engine JEEP CJ 1953 Service Manual
[x] Cancel search | Manufacturer: JEEP, Model Year: 1953, Model line: CJ, Model: JEEP CJ 1953Pages: 376, PDF Size: 19.96 MB
Page 194 of 376
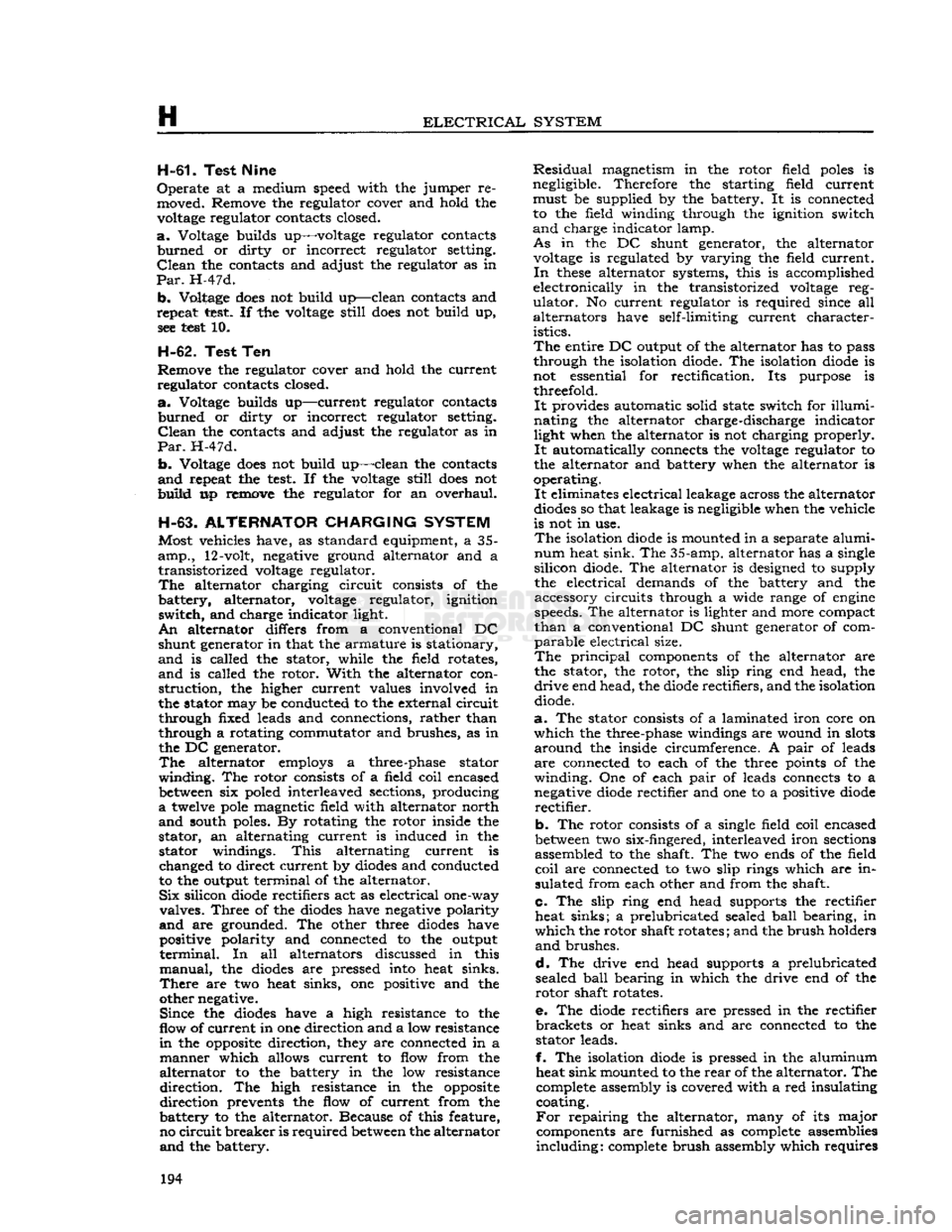
H
ELECTRICAL
SYSTEM H-61.
Test Nine
Operate
at a medium speed with the jumper re moved. Remove the regulator cover and hold the
voltage
regulator contacts closed.
a.
Voltage builds up—voltage regulator contacts
burned
or dirty or incorrect regulator setting.
Clean
the contacts and adjust the regulator as in
Par.
H-47d.
b.
Voltage
does
not build up—clean contacts and
repeat
test.
If the
voltage
still
does
not build up, see
test
10.
H-62.
Test Ten
Remove the regulator cover and hold the current
regulator contacts closed.
a.
Voltage builds up—current regulator contacts
burned
or dirty or incorrect regulator setting.
Clean
the contacts and adjust the regulator as in
Par.
H-47d.
b.
Voltage
does
not build up—clean the contacts
and
repeat the
test.
If the
voltage
still
does
not
build
up remove the regulator for an overhaul.
H-63. ALTERNATOR CHARGING SYSTEM
Most vehicles have, as standard equipment, a 35-
amp.,
12-volt, negative ground alternator and a
transistorized
voltage
regulator.
The
alternator charging circuit consists of the
battery, alternator,
voltage
regulator, ignition
switch,
and charge indicator light.
An
alternator differs from a conventional DC
shunt generator in that the armature is stationary,
and
is called the stator, while the field rotates,
and
is called the rotor.
With
the alternator conÂ
struction,
the higher current values involved in
the stator may be conducted to the external circuit through fixed leads and connections, rather than
through a rotating commutator and brushes, as in the DC generator.
The
alternator employs a three-phase stator
winding. The rotor consists of a field coil encased
between
six poled interleaved sections, producing
a
twelve
pole
magnetic field with alternator north
and
south poles. By rotating the rotor inside the stator, an alternating current is induced in the stator windings.
This
alternating current is
changed to direct current by
diodes
and conducted
to the output terminal of the alternator.
Six
silicon
diode
rectifiers act as electrical one-way valves.
Three
of the
diodes
have negative polarity
and
are grounded. The other three
diodes
have
positive polarity and connected to the output
terminal.
In all alternators discussed in this
manual,
the
diodes
are pressed into heat sinks.
There
are two heat sinks, one positive and the
other negative.
Since
the
diodes
have a high resistance to the
flow of
current
in one direction and a low resistance
in
the
opposite
direction, they are connected in a
manner
which allows current to flow from the
alternator to the battery in the low resistance
direction.
The high resistance in the
opposite
direction prevents the flow of current from the
battery to the alternator. Because of this feature,
no
circuit
breaker
is
required
between
the alternator
and
the battery.
Residual
magnetism in the rotor field
poles
is
negligible. Therefore the starting field current must be supplied by the battery. It is connected
to the field winding through the ignition switch
and
charge indicator lamp.
As
in the DC shunt generator, the alternator
voltage
is regulated by varying the field current.
In
these
alternator systems, this is accomplished
electronically in the transistorized
voltage
regÂ
ulator.
No current regulator is required since all
alternators have self-limiting current characterÂ
istics.
The
entire DC output of the alternator has to pass
through the isolation diode. The isolation
diode
is
not essential for rectification. Its purpose is threefold.
It
provides automatic solid
state
switch for
illumiÂ
nating the alternator charge
-
discharge indicator
light when the alternator is not charging properly.
It
automatically connects the
voltage
regulator to
the alternator and battery when the alternator is
operating.
It
eliminates electrical leakage across the alternator
diodes
so that leakage is negligible when the vehicle
is not in use.
The
isolation
diode
is mounted in a separate alumiÂ
num
heat sink. The 35-amp. alternator has a single
silicon diode. The alternator is designed to supply the electrical demands of the battery and the
accessory circuits through a wide range of
engine
speeds. The alternator is lighter and more compact
than
a conventional DC shunt generator of comÂ
parable
electrical size.
The
principal
components of the alternator are
the stator, the rotor, the slip ring end head, the
drive
end head, the
diode
rectifiers, and the isolation diode.
a.
The stator consists of a laminated iron core on
which
the three-phase windings are wound in
slots
around
the inside circumference. A
pair
of leads
are
connected to each of the three points of the
winding. One of each
pair
of leads connects to a
negative
diode
rectifier and one to a positive
diode
rectifier.
b.
The rotor consists of a single field coil encased
between
two six-fingered, interleaved iron sections assembled to the shaft. The two ends of the field
coil
are connected to two slip rings which are inÂ
sulated from each other and from the shaft.
c. The slip ring end head supports the rectifier heat sinks; a prelubricated sealed
ball
bearing, in
which
the rotor shaft rotates; and the brush holders
and
brushes.
d.
The drive end head supports a prelubricated
sealed
ball
bearing in which the drive end of the rotor shaft rotates.
e. The
diode
rectifiers are pressed in the rectifier brackets or heat sinks and are connected to the
stator leads.
f. The isolation
diode
is pressed in the aluminum heat sink mounted to the
rear
of the alternator. The
complete assembly is covered with a red insulating coating.
