PONTIAC FIERO 1988 Service Repair Manual
Manufacturer: PONTIAC, Model Year: 1988, Model line: FIERO, Model: PONTIAC FIERO 1988Pages: 1825, PDF Size: 99.44 MB
Page 721 of 1825
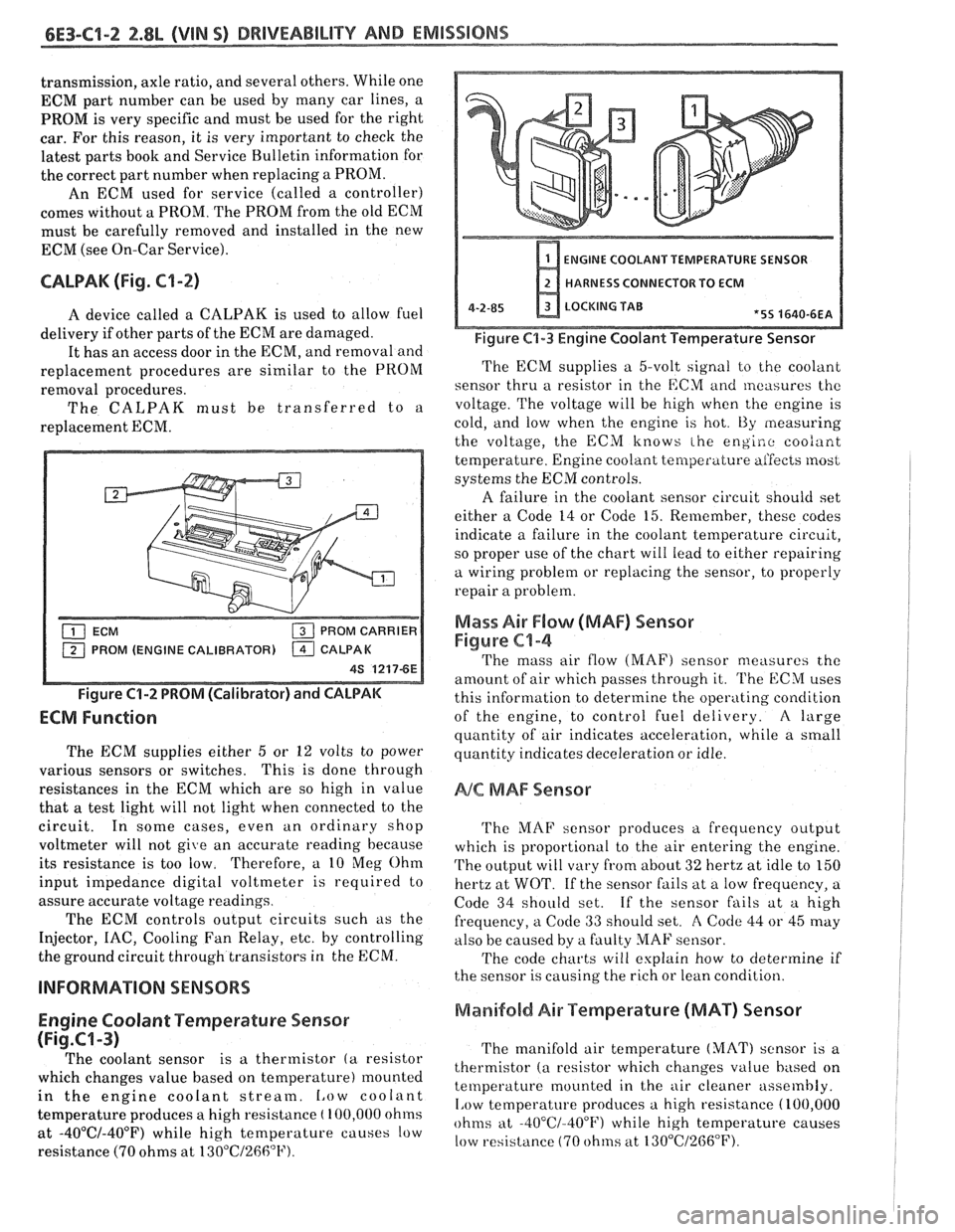
6E3-C1-2 2.8L (VIN S) DRIVEABILITY AND EMISSIONS
transmission, axle ratio, and several others. While one
ECM part number can be used by many car lines, a
PROM is very specific and must be used for the right
car. For this reason, it is very important to check the
latest parts book and Service Bulletin information for
the correct part number when replacing a PROM.
An ECM used for service (called a controller)
comes without a PROM. The PROM from the old ECM
must be carefully removed and installed in the new
ECM (see On-Car Service).
CALPAK (Fig. C1-2)
A device called a CALPAK is used to allow fuel
delivery if other parts of the ECM are damaged.
It has an access door in the ECM, and removal and
replacement procedures are similar to the PROM
removal procedures.
The CALPAK must be transferred to a
replacement ECM.
M (ENGINE CALIBRATOR)
Figure C1-2 PROM (Calibrator) and CALPAK
ECM Function
The ECM supplies either 5 or 12 volts to power
various sensors or switches. This is done through
resistances in the ECM which are so high in value
that
a test light will not light when connected to the
circuit. In some cases, even an ordinary shop
voltmeter will not give an accurate reading because
its resistance is too low. Therefore, a 10
Meg Ohm
input impedance digital voltmeter is required to
assure accurate voltage readings.
The ECM controls output circuits such as the
Injector, IAC, Cooling Fan Relay, etc. by controlling
the ground circuit
thr0ug.h transistors in the ECM.
Engine Coolant Temperature Sensor
(Fig.CI-3)
The coolant sensor is a thermistor (a resistor
which changes value based on temperature) mounted
in the engine coolant stream.
Low coolant
temperature produces a high resistance
( 100,000 ohms
at -40°C/-40°F) while high temperature causes low
resistance (70 ohms at
130"C/26fi°F).
ENGINE COOLANT TEMPERATURE SENIOR
HARNESS CONNECTOR TO ECM
4-2-85 LOCKING TAB *5S 4640-6EA
Figure C1-3 Engine Coolant Temperature Sensor
The ECM supplies a 5-volt signal to the coolant
sensor thru a resistor in the ECM
and measures thc
voltage. The voltage will be high when the engine is
cold, and
low when the engine is hot. t3y measuring
the voltage, the ECM knows
the engiao coo/ant
temperature. Engine coolant temperature aifeces most
systems the ECM controls.
A failure
in the coolant sensor circuit should set
either a Code 14 or Code 15. Remember, these codes
indicate a failure in the coolant temperature circuit,
so proper use of the chart will
lead to either repairing
a wiring problem or replacing the sensor, to properly
repair a problem.
Mass Air F10w (MAF) Sensor
Figure C1-4
The mass air flow (MAF) sensor measures the
amount of air which passes through it.
'I'he ECM uses
this information to determine the operating condition
of the engine, to control
fuel delivery. A large
quantity of air indicates acceleration, while a small
quantity indicates deceleration or idle.
NC MAF Sensor
'I'he MAF sensor produces a frequency output
which is proportional to the air entering the en,'
alne.
The output will vary from about 32 hertz at idle to 150
hertz at WOT. If the sensor fails at a low frequency, a
Code 34 should set. If the sensor fails at a high
frequency, a
Code 33 should set. A Code 44 or 45 may
also be caused by a faulty
MAF sensor.
'I'he code charts will explain how to determine if
the sensor is causing the rich or lean condition.
Manifold Air Temperature (MAT) Sensor
The manifold air temperature (MAT) sensor is a
thermistor
(a resistor which changes value based on
temperature mounted in the
air cleaner assembly.
