JEEP CJ 1953 Service Manual
Manufacturer: JEEP, Model Year: 1953, Model line: CJ, Model: JEEP CJ 1953Pages: 376, PDF Size: 19.96 MB
Page 311 of 376
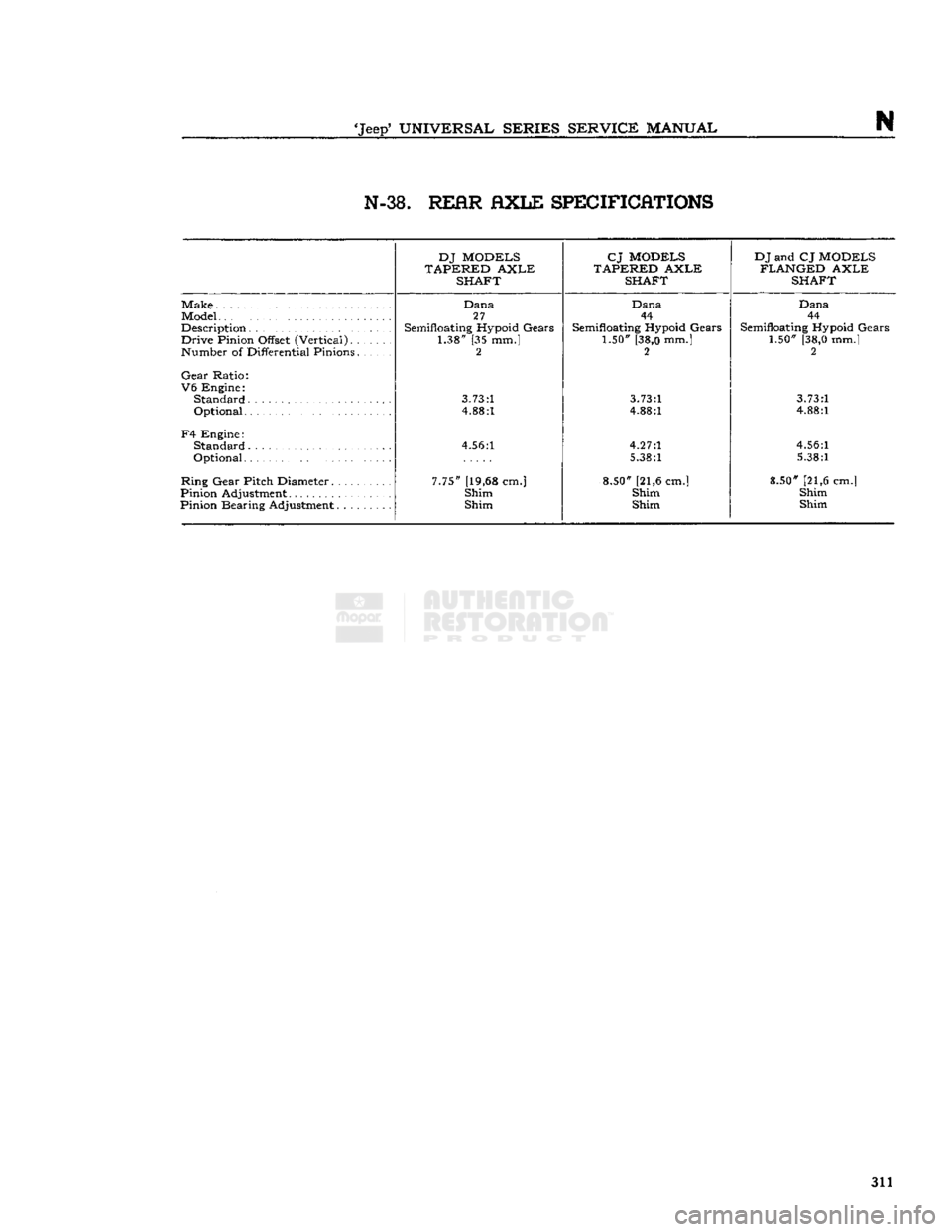
Jeep'
UNIVERSAL SERIES SERVICE
MANUAL
N N-38.
REfiR flXLE SPECIFICATIONS
DJ MODELS
TAPERED AXLE SHAFT CJ MODELS
TAPERED AXLE SHAFT DJ and CJ MODELS
FLANGED AXLE SHAFT
Make
Model
Description Drive Pinion Offset (Vertical)
Number of Differential Pinions.......
Gear Ratio:
V6 Engine:
Standard
Optional
F4 Engine: Standard
Optional
Ring Gear Pitch Diameter
Pinion Adjustment
Pinion Bearing Adjustment Dana
27
Semifloating Hypoid Gears 1.38" [35 mm.] 2
3.73:1
4.88:1
4.56:1
7.75" [19,68 cm.] Shim
Shim Dana
44
Semifloating Hypoid Gears 1.50" [38,0 mm.] 2
3.73:1
4.88:1
4.27:1
5.38:1
8.50" [21,6 cm.] Shim Shim Dana
44
Semifloating Hypoid Gears 1.50" [38,0 mm.] 2
3.73:1
4.88:1
4.56:1
5.38:1
8.50" [21,6 cm.] Shim Shim 311
Page 312 of 376
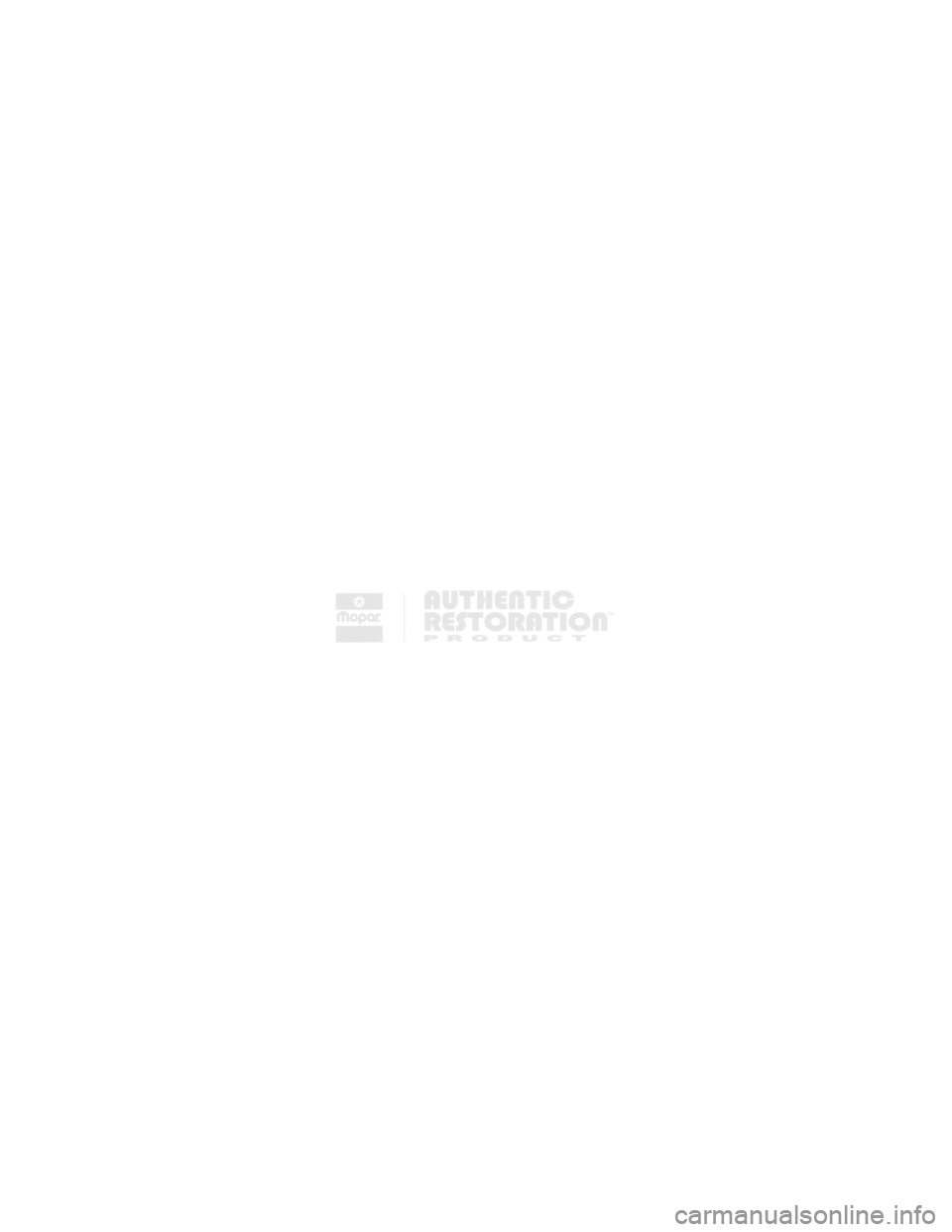
Page 313 of 376
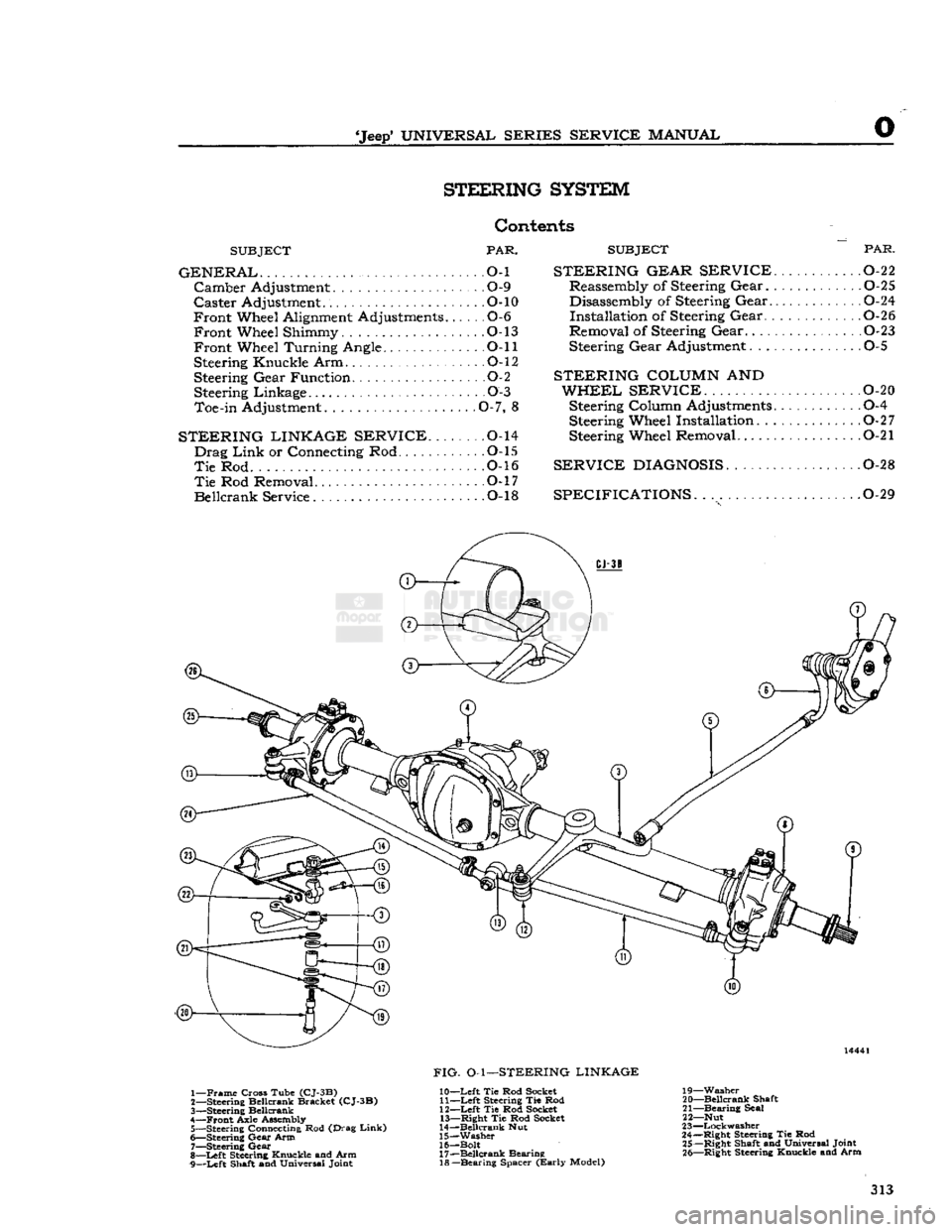
'Jeep'
UNIVERSAL
SERIES SERVICE
MANUAL
STEERING SYSTEM
Contents
SUBJECT
PAR.
GENERAL......
O-l
Camber
Adjustment 0-9
Caster
Adjustment. .0-10
Front
Wheel Alignment Adjustments.....
.
0-6
Front
Wheel Shimmy 0-13
Front
Wheel Turning Angle Oil
Steering Knuckle Arm O-l2
Steering
Gear
Function 0-2
Steering Linkage 0-3
Toe-in
Adjustment 0-7, 8
STEERING LINKAGE SERVICE..
O-l4
Drag
