MITSUBISHI GALANT 1989 Service Repair Manual
Manufacturer: MITSUBISHI, Model Year: 1989, Model line: GALANT, Model: MITSUBISHI GALANT 1989Pages: 1273, PDF Size: 37.62 MB
Page 241 of 1273
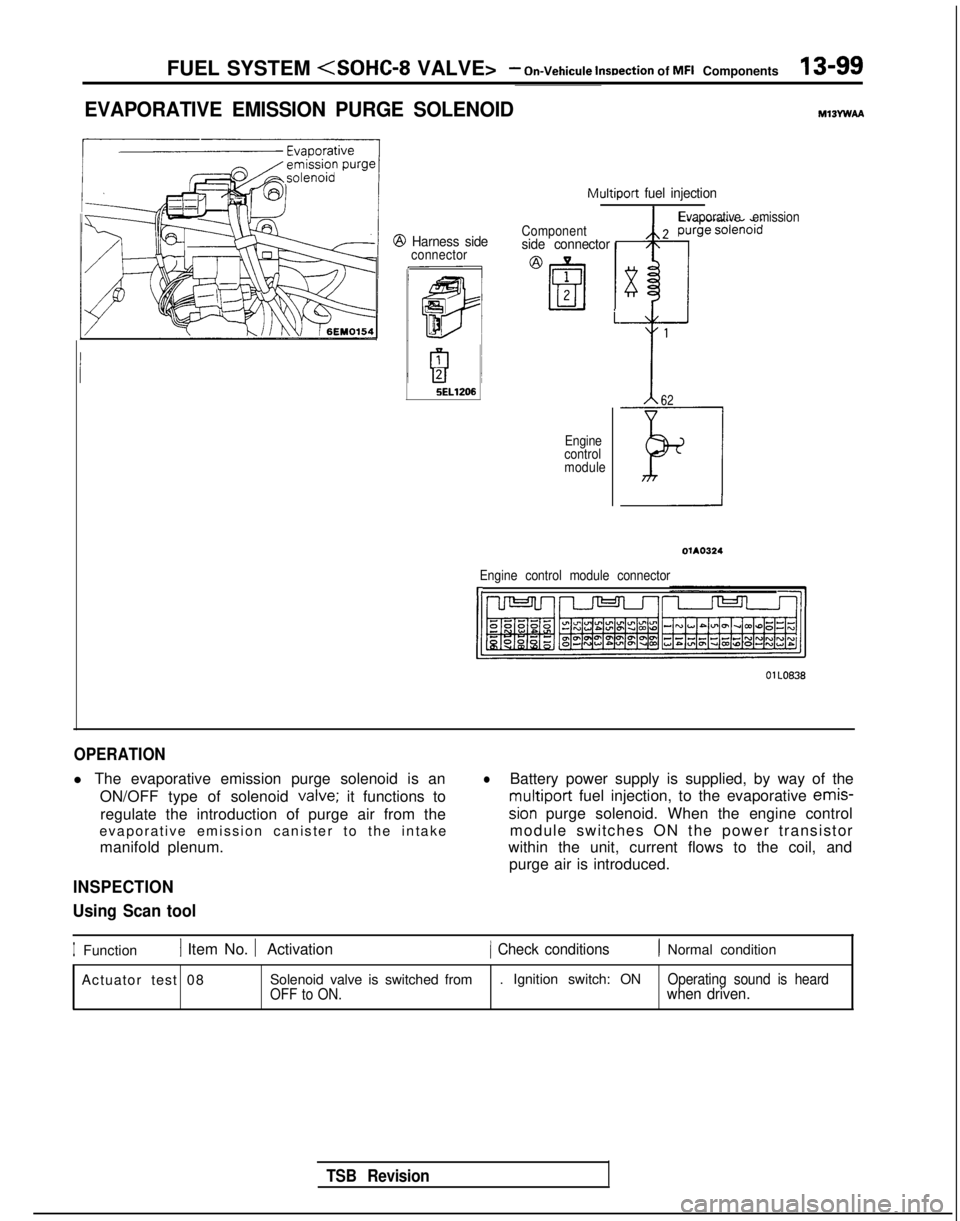
FUEL SYSTEM
EVAPORATIVE EMISSION PURGE SOLENOIDMlBYwAA
Multiport fuel injection
@ Harness sideconnector Componentside connector
i
5EL1206
Engine
control
module
TSB Revision
Evaporative emission
62
Engine control module connectorI,
OlLO838
OPERATION
l The evaporative emission purge solenoid is an
ON/OFF type of solenoid valve;
it functions to
regulate the introduction of purge air from the
evaporative emission canister to the intake
manifold plenum.
INSPECTION
Using Scan tool
lBattery power supply is supplied, by way of the multiport
fuel injection, to the evaporative emis-
sion purge solenoid. When the engine control
module switches ON the power transistor
within the unit, current flows to the coil, and
purge air is introduced.
IFunction1 Item No. 1 Activation1 Check conditions1 Normal condition
Actuator test 08 Solenoid valve is switched from . Ignition switch: ON
Operating sound is heard
OFF to ON.when driven.
