sensor LAND ROVER DISCOVERY 1999 Workshop Manual
[x] Cancel search | Manufacturer: LAND ROVER, Model Year: 1999, Model line: DISCOVERY, Model: LAND ROVER DISCOVERY 1999Pages: 1529, PDF Size: 34.8 MB
Page 787 of 1529
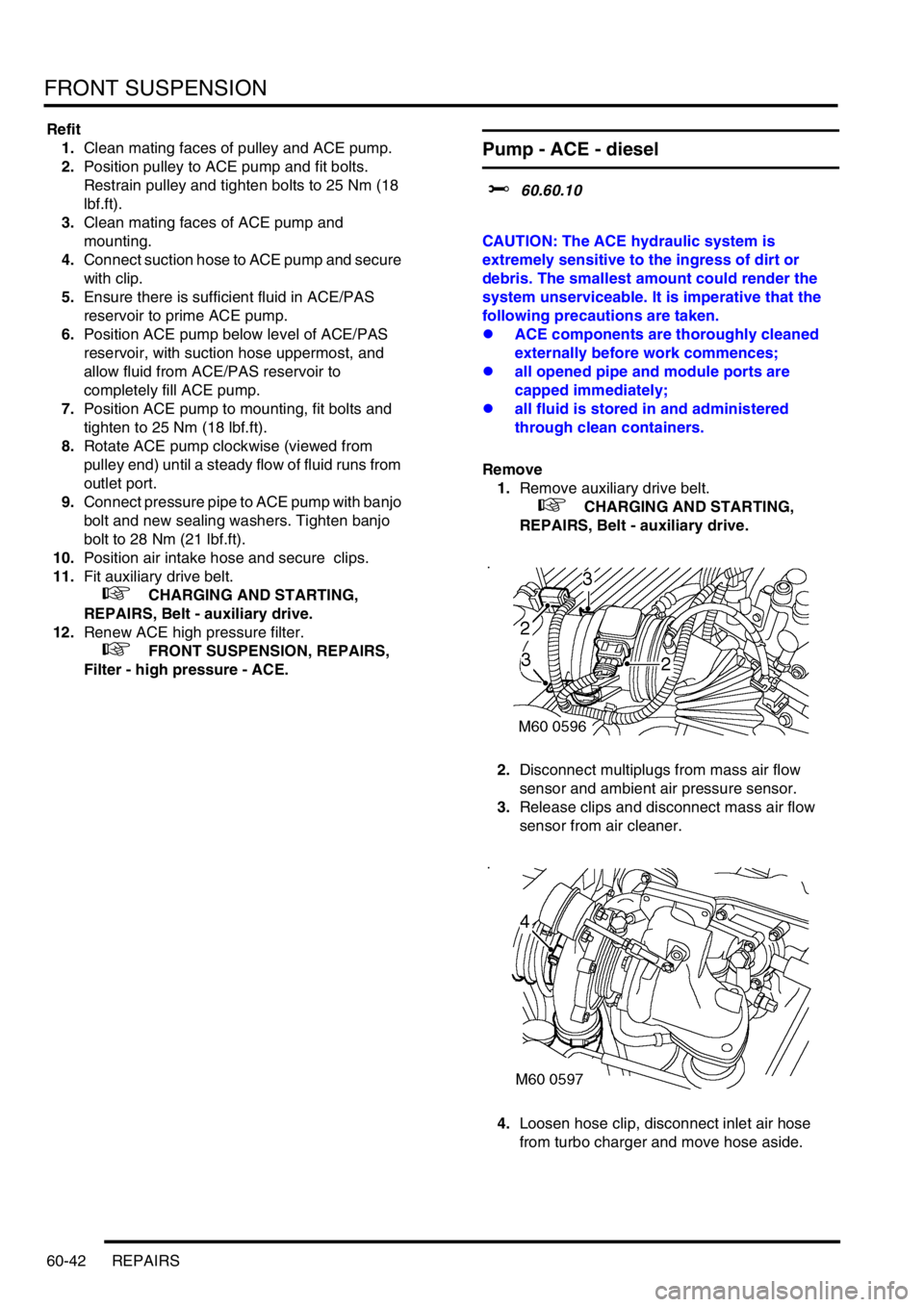
FRONT SUSPENSION
60-42 REPAIRS
Refit
1.Clean mating faces of pulley and ACE pump.
2.Position pulley to ACE pump and fit bolts.
Restrain pulley and tighten bolts to 25 Nm (18
lbf.ft).
3.Clean mating faces of ACE pump and
mounting.
4.Connect suction hose to ACE pump and secure
with clip.
5.Ensure there is sufficient fluid in ACE/PAS
reservoir to prime ACE pump.
6.Position ACE pump below level of ACE/PAS
reservoir, with suction hose uppermost, and
allow fluid from ACE/PAS reservoir to
completely fill ACE pump.
7.Position ACE pump to mounting, fit bolts and
tighten to 25 Nm (18 lbf.ft).
8.Rotate ACE pump clockwise (viewed from
pulley end) until a steady flow of fluid runs from
outlet port.
9.Connect pressure pipe to ACE pump with banjo
bolt and new sealing washers. Tighten banjo
bolt to 28 Nm (21 lbf.ft).
10.Position air intake hose and secure clips.
11.Fit auxiliary drive belt.
+ CHARGING AND STARTING,
REPAIRS, Belt - auxiliary drive.
12.Renew ACE high pressure filter.
+ FRONT SUSPENSION, REPAIRS,
Filter - high pressure - ACE.
Pump - ACE - diesel
$% 60.60.10
CAUTION: The ACE hydraulic system is
extremely sensitive to the ingress of dirt or
debris. The smallest amount could render the
system unserviceable. It is imperative that the
following precautions are taken.
lACE components are thoroughly cleaned
externally before work commences;
lall opened pipe and module ports are
capped immediately;
lall fluid is stored in and administered
through clean containers.
Remove
1.Remove auxiliary drive belt.
+ CHARGING AND STARTING,
REPAIRS, Belt - auxiliary drive.
2.Disconnect multiplugs from mass air flow
sensor and ambient air pressure sensor.
3.Release clips and disconnect mass air flow
sensor from air cleaner.
4.Loosen hose clip, disconnect inlet air hose
from turbo charger and move hose aside.
