LAND ROVER DISCOVERY 2002 Workshop Manual
Manufacturer: LAND ROVER, Model Year: 2002, Model line: DISCOVERY, Model: LAND ROVER DISCOVERY 2002Pages: 1672, PDF Size: 46.1 MB
Page 421 of 1672
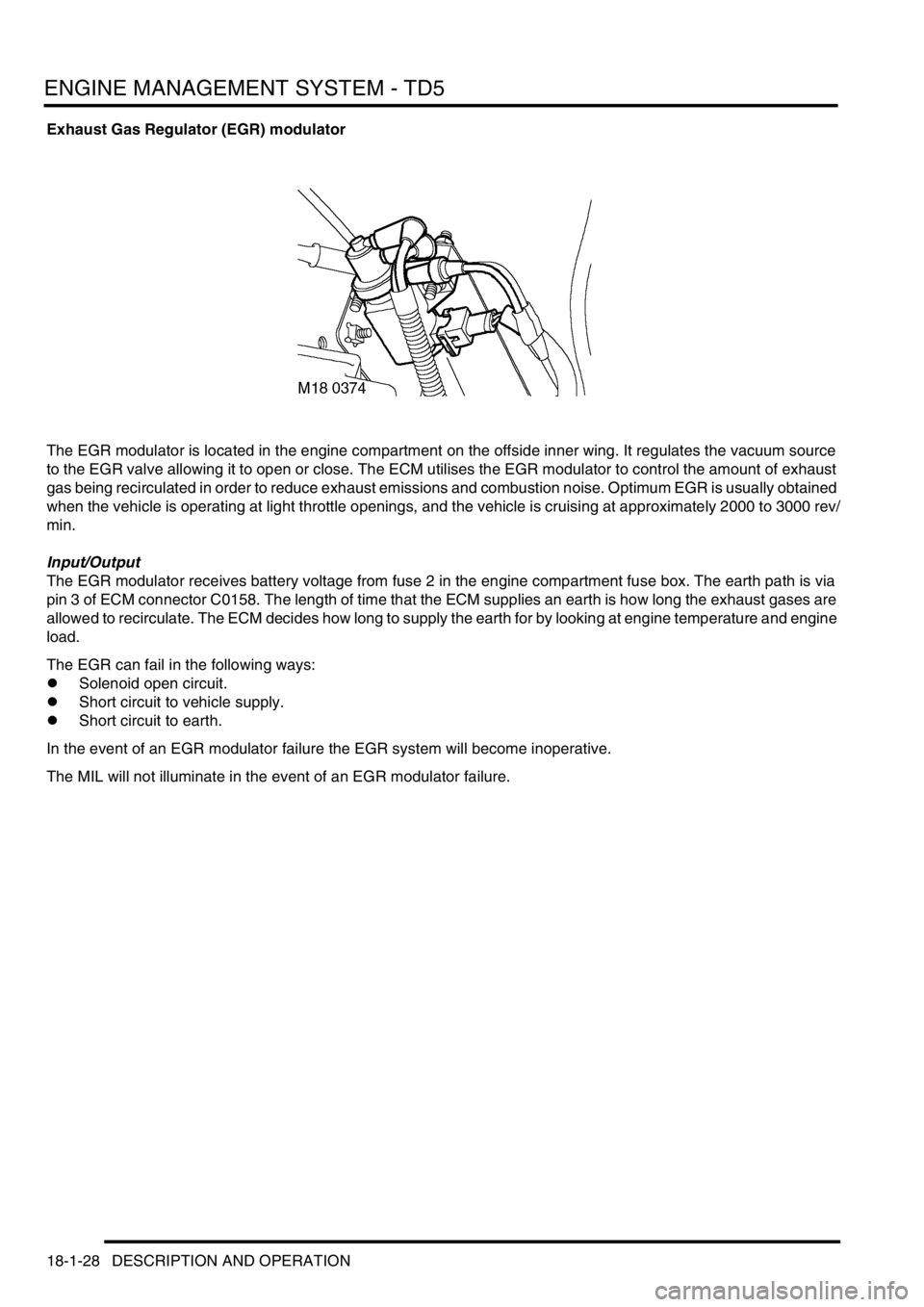
ENGINE MANAGEMENT SYSTEM - TD5
18-1-28 DESCRIPTION AND OPERATION
Exhaust Gas Regulator (EGR) modulator
The EGR modulator is located in the engine compartment on the offside inner wing. It regulates the vacuum source
to the EGR valve allowing it to open or close. The ECM utilises the EGR modulator to control the amount of exhaust
gas being recirculated in order to reduce exhaust emissions and combustion noise. Optimum EGR is usually obtained
when the vehicle is operating at light throttle openings, and the vehicle is cruising at approximately 2000 to 3000 rev/
min.
Input/Output
The EGR modulator receives battery voltage from fuse 2 in the engine compartment fuse box. The earth path is via
pin 3 of ECM connector C0158. The length of time that the ECM supplies an earth is how long the exhaust gases are
allowed to recirculate. The ECM decides how long to supply the earth for by looking at engine temperature and engine
load.
The EGR can fail in the following ways:
lSolenoid open circuit.
lShort circuit to vehicle supply.
lShort circuit to earth.
In the event of an EGR modulator failure the EGR system will become inoperative.
The MIL will not illuminate in the event of an EGR modulator failure.
