CHEVROLET CAMARO 1982 Repair Guide
Manufacturer: CHEVROLET, Model Year: 1982, Model line: CAMARO, Model: CHEVROLET CAMARO 1982Pages: 875, PDF Size: 88.64 MB
Page 701 of 875
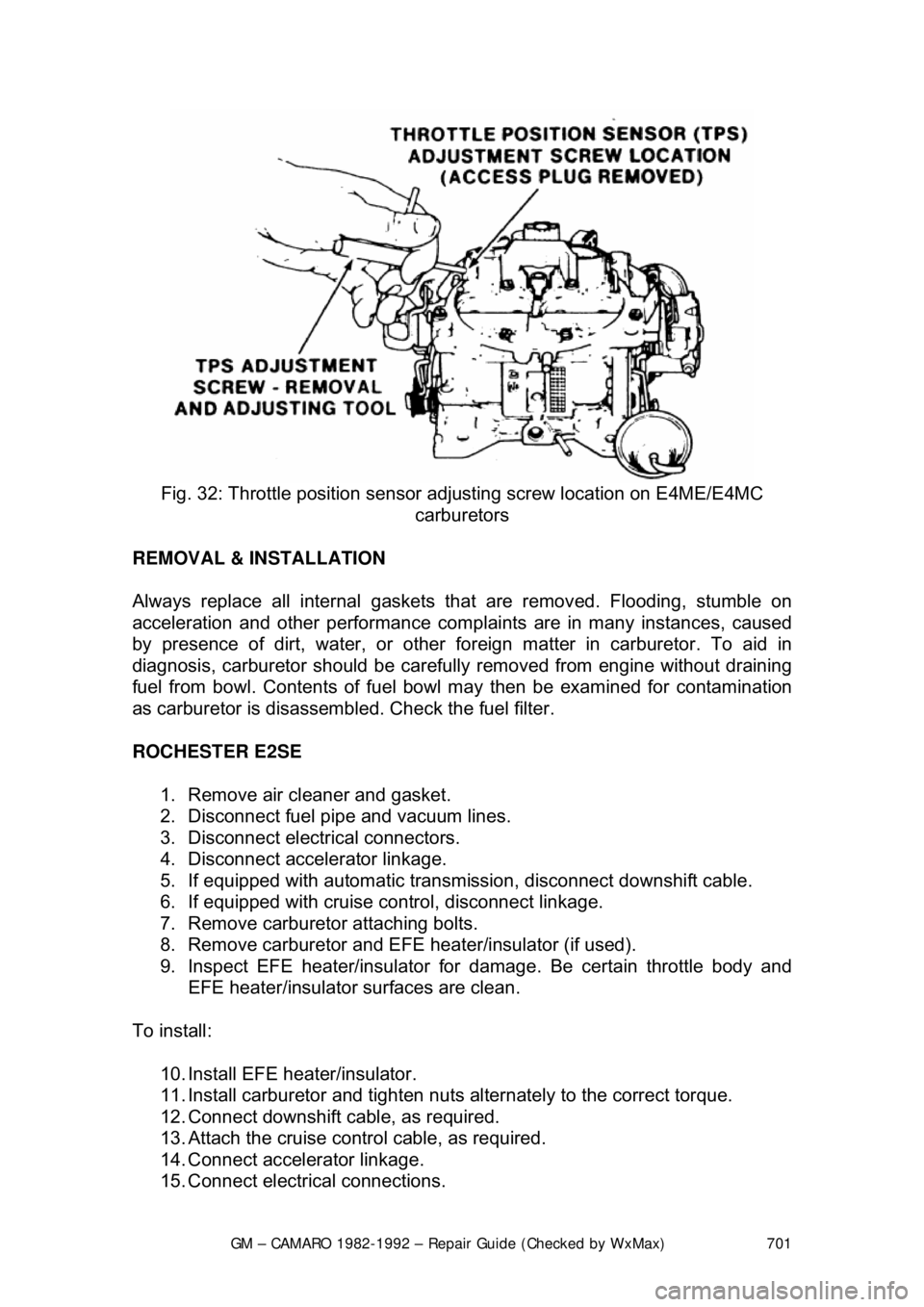
GM – CAMARO 1982-1992 – Repair Guide (Checked by WxMax) 701
Fig. 32: Throttle position sensor adjusting screw location on E4ME/E4MC
carburetors
REMOVAL & INSTALLATION
Always replace all internal gaskets that are removed. Flooding, stumble on
acceleration and other performance comp laints are in many instances, caused
by presence of dirt, water, or other foreign matter in carburetor. To aid in
diagnosis, carburetor should be carefully removed from engine without draining
fuel from bowl. Contents of fuel bowl may then be examined for contamination
as carburetor is disassembl ed. Check the fuel filter.
ROCHESTER E2SE 1. Remove air cleaner and gasket.
2. Disconnect fuel pipe and vacuum lines.
3. Disconnect electrical connectors.
4. Disconnect accelerator linkage.
5. If equipped with automatic transmi ssion, disconnect downshift cable.
6. If equipped with cruise c ontrol, disconnect linkage.
7. Remove carburetor attaching bolts.
8. Remove carburetor and EF E heater/insulator (if used).
9. Inspect EFE heater/insulator for damage. Be certain throttle body and
EFE heater/insulator surfaces are clean.
To install: 10. Install EFE heater/insulator.
