differential MITSUBISHI ECLIPSE 1991 Workshop Manual
[x] Cancel search | Manufacturer: MITSUBISHI, Model Year: 1991, Model line: ECLIPSE, Model: MITSUBISHI ECLIPSE 1991Pages: 1216, PDF Size: 67.42 MB
Page 724 of 1216
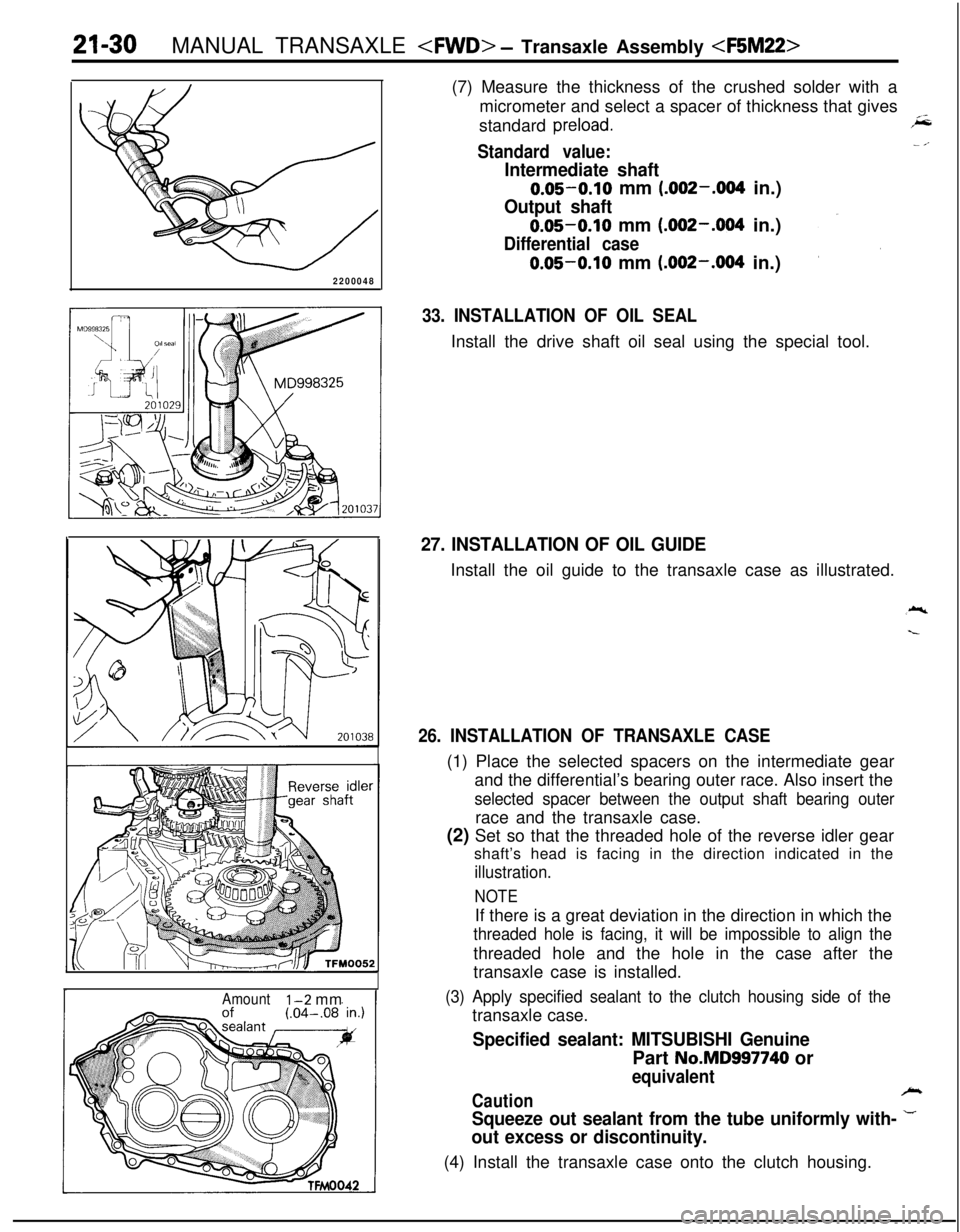
21-30MANUAL TRANSAXLE
2200048
IAmountl-2 mm(7) Measure the thickness of the crushed solder with a
micrometer and select a spacer of thickness that gives
standard
preload.,&
Standard value:
Intermediate shaft0.05-0.10 mm (.002-,004 in.)