For
repairing the alternator, many of its major components are furnished as complete assemblies
including:
complete brush assembly which requires 194
Page 195 of 376
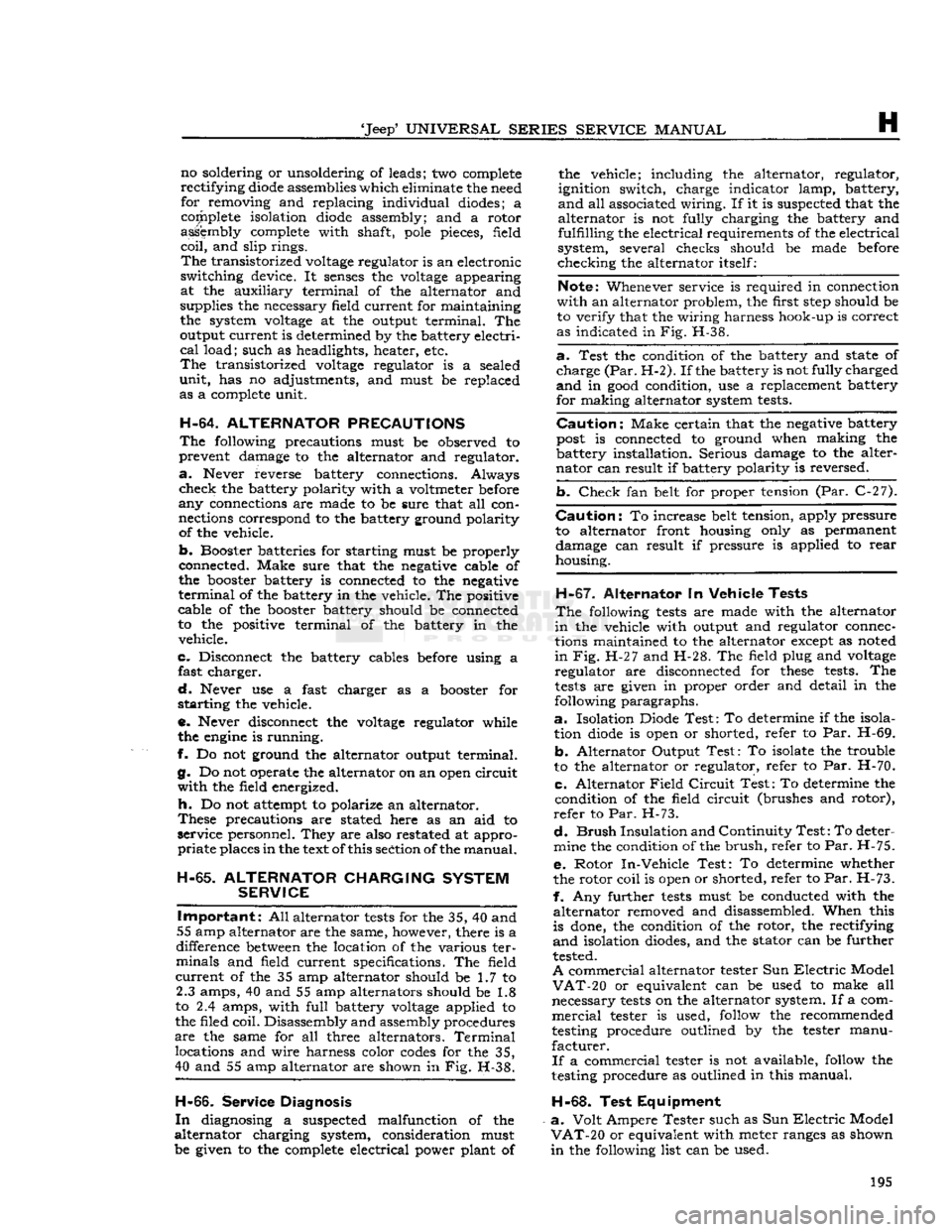
'Jeep*
UNIVERSAL
SERIES SERVICE
MANUAL
H
no soldering or unsoldering of leads; two complete
rectifying
diode assemblies
which
eliminate the need
for removing and replacing individual diodes; a
corpplete isolation diode assembly; and a rotor
assembly complete with shaft,
pole
pieces, field
coil,
and slip rings.
The
transistorized
voltage
regulator is an electronic
switching device. It
senses
the
voltage
appearing
at the auxiliary terminal of the alternator and
supplies the necessary field current for maintaining
the system
voltage
at the output terminal. The
output current is determined by the battery electriÂ
cal
load; such as headlights, heater, etc.
The
transistorized
voltage
regulator is a sealed
unit,
has no adjustments, and must be replaced
as a complete unit.
H-64. ALTERNATOR
PRECAUTIONS
The
following precautions must be observed to
prevent damage to the alternator and regulator.
a.
Never reverse battery connections. Always
check
the battery polarity with a voltmeter before
any
connections are made to be sure that all conÂ
nections correspond to the battery ground polarity of the vehicle.
b.
Booster batteries for starting must be properly
connected. Make sure that the negative cable of
the booster battery is connected to the negative
terminal
of the battery in the vehicle. The positive
cable of the booster battery should be connected
to the positive terminal of the battery in the
vehicle.
c.
Disconnect the battery cables before using a fast charger.
d.
Never use a fast charger as a booster for
starting
the vehicle.
e.
Never disconnect the
voltage
regulator while
the
engine
is running.
f.
Do not ground the alternator output terminal.
g.
Do not operate the alternator on an open
circuit
with
the field energized.
h.
Do not attempt to polarize an alternator.
These
precautions are stated here as an aid to
service
personnel. They are also restated at approÂ
priate
places in the
text
of this section of the
manual.
H-65. ALTERNATOR
CHARGING
SYSTEM SERVICE
Important:
All alternator
tests
for the 35, 40 and
55 amp alternator are the same, however, there is a
difference
between
the location of the various terÂ
minals
and field current specifications. The field
current
of the 35 amp alternator should be 1.7 to 2.3 amps, 40 and 55 amp alternators should be 1.8
to 2.4 amps, with
full
battery
voltage
applied to
the filed coil. Disassembly and assembly procedures
are
the same for all three alternators.
Terminal
locations and wire harness color
codes
for the 35,
40 and 55 amp alternator are shown in Fig. H-38.
H-66.
Service Diagnosis
In
diagnosing a suspected malfunction of the
alternator
charging system, consideration must
be given to the complete electrical power plant of the vehicle; including the alternator, regulator,
ignition switch, charge indicator lamp, battery,
and
all associated wiring. If it is suspected that the
alternator
is not fully charging the battery and
fulfilling
the electrical requirements of the electrical
system, several checks should be made before
checking
the alternator itself:
Note:
Whenever service is required in connection
with
an alternator problem, the first
step
should be to verify that the wiring harness hook-up is correct
as indicated in Fig. H-38.
a.
Test the condition of the battery and
state
of
charge
(Par. H-2).
If the battery is not fully charged
and
in
good
condition, use a replacement battery
for making alternator system
tests.
Caution:
Make certain that the negative battery
post
is connected to ground when making the
battery installation. Serious damage to the alterÂ
nator
can result if battery polarity is reversed.
b.
Check
fan belt for proper tension (Par.
C-27).
Caution:
To increase belt tension, apply pressure
to alternator front housing only as permanent damage can result if pressure is applied to
rear
housing.
H-67.
Alternator In Vehicle Tests
The
following
tests
are made with the alternator
in
the vehicle with output and regulator connecÂ
tions maintained to the alternator except as noted
in
Fig. H-27 and H-28. The field plug and
voltage
regulator are disconnected for
these
tests.
The
tests
are given in proper order and detail in the
following paragraphs.
a.
Isolation Diode Test: To determine if the isolaÂ
tion diode is open or shorted, refer to Par. H-69.
b.
Alternator Output Test: To isolate the trouble
to the alternator or regulator, refer to Par. H-70.
c.
Alternator
Field
Circuit
Test: To determine the condition of the field
circuit
(brushes and rotor),
refer
to Par. H-73.
d.
Brush
Insulation
and Continuity
Test:
To deterÂ
mine the condition of the
brush,
refer to
Par.
H-75.
e.
Rotor In-Vehicle Test: To determine whether
the rotor coil is open or shorted, refer to
Par.
H-73.
f. Any further
tests
must be conducted with the
alternator
removed and disassembled. When this
is done, the condition of the rotor, the rectifying
and
isolation diodes, and the stator can be further
tested.
A
commercial alternator tester Sun
Electric
Model
VAT-20
or equivalent can be used to make all
necessary
tests
on the alternator system. If a comÂ
mercial
tester is used, follow the recommended
testing procedure outlined by the tester manuÂ
facturer.
If
a commercial tester is not available, follow the
testing procedure as outlined in this manual.
