NISSAN X-TRAIL 2003 Electronic Repair Manual
Manufacturer: NISSAN, Model Year: 2003, Model line: X-TRAIL, Model: NISSAN X-TRAIL 2003Pages: 3066, PDF Size: 51.47 MB
Page 2991 of 3066
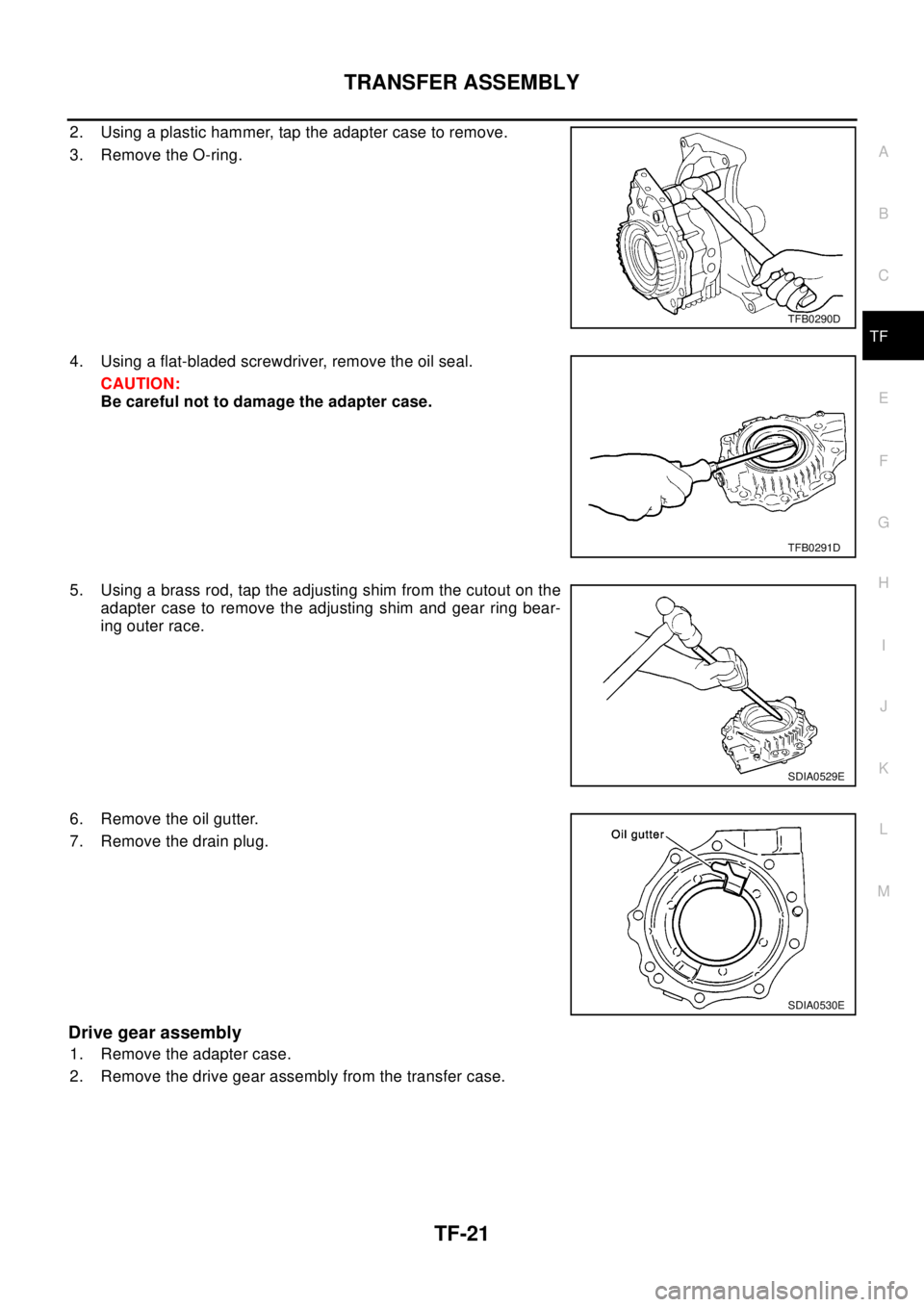
TRANSFER ASSEMBLY
TF-21
C
E
F
G
H
I
J
K
L
MA
B
TF
2. Using a plastic hammer, tap the adapter case to remove.
3. Remove the O-ring.
4. Using a flat-bladed screwdriver, remove the oil seal.
CAUTION:
Be careful not to damage the adapter case.
5. Using a brass rod, tap the adjusting shim from the cutout on the
adapter case to remove the adjusting shim and gear ring bear-
ing outer race.
