SUBARU LEGACY 1999 Service Repair Manual
Manufacturer: SUBARU, Model Year: 1999, Model line: LEGACY, Model: SUBARU LEGACY 1999Pages: 1456, PDF Size: 59.93 MB
Page 801 of 1456
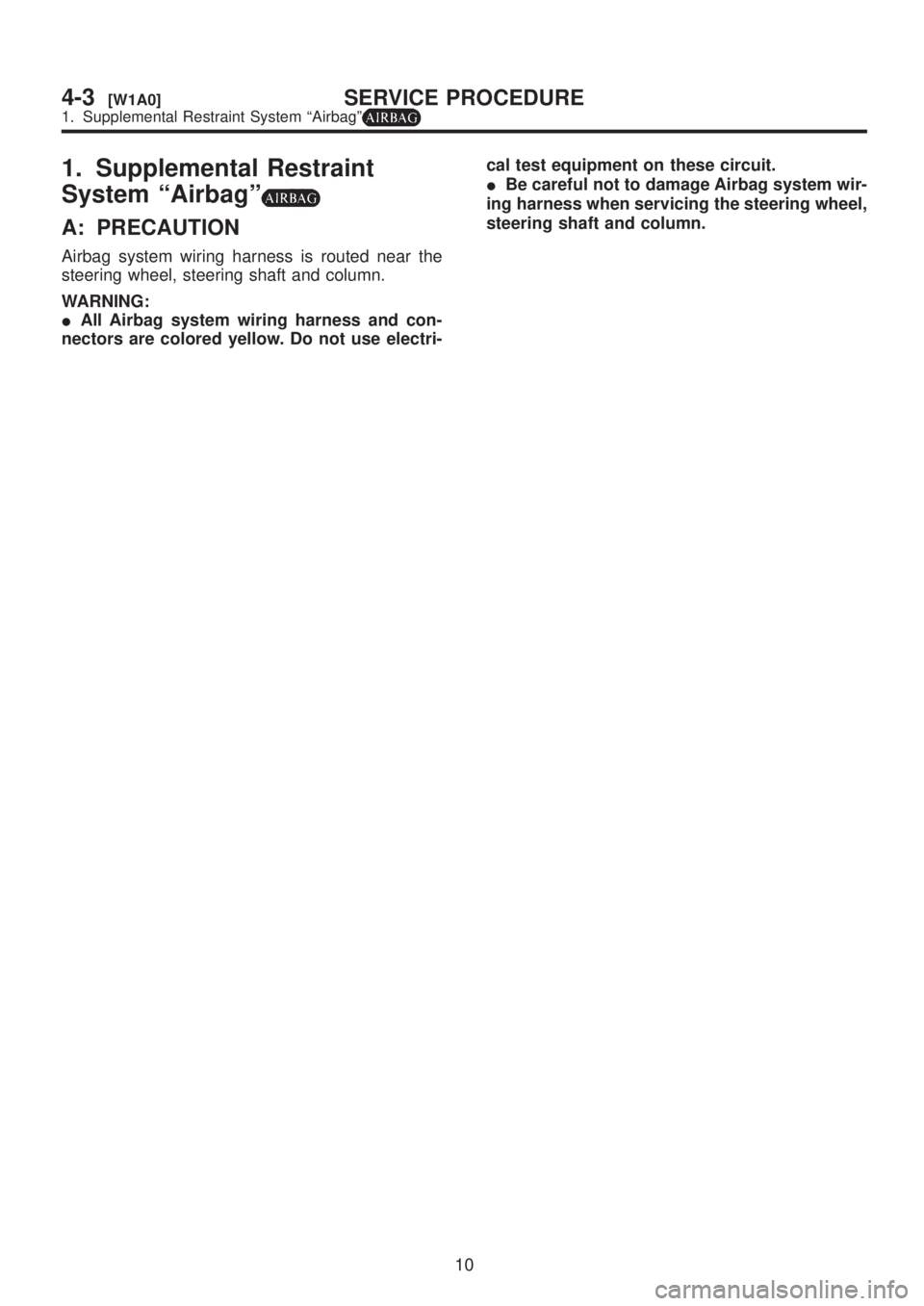
1. Supplemental Restraint
System ªAirbagº
A: PRECAUTION
Airbag system wiring harness is routed near the
steering wheel, steering shaft and column.
WARNING:
IAll Airbag system wiring harness and con-
nectors are colored yellow. Do not use electri-cal test equipment on these circuit.
IBe careful not to damage Airbag system wir-
ing harness when servicing the steering wheel,
steering shaft and column.
10
4-3[W1A0]SERVICE PROCEDURE
1. Supplemental Restraint System ªAirbagº
Page 802 of 1456
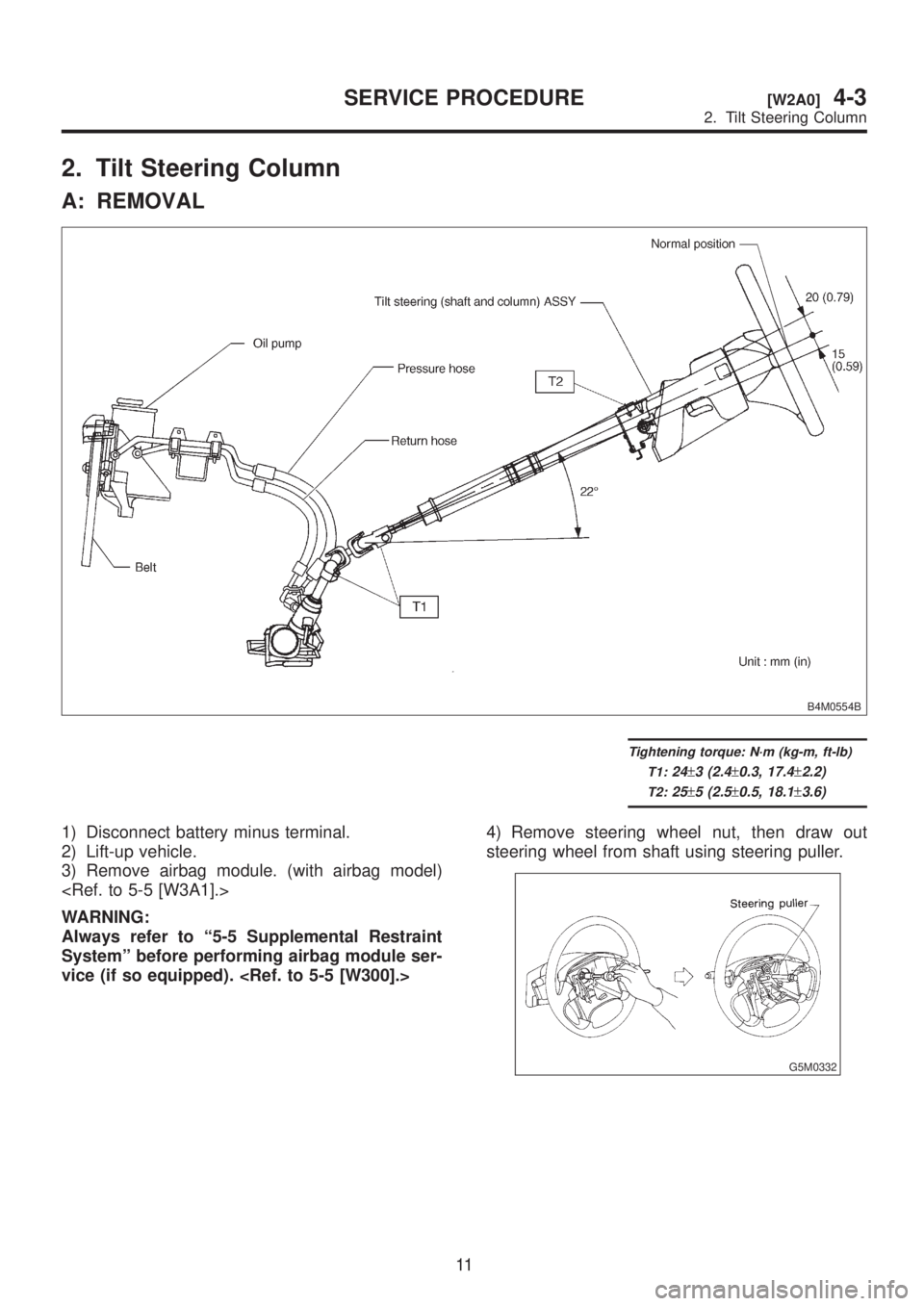
2. Tilt Steering Column
A: REMOVAL
B4M0554B
Tightening torque: N´m (kg-m, ft-lb)
T1:
24±3 (2.4±0.3, 17.4±2.2)
T2:25±5 (2.5±0.5, 18.1±3.6)
1) Disconnect battery minus terminal.