Output shaft0.05-0.10 mm (.002-.004 in.)
Differential case0.05-0.10 mm (.002-,004 in.)
33. INSTALLATION OF OIL SEALInstall the drive shaft oil seal using the special tool.
27. INSTALLATION OF OIL GUIDEInstall the oil guide to the transaxle case as illustrated.
26. INSTALLATION OF TRANSAXLE CASE(1) Place the selected spacers on the intermediate gear
and the differential’s bearing outer race. Also insert the
selected spacer between the output shaft bearing outerrace and the transaxle case.
(2) Set so that the threaded hole of the reverse idler gear
shaft’s head is facing in the direction indicated in the
illustration.
NOTEIf there is a great deviation in the direction in which the
threaded hole is facing, it will be impossible to align thethreaded hole and the hole in the case after the
transaxle case is installed.
(3) Apply specified sealant to the clutch housing side of thetransaxle case.
Specified sealant: MITSUBISHI GenuinePart
No.MD997740 or
equivalent
CautionB
Squeeze out sealant from the tube uniformly with- -
out excess or discontinuity.(4) Install the transaxle case onto the clutch housing.
Page 729 of 1216
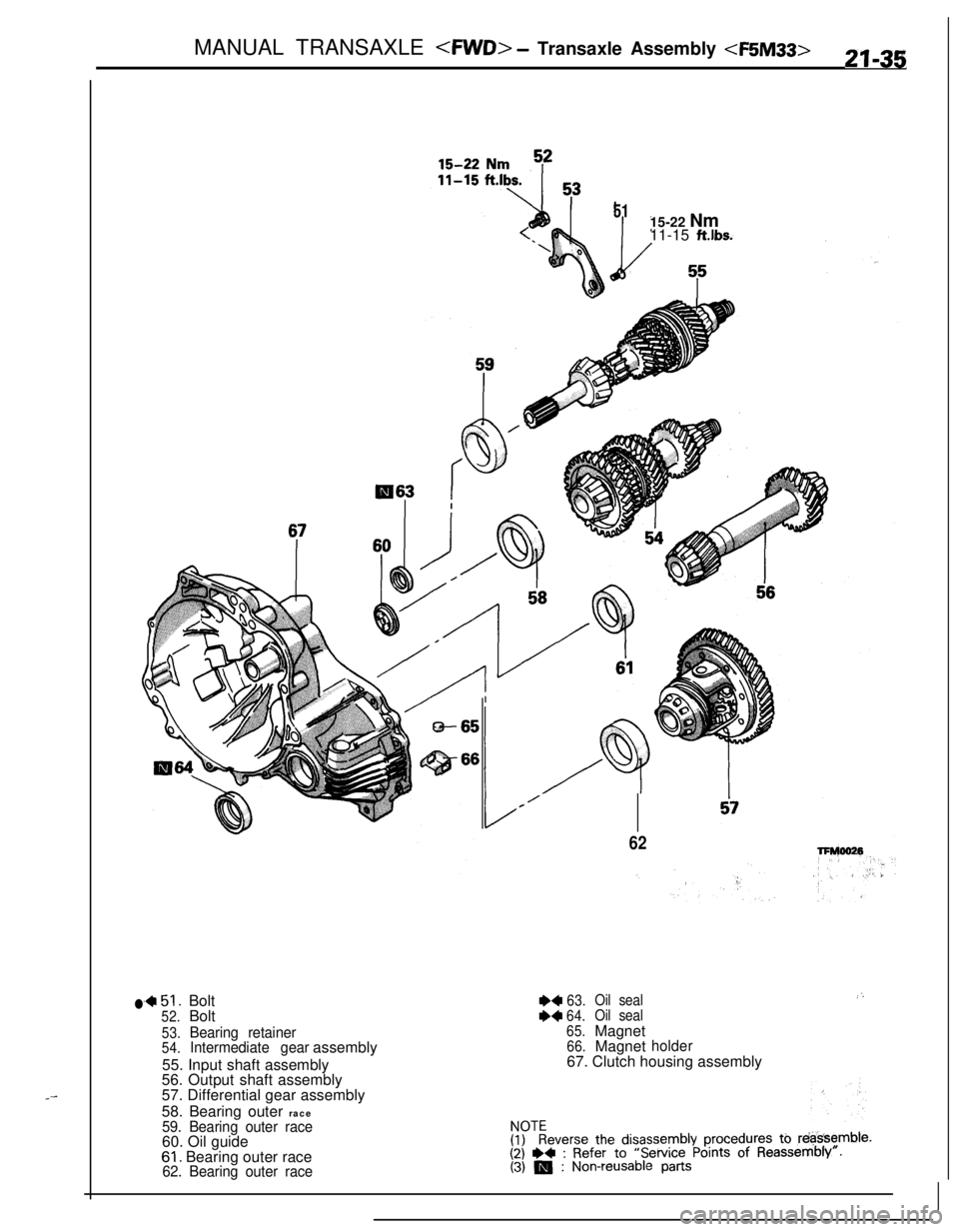
_-MANUAL TRANSAXLE
- Transaxle Assembly
11-15 ftlbs.
