SSANGYONG KORANDO 1997 Service Owner's Manual
Manufacturer: SSANGYONG, Model Year: 1997, Model line: KORANDO, Model: SSANGYONG KORANDO 1997Pages: 2053, PDF Size: 88.33 MB
Page 21 of 2053
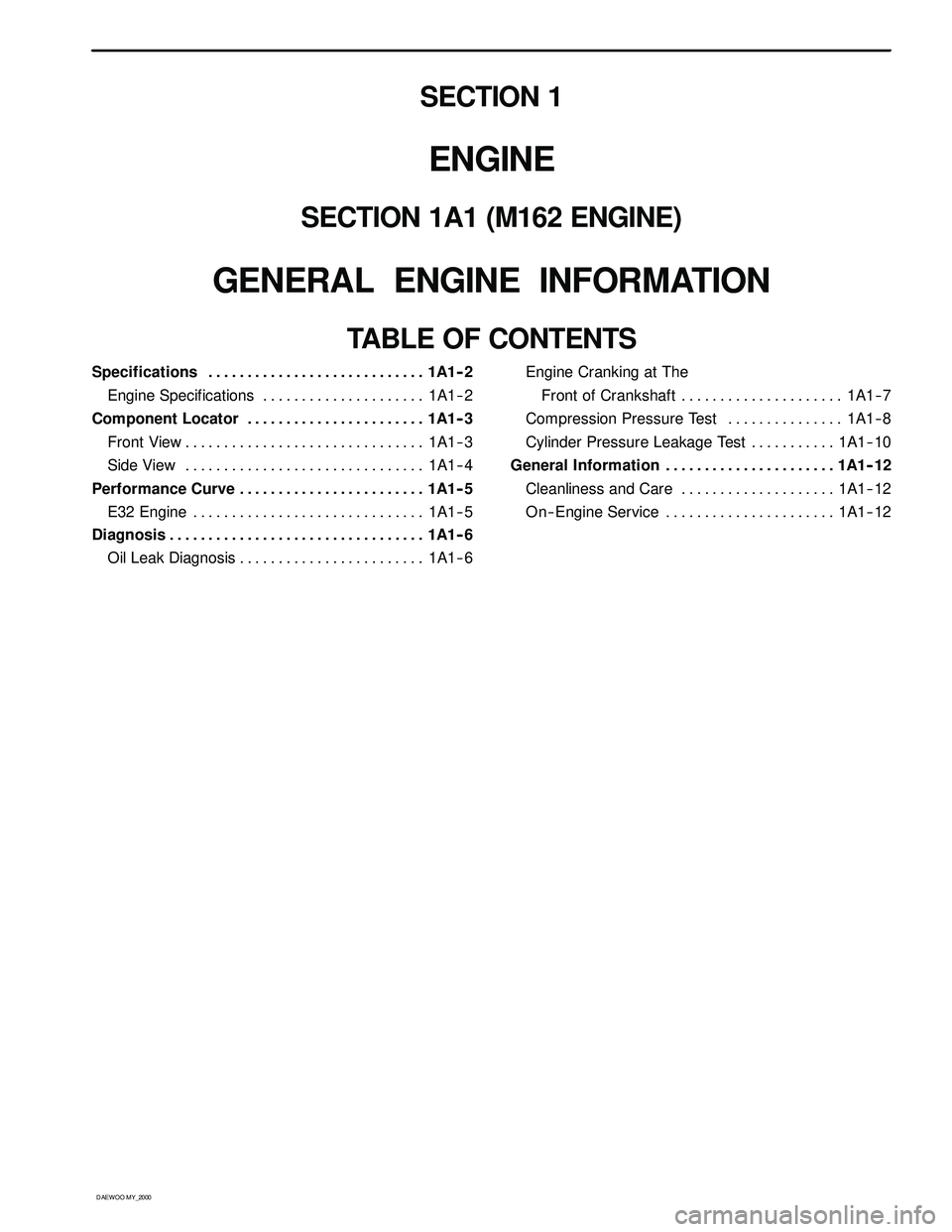
D AEW OO M Y_2000
SECTION 1
ENGINE
SECTION 1A1 (M162 ENGINE)
GENERAL ENGINE INFORMATION
TABLE OF CONTENTS
Specifications 1A1 -- 2............................
Engine Specifications 1A1-- 2.....................
Component Locator 1A1 -- 3.......................
Front View 1A1 -- 3...............................
Side View 1A1-- 4...............................
Performance Curve 1A1-- 5........................
E32 Engine 1A1-- 5..............................
Diagnosis 1A1 -- 6.................................
Oil Leak Diagnosis 1A1-- 6........................Engine Cranking at The
FrontofCrankshaft 1A1--7.....................
Compression Pressure Test 1A1-- 8...............
Cylinder Pressure Leakage Test 1A1-- 10...........
General Information 1A1 -- 12......................
Cleanliness and Care 1A1 -- 12....................
On-- Engine Service 1A1-- 12......................
