MAZDA 626 1987 Owners Manual
Manufacturer: MAZDA, Model Year: 1987, Model line: 626, Model: MAZDA 626 1987Pages: 1865, PDF Size: 94.35 MB
Page 91 of 1865
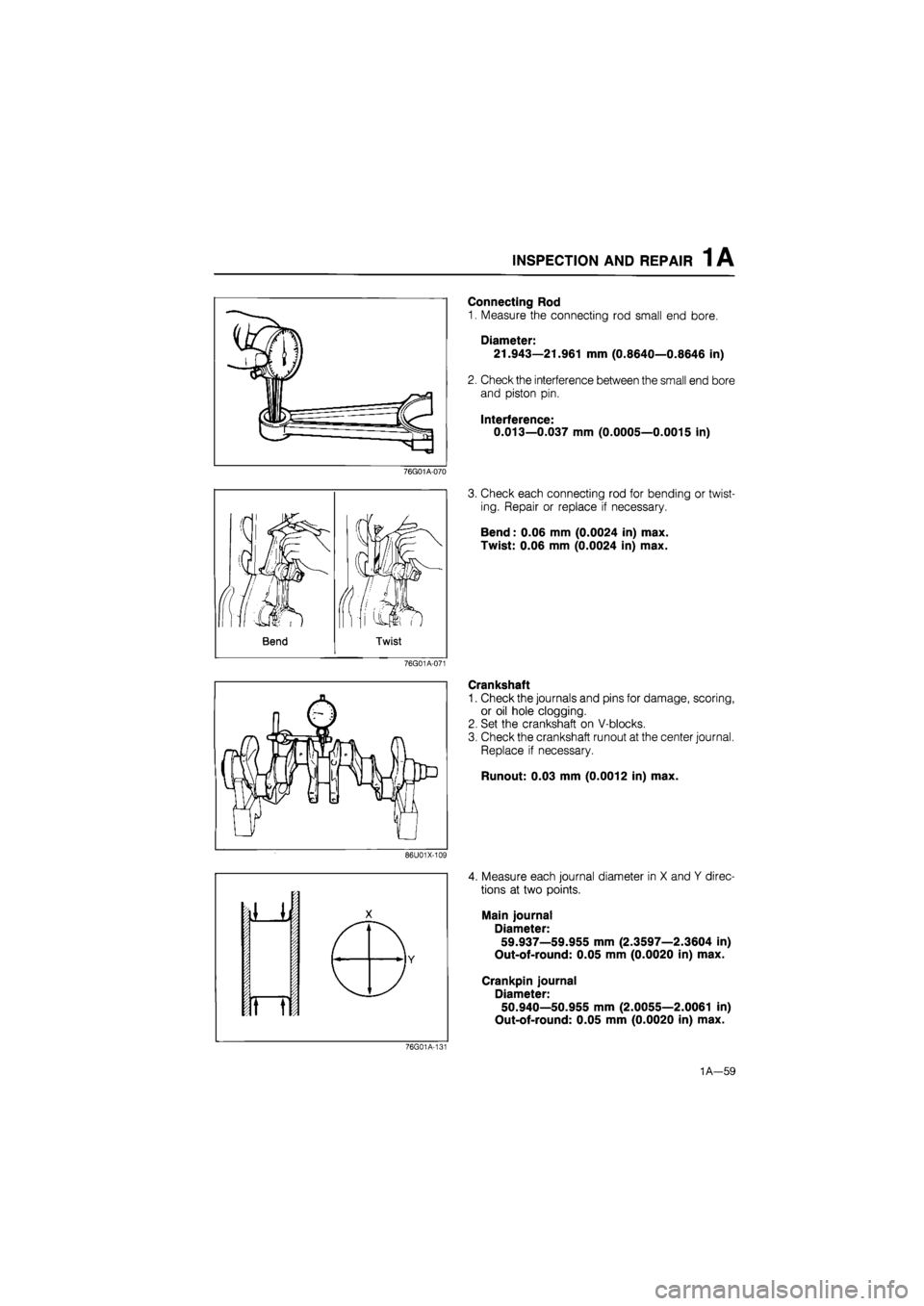
INSPECTION AND REPAIR 1 A
76G01A-070
76G01A-071
86U01X-109
Connecting Rod
1. Measure the connecting rod small end bore.
Diameter: 21.943—21.961 mm (0.8640—0.8646 in)
2. Check the interference between the small end bore
and piston pin.
Interference:
0.013—0.037 mm (0.0005—0.0015 in)
3. Check each connecting rod for bending or twist-
ing. Repair or replace if necessary.
Bend: 0.06 mm (0.0024 in) max.
Twist: 0.06 mm (0.0024 in) max.
Crankshaft
1. Check the journals and pins for damage, scoring,
or oil hole clogging.
2. Set the crankshaft on V-blocks.
3. Check the crankshaft runout at the center journal.
Replace if necessary.
Runout: 0.03 mm (0.0012 in) max.
4. Measure each journal diameter in X and Y direc-
tions at two points.
Main journal
Diameter:
59.937—59.955 mm (2.3597—2.3604 in)
Out-of-round: 0.05 mm (0.0020 in) max.
Crankpin journal
Diameter:
50.940—50.955 mm (2.0055—2.0061 in)
Out-of-round: 0.05 mm (0.0020 in) max.
