Ignition harness INFINITI QX4 2001 Factory Service Manual
[x] Cancel search | Manufacturer: INFINITI, Model Year: 2001, Model line: QX4, Model: INFINITI QX4 2001Pages: 2395, PDF Size: 43.2 MB
Page 953 of 2395
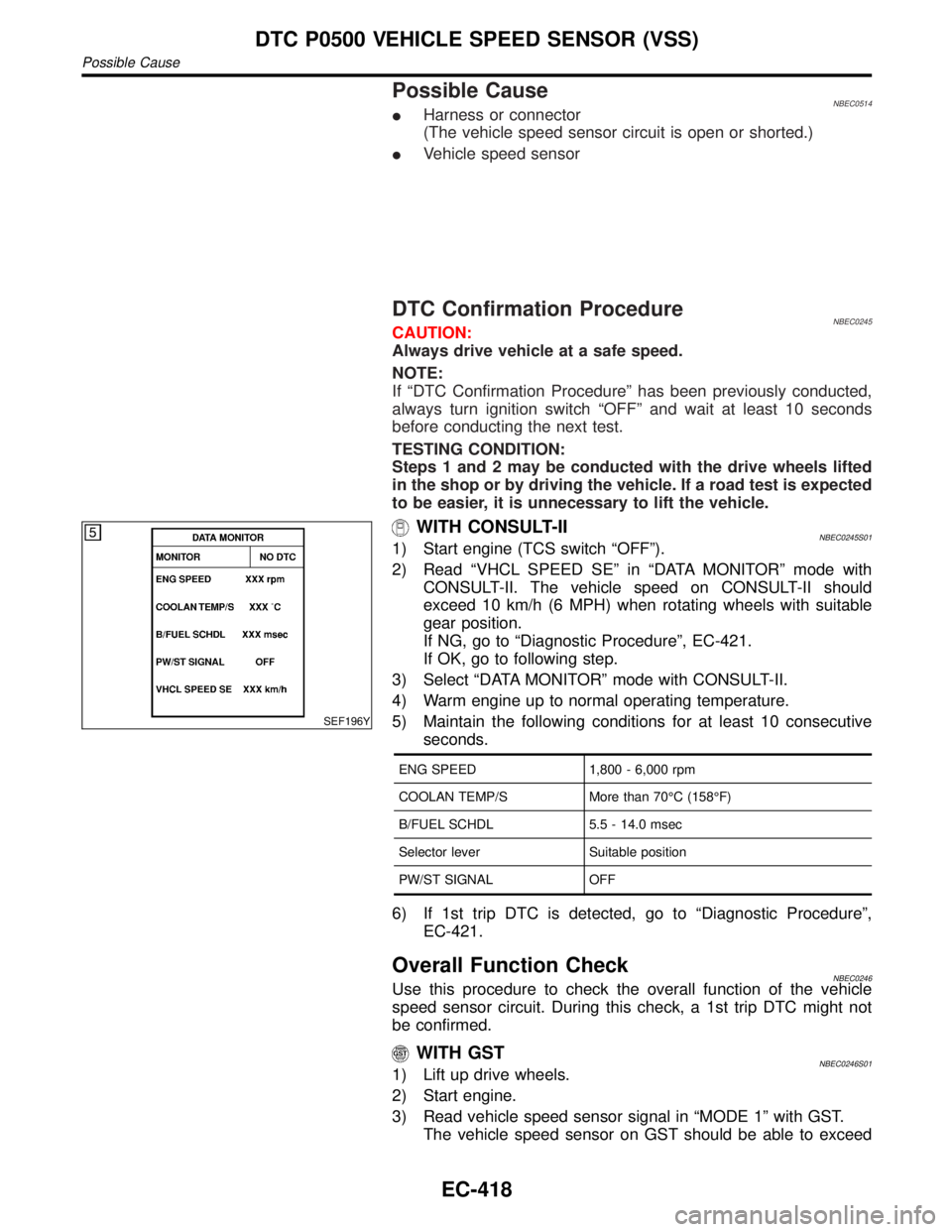
Possible CauseNBEC0514IHarness or connector
(The vehicle speed sensor circuit is open or shorted.)
IVehicle speed sensor
DTC Confirmation ProcedureNBEC0245CAUTION:
Always drive vehicle at a safe speed.
NOTE:
If ªDTC Confirmation Procedureº has been previously conducted,
always turn ignition switch ªOFFº and wait at least 10 seconds
before conducting the next test.
TESTING CONDITION:
Steps 1 and 2 may be conducted with the drive wheels lifted
in the shop or by driving the vehicle. If a road test is expected
to be easier, it is unnecessary to lift the vehicle.
SEF196Y
WITH CONSULT-IINBEC0245S011) Start engine (TCS switch ªOFFº).
2) Read ªVHCL SPEED SEº in ªDATA MONITORº mode with
CONSULT-II. The vehicle speed on CONSULT-II should
exceed 10 km/h (6 MPH) when rotating wheels with suitable
gear position.
If NG, go to ªDiagnostic Procedureº, EC-421.
If OK, go to following step.
3) Select ªDATA MONITORº mode with CONSULT-II.
4) Warm engine up to normal operating temperature.
5) Maintain the following conditions for at least 10 consecutive
seconds.
ENG SPEED 1,800 - 6,000 rpm
COOLAN TEMP/S More than 70ÉC (158ÉF)
B/FUEL SCHDL 5.5 - 14.0 msec
Selector lever Suitable position
PW/ST SIGNAL OFF
6) If 1st trip DTC is detected, go to ªDiagnostic Procedureº,
EC-421.
Overall Function CheckNBEC0246Use this procedure to check the overall function of the vehicle
speed sensor circuit. During this check, a 1st trip DTC might not
be confirmed.
WITH GSTNBEC0246S011) Lift up drive wheels.
2) Start engine.
3) Read vehicle speed sensor signal in ªMODE 1º with GST.
