LAND ROVER DISCOVERY 2002 Workshop Manual
Manufacturer: LAND ROVER, Model Year: 2002, Model line: DISCOVERY, Model: LAND ROVER DISCOVERY 2002Pages: 1672, PDF Size: 46.1 MB
Page 411 of 1672
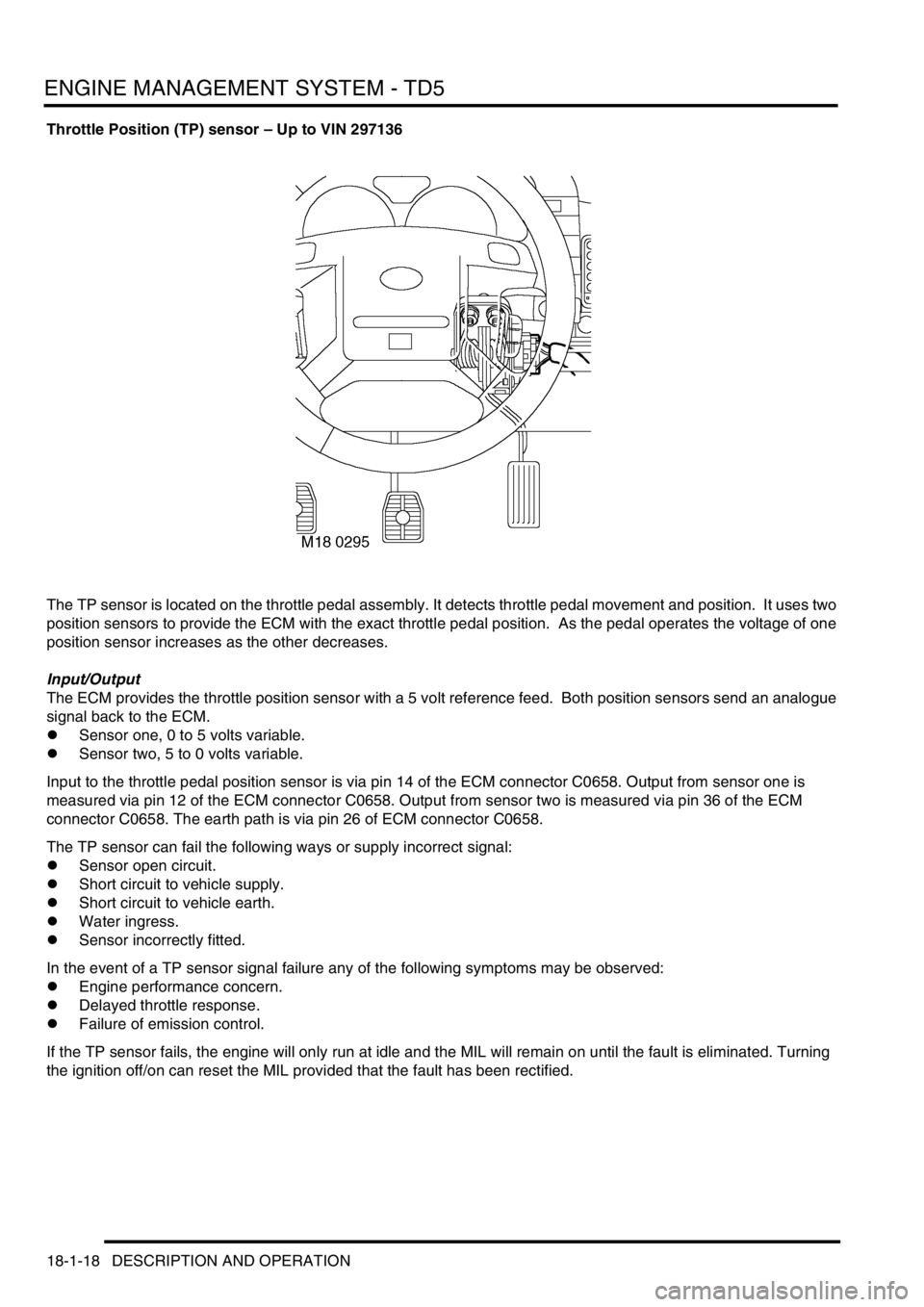
ENGINE MANAGEMENT SYSTEM - TD5
18-1-18 DESCRIPTION AND OPERATION
Throttle Position (TP) sensor – Up to VIN 297136
The TP sensor is located on the throttle pedal assembly. It detects throttle pedal movement and position. It uses two
position sensors to provide the ECM with the exact throttle pedal position. As the pedal operates the voltage of one
position sensor increases as the other decreases.
Input/Output
The ECM provides the throttle position sensor with a 5 volt reference feed. Both position sensors send an analogue
signal back to the ECM.
lSensor one, 0 to 5 volts variable.
lSensor two, 5 to 0 volts variable.
Input to the throttle pedal position sensor is via pin 14 of the ECM connector C0658. Output from sensor one is
measured via pin 12 of the ECM connector C0658. Output from sensor two is measured via pin 36 of the ECM
connector C0658. The earth path is via pin 26 of ECM connector C0658.
The TP sensor can fail the following ways or supply incorrect signal:
lSensor open circuit.
lShort circuit to vehicle supply.
lShort circuit to vehicle earth.
lWater ingress.
lSensor incorrectly fitted.
In the event of a TP sensor signal failure any of the following symptoms may be observed:
lEngine performance concern.
lDelayed throttle response.
lFailure of emission control.
If the TP sensor fails, the engine will only run at idle and the MIL will remain on until the fault is eliminated. Turning
the ignition off/on can reset the MIL provided that the fault has been rectified.