H-68.
Test Equipment
a.
Volt Ampere Tester such as Sun
Electric
Model
VAT-20
or equivalent with meter ranges as shown
in
the following list can be used. 195
Page 196 of 376
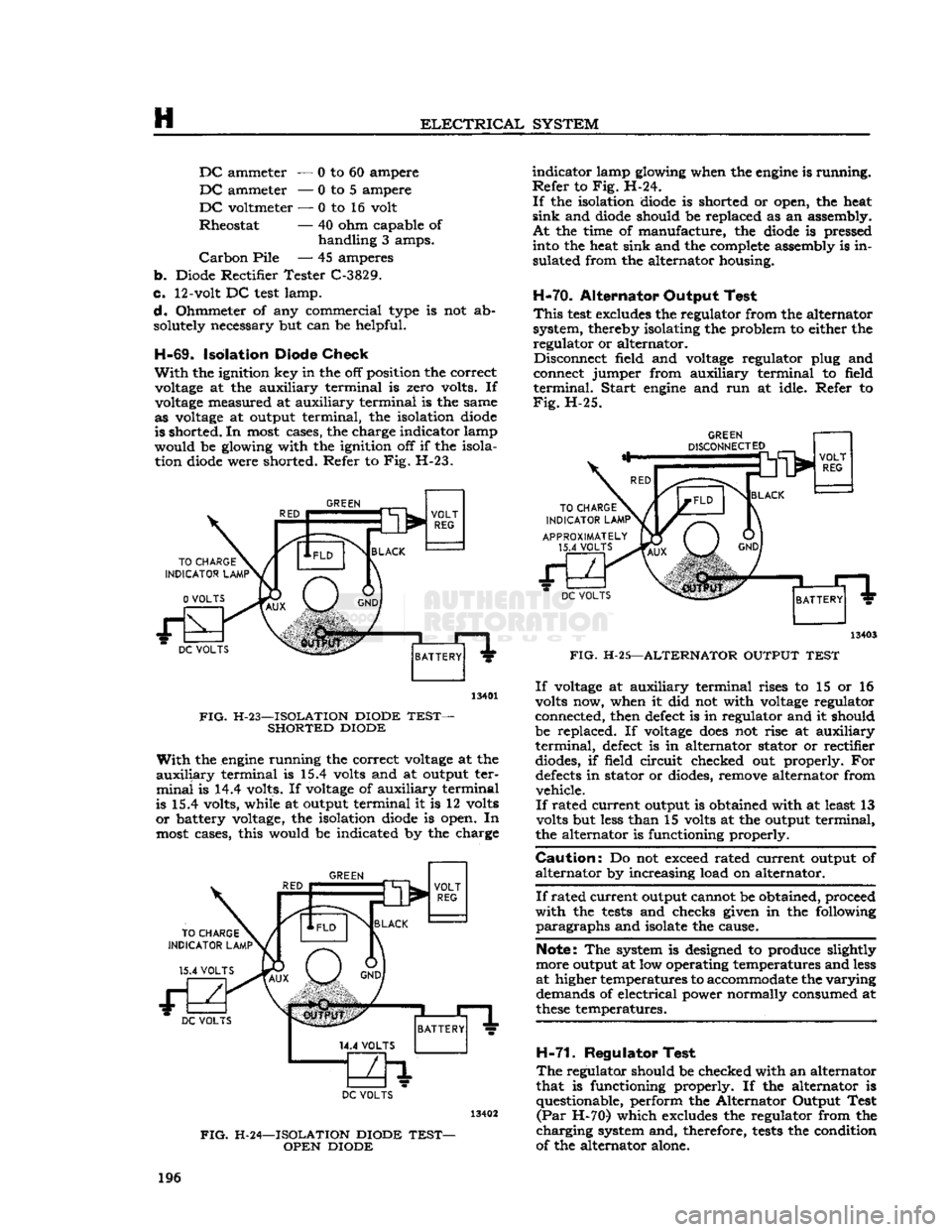
H
ELECTRICAL
SYSTEM DC
ammeter — 0 to 60 ampere
DC
ammeter — 0 to 5 ampere
DC
voltmeter — 0 to 16 volt
Rheostat — 40 ohm capable of
handling
3 amps.
Carbon
Pile — 45 amperes
b.
Diode Rectifier Tester C-3829.
c.
12-volt DC
test
lamp.
d.
Ohmmeter of any commercial type is not abÂsolutely necessary but can be helpful.
H-69.
Isolation Diode
Check
With
the ignition key in the off position the correct voltage at the auxiliary terminal is zero volts. If
voltage measured at auxiliary terminal is the same as voltage at output terminal, the isolation diode
is shorted. In most cases, the charge indicator lamp
would be glowing with the ignition off if the isola tion diode were shorted. Refer to Fig. H-23.
GREEN
DC
VOLTS
13401
FIG.
H-23—ISOLATION DIODE
TEST-
SHORTED DIODE
With
the engine running the correct voltage at the
auxiliary
terminal is 15.4 volts and at output terÂ
minal
is 14.4 volts. If voltage of auxiliary terminal
is 15.4 volts, while at output terminal it is 12 volts
or
battery voltage, the isolation diode is open. In
most cases, this would be indicated by the charge
GREEN
TO
CHARGE
INDICATOR
LAMP1
15.4
VOLTS BLACK
VOLT
REG DC
VOLTS
BATTERY
DC
VOLTS
FIG.
H-24—ISOLATION DIODE
TEST-
OPEN DIODE
indicator
lamp glowing when the engine is running.
Refer
to Fig. H-24.
If
the isolation diode is shorted or open, the heat
sink
and diode should be replaced as an assembly.
At
the time of manufacture, the diode is pressed into the heat sink and the complete assembly is inÂ
sulated from the alternator housing.
H-70.
Alternator Output Test
This
test
excludes the regulator from the alternator
system, thereby isolating the problem to either the regulator or alternator. Disconnect field and voltage regulator plug and
connect jumper from auxiliary terminal to field
terminal.
Start
engine and run at idle. Refer to
Fig.
H-25.
DC
VOLTS
13403
FIG.
H-25—ALTERNATOR OUTPUT
TEST
If
voltage at auxiliary terminal rises to 15 or 16
volts now, when it did not with voltage regulator
connected, then defect is in regulator and it should
be replaced. If voltage
does
not rise at auxiliary
terminal,
defect is in alternator stator or rectifier diodes, if field circuit checked out properly. For
defects
in stator or diodes, remove alternator from vehicle.
If
rated current output is obtained with at least 13
volts but less than 15 volts at the output terminal,
the alternator is functioning properly.
Caution:
Do not exceed rated current output of
alternator
by increasing load on alternator.
If
rated
current
output cannot be obtained, proceed
with
the
tests
and checks given in the following
paragraphs
and isolate the cause.
Note: The system is designed to produce slightly
more output at low operating temperatures and less
at higher temperatures to accommodate the
varying
demands of electrical power normally consumed at
these
temperatures.
H-71.
