Connector JAGUAR X308 1998 2.G Workshop Manual
[x] Cancel search | Manufacturer: JAGUAR, Model Year: 1998, Model line: X308, Model: JAGUAR X308 1998 2.GPages: 2490, PDF Size: 69.81 MB
Page 921 of 2490
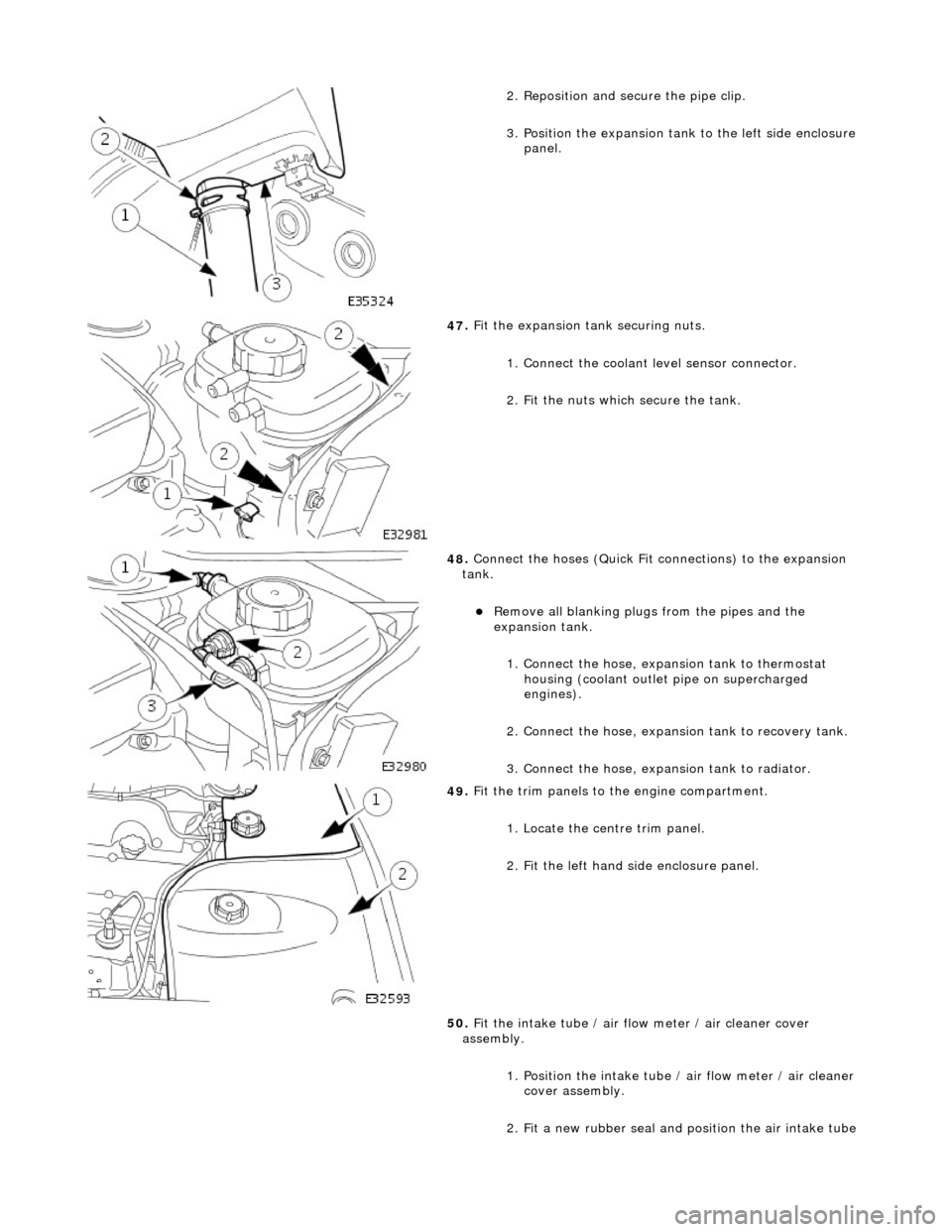
2
. Reposition and secure the pipe clip.
3. Position the expansion tank to the left side enclosure
panel.
47
.
Fit the expansion tank securing nuts.
1. Connect the coolant level sensor connector.
2. Fit the nuts which secure the tank.
48
.
Connect the hoses (Quick Fit connections) to the expansion
tank.
Remove all blanking plug s
from the pipes and the
expansion tank.
1. Connect the hose, expansion tank to thermostat housing (coolant outlet pipe on supercharged
engines).
2. Connect the hose, expansion tank to recovery tank.
3. Connect the hose, expansion tank to radiator.
49
.
Fit the trim panels to the engine compartment.
1. Locate the centre trim panel.
2. Fit the left hand side enclosure panel.
50. Fit the intake tube / air flow meter / air cleaner cover
assembly.
1. Position the intake tube / air flow meter / air cleaner
cover assembly.