2) Lift-up vehicle.
3) Remove airbag module. (with airbag model)
WARNING:
Always refer to ª5-5 Supplemental Restraint
Systemº before performing airbag module ser-
vice (if so equipped).
steering wheel from shaft using steering puller.
G5M0332
11
[W2A0]4-3SERVICE PROCEDURE
2. Tilt Steering Column
Page 803 of 1456
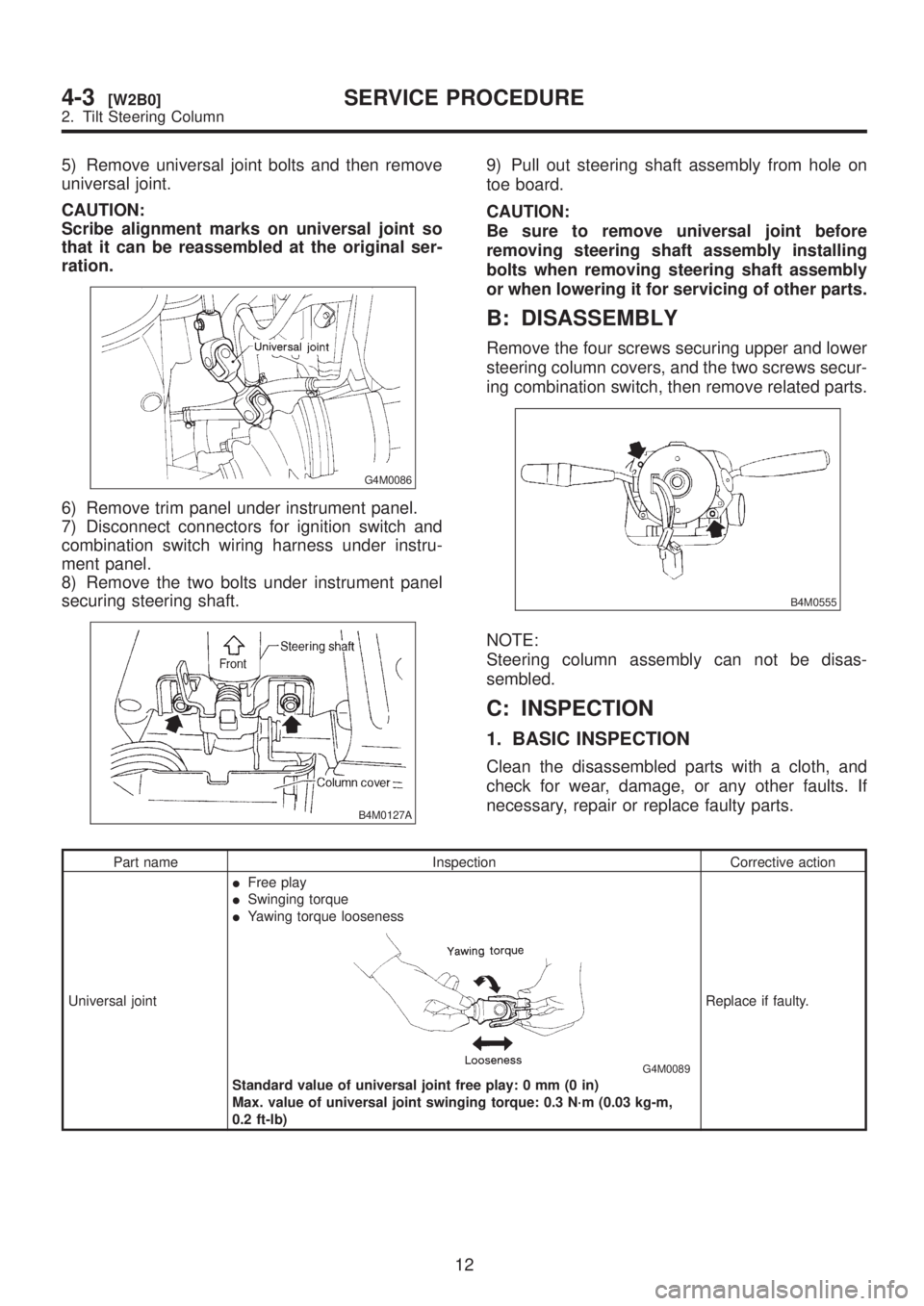
5) Remove universal joint bolts and then remove
universal joint.
CAUTION:
Scribe alignment marks on universal joint so
that it can be reassembled at the original ser-
ration.
G4M0086
6) Remove trim panel under instrument panel.
7) Disconnect connectors for ignition switch and
combination switch wiring harness under instru-
ment panel.
8) Remove the two bolts under instrument panel
securing steering shaft.
B4M0127A
9) Pull out steering shaft assembly from hole on
toe board.
