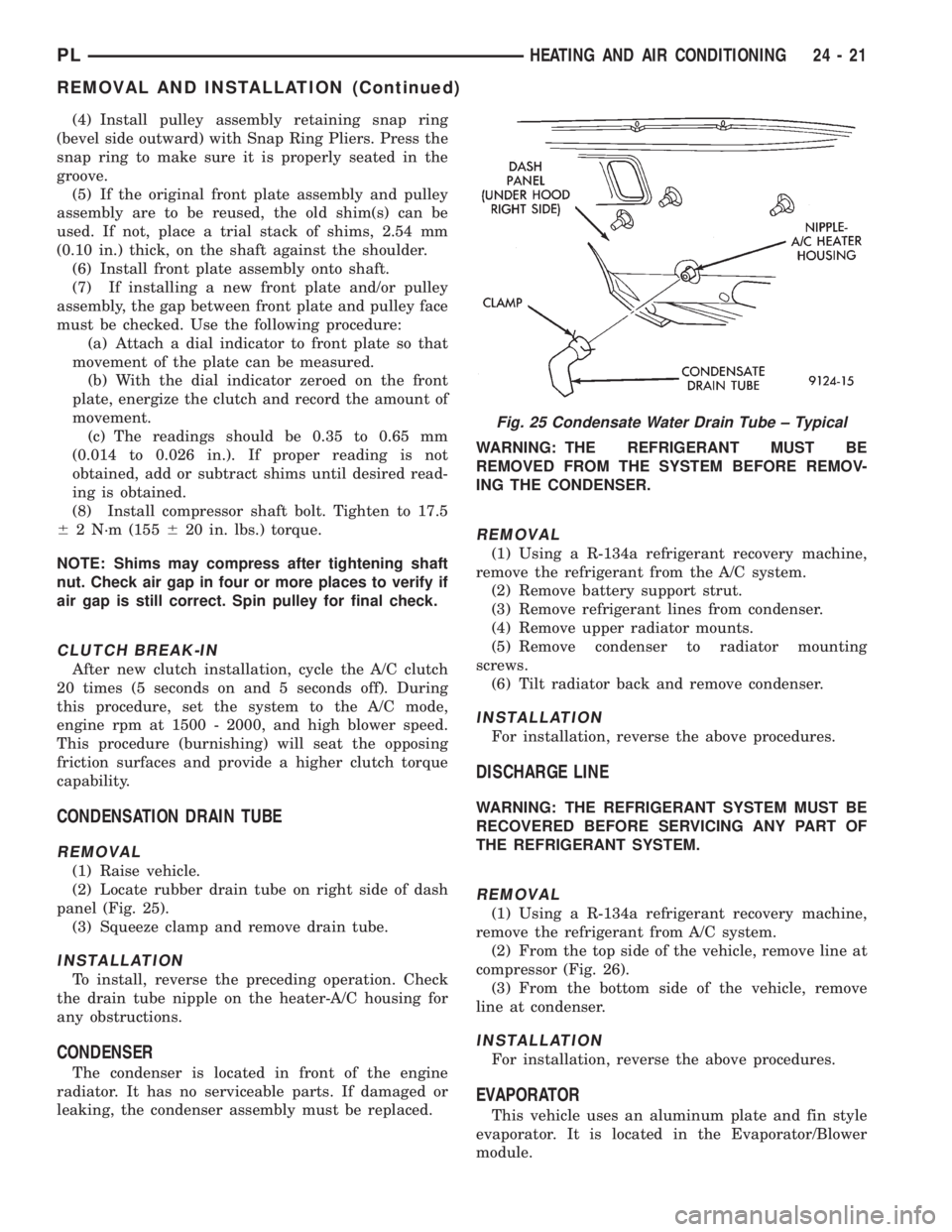
(4) Install pulley assembly retaining snap ring
(bevel side outward) with Snap Ring Pliers. Press the
snap ring to make sure it is properly seated in the
groove.
(5) If the original front plate assembly and pulley
assembly are to be reused, the old shim(s) can be
used. If not, place a trial stack of shims, 2.54 mm
(0.10 in.) thick, on the shaft against the shoulder.
(6) Install front plate assembly onto shaft.
(7) If installing a new front plate and/or pulley
assembly, the gap between front plate and pulley face
must be checked. Use the following procedure:
(a) Attach a dial indicator to front plate so that
movement of the plate can be measured.
(b) With the dial indicator zeroed on the front
plate, energize the clutch and record the amount of
movement.
(c) The readings should be 0.35 to 0.65 mm
(0.014 to 0.026 in.). If proper reading is not
obtained, add or subtract shims until desired read-
ing is obtained.
(8) Install compressor shaft bolt. Tighten to 17.5
62 N´m (155620 in. lbs.) torque.
NOTE: Shims may compress after tightening shaft
nut. Check air gap in four or more places to verify if
air gap is still correct. Spin pulley for final check.