76G01A-131
1A—59
Page 92 of 1865
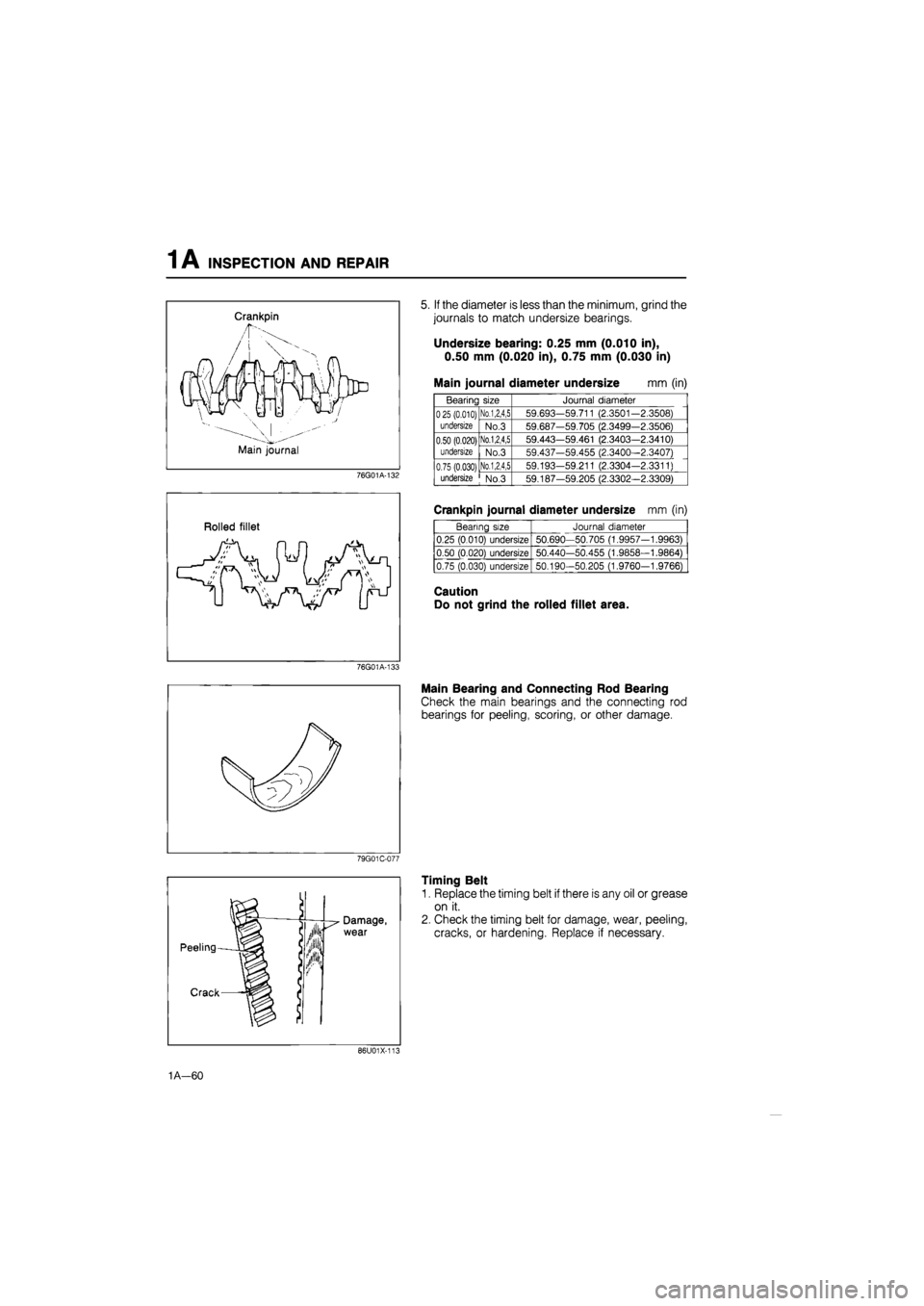
INSPECTION AND REPAIR 1 A
Crankpin
,/f
Main journal
76G01A-132
5. If the diameter is less than the minimum, grind the
journals to match undersize bearings.
Undersize bearing: 0.25 mm (0.010 in),
0.50 mm (0.020 in), 0.75 mm (0.030 in)
Main journal diameter undersize mm (in)
Bearing size Journal diameter
025 (0.010)
undersize
No.1,2,4,5 59.693-59.711 (2.3501-2.3508) 025 (0.010)
undersize No.3 59.687-59.705 (2.3499-2.3506)
0.50 (0.020)
undersize
No.1,2,4,5 59.443-59.461 (2.3403—2.3410) 0.50 (0.020)
undersize No.3 59.437-59.455 (2.3400—2.3407)
0.75 (0.030) undersize
No.1,2,4,5 59.193-59.211 (2.3304-2.3311) 0.75 (0.030) undersize No.3 59.187-59.205 (2.3302-2.3309)
Rolled fillet
Crankpin journal diameter undersize mm (in)
Bearing size Journal diameter
0.25 (0.010) undersize 50.690—50.705 (1.9957-1.9963)
0.50 (0.020) undersize 50.440-50.455 (1.9858—1.9864)
0.75 (0.030) undersize 50.190-50.205 (1.9760-1.9766)
Caution
Do not grind the rolled fillet area.
76G01A-133
Main Bearing and Connecting Rod Bearing
Check the main bearings and the connecting rod
bearings for peeling, scoring, or other damage.
79G01C-077
Timing Belt
1. Replace the timing belt if there is any oil or grease
on it.
2. Check the timing belt for damage, wear, peeling,
cracks, or hardening. Replace if necessary.
