Motor INFINITI M35 2006 Factory Service Manual
[x] Cancel search | Manufacturer: INFINITI, Model Year: 2006, Model line: M35, Model: INFINITI M35 2006Pages: 5621, PDF Size: 65.56 MB
Page 3714 of 5621
![INFINITI M35 2006 Factory Service Manual CAN COMMUNICATION
LAN-45
[CAN]
C
D
E
F
G
H
I
J
L
MA
B
LAN
Revision: 2006 January2006 M35/M45
ACC signal T R R
Blower fan motor switch signal R T
Buzzer output signalTR
TR
RT
Day time running light req INFINITI M35 2006 Factory Service Manual CAN COMMUNICATION
LAN-45
[CAN]
C
D
E
F
G
H
I
J
L
MA
B
LAN
Revision: 2006 January2006 M35/M45
ACC signal T R R
Blower fan motor switch signal R T
Buzzer output signalTR
TR
RT
Day time running light req](/img/42/57023/w960_57023-3713.png)
CAN COMMUNICATION
LAN-45
[CAN]
C
D
E
F
G
H
I
J
L
MA
B
LAN
Revision: 2006 January2006 M35/M45
ACC signal T R R
Blower fan motor switch signal R T
Buzzer output signalTR
TR
RT
Day time running light request signal T R
Door lock/unlock status signal T R
Door switch signal T R R R R R
Door unlock signal T R
Front fog light request signal T R R
Front wiper request signal T R R
High beam request signal T R R
Ignition switch ON signal T R R
Ignition switch signal T R R
Key ID signal T R
Key switch signal T R
Low beam request signal T R
Position light request signal T R R
Rear window defogger switch signal T R
Sleep wake up signal T R R R R
Starter request signal T R
Theft warning horn request signal T R
Trunk switch signal T R R
Turn indicator signal T R R
Tire pressure data signal T R
Tire pressure signal T R R
Steering angle sensor signal R T R
Door lock/unlock trunk open request signal R T
Hazard and horn request signal R T
Key warning signalTR
Meter display signalTR
RT
Panic alarm request signal R T
Power window open request signal R TSignals
ECM
TCM
AWD control unit
AFS control unit*1
BCM
LDW camera unit*2
Low tire pressure warning control unit
Steering angle sensor
Intelligent Key unit
Unified meter and A/C amp.
AV (NAVI) control unit
Pre-crash seat belt control unit*3
Driver seat control unit
ABS actuator and electric unit (control unit)
ICC sensor integrated unit*4
IPDM E/R
Page 4430 of 5621
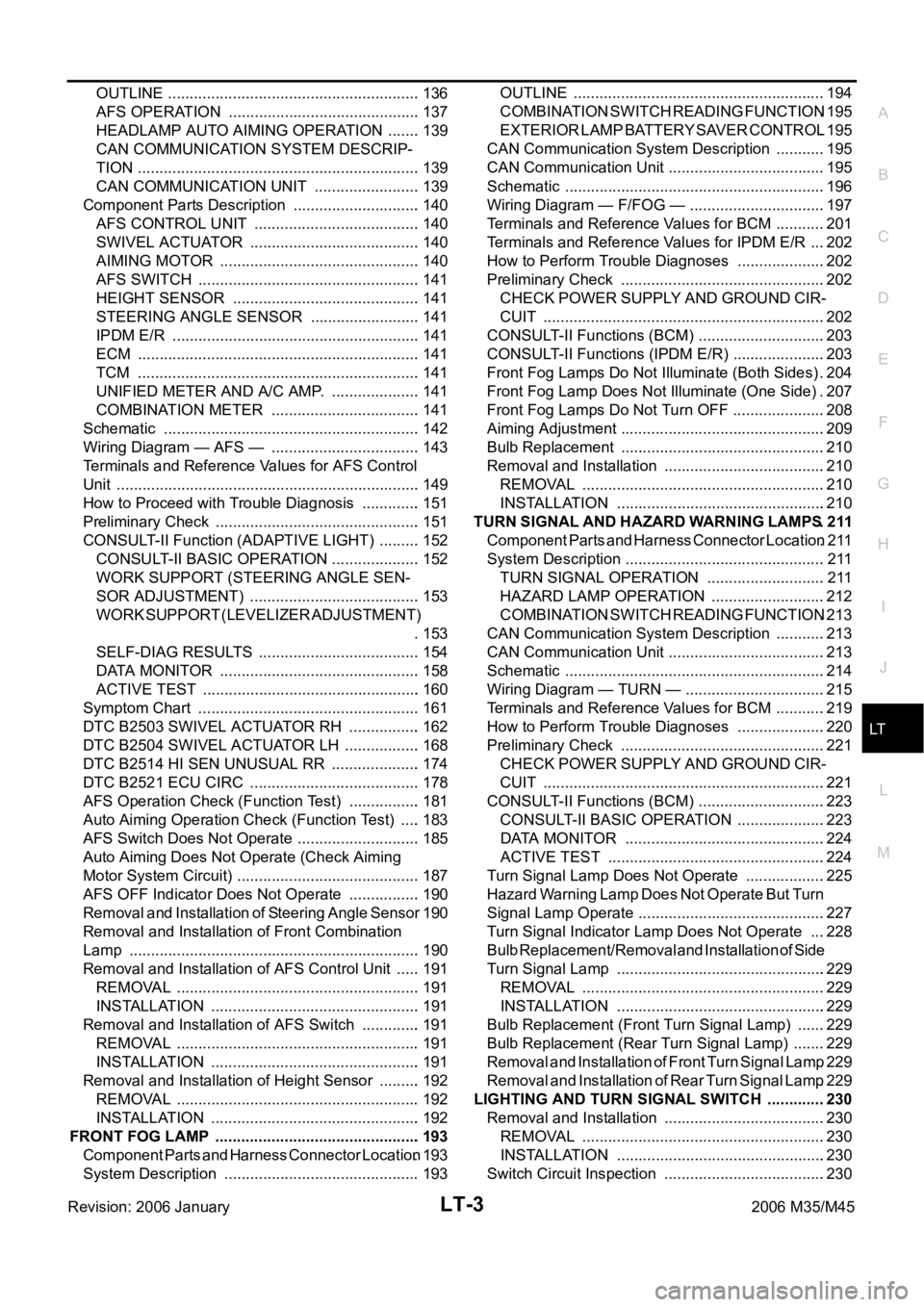
LT-3
C
D
E
F
G
H
I
J
L
MA
B
LT
Revision: 2006 January2006 M35/M45 OUTLINE ...........................................................136
AFS OPERATION .............................................137
HEADLAMP AUTO AIMING OPERATION ........139
CAN COMMUNICATION SYSTEM DESCRIP-
TION ..................................................................139
CAN COMMUNICATION UNIT .........................139
Component Parts Description ..............................140
AFS CONTROL UNIT .......................................140
SWIVEL ACTUATOR ........................................140
AIMING MOTOR ...............................................140
AFS SWITCH ....................................................141
HEIGHT SENSOR ............................................141
STEERING ANGLE SENSOR ..........................141
IPDM E/R ..........................................................141
ECM ..................................................................141
TCM ..................................................................141
UNIFIED METER AND A/C AMP. .....................141
COMBINATION METER ...................................141
Schematic ............................................................142
Wiring Diagram — AFS — ...................................143
Terminals and Reference Values for AFS Control
Unit .......................................................................149
How to Proceed with Trouble Diagnosis ..............151
Preliminary Check ................................................151
CONSULT-II Function (ADAPTIVE LIGHT) ..........152
CONSULT-II BASIC OPERATION .....................152
WORK SUPPORT (STEERING ANGLE SEN-
SOR ADJUSTMENT) ........................................153
WORK SUPPORT (LEVELIZER ADJUSTMENT)
.153
SELF-DIAG RESULTS ......................................154
DATA MONITOR ...............................................158
ACTIVE TEST ...................................................160
Symptom Chart ....................................................161
DTC B2503 SWIVEL ACTUATOR RH .................162
DTC B2504 SWIVEL ACTUATOR LH ..................168
DTC B2514 HI SEN UNUSUAL RR .....................174
DTC B2521 ECU CIRC ........................................178
AFS Operation Check (Function Test) .................181
Auto Aiming Operation Check (Function Test) .....183
AFS Switch Does Not Operate .............................185
Auto Aiming Does Not Operate (Check Aiming
Motor System Circuit) ..........................................
