Motor INFINITI M35 2006 Factory Service Manual
[x] Cancel search | Manufacturer: INFINITI, Model Year: 2006, Model line: M35, Model: INFINITI M35 2006Pages: 5621, PDF Size: 65.56 MB
Page 4610 of 5621
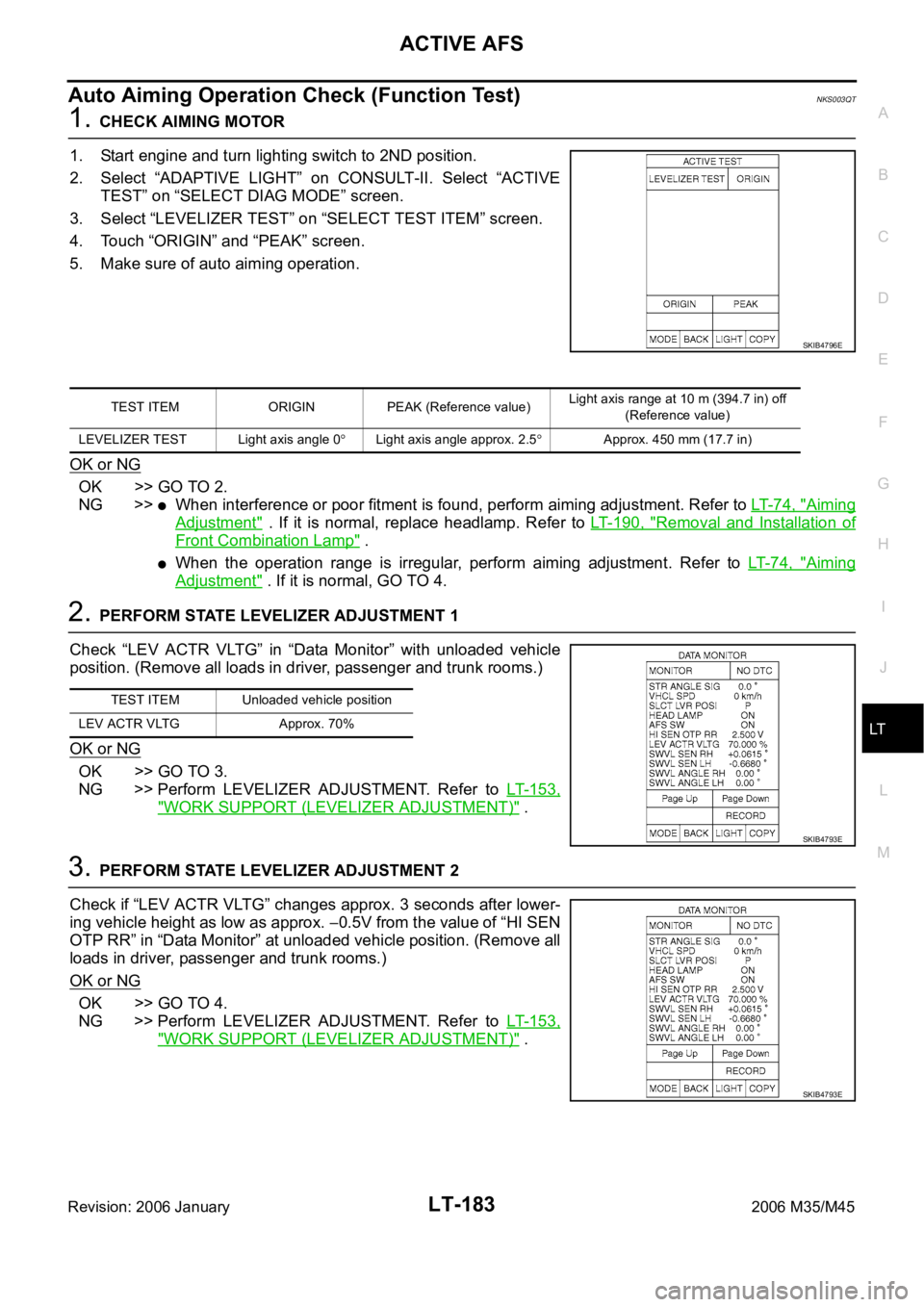
ACTIVE AFS
LT-183
C
D
E
F
G
H
I
J
L
MA
B
LT
Revision: 2006 January2006 M35/M45
Auto Aiming Operation Check (Function Test)NKS003QT
1. CHECK AIMING MOTOR
1. Start engine and turn lighting switch to 2ND position.
2. Select “ADAPTIVE LIGHT” on CONSULT-II. Select “ACTIVE
TEST” on “SELECT DIAG MODE” screen.
3. Select “LEVELIZER TEST” on “SELECT TEST ITEM” screen.
4. Touch “ORIGIN” and “PEAK” screen.
5. Make sure of auto aiming operation.
OK or NG
OK >> GO TO 2.
NG >>
When interference or poor fitment is found, perform aiming adjustment. Refer to LT- 7 4 , "Aiming
Adjustment" . If it is normal, replace headlamp. Refer to LT- 1 9 0 , "Removal and Installation of
Front Combination Lamp" .
When the operation range is irregular, perform aiming adjustment. Refer to LT- 7 4 , "Aiming
Adjustment" . If it is normal, GO TO 4.
2. PERFORM STATE LEVELIZER ADJUSTMENT 1
Check “LEV ACTR VLTG” in “Data Monitor” with unloaded vehicle
position. (Remove all loads in driver, passenger and trunk rooms.)
OK or NG
OK >> GO TO 3.
NG >> Perform LEVELIZER ADJUSTMENT. Refer to LT- 1 5 3 ,
"WORK SUPPORT (LEVELIZER ADJUSTMENT)" .
3. PERFORM STATE LEVELIZER ADJUSTMENT 2
Check if “LEV ACTR VLTG” changes approx. 3 seconds after lower-
ing vehicle height as low as approx.
0.5V from the value of “HI SEN
OTP RR” in “Data Monitor” at unloaded vehicle position. (Remove all
loads in driver, passenger and trunk rooms.)
OK or NG
OK >> GO TO 4.
NG >> Perform LEVELIZER ADJUSTMENT. Refer to LT- 1 5 3 ,
"WORK SUPPORT (LEVELIZER ADJUSTMENT)" .