11. Install carburetor and tighten nuts alternately to the correct torque.
12. Connect downshift cable, as required.
13. Attach the cruise cont rol cable, as required.
14. Connect accelerator linkage.
15. Connect electrical connections.
Page 702 of 875
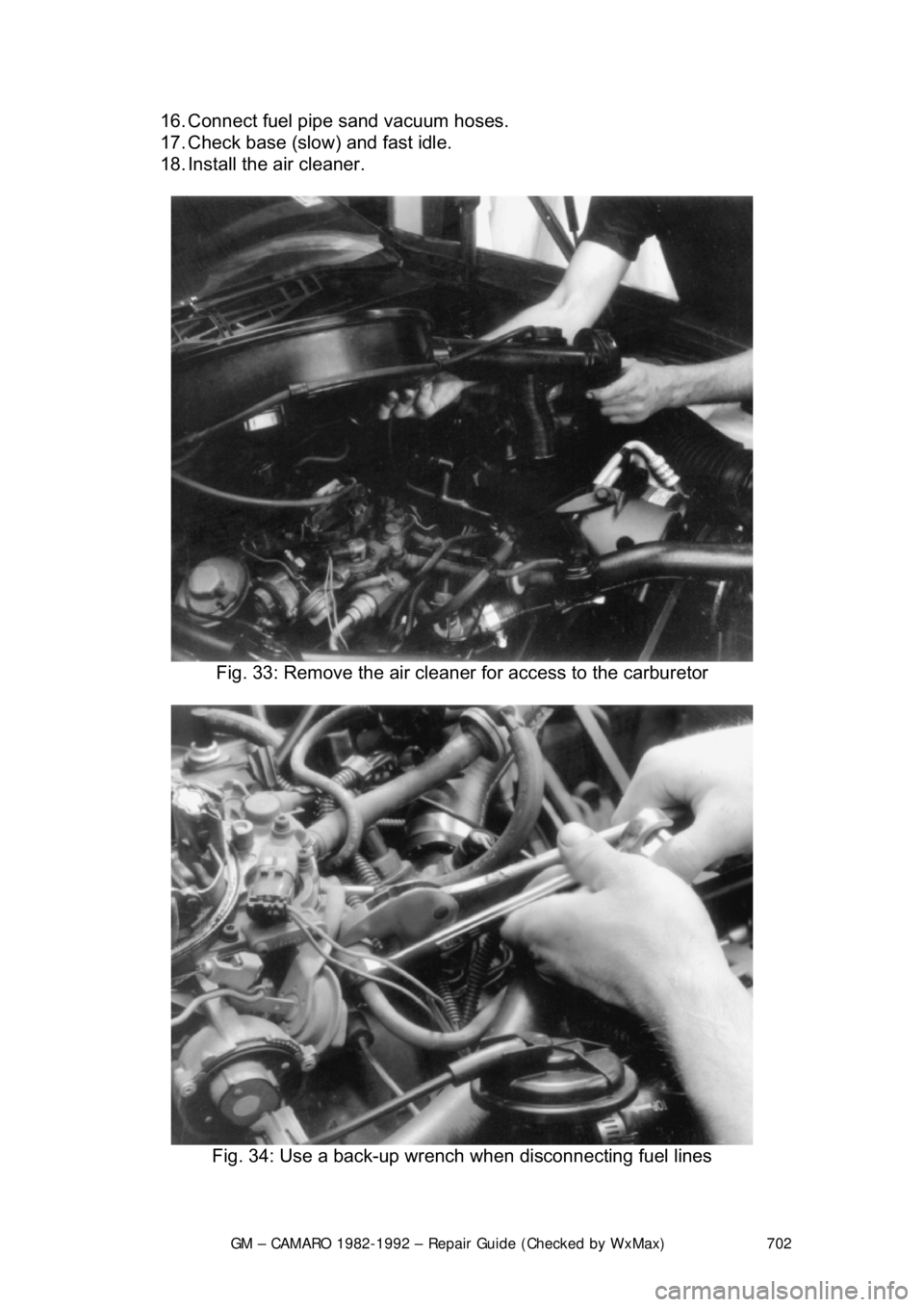
GM – CAMARO 1982-1992 – Repair Guide (Checked by WxMax) 702
16. Connect fuel pipe sand vacuum hoses.
17. Check base (slow) and fast idle.
18. Install the air cleaner.
Fig. 33: Remove the air cleaner for access to the carburetor
Fig. 34: Use a back-up wrench when disconnecting fuel lines
