MITSUBISHI GALANT 1989 Service Repair Manual
Manufacturer: MITSUBISHI, Model Year: 1989, Model line: GALANT, Model: MITSUBISHI GALANT 1989Pages: 1273, PDF Size: 37.62 MB
Page 1041 of 1273
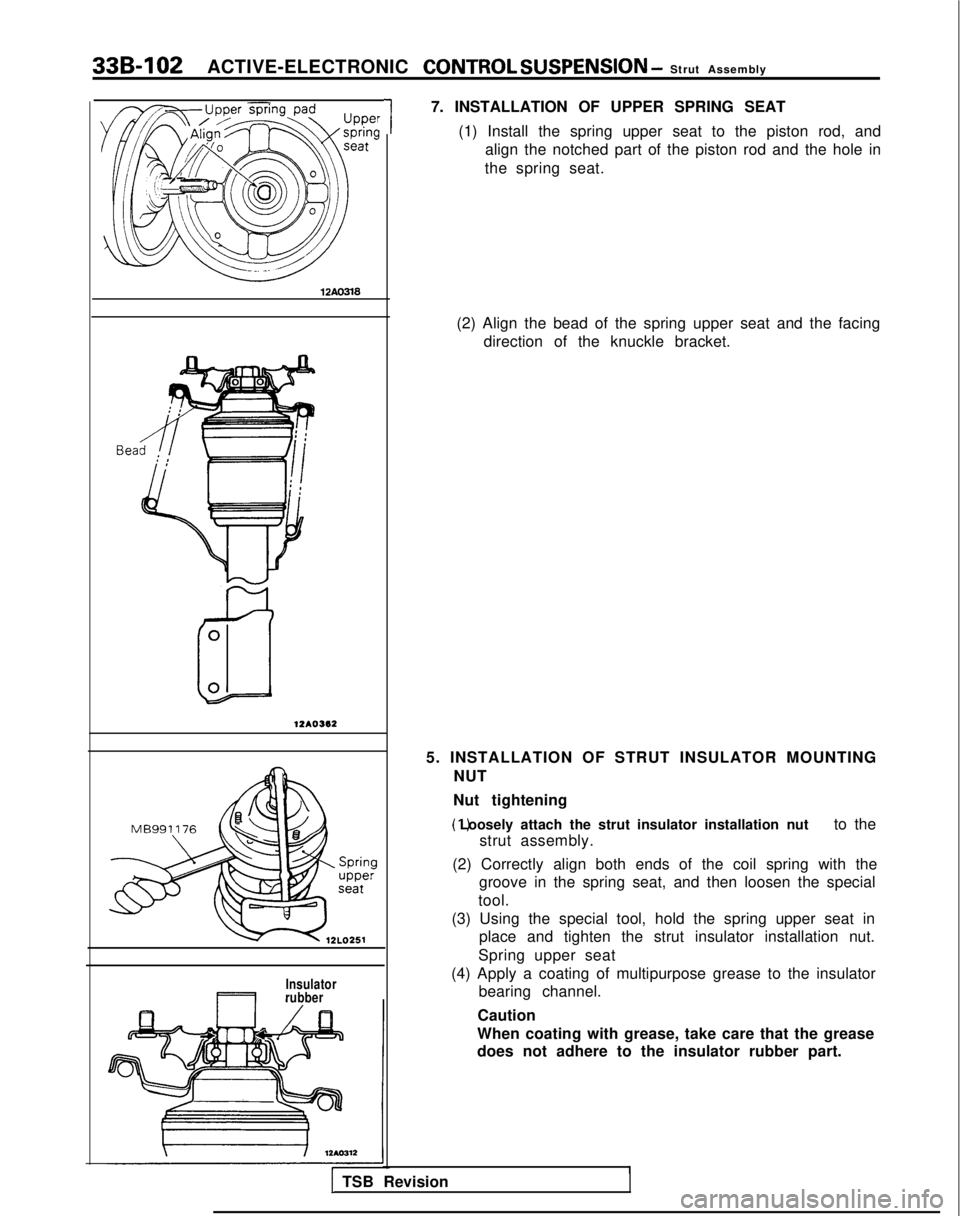
33B-IO2
ACTIVE-ELECTRONIC CONTROL SUSPENSION - Strut Assembly
12Ao3l8
Bea
12AOSI2
Insulator
rubber
1
7. INSTALLATION OF UPPER SPRING SEAT
(1) Install the spring upper seat to the piston rod, andalign the notched part of the piston rod and the hole in
the spring seat.
(2) Align the bead of the spring upper seat and the facing direction of the knuckle bracket.
5. INSTALLATION OF STRUT INSULATOR MOUNTING NUT
Nut tightening (1) Loosely attach the strut insulator installation nut
to the
strut assembly.
(2) Correctly align both ends of the coil spring with the groove in the spring seat, and then loosen the special
tool.
(3) Using the special tool, hold the spring upper seat in place and tighten the strut insulator installation nut.
Spring upper seat
(4) Apply a coating of multipurpose grease to the insulator bearing channel.
Caution
When coating with grease, take care that the grease
does not adhere to the insulator rubber part.