86U01X-117
1A—60
Page 93 of 1865
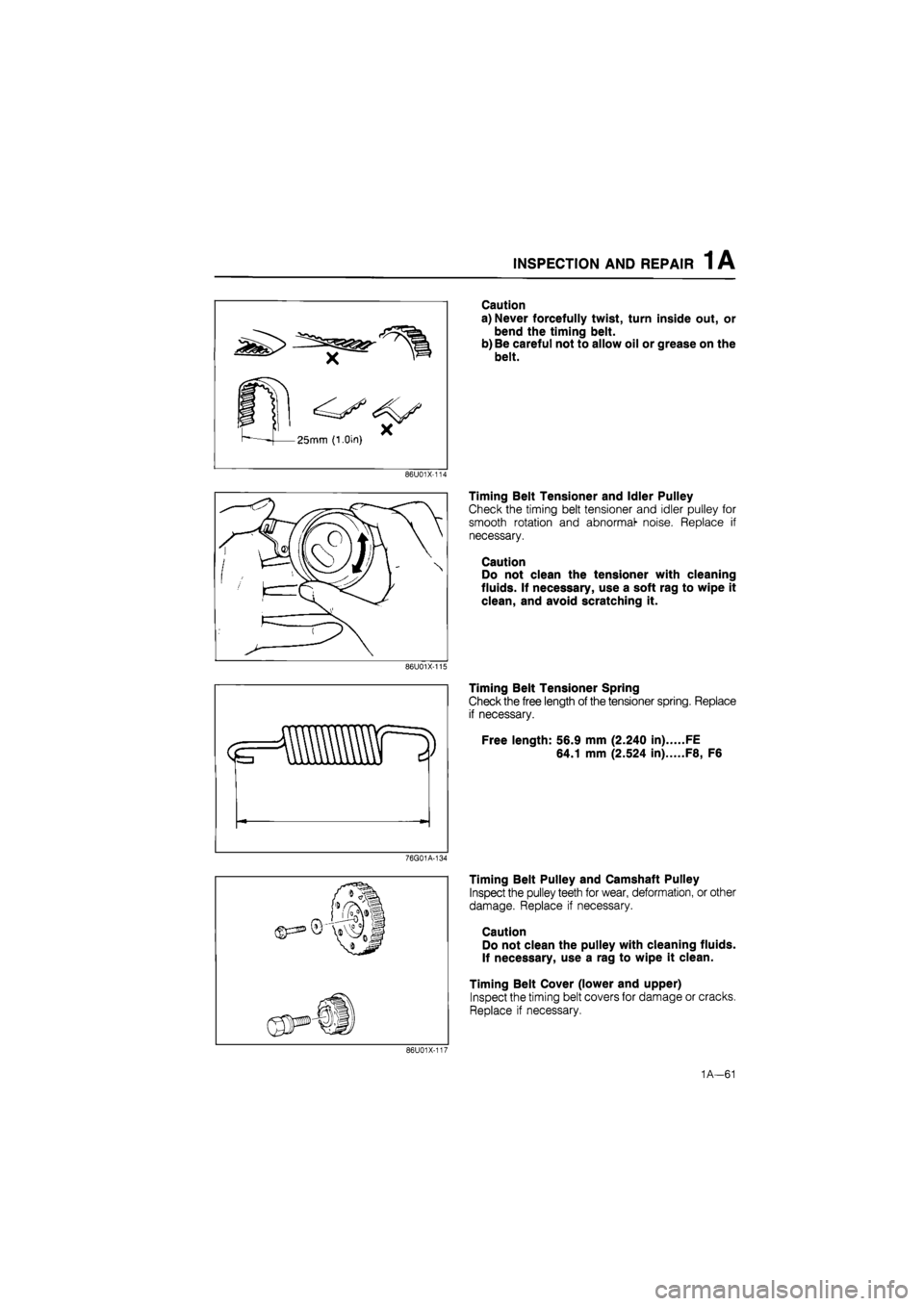
INSPECTION AND REPAIR 1 A
Caution
a) Never forcefully twist, turn inside out, or
bend the timing belt.
b) Be careful not to allow oil or grease on the
belt.
86U01X-114
Timing Belt Tensioner and Idler Pulley
Check the timing belt tensioner and idler pulley for
smooth rotation and abnormal- noise. Replace if
necessary.
Caution
Do not clean the tensioner with cleaning
fluids. If necessary, use a soft rag to wipe it
clean, and avoid scratching it.
86U01X-115
Timing Belt Tensioner Spring
Check the free length of the tensioner spring. Replace
if necessary.
Free length: 56.9 mm (2.240 in) FE
64.1 mm (2.524 in) F8, F6
76G01A-134
Timing Belt Pulley and Camshaft Pulley
Inspect the pulley teeth for wear, deformation, or other
damage. Replace if necessary.
Caution
Do not clean the pulley with cleaning fluids.
If necessary, use a rag to wipe it clean.
Timing Belt Cover (lower and upper)
Inspect the timing belt covers for damage or cracks.
Replace if necessary.