Page 422 of 1672
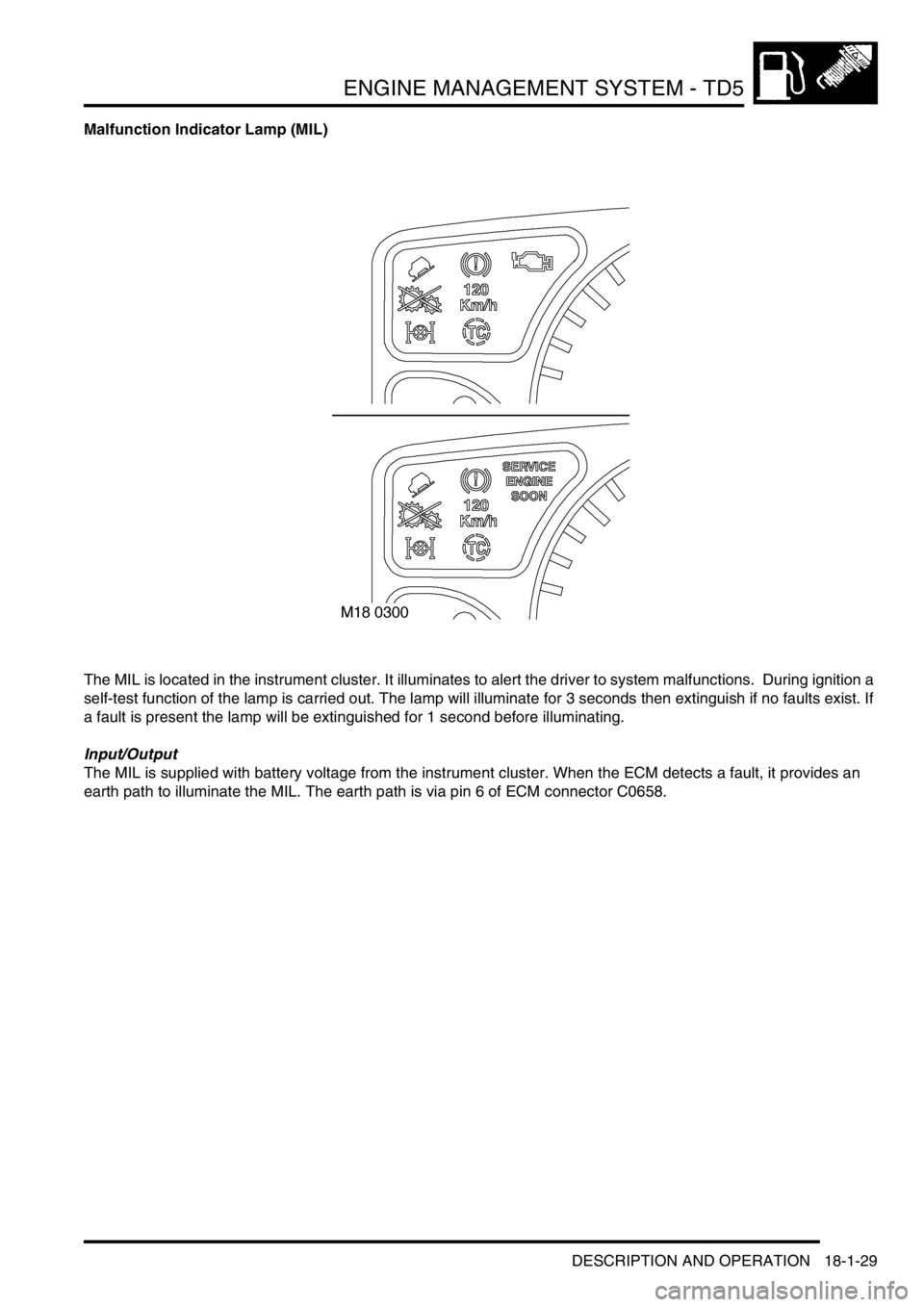
ENGINE MANAGEMENT SYSTEM - TD5
DESCRIPTION AND OPERATION 18-1-29
Malfunction Indicator Lamp (MIL)
The MIL is located in the instrument cluster. It illuminates to alert the driver to system malfunctions. During ignition a
self-test function of the lamp is carried out. The lamp will illuminate for 3 seconds then extinguish if no faults exist. If
a fault is present the lamp will be extinguished for 1 second before illuminating.
Input/Output
The MIL is supplied with battery voltage from the instrument cluster. When the ECM detects a fault, it provides an
earth path to illuminate the MIL. The earth path is via pin 6 of ECM connector C0658.
Page 423 of 1672
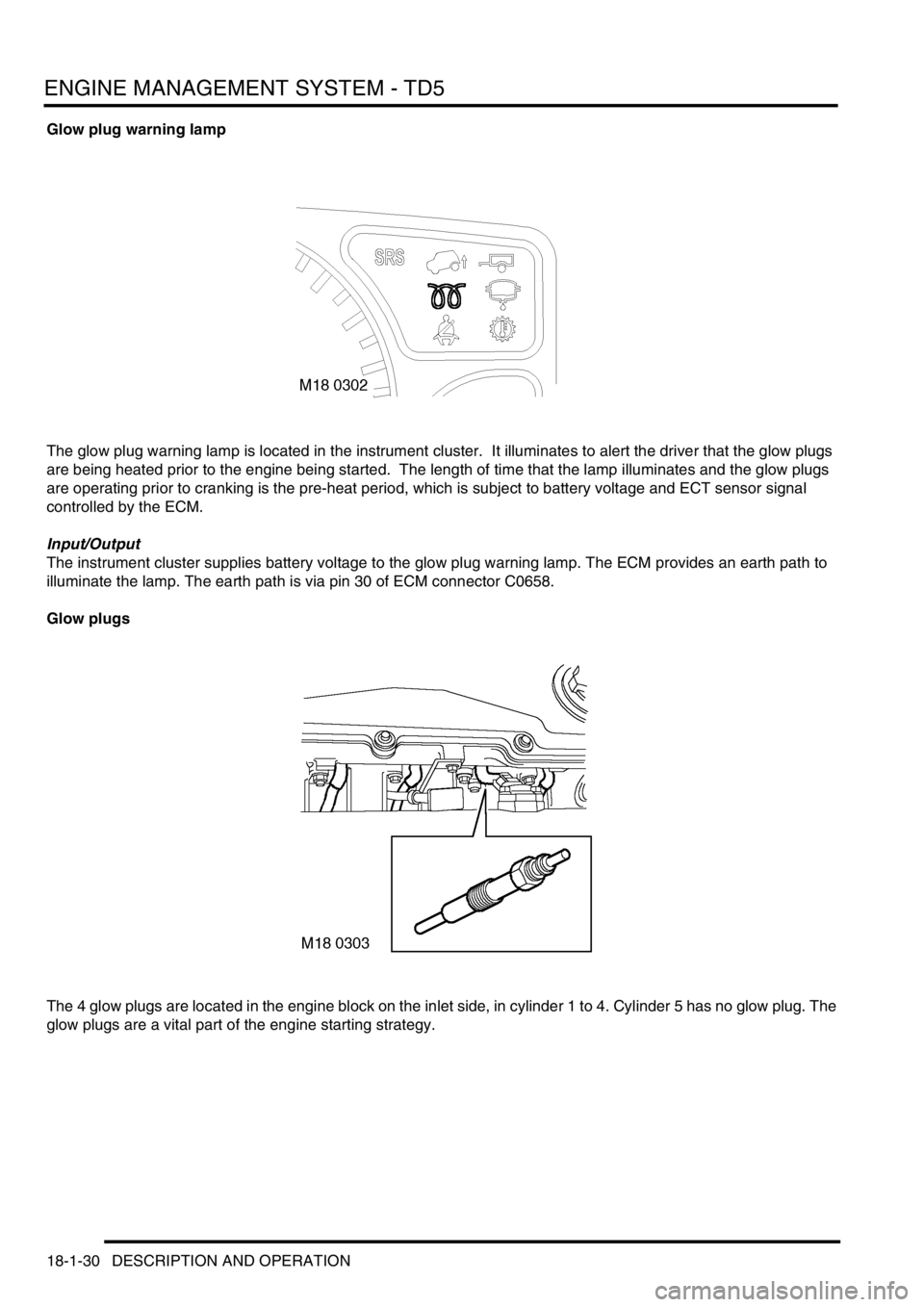
ENGINE MANAGEMENT SYSTEM - TD5
18-1-30 DESCRIPTION AND OPERATION
Glow plug warning lamp
The glow plug warning lamp is located in the instrument cluster. It illuminates to alert the driver that the glow plugs
are being heated prior to the engine being started. The length of time that the lamp illuminates and the glow plugs
are operating prior to cranking is the pre-heat period, which is subject to battery voltage and ECT sensor signal
controlled by the ECM.
