LAND ROVER DISCOVERY 2002 Workshop Manual
Manufacturer: LAND ROVER, Model Year: 2002, Model line: DISCOVERY, Model: LAND ROVER DISCOVERY 2002Pages: 1672, PDF Size: 46.1 MB
Page 401 of 1672
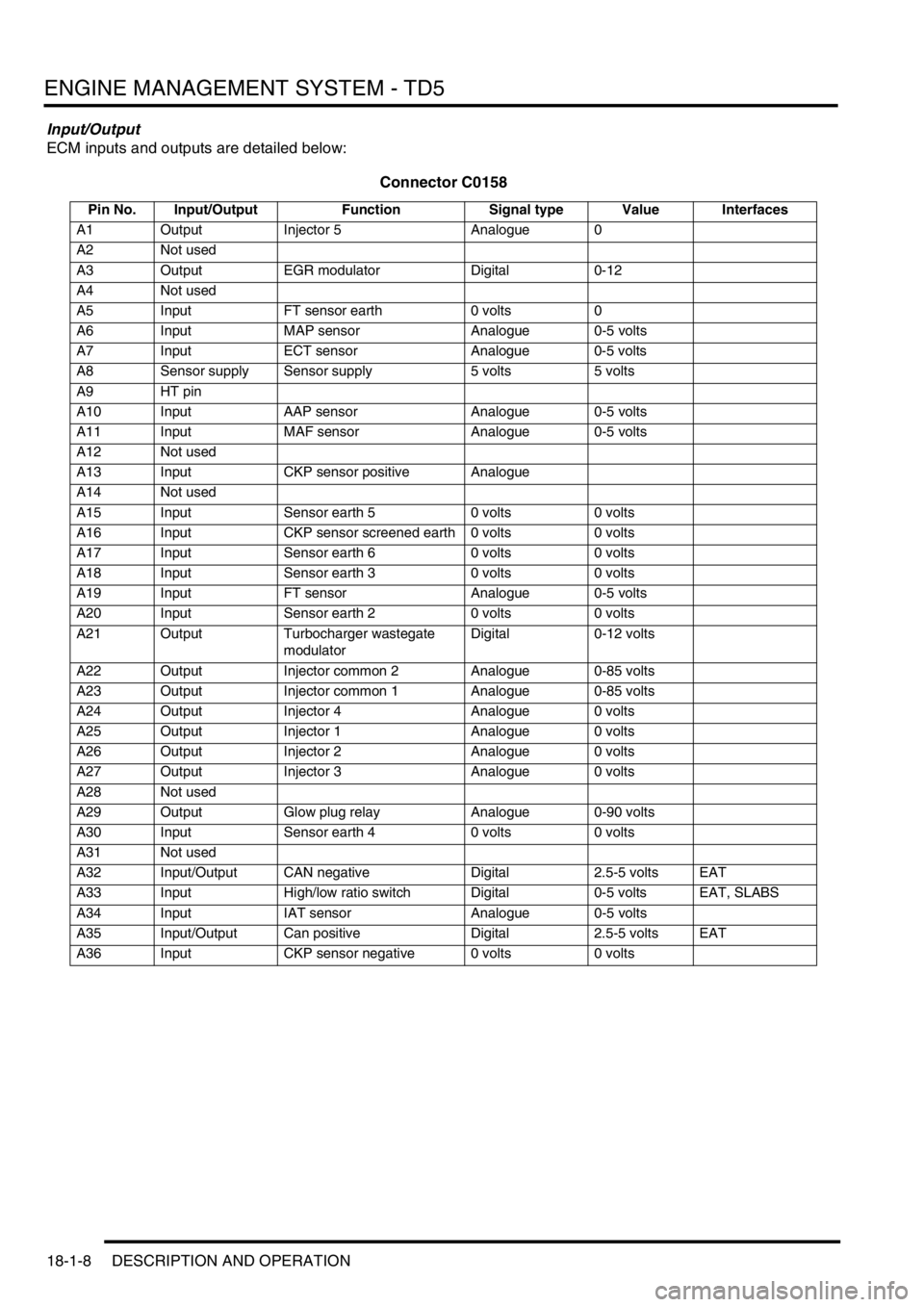
ENGINE MANAGEMENT SYSTEM - TD5
18-1-8 DESCRIPTION AND OPERATION
Input/Output
ECM inputs and outputs are detailed below:
Connector C0158
Pin No. Input/Output Function Signal type Value Interfaces
A1 Output Injector 5 Analogue 0
A2 Not used
A3 Output EGR modulator Digital 0-12
A4 Not used
A5 Input FT sensor earth 0 volts 0
A6 Input MAP sensor Analogue 0-5 volts
A7 Input ECT sensor Analogue 0-5 volts
A8 Sensor supply Sensor supply 5 volts 5 volts
A9 HT pin
A10 Input AAP sensor Analogue 0-5 volts
A11 Input MAF sensor Analogue 0-5 volts
A12 Not used
A13 Input CKP sensor positive Analogue
A14 Not used
A15 Input Sensor earth 5 0 volts 0 volts
A16 Input CKP sensor screened earth 0 volts 0 volts
A17 Input Sensor earth 6 0 volts 0 volts
A18 Input Sensor earth 3 0 volts 0 volts
A19 Input FT sensor Analogue 0-5 volts
A20 Input Sensor earth 2 0 volts 0 volts
A21 Output Turbocharger wastegate
modulatorDigital 0-12 volts
A22 Output Injector common 2 Analogue 0-85 volts
A23 Output Injector common 1 Analogue 0-85 volts
A24 Output Injector 4 Analogue 0 volts
A25 Output Injector 1 Analogue 0 volts
A26 Output Injector 2 Analogue 0 volts
A27 Output Injector 3 Analogue 0 volts
A28 Not used
A29 Output Glow plug relay Analogue 0-90 volts
A30 Input Sensor earth 4 0 volts 0 volts
A31 Not used
A32 Input/Output CAN negative Digital 2.5-5 volts EAT
A33 Input High/low ratio switch Digital 0-5 volts EAT, SLABS
A34 Input IAT sensor Analogue 0-5 volts
A35 Input/Output Can positive Digital 2.5-5 volts EAT
A36 Input CKP sensor negative 0 volts 0 volts
Page 402 of 1672
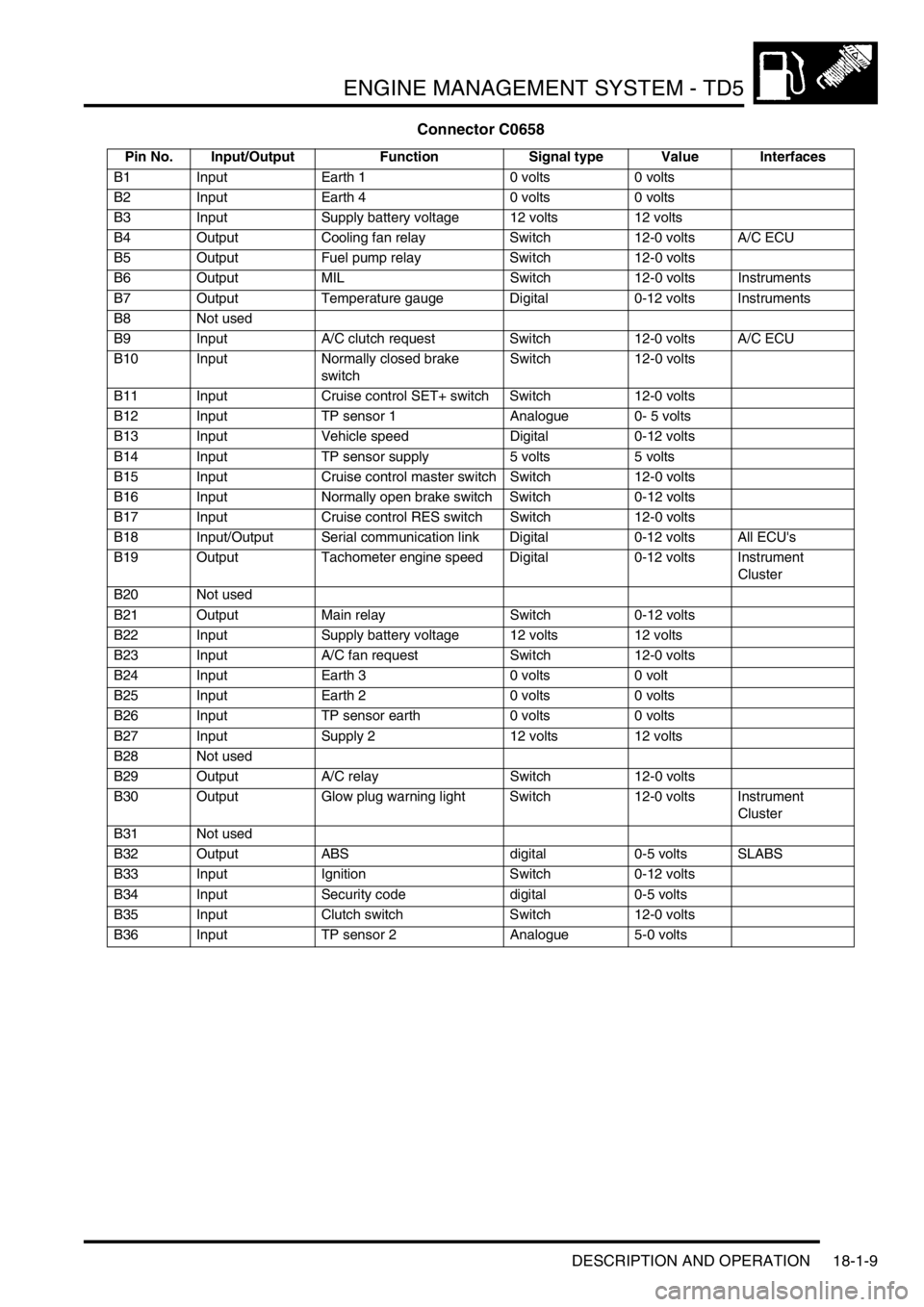
ENGINE MANAGEMENT SYSTEM - TD5
DESCRIPTION AND OPERATION 18-1-9
Connector C0658
Pin No. Input/Output Function Signal type Value Interfaces
B1 Input Earth 1 0 volts 0 volts
B2 Input Earth 4 0 volts 0 volts
B3 Input Supply battery voltage 12 volts 12 volts