5115-22 Nm
11-15
ftlbs.
l,451.Bolt
52.Bolt
53.Bearing retainer54.Intermediate gearassembly
55. Input shaft assembly
56. Output shaft assembly
57. Differential gear assembly
58. Bearing outer race
59. Bearing outer race60. Oil guide
61. Bearing outer race62. Bearing outer race
/’
62
+463.Oil seal+464.Oil seal
65.Magnet
66.Magnetholder67. Clutch housing assembly
; .,
FFkeverse the disassembly procedures to rdassembte.(2) ++ : Refer to “Service Points of Reassem’bly”.(3) m : Non-reusable parts
Page 733 of 1216
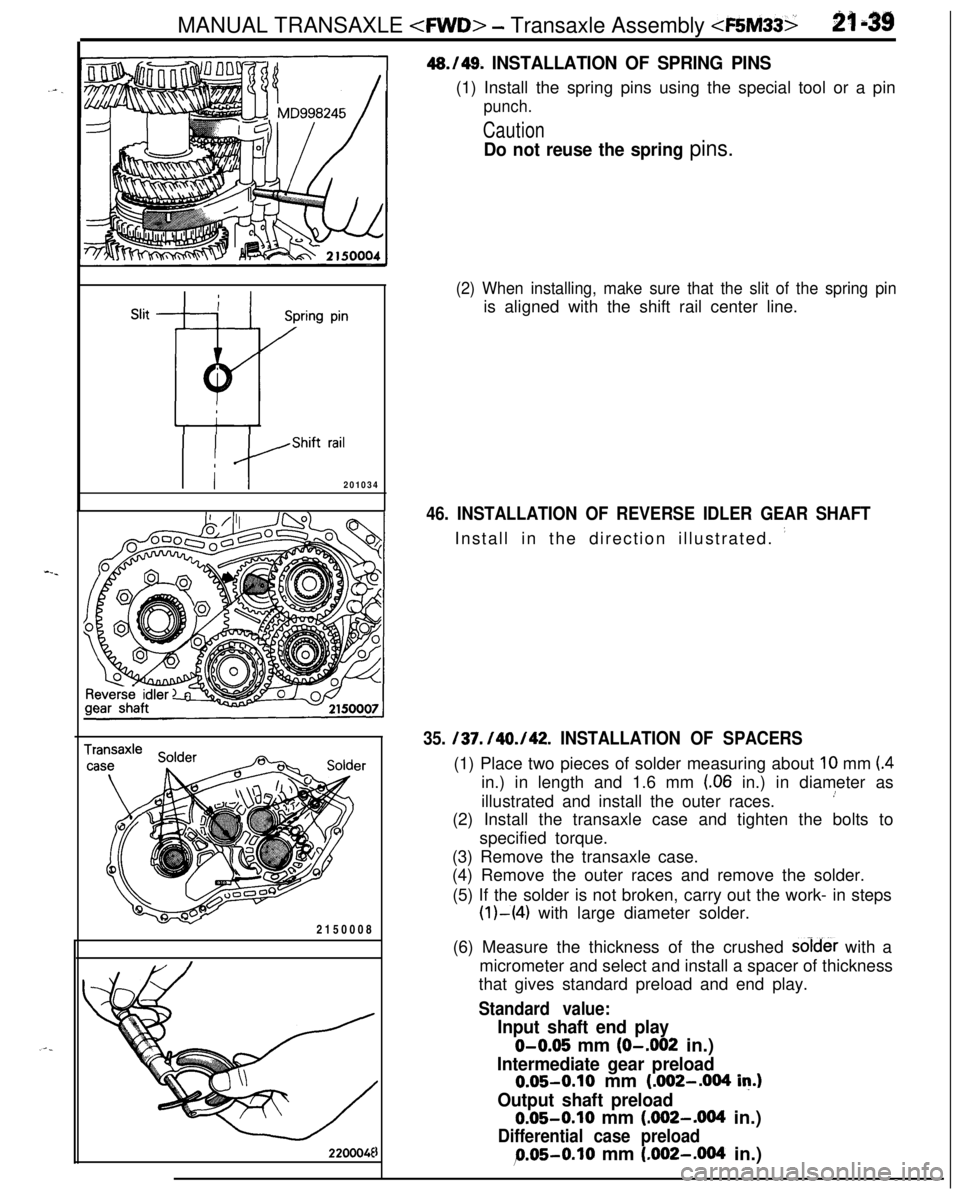
MANUAL TRANSAXLE
/Shift rail
11-t201034er
2150008
220004E46./49.