CLUTCH BREAK-IN
After new clutch installation, cycle the A/C clutch
20 times (5 seconds on and 5 seconds off). During
this procedure, set the system to the A/C mode,
engine rpm at 1500 - 2000, and high blower speed.
This procedure (burnishing) will seat the opposing
friction surfaces and provide a higher clutch torque
capability.
CONDENSATION DRAIN TUBE
REMOVAL
(1) Raise vehicle.
(2) Locate rubber drain tube on right side of dash
panel (Fig. 25).
(3) Squeeze clamp and remove drain tube.
INSTALLATION
To install, reverse the preceding operation. Check
the drain tube nipple on the heater-A/C housing for
any obstructions.
CONDENSER
The condenser is located in front of the engine
radiator. It has no serviceable parts. If damaged or
leaking, the condenser assembly must be replaced.WARNING: THE REFRIGERANT MUST BE
REMOVED FROM THE SYSTEM BEFORE REMOV-
ING THE CONDENSER.
REMOVAL
(1) Using a R-134a refrigerant recovery machine,
remove the refrigerant from the A/C system.
(2) Remove battery support strut.
(3) Remove refrigerant lines from condenser.
(4) Remove upper radiator mounts.
(5) Remove condenser to radiator mounting
screws.
(6) Tilt radiator back and remove condenser.
INSTALLATION
For installation, reverse the above procedures.
DISCHARGE LINE
WARNING: THE REFRIGERANT SYSTEM MUST BE
RECOVERED BEFORE SERVICING ANY PART OF
THE REFRIGERANT SYSTEM.
REMOVAL
(1) Using a R-134a refrigerant recovery machine,
remove the refrigerant from A/C system.
(2) From the top side of the vehicle, remove line at
compressor (Fig. 26).
(3) From the bottom side of the vehicle, remove
line at condenser.
INSTALLATION
For installation, reverse the above procedures.
EVAPORATOR
This vehicle uses an aluminum plate and fin style
evaporator. It is located in the Evaporator/Blower
module.
Fig. 25 Condensate Water Drain Tube ± Typical
PLHEATING AND AIR CONDITIONING 24 - 21
REMOVAL AND INSTALLATION (Continued)
Page 1155 of 1200
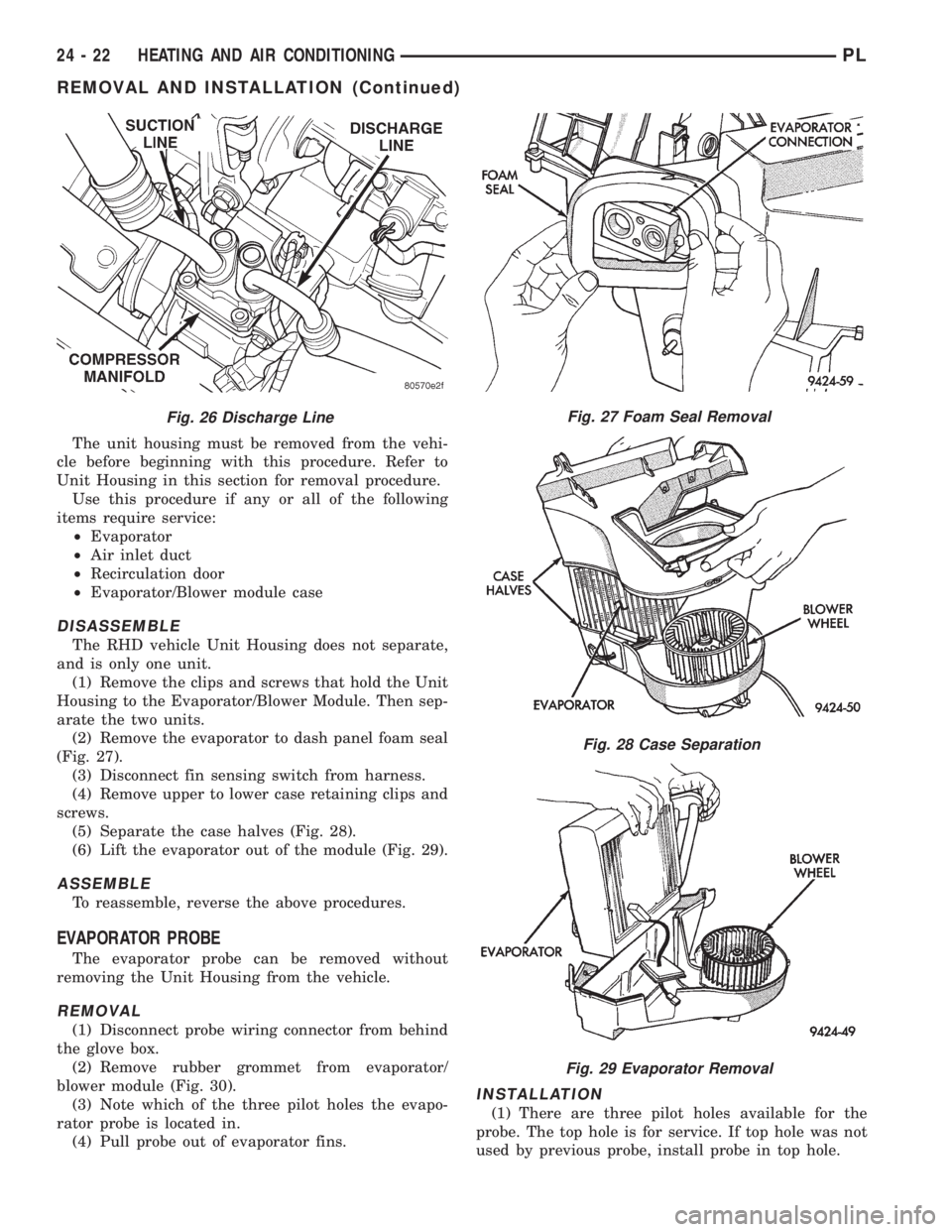
The unit housing must be removed from the vehi-
cle before beginning with this procedure. Refer to
Unit Housing in this section for removal procedure.