1,ow temperature produces a high resistance (100,000
ohms at -40°C/-400F) while high temperature causes
low resistance (70 ohms at
130"C/2G6"F).
Page 722 of 1825
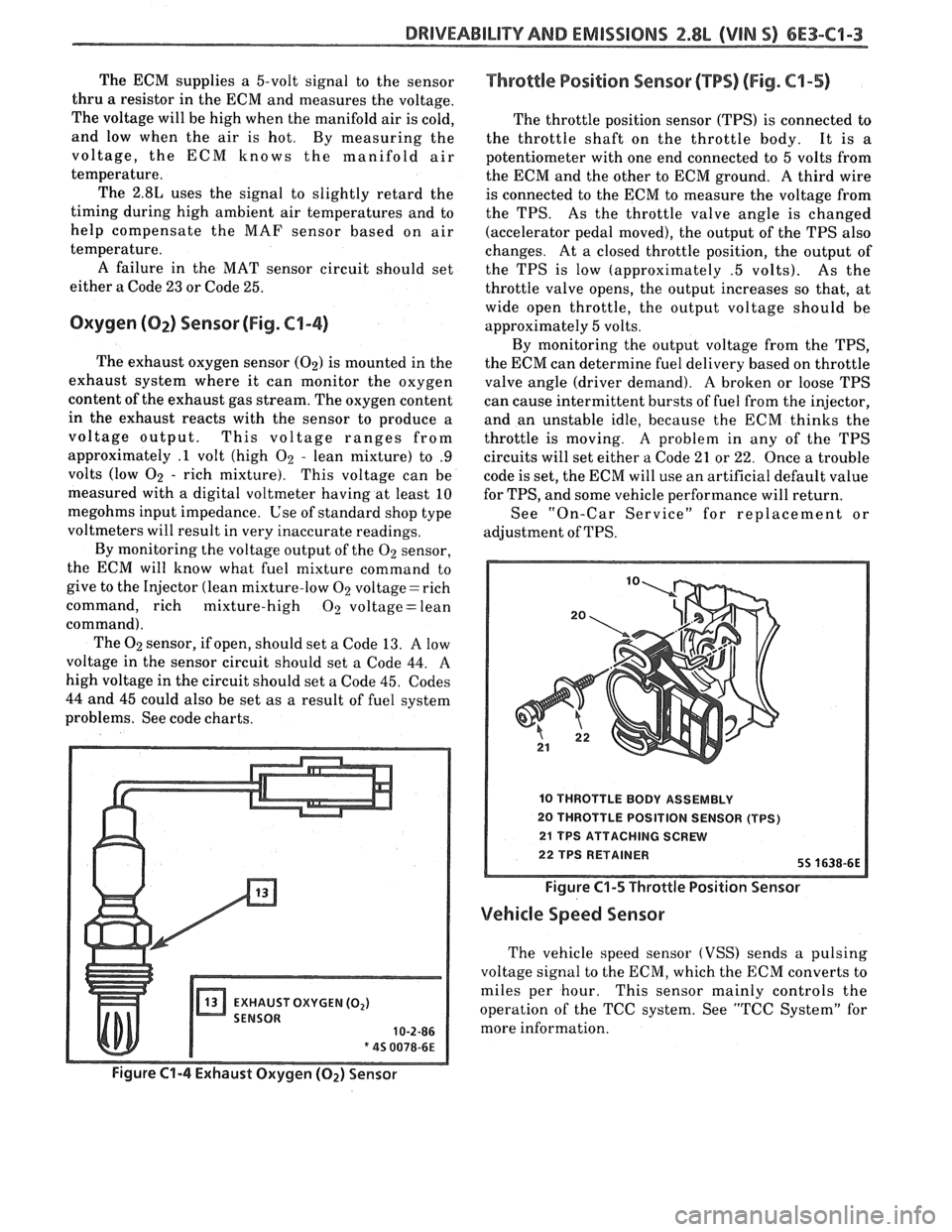
The ECM supplies a 5-volt signal to the sensor
thru
a resistor in the ECM and measures the voltage.
The voltage will be high when the manifold air is cold,
and low when the air is hot. By measuring the
voltage, the ECM knows the manifold air
temperature.
The
2.8L uses the signal to slightly retard the
timing during high ambient air temperatures and to
help compensate the MAF sensor based on air
temperature.
A failure in the MAT sensor circuit should set
either a Code
23 or Code 25.
Oxygen (02) Sensor (Fig. C1-4)
The exhaust oxygen sensor (02) is mounted in the
exhaust system where it can monitor the oxygen
content of the exhaust gas stream. The oxygen content
in the exhaust reacts with the sensor to produce a
voltage output. This voltage ranges from
approximately
.1 volt (high 02 - lean mixture) to .9
volts (low 02 - rich mixture). This voltage can be
measured with a digital voltmeter having at least
10
megohms input impedance. Use of standard shop type
voltmeters will result in very inaccurate readings.
By monitoring the voltage output of the
02 sensor,
the ECM will know what fuel mixture command to
give to the Injector (lean mixture-low
02 voltage = rich
command, rich mixture-high
02 voltage = lean
command). The
02 sensor, if open, should set a Code 13. A low
voltage in the sensor circuit should set a Code 44. A
high voltage in the circuit should set a Code 45. Codes
44 and 45 could also be set
as a result of fuel system
problems. See code charts.
Throttle Position Sensor (PPS) (Fig. C4-5)
The throttle position sensor (TPS) is connected to
the throttle shaft on the throttle body. It is
a
potentiometer with one end connected to 5 volts from
the ECM and the other to ECM ground.
A third wire
is connected to the ECM to measure the voltage from
the TPS. As the throttle valve angle is changed
(accelerator pedal moved), the output of the TPS also
changes. At a closed throttle position, the output of
the TPS is low (approximately
.5 volts). As the
throttle valve opens, the output increases so that, at
wide open throttle, the output voltage should be
approximately 5 volts.
By monitoring the output voltage from the TPS,
the ECM can determine fuel delivery based on throttle
valve angle (driver demand). A
broken or loose TPS
can cause intermittent bursts of fuel from the injector,
and an unstable idle, because the ECM thinks the
throttle is moving.
A problem in any of the TPS
circuits will set either
a Code 21 or 22. Once a trouble
code is set, the ECM will use an artificial default value
for TPS, and some vehicle performance will return.
See "On-Car Service" for replacement or
adjustment of TPS.
10 THROTTLE BODY ASSEMBLY
20 THROTTLE POSITION SENSOR (TPS)
21 TPS ATTACHING SCREW
22 TPS RETAINER 55 1638-6E
Figure C1-5 Throttle Position Sensor
Vehicle Speed Sensor
The vehicle speed sensor (VSS) sends a pulsing
voltage signal to the ECM, which the ECM converts to
miles per hour. This sensor mainly controls the
operation of the TCC system. See "TCC System" for
more information.