6. Remove the oil gutter.
7. Remove the drain plug.
Drive gear assembly
1. Remove the adapter case.
2. Remove the drive gear assembly from the transfer case.
TFB0290D
TFB0291D
SDIA0529E
SDIA0530E
Page 2992 of 3066
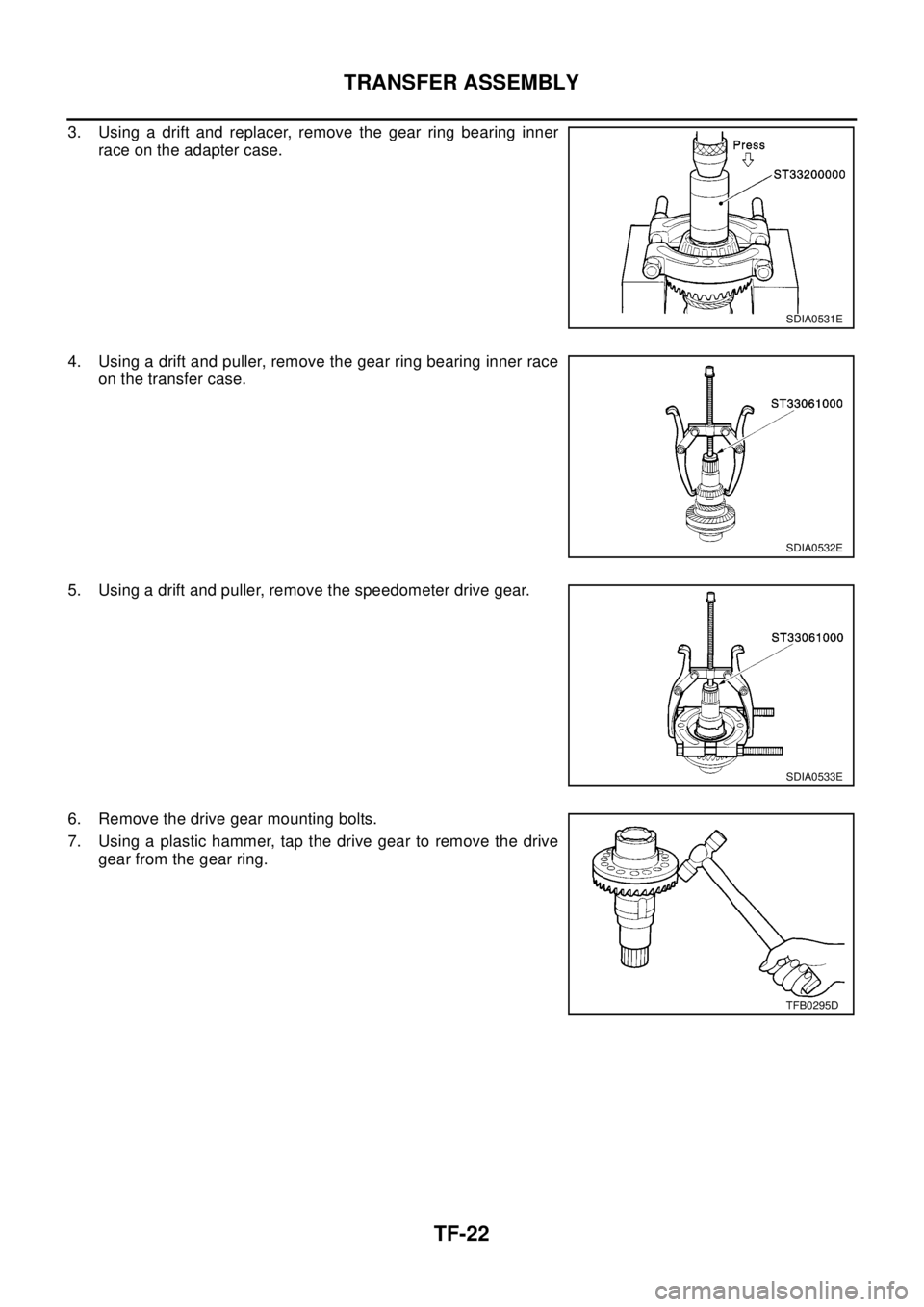
TF-22
TRANSFER ASSEMBLY
3. Using a drift and replacer, remove the gear ring bearing inner
race on the adapter case.
4. Using a drift and puller, remove the gear ring bearing inner race
on the transfer case.
5. Using a drift and puller, remove the speedometer drive gear.
6. Remove the drive gear mounting bolts.
7. Using a plastic hammer, tap the drive gear to remove the drive
gear from the gear ring.
SDIA0531E
SDIA0532E
SDIA0533E
TFB0295D
Page 2993 of 3066
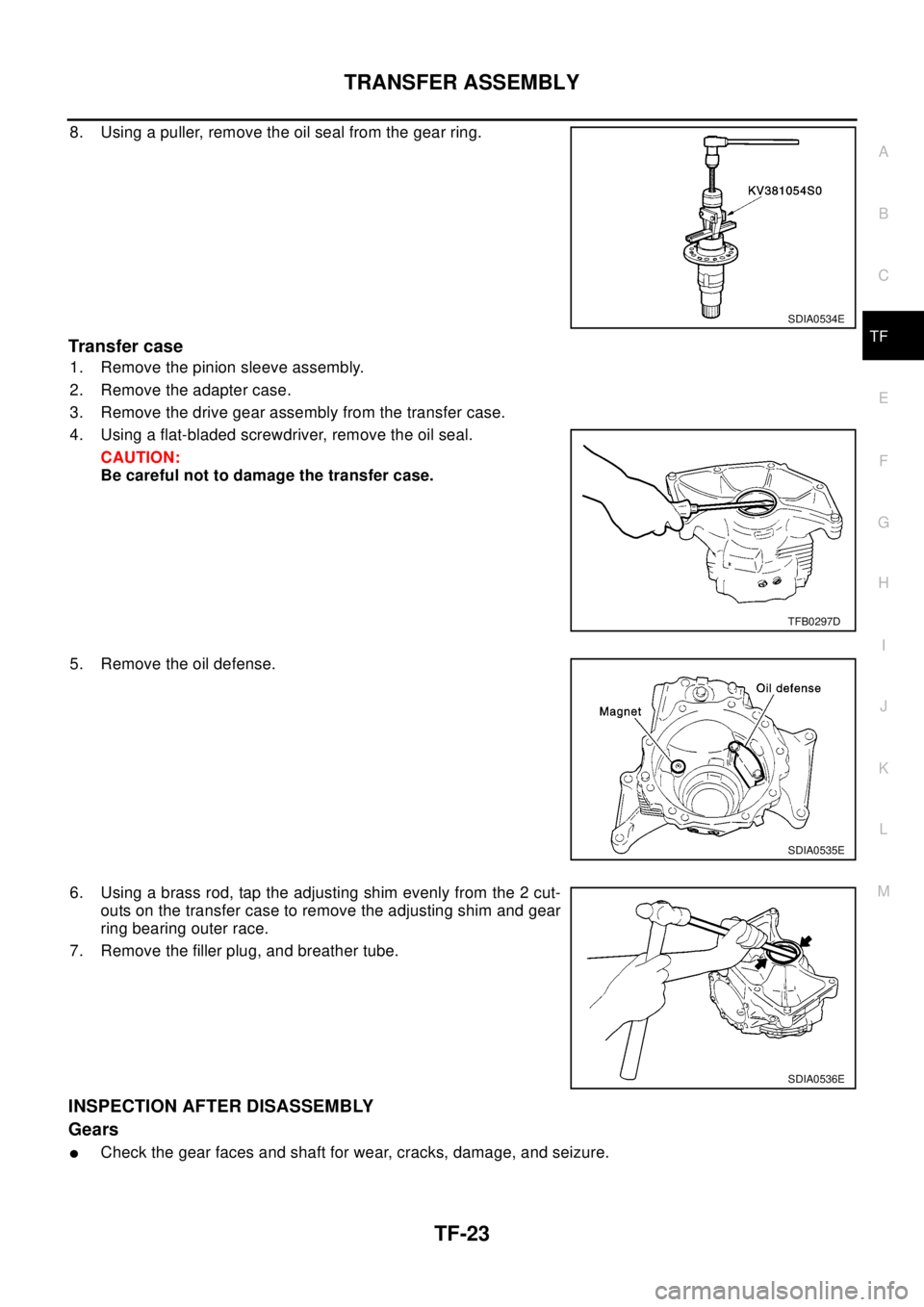
TRANSFER ASSEMBLY
TF-23
C
E
F
G
H
I
J
K
L
MA
B
TF
8. Using a puller, remove the oil seal from the gear ring.
Transfer case
1. Remove the pinion sleeve assembly.
2. Remove the adapter case.
3. Remove the drive gear assembly from the transfer case.
4. Using a flat-bladed screwdriver, remove the oil seal.
CAUTION:
Be careful not to damage the transfer case.