Page 412 of 1672
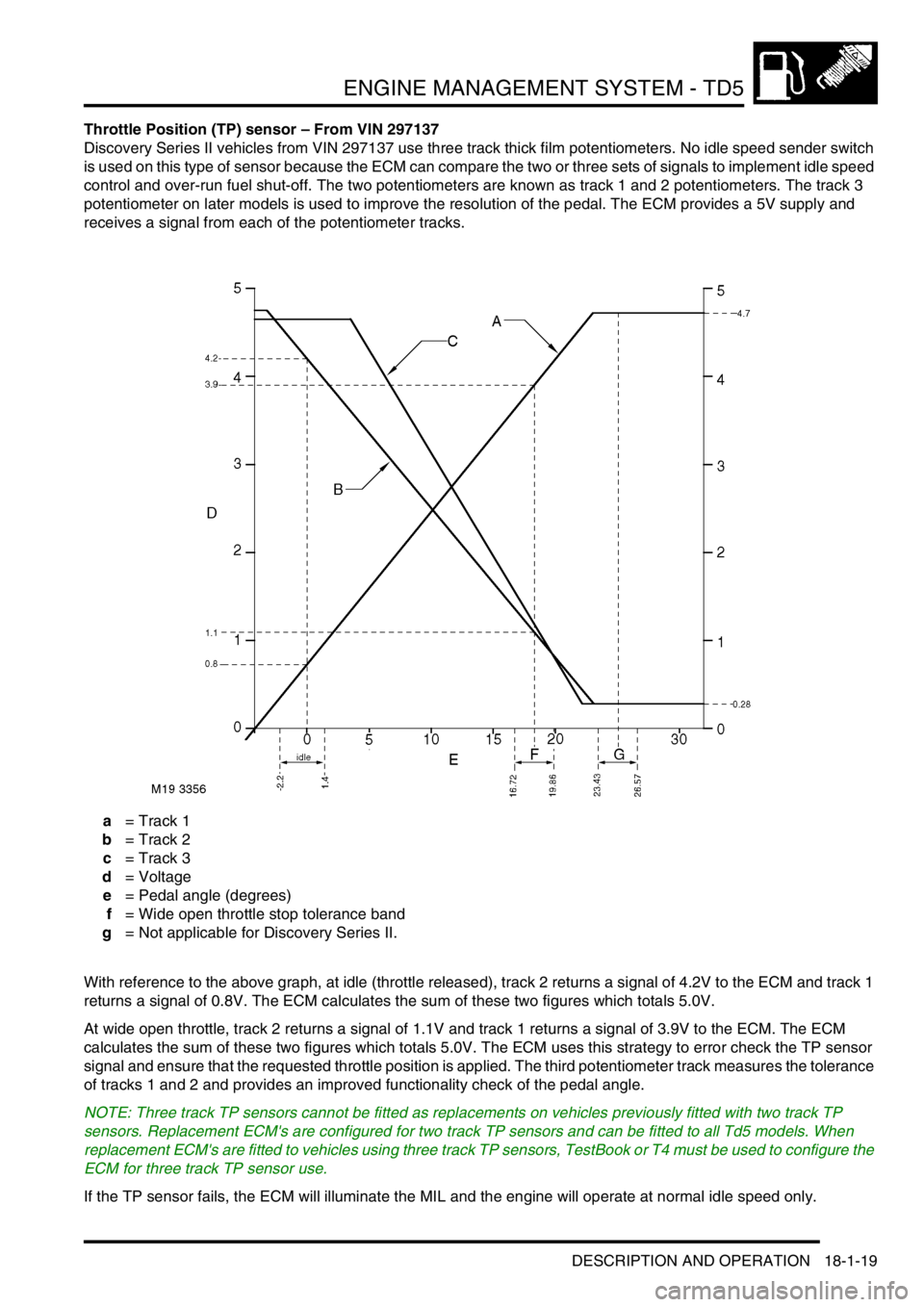
ENGINE MANAGEMENT SYSTEM - TD5
DESCRIPTION AND OPERATION 18-1-19
Throttle Position (TP) sensor – From VIN 297137
Discovery Series II vehicles from VIN 297137 use three track thick film potentiometers. No idle speed sender switch
is used on this type of sensor because the ECM can compare the two or three sets of signals to implement idle speed
control and over-run fuel shut-off. The two potentiometers are known as track 1 and 2 potentiometers. The track 3
potentiometer on later models is used to improve the resolution of the pedal. The ECM provides a 5V supply and
receives a signal from each of the potentiometer tracks.
a = Track 1
b = Track 2
c = Track 3
d = Voltage
e = Pedal angle (degrees)
f = Wide open throttle stop tolerance band
g = Not applicable for Discovery Series II.
With reference to the above graph, at idle (throttle released), track 2 returns a signal of 4.2V to the ECM and track 1
returns a signal of 0.8V. The ECM calculates the sum of these two figures which totals 5.0V.
At wide open throttle, track 2 returns a signal of 1.1V and track 1 returns a signal of 3.9V to the ECM. The ECM
calculates the sum of these two figures which totals 5.0V. The ECM uses this strategy to error check the TP sensor
signal and ensure that the requested throttle position is applied. The third potentiometer track measures the tolerance
of tracks 1 and 2 and provides an improved functionality check of the pedal angle.
NOTE: Three track TP sensors cannot be fitted as replacements on vehicles previously fitted with two track TP
sensors. Replacement ECM's are configured for two track TP sensors and can be fitted to all Td5 models. When
replacement ECM's are fitted to vehicles using three track TP sensors, TestBook or T4 must be used to configure the
ECM for three track TP sensor use.
If the TP sensor fails, the ECM will illuminate the MIL and the engine will operate at normal idle speed only.