Input/Output
The instrument cluster supplies battery voltage to the glow plug warning lamp. The ECM provides an earth path to
illuminate the lamp. The earth path is via pin 30 of ECM connector C0658.
Glow plugs
The 4 glow plugs are located in the engine block on the inlet side, in cylinder 1 to 4. Cylinder 5 has no glow plug. The
glow plugs are a vital part of the engine starting strategy.
Page 424 of 1672
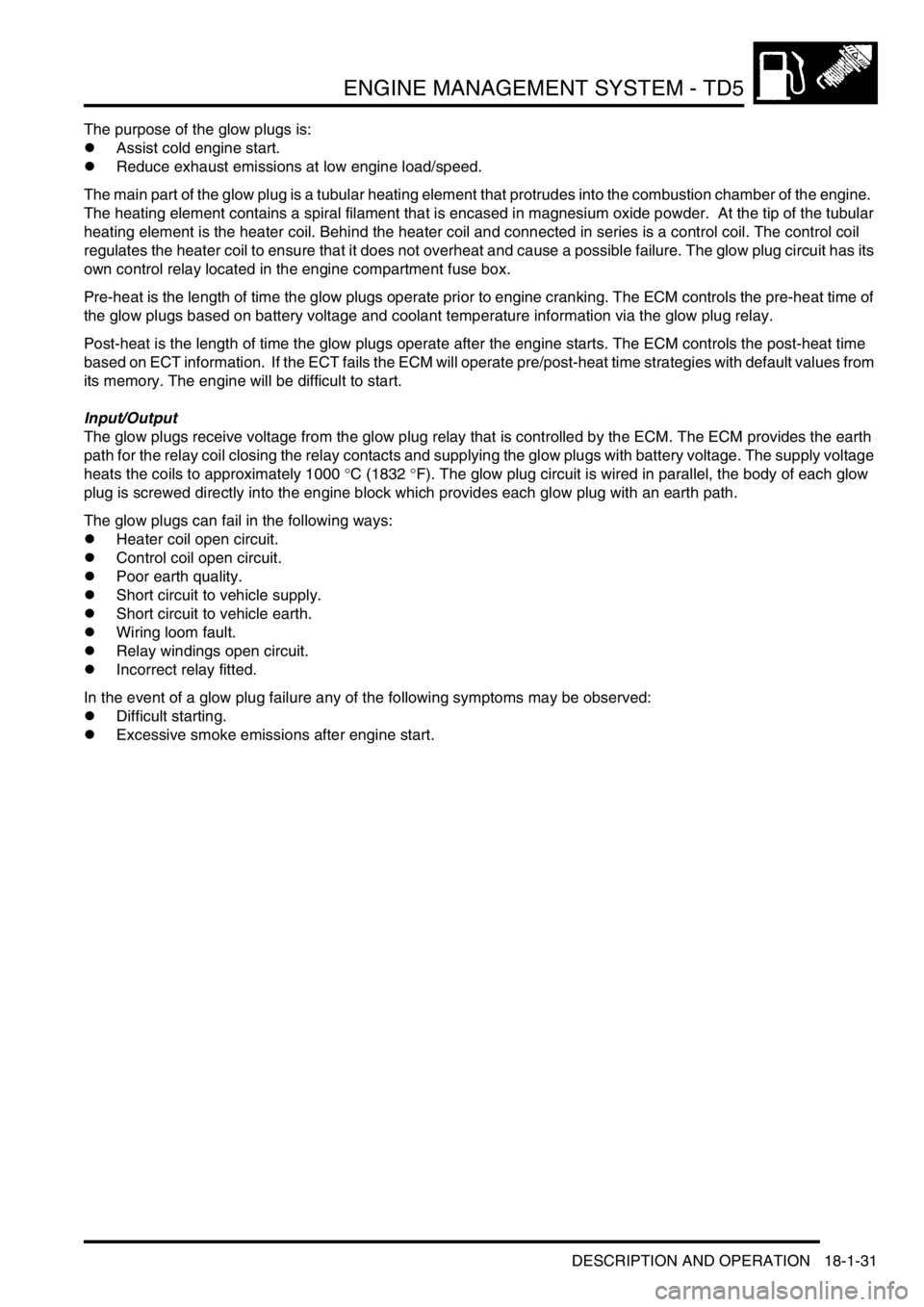
ENGINE MANAGEMENT SYSTEM - TD5
DESCRIPTION AND OPERATION 18-1-31
The purpose of the glow plugs is:
lAssist cold engine start.
lReduce exhaust emissions at low engine load/speed.
The main part of the glow plug is a tubular heating element that protrudes into the combustion chamber of the engine.
The heating element contains a spiral filament that is encased in magnesium oxide powder. At the tip of the tubular
heating element is the heater coil. Behind the heater coil and connected in series is a control coil. The control coil
regulates the heater coil to ensure that it does not overheat and cause a possible failure. The glow plug circuit has its
own control relay located in the engine compartment fuse box.
Pre-heat is the length of time the glow plugs operate prior to engine cranking. The ECM controls the pre-heat time of
the glow plugs based on battery voltage and coolant temperature information via the glow plug relay.
Post-heat is the length of time the glow plugs operate after the engine starts. The ECM controls the post-heat time
based on ECT information. If the ECT fails the ECM will operate pre/post-heat time strategies with default values from
its memory. The engine will be difficult to start.