5. Remove the oil defense.
6. Using a brass rod, tap the adjusting shim evenly from the 2 cut-
outs on the transfer case to remove the adjusting shim and gear
ring bearing outer race.
7. Remove the filler plug, and breather tube.
INSPECTION AFTER DISASSEMBLY
Gears
lCheck the gear faces and shaft for wear, cracks, damage, and seizure.
SDIA0534E
TFB0297D
SDIA0535E
SDIA0536E
Page 2994 of 3066
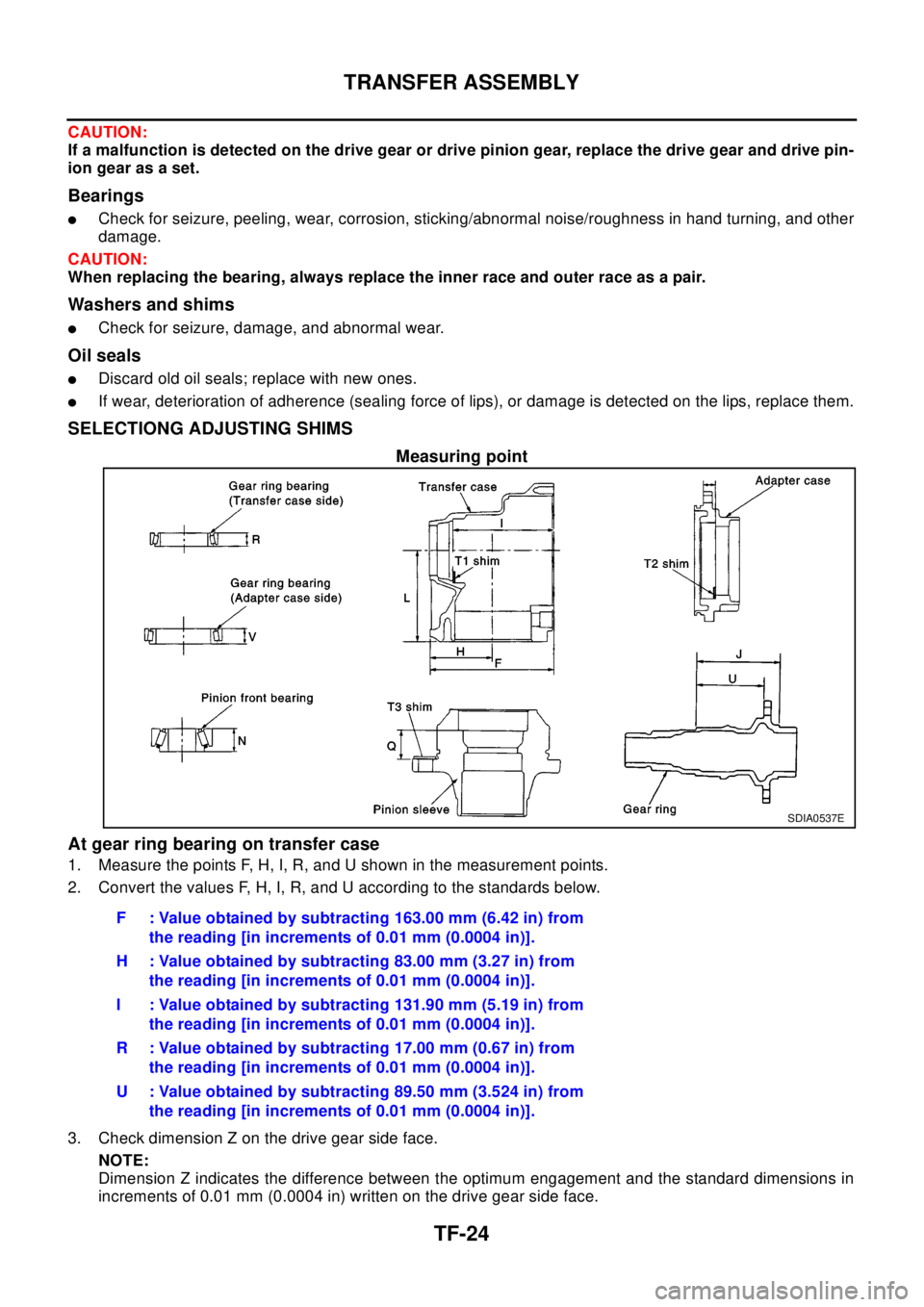
TF-24
TRANSFER ASSEMBLY
CAUTION:
If a malfunction is detected on the drive gear or drive pinion gear, replace the drive gear and drive pin-
ion gear as a set.
Bearings
lCheck for seizure, peeling, wear, corrosion, sticking/abnormal noise/roughness in hand turning, and other
damage.
CAUTION:
When replacing the bearing, always replace the inner race and outer race as a pair.
Washers and shims
lCheck for seizure, damage, and abnormal wear.
Oil seals
lDiscard old oil seals; replace with new ones.
lIf wear, deterioration of adherence (sealing force of lips), or damage is detected on the lips, replace them.
SELECTIONG ADJUSTING SHIMS
Measuring point
At gear ring bearing on transfer case
1. Measure the points F, H, I, R, and U shown in the measurement points.
2. Convert the values F, H, I, R, and U according to the standards below.
3. Check dimension Z on the drive gear side face.
NOTE:
Dimension Z indicates the difference between the optimum engagement and the standard dimensions in
increments of 0.01 mm (0.0004 in) written on the drive gear side face.
SDIA0537E
F : Value obtained by subtracting 163.00 mm (6.42 in) from
the reading [in increments of 0.01 mm (0.0004 in)].
H : Value obtained by subtracting 83.00 mm (3.27 in) from
the reading [in increments of 0.01 mm (0.0004 in)].
I : Value obtained by subtracting 131.90 mm (5.19 in) from
the reading [in increments of 0.01 mm (0.0004 in)].
R : Value obtained by subtracting 17.00 mm (0.67 in) from
the reading [in increments of 0.01 mm (0.0004 in)].
U : Value obtained by subtracting 89.50 mm (3.524 in) from
the reading [in increments of 0.01 mm (0.0004 in)].