SKIB4796E
TEST ITEM ORIGIN PEAK (Reference value)Light axis range at 10 m (394.7 in) off
(Reference value)
LEVELIZER TEST Light axis angle 0
Light axis angle approx. 2.5Approx. 450 mm (17.7 in)
TEST ITEM Unloaded vehicle position
LEV ACTR VLTG Approx. 70%
SKIB4793E
SKIB4793E
Page 4611 of 5621
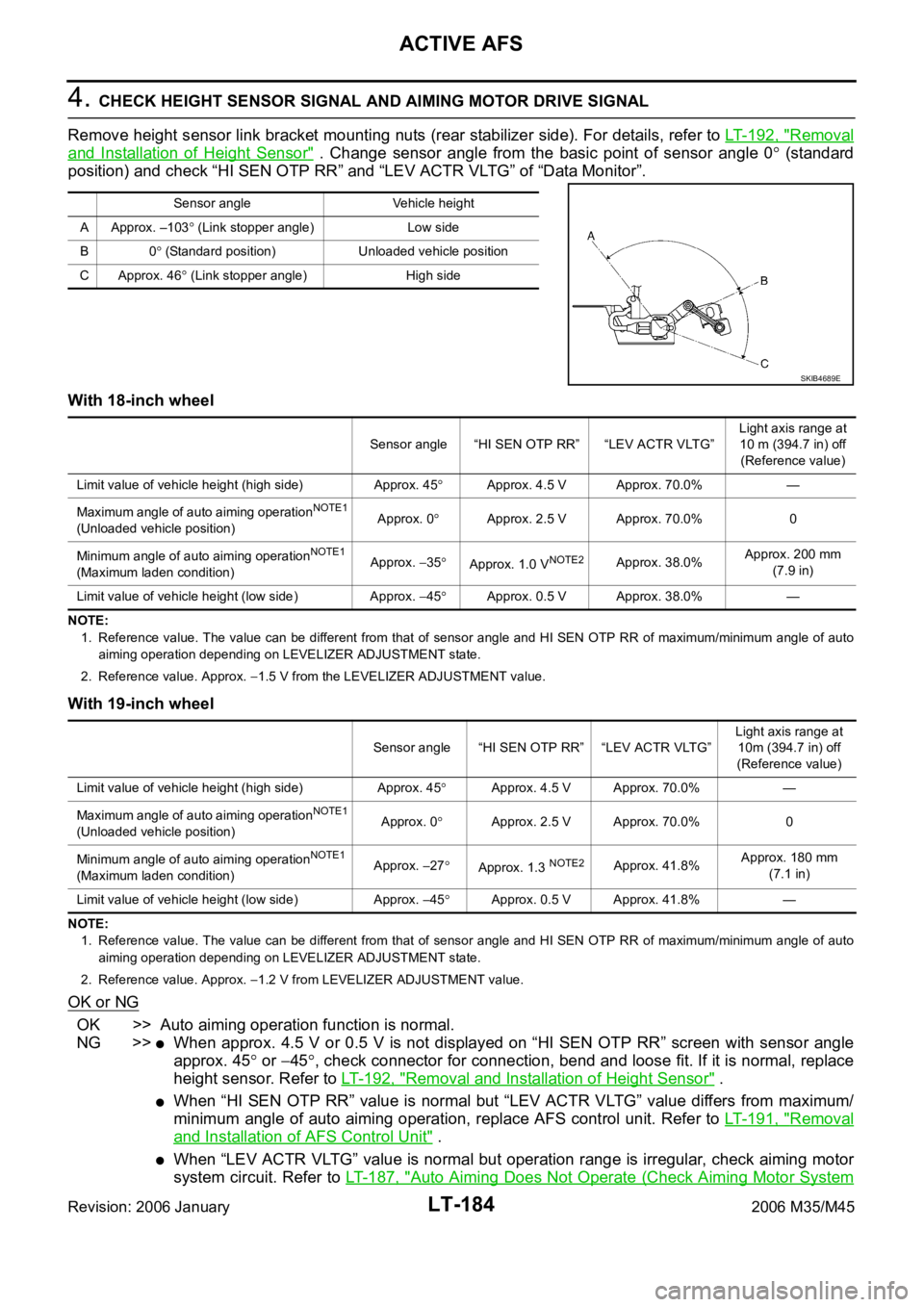
LT-184
ACTIVE AFS
Revision: 2006 January2006 M35/M45
4. CHECK HEIGHT SENSOR SIGNAL AND AIMING MOTOR DRIVE SIGNAL
Remove height sensor link bracket mounting nuts (rear stabilizer side). For details, refer to LT- 1 9 2 , "
Removal
and Installation of Height Sensor" . Change sensor angle from the basic point of sensor angle 0 (standard
position) and check “HI SEN OTP RR” and “LEV ACTR VLTG” of “Data Monitor”.
With 18-inch wheel
NOTE:
1. Reference value. The value can be different from that of sensor angle and HI SEN OTP RR of maximum/minimum angle of auto
aiming operation depending on LEVELIZER ADJUSTMENT state.
2. Reference value. Approx.
1.5 V from the LEVELIZER ADJUSTMENT value.
With 19-inch wheel
NOTE:
1. Reference value. The value can be different from that of sensor angle and HI SEN OTP RR of maximum/minimum angle of auto
aiming operation depending on LEVELIZER ADJUSTMENT state.
2. Reference value. Approx.
1.2 V from LEVELIZER ADJUSTMENT value.
OK or NG
OK >> Auto aiming operation function is normal.
NG >>
When approx. 4.5 V or 0.5 V is not displayed on “HI SEN OTP RR” screen with sensor angle
approx. 45
or 45, check connector for connection, bend and loose fit. If it is normal, replace
height sensor. Refer to LT- 1 9 2 , "
Removal and Installation of Height Sensor" .
When “HI SEN OTP RR” value is normal but “LEV ACTR VLTG” value differs from maximum/
minimum angle of auto aiming operation, replace AFS control unit. Refer to LT- 1 9 1 , "
Removal
and Installation of AFS Control Unit" .
When “LEV ACTR VLTG” value is normal but operation range is irregular, check aiming motor
system circuit. Refer to LT- 1 8 7 , "
Auto Aiming Does Not Operate (Check Aiming Motor System
Sensor angle Vehicle height
A Approx. –103
(Link stopper angle) Low side
B0
(Standard position) Unloaded vehicle position
C Approx. 46
(Link stopper angle) High side
SKIB4689E
Sensor angle “HI SEN OTP RR” “LEV ACTR VLTG”Light axis range at
10 m (394.7 in) off
(Reference value)
Limit value of vehicle height (high side) Approx. 45
Approx. 4.5 V Approx. 70.0% —
Maximum angle of auto aiming operation
NOTE1
(Unloaded vehicle position)Approx. 0Approx. 2.5 V Approx. 70.0% 0
Minimum angle of auto aiming operation
NOTE1
(Maximum laden condition)Approx. 35Approx. 1.0 VNOTE2Approx. 38.0%Approx. 200 mm
(7.9 in)
Limit value of vehicle height (low side) Approx.
45Approx. 0.5 V Approx. 38.0% —
Sensor angle “HI SEN OTP RR” “LEV ACTR VLTG”Light axis range at
10m (394.7 in) off
(Reference value)
Limit value of vehicle height (high side) Approx. 45
Approx. 4.5 V Approx. 70.0% —
Maximum angle of auto aiming operation
NOTE1
(Unloaded vehicle position)Approx. 0Approx. 2.5 V Approx. 70.0% 0
Minimum angle of auto aiming operation
NOTE1
(Maximum laden condition)Approx. 27Approx. 1.3 NOTE2Approx. 41.8%Approx. 180 mm
(7.1 in)
Limit value of vehicle height (low side) Approx.
