CHRYSLER VOYAGER 1996 Service Manual
Manufacturer: CHRYSLER, Model Year: 1996, Model line: VOYAGER, Model: CHRYSLER VOYAGER 1996Pages: 1938, PDF Size: 55.84 MB
Page 101 of 1938
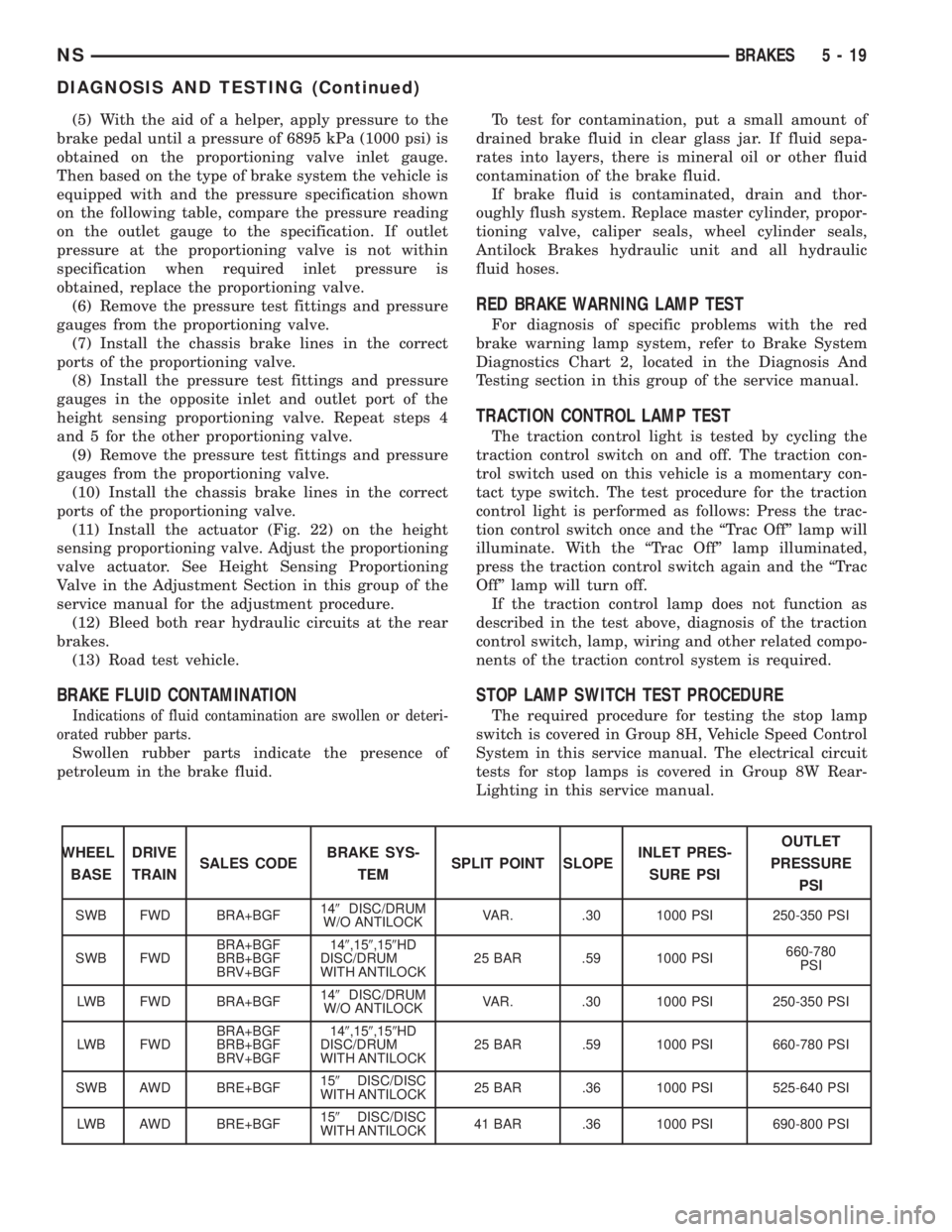
(5) With the aid of a helper, apply pressure to the
brake pedal until a pressure of 6895 kPa (1000 psi) is
obtained on the proportioning valve inlet gauge.
Then based on the type of brake system the vehicle is
equipped with and the pressure specification shown
on the following table, compare the pressure reading
on the outlet gauge to the specification. If outlet
pressure at the proportioning valve is not within
specification when required inlet pressure is
obtained, replace the proportioning valve.
(6) Remove the pressure test fittings and pressure
gauges from the proportioning valve.
(7) Install the chassis brake lines in the correct
ports of the proportioning valve.
(8) Install the pressure test fittings and pressure
gauges in the opposite inlet and outlet port of the
height sensing proportioning valve. Repeat steps 4
and 5 for the other proportioning valve.
(9) Remove the pressure test fittings and pressure
gauges from the proportioning valve.
(10) Install the chassis brake lines in the correct
ports of the proportioning valve.
(11) Install the actuator (Fig. 22) on the height
sensing proportioning valve. Adjust the proportioning
valve actuator. See Height Sensing Proportioning
Valve in the Adjustment Section in this group of the
service manual for the adjustment procedure.
(12) Bleed both rear hydraulic circuits at the rear
brakes.
(13) Road test vehicle.
BRAKE FLUID CONTAMINATION
Indications of fluid contamination are swollen or deteri-
orated rubber parts.
Swollen rubber parts indicate the presence of
petroleum in the brake fluid.To test for contamination, put a small amount of
drained brake fluid in clear glass jar. If fluid sepa-
rates into layers, there is mineral oil or other fluid
contamination of the brake fluid.
If brake fluid is contaminated, drain and thor-
oughly flush system. Replace master cylinder, propor-
tioning valve, caliper seals, wheel cylinder seals,
Antilock Brakes hydraulic unit and all hydraulic
fluid hoses.
RED BRAKE WARNING LAMP TEST
For diagnosis of specific problems with the red
brake warning lamp system, refer to Brake System
Diagnostics Chart 2, located in the Diagnosis And
Testing section in this group of the service manual.
TRACTION CONTROL LAMP TEST
The traction control light is tested by cycling the
traction control switch on and off. The traction con-
trol switch used on this vehicle is a momentary con-
tact type switch. The test procedure for the traction
control light is performed as follows: Press the trac-
tion control switch once and the ªTrac Offº lamp will
illuminate. With the ªTrac Offº lamp illuminated,
press the traction control switch again and the ªTrac
Offº lamp will turn off.
If the traction control lamp does not function as
described in the test above, diagnosis of the traction
control switch, lamp, wiring and other related compo-
nents of the traction control system is required.
STOP LAMP SWITCH TEST PROCEDURE
The required procedure for testing the stop lamp
switch is covered in Group 8H, Vehicle Speed Control
System in this service manual. The electrical circuit
tests for stop lamps is covered in Group 8W Rear-
Lighting in this service manual.