.187
AFS OFF Indicator Does Not Operate .................190
Removal and Installation of Steering Angle Sensor .190
Removal and Installation of Front Combination
Lamp ....................................................................190
Removal and Installation of AFS Control Unit ......191
REMOVAL ........................................................
.191
INSTALLATION .................................................191
Removal and Installation of AFS Switch ..............191
REMOVAL ........................................................
.191
INSTALLATION .................................................191
Removal and Installation of Height Sensor ..........192
REMOVAL ........................................................
.192
INSTALLATION .................................................192
FRONT FOG LAMP ................................................193
Component Parts and Harness Connector Location .193
System Description ..............................................193OUTLINE ...........................................................194
COMBINATION SWITCH READING FUNCTION .195
EXTERIOR LAMP BATTERY SAVER CONTROL .195
CAN Communication System Description ............195
CAN Communication Unit .....................................195
Schematic .............................................................196
Wiring Diagram — F/FOG — ................................197
Terminals and Reference Values for BCM ............201
Terminals and Reference Values for IPDM E/R ....202
How to Perform Trouble Diagnoses .....................202
Preliminary Check ................................................202
CHECK POWER SUPPLY AND GROUND CIR-
CUIT ..................................................................202
CONSULT-II Functions (BCM) ..............................203
CONSULT-II Functions (IPDM E/R) ......................203
Front Fog Lamps Do Not Illuminate (Both Sides) . 204
Front Fog Lamp Does Not Illuminate (One Side) . 207
Front Fog Lamps Do Not Turn OFF ......................208
Aiming Adjustment ................................................209
Bulb Replacement ................................................210
Removal and Installation ......................................210
REMOVAL ........................................................
.210
INSTALLATION .................................................210
TURN SIGNAL AND HAZARD WARNING LAMPS .211
Component Parts and Harness Connector Location .211
System Description ...............................................211
TURN SIGNAL OPERATION ............................211
HAZARD LAMP OPERATION ...........................212
COMBINATION SWITCH READING FUNCTION .213
CAN Communication System Description ............213
CAN Communication Unit .....................................213
Schematic .............................................................214
Wiring Diagram — TURN — .................................215
Terminals and Reference Values for BCM ............219
How to Perform Trouble Diagnoses .....................220
Preliminary Check ................................................221
CHECK POWER SUPPLY AND GROUND CIR-
CUIT ..................................................................221
CONSULT-II Functions (BCM) ..............................223
CONSULT-II BASIC OPERATION .....................223
DATA MONITOR ...............................................224
ACTIVE TEST ...................................................224
Turn Signal Lamp Does Not Operate ...................225
H a z a r d W a r n i n g L a m p D o e s N o t O p e r a t e B u t T u r n
Signal Lamp Operate ............................................227
Turn Signal Indicator Lamp Does Not Operate ....228
Bulb Replacement/Removal and Installation of Side
Turn Signal Lamp .................................................229
REMOVAL ........................................................
.229
INSTALLATION .................................................229
Bulb Replacement (Front Turn Signal Lamp) .......229
Bulb Replacement (Rear Turn Signal Lamp) ........229
Removal and Installation of Front Turn Signal Lamp .229
Removal and Installation of Rear Turn Signal Lamp .229
LIGHTING AND TURN SIGNAL SWITCH ..............230
Removal and Installation ......................................230
REMOVAL ........................................................
.230
INSTALLATION .................................................230
Switch Circuit Inspection ......................................230
Page 4562 of 5621
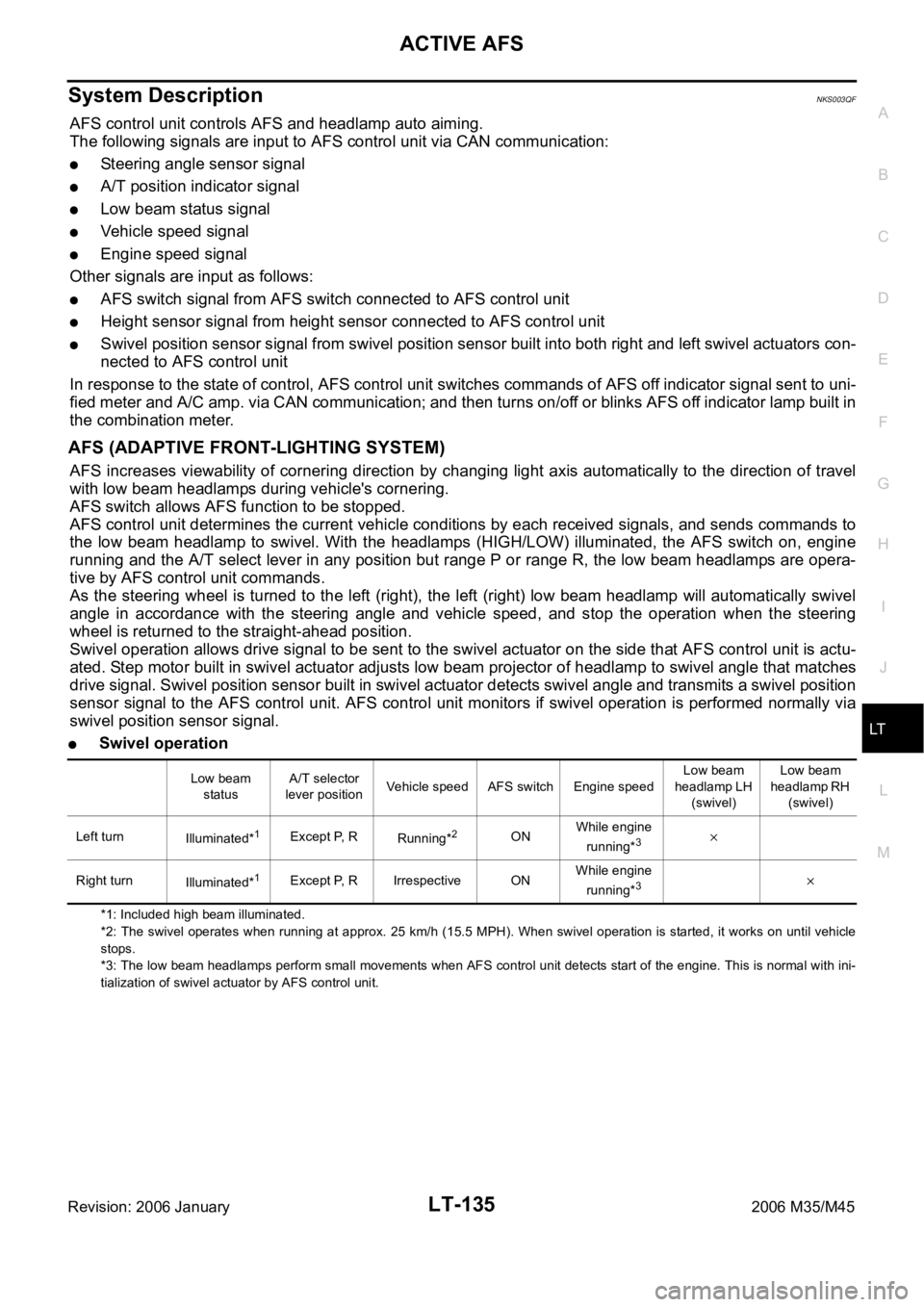
ACTIVE AFS
LT-135
C
D
E
F
G
H
I
J
L
MA
B
LT
Revision: 2006 January2006 M35/M45
System DescriptionNKS003QF
AFS control unit controls AFS and headlamp auto aiming.