Page 22 of 2053
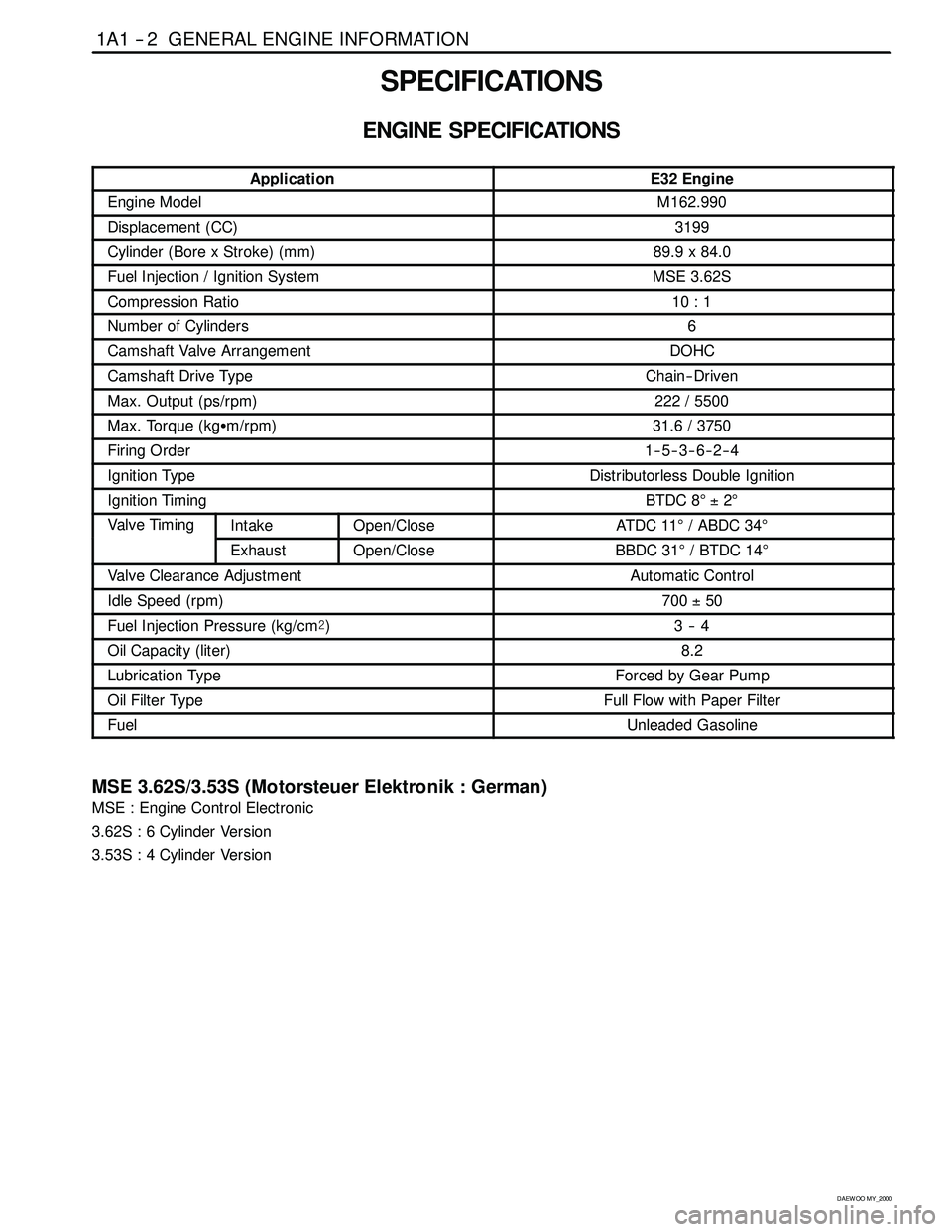
1A1 -- 2 GENERAL ENGINE INFORMATION
D AEW OO M Y_2000
SPECIFICATIONS
ENGINE SPECIFICATIONS
ApplicationE32 Engine
Engine ModelM162.990
Displacement (CC)3199
Cylinder (Bore x Stroke)(mm)89.9 x 84.0
Fuel Injection / Ignition SystemMSE 3.62S
Compression Ratio10 : 1
Number of Cylinders6
Camshaft Valve ArrangementDOHC
Camshaft Drive TypeChain-- Driven
Max. Output (ps/rpm)222 / 5500
Max. Torque (kgSm/rpm)31.6 / 3750
Firing Order1--5--3--6--2--4
Ignition TypeDistributorless Double Ignition
Ignition TimingBTDC 8°±2°
Valve TimingIntakeOpen/CloseAT DC 11°/ ABDC 34°g
ExhaustOpen/CloseBBDC 31°/BTDC14°
Valve Clearance AdjustmentAutomatic Control
Idle Speed (rpm)700±50
Fuel Injection Pressure (kg/cm@)3--4
Oil Capacity (liter)8.2
Lubrication TypeForced by Gear Pump
Oil Filter TypeFull Flow with Paper Filter
FuelUnleaded Gasoline
MSE 3.62S/3.53S (Motorsteuer Elektronik : German)
MSE : Engine Control Electronic
3.62S : 6 Cylinder Version
3.53S : 4 Cylinder Version
Page 23 of 2053
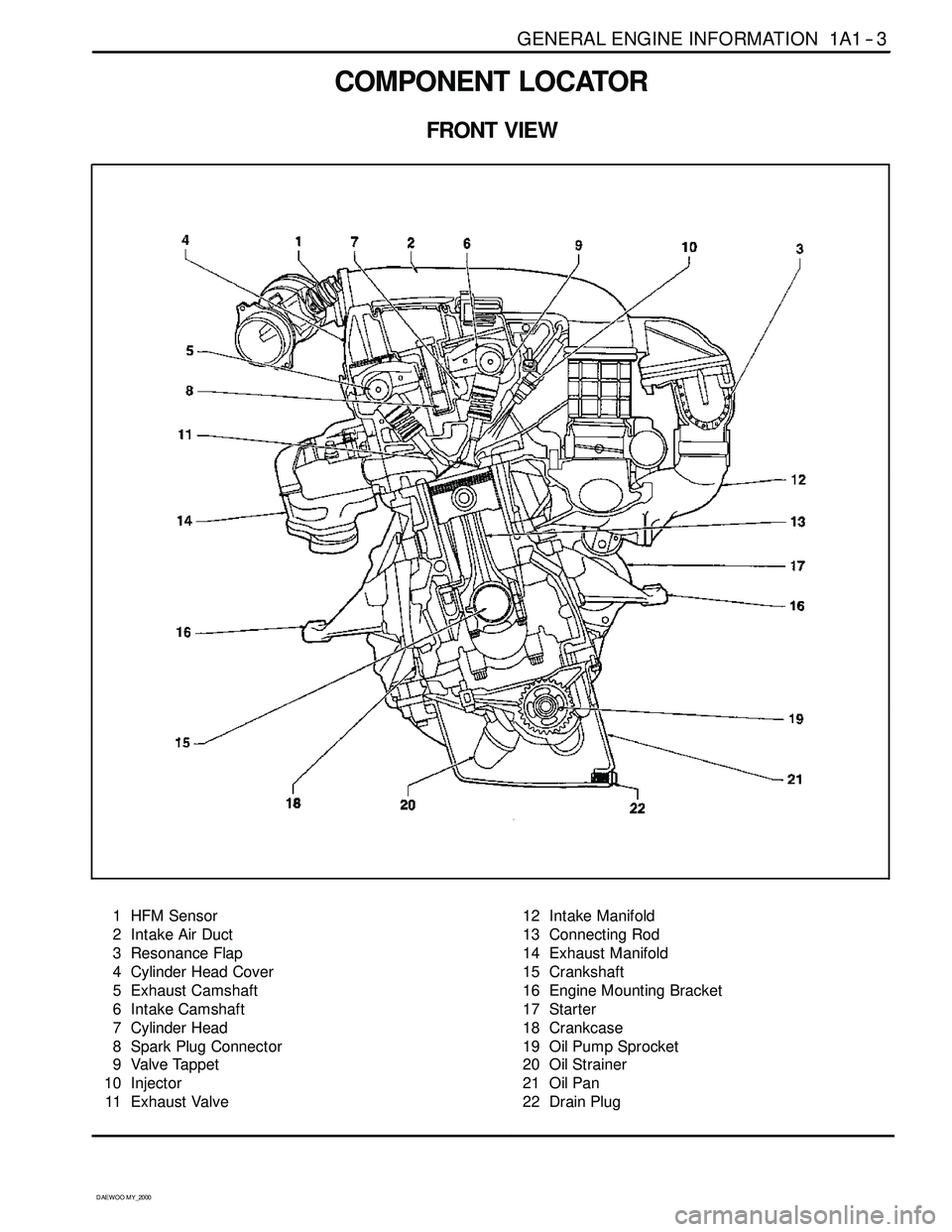
GENERAL ENGINE INFORMATION 1A1 -- 3
D AEW OO M Y_2000
COMPONENT LOCATOR
FRONT VIEW
1 HFM Sensor
2 Intake Air Duct
3 Resonance Flap
4 Cylinder Head Cover
5 Exhaust Camshaft
6 Intake Camshaft
7 Cylinder Head
8 Spark Plug Connector