CAUTION:
Be sure to remove universal joint before
removing steering shaft assembly installing
bolts when removing steering shaft assembly
or when lowering it for servicing of other parts.
B: DISASSEMBLY
Remove the four screws securing upper and lower
steering column covers, and the two screws secur-
ing combination switch, then remove related parts.
B4M0555
NOTE:
Steering column assembly can not be disas-
sembled.
C: INSPECTION
1. BASIC INSPECTION
Clean the disassembled parts with a cloth, and
check for wear, damage, or any other faults. If
necessary, repair or replace faulty parts.
Part name Inspection Corrective action
Universal jointIFree play
ISwinging torque
IYawing torque looseness
G4M0089
Standard value of universal joint free play: 0 mm (0 in)
Max. value of universal joint swinging torque: 0.3 N´m (0.03 kg-m,
0.2 ft-lb)Replace if faulty.
12
4-3[W2B0]SERVICE PROCEDURE
2. Tilt Steering Column
Page 804 of 1456
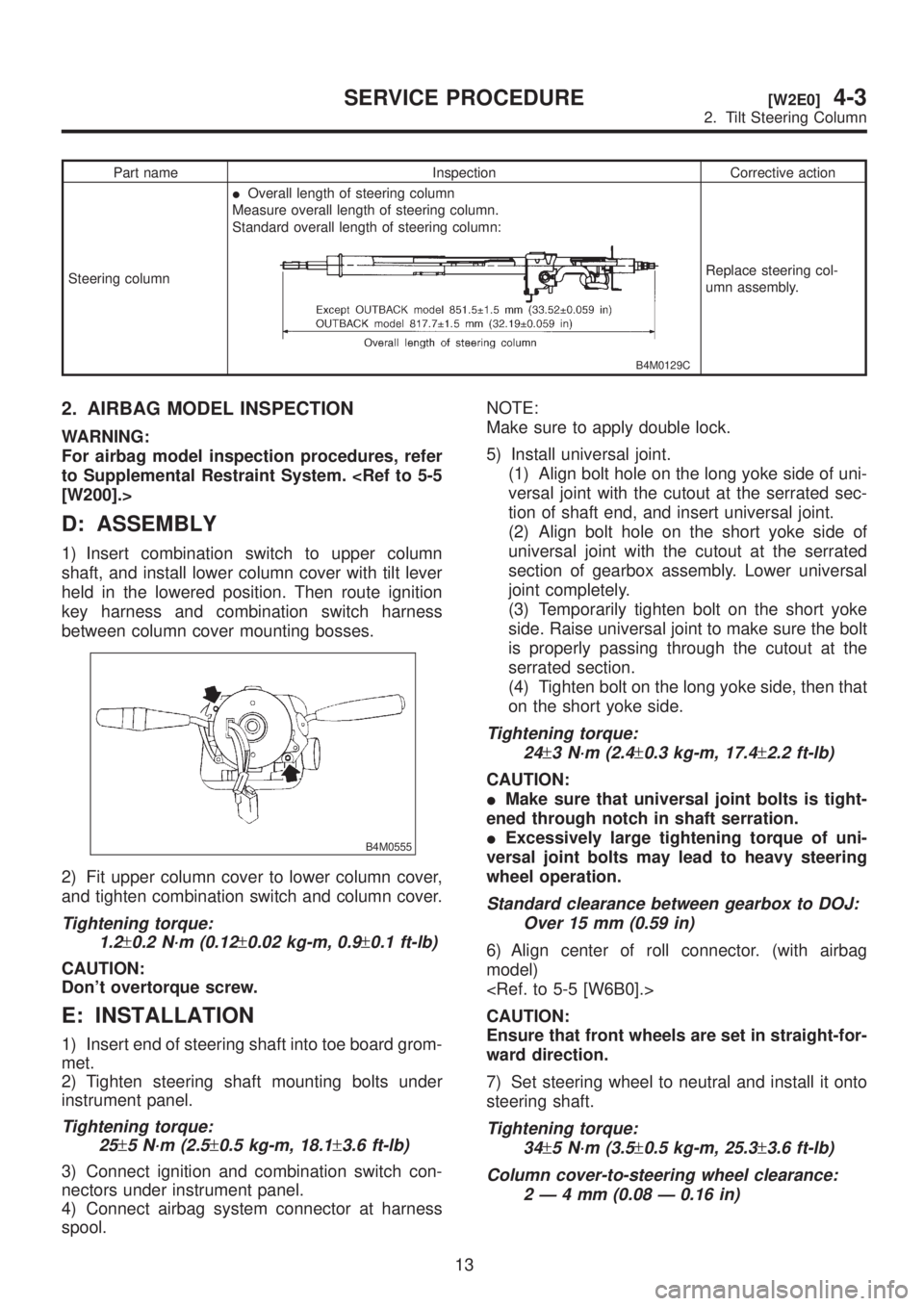
Part name Inspection Corrective action
Steering columnIOverall length of steering column
Measure overall length of steering column.
Standard overall length of steering column:
B4M0129C
Replace steering col-
umn assembly.
2. AIRBAG MODEL INSPECTION
WARNING:
For airbag model inspection procedures, refer
to Supplemental Restraint System.
[W200].>
D: ASSEMBLY
1) Insert combination switch to upper column
shaft, and install lower column cover with tilt lever
held in the lowered position. Then route ignition
key harness and combination switch harness
between column cover mounting bosses.
B4M0555
2) Fit upper column cover to lower column cover,
and tighten combination switch and column cover.
Tightening torque:
1.2
±0.2 N´m (0.12±0.02 kg-m, 0.9±0.1 ft-lb)
CAUTION:
Don't overtorque screw.
E: INSTALLATION
1) Insert end of steering shaft into toe board grom-
met.
2) Tighten steering shaft mounting bolts under
instrument panel.
Tightening torque:
25
±5 N´m (2.5±0.5 kg-m, 18.1±3.6 ft-lb)
3) Connect ignition and combination switch con-
nectors under instrument panel.
4) Connect airbag system connector at harness
spool.NOTE:
Make sure to apply double lock.
5) Install universal joint.
(1) Align bolt hole on the long yoke side of uni-
versal joint with the cutout at the serrated sec-
tion of shaft end, and insert universal joint.
(2) Align bolt hole on the short yoke side of
universal joint with the cutout at the serrated
section of gearbox assembly. Lower universal
joint completely.
(3) Temporarily tighten bolt on the short yoke
side. Raise universal joint to make sure the bolt
is properly passing through the cutout at the
serrated section.
(4) Tighten bolt on the long yoke side, then that
on the short yoke side.
Tightening torque:
24
±3 N´m (2.4±0.3 kg-m, 17.4±2.2 ft-lb)
CAUTION:
IMake sure that universal joint bolts is tight-
ened through notch in shaft serration.
IExcessively large tightening torque of uni-
versal joint bolts may lead to heavy steering
wheel operation.