Page 703 of 875
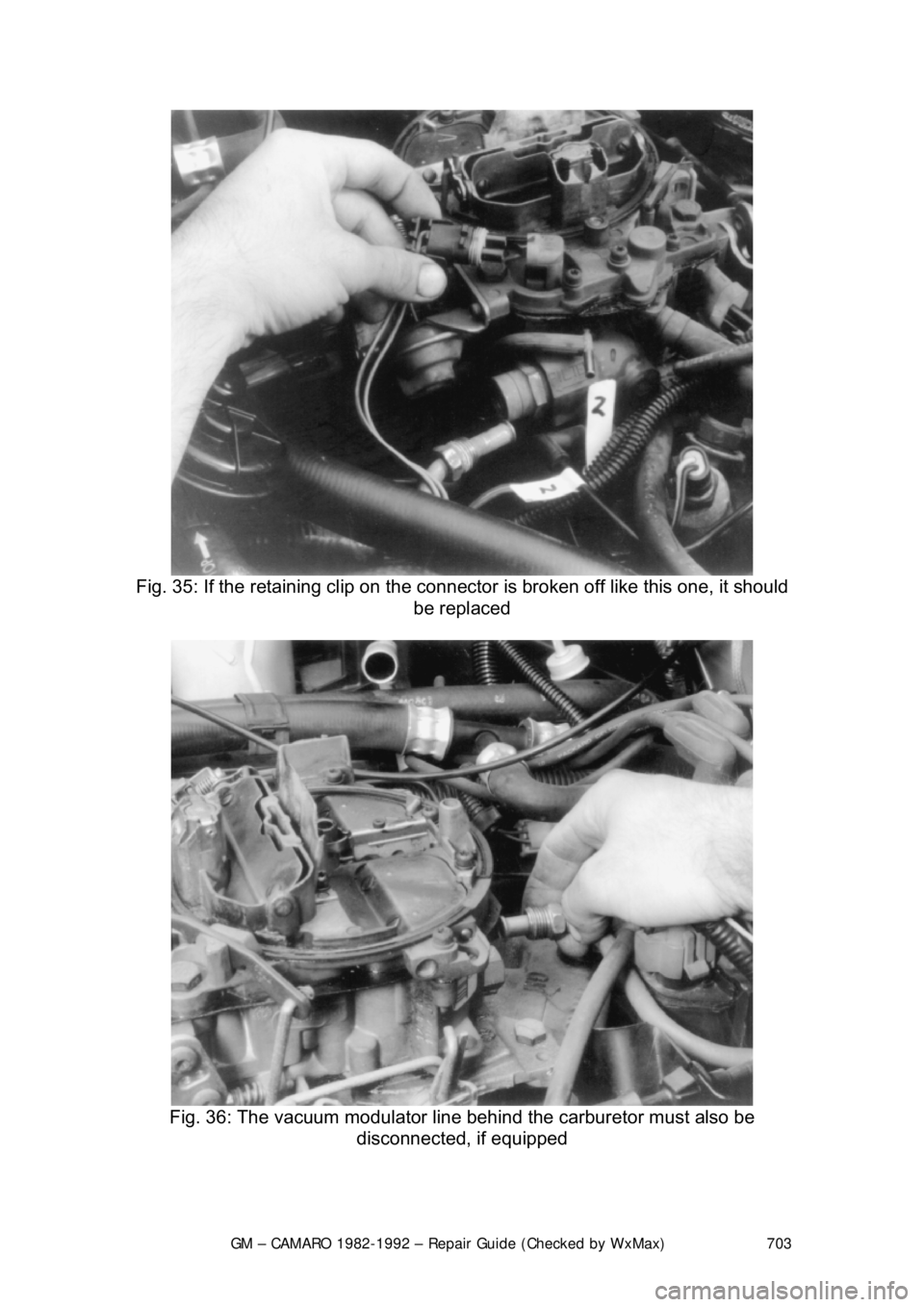
GM – CAMARO 1982-1992 – Repair Guide (Checked by WxMax) 703
Fig. 35: If the retaining clip on the connec tor is broken off like this one, it should
be replaced
Fig. 36: The vacuum modulator line behind the carburetor must also be
disconnected, if equipped
Page 704 of 875
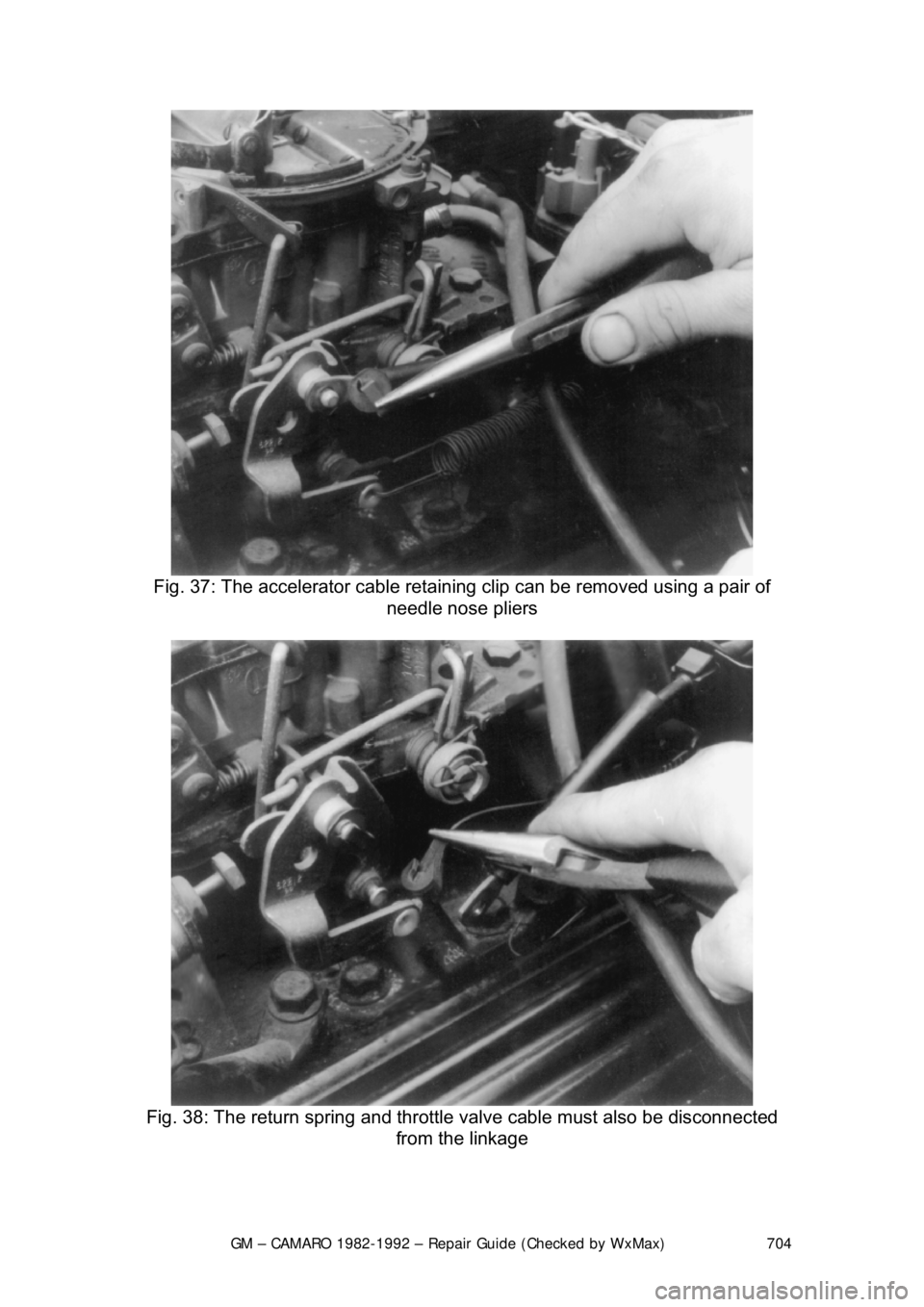
GM – CAMARO 1982-1992 – Repair Guide (Checked by WxMax) 704
Fig. 37: The accelerator cable retaini ng clip can be removed using a pair of
needle nose pliers