Page 413 of 1672
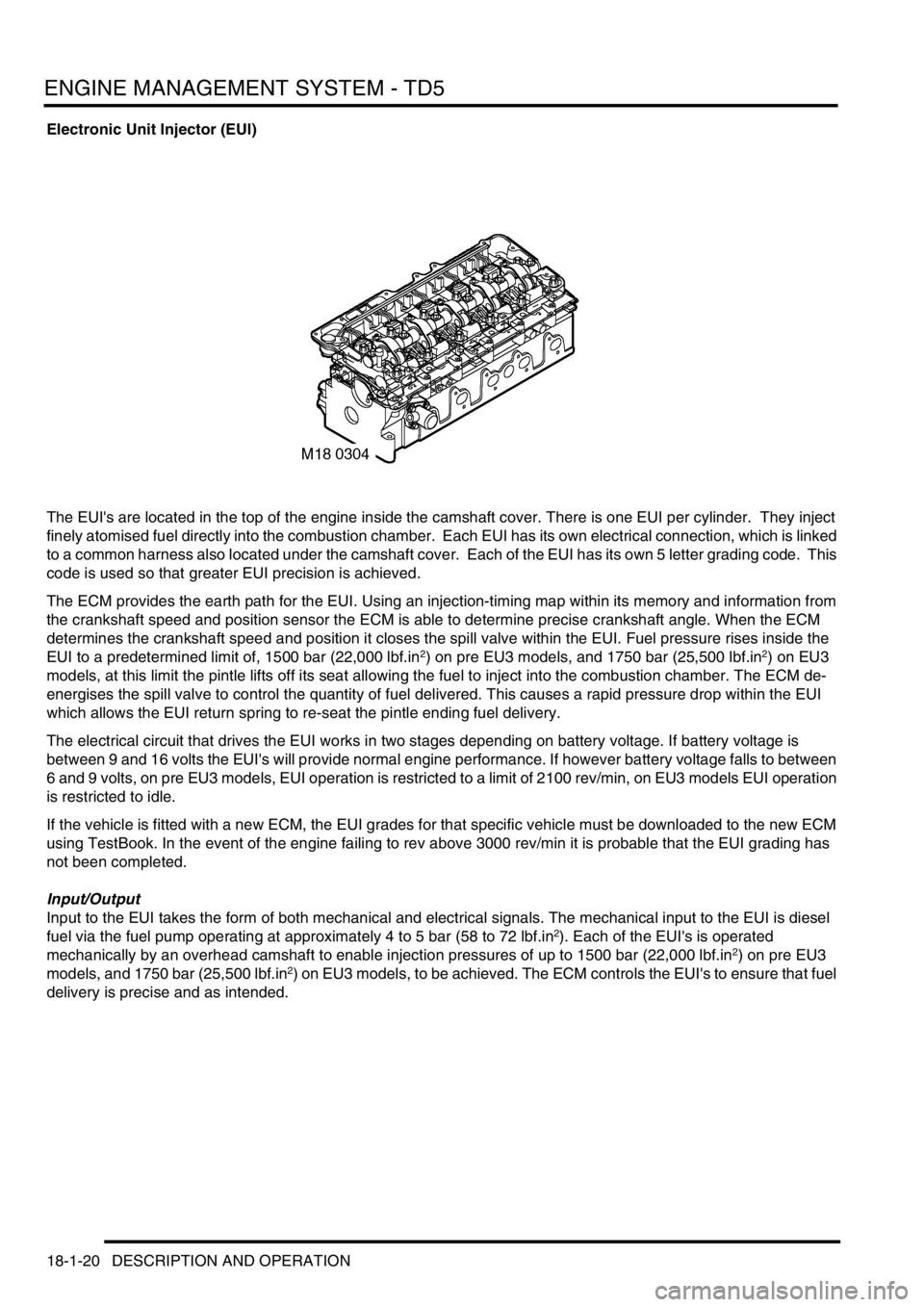
ENGINE MANAGEMENT SYSTEM - TD5
18-1-20 DESCRIPTION AND OPERATION
Electronic Unit Injector (EUI)
The EUI's are located in the top of the engine inside the camshaft cover. There is one EUI per cylinder. They inject
finely atomised fuel directly into the combustion chamber. Each EUI has its own electrical connection, which is linked
to a common harness also located under the camshaft cover. Each of the EUI has its own 5 letter grading code. This
code is used so that greater EUI precision is achieved.
The ECM provides the earth path for the EUI. Using an injection-timing map within its memory and information from
the crankshaft speed and position sensor the ECM is able to determine precise crankshaft angle. When the ECM
determines the crankshaft speed and position it closes the spill valve within the EUI. Fuel pressure rises inside the
EUI to a predetermined limit of, 1500 bar (22,000 lbf.in
2) on pre EU3 models, and 1750 bar (25,500 lbf.in2) on EU3
models, at this limit the pintle lifts off its seat allowing the fuel to inject into the combustion chamber. The ECM de-
energises the spill valve to control the quantity of fuel delivered. This causes a rapid pressure drop within the EUI
which allows the EUI return spring to re-seat the pintle ending fuel delivery.
The electrical circuit that drives the EUI works in two stages depending on battery voltage. If battery voltage is
between 9 and 16 volts the EUI's will provide normal engine performance. If however battery voltage falls to between
6 and 9 volts, on pre EU3 models, EUI operation is restricted to a limit of 2100 rev/min, on EU3 models EUI operation
is restricted to idle.
If the vehicle is fitted with a new ECM, the EUI grades for that specific vehicle must be downloaded to the new ECM
using TestBook. In the event of the engine failing to rev above 3000 rev/min it is probable that the EUI grading has
not been completed.
Input/Output
Input to the EUI takes the form of both mechanical and electrical signals. The mechanical input to the EUI is diesel
fuel via the fuel pump operating at approximately 4 to 5 bar (58 to 72 lbf.in
2). Each of the EUI's is operated
mechanically by an overhead camshaft to enable injection pressures of up to 1500 bar (22,000 lbf.in2) on pre EU3
models, and 1750 bar (25,500 lbf.in2) on EU3 models, to be achieved. The ECM controls the EUI's to ensure that fuel
delivery is precise and as intended.
Page 414 of 1672
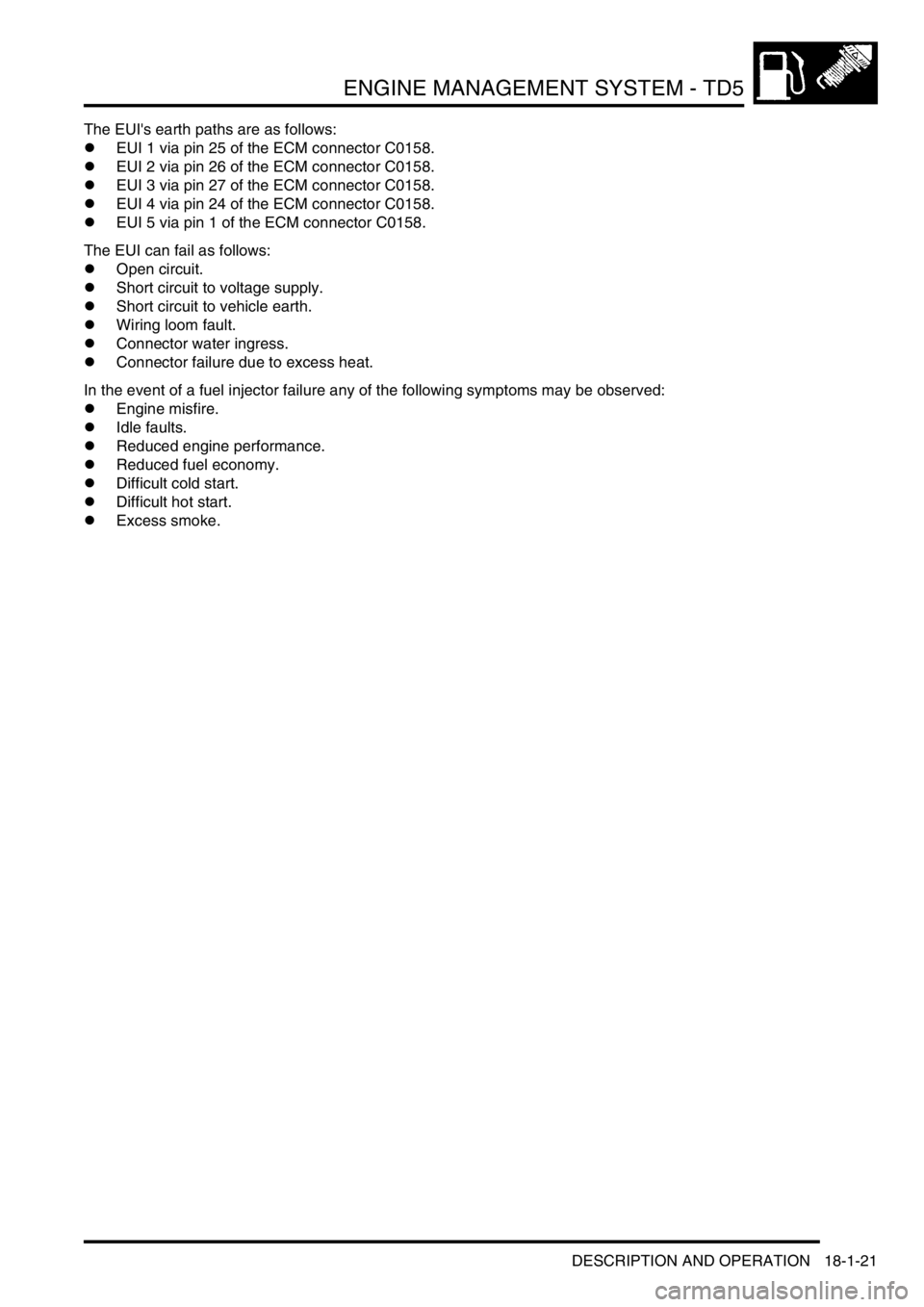
ENGINE MANAGEMENT SYSTEM - TD5
DESCRIPTION AND OPERATION 18-1-21
The EUI's earth paths are as follows:
lEUI 1 via pin 25 of the ECM connector C0158.
