LAND ROVER FREELANDER 2001 Repair Manual
Manufacturer: LAND ROVER, Model Year: 2001, Model line: FREELANDER, Model: LAND ROVER FREELANDER 2001Pages: 1007, PDF Size: 23.47 MB
Page 61 of 1007
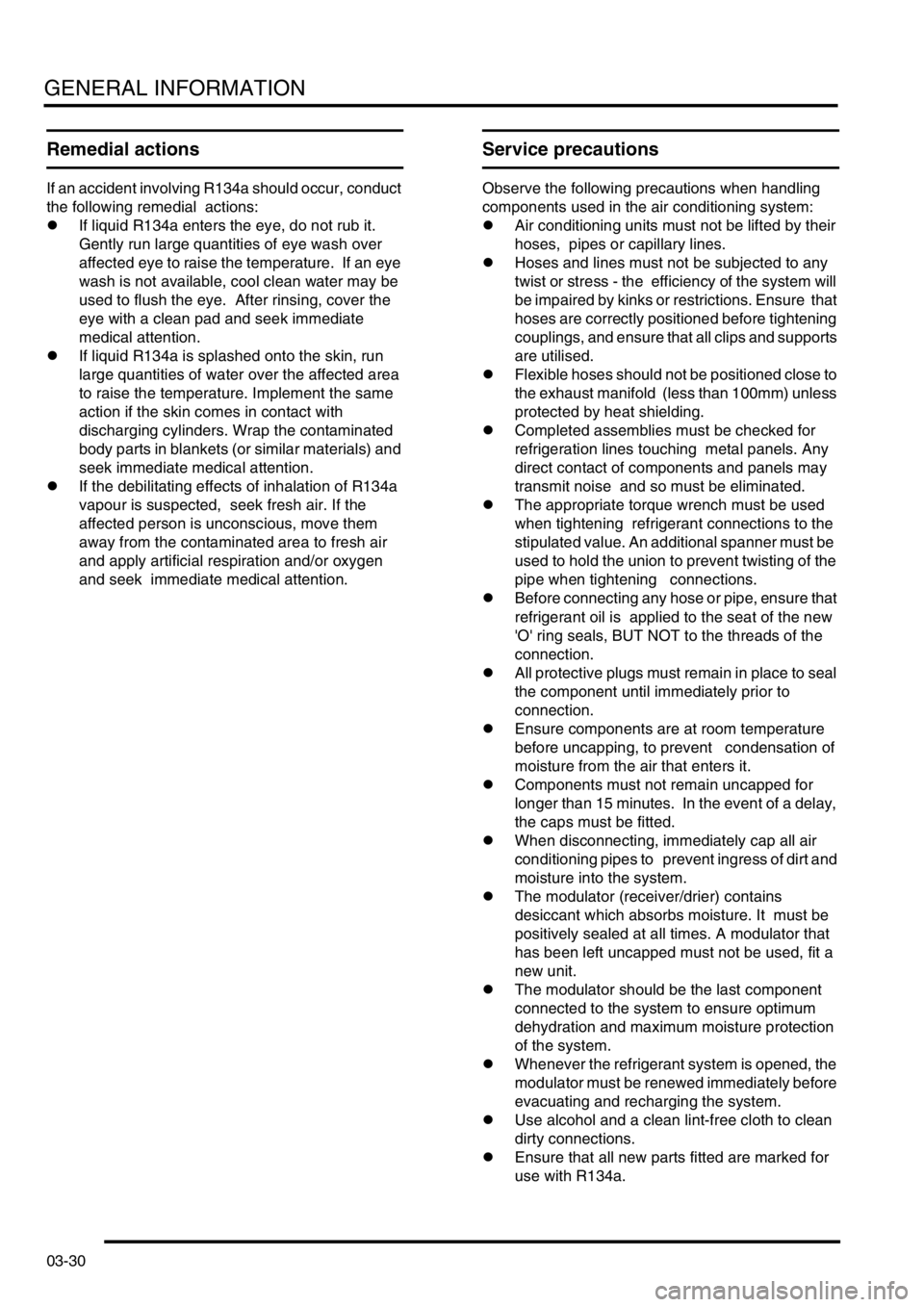
GENERAL INFORMATION
03-30
Remedial actions
If an accident involving R134a should occur, conduct
the following remedial actions:
lIf liquid R134a enters the eye, do not rub it.
Gently run large quantities of eye wash over
affected eye to raise the temperature. If an eye
wash is not available, cool clean water may be
used to flush the eye. After rinsing, cover the
eye with a clean pad and seek immediate
medical attention.
lIf liquid R134a is splashed onto the skin, run
large quantities of water over the affected area
to raise the temperature. Implement the same
action if the skin comes in contact with
discharging cylinders. Wrap the contaminated
body parts in blankets (or similar materials) and
seek immediate medical attention.
lIf the debilitating effects of inhalation of R134a
vapour is suspected, seek fresh air. If the
affected person is unconscious, move them
away from the contaminated area to fresh air
and apply artificial respiration and/or oxygen
and seek immediate medical attention.
Service precautions
Observe the following precautions when handling
components used in the air conditioning system:
lAir conditioning units must not be lifted by their
hoses, pipes or capillary lines.
lHoses and lines must not be subjected to any
twist or stress - the efficiency of the system will
be impaired by kinks or restrictions. Ensure that
hoses are correctly positioned before tightening
couplings, and ensure that all clips and supports
are utilised.
lFlexible hoses should not be positioned close to
the exhaust manifold (less than 100mm) unless
protected by heat shielding.
lCompleted assemblies must be checked for
refrigeration lines touching metal panels. Any
direct contact of components and panels may
transmit noise and so must be eliminated.
lThe appropriate torque wrench must be used
when tightening refrigerant connections to the
stipulated value. An additional spanner must be
used to hold the union to prevent twisting of the
pipe when tightening connections.
lBefore connecting any hose or pipe, ensure that
refrigerant oil is applied to the seat of the new
'O' ring seals, BUT NOT to the threads of the
connection.
lAll protective plugs must remain in place to seal
the component until immediately prior to
connection.
lEnsure components are at room temperature
before uncapping, to prevent condensation of
moisture from the air that enters it.
lComponents must not remain uncapped for
longer than 15 minutes. In the event of a delay,
the caps must be fitted.
lWhen disconnecting, immediately cap all air
conditioning pipes to prevent ingress of dirt and
moisture into the system.
lThe modulator (receiver/drier) contains
desiccant which absorbs moisture. It must be
positively sealed at all times. A modulator that
has been left uncapped must not be used, fit a
new unit.
lThe modulator should be the last component
connected to the system to ensure optimum
dehydration and maximum moisture protection
of the system.
lWhenever the refrigerant system is opened, the
modulator must be renewed immediately before
evacuating and recharging the system.
lUse alcohol and a clean lint-free cloth to clean
dirty connections.
lEnsure that all new parts fitted are marked for
use with R134a.