Fig. 38: The return spring and throttle valve cable must also be disconnected
from the linkage
Page 705 of 875
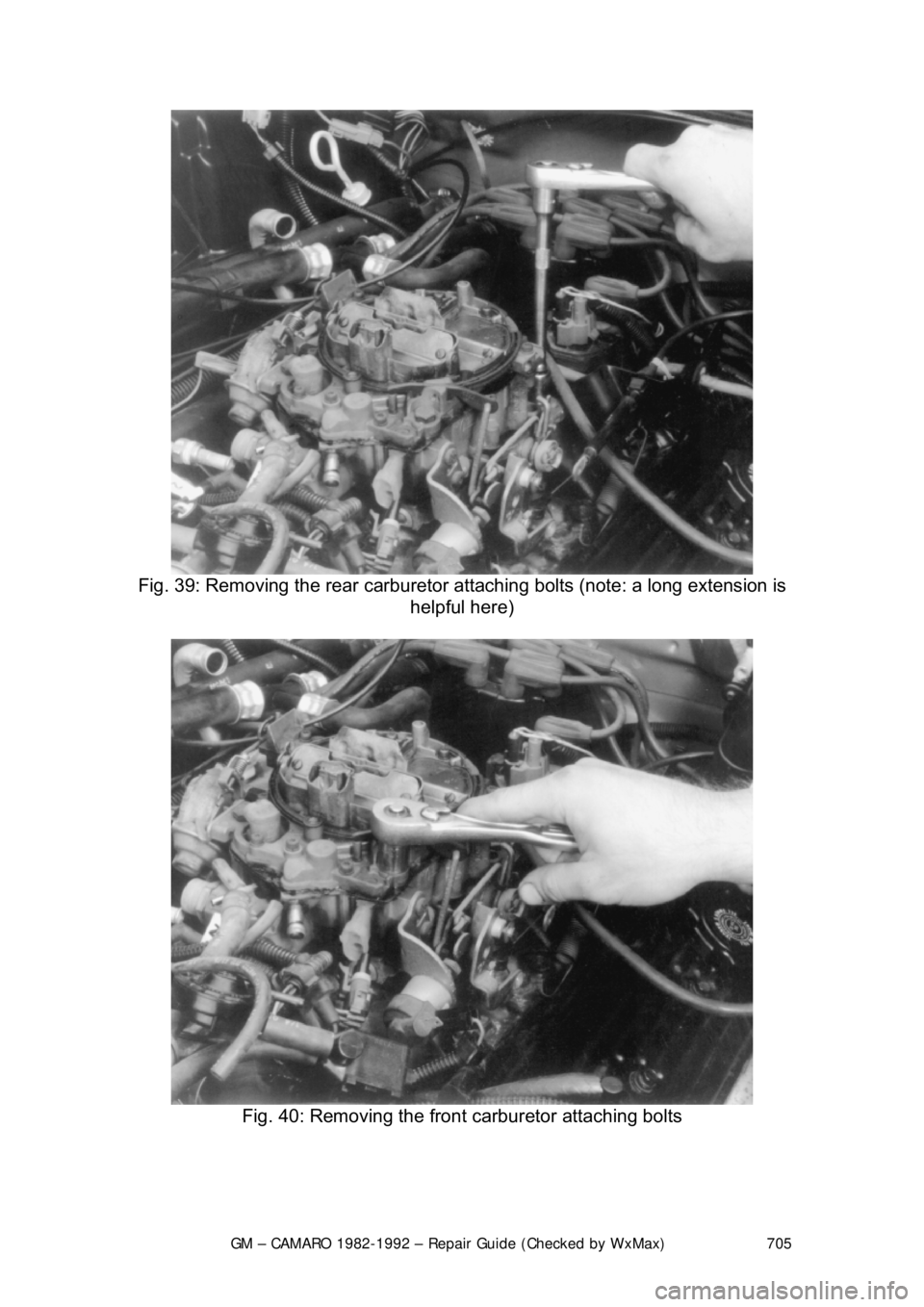
GM – CAMARO 1982-1992 – Repair Guide (Checked by WxMax) 705
Fig. 39: Removing the rear carburetor at taching bolts (note: a long extension is
helpful here)
Fig. 40: Removing the front carburetor attaching bolts
Page 706 of 875
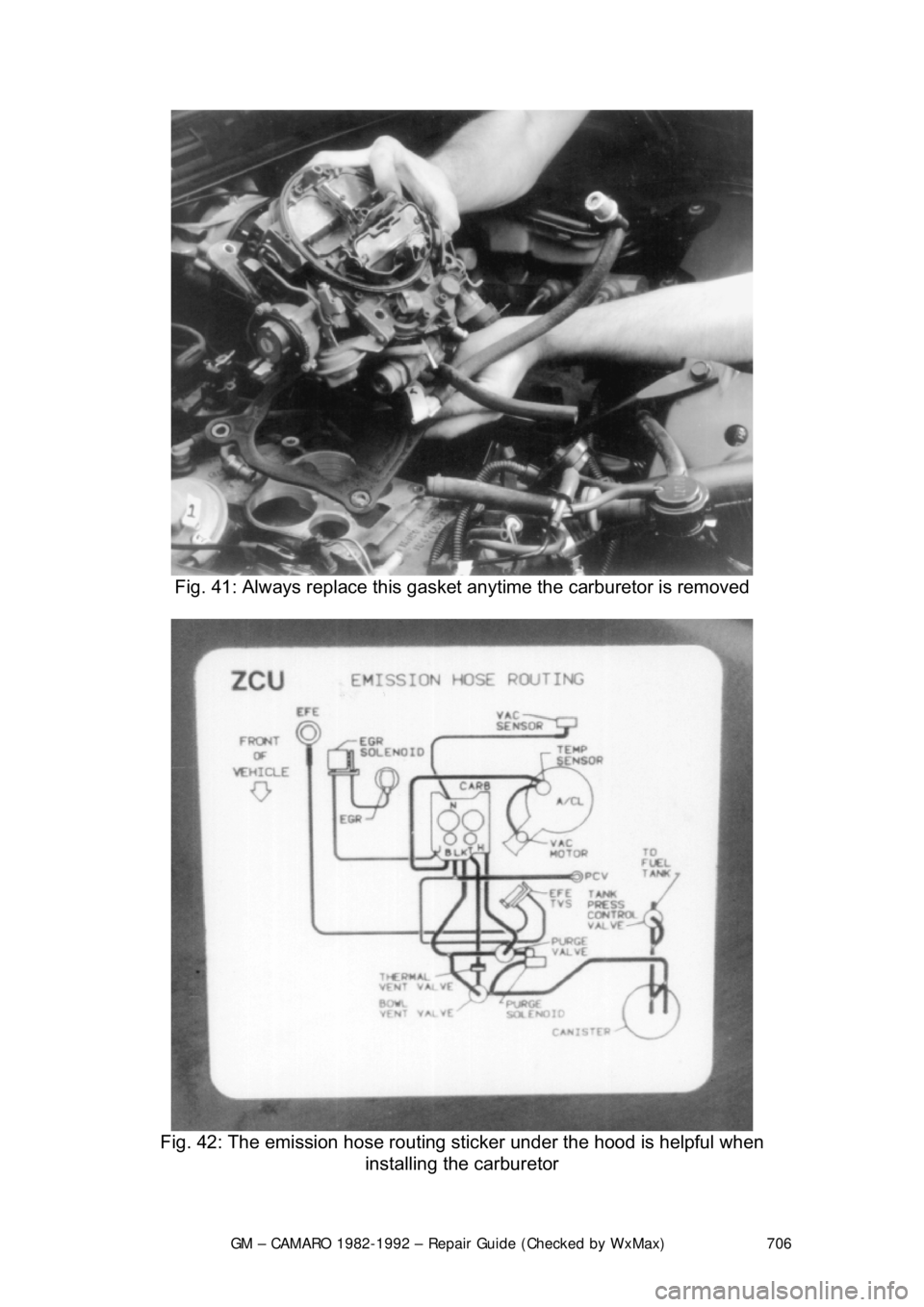
GM – CAMARO 1982-1992 – Repair Guide (Checked by WxMax) 706
Fig. 41: Always replace this gasket anytime the carburetor is removed
Fig. 42: The emission hose routing sticker under the hood is helpful when
