NISSAN PICK-UP 1998 Repair Manual
PICK-UP 1998
NISSAN
NISSAN
https://www.carmanualsonline.info/img/5/57374/w960_57374-0.png
NISSAN PICK-UP 1998 Repair Manual
Trending: wiper size, coolant reservoir, charging, tow, checking oil, injector pump, flat tire
Page 691 of 1659
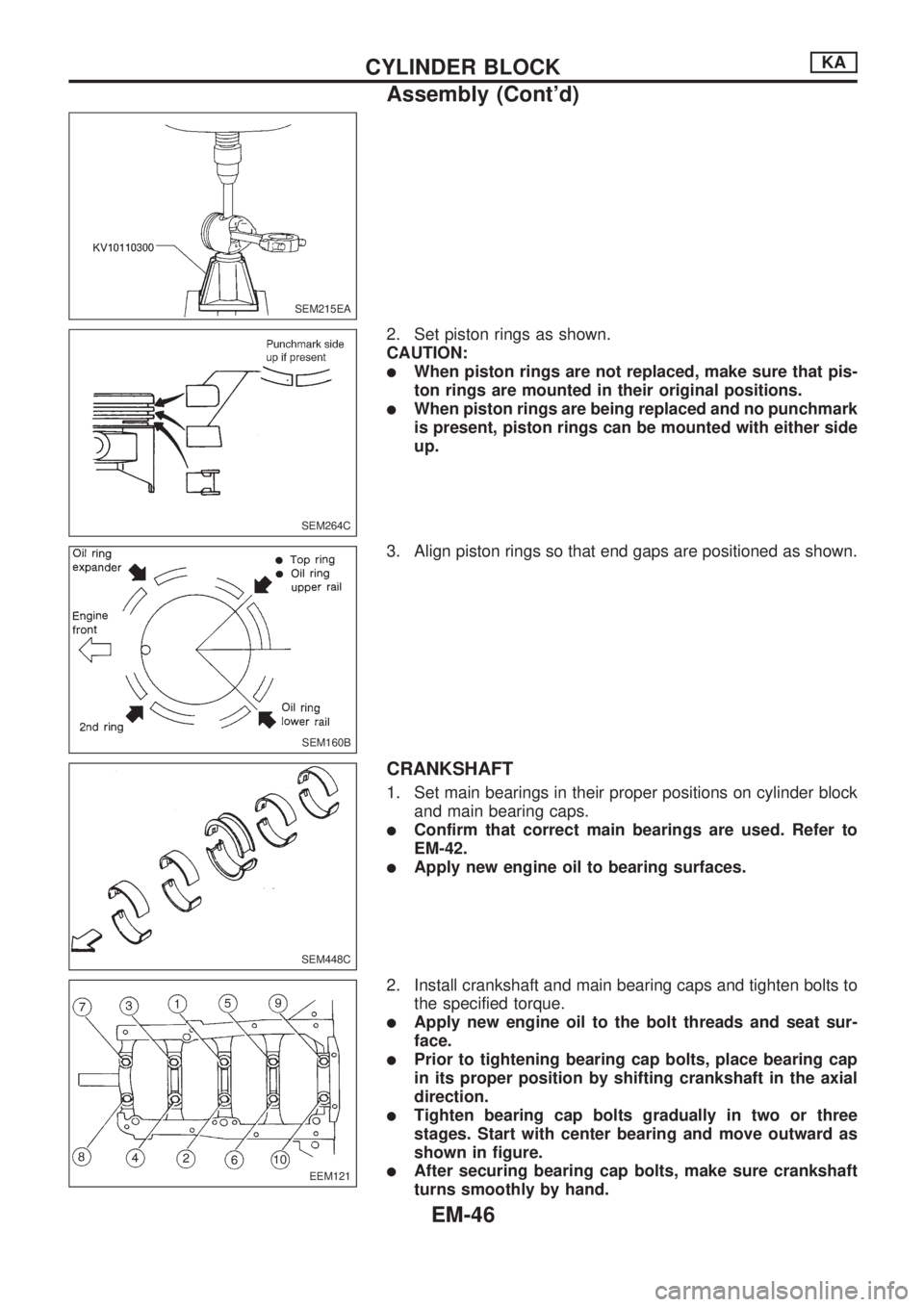
2. Set piston rings as shown.
CAUTION:
lWhen piston rings are not replaced, make sure that pis-
ton rings are mounted in their original positions.
lWhen piston rings are being replaced and no punchmark
is present, piston rings can be mounted with either side
up.