Page 2995 of 3066
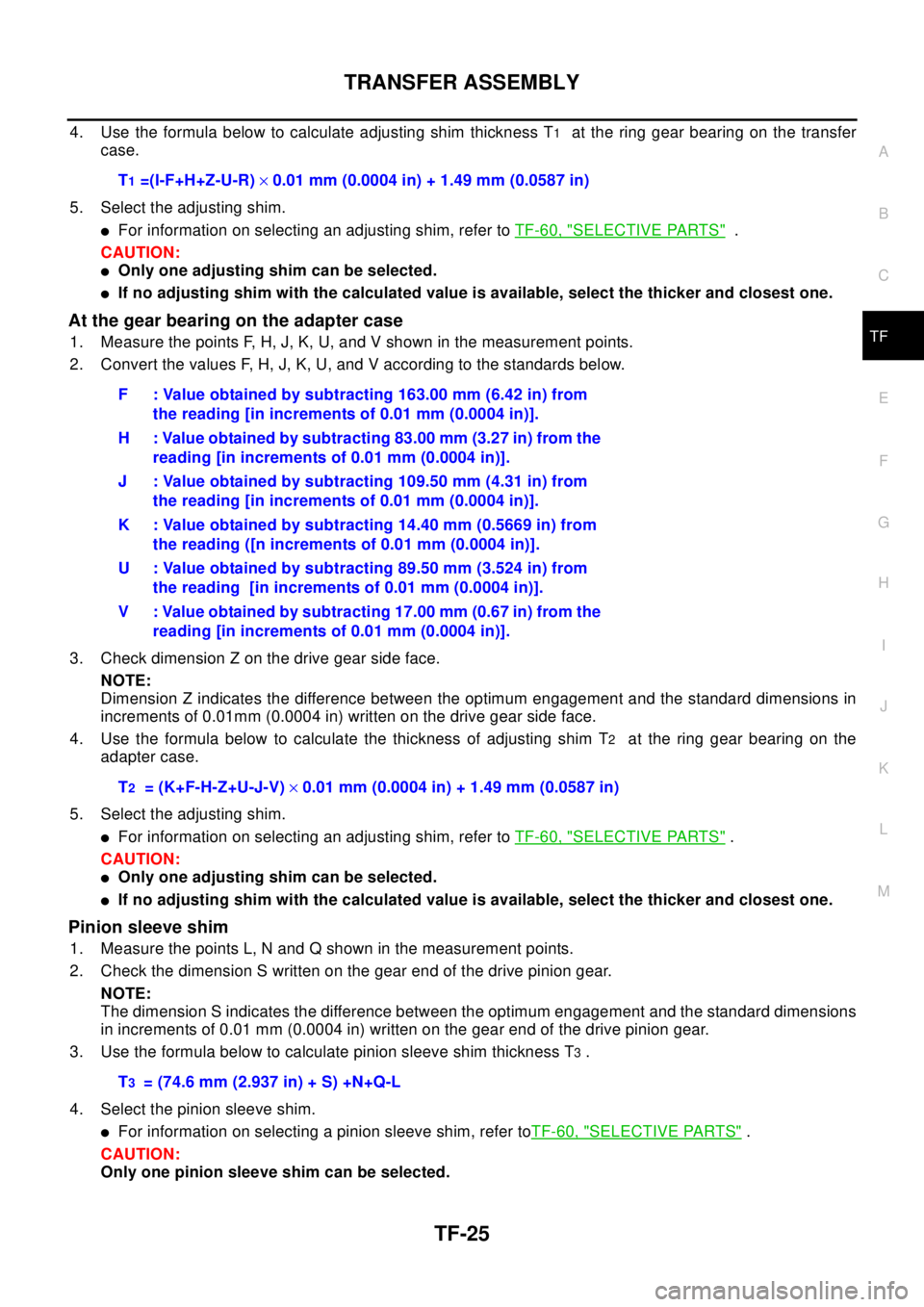
TRANSFER ASSEMBLY
TF-25
C
E
F
G
H
I
J
K
L
MA
B
TF
4. Use the formula below to calculate adjusting shim thickness T1at the ring gear bearing on the transfer
case.
5. Select the adjusting shim.
lFor information on selecting an adjusting shim, refer toTF-60, "SELECTIVE PARTS".
CAUTION:
lOnly one adjusting shim can be selected.
lIf no adjusting shim with the calculated value is available, select the thicker and closest one.
At the gear bearing on the adapter case
1. Measure the points F, H, J, K, U, and V shown in the measurement points.
2. Convert the values F, H, J, K, U, and V according to the standards below.
3. Check dimension Z on the drive gear side face.
NOTE:
Dimension Z indicates the difference between the optimum engagement and the standard dimensions in
increments of 0.01mm (0.0004 in) written on the drive gear side face.
4. Use the formula below to calculate the thickness of adjusting shim T
2attheringgearbearingonthe
adapter case.
5. Select the adjusting shim.
lFor information on selecting an adjusting shim, refer toTF-60, "SELECTIVE PARTS".
CAUTION:
lOnly one adjusting shim can be selected.
lIf no adjusting shim with the calculated value is available, select the thicker and closest one.
Pinion sleeve shim
1. Measure the points L, N and Q shown in the measurement points.
2. Check the dimension S written on the gear end of the drive pinion gear.
NOTE:
The dimension S indicates the difference between the optimum engagement and the standard dimensions
in increments of 0.01 mm (0.0004 in) written on the gear end of the drive pinion gear.
3. Use the formula below to calculate pinion sleeve shim thickness T
3.
4. Select the pinion sleeve shim.
lFor information on selecting a pinion sleeve shim, refer toTF-60, "SELECTIVE PARTS".
CAUTION:
Only one pinion sleeve shim can be selected.T
1=(I-F+H+Z-U-R)´0.01 mm (0.0004 in) + 1.49 mm (0.0587 in)
F : Value obtained by subtracting 163.00 mm (6.42 in) from
the reading [in increments of 0.01 mm (0.0004 in)].
H : Value obtained by subtracting 83.00 mm (3.27 in) from the
reading [in increments of 0.01 mm (0.0004 in)].
J : Value obtained by subtracting 109.50 mm (4.31 in) from
the reading [in increments of 0.01 mm (0.0004 in)].
K : Value obtained by subtracting 14.40 mm (0.5669 in) from
the reading ([n increments of 0.01 mm (0.0004 in)].
U : Value obtained by subtracting 89.50 mm (3.524 in) from
the reading [in increments of 0.01 mm (0.0004 in)].
V : Value obtained by subtracting 17.00 mm (0.67 in) from the
reading [in increments of 0.01 mm (0.0004 in)].