The vehicle speed sensor on GST should be able to exceed
DTC P0500 VEHICLE SPEED SENSOR (VSS)
Possible Cause
EC-418
Page 956 of 2395
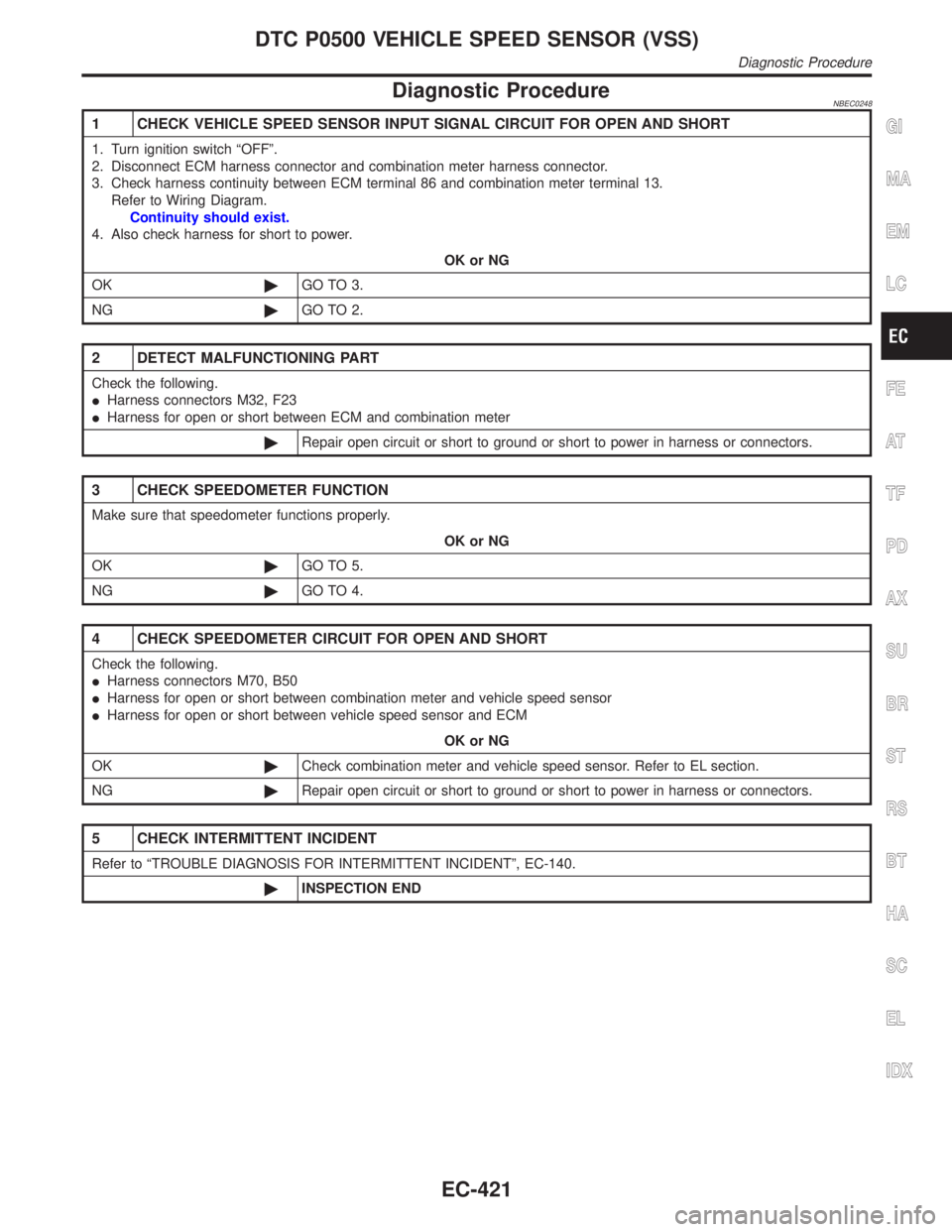
Diagnostic ProcedureNBEC0248
1 CHECK VEHICLE SPEED SENSOR INPUT SIGNAL CIRCUIT FOR OPEN AND SHORT
1. Turn ignition switch ªOFFº.
2. Disconnect ECM harness connector and combination meter harness connector.
3. Check harness continuity between ECM terminal 86 and combination meter terminal 13.
Refer to Wiring Diagram.
Continuity should exist.
4. Also check harness for short to power.
OK or NG
OK©GO TO 3.
NG©GO TO 2.
2 DETECT MALFUNCTIONING PART
Check the following.
IHarness connectors M32, F23
IHarness for open or short between ECM and combination meter
©Repair open circuit or short to ground or short to power in harness or connectors.
3 CHECK SPEEDOMETER FUNCTION
Make sure that speedometer functions properly.
OK or NG
OK©GO TO 5.
NG©GO TO 4.
4 CHECK SPEEDOMETER CIRCUIT FOR OPEN AND SHORT
Check the following.
IHarness connectors M70, B50
IHarness for open or short between combination meter and vehicle speed sensor
IHarness for open or short between vehicle speed sensor and ECM
OK or NG
OK©Check combination meter and vehicle speed sensor. Refer to EL section.
NG©Repair open circuit or short to ground or short to power in harness or connectors.
5 CHECK INTERMITTENT INCIDENT
Refer to ªTROUBLE DIAGNOSIS FOR INTERMITTENT INCIDENTº, EC-140.
©INSPECTION END
GI
MA
EM
LC
FE
AT
TF
PD
AX
SU
BR
ST
RS
BT
HA
SC
EL
IDX
DTC P0500 VEHICLE SPEED SENSOR (VSS)
Diagnostic Procedure
EC-421
Page 958 of 2395
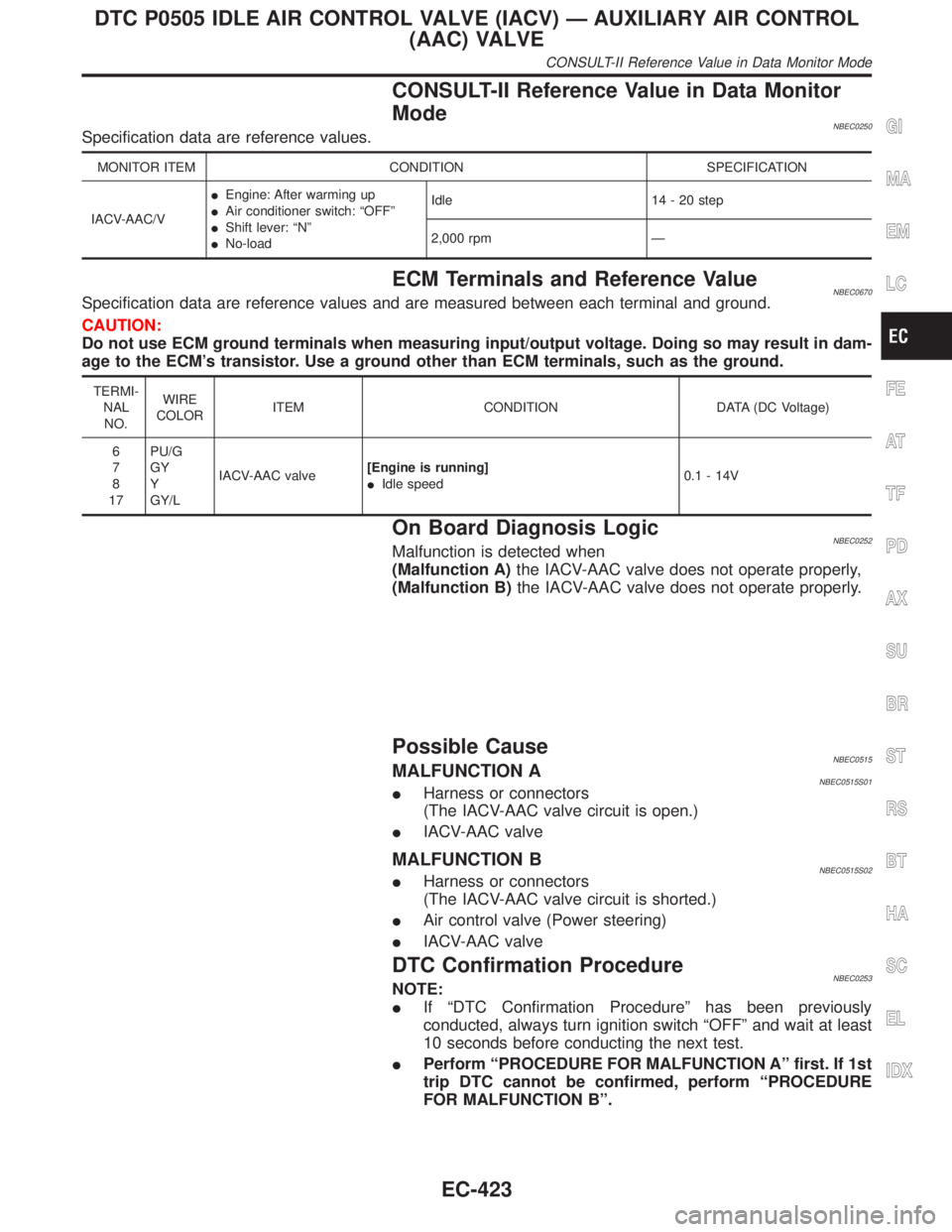
CONSULT-II Reference Value in Data Monitor
Mode
NBEC0250Specification data are reference values.