3. Align piston rings so that end gaps are positioned as shown.
CRANKSHAFT
1. Set main bearings in their proper positions on cylinder block
and main bearing caps.
lConfirm that correct main bearings are used. Refer to
EM-42.
lApply new engine oil to bearing surfaces.
2. Install crankshaft and main bearing caps and tighten bolts to
the specified torque.
lApply new engine oil to the bolt threads and seat sur-
face.
lPrior to tightening bearing cap bolts, place bearing cap
in its proper position by shifting crankshaft in the axial
direction.
lTighten bearing cap bolts gradually in two or three
stages. Start with center bearing and move outward as
shown in figure.
lAfter securing bearing cap bolts, make sure crankshaft
turns smoothly by hand.
SEM215EA
SEM264C
SEM160B
SEM448C
EEM121
CYLINDER BLOCKKA
Assembly (Cont'd)
EM-46
Page 692 of 1659
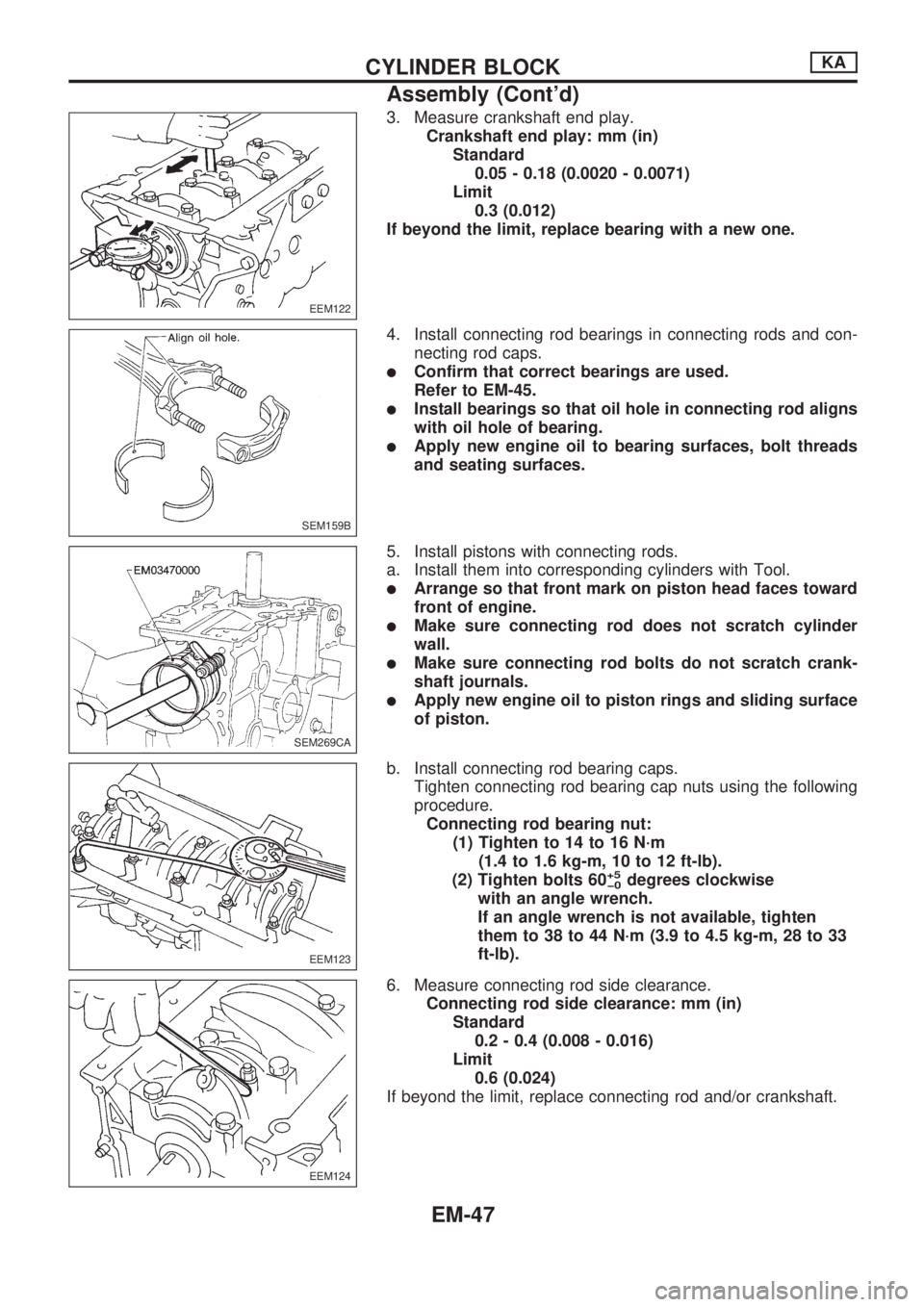
3. Measure crankshaft end play.
Crankshaft end play: mm (in)
Standard
0.05 - 0.18 (0.0020 - 0.0071)
Limit
0.3 (0.012)
If beyond the limit, replace bearing with a new one.
4. Install connecting rod bearings in connecting rods and con-
necting rod caps.
lConfirm that correct bearings are used.
