engine MITSUBISHI ECLIPSE 1991 Service Manual
[x] Cancel search | Manufacturer: MITSUBISHI, Model Year: 1991, Model line: ECLIPSE, Model: MITSUBISHI ECLIPSE 1991Pages: 1216, PDF Size: 67.42 MB
Page 1160 of 1216
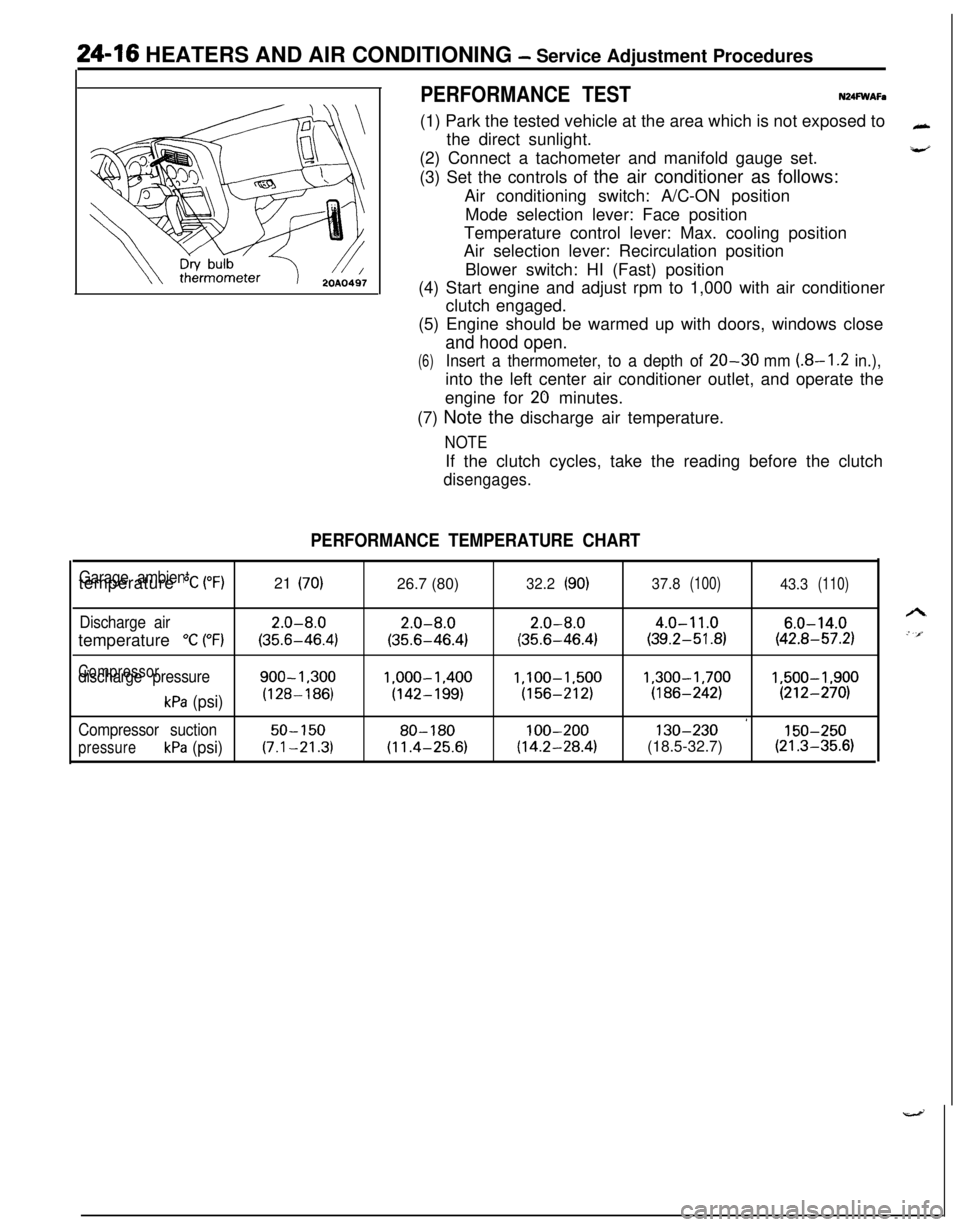
24-16 HEATERS AND AIR CONDITIONING - Service Adjustment Procedures
PERFORMANCE TESTN24FWAFa(1) Park the tested vehicle at the area which is not exposed to
the direct sunlight.
(2) Connect a tachometer and manifold gauge set.
(3) Set the controls of the air conditioner as follows:
Air conditioning switch: A/C-ON position
Mode selection lever: Face position
Temperature control lever: Max. cooling position
Air selection lever: Recirculation position
Blower switch: HI (Fast) position
(4) Start engine and adjust rpm to 1,000 with air conditioner
clutch engaged.
(5) Engine should be warmed up with doors, windows close
and hood open.
(6)Insert a thermometer, to a depth of 20-30 mm (8-I .2 in.),into the left center air conditioner outlet, and operate the
engine for
20 minutes.
(7) Note the discharge air temperature.
NOTEIf the clutch cycles, take the reading before the clutch
disengages.
PERFORMANCE TEMPERATURE CHART
Garage ambienttemperature “C (“F)21 (70)26.7 (80)32.2(90)37.8(100)43.3(110)
Discharge air2.0-8.02.0-8.02.0-8.04.0-11.06.0-14.0temperature
“C (“F)(35.6-46.4)(35.6-46.4)(35.6-46.4)(39.2-51.8)(42.8-57.2)
Compressordischarge pressure900-1.3001.000-1.400l,lOO-1,5001,300-1,7001,500-1,900
kPa (psi)(128-186)(142-199)(156-212)(186-242)(212-270)
’Compressor suction50-15080-180100-200130-230150-250
pressurekPa (psi)(7.1-21.3)(11.4-25.6)(14.2-28.4)(18.5-32.7)(21.3-35.6)
Page 1162 of 1216
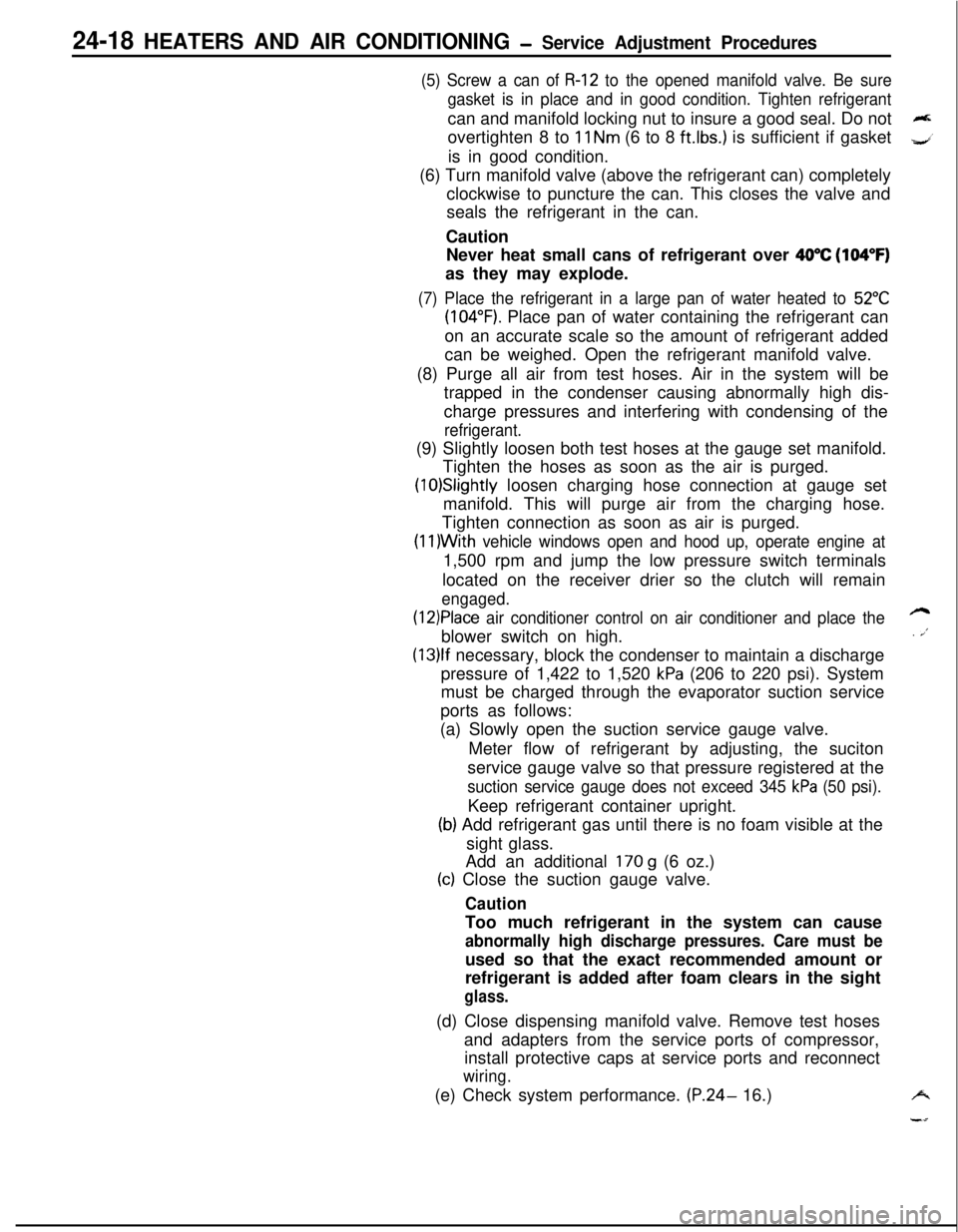
24-18 HEATERS AND AIR CONDITIONING - Service Adjustment Procedures
(5) Screw a can of R-12 to the opened manifold valve. Be sure
gasket is in place and in good condition. Tighten refrigerantcan and manifold locking nut to insure a good seal. Do not
overtighten 8 to
11 Nm (6 to 8 ft.lbs.) is sufficient if gasket
is in good condition.
(6) Turn manifold valve (above the refrigerant can) completely
clockwise to puncture the can. This closes the valve and
seals the refrigerant in the can.
Caution
Never heat small cans of refrigerant over