Page 723 of 1825
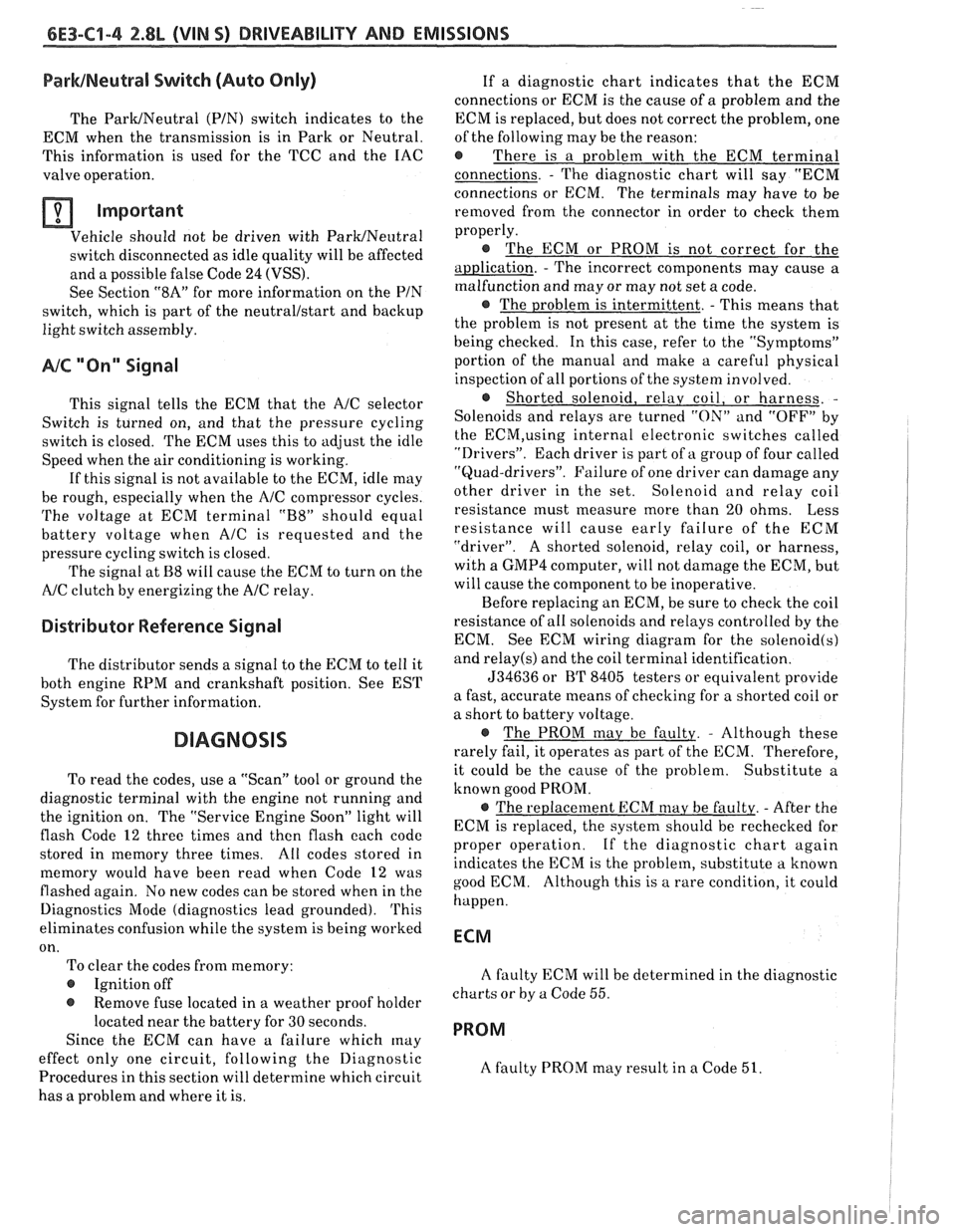
6E3-Cl-4 2.8L (VIN S) DRIVEABILITY AND EMISSIONS
BarWNeutral Switch (Auto Only)
The ParWNeutral (PIN) switch indicates to the
ECM when the transmission is in Park or Neutral.
This information is used for the TCC and the IAC
valve operation.
Important
Vehicle should not be driven with ParWNeutral
switch disconnected as idle quality will be affected
and a possible false Code
24 (VSS).
See Section "$A" for more information on the PIN
switch, which is part of the neutrallstart and backup
light switch assembly.
NC '"n" Signal
This signal tells the ECM that the A/C selector
Switch is turned on, and that the pressure cycling
switch is closed. The ECM uses this to adjust the idle
Speed when the air conditioning is working.
If this signal is not available to the ECM, idle may
be rough, especially when the
A/C compressor cycles.
The voltage at ECM terminal "B8" should equal
battery voltage when
AIC is requested and the
pressure cycling switch is closed.
The signal at
B8 will cause the ECM to turn on the
A/C clutch by energizing the A/C relay.
Distributor Reference Signal
The distributor sends a signal to the ECM to tell it
both engine RPM and crankshaft position. See EST
System for further information.
To read the codes, use a "Scan" tool or ground the
diagnostic terminal with the engine not running and
the ignition on. The "Service Engine Soon" light will
flash Code 12 three times and
then flash each code
stored in memory three times. All codes stored in
memory would have been read when Code 12 was
flashed again. No new codes can be stored when in the
Diagnostics Mode (diagnostics lead grounded).
This
eliminates confusion while the system is being worked
on. To clear the codes from memory:
@ Ignition off
@ Remove fuse located in a weather proof holder
located near the battery for 30 seconds.
Since the ECM can have
a failure which may
effect only one circuit, following the Diagnostic
Procedures in this section will determine which circuit
has a problem and where it is. If
a diagnostic chart indicates that the ECM
connections or ECM is the cause of
a problem and the
ECM is replaced, but does not correct the problem, one
of the following may be the reason:
€9
connections. - The diagnostic chart will say "ECM
connections or ECM. The terminals may have to be
removed from the connector in order to check them
properly.
@ The ECM or PROM is not correct for the
application.
- The incorrect components may cause a
malfunction and may or may not set a code.
@ The problem is intermittent. - This means that
the problem is not present at the time the system is
being checked. In this case, refer to the "Symptoms"
portion of the manual and make a careful physical
inspection of all portions of the system involved.
@ Shorted solenoid, relay coil, or harness. -
Solenoids and relays are turned "ON" and "OFF" by
the
ECM,using internal electronic switches called
"Drivers". Each driver is part of
a group of four called
"Quad-drivers". Failure of one driver can damage any
other driver in the set.
Solelloid and relay coil
resistance must measure more than 20 ohms. Less
resistance will cause early failure of the ECM
"driver". A shorted solenoid, relay coil, or harness,
with a GMP4 computer, will not damage the ECM, but
will cause the component to be inoperative.
Before replacing an ECM, be sure to check the coil
resistance of all solenoids and relays controlled by the
ECM. See ECM wiring diagram for the
solenoid(s)
and relay(s) and the coil terminal identification.
534636 or BT 8405 testers or equivalent provide
a fast, accurate means of checking for a shorted coil or
a short to battery voltage.
@ The PROM may be faulty. - Although these
rarely fail, it operates as part of the ECM. Therefore,
it could be the cause of the problem. Substitute a
known good PROM.
@ The replacement ECM may be faulty. - After the
ECM is replaced, the system should be rechecked for
proper operation. If the diagnostic chart again
indicates the ECM is the problem, substitute
a known
good ECM. Although this is a rare condition, it could
happen.
ECM
A faulty ECM will be determined in the diagnostic
charts or
by a Code 55.
PROM
A faulty PROM may result in a Code 51.
Page 724 of 1825

DRIVEABILITY AND EMlSSlQNS 2.8L (VIN S) 6E3-C1-5
ECM Inputs
All of the sensors and input switches can be
diagnosed by the use of a "Scan" tool. Following is a
short description of how the sensors and switches can
be diagnosed by the use of "Scan".
The "Scan" can
also be used to compare the values for a normal
running engine with the engine you're diagnosing.