9 Valve Tappet
10 Injector
11 Exhaust Valve12 Intake Manifold
13 Connecting Rod
14 Exhaust Manifold
15 Crankshaft
16 Engine Mounting Bracket
17 Starter
18 Crankcase
19 Oil Pump Sprocket
20 Oil Strainer
21 Oil Pan
22 Drain Plug
Page 24 of 2053
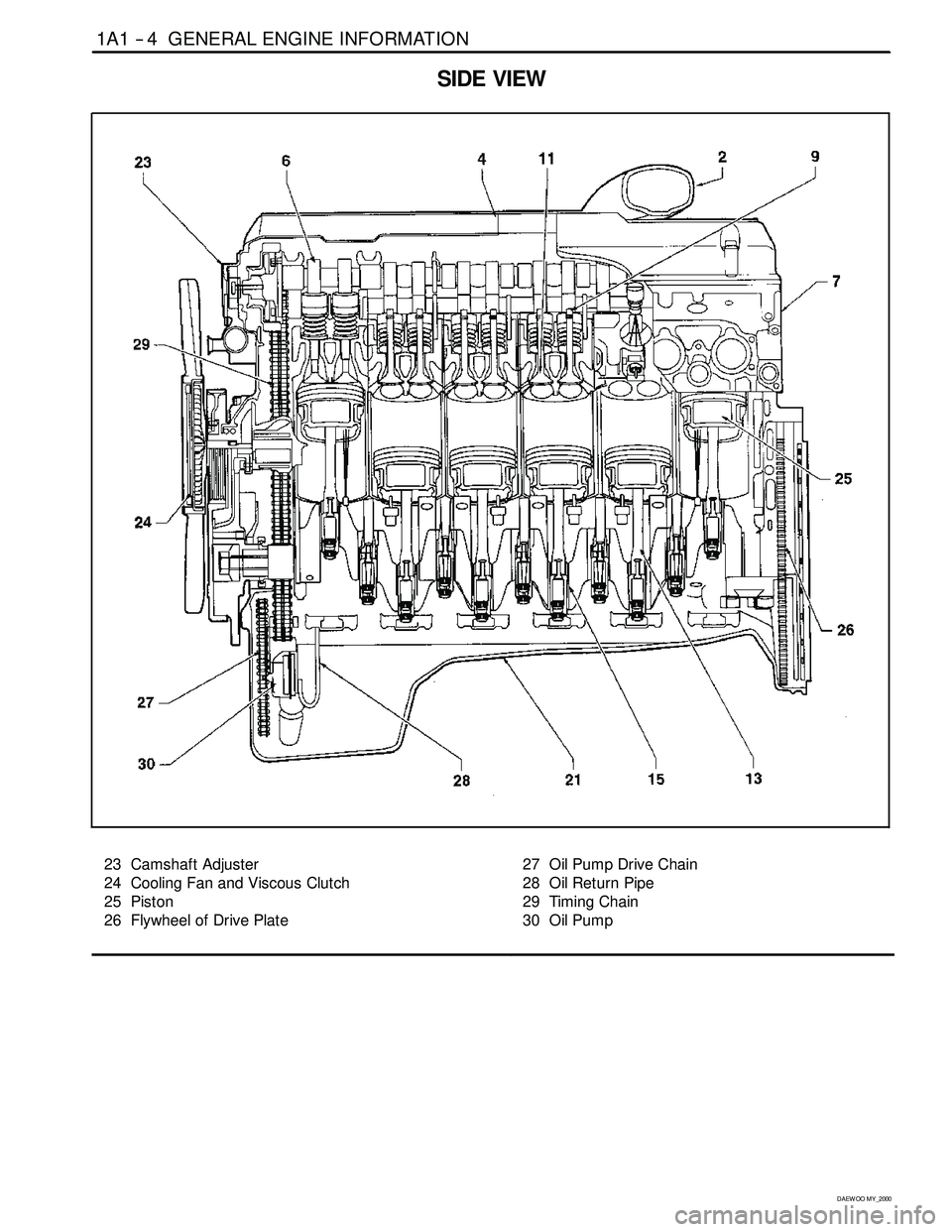
1A1 -- 4 GENERAL ENGINE INFORMATION
D AEW OO M Y_2000
SIDE VIEW
23 Camshaft Adjuster
24 Cooling Fan and Viscous Clutch
25 Piston
26 Flywheel of Drive Plate27 Oil Pump Drive Chain
28 Oil Return Pipe
29 Timing Chain
30 Oil Pump
Page 25 of 2053
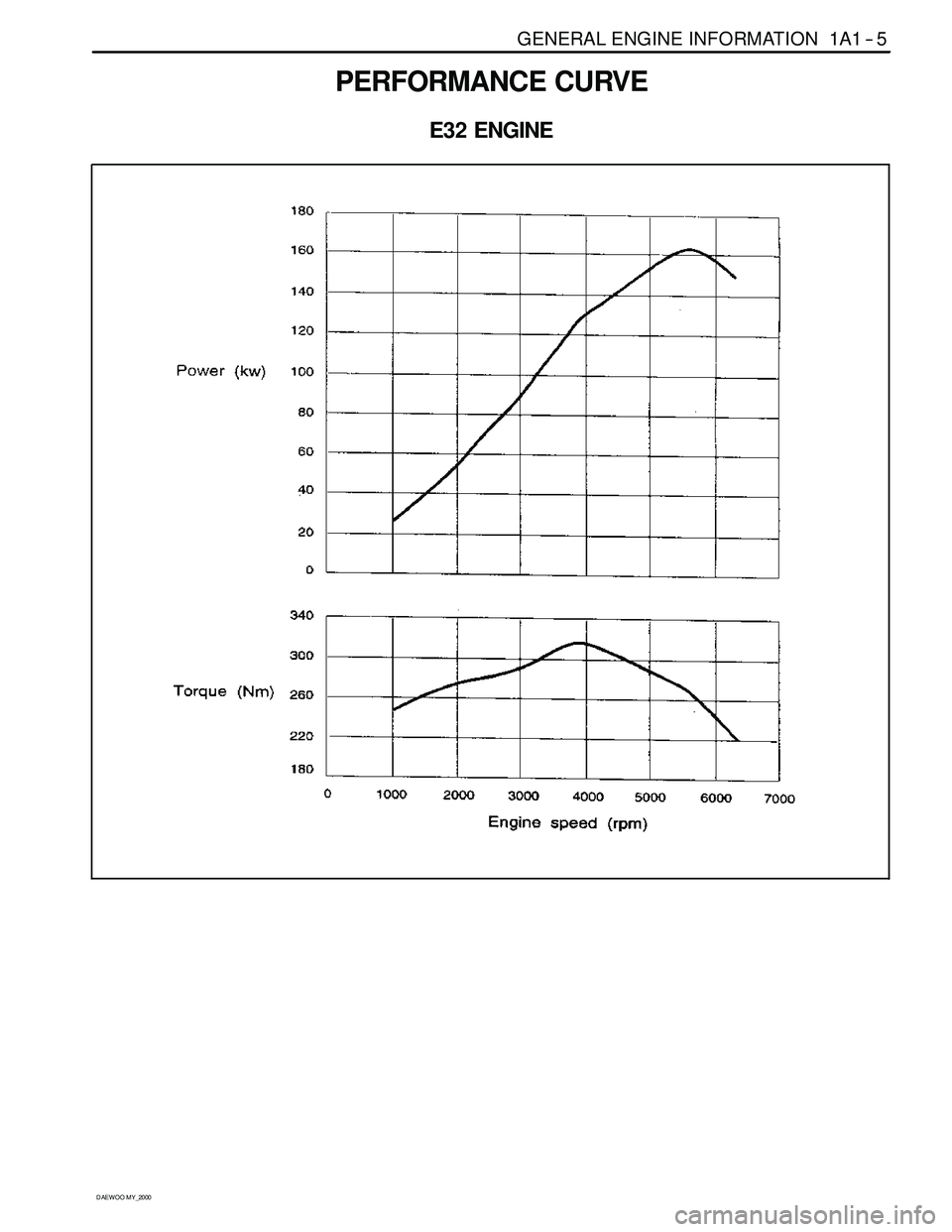
GENERAL ENGINE INFORMATION 1A1 -- 5
D AEW OO M Y_2000
PERFORMANCE CURVE
E32 ENGINE
Page 26 of 2053
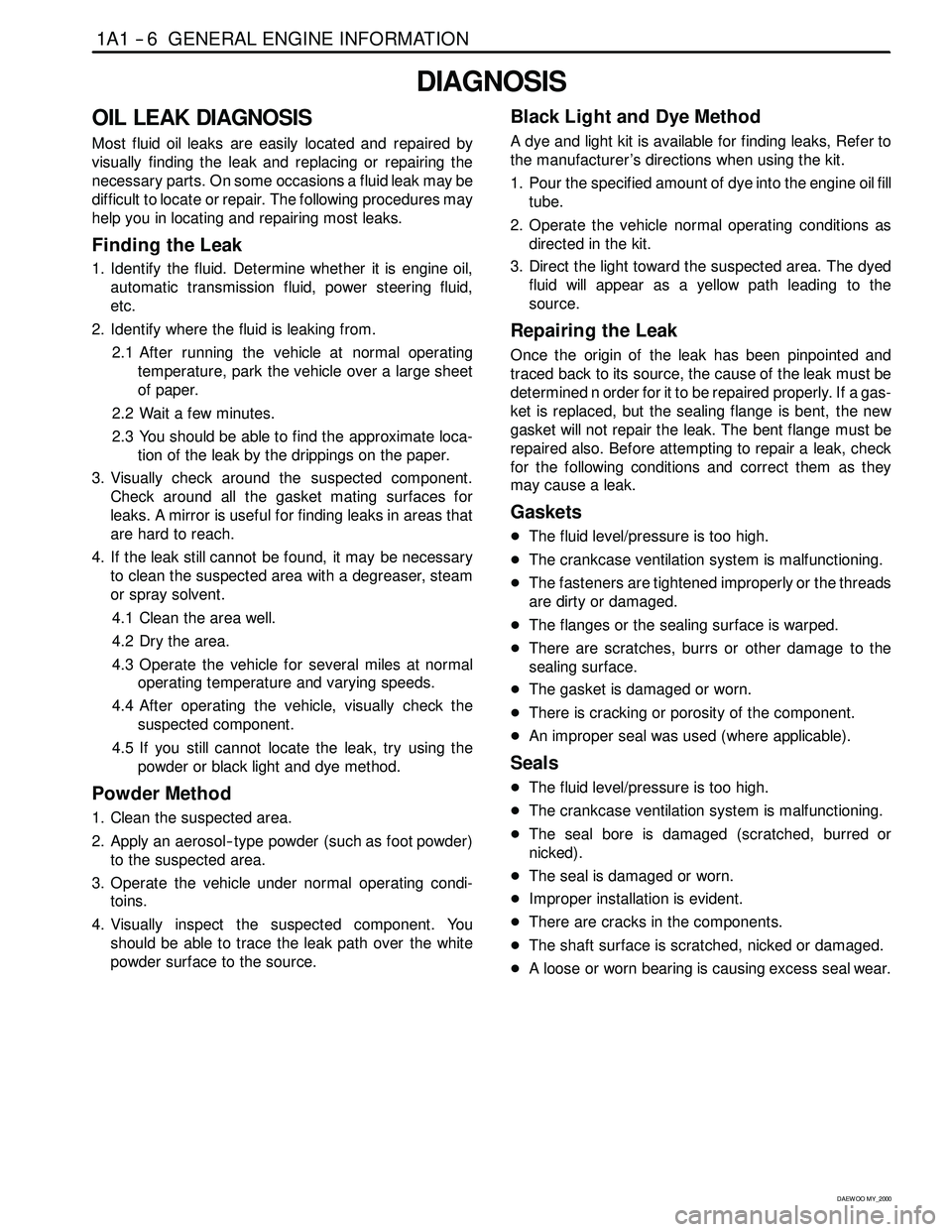
1A1 -- 6 GENERAL ENGINE INFORMATION
D AEW OO M Y_2000
DIAGNOSIS
OIL LEAK DIAGNOSIS
Most fluid oil leaks are easily located and repaired by
visually finding the leak and replacing or repairing the
necessary parts. On some occasions a fluid leak may be
difficult to locate or repair. The following procedures may
help you in locating and repairing most leaks.
Finding the Leak
1. Identify the fluid. Determine whether it is engine oil,
automatic transmission fluid, power steering fluid,
etc.
2. Identify where the fluid is leaking from.
2.1 After running the vehicle at normal operating