Regulator Test
The
regulator should be checked with an alternator
that is functioning properly. If the alternator is questionable, perform the Alternator Output Test
(Par
H-70) which excludes the regulator from the
charging
system and, therefore,
tests
the condition
of the alternator alone. 196
Page 197 of 376
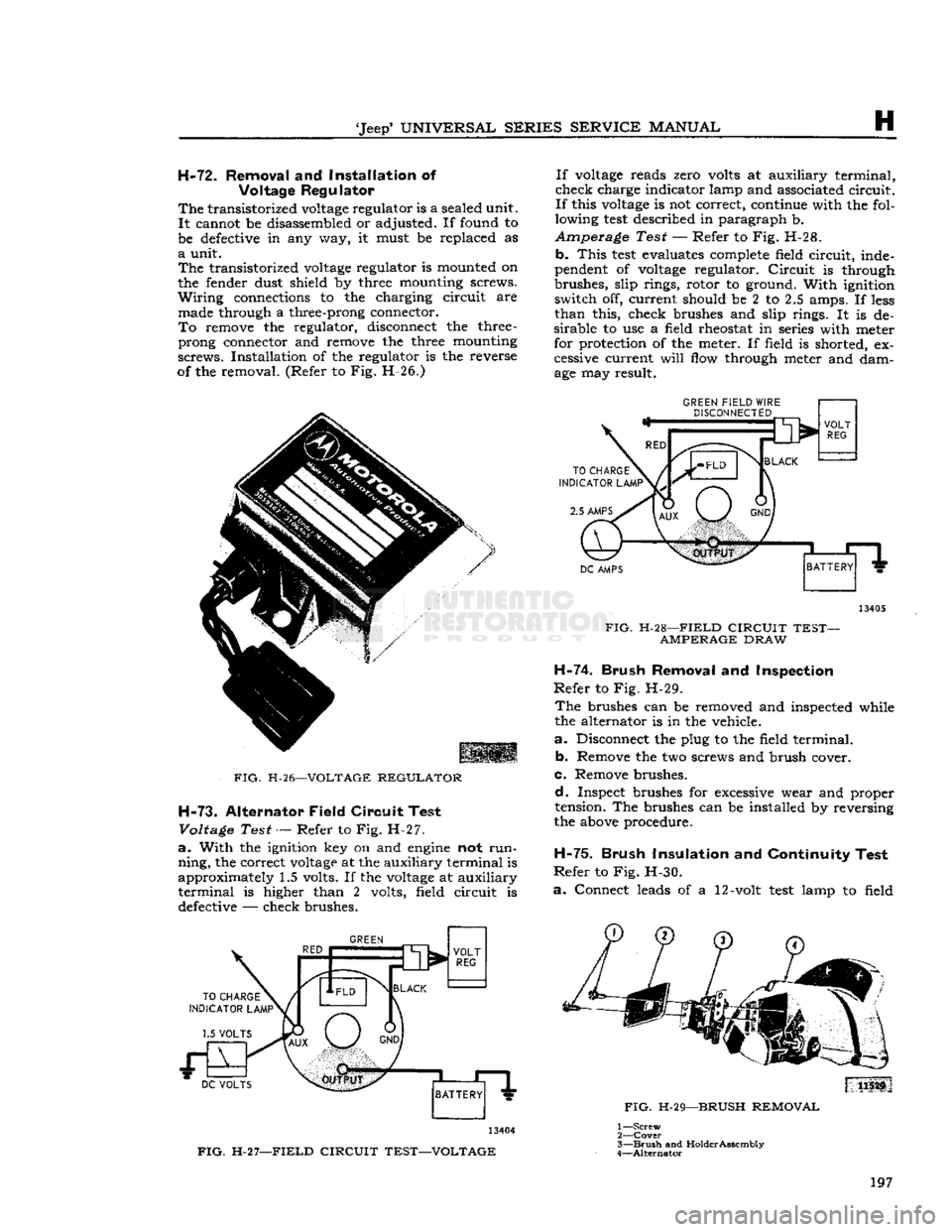
'Jeep'
UNIVERSAL SERIES SERVICE
MANUAL
H
H-72.
Removal
and
Installation
of
Voltage Regulator
The
transistorized
voltage
regulator is a sealed unit.
It
cannot be disassembled or adjusted. If found to
be defective in any way, it must be replaced as
a
unit.
The
transistorized
voltage
regulator is mounted on
the fender dust shield by three mounting screws.
Wiring
connections to the charging circuit are made through a three-prong connector.
To
remove the regulator, disconnect the three
-
prong connector and remove the three mounting
screws.
Installation of the regulator is the reverse
of the removal. (Refer to Fig. H-26.)
FIG.
H-26—VOLTAGE
REGULATOR
H-73.
Alternator Field Circuit Test
Voltage
Test — Refer to Fig. H-27.
a.
With the ignition key on and
engine
not
runÂ
ning,
the correct
voltage
at the auxiliary terminal is
approximately 1.5 volts. If the
voltage
at auxiliary
terminal
is higher than 2 volts, field circuit is defective — check brushes.
GREEN
13404
FIG.
H-27—FIELD
CIRCUIT TEST—VOLTAGE If
voltage
reads zero volts at auxiliary terminal,
check charge indicator lamp and associated circuit.
If
this
voltage
is not correct, continue with the folÂ
lowing
test
described in paragraph b.
Amperage Test — Refer to Fig. H-28. b.
This
test
evaluates complete field circuit, indeÂ
pendent of
voltage
regulator.
Circuit
is through
brushes, slip rings, rotor to ground. With ignition switch off, current should be 2 to 2.5 amps. If
less
than
this, check brushes and slip rings. It is deÂ
sirable
to use a field rheostat in series with meter
for protection of the meter. If field is shorted, exÂ
cessive current
will
flow through meter and damÂ
age may result.
GREEN
FIELD
WIRE
DISCONNECTED
13405
FIG.
H-28—FIELD
CIRCUIT TEST- AMPERAGE
DRAW
H-74.
Brush Removal
and
Inspection
Refer
to Fig. H-29.
The
brushes can be removed and inspected while
the alternator is in the vehicle.
a.
Disconnect the plug to the field terminal. b. Remove the two screws and brush cover.
c. Remove brushes.
d.
Inspect brushes for excessive wear and proper
tension. The brushes can be installed by reversing
the above procedure.
H-75.
Brush Insulation
and
Continuity Test
Refer
to Fig. H-30.
a.
Connect leads of a 12-volt
test
lamp to field
FIG.
H-29—BRUSH
REMOVAL
1—
Screw
2—
Cover
3—
Brush
and
Holder
Assembly
4—
Alternator
197
Page 202 of 376
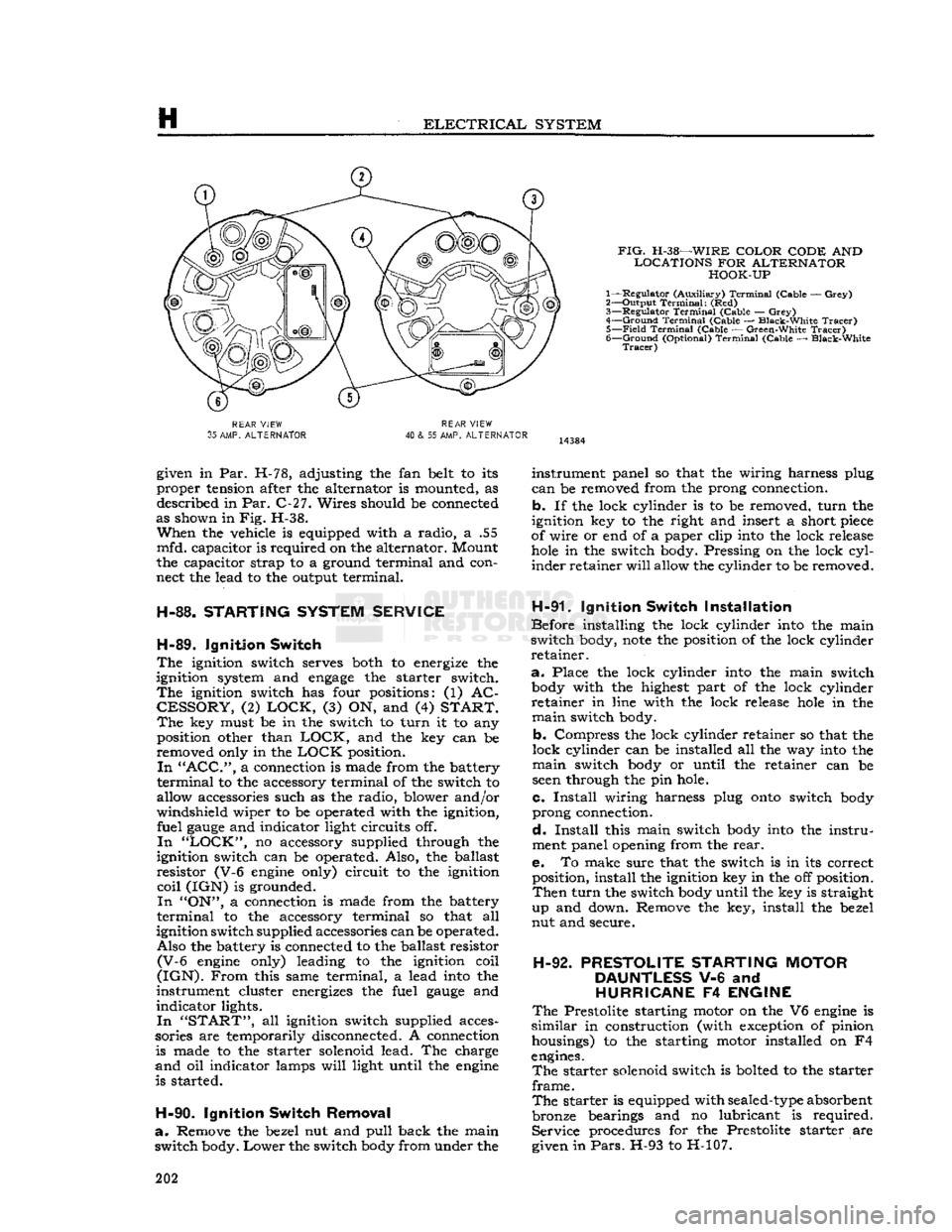
H
ELECTRICAL
SYSTEM
FIG.
H-38—WIRE
COLOR CODE
AND
LOCATIONS
FOR
ALTERNATOR HOOK-UP
1— Regulator (Auxiliary)
Terminal
(Cable —
Grey)
2— Output
Terminal:
(Red)
3—
Regulator
Terminal
(Cable —
Grey)
4—
Ground
Terminal
(Cable — Black-White
Tracer)
5—
Field
Terminal
(Cable — Green-White
Tracer)
6—
Ground
(Optional)
Terminal
(Cable — Black-White
Tracer)
REAR
VIEW
35
AMP.