Link
or Connecting Rod O-l5
Tie
Rod 0-16
Tie
Rod Removal.. O-l7
Beilcrank
Service O-l8
SUBJECT
PAR.
STEERING GEAR SERVICE
.0-22 Reassembly of Steering
Gear
0-25 Disassembly of Steering
Gear
0-24 Installation of Steering
Gear
0-26
Removal
of Steering
Gear
0-23
Steering
Gear
Adjustment. . 0-5
STEERING
COLUMN
AND
WHEEL SERVICE.
..................
.0-20
Steering Column Adjustments 0-4
Steering Wheel Installation 0-27
Steering Wheel Removal 0-21
SERVICE
DIAGNOSIS.
. 0-28
SPECIFICATIONS.
.0-29
<§>-
i©1
CJ-3B
0
0 0
®
1—
Frame
Cross Tube
(CJ-3B)
2— Steering Beilcrank Bracket
(CJ-3B)
3—
Steering Beilcrank
4—
Front
Axle Assembly 5— Steering Connecting Rod (Drag
Link)
6— Steering
Gear
Arm
7—
Steering
Gear
8—
Left
Steering Knuckle and Arm
9—
Left
Shaft and Universal Joint
FIG.
O-l—STEERING LINKAGE
10—
Left
Tie Rod Socket 11—
Left
Steering Tie Rod
12—
Left
Tie Rod Socket 13—
Right
Tie Rod Socket
14—
Beilcrank
Nut
15—
Washer
16— Bolt 17—
Beilcrank
Bearing 18—
Bearing
Spacer
(Early
Model) 19—
Washer
20—
Beilcrank
Shaft
21—
Bearing
Seal
22— Nut
23—
Lockwasher
24—
Right
Steering Tie Rod 25—
Right
Shaft and Universal Joint 26—
Right
Steering Knuckle and Arm 313
Page 314 of 376
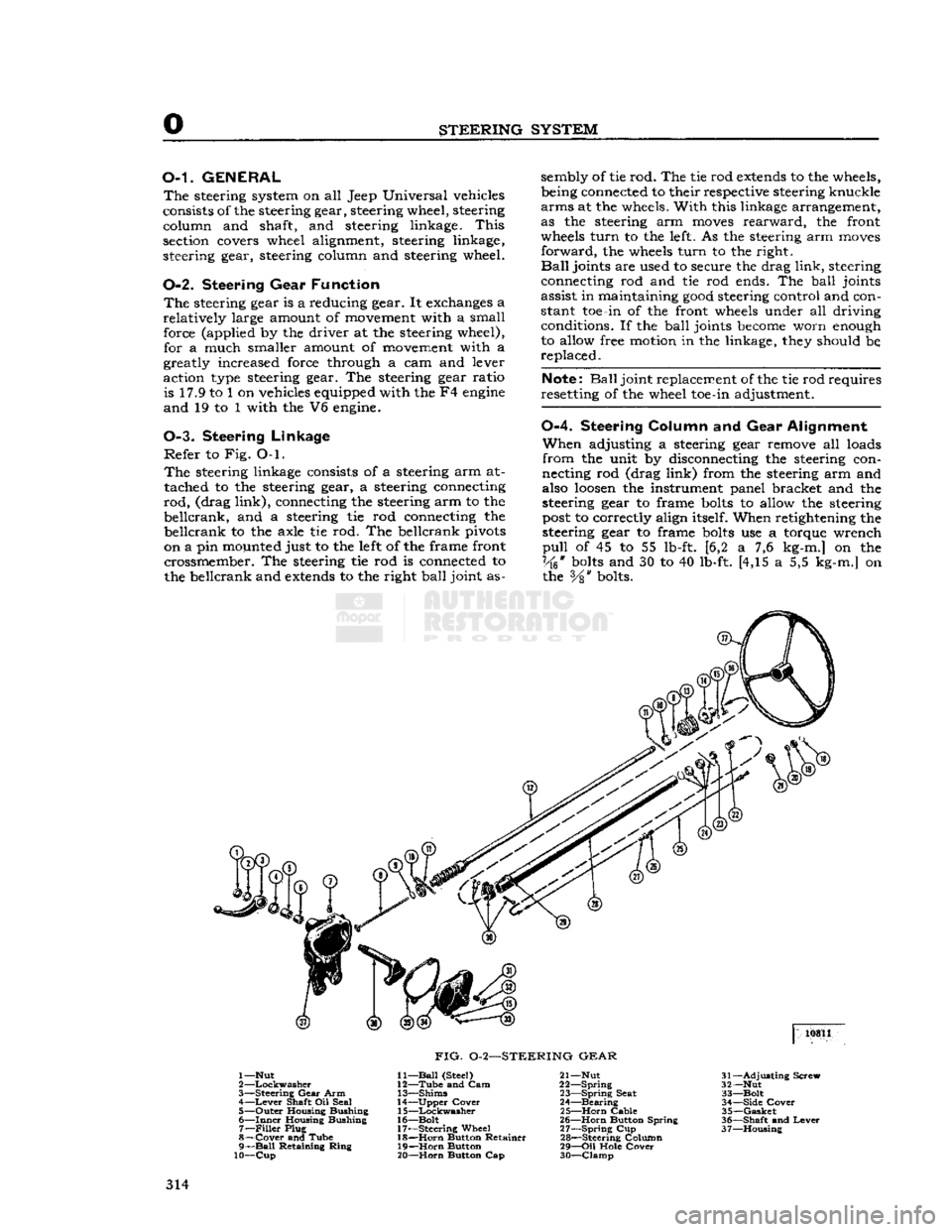
STEERING
SYSTEM
O-L
GENERAL
The
steering system on all Jeep Universal vehicles
consists of the steering gear, steering wheel, steering column and shaft, and steering linkage.