45Approx. 0.5 V Approx. 41.8% —
Page 4614 of 5621
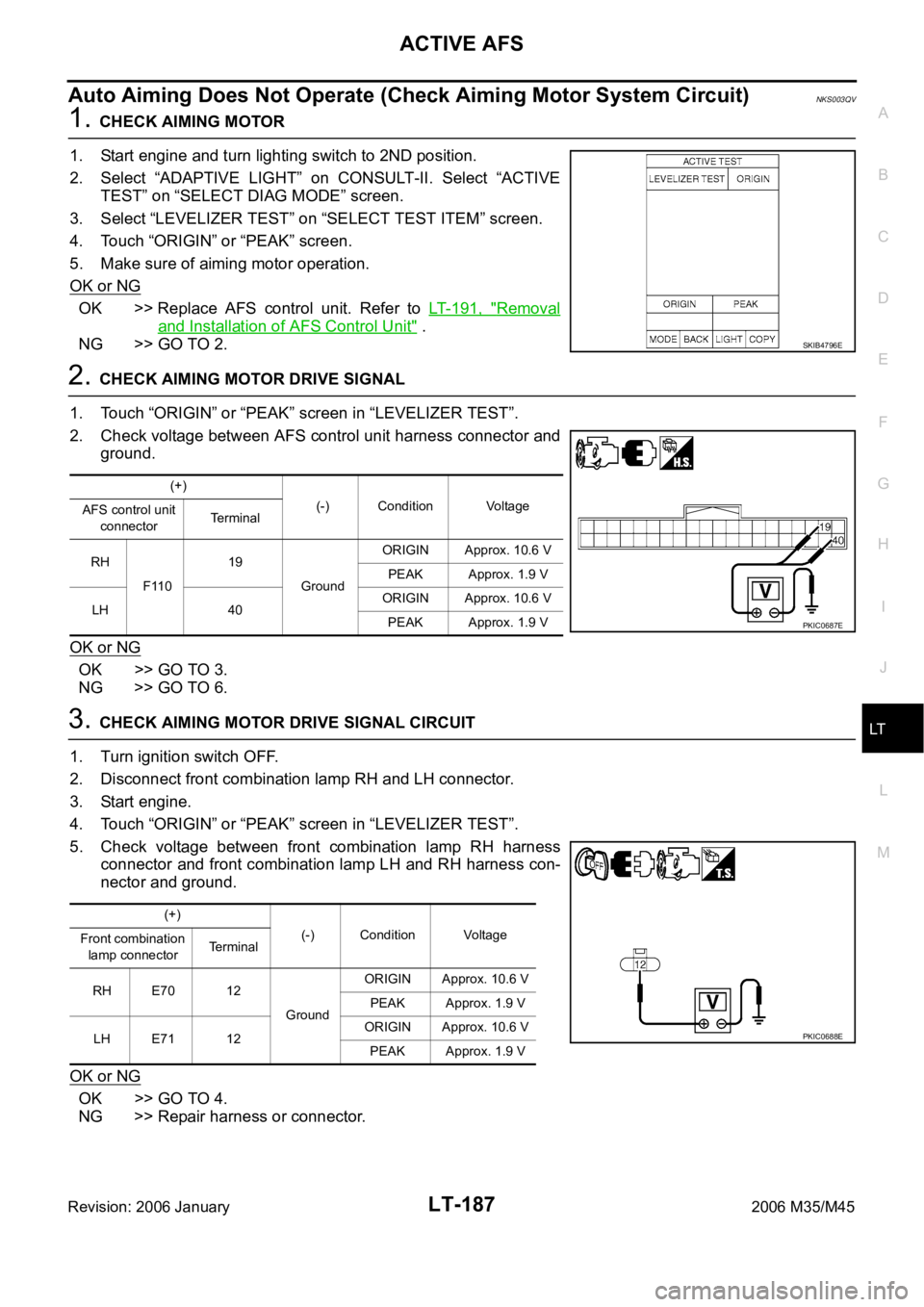
ACTIVE AFS
LT-187
C
D
E
F
G
H
I
J
L
MA
B
LT
Revision: 2006 January2006 M35/M45
Auto Aiming Does Not Operate (Check Aiming Motor System Circuit)NKS003QV
1. CHECK AIMING MOTOR
1. Start engine and turn lighting switch to 2ND position.
2. Select “ADAPTIVE LIGHT” on CONSULT-II. Select “ACTIVE
TEST” on “SELECT DIAG MODE” screen.
3. Select “LEVELIZER TEST” on “SELECT TEST ITEM” screen.
4. Touch “ORIGIN” or “PEAK” screen.
5. Make sure of aiming motor operation.
OK or NG
OK >> Replace AFS control unit. Refer to LT- 1 9 1 , "Removal
and Installation of AFS Control Unit" .
NG >> GO TO 2.
2. CHECK AIMING MOTOR DRIVE SIGNAL
1. Touch “ORIGIN” or “PEAK” screen in “LEVELIZER TEST”.
2. Check voltage between AFS control unit harness connector and
ground.
OK or NG
OK >> GO TO 3.
NG >> GO TO 6.
3. CHECK AIMING MOTOR DRIVE SIGNAL CIRCUIT
1. Turn ignition switch OFF.
2. Disconnect front combination lamp RH and LH connector.
3. Start engine.
4. Touch “ORIGIN” or “PEAK” screen in “LEVELIZER TEST”.
5. Check voltage between front combination lamp RH harness
connector and front combination lamp LH and RH harness con-
nector and ground.
OK or NG
OK >> GO TO 4.
NG >> Repair harness or connector.
SKIB4796E
(+)
(-) Condition Voltage
AFS control unit
connectorTerminal
RH
F11019
GroundORIGIN Approx. 10.6 V
PEAK Approx. 1.9 V
LH 40ORIGIN Approx. 10.6 V
PEAK Approx. 1.9 V
PKIC0687E
(+)