Use this procedure if any or all of the following
items require service:
²Evaporator
²Air inlet duct
²Recirculation door
²Evaporator/Blower module case
DISASSEMBLE
The RHD vehicle Unit Housing does not separate,
and is only one unit.
(1) Remove the clips and screws that hold the Unit
Housing to the Evaporator/Blower Module. Then sep-
arate the two units.
(2) Remove the evaporator to dash panel foam seal
(Fig. 27).
(3) Disconnect fin sensing switch from harness.
(4) Remove upper to lower case retaining clips and
screws.
(5) Separate the case halves (Fig. 28).
(6) Lift the evaporator out of the module (Fig. 29).
ASSEMBLE
To reassemble, reverse the above procedures.
EVAPORATOR PROBE
The evaporator probe can be removed without
removing the Unit Housing from the vehicle.
REMOVAL
(1) Disconnect probe wiring connector from behind
the glove box.
(2) Remove rubber grommet from evaporator/
blower module (Fig. 30).
(3) Note which of the three pilot holes the evapo-
rator probe is located in.
(4) Pull probe out of evaporator fins.
INSTALLATION
(1) There are three pilot holes available for the
probe. The top hole is for service. If top hole was not
used by previous probe, install probe in top hole.
Fig. 27 Foam Seal Removal
Fig. 28 Case Separation
Fig. 29 Evaporator Removal
Fig. 26 Discharge Line
24 - 22 HEATING AND AIR CONDITIONINGPL
REMOVAL AND INSTALLATION (Continued)
Page 1156 of 1200

(2) If previous probe was removed from top hole,
use a small plastic stick and make a new hole. Make
the hole 1/4 inch above or below the original hole in
the evaporator core.
(3) Insert new probe into hole between evaporator
fins.
(4) Reinstall rubber grommet into evaporator
probe access hole.
EXPANSION VALVE
WARNING: THE REFRIGERATION SYSTEM MUST
BE COMPLETELY EMPTY BEFORE PROCEEDING
WITH THIS OPERATION.
REMOVAL
(1) Remove the boot-type wire connector from the
pressure cut-off switch.
(2) Remove the center bolt of refrigerant line
plumbing sealing plate (Fig. 31).
(3) Carefully pull the refrigerant line-sealing plate
assembly from the expansion valve towards front of
vehicle. Do not scratch the expansion valve sealing
surfaces with pilot tubes.
(4) Cover the openings on A/C line-sealing plate
assembly to prevent contamination.
(5) Remove two screws securing the expansion
valve to the evaporator sealing plate.
(6) Carefully remove valve.
INSTALLATION
(1) Remove and replace the aluminum gasket on
the evaporator sealing plate.
(2) Carefully hold the expansion valve to the evap-
orator sealing plate so not to scratch the sealing sur-
face. Install two screws and tighten to 1163 N´m
(100630 in. lbs.).
(3) Remove and replace the aluminum gasket on
the refrigerant line- sealing plate assembly.(4) Carefully hold the refrigerant line-sealing plate
assembly to the expansion valve. Install bolt and
tighten to 2363 N´m (200630 in. lbs.).
(5) Connect wires to low pressure cut-off switch.
(6) Evacuate and recharge system.
(7) After expansion valve is installed, system is
charged, and leaks have been checked, repeat A/C
performance check.
A/C FILTER/DRIER
The filter/drier is mounted in a rubber grommet on
the right side of the engine compartment. The refrig-
erant must be recovered from the A/C system before
replacing the filter/drier assembly.