Standard clearance between gearbox to DOJ:
Over 15 mm (0.59 in)
6) Align center of roll connector. (with airbag
model)
CAUTION:
Ensure that front wheels are set in straight-for-
ward direction.
7) Set steering wheel to neutral and install it onto
steering shaft.
Tightening torque:
34
±5 N´m (3.5±0.5 kg-m, 25.3±3.6 ft-lb)
Column cover-to-steering wheel clearance:
2Ð4mm(0.08 Ð 0.16 in)
13
[W2E0]4-3SERVICE PROCEDURE
2. Tilt Steering Column
Page 805 of 1456
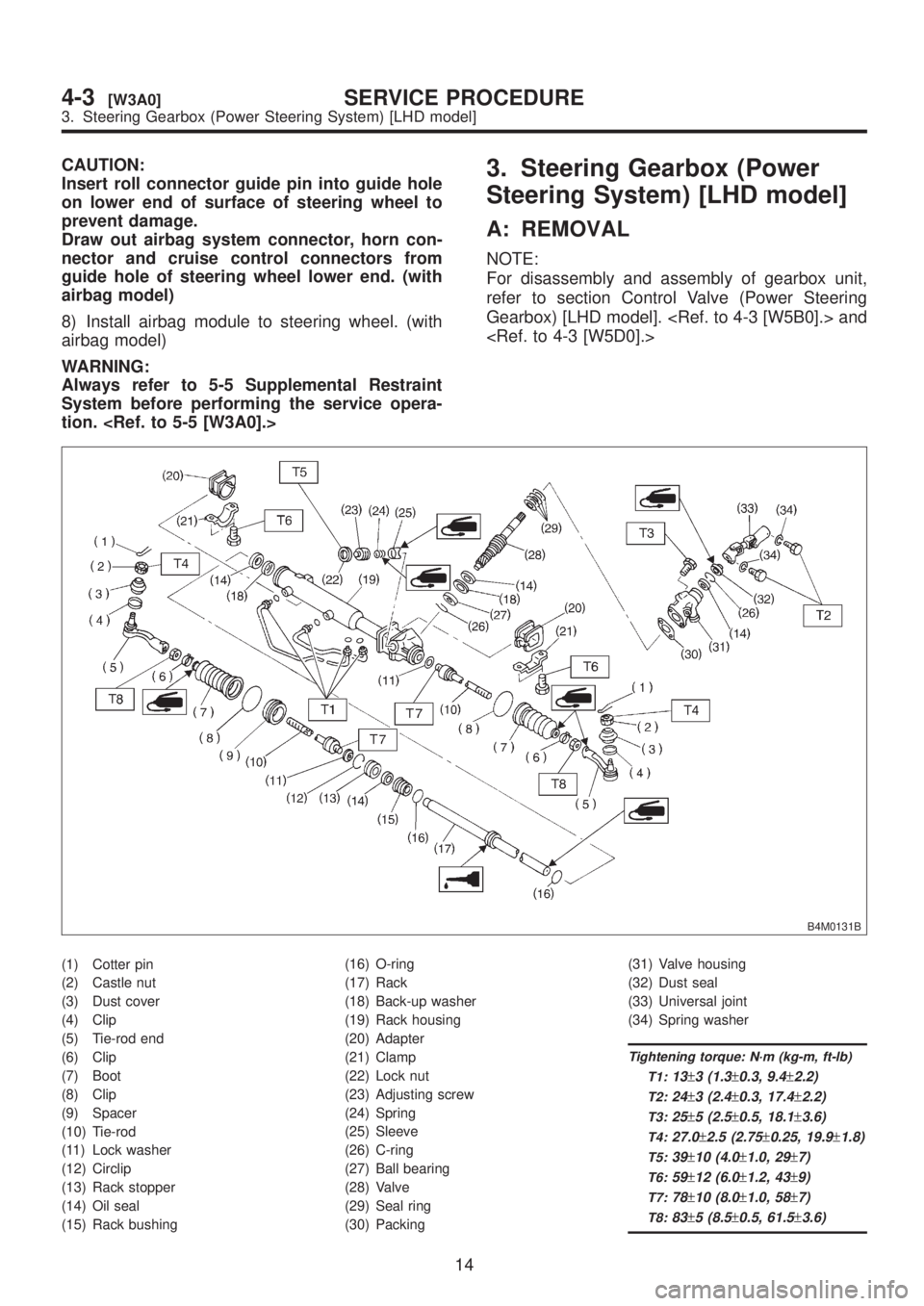
CAUTION:
Insert roll connector guide pin into guide hole
on lower end of surface of steering wheel to
prevent damage.
Draw out airbag system connector, horn con-
nector and cruise control connectors from
guide hole of steering wheel lower end. (with
airbag model)
8) Install airbag module to steering wheel. (with
airbag model)
WARNING:
Always refer to 5-5 Supplemental Restraint
System before performing the service opera-
tion.
Steering System) [LHD model]
A: REMOVAL
NOTE:
For disassembly and assembly of gearbox unit,
refer to section Control Valve (Power Steering
Gearbox) [LHD model].