This
section covers wheel alignment, steering linkage,
steering gear, steering column and steering wheel.
0-2. Steering
Gear
Function
The
steering gear is a reducing gear. It exchanges a
relatively
large amount of movement with a small force (applied by the driver at the steering wheel), for a much smaller amount of movement with a
greatly increased force through a cam and lever
action type steering gear. The steering gear ratio is 17.9 to 1 on vehicles equipped with the F4
engine
and
19 to 1 with the V6 engine.
0-3. Steering
Linkage
Refer
to Fig. O-l.
The
steering linkage consists of a steering arm at
tached to the steering gear, a steering connecting
rod,
(drag
link),
connecting the steering arm to the
beilcrank,
and a steering tie rod connecting the
beilcrank
to the axle tie rod. The beilcrank pivots
on a pin mounted just to the left of the frame front crossmember. The steering tie rod is connected to
the beilcrank and
extends
to the right
ball
joint as sembly of tie rod. The tie rod
extends
to the wheels,
being connected to their respective steering knuckle
arms
at the wheels.
With
this linkage arrangement,
as the steering arm
moves
rearward,
the front
wheels
turn
to the left. As the steering arm
moves
forward,
the wheels
turn
to the right.
Ball
joints are used to secure the drag
link,
steering
connecting rod and tie rod ends. The
ball
joints
assist in maintaining
good
steering control and con
stant toe-in of the front wheels under all driving conditions. If the
ball
joints
become
worn enough
to allow free motion in the linkage, they should be,
replaced.
Note:
Ball
joint replacement of the tie rod requires
resetting of the wheel toe-in adjustment.
0-4.
Steering
Column
and Gear
Alignment
When
adjusting a steering gear remove all loads
from
the unit by disconnecting the steering con
necting rod (drag
link)
from the steering arm and
also
loosen
the instrument panel bracket and the
steering gear to frame
bolts
to allow the steering
post
to correctly align itself. When retightening the
steering gear to frame
bolts
use a torque wrench
pull
of 45 to 55 lb-ft. [6,2 a 7,6 kg-m.] on the
Vk*
bolts
and 30 to 40 lb-ft. [4,15 a 5,5 kg-m.] on the
Vs"
bolts. 10811
FIG.
0-2—STEERING
GEAR
1—Nut
2
—Lockwasher
3—
Steering
Gear
Arm 4—
Lever
Shaft Oil Seal
5—
Outer
Housing Bushing
6—
Inner
Housing Bushing 7—
Filler
Plug
8—
Cover
and Tube
9—
Ball
Retaining
Ring
10—Cup
11—
Ball
(Steel)
12—
Tube
and Cam
13—
Shims
14—
Upper
Cover
15—
Lockwasher
16—
Bolt
17—
Steering
Wheel 18—
Horn
Button Retainer
19—
Horn
Button
20—
Horn
Button Cap 21— Nut
22—
Spring
23—
Spring
Seat
24—
Bearing
25—
Horn
Cable
26—
Horn
Button Spring
27—
Spring
Cup
28—
Steering Column
29—
Oil
Hole
Cover
30—
Clamp
31—
Adjusting
Screw
32— Nut
33—
Bolt
34—
Side
Cover
35—
Gasket
36—
Shaft
and
Lever
37—
Housing
314
Page 315 of 376
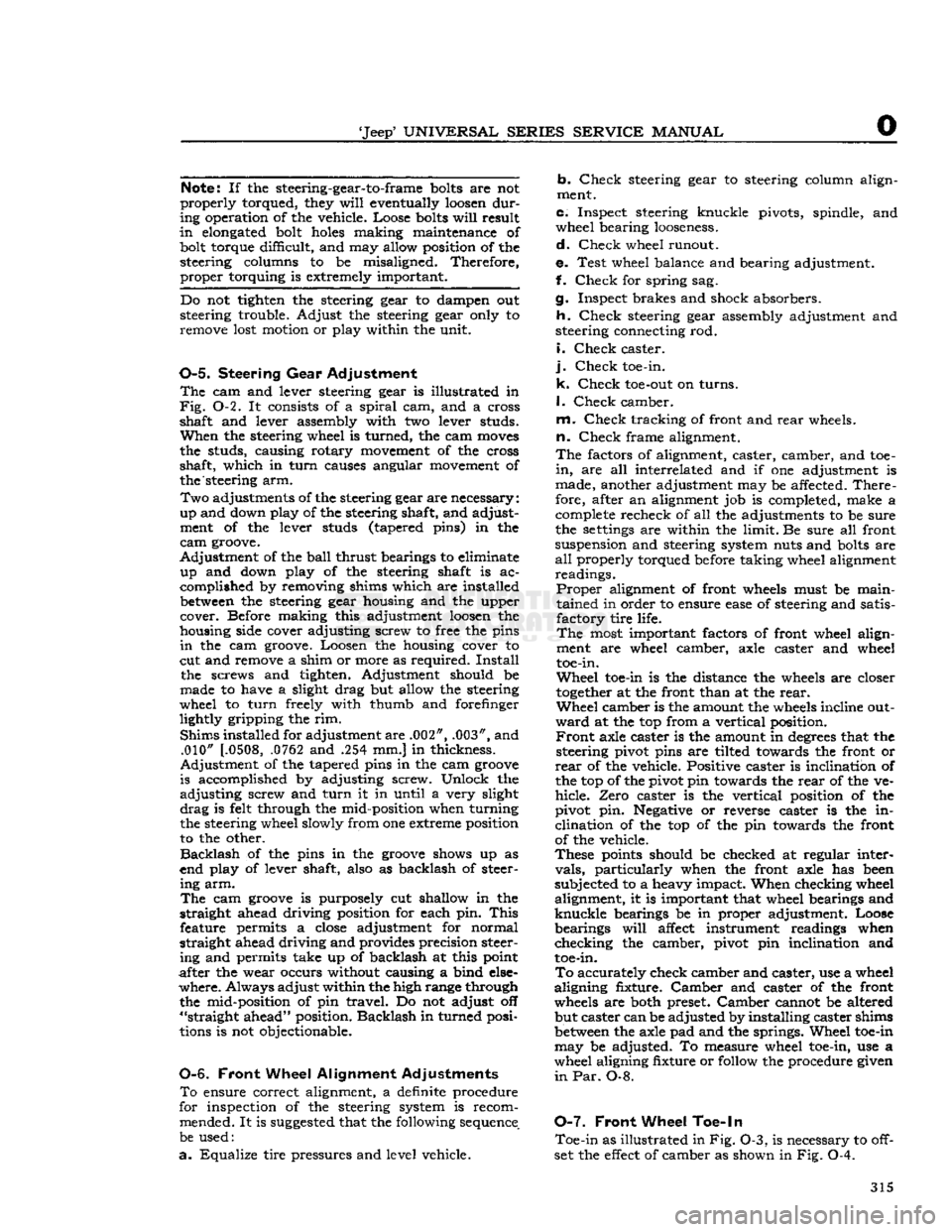
'Jeep'
UNIVERSAL
SERIES SERVICE
MANUAL
O Note:
If the steering-gear-to-frame
bolts
are not
properly
torqued, they
will
eventually
loosen
dur
ing operation of the vehicle. Loose
bolts
will
result
in
elongated
bolt
holes
making maintenance of bolt torque difficult, and may allow position of the
steering columns to be misaligned. Therefore,
proper
torquing is extremely important.