WARNING: THE REFRIGERATION SYSTEM MUST
BE COMPLETELY RECOVERED BEFORE PRO-
CEEDING WITH THIS OPERATION.
REMOVAL
(1) Disconnect liquid line from filter/drier.
(2) Disconnect liquid line on suction line assembly
from filter/drier.
(3) Pull filter/drier out of rubber grommet.
INSTALLATION
For installation, reverse the above procedures.
HIGH PRESSURE CUT OUT SWITCH
WARNING: THE REFRIGERANT MUST BE
REMOVED FROM THE SYSTEM BEFORE REMOV-
ING THE HIGH PRESSURE CUT OUT SWITCH.
REMOVAL
(1) Disconnect wiring connector at the switch (Fig.
32).
(2) Remove internal snap ring.
Fig. 30 Evaporator Probe LocationFig. 31 Expansion Valve
PLHEATING AND AIR CONDITIONING 24 - 23
REMOVAL AND INSTALLATION (Continued)
Page 1157 of 1200
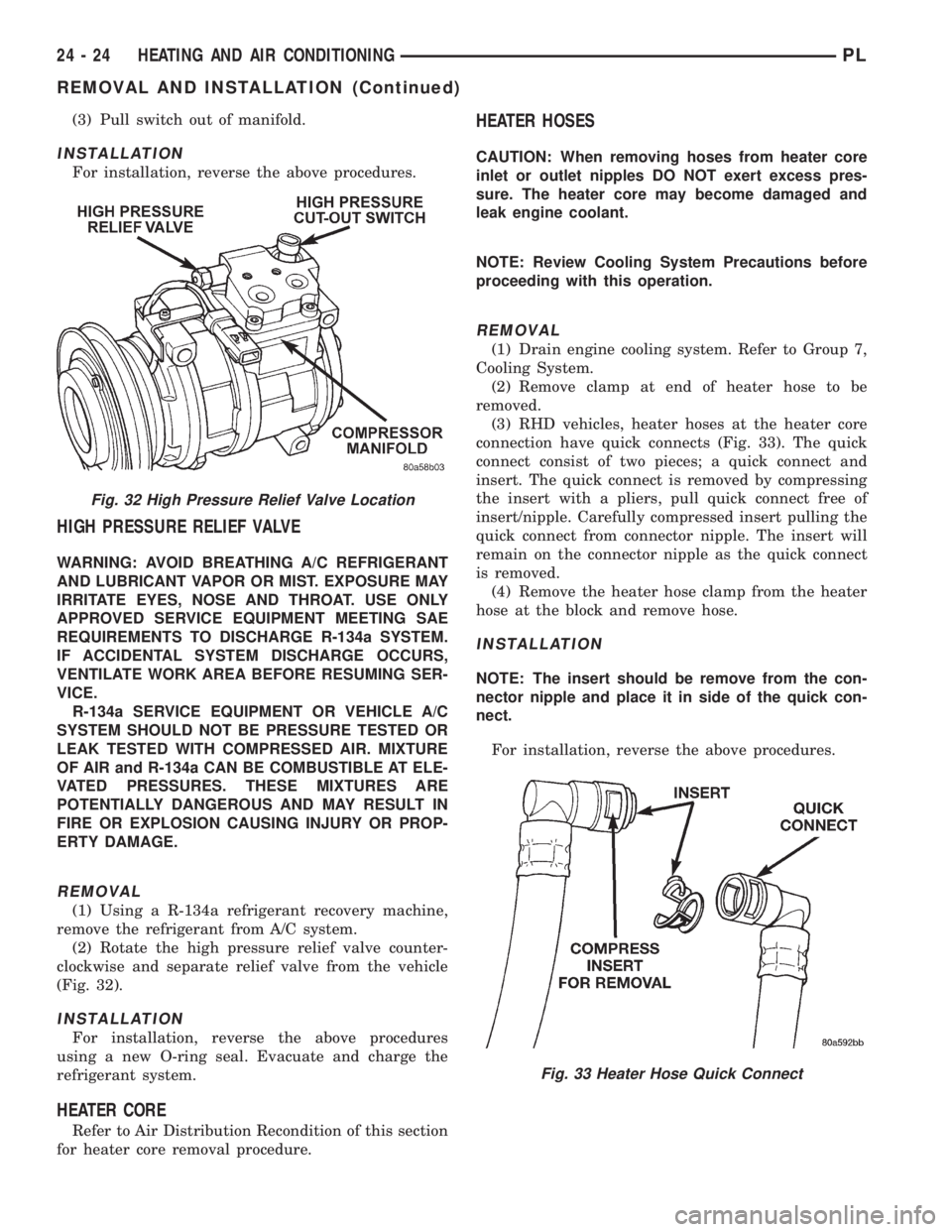
(3) Pull switch out of manifold.