2. Fit a new rubber seal and po sition the air intake tube
Page 922 of 2490
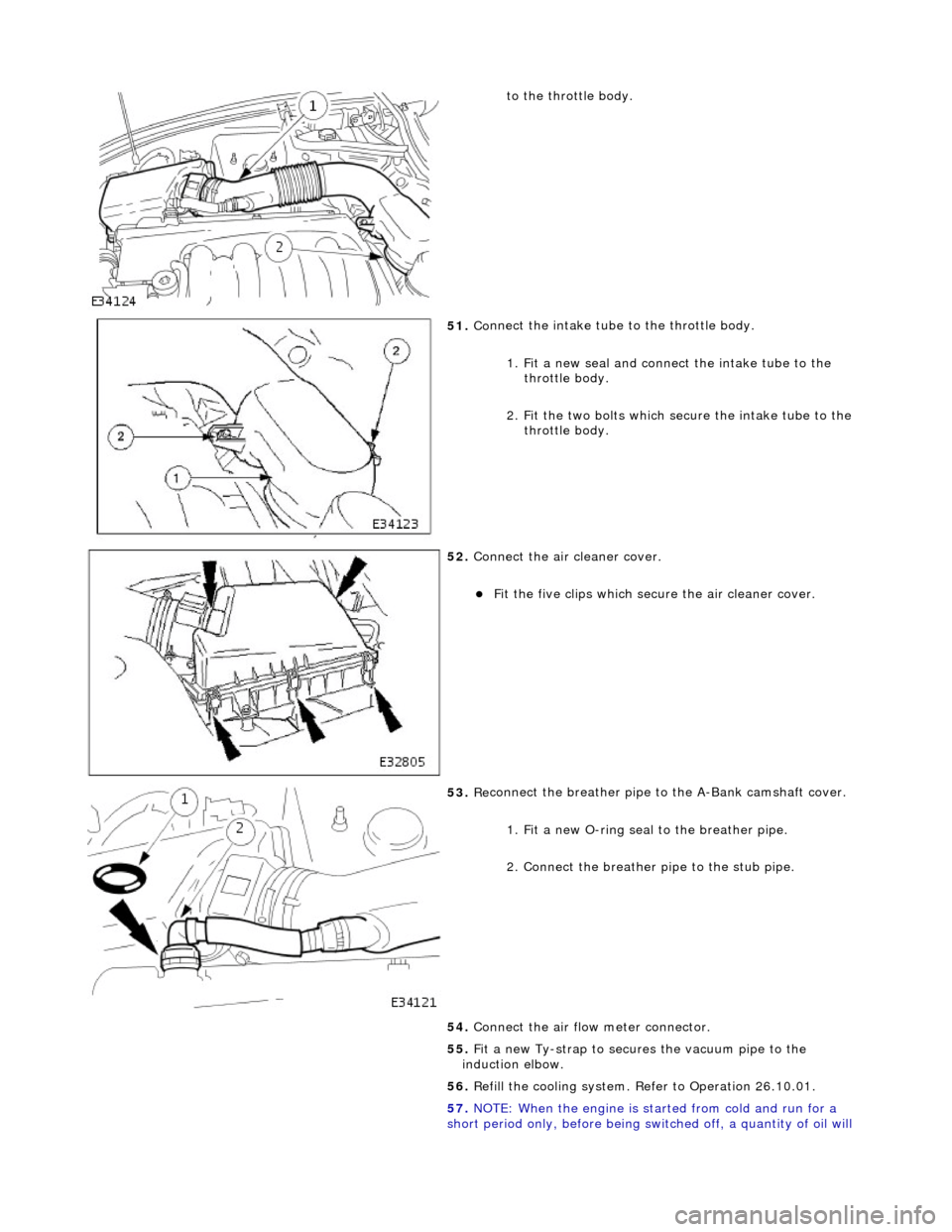
to th
e throttle body.
51 . Co
nnect the intake tube to the throttle body.
1. Fit a new seal and connect the intake tube to the throttle body.
2. Fit the two bolts which secure the intake tube to the throttle body.
52 . Conne
ct the air cleaner cover.
F
it
the five clips which secu
re the air cleaner cover.
53 . Re
connect the breather pipe to the A-Bank camshaft cover.
1. Fit a new O-ring seal to the breather pipe.
2. Connect the breather pipe to the stub pipe.
54. Connect the air flow meter connector.
55. Fit a new Ty-strap to secures the vacuum pipe to the
induction elbow.
56. Refill the cooling system. Refer to Operation 26.10.01.
57. NOTE: When the engine is star ted from cold and run for a
short period only, before being swit ched off, a quantity of oil will
Page 932 of 2490
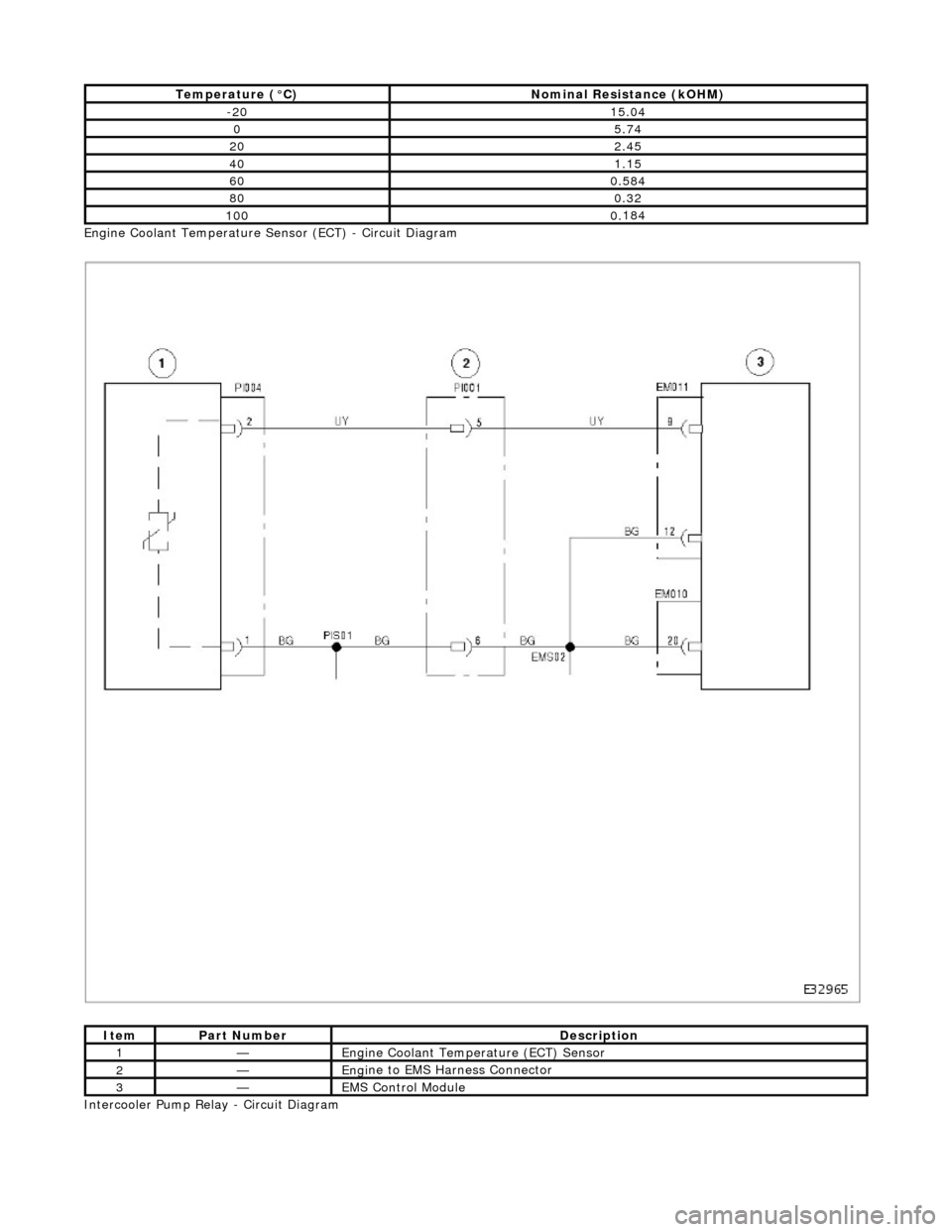
Engi
ne Coolant Temperature Sensor (ECT) - Circuit Diagram
Intercooler Pump Relay - Circuit Diagram
T emper
ature (°C)
No
mi
nal Resistance (kOHM)
-2
015 .0
4
05.7
4
202.45
401.15
600.