T
2= (K+F-H-Z+U-J-V)´0.01 mm (0.0004 in) + 1.49 mm (0.0587 in)
T
3= (74.6 mm (2.937 in) + S) +N+Q-L
Page 2996 of 3066
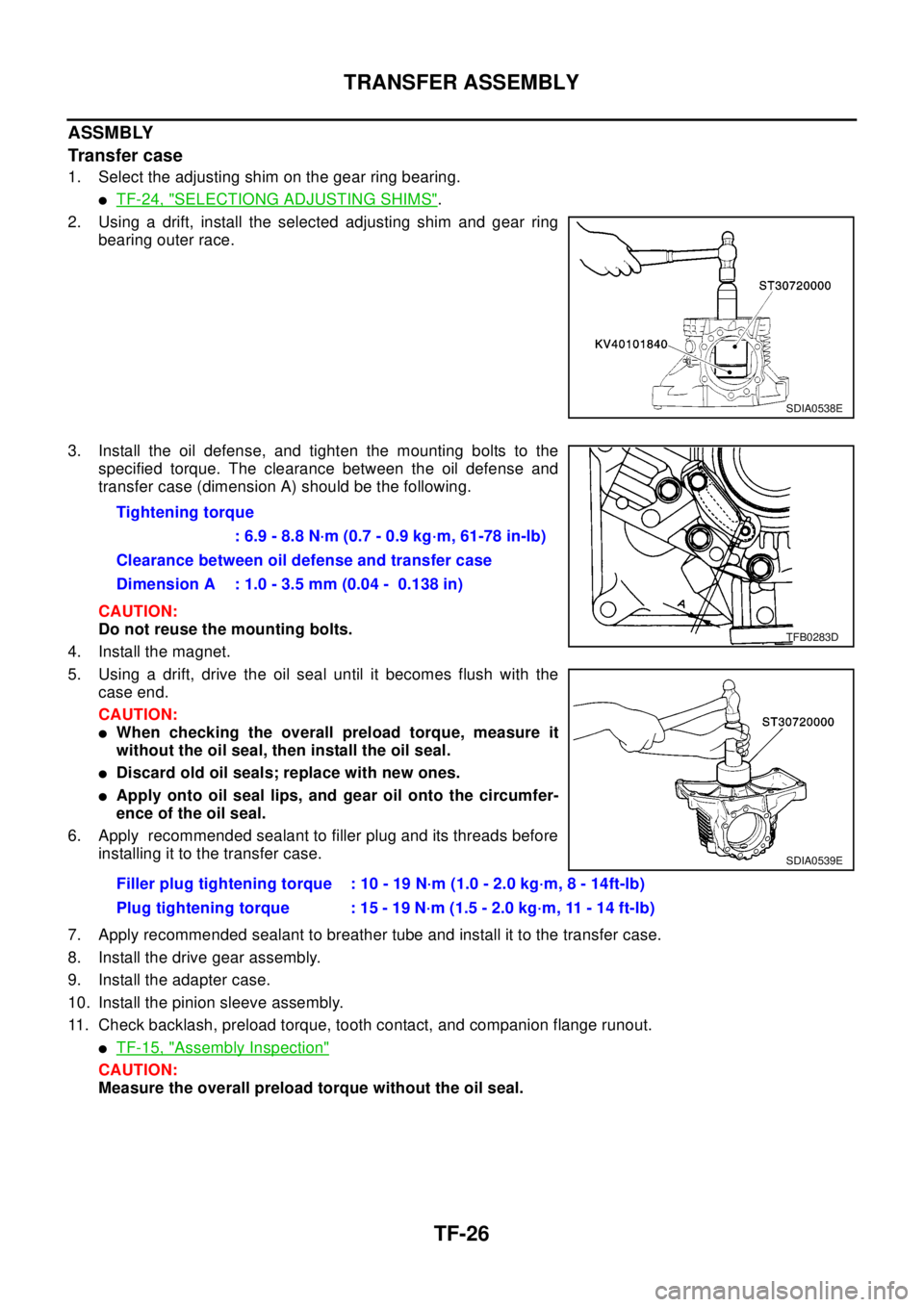
TF-26
TRANSFER ASSEMBLY
ASSMBLY
Transfer case
1. Select the adjusting shim on the gear ring bearing.
lTF-24, "SELECTIONG ADJUSTING SHIMS".
2. Using a drift, install the selected adjusting shim and gear ring
bearing outer race.
3. Install the oil defense, and tighten the mounting bolts to the
specified torque. The clearance between the oil defense and
transfer case (dimension A) should be the following.
CAUTION:
Do not reuse the mounting bolts.
4. Install the magnet.
5. Using a drift, drive the oil seal until it becomes flush with the
case end.
CAUTION:
lWhen checking the overall preload torque, measure it
without the oil seal, then install the oil seal.
lDiscard old oil seals; replace with new ones.
lApply onto oil seal lips, and gear oil onto the circumfer-
ence of the oil seal.
6. Apply recommended sealant to filler plug and its threads before
installing it to the transfer case.
7. Apply recommended sealant to breather tube and install it to the transfer case.
8. Install the drive gear assembly.
9. Install the adapter case.
10. Install the pinion sleeve assembly.
11. Check backlash, preload torque, tooth contact, and companion flange runout.
lTF-15, "Assembly Inspection"
CAUTION:
Measure the overall preload torque without the oil seal.
SDIA0538E
Tightening torque
: 6.9 - 8.8 N·m (0.7 - 0.9 kg·m, 61-78 in-lb)
Clearance between oil defense and transfer case
Dimension A : 1.0 - 3.5 mm (0.04 - 0.138 in)
Filler plug tightening torque : 10 - 19 N·m (1.0 - 2.0 kg·m, 8 - 14ft-lb)
Plug tightening torque : 15 - 19 N·m (1.5 - 2.0 kg·m, 11 - 14 ft-lb)
TFB0283D
SDIA0539E
Page 2997 of 3066
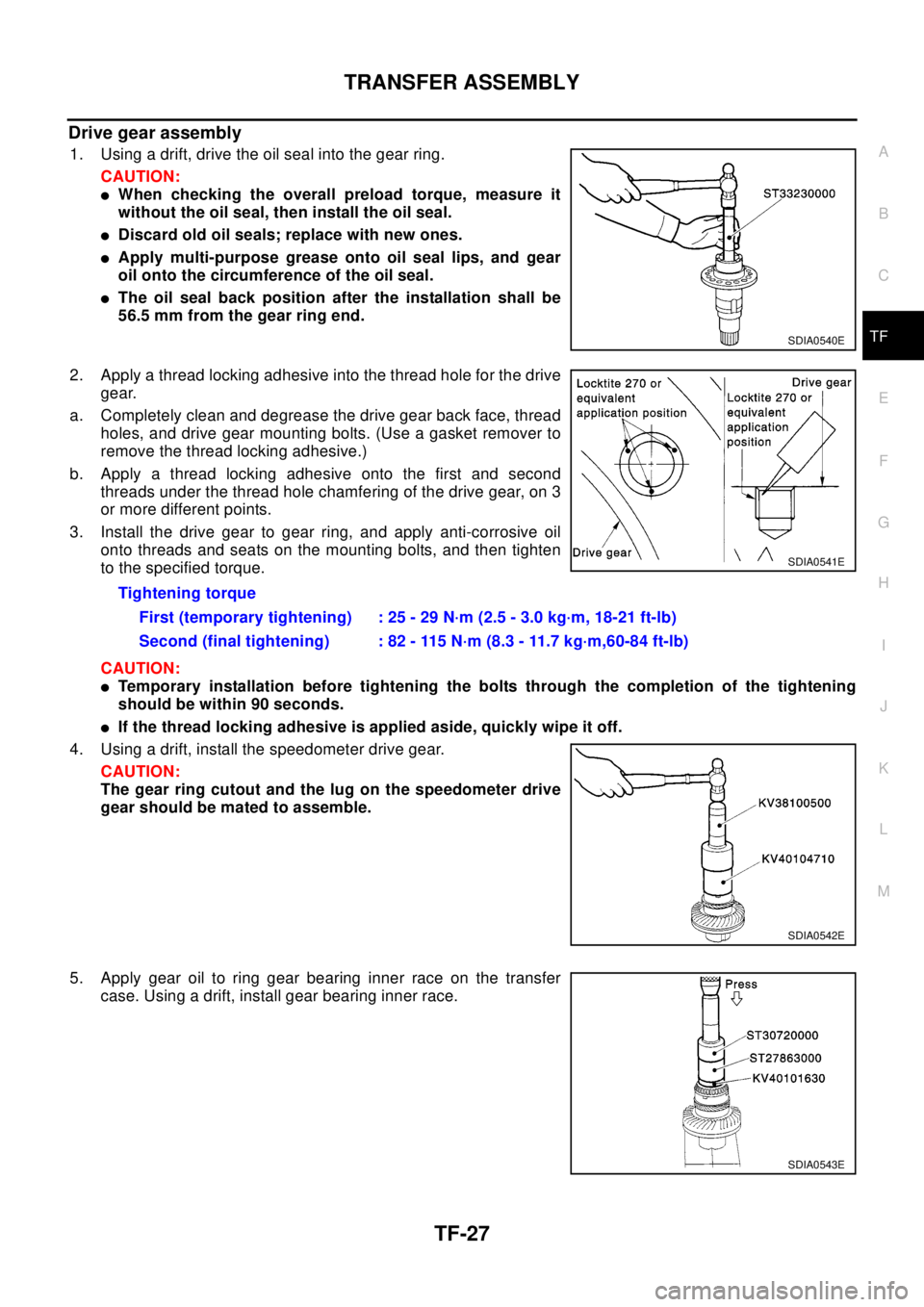
TRANSFER ASSEMBLY
TF-27
C
E
F
G
H
I
J
K
L
MA
B
TF