INSTALLATION
For installation, reverse the above procedures.
HIGH PRESSURE RELIEF VALVE
WARNING: AVOID BREATHING A/C REFRIGERANT
AND LUBRICANT VAPOR OR MIST. EXPOSURE MAY
IRRITATE EYES, NOSE AND THROAT. USE ONLY
APPROVED SERVICE EQUIPMENT MEETING SAE
REQUIREMENTS TO DISCHARGE R-134a SYSTEM.
IF ACCIDENTAL SYSTEM DISCHARGE OCCURS,
VENTILATE WORK AREA BEFORE RESUMING SER-
VICE.
R-134a SERVICE EQUIPMENT OR VEHICLE A/C
SYSTEM SHOULD NOT BE PRESSURE TESTED OR
LEAK TESTED WITH COMPRESSED AIR. MIXTURE
OF AIR and R-134a CAN BE COMBUSTIBLE AT ELE-
VATED PRESSURES. THESE MIXTURES ARE
POTENTIALLY DANGEROUS AND MAY RESULT IN
FIRE OR EXPLOSION CAUSING INJURY OR PROP-
ERTY DAMAGE.
REMOVAL
(1) Using a R-134a refrigerant recovery machine,
remove the refrigerant from A/C system.
(2) Rotate the high pressure relief valve counter-
clockwise and separate relief valve from the vehicle
(Fig. 32).
INSTALLATION
For installation, reverse the above procedures
using a new O-ring seal. Evacuate and charge the
refrigerant system.
HEATER CORE
Refer to Air Distribution Recondition of this section
for heater core removal procedure.
HEATER HOSES
CAUTION: When removing hoses from heater core
inlet or outlet nipples DO NOT exert excess pres-
sure. The heater core may become damaged and
leak engine coolant.
NOTE: Review Cooling System Precautions before
proceeding with this operation.
REMOVAL
(1) Drain engine cooling system. Refer to Group 7,
Cooling System.
(2) Remove clamp at end of heater hose to be
removed.
(3) RHD vehicles, heater hoses at the heater core
connection have quick connects (Fig. 33). The quick
connect consist of two pieces; a quick connect and
insert. The quick connect is removed by compressing
the insert with a pliers, pull quick connect free of
insert/nipple. Carefully compressed insert pulling the
quick connect from connector nipple. The insert will
remain on the connector nipple as the quick connect
is removed.