86U01X-117
1A—61
Page 94 of 1865
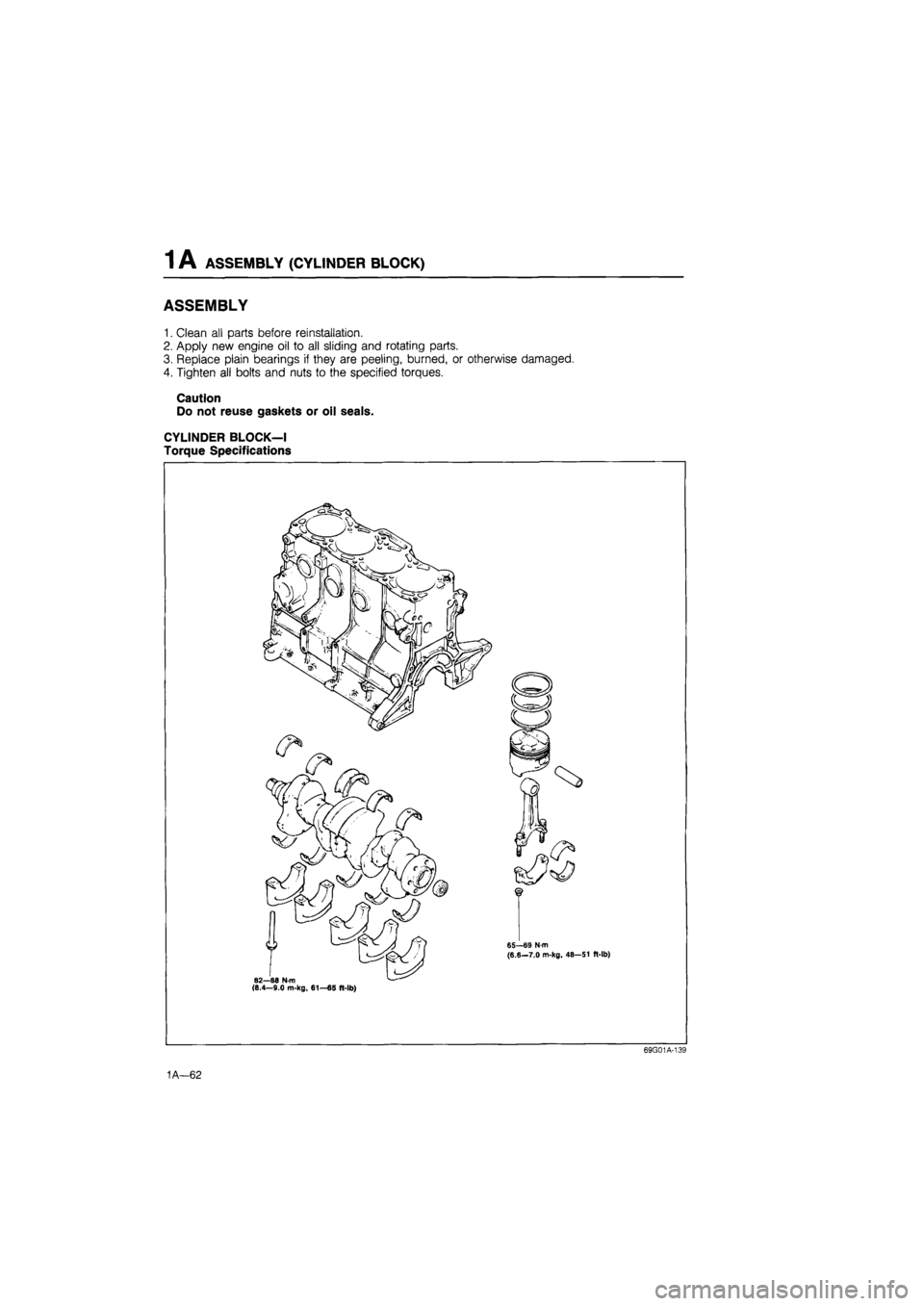
1 A ASSEMBLY (CYLINDER BLOCK)
ASSEMBLY
1. Clean all parts before reinstallation.
2. Apply new engine oil to all sliding and rotating parts.
3. Replace plain bearings if they are peeling, burned, or otherwise damaged.
4. Tighten all bolts and nuts to the specified torques.
Caution
Do not reuse gaskets or oil seals.
CYLINDER BLOCK—I
Torque Specifications
69G01A-139
1A—62
Page 95 of 1865

ASSEMBLY (CYLINDER BLOCK) 1 A
Connecting Rod
1. Assemble the SST to the piston pin.
2. Apply engine oil to the piston pin.
86U01X-118
3. Set the piston on the SST with the F mark facing
upward.
4. Set the connecting rod in piston with the oil hole
in the large end opposite the F mark.
76G01A-135
5. Press the piston pin into the piston and connect-
ing rod until the SST contacts the block.
While inserting the piston pin, check the pressure
force. If it is less than specified, replace the piston
pin or the connecting rod.
Press force:
5—15 kN (500—1,500 kg, 1,100—3,300 lb)
Check the oscillation torque of the connecting rod.
(Refer to page 1A—47.)
76G01A-072
Piston Ring
1. Install the three-piece oil rings on the pistons.
(1) Apply engine oil to the oil ring spacer and rails.
(2) Install the oil ring spacer so that the opening
faces upward.
(3) Install the upper rail and lower rail.