Page 242 of 1273
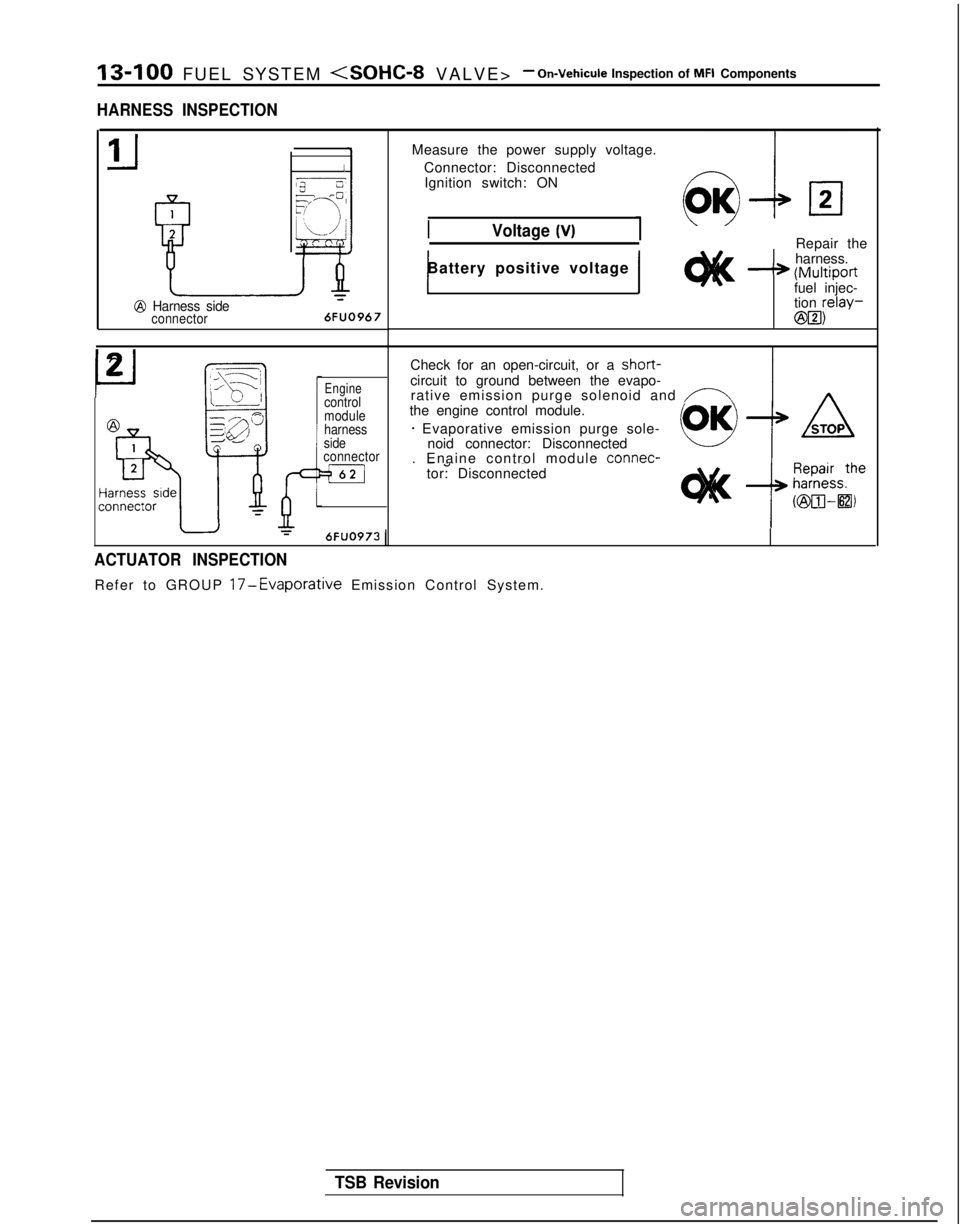
13-100 FUEL SYSTEM
- On-Vehicule Inspection of MFI Components
HARNESS INSPECTION
1
2
P
Izj----=2T !r/
‘3“L j
k&
-&@ Harness sideconnector
6FUO967
Measure
the power supply voltage.
Connector: Disconnected Ignition switch: ON
Voltage (V)Repair the
harness.
-* (Multiportfuel injec-
tion relay-
@B3)
1Battery positive voltage 1
P
2_Fq,/-\i-1- /-
F
&--
Y
Enginecontrol
module
harness
side
connector
=m
Check for an open-circuit, or a short-circuit to ground between the evapo-
rative emission purge solenoid and /-Athe engine control module.
* Evaporative emission purge sole- noid connector: Disconnected
. Enaine control module connec-
-a ~~tor: Disconnected
6FUO973
1
ACTUATOR INSPECTION
Refer to GROUP 17-Evaporative Emission Control System.
TSB Revision
Page 243 of 1273
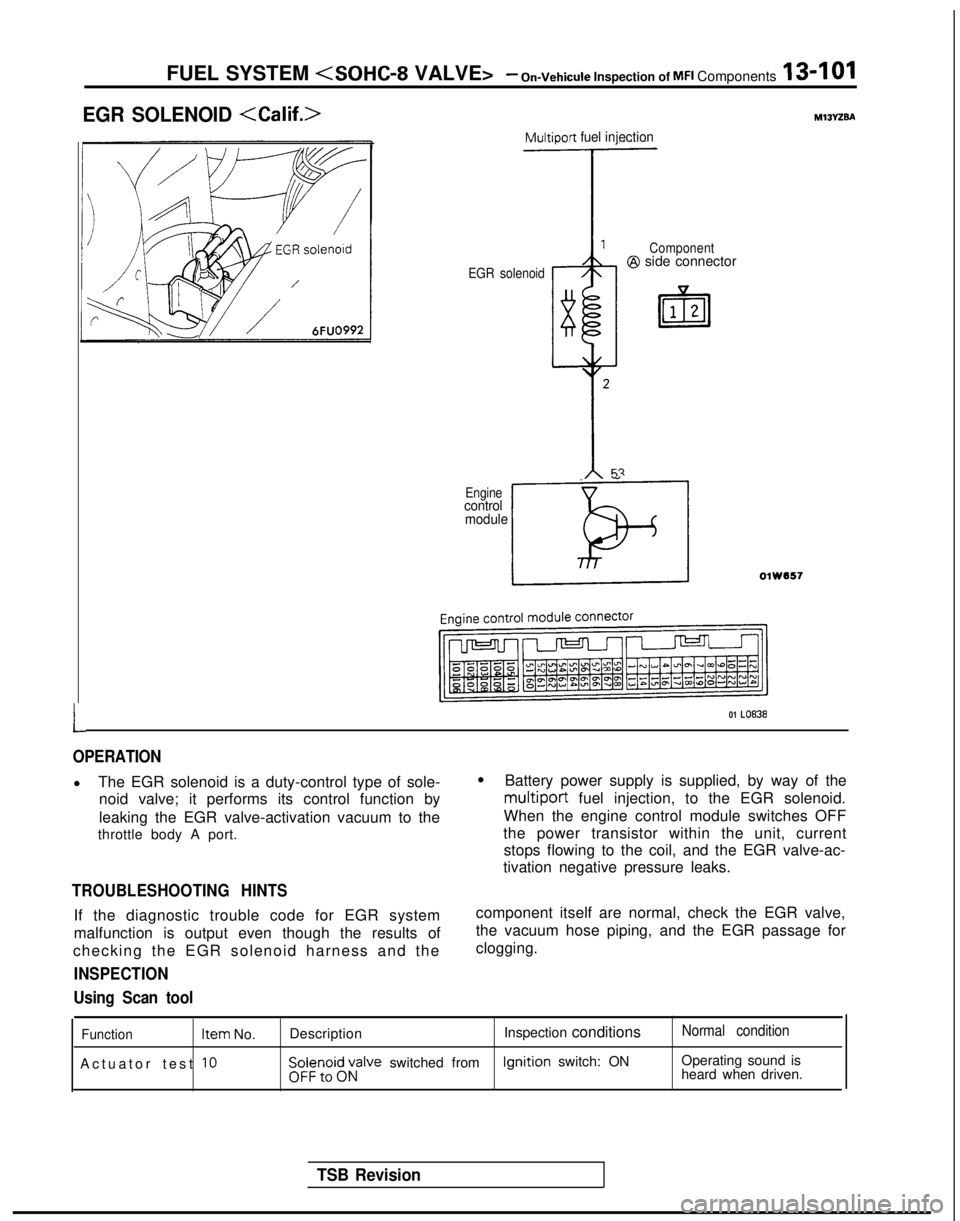
FUEL SYSTEM
EGR SOLENOID
L
Multiport fuel injection
EGR solenoid Component@I side connector
_ ”
Enginecontrol
module
LOlW557
01 LO838
OPERATION
l The EGR solenoid is a duty-control type of sole-
noid valve; it performs its control function by
leaking the EGR valve-activation vacuum to the
throttle body A port.