Input/Output
The glow plugs receive voltage from the glow plug relay that is controlled by the ECM. The ECM provides the earth
path for the relay coil closing the relay contacts and supplying the glow plugs with battery voltage. The supply voltage
heats the coils to approximately 1000
°C (1832 °F). The glow plug circuit is wired in parallel, the body of each glow
plug is screwed directly into the engine block which provides each glow plug with an earth path.
The glow plugs can fail in the following ways:
lHeater coil open circuit.
lControl coil open circuit.
lPoor earth quality.
lShort circuit to vehicle supply.
lShort circuit to vehicle earth.
lWiring loom fault.
lRelay windings open circuit.
lIncorrect relay fitted.
In the event of a glow plug failure any of the following symptoms may be observed:
lDifficult starting.
lExcessive smoke emissions after engine start.
Page 425 of 1672
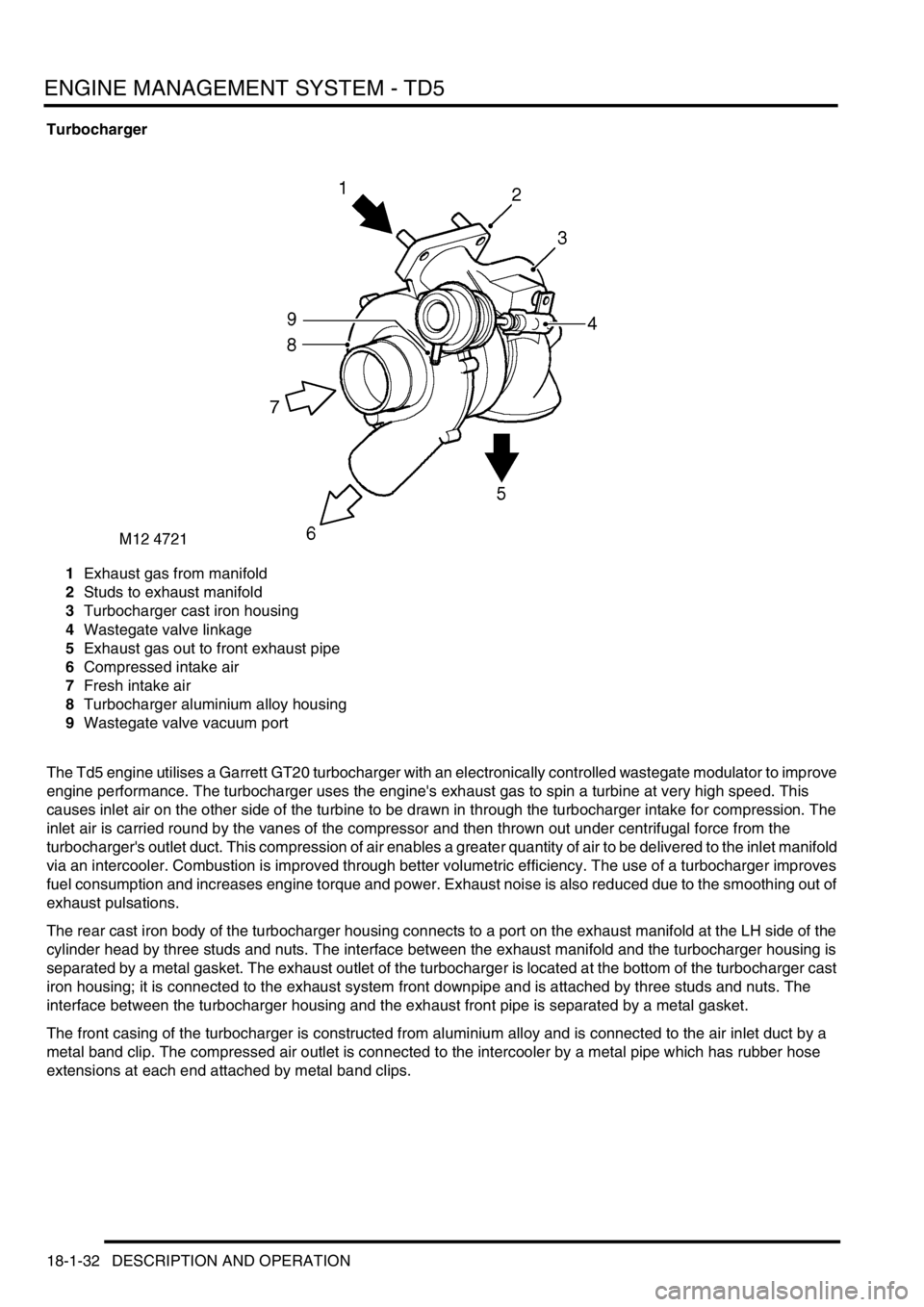
ENGINE MANAGEMENT SYSTEM - TD5
18-1-32 DESCRIPTION AND OPERATION
Turbocharger
1Exhaust gas from manifold
2Studs to exhaust manifold
3Turbocharger cast iron housing
4Wastegate valve linkage
5Exhaust gas out to front exhaust pipe
6Compressed intake air
7Fresh intake air
8Turbocharger aluminium alloy housing
9Wastegate valve vacuum port
The Td5 engine utilises a Garrett GT20 turbocharger with an electronically controlled wastegate modulator to improve
engine performance. The turbocharger uses the engine's exhaust gas to spin a turbine at very high speed. This
causes inlet air on the other side of the turbine to be drawn in through the turbocharger intake for compression. The
inlet air is carried round by the vanes of the compressor and then thrown out under centrifugal force from the
turbocharger's outlet duct. This compression of air enables a greater quantity of air to be delivered to the inlet manifold
via an intercooler. Combustion is improved through better volumetric efficiency. The use of a turbocharger improves
fuel consumption and increases engine torque and power. Exhaust noise is also reduced due to the smoothing out of
exhaust pulsations.
The rear cast iron body of the turbocharger housing connects to a port on the exhaust manifold at the LH side of the
cylinder head by three studs and nuts. The interface between the exhaust manifold and the turbocharger housing is
separated by a metal gasket. The exhaust outlet of the turbocharger is located at the bottom of the turbocharger cast
iron housing; it is connected to the exhaust system front downpipe and is attached by three studs and nuts. The
interface between the turbocharger housing and the exhaust front pipe is separated by a metal gasket.
The front casing of the turbocharger is constructed from aluminium alloy and is connected to the air inlet duct by a
metal band clip. The compressed air outlet is connected to the intercooler by a metal pipe which has rubber hose
extensions at each end attached by metal band clips.