(-) Condition Voltage
Front combination
lamp connectorTerminal
RH E70 12
GroundORIGIN Approx. 10.6 V
PEAK Approx. 1.9 V
LH E71 12ORIGIN Approx. 10.6 V
PEAK Approx. 1.9 V
PKIC0688E
Page 4615 of 5621
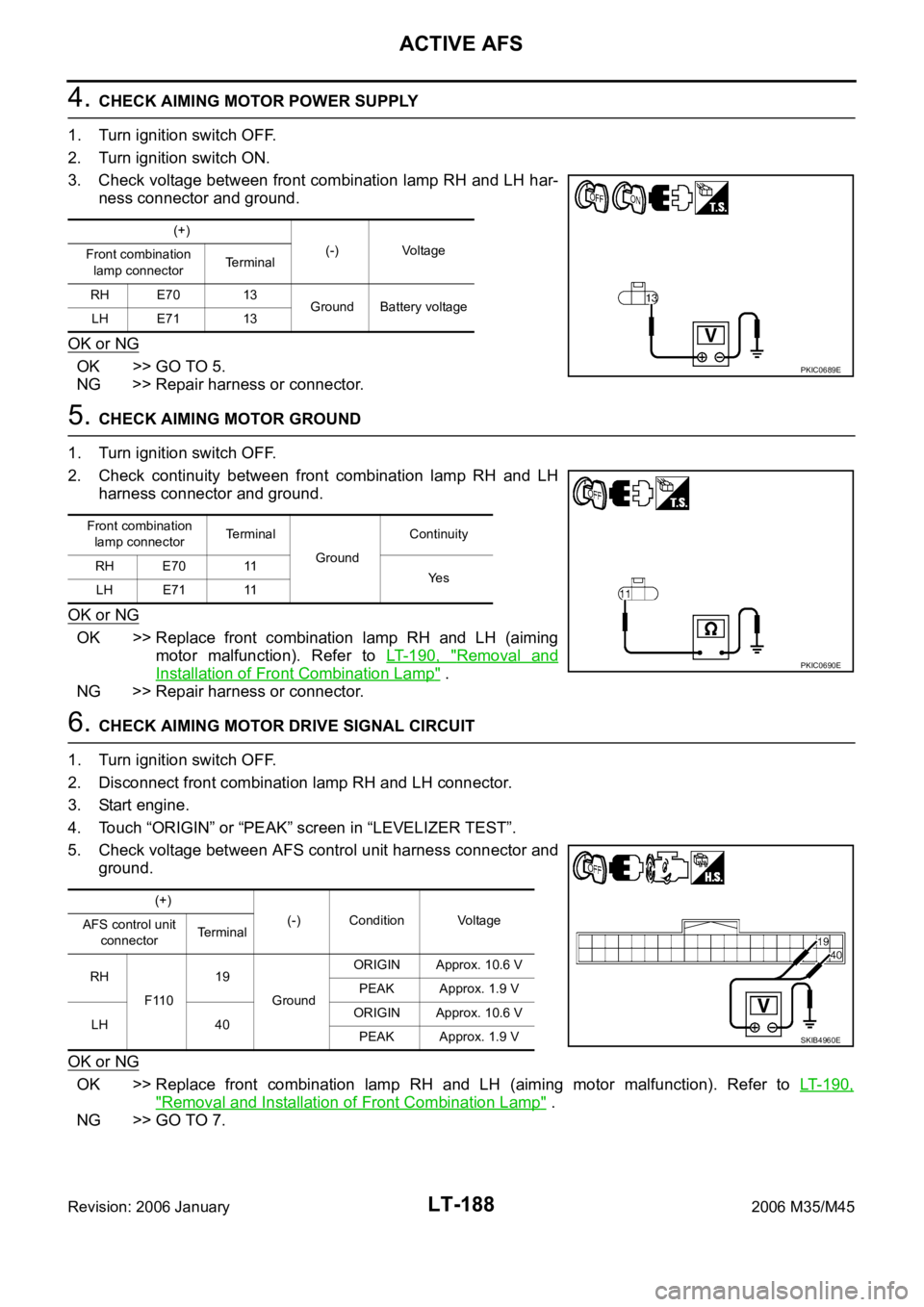
LT-188
ACTIVE AFS
Revision: 2006 January2006 M35/M45
4. CHECK AIMING MOTOR POWER SUPPLY
1. Turn ignition switch OFF.
2. Turn ignition switch ON.
3. Check voltage between front combination lamp RH and LH har-
ness connector and ground.
OK or NG
OK >> GO TO 5.
NG >> Repair harness or connector.
5. CHECK AIMING MOTOR GROUND
1. Turn ignition switch OFF.
2. Check continuity between front combination lamp RH and LH
harness connector and ground.
OK or NG
OK >> Replace front combination lamp RH and LH (aiming
motor malfunction). Refer to LT- 1 9 0 , "
Removal and
Installation of Front Combination Lamp" .
NG >> Repair harness or connector.
6. CHECK AIMING MOTOR DRIVE SIGNAL CIRCUIT
1. Turn ignition switch OFF.
2. Disconnect front combination lamp RH and LH connector.
3. Start engine.
4. Touch “ORIGIN” or “PEAK” screen in “LEVELIZER TEST”.
5. Check voltage between AFS control unit harness connector and
ground.
OK or NG
OK >> Replace front combination lamp RH and LH (aiming motor malfunction). Refer to LT- 1 9 0 ,
"Removal and Installation of Front Combination Lamp" .
NG >> GO TO 7.
(+)
(-) Voltage
Front combination
lamp connectorTerminal
RH E70 13
Ground Battery voltage
LH E71 13
PKIC0689E
Front combination
lamp connectorTerminal
GroundContinuity
RH E70 11
Ye s
LH E71 11
PKIC0690E
(+)
(-) Condition Voltage
AFS control unit
connectorTerminal
RH
F11019
GroundORIGIN Approx. 10.6 V
PEAK Approx. 1.9 V
LH 40ORIGIN Approx. 10.6 V
PEAK Approx. 1.9 V
SKIB4960E
Page 4616 of 5621
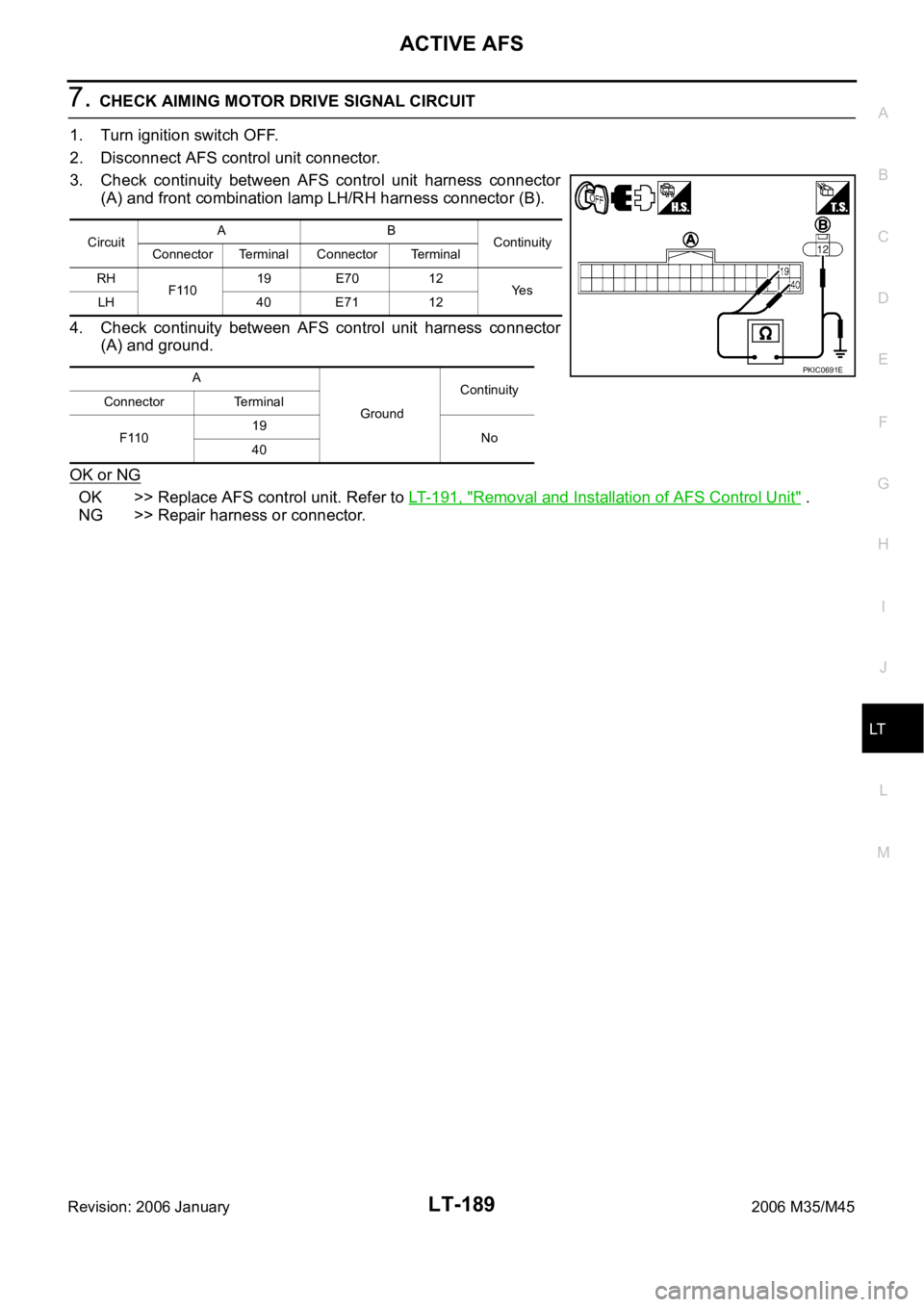
ACTIVE AFS
LT-189
C
D
E
F
G
H
I
J
L
MA
B
LT
Revision: 2006 January2006 M35/M45
7. CHECK AIMING MOTOR DRIVE SIGNAL CIRCUIT
1. Turn ignition switch OFF.
2. Disconnect AFS control unit connector.
3. Check continuity between AFS control unit harness connector
(A) and front combination lamp LH/RH harness connector (B).