WHEEL
BASEDRIVE
TRAINSALES CODEBRAKE SYS-
TEMSPLIT POINT SLOPEINLET PRES-
SURE PSIOUTLET
PRESSURE
PSI
SWB FWD BRA+BGF149DISC/DRUM
W/O ANTILOCKVAR. .30 1000 PSI 250-350 PSI
SWB FWDBRA+BGF
BRB+BGF
BRV+BGF149,159,159HD
DISC/DRUM
WITH ANTILOCK25 BAR .59 1000 PSI660-780
PSI
LWB FWD BRA+BGF149DISC/DRUM
W/O ANTILOCKVAR. .30 1000 PSI 250-350 PSI
LWB FWDBRA+BGF
BRB+BGF
BRV+BGF149,159,159HD
DISC/DRUM
WITH ANTILOCK25 BAR .59 1000 PSI 660-780 PSI
SWB AWD BRE+BGF159DISC/DISC
WITH ANTILOCK25 BAR .36 1000 PSI 525-640 PSI
LWB AWD BRE+BGF159DISC/DISC
WITH ANTILOCK41 BAR .36 1000 PSI 690-800 PSI
NSBRAKES 5 - 19
DIAGNOSIS AND TESTING (Continued)
Page 102 of 1938
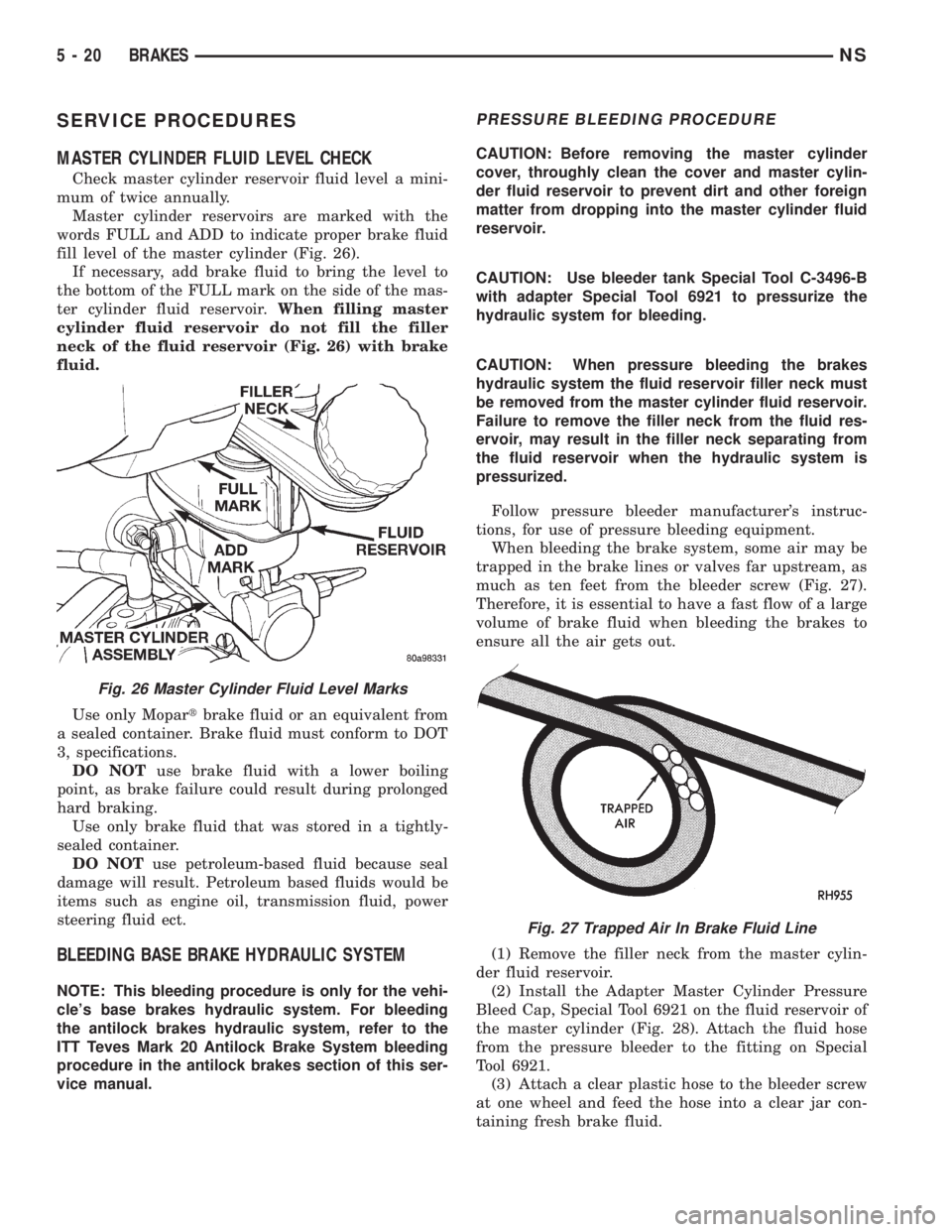
SERVICE PROCEDURES
MASTER CYLINDER FLUID LEVEL CHECK
Check master cylinder reservoir fluid level a mini-
mum of twice annually.
Master cylinder reservoirs are marked with the
words FULL and ADD to indicate proper brake fluid
fill level of the master cylinder (Fig. 26).
If necessary, add brake fluid to bring the level to
the bottom of the FULL mark on the side of the mas-
ter cylinder fluid reservoir.When filling master
cylinder fluid reservoir do not fill the filler
neck of the fluid reservoir (Fig. 26) with brake
fluid.
Use only Mopartbrake fluid or an equivalent from
a sealed container. Brake fluid must conform to DOT
3, specifications.
DO NOTuse brake fluid with a lower boiling
point, as brake failure could result during prolonged
hard braking.
Use only brake fluid that was stored in a tightly-
sealed container.
DO NOTuse petroleum-based fluid because seal
damage will result. Petroleum based fluids would be
items such as engine oil, transmission fluid, power
steering fluid ect.
BLEEDING BASE BRAKE HYDRAULIC SYSTEM
NOTE: This bleeding procedure is only for the vehi-
cle's base brakes hydraulic system. For bleeding
the antilock brakes hydraulic system, refer to the
ITT Teves Mark 20 Antilock Brake System bleeding
procedure in the antilock brakes section of this ser-
vice manual.
PRESSURE BLEEDING PROCEDURE
CAUTION: Before removing the master cylinder
cover, throughly clean the cover and master cylin-
der fluid reservoir to prevent dirt and other foreign
matter from dropping into the master cylinder fluid
reservoir.
CAUTION: Use bleeder tank Special Tool C-3496-B
with adapter Special Tool 6921 to pressurize the
hydraulic system for bleeding.
CAUTION: When pressure bleeding the brakes
hydraulic system the fluid reservoir filler neck must
be removed from the master cylinder fluid reservoir.
Failure to remove the filler neck from the fluid res-
ervoir, may result in the filler neck separating from
the fluid reservoir when the hydraulic system is
pressurized.
Follow pressure bleeder manufacturer's instruc-
tions, for use of pressure bleeding equipment.
When bleeding the brake system, some air may be
trapped in the brake lines or valves far upstream, as
much as ten feet from the bleeder screw (Fig. 27).
Therefore, it is essential to have a fast flow of a large
volume of brake fluid when bleeding the brakes to
ensure all the air gets out.
(1) Remove the filler neck from the master cylin-
der fluid reservoir.
(2) Install the Adapter Master Cylinder Pressure
Bleed Cap, Special Tool 6921 on the fluid reservoir of
the master cylinder (Fig. 28). Attach the fluid hose
from the pressure bleeder to the fitting on Special
Tool 6921.
(3) Attach a clear plastic hose to the bleeder screw
at one wheel and feed the hose into a clear jar con-
taining fresh brake fluid.