The following signals are input to AFS control unit via CAN communication:
Steering angle sensor signal
A/T position indicator signal
Low beam status signal
Vehicle speed signal
Engine speed signal
Other signals are input as follows:
AFS switch signal from AFS switch connected to AFS control unit
Height sensor signal from height sensor connected to AFS control unit
Swivel position sensor signal from swivel position sensor built into both right and left swivel actuators con-
nected to AFS control unit
In response to the state of control, AFS control unit switches commands of AFS off indicator signal sent to uni-
fied meter and A/C amp. via CAN communication; and then turns on/off or blinks AFS off indicator lamp built in
the combination meter.
AFS (ADAPTIVE FRONT-LIGHTING SYSTEM)
AFS increases viewability of cornering direction by changing light axis automatically to the direction of travel
with low beam headlamps during vehicle's cornering.
AFS switch allows AFS function to be stopped.
AFS control unit determines the current vehicle conditions by each received signals, and sends commands to
the low beam headlamp to swivel. With the headlamps (HIGH/LOW) illuminated, the AFS switch on, engine
running and the A/T select lever in any position but range P or range R, the low beam headlamps are opera-
tive by AFS control unit commands.
As the steering wheel is turned to the left (right), the left (right) low beam headlamp will automatically swivel
angle in accordance with the steering angle and vehicle speed, and stop the operation when the steering
wheel is returned to the straight-ahead position.
Swivel operation allows drive signal to be sent to the swivel actuator on the side that AFS control unit is actu-
ated. Step motor built in swivel actuator adjusts low beam projector of headlamp to swivel angle that matches
drive signal. Swivel position sensor built in swivel actuator detects swivel angle and transmits a swivel position
sensor signal to the AFS control unit. AFS control unit monitors if swivel operation is performed normally via
swivel position sensor signal.
Swivel operation
*1: Included high beam illuminated.
*2: The swivel operates when running at approx. 25 km/h (15.5 MPH). When swivel operation is started, it works on until vehicle
stops.
*3: The low beam headlamps perform small movements when AFS control unit detects start of the engine. This is normal with ini-
tialization of swivel actuator by AFS control unit.Low beam
statusA/T selector
lever positionVehicle speed AFS switch Engine speed Low beam
headlamp LH
(swivel)Low beam
headlamp RH
(swivel)
Left turn
Illuminated*
1Except P, R
Running*2ONWhile engine
running*3
Right turn
Illuminated*1Except P, R Irrespective ONWhile engine
running*3
Page 4564 of 5621
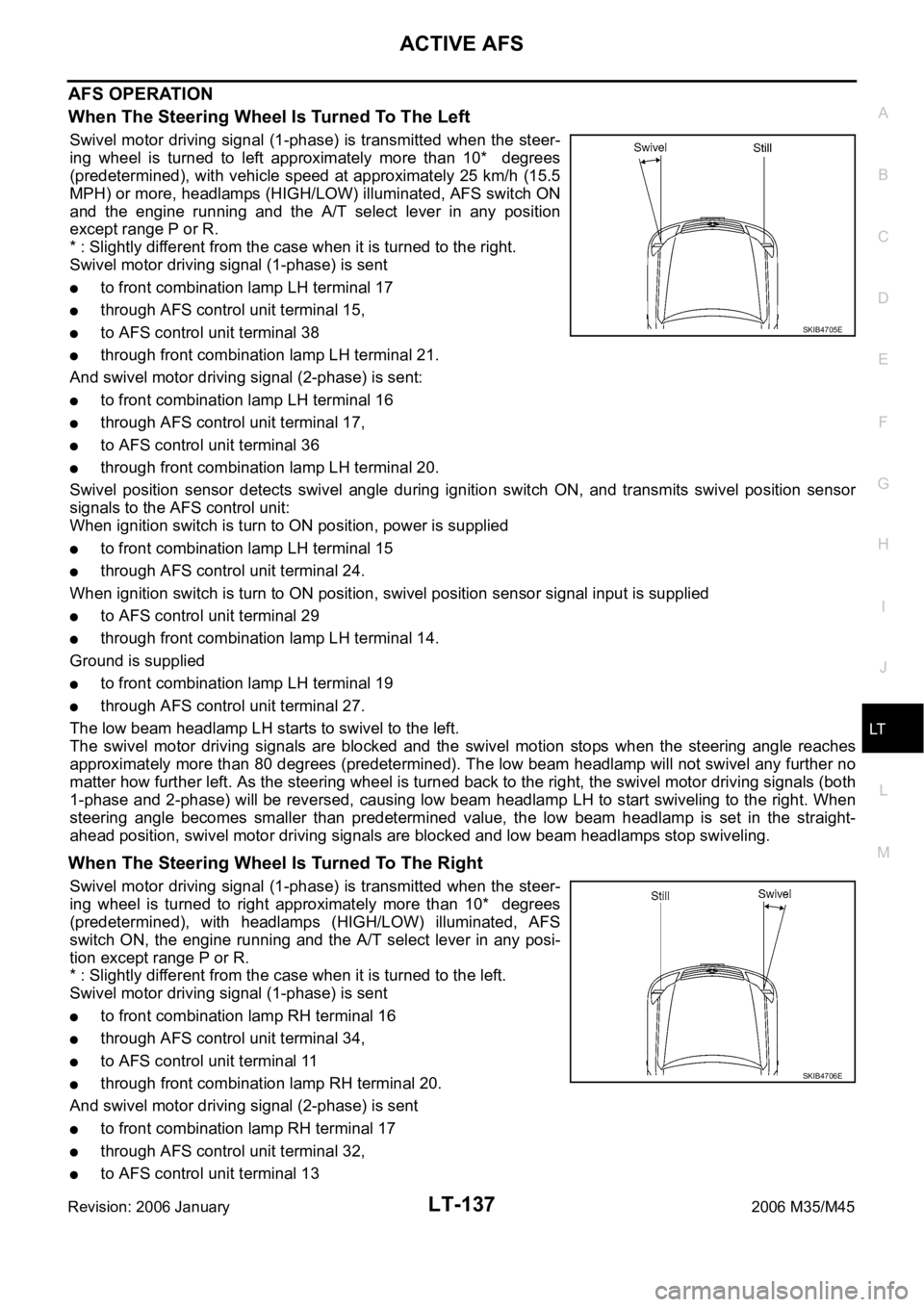
ACTIVE AFS
LT-137
C
D
E
F
G
H
I
J
L
MA
B
LT
Revision: 2006 January2006 M35/M45
AFS OPERATION
When The Steering Wheel Is Turned To The Left
Swivel motor driving signal (1-phase) is transmitted when the steer-
ing wheel is turned to left approximately more than 10* degrees
(predetermined), with vehicle speed at approximately 25 km/h (15.5
MPH) or more, headlamps (HIGH/LOW) illuminated, AFS switch ON
and the engine running and the A/T select lever in any position
except range P or R.