Page 62 of 1007
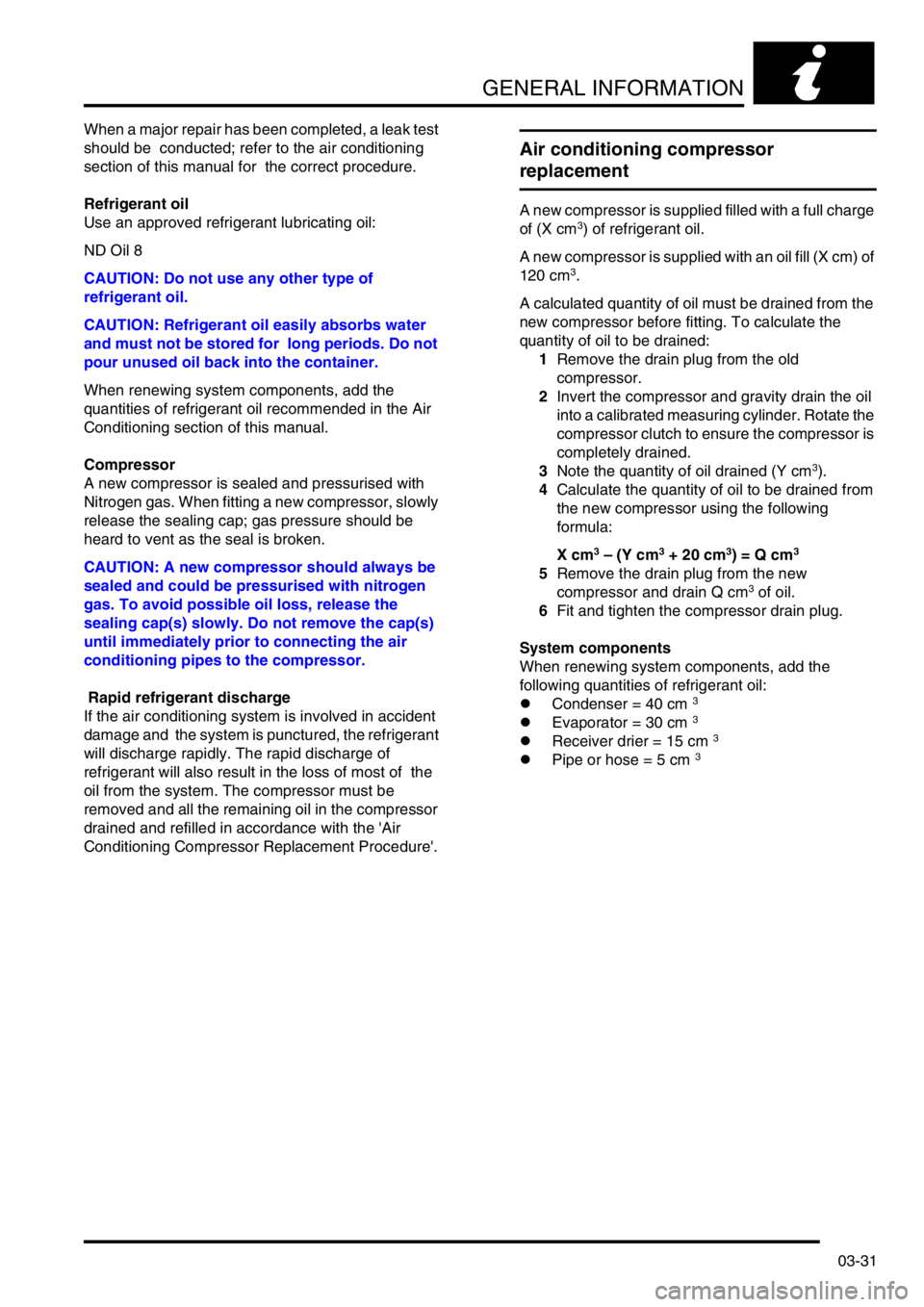
GENERAL INFORMATION
03-31
When a major repair has been completed, a leak test
should be conducted; refer to the air conditioning
section of this manual for the correct procedure.
Refrigerant oil
Use an approved refrigerant lubricating oil:
ND Oil 8
CAUTION: Do not use any other type of
refrigerant oil.
CAUTION: Refrigerant oil easily absorbs water
and must not be stored for long periods. Do not
pour unused oil back into the container.
When renewing system components, add the
quantities of refrigerant oil recommended in the Air
Conditioning section of this manual.
Compressor
A new compressor is sealed and pressurised with
Nitrogen gas. When fitting a new compressor, slowly
release the sealing cap; gas pressure should be
heard to vent as the seal is broken.
CAUTION: A new compressor should always be
sealed and could be pressurised with nitrogen
gas. To avoid possible oil loss, release the
sealing cap(s) slowly. Do not remove the cap(s)
until immediately prior to connecting the air
conditioning pipes to the compressor.
Rapid refrigerant discharge
If the air conditioning system is involved in accident
damage and the system is punctured, the refrigerant
will discharge rapidly. The rapid discharge of
refrigerant will also result in the loss of most of the
oil from the system. The compressor must be
removed and all the remaining oil in the compressor
drained and refilled in accordance with the 'Air
Conditioning Compressor Replacement Procedure'.
Air conditioning compressor
replacement
A new compressor is supplied filled with a full charge
of (X cm3) of refrigerant oil.
A new compressor is supplied with an oil fill (X cm) of
120 cm
3.
A calculated quantity of oil must be drained from the
new compressor before fitting. To calculate the
quantity of oil to be drained:
1Remove the drain plug from the old
compressor.
2Invert the compressor and gravity drain the oil
into a calibrated measuring cylinder. Rotate the
compressor clutch to ensure the compressor is
completely drained.
3Note the quantity of oil drained (Y cm
3).
4Calculate the quantity of oil to be drained from
the new compressor using the following
formula:
X cm
3 – (Y cm3 + 20 cm3) = Q cm3
5Remove the drain plug from the new
compressor and drain Q cm3 of oil.
6Fit and tighten the compressor drain plug.