(4) Remove the heater hose clamp from the heater
hose at the block and remove hose.
INSTALLATION
NOTE: The insert should be remove from the con-
nector nipple and place it in side of the quick con-
nect.
For installation, reverse the above procedures.
Fig. 33 Heater Hose Quick Connect
Fig. 32 High Pressure Relief Valve Location
24 - 24 HEATING AND AIR CONDITIONINGPL
REMOVAL AND INSTALLATION (Continued)
Page 1158 of 1200
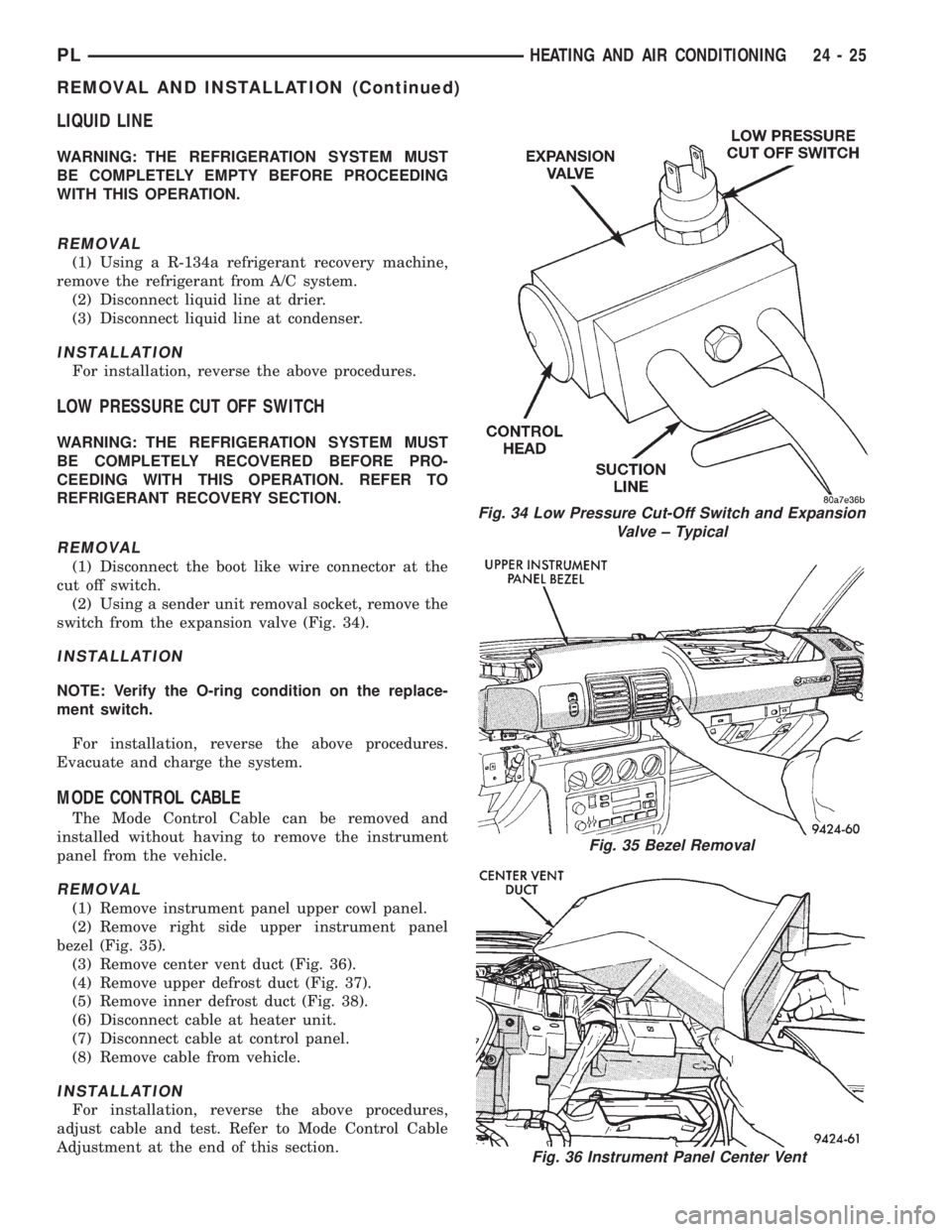
LIQUID LINE
WARNING: THE REFRIGERATION SYSTEM MUST
BE COMPLETELY EMPTY BEFORE PROCEEDING
WITH THIS OPERATION.
REMOVAL
(1) Using a R-134a refrigerant recovery machine,
remove the refrigerant from A/C system.
(2) Disconnect liquid line at drier.
(3) Disconnect liquid line at condenser.
INSTALLATION
For installation, reverse the above procedures.
LOW PRESSURE CUT OFF SWITCH
WARNING: THE REFRIGERATION SYSTEM MUST
BE COMPLETELY RECOVERED BEFORE PRO-
CEEDING WITH THIS OPERATION. REFER TO
REFRIGERANT RECOVERY SECTION.
REMOVAL
(1) Disconnect the boot like wire connector at the
cut off switch.
(2) Using a sender unit removal socket, remove the
switch from the expansion valve (Fig. 34).
INSTALLATION
NOTE: Verify the O-ring condition on the replace-
ment switch.
For installation, reverse the above procedures.
Evacuate and charge the system.
MODE CONTROL CABLE
The Mode Control Cable can be removed and
installed without having to remove the instrument
panel from the vehicle.
REMOVAL
(1) Remove instrument panel upper cowl panel.
(2) Remove right side upper instrument panel
bezel (Fig. 35).
(3) Remove center vent duct (Fig. 36).
(4) Remove upper defrost duct (Fig. 37).
(5) Remove inner defrost duct (Fig. 38).
(6) Disconnect cable at heater unit.
(7) Disconnect cable at control panel.
(8) Remove cable from vehicle.
INSTALLATION
For installation, reverse the above procedures,
adjust cable and test. Refer to Mode Control Cable
Adjustment at the end of this section.