MONITOR ITEM CONDITION SPECIFICATION
IACV-AAC/VIEngine: After warming up
IAir conditioner switch: ªOFFº
IShift lever: ªNº
INo-loadIdle 14 - 20 step
2,000 rpm Ð
ECM Terminals and Reference ValueNBEC0670Specification data are reference values and are measured between each terminal and ground.
CAUTION:
Do not use ECM ground terminals when measuring input/output voltage. Doing so may result in dam-
age to the ECM's transistor. Use a ground other than ECM terminals, such as the ground.
TERMI-
NAL
NO.WIRE
COLORITEM CONDITION DATA (DC Voltage)
6
7
8
17PU/G
GY
Y
GY/LIACV-AAC valve[Engine is running]
IIdle speed0.1 - 14V
On Board Diagnosis LogicNBEC0252Malfunction is detected when
(Malfunction A)the IACV-AAC valve does not operate properly,
(Malfunction B)the IACV-AAC valve does not operate properly.
Possible CauseNBEC0515MALFUNCTION ANBEC0515S01IHarness or connectors
(The IACV-AAC valve circuit is open.)
IIACV-AAC valve
MALFUNCTION BNBEC0515S02IHarness or connectors
(The IACV-AAC valve circuit is shorted.)
IAir control valve (Power steering)
IIACV-AAC valve
DTC Confirmation ProcedureNBEC0253NOTE:
IIf ªDTC Confirmation Procedureº has been previously
conducted, always turn ignition switch ªOFFº and wait at least
10 seconds before conducting the next test.
IPerform ªPROCEDURE FOR MALFUNCTION Aº first. If 1st
trip DTC cannot be confirmed, perform ªPROCEDURE
FOR MALFUNCTION Bº.