Do not tighten the steering gear to dampen out
steering trouble. Adjust the steering gear only to
remove lost motion or play within the unit.
0-5. Steering
Gear
Adjustment
The
cam and lever steering gear is illustrated in
Fig.
0-2. It consists of a
spiral
cam, and a cross shaft and lever assembly with two lever studs.
When
the steering wheel is turned, the cam
moves
the studs, causing rotary movement of the cross
shaft, which in
turn
causes angular movement of
the*steering arm.
Two
adjustments of the steering gear are necessary:
up and down play of the steering shaft, and adjustment of the lever studs (tapered pins) in the
cam
groove.
Adjustment
of the
ball
thrust bearings to eliminate up and down play of the steering shaft is ac
complished by removing shims which are installed
between
the steering gear housing and the upper
cover. Before making this adjustment
loosen
the
housing side cover adjusting screw to free the pins
in
the cam groove. Loosen the housing cover to
cut and remove a shim or more as required.
Install
the screws and tighten. Adjustment should be
made to have a slight drag but allow the steering
wheel to
turn
freely with thumb and forefinger
lightly gripping the rim.
Shims
installed for adjustment are .002*, .003", and .010"
[.0508,
.0762
and .254 mm.] in thickness.
Adjustment
of the tapered pins in the cam
groove
is accomplished by adjusting screw. Unlock the
adjusting
screw and
turn
it in until a very slight
drag
is felt through the mid-position when turning
the steering wheel slowly from one extreme position
to the other.
Backlash
of the pins in the
groove
shows up as
end play of lever shaft, also as backlash of steer ing arm.
The
cam
groove
is purposely cut shallow in the
straight
ahead driving position for each pin.
This
feature permits a
close
adjustment for normal
straight
ahead driving and provides precision steer ing and permits take up of backlash at this point
after the wear occurs without causing a bind else
where.
Always
adjust within the high range through
the mid-position of pin travel. Do not adjust off
"straight
ahead" position.
Backlash
in turned posi
tions is not objectionable.
0-6.
Front
Wheel Alignment Adjustments
To
ensure correct alignment, a definite procedure
for inspection of the steering system is recom mended. It is
suggested
that the following sequence
be used:
a.
Equalize
tire pressures and level vehicle.
b.
Check
steering gear to steering column align
ment.
c.
Inspect steering knuckle pivots, spindle, and
wheel bearing
looseness.
d.
Check
wheel runout.
e.
Test wheel balance and bearing adjustment.
f.
Check
for spring sag.
g.
Inspect brakes and shock absorbers.
h.
Check
steering gear assembly adjustment and
steering connecting rod.
i.
Check
caster,
j.
Check
toe-in.
k.
Check
toe-out
on turns.
I.
Check
camber.
m.
Check
tracking of front and
rear
wheels,
n.
Check
frame alignment.
The
factors of alignment, caster, camber, and toe-
in,
are all interrelated and if one adjustment is
made, another adjustment may be affected.
There
fore, after an alignment job is completed, make a
complete recheck of all the adjustments to be sure
the
settings
are within the limit. Be sure all front
suspension and steering system nuts and
bolts
are
all
properly torqued before taking wheel alignment readings.
Proper
alignment of front wheels must be main
tained in order to ensure
ease
of steering and satisfactory tire life.
The
most important factors of front wheel alignment are wheel camber, axle caster and wheel
toe-in.
Wheel
toe-in is the distance the wheels are closer
together
at the front than at the
rear.
Wheel
camber is the amount the wheels incline out
ward
at the top from a vertical position.
Front
axle caster is the amount in
degrees
that the
steering pivot pins are tilted towards the front or
rear
of the vehicle. Positive caster is inclination of
the top of the pivot pin towards the
rear
of the ve
hicle.
Zero caster is the vertical position of the
pivot pin. Negative or reverse caster is the in
clination
of the top of the pin towards the front
of the vehicle.
These
points should be checked at regular inter
vals,
particularly when the front axle has been
subjected to a heavy impact. When checking wheel alignment, it is important that wheel bearings and
knuckle
bearings be in proper adjustment. Loose bearings
will
affect instrument readings when
checking
the camber, pivot pin inclination and
toe-in.
To
accurately check camber and caster, use a wheel
aligning fixture.
Camber
and caster of the front
wheels are both preset.
Camber
cannot be altered
but caster can be adjusted by installing caster shims
between
the axle pad and the springs. Wheel toe-in
may
be adjusted. To measure wheel toe-in, use a
wheel aligning fixture or follow the procedure given
in Par.
0-8.
0-7.
Front Wheel Toe-in
Toe-in
as illustrated in
Fig.
0-3, is necessary to
off
set the
effect
of camber as shown in Fig. Q-4. 315
Page 316 of 376
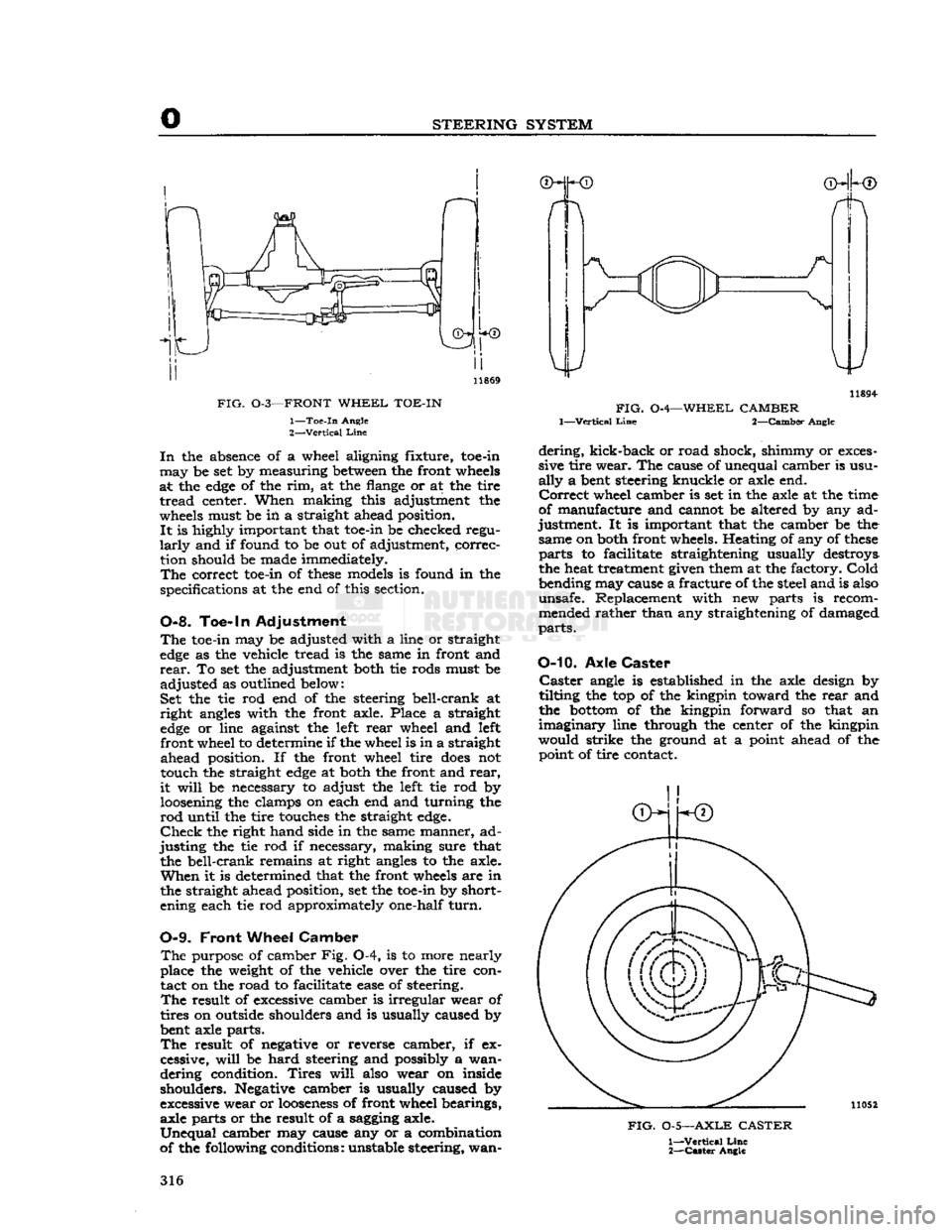
o
STEERING SYSTEM
FIG.