* : Slightly different from the case when it is turned to the right.
Swivel motor driving signal (1-phase) is sent
to front combination lamp LH terminal 17
through AFS control unit terminal 15,
to AFS control unit terminal 38
through front combination lamp LH terminal 21.
And swivel motor driving signal (2-phase) is sent:
to front combination lamp LH terminal 16
through AFS control unit terminal 17,
to AFS control unit terminal 36
through front combination lamp LH terminal 20.
Swivel position sensor detects swivel angle during ignition switch ON, and transmits swivel position sensor
signals to the AFS control unit:
When ignition switch is turn to ON position, power is supplied
to front combination lamp LH terminal 15
through AFS control unit terminal 24.
When ignition switch is turn to ON position, swivel position sensor signal input is supplied
to AFS control unit terminal 29
through front combination lamp LH terminal 14.
Ground is supplied
to front combination lamp LH terminal 19
through AFS control unit terminal 27.
The low beam headlamp LH starts to swivel to the left.
The swivel motor driving signals are blocked and the swivel motion stops when the steering angle reaches
approximately more than 80 degrees (predetermined). The low beam headlamp will not swivel any further no
matter how further left. As the steering wheel is turned back to the right, the swivel motor driving signals (both
1-phase and 2-phase) will be reversed, causing low beam headlamp LH to start swiveling to the right. When
steering angle becomes smaller than predetermined value, the low beam headlamp is set in the straight-
ahead position, swivel motor driving signals are blocked and low beam headlamps stop swiveling.
When The Steering Wheel Is Turned To The Right
Swivel motor driving signal (1-phase) is transmitted when the steer-
ing wheel is turned to right approximately more than 10* degrees
(predetermined), with headlamps (HIGH/LOW) illuminated, AFS
switch ON, the engine running and the A/T select lever in any posi-
tion except range P or R.
* : Slightly different from the case when it is turned to the left.
Swivel motor driving signal (1-phase) is sent
to front combination lamp RH terminal 16
through AFS control unit terminal 34,
to AFS control unit terminal 11
through front combination lamp RH terminal 20.
And swivel motor driving signal (2-phase) is sent
to front combination lamp RH terminal 17
through AFS control unit terminal 32,
to AFS control unit terminal 13
SKIB4705E
SKIB4706E
Page 4565 of 5621
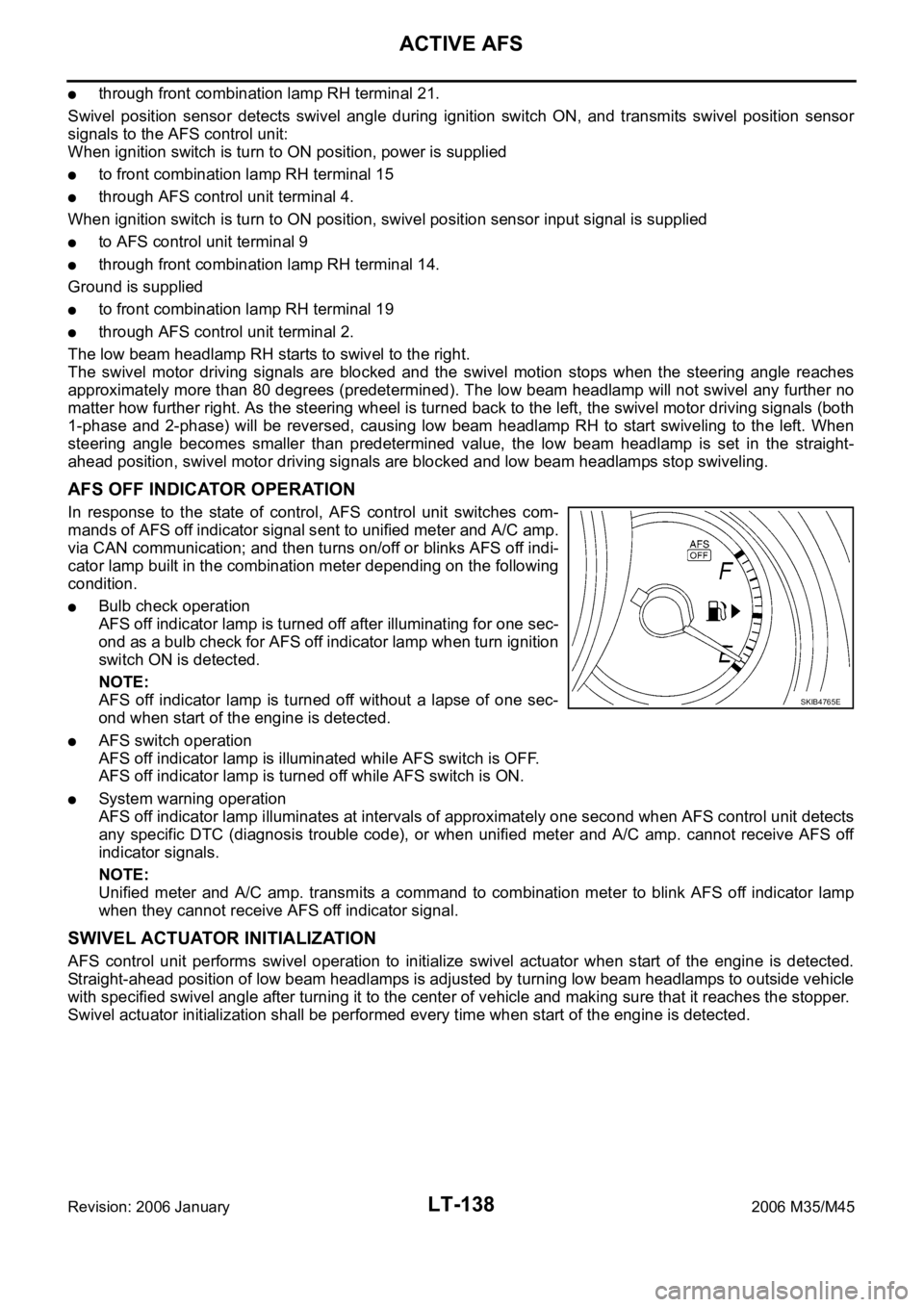
LT-138
ACTIVE AFS
Revision: 2006 January2006 M35/M45
through front combination lamp RH terminal 21.