4. Check continuity between AFS control unit harness connector
(A) and ground.
OK or NG
OK >> Replace AFS control unit. Refer to LT-191, "Removal and Installation of AFS Control Unit" .
NG >> Repair harness or connector.
CircuitAB
Continuity
Connector Terminal Connector Terminal
RH
F11019 E70 12
Ye s
LH 40 E71 12
A
GroundContinuity
Connector Terminal
F11019
No
40
PKIC0691E
Page 4845 of 5621
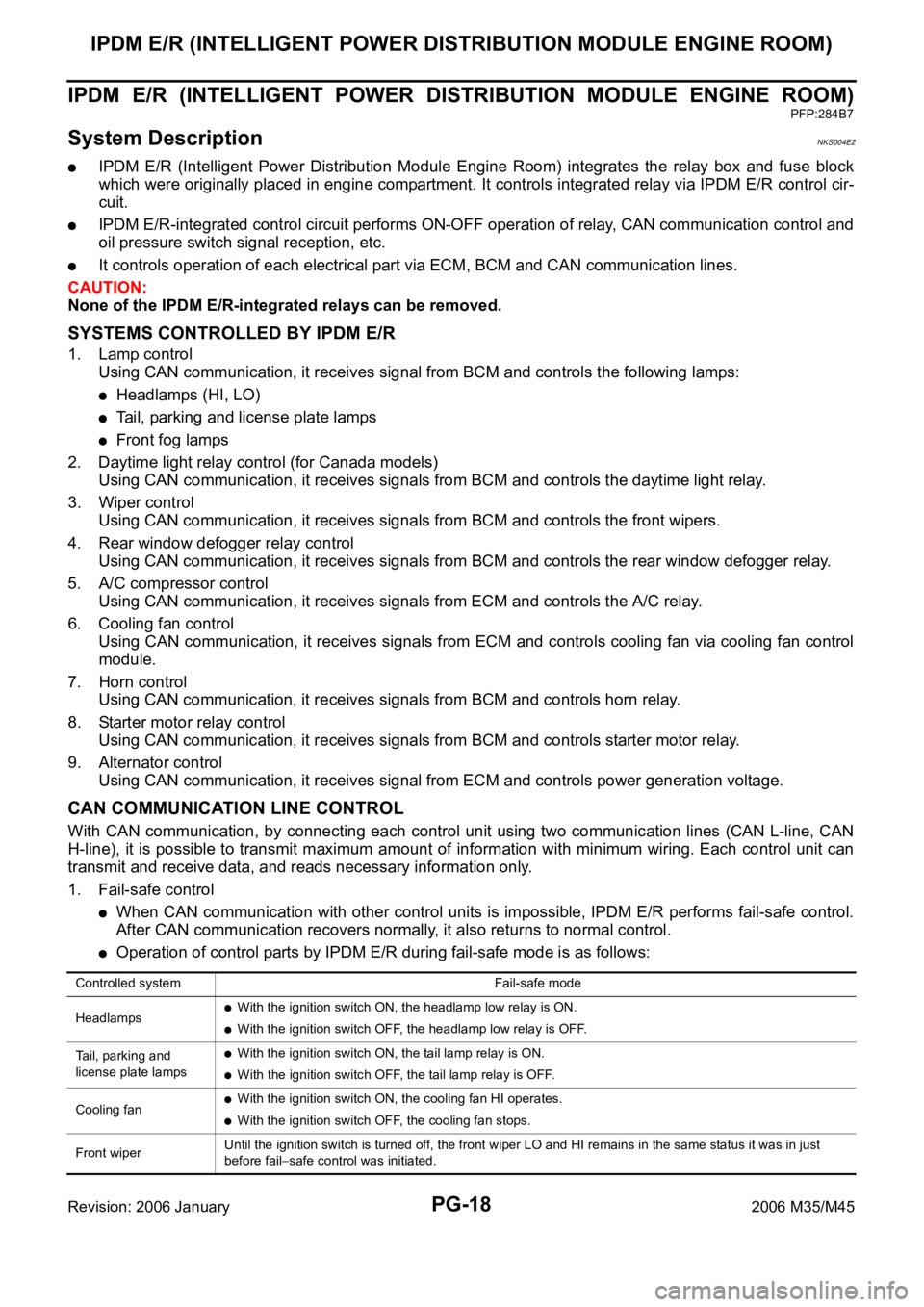
PG-18
IPDM E/R (INTELLIGENT POWER DISTRIBUTION MODULE ENGINE ROOM)
Revision: 2006 January2006 M35/M45
IPDM E/R (INTELLIGENT POWER DISTRIBUTION MODULE ENGINE ROOM)
PFP:284B7
System DescriptionNKS004E2
IPDM E/R (Intelligent Power Distribution Module Engine Room) integrates the relay box and fuse block
which were originally placed in engine compartment. It controls integrated relay via IPDM E/R control cir-
cuit.
IPDM E/R-integrated control circuit performs ON-OFF operation of relay, CAN communication control and
oil pressure switch signal reception, etc.
It controls operation of each electrical part via ECM, BCM and CAN communication lines.
CAUTION:
None of the IPDM E/R-integrated relays can be removed.
SYSTEMS CONTROLLED BY IPDM E/R
1. Lamp control
Using CAN communication, it receives signal from BCM and controls the following lamps:
Headlamps (HI, LO)
Tail, parking and license plate lamps
Front fog lamps
2. Daytime light relay control (for Canada models)
Using CAN communication, it receives signals from BCM and controls the daytime light relay.
3. Wiper control
Using CAN communication, it receives signals from BCM and controls the front wipers.
4. Rear window defogger relay control
Using CAN communication, it receives signals from BCM and controls the rear window defogger relay.
5. A/C compressor control
Using CAN communication, it receives signals from ECM and controls the A/C relay.
6. Cooling fan control
Using CAN communication, it receives signals from ECM and controls cooling fan via cooling fan control
module.
7. Horn control
Using CAN communication, it receives signals from BCM and controls horn relay.
8. Starter motor relay control
Using CAN communication, it receives signals from BCM and controls starter motor relay.
9. Alternator control
Using CAN communication, it receives signal from ECM and controls power generation voltage.
CAN COMMUNICATION LINE CONTROL
With CAN communication, by connecting each control unit using two communication lines (CAN L-line, CAN
H-line), it is possible to transmit maximum amount of information with minimum wiring. Each control unit can
transmit and receive data, and reads necessary information only.
1. Fail-safe control
When CAN communication with other control units is impossible, IPDM E/R performs fail-safe control.
After CAN communication recovers normally, it also returns to normal control.
Operation of control parts by IPDM E/R during fail-safe mode is as follows:
Controlled system Fail-safe mode
Headlamps
With the ignition switch ON, the headlamp low relay is ON.
With the ignition switch OFF, the headlamp low relay is OFF.
Tail, parking and
license plate lamps
With the ignition switch ON, the tail lamp relay is ON.
With the ignition switch OFF, the tail lamp relay is OFF.
Cooling fan
With the ignition switch ON, the cooling fan HI operates.
With the ignition switch OFF, the cooling fan stops.
Front wiperUntil the ignition switch is turned off, the front wiper LO and HI remains in the same status it was in just
before fail
safe control was initiated.