0-3—FRONT
WHEEL
TOE-IN
1—
Toe-in
Angle
2—
Vertical
Line
In
the absence of a wheel aligning fixture, toe-in
may
be set by measuring
between
the front wheels
at the
edge
of the rim, at the flange or at the tire
tread
center. When making this adjustment the
wheels must be in a straight ahead position.
It
is highly important that toe-in be checked regu
larly
and if found to be out of adjustment, correc tion should be made immediately.
The
correct toe-in of
these
models is found in the
specifications at the end of this section.
0-8. Toe-in Adjustment
The
toe-in may be adjusted with a line or straight
edge
as the vehicle tread is the same in front and
rear.
To set the adjustment both tie rods must be
adjusted
as outlined below:
Set the tie rod end of the steering bell-crank at
right
angles with the front axle. Place a straight
edge
or line against the left
rear
wheel and left front wheel to determine if the wheel is in a straight
ahead
position. If the front wheel tire
does
not touch the straight
edge
at both the front and
rear,
it
will
be necessary to adjust the left tie rod by loosening the clamps on each end and turning the
rod
until the tire touches the straight
edge.
Check
the right hand side in the same manner, ad
justing
the tie rod if necessary, making sure that the bell-crank remains at right angles to the axle.
When
it is determined that the front wheels are in the straight ahead position, set the toe-in by short
ening each tie rod approximately one-half
turn.
0-9.
Front
Wheel
Camber
The
purpose of camber Fig. 0-4, is to more nearly
place the weight of the vehicle over the tire con tact on the road to facilitate
ease
of steering.
The
result of excessive camber is irregular wear of
tires on outside shoulders and is usually caused by
bent axle parts.
The
result of negative or reverse camber, if ex
cessive,
will
be
hard
steering and possibly a wan
dering
condition.
Tires
will
also wear on inside shoulders. Negative camber is usually caused by
excessive wear or
looseness
of front wheel bearings, axle parts or the result of a sagging axle.
Unequal
camber may cause any or a combination
of the following conditions: unstable steering, wan- 11894-
FIG.
0-4—WHEEL CAMBER
1—Vertical
Line
2—Camber Angle
dering,
kick-back or road shock, shimmy or exces
sive tire wear. The cause of unequal camber is usu
ally
a bent steering knuckle or axle end.
Correct
wheel camber is set in the axle at the time
of manufacture and cannot be altered by any ad
justment. It is important that the camber be the same on both front wheels. Heating of any of
these
parts
to facilitate straightening usually destroys
the heat treatment given them at the factory.
Cold
bending may cause a fracture of the steel and is also
unsafe. Replacement with new parts is recom mended rather than any straightening of damaged
parts.
O-10.
Axle
Caster Caster
angle is established in the axle design by
tilting the top of the kingpin toward the
rear
and
the
bottom
of the kingpin forward so that an
imaginary
line through the center of the kingpin
would strike the ground at a point ahead of the point of tire contact.
FIG.
0-5—AXLE
CASTER
1—
Vertical
Line
2—
Caster
Angle
316
Page 317 of 376
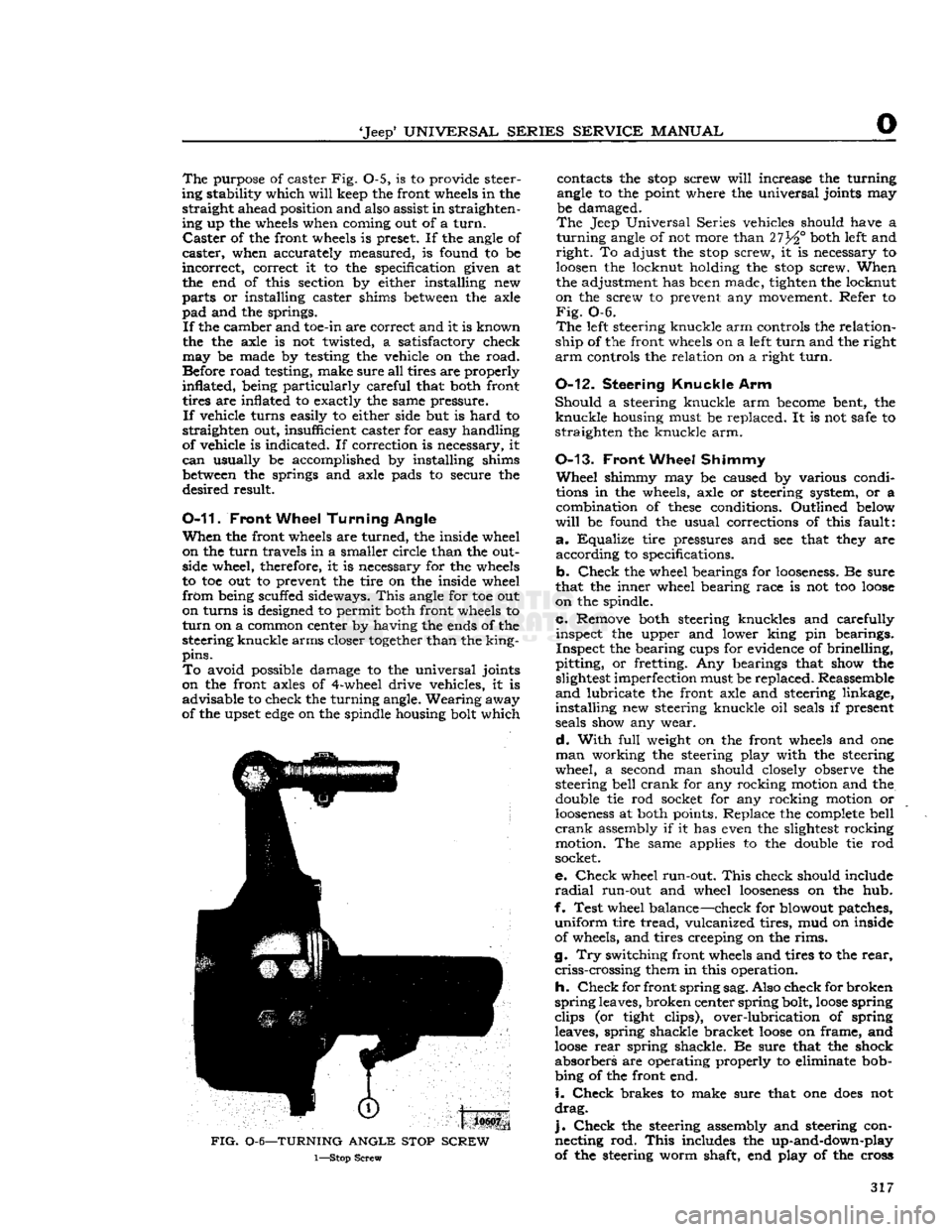
'Jeep'
UNIVERSAL SERIES SERVICE
MANUAL
The
purpose of caster Fig. O-S, is to provide steer
ing stability which
will
keep the front wheels in the
straight
ahead position and also assist in straighten
ing up the wheels when coming out of a
turn.
Caster
of the front wheels is preset. If the angle of
caster,
when accurately measured, is found to be
incorrect,
correct it to the specification given at
the end of this section by either installing new
parts
or installing caster shims
between
the axle
pad
and the springs.
If
the camber and toe-in are correct and it is known
the the axle is not twisted, a satisfactory check
may
be made by testing the vehicle on the road.
Before road testing, make sure all tires are properly
inflated,
being particularly careful that both front
tires are inflated to exactly the same pressure.