Note
a) The upper rail and lower rail are the same.
b) Each rail can be installed with either face
upward.
69G01A-144
1A—63
Page 96 of 1865
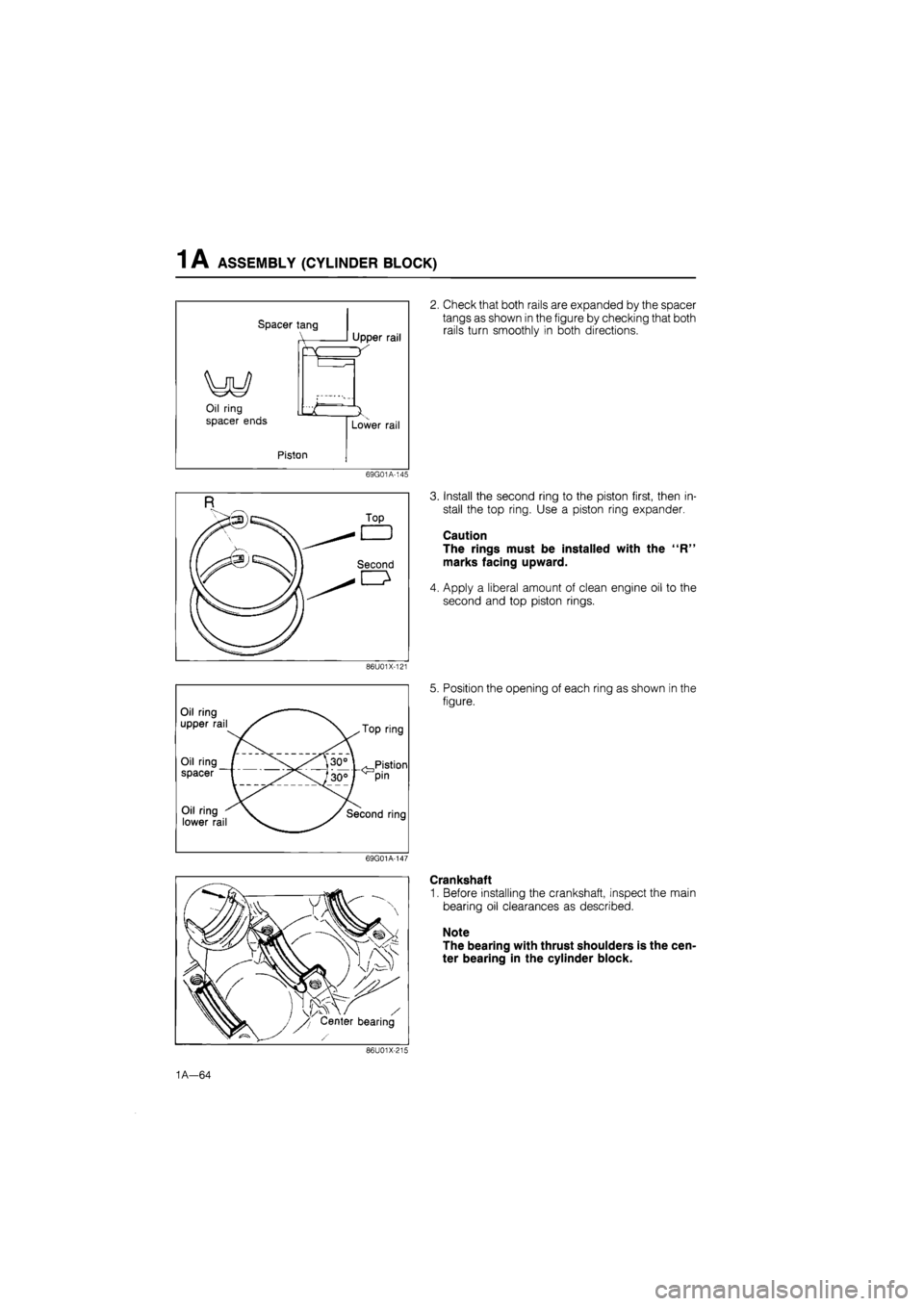
1 A ASSEMBLY (CYLINDER BLOCK)
Spacer iang
Oil ring
spacer ends
Upper rail
Piston
Lower rail
69G01A-145
86U01X-121
Oil ring —
upper rail f .Top ring
Oil ring (
spacer r \30° \ . Pistion
^-^/ao0F pin
Oil ring
lower rail /Second ring
69G01A-147
2. Check that both rails are expanded by the spacer
tangs as shown in the figure by checking that both
rails turn smoothly in both directions.
3. Install the second ring to the piston first, then in-
stall the top ring. Use a piston ring expander.
Caution
The rings must be installed with the "R"
marks facing upward.
4. Apply a liberal amount of clean engine oil to the
second and top piston rings.
5. Position the opening of each ring as shown in the
figure.
Crankshaft
1. Before installing the crankshaft, inspect the main
bearing oil clearances as described.
Note
The bearing with thrust shoulders is the cen-
ter bearing in the cylinder block.
86U01X-136
1A—64
Page 97 of 1865
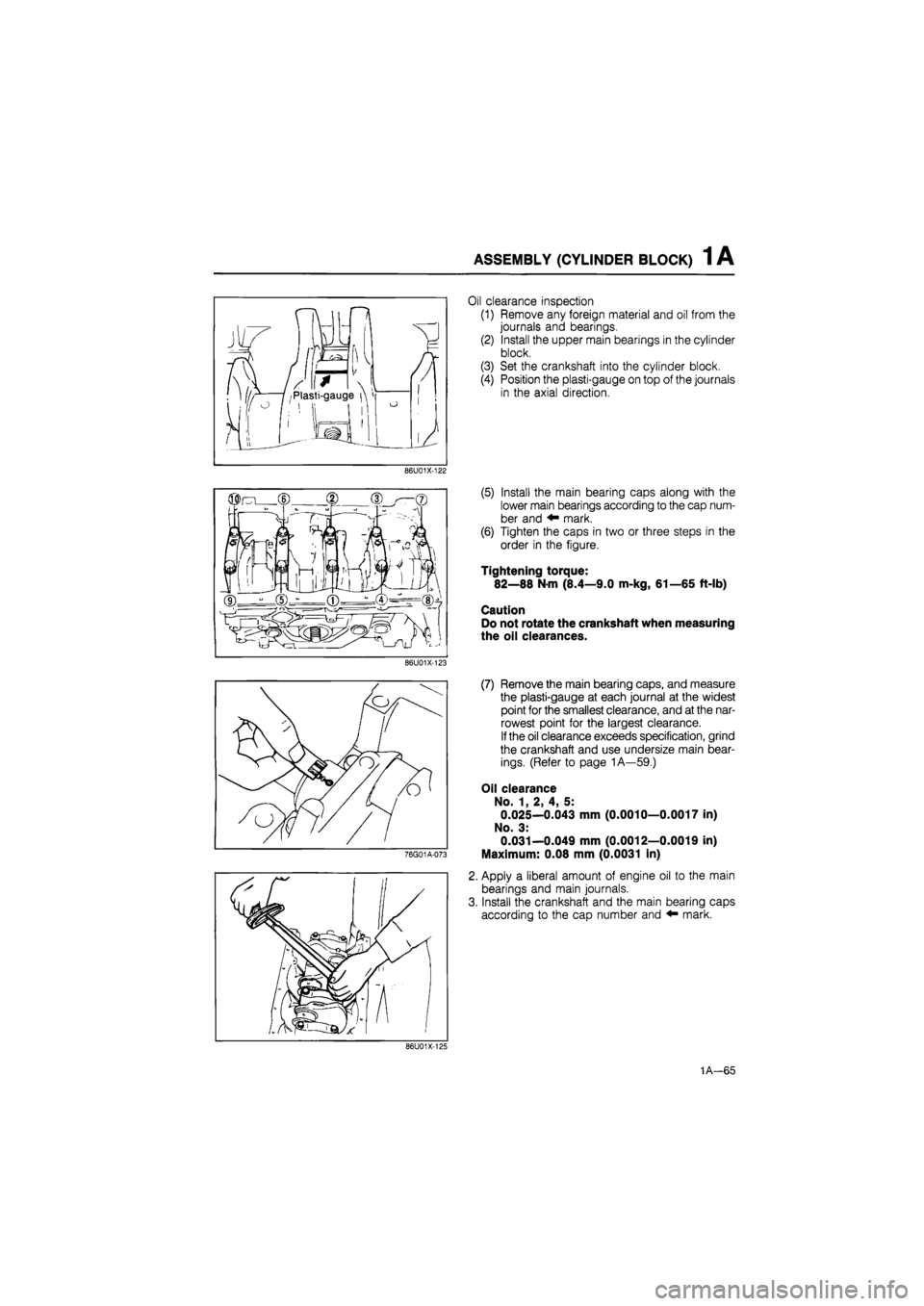
ASSEMBLY (CYLINDER BLOCK) 1 A
86U01X-122
UJlJt^LM
.•I
86U01X-123
76G01A-073
Oil clearance inspection
(1) Remove any foreign material and oil from the
journals and bearings.