GI
MA
EM
LC
FE
AT
TF
PD
AX
SU
BR
ST
RS
BT
HA
SC
EL
IDX
DTC P0505 IDLE AIR CONTROL VALVE (IACV) Ð AUXILIARY AIR CONTROL
(AAC) VALVE
CONSULT-II Reference Value in Data Monitor Mode
EC-423
Page 961 of 2395
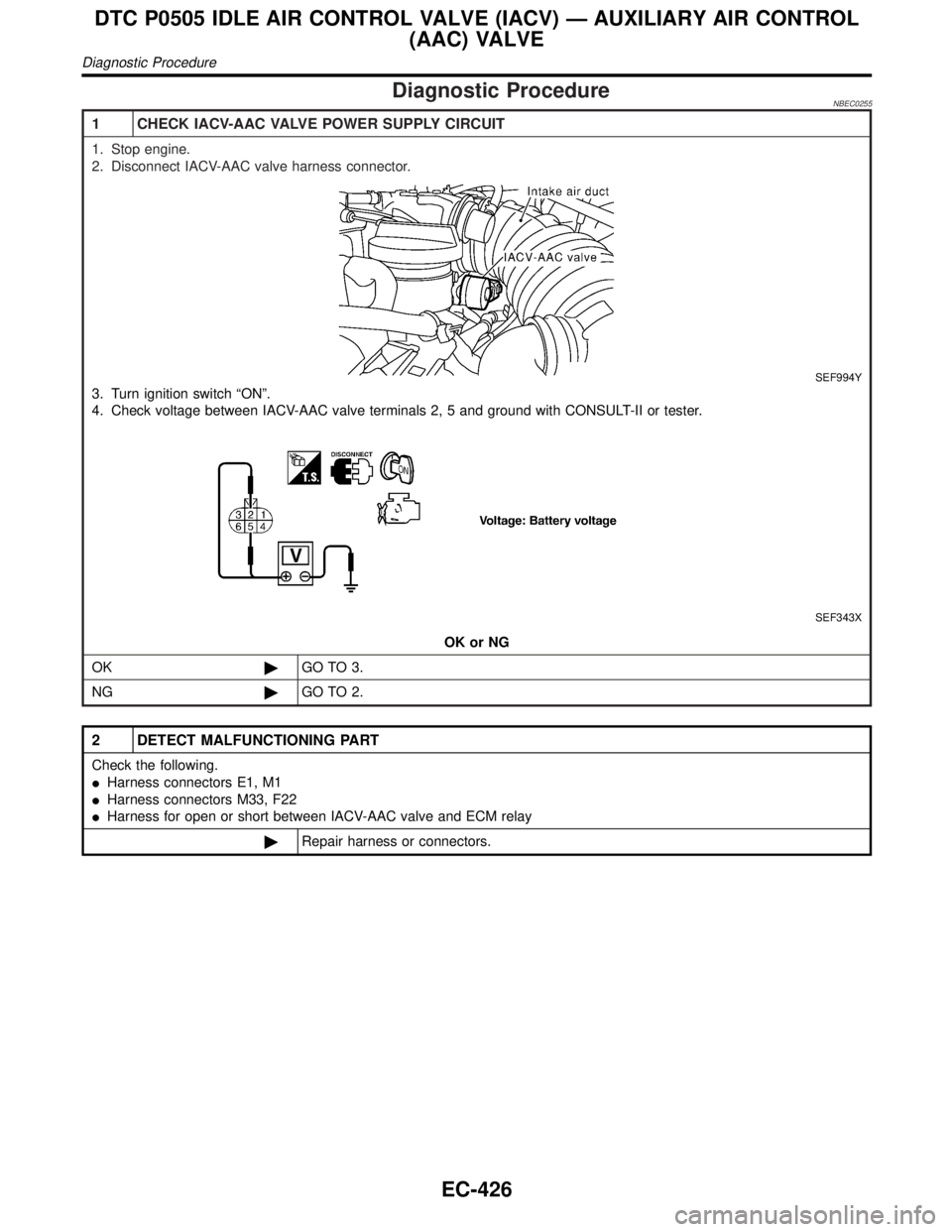
Diagnostic ProcedureNBEC0255
1 CHECK IACV-AAC VALVE POWER SUPPLY CIRCUIT
1. Stop engine.
2. Disconnect IACV-AAC valve harness connector.
SEF994Y
3. Turn ignition switch ªONº.
4. Check voltage between IACV-AAC valve terminals 2, 5 and ground with CONSULT-II or tester.
SEF343X
OK or NG
OK©GO TO 3.
NG©GO TO 2.
2 DETECT MALFUNCTIONING PART
Check the following.
IHarness connectors E1, M1
IHarness connectors M33, F22
IHarness for open or short between IACV-AAC valve and ECM relay
©Repair harness or connectors.
DTC P0505 IDLE AIR CONTROL VALVE (IACV) Ð AUXILIARY AIR CONTROL
(AAC) VALVE
Diagnostic Procedure
EC-426
Page 962 of 2395
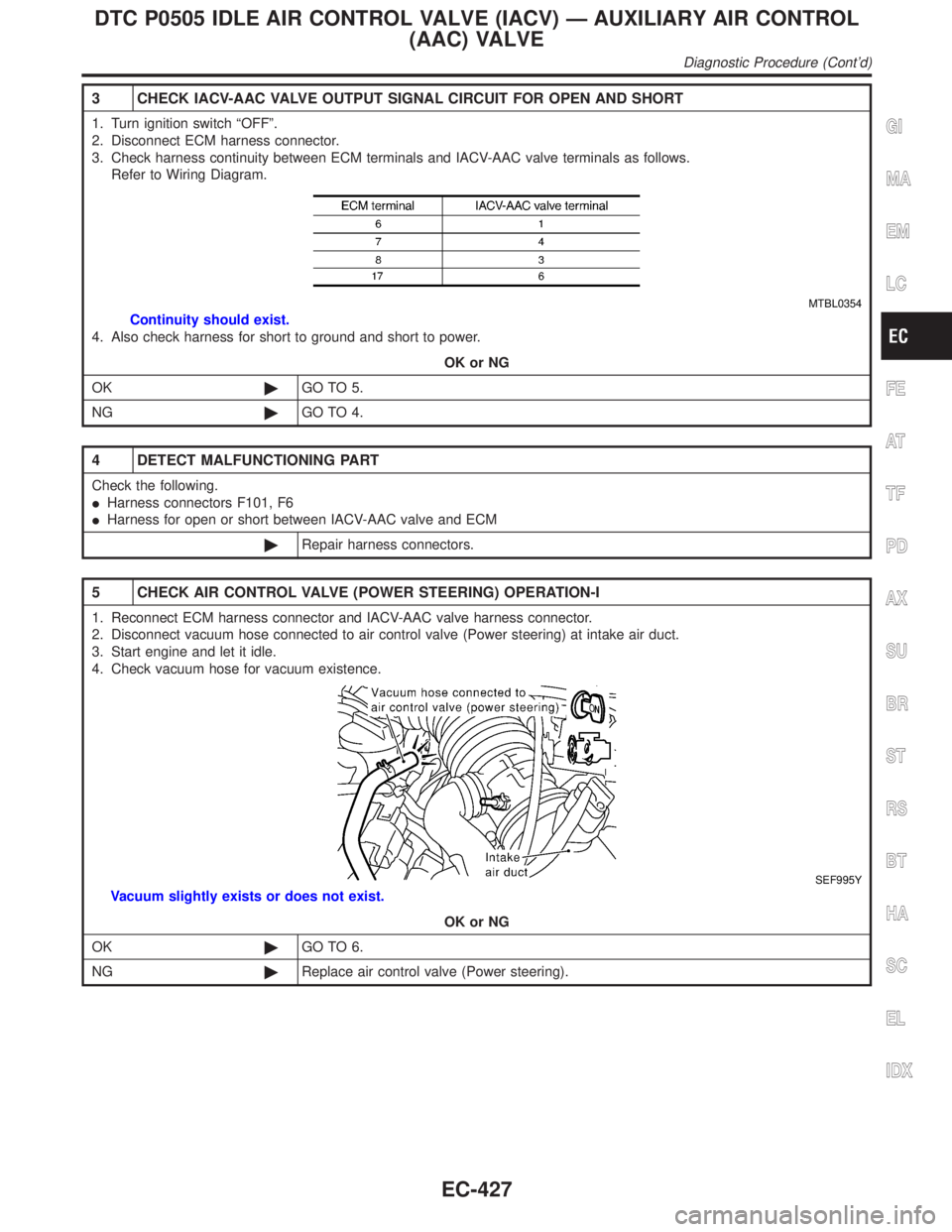
3 CHECK IACV-AAC VALVE OUTPUT SIGNAL CIRCUIT FOR OPEN AND SHORT
1. Turn ignition switch ªOFFº.
2. Disconnect ECM harness connector.
3. Check harness continuity between ECM terminals and IACV-AAC valve terminals as follows.
Refer to Wiring Diagram.
MTBL0354
Continuity should exist.
4. Also check harness for short to ground and short to power.
OK or NG
OK©GO TO 5.
NG©GO TO 4.
4 DETECT MALFUNCTIONING PART
Check the following.
IHarness connectors F101, F6
IHarness for open or short between IACV-AAC valve and ECM
©Repair harness connectors.
5 CHECK AIR CONTROL VALVE (POWER STEERING) OPERATION-I
1. Reconnect ECM harness connector and IACV-AAC valve harness connector.
2. Disconnect vacuum hose connected to air control valve (Power steering) at intake air duct.
3. Start engine and let it idle.
4. Check vacuum hose for vacuum existence.
SEF995Y
Vacuum slightly exists or does not exist.