B4 Output Cooling fan relay Switch 12-0 volts A/C ECU
B5 Output Fuel pump relay Switch 12-0 volts
B6 Output MIL Switch 12-0 volts Instruments
B7 Output Temperature gauge Digital 0-12 volts Instruments
B8 Not used
B9 Input A/C clutch request Switch 12-0 volts A/C ECU
B10 Input Normally closed brake
switchSwitch 12-0 volts
B11 Input Cruise control SET+ switch Switch 12-0 volts
B12 Input TP sensor 1 Analogue 0- 5 volts
B13 Input Vehicle speed Digital 0-12 volts
B14 Input TP sensor supply 5 volts 5 volts
B15 Input Cruise control master switch Switch 12-0 volts
B16 Input Normally open brake switch Switch 0-12 volts
B17 Input Cruise control RES switch Switch 12-0 volts
B18 Input/Output Serial communication link Digital 0-12 volts All ECU's
B19 Output Tachometer engine speed Digital 0-12 volts Instrument
Cluster
B20 Not used
B21 Output Main relay Switch 0-12 volts
B22 Input Supply battery voltage 12 volts 12 volts
B23 Input A/C fan request Switch 12-0 volts
B24 Input Earth 3 0 volts 0 volt
B25 Input Earth 2 0 volts 0 volts
B26 Input TP sensor earth 0 volts 0 volts
B27 Input Supply 2 12 volts 12 volts
B28 Not used
B29 Output A/C relay Switch 12-0 volts
B30 Output Glow plug warning light Switch 12-0 volts Instrument
Cluster
B31 Not used
B32 Output ABS digital 0-5 volts SLABS
B33 Input Ignition Switch 0-12 volts
B34 Input Security code digital 0-5 volts
B35 Input Clutch switch Switch 12-0 volts
B36 Input TP sensor 2 Analogue 5-0 volts
Page 403 of 1672
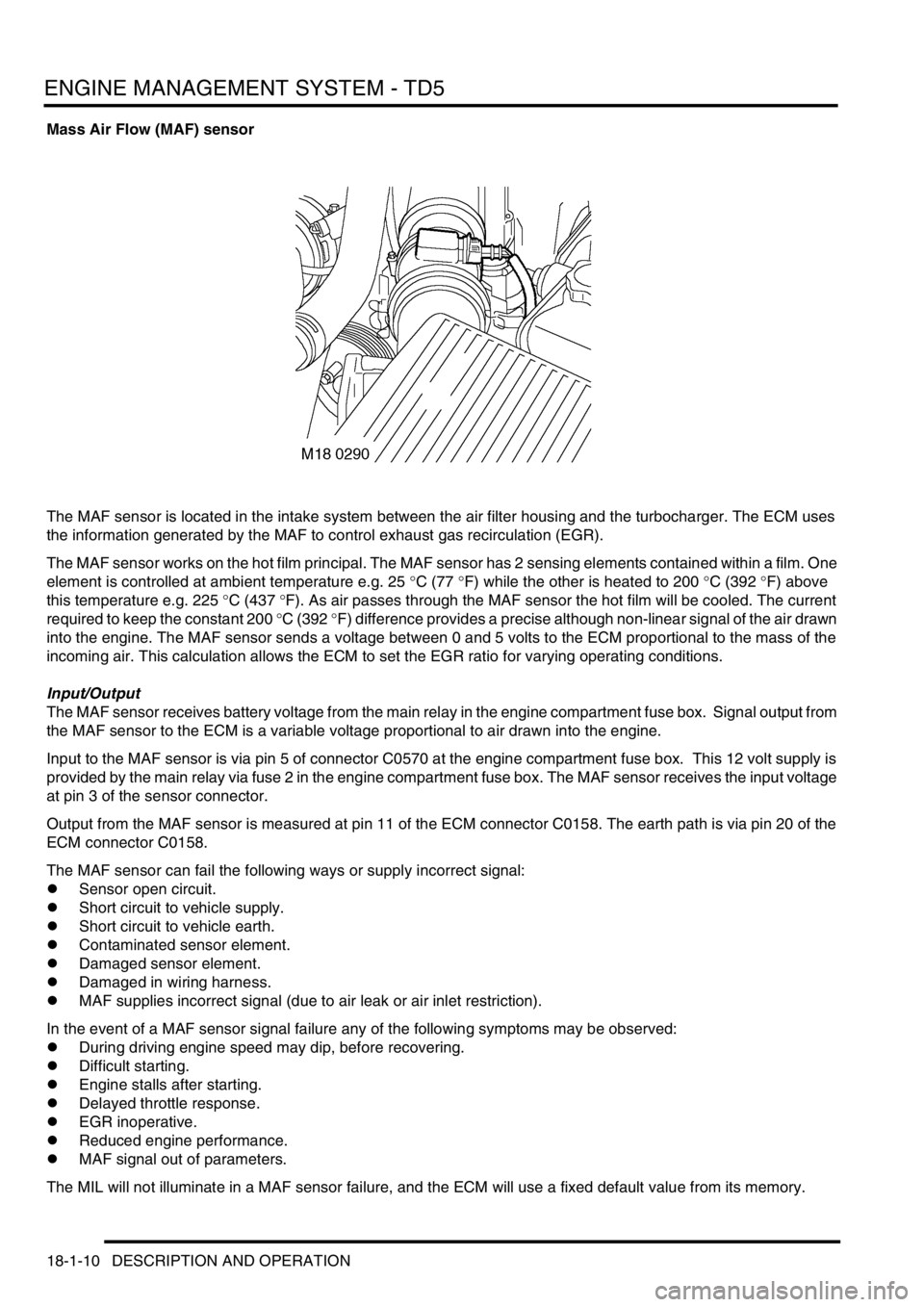
ENGINE MANAGEMENT SYSTEM - TD5
18-1-10 DESCRIPTION AND OPERATION
Mass Air Flow (MAF) sensor
The MAF sensor is located in the intake system between the air filter housing and the turbocharger. The ECM uses
the information generated by the MAF to control exhaust gas recirculation (EGR).
The MAF sensor works on the hot film principal. The MAF sensor has 2 sensing elements contained within a film. One
element is controlled at ambient temperature e.g. 25
°C (77 °F) while the other is heated to 200 °C (392 °F) above
this temperature e.g. 225
°C (437 °F). As air passes through the MAF sensor the hot film will be cooled. The current