TROUBLESHOOTING HINTS
If the diagnostic trouble code for EGR system
malfunction is output even though the results of
checking the EGR solenoid harness and the
INSPECTION
l Battery power supply is supplied, by way of the
multiport fuel injection, to the EGR solenoid.
When the engine control module switches OFF
the power transistor within the unit, current stops flowing to the coil, and the EGR valve-ac-
tivation negative pressure leaks.
component itself are normal, check the EGR valve,
the vacuum hose piping, and the EGR passage for
clogging.
Using Scan tool
Function Item
No.
Actuator test
10
Description Inspection conditionsNormal condition
$i;;,oi$;;alve switched from Ignition
switch: ON Operating sound is
heard when driven.
TSB Revision
Page 244 of 1273
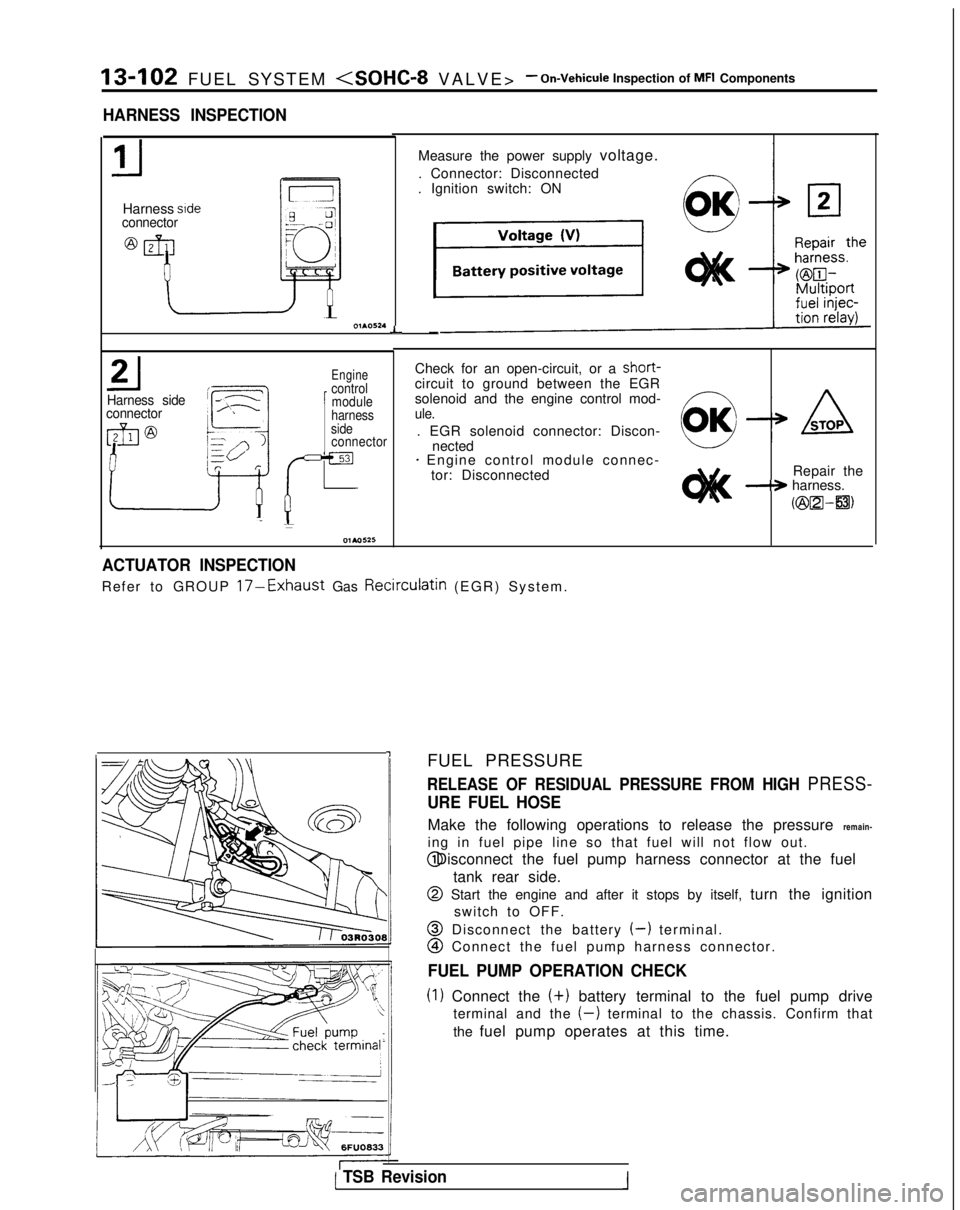
13-102 FUEL SYSTEM
- On-Vehicule Inspection of MFI Components
HARNESS INSPECTION
Harness sideconnector
L
Harness side
connector
Engine
1
control module
Check for an open-circuit, or a short-
circuit to ground between the EGR
solenoid and the engine control mod-
harnessule.side. EGR solenoid connector: Discon-connectornected+ Engine control module connec- tor: Disconnected Repair the
-+ harness.
Kzix2l-a)
-I
Measure the power supply voltage.
. Connector: Disconnected
. Ignition switch: ON
-
ACTUATOR INSPECTION
Refer to GROUP 17-Exhaust Gas Recirculatin (EGR) System
.
FUEL PRESSURE
RELEASE OF RESIDUAL PRESSURE FROM HIGH PRESS-
URE FUEL HOSE
Make the following operations to release the pressure remain-
ing in fuel pipe line so that fuel will not flow out. @ Disconnect the fuel pump harness connector at the fuel
tank rear side.
@ Start the engine and after it stops by itself, turn the ignitionswitch to OFF.
@ Disconnect the battery (-) terminal.
@I Connect the fuel pump harness connector.
FUEL PUMP OPERATION CHECK
(1) Connect the (+)
battery terminal to the fuel pump drive
terminal and the
(-) terminal to the chassis. Confirm that
the fuel pump operates at this time.
