JAGUAR XFR 2010 1.G Workshop Manual
Manufacturer: JAGUAR, Model Year: 2010, Model line: XFR, Model: JAGUAR XFR 2010 1.GPages: 3039, PDF Size: 58.49 MB
Page 101 of 3039
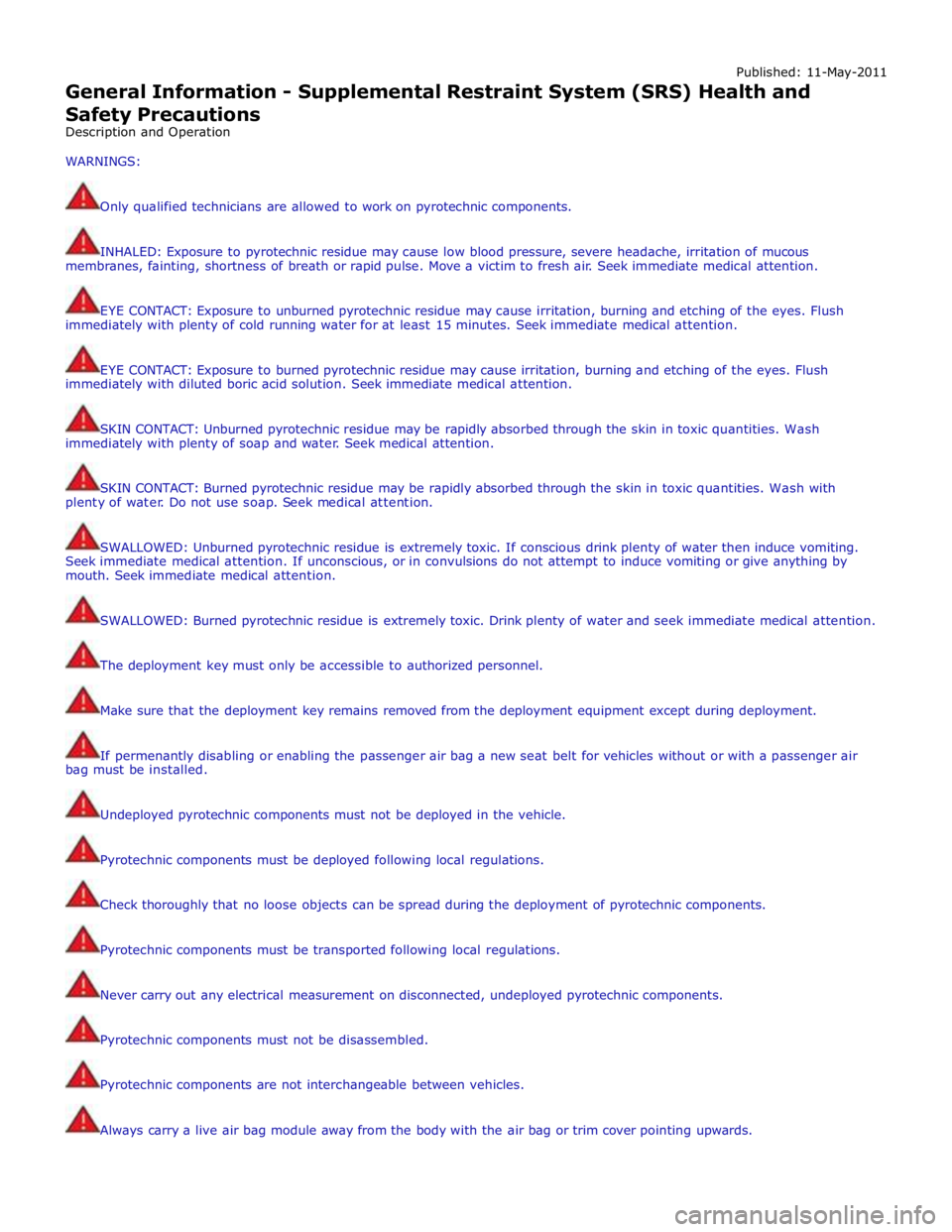
Published: 11-May-2011
General Information - Supplemental Restraint System (SRS) Health and
Safety Precautions
Description and Operation
WARNINGS:
Only qualified technicians are allowed to work on pyrotechnic components.
INHALED: Exposure to pyrotechnic residue may cause low blood pressure, severe headache, irritation of mucous
membranes, fainting, shortness of breath or rapid pulse. Move a victim to fresh air. Seek immediate medical attention.
EYE CONTACT: Exposure to unburned pyrotechnic residue may cause irritation, burning and etching of the eyes. Flush
immediately with plenty of cold running water for at least 15 minutes. Seek immediate medical attention.
EYE CONTACT: Exposure to burned pyrotechnic residue may cause irritation, burning and etching of the eyes. Flush
immediately with diluted boric acid solution. Seek immediate medical attention.
SKIN CONTACT: Unburned pyrotechnic residue may be rapidly absorbed through the skin in toxic quantities. Wash
immediately with plenty of soap and water. Seek medical attention.
SKIN CONTACT: Burned pyrotechnic residue may be rapidly absorbed through the skin in toxic quantities. Wash with
plenty of water. Do not use soap. Seek medical attention.
SWALLOWED: Unburned pyrotechnic residue is extremely toxic. If conscious drink plenty of water then induce vomiting.
Seek immediate medical attention. If unconscious, or in convulsions do not attempt to induce vomiting or give anything by
mouth. Seek immediate medical attention.
SWALLOWED: Burned pyrotechnic residue is extremely toxic. Drink plenty of water and seek immediate medical attention.
The deployment key must only be accessible to authorized personnel.
Make sure that the deployment key remains removed from the deployment equipment except during deployment.
If permenantly disabling or enabling the passenger air bag a new seat belt for vehicles without or with a passenger air
bag must be installed.
Undeployed pyrotechnic components must not be deployed in the vehicle.
Pyrotechnic components must be deployed following local regulations.
Check thoroughly that no loose objects can be spread during the deployment of pyrotechnic components.
Pyrotechnic components must be transported following local regulations.
Never carry out any electrical measurement on disconnected, undeployed pyrotechnic components.
Pyrotechnic components must not be disassembled.
Pyrotechnic components are not interchangeable between vehicles.
Always carry a live air bag module away from the body with the air bag or trim cover pointing upwards.
Page 102 of 3039
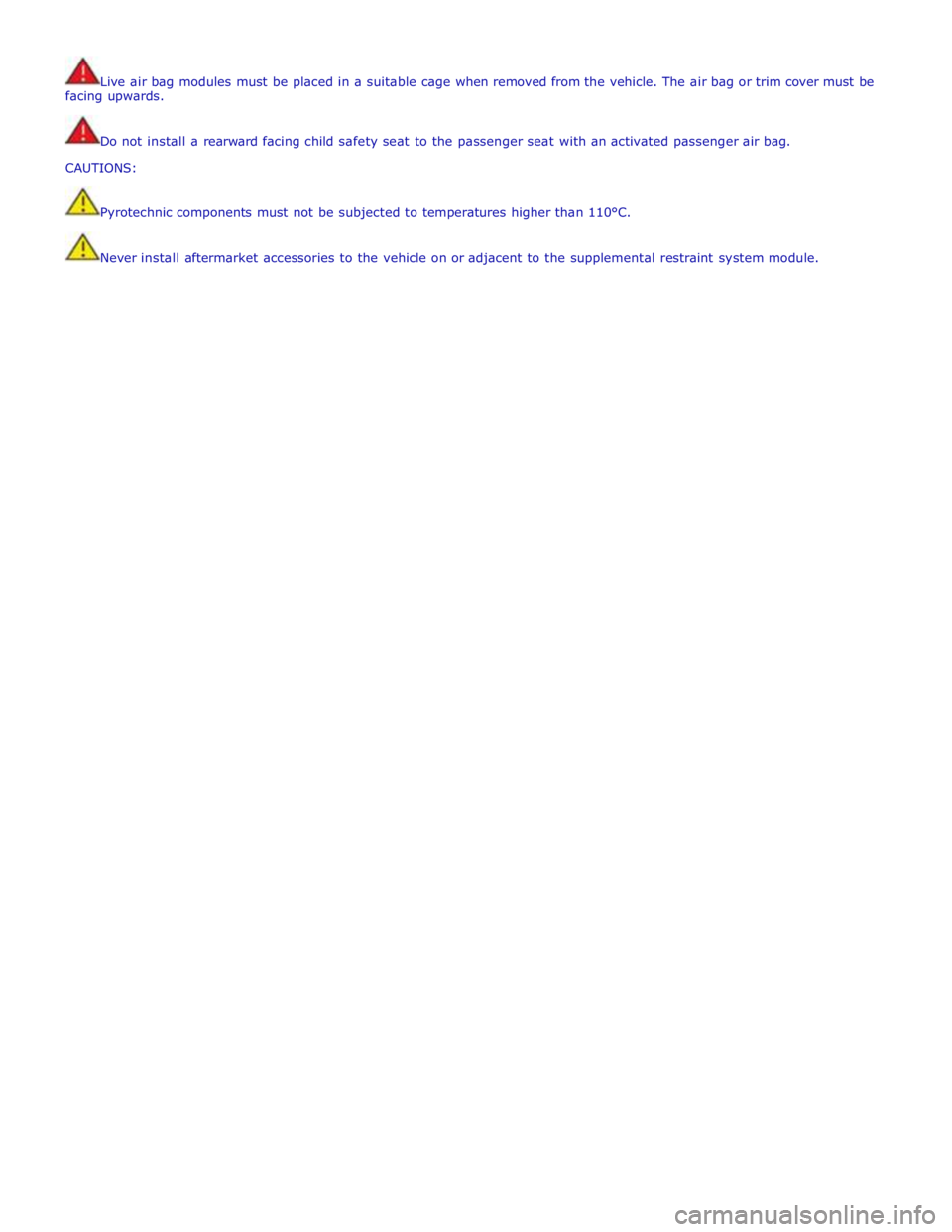
Live air bag modules must be placed in a suitable cage when removed from the vehicle. The air bag or trim cover must be
facing upwards.