Page 4849 of 5621
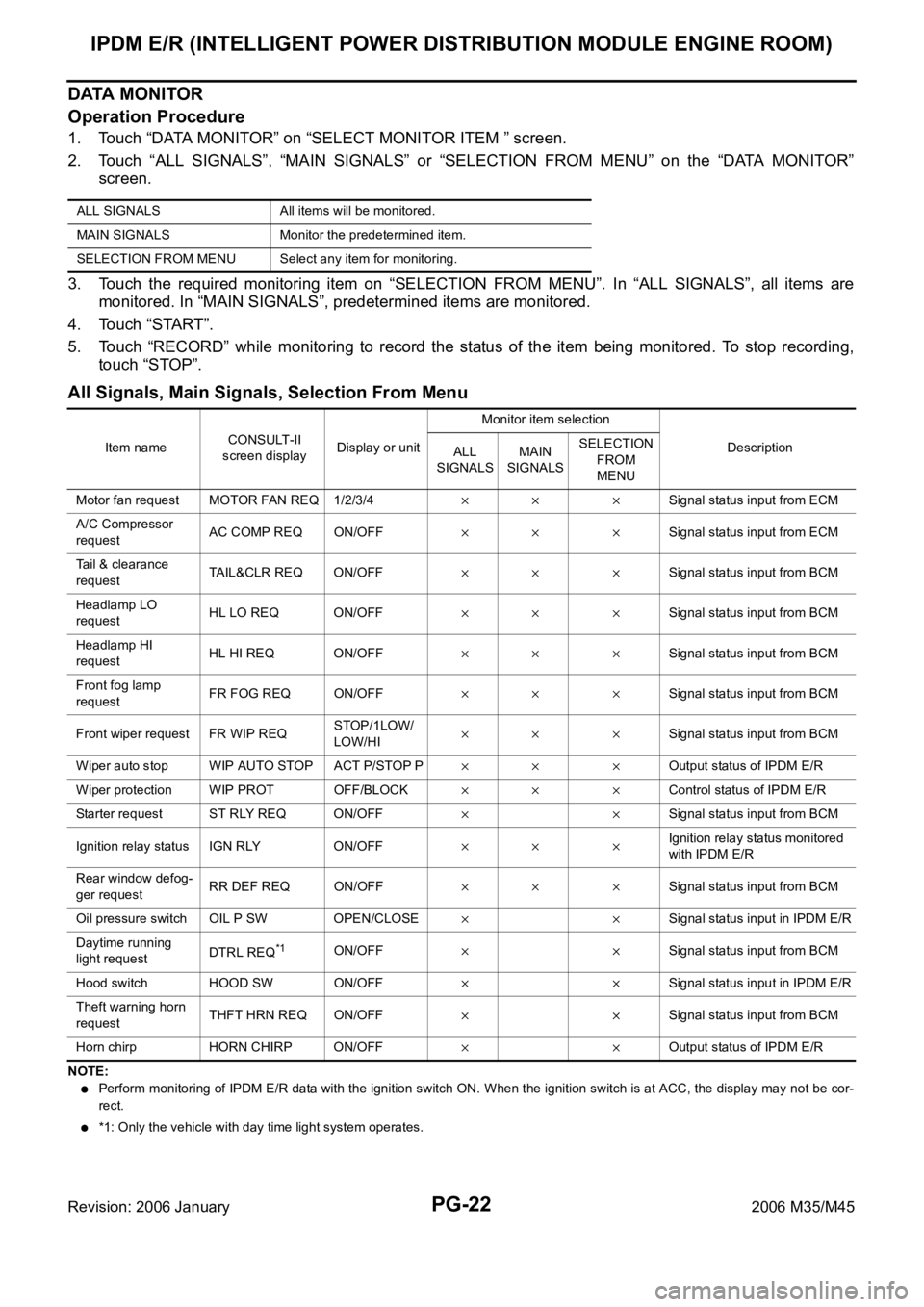
PG-22
IPDM E/R (INTELLIGENT POWER DISTRIBUTION MODULE ENGINE ROOM)
Revision: 2006 January2006 M35/M45
DATA MONITOR
Operation Procedure
1. Touch “DATA MONITOR” on “SELECT MONITOR ITEM ” screen.
2. Touch “ALL SIGNALS”, “MAIN SIGNALS” or “SELECTION FROM MENU” on the “DATA MONITOR”
screen.
3. Touch the required monitoring item on “SELECTION FROM MENU”. In “ALL SIGNALS”, all items are
monitored. In “MAIN SIGNALS”, predetermined items are monitored.
4. Touch “START”.
5. Touch “RECORD” while monitoring to record the status of the item being monitored. To stop recording,
touch “STOP”.
All Signals, Main Signals, Selection From Menu
NOTE:
Perform monitoring of IPDM E/R data with the ignition switch ON. When the ignition switch is at ACC, the display may not be cor-
rect.
*1: Only the vehicle with day time light system operates. ALL SIGNALS All items will be monitored.
MAIN SIGNALS Monitor the predetermined item.
SELECTION FROM MENU Select any item for monitoring.
Item nameCONSULT-II
screen displayDisplay or unitMonitor item selection
Description
ALL
SIGNALSMAIN
SIGNALSSELECTION
FROM
MENU
Motor fan request MOTOR FAN REQ 1/2/3/4
Signal status input from ECM
A/C Compressor
requestAC COMP REQ ON/OFF
Signal status input from ECM
Tail & clearance
requestTAIL&CLR REQ ON/OFF
Signal status input from BCM
Headlamp LO
requestHL LO REQ ON/OFF
Signal status input from BCM
Headlamp HI
requestHL HI REQ ON/OFF
Signal status input from BCM
Front fog lamp
request FR FOG REQ ON/OFF
Signal status input from BCM
Front wiper request FR WIP REQSTOP/1LOW/
LOW/HI
Signal status input from BCM
Wiper auto stop WIP AUTO STOP ACT P/STOP P
Output status of IPDM E/R
Wiper protection WIP PROT OFF/BLOCK
Control status of IPDM E/R
Starter request ST RLY REQ ON/OFF
Signal status input from BCM
Ignition relay status IGN RLY ON/OFF
Ignition relay status monitored
with IPDM E/R
Rear window defog-
ger requestRR DEF REQ ON/OFF