Refer to EM-45.
lInstall bearings so that oil hole in connecting rod aligns
with oil hole of bearing.
lApply new engine oil to bearing surfaces, bolt threads
and seating surfaces.
5. Install pistons with connecting rods.
a. Install them into corresponding cylinders with Tool.
lArrange so that front mark on piston head faces toward
front of engine.
lMake sure connecting rod does not scratch cylinder
wall.
lMake sure connecting rod bolts do not scratch crank-
shaft journals.
lApply new engine oil to piston rings and sliding surface
of piston.
b. Install connecting rod bearing caps.
Tighten connecting rod bearing cap nuts using the following
procedure.
Connecting rod bearing nut:
(1) Tighten to 14 to 16 N´m
(1.4 to 1.6 kg-m, 10 to 12 ft-lb).
(2) Tighten bolts 60
+5
þ0degrees clockwise
with an angle wrench.
If an angle wrench is not available, tighten
them to 38 to 44 N´m (3.9 to 4.5 kg-m, 28 to 33
ft-lb).
6. Measure connecting rod side clearance.
Connecting rod side clearance: mm (in)
Standard
0.2 - 0.4 (0.008 - 0.016)
Limit
0.6 (0.024)
If beyond the limit, replace connecting rod and/or crankshaft.
EEM122
SEM159B
SEM269CA
EEM123
EEM124
CYLINDER BLOCKKA
Assembly (Cont'd)