Page 789 of 1529
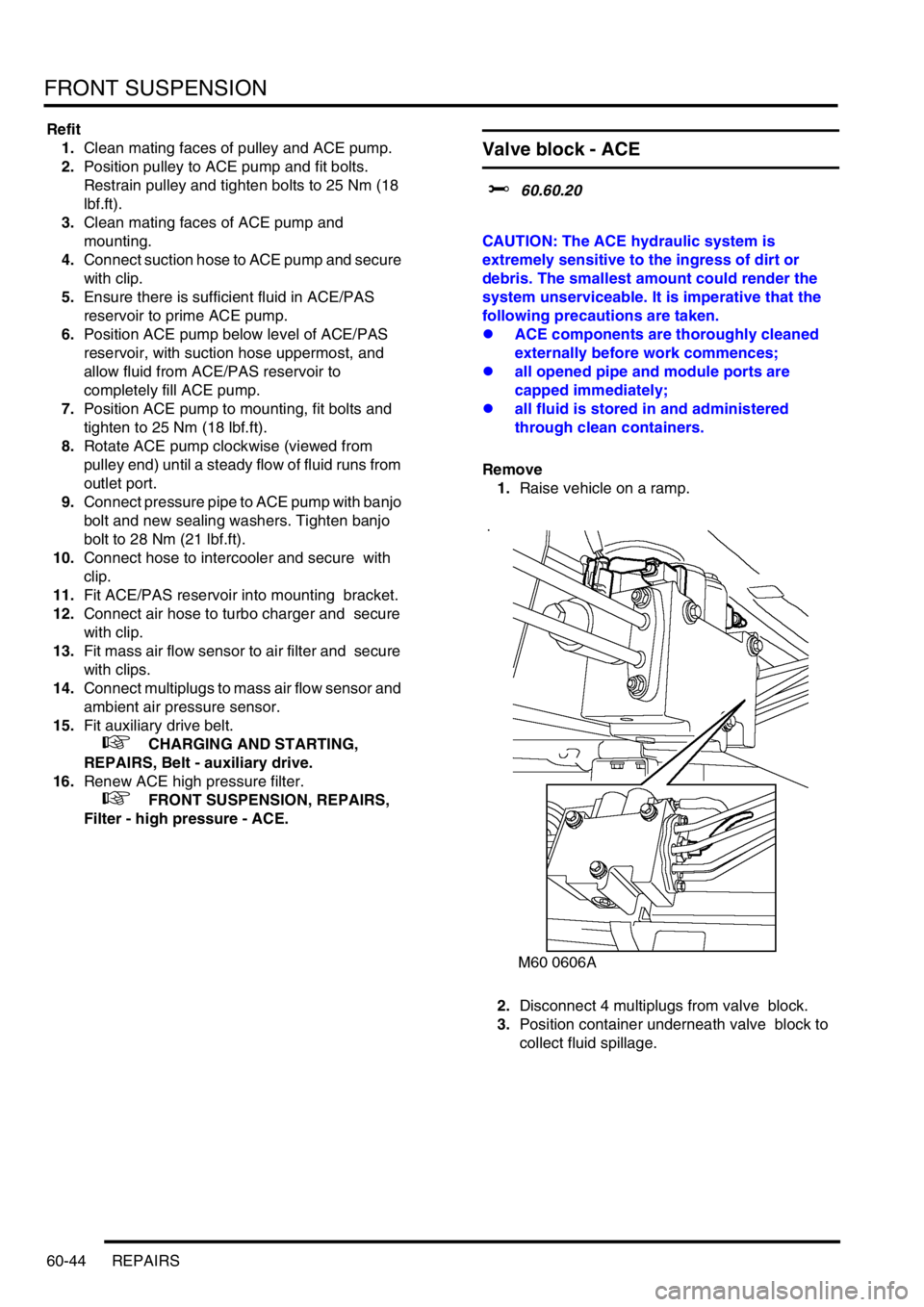
FRONT SUSPENSION
60-44 REPAIRS
Refit
1.Clean mating faces of pulley and ACE pump.
2.Position pulley to ACE pump and fit bolts.
Restrain pulley and tighten bolts to 25 Nm (18
lbf.ft).
3.Clean mating faces of ACE pump and
mounting.
4.Connect suction hose to ACE pump and secure
with clip.
5.Ensure there is sufficient fluid in ACE/PAS
reservoir to prime ACE pump.
6.Position ACE pump below level of ACE/PAS
reservoir, with suction hose uppermost, and
allow fluid from ACE/PAS reservoir to
completely fill ACE pump.
7.Position ACE pump to mounting, fit bolts and
tighten to 25 Nm (18 lbf.ft).
8.Rotate ACE pump clockwise (viewed from
pulley end) until a steady flow of fluid runs from
outlet port.
9.Connect pressure pipe to ACE pump with banjo
bolt and new sealing washers. Tighten banjo
bolt to 28 Nm (21 lbf.ft).
10.Connect hose to intercooler and secure with
clip.
11.Fit ACE/PAS reservoir into mounting bracket.
12.Connect air hose to turbo charger and secure
with clip.
13.Fit mass air flow sensor to air filter and secure
with clips.
14.Connect multiplugs to mass air flow sensor and
ambient air pressure sensor.
15.Fit auxiliary drive belt.
+ CHARGING AND STARTING,
REPAIRS, Belt - auxiliary drive.
16.Renew ACE high pressure filter.
+ FRONT SUSPENSION, REPAIRS,
Filter - high pressure - ACE.
Valve block - ACE
$% 60.60.20
CAUTION: The ACE hydraulic system is
extremely sensitive to the ingress of dirt or
debris. The smallest amount could render the
system unserviceable. It is imperative that the
following precautions are taken.
lACE components are thoroughly cleaned
externally before work commences;
lall opened pipe and module ports are
capped immediately;
lall fluid is stored in and administered
through clean containers.
Remove
1.Raise vehicle on a ramp.
2.Disconnect 4 multiplugs from valve block.
3.Position container underneath valve block to
collect fluid spillage.