( TSB Revision1
Page 245 of 1273
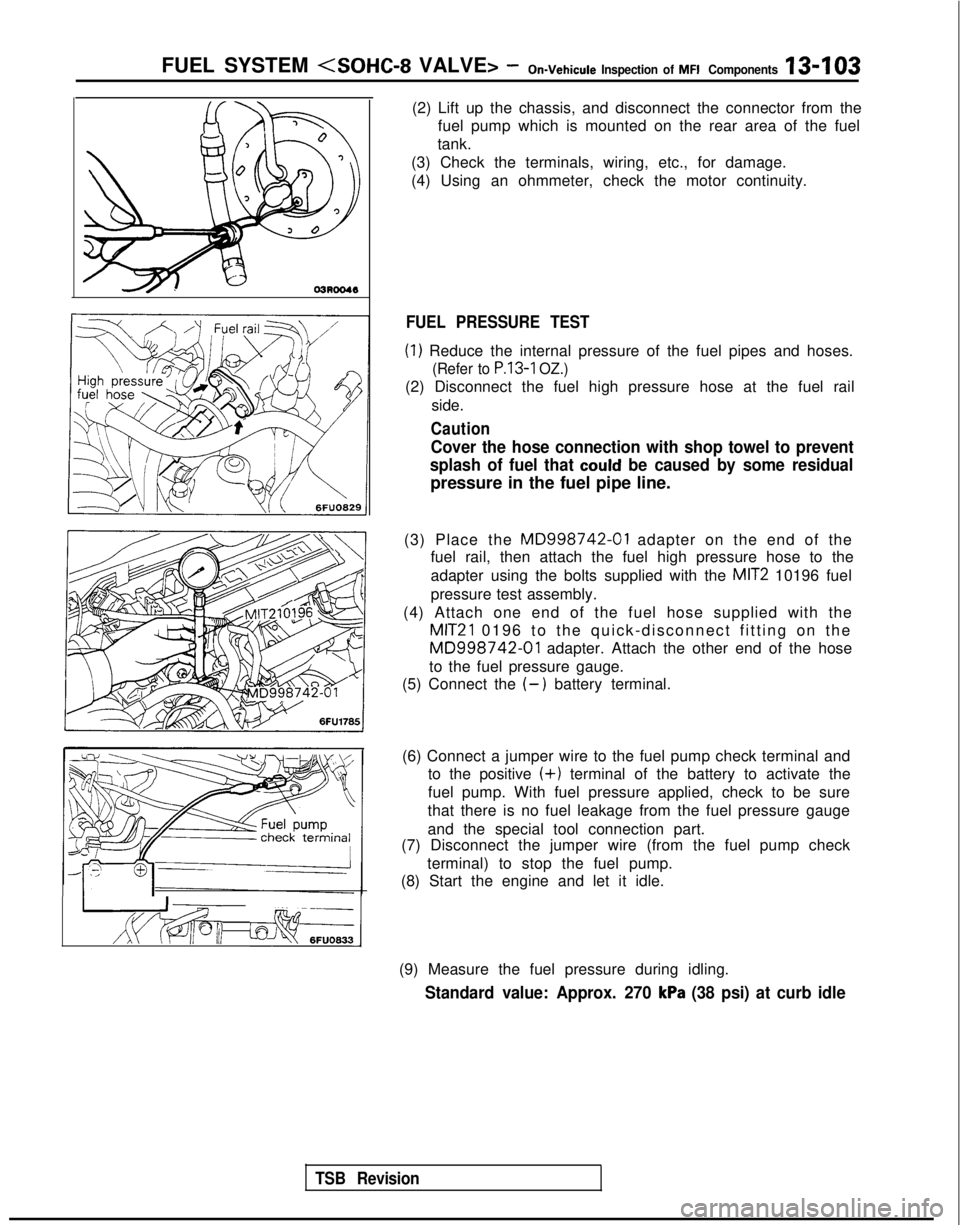
FUEL SYSTEM
TSB Revision
---
I g$qfq, tcJ-s6FUO633
(2) Lift up the chassis, and disconnect the connector from the
fuel pump which is mounted on the rear area of the fuel
tank.
(3) Check the terminals, wiring, etc., for damage.
(4) Using an ohmmeter, check the motor continuity.
FUEL PRESSURE TEST
(1) Reduce the internal pressure of the fuel pipes and hoses.
(Refer to P.13-1 OZ.)
(2) Disconnect the fuel high pressure hose at the fuel rail
side.
Caution
Cover the hose connection with shop towel to prevent
splash of fuel that
could be caused by some residual
pressure in the fuel pipe line.
(3) Place the
MD998742-01 adapter on the end of the
fuel rail, then attach the fuel high pressure hose to the
adapter using the bolts supplied with the
MIT2 10196 fuel
pressure test assembly.
(4) Attach one end of the fuel hose supplied with the
MIT21 0196 to the quick-disconnect fitting on the
MD998742-01 adapter. Attach the other end of the hose
to the fuel pressure gauge.
(5) Connect the
(-) battery terminal.
(6) Connect a jumper wire to the fuel pump check terminal and to the positive
(+) terminal of the battery to activate the
fuel pump. With fuel pressure applied, check to be sure
that there is no fuel leakage from the fuel pressure gauge
and the special tool connection part.
(7) Disconnect the jumper wire (from the fuel pump check
terminal) to stop the fuel pump.
(8) Start the engine and let it idle.
(9) Measure the fuel pressure during idling.