Fig. 26 Master Cylinder Fluid Level Marks
Fig. 27 Trapped Air In Brake Fluid Line
5 - 20 BRAKESNS
Page 103 of 1938
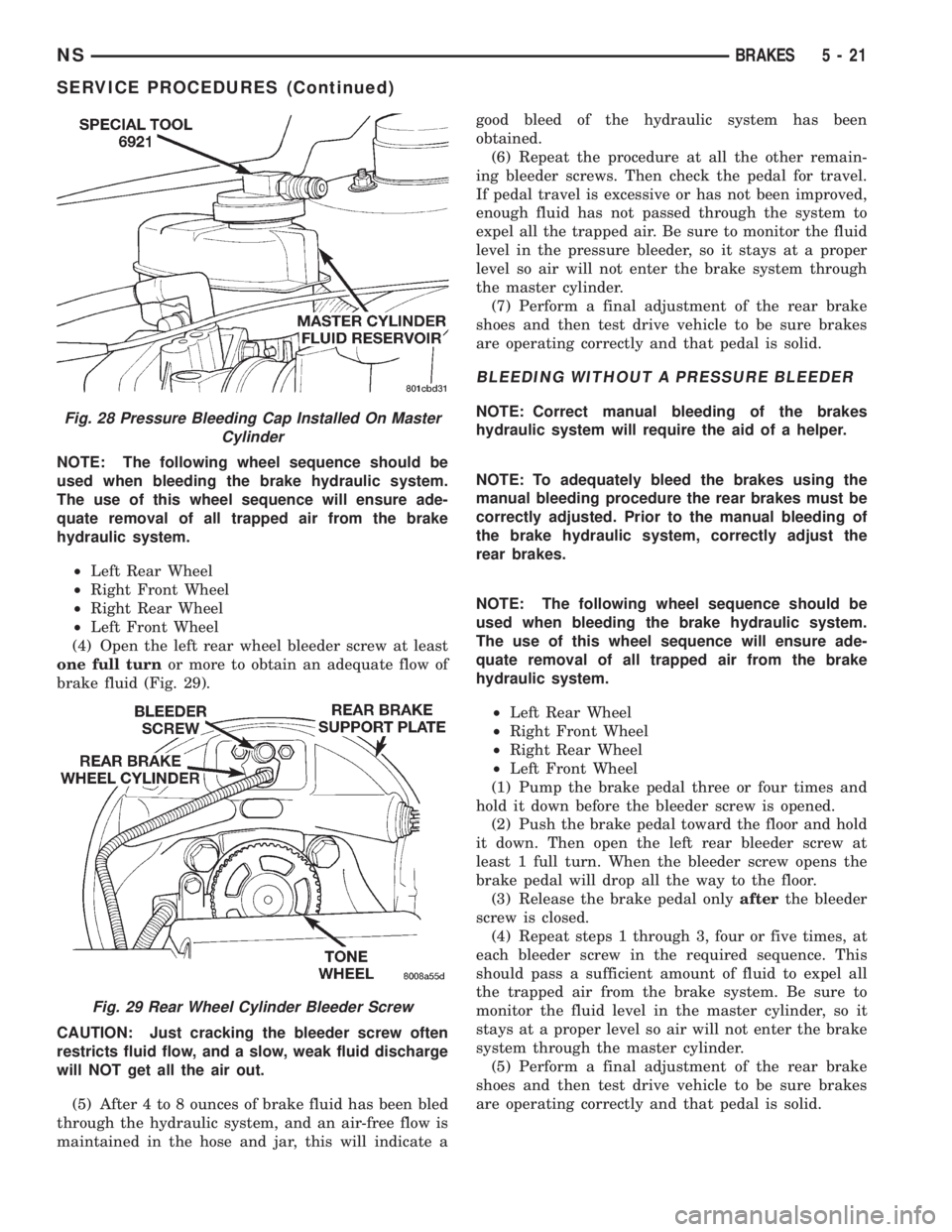
NOTE: The following wheel sequence should be
used when bleeding the brake hydraulic system.
The use of this wheel sequence will ensure ade-
quate removal of all trapped air from the brake
hydraulic system.
²Left Rear Wheel
²Right Front Wheel
²Right Rear Wheel
²Left Front Wheel
(4) Open the left rear wheel bleeder screw at least
one full turnor more to obtain an adequate flow of
brake fluid (Fig. 29).
CAUTION: Just cracking the bleeder screw often
restricts fluid flow, and a slow, weak fluid discharge
will NOT get all the air out.
(5) After 4 to 8 ounces of brake fluid has been bled
through the hydraulic system, and an air-free flow is
maintained in the hose and jar, this will indicate agood bleed of the hydraulic system has been
obtained.
(6) Repeat the procedure at all the other remain-
ing bleeder screws. Then check the pedal for travel.
If pedal travel is excessive or has not been improved,
enough fluid has not passed through the system to
expel all the trapped air. Be sure to monitor the fluid
level in the pressure bleeder, so it stays at a proper
level so air will not enter the brake system through
the master cylinder.
(7) Perform a final adjustment of the rear brake
shoes and then test drive vehicle to be sure brakes
are operating correctly and that pedal is solid.
BLEEDING WITHOUT A PRESSURE BLEEDER
NOTE: Correct manual bleeding of the brakes
hydraulic system will require the aid of a helper.
NOTE: To adequately bleed the brakes using the
manual bleeding procedure the rear brakes must be
correctly adjusted. Prior to the manual bleeding of
the brake hydraulic system, correctly adjust the
rear brakes.
NOTE: The following wheel sequence should be
used when bleeding the brake hydraulic system.
The use of this wheel sequence will ensure ade-
quate removal of all trapped air from the brake
hydraulic system.
²Left Rear Wheel
²Right Front Wheel
²Right Rear Wheel
²Left Front Wheel
(1) Pump the brake pedal three or four times and
hold it down before the bleeder screw is opened.
(2) Push the brake pedal toward the floor and hold
it down. Then open the left rear bleeder screw at
least 1 full turn. When the bleeder screw opens the
brake pedal will drop all the way to the floor.
(3) Release the brake pedal onlyafterthe bleeder
screw is closed.
(4) Repeat steps 1 through 3, four or five times, at
each bleeder screw in the required sequence. This
should pass a sufficient amount of fluid to expel all
the trapped air from the brake system. Be sure to
monitor the fluid level in the master cylinder, so it
stays at a proper level so air will not enter the brake
system through the master cylinder.
(5) Perform a final adjustment of the rear brake
shoes and then test drive vehicle to be sure brakes
are operating correctly and that pedal is solid.Fig. 28 Pressure Bleeding Cap Installed On Master
Cylinder
Fig. 29 Rear Wheel Cylinder Bleeder Screw
NSBRAKES 5 - 21
SERVICE PROCEDURES (Continued)
Page 104 of 1938
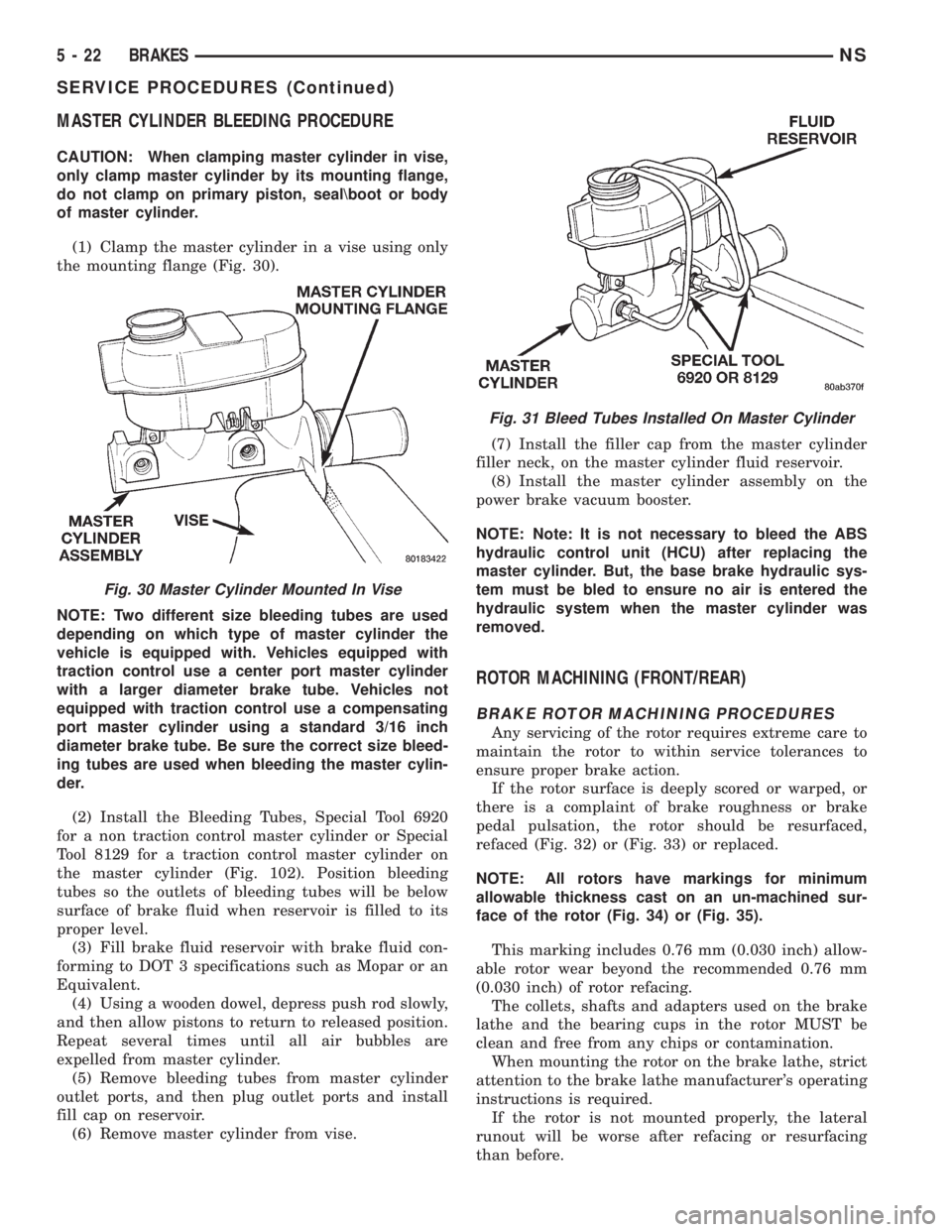
MASTER CYLINDER BLEEDING PROCEDURE
CAUTION: When clamping master cylinder in vise,
only clamp master cylinder by its mounting flange,
do not clamp on primary piston, seal\boot or body
of master cylinder.