ALTERNATOR
REAR
VIEW
40
& 55 AMP.
ALTERNATOR
given in Par. H-78, adjusting the fan belt to its
proper tension after the alternator is mounted, as described in Par. C-27. Wires should be connected
as shown in Fig. H-38.
When
the vehicle is equipped with a radio, a .55
mfd. capacitor is required on the alternator. Mount
the capacitor strap to a ground terminal and conÂ
nect the lead to the output terminal.
H-88.
STARTING
SYSTEM
SERVICE
H-89.
Ignition
Switch
The
ignition switch serves both to energize the
ignition system and
engage
the starter switch.
The
ignition switch has four positions: (1) ACÂ
CESSORY,
(2)
LOCK,
(3) ON, and (4)
START. The
key must be in the switch to turn it to any position other than
LOCK,
and the key can be
removed only in the
LOCK
position.
In "ACC",
a connection is made from the battery
terminal
to the accessory terminal of the switch to
allow accessories such as the radio, blower and/or
windshield wiper to be operated with the ignition, fuel
gauge
and indicator light circuits off.
In "LOCK",
no accessory supplied through the
ignition switch can be operated. Also, the ballast
resistor (V-6
engine
only) circuit to the ignition
coil
(IGN) is grounded.
In
"ON", a connection is made from the battery
terminal
to the accessory terminal so that all
ignition switch supplied accessories can be operated. Also the battery is connected to the ballast resistor
(V-6
engine
only) leading to the ignition coil
(IGN).
From
this same terminal, a lead
into
the
instrument cluster energizes the fuel
gauge
and
indicator lights.
In "START",
all ignition switch supplied accesÂ
sories are temporarily disconnected. A connection is made to the starter solenoid lead. The charge
and
oil indicator lamps
will
light until the
engine
is started.
H-90.
Ignition
Switch
Removal
a.
Remove the bezel nut and pull back the main
switch body.
Lower
the switch
body
from under the instrument panel so that the wiring harness plug
can
be removed from the prong connection,
b. If the lock cylinder is to be removed, turn the
ignition key to the right and insert a short
piece
of wire or end of a paper clip
into
the lock release
hole
in the switch body. Pressing on the lock
cylÂ
inder retainer
will
allow the cylinder to be removed.
H-91.
Ignition
Switch
Installation
Before installing the lock cylinder
into
the main
switch body,
note
the position of the lock cylinder
retainer.
a.
Place the lock cylinder
into
the main switch
body
with the highest part of the lock cylinder
retainer in line with the lock release
hole
in the
main
switch body.
b. Compress the lock cylinder retainer so that the
lock cylinder can be installed all the way
into
the
main
switch
body
or until the retainer can be
seen
through the pin hole.
c.
Install
wiring harness plug
onto
switch
body
prong connection.
d.
Install
this main switch
body
into
the instruÂ
ment panel opening from the
rear.
e. To make sure that the switch is in its correct position, install the ignition key in the off position.
Then
turn the switch
body
until the key is straight
up and down. Remove the key, install the bezel
nut and secure.
H-92.
PRESTOLITE
STARTING
MOTOR
DAUNTLESS
V-6 and
HURRICANE
F4
ENGINE
The
Prestolite starting motor on the V6
engine
is
similar
in construction (with exception of pinion housings) to the starting motor installed on F4
engines.
The
starter solenoid switch is bolted to the starter
frame.
The
starter is equipped with
sealed-type
absorbent
bronze bearings and no lubricant is required. Service procedures for the Prestolite starter are
given in
Pars.
H-93 to H-107. 202
Page 203 of 376
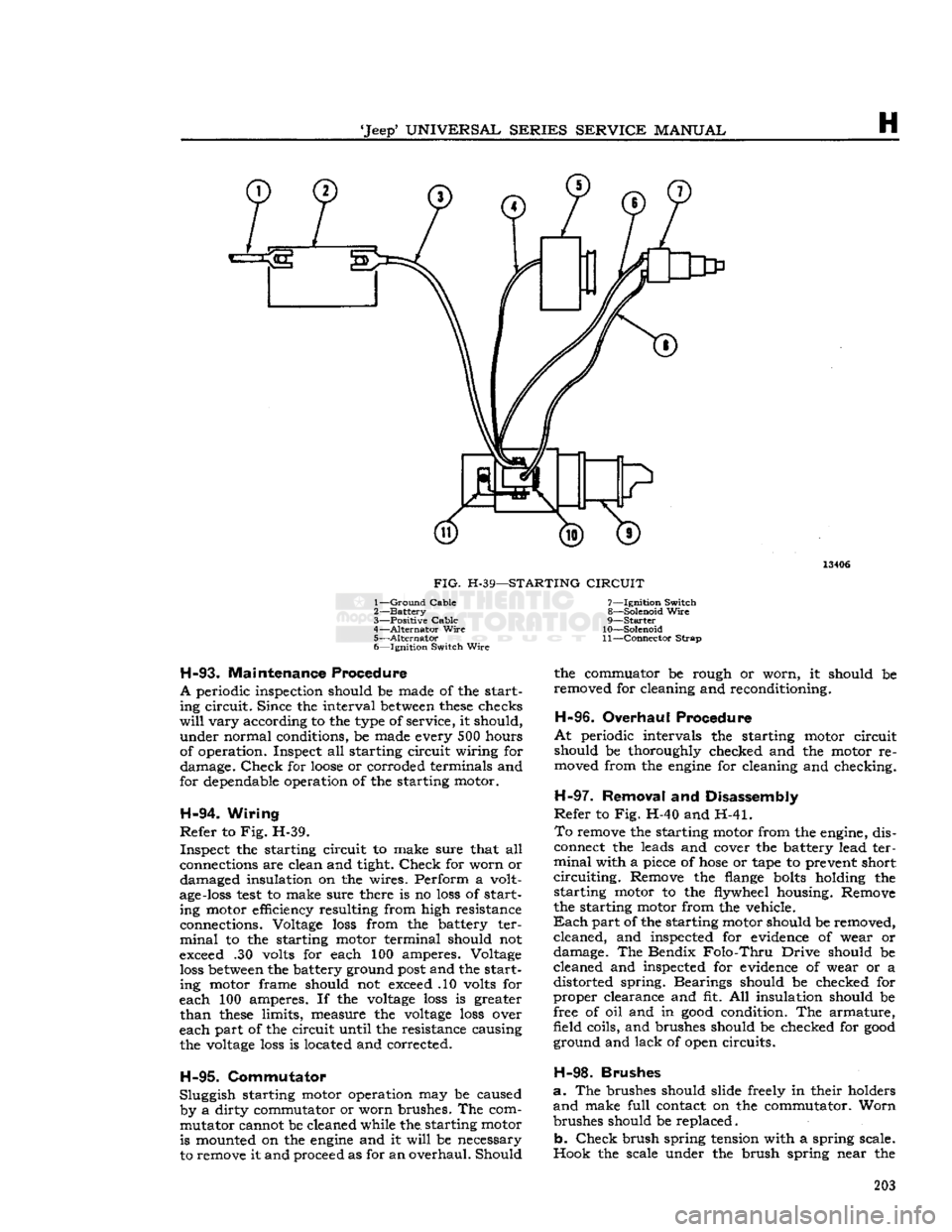
'Jeep*
UNIVERSAL
SERIES SERVICE
MANUAL
H
13406
FIG.
H-39—STARTING
CIRCUIT
1—
Ground
Cable
2—
Battery
3—
Positive Cable
4—
Alternator
Wire
5—
Alternator
6— Ignition Switch
Wire
H-93.
Maintenance Procedure
A
periodic inspection should be made of the start ing circuit. Since the interval
between
these
checks
will
vary according to the type of service, it should, under normal conditions, be made every 500 hours
of operation. Inspect all starting circuit wiring for damage.
Check
for
loose
or corroded terminals and
for dependable operation of the starting motor.
H-94.
Wiring
Refer
to Fig. H-39. Inspect the starting circuit to make sure that all
connections are clean and tight.
Check
for worn or damaged insulation on the wires. Perform a voltÂ
age-loss
test
to make sure there is no
loss
of start ing motor efficiency resulting from high resistance
connections. Voltage
loss
from the battery terÂ
minal
to the starting motor terminal should not
exceed .30 volts for each 100 amperes. Voltage
loss
between
the battery ground
post
and the startÂing motor frame should not exceed .10 volts for
each 100 amperes. If the
voltage
loss
is greater
than
these
limits, measure the
voltage
loss
over
each part of the circuit until the resistance causing the
voltage
loss
is located and corrected.
H-95.