(2) Install the upper main bearings in the cylinder
block.
(3) Set the crankshaft into the cylinder block.
(4) Position the plasti-gauge on top of the journals
in the axial direction.
(5) Install the main bearing caps along with the
lower main bearings according to the cap num-
ber and ^ mark.
(6) Tighten the caps in two or three steps in the
order in the figure.
Tightening torque:
82—88 N-m (8.4—9.0 m-kg, 61—65 ft-lb)
Caution
Do not rotate the crankshaft when measuring
the oil clearances.
(7) Remove the main bearing caps, and measure
the plasti-gauge at each journal at the widest
point for the smallest clearance, and at the nar-
rowest point for the largest clearance.
If the oil clearance exceeds specification, grind
the crankshaft and use undersize main bear-
ings. (Refer to page 1A—59.)
Oil clearance
No. 1, 2, 4, 5:
0.025—0.043 mm (0.0010—0.0017 in)
No. 3:
0.031—0.049 mm (0.0012—0.0019 in)
Maximum: 0.08 mm (0.0031 in)
2. Apply a liberal amount of engine oil to the main
bearings and main journals.
3. Install the crankshaft and the main bearing caps
according to the cap number and mark.
86U01X-130
1A—65
Page 98 of 1865
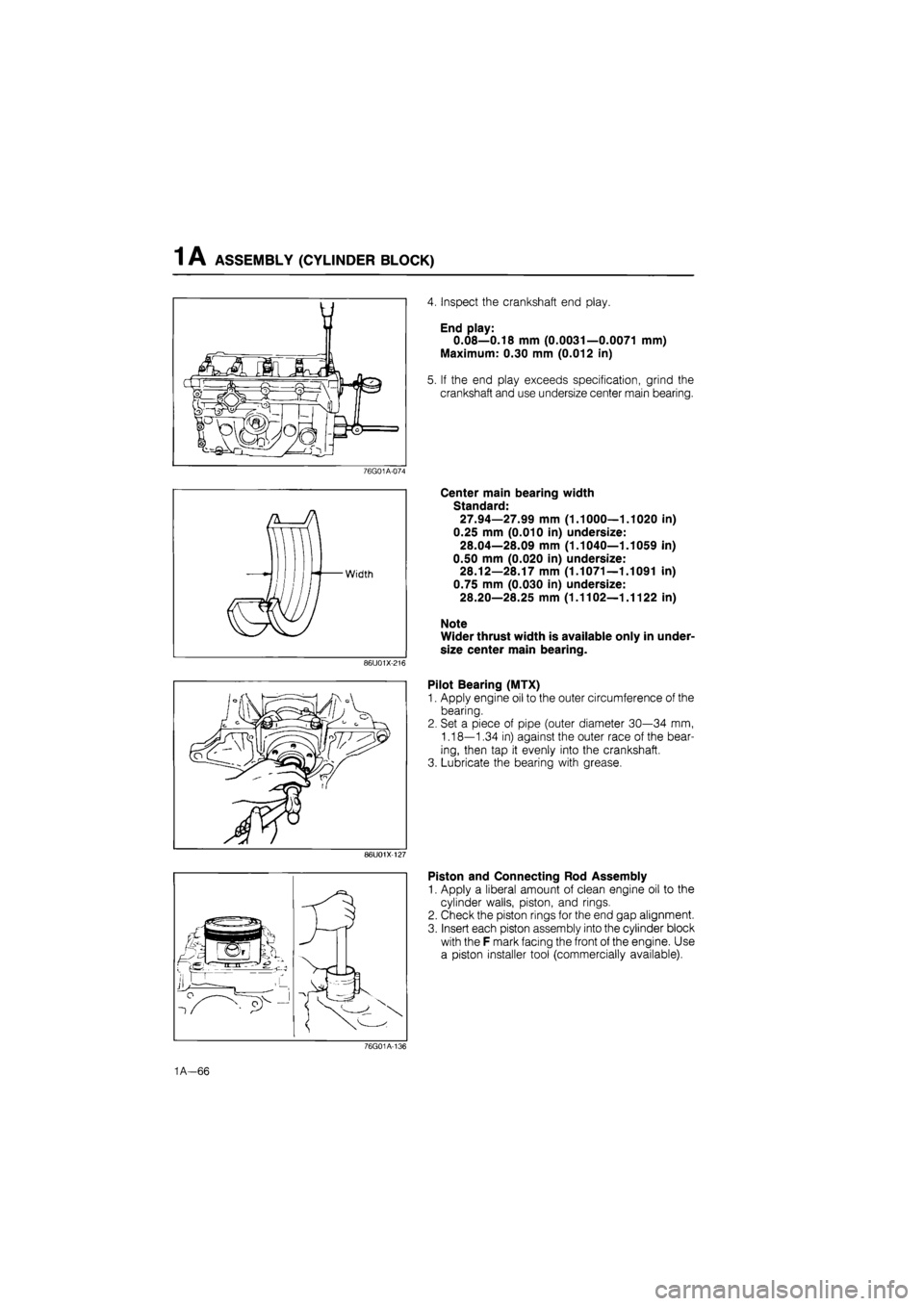
1 A ASSEMBLY (CYLINDER BLOCK)
76G01A-074
86U01X-216
86U01X-127
4. Inspect the crankshaft end play.
End play:
0.08—0.18 mm (0.0031—0.0071 mm)
Maximum: 0.30 mm (0.012 in)
5. If the end play exceeds specification, grind the
crankshaft and use undersize center main bearing.