(1) Clamp the master cylinder in a vise using only
the mounting flange (Fig. 30).
NOTE: Two different size bleeding tubes are used
depending on which type of master cylinder the
vehicle is equipped with. Vehicles equipped with
traction control use a center port master cylinder
with a larger diameter brake tube. Vehicles not
equipped with traction control use a compensating
port master cylinder using a standard 3/16 inch
diameter brake tube. Be sure the correct size bleed-
ing tubes are used when bleeding the master cylin-
der.
(2) Install the Bleeding Tubes, Special Tool 6920
for a non traction control master cylinder or Special
Tool 8129 for a traction control master cylinder on
the master cylinder (Fig. 102). Position bleeding
tubes so the outlets of bleeding tubes will be below
surface of brake fluid when reservoir is filled to its
proper level.
(3) Fill brake fluid reservoir with brake fluid con-
forming to DOT 3 specifications such as Mopar or an
Equivalent.
(4) Using a wooden dowel, depress push rod slowly,
and then allow pistons to return to released position.
Repeat several times until all air bubbles are
expelled from master cylinder.
(5) Remove bleeding tubes from master cylinder
outlet ports, and then plug outlet ports and install
fill cap on reservoir.
(6) Remove master cylinder from vise.(7) Install the filler cap from the master cylinder
filler neck, on the master cylinder fluid reservoir.
(8) Install the master cylinder assembly on the
power brake vacuum booster.
NOTE: Note: It is not necessary to bleed the ABS
hydraulic control unit (HCU) after replacing the
master cylinder. But, the base brake hydraulic sys-
tem must be bled to ensure no air is entered the
hydraulic system when the master cylinder was
removed.
ROTOR MACHINING (FRONT/REAR)
BRAKE ROTOR MACHINING PROCEDURES
Any servicing of the rotor requires extreme care to
maintain the rotor to within service tolerances to
ensure proper brake action.
If the rotor surface is deeply scored or warped, or
there is a complaint of brake roughness or brake
pedal pulsation, the rotor should be resurfaced,
refaced (Fig. 32) or (Fig. 33) or replaced.
NOTE: All rotors have markings for minimum
allowable thickness cast on an un-machined sur-
face of the rotor (Fig. 34) or (Fig. 35).
This marking includes 0.76 mm (0.030 inch) allow-
able rotor wear beyond the recommended 0.76 mm
(0.030 inch) of rotor refacing.
The collets, shafts and adapters used on the brake
lathe and the bearing cups in the rotor MUST be
clean and free from any chips or contamination.
When mounting the rotor on the brake lathe, strict
attention to the brake lathe manufacturer's operating
instructions is required.
If the rotor is not mounted properly, the lateral
runout will be worse after refacing or resurfacing
than before.
Fig. 30 Master Cylinder Mounted In Vise
Fig. 31 Bleed Tubes Installed On Master Cylinder
5 - 22 BRAKESNS
SERVICE PROCEDURES (Continued)
Page 105 of 1938
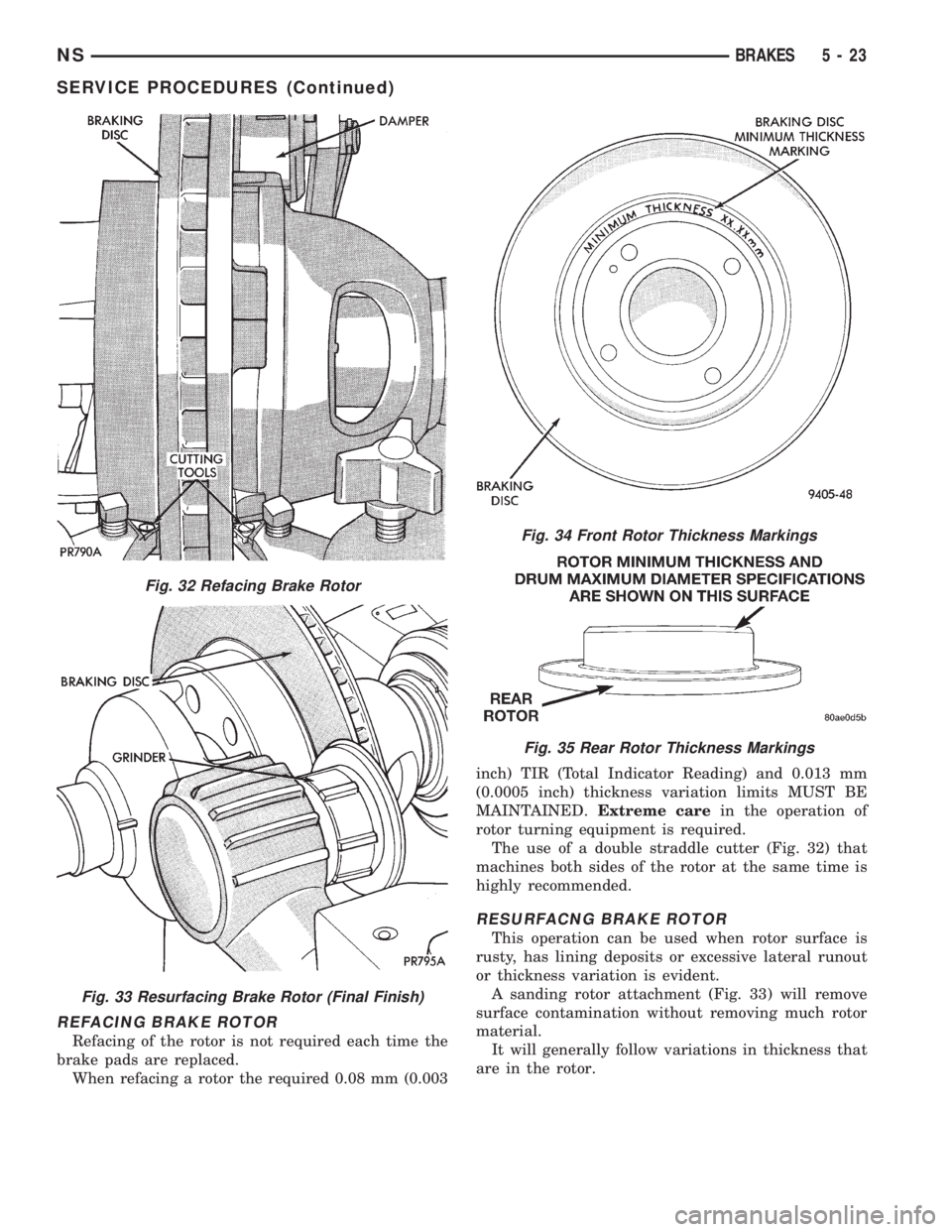
REFACING BRAKE ROTOR
Refacing of the rotor is not required each time the
brake pads are replaced.
When refacing a rotor the required 0.08 mm (0.003inch) TIR (Total Indicator Reading) and 0.013 mm
(0.0005 inch) thickness variation limits MUST BE
MAINTAINED.Extreme carein the operation of
rotor turning equipment is required.
The use of a double straddle cutter (Fig. 32) that
machines both sides of the rotor at the same time is
highly recommended.
RESURFACNG BRAKE ROTOR
This operation can be used when rotor surface is
rusty, has lining deposits or excessive lateral runout
or thickness variation is evident.
A sanding rotor attachment (Fig. 33) will remove
surface contamination without removing much rotor
material.
It will generally follow variations in thickness that
are in the rotor.