Standard value: Approx. 270 kPa (38 psi) at curb idle
Page 246 of 1273
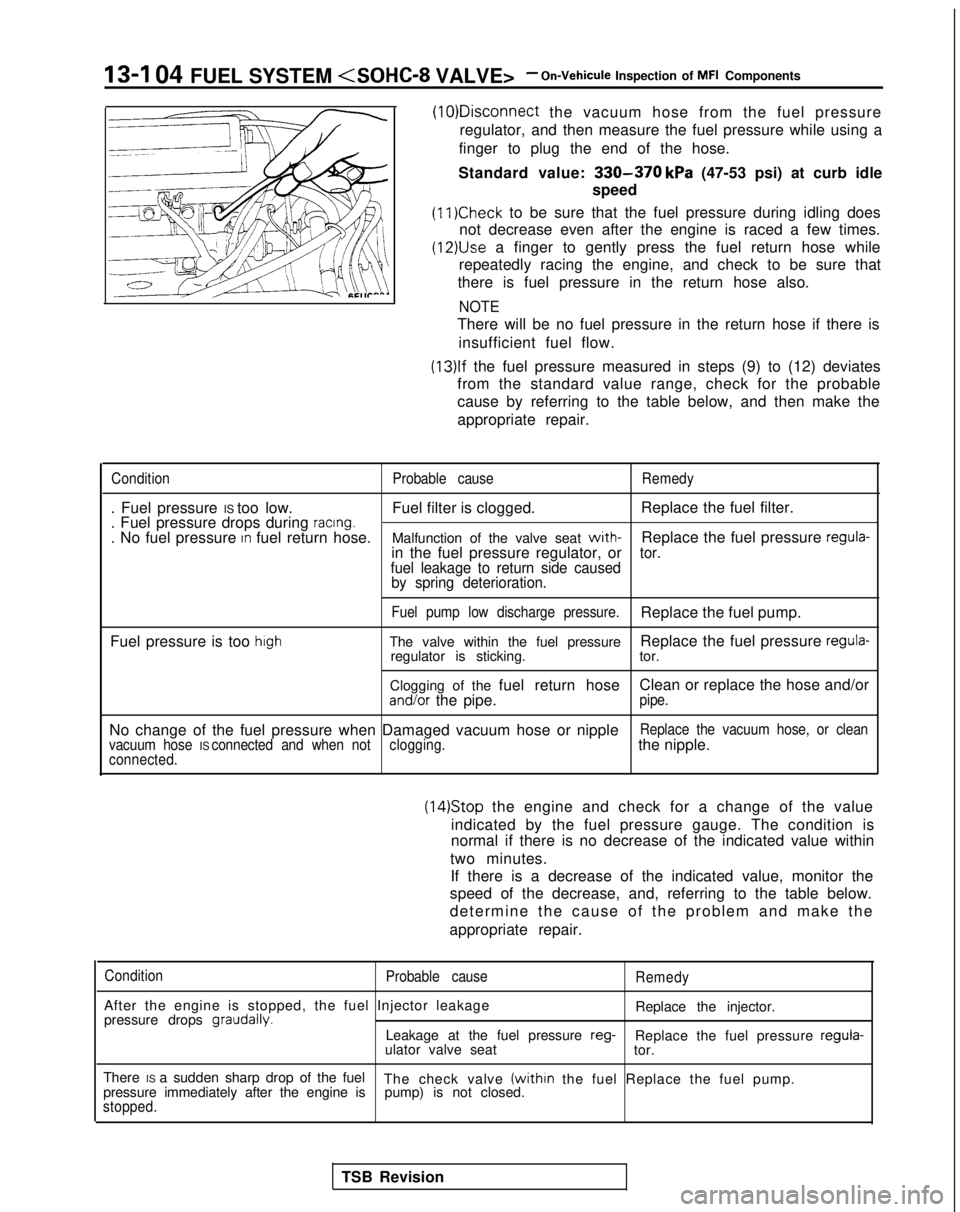
13-I 04 FUEL SYSTEM
the vacuum hose from the fuel pressure
regulator, and then measure the fuel pressure while using a
finger to plug the end of the hose.
Standard value:
330-370 kPa (47-53 psi) at curb idle
speed
(11)Check to be sure that the fuel pressure during idling does
not decrease even after the engine is raced a few times.
(12)&e a finger to gently press the fuel return hose while
repeatedly racing the engine, and check to be sure that
there is fuel pressure in the return hose also.
NOTE
There will be no fuel pressure in the return hose if there is
insufficient fuel flow.
(13)lf the fuel pressure measured in steps (9) to (12) deviates
from the standard value range, check for the probable
cause by referring to the table below, and then make the
appropriate repair.
Condition Probable causeRemedy
. Fuel pressure IS too low. Fuel filter is clogged.Replace the fuel filter.
. Fuel pressure drops during racing.. No fuel pressure In fuel return hose. Malfunction of the valve seat with-Replace the fuel pressure regula-in the fuel pressure regulator, ortor.
fuel leakage to return side caused by spring deterioration.
Fuel pump low discharge pressure.Replace the fuel pump.
Fuel pressure is too
highThe valve within the fuel pressure Replace the fuel pressure regula-regulator is sticking.
tor.
Clogging of the fuel return hose Clean or replace the hose and/or
and/or the pipe.pipe.
No change of the fuel pressure when Damaged vacuum hose or nippleReplace the vacuum hose, or clean
vacuum hose IS connected and when not clogging.the nipple.connected.
(14)Stop the engine and check for a change of the value
indicated by the fuel pressure gauge. The condition is
normal if there is no decrease of the indicated value within
two minutes. If there is a decrease of the indicated value, monitor the
speed of the decrease, and, referring to the table below.
determine the cause of the problem and make the
appropriate repair.
Condition Probable cause
After the engine is stopped, the fuel Injector leakage
pressure drops graudally.
Remedy
Replace the injector.
Leakage at the fuel pressure reg-
Replace the fuel pressure regula-
ulator valve seat tor.
There IS a sudden sharp drop of the fuel The check valve
(within the fuel Replace the fuel pump.
pressure immediately after the engine is pump) is not closed.
stopped.
TSB Revision
Page 247 of 1273
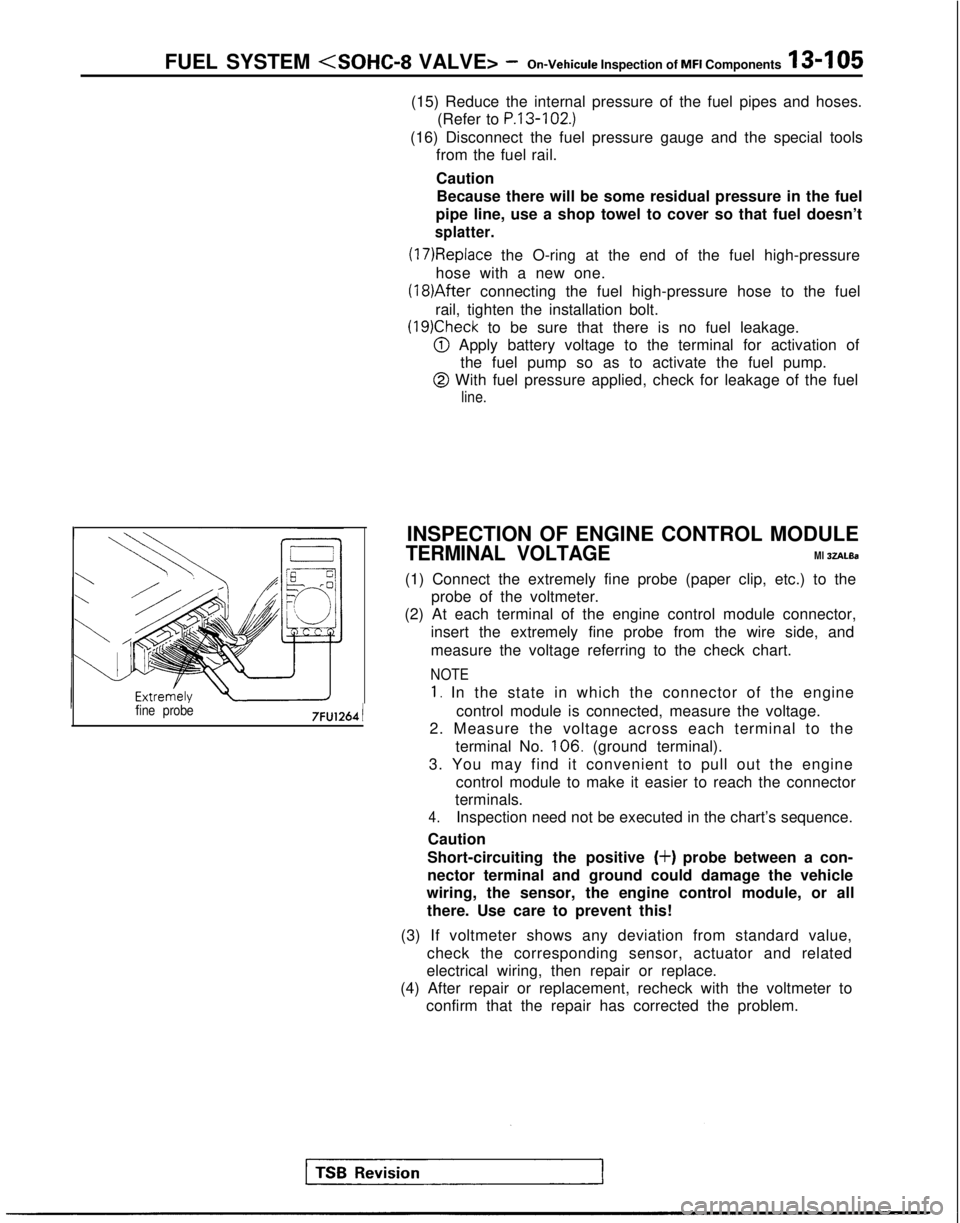
FUEL SYSTEM
fine probe7FU1264 1
(15) Reduce the internal pressure of the fuel pipes and hoses.