B4M0131B
(1) Cotter pin
(2) Castle nut
(3) Dust cover
(4) Clip
(5) Tie-rod end
(6) Clip
(7) Boot
(8) Clip
(9) Spacer
(10) Tie-rod
(11) Lock washer
(12) Circlip
(13) Rack stopper
(14) Oil seal
(15) Rack bushing(16) O-ring
(17) Rack
(18) Back-up washer
(19) Rack housing
(20) Adapter
(21) Clamp
(22) Lock nut
(23) Adjusting screw
(24) Spring
(25) Sleeve
(26) C-ring
(27) Ball bearing
(28) Valve
(29) Seal ring
(30) Packing(31) Valve housing
(32) Dust seal
(33) Universal joint
(34) Spring washer
Tightening torque: N´m (kg-m, ft-lb)
T1:
13±3 (1.3±0.3, 9.4±2.2)
T2:24±3 (2.4±0.3, 17.4±2.2)
T3:25±5 (2.5±0.5, 18.1±3.6)
T4:27.0±2.5 (2.75±0.25, 19.9±1.8)
T5:39±10 (4.0±1.0, 29±7)
T6:59±12 (6.0±1.2, 43±9)
T7:78±10 (8.0±1.0, 58±7)
T8:83±5 (8.5±0.5, 61.5±3.6)
14
4-3[W3A0]SERVICE PROCEDURE
3. Steering Gearbox (Power Steering System) [LHD model]
Page 806 of 1456
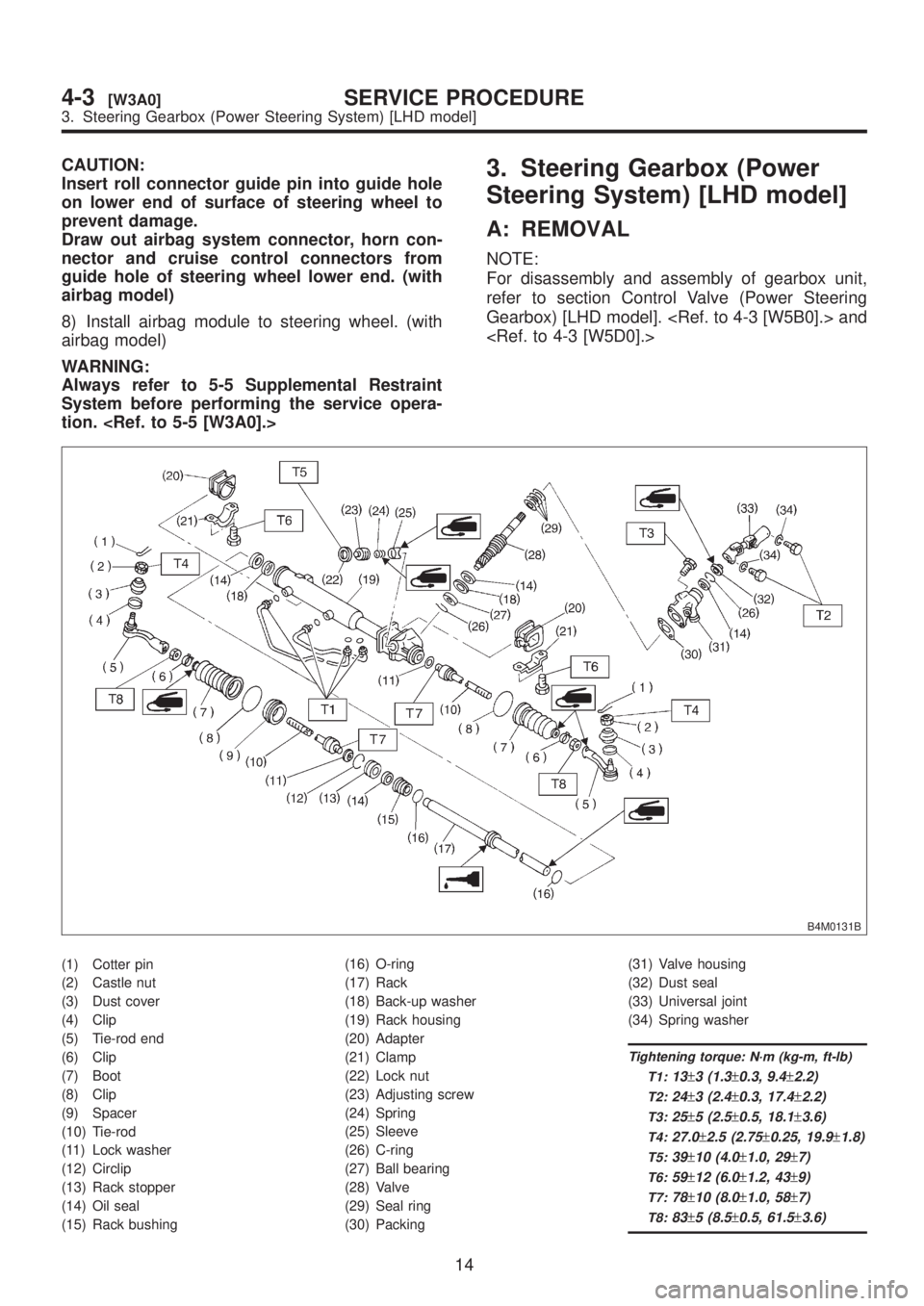
CAUTION:
Insert roll connector guide pin into guide hole
on lower end of surface of steering wheel to
prevent damage.
Draw out airbag system connector, horn con-
nector and cruise control connectors from
guide hole of steering wheel lower end. (with
airbag model)
8) Install airbag module to steering wheel. (with
airbag model)
WARNING:
Always refer to 5-5 Supplemental Restraint
System before performing the service opera-
tion.
Steering System) [LHD model]
A: REMOVAL
NOTE:
For disassembly and assembly of gearbox unit,
refer to section Control Valve (Power Steering
Gearbox) [LHD model].
B4M0131B
(1) Cotter pin
(2) Castle nut
(3) Dust cover
(4) Clip
(5) Tie-rod end
(6) Clip
(7) Boot
(8) Clip
(9) Spacer
(10) Tie-rod
(11) Lock washer
(12) Circlip
(13) Rack stopper
(14) Oil seal
(15) Rack bushing(16) O-ring
(17) Rack
(18) Back-up washer
(19) Rack housing
(20) Adapter
(21) Clamp
(22) Lock nut
(23) Adjusting screw
(24) Spring
(25) Sleeve
(26) C-ring