40°C (104°F)as they may explode.
(7) Place the refrigerant in a large pan of water heated to 52°C
(104°F). Place pan of water containing the refrigerant can
on an accurate scale so the amount of refrigerant added
can be weighed. Open the refrigerant manifold valve.
(8) Purge all air from test hoses. Air in the system will be
trapped in the condenser causing abnormally high dis-
charge pressures and interfering with condensing of the
refrigerant.(9) Slightly loosen both test hoses at the gauge set manifold.
Tighten the hoses as soon as the air is purged.
(10)Slightly loosen charging hose connection at gauge set
manifold. This will purge air from the charging hose.
Tighten connection as soon as air is purged.
(I l)With vehicle windows open and hood up, operate engine at1,500 rpm and jump the low pressure switch terminals
located on the receiver drier so the clutch will remain
engaged.
(12)Place air conditioner control on air conditioner and place theblower switch on high.
(13)lf necessary, block the condenser to maintain a discharge
pressure of 1,422 to 1,520
kPa (206 to 220 psi). System
must be charged through the evaporator suction service
ports as follows:
(a) Slowly open the suction service gauge valve.
Meter flow of refrigerant by adjusting, the suciton
service gauge valve so that pressure registered at the
suction service gauge does not exceed 345 kPa (50 psi).Keep refrigerant container upright.
(b) Add refrigerant gas until there is no foam visible at the
sight glass.
Add an additional
170 g (6 oz.)
(c) Close the suction gauge valve.
CautionToo much refrigerant in the system can cause
abnormally high discharge pressures. Care must beused so that the exact recommended amount or
refrigerant is added after foam clears in the sight
glass.(d) Close dispensing manifold valve. Remove test hoses
and adapters from the service ports of compressor,
install protective caps at service ports and reconnect
wiring.(e) Check system performance.
(P.24- 16.)
e
. i”
A
i-4
Page 1165 of 1216
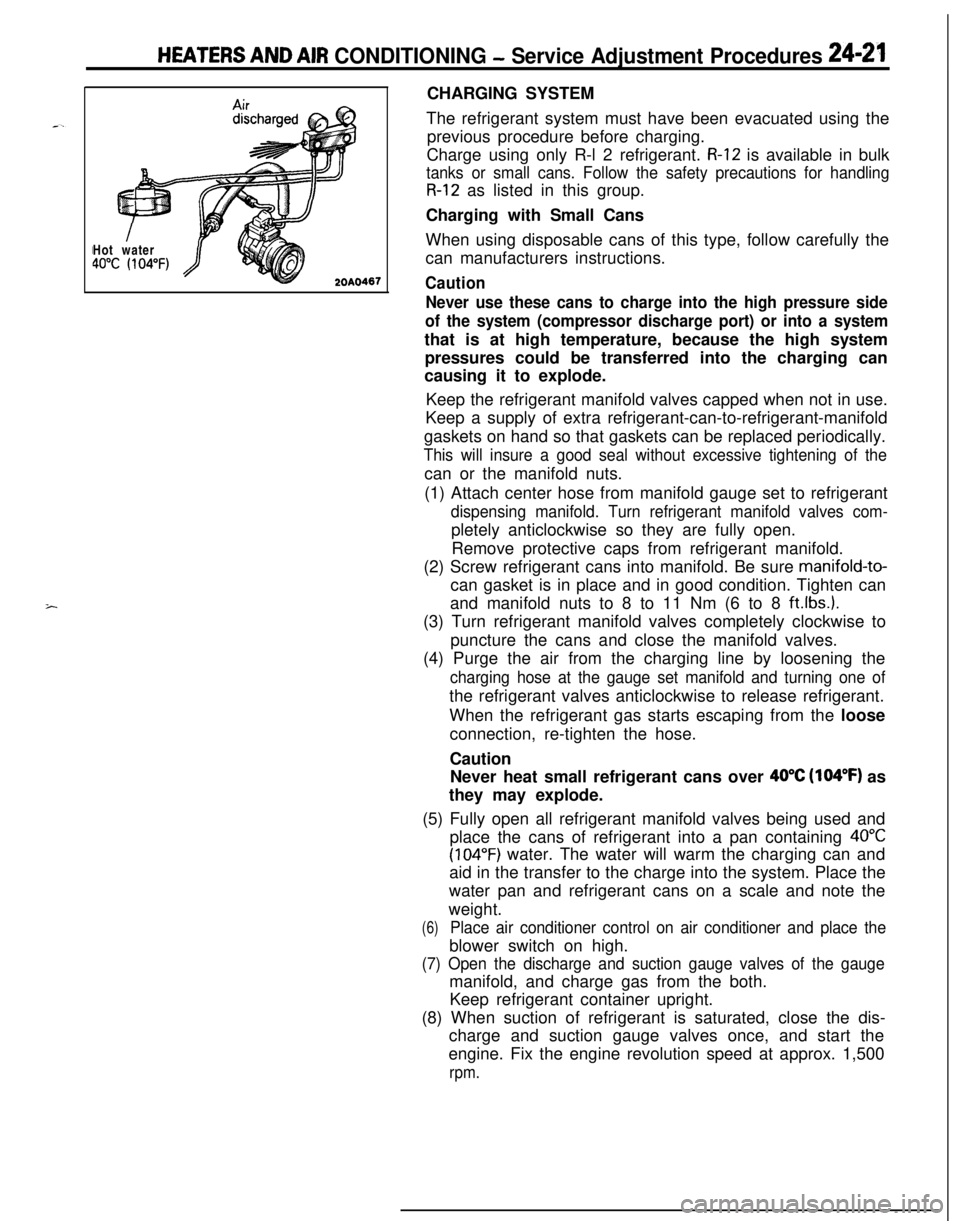
i
HEATERS AND AIR CONDITIONING - Service Adjustment Procedures 24-21Hot water40°C (104°F)
1467CHARGING SYSTEM
The refrigerant system must have been evacuated using the
previous procedure before charging.