(Refer to
P.13-102.)
(16) Disconnect the fuel pressure gauge and the special toolsfrom the fuel rail.
Caution
Because there will be some residual pressure in the fuel
pipe line, use a shop towel to cover so that fuel doesn’t
splatter.
(17)Replace the O-ring at the end of the fuel high-pressure
hose with a new one. (18)After
connecting the fuel high-pressure hose to the fuel
rail, tighten the installation bolt.
(19)Check to be sure that there is no fuel leakage.
@ Apply battery voltage to the terminal for activation of the fuel pump so as to activate the fuel pump.
@ With fuel pressure applied, check for leakage of the fuel
line.
INSPECTION OF ENGINE CONTROL MODULE
TERMINAL VOLTAGEMl 3ZALBa
(1) Connect the extremely fine probe (paper clip, etc.) to the probe of the voltmeter.
(2) At each terminal of the engine control module connector,
insert the extremely fine probe from the wire side, and
measure the voltage referring to the check chart.
NOTE
1. In the state in which the connector of the engine
control module is connected, measure the voltage.
2. Measure the voltage across each terminal to the
terminal No. 106.
(ground terminal).
3. You may find it convenient to pull out the engine control module to make it easier to reach the connector
terminals.
4.Inspection need not be executed in the chart’s sequence.
Caution
Short-circuiting the positive
(+) probe between a con-
nector terminal and ground could damage the vehicle
wiring, the sensor, the engine control module, or all
there. Use care to prevent this!
(3) If voltmeter shows any deviation from standard value, check the corresponding sensor, actuator and related
electrical wiring, then repair or replace.
(4) After repair or replacement, recheck with the voltmeter to confirm that the repair has corrected the problem.
Page 248 of 1273
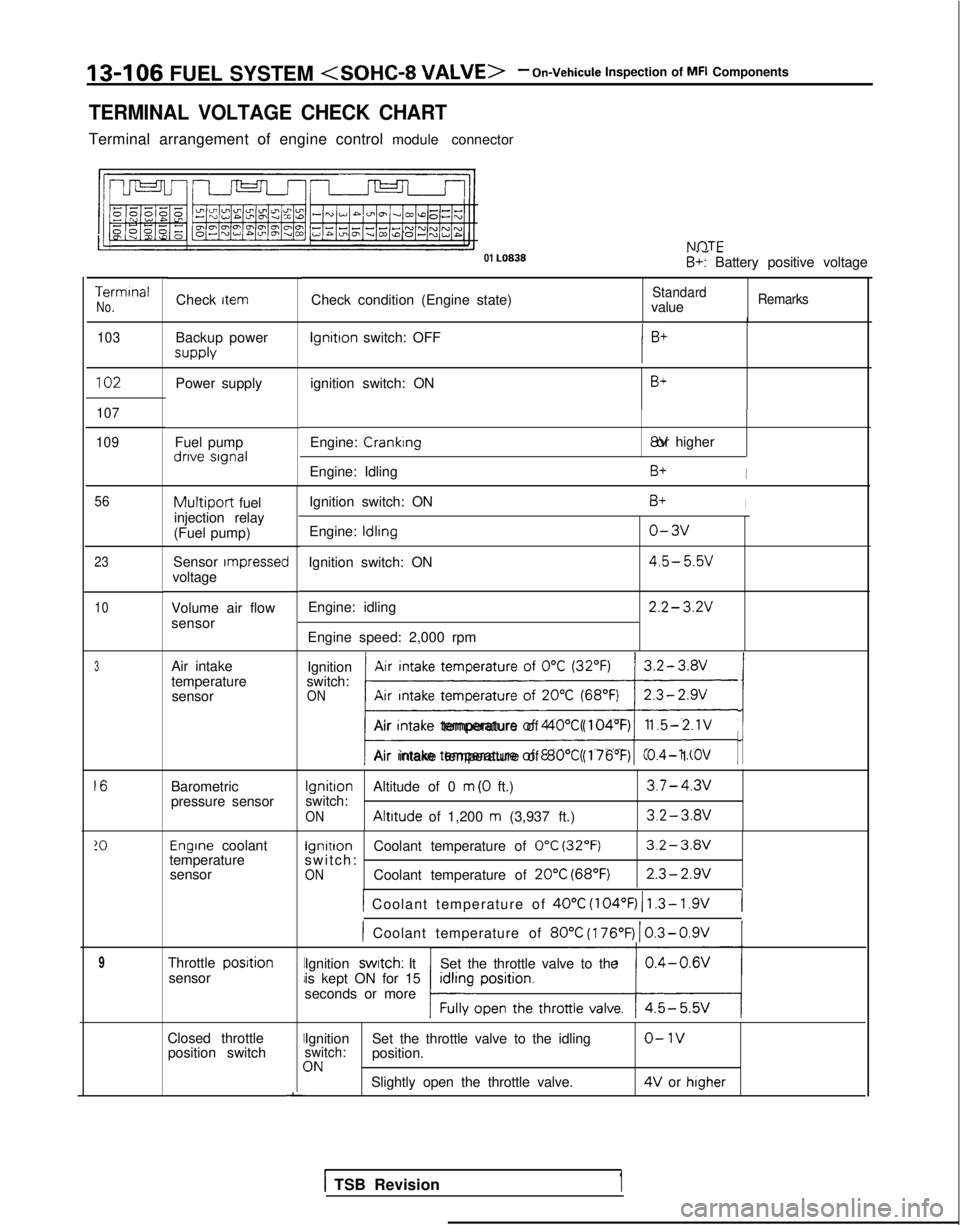
13-106
FUEL SYSTEM
TERMINAL VOLTAGE CHECK CHART
Terminal arrangement of engine control module connector NflTF