required to keep the constant 200
°C (392 °F) difference provides a precise although non-linear signal of the air drawn
into the engine. The MAF sensor sends a voltage between 0 and 5 volts to the ECM proportional to the mass of the
incoming air. This calculation allows the ECM to set the EGR ratio for varying operating conditions.
Input/Output
The MAF sensor receives battery voltage from the main relay in the engine compartment fuse box. Signal output from
the MAF sensor to the ECM is a variable voltage proportional to air drawn into the engine.
Input to the MAF sensor is via pin 5 of connector C0570 at the engine compartment fuse box. This 12 volt supply is
provided by the main relay via fuse 2 in the engine compartment fuse box. The MAF sensor receives the input voltage
at pin 3 of the sensor connector.
Output from the MAF sensor is measured at pin 11 of the ECM connector C0158. The earth path is via pin 20 of the
ECM connector C0158.
The MAF sensor can fail the following ways or supply incorrect signal:
lSensor open circuit.
lShort circuit to vehicle supply.
lShort circuit to vehicle earth.
lContaminated sensor element.
lDamaged sensor element.
lDamaged in wiring harness.
lMAF supplies incorrect signal (due to air leak or air inlet restriction).
In the event of a MAF sensor signal failure any of the following symptoms may be observed:
lDuring driving engine speed may dip, before recovering.
lDifficult starting.
lEngine stalls after starting.
lDelayed throttle response.
lEGR inoperative.
lReduced engine performance.
lMAF signal out of parameters.
The MIL will not illuminate in a MAF sensor failure, and the ECM will use a fixed default value from its memory.
Page 404 of 1672
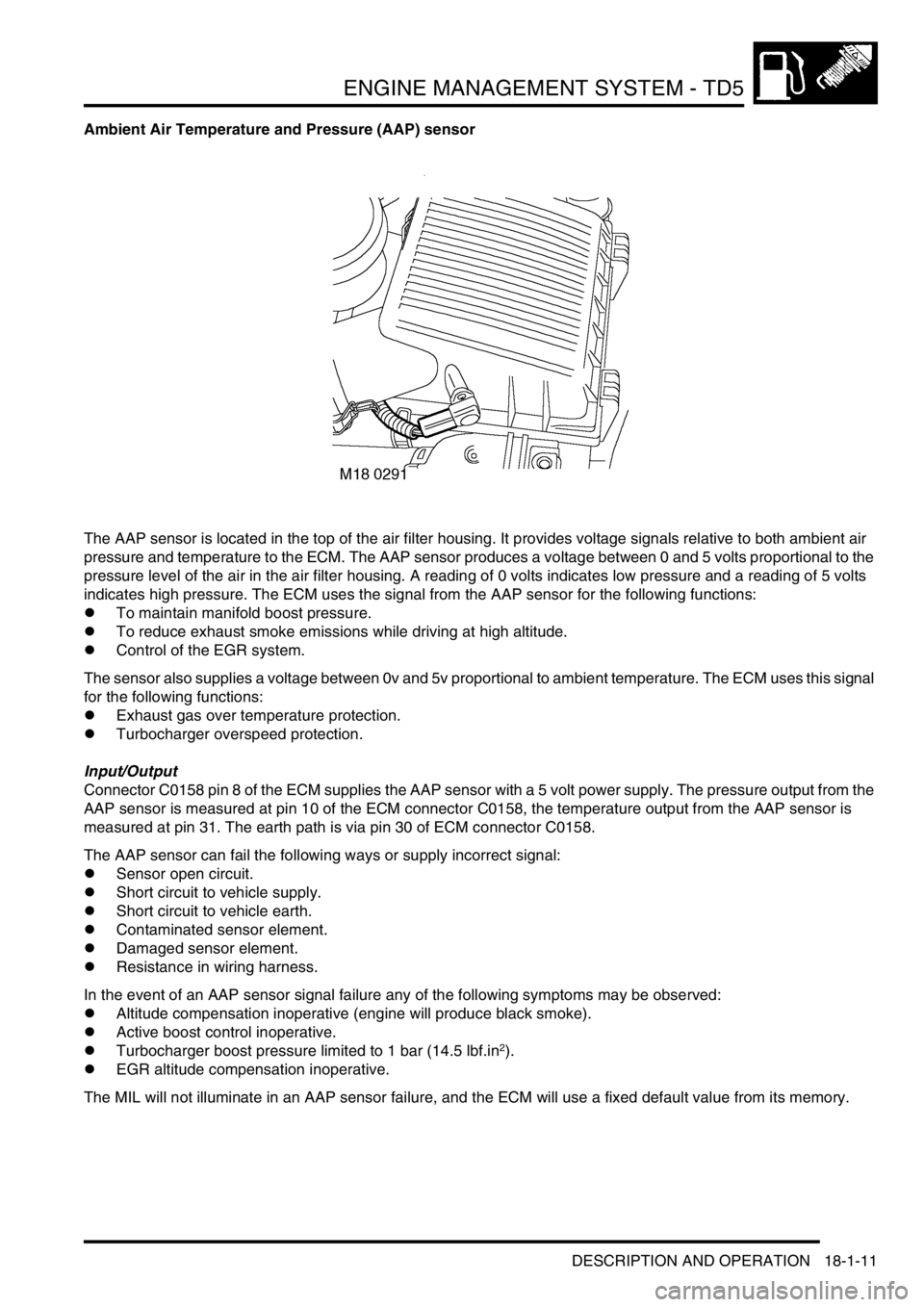
ENGINE MANAGEMENT SYSTEM - TD5
DESCRIPTION AND OPERATION 18-1-11
Ambient Air Temperature and Pressure (AAP) sensor
The AAP sensor is located in the top of the air filter housing. It provides voltage signals relative to both ambient air
pressure and temperature to the ECM. The AAP sensor produces a voltage between 0 and 5 volts proportional to the