INSTALLATION OF SPRING PINS(1) Install the spring pins using the special tool or a pin
punch.
Caution
Do not reuse the spring pins.
(2) When installing, make sure that the slit of the spring pinis aligned with the shift rail center line.
46. INSTALLATION OF REVERSE IDLER GEAR SHAFTInstall in the direction illustrated.
’
35. /37. /40./42. INSTALLATION OF SPACERS(1) Place two pieces of solder measuring about
10 mm (4in.) in length and 1.6 mm
(.06 in.) in diameter as
illustrated and install the outer races.
’(2) Install the transaxle case and tighten the bolts to
specified torque.
(3) Remove the transaxle case.
(4) Remove the outer races and remove the solder.
(5) If the solder is not broken, carry out the work- in steps
(l)-(4) with large diameter solder.
(6) Measure the thickness of the crushed soid& with a
micrometer and select and install a spacer of thickness
that gives standard preload and end play.
Standard value:
Input shaft end play
O-0.05 mm (O-.002 in.)
Intermediate gear preload0.05-0.10 mm (.002-.004
in.)
Output shaft preload0.05-0.10 mm (.092-.004 in.)
Differential case preload
9.05-0.10 mm (.002-.004 in.)
Page 734 of 1216
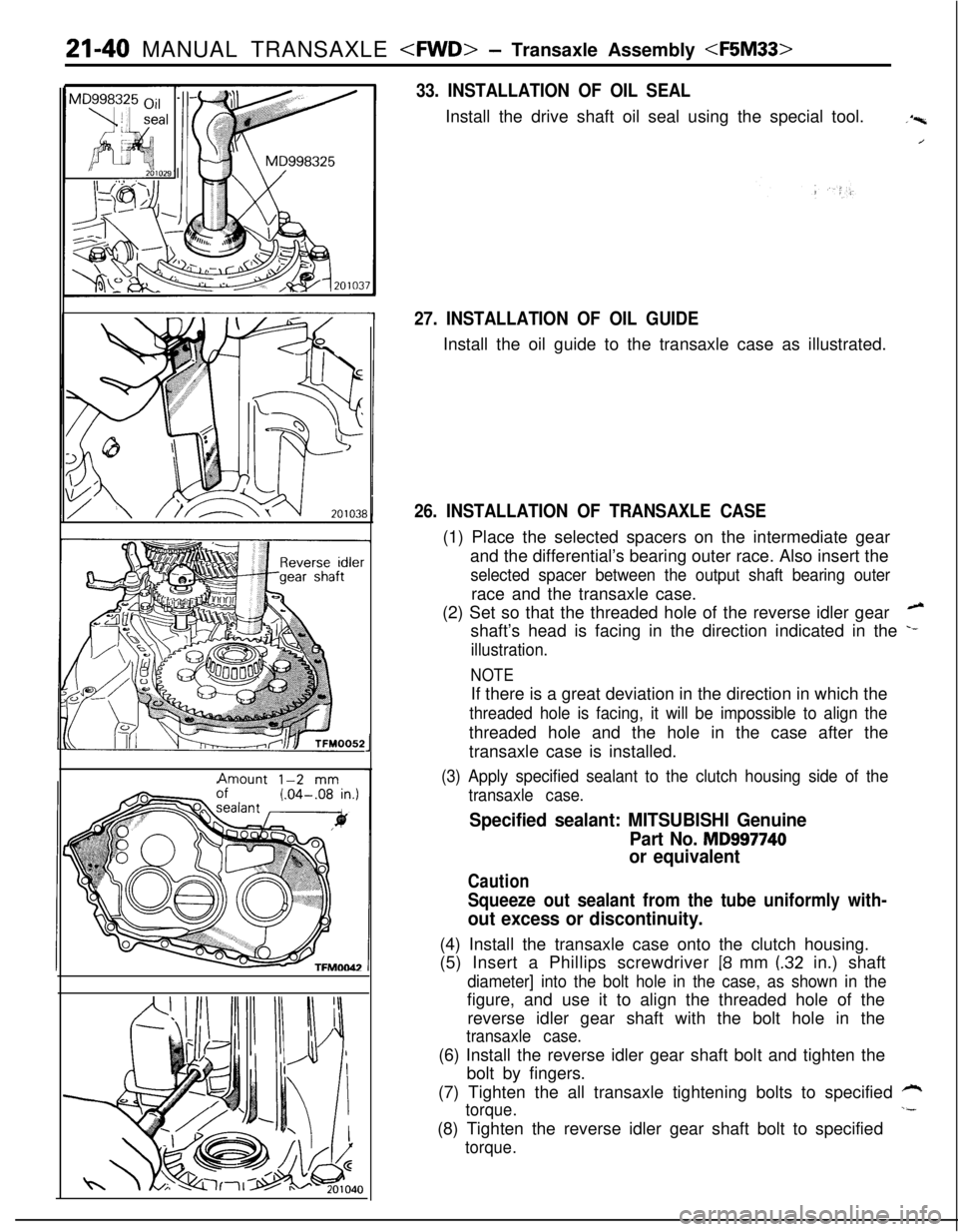
21-40 MANUAL TRANSAXLE
1-2 mm
J
33. INSTALLATION OF OIL SEALInstall the drive shaft oil seal using the special tool.
.‘p,
/