Do not install a rearward facing child safety seat to the passenger seat with an activated passenger air bag.
CAUTIONS:
Pyrotechnic components must not be subjected to temperatures higher than 110°C.
Never install aftermarket accessories to the vehicle on or adjacent to the supplemental restraint system module.
Page 103 of 3039
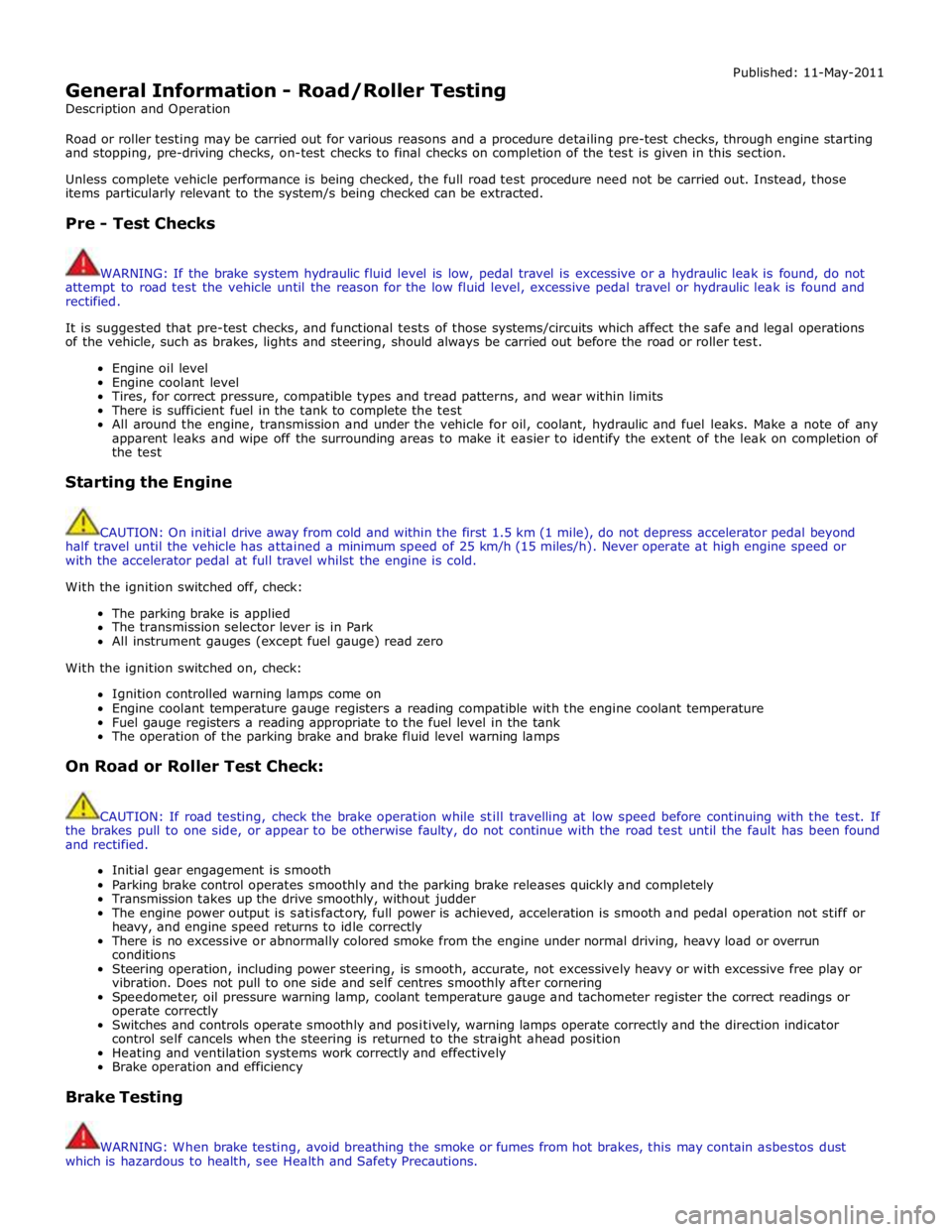
General Information - Road/Roller Testing
Description and Operation Published: 11-May-2011
Road or roller testing may be carried out for various reasons and a procedure detailing pre-test checks, through engine starting
and stopping, pre-driving checks, on-test checks to final checks on completion of the test is given in this section.
Unless complete vehicle performance is being checked, the full road test procedure need not be carried out. Instead, those
items particularly relevant to the system/s being checked can be extracted.
Pre - Test Checks
WARNING: If the brake system hydraulic fluid level is low, pedal travel is excessive or a hydraulic leak is found, do not
attempt to road test the vehicle until the reason for the low fluid level, excessive pedal travel or hydraulic leak is found and
rectified.
It is suggested that pre-test checks, and functional tests of those systems/circuits which affect the safe and legal operations
of the vehicle, such as brakes, lights and steering, should always be carried out before the road or roller test.
Engine oil level
Engine coolant level
Tires, for correct pressure, compatible types and tread patterns, and wear within limits
There is sufficient fuel in the tank to complete the test
All around the engine, transmission and under the vehicle for oil, coolant, hydraulic and fuel leaks. Make a note of any
apparent leaks and wipe off the surrounding areas to make it easier to identify the extent of the leak on completion of
the test
Starting the Engine
CAUTION: On initial drive away from cold and within the first 1.5 km (1 mile), do not depress accelerator pedal beyond
half travel until the vehicle has attained a minimum speed of 25 km/h (15 miles/h). Never operate at high engine speed or
with the accelerator pedal at full travel whilst the engine is cold.
With the ignition switched off, check:
The parking brake is applied
The transmission selector lever is in Park
All instrument gauges (except fuel gauge) read zero
With the ignition switched on, check:
Ignition controlled warning lamps come on
Engine coolant temperature gauge registers a reading compatible with the engine coolant temperature
Fuel gauge registers a reading appropriate to the fuel level in the tank
The operation of the parking brake and brake fluid level warning lamps
On Road or Roller Test Check:
CAUTION: If road testing, check the brake operation while still travelling at low speed before continuing with the test. If
the brakes pull to one side, or appear to be otherwise faulty, do not continue with the road test until the fault has been found
and rectified.