Commutator
Sluggish starting motor operation may be caused by a dirty commutator or worn brushes. The comÂmutator cannot be cleaned while the. starting motor is mounted on the
engine
and it
will
be necessary
to remove it and proceed as for an overhaul. Should 7— Ignition Switch
8— Solenoid
Wire
9—
Starter
10— Solenoid
11—
Connector
Strap
the commuator be rough or worn, it should be
removed for cleaning and reconditioning.
H-96.
Overhaul Procedure
At
periodic intervals the starting motor circuit
should be thoroughly checked and the motor re moved from the
engine
for cleaning and checking.
H-97.
Removal and Disassembly
Refer
to Fig. H-40 and H-41.
To
remove the starting motor from the engine, disÂ
connect the leads and cover the battery lead terÂ
minal
with a piece of
hose
or tape to prevent short
circuiting.
Remove the flange
bolts
holding the starting motor to the flywheel housing. Remove
the starting motor from the vehicle.
Each
part of the starting motor should be removed, cleaned, and inspected for evidence of wear or
damage. The Bendix
Folo-Thru
Drive should be
cleaned and inspected for evidence of wear or a distorted spring. Bearings should be checked for
proper clearance and fit. All insulation should be
free of oil and in
good
condition. The armature,
field coils, and brushes should be checked for
good
ground and lack of open circuits.
H-98.
Brushes
a.
The brushes should slide freely in their holders
and
make full contact on the commutator. Worn
brushes should be replaced.
b.
Check
brush spring tension with a spring scale.
Hook the scale under the brush spring near the 203
Page 204 of 376
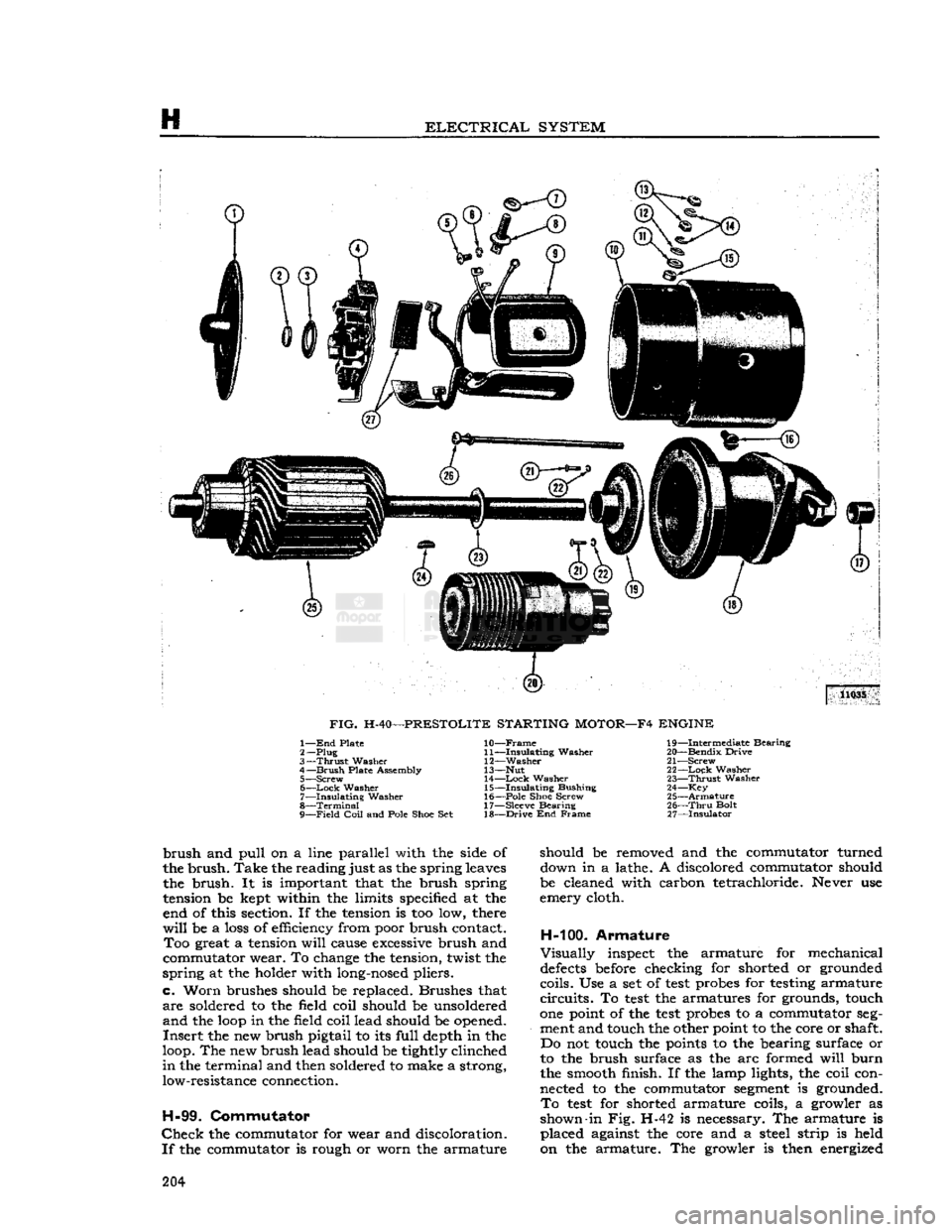
H
ELECTRICAL
SYSTEM
11035
FIG.
H-40—PRESTOLITE STARTING MOTOR—F4 ENGINE 1— End
Plate
2—
Plug
3—
Thrust
Washer
4—
Brush
Plate Assembly 5— Screw
6—
—Lock
Washer
7—
Insulating
Washer
8—
Terminal
9—
Field
Coil
and Pole
Shoe
Set
10—
Frame
11—
Insulating
Washer
12—
Washer
13— Nut 14—
Lock
Washer
15—
Insulating
Bushing
16—
Pole
Shoe
Screw
17— Sleeve Bearing
18—
Drive
End Frame
19—
Intermediate Bearing
20—
Bendix
Drive
21—
Screw
22—
Lock
Washer
23—
Thrust
Washer
24— Key
25—
Armature
26—
Thru
Bolt
27—
Insulator
brush
and
pull
On
a line parallel with the side of
the
brush.
Take
the
reading
just as the spring leaves the
brush.
It is important that the brush spring
tension be kept within the limits specified at the end of this section. If the tension is too low, there
will
be a loss of efficiency from poor brush contact.
Too
great a tension
will
cause excessive brush and
commutator wear. To change the tension, twist the
spring
at the holder with long-nosed pliers,
c.
Worn
brushes should be replaced. Brushes that
are
soldered to the field coil should be unsoldered
and
the
loop
in the field coil lead should be opened.
Insert
the new brush pigtail to its
full
depth in the
loop. The new brush lead should be tightly clinched
in
the terminal and then soldered to make a strong, low-resistance connection.
H-99.
Commutator
Check
the commutator for wear and discoloration.
If
the commutator is rough or worn the armature should be removed and the commutator turned
down in a lathe. A discolored commutator should
be cleaned with carbon tetrachloride. Never use
emery cloth.
H-100.
Armature
Visually
inspect the armature for mechanical
defects
before checking for shorted or grounded
coils. Use a set of
test
probes for testing armature
circuits.
To
test
the armatures for grounds, touch
one point of the
test
probes to a commutator segÂ
ment and touch the other point to the core or shaft. Do not touch the points to the bearing surface or
to the brush surface as the arc formed
will
burn
the smooth finish. If the lamp lights, the coil con nected to the commutator segment is grounded.