01 LO838
. .- -B+: Battery positive voltage
Terminal
No.Check condition (Engine state)StandardvalueRemarksCheck item
103
Backup power supply lgnitron
switch: OFF
102Power supply ignition switch: ONB+
107
109
Fuel pump dnve signal
Engine: Cranking 8V or higher
Engine: Idling
B+I
Ignition switch: ON
Engine:
ldlrng
Ignition switch: ON
Engine: idling
Engine speed: 2,000 rpm
B+I
o-3v
4.5- 5.5v
2.2- 3.2V
56
23
10
Multiport fuel
injection relay
(Fuel pump)
Sensor
rmpressecvoltage
Volume air flow
sensor
Air intake
temperature sensor Ignition
Air intake temperature of
0°C (32°F)switch:ONAir Intake temperature of 20°C (68°F); ji/
Air Intake temperature of 40°C (104°F)1.5-2.1V
Air intake temperature of 80°C (176’F)0.4- 1 .OV
Barometric
pressure sensor
Ignition
Altitude of 0 m (0 ft.)3.7-4.3vswitch:ON Altitude
of 1,200 m (3,937 ft.)3.2-3.av
Engrne coolant lgnitron
Coolant temperature of 0°C (32°F)3.2-3.Wtemperature switch: -sensorONCoolant temperature of 20°C (68°F)2.3-2.9v
1 Coolant temperature of 40°C
(104°F) 1 1.3- 1.9V(
) Coolant temperature of 80°C
(176’F)
1 0.3-0.9V
Throttle posrtionsensor Ignition swatch: It
Set the throttle valve to the
is kept ON for 15
seconds or more
Closed throttle position switchII
I
I
-
Ignition Set the throttle valve to the idlingo-1vswitch:position.3NSlightly open the throttle valve. 4V
or higher
3
16
!O
9
1 TSB Revision1
Page 249 of 1273
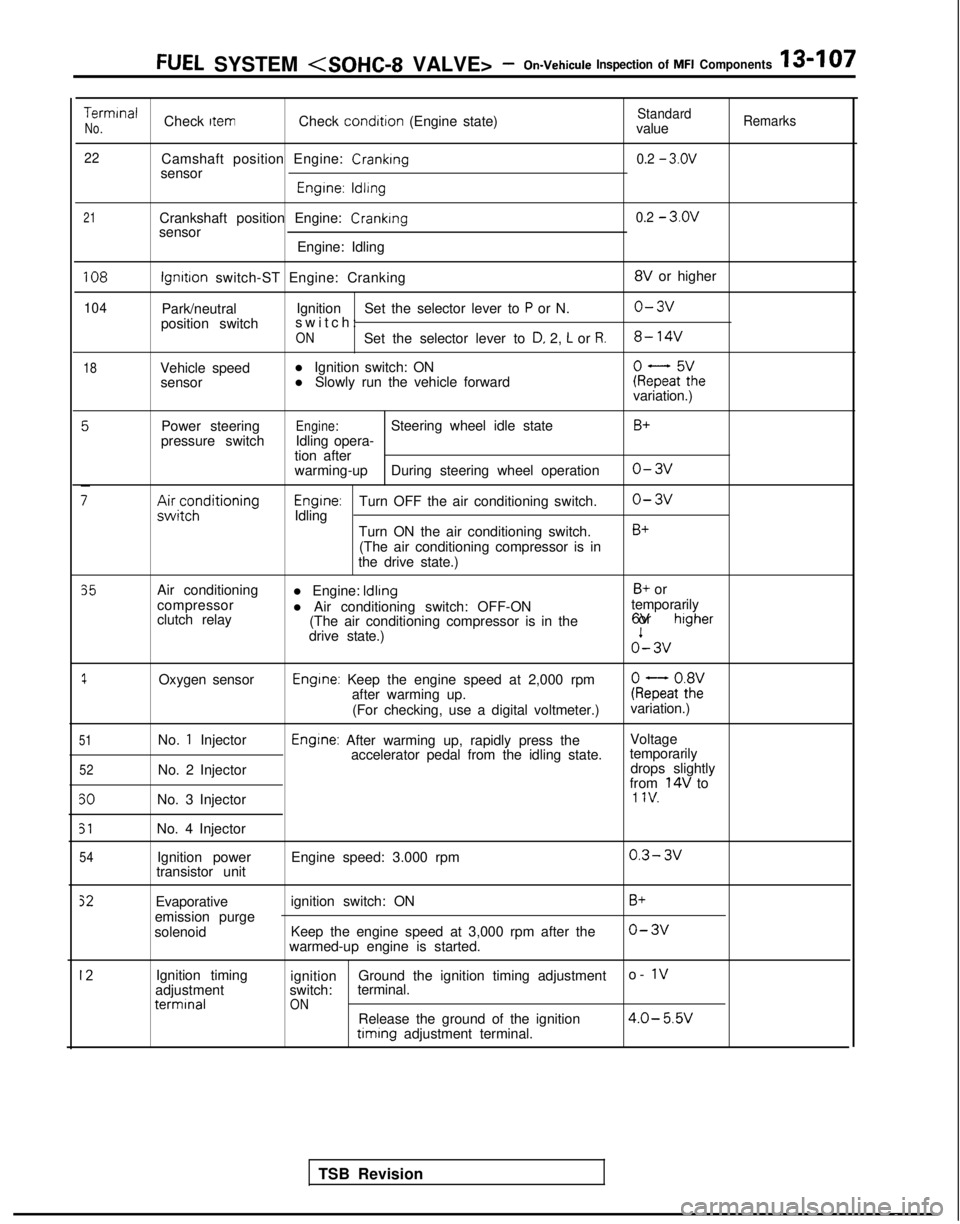
FUEL SYSTEM
TerminalCheck ItemCheck condition
(Engine state)StandardNo.valueRemarks
22
Camshaft position Engine: Cranking0.2 - 3.ov
sensor
Engrne: ldllng
21Crankshaft position Engine: Crankingsensor
Engine: Idling0.2 - 3.ov
108
104
18
lgnrtron switch-ST Engine: Cranking 8V
or higher
Park/neutral Ignition
Set the selector lever to
P or N.o-3v
position switch switch
:
ONSet the selector lever to D, 2, L or R.8- 14V
Vehicle speed
l Ignition switch: ON
sensor l Slowly run the vehicle forwardkeFaF:hevariation.)