EM-47
Page 693 of 1659
REPLACING PILOT BUSHING
1. Remove pilot bushing.
2. Install pilot bushing.
SEM916AB
SEM561E
CYLINDER BLOCKKA
Assembly (Cont'd)
EM-48
Page 694 of 1659
DEM105N
OUTER COMPONENT PARTSTD
EM-49
Page 695 of 1659
DEM106N
OUTER COMPONENT PARTSTD
EM-50
Page 696 of 1659
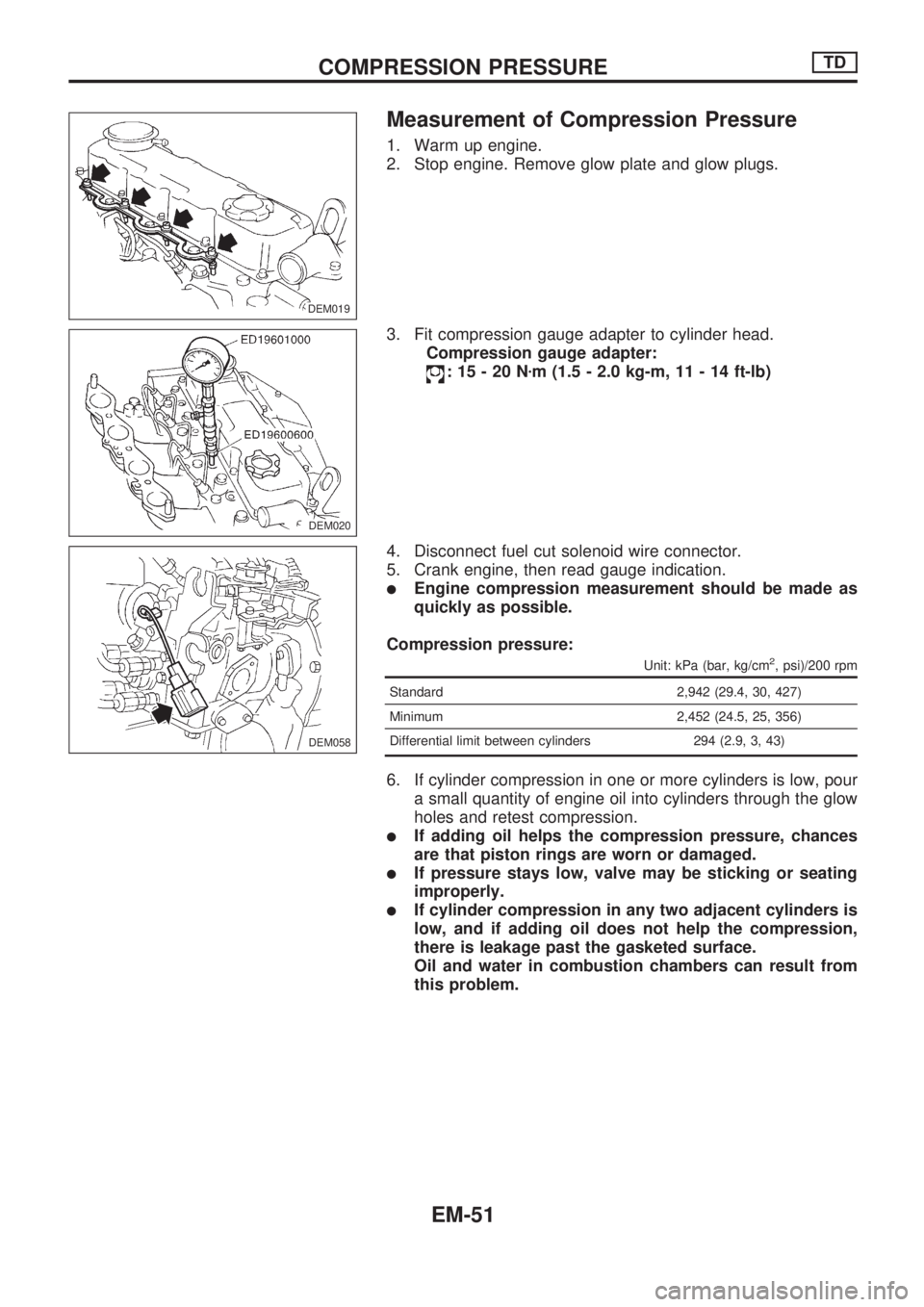
Measurement of Compression Pressure
1. Warm up engine.
2. Stop engine. Remove glow plate and glow plugs.
3. Fit compression gauge adapter to cylinder head.
Compression gauge adapter:
:15-20Nzm (1.5 - 2.0 kg-m, 11 - 14 ft-lb)
4. Disconnect fuel cut solenoid wire connector.
5. Crank engine, then read gauge indication.
lEngine compression measurement should be made as
quickly as possible.