Page 797 of 1529
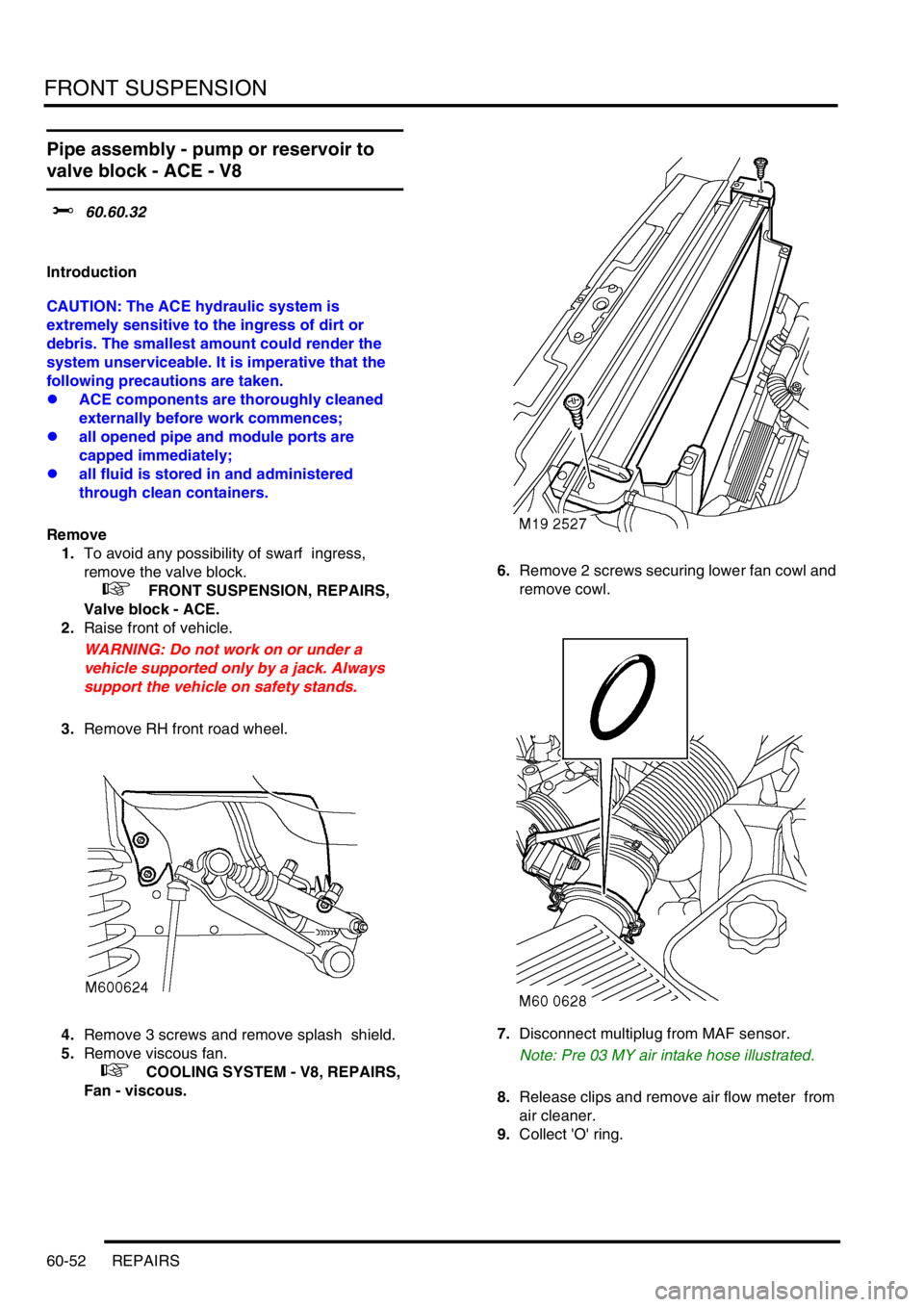
FRONT SUSPENSION
60-52 REPAIRS
Pipe assembly - pump or reservoir to
valve block - ACE - V8
$% 60.60.32
Introduction
CAUTION: The ACE hydraulic system is
extremely sensitive to the ingress of dirt or
debris. The smallest amount could render the
system unserviceable. It is imperative that the
following precautions are taken.
lACE components are thoroughly cleaned
externally before work commences;
lall opened pipe and module ports are
capped immediately;
lall fluid is stored in and administered
through clean containers.
Remove
1.To avoid any possibility of swarf ingress,
remove the valve block.
+ FRONT SUSPENSION, REPAIRS,
Valve block - ACE.
2.Raise front of vehicle.
WARNING: Do not work on or under a
vehicle supported only by a jack. Always
support the vehicle on safety stands.
3.Remove RH front road wheel.
4.Remove 3 screws and remove splash shield.
5.Remove viscous fan.
+ COOLING SYSTEM - V8, REPAIRS,
Fan - viscous.6.Remove 2 screws securing lower fan cowl and
remove cowl.
7.Disconnect multiplug from MAF sensor.
Note: Pre 03 MY air intake hose illustrated.
8.Release clips and remove air flow meter from
air cleaner.
9.Collect 'O' ring.
Page 799 of 1529
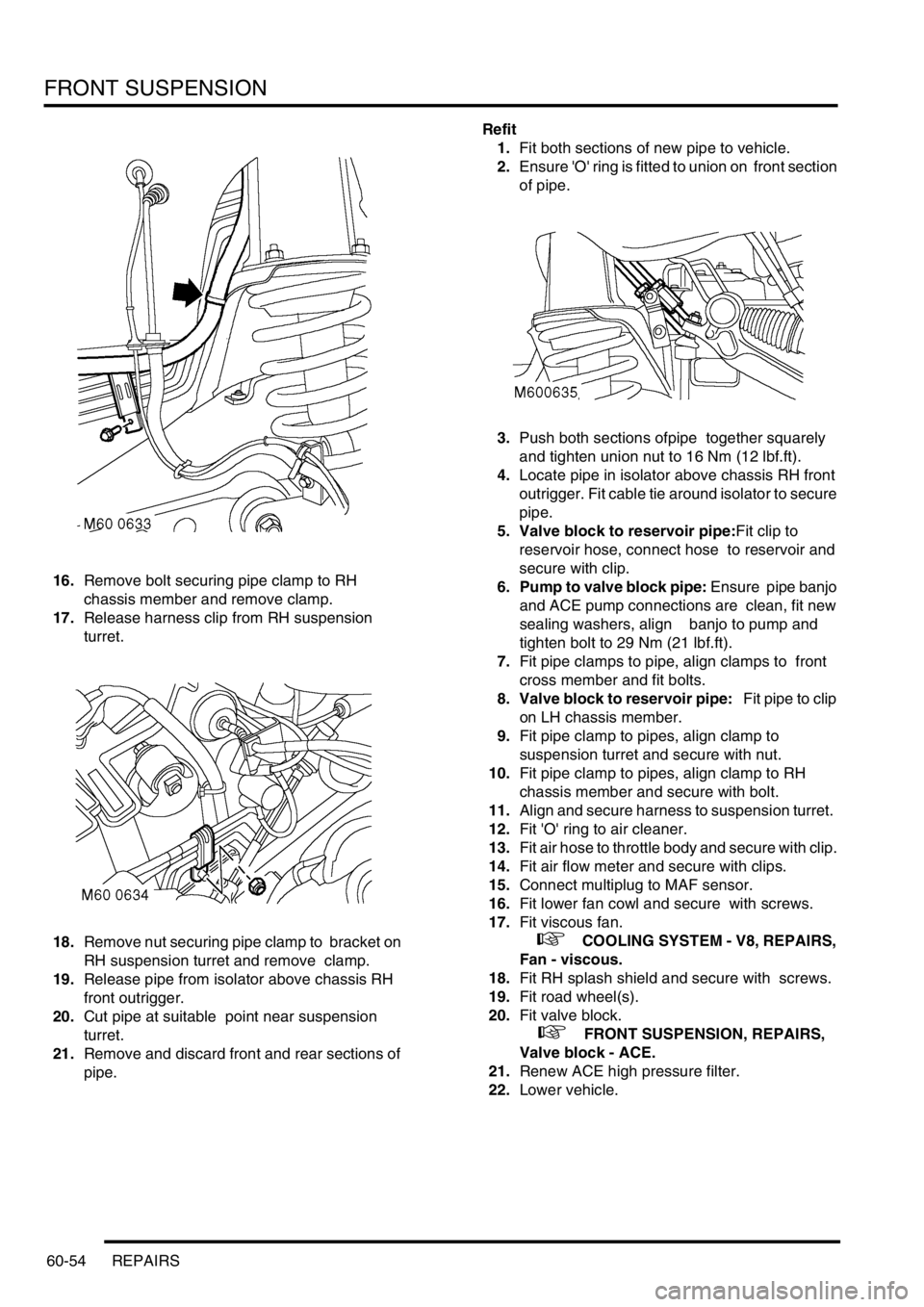
FRONT SUSPENSION
60-54 REPAIRS
16.Remove bolt securing pipe clamp to RH
chassis member and remove clamp.