I1 TSB Revision
Page 1042 of 1273
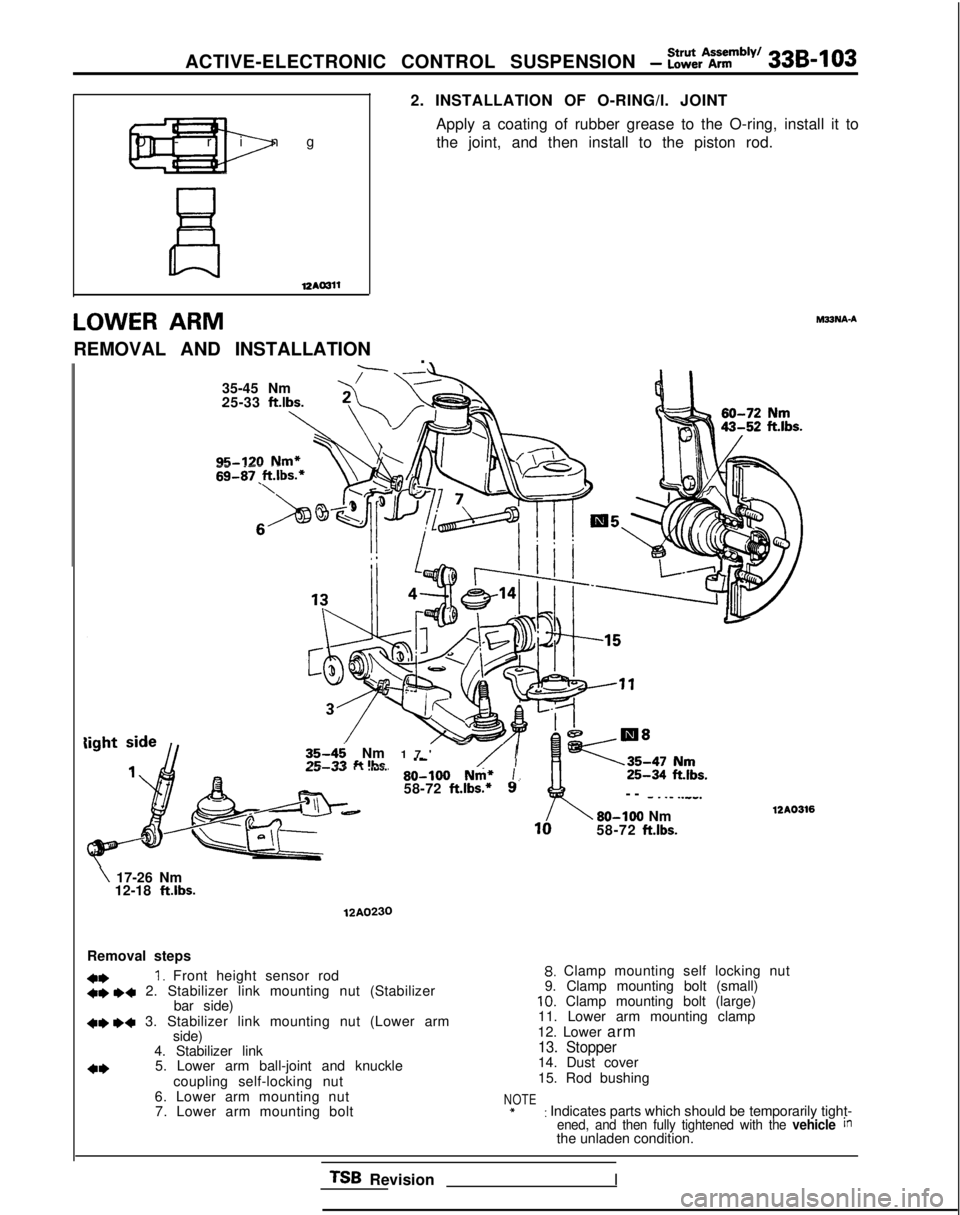
ACTIVE-ELECTRONIC CONTROL SUSPENSION - f:::,%tmb’y’ 33B-103
pF&O-rin
g
81210311
2. INSTALLATION OF O-RING/l. JOINT
Apply a coating of rubber grease to the O-ring, install it tothe joint, and then install to the piston rod.
LOWER ARM
REMOVAL AND INSTALLATION .
35-45 Nm
25-33
ft.lbs.
.-- ~~69-87 .ft.lbs.*
eLII-uu. . ..“a. 80-100
Nni*
1.
35-45 Nm 17
'
- /I MJJNA-A
58-72
ft.lbs.* 9
---. .- ..__.
SO-100 Nm12A0316
1058-72ft.lbs.
\ 17-26 Nm
12-18 ft.lbs.
lZA0230
Removal steps
4*1. Front height sensor rod+e I)+ 2. Stabilizer link mounting nut (Stabilizer
bar side)
+e I)* 3. Stabilizer link mounting nut (Lower armside)
4. Stabilizer link
4*5. Lower arm ball-joint and knuckle
coupling self-locking nut
6. Lower arm mounting nut 7. Lower arm mounting bolt
8. Clamp mounting self locking nut
9. Clamp mounting bolt (small)
10. Clamp mounting bolt (large)
11. Lower arm mounting clamp
12. Lower arm
13. Stopper14. Dust cover
15. Rod bushing
NOTE*: Indicates parts which should be temporarily tight-ened, and then fully tightened with the vehicle inthe unladen condition.
TSB RevisionI
Page 1043 of 1273
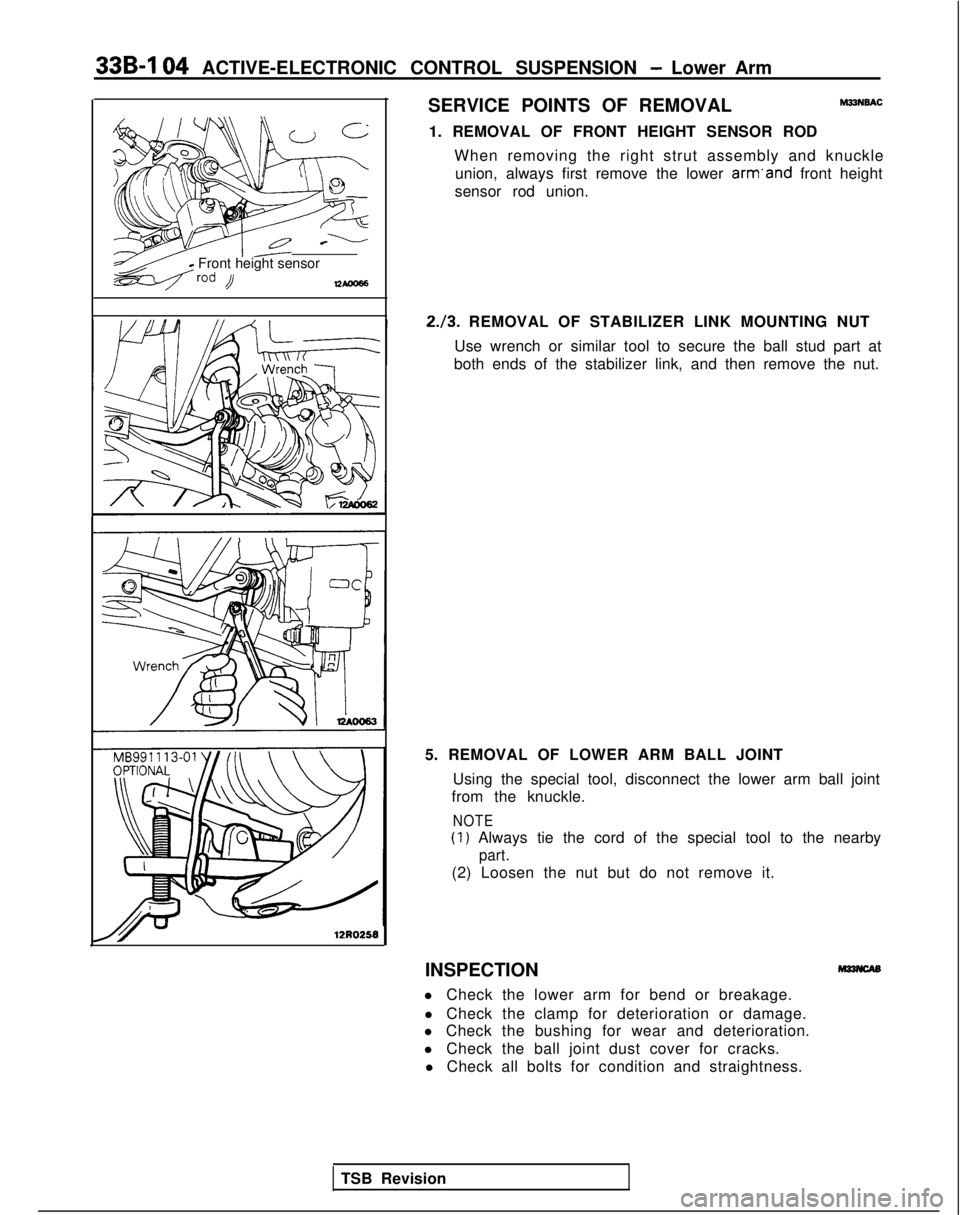