If
vehicle turns easily to either side but is
hard
to
straighten out, insufficient caster for easy handling of vehicle is indicated. If correction is necessary, it
can
usually be accomplished by installing shims
between
the springs and axle pads to secure the
desired
result.
0-11-
Front
Wheel
Turning
Angle
When
the front wheels are turned, the inside wheel
on the
turn
travels in a smaller circle than the outside wheel, therefore, it is necessary for the wheels
to toe out to prevent the tire on the inside wheel
frOm
being scuffed sideways.
This
angle for toe out
on turns is designed to permit both front wheels to
turn
on a common center by having the ends of the
steering
knuckle
arms closer
together
than the king
pins.
To
avoid possible damage to the universal joints
on the front axles of 4-wheel drive vehicles, it is advisable to check the turning angle.
Wearing
away
of the upset
edge
on the spindle housing bolt which
10607
FIG.
0-6—TURNING
ANGLE
STOP
SCREW
1—Stop
Screw
contacts the
stop
screw
will
increase the turning
angle to the point where the universal joints may
be damaged.
The
Jeep Universal Series vehicles should have a
turning
angle of not more than 27^° both left and
right.
To adjust the
stop
screw, it is necessary to
loosen
the locknut holding the
stop
screw. When
the adjustment has been made, tighten the locknut
on the screw to prevent any movement. Refer to
Fig.
O 6.
The
left steering knuckle arm controls the relation
ship of the front wheels on a left
turn
and the right
arm
controls the relation on a right
turn.
0-12. Steering
Knuckle
Arm
Should
a steering knuckle arm
become
bent, the
knuckle
housing must be replaced. It is not safe to
straighten the knuckle arm.
0-13.
Front
Wheel
Shimmy
Wheel
shimmy may be caused by various condi
tions in the wheels, axle or steering system, or a
combination of
these
conditions. Outlined below
will
be found the usual corrections of this fault:
a.
Equalize
tire pressures and see that they are
according
to specifications.
b.
Check
the wheel bearings for
looseness.
Be sure
that the inner wheel bearing race is not too
loose
on the spindle.
c.
Remove both steering knuckles and carefully inspect the upper and lower king pin bearings.
Inspect
the bearing cups for evidence of brinelling,
pitting, or fretting. Any bearings that show the slightest imperfection must be
replaced.
Reassemble
and
lubricate the front axle and steering linkage,
installing
new steering knuckle oil seals if present
seals show any wear.
d.
With
full
weight on the front wheels and one
man
working the steering play with the steering
wheel, a second man should closely observe the steering bell
crank
for any rocking motion and the
double tie rod socket for any rocking motion or
looseness
at both points. Replace the complete bell
crank
assembly if it has even the slightest rocking motion. The same applies to the double tie rod
socket.
e.
Check
wheel run-out.
This
check should include
radial
run-out and wheel
looseness
on the hub.
f- Test wheel balance—check for blowout patches,
uniform
tire tread, vulcanized tires, mud on inside
of wheels, and tires creeping on the
rims.
g.
Try
switching front wheels and tires to the
rear,
criss-crossing
them in this operation.
h.
Check
for front
spring
sag. Also check for broken
spring
leaves, broken center
spring
bolt,
loose
spring
clips
(or tight clips), over-lubrication of spring leaves, spring shackle bracket
loose
on frame, and
loose
rear
spring shackle. Be sure that the shock
absorbers
are operating properly to eliminate bobbing of the front end.
i.
Check
brakes to make sure that one
does
not
drag.
j.
Check
the steering assembly and steering con necting rod.
This
includes the up-and-down-play
of the steering worm shaft, end play of the cross 317
Page 318 of 376
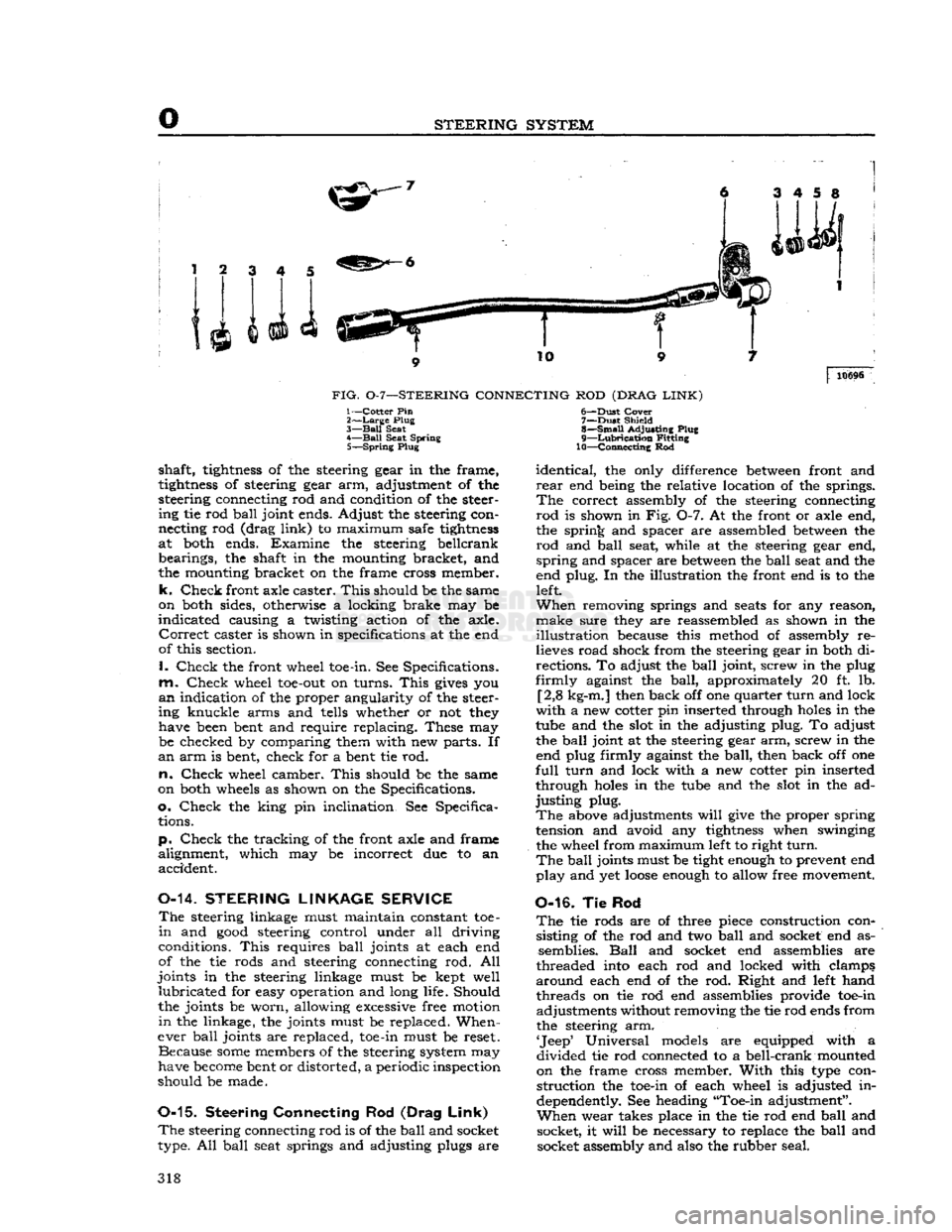
o
STEERING
SYSTEM
10
FIG.
0-7—STEERING
CONNECTING
ROD
(DRAG
LINK)
10696
1—Cotter Pin
2>—Large
Plug
3—
Ball
Seat
4—
Ball
Seat Spring 5—
Spring
Plug
shaft,
tightness
of the steering gear in the frame,
tightness
of steering gear arm, adjustment of the
steering connecting rod and condition of the steer ing tie rod
ball
joint ends. Adjust the steering con
necting rod (drag
link)
to maximum safe
tightness
at both ends. Examine the steering beilcrank bearings, the shaft in the mounting bracket, and
the mounting bracket on the frame cross member,
k.
Check
front axle caster.
This
should be the same
on both sides, otherwise a locking brake may be
indicated
causing a twisting action of the axle.
Correct
caster is shown in specifications at the end
of this section.
I.
Check
the front wheel toe-in. See Specifications,
m.
Check
wheel
toe-out
on turns.
This
gives
you
an
indication of the proper angularity of the steer
ing knuckle arms and tells whether or not they have been bent and require replacing. These may be checked by comparing them with new parts. If
an
arm is bent, check for a bent tie rod.
n.