584
800.3
2
1000.
184
ItemPar
t
Number
De
scrip
tion
1—Eng
i
ne Coolant Temperature (ECT) Sensor
2—Eng
i
ne to EMS Harness Connector
3—EMS Con
trol Modu
le
Page 934 of 2490
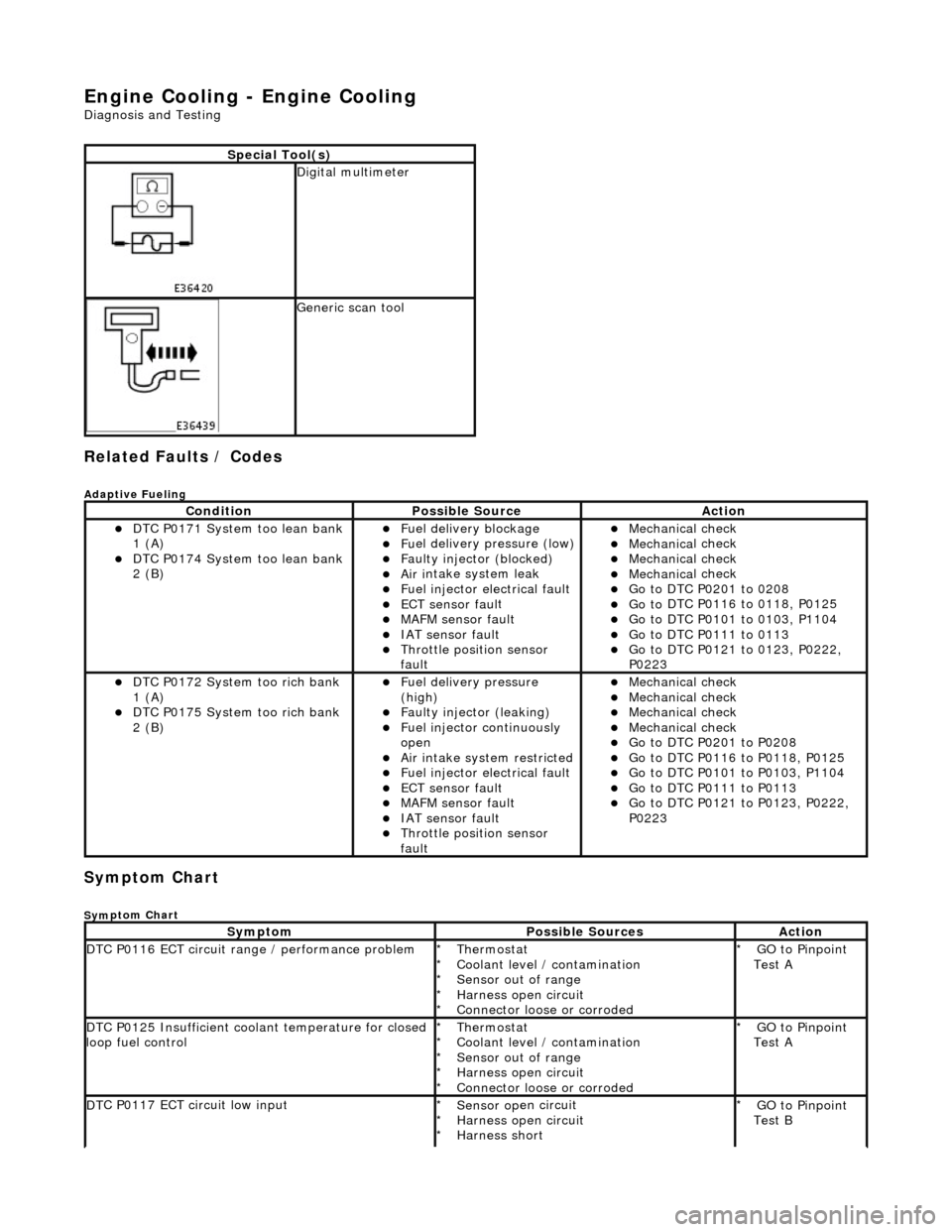
Engine Cooling - Engine Cooling
Diagn
osis and Testing
Related Faults / Codes
Adaptive
Fue
ling
Sym
p
tom Chart
Sy
m
ptom Chart
S
p
ecial Tool(s)
D
i
gital multimeter
Generi
c scan tool
Conditi
on
Possib
l
e Source
Acti
o
n
D
T
C P0171 System too lean bank
1 (A)
D T
C P0174 System too lean bank
2 (B)
Fuel delivery blockage Fu
el delivery pressure (low)
F
a
ulty injector (blocked)
Ai
r i
ntake system leak
F
u
el injector electrical fault
ECT sensor
faul
t
MAFM sensor fault IAT se
nsor fault
Thro
tt
le position sensor
fault
Mec hanica
l check
Mec
hanica
l check
Mec
hanica
l check
Mec
hanica
l check
Go t
o DTC P020
1 to 0208
Go t
o
DTC P0116 to 0118, P0125
Go t
o
DTC P0101 to 0103, P1104
Go t
o DTC P011
1 to 0113
Go t
o
DTC P0121 to 0123, P0222,
P0223
D T
C P0172 System too rich bank
1 (A)
D T
C P0175 System too rich bank
2 (B)
F u
el delivery pressure
(high)
F a
ulty injector (leaking)
F
u
el injector continuously
open
Ai r i
ntake system restricted
Fu
el injector electrical fault
ECT sensor
faul
t
MAFM sensor fault IAT sensor fault
Thrott
le position sensor
fault
Mec hanica
l check
Mec
hanica
l check
Mec
hanica
l check
Mec
hanica
l check
Go t
o DTC P020
1 to P0208
Go t
o
DTC P0116 to P0118, P0125
Go t
o
DTC P0101 to P0103, P1104