Initial gear engagement is smooth
Parking brake control operates smoothly and the parking brake releases quickly and completely
Transmission takes up the drive smoothly, without judder
The engine power output is satisfactory, full power is achieved, acceleration is smooth and pedal operation not stiff or
heavy, and engine speed returns to idle correctly
There is no excessive or abnormally colored smoke from the engine under normal driving, heavy load or overrun
conditions
Steering operation, including power steering, is smooth, accurate, not excessively heavy or with excessive free play or
vibration. Does not pull to one side and self centres smoothly after cornering
Speedometer, oil pressure warning lamp, coolant temperature gauge and tachometer register the correct readings or
operate correctly
Switches and controls operate smoothly and positively, warning lamps operate correctly and the direction indicator
control self cancels when the steering is returned to the straight ahead position
Heating and ventilation systems work correctly and effectively
Brake operation and efficiency
Brake Testing
WARNING: When brake testing, avoid breathing the smoke or fumes from hot brakes, this may contain asbestos dust
which is hazardous to health, see Health and Safety Precautions.
Page 104 of 3039
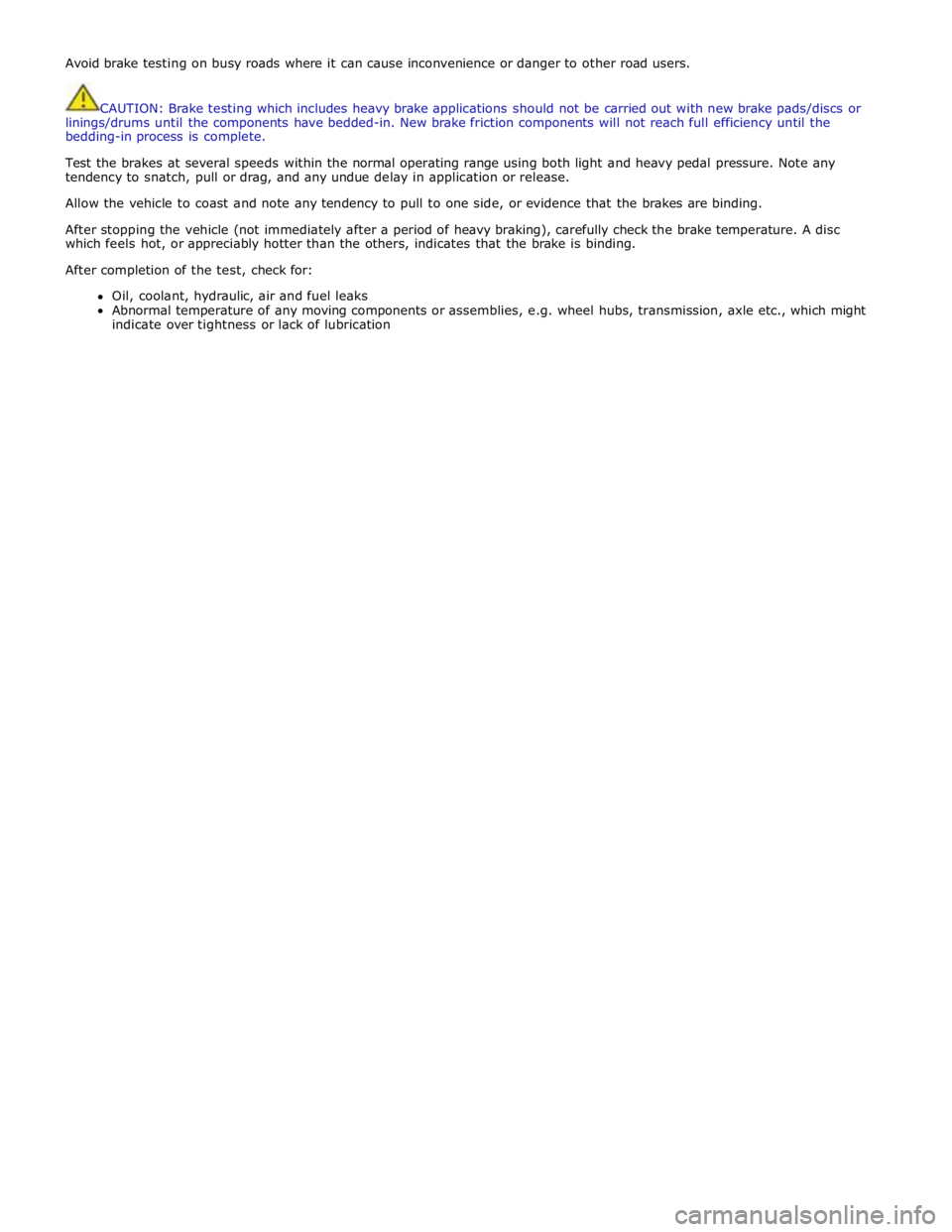
Avoid brake testing on busy roads where it can cause inconvenience or danger to other road users.
CAUTION: Brake testing which includes heavy brake applications should not be carried out with new brake pads/discs or
linings/drums until the components have bedded-in. New brake friction components will not reach full efficiency until the
bedding-in process is complete.
Test the brakes at several speeds within the normal operating range using both light and heavy pedal pressure. Note any
tendency to snatch, pull or drag, and any undue delay in application or release.
Allow the vehicle to coast and note any tendency to pull to one side, or evidence that the brakes are binding.
After stopping the vehicle (not immediately after a period of heavy braking), carefully check the brake temperature. A disc
which feels hot, or appreciably hotter than the others, indicates that the brake is binding.
After completion of the test, check for:
Oil, coolant, hydraulic, air and fuel leaks
Abnormal temperature of any moving components or assemblies, e.g. wheel hubs, transmission, axle etc., which might
indicate over tightness or lack of lubrication
Page 105 of 3039
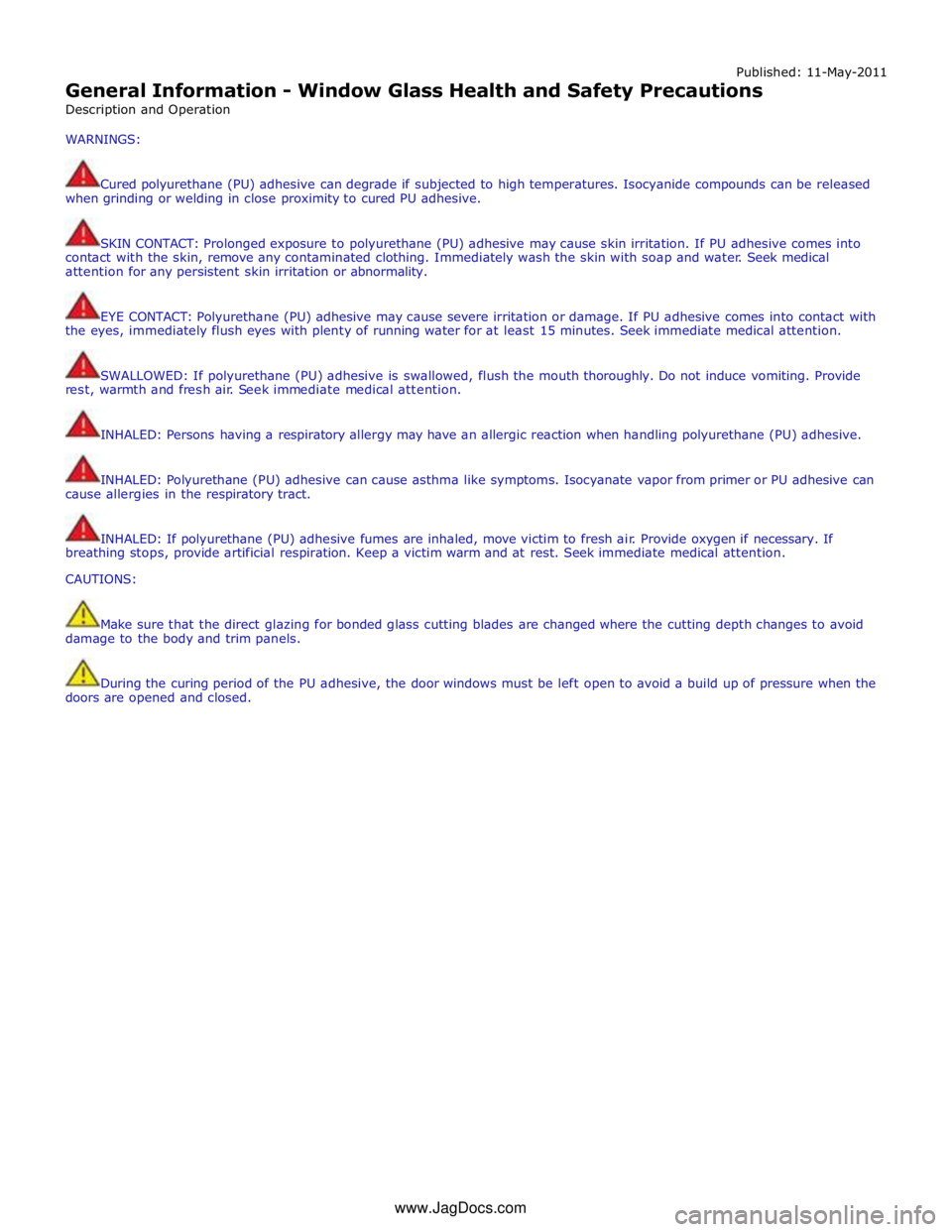
Published: 11-May-2011
General Information - Window Glass Health and Safety Precautions
Description and Operation
WARNINGS:
Cured polyurethane (PU) adhesive can degrade if subjected to high temperatures. Isocyanide compounds can be released
when grinding or welding in close proximity to cured PU adhesive.