lEUI 2 via pin 26 of the ECM connector C0158.
lEUI 3 via pin 27 of the ECM connector C0158.
lEUI 4 via pin 24 of the ECM connector C0158.
lEUI 5 via pin 1 of the ECM connector C0158.
The EUI can fail as follows:
lOpen circuit.
lShort circuit to voltage supply.
lShort circuit to vehicle earth.
lWiring loom fault.
lConnector water ingress.
lConnector failure due to excess heat.
In the event of a fuel injector failure any of the following symptoms may be observed:
lEngine misfire.
lIdle faults.
lReduced engine performance.
lReduced fuel economy.
lDifficult cold start.
lDifficult hot start.
lExcess smoke.
Page 415 of 1672
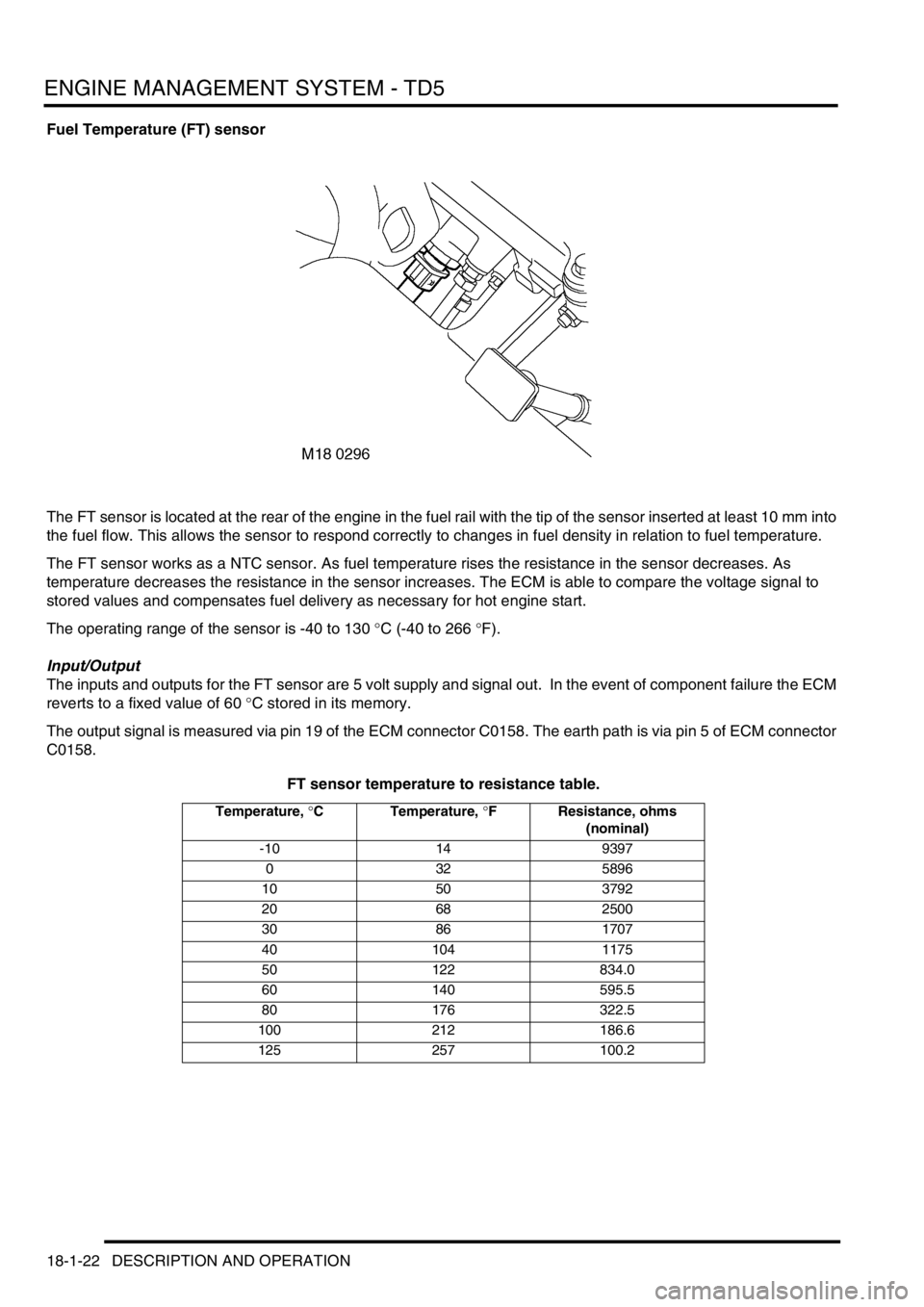
ENGINE MANAGEMENT SYSTEM - TD5
18-1-22 DESCRIPTION AND OPERATION
Fuel Temperature (FT) sensor
The FT sensor is located at the rear of the engine in the fuel rail with the tip of the sensor inserted at least 10 mm into
the fuel flow. This allows the sensor to respond correctly to changes in fuel density in relation to fuel temperature.