temperature, park the vehicle over a large sheet
of paper.
2.2 Wait a few minutes.
2.3 You should be able to find the approximate loca-
tion of the leak by the drippings on the paper.
3. Visually check around the suspected component.
Check around all the gasket mating surfaces for
leaks. A mirror is useful for finding leaks in areas that
are hard to reach.
4. If the leak still cannot be found, it may be necessary
to clean the suspected area with a degreaser, steam
or spray solvent.
4.1 Clean the area well.
4.2 Dry the area.
4.3 Operate the vehicle for several miles at normal
operating temperature and varying speeds.
4.4 After operating the vehicle, visually check the
suspected component.
4.5 If you still cannot locate the leak, try using the
powder or black light and dye method.
Powder Method
1. Clean the suspected area.
2. Apply an aerosol-- type powder (such as foot powder)
to the suspected area.
3. Operate the vehicle under normal operating condi-
toins.
4. Visually inspect the suspected component. You
should be able to trace the leak path over the white
powder surface to the source.
Black Light and Dye Method
A dye and light kit is available for finding leaks, Refer to
the manufacturer ’s directions when using the kit.
1. Pour the specified amount of dye into the engine oil fill
tube.
2. Operate the vehicle normal operating conditions as
directed in the kit.
3. Direct the light toward the suspected area. The dyed
fluid willappear as a yellow path leading to the
source.
Repairing the Leak
Once the origin of the leak has been pinpointed and
traced back to its source, the cause of the leak must be
determined n order for it to be repaired properly. If a gas-
ket is replaced, but the sealing flange is bent, the new
gasket will not repair the leak. Thebent flange must be
repaired also. Before attempting to repair a leak, check
for the following conditions and correct them as they
may cause a leak.
Gaskets
DThe fluid level/pressure is too high.
DThe crankcase ventilation system is malfunctioning.
DThe fasteners are tightened improperly or the threads
are dirty or damaged.
DThe flanges or the sealing surface is warped.
DThere are scratches, burrs or other damage to the
sealing surface.
DThe gasket is damaged or worn.
DThere is cracking or porosity of the component.
DAn improper seal was used (where applicable).
Seals
DThe fluid level/pressure is too high.
DThe crankcase ventilation system is malfunctioning.
DThe seal bore is damaged (scratched, burred or
nicked).
DThe seal is damaged or worn.
DImproper installation is evident.
DThere are cracks in the components.