17.Release harness clip from RH suspension
turret.
18.Remove nut securing pipe clamp to bracket on
RH suspension turret and remove clamp.
19.Release pipe from isolator above chassis RH
front outrigger.
20.Cut pipe at suitable point near suspension
turret.
21.Remove and discard front and rear sections of
pipe. Refit
1.Fit both sections of new pipe to vehicle.
2.Ensure 'O' ring is fitted to union on front section
of pipe.
3.Push both sections ofpipe together squarely
and tighten union nut to 16 Nm (12 lbf.ft).
4.Locate pipe in isolator above chassis RH front
outrigger. Fit cable tie around isolator to secure
pipe.
5. Valve block to reservoir pipe:Fit clip to
reservoir hose, connect hose to reservoir and
secure with clip.
6. Pump to valve block pipe: Ensure pipe banjo
and ACE pump connections are clean, fit new
sealing washers, align banjo to pump and
tighten bolt to 29 Nm (21 lbf.ft).
7.Fit pipe clamps to pipe, align clamps to front
cross member and fit bolts.
8. Valve block to reservoir pipe: Fit pipe to clip
on LH chassis member.
9.Fit pipe clamp to pipes, align clamp to
suspension turret and secure with nut.
10.Fit pipe clamp to pipes, align clamp to RH
chassis member and secure with bolt.
11.Align and secure harness to suspension turret.
12.Fit 'O' ring to air cleaner.
13.Fit air hose to throttle body and secure with clip.
14.Fit air flow meter and secure with clips.
15.Connect multiplug to MAF sensor.
16.Fit lower fan cowl and secure with screws.
17.Fit viscous fan.
+ COOLING SYSTEM - V8, REPAIRS,
Fan - viscous.
18.Fit RH splash shield and secure with screws.
19.Fit road wheel(s).
20.Fit valve block.
+ FRONT SUSPENSION, REPAIRS,
Valve block - ACE.
21.Renew ACE high pressure filter.
22.Lower vehicle.
Page 815 of 1529
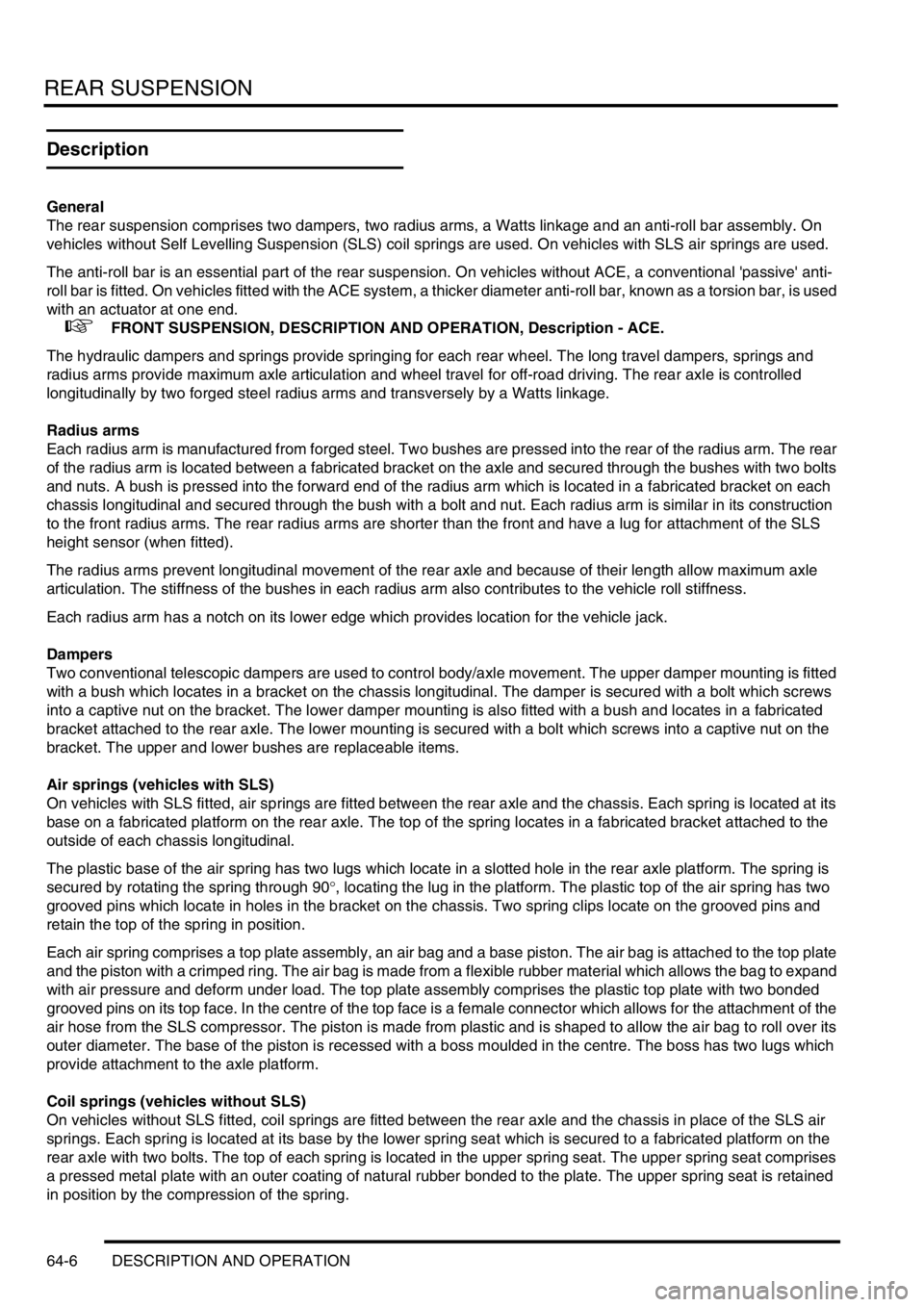
REAR SUSPENSION
64-6 DESCRIPTION AND OPERATION
Description
General
The rear suspension comprises two dampers, two radius arms, a Watts linkage and an anti-roll bar assembly. On
vehicles without Self Levelling Suspension (SLS) coil springs are used. On vehicles with SLS air springs are used.
The anti-roll bar is an essential part of the rear suspension. On vehicles without ACE, a conventional 'passive' anti-
roll bar is fitted. On vehicles fitted with the ACE system, a thicker diameter anti-roll bar, known as a torsion bar, is used
with an actuator at one end.
+ FRONT SUSPENSION, DESCRIPTION AND OPERATION, Description - ACE.
The hydraulic dampers and springs provide springing for each rear wheel. The long travel dampers, springs and
radius arms provide maximum axle articulation and wheel travel for off-road driving. The rear axle is controlled
longitudinally by two forged steel radius arms and transversely by a Watts linkage.