pressure level of the air in the air filter housing. A reading of 0 volts indicates low pressure and a reading of 5 volts
indicates high pressure. The ECM uses the signal from the AAP sensor for the following functions:
lTo maintain manifold boost pressure.
lTo reduce exhaust smoke emissions while driving at high altitude.
lControl of the EGR system.
The sensor also supplies a voltage between 0v and 5v proportional to ambient temperature. The ECM uses this signal
for the following functions:
lExhaust gas over temperature protection.
lTurbocharger overspeed protection.
Input/Output
Connector C0158 pin 8 of the ECM supplies the AAP sensor with a 5 volt power supply. The pressure output from the
AAP sensor is measured at pin 10 of the ECM connector C0158, the temperature output from the AAP sensor is
measured at pin 31. The earth path is via pin 30 of ECM connector C0158.
The AAP sensor can fail the following ways or supply incorrect signal:
lSensor open circuit.
lShort circuit to vehicle supply.
lShort circuit to vehicle earth.
lContaminated sensor element.
lDamaged sensor element.
lResistance in wiring harness.
In the event of an AAP sensor signal failure any of the following symptoms may be observed:
lAltitude compensation inoperative (engine will produce black smoke).
lActive boost control inoperative.
lTurbocharger boost pressure limited to 1 bar (14.5 lbf.in
2).
lEGR altitude compensation inoperative.
The MIL will not illuminate in an AAP sensor failure, and the ECM will use a fixed default value from its memory.
Page 405 of 1672
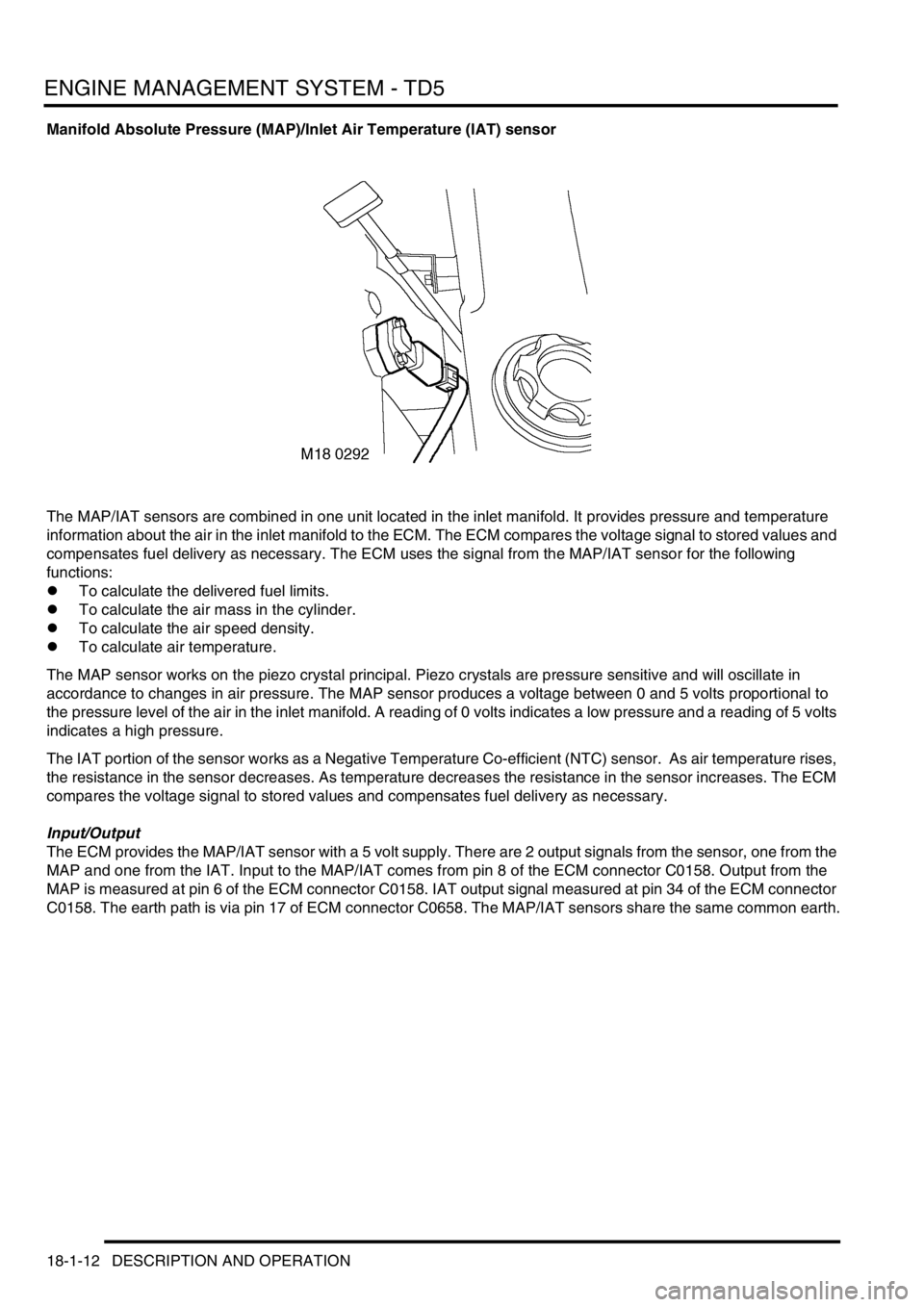
ENGINE MANAGEMENT SYSTEM - TD5
18-1-12 DESCRIPTION AND OPERATION
Manifold Absolute Pressure (MAP)/Inlet Air Temperature (IAT) sensor
The MAP/IAT sensors are combined in one unit located in the inlet manifold. It provides pressure and temperature
information about the air in the inlet manifold to the ECM. The ECM compares the voltage signal to stored values and
compensates fuel delivery as necessary. The ECM uses the signal from the MAP/IAT sensor for the following
functions:
lTo calculate the delivered fuel limits.