Compression pressure:
Unit: kPa (bar, kg/cm2, psi)/200 rpm
Standard 2,942 (29.4, 30, 427)
Minimum 2,452 (24.5, 25, 356)
Differential limit between cylinders 294 (2.9, 3, 43)
6. If cylinder compression in one or more cylinders is low, pour
a small quantity of engine oil into cylinders through the glow
holes and retest compression.
lIf adding oil helps the compression pressure, chances
are that piston rings are worn or damaged.
lIf pressure stays low, valve may be sticking or seating
improperly.
lIf cylinder compression in any two adjacent cylinders is
low, and if adding oil does not help the compression,
there is leakage past the gasketed surface.
Oil and water in combustion chambers can result from
this problem.
DEM019.DEM019
DEM020
DEM058
COMPRESSION PRESSURETD
EM-51
Page 697 of 1659
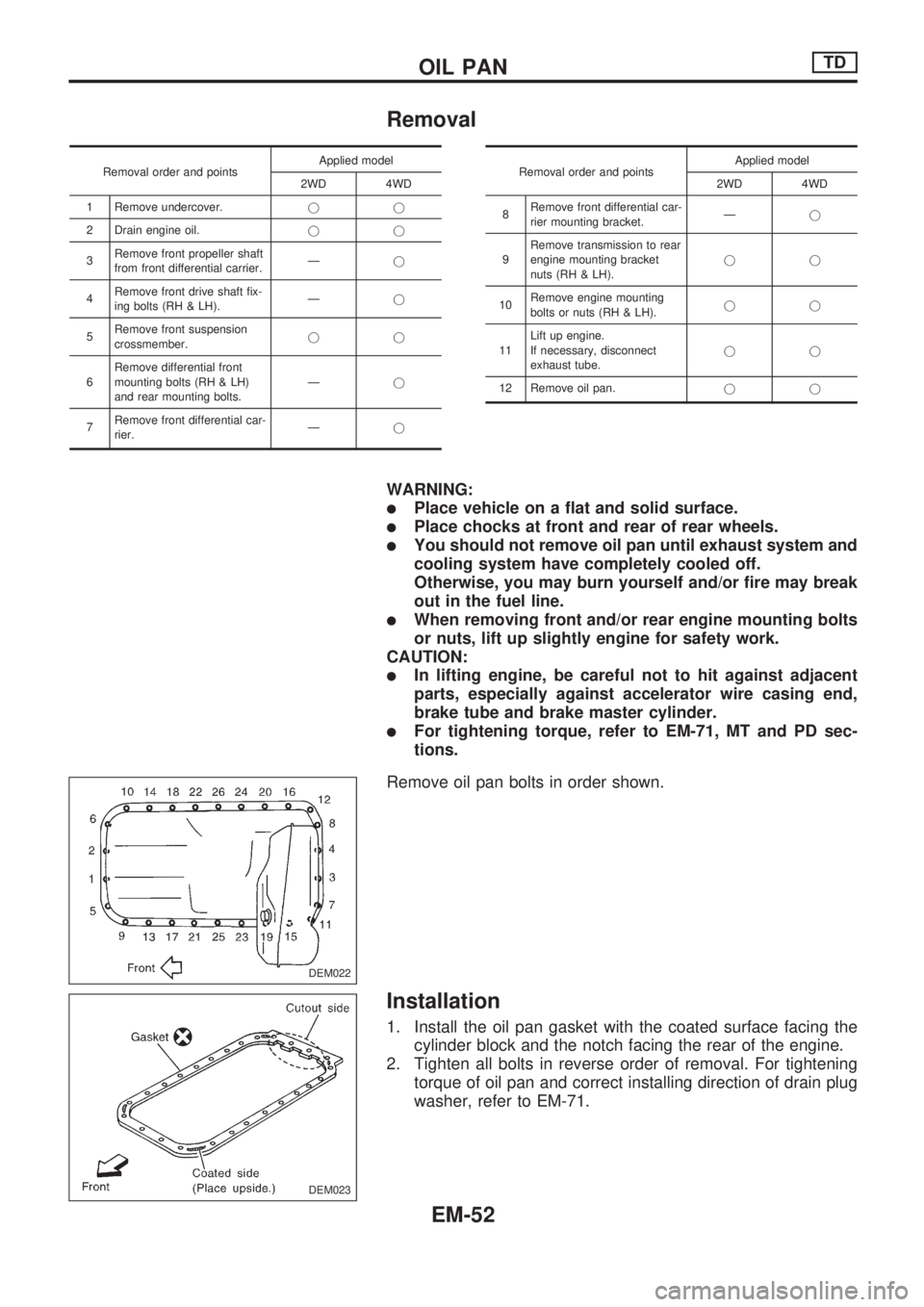
Removal
Removal order and pointsApplied model
2WD 4WD
1 Remove undercover.jj
2 Drain engine oil.jj
3Remove front propeller shaft
from front differential carrier.Ðj
4Remove front drive shaft fix-
ing bolts (RH & LH).Ðj
5Remove front suspension
crossmember.jj
6Remove differential front
mounting bolts (RH & LH)
and rear mounting bolts.Ðj
7Remove front differential car-
rier.ÐjRemoval order and pointsApplied model
2WD 4WD
8Remove front differential car-
rier mounting bracket.Ðj
9Remove transmission to rear
engine mounting bracket
nuts (RH & LH).jj
10Remove engine mounting
bolts or nuts (RH & LH).jj
11Lift up engine.