DThe shaft surface is scratched, nicked or damaged.
DA loose or worn bearing is causing excess seal wear.
Page 27 of 2053
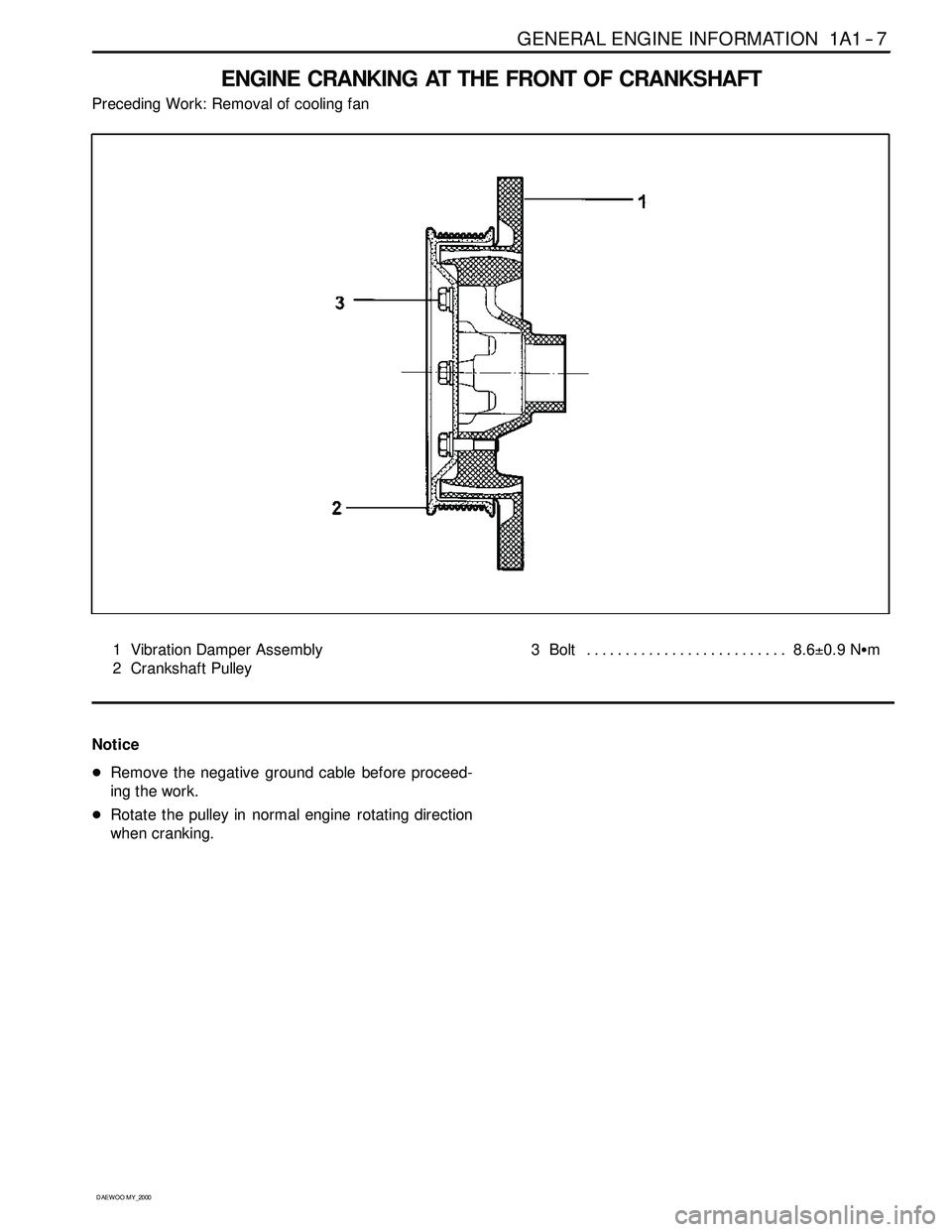
GENERAL ENGINE INFORMATION 1A1 -- 7
D AEW OO M Y_2000
ENGINE CRANKING AT THE FRONT OF CRANKSHAFT
Preceding Work: Removal of cooling fan
1 Vibration Damper Assembly
2 Crankshaft Pulley3Bolt 8.6±0.9 NSm ..........................
Notice
DRemove the negative ground cable before proceed-
ing the work.
DRotate the pulley in normal engine rotating direction
when cranking.