installing the carburetor
Page 707 of 875
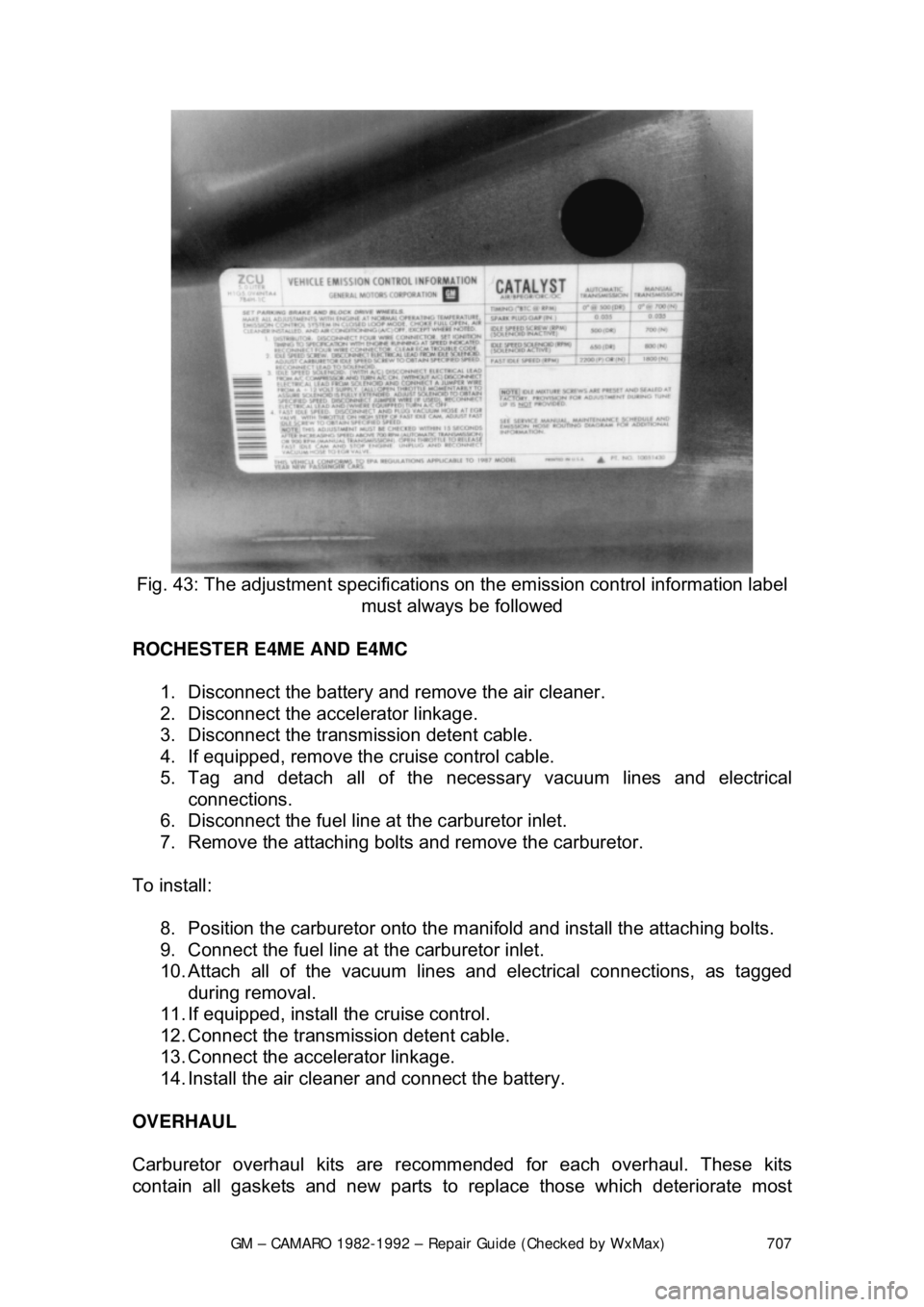
GM – CAMARO 1982-1992 – Repair Guide (Checked by WxMax) 707
Fig. 43: The adjustment specifications on the emission control information label
must always be followed
ROCHESTER E4ME AND E4MC 1. Disconnect the battery and remove the air cleaner.
2. Disconnect the accelerator linkage.
3. Disconnect the transmission detent cable.
4. If equipped, remove the cr uise control cable.
5. Tag and detach all of the necessa ry vacuum lines and electrical
connections.