If necessary, disconnect
exhaust tube.jj
12 Remove oil pan.jj
WARNING:
lPlace vehicle on a flat and solid surface.
lPlace chocks at front and rear of rear wheels.
lYou should not remove oil pan until exhaust system and
cooling system have completely cooled off.
Otherwise, you may burn yourself and/or fire may break
out in the fuel line.
lWhen removing front and/or rear engine mounting bolts
or nuts, lift up slightly engine for safety work.
CAUTION:
lIn lifting engine, be careful not to hit against adjacent
parts, especially against accelerator wire casing end,
brake tube and brake master cylinder.
lFor tightening torque, refer to EM-71, MT and PD sec-
tions.
Remove oil pan bolts in order shown.
Installation
1. Install the oil pan gasket with the coated surface facing the
cylinder block and the notch facing the rear of the engine.
2. Tighten all bolts in reverse order of removal. For tightening
torque of oil pan and correct installing direction of drain plug
washer, refer to EM-71.
DEM022
DEM023
OIL PANTD
EM-52
Page 698 of 1659
DEM110
CYLINDER HEADTD
EM-53
Page 699 of 1659
CAUTION:
lWhen installing sliding parts such as rocker arms, cam-
shaft and oil seal, be sure to apply new engine oil on
their sliding surfaces.
lWhen tightening cylinder head bolts and rocker shaft
bolts, apply new engine oil to thread portions and seat
surfaces of bolts.
Removal
1. Set No. 1 cylinder at TDC (top dead center) on its compres-
sion stroke.
2. Drain engine coolant from drain plugs on cylinder block and
radiator.
3. Remove air cleaner and/or air duct.
4. Remove alternator adjusting bolt.
5. Disconnect exhaust manifold from front exhaust tube.
6. Disconnect radiator outlet hose and thermostat housing
water inlet hose.
7. Remove air intake housing.
8. Remove fuel injection tube assembly and spill tube.
9. Remove injection nozzle holder and top nozzle gasket using
deep socket wrench.
MEM125A
DEM024
DEM025
DEM026
CYLINDER HEADTD
EM-54
Page 700 of 1659
10. Remove rocker cover.
11. Remove rocker shaft with rocker arms.
12. Remove push rods.
13. Remove cylinder head bolts in numerical order and remove
cylinder head.
Head warpage or cracking could result from removing in
incorrect order.
Disassembly
1. Remove following parts:
a. Intake manifold
b. Exhaust manifold
c. Thermostat housing
d. Alternator adjusting bar & engine slinger
e. Glow plate and glow plugs
2. Remove valve component parts with Tool.
SEM607F
DEM028
SEM623B
SEM624B
DEM029-A
CYLINDER HEADTD
Removal (Cont'd)
EM-55
Trending: spark plugs, set clock, change wheel, hood release, maintenance schedule, door lock, jack points