27. INSTALLATION OF OIL GUIDEInstall the oil guide to the transaxle case as illustrated.
26. INSTALLATION OF TRANSAXLE CASE(1) Place the selected spacers on the intermediate gear
and the differential’s bearing outer race. Also insert the
selected spacer between the output shaft bearing outerrace and the transaxle case.
(2) Set so that the threaded hole of the reverse idler gear
hshaft’s head is facing in the direction indicated in the
.-
illustration.
NOTEIf there is a great deviation in the direction in which the
threaded hole is facing, it will be impossible to align thethreaded hole and the hole in the case after the
transaxle case is installed.
(3) Apply specified sealant to the clutch housing side of the
transaxle case.
Specified sealant: MITSUBISHI Genuine
Part No.
MD997740
or equivalent
Caution
Squeeze out sealant from the tube uniformly with-
out excess or discontinuity.(4) Install the transaxle case onto the clutch housing.
(5) Insert a Phillips screwdriver
18 mm (32 in.) shaft
diameter] into the bolt hole in the case, as shown in thefigure, and use it to align the threaded hole of the
reverse idler gear shaft with the bolt hole in the
transaxle case.(6) Install the reverse idler gear shaft bolt and tighten the
bolt by fingers.
(7) Tighten the all transaxle tightening bolts to specified
*
torque.,-(8) Tighten the reverse idler gear shaft bolt to specified
torque.