(27) Ball bearing
(28) Valve
(29) Seal ring
(30) Packing(31) Valve housing
(32) Dust seal
(33) Universal joint
(34) Spring washer
Tightening torque: N´m (kg-m, ft-lb)
T1:
13±3 (1.3±0.3, 9.4±2.2)
T2:24±3 (2.4±0.3, 17.4±2.2)
T3:25±5 (2.5±0.5, 18.1±3.6)
T4:27.0±2.5 (2.75±0.25, 19.9±1.8)
T5:39±10 (4.0±1.0, 29±7)
T6:59±12 (6.0±1.2, 43±9)
T7:78±10 (8.0±1.0, 58±7)
T8:83±5 (8.5±0.5, 61.5±3.6)
14
4-3[W3A0]SERVICE PROCEDURE
3. Steering Gearbox (Power Steering System) [LHD model]
Page 807 of 1456
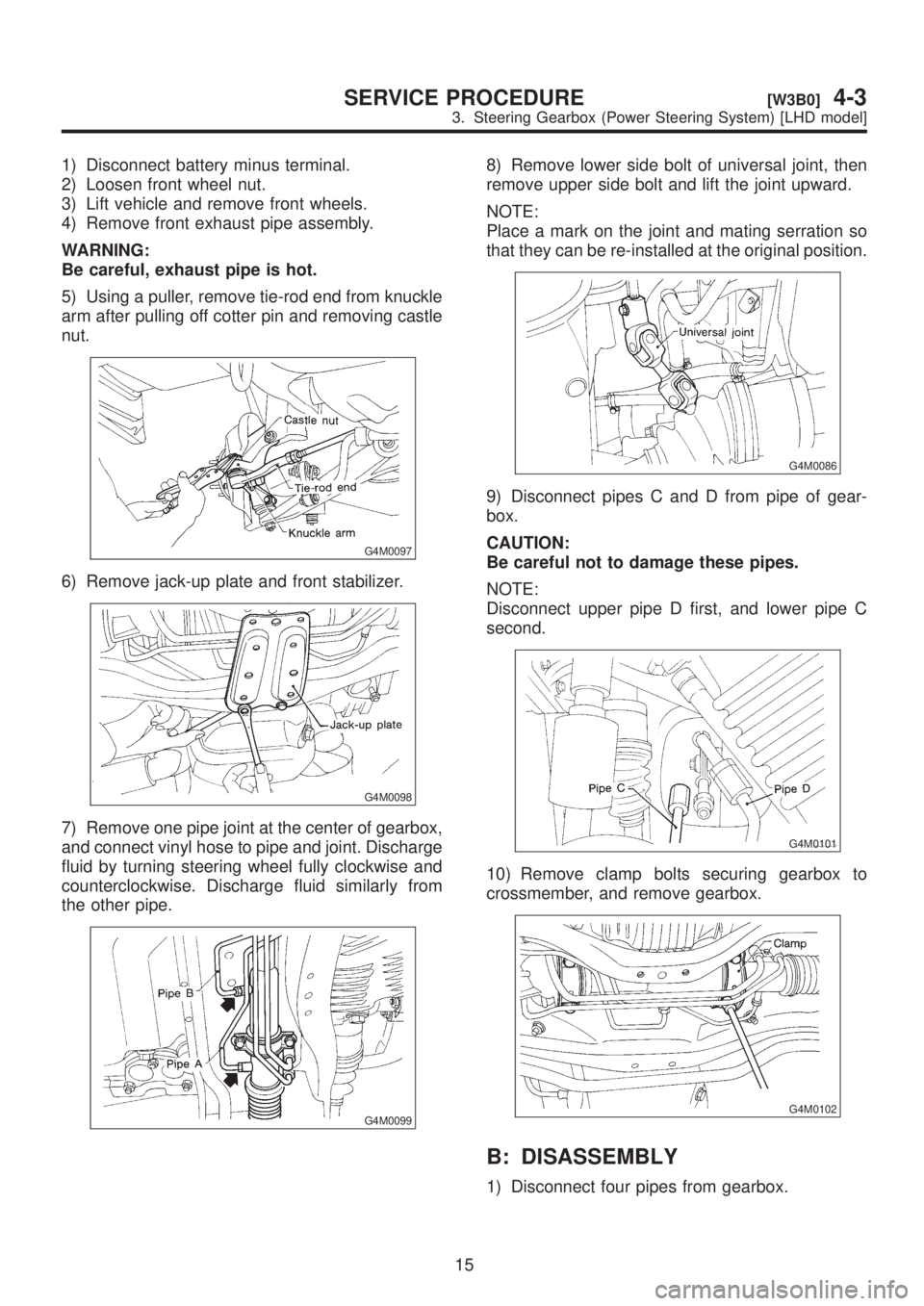
1) Disconnect battery minus terminal.
2) Loosen front wheel nut.
3) Lift vehicle and remove front wheels.
4) Remove front exhaust pipe assembly.
WARNING:
Be careful, exhaust pipe is hot.
5) Using a puller, remove tie-rod end from knuckle
arm after pulling off cotter pin and removing castle
nut.
G4M0097
6) Remove jack-up plate and front stabilizer.
G4M0098
7) Remove one pipe joint at the center of gearbox,
and connect vinyl hose to pipe and joint. Discharge
fluid by turning steering wheel fully clockwise and
counterclockwise. Discharge fluid similarly from
the other pipe.
G4M0099
8) Remove lower side bolt of universal joint, then
remove upper side bolt and lift the joint upward.
NOTE:
Place a mark on the joint and mating serration so
that they can be re-installed at the original position.
G4M0086
9) Disconnect pipes C and D from pipe of gear-
box.
CAUTION:
Be careful not to damage these pipes.
NOTE:
Disconnect upper pipe D first, and lower pipe C
second.
G4M0101
10) Remove clamp bolts securing gearbox to
crossmember, and remove gearbox.
G4M0102
B: DISASSEMBLY
1) Disconnect four pipes from gearbox.
15
[W3B0]4-3SERVICE PROCEDURE
3. Steering Gearbox (Power Steering System) [LHD model]
Page 808 of 1456
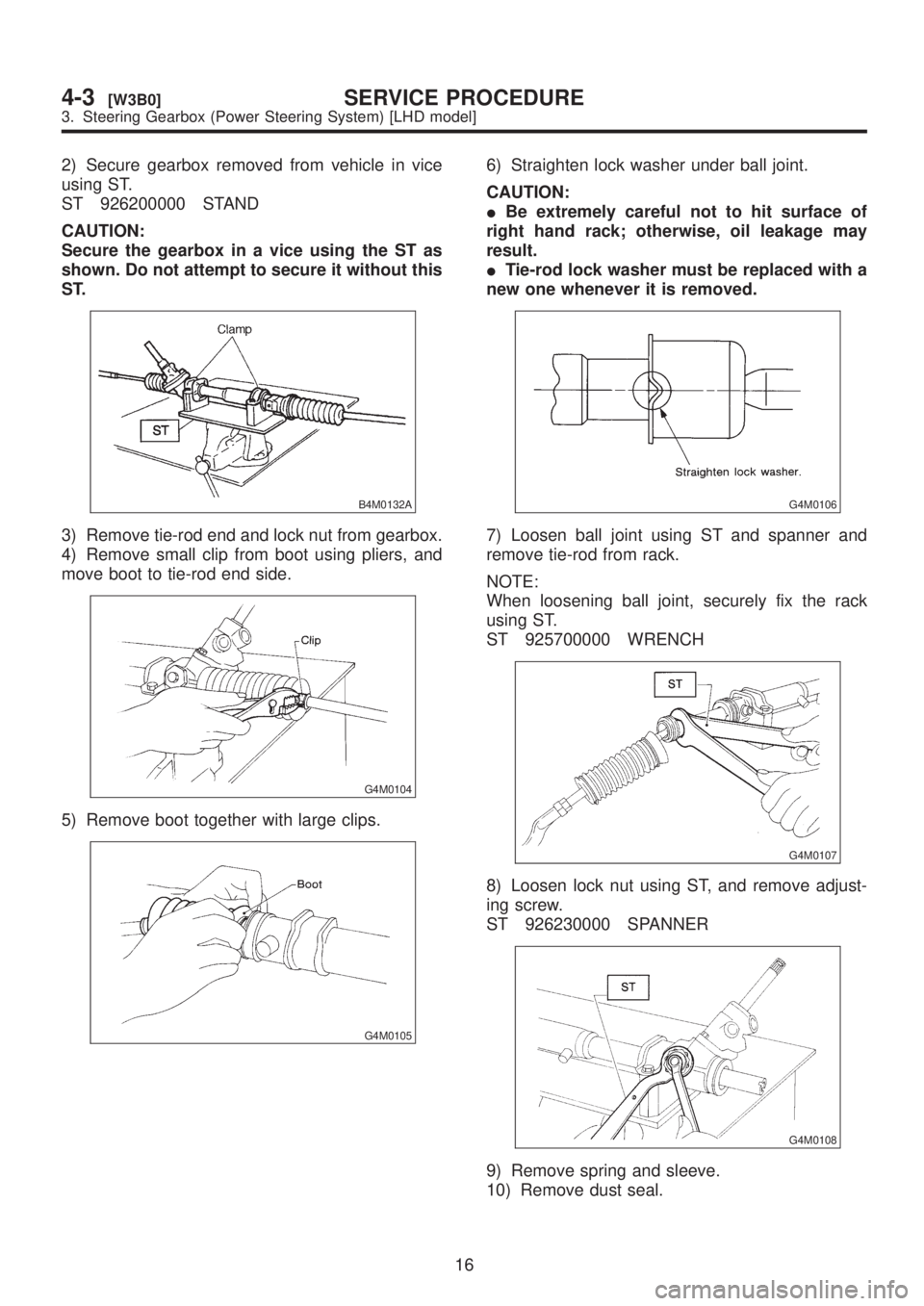
2) Secure gearbox removed from vehicle in vice
using ST.