Page 426 of 1672
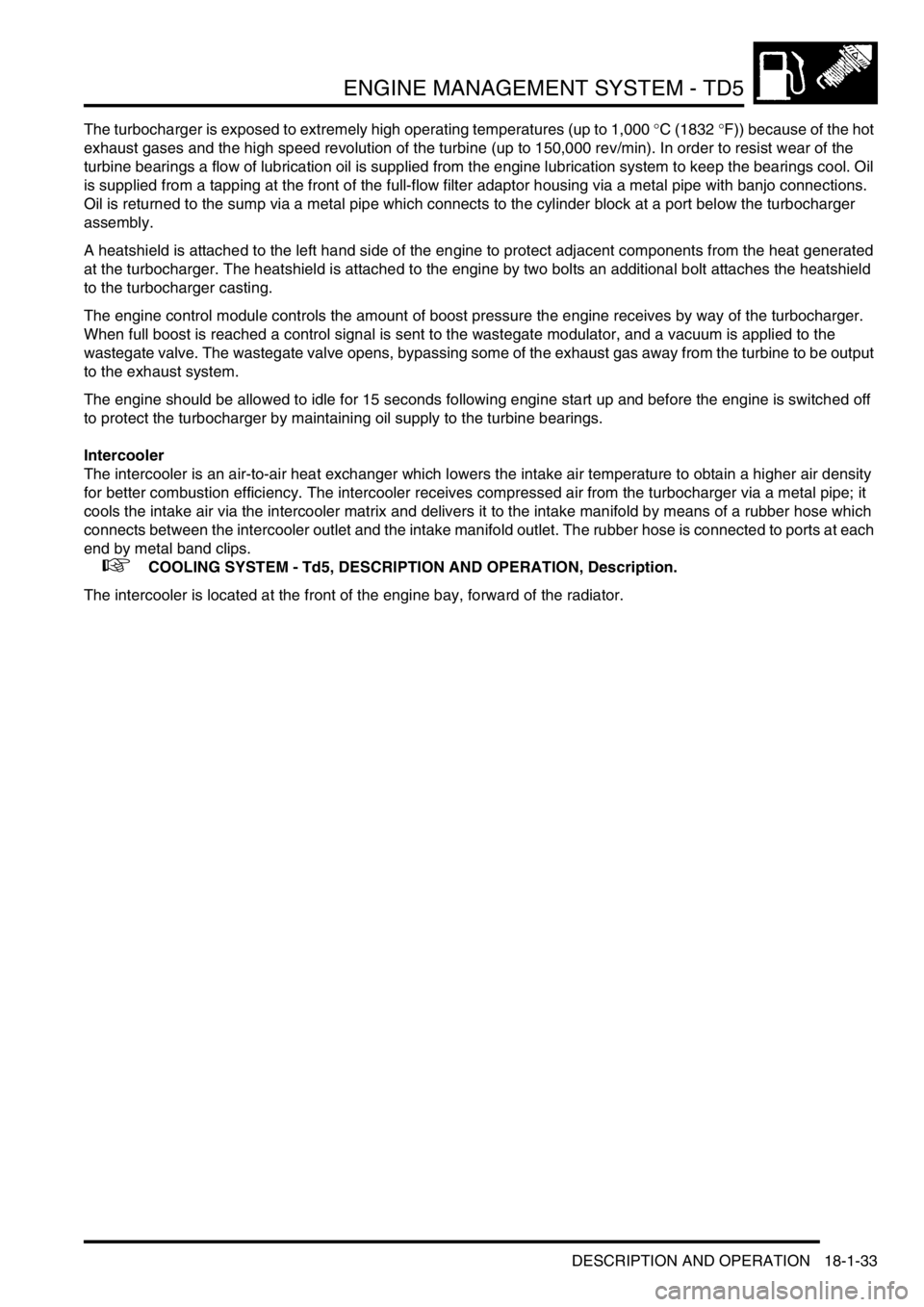
ENGINE MANAGEMENT SYSTEM - TD5
DESCRIPTION AND OPERATION 18-1-33
The turbocharger is exposed to extremely high operating temperatures (up to 1,000 °C (1832 °F)) because of the hot
exhaust gases and the high speed revolution of the turbine (up to 150,000 rev/min). In order to resist wear of the
turbine bearings a flow of lubrication oil is supplied from the engine lubrication system to keep the bearings cool. Oil
is supplied from a tapping at the front of the full-flow filter adaptor housing via a metal pipe with banjo connections.
Oil is returned to the sump via a metal pipe which connects to the cylinder block at a port below the turbocharger
assembly.
A heatshield is attached to the left hand side of the engine to protect adjacent components from the heat generated
at the turbocharger. The heatshield is attached to the engine by two bolts an additional bolt attaches the heatshield
to the turbocharger casting.
The engine control module controls the amount of boost pressure the engine receives by way of the turbocharger.
When full boost is reached a control signal is sent to the wastegate modulator, and a vacuum is applied to the
wastegate valve. The wastegate valve opens, bypassing some of the exhaust gas away from the turbine to be output
to the exhaust system.
The engine should be allowed to idle for 15 seconds following engine start up and before the engine is switched off
to protect the turbocharger by maintaining oil supply to the turbine bearings.
Intercooler
The intercooler is an air-to-air heat exchanger which lowers the intake air temperature to obtain a higher air density
for better combustion efficiency. The intercooler receives compressed air from the turbocharger via a metal pipe; it
cools the intake air via the intercooler matrix and delivers it to the intake manifold by means of a rubber hose which
connects between the intercooler outlet and the intake manifold outlet. The rubber hose is connected to ports at each
end by metal band clips.
+ COOLING SYSTEM - Td5, DESCRIPTION AND OPERATION, Description.
The intercooler is located at the front of the engine bay, forward of the radiator.