6. Disconnect the fuel line at the carburetor inlet.
7. Remove the attaching bolts and remove the carburetor.
To install: 8. Position the carburetor onto the manifold and install the attaching bolts.
9. Connect the fuel line at the carburetor inlet.
10. Attach all of the vacuum lines and electrical connections, as tagged
during removal.
11. If equipped, install the cruise control.
12. Connect the transmission detent cable.
13. Connect the accelerator linkage.
14. Install the air cleaner and connect the battery.
OVERHAUL
Carburetor overhaul kits are reco mmended for each overhaul. These kits
contain all gaskets and new parts to re place those which deteriorate most
Page 708 of 875
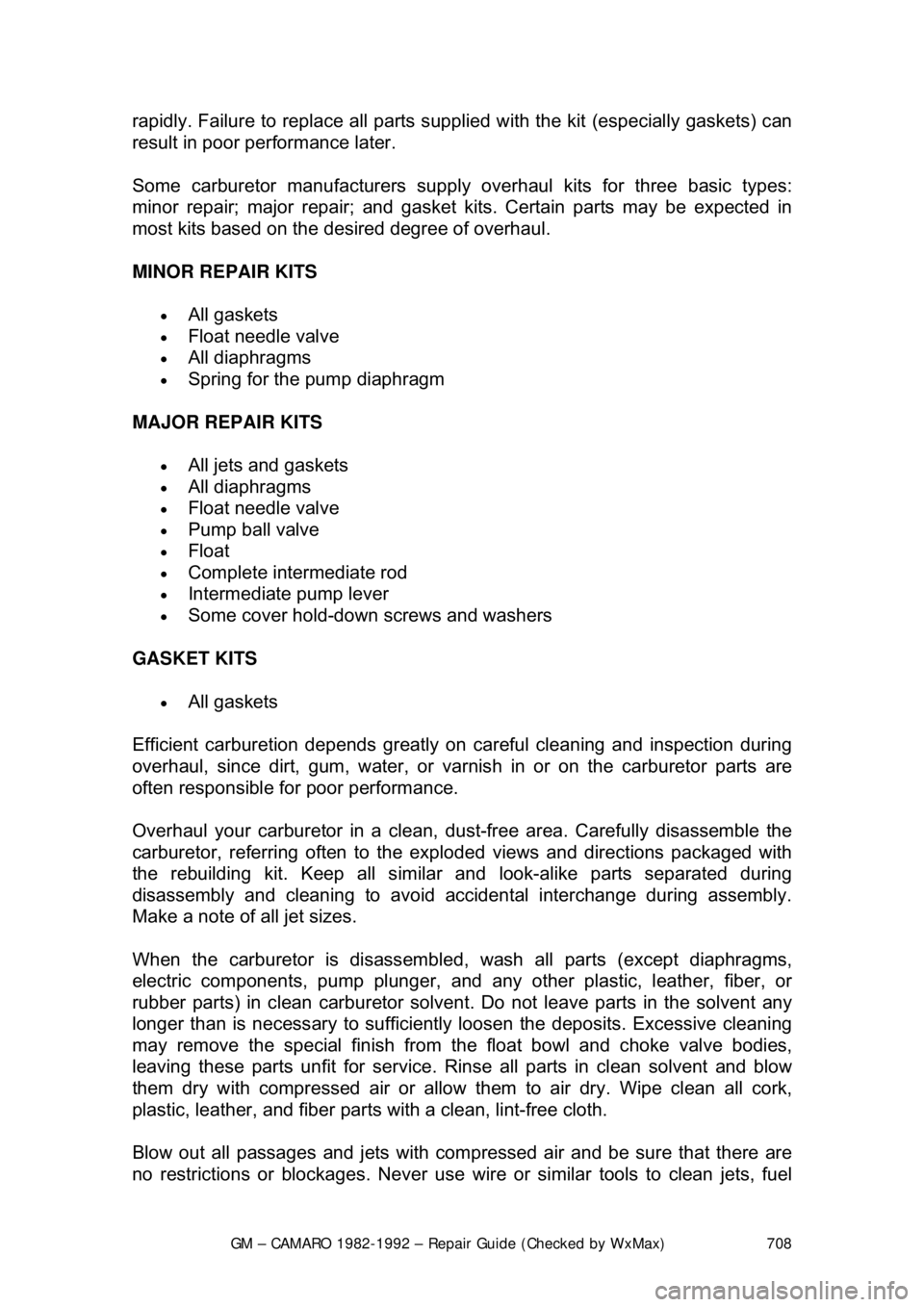
GM – CAMARO 1982-1992 – Repair Guide (Checked by WxMax) 708
rapidly. Failure to replace all parts s
upplied with the kit (especially gaskets) can
result in poor performance later.
Some carburetor manufacturers supply overhaul kits for three basic types:
minor repair; major repair; and gasket kits. Certain parts may be expected in
most kits based on the desired degree of overhaul.
MINOR REPAIR KITS
• All gaskets
• Float needle valve
• All diaphragms
• Spring for the pump diaphragm
MAJOR REPAIR KITS
• All jets and gaskets
• All diaphragms
• Float needle valve
• Pump ball valve
• Float
• Complete intermediate rod
• Intermediate pump lever
• Some cover hold-down screws and washers
GASKET KITS
• All gaskets
Efficient carburetion depends greatly on careful cleaning and inspection during
overhaul, since dirt, gum, water, or varnis h in or on the carburetor parts are
often responsible for poor performance.
Overhaul your carburetor in a clean, dust-free area. Carefully disassemble the
carburetor, referring often to the explod ed views and directions packaged with
the rebuilding kit. Keep all similar and look-alike parts separated during
disassembly and cleaning to avoid accidental interchange during assembly\
.
Make a note of all jet sizes.
When the carburetor is disassembled, wash all parts (except diaphragms,
electric components, pump pl unger, and any other plastic, leather, fiber, or
rubber parts) in clean carbur etor solvent. Do not leave parts in the solvent any
longer than is necessary to sufficiently loosen the deposits. Excessive cleaning
may remove the special finish from the float bowl and choke valve bodies,
leaving these parts unfit for service. Rinse all parts in clean solvent and blow
them dry with compressed air or allow them to air dry. Wipe clean all cork,
plastic, leather, and fiber parts with a clean, lint-free cloth.