Fig. 34 Low Pressure Cut-Off Switch and Expansion
Valve ± Typical
Fig. 35 Bezel Removal
Fig. 36 Instrument Panel Center Vent
PLHEATING AND AIR CONDITIONING 24 - 25
REMOVAL AND INSTALLATION (Continued)
Page 1159 of 1200
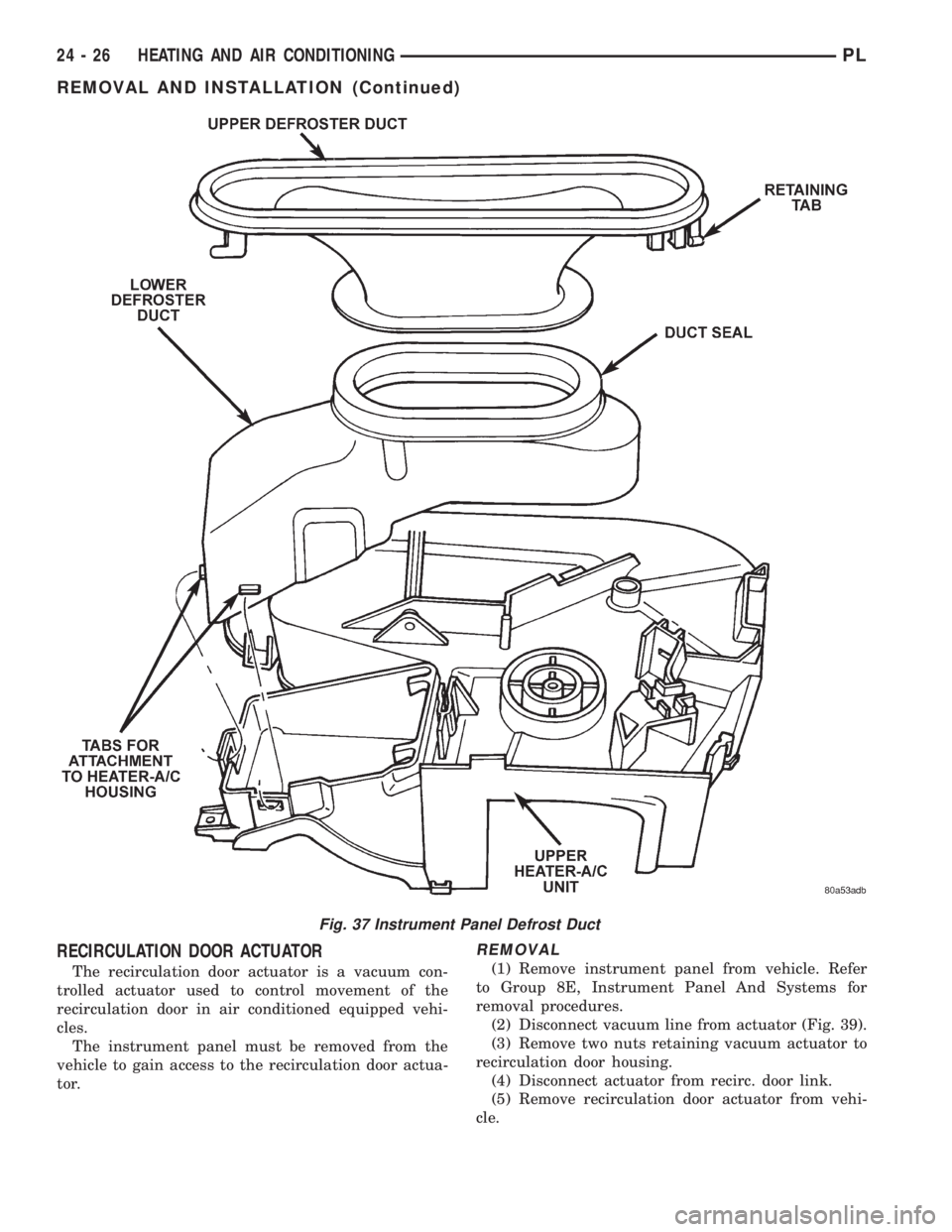
RECIRCULATION DOOR ACTUATOR
The recirculation door actuator is a vacuum con-
trolled actuator used to control movement of the
recirculation door in air conditioned equipped vehi-
cles.
The instrument panel must be removed from the
vehicle to gain access to the recirculation door actua-
tor.
REMOVAL
(1) Remove instrument panel from vehicle. Refer
to Group 8E, Instrument Panel And Systems for
removal procedures.
(2) Disconnect vacuum line from actuator (Fig. 39).
(3) Remove two nuts retaining vacuum actuator to
recirculation door housing.
(4) Disconnect actuator from recirc. door link.
(5) Remove recirculation door actuator from vehi-
cle.