lTo calculate the air mass in the cylinder.
lTo calculate the air speed density.
lTo calculate air temperature.
The MAP sensor works on the piezo crystal principal. Piezo crystals are pressure sensitive and will oscillate in
accordance to changes in air pressure. The MAP sensor produces a voltage between 0 and 5 volts proportional to
the pressure level of the air in the inlet manifold. A reading of 0 volts indicates a low pressure and a reading of 5 volts
indicates a high pressure.
The IAT portion of the sensor works as a Negative Temperature Co-efficient (NTC) sensor. As air temperature rises,
the resistance in the sensor decreases. As temperature decreases the resistance in the sensor increases. The ECM
compares the voltage signal to stored values and compensates fuel delivery as necessary.
Input/Output
The ECM provides the MAP/IAT sensor with a 5 volt supply. There are 2 output signals from the sensor, one from the
MAP and one from the IAT. Input to the MAP/IAT comes from pin 8 of the ECM connector C0158. Output from the
MAP is measured at pin 6 of the ECM connector C0158. IAT output signal measured at pin 34 of the ECM connector
C0158. The earth path is via pin 17 of ECM connector C0658. The MAP/IAT sensors share the same common earth.
Page 406 of 1672
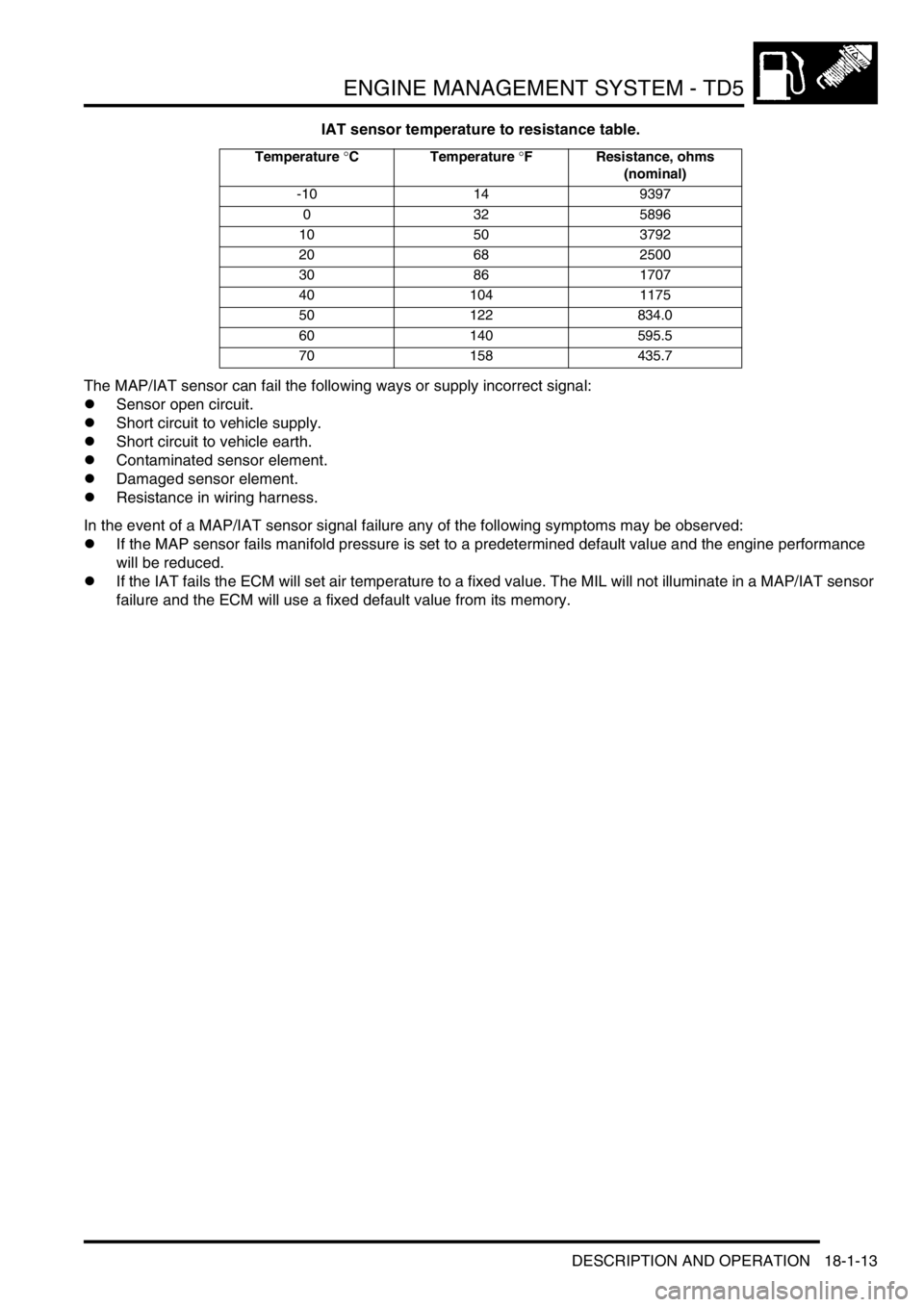
ENGINE MANAGEMENT SYSTEM - TD5
DESCRIPTION AND OPERATION 18-1-13
IAT sensor temperature to resistance table.
The MAP/IAT sensor can fail the following ways or supply incorrect signal:
lSensor open circuit.
lShort circuit to vehicle supply.
lShort circuit to vehicle earth.
lContaminated sensor element.
lDamaged sensor element.
lResistance in wiring harness.
In the event of a MAP/IAT sensor signal failure any of the following symptoms may be observed:
lIf the MAP sensor fails manifold pressure is set to a predetermined default value and the engine performance
will be reduced.
lIf the IAT fails the ECM will set air temperature to a fixed value. The MIL will not illuminate in a MAP/IAT sensor
failure and the ECM will use a fixed default value from its memory.