Swivel position sensor detects swivel angle during ignition switch ON, and transmits swivel position sensor
signals to the AFS control unit:
When ignition switch is turn to ON position, power is supplied
to front combination lamp RH terminal 15
through AFS control unit terminal 4.
When ignition switch is turn to ON position, swivel position sensor input signal is supplied
to AFS control unit terminal 9
through front combination lamp RH terminal 14.
Ground is supplied
to front combination lamp RH terminal 19
through AFS control unit terminal 2.
The low beam headlamp RH starts to swivel to the right.
The swivel motor driving signals are blocked and the swivel motion stops when the steering angle reaches
approximately more than 80 degrees (predetermined). The low beam headlamp will not swivel any further no
matter how further right. As the steering wheel is turned back to the left, the swivel motor driving signals (both
1-phase and 2-phase) will be reversed, causing low beam headlamp RH to start swiveling to the left. When
steering angle becomes smaller than predetermined value, the low beam headlamp is set in the straight-
ahead position, swivel motor driving signals are blocked and low beam headlamps stop swiveling.
AFS OFF INDICATOR OPERATION
In response to the state of control, AFS control unit switches com-
mands of AFS off indicator signal sent to unified meter and A/C amp.
via CAN communication; and then turns on/off or blinks AFS off indi-
cator lamp built in the combination meter depending on the following
condition.
Bulb check operation
AFS off indicator lamp is turned off after illuminating for one sec-
ond as a bulb check for AFS off indicator lamp when turn ignition
switch ON is detected.
NOTE:
AFS off indicator lamp is turned off without a lapse of one sec-
ond when start of the engine is detected.
AFS switch operation
AFS off indicator lamp is illuminated while AFS switch is OFF.
AFS off indicator lamp is turned off while AFS switch is ON.
System warning operation
AFS off indicator lamp illuminates at intervals of approximately one second when AFS control unit detects
any specific DTC (diagnosis trouble code), or when unified meter and A/C amp. cannot receive AFS off
indicator signals.
NOTE:
Unified meter and A/C amp. transmits a command to combination meter to blink AFS off indicator lamp
when they cannot receive AFS off indicator signal.
SWIVEL ACTUATOR INITIALIZATION
AFS control unit performs swivel operation to initialize swivel actuator when start of the engine is detected.
Straight-ahead position of low beam headlamps is adjusted by turning low beam headlamps to outside vehicle
with specified swivel angle after turning it to the center of vehicle and making sure that it reaches the stopper.
Swivel actuator initialization shall be performed every time when start of the engine is detected.
SKIB4765E
Page 4566 of 5621
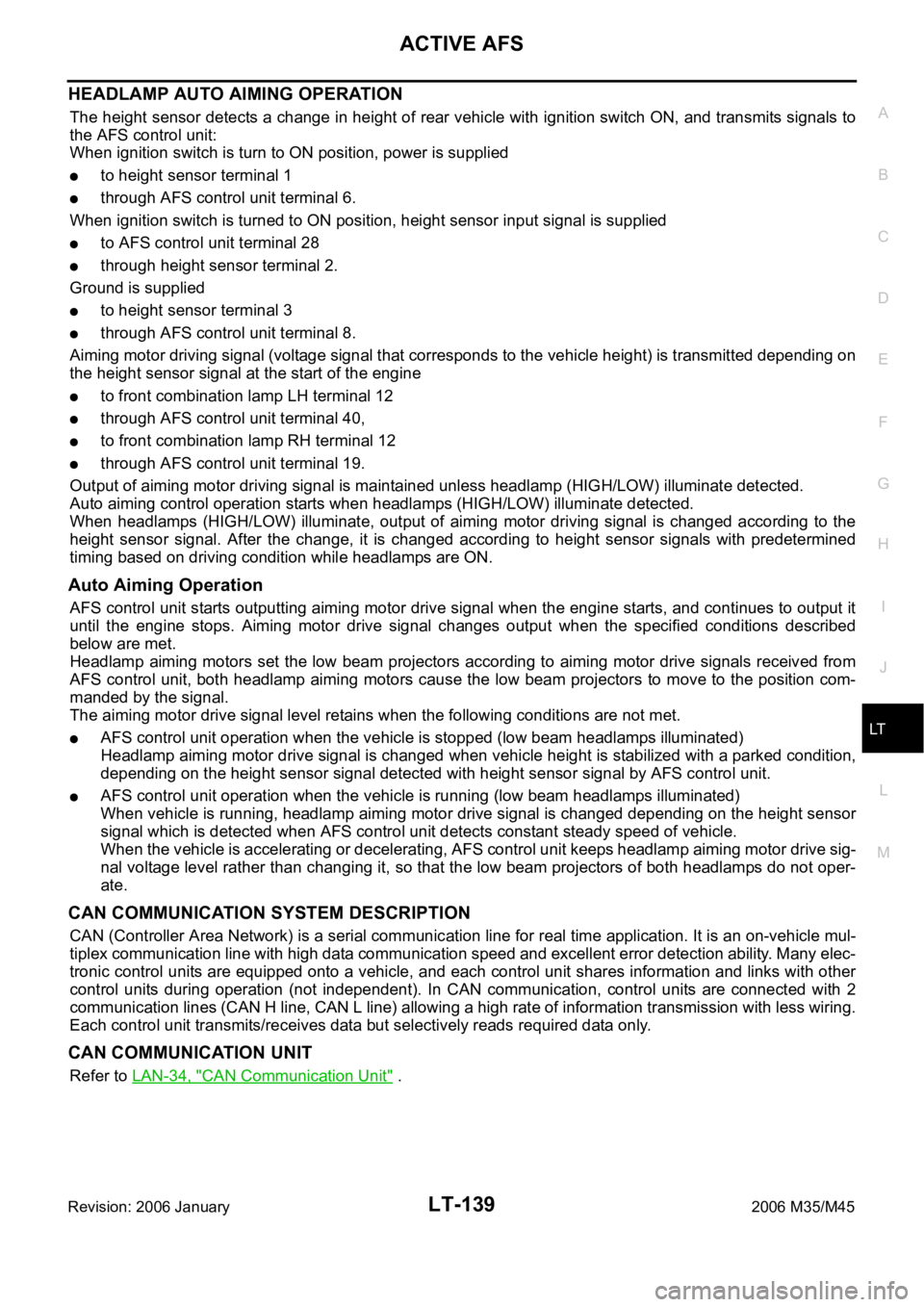
ACTIVE AFS
LT-139
C
D
E
F
G
H
I
J
L
MA
B
LT
Revision: 2006 January2006 M35/M45
HEADLAMP AUTO AIMING OPERATION
The height sensor detects a change in height of rear vehicle with ignition switch ON, and transmits signals to
the AFS control unit:
When ignition switch is turn to ON position, power is supplied
to height sensor terminal 1
through AFS control unit terminal 6.