Blow out all passages and jets with comp ressed air and be sure that there are
no restrictions or blockages. Never use wi re or similar tools to clean jets, fuel
Page 709 of 875
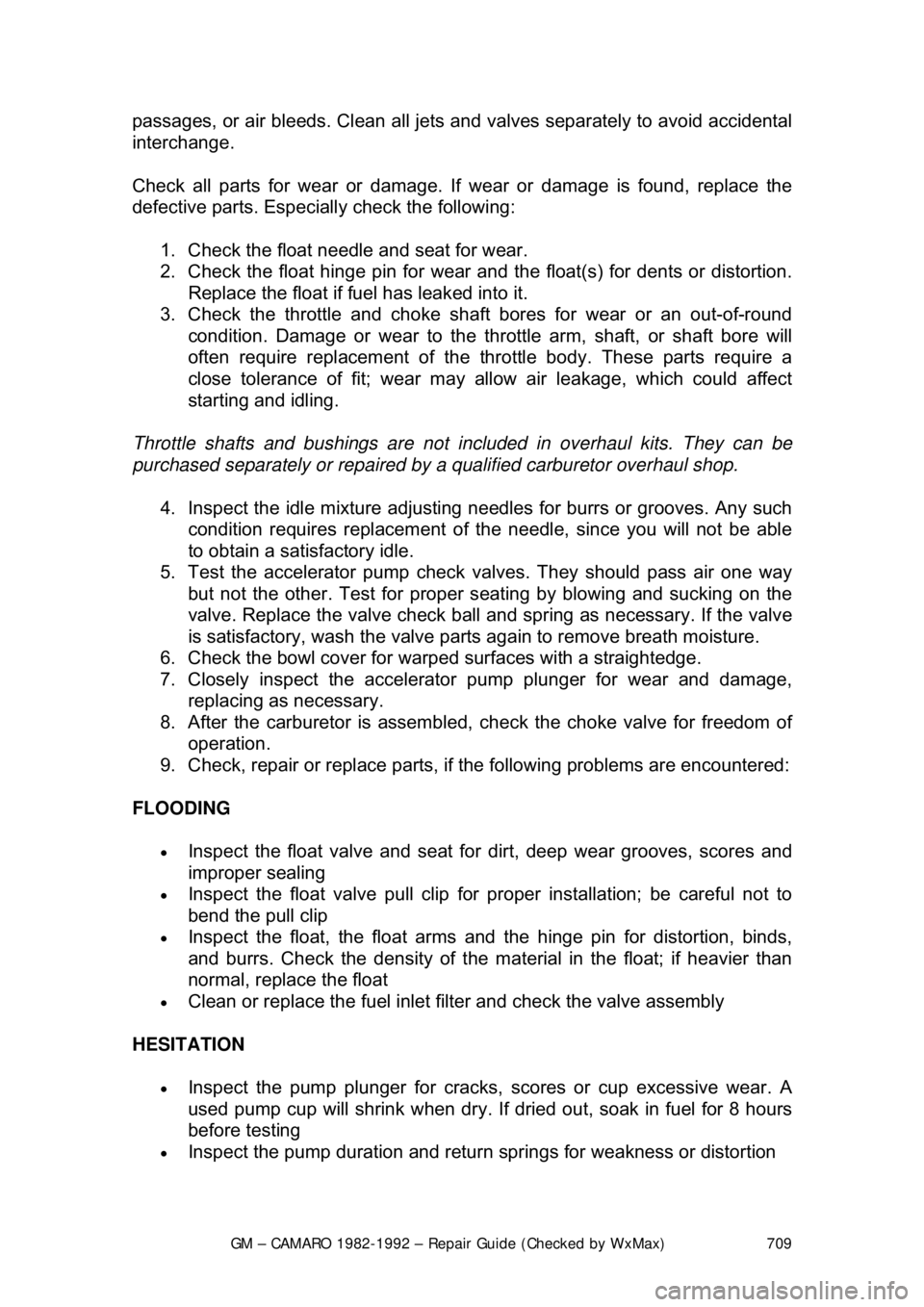
GM – CAMARO 1982-1992 – Repair Guide (Checked by WxMax) 709
passages, or air bleeds. Clean all jets and va
lves separately to avoid accidental
interchange.
Check all parts for wear or damage. If we ar or damage is found, replace the
defective parts. Especially check the following:
1. Check the float needle and seat for wear.
2. Check the float hinge pin for wear and the float(s) for dents or distortion.
Replace the float if fuel has leaked into it.
3. Check the throttle and choke sha ft bores for wear or an out-of-round
condition. Damage or wear to the thro ttle arm, shaft, or shaft bore will
often require replacement of the throttle body. These parts require a
close tolerance of fit; wear may allow air leakage, which could affect
starting and idling.
Throttle shafts and bushings are not included in overhaul kits. They can be
purchased separately or repaired by a qualified carburetor overhaul shop.
4. Inspect the idle mixt ure adjusting needles for bu rrs or grooves. Any such
condition requires replacement of t he needle, since you will not be able
to obtain a satisfactory idle.
5. Test the accelerator pump check va lves. They should pass air one way
but not the other. Test for proper s eating by blowing and sucking on the
valve. Replace the valve check ball and spring as necessary. If the valve
is satisfactory, wash the valve part s again to remove breath moisture.
6. Check the bowl cover for war ped surfaces with a straightedge.
7. Closely inspect the accelerato r pump plunger for wear and damage,
replacing as necessary.
8. After the carburetor is assembled, check the choke valve for freedom of
operation.