Go t
o DTC P011
1 to P0113
Go t
o
DTC P0121 to P0123, P0222,
P0223
Sy m
ptom
Possib
l
e Sources
Acti
o
n
D
T
C P0116 ECT circuit range / performance problem
Thermostat
Coo
l
ant level / contamination
Sensor out of range
Harness open circuit
Connector loose or corroded
*
*
*
*
*
GO to Pinpoint
Test A
*
D
T
C P0125 Insufficient coolant temperature for closed
loop fuel control
Thermostat
Coo l
ant level / contamination
Sensor out of range
Harness open circuit
Connector loose or corroded
*
*
*
*
*
GO to Pinpoint
Test A
*
D
T
C P0117 ECT circuit low input
Sensor o
p
en circuit
Harness open circuit
Harness short
*
*
*
GO to Pinpoint
Test B
*
Page 935 of 2490
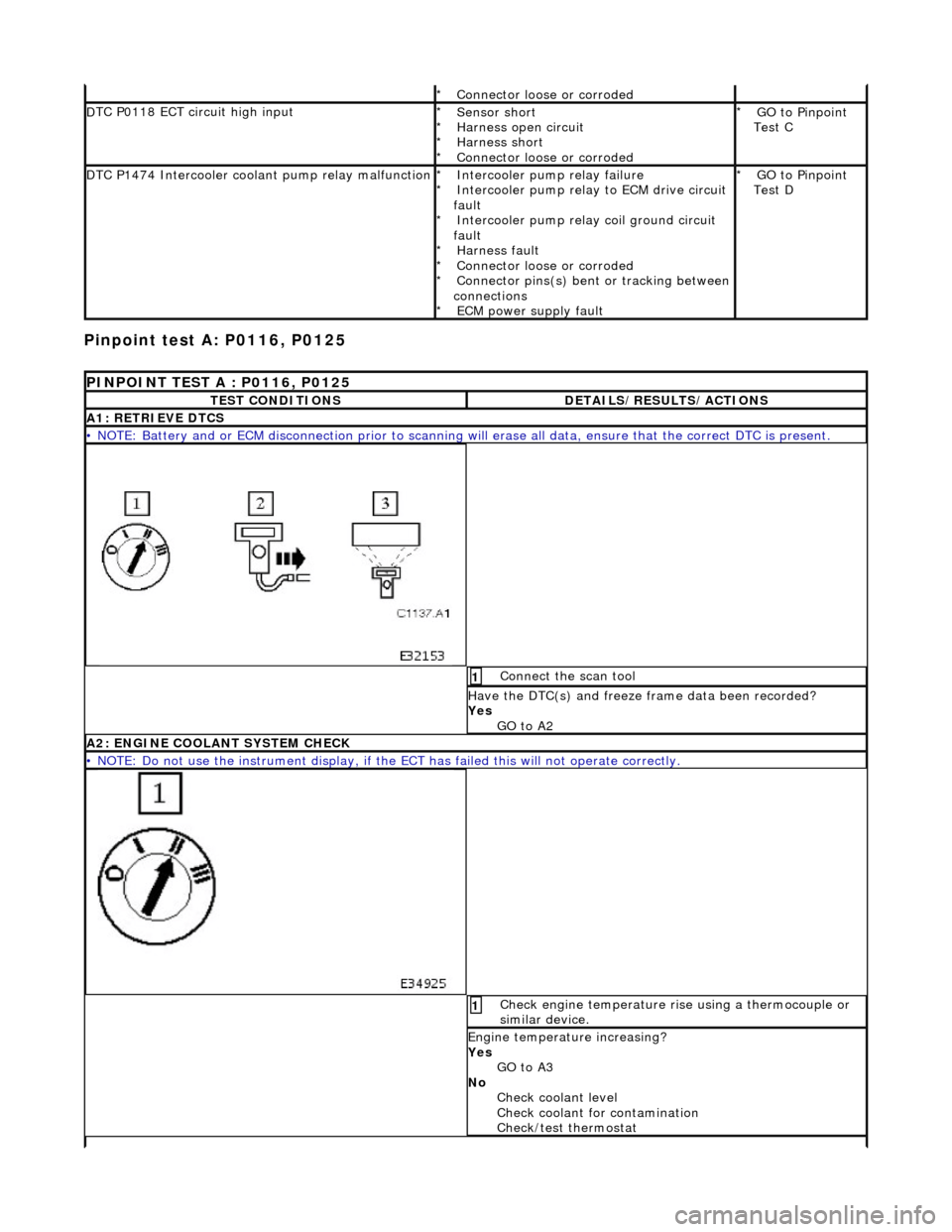
Pinpoint test
A: P0116, P0125
Connector
loose or corroded
*
D
TC P0118 ECT circuit high input
Sensor short
Harness open circui
t
Harness short
Connector loose or corroded
*
*
*
*
GO to Pinpoint
Test C
*
D
TC P1474 Intercooler coolant pump relay malfunction
Intercooler pump relay
failure
Intercooler pump relay to ECM drive circuit
fault Intercooler pump relay coil ground circuit
fault Harness fault
Connector loose or corroded
Connector pins(s) bent or tracking between
connections ECM power supply fault
*
*
*
*
*
*
*
GO to Pinpoint
Test D
*
P
INPOINT TEST A : P0116, P0125
T
EST CONDITIONS
D
ETAILS/RESULTS/ACTIONS
A1
: RETRIEVE DTCS
•
NOTE: Battery and or ECM disconnection prior to scanning wi
ll erase all data, ensure that the correct DTC is present.