Check
wheel camber.
This
should be the same
on both wheels as shown on the Specifications,
o.
Check
the king pin inclination. See Specifica tions.
p.
Check
the tracking of the front axle and frame
alignment, which may be incorrect due to an accident.
0-14.
STEERING
LINKAGE
SERVICE
The
steering linkage must maintain constant toe-
in
and
good
steering control under all driving
conditions.
This
requires
ball
joints at each end
of the tie rods and steering connecting rod. All
joints in the steering linkage must be kept well
lubricated
for easy operation and long life. Should
the joints be worn, allowing excessive free motion
in
the linkage, the joints must be replaced. When
ever
ball
joints are replaced, toe-in must be reset. Because
some
members of the steering system may
have
become
bent or distorted, a periodic inspection
should be made.
0-15.
Steering Connecting
Rod
(Drag
Link)
The
steering connecting rod is of the
ball
and socket
type. All
ball
seat springs and adjusting plugs are 6—
-Dust
Cover
7—
Dust
Shield
8—
Small
Adjusting Plug
9—
Lubrication
Fitting
10—Connecting Rod
identical,
the only difference
between
front and
rear
end being the relative location of the springs.
The
correct assembly of the steering connecting
rod
is shown in Fig. 0-7. At the front or axle end,
the spring and spacer are assembled
between
the
rod
and
ball
seat, while at the steering gear end,
spring
and spacer are
between
the
ball
seat and the
end plug. In the illustration the front end is to the left.
When
removing springs and
seats
for any reason,
make
sure they are reassembled as shown in the
illustration
because this method of assembly re
lieves road shock from the steering gear in both di
rections. To adjust the
ball
joint, screw in the plug
firmly
against the
ball,
approximately 20 ft. lb. [2,8 kg-m.] then back off one quarter
turn
and lock
with
a new cotter pin inserted through
holes
in the
tube and the slot in the adjusting plug. To adjust the
ball
joint at the steering gear arm, screw in the end plug firmly against the
ball,
then back off one
full
turn
and lock with a new cotter pin inserted
through
holes
in the tube and the slot in the ad
justing
plug.
The
above adjustments
will
give
the proper spring
tension and avoid any
tightness
when swinging
the wheel from maximum left to right
turn.
The
ball
joints must be tight enough to prevent end
play
and yet
loose
enough to allow free movement.
0-16. Tie Rod
The
tie rods are of three piece construction consisting of the rod and two
ball
and socket end as semblies.
Ball
and socket end assemblies are
threaded into each rod and locked with clamps,
around
each end of the rod. Right and left hand threads on tie rod end assemblies provide toe-in adjustments without removing the tie rod ends from
the steering arm.
'Jeep'
Universal models are equipped with a
divided
tie rod connected to a bell-crank mounted
on the frame cross member.
With
this type con
struction
the toe-in of each wheel is adjusted in
dependently. See heading "Toe-in adjustment".
When
wear takes place in the tie rod end
ball
and socket, it
will
be necessary to replace the
ball
and socket assembly and also the rubber seal. 318
Page 319 of 376
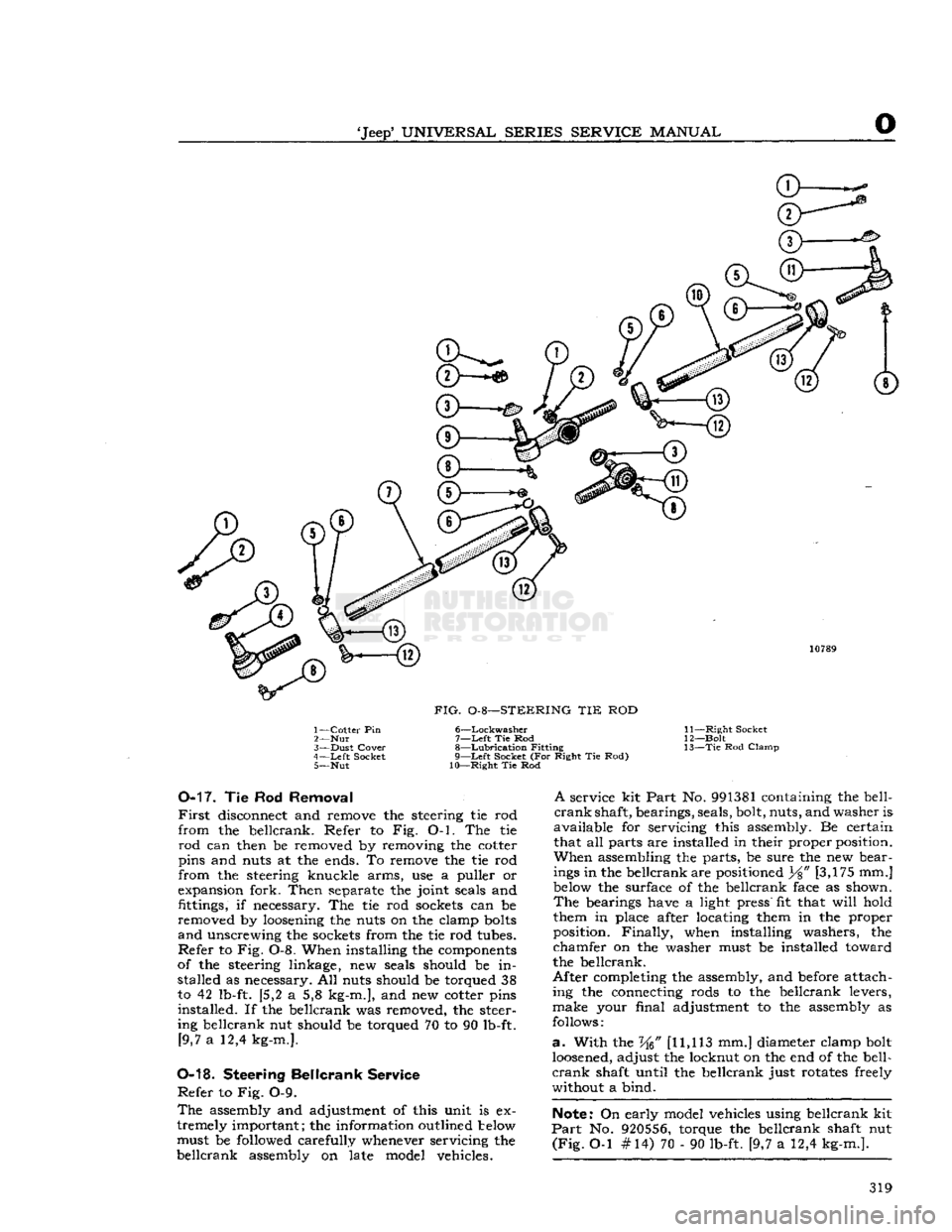
'Jeep*
UNIVERSAL
SERIES SERVICE
MANUAL
D
©—P3
10789
FIG.
0-8—STEERING TIE ROD
1—
Cotter
Pin 6—Lockwasher
2—
Nut 7—Left Tie Rod
3—
Dust
Cover
8—Lubrication
Fitting
4—
Left
Socket 9—Left Socket (For Right Tie Rod) 5— Nut 10—Right Tie Rod 11—
Right
Socket
12—
Bolt
13— Tie
Rod
Clamp
0-17.
Tie Rod
Removal
First
disconnect and remove the steering tie rod
from
the bellcrank. Refer to Fig. O-l. The tie
rod
can then be removed by removing the cotter
pins and
nuts
at the
ends.
To remove the tie rod
from
the steering knuckle arms, use a puller or
expansion
fork.
Then
separate
the
joint
seals
and
fittings,
if
necessary.
The tie rod
sockets
can be
removed by loosening the
nuts
on the clamp bolts
and unscrewing the
sockets
from
the tie rod
tubes.
Refer to Fig. 0-8. When installing the
components
of
the steering linkage, new
seals
should be in stalled as
necessary.
All
nuts
should be torqued 38
to 42
lb-ft.
{5,2 a 5,8
kg-m.],
and new cotter pins
installed.
If the bellcrank was removed, the
steer
ing
bellcrank nut should be torqued 70 to 90
lb-ft.
[9,7
a 12,4
kg-m.].
0-18.
Steering
Bellcrank
Service
Refer to Fig. 0-9.
The
assembly
and adjustment of this unit is ex
tremely important; the information outlined below must be
followed
carefully whenever servicing the
bellcrank
assembly
on late model vehicles.