ST 926200000 STAND
CAUTION:
Secure the gearbox in a vice using the ST as
shown. Do not attempt to secure it without this
ST.
B4M0132A
3) Remove tie-rod end and lock nut from gearbox.
4) Remove small clip from boot using pliers, and
move boot to tie-rod end side.
G4M0104
5) Remove boot together with large clips.
G4M0105
6) Straighten lock washer under ball joint.
CAUTION:
IBe extremely careful not to hit surface of
right hand rack; otherwise, oil leakage may
result.
ITie-rod lock washer must be replaced with a
new one whenever it is removed.
G4M0106
7) Loosen ball joint using ST and spanner and
remove tie-rod from rack.
NOTE:
When loosening ball joint, securely fix the rack
using ST.
ST 925700000 WRENCH
G4M0107
8) Loosen lock nut using ST, and remove adjust-
ing screw.
ST 926230000 SPANNER
G4M0108
9) Remove spring and sleeve.
10) Remove dust seal.
16
4-3[W3B0]SERVICE PROCEDURE
3. Steering Gearbox (Power Steering System) [LHD model]
Page 809 of 1456
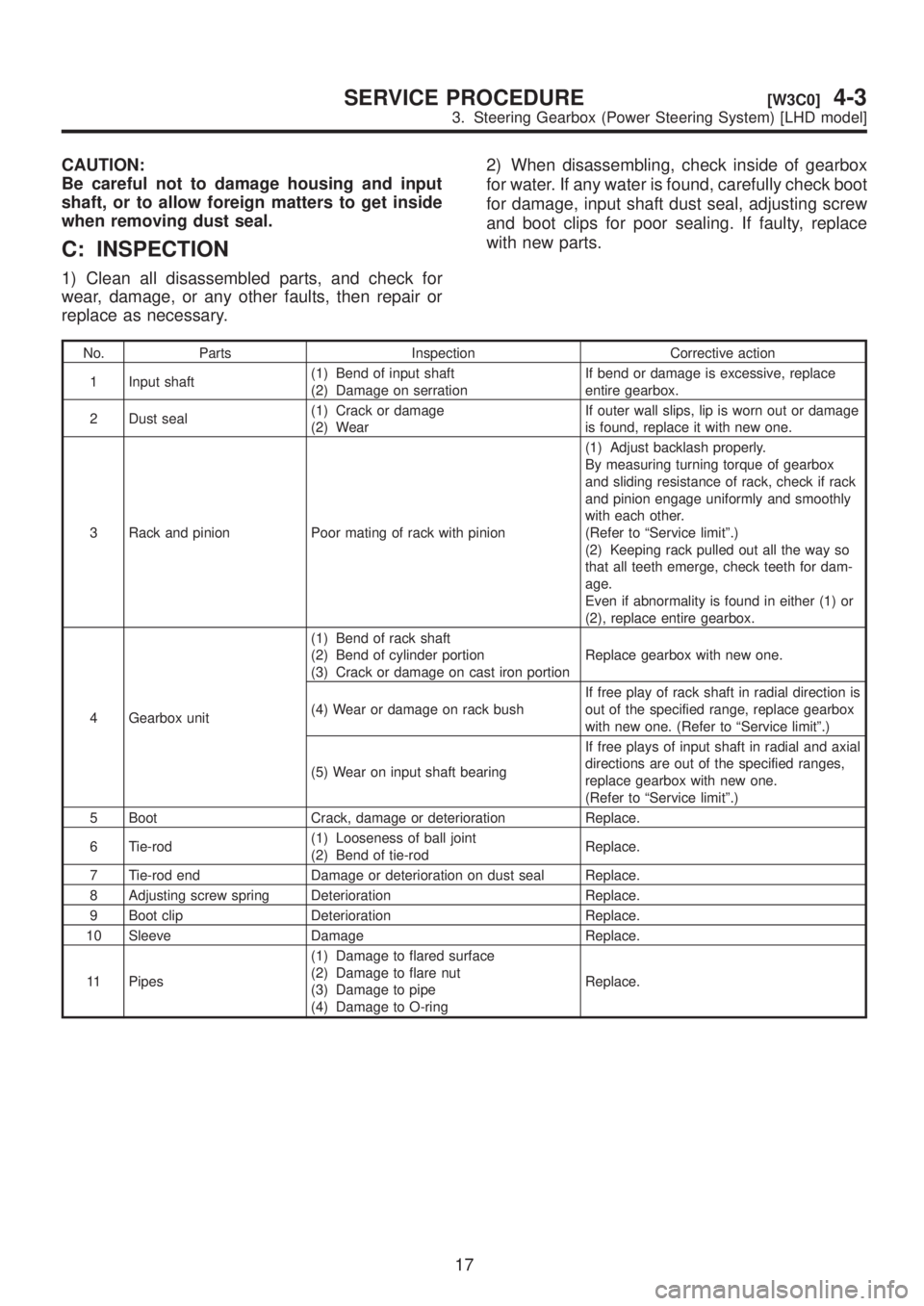
CAUTION:
Be careful not to damage housing and input
shaft, or to allow foreign matters to get inside
when removing dust seal.
C: INSPECTION
1) Clean all disassembled parts, and check for
wear, damage, or any other faults, then repair or
replace as necessary.2) When disassembling, check inside of gearbox
for water. If any water is found, carefully check boot
for damage, input shaft dust seal, adjusting screw
and boot clips for poor sealing. If faulty, replace
with new parts.
No. Parts Inspection Corrective action
1 Input shaft(1) Bend of input shaft
(2) Damage on serrationIf bend or damage is excessive, replace
entire gearbox.