Conne
ct the scan tool
1
Have the DTC(s) and fr
eeze
frame data been recorded?
Yes GO to A2
A2: ENGINE
COOLANT SYSTEM CHECK
•
NOTE: Do not use the instrument display, if th
e ECT has failed this will not operate correctly.
Chec
k engine temperature rise using a thermocouple or
similar device.
1
Engine
temperature increasing?
Yes GO to A3
No Check coolant level
Check coolant for contamination
Check/test thermostat
Page 937 of 2490
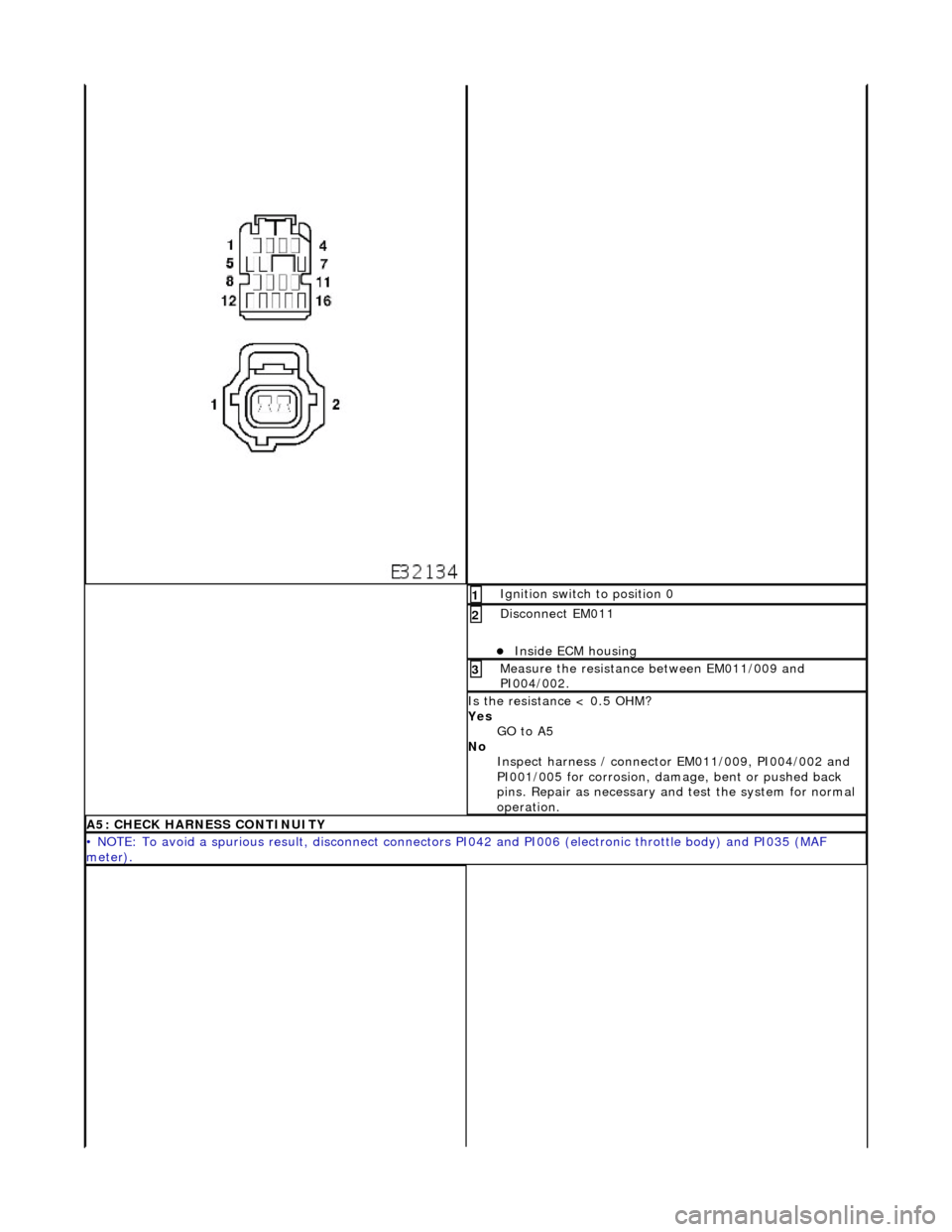
I
gnition switch to position 0
1
Di
sconnect EM011
Inside E
CM housing
2
Me
asure the resistance between EM011/009 and
PI004/002.
3
I
s the resistance < 0.5 OHM?
Yes GO to A5
No Inspect harness / connector EM011/009, PI004/002 and
PI001/005 for corrosion, damage , bent or pushed back
pins. Repair as necessary and test the system for normal
operation.
A5: CHECK
HARNESS CONTINUITY
•
NOTE: To avoid a spurious result, disconnect connectors PI042 and PI006 (electronic throttle body) and PI035 (MAF
meter).