Radius arms
Each radius arm is manufactured from forged steel. Two bushes are pressed into the rear of the radius arm. The rear
of the radius arm is located between a fabricated bracket on the axle and secured through the bushes with two bolts
and nuts. A bush is pressed into the forward end of the radius arm which is located in a fabricated bracket on each
chassis longitudinal and secured through the bush with a bolt and nut. Each radius arm is similar in its construction
to the front radius arms. The rear radius arms are shorter than the front and have a lug for attachment of the SLS
height sensor (when fitted).
The radius arms prevent longitudinal movement of the rear axle and because of their length allow maximum axle
articulation. The stiffness of the bushes in each radius arm also contributes to the vehicle roll stiffness.
Each radius arm has a notch on its lower edge which provides location for the vehicle jack.
Dampers
Two conventional telescopic dampers are used to control body/axle movement. The upper damper mounting is fitted
with a bush which locates in a bracket on the chassis longitudinal. The damper is secured with a bolt which screws
into a captive nut on the bracket. The lower damper mounting is also fitted with a bush and locates in a fabricated
bracket attached to the rear axle. The lower mounting is secured with a bolt which screws into a captive nut on the
bracket. The upper and lower bushes are replaceable items.
Air springs (vehicles with SLS)
On vehicles with SLS fitted, air springs are fitted between the rear axle and the chassis. Each spring is located at its
base on a fabricated platform on the rear axle. The top of the spring locates in a fabricated bracket attached to the
outside of each chassis longitudinal.
The plastic base of the air spring has two lugs which locate in a slotted hole in the rear axle platform. The spring is
secured by rotating the spring through 90°, locating the lug in the platform. The plastic top of the air spring has two
grooved pins which locate in holes in the bracket on the chassis. Two spring clips locate on the grooved pins and
retain the top of the spring in position.
Each air spring comprises a top plate assembly, an air bag and a base piston. The air bag is attached to the top plate
and the piston with a crimped ring. The air bag is made from a flexible rubber material which allows the bag to expand
with air pressure and deform under load. The top plate assembly comprises the plastic top plate with two bonded
grooved pins on its top face. In the centre of the top face is a female connector which allows for the attachment of the