Page 28 of 2053
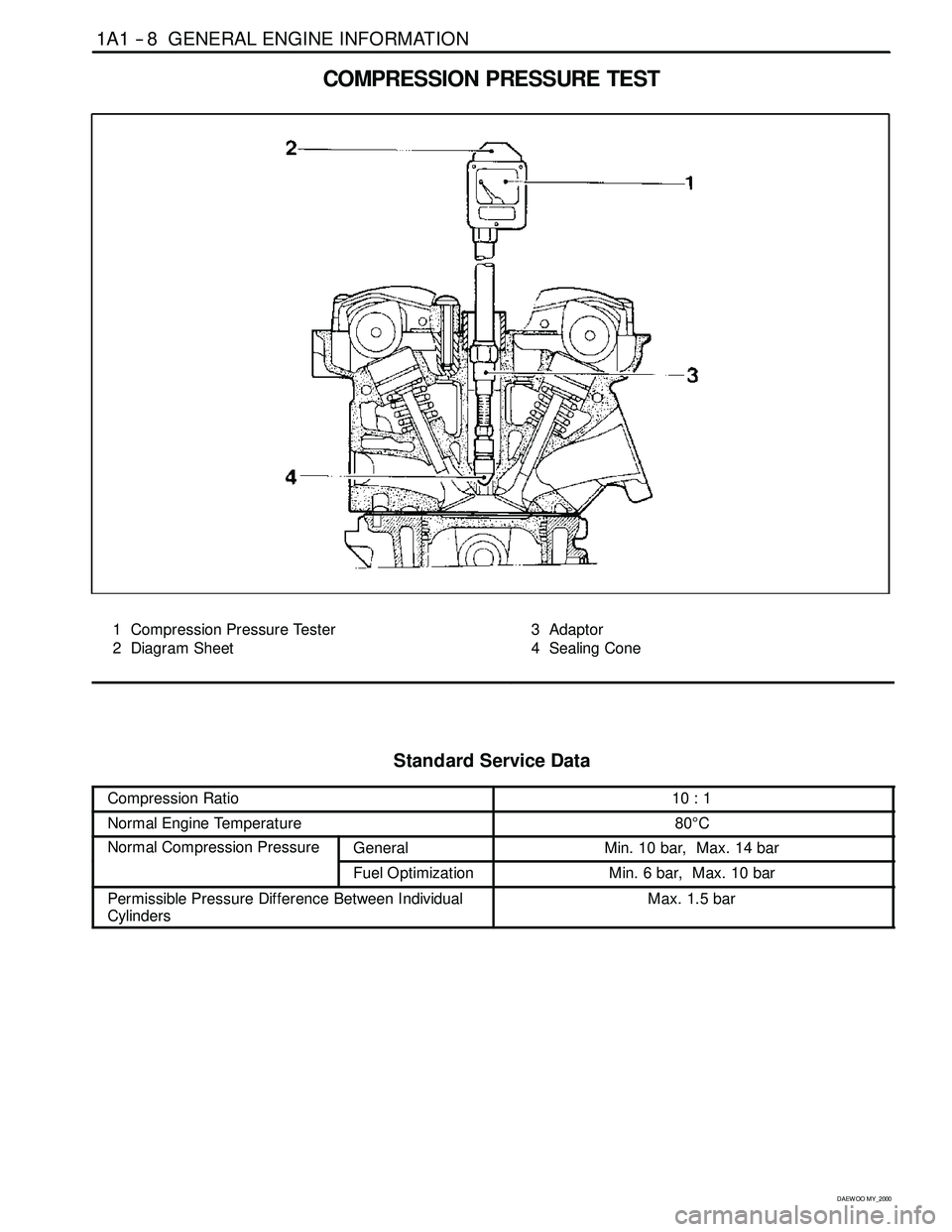
1A1 -- 8 GENERAL ENGINE INFORMATION
D AEW OO M Y_2000
COMPRESSION PRESSURE TEST
1 Compression Pressure Tester
2 Diagram Sheet3 Adaptor
4 Sealing Cone
Standard Service Data
Compression Ratio10 : 1
Normal Engine Temperature80°C
Normal Compression PressureGeneralMin. 10 bar, Max. 14 barp
Fuel OptimizationMin. 6 bar, Max. 10 bar
Permissible Pressure Difference Between Individual
CylindersMax. 1.5 bar
Page 29 of 2053
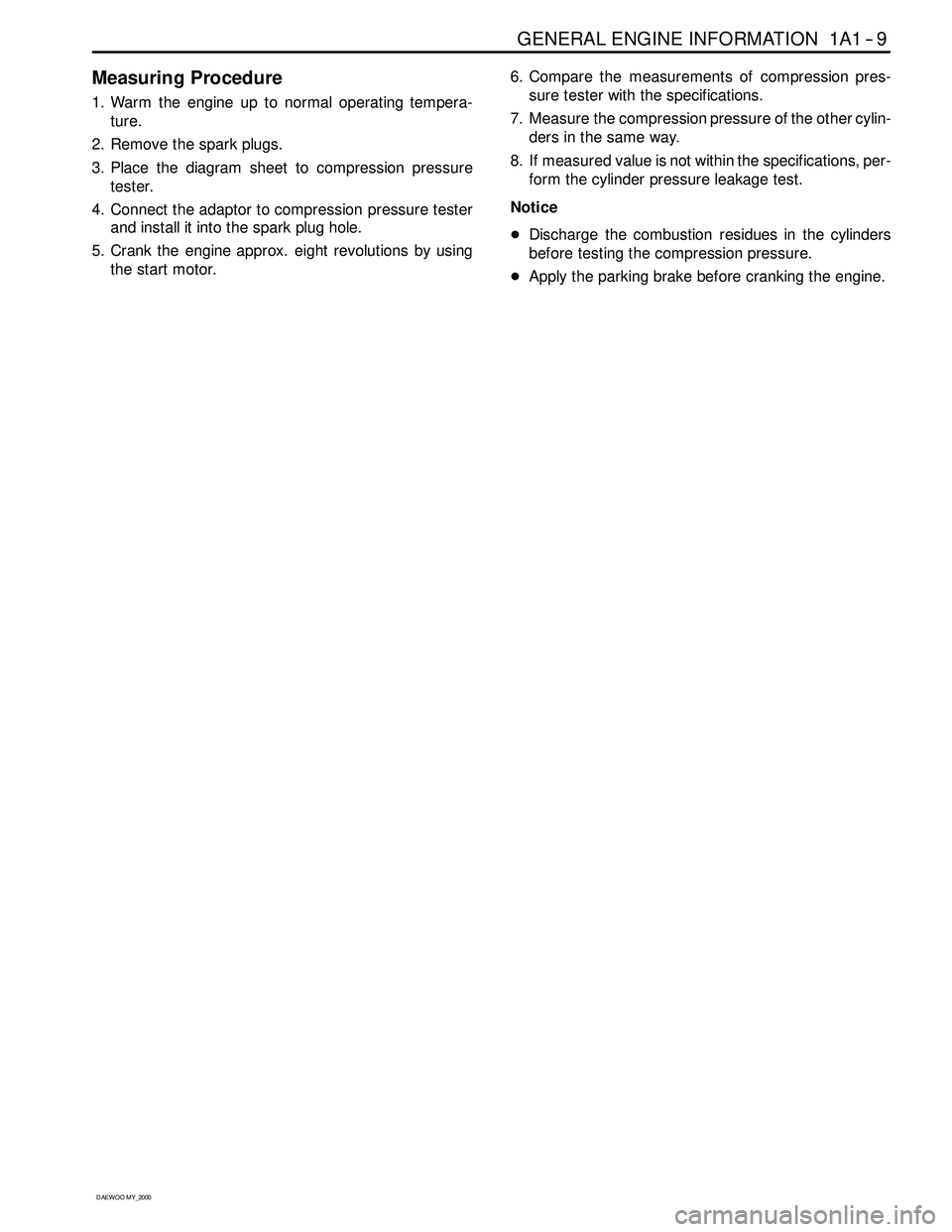
GENERAL ENGINE INFORMATION 1A1 -- 9
D AEW OO M Y_2000
Measuring Procedure
1. Warm the engine up to normal operating tempera-
ture.