Center main bearing width
Standard:
27.94—27.99 mm (1.1000—1.1020 in)
0.25 mm (0.010 in) undersize:
28.04—28.09 mm (1.1040—1.1059 in)
0.50 mm (0.020 in) undersize:
28.12—28.17 mm (1.1071—1.1091 in)
0.75 mm (0.030 in) undersize:
28.20—28.25 mm (1.1102—1.1122 in)
Note
Wider thrust width is available only in under-
size center main bearing.
Pilot Bearing (MTX)
1. Apply engine oil to the outer circumference of the
bearing.
2. Set a piece of pipe (outer diameter 30—34 mm,
1.18—1.34 in) against the outer race of the bear-
ing, then tap it evenly into the crankshaft.
3. Lubricate the bearing with grease.
Piston and Connecting Rod Assembly
1. Apply a liberal amount of clean engine oil to the
cylinder walls, piston, and rings.
2. Check the piston rings for the end gap alignment.
3. Insert each piston assembly into the cylinder block
with the F mark facing the front of the engine. Use
a piston installer tool (commercially available).
76G01A-136
1A—66
Page 99 of 1865
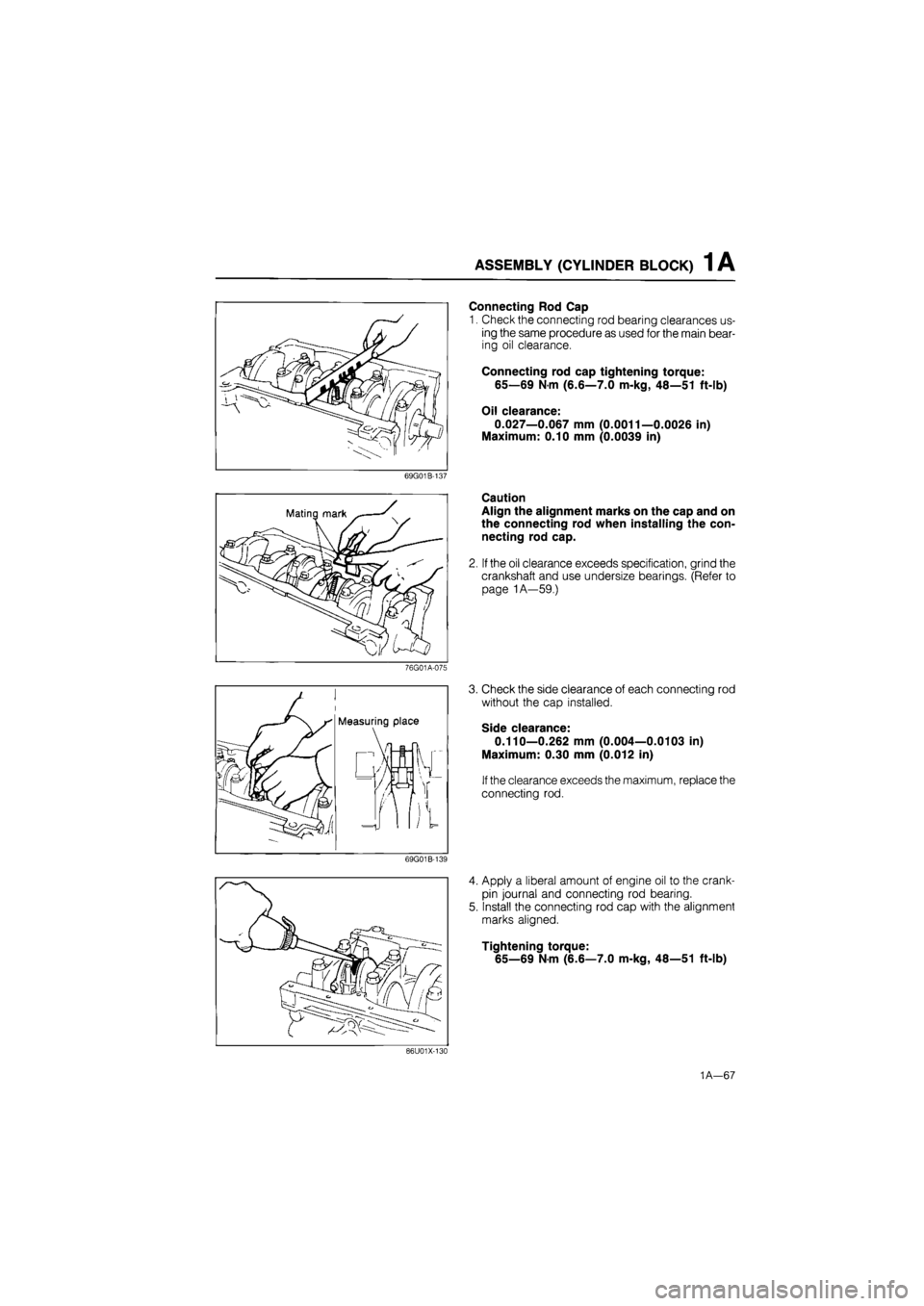
ASSEMBLY (CYLINDER BLOCK) 1 A
69G01B-137
Matin
76G01A-075
69G01B-139
Connecting Rod Cap
1. Check the connecting rod bearing clearances us-
ing the same procedure as used for the main bear-
ing oil clearance.