339-l 04 ACTIVE-ELECTRONIC CONTROL SUSPENSION - Lower Arm
SERVICE POINTS OF REMOVAL
hl33NBAC
1. REMOVAL OF FRONT HEIGHT SENSOR ROD When removing the right strut assembly and knuckleunion, always first remove the lower arm’and
front height
sensor rod union.
yz--q--o .-L
T Front height sensor
lzAm66
12RO258
2./3. REMOVAL OF STABILIZER LINK MOUNTING NUT
Use wrench or similar tool to secure the ball stud part at
both ends of the stabilizer link, and then remove the nut.
5. REMOVAL OF LOWER ARM BALL JOINT Using the special tool, disconnect the lower arm ball joint
from the knuckle.
NOTE
(1) Always tie the cord of the special tool to the nearby
part.
(2) Loosen the nut but do not remove it.
INSPECTION
l Check the lower arm for bend or breakage. l Check the clamp for deterioration or damage.
l Check the bushing for wear and deterioration.
l Check the ball joint dust cover for cracks.
l Check all bolts for condition and straightness.
TSB Revision
Page 1044 of 1273
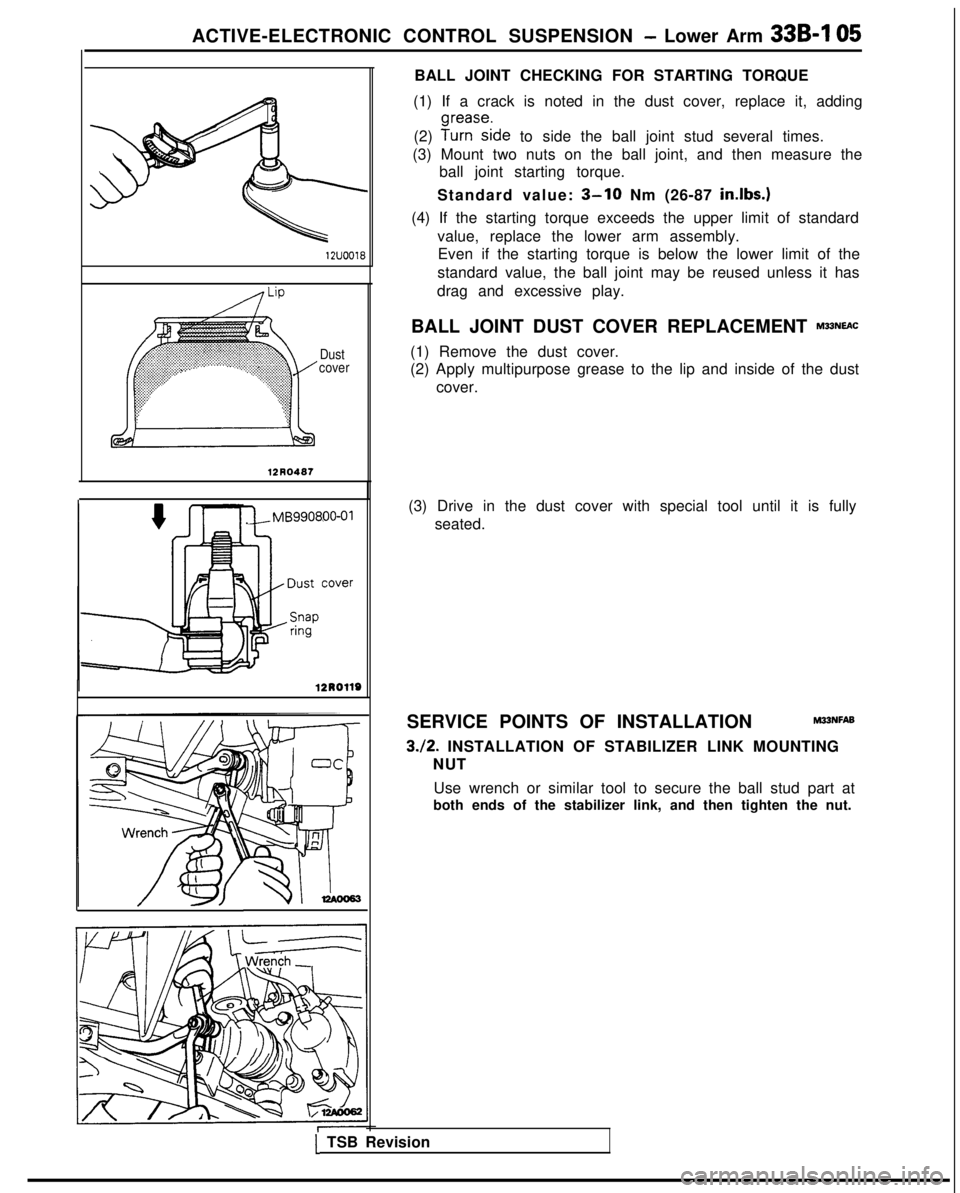
ACTIVE-ELECTRONIC CONTROL SUSPENSION - Lower Arm 339-l
05 12UOO18
Dust
cover
12R0487
j/MB990800-01
BALL JOINT CHECKING FOR STARTING TORQUE
(1) If a crack is noted in the dust cover, replace it, adding
(2)
?:“rE?/de to side the ball joint stud several times.