Charge using only R-l 2 refrigerant.
R-12 is available in bulk
tanks or small cans. Follow the safety precautions for handling
R-12 as listed in this group.
Charging with Small Cans
When using disposable cans of this type, follow carefully the
can manufacturers instructions.
Caution
Never use these cans to charge into the high pressure side
of the system (compressor discharge port) or into a systemthat is at high temperature, because the high system
pressures could be transferred into the charging can
causing it to explode.
Keep the refrigerant manifold valves capped when not in use.
Keep a supply of extra refrigerant-can-to-refrigerant-manifold
gaskets on hand so that gaskets can be replaced periodically.
This will insure a good seal without excessive tightening of thecan or the manifold nuts.
(1) Attach center hose from manifold gauge set to refrigerant
dispensing manifold. Turn refrigerant manifold valves com-pletely anticlockwise so they are fully open.
Remove protective caps from refrigerant manifold.
(2) Screw refrigerant cans into manifold. Be sure
manifold-to-can gasket is in place and in good condition. Tighten can
and manifold nuts to 8 to 11 Nm (6 to 8
ft.lbs.).(3) Turn refrigerant manifold valves completely clockwise to
puncture the cans and close the manifold valves.
(4) Purge the air from the charging line by loosening the
charging hose at the gauge set manifold and turning one ofthe refrigerant valves anticlockwise to release refrigerant.
When the refrigerant gas starts escaping from the loose
connection, re-tighten the hose.
Caution
Never heat small refrigerant cans over
40°C (104°F) as
they may explode.
(5) Fully open all refrigerant manifold valves being used and
place the cans of refrigerant into a pan containing
40°C
(104°F) water. The water will warm the charging can and
aid in the transfer to the charge into the system. Place the
water pan and refrigerant cans on a scale and note the
weight.
(6)Place air conditioner control on air conditioner and place theblower switch on high.
(7) Open the discharge and suction gauge valves of the gaugemanifold, and charge gas from the both.
Keep refrigerant container upright.
(8) When suction of refrigerant is saturated, close the dis-
charge and suction gauge valves once, and start the
engine. Fix the engine revolution speed at approx. 1,500
rpm.
Page 1167 of 1216
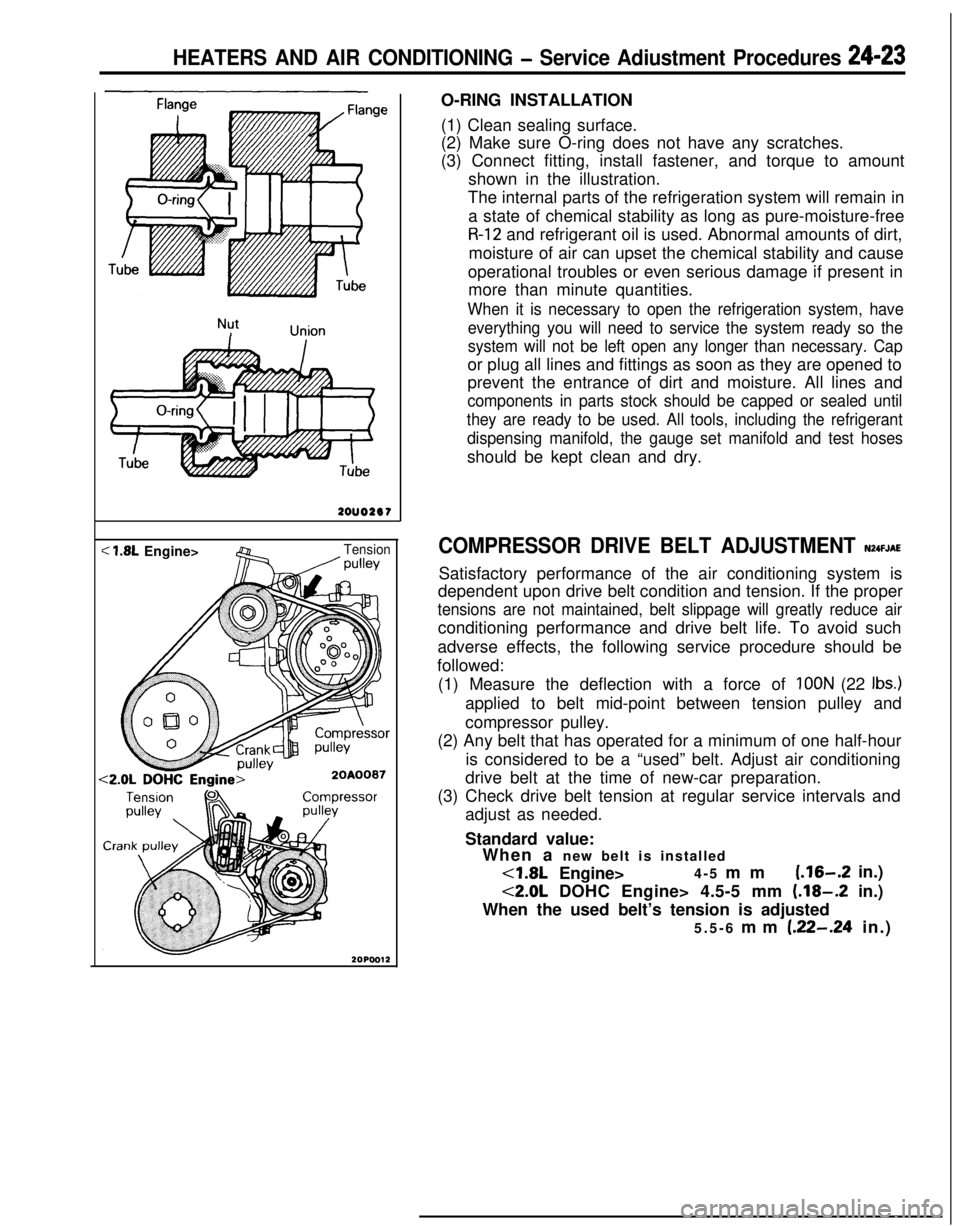
HEATERS AND AIR CONDITIONING - Service Adiustment Procedures 24-23
<
we2ouo2er
< 1.8L Engine>Tension/ wllevO-RING INSTALLATION
(1) Clean sealing surface.