Coolant Temperature Sensor
A "Scan" tool displays engine temperature in
degrees centigrade. After
engine is started, the
temperature should rise steadily to about 90°C then
stabilize when thermostat opens. If the engine has not
been run for several hours (overnight) the coolant
temperature and MAT temperatures should read close
to each other. A fault in the coolant sensor circuit
should set a Code
14 or 15. The code charts also
contain a chart to check for sensor resistance values
relative to temperature.
MAF Sensor
A "Scan" tool reads the MAF value and displays it
in grams per second. Should read between 4-7 on a
fully warmed up idling engine. Values should change
rather quickly on acceleration, but values should
remain fairly stable at any given RPM. Most "Scan"
tools will have 2 positions for reading
MAE' sensor
values. (MAF
& Air Flow). Both values should read
the same if no Code 33 or 34 is set, but if a code is set,
the MAF values will be the default value and the Air
Flow parameter will lock in on the value to which the
ECM recognized the fault. A failure in the MAF
sensor or circuit should set a Code 33 or 34.
MAT Sensor
A "Scan" tool displays temperature of the air
entering the engine and should read close to ambient
air temperature when engine is cold, and rise as
underhood temperature increases. If the engine has
not been run for several hours (overnight) the MAT
sensor temperature and coolant temperature should
read close to each other. A failure in the MAT sensor
circuit should set
a Code 23 or 25. The code charts also
contain a chart to check for sensor resistance values
relative to temperature.
02 Sensor
The "Scan" has several positions that will indicate
the state of the exhaust gases,
O1! voltage, integrator,
and block learn. See "Scan" position information in
"Introduction," Section
"6E".
A problem in the O2 sensor circuit, or fuel system,
should set a Code 13 (open circuit), Code 44 (lean
indication), Code 45 (rich indication). Refer to
applicable chart if any of these codes
were stored in
memory.
TPS
A "Scan" tool displays throttle position in volts.
You should read
.55V f .08V, with throttle closed and
ignition on, or at idle. Voltage should increase at
a
steady rate as throttle is moved toward WOT.
The ECM has the ability to Auto-Zero the TPS
voltage if it is below about .7V (700
mV). This means
that any voltage less than
.7 volts will be determined
by the ECM to be
0% throttle. A failure in the TPS or
circuit should set a Code 21 or 22.
A "Scan" tools reading should closely match with
speedometer reading with drive wheels turning.
A
failure in the VSS circuit should set a Code 24.
PIN Switch
A "Scan" tool should read PIN when in Park, or
Neutral, and R-D, L, when in Drive or Overdrive.
This reading may vary with different makes of tools.
Refer to CHART
C-1A for PIN switch diagnosis.
NC Request Signal
"Scan" tool should indicate A/C request "ON,"
when A/C is requested and the pressure cycling switch
is closed.
Power Steering Pressure Switch
A "Scan" tool should read "OFF" normally and
"ON" with high pressure. This reading may vary with
different make of tools. Refer to CHART
C-1E for
PSPS diagnosis.
Reference Signal
A "ScanJ' tool will read this signal and is displayed
in rpm.
ON-CAR SERVICE
ELECTRONIC CONTROL MODULE (ECM)
Service of the ECM should normally consist of
either replacement of the ECM or a PROM change.
If the diagnostic
procedures call for the ECM to be
replaced, the engine calibrator (PROM) and ECM
should be checked first to see if they are the correct
parts. If they are, remove the PROM from the faulty
ECM
and install it in the new service ECM. THE
SERVICE ECM WILL NOT CONTAIN A PROM or
CALPAK. Trouble Code 51 indicates the PROM is
installed improperly or has malfunctioned. When
Code
51 is obtained, check the PROM installation for
bent pins or pins not fully seated in the socket. If it is
installed correctly and Code 51 still shows, replace the
PROM.
Page 725 of 1825
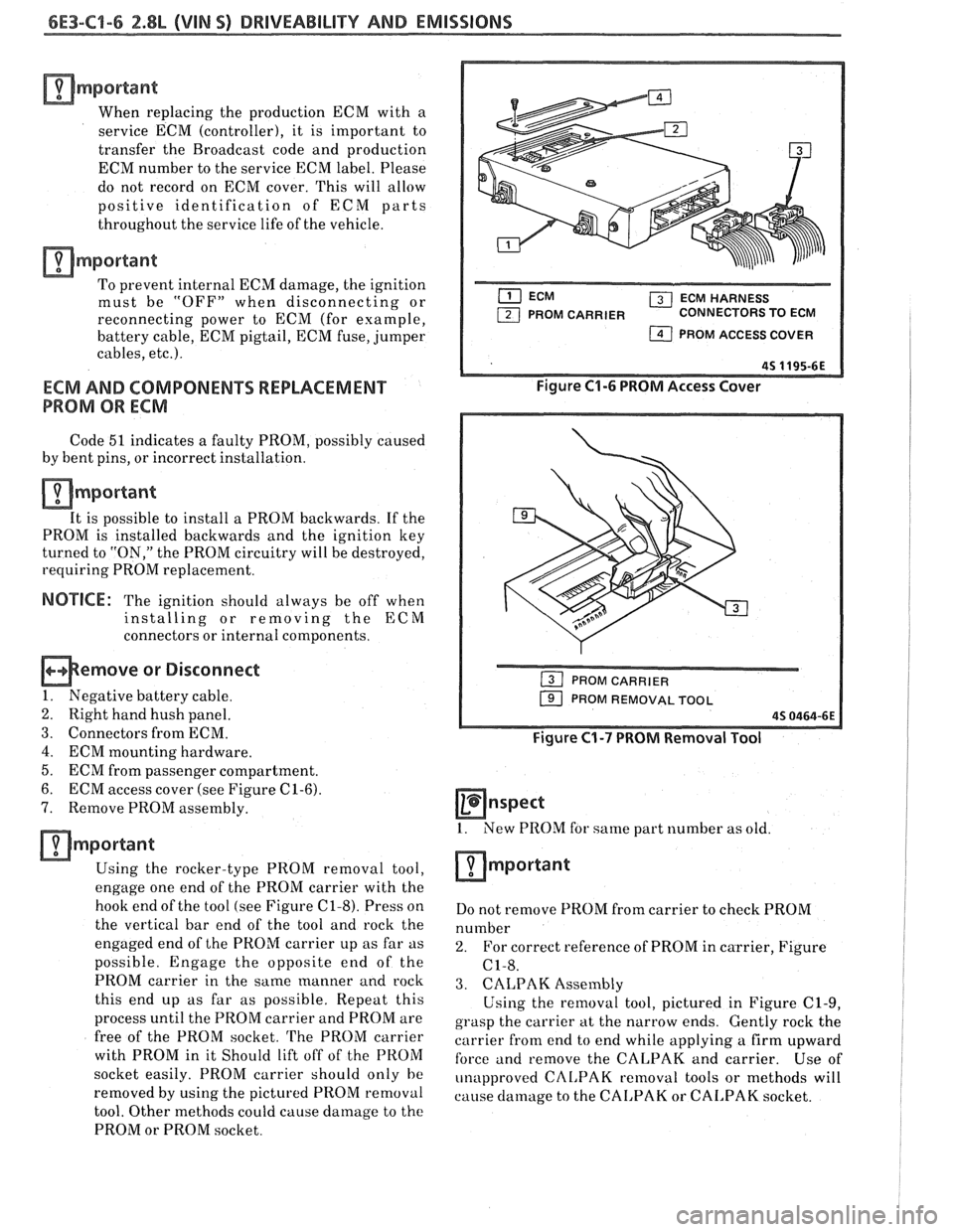
6E3-C1-6 2.8L (VIM O) DRlVEABlLlTY AND EMISSIONS
amportant
When replacing the production ECM with a
service ECM (controller), it is important to
transfer the Broadcast code and production
ECM number to the service ECM label. Please
do not record on ECM cover. This will allow
positive identification of ECM parts
throughout the service life of the vehicle.
amportant
To prevent internal ECM damage, the ignition
must be "OFF" when disconnecting or
reconnecting power to ECM (for example,
battery cable, ECM pigtail, ECM fuse, jumper
cables,
etc.).