Connecting rod cap tightening torque:
65—69 Nm (6.6—7.0 m-kg, 48—51 ft-lb)
Oil clearance:
0.027—0.067 mm (0.0011—0.0026 in)
Maximum: 0.10 mm (0.0039 in)
Caution
Align the alignment marks on the cap and on
the connecting rod when installing the con-
necting rod cap.
If the oil clearance exceeds specification, grind the
crankshaft and use undersize bearings. (Refer to
page 1A—59.)
3. Check the side clearance of each connecting rod
without the cap installed.
Side clearance:
0.110—0.262 mm (0.004—0.0103 in)
Maximum: 0.30 mm (0.012 in)
If the clearance exceeds the maximum, replace the
connecting rod.
4. Apply a liberal amount of engine oil to the crank-
pin journal and connecting rod bearing.
5. Install the connecting rod cap with the alignment
marks aligned.
Tightening torque:
65—69 Nm (6.6—7.0 m-kg, 48—51 ft-lb)
86U01X-130
1A—67
Page 100 of 1865
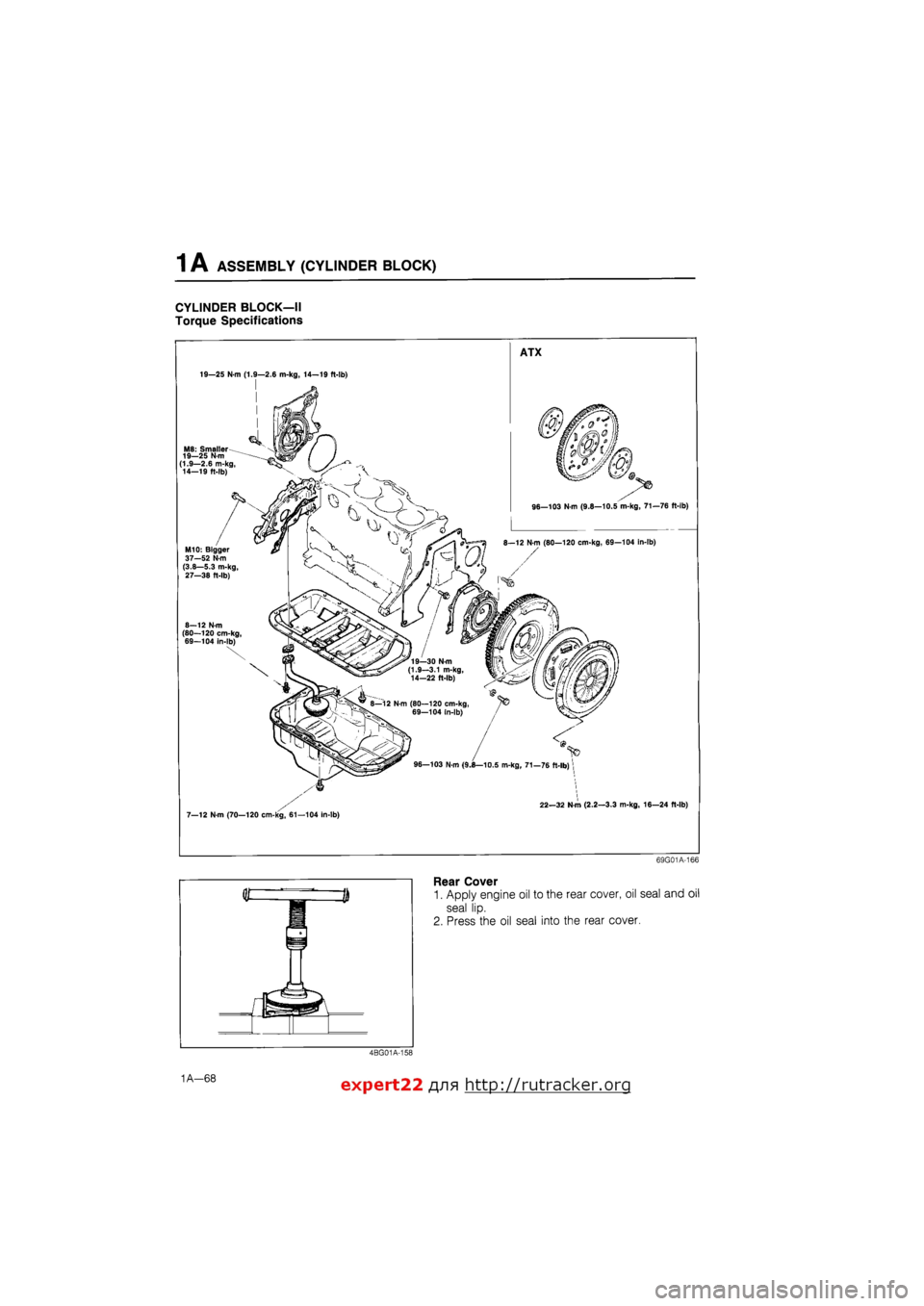
1 A ASSEMBLY (CYLINDER BLOCK)
CYLINDER BLOCK—II
Torque Specifications
ATX
MS: Smaller 19—25 N-m (1.9—2.6 m-kg, 14—19 ft-lb)
M10: Bigger 37—52 N-m (3.8—5.3 m-kg, 27—38 ft-lb)
96—103 N-m (9.8—10.5 m-kg, 71—76 ft-lb)
69G01A-166
Rear Cover
1. Apply engine oil to the rear cover, oil seal and oil
seal lip.
2. Press the oil seal into the rear cover.
4BG01A-158
expert22 fl/ifl http://rutracker.org