System components
When renewing system components, add the
following quantities of refrigerant oil:
lCondenser = 40 cm
3
lEvaporator = 30 cm 3
lReceiver drier = 15 cm 3
lPipe or hose = 5 cm 3
Page 63 of 1007
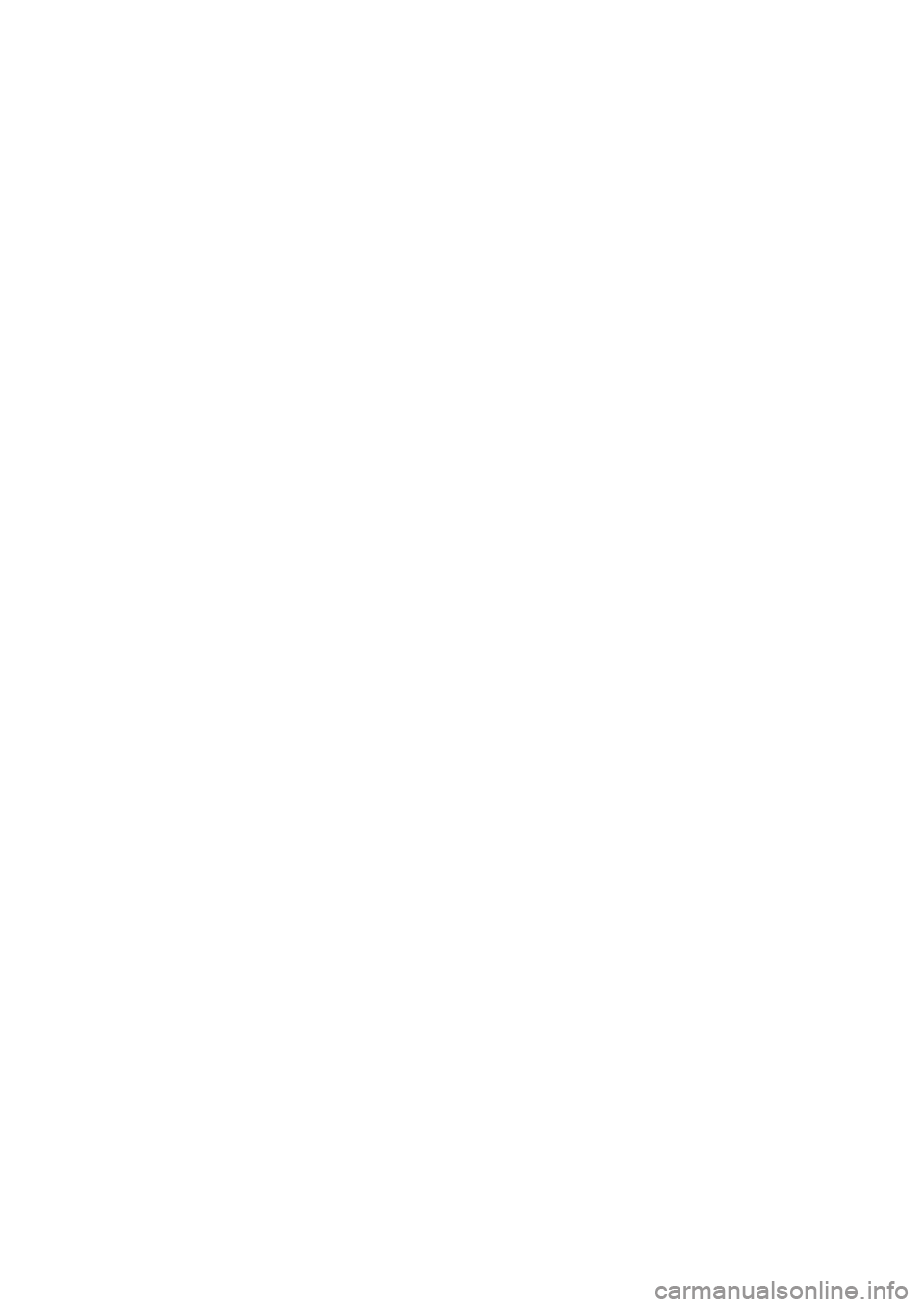
Page 64 of 1007
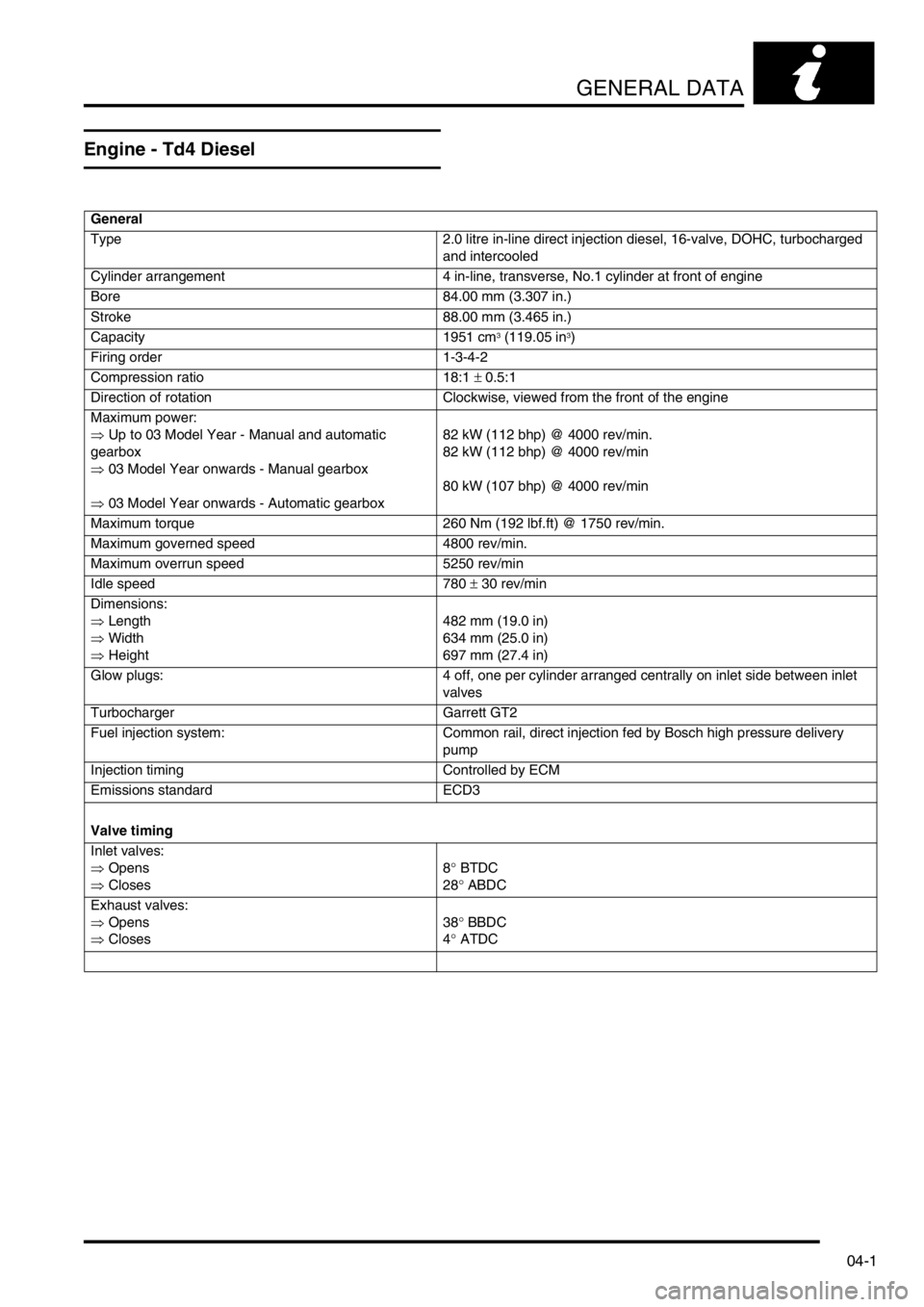
GENERAL DATA
04-1
GENERAL DATA
Engine - Td4 Diesel
General
Type 2.0 litre in-line direct injection diesel, 16-valve, DOHC, turbocharged
and intercooled
Cylinder arrangement 4 in-line, transverse, No.1 cylinder at front of engine
Bore 84.00 mm (3.307 in.)
Stroke 88.00 mm (3.465 in.)
Capacity 1951 cm
3 (119.05 in3)
Firing order 1-3-4-2
Compression ratio 18:1 ± 0.5:1
Direction of rotation Clockwise, viewed from the front of the engine
Maximum power:
⇒ Up to 03 Model Year - Manual and automatic
gearbox
⇒ 03 Model Year onwards - Manual gearbox
⇒ 03 Model Year onwards - Automatic gearbox82 kW (112 bhp) @ 4000 rev/min.
82 kW (112 bhp) @ 4000 rev/min
80 kW (107 bhp) @ 4000 rev/min
Maximum torque 260 Nm (192 lbf.ft) @ 1750 rev/min.
Maximum governed speed 4800 rev/min.