OK or NG
OK©GO TO 6.
NG©Replace air control valve (Power steering).
GI
MA
EM
LC
FE
AT
TF
PD
AX
SU
BR
ST
RS
BT
HA
SC
EL
IDX
DTC P0505 IDLE AIR CONTROL VALVE (IACV) Ð AUXILIARY AIR CONTROL
(AAC) VALVE
Diagnostic Procedure (Cont'd)
EC-427
Page 965 of 2395
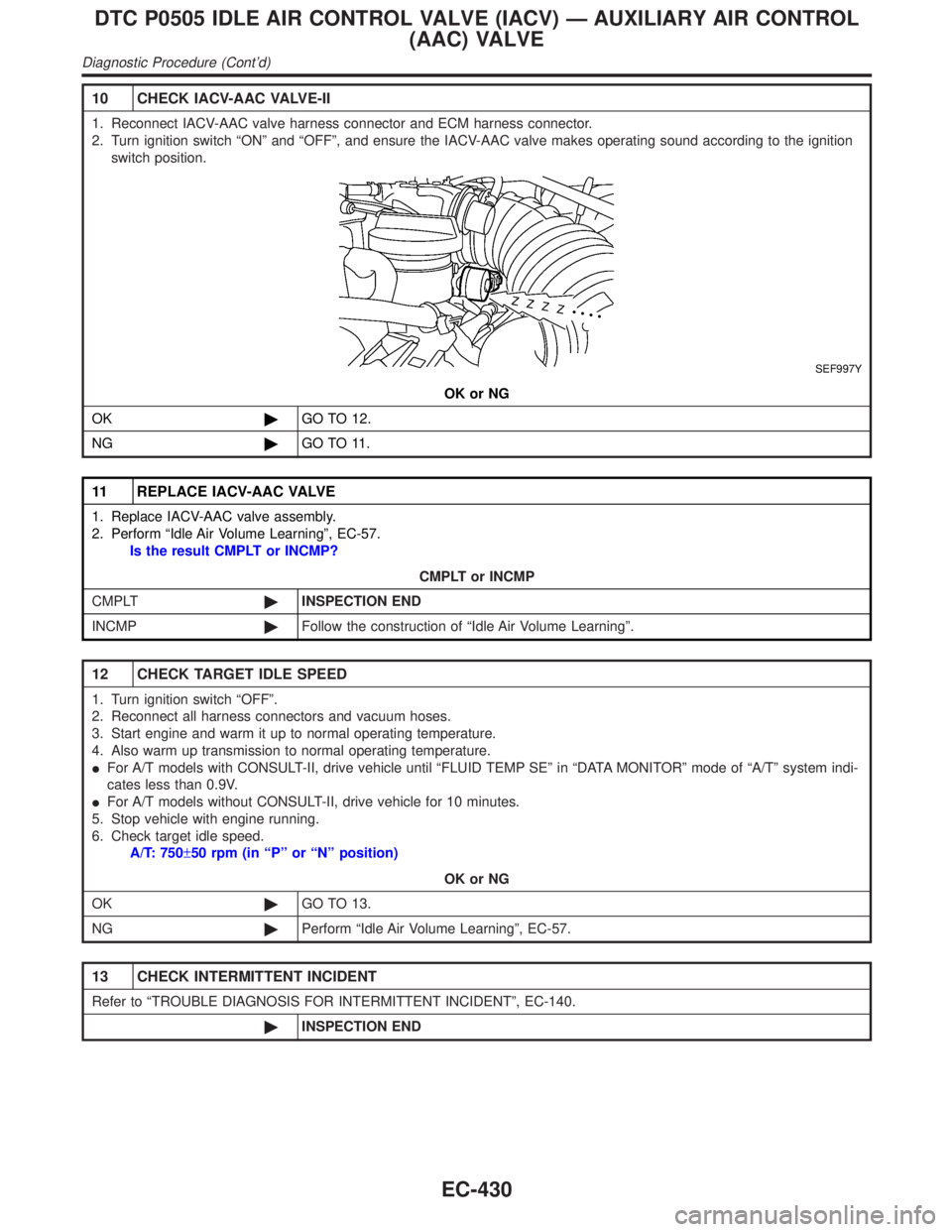
10 CHECK IACV-AAC VALVE-II
1. Reconnect IACV-AAC valve harness connector and ECM harness connector.
2. Turn ignition switch ªONº and ªOFFº, and ensure the IACV-AAC valve makes operating sound according to the ignition
switch position.
SEF997Y
OK or NG
OK©GO TO 12.
NG©GO TO 11.
11 REPLACE IACV-AAC VALVE
1. Replace IACV-AAC valve assembly.
2. Perform ªIdle Air Volume Learningº, EC-57.
Is the result CMPLT or INCMP?
CMPLT or INCMP
CMPLT©INSPECTION END
INCMP©Follow the construction of ªIdle Air Volume Learningº.
12 CHECK TARGET IDLE SPEED
1. Turn ignition switch ªOFFº.
2. Reconnect all harness connectors and vacuum hoses.
3. Start engine and warm it up to normal operating temperature.
4. Also warm up transmission to normal operating temperature.
IFor A/T models with CONSULT-II, drive vehicle until ªFLUID TEMP SEº in ªDATA MONITORº mode of ªA/Tº system indi-
cates less than 0.9V.
IFor A/T models without CONSULT-II, drive vehicle for 10 minutes.
5. Stop vehicle with engine running.
6. Check target idle speed.
A/T: 750±50 rpm (in ªPº or ªNº position)
OK or NG
OK©GO TO 13.
NG©Perform ªIdle Air Volume Learningº, EC-57.
13 CHECK INTERMITTENT INCIDENT
Refer to ªTROUBLE DIAGNOSIS FOR INTERMITTENT INCIDENTº, EC-140.