(3) Mount two nuts on the ball joint, and then measure the ball joint starting torque.
Standard value:
3-10 Nm (26-87 in.lbs.)
(4) If the starting torque exceeds the upper limit of standard value, replace the lower arm assembly.Even if the starting torque is below the lower limit of the
standard value, the ball joint may be reused unless it has
drag and excessive play.
BALL JOINT DUST COVER REPLACEMENT
M=NEAC
(1) Remove the dust cover.
(2) Apply multipurpose grease to the lip and inside of the dust cover.
(3) Drive in the dust cover with special tool until it is fully seated.
SERVICE POINTS OF INSTALLATION
M33NFAB
3./2. INSTALLATION OF STABILIZER LINK MOUNTING
NUT
Use wrench or similar tool to secure the ball stud part at
both ends of the stabilizer link, and then tighten the nut.
1 TSB Revision
Page 1045 of 1273
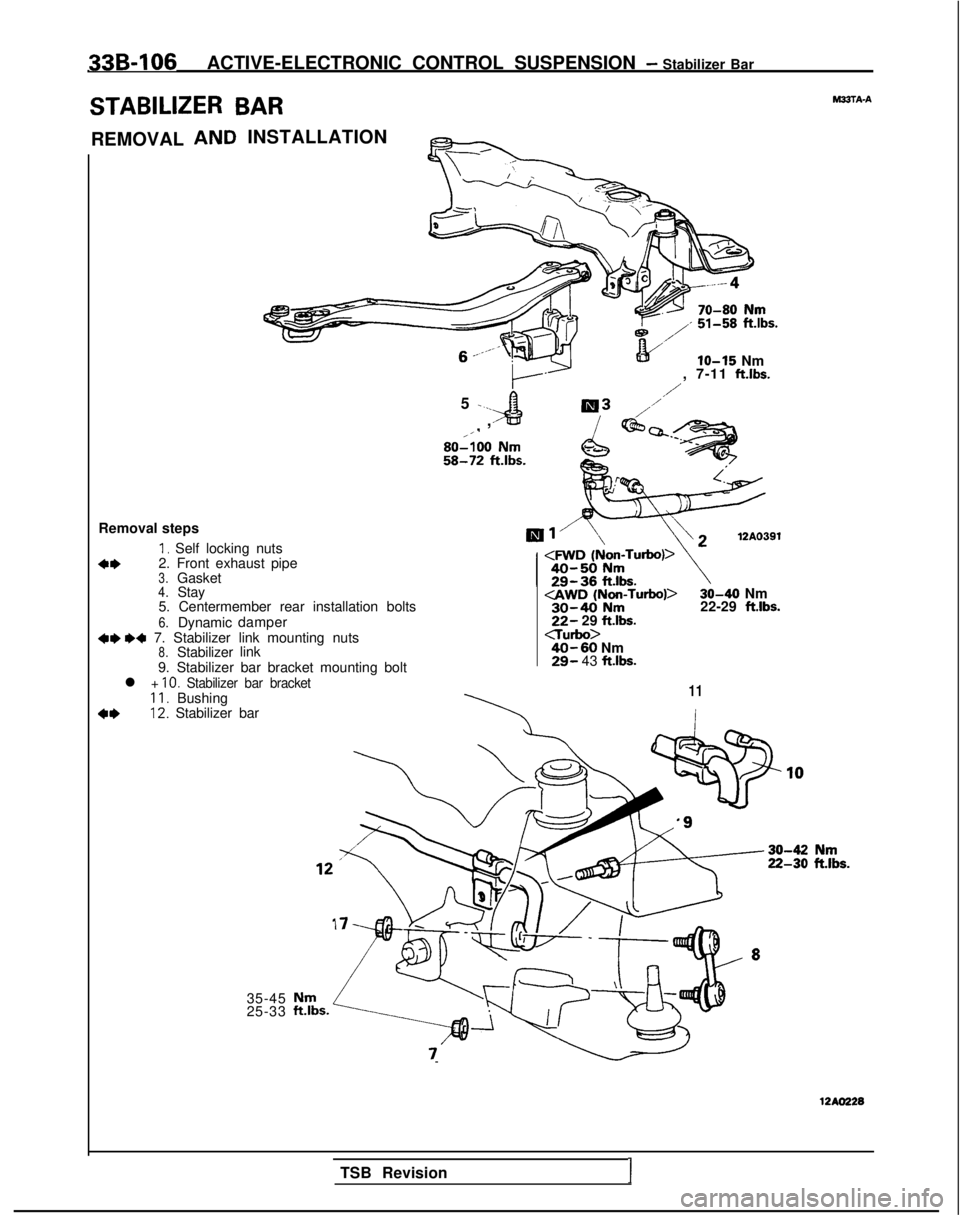
33B-106ACTIVE-ELECTRONIC CONTROL SUSPENSION - Stabilizer Bar
STABILIZER BARMBBTA-A
REMOVALINSTALLATION
lo-15 Nm
Removal steps
1, Self locking nuts
4*2. Front exhaust pipe3.Gasket4.Stay
5. Centermember rear installation bolts
6.Dynamic damper+I) .C 7. Stabilizer link mounting nuts8.Stabilizer link
9. Stabilizer bar bracket mounting bolt
l + 10. Stabilizer bar bracket11.Bushing
*I)12. Stabilizer bar
35-45
Nm25-33ft.lbs.
I---.I
5 ‘_.
x4,
,
BOL;OO Nm58-72 ft.lbs.
, 7-11 ti.lbs.
/ ~OWD$NN~-TurbO
30-40 Nm
22-29 ft.lbs.22- 29 ft.lbs. crurbo>
40-60 Nm29- 43 ft.lbs.