SKIN CONTACT: Prolonged exposure to polyurethane (PU) adhesive may cause skin irritation. If PU adhesive comes into
contact with the skin, remove any contaminated clothing. Immediately wash the skin with soap and water. Seek medical
attention for any persistent skin irritation or abnormality.
EYE CONTACT: Polyurethane (PU) adhesive may cause severe irritation or damage. If PU adhesive comes into contact with
the eyes, immediately flush eyes with plenty of running water for at least 15 minutes. Seek immediate medical attention.
SWALLOWED: If polyurethane (PU) adhesive is swallowed, flush the mouth thoroughly. Do not induce vomiting. Provide
rest, warmth and fresh air. Seek immediate medical attention.
INHALED: Persons having a respiratory allergy may have an allergic reaction when handling polyurethane (PU) adhesive.
INHALED: Polyurethane (PU) adhesive can cause asthma like symptoms. Isocyanate vapor from primer or PU adhesive can
cause allergies in the respiratory tract.
INHALED: If polyurethane (PU) adhesive fumes are inhaled, move victim to fresh air. Provide oxygen if necessary. If
breathing stops, provide artificial respiration. Keep a victim warm and at rest. Seek immediate medical attention.
CAUTIONS:
Make sure that the direct glazing for bonded glass cutting blades are changed where the cutting depth changes to avoid
damage to the body and trim panels.
During the curing period of the PU adhesive, the door windows must be left open to avoid a build up of pressure when the
doors are opened and closed.
www.JagDocs.com
Page 106 of 3039
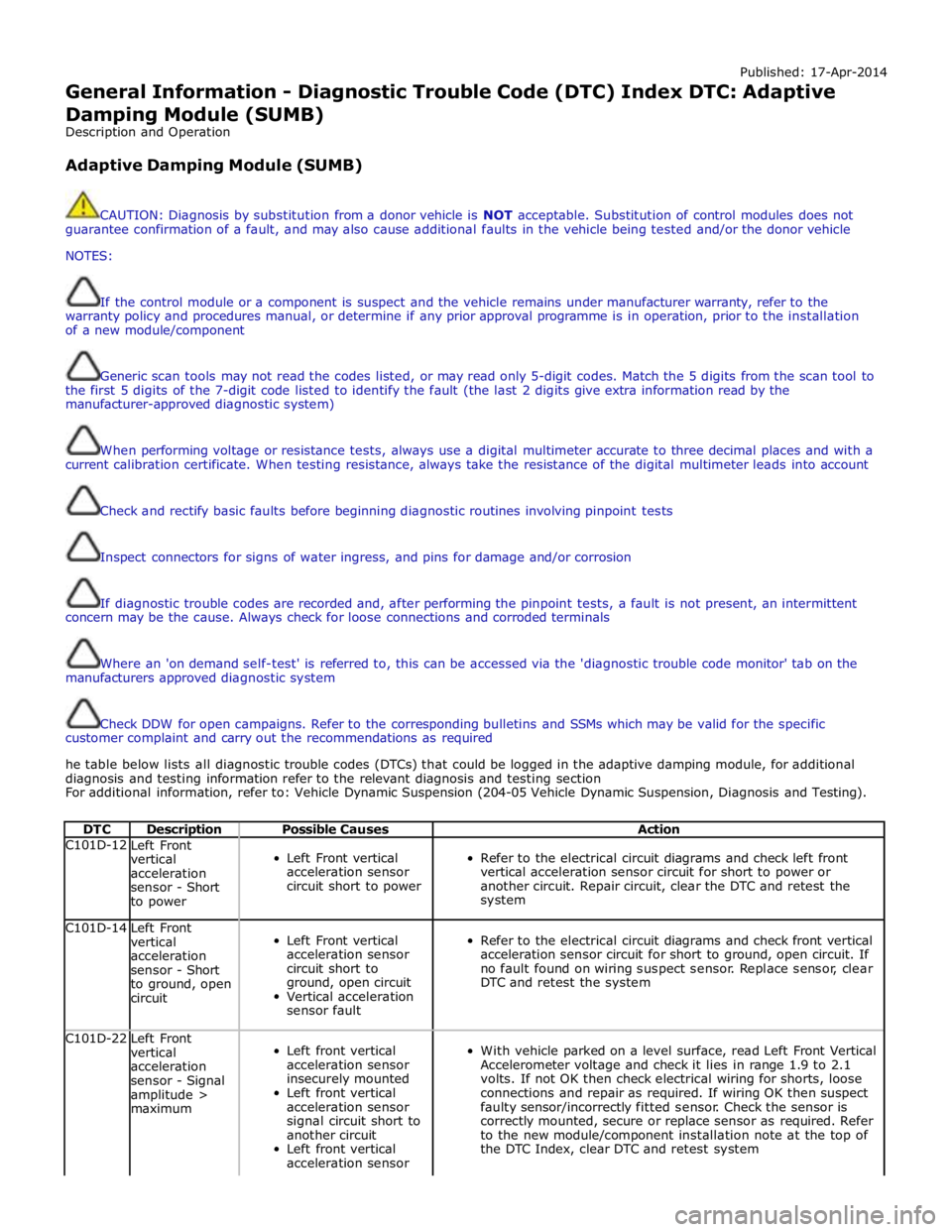
Published: 17-Apr-2014
General Information - Diagnostic Trouble Code (DTC) Index DTC: Adaptive
Damping Module (SUMB)
Description and Operation
Adaptive Damping Module (SUMB)
CAUTION: Diagnosis by substitution from a donor vehicle is NOT acceptable. Substitution of control modules does not
guarantee confirmation of a fault, and may also cause additional faults in the vehicle being tested and/or the donor vehicle
NOTES:
If the control module or a component is suspect and the vehicle remains under manufacturer warranty, refer to the
warranty policy and procedures manual, or determine if any prior approval programme is in operation, prior to the installation
of a new module/component
Generic scan tools may not read the codes listed, or may read only 5-digit codes. Match the 5 digits from the scan tool to
the first 5 digits of the 7-digit code listed to identify the fault (the last 2 digits give extra information read by the
manufacturer-approved diagnostic system)
When performing voltage or resistance tests, always use a digital multimeter accurate to three decimal places and with a
current calibration certificate. When testing resistance, always take the resistance of the digital multimeter leads into account
Check and rectify basic faults before beginning diagnostic routines involving pinpoint tests
Inspect connectors for signs of water ingress, and pins for damage and/or corrosion
If diagnostic trouble codes are recorded and, after performing the pinpoint tests, a fault is not present, an intermittent
concern may be the cause. Always check for loose connections and corroded terminals
Where an 'on demand self-test' is referred to, this can be accessed via the 'diagnostic trouble code monitor' tab on the
manufacturers approved diagnostic system
Check DDW for open campaigns. Refer to the corresponding bulletins and SSMs which may be valid for the specific
customer complaint and carry out the recommendations as required
he table below lists all diagnostic trouble codes (DTCs) that could be logged in the adaptive damping module, for additional
diagnosis and testing information refer to the relevant diagnosis and testing section
For additional information, refer to: Vehicle Dynamic Suspension (204-05 Vehicle Dynamic Suspension, Diagnosis and Testing).