©INSPECTION END
DTC P0505 IDLE AIR CONTROL VALVE (IACV) Ð AUXILIARY AIR CONTROL
(AAC) VALVE
Diagnostic Procedure (Cont'd)
EC-430
Page 970 of 2395
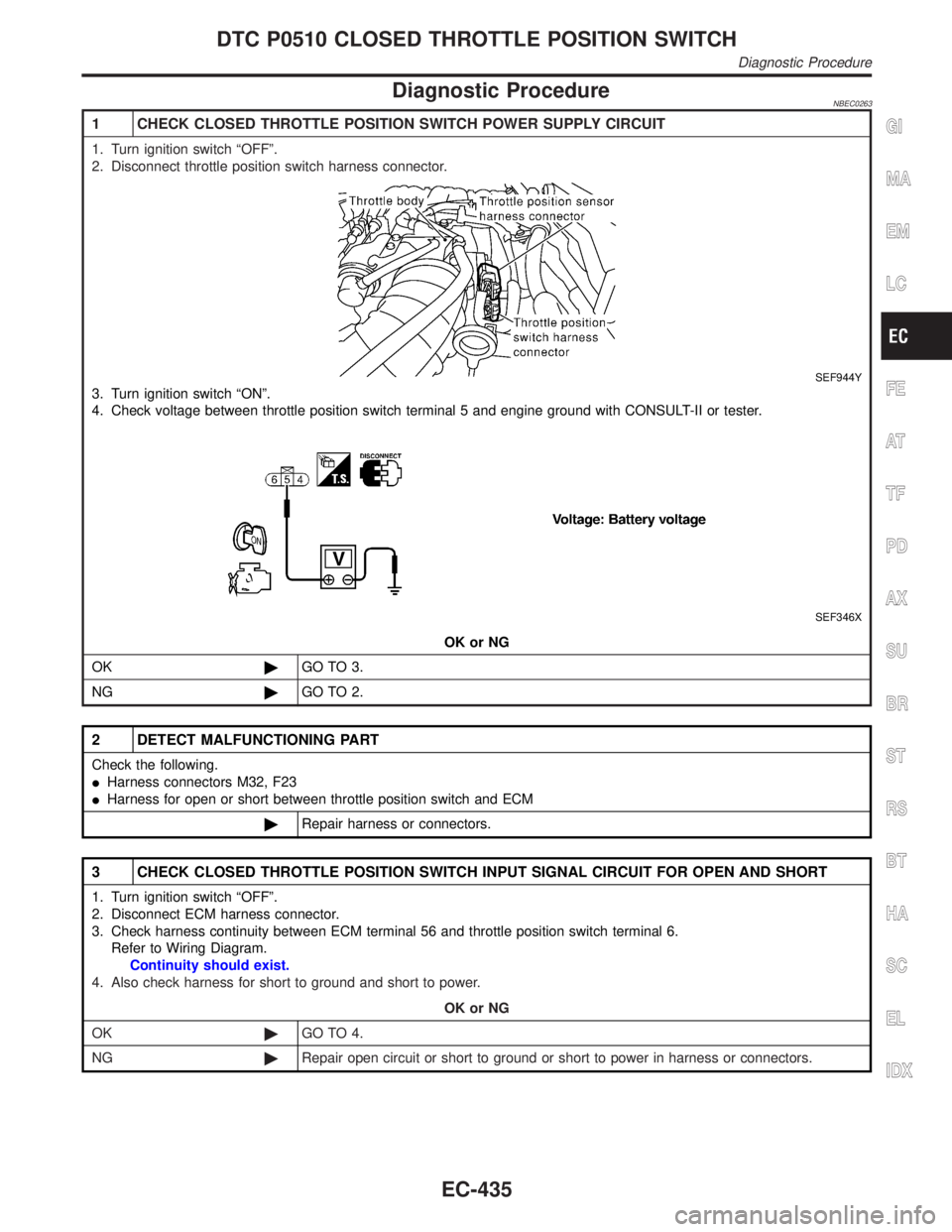
Diagnostic ProcedureNBEC0263
1 CHECK CLOSED THROTTLE POSITION SWITCH POWER SUPPLY CIRCUIT
1. Turn ignition switch ªOFFº.
2. Disconnect throttle position switch harness connector.
SEF944Y
3. Turn ignition switch ªONº.
4. Check voltage between throttle position switch terminal 5 and engine ground with CONSULT-II or tester.
SEF346X
OK or NG
OK©GO TO 3.
NG©GO TO 2.
2 DETECT MALFUNCTIONING PART
Check the following.
IHarness connectors M32, F23
IHarness for open or short between throttle position switch and ECM
©Repair harness or connectors.
3 CHECK CLOSED THROTTLE POSITION SWITCH INPUT SIGNAL CIRCUIT FOR OPEN AND SHORT
1. Turn ignition switch ªOFFº.
2. Disconnect ECM harness connector.
3. Check harness continuity between ECM terminal 56 and throttle position switch terminal 6.
Refer to Wiring Diagram.
Continuity should exist.
4. Also check harness for short to ground and short to power.
OK or NG
OK©GO TO 4.
NG©Repair open circuit or short to ground or short to power in harness or connectors.
