SSANGYONG KORANDO 1997 Service Repair Manual
KORANDO 1997
SSANGYONG
SSANGYONG
https://www.carmanualsonline.info/img/67/57502/w960_57502-0.png
SSANGYONG KORANDO 1997 Service Repair Manual
Page 730 of 2053
OM600 ENGINE MECHANICAL 1B3 -- 181
D AEW OO M Y_2000
Tools Required
102589001500 Drift
102589121500 Drift
Replacement Procedure
1. Completely drain the coolant.
2. Remove any parts which impede access.
(Example : transmission, injection pump)
3. Place the screwdriver to the deepdrawn edge of the
core plug and pull forward and then rotate 90_.
4. Pull out the core plug with pliers.
5. Thoroughly clean the sealing surface and apply Loc-
tite 241.
6. Install the new core plug by using a drift.
Drift 102 589 00 15 00 (F34)
Drift 102 589 12 15 00 (F17)
7. Install the removed parts and fill the coolant.
Notice
The adhesive must be allowed to harden for about
45 minutes before filling of coolant.
8. Warm up the engine and check the coolant for leaks.
Page 731 of 2053
1B3 -- 182 OM600 ENGINE MECHANICAL
D AEW OO M Y_2000
FACING CRANKCASE CONTACTING SURFACE
1 Crankcase
2 Crankcase Contacting Surface
Y Height (crankcase upper surface -- crankcase
lower surface)B Longitudinal Direction
C Transverse Direction
H Chamfer Height
b Chamfer Angle
Service Data
Height ’Y’Min. 299.62 mm
PermissibleunevennessofcontactingsurfaceIn longitudinal direction (B)0.06 mmPermissible unevenness of contacting surfaceIn transverse direction (C)0.06 mm
Permissible roughness upper contacting surface0.0006 -- 0.0016 mm
Permissible variation of parallelism of crankcase upper
surface to lower surface in longitudinal direction0.05 mm
PittitTDCtkfMax.0.965 mmPiston protrusion at TDC to crankcase upper surfaceMin.0.735 mm
Page 732 of 2053
OM600 ENGINE MECHANICAL 1B3 -- 183
D AEW OO M Y_2000
OIL GALLERY STEEL BALL
Preceding Work : Removal of cooling fan
Removal of the water pump housing
Removal of the flywheel and driven plate
1 Steel Ballφ15mm .........................2 Screw Plug Loctite 241, 50N∙m .............
Notice
The screw plug (2) has to be installed as a repair
solution if the steel ball (1) is leaking.
Page 733 of 2053
1B3 -- 184 OM600 ENGINE MECHANICAL
D AEW OO M Y_2000
3 Steel Ballφ17mm .........................
4 Seal5 Screw Plug 50N∙m (37 lb-ft) ................
Notice
The seal (4) and screw plug (5) have to be installed as a
repair solution if the steel ball (3) is leaking.
Tools Required
601 589 08 15 00 Drift
Page 734 of 2053
OM600 ENGINE MECHANICAL 1B3 -- 185
D AEW OO M Y_2000
Removal & Installation Procedure
1. Remove the timing case cover.
2. By inserting a round bar (6) approx. 0.7m from the
back to the front side through the oil gallery, knock
out the steel balls (1,3).
Notice
Be careful not to damage the bores of the steel
balls.
6 Shop -- made tool
3. Thoroughly clean the bores of steel balls.
4. Place the steel ball (3) onto the drift (7) with a little
grease and position to the bore and then tap until the
drift stops.
Drift 601 589 08 15 00
5. Place the steel ball (1) onto the drift (7) with a little
grease and position to the bore and then tap until the
drift stops.
Drift 601 589 08 1500
6. Warm up the engine and check the oil for leaks.
Page 735 of 2053
1B3 -- 186 OM600 ENGINE MECHANICAL
D AEW OO M Y_2000
Installation of Screw Plug
Notice
If steel ball leaks again, install the screw plug.