Page 938 of 2490
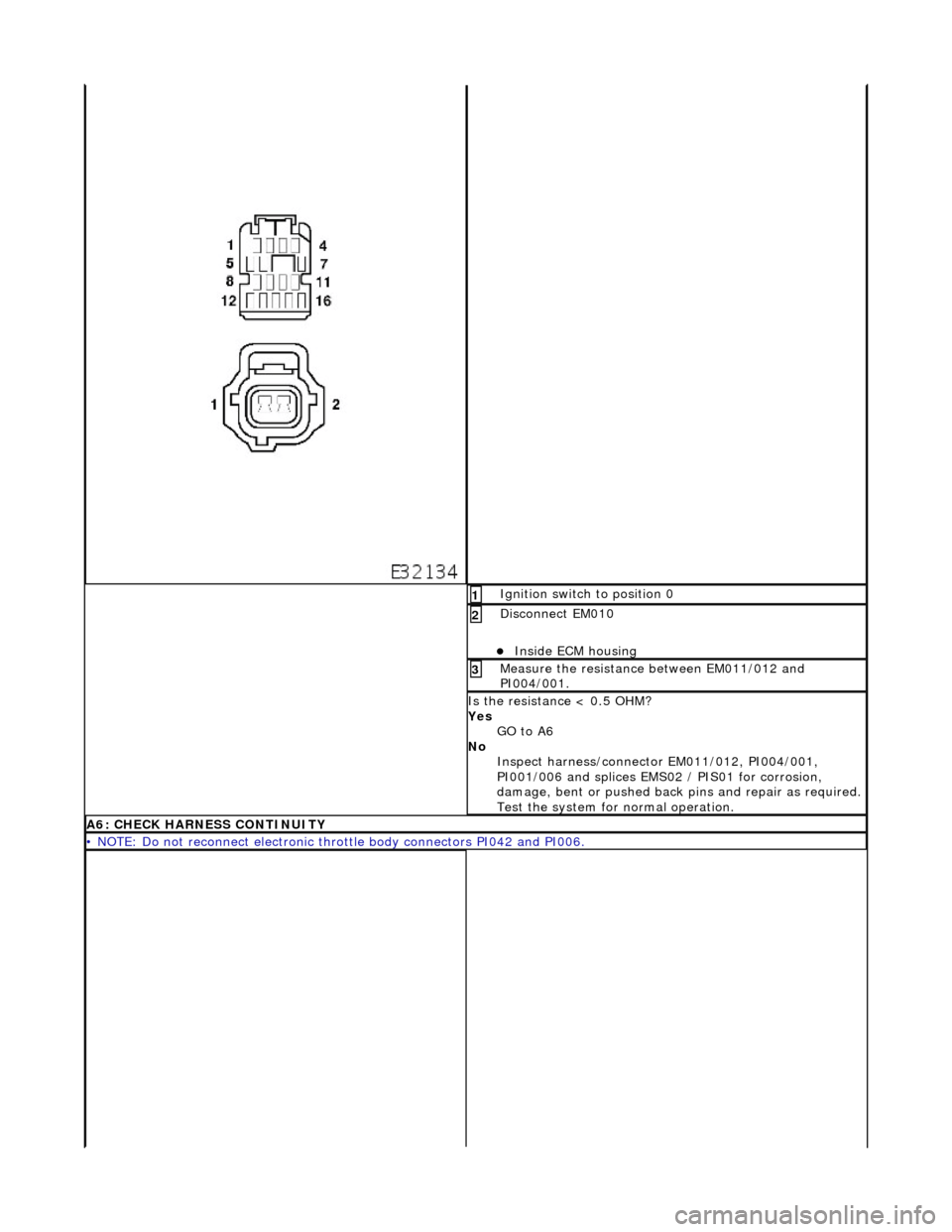
Ig
nition switch to position 0
1
Di
sc
onnect EM010
Inside E
C
M housing
2
Me
asure
the resistance between EM011/012 and
PI004/001.
3
I s
the resistance < 0.5 OHM?
Yes GO to A6
No Inspect harness/connector EM011/012, PI004/001,
PI001/006 and splices EMS02 / PIS01 for corrosion,
damage, bent or pushed back pins and repair as required.
Test the system for normal operation.
A6: CHECK HARNESS
CONTINUITY
•
NOTE
: Do not reconnect electronic thro
ttle body connectors PI042 and PI006.