Fig. 32 Refacing Brake Rotor
Fig. 33 Resurfacing Brake Rotor (Final Finish)
Fig. 34 Front Rotor Thickness Markings
Fig. 35 Rear Rotor Thickness Markings
NSBRAKES 5 - 23
SERVICE PROCEDURES (Continued)
Page 106 of 1938
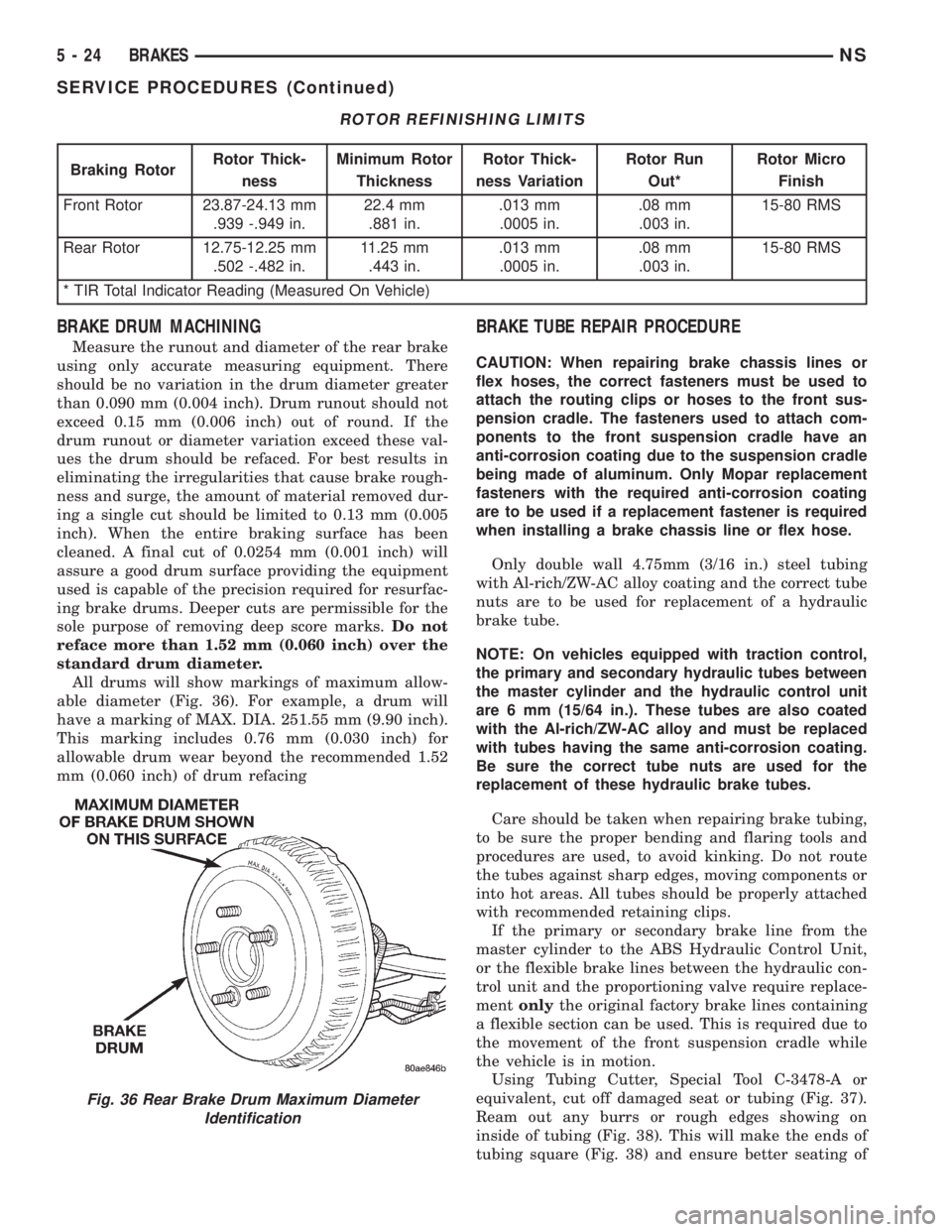
BRAKE DRUM MACHINING
Measure the runout and diameter of the rear brake
using only accurate measuring equipment. There
should be no variation in the drum diameter greater
than 0.090 mm (0.004 inch). Drum runout should not
exceed 0.15 mm (0.006 inch) out of round. If the
drum runout or diameter variation exceed these val-
ues the drum should be refaced. For best results in
eliminating the irregularities that cause brake rough-
ness and surge, the amount of material removed dur-
ing a single cut should be limited to 0.13 mm (0.005
inch). When the entire braking surface has been
cleaned. A final cut of 0.0254 mm (0.001 inch) will
assure a good drum surface providing the equipment
used is capable of the precision required for resurfac-
ing brake drums. Deeper cuts are permissible for the
sole purpose of removing deep score marks.Do not
reface more than 1.52 mm (0.060 inch) over the
standard drum diameter.
All drums will show markings of maximum allow-
able diameter (Fig. 36). For example, a drum will
have a marking of MAX. DIA. 251.55 mm (9.90 inch).
This marking includes 0.76 mm (0.030 inch) for
allowable drum wear beyond the recommended 1.52
mm (0.060 inch) of drum refacing
BRAKE TUBE REPAIR PROCEDURE
CAUTION: When repairing brake chassis lines or
flex hoses, the correct fasteners must be used to
attach the routing clips or hoses to the front sus-
pension cradle. The fasteners used to attach com-
ponents to the front suspension cradle have an
anti-corrosion coating due to the suspension cradle
being made of aluminum. Only Mopar replacement
fasteners with the required anti-corrosion coating
are to be used if a replacement fastener is required
when installing a brake chassis line or flex hose.
Only double wall 4.75mm (3/16 in.) steel tubing
with Al-rich/ZW-AC alloy coating and the correct tube
nuts are to be used for replacement of a hydraulic
brake tube.
NOTE: On vehicles equipped with traction control,
the primary and secondary hydraulic tubes between
the master cylinder and the hydraulic control unit
are 6 mm (15/64 in.). These tubes are also coated
with the Al-rich/ZW-AC alloy and must be replaced
with tubes having the same anti-corrosion coating.
Be sure the correct tube nuts are used for the
replacement of these hydraulic brake tubes.
Care should be taken when repairing brake tubing,
to be sure the proper bending and flaring tools and
procedures are used, to avoid kinking. Do not route
the tubes against sharp edges, moving components or
into hot areas. All tubes should be properly attached
with recommended retaining clips.
If the primary or secondary brake line from the
master cylinder to the ABS Hydraulic Control Unit,
or the flexible brake lines between the hydraulic con-
trol unit and the proportioning valve require replace-
mentonlythe original factory brake lines containing
a flexible section can be used. This is required due to
the movement of the front suspension cradle while
the vehicle is in motion.
Using Tubing Cutter, Special Tool C-3478-A or
equivalent, cut off damaged seat or tubing (Fig. 37).