The FT sensor works as a NTC sensor. As fuel temperature rises the resistance in the sensor decreases. As
temperature decreases the resistance in the sensor increases. The ECM is able to compare the voltage signal to
stored values and compensates fuel delivery as necessary for hot engine start.
The operating range of the sensor is -40 to 130
°C (-40 to 266 °F).
Input/Output
The inputs and outputs for the FT sensor are 5 volt supply and signal out. In the event of component failure the ECM
reverts to a fixed value of 60
°C stored in its memory.
The output signal is measured via pin 19 of the ECM connector C0158. The earth path is via pin 5 of ECM connector
C0158.
FT sensor temperature to resistance table.
Temperature, °C Temperature, °F Resistance, ohms
(nominal)
-10 14 9397
0325896
10 50 3792
20 68 2500
30 86 1707
40 104 1175
50 122 834.0
60 140 595.5
80 176 322.5
100 212 186.6
125 257 100.2
Page 416 of 1672
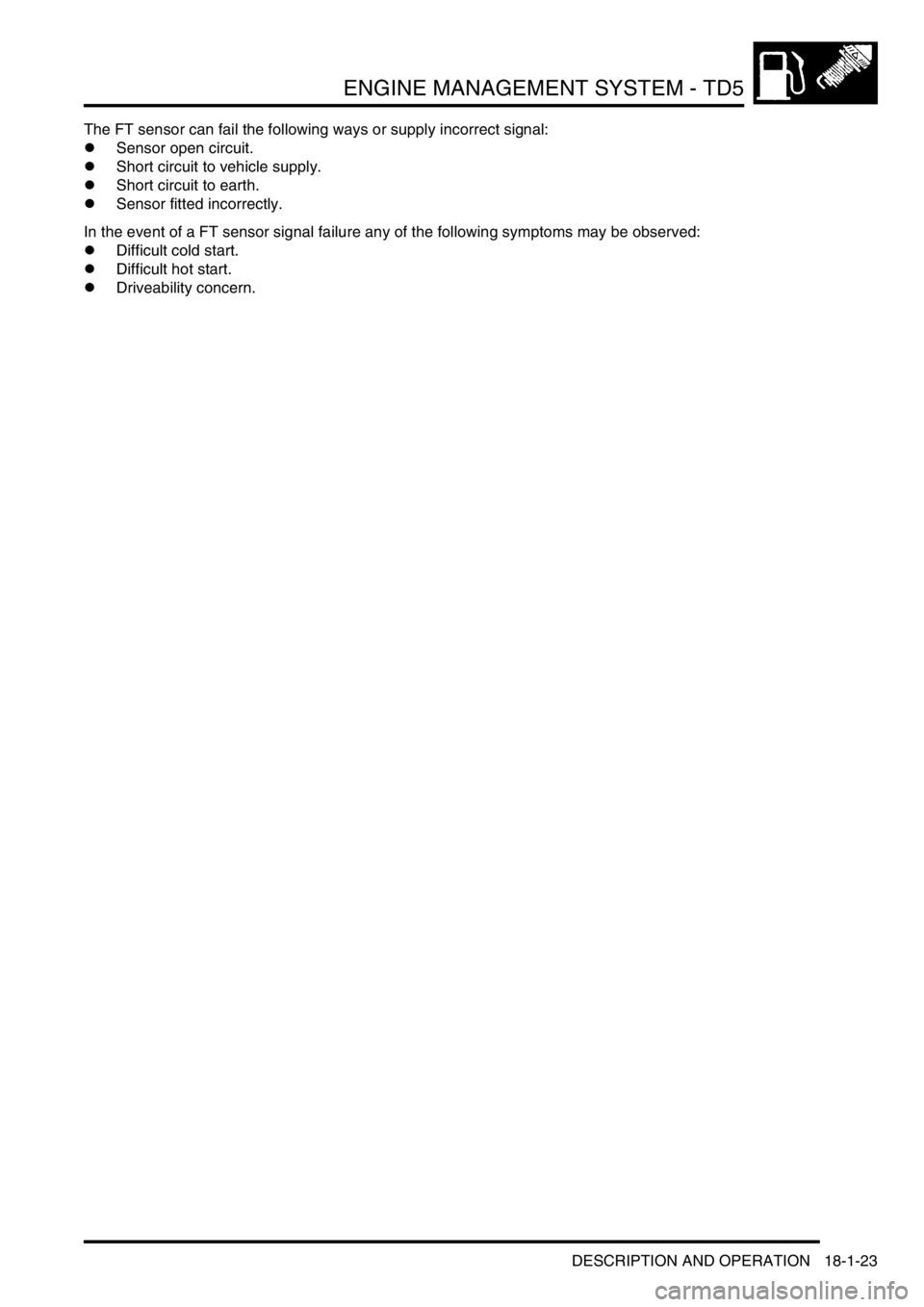
ENGINE MANAGEMENT SYSTEM - TD5
DESCRIPTION AND OPERATION 18-1-23
The FT sensor can fail the following ways or supply incorrect signal:
lSensor open circuit.
lShort circuit to vehicle supply.
lShort circuit to earth.
lSensor fitted incorrectly.
In the event of a FT sensor signal failure any of the following symptoms may be observed:
lDifficult cold start.
lDifficult hot start.
lDriveability concern.