Drive gear assembly
1. Using a drift, drive the oil seal into the gear ring.
CAUTION:
lWhen checking the overall preload torque, measure it
without the oil seal, then install the oil seal.
lDiscard old oil seals; replace with new ones.
lApply multi-purpose grease onto oil seal lips, and gear
oil onto the circumference of the oil seal.
lThe oil seal back position after the installation shall be
56.5 mm from the gear ring end.
2. Apply a thread locking adhesive into the thread hole for the drive
gear.
a. Completely clean and degrease the drive gear back face, thread
holes, and drive gear mounting bolts. (Use a gasket remover to
remove the thread locking adhesive.)
b. Apply a thread locking adhesive onto the first and second
threads under the thread hole chamfering of the drive gear, on 3
or more different points.
3. Install the drive gear to gear ring, and apply anti-corrosive oil
onto threads and seats on the mounting bolts, and then tighten
to the specified torque.
CAUTION:
lTemporary installation before tightening the bolts through the completion of the tightening
should be within 90 seconds.
lIf the thread locking adhesive is applied aside, quickly wipe it off.
4. Using a drift, install the speedometer drive gear.
CAUTION:
The gear ring cutout and the lug on the speedometer drive
gear should be mated to assemble.
5. Apply gear oil to ring gear bearing inner race on the transfer
case. Using a drift, install gear bearing inner race.
SDIA0540E
Tightening torque
First (temporary tightening) : 25 - 29 N·m (2.5 - 3.0 kg·m, 18-21 ft-lb)
Second (final tightening) : 82 - 115 N·m (8.3 - 11.7 kg·m,60-84 ft-lb)
SDIA0541E
SDIA0542E
SDIA0543E
Page 2998 of 3066
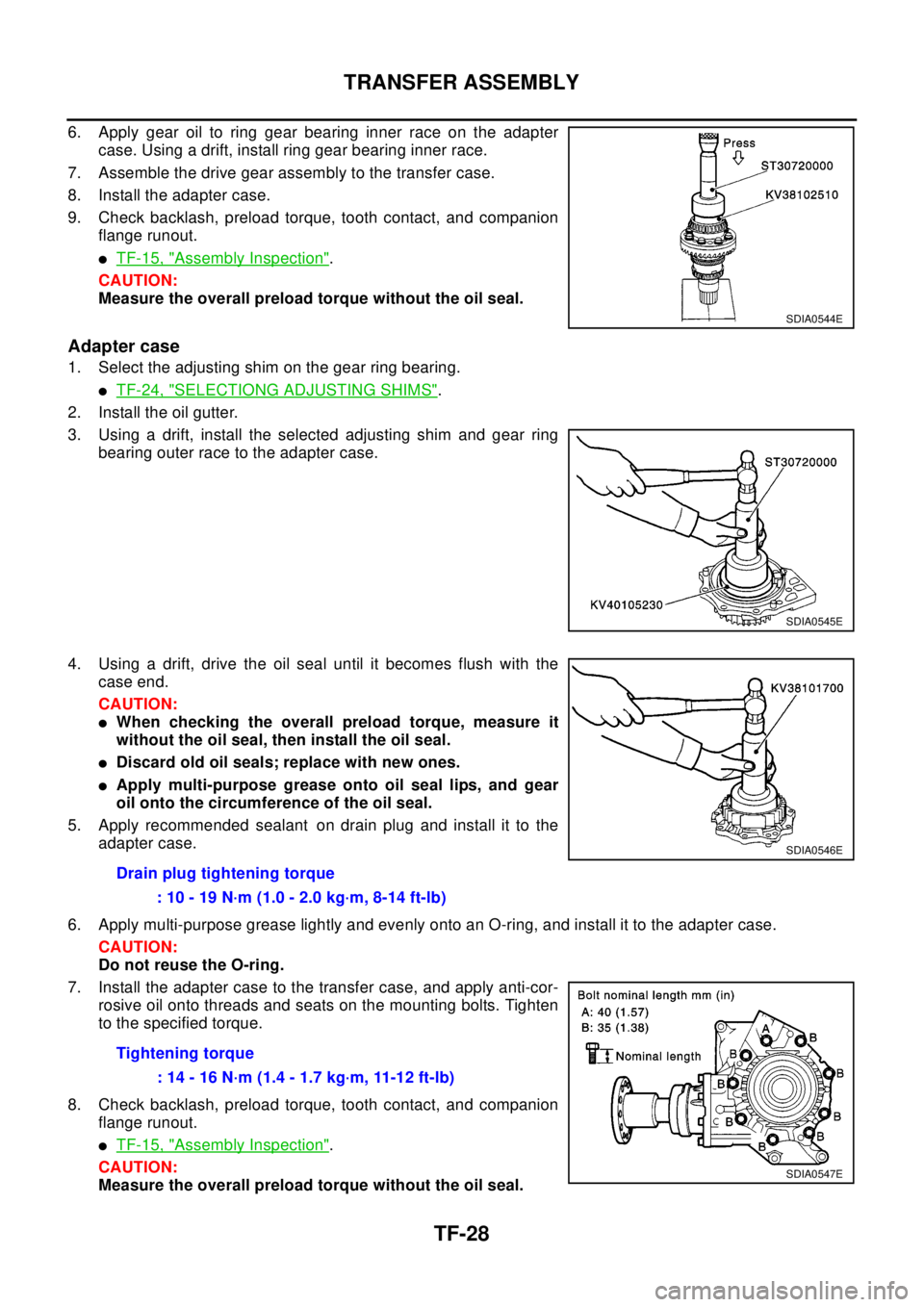
TF-28
TRANSFER ASSEMBLY
6. Apply gear oil to ring gear bearing inner race on the adapter
case. Using a drift, install ring gear bearing inner race.