Maximum overrun speed 5250 rev/min
Idle speed 780 ± 30 rev/min
Dimensions:
⇒ Length
⇒ Width
⇒ Height482 mm (19.0 in)
634 mm (25.0 in)
697 mm (27.4 in)
Glow plugs: 4 off, one per cylinder arranged centrally on inlet side between inlet
valves
Turbocharger Garrett GT2
Fuel injection system: Common rail, direct injection fed by Bosch high pressure delivery
pump
Injection timing Controlled by ECM
Emissions standard ECD3
Valve timing
Inlet valves:
⇒ Opens
⇒ Closes8° BTDC
28° ABDC
Exhaust valves:
⇒ Opens
⇒ Closes38° BBDC
4° ATDC
Page 65 of 1007
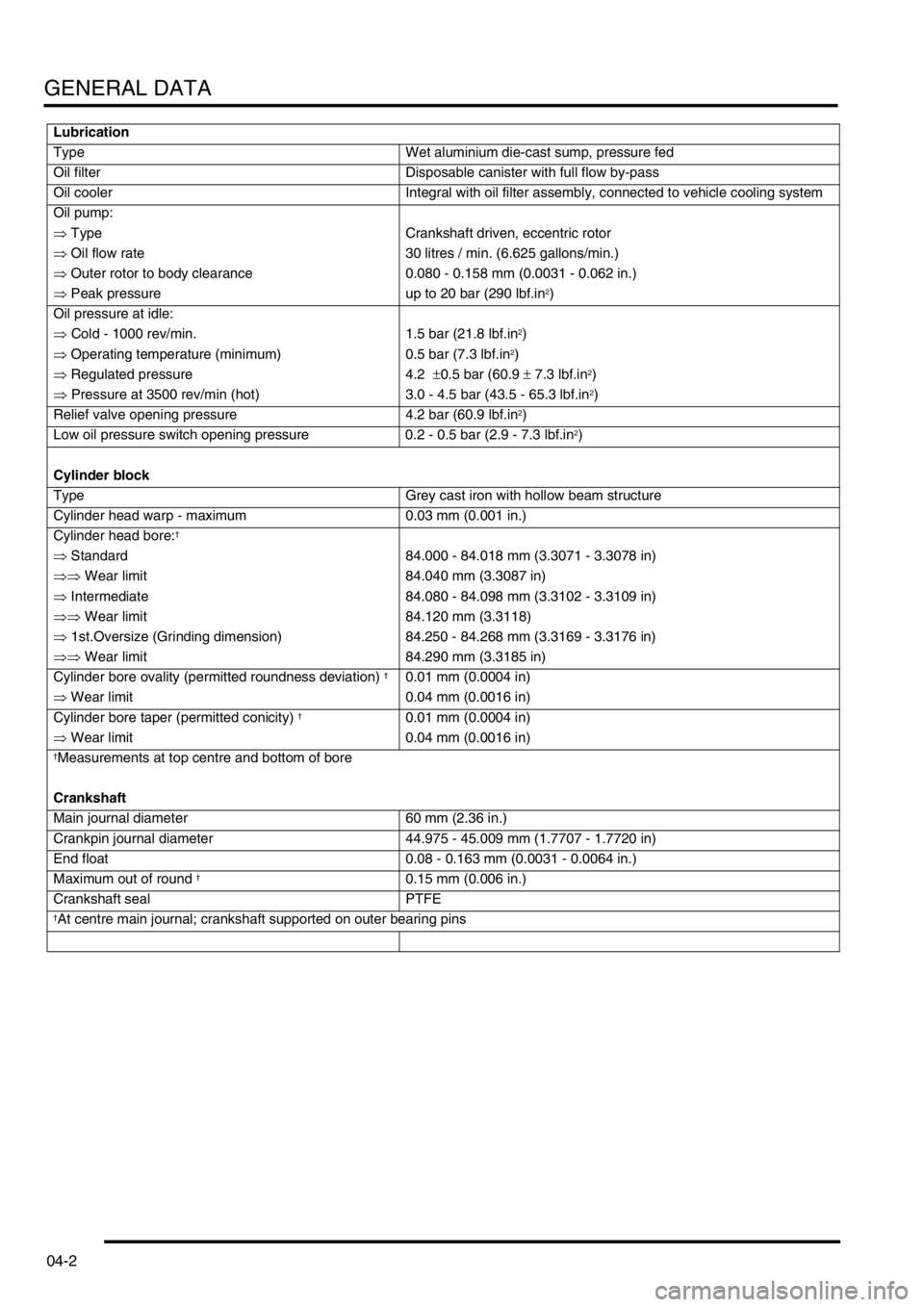
GENERAL DATA
04-2
Lubrication
Type Wet aluminium die-cast sump, pressure fed
Oil filter Disposable canister with full flow by-pass
Oil cooler Integral with oil filter assembly, connected to vehicle cooling system
Oil pump:
⇒ Type Crankshaft driven, eccentric rotor
⇒ Oil flow rate 30 litres / min. (6.625 gallons/min.)
⇒ Outer rotor to body clearance 0.080 - 0.158 mm (0.0031 - 0.062 in.)
⇒ Peak pressure up to 20 bar (290 lbf.in
2)
Oil pressure at idle:
⇒ Cold - 1000 rev/min. 1.5 bar (21.8 lbf.in
2)
⇒ Operating temperature (minimum) 0.5 bar (7.3 lbf.in
2)
⇒ Regulated pressure 4.2 ±0.5 bar (60.9 ± 7.3 lbf.in
2)
⇒ Pressure at 3500 rev/min (hot) 3.0 - 4.5 bar (43.5 - 65.3 lbf.in
2)
Relief valve opening pressure 4.2 bar (60.9 lbf.in
2)
Low oil pressure switch opening pressure 0.2 - 0.5 bar (2.9 - 7.3 lbf.in
2)
Cylinder block
Type Grey cast iron with hollow beam structure
Cylinder head warp - maximum 0.03 mm (0.001 in.)
Cylinder head bore:
†
⇒ Standard 84.000 - 84.018 mm (3.3071 - 3.3078 in)
⇒⇒ Wear limit 84.040 mm (3.3087 in)
⇒ Intermediate 84.080 - 84.098 mm (3.3102 - 3.3109 in)
⇒⇒ Wear limit 84.120 mm (3.3118)
⇒ 1st.Oversize (Grinding dimension) 84.250 - 84.268 mm (3.3169 - 3.3176 in)
⇒⇒ Wear limit 84.290 mm (3.3185 in)
Cylinder bore ovality (permitted roundness deviation)
†0.01 mm (0.0004 in)
⇒ Wear limit 0.04 mm (0.0016 in)
Cylinder bore taper (permitted conicity)
†0.01 mm (0.0004 in)
⇒ Wear limit 0.04 mm (0.0016 in)
†Measurements at top centre and bottom of bore
Crankshaft
Main journal diameter 60 mm (2.36 in.)
Crankpin journal diameter 44.975 - 45.009 mm (1.7707 - 1.7720 in)
End float 0.08 - 0.163 mm (0.0031 - 0.0064 in.)
Maximum out of round
†0.15 mm (0.006 in.)