(2) Make sure O-ring does not have any scratches.
(3) Connect fitting, install fastener, and torque to amount
shown in the illustration.
The internal parts of the refrigeration system will remain in
a state of chemical stability as long as pure-moisture-free
R-12 and refrigerant oil is used. Abnormal amounts of dirt,
moisture of air can upset the chemical stability and cause
operational troubles or even serious damage if present in
more than minute quantities.
When it is necessary to open the refrigeration system, have
everything you will need to service the system ready so the
system will not be left open any longer than necessary. Capor plug all lines and fittings as soon as they are opened to
prevent the entrance of dirt and moisture. All lines and
components in parts stock should be capped or sealed until
they are ready to be used. All tools, including the refrigerant
dispensing manifold, the gauge set manifold and test hosesshould be kept clean and dry.
COMPRESSOR DRIVE BELT ADJUSTMENT N24FJAESatisfactory performance of the air conditioning system is
dependent upon drive belt condition and tension. If the proper
tensions are not maintained, belt slippage will greatly reduce airconditioning performance and drive belt life. To avoid such
adverse effects, the following service procedure should be
followed:
(1) Measure the deflection with a force of
IOON (22 Ibs.)applied to belt mid-point between tension pulley and
compressor pulley.
(2) Any belt that has operated for a minimum of one half-hour
is considered to be a “used” belt. Adjust air conditioning
drive belt at the time of new-car preparation.
(3) Check drive belt tension at regular service intervals and
adjust as needed.
Standard value:
When a new belt is installed<1.8L Engine>4-5 mm
(.16-.2 in.)
<2.0L DOHC Engine> 4.5-5 mm (.18-.2 in.)
When the used belt’s tension is adjusted
5.5-6 mm
(.22-.24 in.)
Page 1168 of 1216
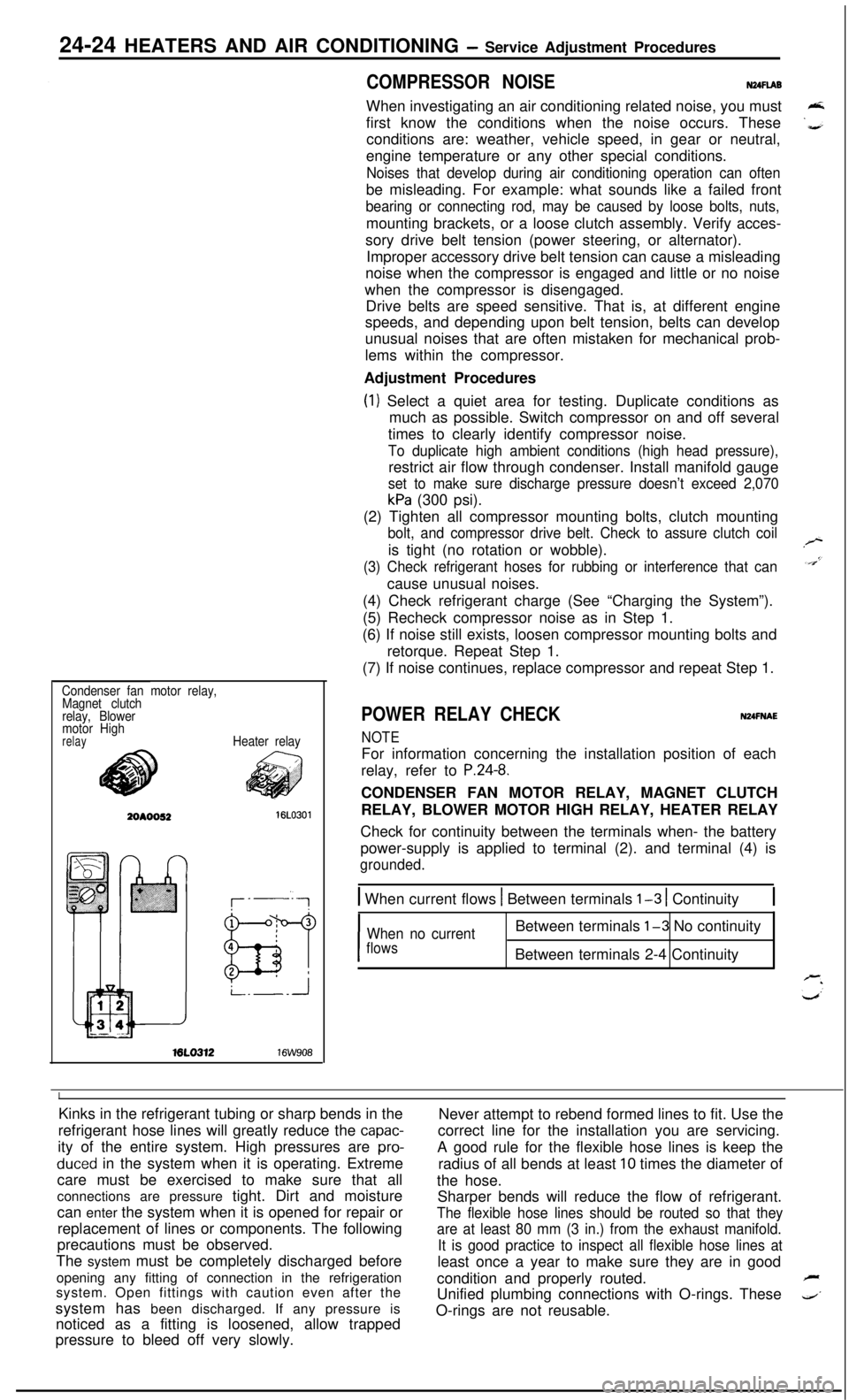
24-24 HEATERS AND AIR CONDITIONING - Service Adjustment Procedures
COMPRESSOR NOISENUFIABWhen investigating an air conditioning related noise, you must
first know the conditions when the noise occurs. These
conditions are: weather, vehicle speed, in gear or neutral,
engine temperature or any other special conditions.
Noises that develop during air conditioning operation can oftenbe misleading. For example: what sounds like a failed front
bearing or connecting rod, may be caused by loose bolts, nuts,mounting brackets, or a loose clutch assembly. Verify acces-
sory drive belt tension (power steering, or alternator).
Improper accessory drive belt tension can cause a misleading
noise when the compressor is engaged and little or no noise
when the compressor is disengaged.
Drive belts are speed sensitive. That is, at different engine
speeds, and depending upon belt tension, belts can develop
unusual noises that are often mistaken for mechanical prob-
lems within the compressor.
Adjustment Procedures
(1) Select a quiet area for testing. Duplicate conditions as
much as possible. Switch compressor on and off several
times to clearly identify compressor noise.