ECM AND COMPONENTS REPLACEMENT
PROM OR ECM
Code 51 indicates a faulty PROM, possibly caused
by bent pins, or incorrect installation.
mmportant
It is possible to install a PROM backwards. If the
PROM
is installed backwards and the ignition key
turned to "ON," the PROM circuitry will be destroyed,
requiring PROM replacement.
NOTICE: The ignition should always be off when
installing or removing the ECM
connectors or internal components.
memove or Disconnect
1. Negative battery cable.
2. Right hand hush panel.
3. Connectors from ECM.
4. ECM mounting hardware.
5. ECM from passenger compartment.
6. ECM access cover (see Figure
C1-6).
7. Remove PROM assembly.
amportant
Using the rocker-type PROM removal tool,
enga& one end of t-hk PROM carrier with the
hook end of the tool (see Figure
C1-8). Press on
the vertical bar end of the tool and rock the
engaged end of the PROM carrier up as far as
possible. Engage the opposite end of the
PROM carrier in the same manner and
rock
this end up as far as possible. Repeat this
process until the PROM carrier and PROM are
free of the PROM socket.
The PROM carrier
with PROM in it Should lift off of the PROM
socket easily. PROM carrier should only
he
removed by using the pictured PROM removal
tool. Other methods could cause damage to the
PROM or PROM socket.
( ECM HARNESS
PROM CARRIER CONNECTORS TO ECM
1 PROM ACCESS COVER
Figure C1-6 PROM Access Cover
PROM CARRIER
PROM REMOVAL TOOL
Figure C1-7 PROM Removal Tool
Hnspect
1. New PROM for same part number as old.
Do not remove PROM from carrier to check PROM
number
2. For correct reference of PROM in carrier, Figure
C1-8.
3. CALPAK Assembly
Using the removal tool, pictured in Figure C1-9,
grasp the carrier
at the narrow ends. Gently rock the
carrier
from end to end while applying a firm upward
force and remove the CALPAK and carrier. Use of
unapproved
CAL,PAK removal tools or methods will
cause
damage to the CAI,PAK or CALPAK socket.
Page 726 of 1825
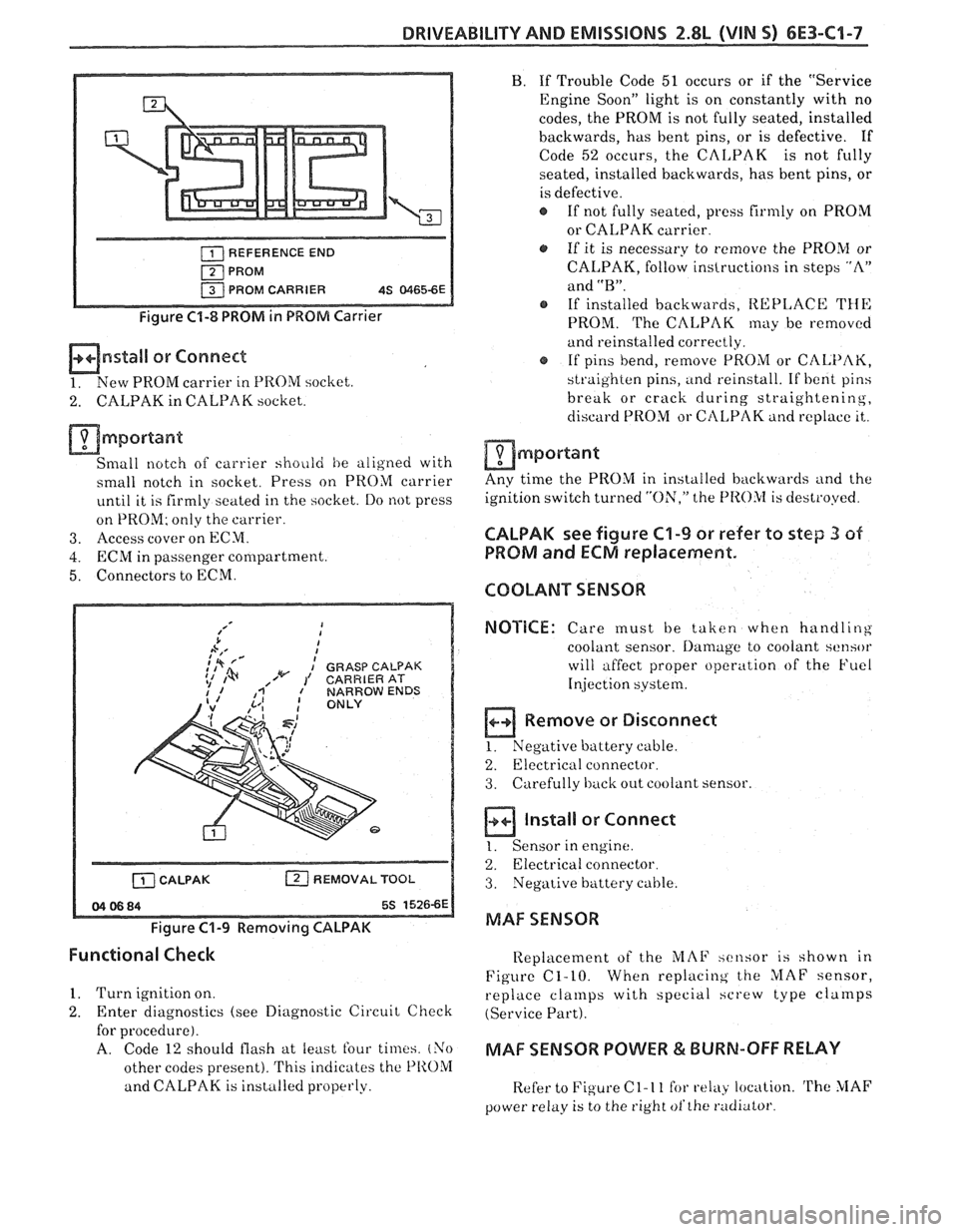
DRIVEABILITY AND EMISSIONS 2.8L (VIN S) 6E3-C1-7
REFERENCE END
PROM PROM CARRIER
4S 81165-6E
Figure C1-8 PROM in PROM Carrier
mnstall or Connect
1. New PROM carrier in PROM socliet.
2. CALPAK in CALPAK socket.
mmportant
Small notch of carrier shoiild he aligned with
small notch in socket. Press on PROM carrier
until it is firmly seated in the socket. Do not press
on PROM; only the carrier.
3. Access cover on ECM.
4. ECRil in passenger compartment.
5. Connectors to ECM.
b A,' I
;,* fd I
: GRASP CALPAK 1% ,/w 1' CARRIERAT
[ZJ REMOVAL TOOL
Figure C1-9 Removing CALPAK
B. If Trouble Code 51 occurs or if the "Service
Engine Soon" light is on constantly with no
codes, the PROM is not fully seated, installed
backwards, has bent pins, or is defective. If
Code
52 occurs, the CALPAK is not fully
seated, installed backwards, has bent pins, or
is defective.
If not fully seated,
press firmly on PROM
or CALPAK carrier
a, If it is necessary to remove the PROM or
CALPAK, follow instructions in steps "A"
and
"B".