When ignition switch is turned to ON position, height sensor input signal is supplied
to AFS control unit terminal 28
through height sensor terminal 2.
Ground is supplied
to height sensor terminal 3
through AFS control unit terminal 8.
Aiming motor driving signal (voltage signal that corresponds to the vehicle height) is transmitted depending on
the height sensor signal at the start of the engine
to front combination lamp LH terminal 12
through AFS control unit terminal 40,
to front combination lamp RH terminal 12
through AFS control unit terminal 19.
Output of aiming motor driving signal is maintained unless headlamp (HIGH/LOW) illuminate detected.
Auto aiming control operation starts when headlamps (HIGH/LOW) illuminate detected.
When headlamps (HIGH/LOW) illuminate, output of aiming motor driving signal is changed according to the
height sensor signal. After the change, it is changed according to height sensor signals with predetermined
timing based on driving condition while headlamps are ON.
Auto Aiming Operation
AFS control unit starts outputting aiming motor drive signal when the engine starts, and continues to output it
until the engine stops. Aiming motor drive signal changes output when the specified conditions described
below are met.
Headlamp aiming motors set the low beam projectors according to aiming motor drive signals received from
AFS control unit, both headlamp aiming motors cause the low beam projectors to move to the position com-
manded by the signal.
The aiming motor drive signal level retains when the following conditions are not met.
AFS control unit operation when the vehicle is stopped (low beam headlamps illuminated)
Headlamp aiming motor drive signal is changed when vehicle height is stabilized with a parked condition,
depending on the height sensor signal detected with height sensor signal by AFS control unit.
AFS control unit operation when the vehicle is running (low beam headlamps illuminated)
When vehicle is running, headlamp aiming motor drive signal is changed depending on the height sensor
signal which is detected when AFS control unit detects constant steady speed of vehicle.
When the vehicle is accelerating or decelerating, AFS control unit keeps headlamp aiming motor drive sig-
nal voltage level rather than changing it, so that the low beam projectors of both headlamps do not oper-
ate.
CAN COMMUNICATION SYSTEM DESCRIPTION
CAN (Controller Area Network) is a serial communication line for real time application. It is an on-vehicle mul-
tiplex communication line with high data communication speed and excellent error detection ability. Many elec-
tronic control units are equipped onto a vehicle, and each control unit shares information and links with other
control units during operation (not independent). In CAN communication, control units are connected with 2
communication lines (CAN H line, CAN L line) allowing a high rate of information transmission with less wiring.
Each control unit transmits/receives data but selectively reads required data only.
CAN COMMUNICATION UNIT
Refer to LAN-34, "CAN Communication Unit" .
Page 4567 of 5621
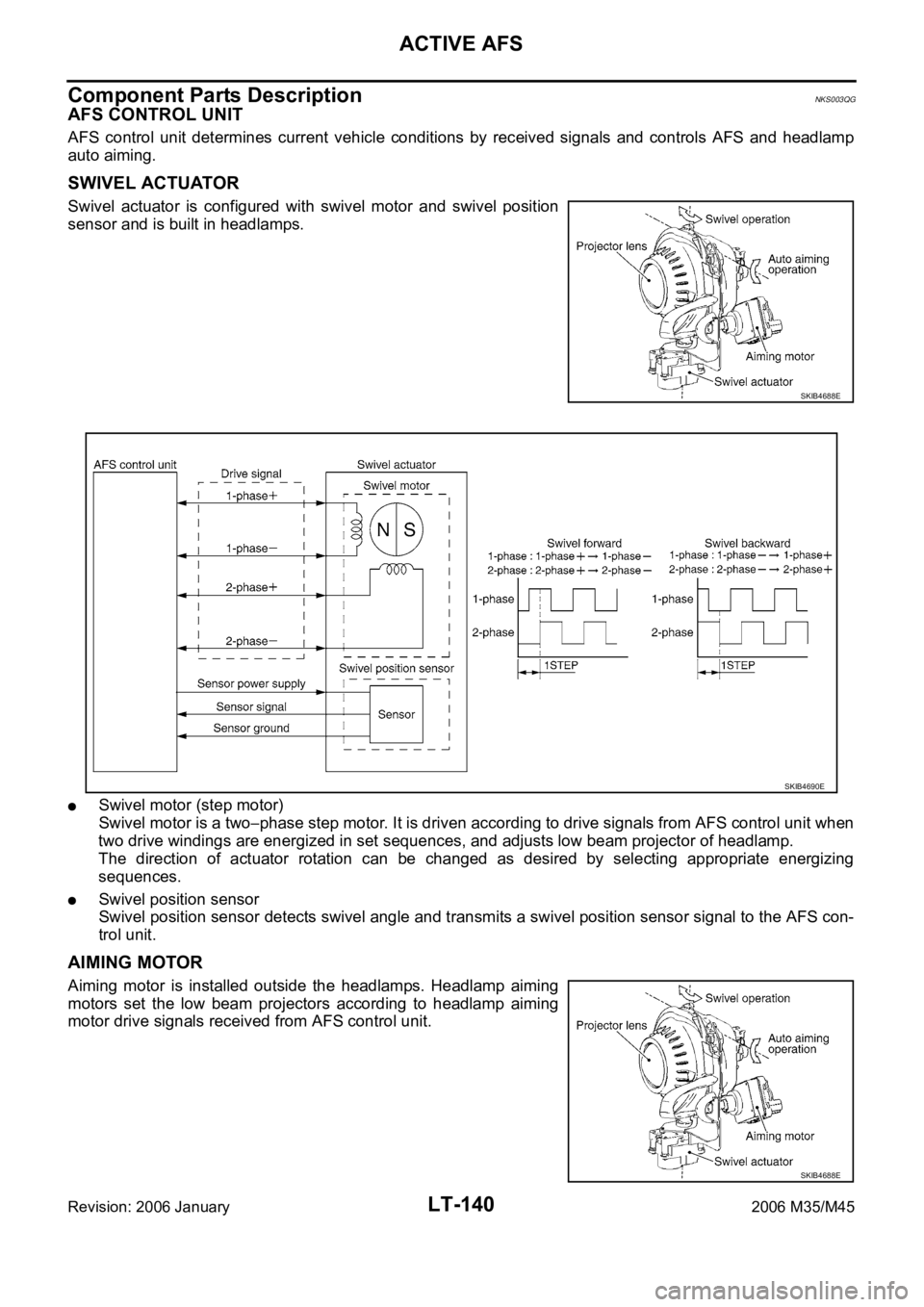
LT-140
ACTIVE AFS
Revision: 2006 January2006 M35/M45
Component Parts DescriptionNKS003QG
AFS CONTROL UNIT
AFS control unit determines current vehicle conditions by received signals and controls AFS and headlamp
auto aiming.