Page 417 of 1672
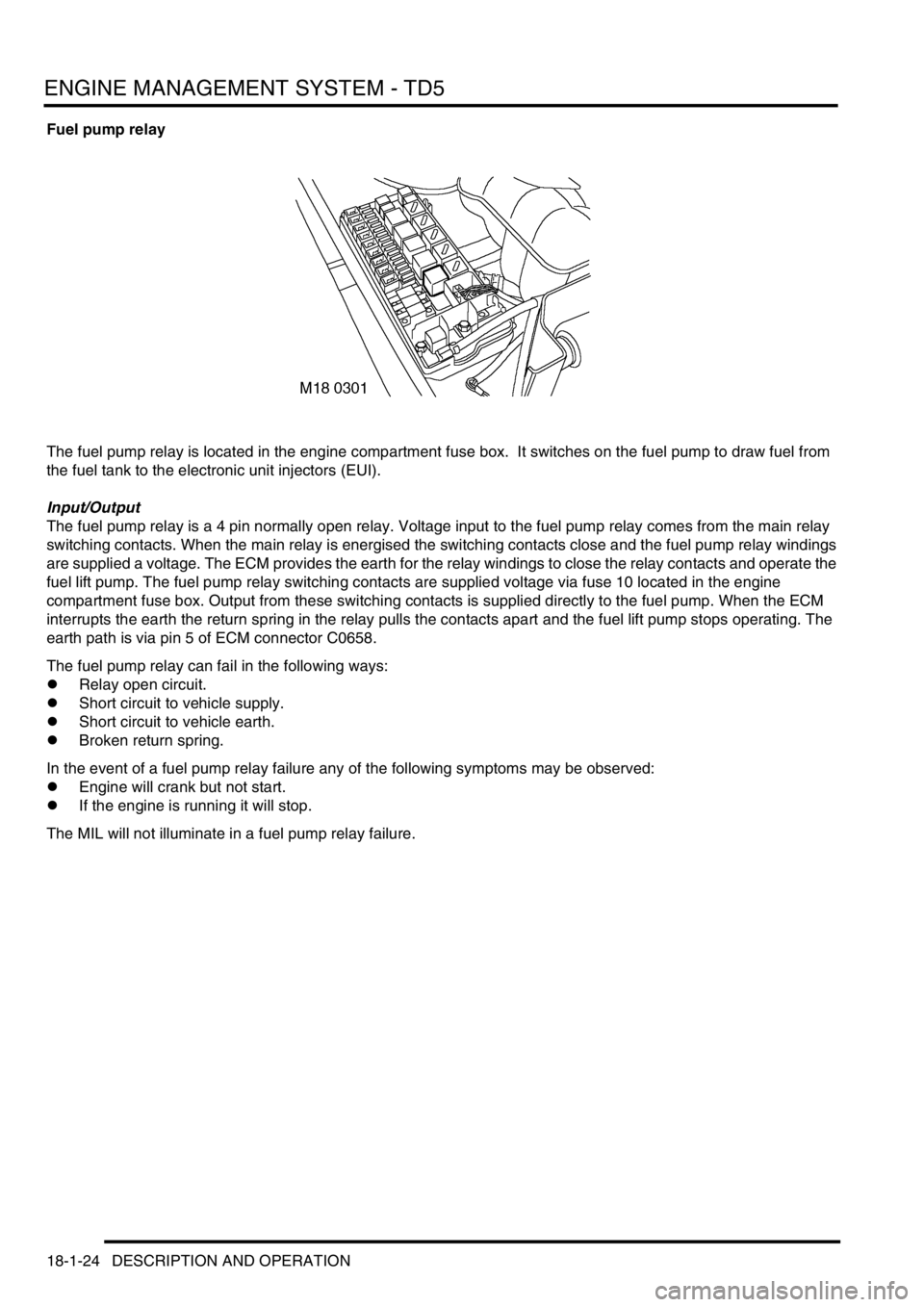
ENGINE MANAGEMENT SYSTEM - TD5
18-1-24 DESCRIPTION AND OPERATION
Fuel pump relay
The fuel pump relay is located in the engine compartment fuse box. It switches on the fuel pump to draw fuel from
the fuel tank to the electronic unit injectors (EUI).
Input/Output
The fuel pump relay is a 4 pin normally open relay. Voltage input to the fuel pump relay comes from the main relay
switching contacts. When the main relay is energised the switching contacts close and the fuel pump relay windings
are supplied a voltage. The ECM provides the earth for the relay windings to close the relay contacts and operate the
fuel lift pump. The fuel pump relay switching contacts are supplied voltage via fuse 10 located in the engine
compartment fuse box. Output from these switching contacts is supplied directly to the fuel pump. When the ECM
interrupts the earth the return spring in the relay pulls the contacts apart and the fuel lift pump stops operating. The
earth path is via pin 5 of ECM connector C0658.
The fuel pump relay can fail in the following ways:
lRelay open circuit.
lShort circuit to vehicle supply.
lShort circuit to vehicle earth.
lBroken return spring.
In the event of a fuel pump relay failure any of the following symptoms may be observed:
lEngine will crank but not start.
lIf the engine is running it will stop.
The MIL will not illuminate in a fuel pump relay failure.
Page 418 of 1672
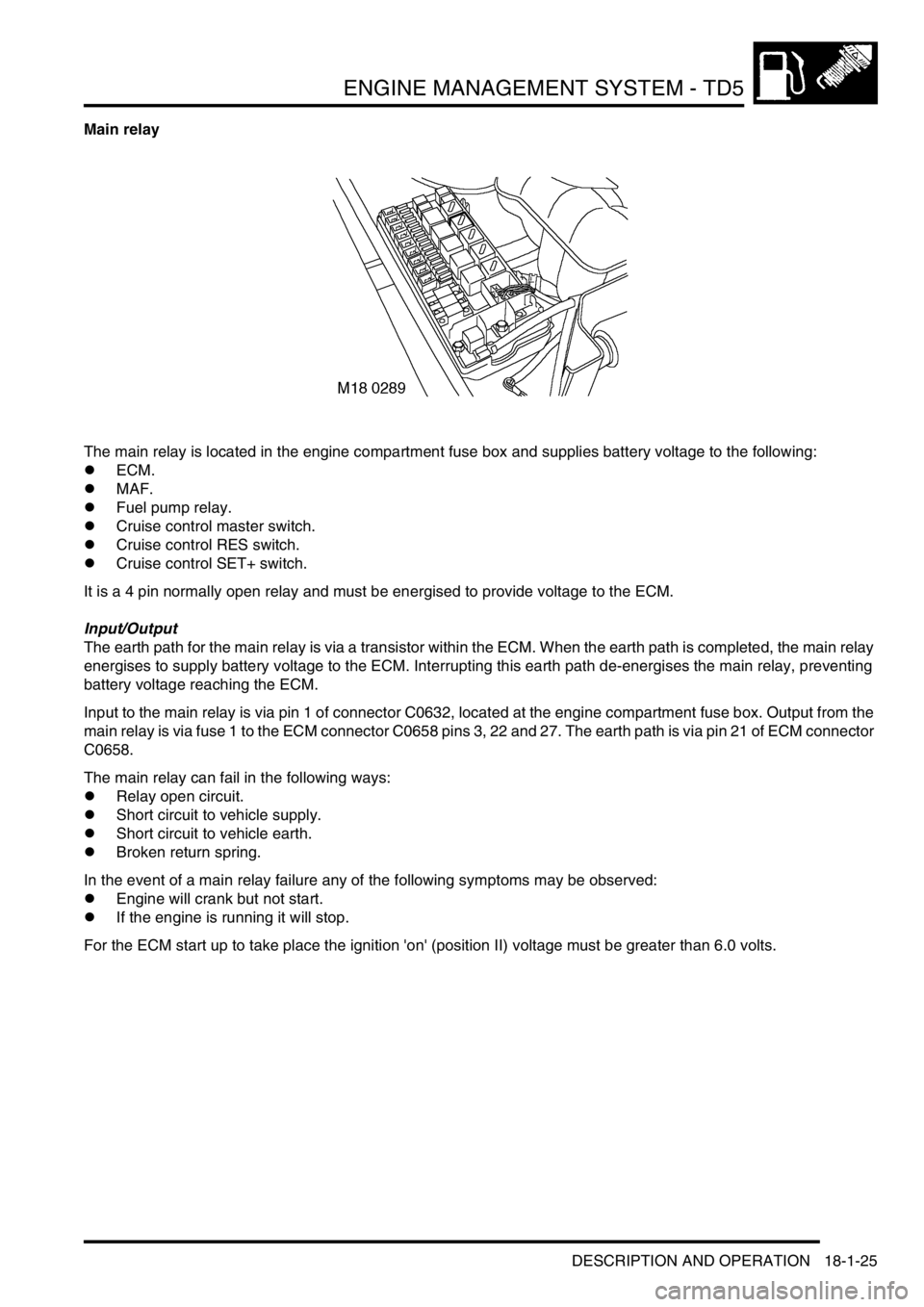
ENGINE MANAGEMENT SYSTEM - TD5
DESCRIPTION AND OPERATION 18-1-25
Main relay
The main relay is located in the engine compartment fuse box and supplies battery voltage to the following:
lECM.