DTC Description Possible Causes Action C101D-12
Left Front
vertical
acceleration
sensor - Short
to power
Left Front vertical
acceleration sensor
circuit short to power
Refer to the electrical circuit diagrams and check left front
vertical acceleration sensor circuit for short to power or
another circuit. Repair circuit, clear the DTC and retest the
system C101D-14
Left Front
vertical
acceleration
sensor - Short
to ground, open
circuit
Left Front vertical
acceleration sensor
circuit short to
ground, open circuit
Vertical acceleration
sensor fault
Refer to the electrical circuit diagrams and check front vertical
acceleration sensor circuit for short to ground, open circuit. If
no fault found on wiring suspect sensor. Replace sensor, clear
DTC and retest the system C101D-22
Left Front
vertical
acceleration
sensor - Signal
amplitude >
maximum
Left front vertical
acceleration sensor
insecurely mounted
Left front vertical
acceleration sensor
signal circuit short to
another circuit
Left front vertical
acceleration sensor
With vehicle parked on a level surface, read Left Front Vertical
Accelerometer voltage and check it lies in range 1.9 to 2.1
volts. If not OK then check electrical wiring for shorts, loose
connections and repair as required. If wiring OK then suspect
faulty sensor/incorrectly fitted sensor. Check the sensor is
correctly mounted, secure or replace sensor as required. Refer
to the new module/component installation note at the top of
the DTC Index, clear DTC and retest system
Page 107 of 3039
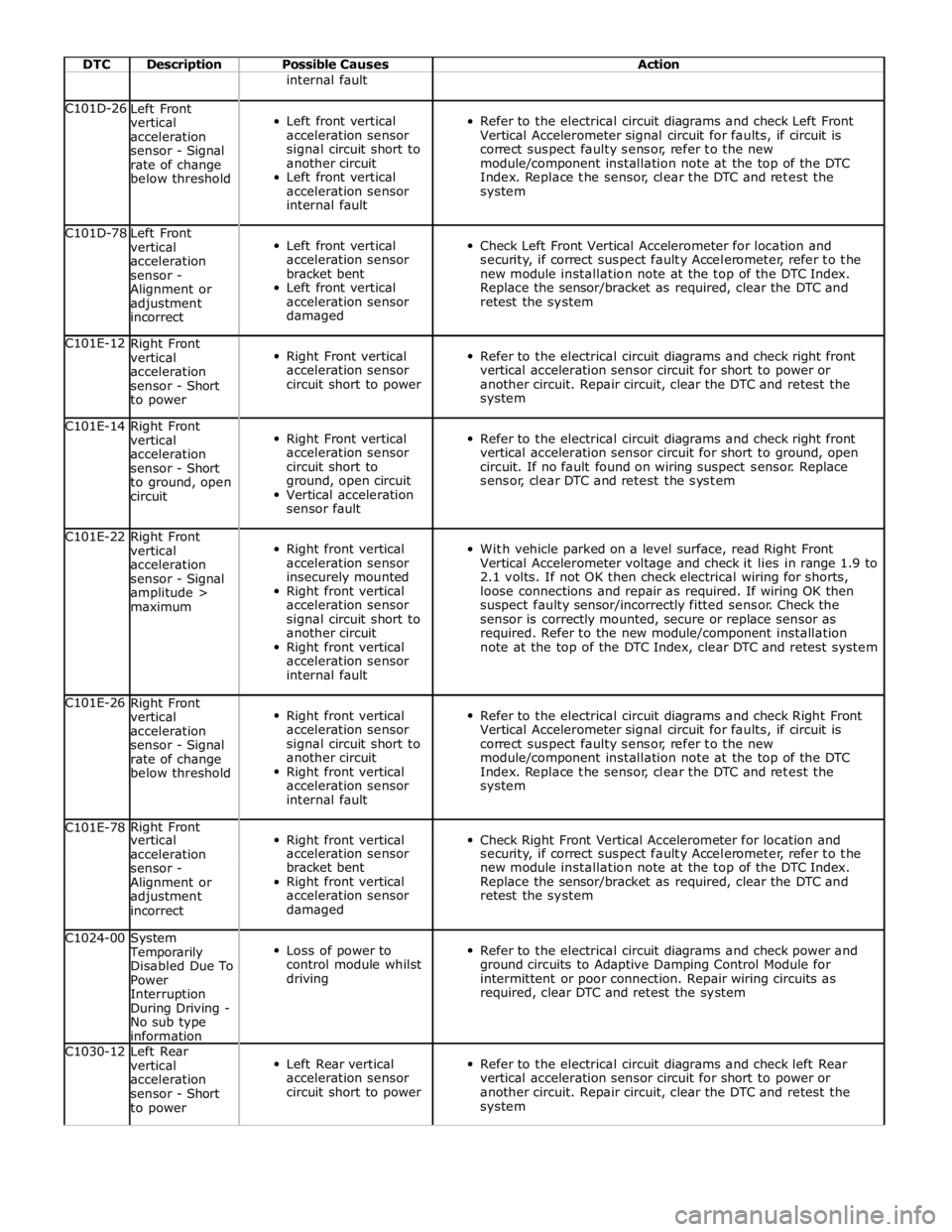
DTC Description Possible Causes Action internal fault
C101D-26
Left Front
vertical
acceleration
sensor - Signal
rate of change
below threshold
Left front vertical
acceleration sensor
signal circuit short to
another circuit
Left front vertical
acceleration sensor
internal fault
Refer to the electrical circuit diagrams and check Left Front
Vertical Accelerometer signal circuit for faults, if circuit is
correct suspect faulty sensor, refer to the new
module/component installation note at the top of the DTC
Index. Replace the sensor, clear the DTC and retest the
system C101D-78
Left Front
vertical
acceleration
sensor -
Alignment or
adjustment
incorrect
Left front vertical
acceleration sensor
bracket bent
Left front vertical
acceleration sensor
damaged
Check Left Front Vertical Accelerometer for location and
security, if correct suspect faulty Accelerometer, refer to the
new module installation note at the top of the DTC Index.