1. Remove the steel ball.
2. Tap thread into the bores of the oil gallery.
Notice
Front bore : M18′1.5, depth 10mm
Rear bore : M16′1.5, depth 14mm
3. Thoroughly clean the oil gallery.
4. Tighten the front plug (5) with seal (4).
Tightening Torque50 N∙m (37 lb-ft)
5. Apply Loctite 241 and then tighten the rear plug (2).
Tightening Torque50 N∙m (37 lb-ft)
Page 736 of 2053
OM600 ENGINE MECHANICAL 1B3 -- 187
D AEW OO M Y_2000
CYLINDER BORE MEASUREMENT
a Longitudinal Direction
b Transverse Direction
c, d, e. Measuring Point
1 Crankcase Contacting Surface
2 TDC of 1st Piston Ring
4 BDC of Ring
Service Data
Code letter ’A’89.000 -- 89.006mm
Standard sizeCode letter ’X’89.006 -- 89.012mmStandardsize
Code letter ’B’89.012 -- 89.018mm
WearlimitindirectionoftravelandintransversedirectionMax. 0.20mmWear limit in direction of travel and in transverse directionWhen new0.01mm
Permissible deviation of cylinder shapeWear limit0.05mm
Honing angle50_±10_
Page 737 of 2053
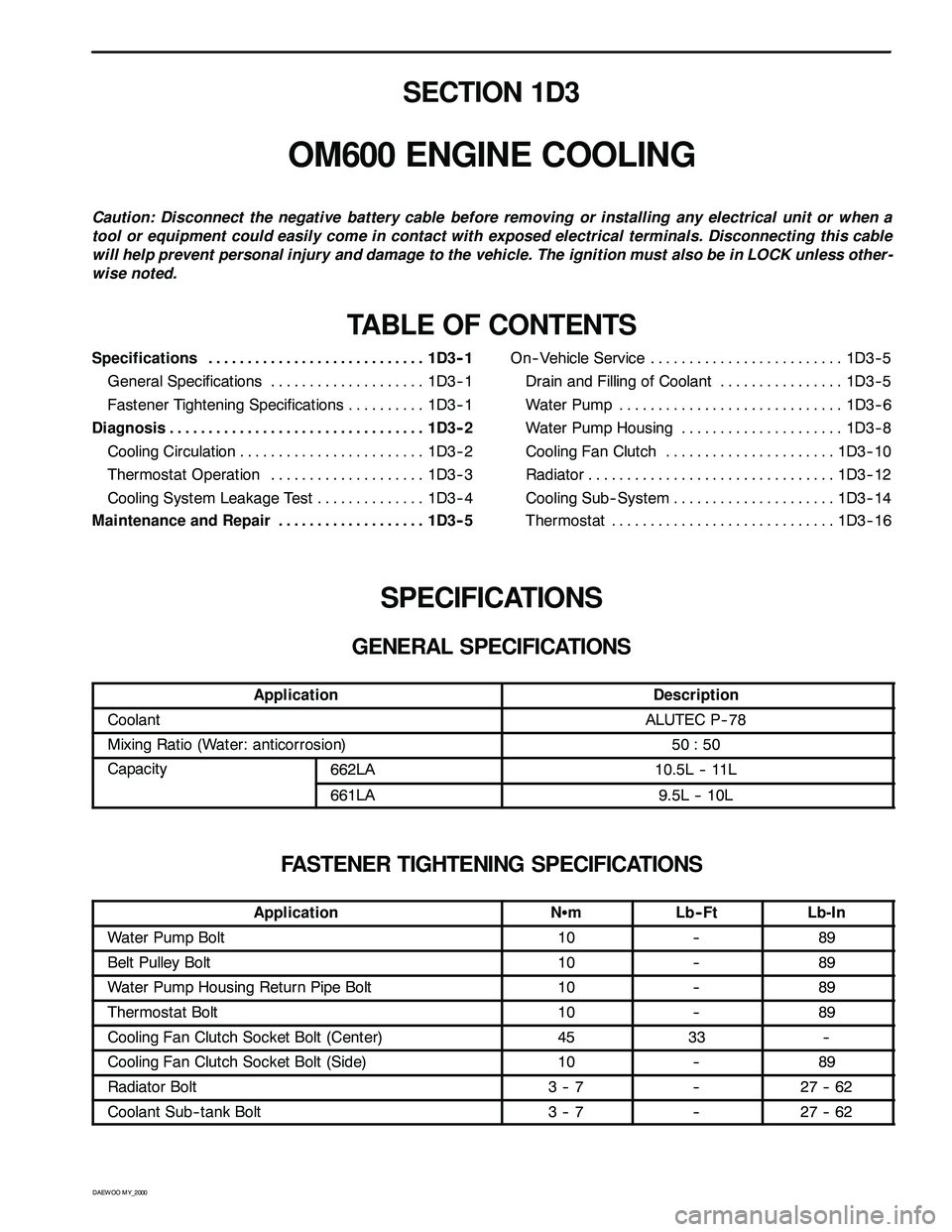
D AEW OO M Y_2000
SECTION 1D3
OM600 ENGINE COOLING
Caution: Disconnect the negative battery cable before removing or installing any electrical unit or when a
tool or equipment could easily come in contact with exposed electrical terminals. Disconnecting this cable
will help prevent personal injury and damage to the vehicle. The ignition must also be in LOCK unless other -
wise noted.
TABLE OF CONTENTS
Specifications 1D3 -- 1............................
General Specifications 1D3-- 1....................
Fastener Tightening Specifications 1D3 -- 1..........
Diagnosis 1D3 -- 2.................................
Cooling Circulation 1D3 -- 2........................
Thermostat Operation 1D3 -- 3....................