Page 427 of 1672
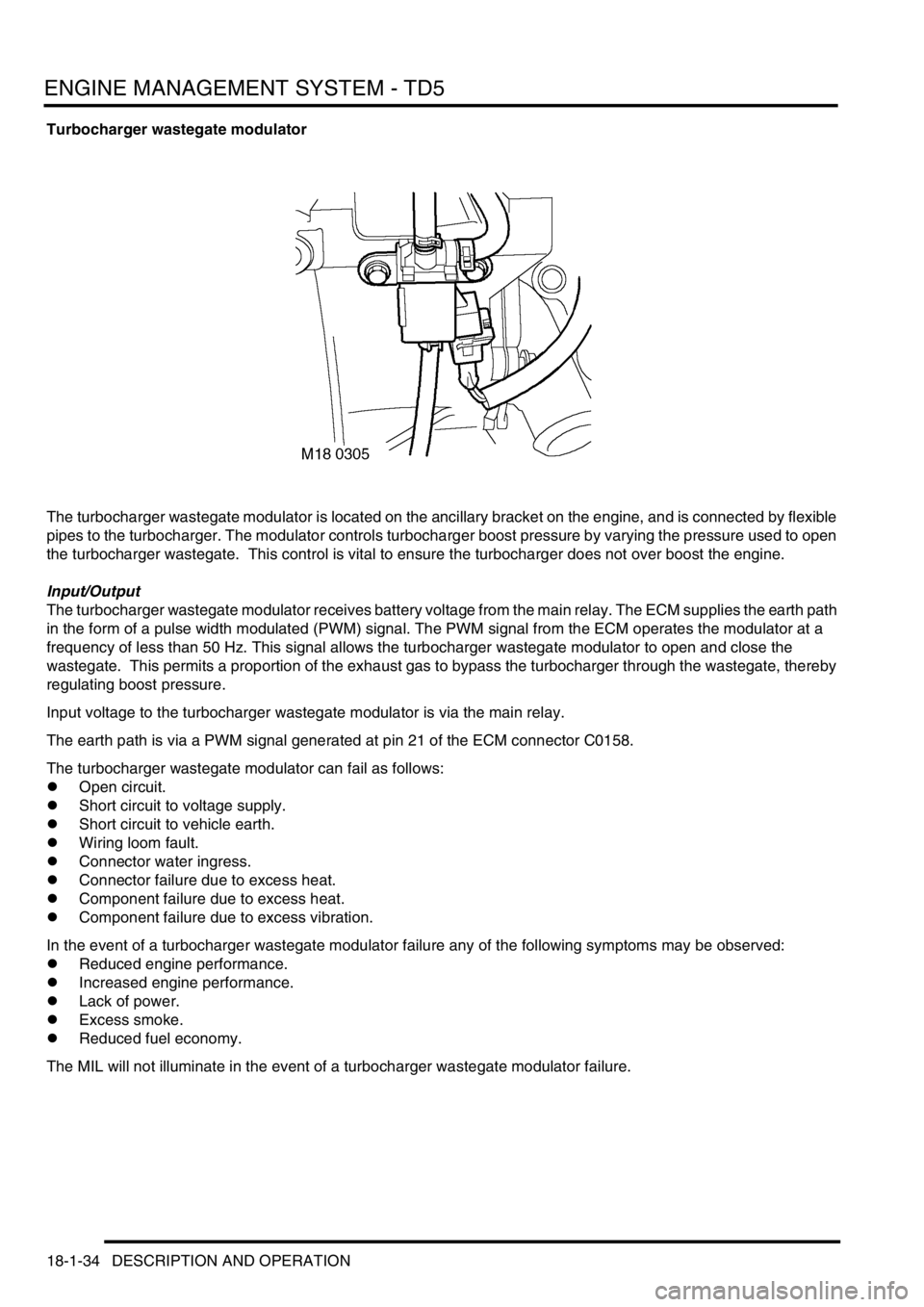
ENGINE MANAGEMENT SYSTEM - TD5
18-1-34 DESCRIPTION AND OPERATION
Turbocharger wastegate modulator
The turbocharger wastegate modulator is located on the ancillary bracket on the engine, and is connected by flexible
pipes to the turbocharger. The modulator controls turbocharger boost pressure by varying the pressure used to open
the turbocharger wastegate. This control is vital to ensure the turbocharger does not over boost the engine.
Input/Output
The turbocharger wastegate modulator receives battery voltage from the main relay. The ECM supplies the earth path
in the form of a pulse width modulated (PWM) signal. The PWM signal from the ECM operates the modulator at a
frequency of less than 50 Hz. This signal allows the turbocharger wastegate modulator to open and close the
wastegate. This permits a proportion of the exhaust gas to bypass the turbocharger through the wastegate, thereby
regulating boost pressure.
Input voltage to the turbocharger wastegate modulator is via the main relay.
The earth path is via a PWM signal generated at pin 21 of the ECM connector C0158.
The turbocharger wastegate modulator can fail as follows:
lOpen circuit.
lShort circuit to voltage supply.
lShort circuit to vehicle earth.
lWiring loom fault.
lConnector water ingress.
lConnector failure due to excess heat.
lComponent failure due to excess heat.
lComponent failure due to excess vibration.
In the event of a turbocharger wastegate modulator failure any of the following symptoms may be observed:
lReduced engine performance.
lIncreased engine performance.
lLack of power.
lExcess smoke.
lReduced fuel economy.
The MIL will not illuminate in the event of a turbocharger wastegate modulator failure.