@ If installed backwards, REPLACE THE
PROM. The CALPAK may be removed
and reinstalled correctly.
@ If pins bend, remove PROM or CALPAK,
straighten pins, and reinstall. If
bent pins
break or crack during
straightening,
discard PROM or CtILPAK and replace it,.
am port ant
Any time the PROM in installed backwards and the
ignition switch turned
"ON," the f'I
PROM and ECM replacement.
COOLANT SENSOR
NOTICE:
Care must be taken when handling
coolant sensor.
Damage to coolant sensor
will affect proper operation of the Fuel
Injection
system.
B Remove or Disconnect
1. Negative buttery cable.
2.
Electricril connector.
3. Carefully back out coolant sensor.
a ln,aIl
1. Sensor in
or Connect
engine.
2. Electrical connector.
3. Negative battery cable.
MAF SENSOR
Functional Check
Replacement of the iL'IAF xcnsor is shown in
Figure C1-10. When
replacing the MAF sensor,
1. Turn ignition on.
replace cla~llps with special hcrew type cla~rlps
2. Enter diagnostics (see Diagnostic Circuit Check (Service Part).
for procedure).
A. Code 12 should flash at least four times. (Yo MAF SENSOR POWER & BURN-OFF RELAY
other codes present). This indicates the PIIOM
and CALPAK is installed properly.
Refer to Figure C 1- 1 1 for relay location. 'rhe MAF
power relay is to the right ofthe radiator
Page 727 of 1825
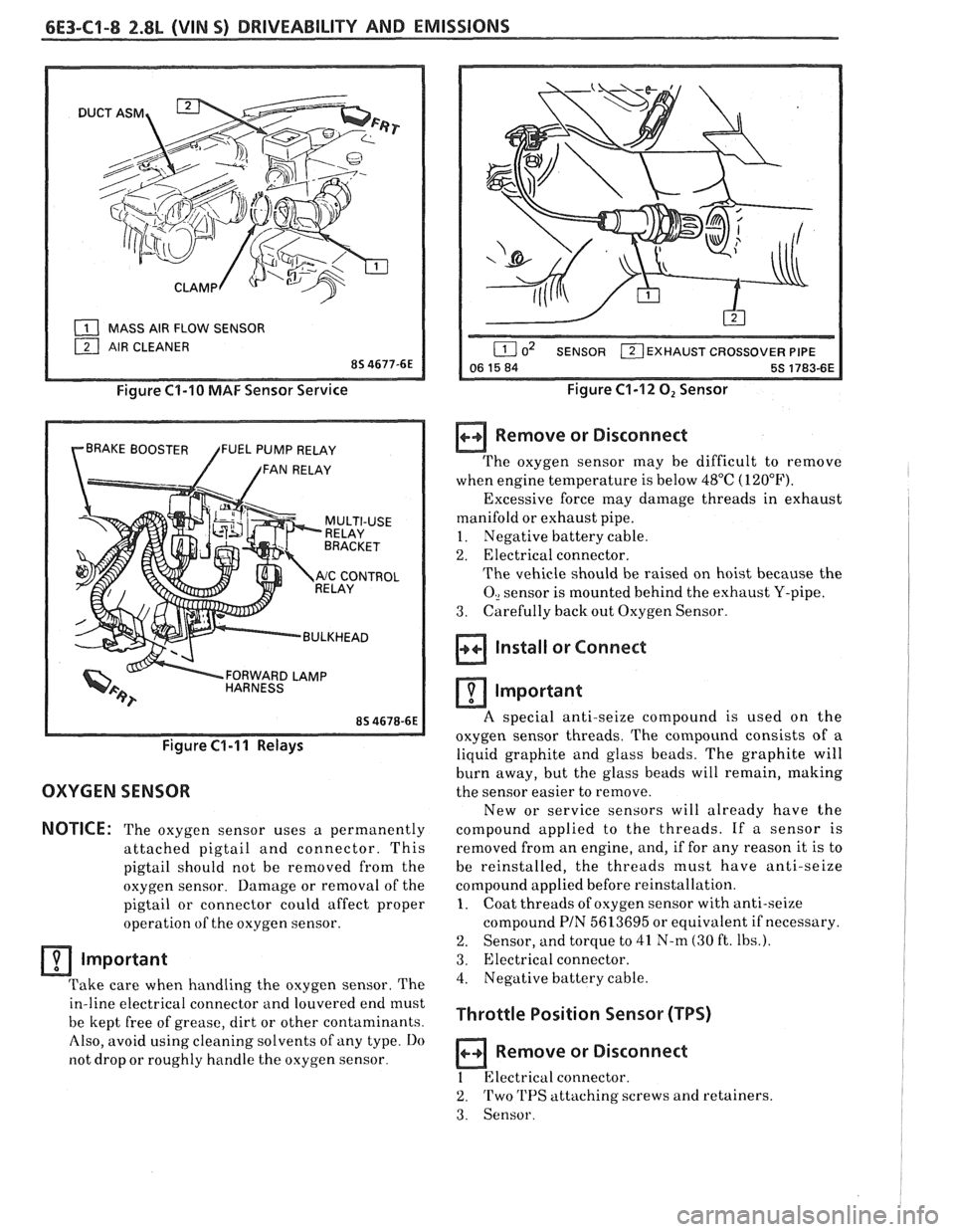
6E3-(31-8 2.8L (VIN S) DRIVEABILITY AND EMISSIONS
( MASS AIR FLOW SENSOR
Figure C1-10 MAF Sensor Service
BRAKE BOOSTER FUEL PUMP RELAY
/ /FAN RELAY
FORWARD LAMP
/ BULKHEAD
Figure C1-I I Relays
OXYGEN SENSOR
NOTICE:
The oxygen sensor uses a permanently
attached pigtail and connector. This
pigtail should not be removed from the
oxygen sensor. Damage or removal of the
pigtail or connector could affect proper
operation of the oxygen sensor.
Important
Take care when handling the oxygen sensor. The
in-line electrical connector and louvered end must
be kept free of grease, dirt or other contaminants.
Also, avoid using cleaning solvents of any type.
Do
not drop or roughly handle the oxygen sensor.
EXHAUST CROSSOVER PIPE
Figure C1-12 0, Sensor
Remove or Disconnect
The oxygen sensor may be difficult to remove
when engine temperature is below 48°C (120°F).
Excessive force may damage threads in exhaust
manifold or exhaust pipe.
~
1. Negative battery cable.
2. Electrical connector.
The vehicle should be raised on hoist because the
0, sensor is mounted behind the exhaust Y-pipe.
3. Carefully
back out Oxygen Sensor.
Install or Connect 1 i
Important I I
A special anti-seize compound is used on the
oxygen sensor threads. The compound consists
of a
liquid graphite and glass beads. The graphite will
burn away, but the glass beads will remain, making
the sensor easier to remove.
New or service sensors will already have the
compound applied to the threads. If a sensor is
removed from an engine, and, if for any reason it is to
be reinstalled, the threads must have anti-seize
compound applied before reinstallation.
1. Coat threads of oxygen sensor with anti-seize
compound
PIN 5613695 or equivalent if necessary.