Signal status input from BCM
Oil pressure switch OIL P SW OPEN/CLOSE
Signal status input in IPDM E/R
Daytime running
light requestDTRL REQ
*1ON/OFFSignal status input from BCM
Hood switch HOOD SW ON/OFF
Signal status input in IPDM E/R
Theft warning horn
requestTHFT HRN REQ ON/OFF
Signal status input from BCM
Horn chirp HORN CHIRP ON/OFF
Output status of IPDM E/R
Page 4850 of 5621
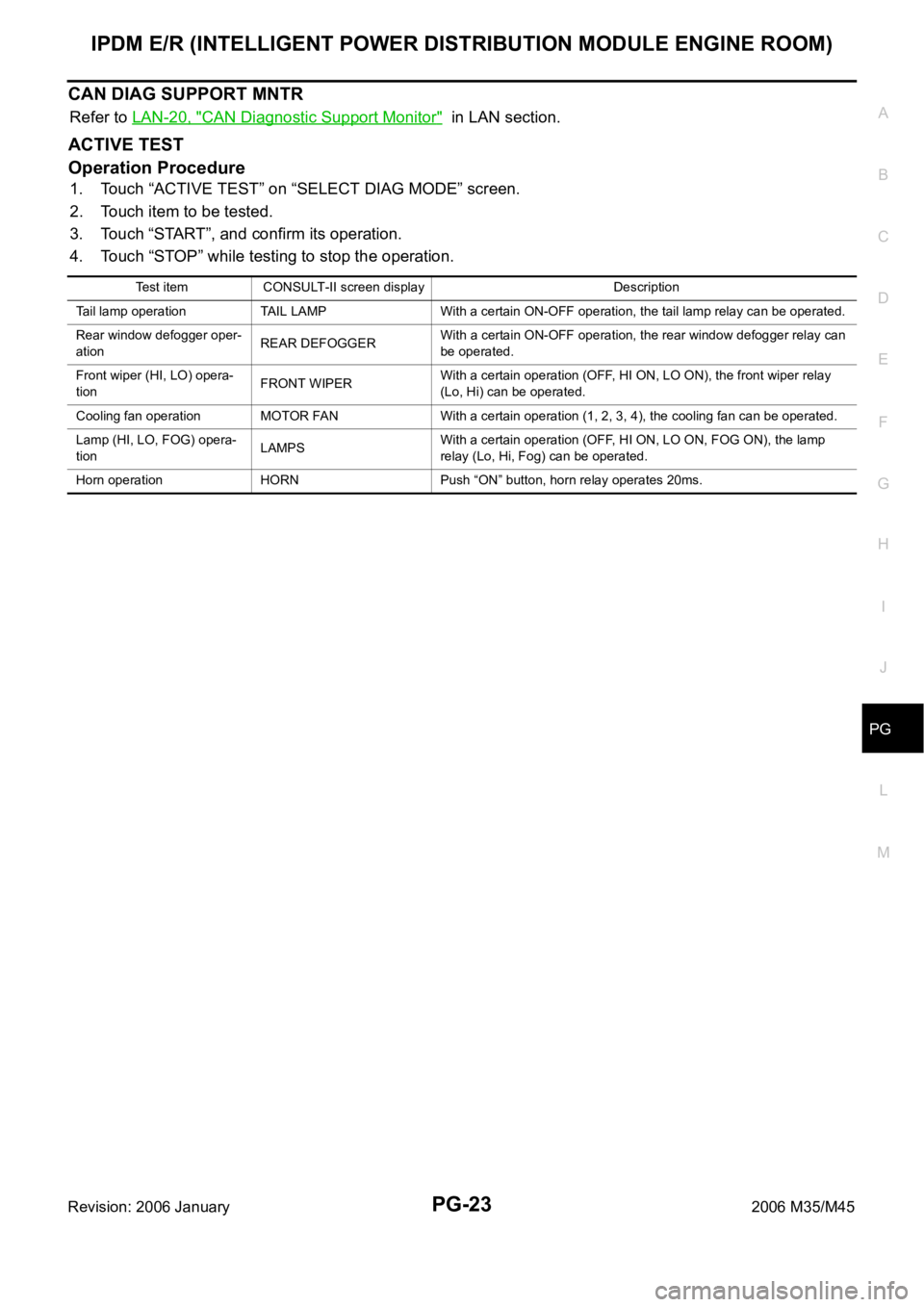
IPDM E/R (INTELLIGENT POWER DISTRIBUTION MODULE ENGINE ROOM)
PG-23
C
D
E
F
G
H
I
J
L
MA
B
PG
Revision: 2006 January2006 M35/M45
CAN DIAG SUPPORT MNTR
Refer to LAN-20, "CAN Diagnostic Support Monitor" in LAN section.
ACTIVE TEST
Operation Procedure
1. Touch “ACTIVE TEST” on “SELECT DIAG MODE” screen.
2. Touch item to be tested.
3. Touch “START”, and confirm its operation.
4. Touch “STOP” while testing to stop the operation.
Test item CONSULT-II screen display Description
Tail lamp operation TAIL LAMP With a certain ON-OFF operation, the tail lamp relay can be operated.
Rear window defogger oper-
ationREAR DEFOGGERWith a certain ON-OFF operation, the rear window defogger relay can
be operated.
Front wiper (HI, LO) opera-
tionFRONT WIPERWith a certain operation (OFF, HI ON, LO ON), the front wiper relay
(Lo, Hi) can be operated.
Cooling fan operation MOTOR FAN With a certain operation (1, 2, 3, 4), the cooling fan can be operated.
Lamp (HI, LO, FOG) opera-
tionLAMPSWith a certain operation (OFF, HI ON, LO ON, FOG ON), the lamp
relay (Lo, Hi, Fog) can be operated.
Horn operation HORN Push “ON” button, horn relay operates 20ms.
Page 4853 of 5621
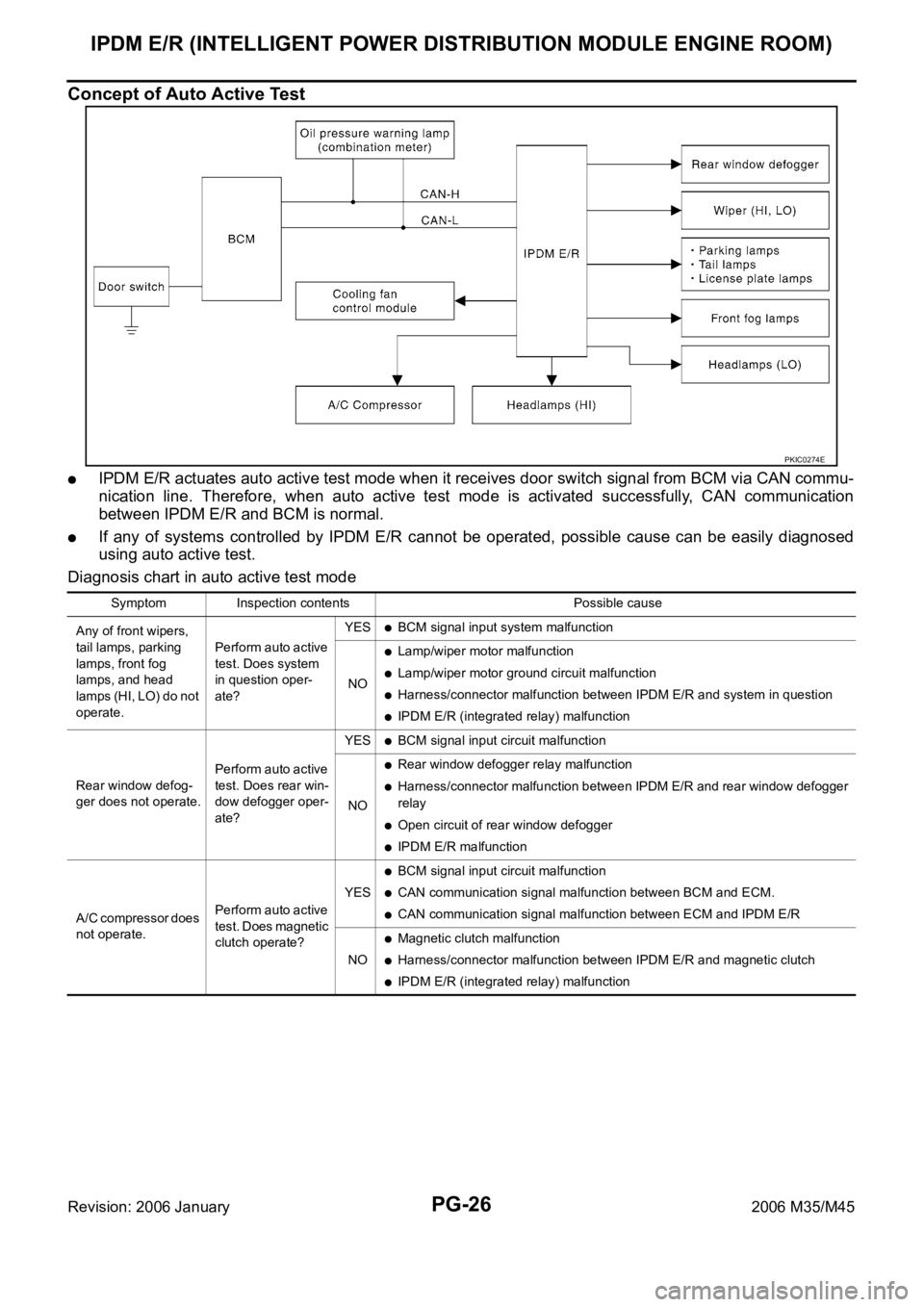
PG-26
IPDM E/R (INTELLIGENT POWER DISTRIBUTION MODULE ENGINE ROOM)
Revision: 2006 January2006 M35/M45
Concept of Auto Active Test
IPDM E/R actuates auto active test mode when it receives door switch signal from BCM via CAN commu-
nication line. Therefore, when auto active test mode is activated successfully, CAN communication
between IPDM E/R and BCM is normal.