Temperature °CTemperature °F Resistance, ohms
(nominal)
-10 14 9397
0 32 5896
10 50 3792
20 68 2500
30 86 1707
40 104 1175
50 122 834.0
60 140 595.5
70 158 435.7
Page 407 of 1672
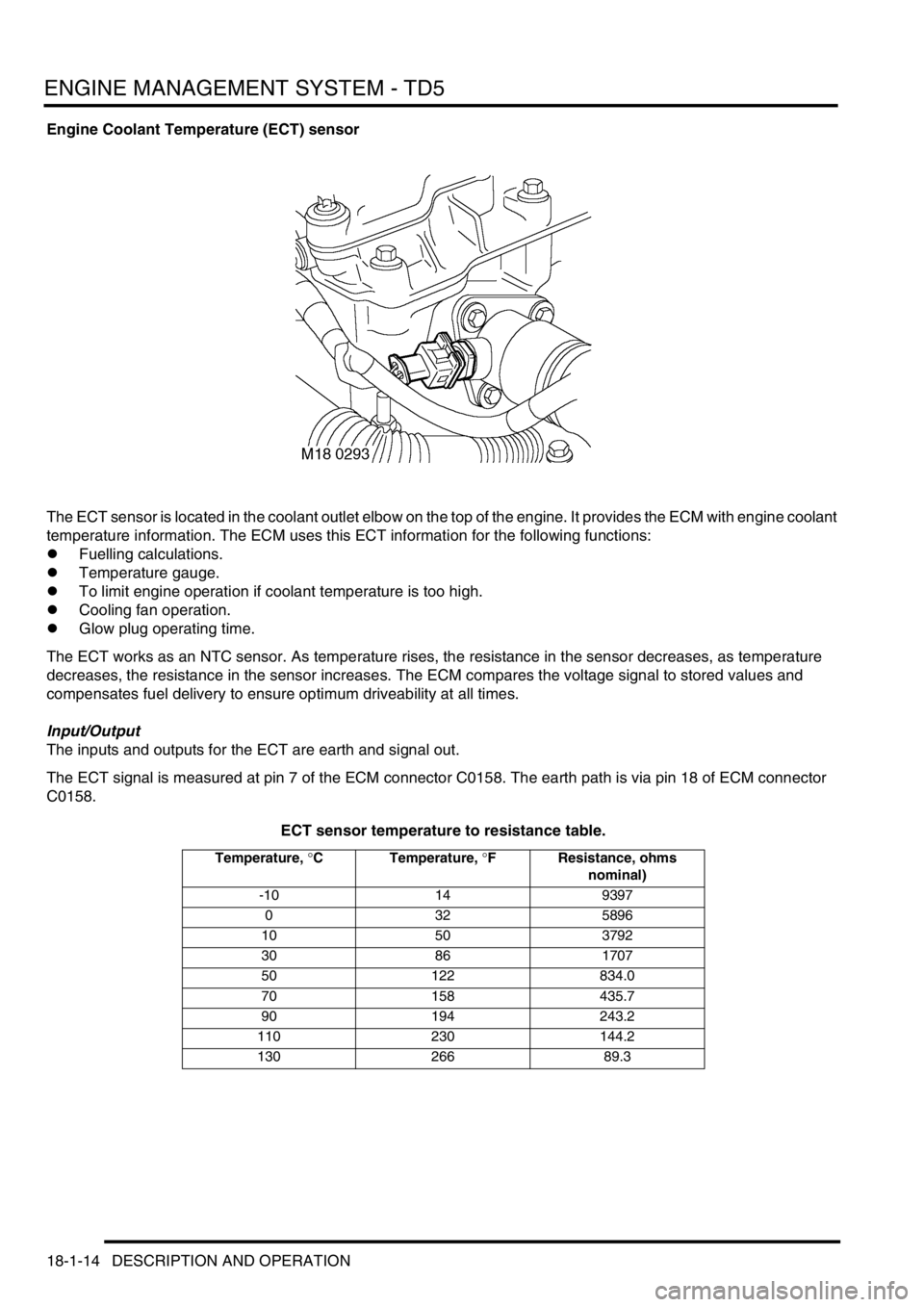
ENGINE MANAGEMENT SYSTEM - TD5
18-1-14 DESCRIPTION AND OPERATION
Engine Coolant Temperature (ECT) sensor
The ECT sensor is located in the coolant outlet elbow on the top of the engine. It provides the ECM with engine coolant
temperature information. The ECM uses this ECT information for the following functions:
lFuelling calculations.
lTemperature gauge.
lTo limit engine operation if coolant temperature is too high.
lCooling fan operation.
lGlow plug operating time.
The ECT works as an NTC sensor. As temperature rises, the resistance in the sensor decreases, as temperature
decreases, the resistance in the sensor increases. The ECM compares the voltage signal to stored values and
compensates fuel delivery to ensure optimum driveability at all times.
Input/Output
The inputs and outputs for the ECT are earth and signal out.
The ECT signal is measured at pin 7 of the ECM connector C0158. The earth path is via pin 18 of ECM connector
C0158.
ECT sensor temperature to resistance table.