lMAF.
lFuel pump relay.
lCruise control master switch.
lCruise control RES switch.
lCruise control SET+ switch.
It is a 4 pin normally open relay and must be energised to provide voltage to the ECM.
Input/Output
The earth path for the main relay is via a transistor within the ECM. When the earth path is completed, the main relay
energises to supply battery voltage to the ECM. Interrupting this earth path de-energises the main relay, preventing
battery voltage reaching the ECM.
Input to the main relay is via pin 1 of connector C0632, located at the engine compartment fuse box. Output from the
main relay is via fuse 1 to the ECM connector C0658 pins 3, 22 and 27. The earth path is via pin 21 of ECM connector
C0658.
The main relay can fail in the following ways:
lRelay open circuit.
lShort circuit to vehicle supply.
lShort circuit to vehicle earth.
lBroken return spring.
In the event of a main relay failure any of the following symptoms may be observed:
lEngine will crank but not start.
lIf the engine is running it will stop.
For the ECM start up to take place the ignition 'on' (position II) voltage must be greater than 6.0 volts.
Page 419 of 1672
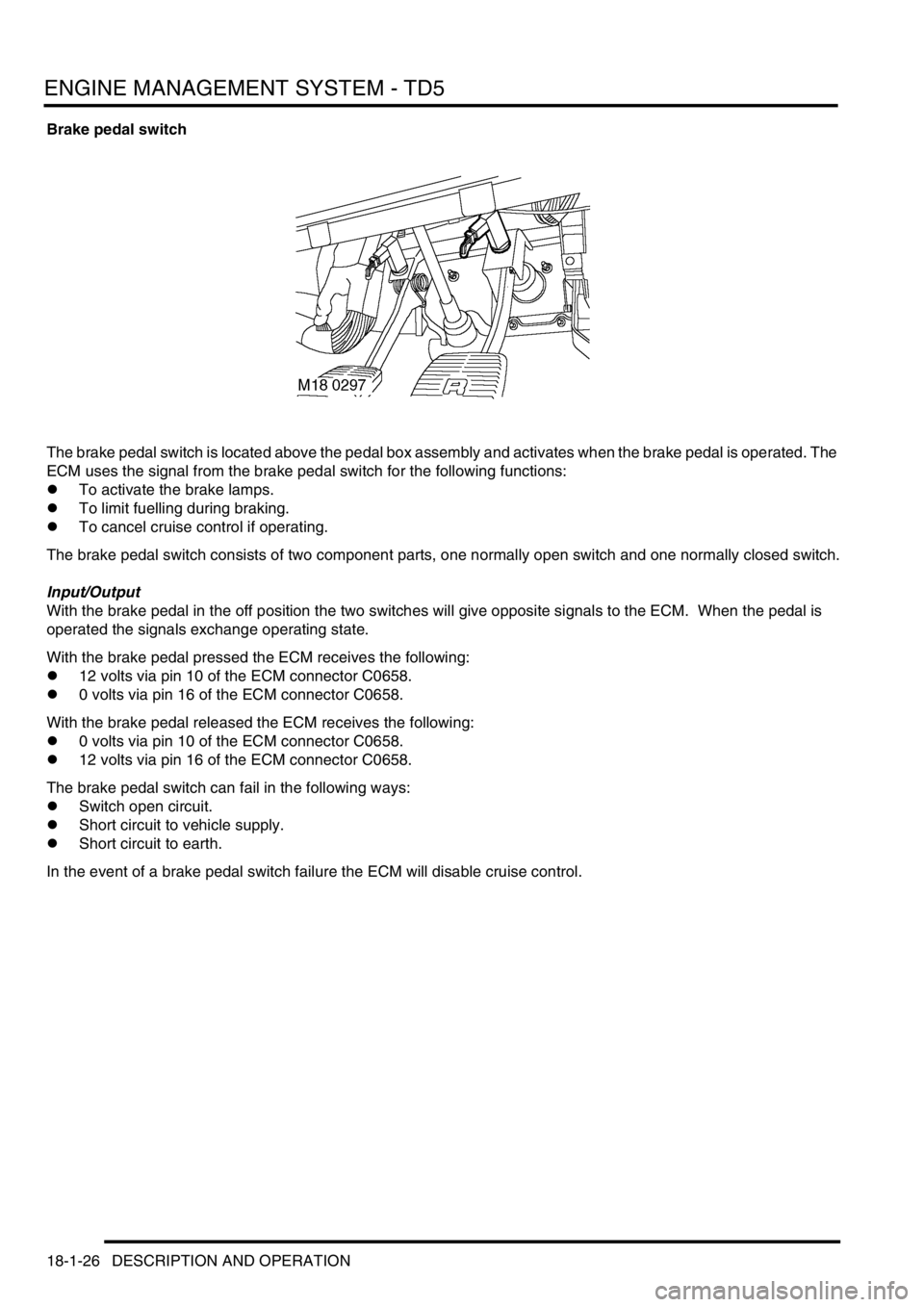
ENGINE MANAGEMENT SYSTEM - TD5
18-1-26 DESCRIPTION AND OPERATION
Brake pedal switch
The brake pedal switch is located above the pedal box assembly and activates when the brake pedal is operated. The
ECM uses the signal from the brake pedal switch for the following functions:
lTo activate the brake lamps.
lTo limit fuelling during braking.
lTo cancel cruise control if operating.