To duplicate high ambient conditions (high head pressure),restrict air flow through condenser. Install manifold gauge
set to make sure discharge pressure doesn’t exceed 2,070
kPa (300 psi).
(2) Tighten all compressor mounting bolts, clutch mounting
bolt, and compressor drive belt. Check to assure clutch coilis tight (no rotation or wobble).
(3) Check refrigerant hoses for rubbing or interference that cancause unusual noises.
(4) Check refrigerant charge (See “Charging the System”).
(5) Recheck compressor noise as in Step 1.
(6) If noise still exists, loosen compressor mounting bolts and
retorque. Repeat Step 1.
(7) If noise continues, replace compressor and repeat Step 1.
Condenser fan motor relay,
Magnet clutch
relay, Blower
motor High
relayHeater relayML0312
16W908
POWER RELAY CHECKNUFNAE
NOTEFor information concerning the installation position of each
relay, refer to
P.24-8.CONDENSER FAN MOTOR RELAY, MAGNET CLUTCH
RELAY, BLOWER MOTOR HIGH RELAY, HEATER RELAY
Check for continuity between the terminals when- the battery
power-supply is applied to terminal (2). and terminal (4) is
grounded.
1 When current flows 1 Between terminals l-3 1 Continuity1
I
When no currentBetween terminals l-3 No continuity
flowsBetween terminals 2-4 Continuity
IKinks in the refrigerant tubing or sharp bends in the
Never attempt to rebend formed lines to fit. Use the
refrigerant hose lines will greatly reduce the
capac-correct line for the installation you are servicing.
ity of the entire system. High pressures are
pro-A good rule for the flexible hose lines is keep the
duced in the system when it is operating. Extreme
radius of all bends at least 10 times the diameter of
care must be exercised to make sure that all
the hose.
connections are pressure tight. Dirt and moisture
Sharper bends will reduce the flow of refrigerant.
can enter the system when it is opened for repair or
The flexible hose lines should be routed so that theyreplacement of lines or components. The following
are at least 80 mm (3 in.) from the exhaust manifold.precautions must be observed.
It is good practice to inspect all flexible hose lines atThe system must be completely discharged before
least once a year to make sure they are in good
opening any fitting of connection in the refrigeration
condition and properly routed.
Fsystem. Open fittings with caution even after the
Unified plumbing connections with O-rings. These
4’system has been discharged. If any pressure is
noticed as a fitting is loosened, allow trappedO-rings are not reusable.
pressure to bleed off very slowly.
Page 1169 of 1216
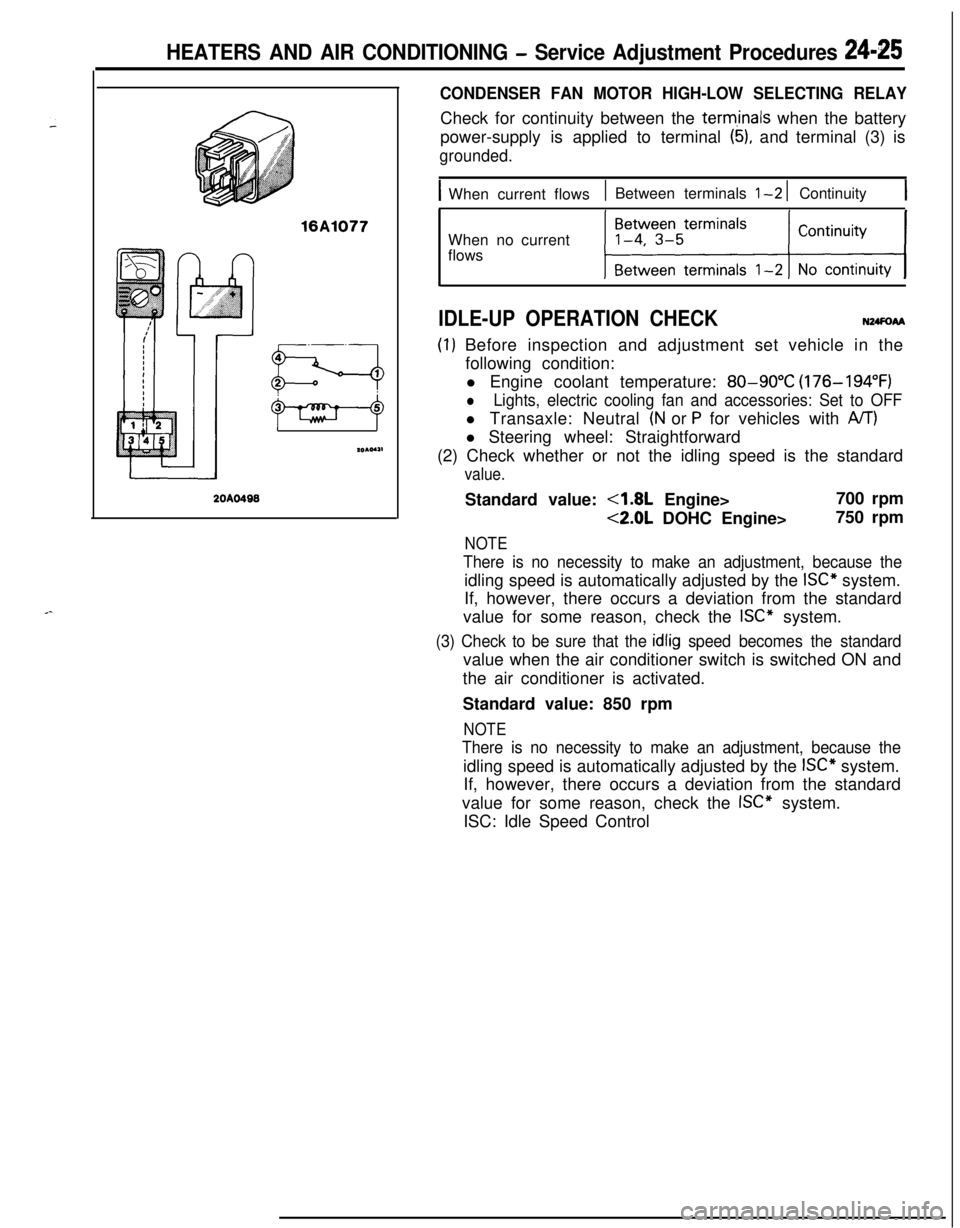
HEATERS AND AIR CONDITIONING - Service Adjustment Procedures 24-25
16A1077
20AO499
CONDENSER FAN MOTOR HIGH-LOW SELECTING RELAYCheck for continuity between the
term,inals when the battery
power-supply is applied to terminal
(5), and terminal (3) is
grounded.
IWhen current flows1 Between terminals l-2 1 Continuity1When no current
flows
IDLE-UP OPERATION CHECKN24FoAA
(I) Before inspection and adjustment set vehicle in the
following condition:
l Engine coolant temperature:
80-90°C (176-194°F)
lLights, electric cooling fan and accessories: Set to OFFl Transaxle: Neutral
(N or P for vehicles with A/T)l Steering wheel: Straightforward
(2) Check whether or not the idling speed is the standard
value.Standard value:
4.8L Engine>700 rpm
<2.0L DOHC Engine>750 rpm
NOTE
There is no necessity to make an adjustment, because theidling speed is automatically adjusted by the
ISC” system.