7. Assemble the drive gear assembly to the transfer case.
8. Install the adapter case.
9. Check backlash, preload torque, tooth contact, and companion
flange runout.
lTF-15, "Assembly Inspection".
CAUTION:
Measure the overall preload torque without the oil seal.
Adapter case
1. Select the adjusting shim on the gear ring bearing.
lTF-24, "SELECTIONG ADJUSTING SHIMS".
2. Install the oil gutter.
3. Using a drift, install the selected adjusting shim and gear ring
bearing outer race to the adapter case.
4. Using a drift, drive the oil seal until it becomes flush with the
case end.
CAUTION:
lWhen checking the overall preload torque, measure it
without the oil seal, then install the oil seal.
lDiscard old oil seals; replace with new ones.
lApply multi-purpose grease onto oil seal lips, and gear
oil onto the circumference of the oil seal.
5. Apply recommended sealant on drain plug and install it to the
adapter case.
6. Apply multi-purpose grease lightly and evenly onto an O-ring, and install it to the adapter case.
CAUTION:
Do not reuse the O-ring.
7. Install the adapter case to the transfer case, and apply anti-cor-
rosive oil onto threads and seats on the mounting bolts. Tighten
to the specified torque.
8. Check backlash, preload torque, tooth contact, and companion
flange runout.
lTF-15, "Assembly Inspection".
CAUTION:
Measure the overall preload torque without the oil seal.
SDIA0544E
SDIA0545E
Drain plug tightening torque
: 10 - 19 N·m (1.0 - 2.0 kg·m, 8-14 ft-lb)
Tightening torque
: 14 - 16 N·m (1.4 - 1.7 kg·m, 11-12 ft-lb)
SDIA0546E
SDIA0547E
Page 2999 of 3066
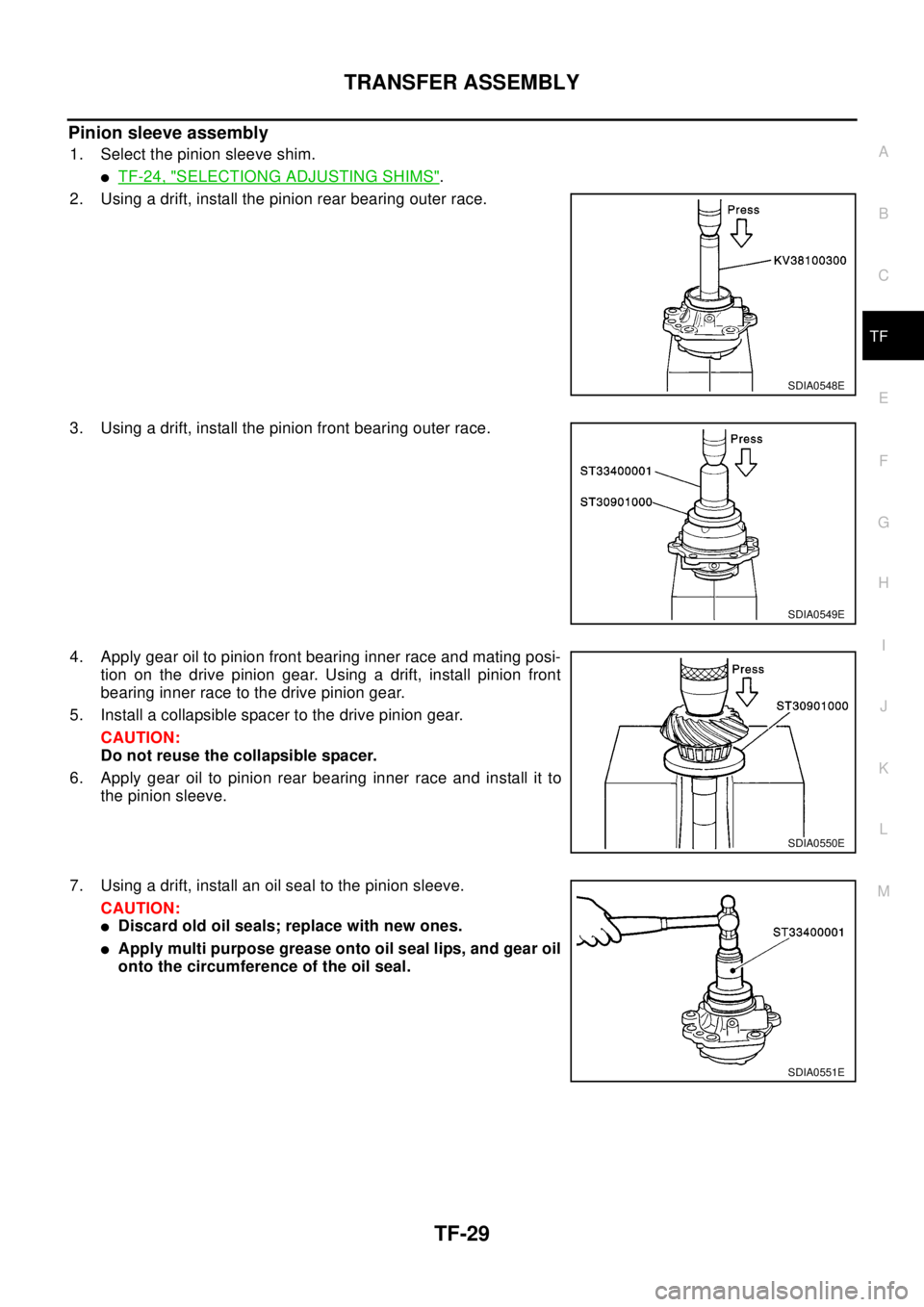
TRANSFER ASSEMBLY
TF-29
C
E
F
G
H
I
J
K
L
MA
B
TF
Pinion sleeve assembly
1. Select the pinion sleeve shim.
lTF-24, "SELECTIONG ADJUSTING SHIMS".