The brake pedal switch consists of two component parts, one normally open switch and one normally closed switch.
Input/Output
With the brake pedal in the off position the two switches will give opposite signals to the ECM. When the pedal is
operated the signals exchange operating state.
With the brake pedal pressed the ECM receives the following:
l12 volts via pin 10 of the ECM connector C0658.
l0 volts via pin 16 of the ECM connector C0658.
With the brake pedal released the ECM receives the following:
l0 volts via pin 10 of the ECM connector C0658.
l12 volts via pin 16 of the ECM connector C0658.
The brake pedal switch can fail in the following ways:
lSwitch open circuit.
lShort circuit to vehicle supply.
lShort circuit to earth.
In the event of a brake pedal switch failure the ECM will disable cruise control.
Page 420 of 1672
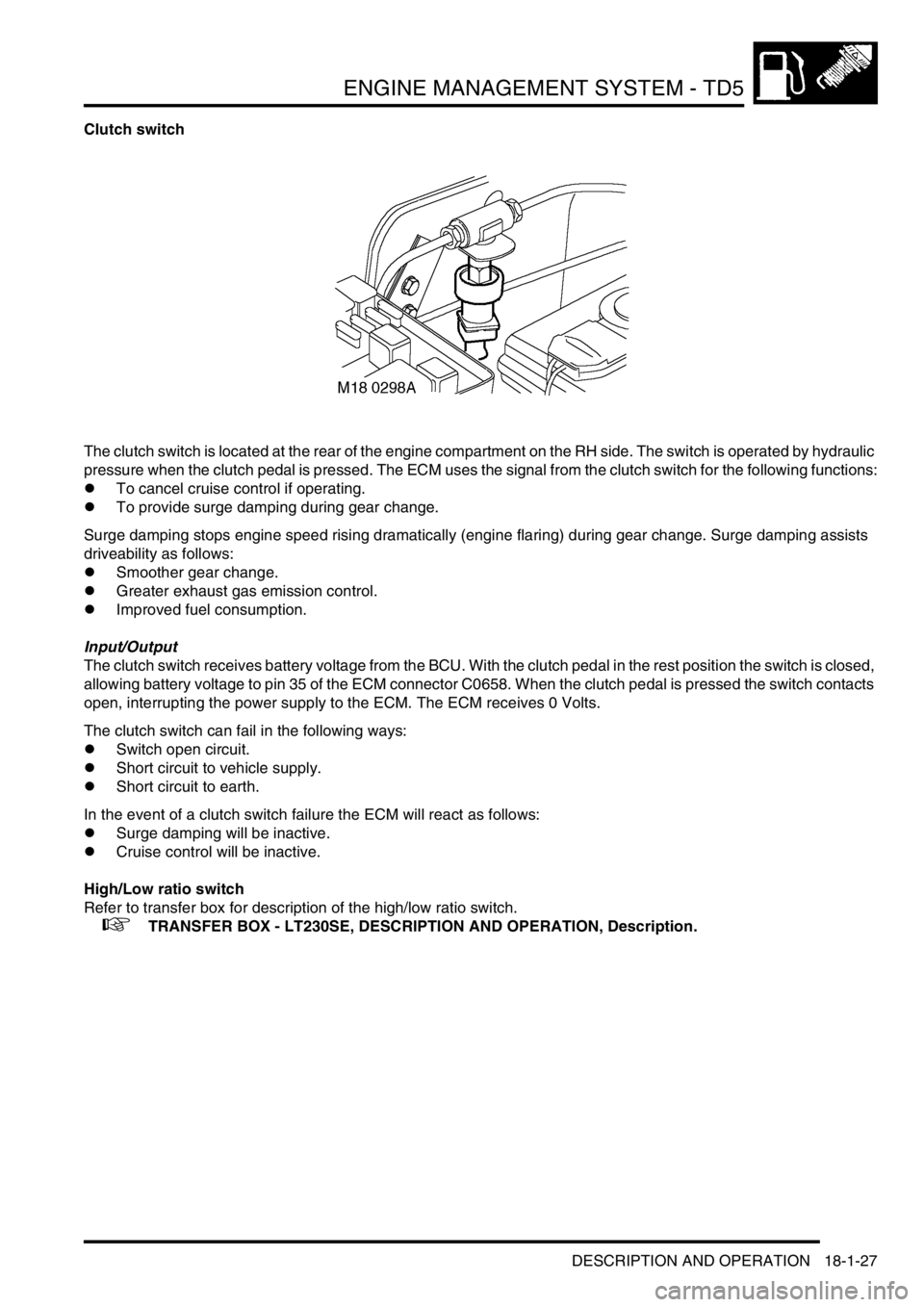
ENGINE MANAGEMENT SYSTEM - TD5
DESCRIPTION AND OPERATION 18-1-27
Clutch switch
The clutch switch is located at the rear of the engine compartment on the RH side. The switch is operated by hydraulic
pressure when the clutch pedal is pressed. The ECM uses the signal from the clutch switch for the following functions:
lTo cancel cruise control if operating.
lTo provide surge damping during gear change.
Surge damping stops engine speed rising dramatically (engine flaring) during gear change. Surge damping assists
driveability as follows:
lSmoother gear change.
lGreater exhaust gas emission control.
lImproved fuel consumption.
Input/Output
The clutch switch receives battery voltage from the BCU. With the clutch pedal in the rest position the switch is closed,
allowing battery voltage to pin 35 of the ECM connector C0658. When the clutch pedal is pressed the switch contacts
open, interrupting the power supply to the ECM. The ECM receives 0 Volts.
The clutch switch can fail in the following ways:
lSwitch open circuit.
lShort circuit to vehicle supply.
lShort circuit to earth.
In the event of a clutch switch failure the ECM will react as follows:
lSurge damping will be inactive.
lCruise control will be inactive.
High/Low ratio switch
Refer to transfer box for description of the high/low ratio switch.
+ TRANSFER BOX - LT230SE, DESCRIPTION AND OPERATION, Description.