If, however, there occurs a deviation from the standard
value for some reason, check the
ISC” system.
(3) Check to be sure that the idlig speed becomes the standardvalue when the air conditioner switch is switched ON and
the air conditioner is activated.
Standard value: 850 rpm
NOTE
There is no necessity to make an adjustment, because theidling speed is automatically adjusted by the
ISC” system.
If, however, there occurs a deviation from the standard
value for some reason, check the
ISC” system.
ISC: Idle Speed Control
Page 1175 of 1216
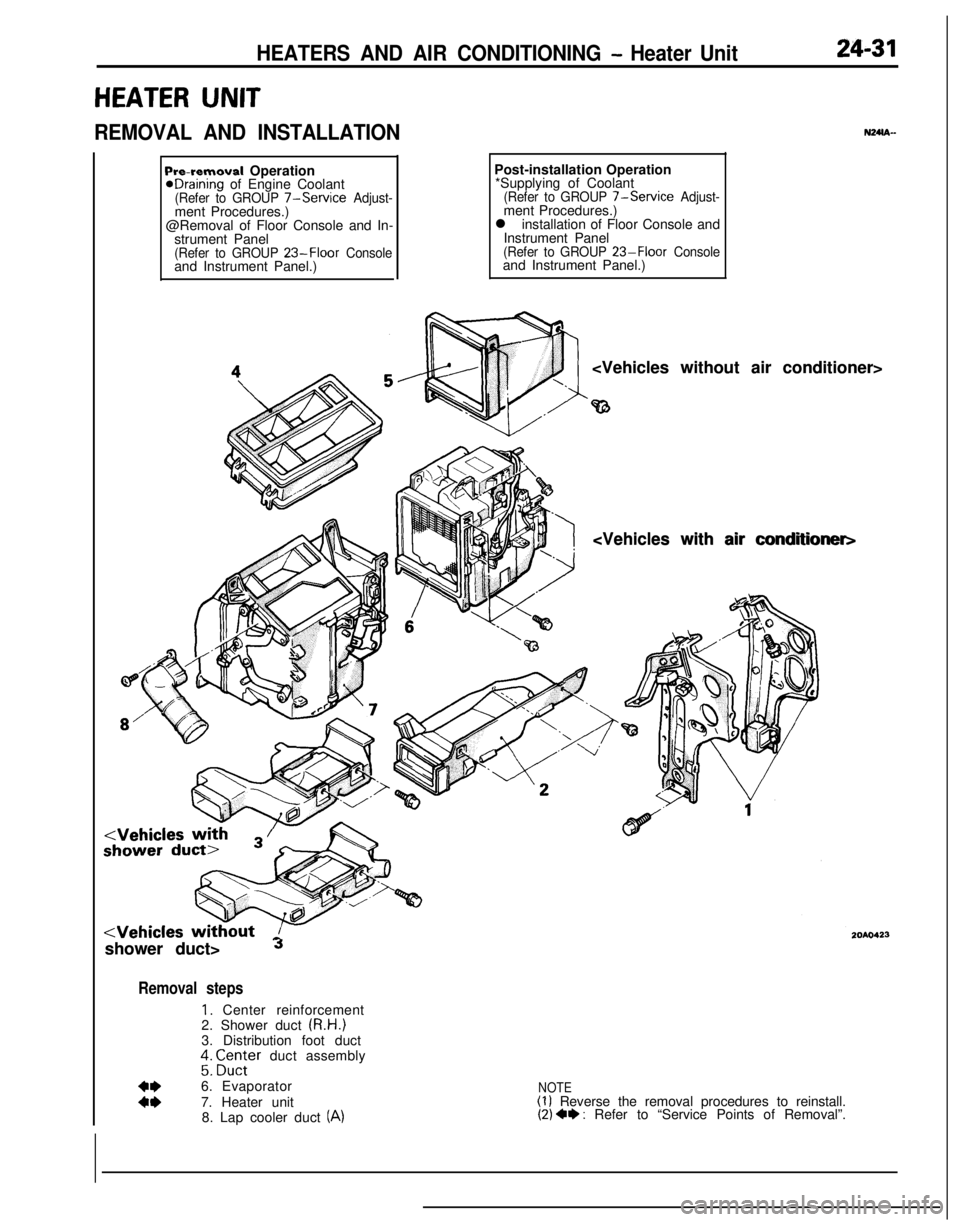
HEATERS AND AIR CONDITIONING - Heater Unit24-31
HEATER UNIT
REMOVAL AND INSTALLATIONN24m-
Pre-removal OperationeDraining of Engine Coolant(Refer to GROUP 7-Service Adjust-ment Procedures.)
@Removal of Floor Console and In-
strument Panel
(Refer to GROUP 23-Floor Consoleand Instrument Panel.)Post-installation Operation
*Supplying of Coolant
(Refer to GROUP 7-Service Adjust-ment Procedures.)
l installation of Floor Console and
Instrument Panel
(Refer to GROUP 23-Floor Consoleand Instrument Panel.)
shower duct>
Jshower duct>
Removal steps
1. Center reinforcement
2. Shower duct (R.H.)
3. Distribution foot duct
;: ;Z;;er duct assembly
:z6. Evaporator
7. Heater unit
8. Lap cooler duct (A)
NOTE(1) Reverse the removal procedures to reinstall.(2) 4* : Refer to “Service Points of Removal”.