Temperature, °C Temperature, °F Resistance, ohms
nominal)
-10 14 9397
0325896
10 50 3792
30 86 1707
50 122 834.0
70 158 435.7
90 194 243.2
110 230 144.2
130 266 89.3
Page 408 of 1672
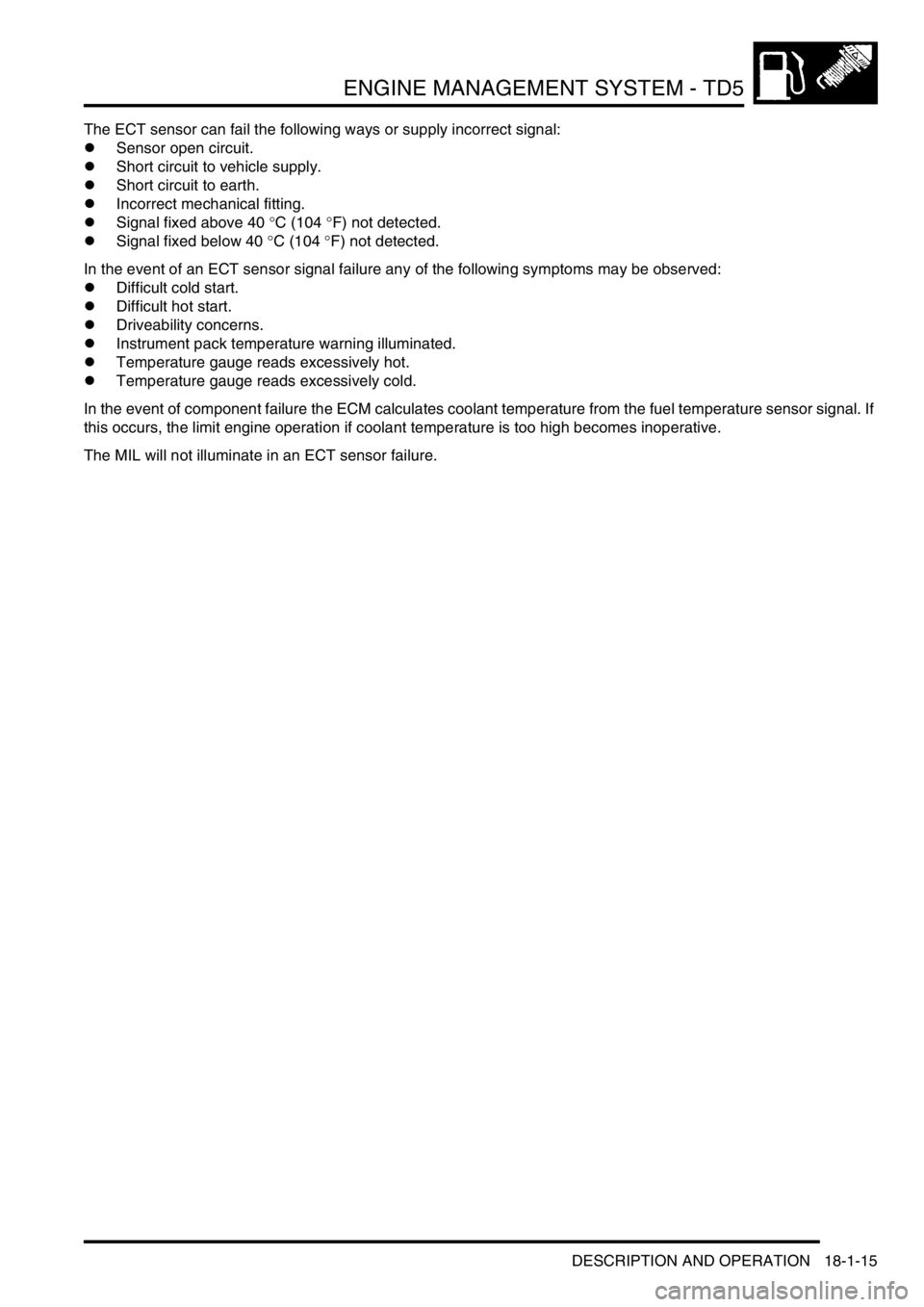
ENGINE MANAGEMENT SYSTEM - TD5
DESCRIPTION AND OPERATION 18-1-15
The ECT sensor can fail the following ways or supply incorrect signal:
lSensor open circuit.
lShort circuit to vehicle supply.
lShort circuit to earth.
lIncorrect mechanical fitting.
lSignal fixed above 40
°C (104 °F) not detected.
lSignal fixed below 40
°C (104 °F) not detected.
In the event of an ECT sensor signal failure any of the following symptoms may be observed:
lDifficult cold start.
lDifficult hot start.
lDriveability concerns.
lInstrument pack temperature warning illuminated.
lTemperature gauge reads excessively hot.
lTemperature gauge reads excessively cold.
In the event of component failure the ECM calculates coolant temperature from the fuel temperature sensor signal. If
this occurs, the limit engine operation if coolant temperature is too high becomes inoperative.
The MIL will not illuminate in an ECT sensor failure.
Page 409 of 1672
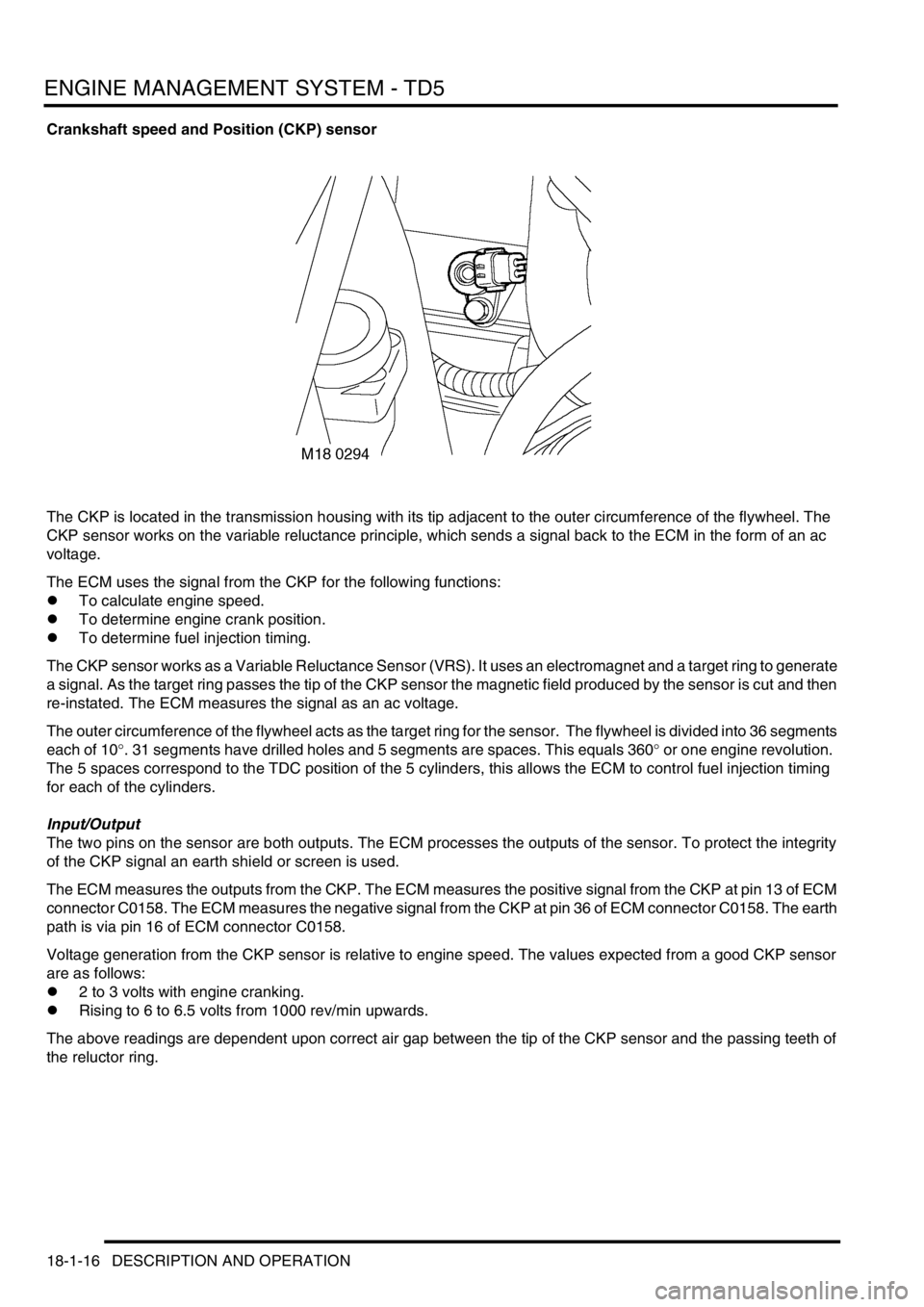
ENGINE MANAGEMENT SYSTEM - TD5
18-1-16 DESCRIPTION AND OPERATION
Crankshaft speed and Position (CKP) sensor
The CKP is located in the transmission housing with its tip adjacent to the outer circumference of the flywheel. The
CKP sensor works on the variable reluctance principle, which sends a signal back to the ECM in the form of an ac
voltage.