air hose from the SLS compressor. The piston is made from plastic and is shaped to allow the air bag to roll over its
outer diameter. The base of the piston is recessed with a boss moulded in the centre. The boss has two lugs which
provide attachment to the axle platform.
Coil springs (vehicles without SLS)
On vehicles without SLS fitted, coil springs are fitted between the rear axle and the chassis in place of the SLS air
springs. Each spring is located at its base by the lower spring seat which is secured to a fabricated platform on the
rear axle with two bolts. The top of each spring is located in the upper spring seat. The upper spring seat comprises
a pressed metal plate with an outer coating of natural rubber bonded to the plate. The upper spring seat is retained
in position by the compression of the spring.
Page 818 of 1529
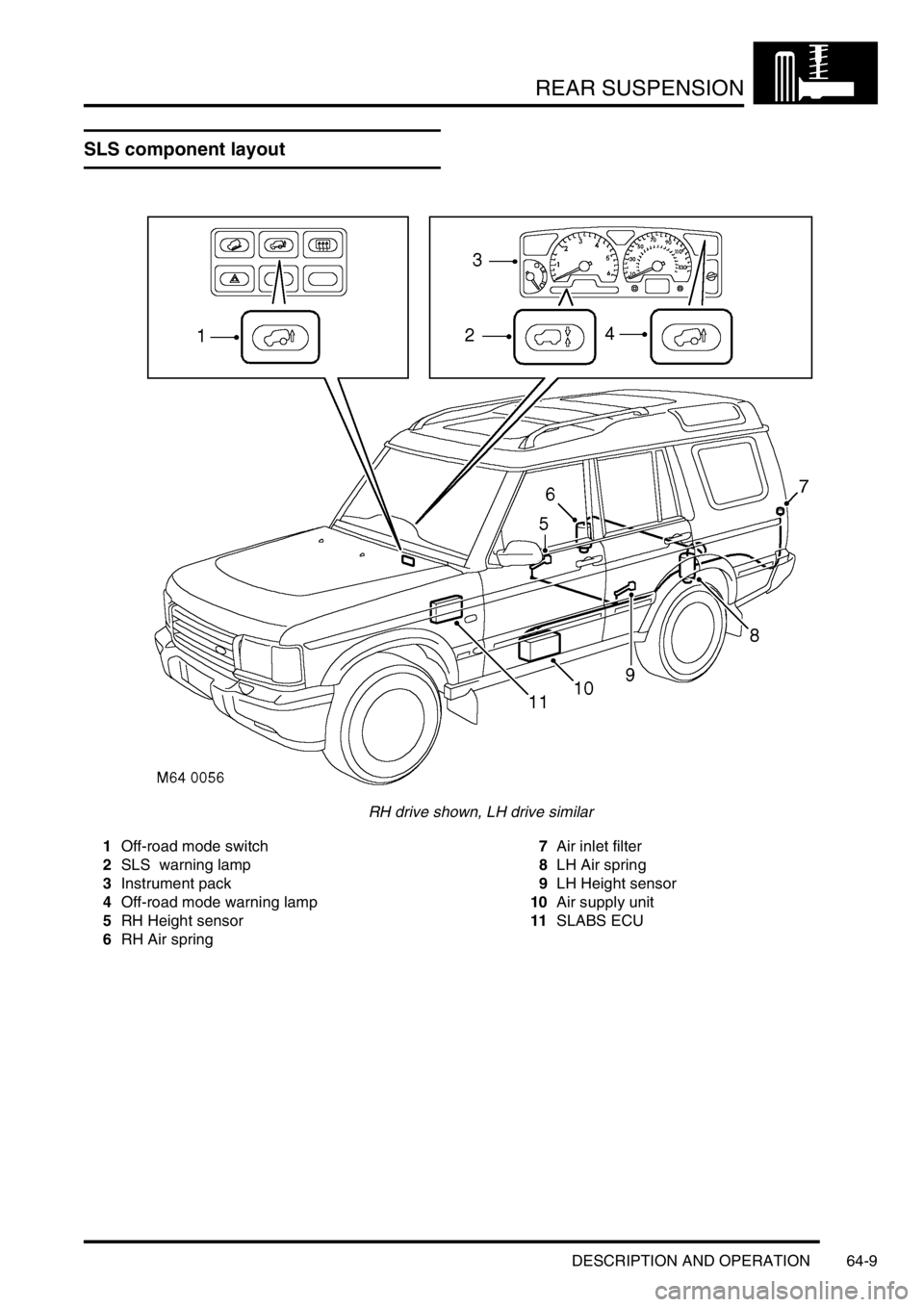
REAR SUSPENSION
DESCRIPTION AND OPERATION 64-9
DESCRIPTION AND OPERAT ION
SLS component layout
RH drive shown, LH drive similar
1Off-road mode switch
2SLS warning lamp
3Instrument pack
4Off-road mode warning lamp
5RH Height sensor
6RH Air spring7Air inlet filter
8LH Air spring
9LH Height sensor
10Air supply unit
11SLABS ECU
Page 820 of 1529
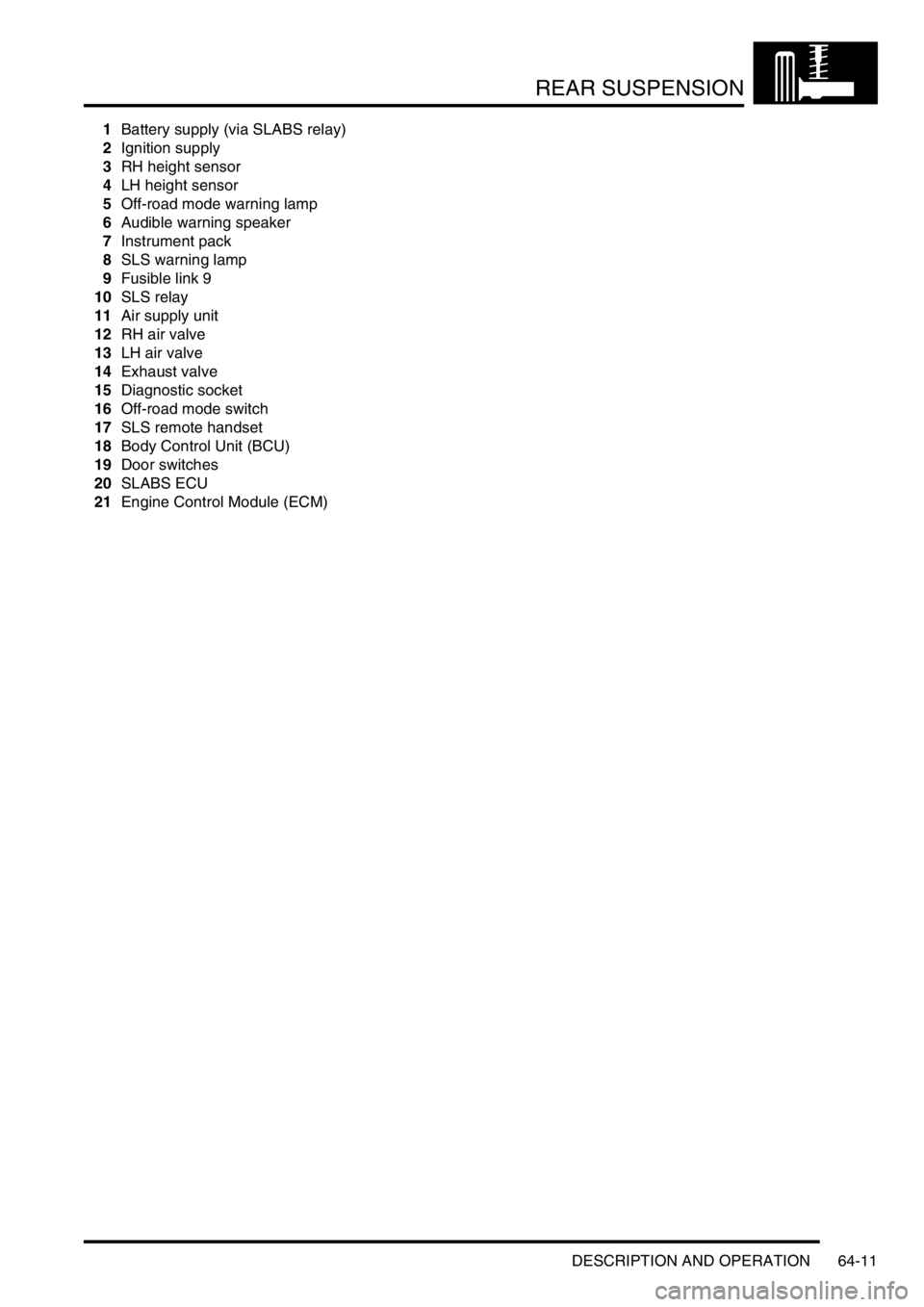
REAR SUSPENSION
DESCRIPTION AND OPERATION 64-11
1Battery supply (via SLABS relay)
2Ignition supply
3RH height sensor
4LH height sensor
5Off-road mode warning lamp
6Audible warning speaker
7Instrument pack
8SLS warning lamp
9Fusible link 9
10SLS relay
11Air supply unit
12RH air valve
13LH air valve
14Exhaust valve
15Diagnostic socket
16Off-road mode switch
17SLS remote handset
18Body Control Unit (BCU)
19Door switches
20SLABS ECU
21Engine Control Module (ECM)
Page 821 of 1529
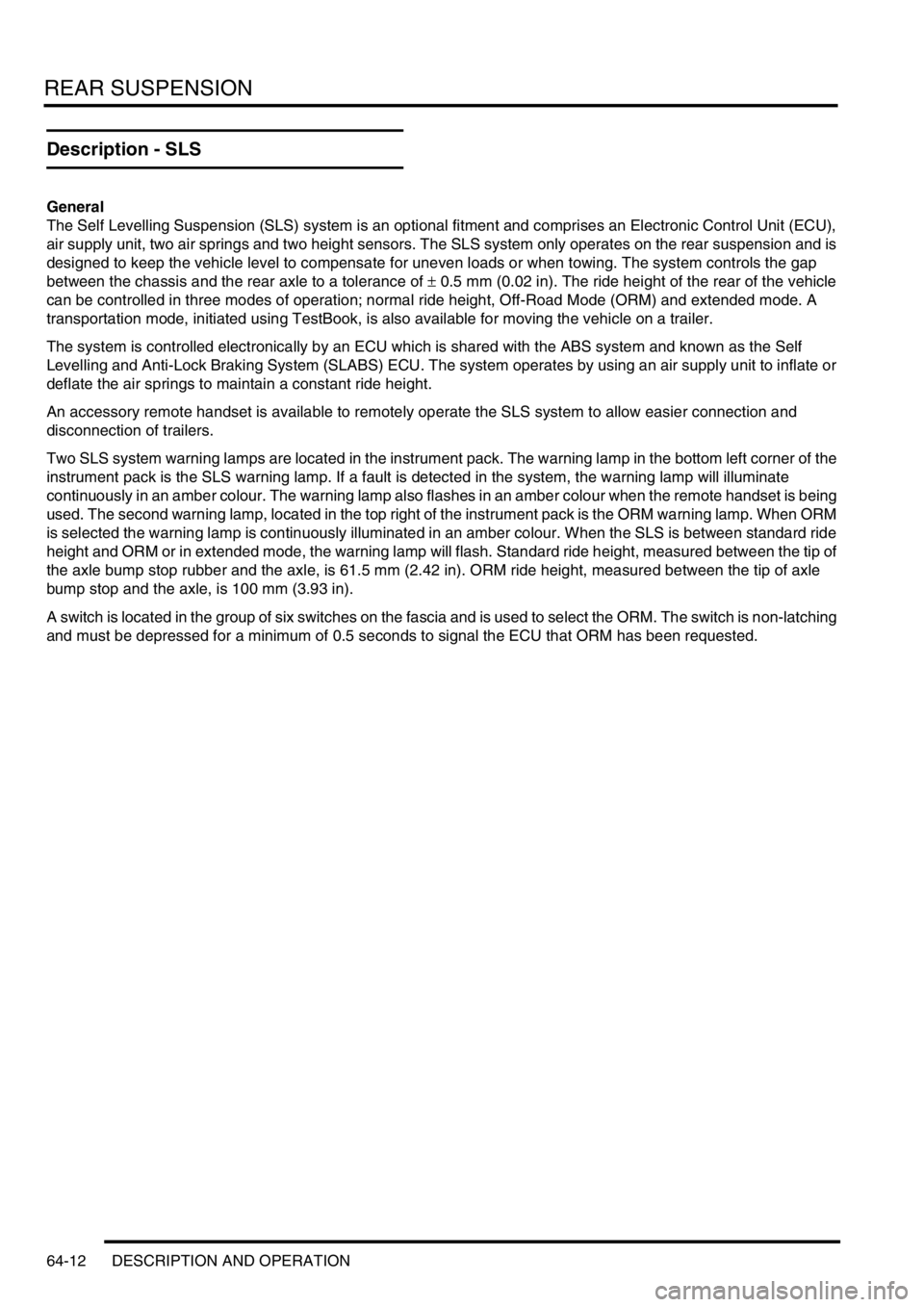
REAR SUSPENSION
64-12 DESCRIPTION AND OPERATION
Description - SLS
General
The Self Levelling Suspension (SLS) system is an optional fitment and comprises an Electronic Control Unit (ECU),
air supply unit, two air springs and two height sensors. The SLS system only operates on the rear suspension and is
designed to keep the vehicle level to compensate for uneven loads or when towing. The system controls the gap
between the chassis and the rear axle to a tolerance of ± 0.5 mm (0.02 in). The ride height of the rear of the vehicle
can be controlled in three modes of operation; normal ride height, Off-Road Mode (ORM) and extended mode. A
transportation mode, initiated using TestBook, is also available for moving the vehicle on a trailer.