2. Using a drift, install the pinion rear bearing outer race.
3. Using a drift, install the pinion front bearing outer race.
4. Apply gear oil to pinion front bearing inner race and mating posi-
tion on the drive pinion gear. Using a drift, install pinion front
bearing inner race to the drive pinion gear.
5. Install a collapsible spacer to the drive pinion gear.
CAUTION:
Do not reuse the collapsible spacer.
6. Apply gear oil to pinion rear bearing inner race and install it to
the pinion sleeve.
7. Using a drift, install an oil seal to the pinion sleeve.
CAUTION:
lDiscard old oil seals; replace with new ones.
lApply multi purpose grease onto oil seal lips, and gear oil
onto the circumference of the oil seal.
SDIA0548E
SDIA0549E
SDIA0550E
SDIA0551E
Page 3000 of 3066
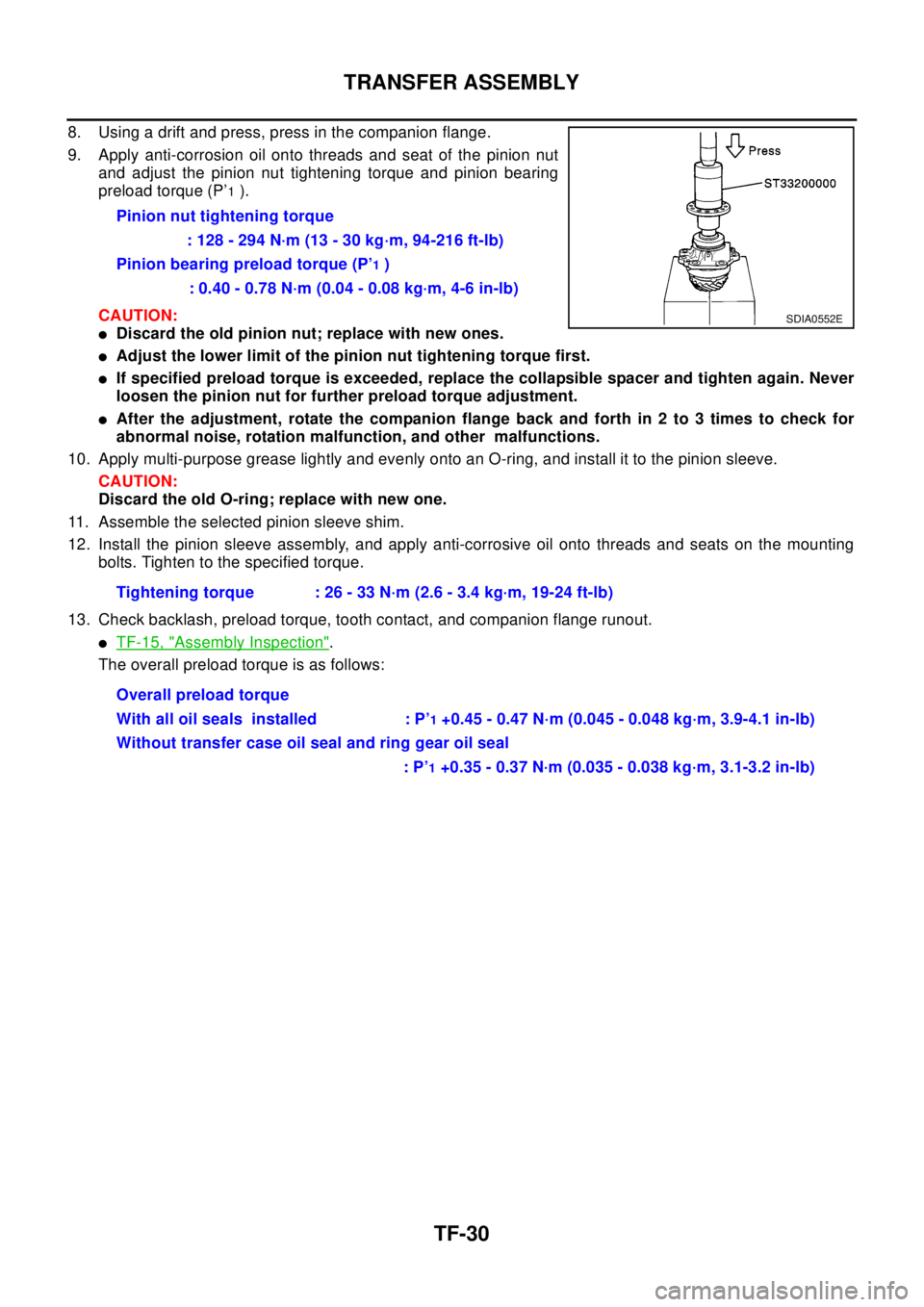
TF-30
TRANSFER ASSEMBLY
8. Using a drift and press, press in the companion flange.
9. Apply anti-corrosion oil onto threads and seat of the pinion nut
and adjust the pinion nut tightening torque and pinion bearing
preload torque (P’
1).
CAUTION:
lDiscard the old pinion nut; replace with new ones.
lAdjust the lower limit of the pinion nut tightening torque first.
lIf specified preload torque is exceeded, replace the collapsible spacer and tighten again. Never
loosen the pinion nut for further preload torque adjustment.
lAfter the adjustment, rotate the companion flange back and forth in 2 to 3 times to check for
abnormal noise, rotation malfunction, and other malfunctions.
10. Apply multi-purpose grease lightly and evenly onto an O-ring, and install it to the pinion sleeve.
CAUTION:
Discard the old O-ring; replace with new one.
11. Assemble the selected pinion sleeve shim.
12. Install the pinion sleeve assembly, and apply anti-corrosive oil onto threads and seats on the mounting
bolts. Tighten to the specified torque.
13. Check backlash, preload torque, tooth contact, and companion flange runout.
lTF-15, "Assembly Inspection".
The overall preload torque is as follows:Pinion nut tightening torque
: 128 - 294 N·m (13 - 30 kg·m, 94-216 ft-lb)
Pinion bearing preload torque (P’
1)
: 0.40 - 0.78 N·m (0.04 - 0.08 kg·m, 4-6 in-lb)
Tightening torque : 26 - 33 N·m (2.6 - 3.4 kg·m, 19-24 ft-lb)
Overall preload torque
With all oil seals installed : P’
1+0.45 - 0.47 N·m (0.045 - 0.048 kg·m, 3.9-4.1 in-lb)
Without transfer case oil seal and ring gear oil seal
:P’
1+0.35 - 0.37 N·m (0.035 - 0.038 kg·m, 3.1-3.2 in-lb)
SDIA0552E