11
12440228
TSB Revision1
Page 1046 of 1273
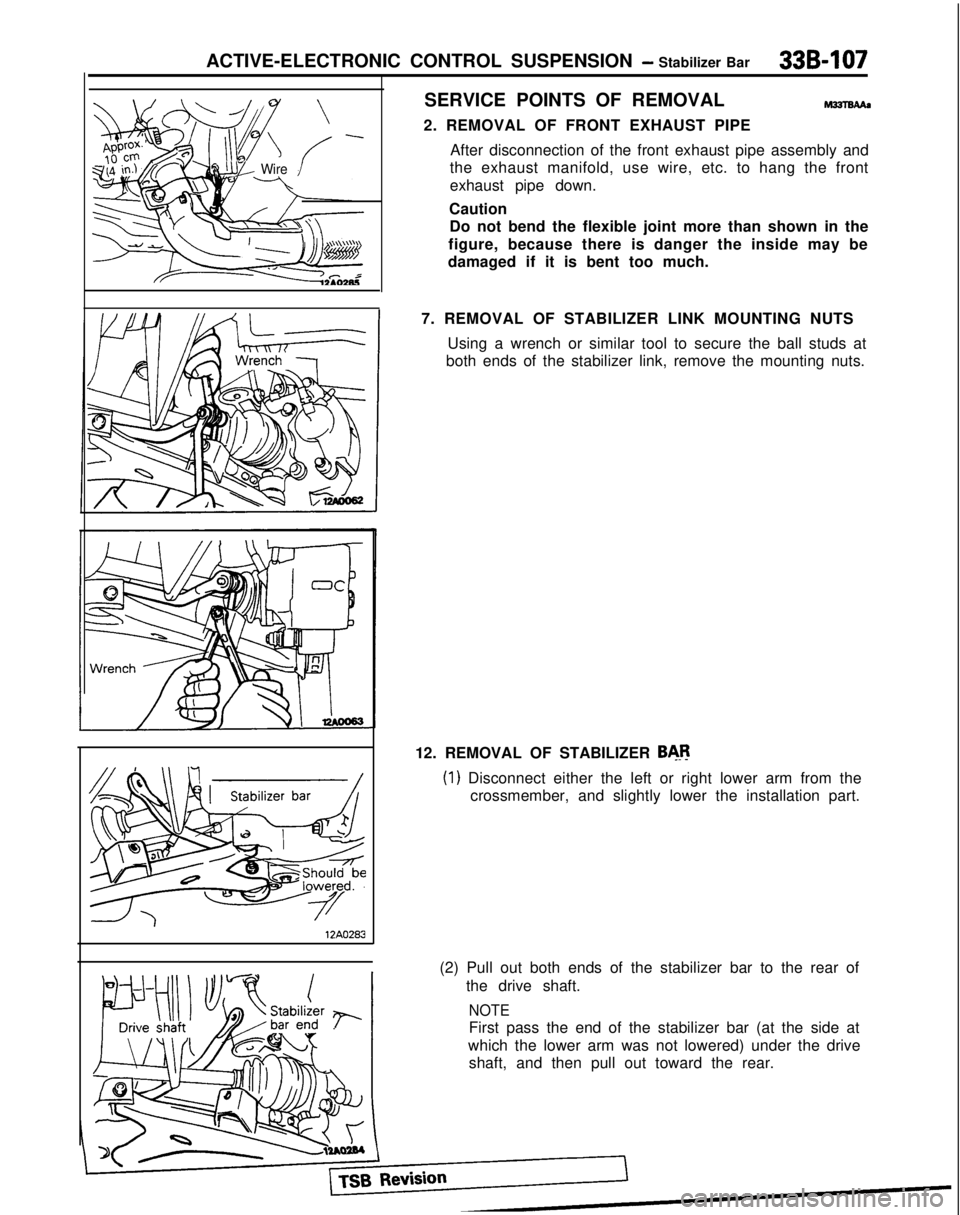
ACTIVE-ELECTRONIC CONTROL SUSPENSION - Stabilizer Bar33Bl107
UL Wire/
12A0283SERVICE POINTS OF REMOVAL
2. REMOVAL OF FRONT EXHAUST PIPE
After disconnection of the front exhaust pipe assembly and
the exhaust manifold, use wire, etc. to hang the front
exhaust pipe down.
Caution Do not bend the flexible joint more than shown in the
figure, because there is danger the inside may be
damaged if it is bent too much.
7. REMOVAL OF STABILIZER LINK MOUNTING NUTS Using a wrench or similar tool to secure the ball studs at
both ends of the stabilizer link, remove the mounting nuts.
12. REMOVAL OF STABILIZER
BAR
(1) Disconnect either the left or right lower arm from the crossmember, and slightly lower the installation part.
(2) Pull out both ends of the stabilizer bar to the rear of the drive shaft.
NOTE
First pass the end of the stabilizer bar (at the side at
which the lower arm was not lowered) under the drive shaft, and then pull out toward the rear.