Page 428 of 1672
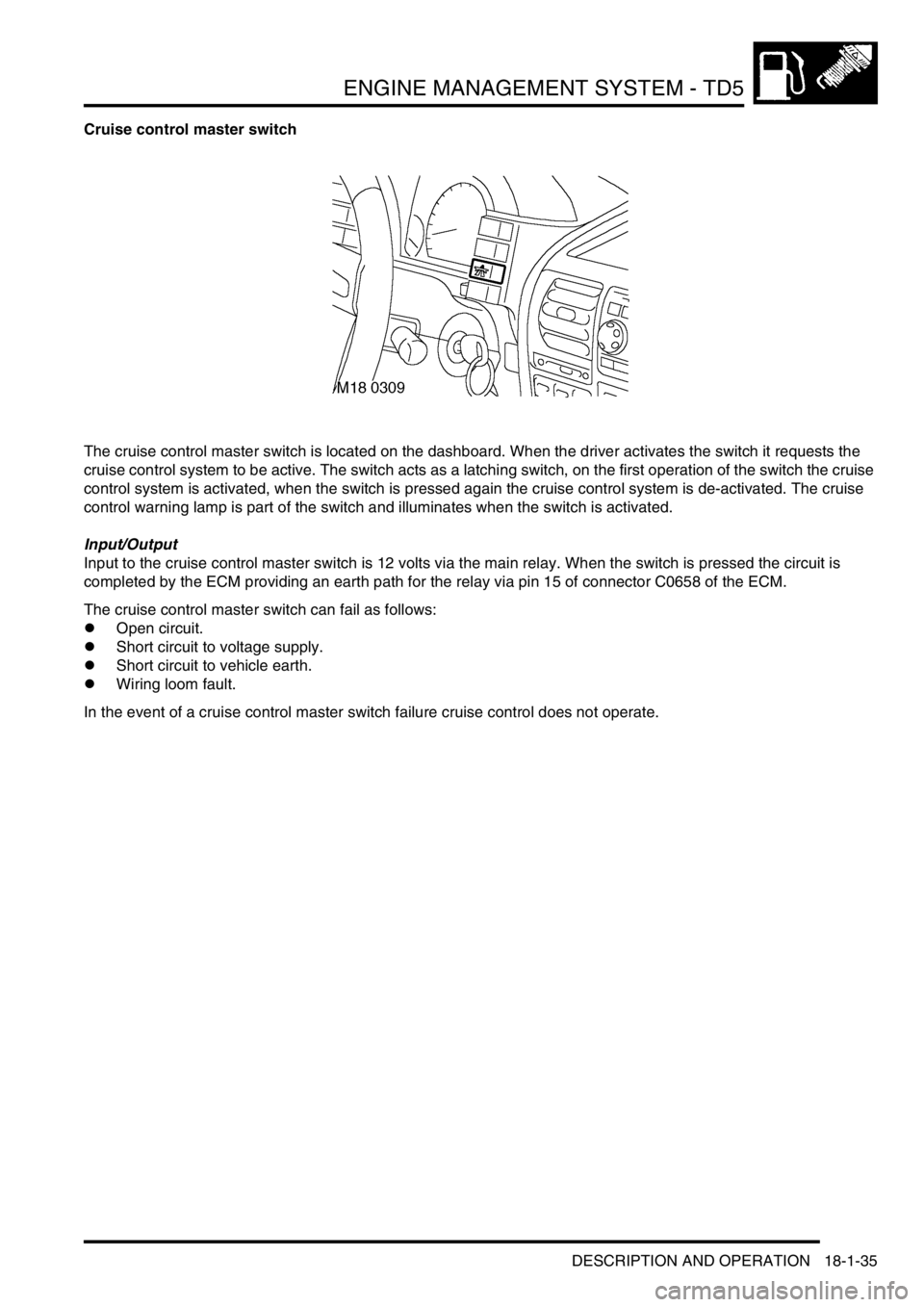
ENGINE MANAGEMENT SYSTEM - TD5
DESCRIPTION AND OPERATION 18-1-35
Cruise control master switch
The cruise control master switch is located on the dashboard. When the driver activates the switch it requests the
cruise control system to be active. The switch acts as a latching switch, on the first operation of the switch the cruise
control system is activated, when the switch is pressed again the cruise control system is de-activated. The cruise
control warning lamp is part of the switch and illuminates when the switch is activated.
Input/Output
Input to the cruise control master switch is 12 volts via the main relay. When the switch is pressed the circuit is
completed by the ECM providing an earth path for the relay via pin 15 of connector C0658 of the ECM.
The cruise control master switch can fail as follows:
lOpen circuit.
lShort circuit to voltage supply.
lShort circuit to vehicle earth.
lWiring loom fault.
In the event of a cruise control master switch failure cruise control does not operate.
Page 429 of 1672
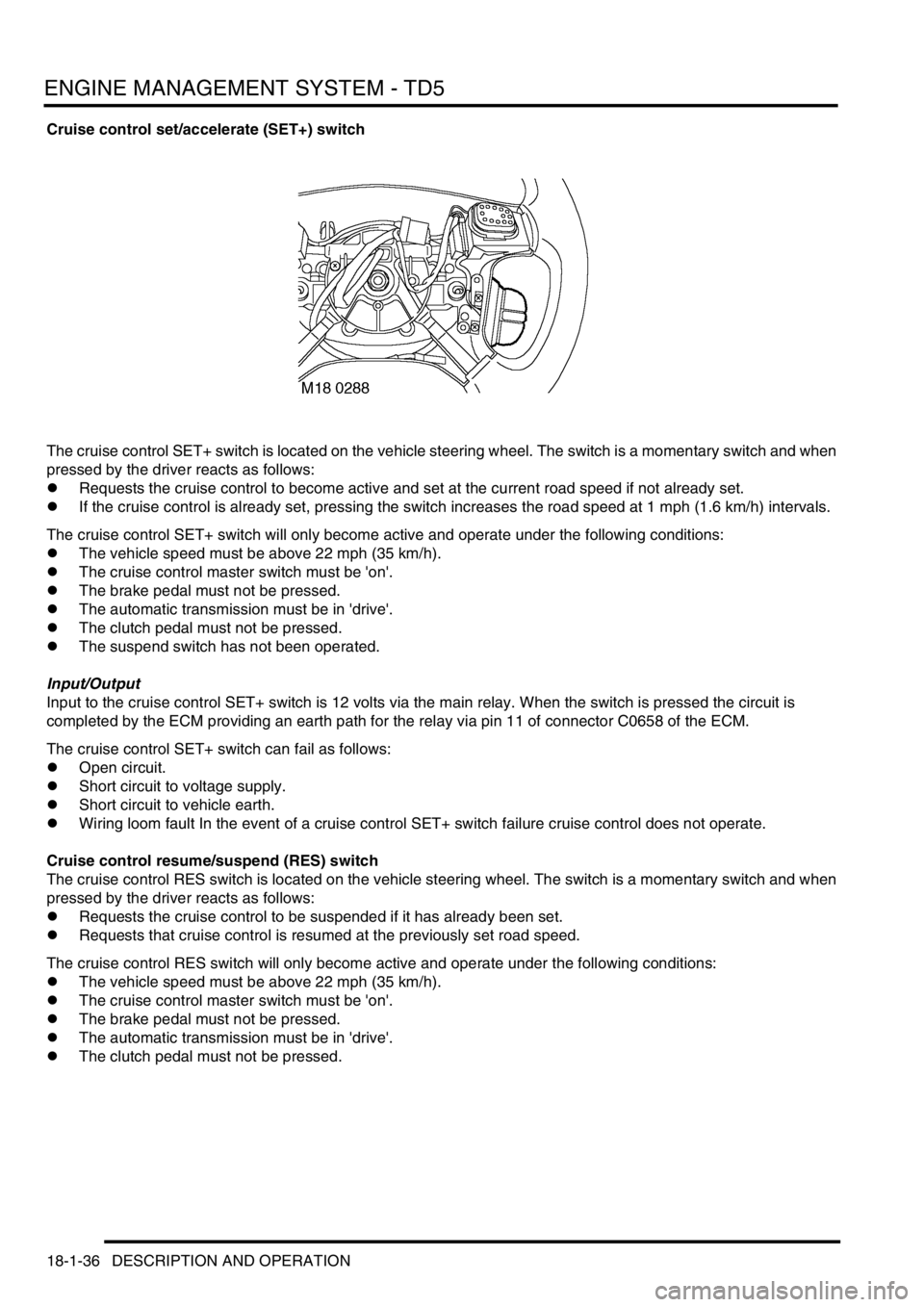
ENGINE MANAGEMENT SYSTEM - TD5
18-1-36 DESCRIPTION AND OPERATION
Cruise control set/accelerate (SET+) switch
The cruise control SET+ switch is located on the vehicle steering wheel. The switch is a momentary switch and when
pressed by the driver reacts as follows:
lRequests the cruise control to become active and set at the current road speed if not already set.
lIf the cruise control is already set, pressing the switch increases the road speed at 1 mph (1.6 km/h) intervals.