Ream out any burrs or rough edges showing on
inside of tubing (Fig. 38). This will make the ends of
tubing square (Fig. 38) and ensure better seating of
ROTOR REFINISHING LIMITS
Braking RotorRotor Thick-
nessMinimum Rotor
ThicknessRotor Thick-
ness VariationRotor Run
Out*Rotor Micro
Finish
Front Rotor 23.87-24.13 mm
.939 -.949 in.22.4 mm
.881 in..013 mm
.0005 in..08 mm
.003 in.15-80 RMS
Rear Rotor 12.75-12.25 mm
.502 -.482 in.11.25 mm
.443 in..013 mm
.0005 in..08 mm
.003 in.15-80 RMS
* TIR Total Indicator Reading (Measured On Vehicle)
Fig. 36 Rear Brake Drum Maximum Diameter
Identification
5 - 24 BRAKESNS
SERVICE PROCEDURES (Continued)
Page 107 of 1938
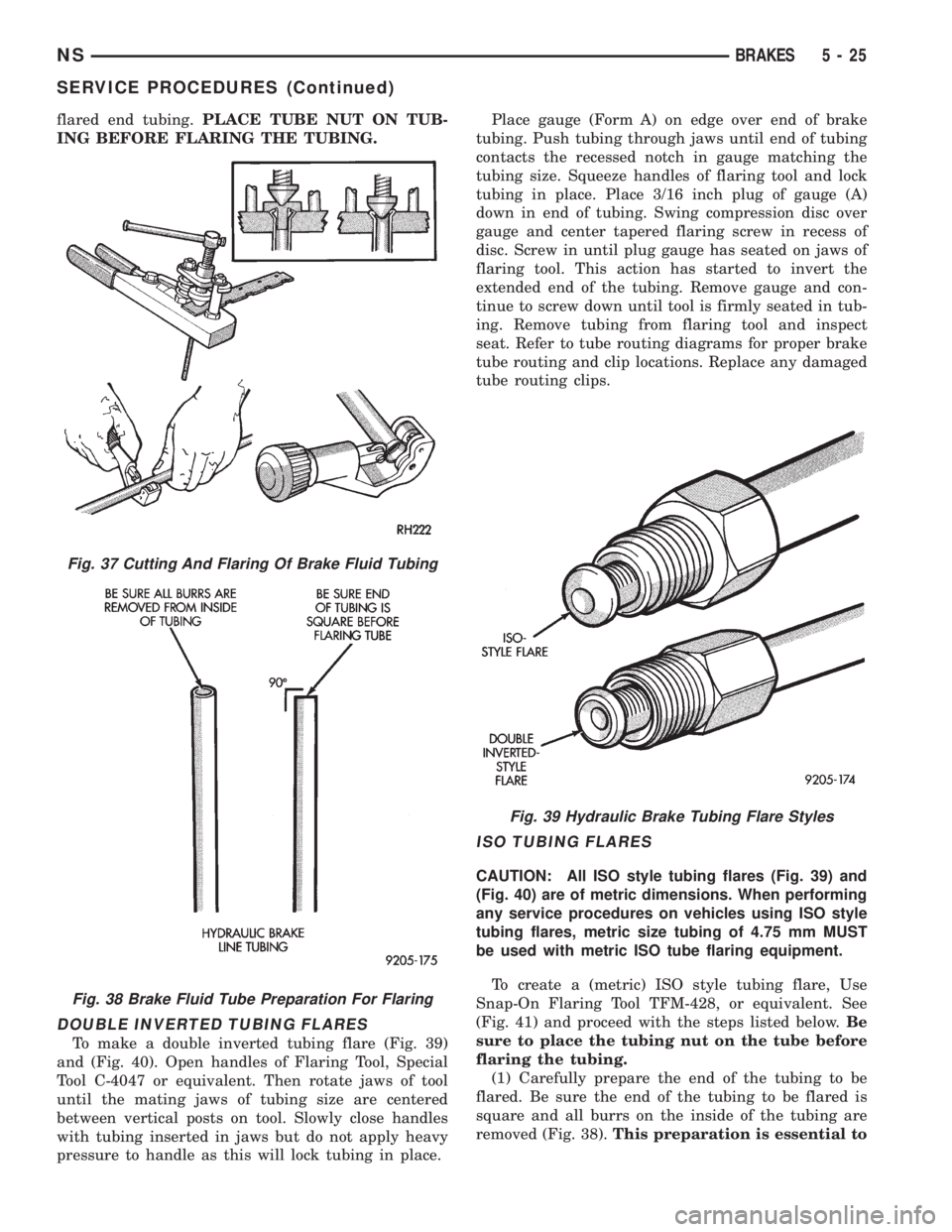
flared end tubing.PLACE TUBE NUT ON TUB-
ING BEFORE FLARING THE TUBING.
DOUBLE INVERTED TUBING FLARES
To make a double inverted tubing flare (Fig. 39)
and (Fig. 40). Open handles of Flaring Tool, Special
Tool C-4047 or equivalent. Then rotate jaws of tool
until the mating jaws of tubing size are centered
between vertical posts on tool. Slowly close handles
with tubing inserted in jaws but do not apply heavy
pressure to handle as this will lock tubing in place.Place gauge (Form A) on edge over end of brake
tubing. Push tubing through jaws until end of tubing
contacts the recessed notch in gauge matching the
tubing size. Squeeze handles of flaring tool and lock
tubing in place. Place 3/16 inch plug of gauge (A)
down in end of tubing. Swing compression disc over
gauge and center tapered flaring screw in recess of
disc. Screw in until plug gauge has seated on jaws of
flaring tool. This action has started to invert the
extended end of the tubing. Remove gauge and con-
tinue to screw down until tool is firmly seated in tub-
ing. Remove tubing from flaring tool and inspect
seat. Refer to tube routing diagrams for proper brake
tube routing and clip locations. Replace any damaged
tube routing clips.
ISO TUBING FLARES
CAUTION: All ISO style tubing flares (Fig. 39) and
(Fig. 40) are of metric dimensions. When performing
any service procedures on vehicles using ISO style
tubing flares, metric size tubing of 4.75 mm MUST
be used with metric ISO tube flaring equipment.
To create a (metric) ISO style tubing flare, Use
Snap-On Flaring Tool TFM-428, or equivalent. See
(Fig. 41) and proceed with the steps listed below.Be
sure to place the tubing nut on the tube before
flaring the tubing.
(1) Carefully prepare the end of the tubing to be
flared. Be sure the end of the tubing to be flared is
square and all burrs on the inside of the tubing are
removed (Fig. 38).This preparation is essential to
Fig. 37 Cutting And Flaring Of Brake Fluid Tubing
Fig. 38 Brake Fluid Tube Preparation For Flaring
Fig. 39 Hydraulic Brake Tubing Flare Styles
NSBRAKES 5 - 25
SERVICE PROCEDURES (Continued)
Page 108 of 1938
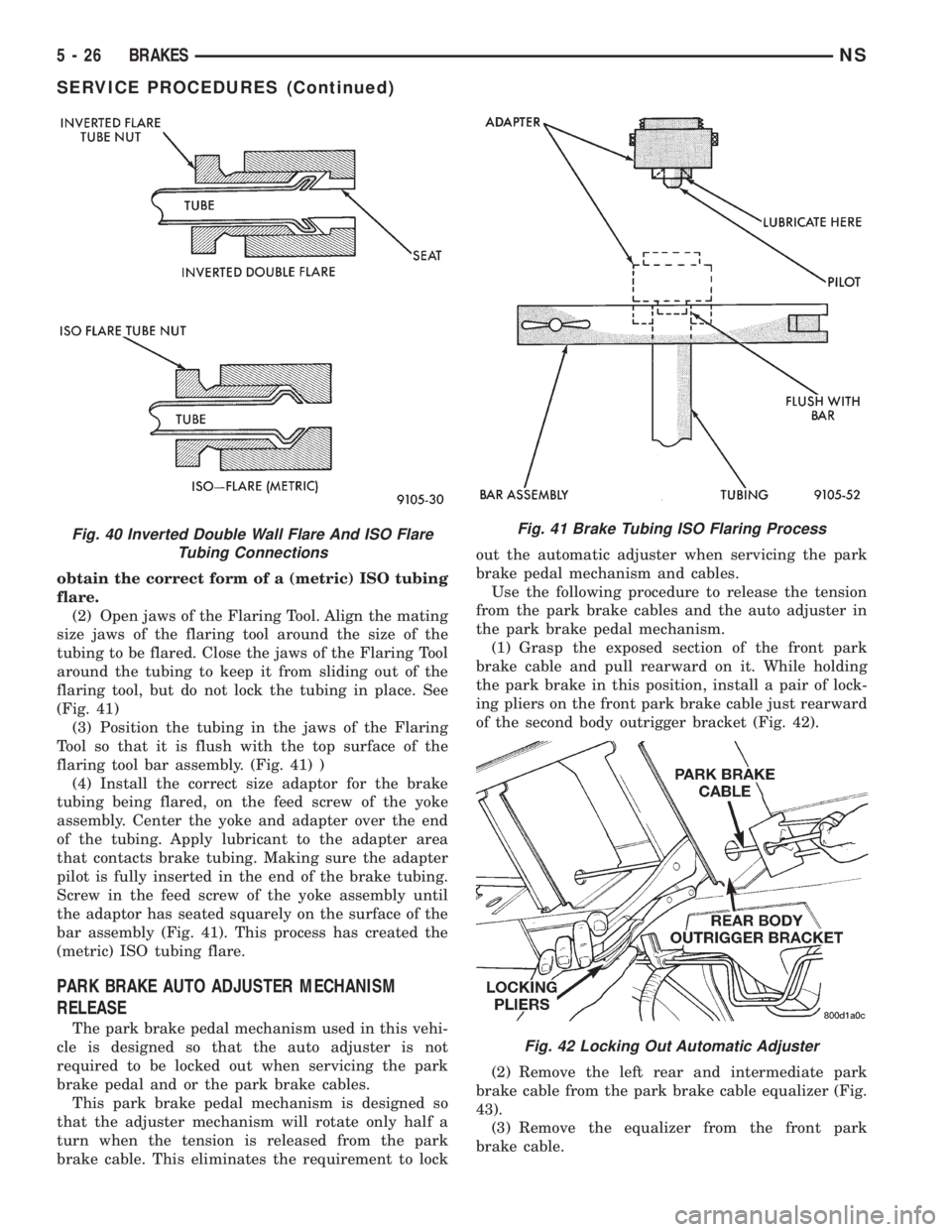
obtain the correct form of a (metric) ISO tubing
flare.