Page 939 of 2490
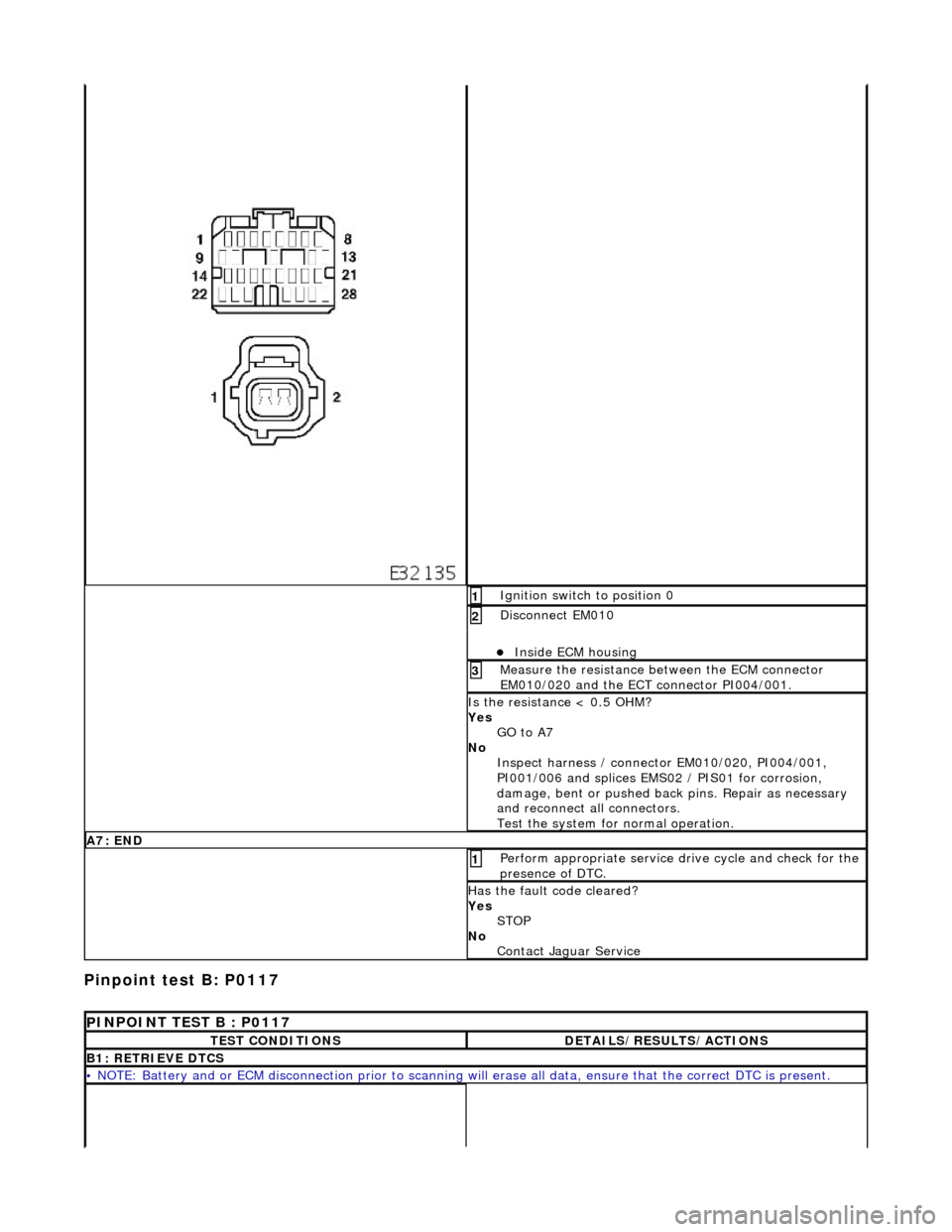
Pinpoint test
B: P0117
I
gnition switch to position 0
1
Di
sconnect EM010
Inside E
CM housing
2
Meas
ure the resistance between the ECM connector
EM010/020 and the ECT connector PI004/001.
3
I
s the resistance < 0.5 OHM?
Yes GO to A7
No Inspect harness / connector EM010/020, PI004/001,
PI001/006 and splices EMS02 / PIS01 for corrosion,
damage, bent or pushed back pins. Repair as necessary
and reconnect all connectors.
Test the system for normal operation.
A7
: END
Perform
appropriate service drive cycle and check for the
presence of DTC.
1
Has
the fault code cleared?
Yes STOP
No Contact Jaguar Service
P
INPOINT TEST B : P0117
T
EST CONDITIONS
D
ETAILS/RESULTS/ACTIONS
B1
: RETRIEVE DTCS
•
NOTE: Battery and or ECM disconnection prior to scanning wi
ll erase all data, ensure that the correct DTC is present.
Page 941 of 2490
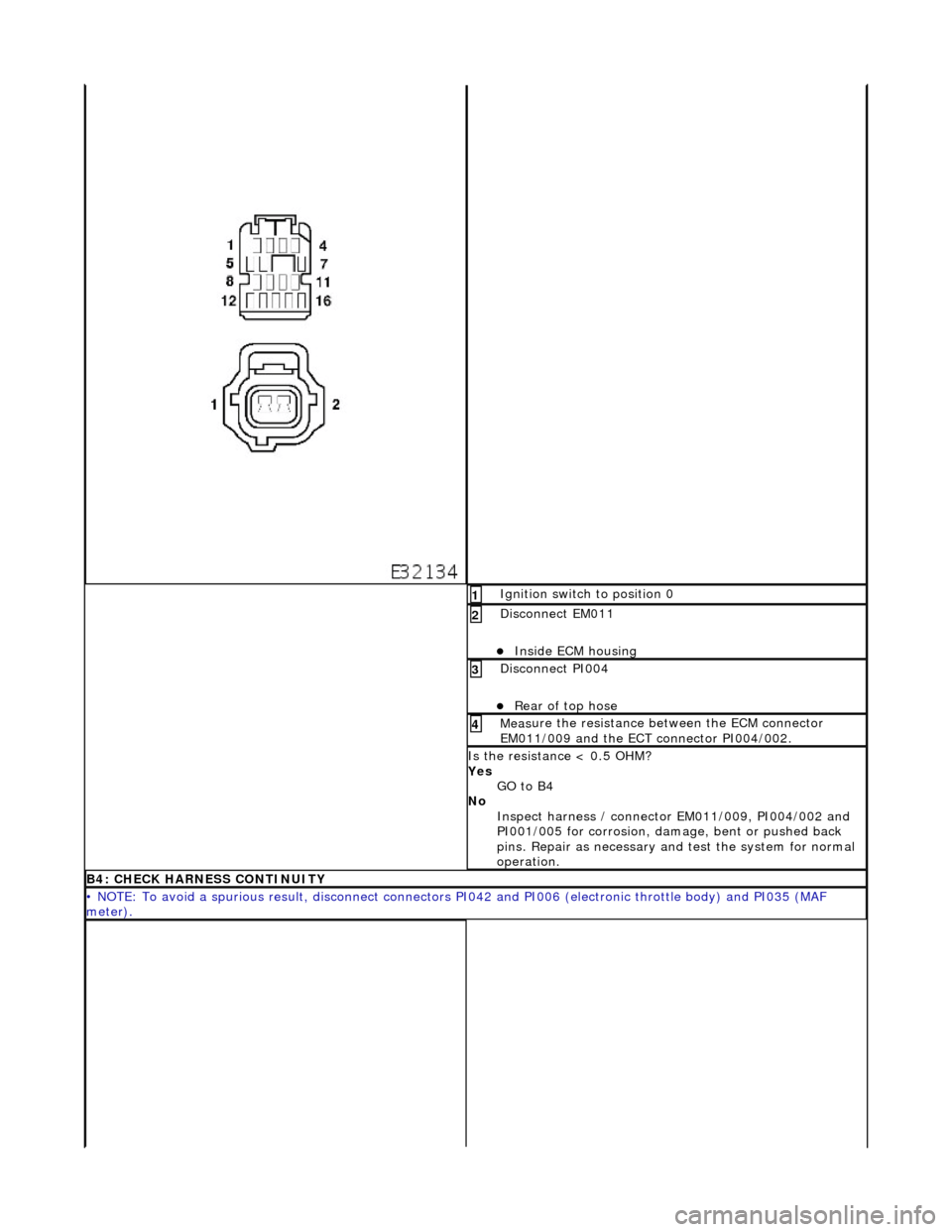
I
gnition switch to position 0
1
Di
sconnect EM011
Inside E
CM housing
2
D
isconnect PI004
Re
ar of top hose
3
Meas
ure the resistance between the ECM connector
EM011/009 and the ECT connector PI004/002.