2 Dust seal(1) Crack or damage
(2) WearIf outer wall slips, lip is worn out or damage
is found, replace it with new one.
3 Rack and pinion Poor mating of rack with pinion(1) Adjust backlash properly.
By measuring turning torque of gearbox
and sliding resistance of rack, check if rack
and pinion engage uniformly and smoothly
with each other.
(Refer to ªService limitº.)
(2) Keeping rack pulled out all the way so
that all teeth emerge, check teeth for dam-
age.
Even if abnormality is found in either (1) or
(2), replace entire gearbox.
4 Gearbox unit(1) Bend of rack shaft
(2) Bend of cylinder portion
(3) Crack or damage on cast iron portionReplace gearbox with new one.
(4) Wear or damage on rack bushIf free play of rack shaft in radial direction is
out of the specified range, replace gearbox
with new one. (Refer to ªService limitº.)
(5) Wear on input shaft bearingIf free plays of input shaft in radial and axial
directions are out of the specified ranges,
replace gearbox with new one.
(Refer to ªService limitº.)
5 Boot Crack, damage or deterioration Replace.
6 Tie-rod(1) Looseness of ball joint
(2) Bend of tie-rodReplace.
7 Tie-rod end Damage or deterioration on dust seal Replace.
8 Adjusting screw spring Deterioration Replace.
9 Boot clip Deterioration Replace.
10 Sleeve Damage Replace.
11 Pipes(1) Damage to flared surface
(2) Damage to flare nut
(3) Damage to pipe
(4) Damage to O-ringReplace.
17
[W3C0]4-3SERVICE PROCEDURE
3. Steering Gearbox (Power Steering System) [LHD model]
Page 810 of 1456
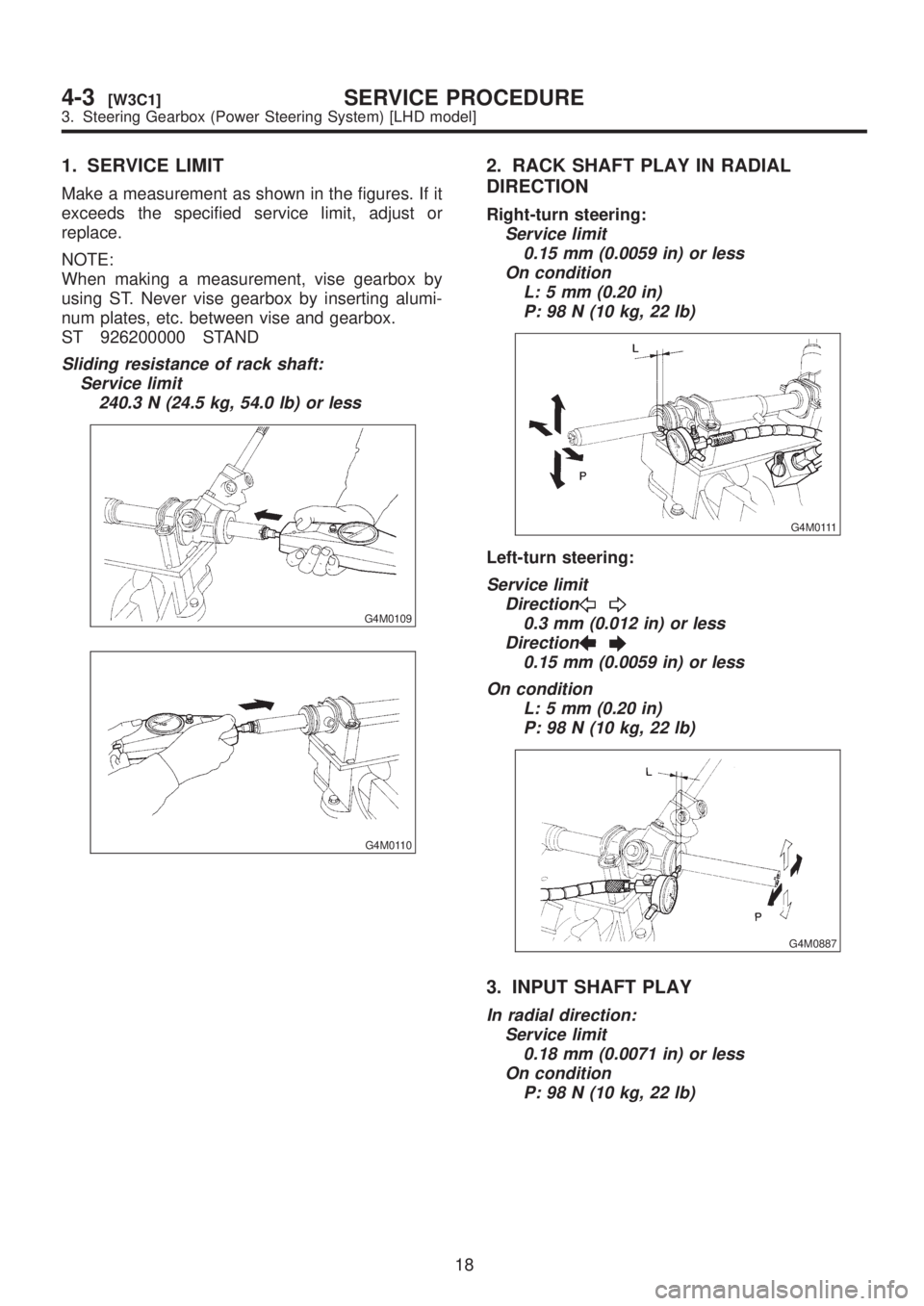
1. SERVICE LIMIT
Make a measurement as shown in the figures. If it
exceeds the specified service limit, adjust or
replace.
NOTE:
When making a measurement, vise gearbox by
using ST. Never vise gearbox by inserting alumi-
num plates, etc. between vise and gearbox.
ST 926200000 STAND
Sliding resistance of rack shaft:
Service limit
240.3 N (24.5 kg, 54.0 lb) or less
G4M0109
G4M0110
2. RACK SHAFT PLAY IN RADIAL
DIRECTION
Right-turn steering:
Service limit
0.15 mm (0.0059 in) or less
On condition
L: 5 mm (0.20 in)
P: 98 N (10 kg, 22 lb)
G4M0111
Left-turn steering:
Service limit
Direction
0.3 mm (0.012 in) or less
Direction
0.15 mm (0.0059 in) or less
On condition
L: 5 mm (0.20 in)
P: 98 N (10 kg, 22 lb)
G4M0887
3. INPUT SHAFT PLAY
In radial direction:
Service limit
0.18 mm (0.0071 in) or less
On condition
P: 98 N (10 kg, 22 lb)
18
4-3[W3C1]SERVICE PROCEDURE
3. Steering Gearbox (Power Steering System) [LHD model]