The system is controlled electronically by an ECU which is shared with the ABS system and known as the Self
Levelling and Anti-Lock Braking System (SLABS) ECU. The system operates by using an air supply unit to inflate or
deflate the air springs to maintain a constant ride height.
An accessory remote handset is available to remotely operate the SLS system to allow easier connection and
disconnection of trailers.
Two SLS system warning lamps are located in the instrument pack. The warning lamp in the bottom left corner of the
instrument pack is the SLS warning lamp. If a fault is detected in the system, the warning lamp will illuminate
continuously in an amber colour. The warning lamp also flashes in an amber colour when the remote handset is being
used. The second warning lamp, located in the top right of the instrument pack is the ORM warning lamp. When ORM
is selected the warning lamp is continuously illuminated in an amber colour. When the SLS is between standard ride
height and ORM or in extended mode, the warning lamp will flash. Standard ride height, measured between the tip of
the axle bump stop rubber and the axle, is 61.5 mm (2.42 in). ORM ride height, measured between the tip of axle
bump stop and the axle, is 100 mm (3.93 in).
A switch is located in the group of six switches on the fascia and is used to select the ORM. The switch is non-latching
and must be depressed for a minimum of 0.5 seconds to signal the ECU that ORM has been requested.
Page 824 of 1529
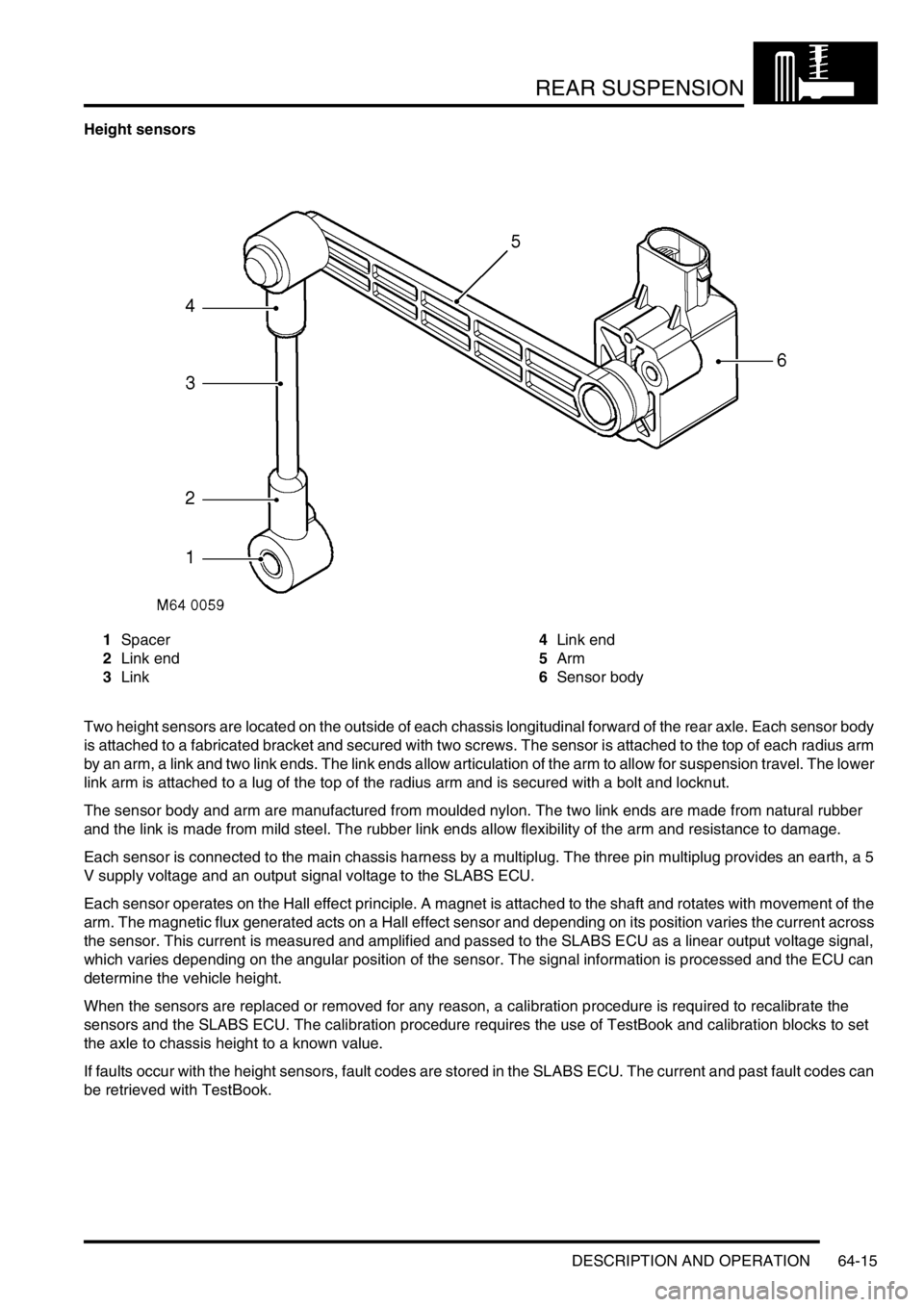
REAR SUSPENSION
DESCRIPTION AND OPERATION 64-15
Height sensors
1Spacer
2Link end
3Link4Link end
5Arm
6Sensor body
Two height sensors are located on the outside of each chassis longitudinal forward of the rear axle. Each sensor body
is attached to a fabricated bracket and secured with two screws. The sensor is attached to the top of each radius arm
by an arm, a link and two link ends. The link ends allow articulation of the arm to allow for suspension travel. The lower
link arm is attached to a lug of the top of the radius arm and is secured with a bolt and locknut.