Replace the sensor/bracket as required, clear the DTC and
retest the system C101E-12
Right Front
vertical
acceleration
sensor - Short
to power
Right Front vertical
acceleration sensor
circuit short to power
Refer to the electrical circuit diagrams and check right front
vertical acceleration sensor circuit for short to power or
another circuit. Repair circuit, clear the DTC and retest the
system C101E-14
Right Front
vertical
acceleration
sensor - Short
to ground, open
circuit
Right Front vertical
acceleration sensor
circuit short to
ground, open circuit
Vertical acceleration
sensor fault
Refer to the electrical circuit diagrams and check right front
vertical acceleration sensor circuit for short to ground, open
circuit. If no fault found on wiring suspect sensor. Replace
sensor, clear DTC and retest the system C101E-22
Right Front
vertical
acceleration
sensor - Signal
amplitude >
maximum
Right front vertical
acceleration sensor
insecurely mounted
Right front vertical
acceleration sensor
signal circuit short to
another circuit
Right front vertical
acceleration sensor
internal fault
With vehicle parked on a level surface, read Right Front
Vertical Accelerometer voltage and check it lies in range 1.9 to
2.1 volts. If not OK then check electrical wiring for shorts,
loose connections and repair as required. If wiring OK then
suspect faulty sensor/incorrectly fitted sensor. Check the
sensor is correctly mounted, secure or replace sensor as
required. Refer to the new module/component installation
note at the top of the DTC Index, clear DTC and retest system C101E-26
Right Front
vertical
acceleration
sensor - Signal
rate of change
below threshold
Right front vertical
acceleration sensor
signal circuit short to
another circuit
Right front vertical
acceleration sensor
internal fault
Refer to the electrical circuit diagrams and check Right Front
Vertical Accelerometer signal circuit for faults, if circuit is
correct suspect faulty sensor, refer to the new
module/component installation note at the top of the DTC
Index. Replace the sensor, clear the DTC and retest the
system C101E-78 Right Front
Right front vertical
Check Right Front Vertical Accelerometer for location and vertical acceleration acceleration sensor security, if correct suspect faulty Accelerometer, refer to the sensor - bracket bent new module installation note at the top of the DTC Index. Alignment or Right front vertical Replace the sensor/bracket as required, clear the DTC and adjustment acceleration sensor retest the system incorrect damaged C1024-00
System Temporarily
Disabled Due To
Power
Interruption
During Driving -
No sub type
information
Loss of power to
control module whilst
driving
Refer to the electrical circuit diagrams and check power and
ground circuits to Adaptive Damping Control Module for
intermittent or poor connection. Repair wiring circuits as
required, clear DTC and retest the system C1030-12
Left Rear
vertical
acceleration
sensor - Short
to power
Left Rear vertical
acceleration sensor
circuit short to power
Refer to the electrical circuit diagrams and check left Rear
vertical acceleration sensor circuit for short to power or
another circuit. Repair circuit, clear the DTC and retest the
system
Page 108 of 3039
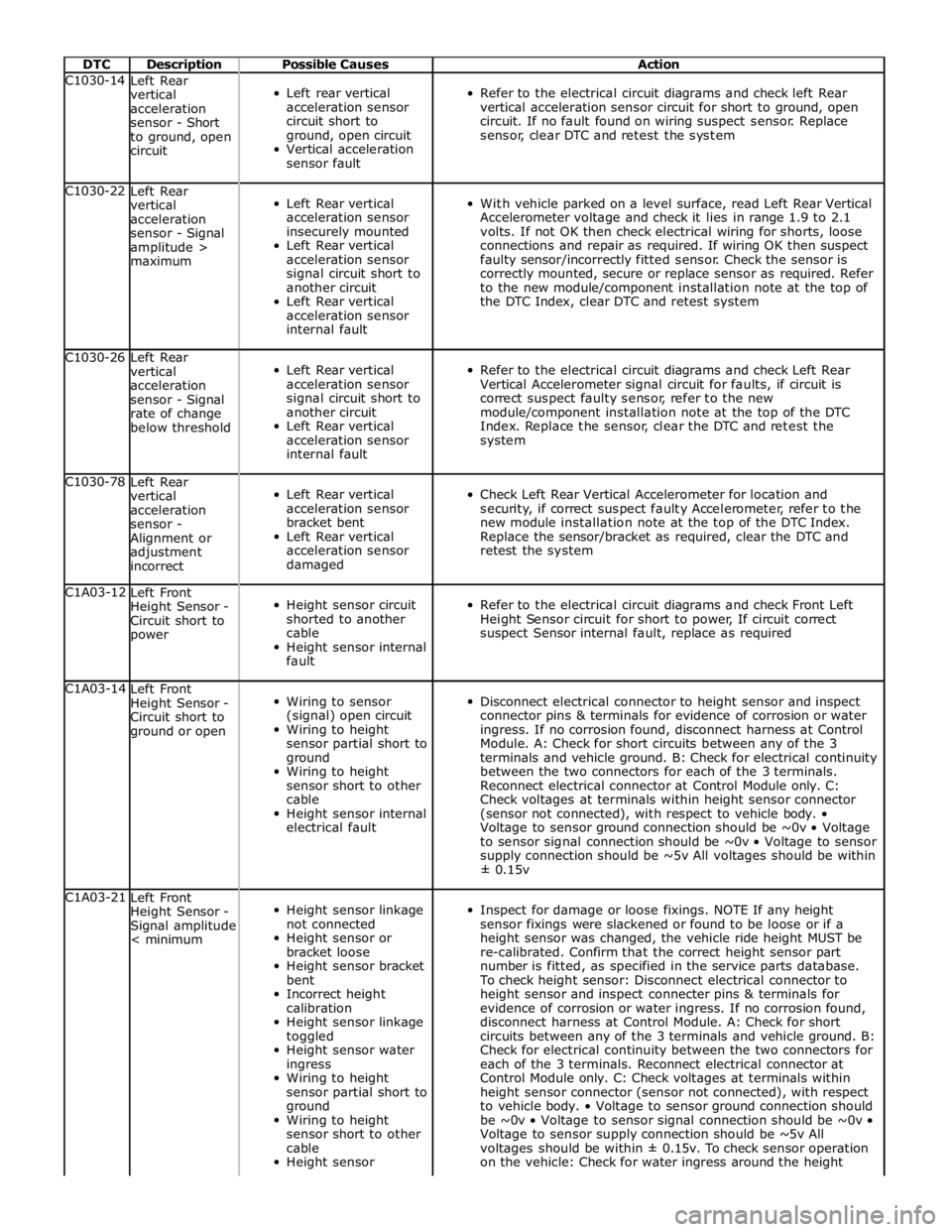
DTC Description Possible Causes Action C1030-14
Left Rear
vertical
acceleration
sensor - Short
to ground, open
circuit
Left rear vertical
acceleration sensor
circuit short to
ground, open circuit
Vertical acceleration
sensor fault
Refer to the electrical circuit diagrams and check left Rear
vertical acceleration sensor circuit for short to ground, open
circuit. If no fault found on wiring suspect sensor. Replace
sensor, clear DTC and retest the system C1030-22
Left Rear
vertical
acceleration
sensor - Signal
amplitude >
maximum
Left Rear vertical
acceleration sensor
insecurely mounted
Left Rear vertical
acceleration sensor
signal circuit short to
another circuit
Left Rear vertical
acceleration sensor
internal fault
With vehicle parked on a level surface, read Left Rear Vertical
Accelerometer voltage and check it lies in range 1.9 to 2.1
volts. If not OK then check electrical wiring for shorts, loose
connections and repair as required. If wiring OK then suspect
faulty sensor/incorrectly fitted sensor. Check the sensor is
correctly mounted, secure or replace sensor as required. Refer
to the new module/component installation note at the top of
the DTC Index, clear DTC and retest system C1030-26
Left Rear
vertical
acceleration
sensor - Signal
rate of change
below threshold
Left Rear vertical
acceleration sensor
signal circuit short to
another circuit
Left Rear vertical
acceleration sensor
internal fault
Refer to the electrical circuit diagrams and check Left Rear
Vertical Accelerometer signal circuit for faults, if circuit is
correct suspect faulty sensor, refer to the new
module/component installation note at the top of the DTC
Index. Replace the sensor, clear the DTC and retest the
system C1030-78
Left Rear
vertical
acceleration
sensor -
Alignment or
adjustment
incorrect
Left Rear vertical
acceleration sensor
bracket bent
Left Rear vertical
acceleration sensor
damaged
Check Left Rear Vertical Accelerometer for location and
security, if correct suspect faulty Accelerometer, refer to the
new module installation note at the top of the DTC Index.
Replace the sensor/bracket as required, clear the DTC and
retest the system C1A03-12
Left Front
Height Sensor -
Circuit short to
power
Height sensor circuit
shorted to another
cable
Height sensor internal
fault
Refer to the electrical circuit diagrams and check Front Left
Height Sensor circuit for short to power, If circuit correct
suspect Sensor internal fault, replace as required C1A03-14
Left Front
Height Sensor -
Circuit short to
ground or open
Wiring to sensor
(signal) open circuit
Wiring to height
sensor partial short to
ground
Wiring to height
sensor short to other
cable
Height sensor internal
electrical fault
Disconnect electrical connector to height sensor and inspect
connector pins & terminals for evidence of corrosion or water
ingress. If no corrosion found, disconnect harness at Control
Module. A: Check for short circuits between any of the 3
terminals and vehicle ground. B: Check for electrical continuity
between the two connectors for each of the 3 terminals.
Reconnect electrical connector at Control Module only. C:
Check voltages at terminals within height sensor connector
(sensor not connected), with respect to vehicle body. •
Voltage to sensor ground connection should be ~0v • Voltage
to sensor signal connection should be ~0v • Voltage to sensor
supply connection should be ~5v All voltages should be within
± 0.15v C1A03-21
Left Front
Height Sensor -
Signal amplitude
< minimum
Height sensor linkage
not connected
Height sensor or
bracket loose
Height sensor bracket
bent
Incorrect height
calibration
Height sensor linkage
toggled
Height sensor water
ingress
Wiring to height
sensor partial short to
ground
Wiring to height
sensor short to other
cable
Height sensor
Inspect for damage or loose fixings. NOTE If any height
sensor fixings were slackened or found to be loose or if a
height sensor was changed, the vehicle ride height MUST be
re-calibrated. Confirm that the correct height sensor part
number is fitted, as specified in the service parts database.