Page 1181 of 1216
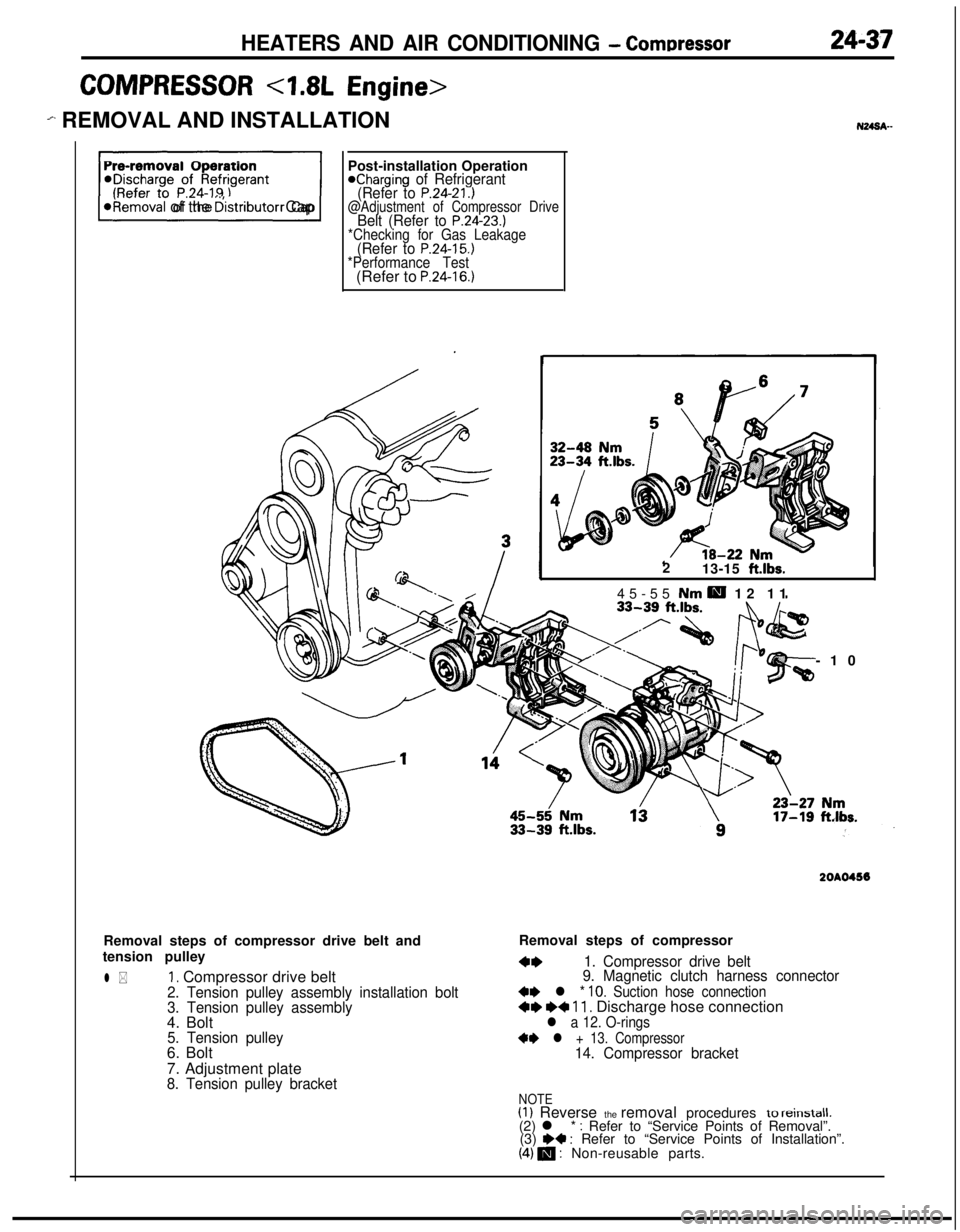
HEATERS AND AIR CONDITIONING - ComDressor24-37
COMPRESSOR <7.8L Engine>
em REMOVAL AND INSTALLATION
F)
*Removal of the distributor CapPost-installation Operation
@Charging of Refrigerant
(Refer to P.24-21.)@Adjustment of Compressor DriveBelt (Refer to P.24-23.)*Checking for Gas Leakage(Refer to P.24-15.)*Performance Test(Refer to P.24-16.)Removal steps of compressor drive belt and
tension pulley
l *1, Compressor drive belt2. Tension pulley assembly installation bolt
3. Tension pulley assembly4. Bolt
5. Tension pulley6. Bolt
7. Adjustment plate
8. Tension pulley bracket2
13-15
ft.lbs.45-55 Nm
H 12 11
-10
2OAO456Removal steps of compressor
4*1. Compressor drive belt
9. Magnetic clutch harness connector
+e l * 10. Suction hose connection+e I)+ 11. Discharge hose connectionl a 12. O-rings
+* l + 13. Compressor14. Compressor bracket
NOTE(1) Reverse the removal procedures to reinstall.(2) l * : Refer to “Service Points of Removal”.
(3) W : Refer to “Service Points of Installation”.(4) m : Non-reusable parts.
Page 1184 of 1216
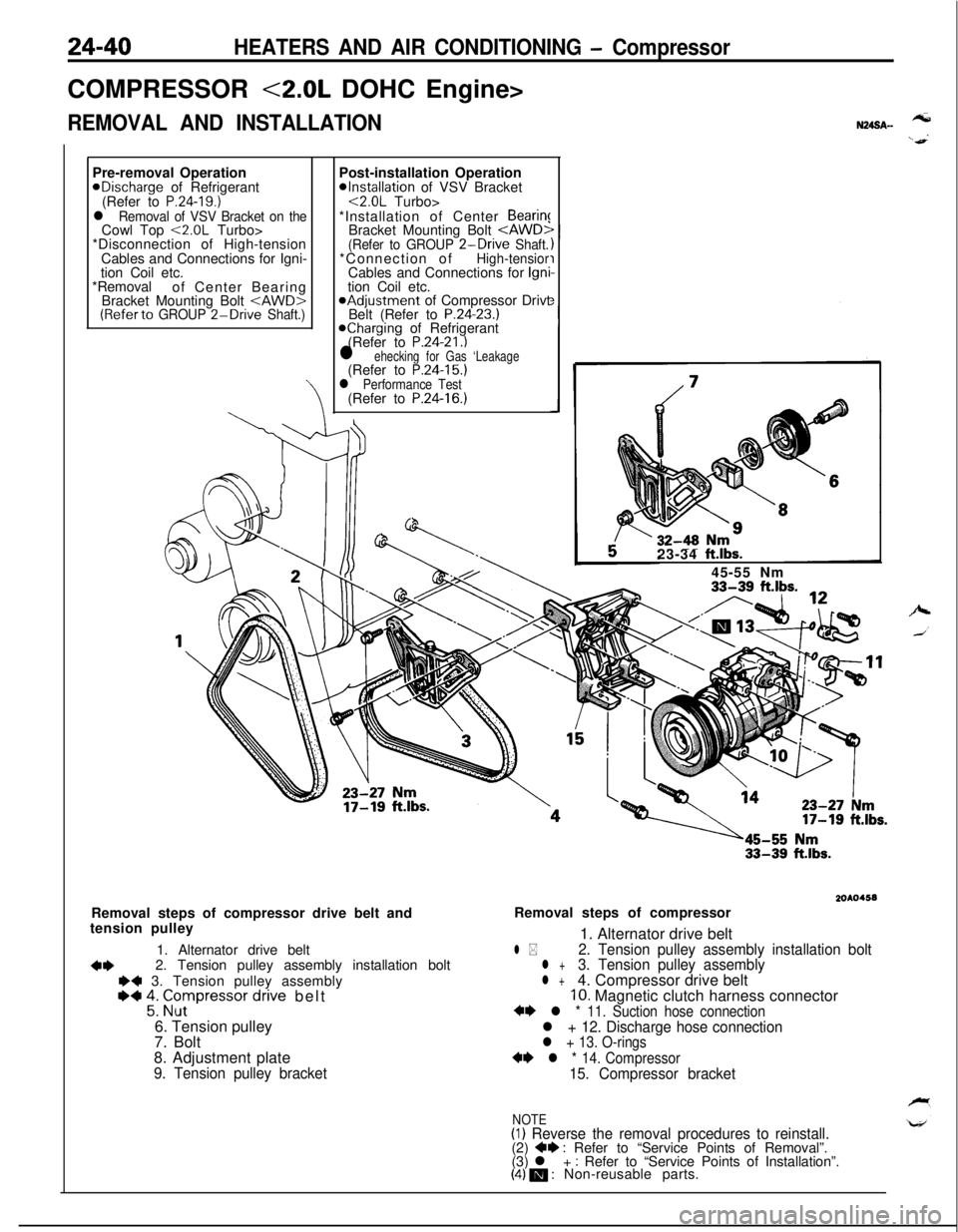
24-40HEATERS AND AIR CONDITIONING - CompressorCOMPRESSOR
<2.0L DOHC Engine>
REMOVAL AND INSTALLATIONPre-removal OperationaDischarge of Refrigerant
(Refer to
P.24-19.)l Removal of VSV Bracket on theCowl Top <2.0L Turbo>
*Disconnection of High-tension
Cables and Connections for Igni-
tion Coil etc.