(2) Open jaws of the Flaring Tool. Align the mating
size jaws of the flaring tool around the size of the
tubing to be flared. Close the jaws of the Flaring Tool
around the tubing to keep it from sliding out of the
flaring tool, but do not lock the tubing in place. See
(Fig. 41)
(3) Position the tubing in the jaws of the Flaring
Tool so that it is flush with the top surface of the
flaring tool bar assembly. (Fig. 41) )
(4) Install the correct size adaptor for the brake
tubing being flared, on the feed screw of the yoke
assembly. Center the yoke and adapter over the end
of the tubing. Apply lubricant to the adapter area
that contacts brake tubing. Making sure the adapter
pilot is fully inserted in the end of the brake tubing.
Screw in the feed screw of the yoke assembly until
the adaptor has seated squarely on the surface of the
bar assembly (Fig. 41). This process has created the
(metric) ISO tubing flare.
PARK BRAKE AUTO ADJUSTER MECHANISM
RELEASE
The park brake pedal mechanism used in this vehi-
cle is designed so that the auto adjuster is not
required to be locked out when servicing the park
brake pedal and or the park brake cables.
This park brake pedal mechanism is designed so
that the adjuster mechanism will rotate only half a
turn when the tension is released from the park
brake cable. This eliminates the requirement to lockout the automatic adjuster when servicing the park
brake pedal mechanism and cables.
Use the following procedure to release the tension
from the park brake cables and the auto adjuster in
the park brake pedal mechanism.
(1) Grasp the exposed section of the front park
brake cable and pull rearward on it. While holding
the park brake in this position, install a pair of lock-
ing pliers on the front park brake cable just rearward
of the second body outrigger bracket (Fig. 42).
(2) Remove the left rear and intermediate park
brake cable from the park brake cable equalizer (Fig.
43).
(3) Remove the equalizer from the front park
brake cable.
Fig. 40 Inverted Double Wall Flare And ISO Flare
Tubing ConnectionsFig. 41 Brake Tubing ISO Flaring Process
Fig. 42 Locking Out Automatic Adjuster
5 - 26 BRAKESNS
SERVICE PROCEDURES (Continued)
Page 109 of 1938
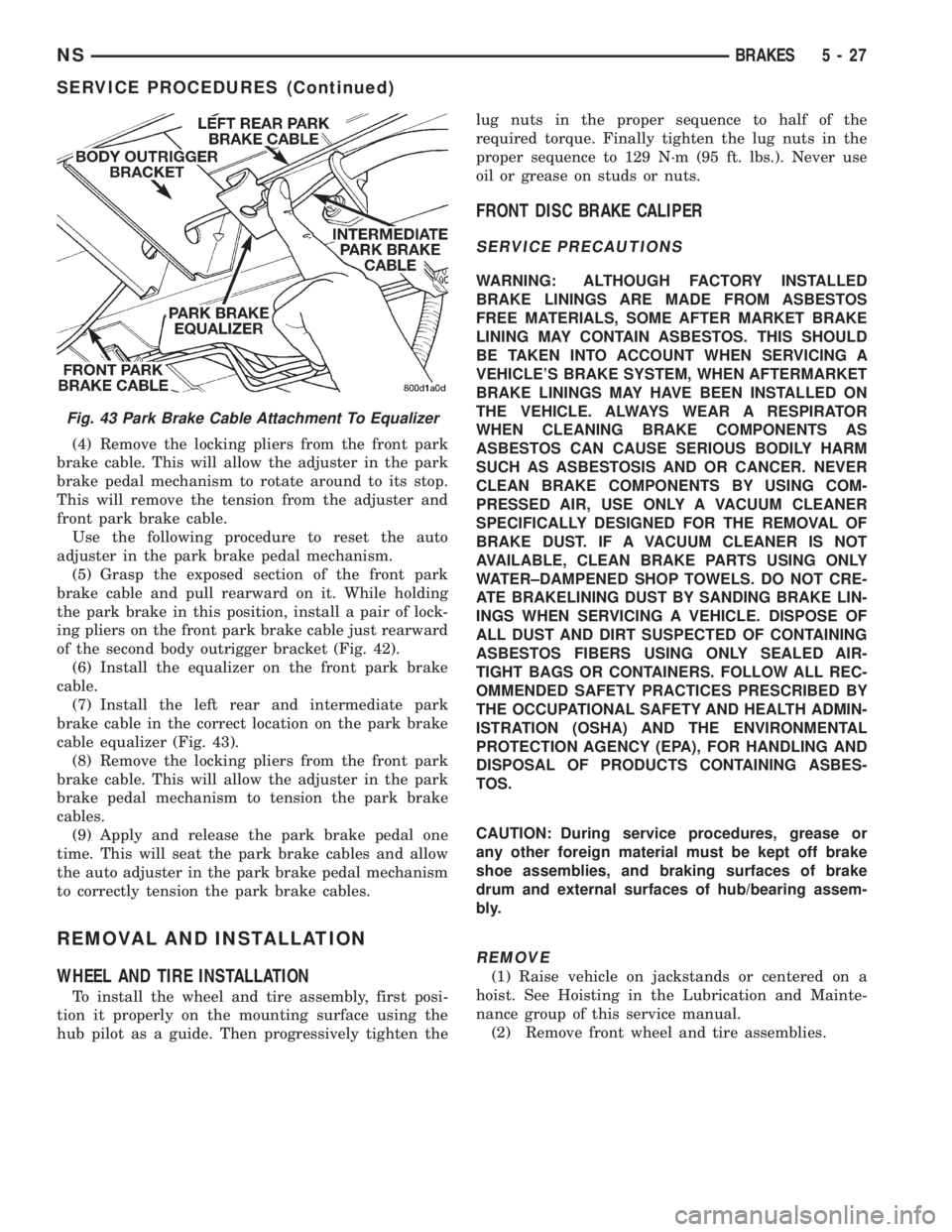
(4) Remove the locking pliers from the front park
brake cable. This will allow the adjuster in the park
brake pedal mechanism to rotate around to its stop.
This will remove the tension from the adjuster and
front park brake cable.
Use the following procedure to reset the auto
adjuster in the park brake pedal mechanism.
(5) Grasp the exposed section of the front park
brake cable and pull rearward on it. While holding
the park brake in this position, install a pair of lock-
ing pliers on the front park brake cable just rearward
of the second body outrigger bracket (Fig. 42).
(6) Install the equalizer on the front park brake
cable.
(7) Install the left rear and intermediate park
brake cable in the correct location on the park brake
cable equalizer (Fig. 43).
(8) Remove the locking pliers from the front park
brake cable. This will allow the adjuster in the park
brake pedal mechanism to tension the park brake
cables.
(9) Apply and release the park brake pedal one
time. This will seat the park brake cables and allow
the auto adjuster in the park brake pedal mechanism
to correctly tension the park brake cables.
REMOVAL AND INSTALLATION
WHEEL AND TIRE INSTALLATION
To install the wheel and tire assembly, first posi-
tion it properly on the mounting surface using the
hub pilot as a guide. Then progressively tighten thelug nuts in the proper sequence to half of the
required torque. Finally tighten the lug nuts in the
proper sequence to 129 N´m (95 ft. lbs.). Never use
oil or grease on studs or nuts.