9. Check, repair or replace parts, if the following problems are encountered:
FLOODING
• Inspect the float valve and seat for dirt, deep wear grooves, scores and
improper sealing
• Inspect the float valve pull clip for proper installation; be careful no\
t to
bend the pull clip
• Inspect the float, the float arms and the hinge pin for distortion, binds,
and burrs. Check the density of the mate rial in the float; if heavier than
normal, replace the float
• Clean or replace the fuel inlet f ilter and check the valve assembly
HESITATION
• Inspect the pump plunger for cracks, scores or cup excessive wear. A
used pump cup will shrink w hen dry. If dried out, soak in fuel for 8 hours
before testing
• Inspect the pump duration and return springs for weakness or distortion \
Page 710 of 875
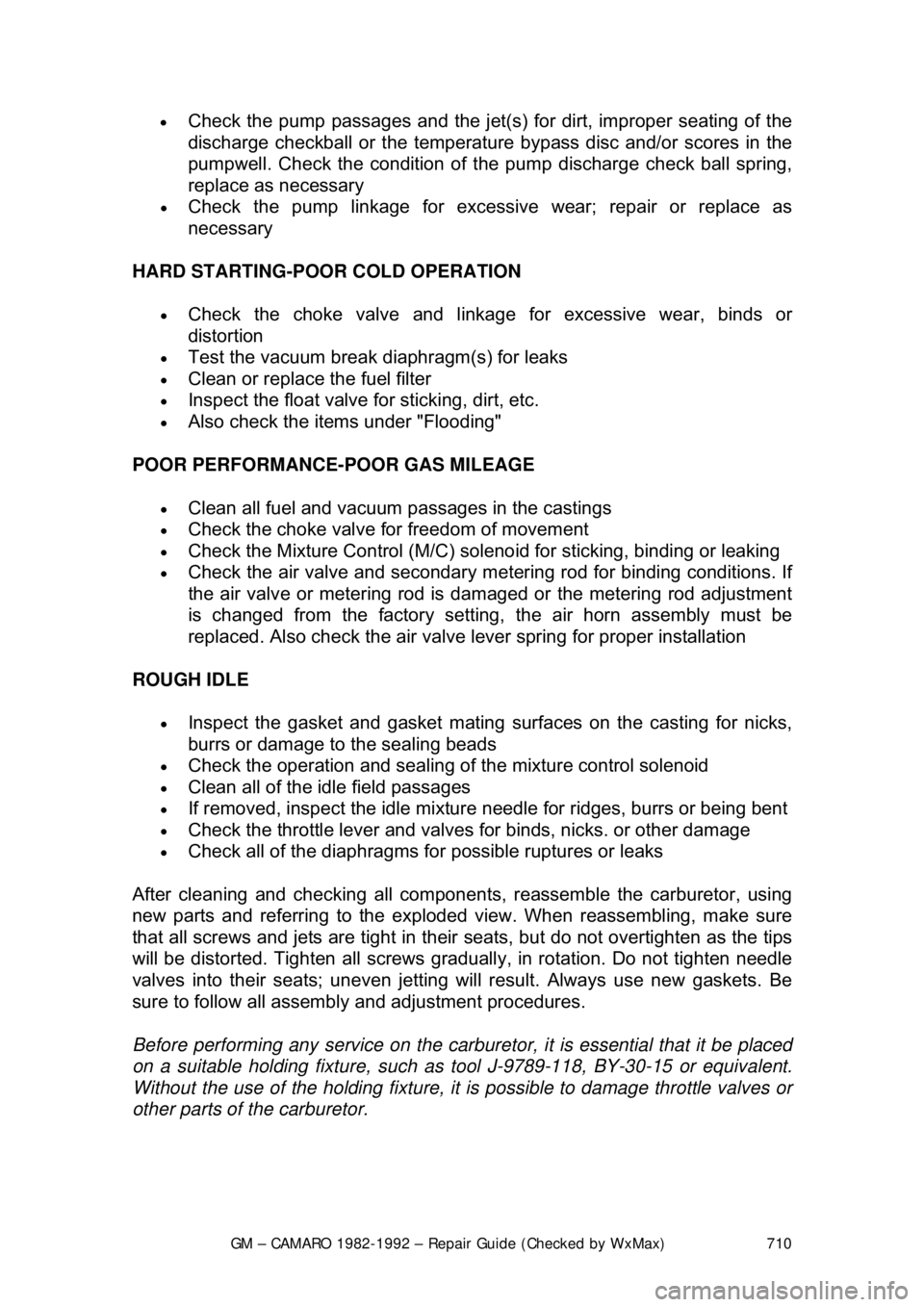
GM – CAMARO 1982-1992 – Repair Guide (Checked by WxMax) 710
•
Check the pump passages and the jet(s) for dirt, improper seating of the
discharge checkball or t he temperature bypass disc and/or scores in the
pumpwell. Check the condition of t he pump discharge check ball spring,
replace as necessary
• Check the pump linkage for excessiv e wear; repair or replace as
necessary
HARD STARTING-POOR COLD OPERATION
• Check the choke valve and linkage for excessive wear, binds or
distortion
• Test the vacuum break diaphragm(s) for leaks
• Clean or replace the fuel filter
• Inspect the float valve fo r sticking, dirt, etc.
• Also check the items under "Flooding"
POOR PERFORMANCE-POOR GAS MILEAGE
• Clean all fuel and vacuum passages in the castings
• Check the choke valve fo r freedom of movement
• Check the Mixture Control (M/C) soleno id for sticking, binding or leaking
• Check the air valve and secondary me tering rod for binding conditions. If
the air valve or metering rod is da maged or the metering rod adjustment
is changed from the factory setting, the air horn assembly must be
replaced. Also check the air valve le ver spring for proper installation
ROUGH IDLE
• Inspect the gasket and gasket mating su rfaces on the casting for nicks,
burrs or damage to the sealing beads
• Check the operation and sealing of the mixture control solenoid
• Clean all of the idle field passages
• If removed, inspect the idle mixture needle for ridges, burrs or being bent
• Check the throttle lever and valves for binds, nicks. or other damage
• Check all of the diaphragms for possible ruptures or leaks
After cleaning and checking all components, reassemble the carburetor, using
new parts and referring to the exploded view. When reassembling, make sure
that all screws and jets are tight in their seats, but do not overtighten as the tips
will be distorted. Tighten al l screws gradually, in rotation. Do not tighten needle
valves into their seats; uneven jetting will result. Always use new gaskets. Be
sure to follow all assembly and adjustment procedures.
Before performing any service on the carburet or, it is essential that it be placed
on a suitable holding fixtur e, such as tool J-9789-118, BY-30-15 or equivalent.
Without the use of the holding fixture, it is possible to damage throttle valves or
other parts of the carburetor.