A
service kit
Part
No. 991381 containing the
bell
crank shaft, bearings,
seals,
bolt, nuts, and
washer
is
available for servicing this
assembly.
Be certain that all
parts
are installed in their proper position.
When assembling the parts, be
sure
the new
bear
ings in the bellcrank are positioned
Y%"
[3,175 mm.]
below the
surface
of the bellcrank
face
as shown. The
bearings
have
a
light
press"
fit that
will
hold
them in
place
after locating them in the proper
position.
Finally, when installing
washers,
the
chamfer on the
washer
must be installed toward
the bellcrank.
After
completing the
assembly,
and before attach
ing
the connecting
rods
to the bellcrank levers,
make
your
final
adjustment to the
assembly
as
follows:
a.
With
the W [11,113 mm.] diameter clamp bolt
loosened, adjust the locknut on the end of the
bell
crank shaft
until
the bellcrank just
rotates
freely
without
a bind.
Note:
On early model vehicles using bellcrank kit
Part
No. 920556, torque the bellcrank shaft nut
(Fig.
O-l #14) 70 - 90
lb-ft.
[9,7 a 12,4
kg-m.].
319
Page 320 of 376
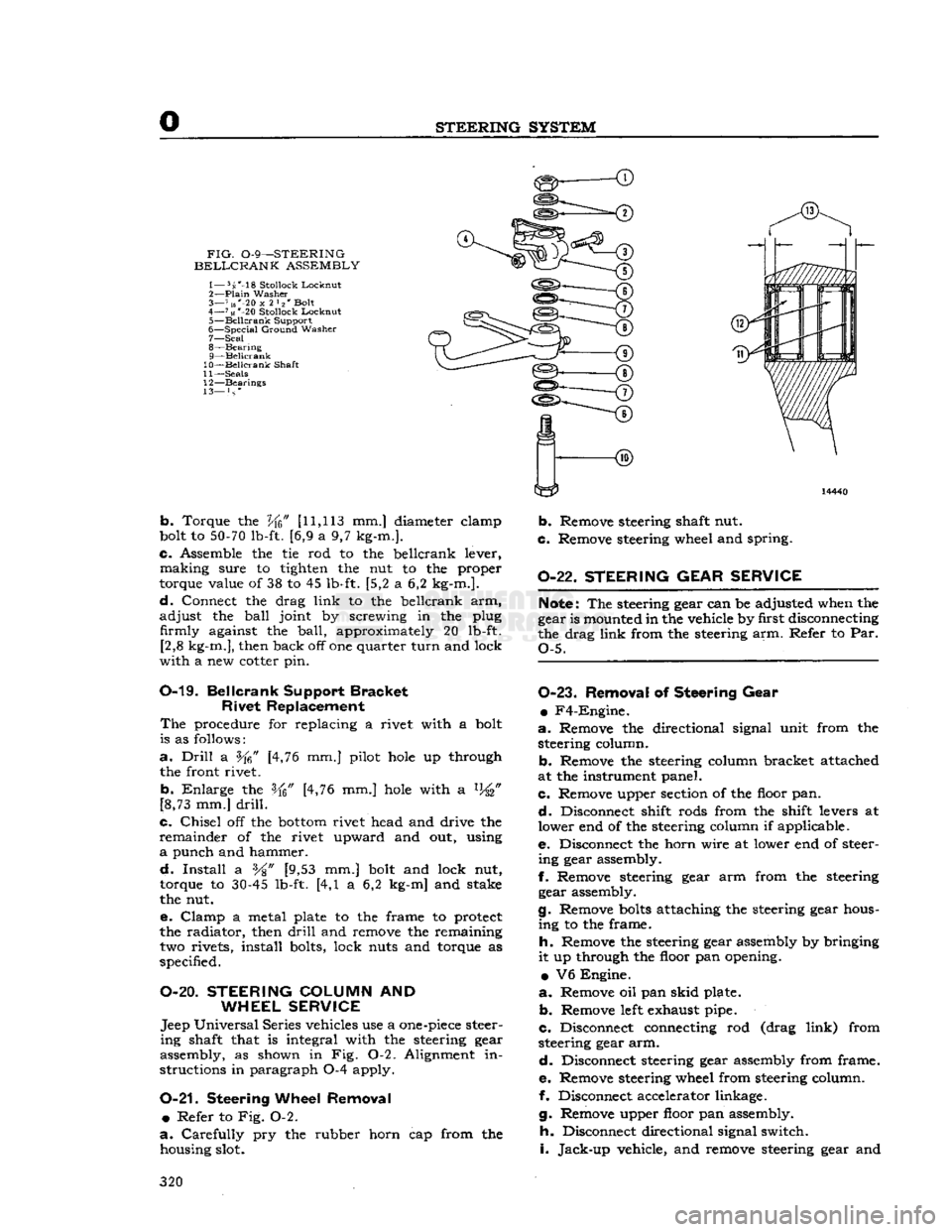
STEERING
SYSTEM
FIG.
0-9—STEERING
BELLCRANK
ASSEMBLY
1— 5s'-18
Stollock
Lockout
2—
Plain
Washer
3— 7 us"-20
x
2 l2' Bolt
4—
71«
*-20
Stollock
Locknut
5—
Beilcrank
Support
6—
Special
Ground
Washer
7— Seal
8—
Bearing
9— Beilcrank
10— Beilcrank
Shaft
11—
Seals
12—
Bearings
13— } s *
b.
Torque the
Vfc"
[11,113
mm.] diameter elamp
bolt to
50-70
lb-ft. [6,9 a 9,7 kg-m.].
c.
Assemble the tie rod to the beilcrank lever,
making
sure to tighten the nut to the proper
torque value of 38 to 45 lb-ft. [5,2 a 6,2 kg-m.].
d.
Connect the drag
link
to the beilcrank arm,
adjust
the
ball
joint by screwing in the plug firmly against the
ball,
approximately 20 lb-ft. [2,8 kg-m.], then back off one quarter
turn
and lock
with
a new cotter pin.
0-19.
Beilcrank
Support
Bracket
Rivet
Replacement
The
procedure for replacing a rivet with a bolt
is as follows:
a.
Drill
a [4,76 mm.] pilot
hole
up through
the front rivet.
b.
Enlarge
the [4,76 mm.]
hole
with a %"
[8,73 mm.]
drill.
c.
Chisel
off the
bottom
rivet head and drive the
remainder
of the rivet upward and out, using
a
punch and hammer.
d.
Install
a %" [9,53 mm.] bolt and lock nut,
torque to
30-45
lb-ft. [4,1 a 6,2 kg-m] and stake
the nut.
e.
Clamp
a metal plate to the frame to protect
the radiator, then
drill
and remove the remaining two rivets, install bolts, lock nuts and torque as
specified.
O-20.
STEERING
COLUMN
AND
WHEEL SERVICE
Jeep
Universal
Series vehicles use a
one-piece
steer
ing
shaft that is integral with the steering gear
assembly, as shown in Fig. 0-2. Alignment in
structions in paragraph 0-4 apply.
0-21.
Steering
Wheel Removal •
Refer to Fig. 0-2.
a.
Carefully
pry the rubber horn cap from the housing slot.
b.
Remove steering shaft nut.
c.
Remove steering wheel and spring.
0-22.
STEERING GEAR SERVICE
Note:
The steering gear can be adjusted when the
gear is mounted in the vehicle by first disconnecting
the drag
link
from the steering arm. Refer to Par.
Q-5.
0-23.
Removal
of
Steering Gear
•
F4-Engine.
a.
Remove the directional signal unit from the steering column.
b.
Remove the steering column bracket attached
at the instrument panel.
c.
Remove upper section of the floor pan.
d.
Disconnect shift rods from the shift levers at
lower end of the steering column if applicable.
e.
Disconnect the horn wire at lower end of steer
ing
gear assembly.
f.
Remove steering gear arm from the steering gear assembly.
g.
Remove
bolts
attaching the steering gear hous
ing
to the frame.
h.
Remove the steering gear assembly by bringing
it
up through the floor pan opening.
•
V6 Engine.
a.
Remove oil pan
skid
plate.
b.
Remove
left
exhaust pipe.
c.
Disconnect connecting rod (drag
link)
from
steering gear arm.
d.
Disconnect steering gear assembly from frame.
e.
Remove steering wheel from steering column.
f. Disconnect accelerator linkage.
g.
Remove upper floor pan assembly.
h.
Disconnect directional signal switch.
i.
Jack-up
vehicle, and remove steering gear and
320