SWIVEL ACTUATOR
Swivel actuator is configured with swivel motor and swivel position
sensor and is built in headlamps.
Swivel motor (step motor)
Swivel motor is a two
phase step motor. It is driven according to drive signals from AFS control unit when
two drive windings are energized in set sequences, and adjusts low beam projector of headlamp.
The direction of actuator rotation can be changed as desired by selecting appropriate energizing
sequences.
Swivel position sensor
Swivel position sensor detects swivel angle and transmits a swivel position sensor signal to the AFS con-
trol unit.
AIMING MOTOR
Aiming motor is installed outside the headlamps. Headlamp aiming
motors set the low beam projectors according to headlamp aiming
motor drive signals received from AFS control unit.
SKIB4688E
SKIB4690E
SKIB4688E
Page 4576 of 5621

ACTIVE AFS
LT-149
C
D
E
F
G
H
I
J
L
MA
B
LT
Revision: 2006 January2006 M35/M45
Terminals and Reference Values for AFS Control UnitNKS003QJ
Te r -
minal
No.Wire
colorItemMeasuring condition
Reference value
Ignition
switchOperation or condition
1 B/R IGN power supply ON — Battery voltage
2W/RSwivel position sensor ground
(right)ON — Approx. 0 V
3 GR AFS switch signal ON AFS switchON Approx. 0 V
OFF Battery voltage
4YSwivel position sensor power
supply (right)ON — Approx. 5 V
6 V/W Height sensor power supply ON — Approx. 5 V
7 P CAN-L — — —
8 B/R Height sensor ground ON — Approx. 0 V
9W/BSwivel position sensor signal
(right)ONLow beam headlamp
(right) swivel angle0
Approx. 1.5 V
Maximum
angleApprox. 2.5 V
11 R Swivel motor 1 phase
(right) ON
Low beam headlamp
(right) swivelONReference waveform
Approx. 8 - 12 V
13 B Swivel motor 2 phase
(right) ON OFF Approx. 9.5 - 11.5 V
15 BR/L Swivel motor 1 phase+ (left) ON
Low beam headlamp
(left) swivelONReference waveform
Approx. 8 - 12 V
17 Y/G Swivel motor 2 phase+ (left) ON OFF Approx. 9.5 - 11.5 V
19 V Aiming motor drive signal (right) ONLow beam headlamp
(right) auto aimingUnloaded
vehicle posi-
tionApprox. 9 V
Maximum
laden condi-
tion Approx. 4.8 V
(With 18- inch wheel)
Approx. 5.2 V
(With 19 -inch wheel)
24 V/RSwivel position sensor power
supply (left)ON — Approx. 5 V
25 B Ground ON — Approx. 0 V
27 R/WSwivel position sensor ground
(left)ON — Approx. 0 V
SKIB2408J
SKIB2408J
Page 4577 of 5621
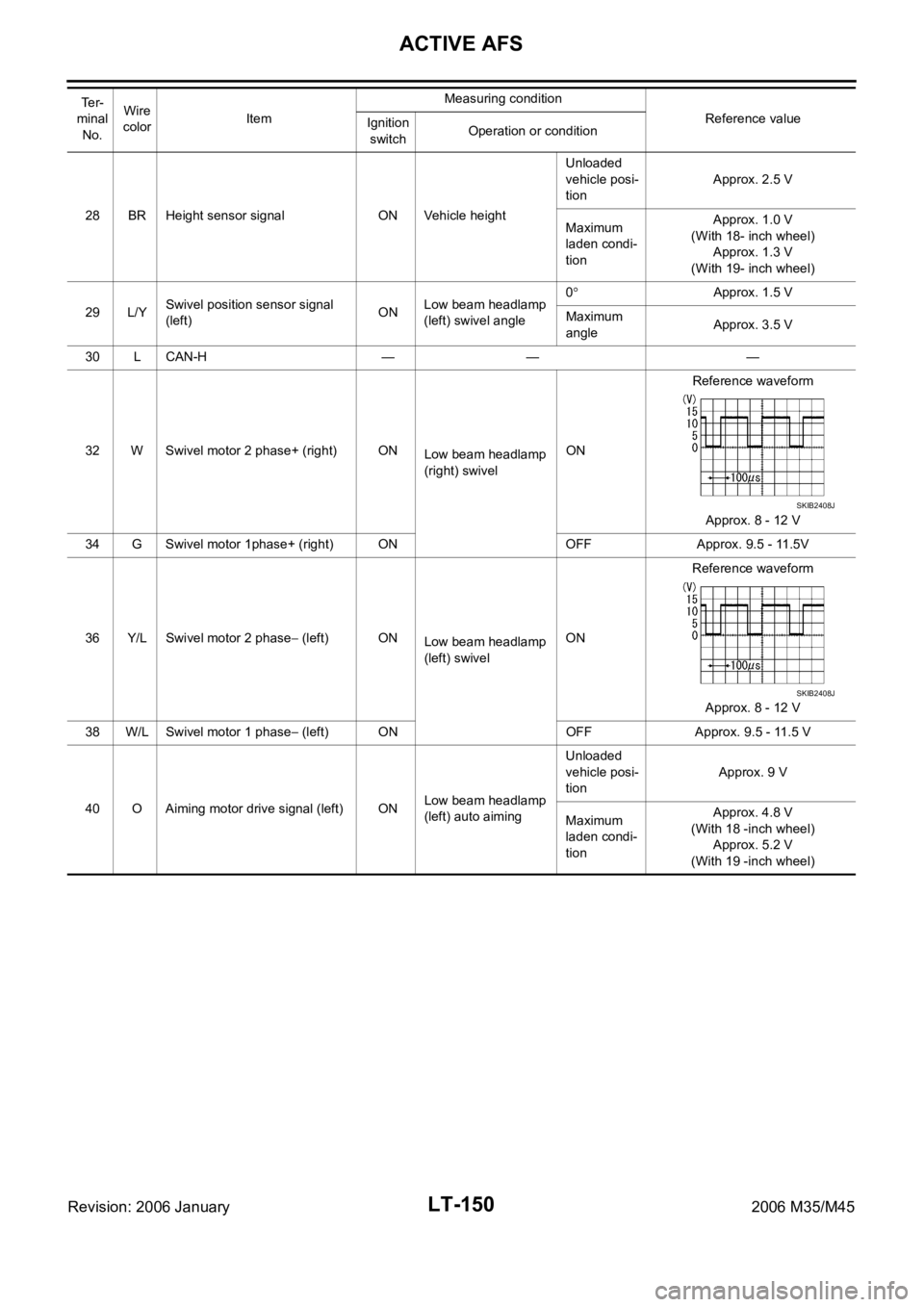
LT-150
ACTIVE AFS
Revision: 2006 January2006 M35/M45
28 BR Height sensor signal ON Vehicle heightUnloaded
vehicle posi-
tionApprox. 2.5 V
Maximum
laden condi-
tion Approx. 1.0 V
(With 18- inch wheel)
Approx. 1.3 V