Page 1047 of 1273
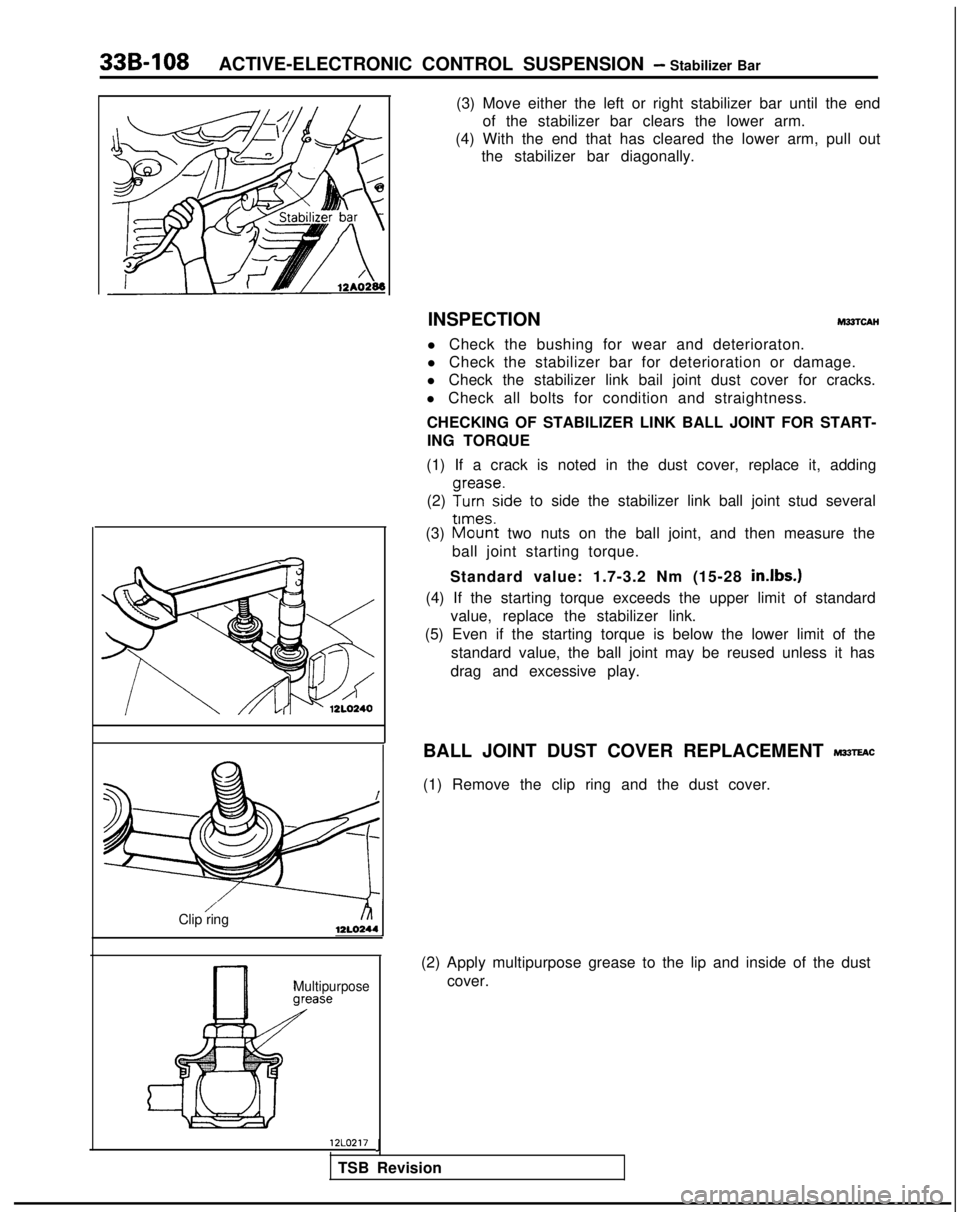
33B-108ACTIVE-ELECTRONIC CONTROL SUSPENSION - Stabilizer Bar
/Clip ring
Multipurpose
(3) Move either the left or right stabilizer bar until the endof the stabilizer bar clears the lower arm.
(4) With the end that has cleared the lower arm, pull out the stabilizer bar diagonally.
INSPECTION M33lCAH
l Check the bushing for wear and deterioraton.
l Check the stabilizer bar for deterioration or damage.
l Check the stabilizer link bail joint dust cover for cracks.
l Check all bolts for condition and straightness.
CHECKING OF STABILIZER LINK BALL JOINT FOR START-ING TORQUE
(1) If a crack is noted in the dust cover, replace it, adding
(2)
?:“li?de to side the stabilizer link ball joint stud several
(3)
h!E% two nuts on the ball joint, and then measure the
ball joint starting torque.
Standard value: 1.7-3.2 Nm (15-28
in.lbs.1
(4) If the starting torque exceeds the upper limit of standard value, replace the stabilizer link.
(5) Even if the starting torque is below the lower limit of the
standard value, the ball joint may be reused unless it has
drag and excessive play.
BALL JOINT DUST COVER REPLACEMENT
mxrrmc
(1) Remove the clip ring and the dust cover.
(2) Apply multipurpose grease to the lip and inside of the dust cover. 12LO217
J
TSB Revision
Page 1048 of 1273
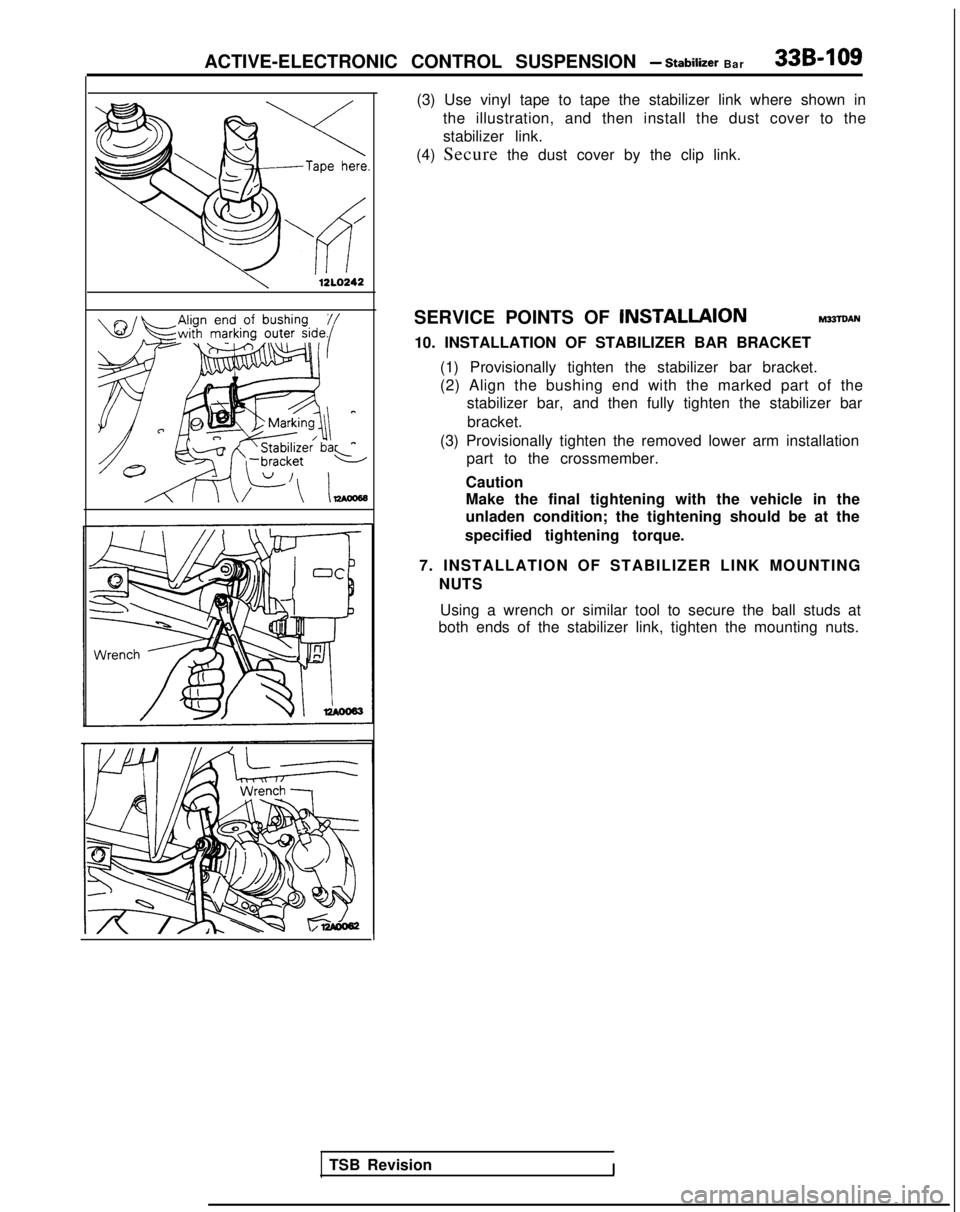
ACTIVE-ELECTRONIC CONTROL SUSPENSION - Stabilizer Bar33B-109
(3) Use vinyl tape to tape the stabilizer link where shown in
the illustration, and then install the dust cover to the
stabilizer link.