2. Sensor, and torque to 41 N-m (30 ft. Ibs.).
3. Electrical connector.
4. Negative battery cable.
Throttle Position Sensor (TPS)
a Remove or Disconnect
1 Electrical connector.
2. Two 'I'PS attaching screws and retainers.
3. Sensor.
Page 728 of 1825
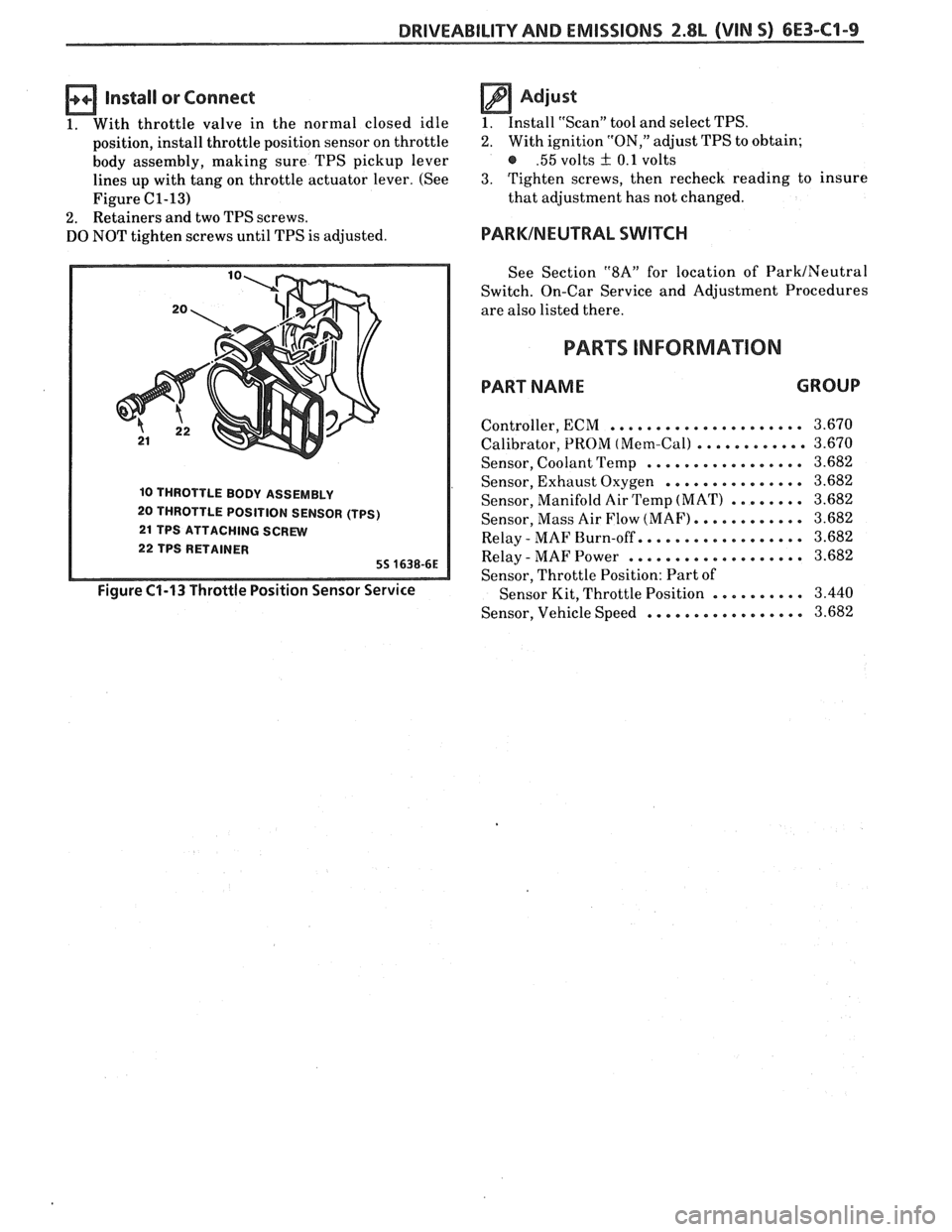
DRIVEABILITY AND EMISSIONS 2.8L (VIN 5) 6E3-C1-9
Install or Connect
1. With throttle valve in the normal closed idle
position, install throttle position sensor on throttle
body assembly, making sure TPS pickup lever
lines up with tang on throttle actuator lever. (See
Figure
C1-13)
2. Retainers and two TPS screws.
DO NOT tighten screws until TPS is adjusted.
10 THROTTLE BODY ASSEMBLY
20 THROTTLE POSITION SENSOR (TPS)
21 TPS ATTACHING SCREW
22 TPS RETAINER
55 1638-6E
Figure C1-13 Throttle Position Sensor Service
Adjust
1. Install "Scan" tool and select TPS.
2. With ignition "ON," adjust TPS to obtain;
@ .55 volts + 0.1 volts
3. Tighten screws, then recheck reading to insure
that adjustment has not changed.
PARKINEUTRAL SWITCH
See Section "$A" for location of ParkINeutral
Switch. On-Car Service and Adjustment Procedures
are also listed there.
PARTS INFORMAION
PART NAME GROUP
..................... Controller, ECM
Calibrator, PROM
(Mem-Call ............
Sensor, Coolant Temp .................
Sensor, Exhaust Oxygen ...............
Sensor, Manifold Air Temp (MAT) ........
Sensor, Mass Air Flow (MAF). ...........
Relay - MAF Burn-off.. ................
Relay - MAF Power ...................
Sensor, Throttle Position: Part of
Sensor Kit, Throttle Position
..........
Sensor, Vehicle Speed .................
Page 729 of 1825
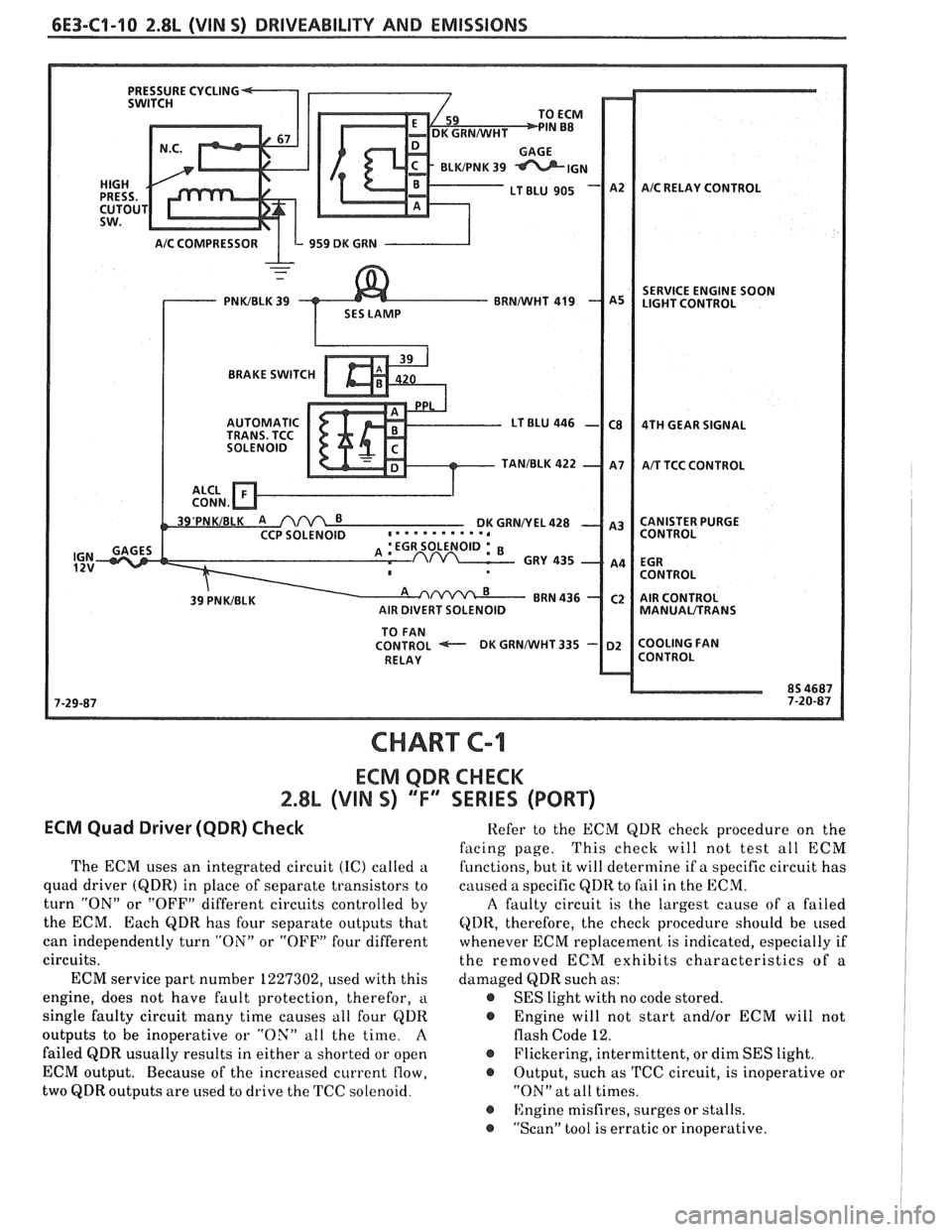
6E3-C1-10 2.8L (VIN 5) DRIVEABILITY AND EMISSIONS
- 959 DK GRN
BRAKE SWITCH
MANUALTRANS
TO FAN
CONTROL +-- DK GRNMIHT335 - COOLING FAN
RELAY
CHART C-I
ECM QDR CHECK
2.8% (VIN S) 'TI' SERIES (PORT)
ECM Quad Driwer (QDR) Check
The ECM uses an integrated circuit (IC) called a
quad driver
(QDR) in place of separate transistors to
turn "ON" or "OFF" different circuits controlled by
the ECM. Each
QDR has four separate outputs that
can independently turn "ON" or "OFF" four different
circuits.