GI
MA
EM
LC
FE
AT
TF
PD
AX
SU
BR
ST
RS
BT
HA
SC
EL
IDX
DTC P0510 CLOSED THROTTLE POSITION SWITCH
Diagnostic Procedure
EC-435
Page 972 of 2395
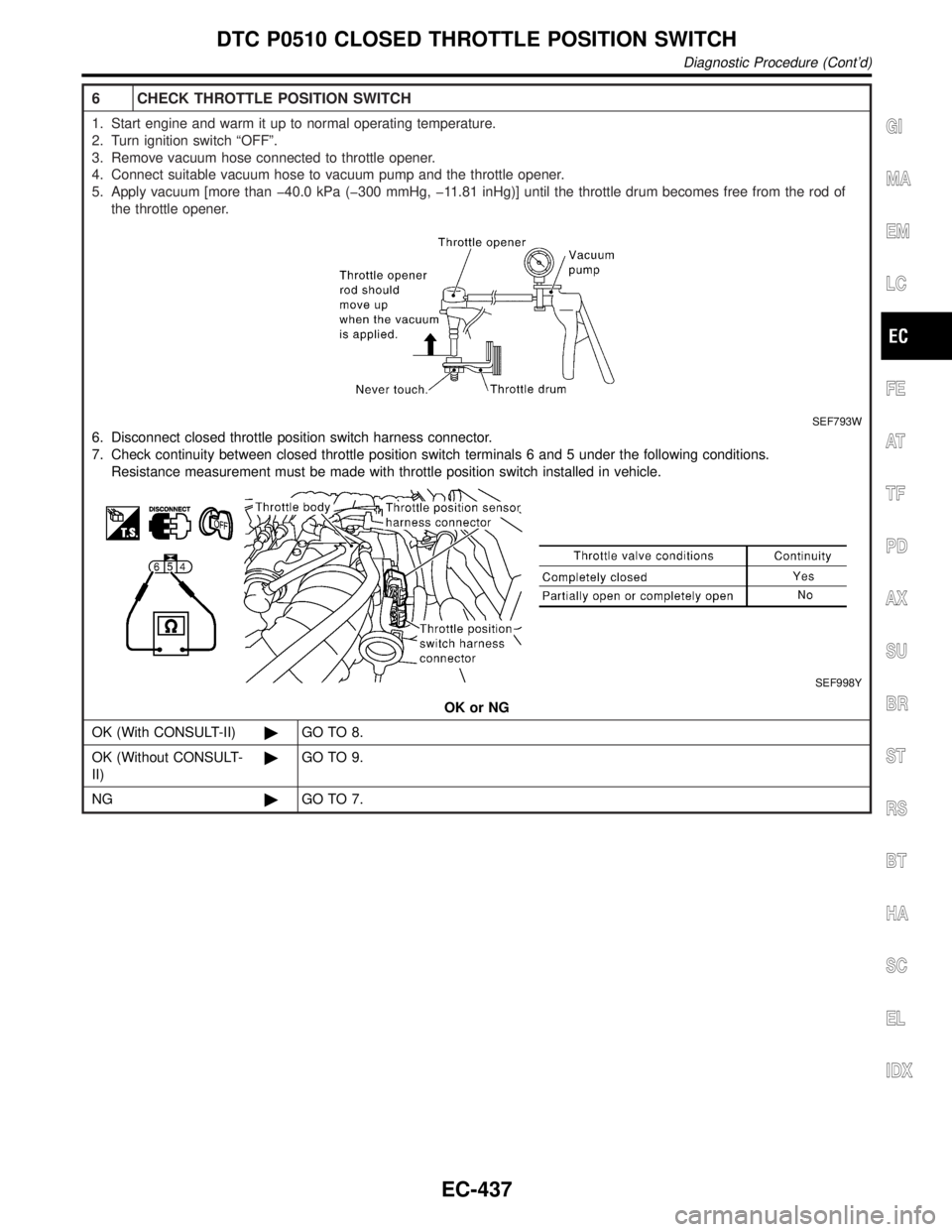
6 CHECK THROTTLE POSITION SWITCH
1. Start engine and warm it up to normal operating temperature.
2. Turn ignition switch ªOFFº.
3. Remove vacuum hose connected to throttle opener.
4. Connect suitable vacuum hose to vacuum pump and the throttle opener.
5. Apply vacuum [more than þ40.0 kPa (þ300 mmHg, þ11.81 inHg)] until the throttle drum becomes free from the rod of
the throttle opener.
SEF793W
6. Disconnect closed throttle position switch harness connector.
7. Check continuity between closed throttle position switch terminals 6 and 5 under the following conditions.
Resistance measurement must be made with throttle position switch installed in vehicle.
SEF998Y
OK or NG
OK (With CONSULT-II)©GO TO 8.
OK (Without CONSULT-
II)©GO TO 9.
NG©GO TO 7.
GI
MA
EM
LC
FE
AT
TF
PD
AX
SU
BR
ST
RS
BT
HA
SC
EL
IDX
DTC P0510 CLOSED THROTTLE POSITION SWITCH
Diagnostic Procedure (Cont'd)
EC-437
Page 975 of 2395
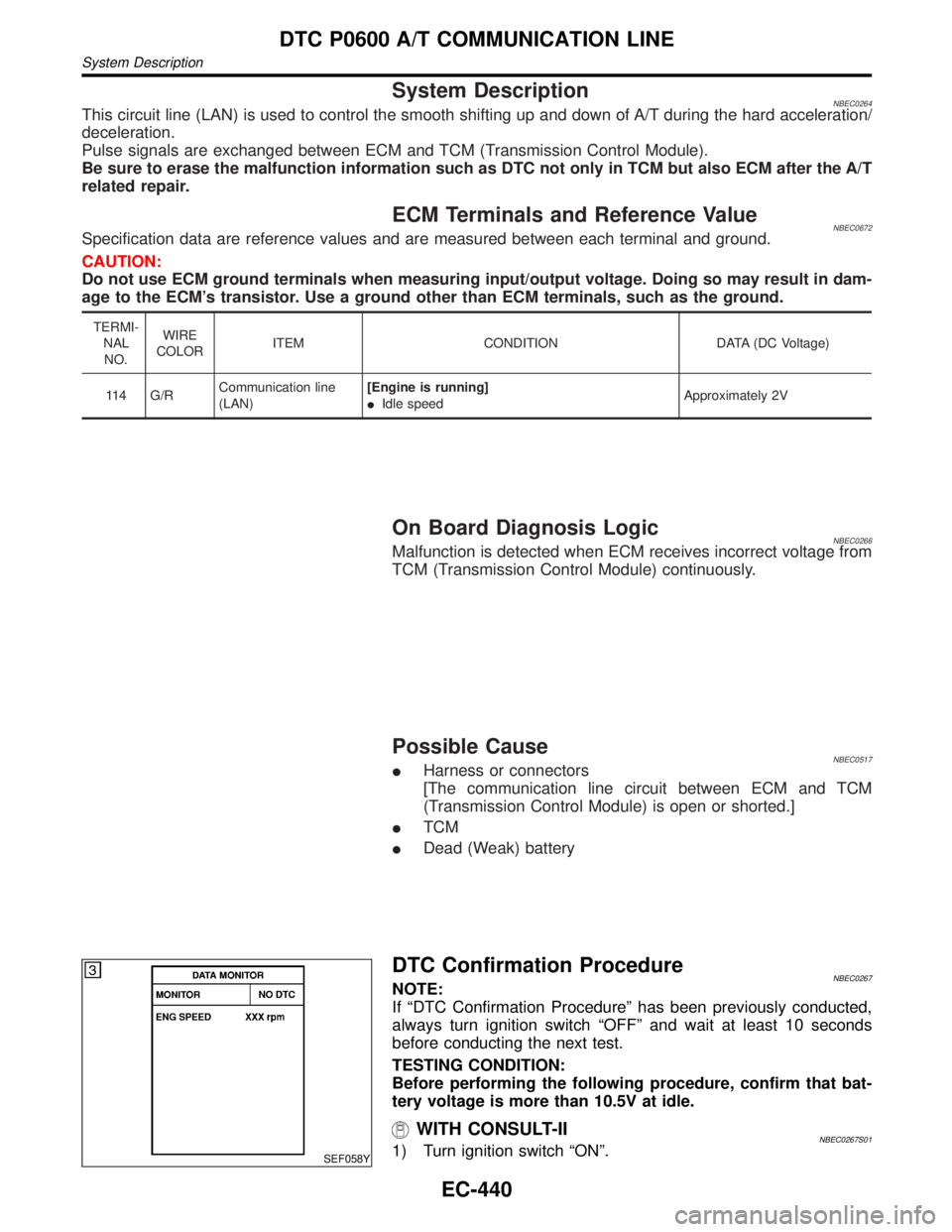
System DescriptionNBEC0264This circuit line (LAN) is used to control the smooth shifting up and down of A/T during the hard acceleration/
deceleration.