(4) Secure the dust cover by the clip link.
SERVICE POINTS OF INSTALLAION
M33TOAN
10. INSTALLATION OF STABILIZER BAR BRACKET
(1) Provisionally tighten the stabilizer bar bracket.
(2) Align the bushing end with the marked part of the stabilizer bar, and then fully tighten the stabilizer bar
bracket.
(3) Provisionally tighten the removed lower arm installation part to the crossmember.
Caution
Make the final tightening with the vehicle in the
unladen condition; the tightening should be at the
specified tightening torque.
7. INSTALLATION OF STABILIZER LINK MOUNTING NUTS
Using a wrench or similar tool to secure the ball studs at
both ends of the stabilizer link, tighten the mounting nuts.
TSB Revision
I
Page 1049 of 1273
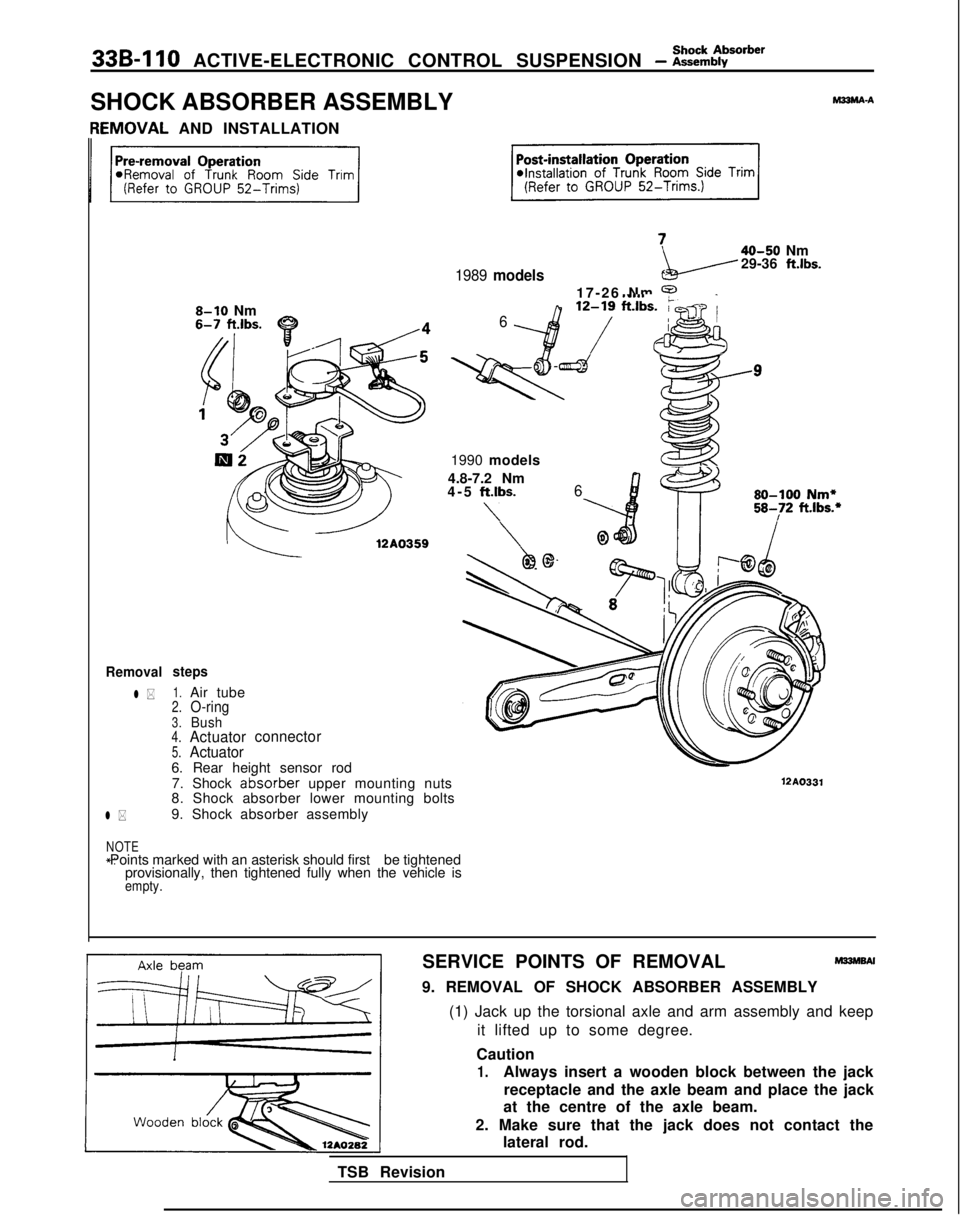
33B-110 ACTIVE-ELECTRONIC CONTROL SUSPENSION - i=ttbborber
SHOCK ABSORBER ASSEMBLYhl33MA-A[EMOVAL
AND INSTALLATION
1989 models
40-50 Nm
29-36 ft.lbs.
Removal
l *
l *
8-10 Nm
steps
1.Air tube2.O-ring3.Bush4.Actuator connector5.Actuator6. Rear height sensor rod
6
17-26 Nm 9127 ft.lbs;.i
1990 modelsz??