Crankshaft seal PTFE
†At centre main journal; crankshaft supported on outer bearing pins
Page 66 of 1007
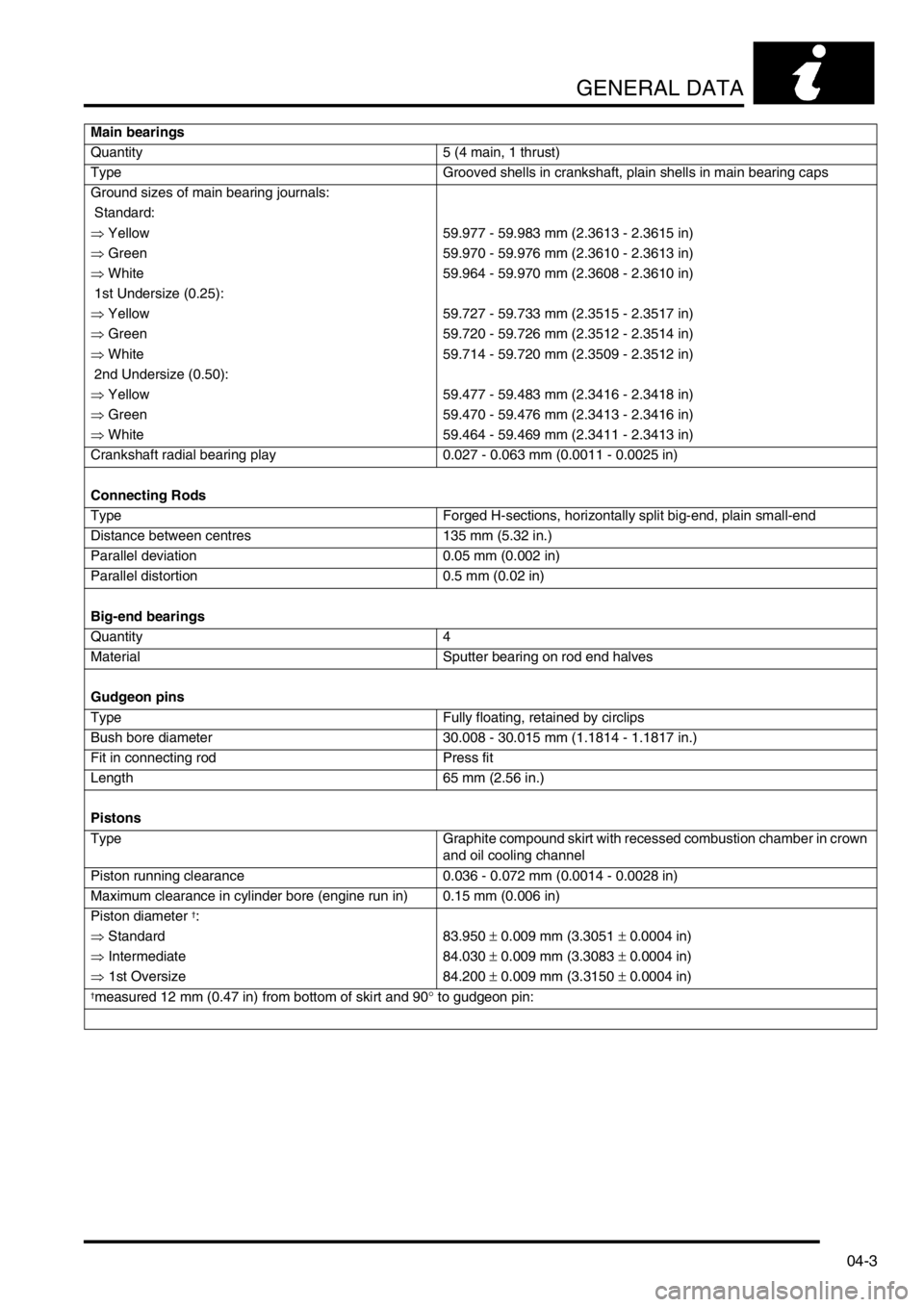
GENERAL DATA
04-3
Main bearings
Quantity 5 (4 main, 1 thrust)
Type Grooved shells in crankshaft, plain shells in main bearing caps
Ground sizes of main bearing journals:
Standard:
⇒ Yellow 59.977 - 59.983 mm (2.3613 - 2.3615 in)
⇒ Green 59.970 - 59.976 mm (2.3610 - 2.3613 in)
⇒ White 59.964 - 59.970 mm (2.3608 - 2.3610 in)
1st Undersize (0.25):
⇒ Yellow 59.727 - 59.733 mm (2.3515 - 2.3517 in)
⇒ Green 59.720 - 59.726 mm (2.3512 - 2.3514 in)
⇒ White 59.714 - 59.720 mm (2.3509 - 2.3512 in)
2nd Undersize (0.50):
⇒ Yellow 59.477 - 59.483 mm (2.3416 - 2.3418 in)
⇒ Green 59.470 - 59.476 mm (2.3413 - 2.3416 in)
⇒ White 59.464 - 59.469 mm (2.3411 - 2.3413 in)
Crankshaft radial bearing play 0.027 - 0.063 mm (0.0011 - 0.0025 in)
Connecting Rods
Type Forged H-sections, horizontally split big-end, plain small-end
Distance between centres 135 mm (5.32 in.)
Parallel deviation 0.05 mm (0.002 in)
Parallel distortion 0.5 mm (0.02 in)
Big-end bearings
Quantity 4
Material Sputter bearing on rod end halves
Gudgeon pins
Type Fully floating, retained by circlips
Bush bore diameter 30.008 - 30.015 mm (1.1814 - 1.1817 in.)
Fit in connecting rod Press fit
Length 65 mm (2.56 in.)