Fig. 37 Instrument Panel Defrost Duct
24 - 26 HEATING AND AIR CONDITIONINGPL
REMOVAL AND INSTALLATION (Continued)
Page 1160 of 1200
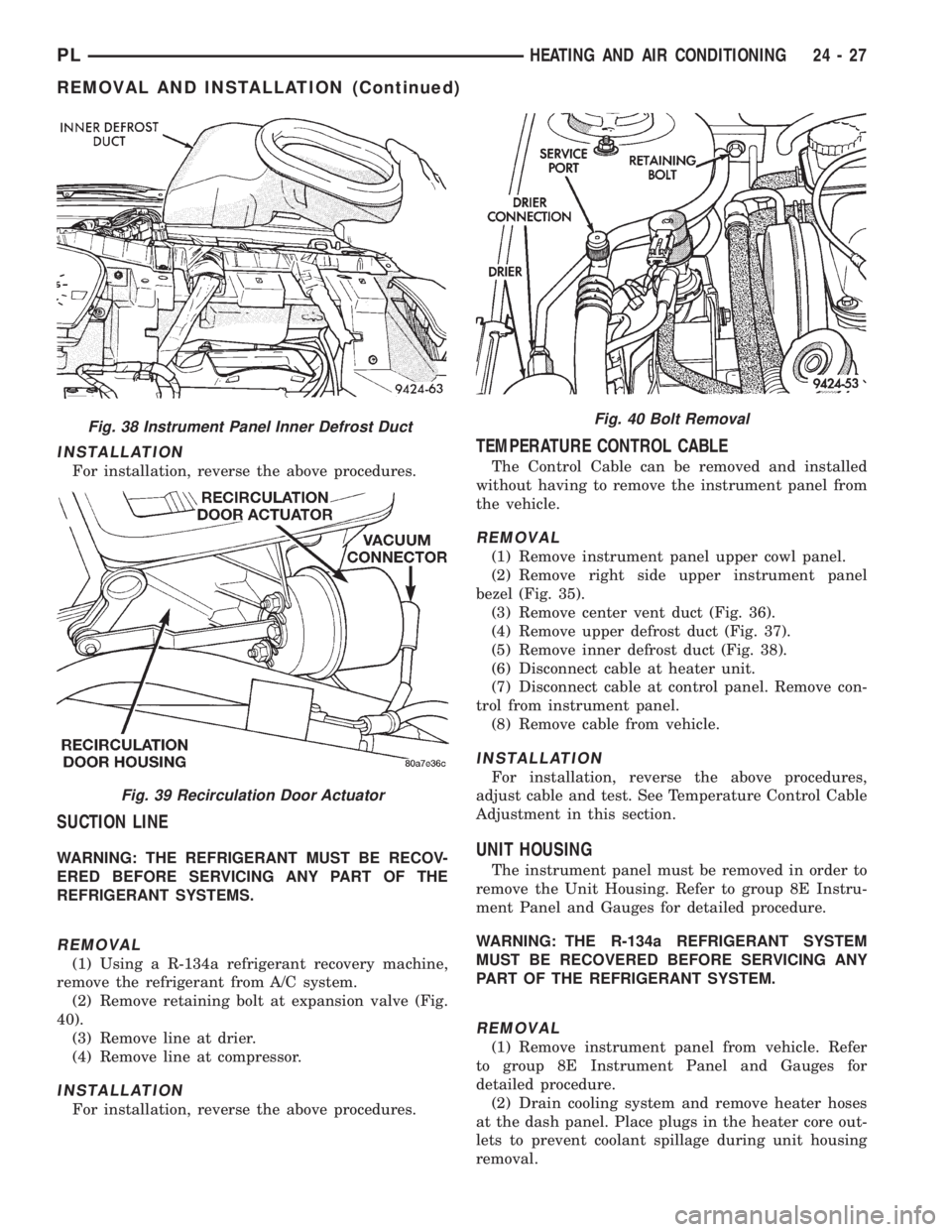
INSTALLATION
For installation, reverse the above procedures.
SUCTION LINE
WARNING: THE REFRIGERANT MUST BE RECOV-
ERED BEFORE SERVICING ANY PART OF THE
REFRIGERANT SYSTEMS.
REMOVAL
(1) Using a R-134a refrigerant recovery machine,
remove the refrigerant from A/C system.
(2) Remove retaining bolt at expansion valve (Fig.
40).
(3) Remove line at drier.
(4) Remove line at compressor.
INSTALLATION
For installation, reverse the above procedures.
TEMPERATURE CONTROL CABLE
The Control Cable can be removed and installed
without having to remove the instrument panel from
the vehicle.
REMOVAL
(1) Remove instrument panel upper cowl panel.
(2) Remove right side upper instrument panel
bezel (Fig. 35).
(3) Remove center vent duct (Fig. 36).
(4) Remove upper defrost duct (Fig. 37).
(5) Remove inner defrost duct (Fig. 38).
(6) Disconnect cable at heater unit.
(7) Disconnect cable at control panel. Remove con-
trol from instrument panel.
(8) Remove cable from vehicle.
INSTALLATION
For installation, reverse the above procedures,
adjust cable and test. See Temperature Control Cable
Adjustment in this section.
UNIT HOUSING
The instrument panel must be removed in order to
remove the Unit Housing. Refer to group 8E Instru-
ment Panel and Gauges for detailed procedure.
WARNING: THE R-134a REFRIGERANT SYSTEM
MUST BE RECOVERED BEFORE SERVICING ANY
PART OF THE REFRIGERANT SYSTEM.
REMOVAL
(1) Remove instrument panel from vehicle. Refer
to group 8E Instrument Panel and Gauges for
detailed procedure.
(2) Drain cooling system and remove heater hoses
at the dash panel. Place plugs in the heater core out-
lets to prevent coolant spillage during unit housing
removal.
Fig. 40 Bolt RemovalFig. 38 Instrument Panel Inner Defrost Duct
Fig. 39 Recirculation Door Actuator
PLHEATING AND AIR CONDITIONING 24 - 27
REMOVAL AND INSTALLATION (Continued)