To check height sensor: Disconnect electrical connector to
height sensor and inspect connecter pins & terminals for
evidence of corrosion or water ingress. If no corrosion found,
disconnect harness at Control Module. A: Check for short
circuits between any of the 3 terminals and vehicle ground. B:
Check for electrical continuity between the two connectors for
each of the 3 terminals. Reconnect electrical connector at
Control Module only. C: Check voltages at terminals within
height sensor connector (sensor not connected), with respect
to vehicle body. • Voltage to sensor ground connection should
be ~0v • Voltage to sensor signal connection should be ~0v •
Voltage to sensor supply connection should be ~5v All
voltages should be within ± 0.15v. To check sensor operation
on the vehicle: Check for water ingress around the height
Page 109 of 3039
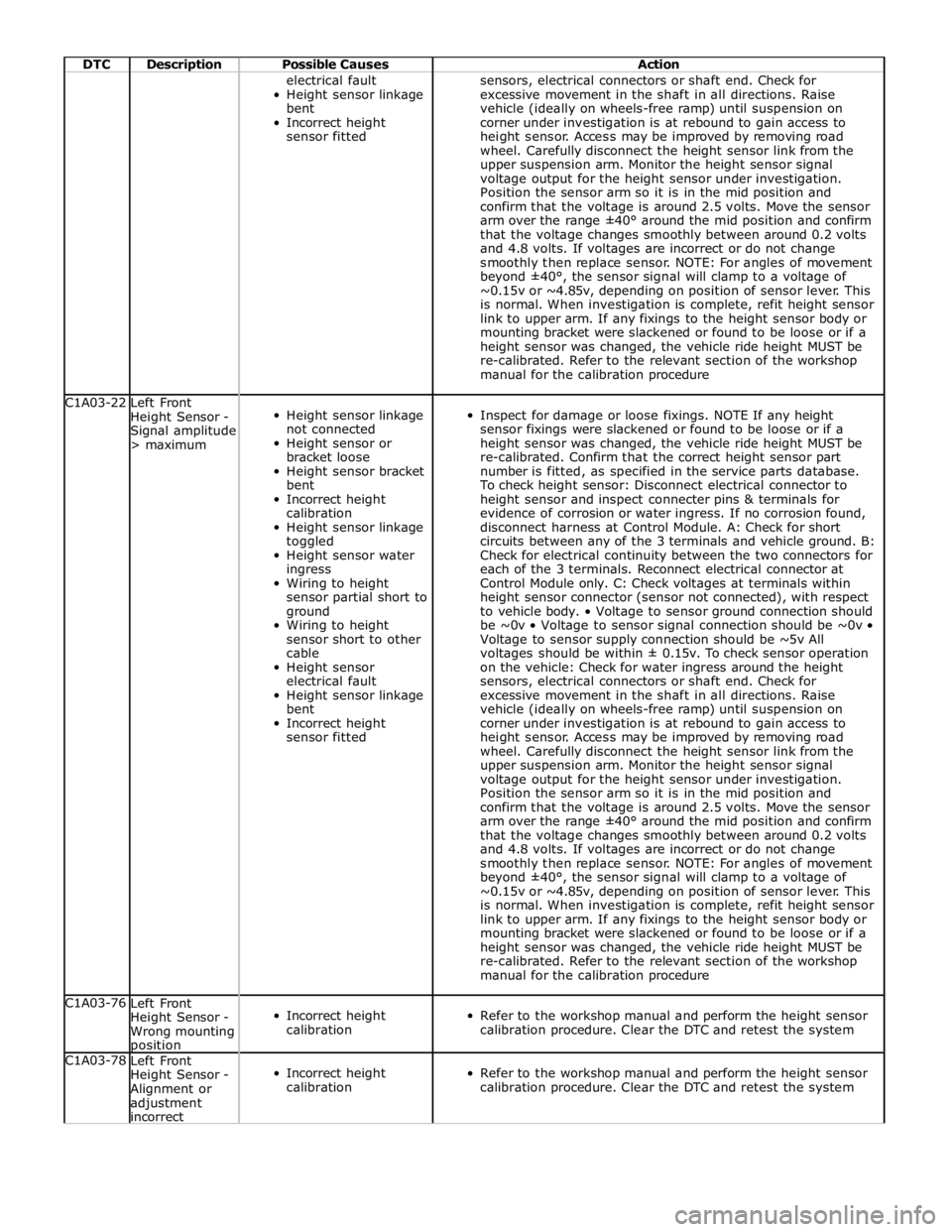
DTC Description Possible Causes Action electrical fault
Height sensor linkage
bent
Incorrect height
sensor fitted sensors, electrical connectors or shaft end. Check for
excessive movement in the shaft in all directions. Raise
vehicle (ideally on wheels-free ramp) until suspension on
corner under investigation is at rebound to gain access to
height sensor. Access may be improved by removing road
wheel. Carefully disconnect the height sensor link from the
upper suspension arm. Monitor the height sensor signal
voltage output for the height sensor under investigation.
Position the sensor arm so it is in the mid position and
confirm that the voltage is around 2.5 volts. Move the sensor
arm over the range ±40° around the mid position and confirm
that the voltage changes smoothly between around 0.2 volts
and 4.8 volts. If voltages are incorrect or do not change
smoothly then replace sensor. NOTE: For angles of movement
beyond ±40°, the sensor signal will clamp to a voltage of
~0.15v or ~4.85v, depending on position of sensor lever. This
is normal. When investigation is complete, refit height sensor
link to upper arm. If any fixings to the height sensor body or
mounting bracket were slackened or found to be loose or if a
height sensor was changed, the vehicle ride height MUST be
re-calibrated. Refer to the relevant section of the workshop
manual for the calibration procedure C1A03-22
Left Front
Height Sensor -
Signal amplitude
> maximum
Height sensor linkage
not connected
Height sensor or
bracket loose
Height sensor bracket
bent
Incorrect height
calibration
Height sensor linkage
toggled
Height sensor water
ingress
Wiring to height
sensor partial short to
ground
Wiring to height
sensor short to other
cable
Height sensor
electrical fault
Height sensor linkage
bent
Incorrect height
sensor fitted
Inspect for damage or loose fixings. NOTE If any height
sensor fixings were slackened or found to be loose or if a
height sensor was changed, the vehicle ride height MUST be
re-calibrated. Confirm that the correct height sensor part
number is fitted, as specified in the service parts database.
To check height sensor: Disconnect electrical connector to
height sensor and inspect connecter pins & terminals for
evidence of corrosion or water ingress. If no corrosion found,
disconnect harness at Control Module. A: Check for short
circuits between any of the 3 terminals and vehicle ground. B:
Check for electrical continuity between the two connectors for
each of the 3 terminals. Reconnect electrical connector at
Control Module only. C: Check voltages at terminals within
height sensor connector (sensor not connected), with respect
to vehicle body. • Voltage to sensor ground connection should
be ~0v • Voltage to sensor signal connection should be ~0v •
Voltage to sensor supply connection should be ~5v All
voltages should be within ± 0.15v. To check sensor operation
on the vehicle: Check for water ingress around the height
sensors, electrical connectors or shaft end. Check for
excessive movement in the shaft in all directions. Raise
vehicle (ideally on wheels-free ramp) until suspension on
corner under investigation is at rebound to gain access to
height sensor. Access may be improved by removing road
wheel. Carefully disconnect the height sensor link from the
upper suspension arm. Monitor the height sensor signal
voltage output for the height sensor under investigation.