To
test
for shorted armature coils, a growler as
shown-in Fig. H-42 is necessary. The armature is placed against the core and a steel strip is held
on the armature. The growler is then energized 204
Page 205 of 376
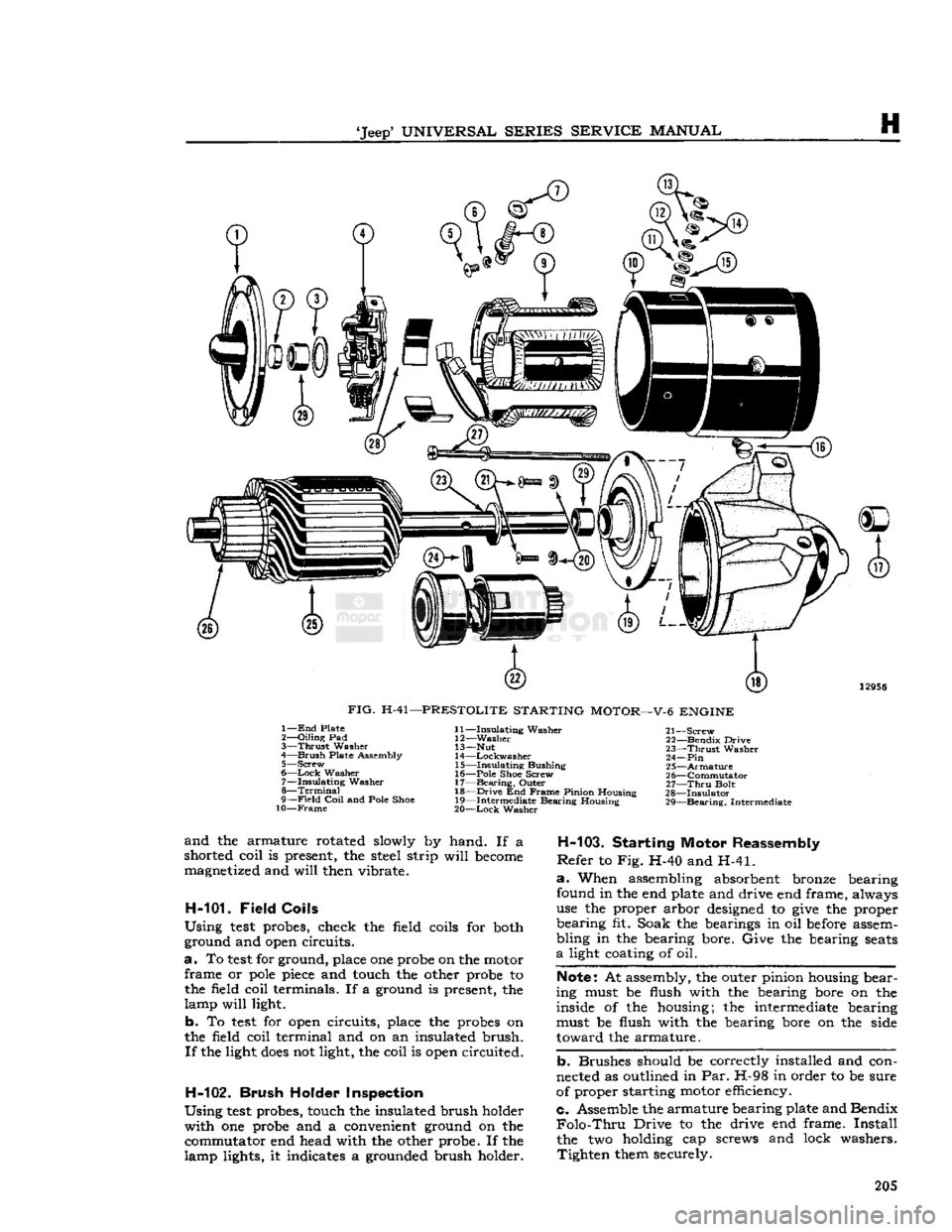
SERIES
SERVICE
MANUAL
H
t
^
12956
FIG.
H-41—PRESTOLITE
STARTING
MOTOR—V-6
ENGINE
1—
End
Plate
2—
Oiling
Pad
3—
Thrust
Washer
4—
Brush
Plate Assembly 5—
Screw
6—
Lock
Washer 7—
Insulating
Washer
8—
Terminal
9—
Field
Coil
and Pole Shoe
10—Frame
11—
Insulating
Washer
12—
Washer
13— Nut
14
—Lockwasher
15—
Insulating
Bushing
16— Pole Shoe Screw
17—
Bearing,
Outer
18—
Drive
End
Frame
Pinion Housing
19— Intermediate Bearing Housing
20—
Lock
Washer 21—
Screw
22— Bendix Drive
23—
Thrust
Washer
24—Pin
25—
Armature
2 6—Commutator
27—
Thru
Bolt
28—
Insulator
29—
Bearing,
Intermediate
and
the armature rotated slowly by hand. If a
shorted coil is present, the steel strip
will
become
magnetized and
will
then vibrate.
H-101-
Field
Coils
Using
test
probes, check the field coils for both
ground and
open
circuits.
a.
To
test
for ground, place one probe on the motor frame or
pole
piece
and touch the other probe to the field coil terminals. If a ground is present, the
lamp
will
light.
b.
To
test
for
open
circuits, place the probes on
the field coil terminal and on an insulated brush.
If
the light,
does
not light, the coil is
open
circuited.
H-102.
Brush
Holder Inspection
Using
test
probes, touch the insulated brush holder with one probe and a convenient ground on the commutator end head with the other probe. If the
lamp lights, it indicates a grounded brush holder.
H-103.
Starting Motor Reassembly
Refer
to Fig. H-40 and H-41.
a.
When assembling absorbent bronze bearing
found in the end plate and drive end frame, always
use the proper arbor
designed
to
give
the proper
bearing fit. Soak the bearings in oil
before
assemÂ
bling in the bearing bore. Give the bearing
seats
a
light coating of oil.
Note:
At assembly, the outer pinion housing bearÂ
ing must be flush with the bearing bore on the inside of the housing; the intermediate bearing
must be flush with the bearing bore on the side
toward the armature.
b.
Brushes should be correctly installed and conÂ
nected as outlined in Par. H-98 in order to be sure
of proper starting motor efficiency.
c. Assemble the armature bearing plate and Bendix
Folo-Thru
Drive to the drive end frame.
Install
the two holding cap screws and lock washers. Tighten them securely. 205
Page 206 of 376
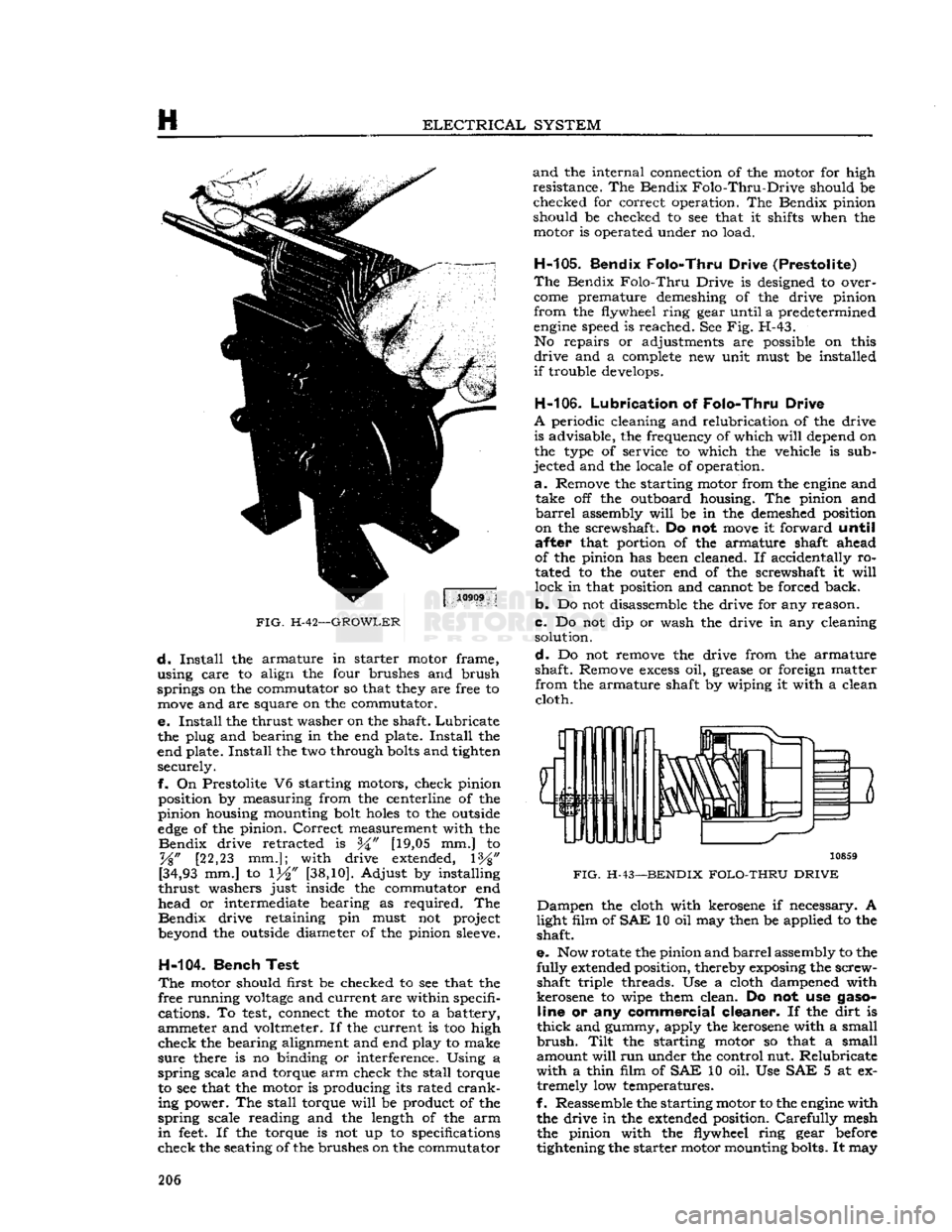
H
ELECTRICAL
SYSTEM
FIG.