The cruise control SET+ switch will only become active and operate under the following conditions:
lThe vehicle speed must be above 22 mph (35 km/h).
lThe cruise control master switch must be 'on'.
lThe brake pedal must not be pressed.
lThe automatic transmission must be in 'drive'.
lThe clutch pedal must not be pressed.
lThe suspend switch has not been operated.
Input/Output
Input to the cruise control SET+ switch is 12 volts via the main relay. When the switch is pressed the circuit is
completed by the ECM providing an earth path for the relay via pin 11 of connector C0658 of the ECM.
The cruise control SET+ switch can fail as follows:
lOpen circuit.
lShort circuit to voltage supply.
lShort circuit to vehicle earth.
lWiring loom fault In the event of a cruise control SET+ switch failure cruise control does not operate.
Cruise control resume/suspend (RES) switch
The cruise control RES switch is located on the vehicle steering wheel. The switch is a momentary switch and when
pressed by the driver reacts as follows:
lRequests the cruise control to be suspended if it has already been set.
lRequests that cruise control is resumed at the previously set road speed.
The cruise control RES switch will only become active and operate under the following conditions:
lThe vehicle speed must be above 22 mph (35 km/h).
lThe cruise control master switch must be 'on'.
lThe brake pedal must not be pressed.
lThe automatic transmission must be in 'drive'.
lThe clutch pedal must not be pressed.
Page 430 of 1672
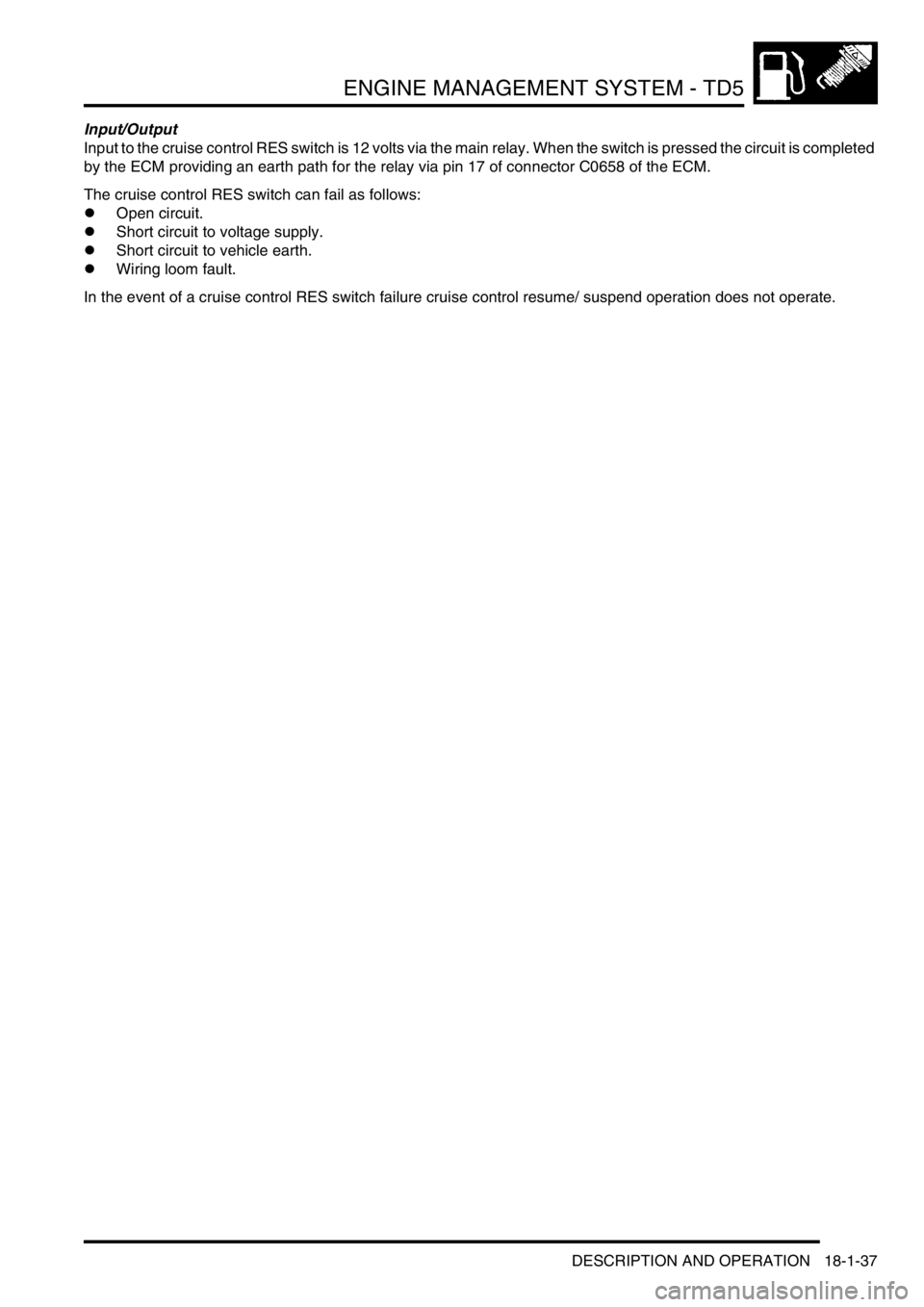
ENGINE MANAGEMENT SYSTEM - TD5
DESCRIPTION AND OPERATION 18-1-37
Input/Output
Input to the cruise control RES switch is 12 volts via the main relay. When the switch is pressed the circuit is completed
by the ECM providing an earth path for the relay via pin 17 of connector C0658 of the ECM.
The cruise control RES switch can fail as follows:
lOpen circuit.
lShort circuit to voltage supply.
lShort circuit to vehicle earth.
lWiring loom fault.
In the event of a cruise control RES switch failure cruise control resume/ suspend operation does not operate.