Pistons
Type Graphite compound skirt with recessed combustion chamber in crown
and oil cooling channel
Piston running clearance 0.036 - 0.072 mm (0.0014 - 0.0028 in)
Maximum clearance in cylinder bore (engine run in) 0.15 mm (0.006 in)
Piston diameter
†:
⇒ Standard 83.950 ± 0.009 mm (3.3051 ± 0.0004 in)
⇒ Intermediate 84.030 ± 0.009 mm (3.3083 ± 0.0004 in)
⇒ 1st Oversize 84.200 ± 0.009 mm (3.3150 ± 0.0004 in)
†measured 12 mm (0.47 in) from bottom of skirt and 90° to gudgeon pin:
Page 67 of 1007
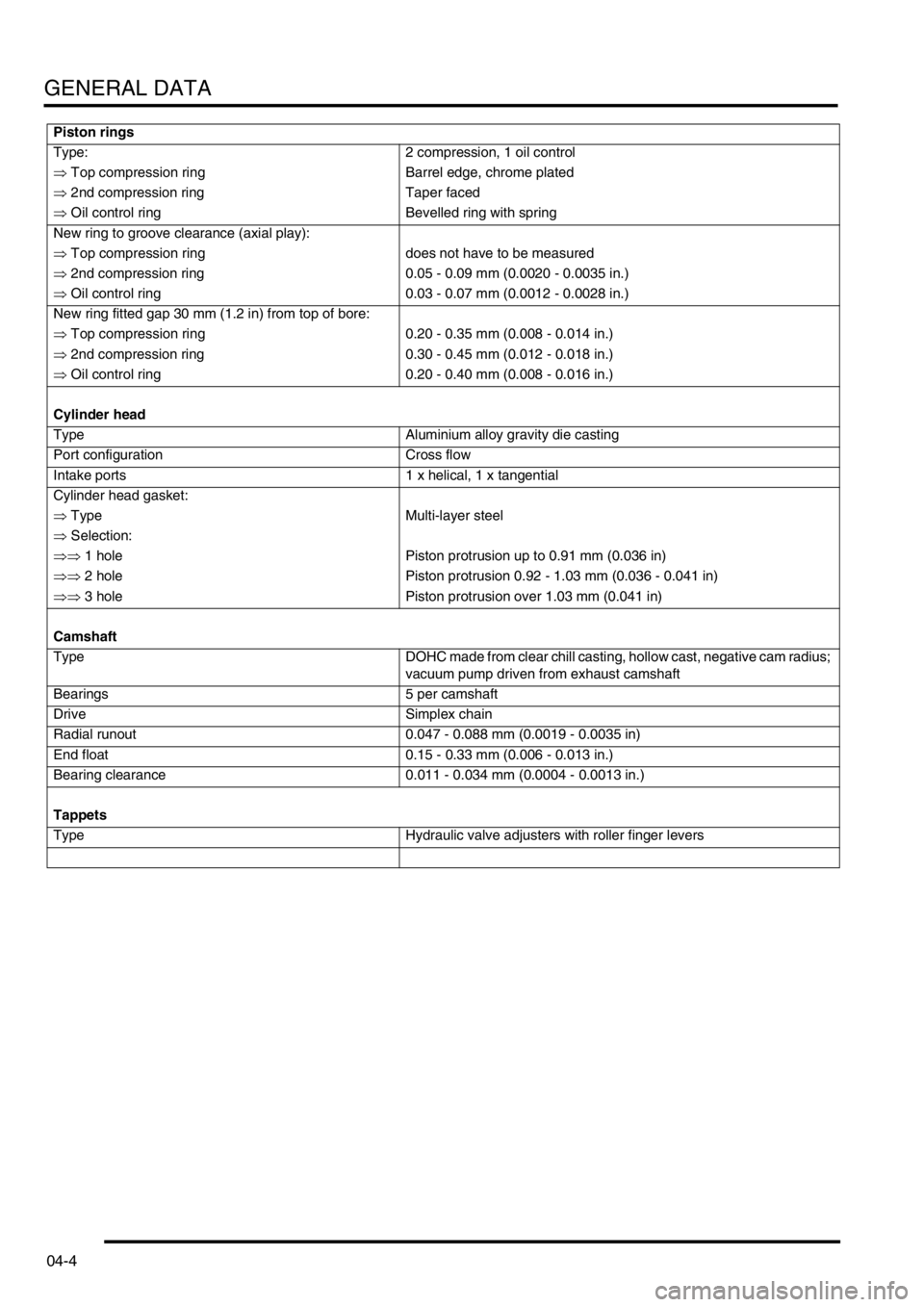
GENERAL DATA
04-4
Piston rings
Type: 2 compression, 1 oil control
⇒ Top compression ring Barrel edge, chrome plated
⇒ 2nd compression ring Taper faced
⇒ Oil control ring Bevelled ring with spring
New ring to groove clearance (axial play):
⇒ Top compression ring does not have to be measured
⇒ 2nd compression ring 0.05 - 0.09 mm (0.0020 - 0.0035 in.)
⇒ Oil control ring 0.03 - 0.07 mm (0.0012 - 0.0028 in.)
New ring fitted gap 30 mm (1.2 in) from top of bore:
⇒ Top compression ring 0.20 - 0.35 mm (0.008 - 0.014 in.)
⇒ 2nd compression ring 0.30 - 0.45 mm (0.012 - 0.018 in.)
⇒ Oil control ring 0.20 - 0.40 mm (0.008 - 0.016 in.)
Cylinder head
Type Aluminium alloy gravity die casting
Port configuration Cross flow
Intake ports 1 x helical, 1 x tangential
Cylinder head gasket:
⇒ Type Multi-layer steel
⇒ Selection:
⇒⇒ 1 hole Piston protrusion up to 0.91 mm (0.036 in)
⇒⇒ 2 hole Piston protrusion 0.92 - 1.03 mm (0.036 - 0.041 in)
⇒⇒ 3 hole Piston protrusion over 1.03 mm (0.041 in)
Camshaft
Type DOHC made from clear chill casting, hollow cast, negative cam radius;
vacuum pump driven from exhaust camshaft
Bearings 5 per camshaft
Drive Simplex chain
Radial runout 0.047 - 0.088 mm (0.0019 - 0.0035 in)
End float 0.15 - 0.33 mm (0.006 - 0.013 in.)
Bearing clearance 0.011 - 0.034 mm (0.0004 - 0.0013 in.)
Tappets
Type Hydraulic valve adjusters with roller finger levers
Page 68 of 1007
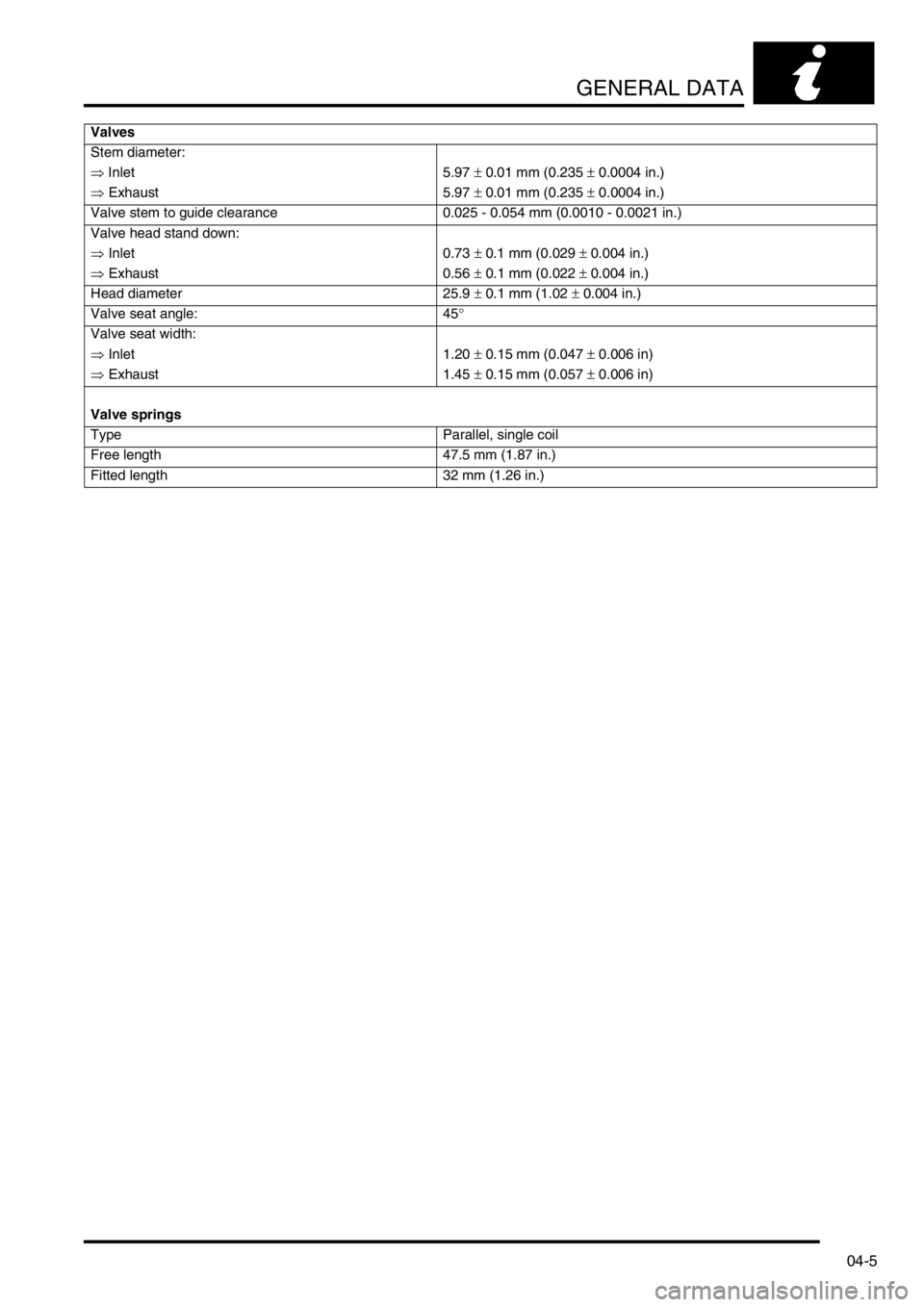
GENERAL DATA
04-5
Valves
Stem diameter:
⇒ Inlet 5.97 ± 0.01 mm (0.235 ± 0.0004 in.)