Pulse signals are exchanged between ECM and TCM (Transmission Control Module).
Be sure to erase the malfunction information such as DTC not only in TCM but also ECM after the A/T
related repair.
ECM Terminals and Reference ValueNBEC0672Specification data are reference values and are measured between each terminal and ground.
CAUTION:
Do not use ECM ground terminals when measuring input/output voltage. Doing so may result in dam-
age to the ECM's transistor. Use a ground other than ECM terminals, such as the ground.
TERMI-
NAL
NO.WIRE
COLORITEM CONDITION DATA (DC Voltage)
114 G/RCommunication line
(LAN)[Engine is running]
IIdle speedApproximately 2V
On Board Diagnosis LogicNBEC0266Malfunction is detected when ECM receives incorrect voltage from
TCM (Transmission Control Module) continuously.
Possible CauseNBEC0517IHarness or connectors
[The communication line circuit between ECM and TCM
(Transmission Control Module) is open or shorted.]
ITCM
IDead (Weak) battery
SEF058Y
DTC Confirmation ProcedureNBEC0267NOTE:
If ªDTC Confirmation Procedureº has been previously conducted,
always turn ignition switch ªOFFº and wait at least 10 seconds
before conducting the next test.
TESTING CONDITION:
Before performing the following procedure, confirm that bat-
tery voltage is more than 10.5V at idle.
WITH CONSULT-IINBEC0267S011) Turn ignition switch ªONº.
DTC P0600 A/T COMMUNICATION LINE
System Description
EC-440
Page 978 of 2395
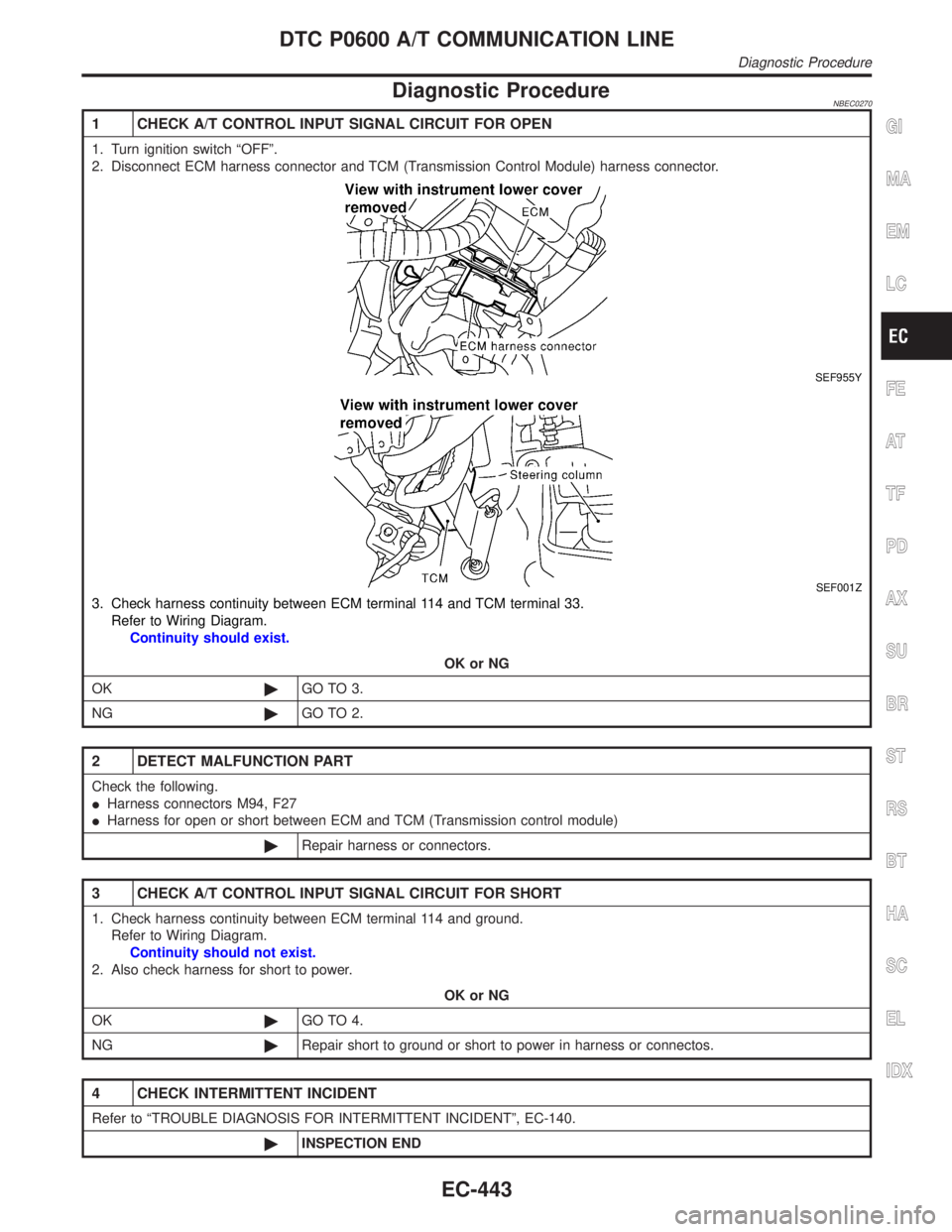
Diagnostic ProcedureNBEC0270
1 CHECK A/T CONTROL INPUT SIGNAL CIRCUIT FOR OPEN
1. Turn ignition switch ªOFFº.
2. Disconnect ECM harness connector and TCM (Transmission Control Module) harness connector.
SEF955Y
SEF001Z
3. Check harness continuity between ECM terminal 114 and TCM terminal 33.
Refer to Wiring Diagram.
Continuity should exist.
OK or NG
OK©GO TO 3.
NG©GO TO 2.
2 DETECT MALFUNCTION PART
Check the following.
IHarness connectors M94, F27
IHarness for open or short between ECM and TCM (Transmission control module)
©Repair harness or connectors.
3 CHECK A/T CONTROL INPUT SIGNAL CIRCUIT FOR SHORT
1. Check harness continuity between ECM terminal 114 and ground.
Refer to Wiring Diagram.
Continuity should not exist.
2. Also check harness for short to power.
OK or NG
OK©GO TO 4.
NG©Repair short to ground or short to power in harness or connectos.
4 CHECK INTERMITTENT INCIDENT
Refer to ªTROUBLE DIAGNOSIS FOR INTERMITTENT INCIDENTº, EC-140.
©INSPECTION END
GI
MA
EM
LC
FE
AT
TF
PD
AX
SU
BR
ST
RS
BT
HA
SC
EL
IDX
DTC P0600 A/T COMMUNICATION LINE
Diagnostic Procedure
EC-443