(With 19- inch wheel)
29 L/YSwivel position sensor signal
(left)ONLow beam headlamp
(left) swivel angle0
Approx. 1.5 V
Maximum
angleApprox. 3.5 V
30 L CAN-H — — —
32 W Swivel motor 2 phase+ (right) ON
Low beam headlamp
(right) swivelONReference waveform
Approx. 8 - 12 V
34 G Swivel motor 1phase+ (right) ON OFF Approx. 9.5 - 11.5V
36 Y/L Swivel motor 2 phase
(left) ON
Low beam headlamp
(left) swivelONReference waveform
Approx. 8 - 12 V
38 W/L Swivel motor 1 phase
(left) ON OFF Approx. 9.5 - 11.5 V
40 O Aiming motor drive signal (left) ONLow beam headlamp
(left) auto aimingUnloaded
vehicle posi-
tionApprox. 9 V
Maximum
laden condi-
tion Approx. 4.8 V
(With 18 -inch wheel)
Approx. 5.2 V
(With 19 -inch wheel) Te r -
minal
No.Wire
colorItemMeasuring condition
Reference value
Ignition
switchOperation or condition
SKIB2408J
SKIB2408J
Page 4581 of 5621
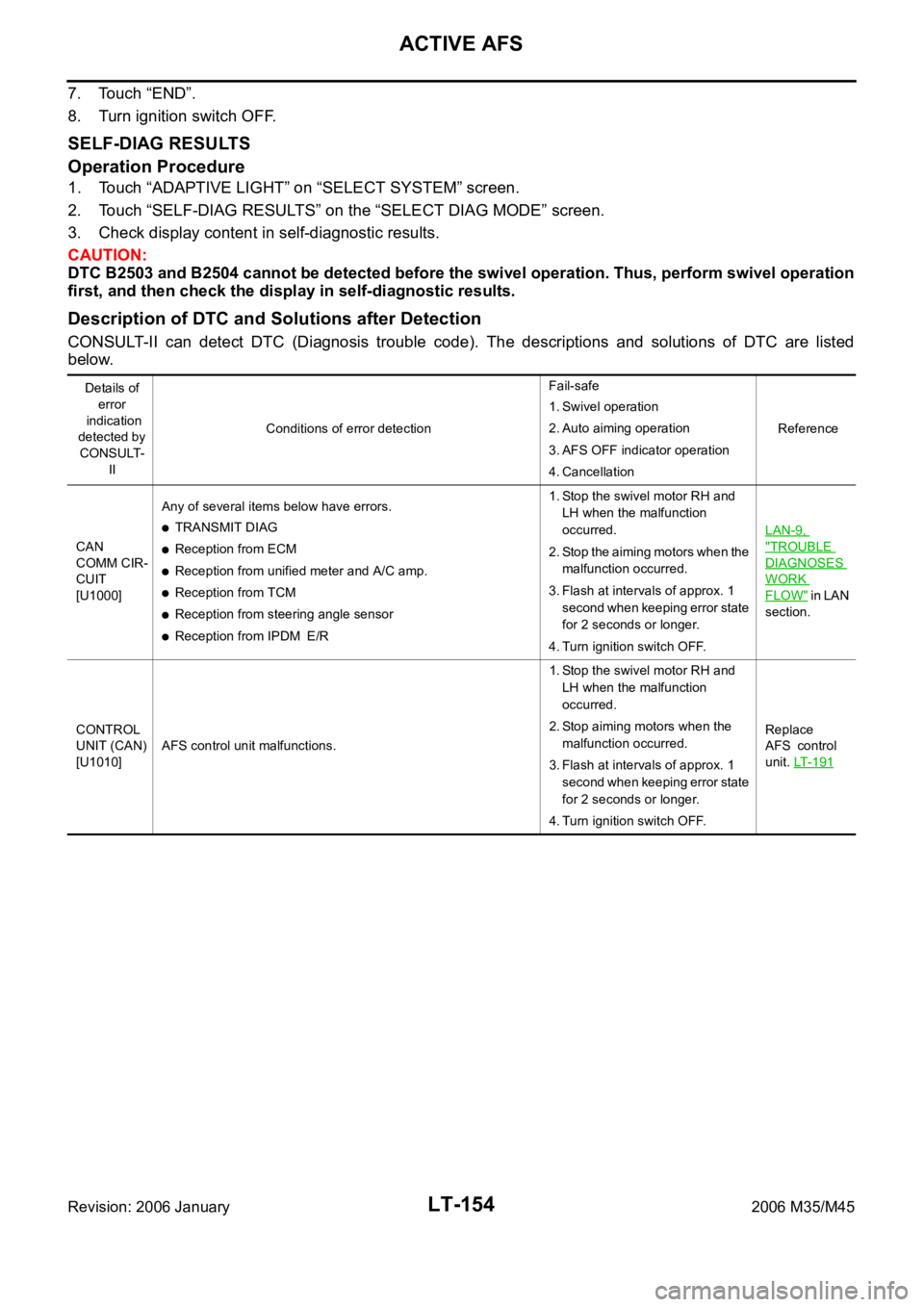
LT-154
ACTIVE AFS
Revision: 2006 January2006 M35/M45
7. Touch “END”.
8. Turn ignition switch OFF.
SELF-DIAG RESULTS
Operation Procedure
1. Touch “ADAPTIVE LIGHT” on “SELECT SYSTEM” screen.
2. Touch “SELF-DIAG RESULTS” on the “SELECT DIAG MODE” screen.
3. Check display content in self-diagnostic results.
CAUTION:
DTC B2503 and B2504 cannot be detected before the swivel operation. Thus, perform swivel operation
first, and then check the display in self-diagnostic results.
Description of DTC and Solutions after Detection
CONSULT-II can detect DTC (Diagnosis trouble code). The descriptions and solutions of DTC are listed
below.
Details of
error
indication
detected by
CONSULT-
IIConditions of error detectionFail-safe
1. Swivel operation
2. Auto aiming operation
3. AFS OFF indicator operation
4. CancellationReference
CAN
COMM CIR-
CUIT
[U1000]Any of several items below have errors.
TRANSMIT DIAG
Reception from ECM
Reception from unified meter and A/C amp.
Reception from TCM
Reception from steering angle sensor
Reception from IPDM E/R1. Stop the swivel motor RH and
LH when the malfunction
occurred.
2. Stop the aiming motors when the
malfunction occurred.
3. Flash at intervals of approx. 1
second when keeping error state
for 2 seconds or longer.
4. Turn ignition switch OFF.LAN-9,
"TROUBLE
DIAGNOSES
WORK
FLOW" i n L A N
section.
CONTROL
UNIT (CAN)
[U1010]AFS control unit malfunctions.1. Stop the swivel motor RH and
LH when the malfunction
occurred.
2. Stop aiming motors when the
malfunction occurred.
3. Flash at intervals of approx. 1
second when keeping error state
for 2 seconds or longer.
4. Turn ignition switch OFF.Replace
AFS control
unit. LT- 1 9 1