H-42—GROWLER
d.
Install
the armature in starter motor frame,
using care to align the four brushes and brush
springs on the commutator so that they are free to
move
and are square on the commutator.
e.
Install
the thrust washer on the shaft.
Lubricate
the plug and bearing in the end plate.
Install
the
end plate.
Install
the two through
bolts
and tighten securely.
f.
On Prestolite V6 starting motors, check pinion position by measuring from the centerline of the
pinion housing mounting bolt
holes
to the outside
edge
of the pinion.
Correct
measurement with the
Bendix
drive retracted is [19,05 mm.] to
%"
[22,23 mm.]; with drive extended, 1%"
[34,93
mm.] to 1^" [38,10]. Adjust by installing
thrust
washers just inside the commutator end
head or intermediate bearing as required. The
Bendix
drive retaining pin must not project
beyond the outside diameter of the pinion
sleeve.
H-104.
Bench Test
The
motor should first be checked to see that the
free running
voltage
and current are within specifi cations. To
test,
connect the motor to a battery,
ammeter and voltmeter. If the current is too high
check
the bearing alignment and end play to make
sure
there is no binding or interference. Using a
spring
scale and torque arm check the stall torque to see that the motor is producing its rated
crankÂ
ing power. The stall torque
will
be product of the
spring
scale reading and the length of the arm
in
feet.
If the torque is not up to specifications
check
the seating of the brushes on the commutator
and
the internal connection of the motor for high
resistance. The Bendix
Folo-Thru-Drive
should be checked for correct operation. The Bendix pinion
should be checked to see that it shifts when the motor is operated under no load.
H-105.
Bendix Folo-Thru Drive (Prestolite)
The
Bendix
Folo-Thru
Drive is designed to overÂ
come
premature demeshing of the drive pinion
from
the flywheel ring gear until a predetermined
engine
speed is reached. See Fig. H-43. No repairs or adjustments are possible on this
drive
and a
complete
new unit must be installed
if
trouble develops.
H-106.
Lubrication
of
Folo-Thru Drive
A
periodic cleaning and relubrication of the drive is advisable, the frequency of which
will
depend on
the type of service to which the vehicle is subÂ
jected and the locale of operation.
a.
Remove the starting motor from the
engine
and take off the outboard housing. The pinion and
barrel
assembly
will
be in the demeshed position
on the screwshaft. Do not
move
it forward
until
after
that portion of the armature shaft ahead
of the pinion has been cleaned. If accidentally roÂ
tated to the outer end of the screwshaft it
will
lock
in that position and cannot be forced back.
b.
Do not disassemble the drive for any reason.
c.
Do not dip or wash the drive in any cleaning solution.
d.
Do not remove the drive from the armature
shaft. Remove
excess
oil, grease or foreign matter
from
the armature shaft by wiping it with a clean cloth.
3
10859
FIG.
H-43—BENDIX
FOLO-THRU DRIVE
Dampen
the cloth with kerosene if necessary. A
light film of
SAE
10 oil may then be applied to the shaft.
e.
Now rotate the pinion and
barrel
assembly to the
fully
extended position, thereby exposing the screw shaft triple threads. Use a cloth dampened with
kerosene to wipe them clean. Do not use
gasoÂ
line
or any
commercial cleaner.
If the dirt is
thick
and gummy, apply the kerosene with a small
brush.
Tilt
the starting motor so that a small
amount
will
run under the control nut. Relubricate
with
a thin film of
SAE
10 oil. Use SAE 5 at ex tremely low temperatures.
f.
Reassemble the starting motor to the
engine
with the drive in the extended position.
Carefully
mesh the pinion with the flywheel ring gear before
tightening the starter motor mounting bolts. It may 206
Page 207 of 376
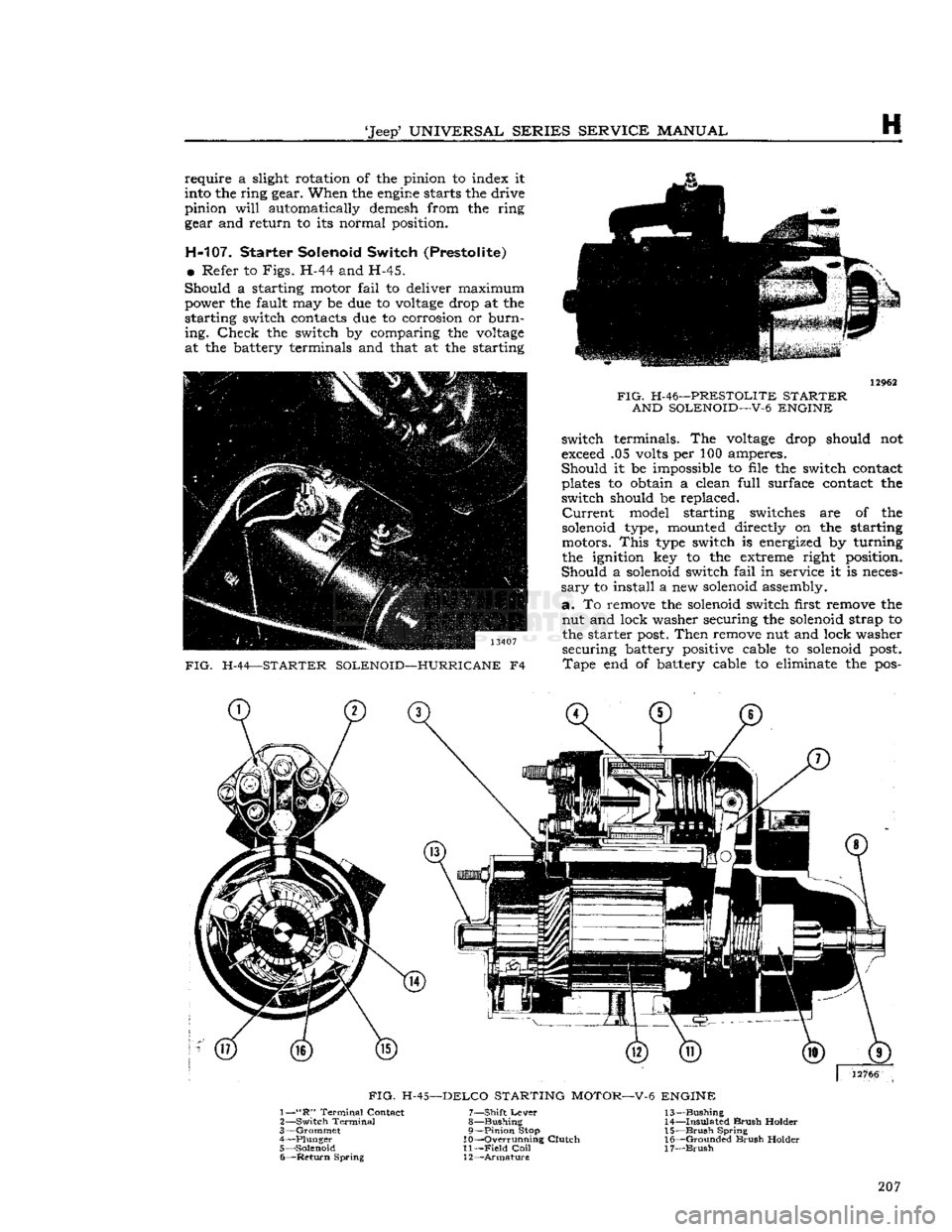
'Jeep'
UNIVERSAL
SERIES
SERVICE
MANUAL
H
require
a slight rotation of the pinion to index it
into the ring gear. When the
engine
starts the drive
pinion
will
automatically demesh from the ring
gear and return to its normal position.
H-107. Starter Solenoid Switch (Prestolite)
•
Refer to
Figs.
H-44 and H-45.
Should
a starting motor
fail
to deliver maximum power the fault may be due to
voltage
drop at the
starting switch contacts due to corrosion or
burnÂ
ing.
Check
the switch by comparing the
voltage
at the battery terminals and that at the starting 13407
FIG.
H-44—STARTER SOLENOID—HURRICANE
F4
FIG.
H-46—PRESTOLITE STARTER
AND SOLENOID—V-6 ENGINE
switch terminals. The
voltage
drop should not
exceed .05 volts per 100 amperes.
Should
it be impossible to file the switch contact
plates to obtain a clean
full
surface contact the
switch should be replaced.
Current
model starting switches are of the
solenoid type, mounted directly on the starting
motors.
This
type switch is energized by turning
the ignition key to the extreme right position.
Should
a solenoid switch
fail
in service it is necesÂ
sary
to install a new solenoid assembly,
a.
To remove the solenoid switch first remove the nut and lock washer securing the solenoid strap to the starter
post.
Then
remove nut and lock washer securing battery positive cable to solenoid
post.
Tape
end of battery cable to eliminate the pos- 207