ECM service part number 1227302, used with this
engine, does not have fault protection, therefor,
a
single faulty circuit many time causes all four QDR
outputs to be inoperative or "OX" all the time.
A
failed QDR usually results in either a shorted or open
ECM output. Because of the increased current
flow,
two QDR outputs are used to drive the TCC solenoid. Refer
to the ECM QDR check procedure on the
facing page. This
check will not test all ECM
functions, but it will determine if a specific circuit has
caused a specific
QDR to fail in the ECM.
A faulty circuit is the largest cause of a failed
QDR, therefore, the check procedure should be used
whenever ECM replacement is indicated, especially if
the removed ECM exhibits characteristics of a
damaged QDR such as:
@ SES light with no code stored.
@ Engine will not start and/or ECM will not
flash Code 12.
@ Flickering, intermittent, or dim SES light.
@ Output, such as TCC circuit, is inoperative or
"ON" at all times.
@ ISngine misfires, surges or stalls.
@ "Scan" tool is erratic or inoperative.
Page 730 of 1825
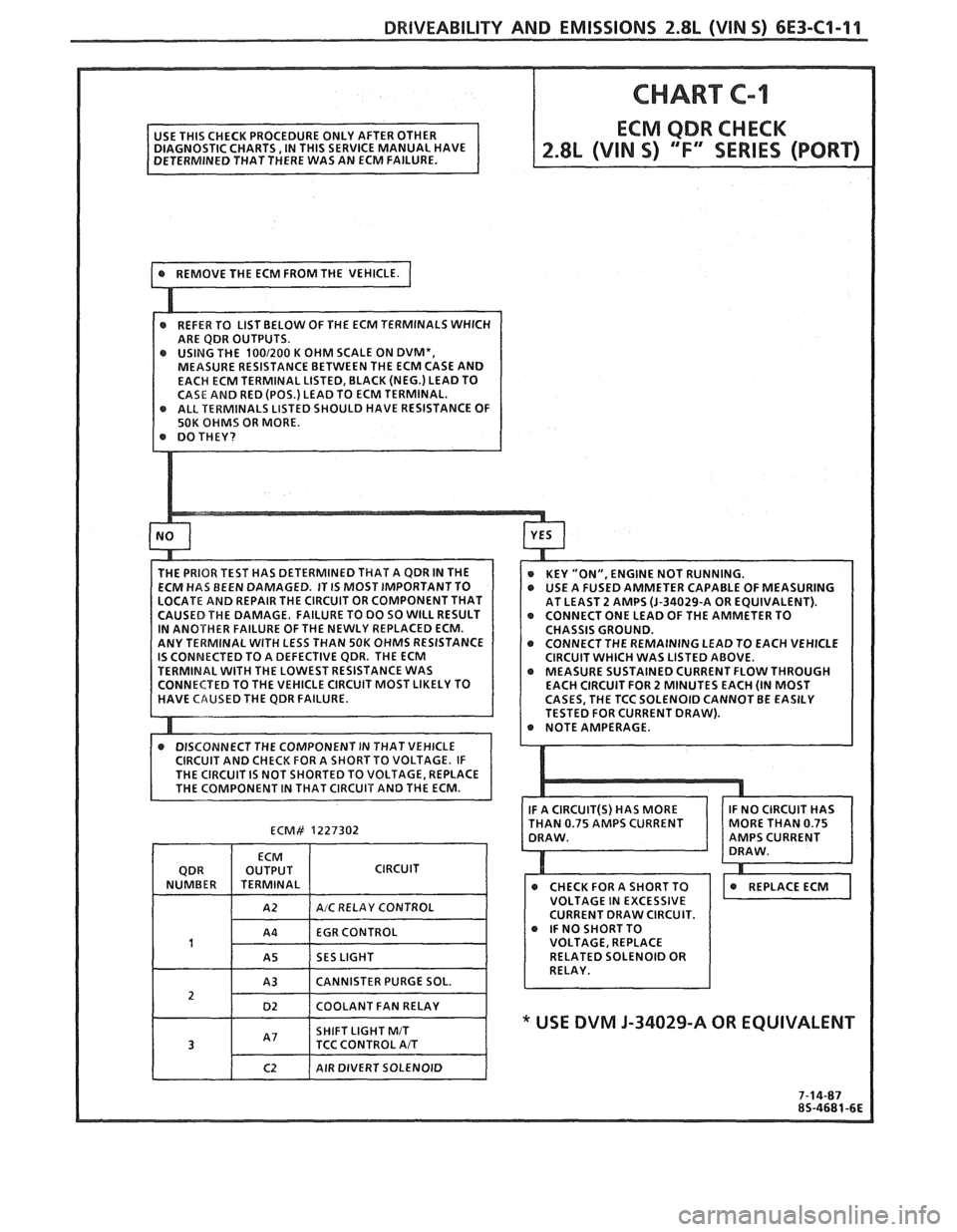
DRlVEABlLlPY AND EMISSIONS 2.8L (VIN S) 6E3-C1-11
USE THIS CHECK PROCEDURE ONLY AFTER OTHER
DIAGNOSTIC CHARTS, IN THIS SERVICE MANUAL HAVE
DETERMINED THAT THERE WAS AN ECM FAILURE.
TERMINAL LISTED, BLACK (NEG.) LEAD TO
RED
(POS.) LEAD TO ECM TERMINAL.
NALS LISTED SHOULD HAVE RESISTANCE OF
EACH VEHICLE
ECM# 1227302
VOLTAGE IN EXCESSIVE
CURRENT DRAW CIRCUIT.
* USE DVM J-34029-A OR EQUIVALENT