Position the sensor arm so it is in the mid position and
confirm that the voltage is around 2.5 volts. Move the sensor
arm over the range ±40° around the mid position and confirm
that the voltage changes smoothly between around 0.2 volts
and 4.8 volts. If voltages are incorrect or do not change
smoothly then replace sensor. NOTE: For angles of movement
beyond ±40°, the sensor signal will clamp to a voltage of
~0.15v or ~4.85v, depending on position of sensor lever. This
is normal. When investigation is complete, refit height sensor
link to upper arm. If any fixings to the height sensor body or
mounting bracket were slackened or found to be loose or if a
height sensor was changed, the vehicle ride height MUST be
re-calibrated. Refer to the relevant section of the workshop
manual for the calibration procedure C1A03-76
Left Front
Height Sensor -
Wrong mounting position
Incorrect height
calibration
Refer to the workshop manual and perform the height sensor
calibration procedure. Clear the DTC and retest the system C1A03-78
Left Front
Height Sensor -
Alignment or
adjustment
incorrect
Incorrect height
calibration
Refer to the workshop manual and perform the height sensor
calibration procedure. Clear the DTC and retest the system
Page 110 of 3039
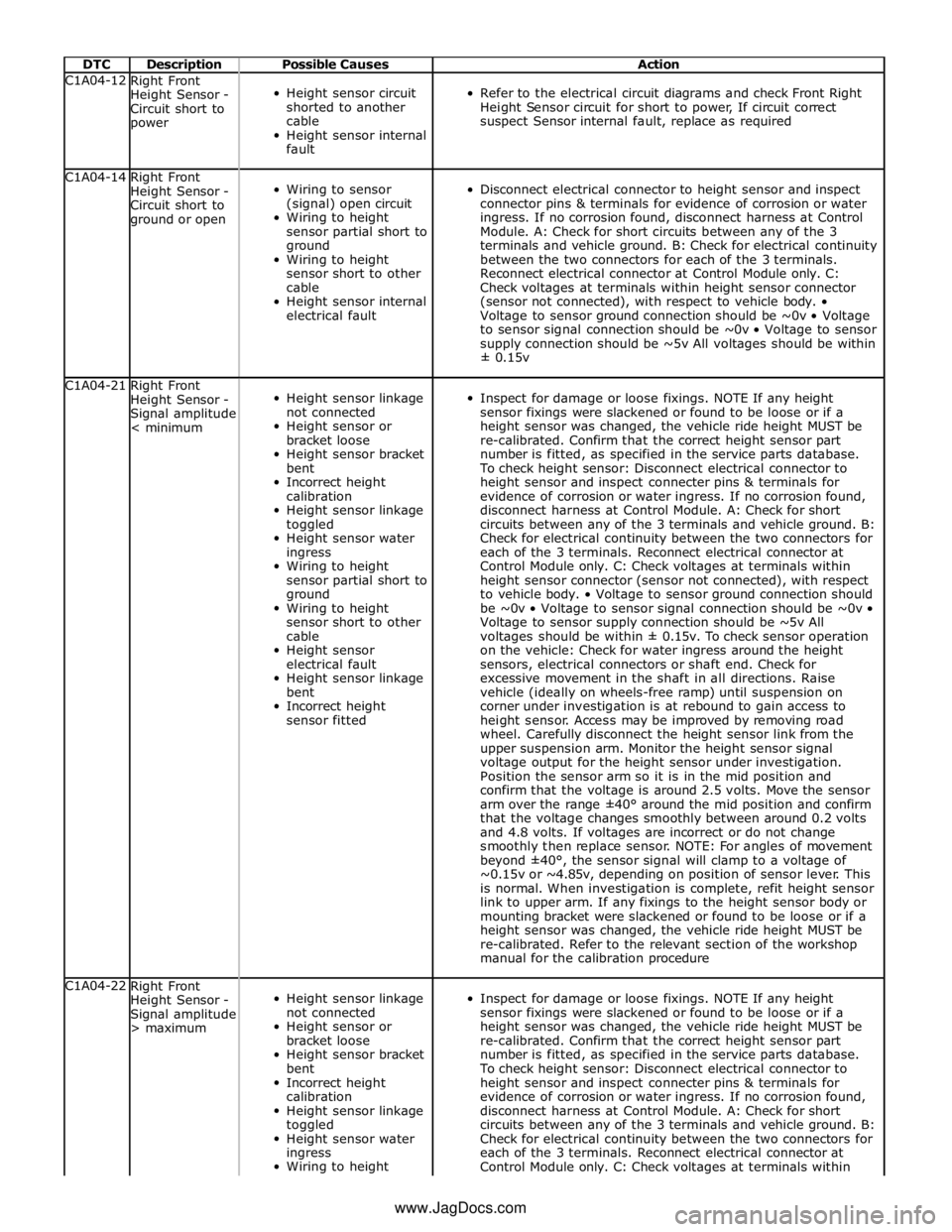
DTC Description Possible Causes Action C1A04-12
Right Front
Height Sensor -
Circuit short to
power
Height sensor circuit
shorted to another
cable
Height sensor internal
fault
Refer to the electrical circuit diagrams and check Front Right
Height Sensor circuit for short to power, If circuit correct
suspect Sensor internal fault, replace as required C1A04-14
Right Front
Height Sensor -
Circuit short to
ground or open
Wiring to sensor
(signal) open circuit
Wiring to height
sensor partial short to
ground
Wiring to height
sensor short to other
cable
Height sensor internal
electrical fault
Disconnect electrical connector to height sensor and inspect
connector pins & terminals for evidence of corrosion or water
ingress. If no corrosion found, disconnect harness at Control
Module. A: Check for short circuits between any of the 3
terminals and vehicle ground. B: Check for electrical continuity
between the two connectors for each of the 3 terminals.
Reconnect electrical connector at Control Module only. C:
Check voltages at terminals within height sensor connector
(sensor not connected), with respect to vehicle body. •
Voltage to sensor ground connection should be ~0v • Voltage
to sensor signal connection should be ~0v • Voltage to sensor
supply connection should be ~5v All voltages should be within
± 0.15v C1A04-21
Right Front
Height Sensor -
Signal amplitude
< minimum
Height sensor linkage
not connected
Height sensor or
bracket loose
Height sensor bracket
bent
Incorrect height
calibration
Height sensor linkage
toggled
Height sensor water
ingress
Wiring to height
sensor partial short to
ground
Wiring to height
sensor short to other
cable
Height sensor
electrical fault
Height sensor linkage
bent
Incorrect height
sensor fitted
Inspect for damage or loose fixings. NOTE If any height
sensor fixings were slackened or found to be loose or if a
height sensor was changed, the vehicle ride height MUST be
re-calibrated. Confirm that the correct height sensor part
number is fitted, as specified in the service parts database.
To check height sensor: Disconnect electrical connector to
height sensor and inspect connecter pins & terminals for
evidence of corrosion or water ingress. If no corrosion found,
disconnect harness at Control Module. A: Check for short
circuits between any of the 3 terminals and vehicle ground. B:
Check for electrical continuity between the two connectors for
each of the 3 terminals. Reconnect electrical connector at
Control Module only. C: Check voltages at terminals within
height sensor connector (sensor not connected), with respect
to vehicle body. • Voltage to sensor ground connection should
be ~0v • Voltage to sensor signal connection should be ~0v •
Voltage to sensor supply connection should be ~5v All
voltages should be within ± 0.15v. To check sensor operation
on the vehicle: Check for water ingress around the height
sensors, electrical connectors or shaft end. Check for
excessive movement in the shaft in all directions. Raise
vehicle (ideally on wheels-free ramp) until suspension on
corner under investigation is at rebound to gain access to
height sensor. Access may be improved by removing road
wheel. Carefully disconnect the height sensor link from the
upper suspension arm. Monitor the height sensor signal
voltage output for the height sensor under investigation.
Position the sensor arm so it is in the mid position and
confirm that the voltage is around 2.5 volts. Move the sensor
arm over the range ±40° around the mid position and confirm
that the voltage changes smoothly between around 0.2 volts
and 4.8 volts. If voltages are incorrect or do not change
smoothly then replace sensor. NOTE: For angles of movement
beyond ±40°, the sensor signal will clamp to a voltage of
~0.15v or ~4.85v, depending on position of sensor lever. This
is normal. When investigation is complete, refit height sensor
link to upper arm. If any fixings to the height sensor body or
mounting bracket were slackened or found to be loose or if a
height sensor was changed, the vehicle ride height MUST be
re-calibrated. Refer to the relevant section of the workshop
manual for the calibration procedure C1A04-22
Right Front
Height Sensor -
Signal amplitude
> maximum
Height sensor linkage
not connected
Height sensor or
bracket loose
Height sensor bracket
bent
Incorrect height
calibration
Height sensor linkage
toggled
Height sensor water
ingress
Wiring to height
Inspect for damage or loose fixings. NOTE If any height
sensor fixings were slackened or found to be loose or if a
height sensor was changed, the vehicle ride height MUST be
re-calibrated. Confirm that the correct height sensor part
number is fitted, as specified in the service parts database.
To check height sensor: Disconnect electrical connector to
height sensor and inspect connecter pins & terminals for
evidence of corrosion or water ingress. If no corrosion found,
disconnect harness at Control Module. A: Check for short
circuits between any of the 3 terminals and vehicle ground. B:
Check for electrical continuity between the two connectors for
each of the 3 terminals. Reconnect electrical connector at
Control Module only. C: Check voltages at terminals within www.JagDocs.com