Power steering
pressure switch
;;ir;z;ditioning
Engine:Steering wheel idle state
Idling opera-
tion after
warming-up During steering wheel operation
Engrne:Turn OFF the air conditioning switch.
Idling
Turn ON the air conditioning switch.(The air conditioning compressor is in
the drive state.)
B+
o-3v
o-3v
B+
35
1
51
52
50
51
54
Air conditioning
compressor
clutch relay
Oxygen sensor
No.
1 Injector
No. 2 Injector
No. 3 Injector
No. 4 Injector Ignition power
transistor unit l Engine: Idling
B+ or
l Air conditioning switch: OFF-ON temporarily
(The air conditioning compressor is in the 6V or
higher
drive state.)o’- 3v
Engine: Keep the engine speed at 2,000 rpm
after warming up. kQatot8h2:
(For checking, use a digital voltmeter.) variation.)
Engine: After warming up, rapidly press the
Voltage
accelerator pedal from the idling state. temporarily
drops slightly
from
14V to1 IV.
Engine speed: 3.000 rpm0.3- 3v
Evaporative
emission purge
solenoid ignition switch: ON
Keep the engine speed at 3,000 rpm after the
warmed-up engine is started.B+
o-3v
12Ignition timing
adjustment terminal
ignition
Ground the ignition timing adjustment o- 1vswitch:
terminal.ONRelease the ground of the ignition4.0- 5.W timing
adjustment terminal.
TSB Revision
Page 250 of 1273
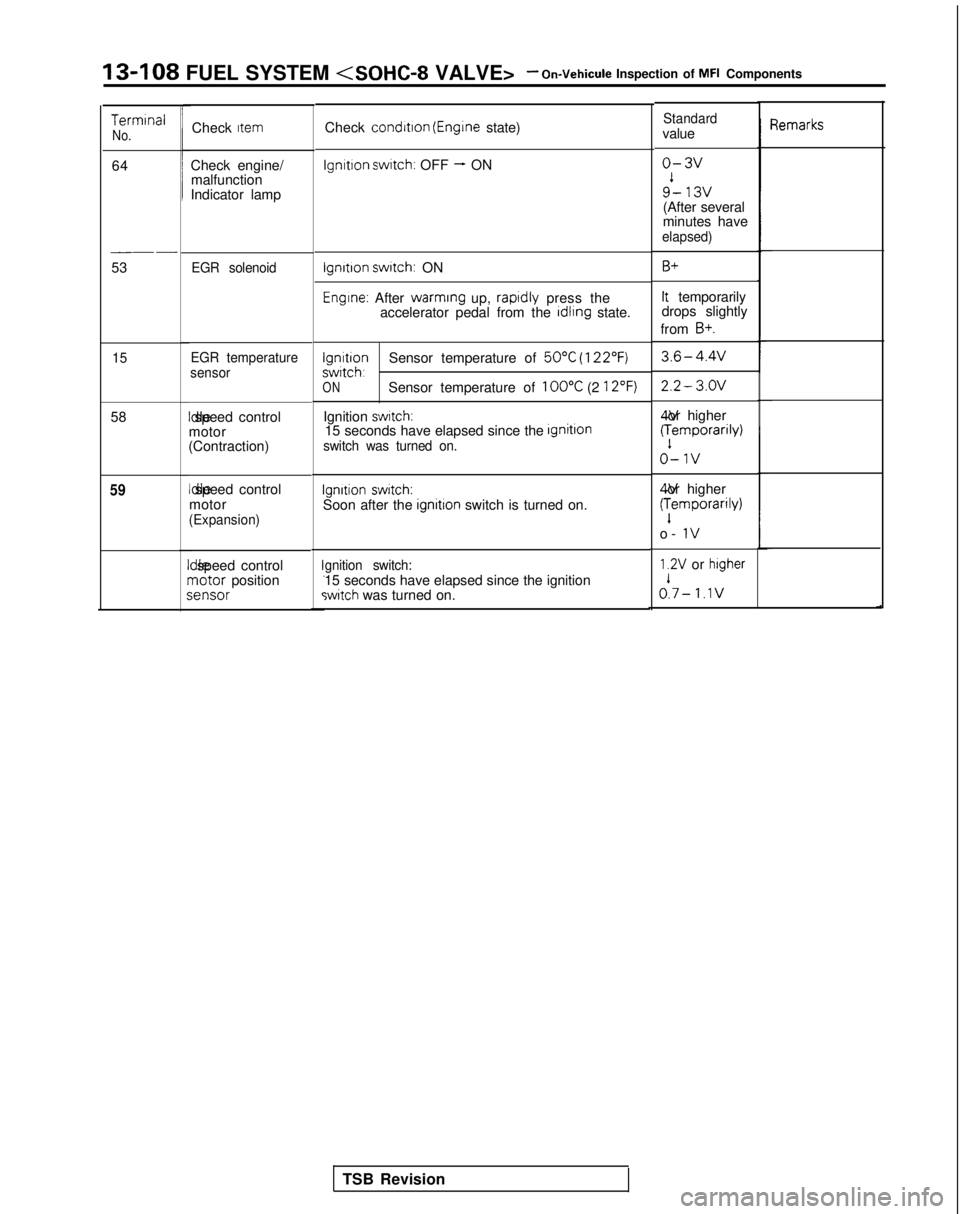
13-108 FUEL SYSTEM
TermrnalNo.
64
__-
53
15
58
59
Check Item
Check engine/
malfunction
Indicator lamp
EGR solenoid
EGR temperature
sensor Idle speed control
motor
(Contraction) Idle speed control
motor
(Expansion)
II
dle speed controlrnotor positions
;ensor
Check
condrtron (Engrne state)
lgnrtron swatch: OFF - ON
lgnrtron swatch: ON
Engine: After warming
up, raprdly press the
accelerator pedal from the rdlrng state.
lgnrtronSensor temperature of 50°C (122°F)swrtch,ONSensor temperature of 100°C (2 12°F)
Ignition swatch:15 seconds have elapsed since the IgnitlOnswitch was turned on.
Ignition switch:Soon after the ignitron switch is turned on.
gnition switch:15 seconds have elapsed since the ignitionswitch was turned on.
Standardvalue
o-3v
9’- 13v(After several
minutes have
elapsed)
B+
It temporarily
drops slightly
from
B+.
3.6-4.4v
2.2- 3.OV 4V or higher
(:emporarily)
o-1v
4V or higher
(:emporarily)
o-
IV
1.2V or higher
A- 1.1v
qemarks
TSB Revision