4
I
s the resistance < 0.5 OHM?
Yes GO to B4
No Inspect harness / connector EM011/009, PI004/002 and
PI001/005 for corrosion, damage , bent or pushed back
pins. Repair as necessary and test the system for normal
operation.
B4: CHECK
HARNESS CONTINUITY
•
NOTE: To avoid a spurious result, disconnect connectors PI042 and PI006 (electronic throttle body) and PI035 (MAF
meter).
Page 942 of 2490
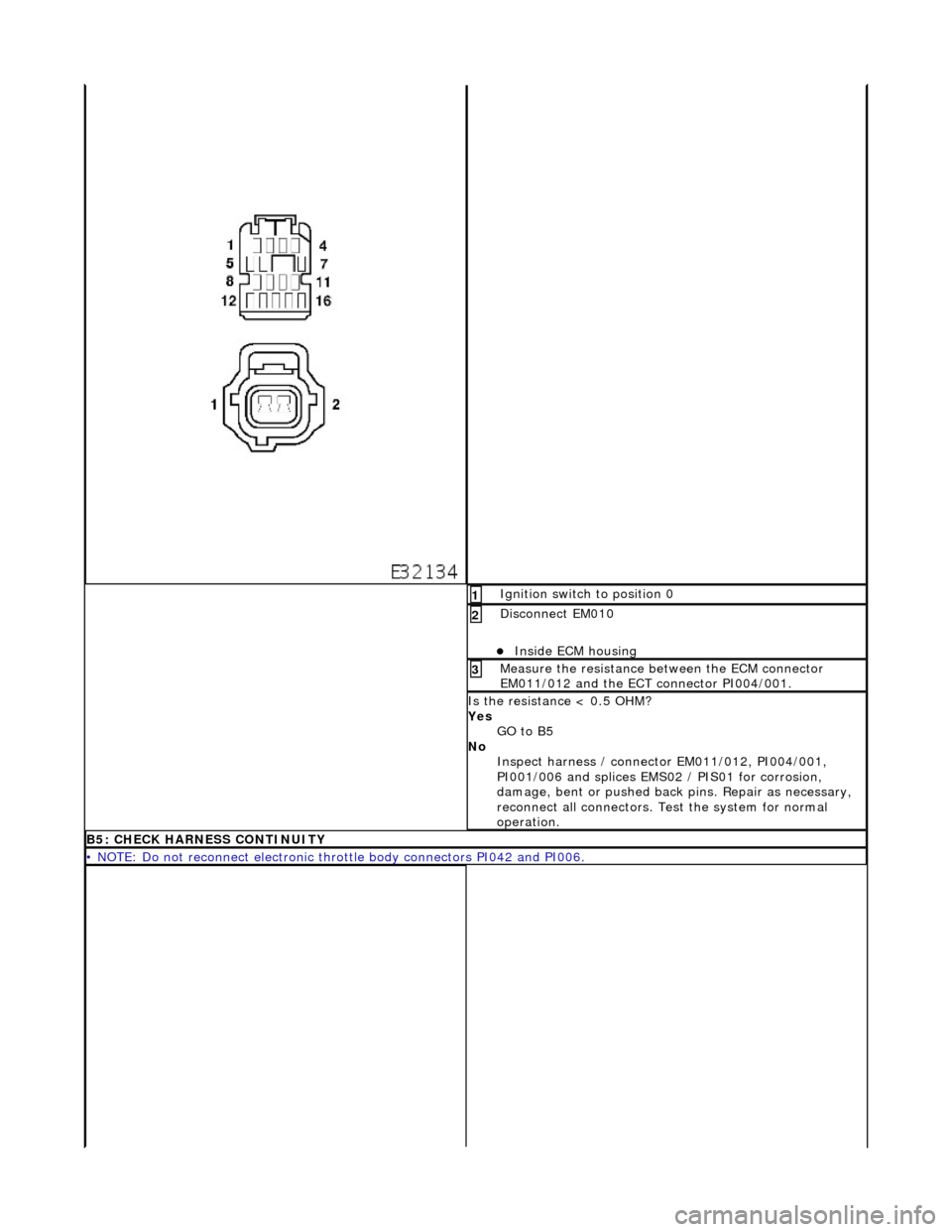
Ig
nition switch to position 0
1
Di
sc
onnect EM010
Inside E
C
M housing
2
Meas
ure t
he resistance between the ECM connector
EM011/012 and the ECT connector PI004/001.
3
I s
the resistance < 0.5 OHM?
Yes GO to B5
No Inspect harness / connector EM011/012, PI004/001,
PI001/006 and splices EMS02 / PIS01 for corrosion,
damage, bent or pushed back pins. Repair as necessary,
reconnect all connectors. Te st the system for normal
operation.
B5: CHECK HARNESS
CONTINUITY
•
NOTE
: Do not reconnect electronic thro
ttle body connectors PI042 and PI006.