The sensor body and arm are manufactured from moulded nylon. The two link ends are made from natural rubber
and the link is made from mild steel. The rubber link ends allow flexibility of the arm and resistance to damage.
Each sensor is connected to the main chassis harness by a multiplug. The three pin multiplug provides an earth, a 5
V supply voltage and an output signal voltage to the SLABS ECU.
Each sensor operates on the Hall effect principle. A magnet is attached to the shaft and rotates with movement of the
arm. The magnetic flux generated acts on a Hall effect sensor and depending on its position varies the current across
the sensor. This current is measured and amplified and passed to the SLABS ECU as a linear output voltage signal,
which varies depending on the angular position of the sensor. The signal information is processed and the ECU can
determine the vehicle height.
When the sensors are replaced or removed for any reason, a calibration procedure is required to recalibrate the
sensors and the SLABS ECU. The calibration procedure requires the use of TestBook and calibration blocks to set
the axle to chassis height to a known value.
If faults occur with the height sensors, fault codes are stored in the SLABS ECU. The current and past fault codes can
be retrieved with TestBook.
Page 826 of 1529
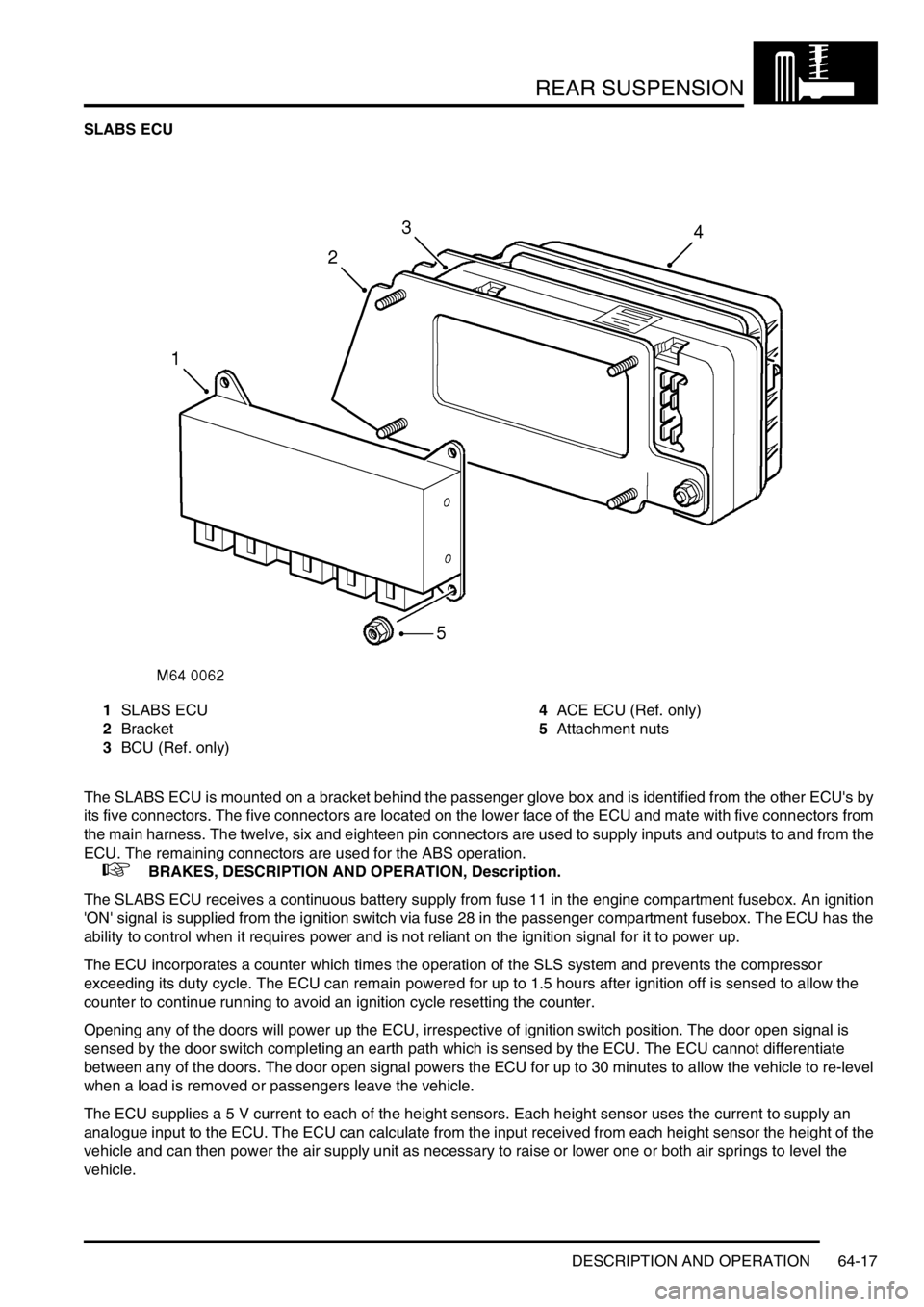
REAR SUSPENSION
DESCRIPTION AND OPERATION 64-17
SLABS ECU
1SLABS ECU
2Bracket
3BCU (Ref. only)4ACE ECU (Ref. only)
5Attachment nuts
The SLABS ECU is mounted on a bracket behind the passenger glove box and is identified from the other ECU's by
its five connectors. The five connectors are located on the lower face of the ECU and mate with five connectors from
the main harness. The twelve, six and eighteen pin connectors are used to supply inputs and outputs to and from the
ECU. The remaining connectors are used for the ABS operation.
+ BRAKES, DESCRIPTION AND OPERATION, Description.
The SLABS ECU receives a continuous battery supply from fuse 11 in the engine compartment fusebox. An ignition
'ON' signal is supplied from the ignition switch via fuse 28 in the passenger compartment fusebox. The ECU has the
ability to control when it requires power and is not reliant on the ignition signal for it to power up.
The ECU incorporates a counter which times the operation of the SLS system and prevents the compressor
exceeding its duty cycle. The ECU can remain powered for up to 1.5 hours after ignition off is sensed to allow the
counter to continue running to avoid an ignition cycle resetting the counter.
Opening any of the doors will power up the ECU, irrespective of ignition switch position. The door open signal is
sensed by the door switch completing an earth path which is sensed by the ECU. The ECU cannot differentiate
between any of the doors. The door open signal powers the ECU for up to 30 minutes to allow the vehicle to re-level
when a load is removed or passengers leave the vehicle.
The ECU supplies a 5 V current to each of the height sensors. Each height sensor uses the current to supply an
analogue input to the ECU. The ECU can calculate from the input received from each height sensor the height of the
vehicle and can then power the air supply unit as necessary to raise or lower one or both air springs to level the
vehicle.