*Removal
of Center Bearing
Bracket Mounting Bolt
*Installation of VSV Bracket<2.0L Turbo>
*Installation of Center
Bearin!Bracket Mounting Bolt
Belt (Refer to P.24-23.)Kharging of Refrigerant
(Refer to P.24-21.)l ehecking for Gas ‘Leakage(Refer to P.24-15.)l Performance Test(Refer to P.24-16.)
N24SA.-tension pulley
1. Alternator drive belt
4*2. Tension pulley assembly installation boltI)+ 3. Tension pulley assembly~~ 2: Grpressor dnve belt
6. Tension pulley
7. Bolt
8. Adjustment plate
9. Tension pulley bracket23-34
ft.lbs.45-55 Nm
33-39 ft.lbs.
2OAO4.58Removal steps of compressor drive belt andRemoval steps of compressor
1. Alternator drive belt
l *2. Tension pulley assembly installation boltl +3. Tension pulley assemblyl +4. Compressor drive belt10. Magnetic clutch harness connector+* l * 11. Suction hose connectionl + 12. Discharge hose connectionl + 13. O-rings
** l * 14. Compressor15. Compressor bracket
NOTE(I) Reverse the removal procedures to reinstall.(2) +e : Refer to “Service Points of Removal”.
(3) l + : Refer to “Service Points of Installation”.(4) m : Non-reusable parts.
Page 1189 of 1216
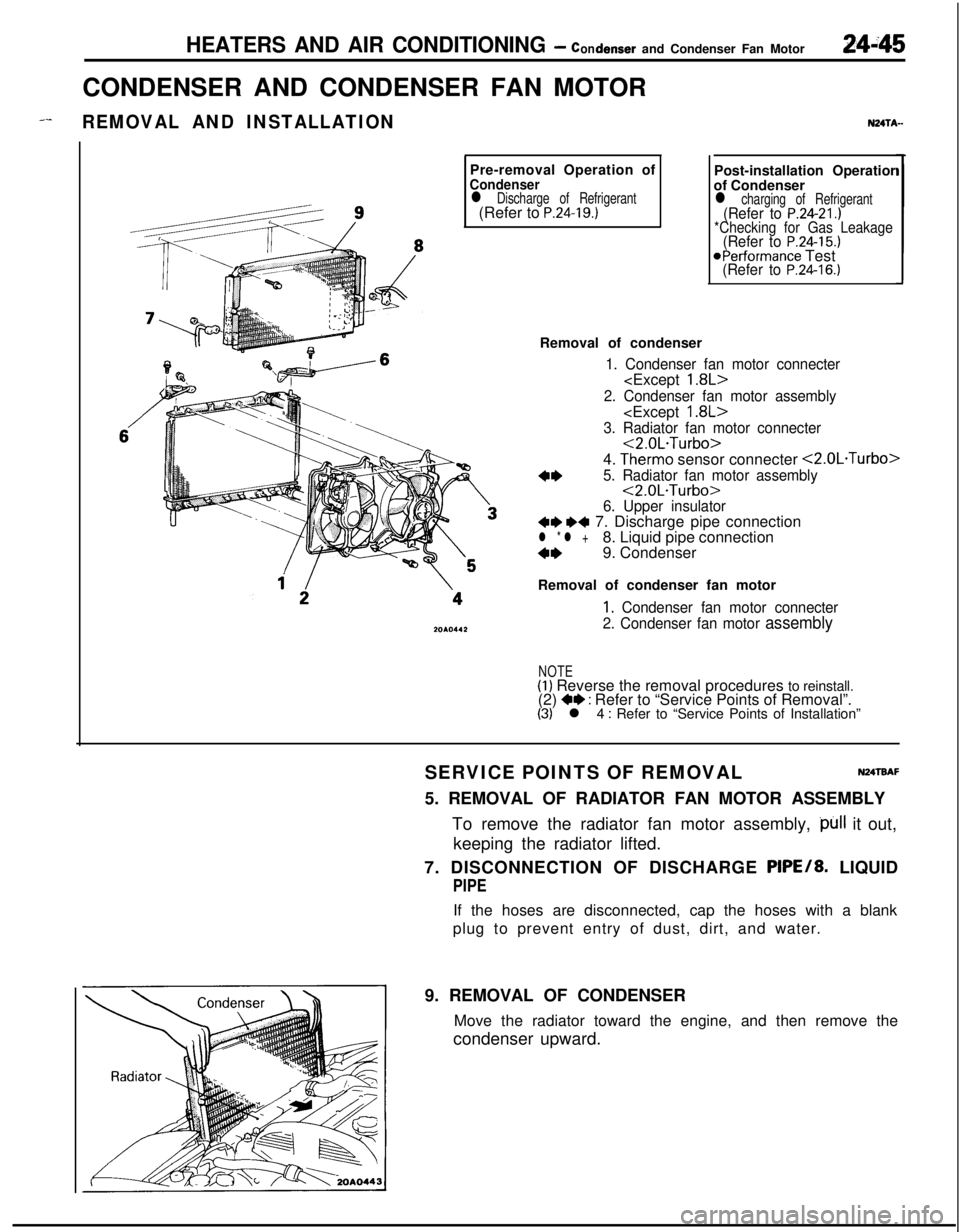
HEATERS AND AIR CONDITIONING - condenser and Condenser Fan Motor24i45CONDENSER AND CONDENSER FAN MOTOR
_--REMOVAL AND INSTALLATIONPre-removal Operation of
Condenserl Discharge of Refrigerant(Refer to P.24-19.)
NZITA-Post-installation Operatior
of Condenser
l charging of Refrigerant(Refer to P.24-21.)*Checking for Gas Leakage(Refer to P.24-15.)@Performance Test(Refer to P.24-16.)Removal of condenser
1. Condenser fan motor connecter
2. Condenser fan motor assembly
3. Radiator fan motor connecter<2.0L.Turbo>
4.
Therm0 sensor connecter <2.0L.Turbo>
4*5. Radiator fan motor assembly<2.0L.Turbo>
6. Upper insulator+e ~~ 7. Discharge pipe connectionl * l +8. Liquid pipe connection
4*9. Condenser
Removal of condenser fan motor
1, Condenser fan motor connecter
2. Condenser fan motor
assembly
NOTE(1) Reverse the removal procedures to reinstall.
(2) +e : Refer to “Service Points of Removal”.(3) l 4 : Refer to “Service Points of Installation”
SERVICE POINTS OF REMOVAL
N24TBAF5. REMOVAL OF RADIATOR FAN MOTOR ASSEMBLY
To remove the radiator fan motor assembly,
)~ll it out,
keeping the radiator lifted.
7. DISCONNECTION OF DISCHARGE PIPE/8. LIQUID
PIPEIf the hoses are disconnected, cap the hoses with a blank
plug to prevent entry of dust, dirt, and water.
9. REMOVAL OF CONDENSER
Move the radiator toward the engine, and then remove the
condenser upward.