⇒ Exhaust 5.97 ± 0.01 mm (0.235 ± 0.0004 in.)
Valve stem to guide clearance 0.025 - 0.054 mm (0.0010 - 0.0021 in.)
Valve head stand down:
⇒ Inlet 0.73 ± 0.1 mm (0.029 ± 0.004 in.)
⇒ Exhaust 0.56 ± 0.1 mm (0.022 ± 0.004 in.)
Head diameter 25.9 ± 0.1 mm (1.02 ± 0.004 in.)
Valve seat angle: 45°
Valve seat width:
⇒ Inlet 1.20 ± 0.15 mm (0.047 ± 0.006 in)
⇒ Exhaust 1.45 ± 0.15 mm (0.057 ± 0.006 in)
Valve springs
Type Parallel, single coil
Free length 47.5 mm (1.87 in.)
Fitted length 32 mm (1.26 in.)
Page 69 of 1007
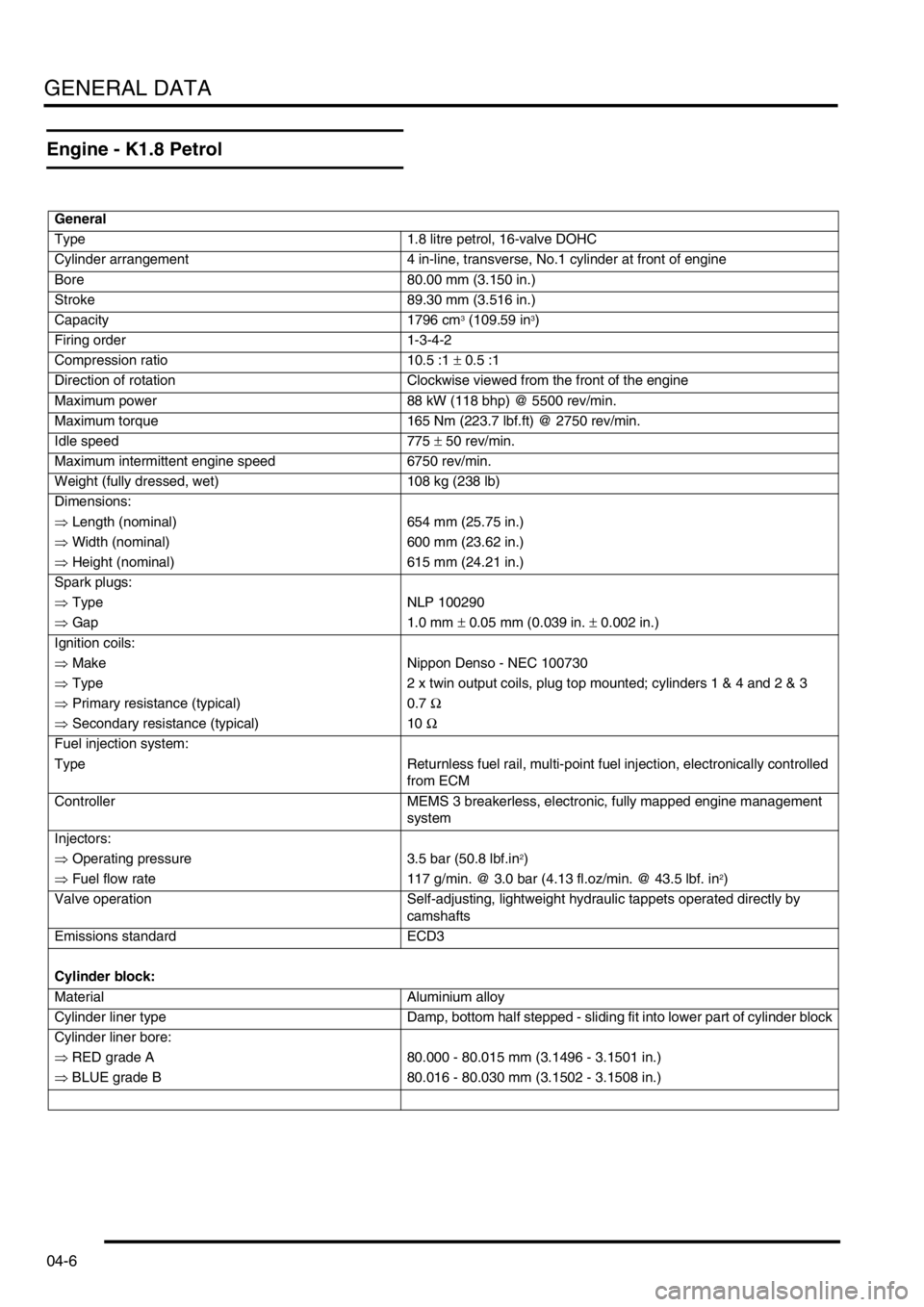
GENERAL DATA
04-6
Engine - K1.8 Petrol
General
Type 1.8 litre petrol, 16-valve DOHC
Cylinder arrangement 4 in-line, transverse, No.1 cylinder at front of engine
Bore 80.00 mm (3.150 in.)
Stroke 89.30 mm (3.516 in.)
Capacity 1796 cm
3 (109.59 in3)
Firing order 1-3-4-2
Compression ratio 10.5 :1 ± 0.5 :1
Direction of rotation Clockwise viewed from the front of the engine
Maximum power 88 kW (118 bhp) @ 5500 rev/min.
Maximum torque 165 Nm (223.7 lbf.ft) @ 2750 rev/min.
Idle speed 775 ± 50 rev/min.
Maximum intermittent engine speed 6750 rev/min.
Weight (fully dressed, wet) 108 kg (238 lb)
Dimensions:
⇒ Length (nominal) 654 mm (25.75 in.)
⇒ Width (nominal) 600 mm (23.62 in.)
⇒ Height (nominal) 615 mm (24.21 in.)
Spark plugs:
⇒ Type NLP 100290
⇒ Gap 1.0 mm ± 0.05 mm (0.039 in. ± 0.002 in.)