Cooling System Leakage Test 1D3-- 4..............
Maintenance and Repair 1D3 -- 5...................On-- Vehicle Service 1D3-- 5.........................
Drain and Filling of Coolant 1D3 -- 5................
Wat er Pum p 1D3 -- 6.............................
Water Pump Housing 1D3-- 8.....................
Cooling Fan Clutch 1D3 -- 10......................
Radiator 1D3-- 12................................
Cooling Sub-- System 1D3-- 14.....................
Thermostat 1D3 -- 16.............................
SPECIFICATIONS
GENERAL SPECIFICATIONS
ApplicationDescription
CoolantALUTEC P-- 78
Mixing Ratio (Water: anticorrosion)50 : 50
Capacity662LA10.5L -- 11Lpy
661LA9.5L -- 10L
FASTENER TIGHTENING SPECIFICATIONS
ApplicationNSmLb-- FtLb-In
Water Pump Bolt10--89
Belt Pulley Bolt10--89
Water Pump Housing Return Pipe Bolt10--89
Thermostat Bolt10--89
Cooling Fan Clutch Socket Bolt (Center)4533--
Cooling Fan Clutch Socket Bolt (Side)10--89
Radiator Bolt3--7--27 -- 62
Coolant Sub-- tank Bolt3--7--27 -- 62
Page 738 of 2053
1D3 -- 2 OM600 ENGINE COOLING
D AEW OO M Y_2000
DIAGNOSIS
COOLING CIRCULATION
A Thermostat
B Radiator
D From Heater
EHoseG Deaeration Line
HReservoir
Page 739 of 2053
1D3 -- 4 OM600 ENGINE COOLING
D AEW OO M Y_2000
COOLING SYSTEM LEAKAGE TEST
Tools Required
124589152100Tester
Test
1. Loosen the pressure cap by 1 notch and remove the
cap after.
Notice
Do not remove radiator cap when coolant is above
90°C.
2. Add the coolant to the arrow mark of coolant reser-
voir.
3. Connect the special tool to the injector of reservoir
and apply 1.4bar pressure.
Tester 124 589 15 21 00
4. If the pressure on the tester drops, check the hose,
pipe and leakage and, replace or retighten.