2. Remove the spark plugs.
3. Place the diagram sheet to compression pressure
tester.
4. Connect the adaptor to compression pressure tester
and install it into the spark plug hole.
5. Crank the engine approx. eight revolutions by using
the start motor.6. Compare the measurements of compression pres-
sure tester with the specifications.
7. Measure the compression pressure of the other cylin-
ders in the same way.
8. If measured value is not within the specifications, per-
form the cylinder pressure leakage test.
Notice
DDischarge the combustion residues in the cylinders
before testing the compression pressure.
DApply the parking brake before cranking the engine.
Page 30 of 2053
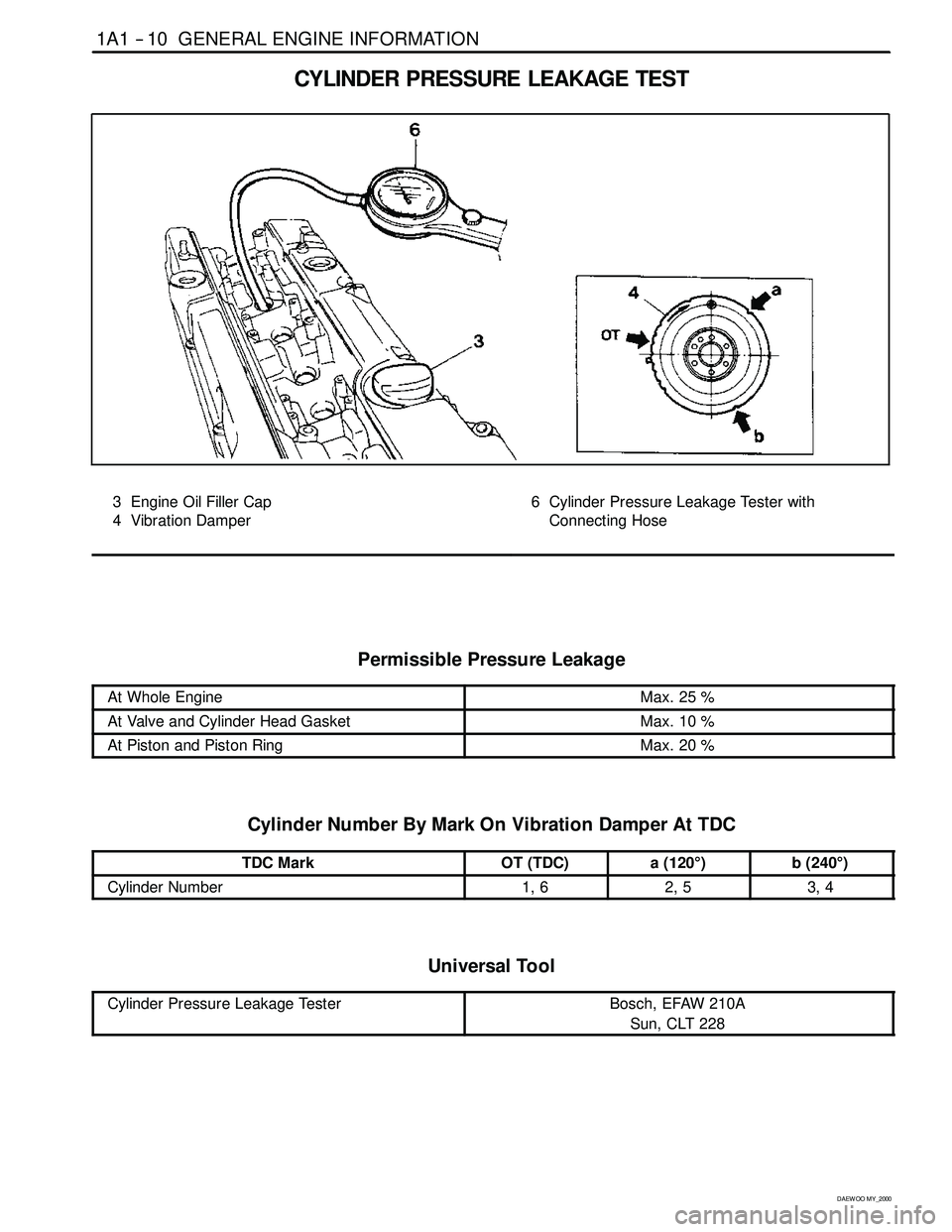
1A1 -- 10 GENERAL ENGINE INFORMATION
D AEW OO M Y_2000
CYLINDER PRESSURE LEAKAGE TEST
3 Engine Oil Filler Cap
4 Vibration Damper6 Cylinder Pressure Leakage Tester with
Connecting Hose
Permissible Pressure Leakage
At Whole EngineMax. 25 %
At Valve and Cylinder Head GasketMax. 10 %
At Piston and Piston RingMax. 20 %
Cylinder Number By Mark On Vibration Damper At TDC
TDC MarkOT (TDC)a(120°)b (240°)
Cylinder Number1, 62, 53, 4
Universal Tool
Cylinder Pressure Leakage TesterBosch, EFAW 210A
Sun, CLT 228