FRONT DISC BRAKE CALIPER
SERVICE PRECAUTIONS
WARNING: ALTHOUGH FACTORY INSTALLED
BRAKE LININGS ARE MADE FROM ASBESTOS
FREE MATERIALS, SOME AFTER MARKET BRAKE
LINING MAY CONTAIN ASBESTOS. THIS SHOULD
BE TAKEN INTO ACCOUNT WHEN SERVICING A
VEHICLE'S BRAKE SYSTEM, WHEN AFTERMARKET
BRAKE LININGS MAY HAVE BEEN INSTALLED ON
THE VEHICLE. ALWAYS WEAR A RESPIRATOR
WHEN CLEANING BRAKE COMPONENTS AS
ASBESTOS CAN CAUSE SERIOUS BODILY HARM
SUCH AS ASBESTOSIS AND OR CANCER. NEVER
CLEAN BRAKE COMPONENTS BY USING COM-
PRESSED AIR, USE ONLY A VACUUM CLEANER
SPECIFICALLY DESIGNED FOR THE REMOVAL OF
BRAKE DUST. IF A VACUUM CLEANER IS NOT
AVAILABLE, CLEAN BRAKE PARTS USING ONLY
WATER±DAMPENED SHOP TOWELS. DO NOT CRE-
ATE BRAKELINING DUST BY SANDING BRAKE LIN-
INGS WHEN SERVICING A VEHICLE. DISPOSE OF
ALL DUST AND DIRT SUSPECTED OF CONTAINING
ASBESTOS FIBERS USING ONLY SEALED AIR-
TIGHT BAGS OR CONTAINERS. FOLLOW ALL REC-
OMMENDED SAFETY PRACTICES PRESCRIBED BY
THE OCCUPATIONAL SAFETY AND HEALTH ADMIN-
ISTRATION (OSHA) AND THE ENVIRONMENTAL
PROTECTION AGENCY (EPA), FOR HANDLING AND
DISPOSAL OF PRODUCTS CONTAINING ASBES-
TOS.
CAUTION: During service procedures, grease or
any other foreign material must be kept off brake
shoe assemblies, and braking surfaces of brake
drum and external surfaces of hub/bearing assem-
bly.
REMOVE
(1) Raise vehicle on jackstands or centered on a
hoist. See Hoisting in the Lubrication and Mainte-
nance group of this service manual.
(2) Remove front wheel and tire assemblies.
Fig. 43 Park Brake Cable Attachment To Equalizer
NSBRAKES 5 - 27
SERVICE PROCEDURES (Continued)
Page 110 of 1938
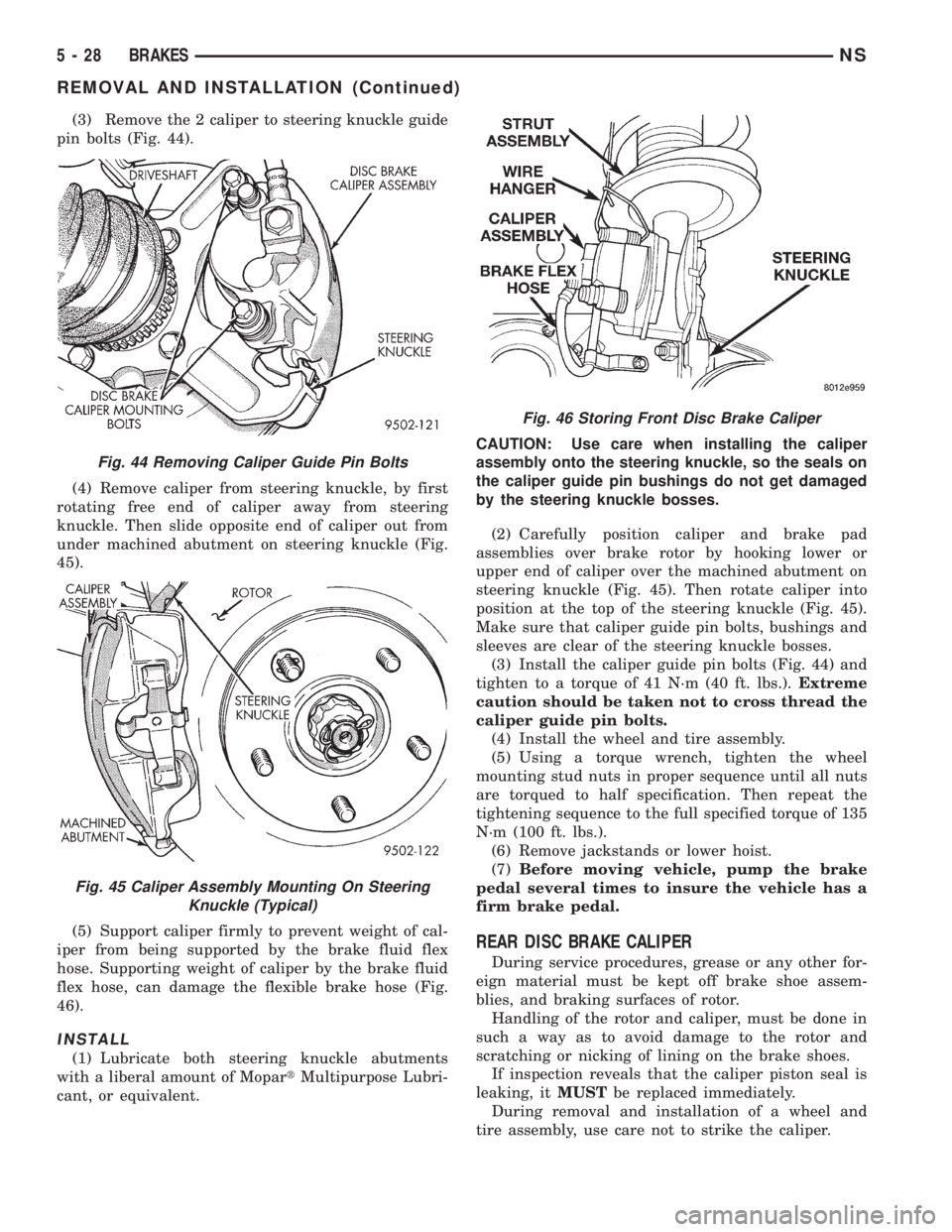
(3) Remove the 2 caliper to steering knuckle guide
pin bolts (Fig. 44).
(4) Remove caliper from steering knuckle, by first
rotating free end of caliper away from steering
knuckle. Then slide opposite end of caliper out from
under machined abutment on steering knuckle (Fig.
45).
(5) Support caliper firmly to prevent weight of cal-
iper from being supported by the brake fluid flex
hose. Supporting weight of caliper by the brake fluid
flex hose, can damage the flexible brake hose (Fig.
46).
INSTALL
(1) Lubricate both steering knuckle abutments
with a liberal amount of MopartMultipurpose Lubri-
cant, or equivalent.CAUTION: Use care when installing the caliper
assembly onto the steering knuckle, so the seals on
the caliper guide pin bushings do not get damaged
by the steering knuckle bosses.
(2) Carefully position caliper and brake pad
assemblies over brake rotor by hooking lower or
upper end of caliper over the machined abutment on
steering knuckle (Fig. 45). Then rotate caliper into
position at the top of the steering knuckle (Fig. 45).
Make sure that caliper guide pin bolts, bushings and
sleeves are clear of the steering knuckle bosses.
(3) Install the caliper guide pin bolts (Fig. 44) and
tighten to a torque of 41 N´m (40 ft. lbs.).Extreme
caution should be taken not to cross thread the
caliper guide pin bolts.
(4) Install the wheel and tire assembly.
(5) Using a torque wrench, tighten the wheel
mounting stud nuts in proper sequence until all nuts
are torqued to half specification. Then repeat the
tightening sequence to the full specified torque of 135
N´m (100 ft. lbs.).
(6) Remove jackstands or lower hoist.
(7)Before moving vehicle, pump the brake
pedal several times to insure the vehicle has a
firm brake pedal.
REAR DISC BRAKE CALIPER
During service procedures, grease or any other for-
eign material must be kept off brake shoe assem-
blies, and braking surfaces of rotor.
Handling of the rotor and caliper, must be done in
such a way as to avoid damage to the rotor and
scratching or nicking of lining on the brake shoes.
If inspection reveals that the caliper piston seal is
leaking, itMUSTbe replaced immediately.
During removal and installation of a wheel and
tire assembly, use care not to strike the caliper.
Fig. 44 Removing Caliper Guide Pin Bolts
Fig. 45 Caliper Assembly Mounting On Steering
Knuckle (Typical)
Fig. 46 Storing Front Disc Brake Caliper
5 - 28 BRAKESNS
REMOVAL AND INSTALLATION (Continued)