The ECM uses the signal from the CKP for the following functions:
lTo calculate engine speed.
lTo determine engine crank position.
lTo determine fuel injection timing.
The CKP sensor works as a Variable Reluctance Sensor (VRS). It uses an electromagnet and a target ring to generate
a signal. As the target ring passes the tip of the CKP sensor the magnetic field produced by the sensor is cut and then
re-instated. The ECM measures the signal as an ac voltage.
The outer circumference of the flywheel acts as the target ring for the sensor. The flywheel is divided into 36 segments
each of 10
°. 31 segments have drilled holes and 5 segments are spaces. This equals 360° or one engine revolution.
The 5 spaces correspond to the TDC position of the 5 cylinders, this allows the ECM to control fuel injection timing
for each of the cylinders.
Input/Output
The two pins on the sensor are both outputs. The ECM processes the outputs of the sensor. To protect the integrity
of the CKP signal an earth shield or screen is used.
The ECM measures the outputs from the CKP. The ECM measures the positive signal from the CKP at pin 13 of ECM
connector C0158. The ECM measures the negative signal from the CKP at pin 36 of ECM connector C0158. The earth
path is via pin 16 of ECM connector C0158.
Voltage generation from the CKP sensor is relative to engine speed. The values expected from a good CKP sensor
are as follows:
l2 to 3 volts with engine cranking.
lRising to 6 to 6.5 volts from 1000 rev/min upwards.
The above readings are dependent upon correct air gap between the tip of the CKP sensor and the passing teeth of
the reluctor ring.
Page 410 of 1672
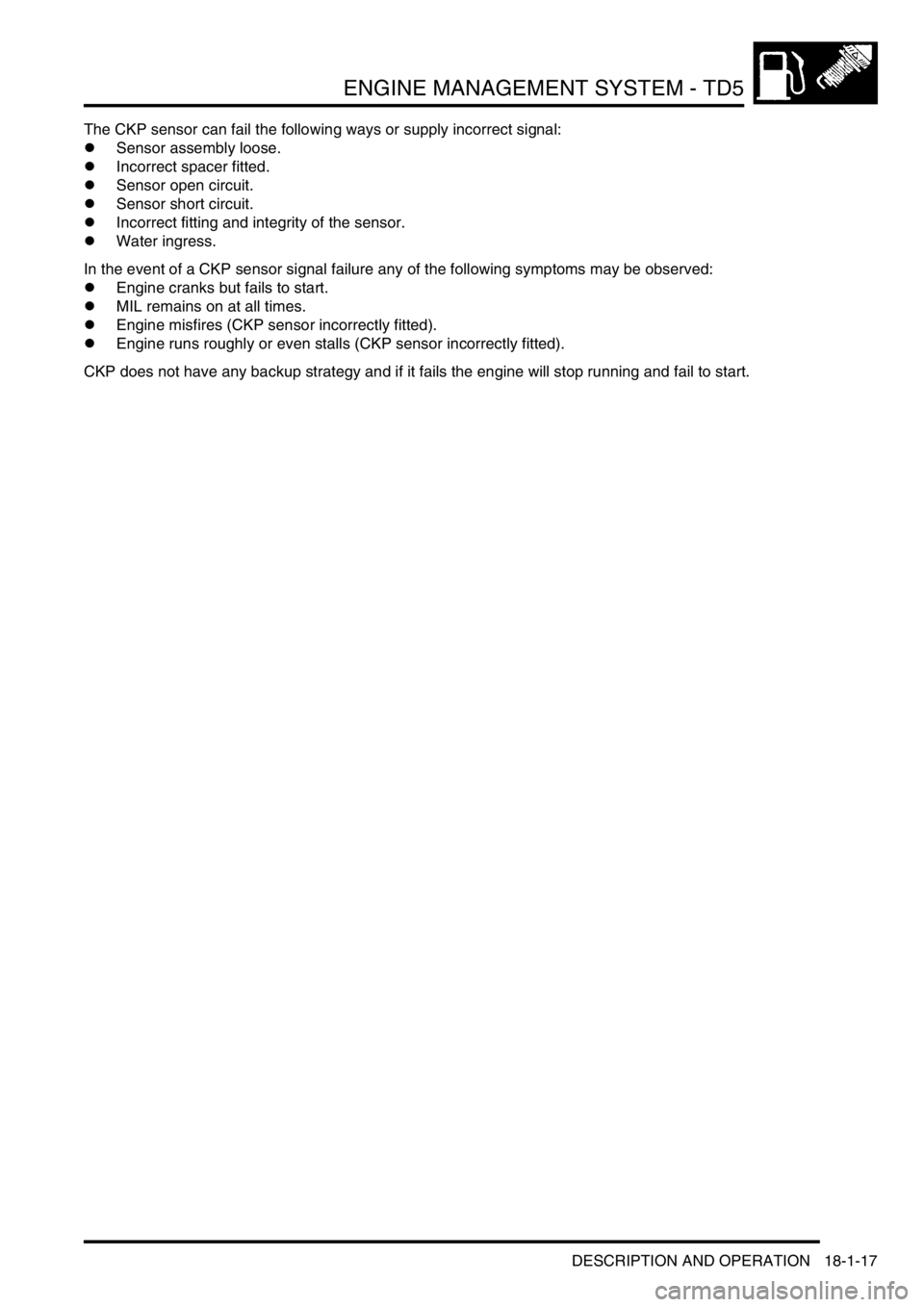
ENGINE MANAGEMENT SYSTEM - TD5
DESCRIPTION AND OPERATION 18-1-17
The CKP sensor can fail the following ways or supply incorrect signal:
lSensor assembly loose.
lIncorrect spacer fitted.
lSensor open circuit.
lSensor short circuit.
lIncorrect fitting and integrity of the sensor.
lWater ingress.
In the event of a CKP sensor signal failure any of the following symptoms may be observed:
lEngine cranks but fails to start.
lMIL remains on at all times.
lEngine misfires (CKP sensor incorrectly fitted).
lEngine runs roughly or even stalls (CKP sensor incorrectly fitted).
CKP does not have any backup strategy and if it fails the engine will stop running and fail to start.