If any of systems controlled by IPDM E/R cannot be operated, possible cause can be easily diagnosed
using auto active test.
Diagnosis chart in auto active test mode
PKIC0274E
Symptom Inspection contents Possible cause
Any of front wipers,
tail lamps, parking
lamps, front fog
lamps, and head
lamps (HI, LO) do not
operate.Perform auto active
test. Does system
in question oper-
ate?YES
BCM signal input system malfunction
NO
Lamp/wiper motor malfunction
Lamp/wiper motor ground circuit malfunction
Harness/connector malfunction between IPDM E/R and system in question
IPDM E/R (integrated relay) malfunction
Rear window defog-
ger does not operate.Perform auto active
test. Does rear win-
dow defogger oper-
ate?YES
BCM signal input circuit malfunction
NO
Rear window defogger relay malfunction
Harness/connector malfunction between IPDM E/R and rear window defogger
relay
Open circuit of rear window defogger
IPDM E/R malfunction
A/C compressor does
not operate.Perform auto active
test. Does magnetic
clutch operate?YES
BCM signal input circuit malfunction
CAN communication signal malfunction between BCM and ECM.
CAN communication signal malfunction between ECM and IPDM E/R
NO
Magnetic clutch malfunction
Harness/connector malfunction between IPDM E/R and magnetic clutch
IPDM E/R (integrated relay) malfunction
Page 4854 of 5621
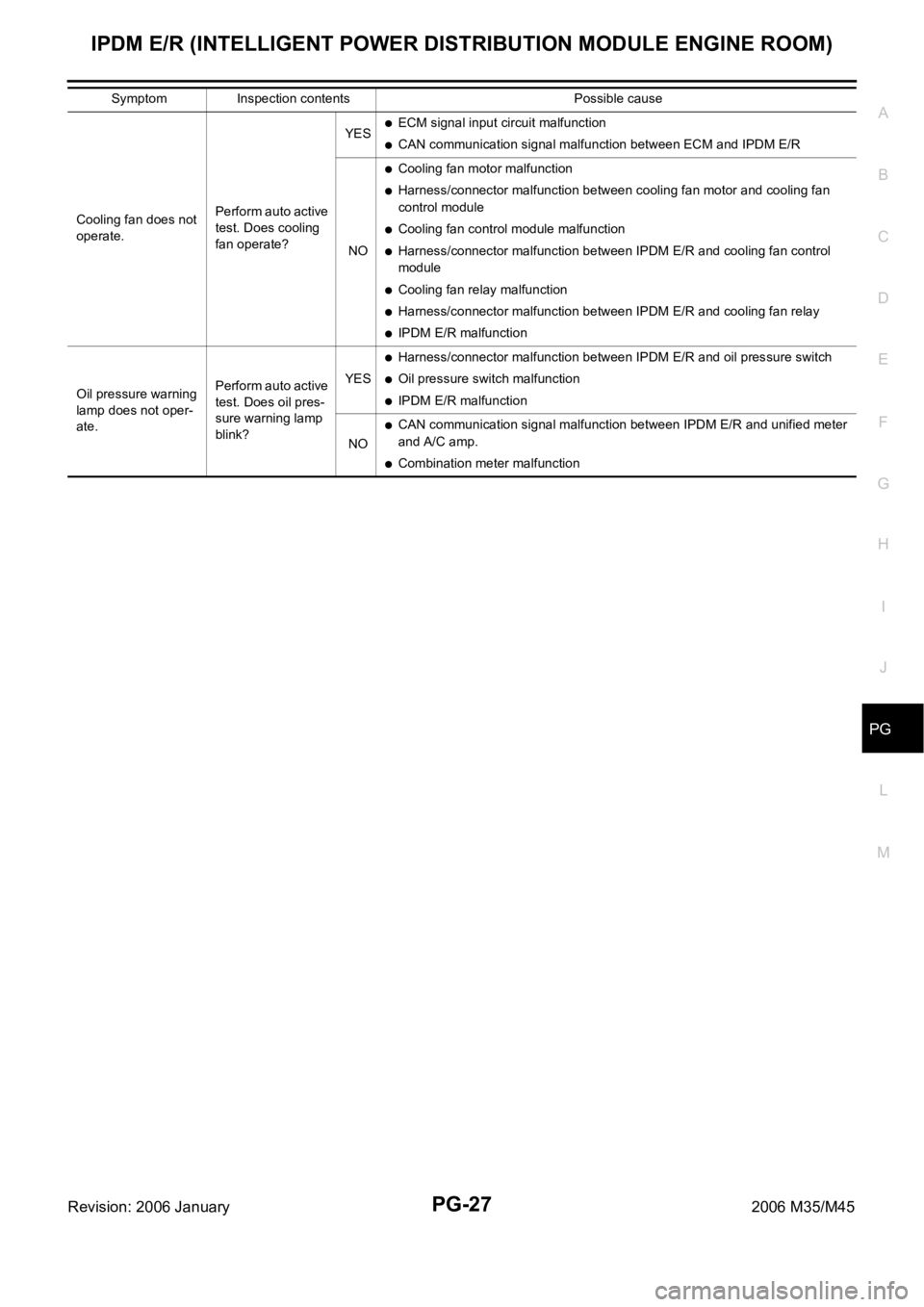
IPDM E/R (INTELLIGENT POWER DISTRIBUTION MODULE ENGINE ROOM)
PG-27
C
D
E
F
G
H
I
J
L
MA
B
PG
Revision: 2006 January2006 M35/M45
Cooling fan does not
operate.Perform auto active
test. Does cooling
fan operate?YES
ECM signal input circuit malfunction
CAN communication signal malfunction between ECM and IPDM E/R
NO
Cooling fan motor malfunction
Harness/connector malfunction between cooling fan motor and cooling fan
control module
Cooling fan control module malfunction
Harness/connector malfunction between IPDM E/R and cooling fan control
module
Cooling fan relay malfunction
Harness/connector malfunction between IPDM E/R and cooling fan relay
IPDM E/R malfunction
Oil pressure warning
lamp does not oper-
ate.Perform auto active
test. Does oil pres-
sure warning lamp
blink?YES
Harness/connector malfunction between IPDM E/R and oil pressure switch
Oil pressure switch malfunction
IPDM E/R malfunction
NO
CAN communication signal malfunction between IPDM E/R and unified meter
and A/C amp.
Combination meter malfunction Symptom Inspection contents Possible cause