Ignition coils:
⇒ Make Nippon Denso - NEC 100730
⇒ Type 2 x twin output coils, plug top mounted; cylinders 1 & 4 and 2 & 3
⇒ Primary resistance (typical) 0.7 Ω
⇒ Secondary resistance (typical) 10 Ω
Fuel injection system:
Type Returnless fuel rail, multi-point fuel injection, electronically controlled
from ECM
Controller MEMS 3 breakerless, electronic, fully mapped engine management
system
Injectors:
⇒ Operating pressure 3.5 bar (50.8 lbf.in
2)
⇒ Fuel flow rate 117 g/min. @ 3.0 bar (4.13 fl.oz/min. @ 43.5 lbf. in
2)
Valve operation Self-adjusting, lightweight hydraulic tappets operated directly by
camshafts
Emissions standard ECD3
Cylinder block:
Material Aluminium alloy
Cylinder liner type Damp, bottom half stepped - sliding fit into lower part of cylinder block
Cylinder liner bore:
⇒ RED grade A 80.000 - 80.015 mm (3.1496 - 3.1501 in.)
⇒ BLUE grade B 80.016 - 80.030 mm (3.1502 - 3.1508 in.)
Page 70 of 1007
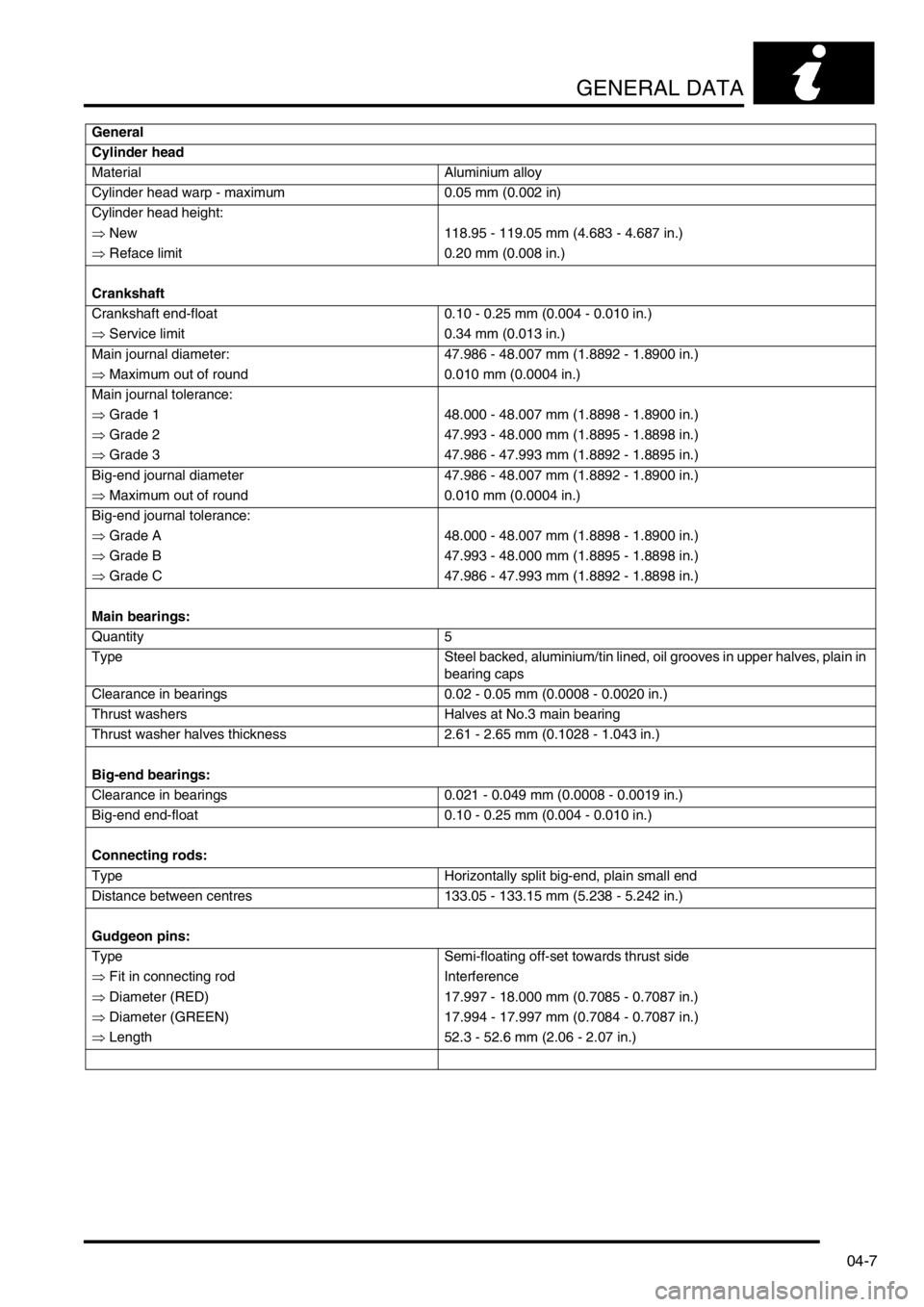
GENERAL DATA
04-7
Cylinder head
Material Aluminium alloy
Cylinder head warp - maximum 0.05 mm (0.002 in)
Cylinder head height:
⇒ New 118.95 - 119.05 mm (4.683 - 4.687 in.)
⇒ Reface limit 0.20 mm (0.008 in.)
Crankshaft
Crankshaft end-float 0.10 - 0.25 mm (0.004 - 0.010 in.)
⇒ Service limit 0.34 mm (0.013 in.)
Main journal diameter: 47.986 - 48.007 mm (1.8892 - 1.8900 in.)
⇒ Maximum out of round 0.010 mm (0.0004 in.)
Main journal tolerance:
⇒ Grade 1 48.000 - 48.007 mm (1.8898 - 1.8900 in.)
⇒ Grade 2 47.993 - 48.000 mm (1.8895 - 1.8898 in.)
⇒ Grade 3 47.986 - 47.993 mm (1.8892 - 1.8895 in.)
Big-end journal diameter 47.986 - 48.007 mm (1.8892 - 1.8900 in.)
⇒ Maximum out of round 0.010 mm (0.0004 in.)
Big-end journal tolerance:
⇒ Grade A 48.000 - 48.007 mm (1.8898 - 1.8900 in.)
⇒ Grade B 47.993 - 48.000 mm (1.8895 - 1.8898 in.)
⇒ Grade C 47.986 - 47.993 mm (1.8892 - 1.8898 in.)
Main bearings:
Quantity 5
Type Steel backed, aluminium/tin lined, oil grooves in upper halves, plain in
bearing caps
Clearance in bearings 0.02 - 0.05 mm (0.0008 - 0.0020 in.)
Thrust washers Halves at No.3 main bearing
Thrust washer halves thickness 2.61 - 2.65 mm (0.1028 - 1.043 in.)
Big-end bearings:
Clearance in bearings 0.021 - 0.049 mm (0.0008 - 0.0019 in.)
Big-end end-float 0.10 - 0.25 mm (0.004 - 0.010 in.)
Connecting rods:
Type Horizontally split big-end, plain small end
Distance between centres 133.05 - 133.15 mm (5.238 - 5.242 in.)
Gudgeon pins:
Type Semi-floating off-set towards thrust side
⇒ Fit in connecting rod Interference
⇒ Diameter (RED) 17.997 - 18.000 mm (0.7085 - 0.7087 in.)
⇒ Diameter (GREEN) 17.994 - 17.997 mm (0.7084 - 0.7087 in.)
⇒ Length 52.3 - 52.6 mm (2.06 - 2.07 in.) General