4.8-7.2 Nm
4-5 ftlbs.
\
6 80-100
Nm*
58-72
ft.lbs.*
7. Shock at%orber
upper mounting nuts
8. Shock absorber lower mounting bolts
9. Shock absorber assemblyWA0331
NOTE *: Points marked with an asterisk should first
be tightened
provisionally, then tightened fully when the vehicle is
empty.
SERVICE POINTS OF REMOVALm33hlsN
9. REMOVAL OF SHOCK ABSORBER ASSEMBLY
(1) Jack up the torsional axle and arm assembly and keep it lifted up to some degree.
Caution
1.Always insert a wooden block between the jack receptacle and the axle beam and place the jack
at the centre of the axle beam.
2. Make sure that the jack does not contact the lateral rod.
TSB Revision
Page 1050 of 1273
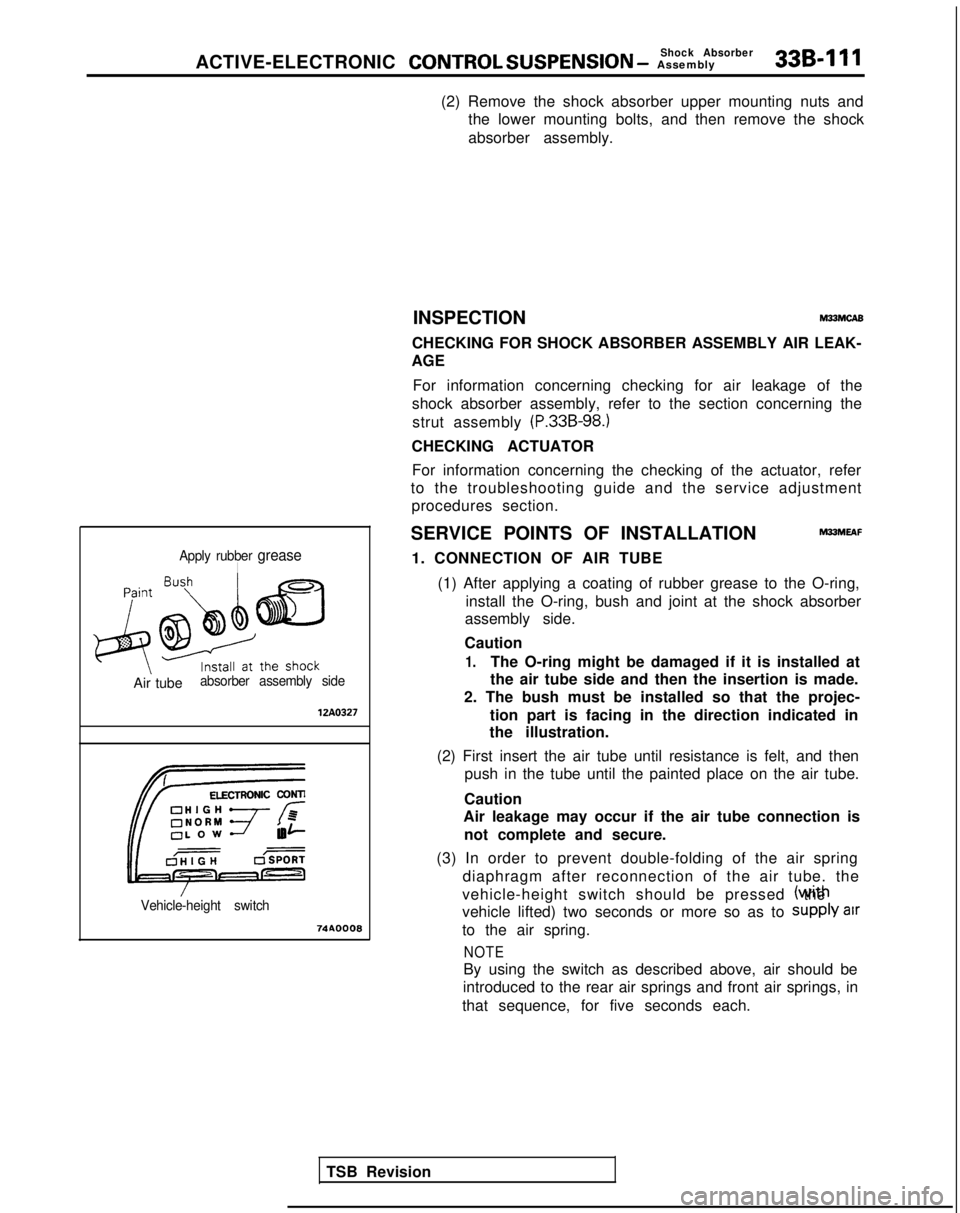
Shock AbsorberACTIVE-ELECTRONIC CONTROL SUSPENSION - Assembly339-111
(2) Remove the shock absorber upper mounting nuts andthe lower mounting bolts, and then remove the shock
absorber assembly.
Apply rubber greaseI
Air tubeabsorber assembly side 12A0327
Vehicle-height switch
741IOO08INSPECTION
M33McA8
CHECKING FOR SHOCK ABSORBER ASSEMBLY AIR LEAK-
AGE
For information concerning checking for air leakage of the
shock absorber assembly, refer to the section concerning the
strut assembly
(P.33B-98.)
CHECKING ACTUATOR
For information concerning the checking of the actuator, refer
to the troubleshooting guide and the service adjustment procedures section.
SERVICE POINTS OF INSTALLATION
M33MEAF
1. CONNECTION OF AIR TUBE (1) After applying a coating of rubber grease to the O-ring, install the O-ring, bush and joint at the shock absorber
assembly side.
Caution
1.The O-ring might be damaged if it is installed at
the air tube side and then the insertion is made.
2. The bush must be installed so that the projec-
tion part is facing in the direction indicated in
the illustration.
(2) First insert the air tube until resistance is felt, and then push in the tube until the painted place on the air tube.
Caution
Air leakage may occur if the air tube connection is
not complete and secure.
(3) In order to prevent double-folding of the air spring diaphragm after reconnection of the air tube. the
vehicle-height switch should be pressed (wrth the
vehicle lifted) two seconds or more so as to
Supply air
to the air spring.
NOTE
By using the switch as described above, air should be
introduced to the rear air springs and front air springs, in
that sequence, for five seconds each.
TSB Revision