Page 757 of 1216
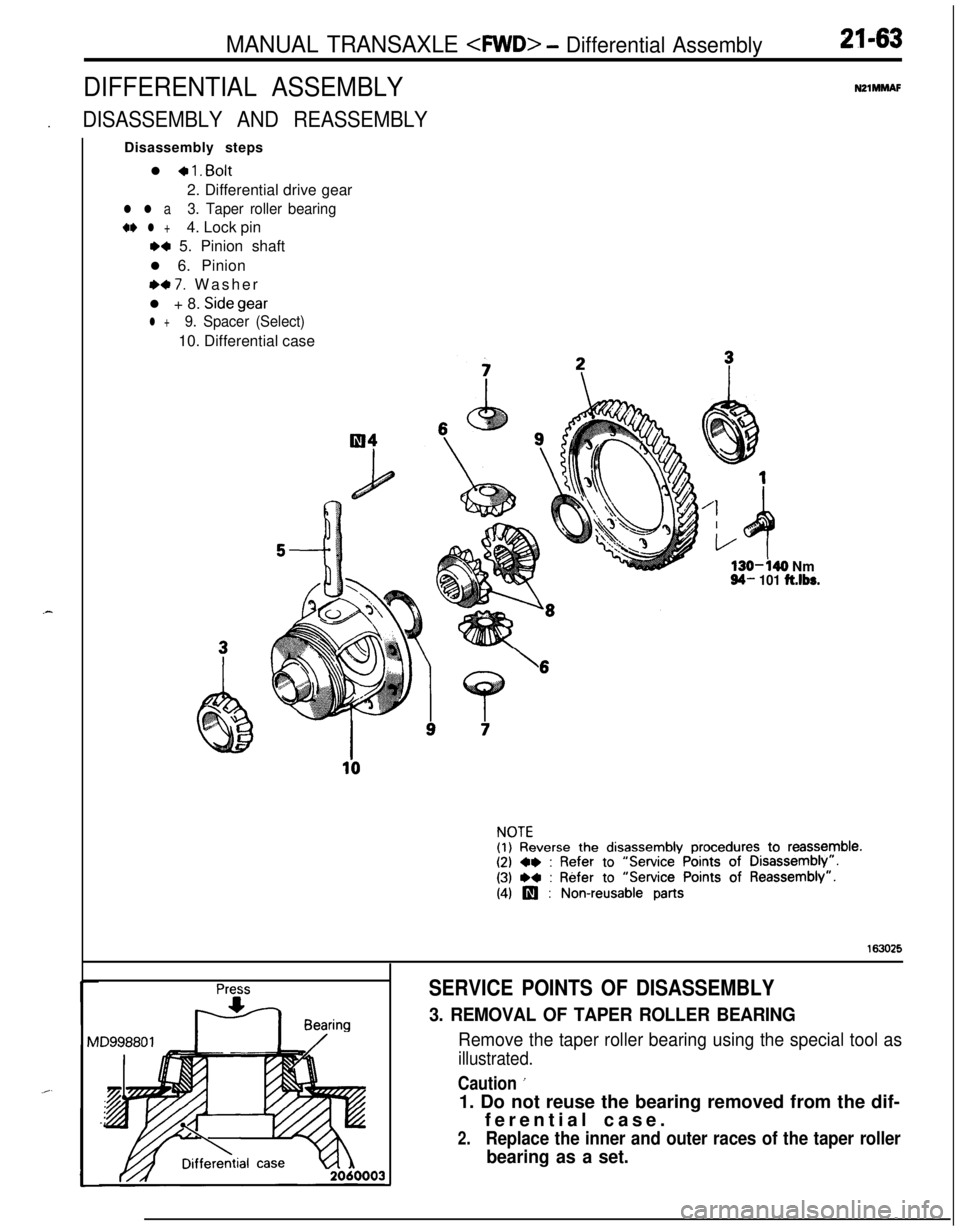
MANUAL TRANSAXLE 4WD> - Differential Assembly21-63
DIFFERENTIAL ASSEMBLYNZlMMAF.
DISASSEMBLY AND REASSEMBLYDisassembly steps
l
+ 1. Bolt2. Differential drive gear
l l a3. Taper roller bearing
+e l +4. Lock pin
M 5. Pinion shaft
l 6. Pinion
e+ 7. Washer
l + 8. Sidegear
l +9. Spacer (Select)10. Differential case
130-440 Nm94- 101 ft.lbs.
\6
NOTE(1) Reverse the disassembly procedures to reassemble.(2) ~~ : Refer to “Service Points of Disassembly”.
(3) ,+ : Refer to “Service Points of Reassembly”.
(4) p : Non-reusable parts
163025
Press
F+ Bearing
SERVICE POINTS OF DISASSEMBLY
3. REMOVAL OF TAPER ROLLER BEARING
Remove the taper roller bearing using the special tool as
illustrated.
Caution ’1. Do not reuse the bearing removed from the dif-
ferential case.
2.Replace the inner and outer races of the taper roller
bearing as a set.
Page 758 of 1216
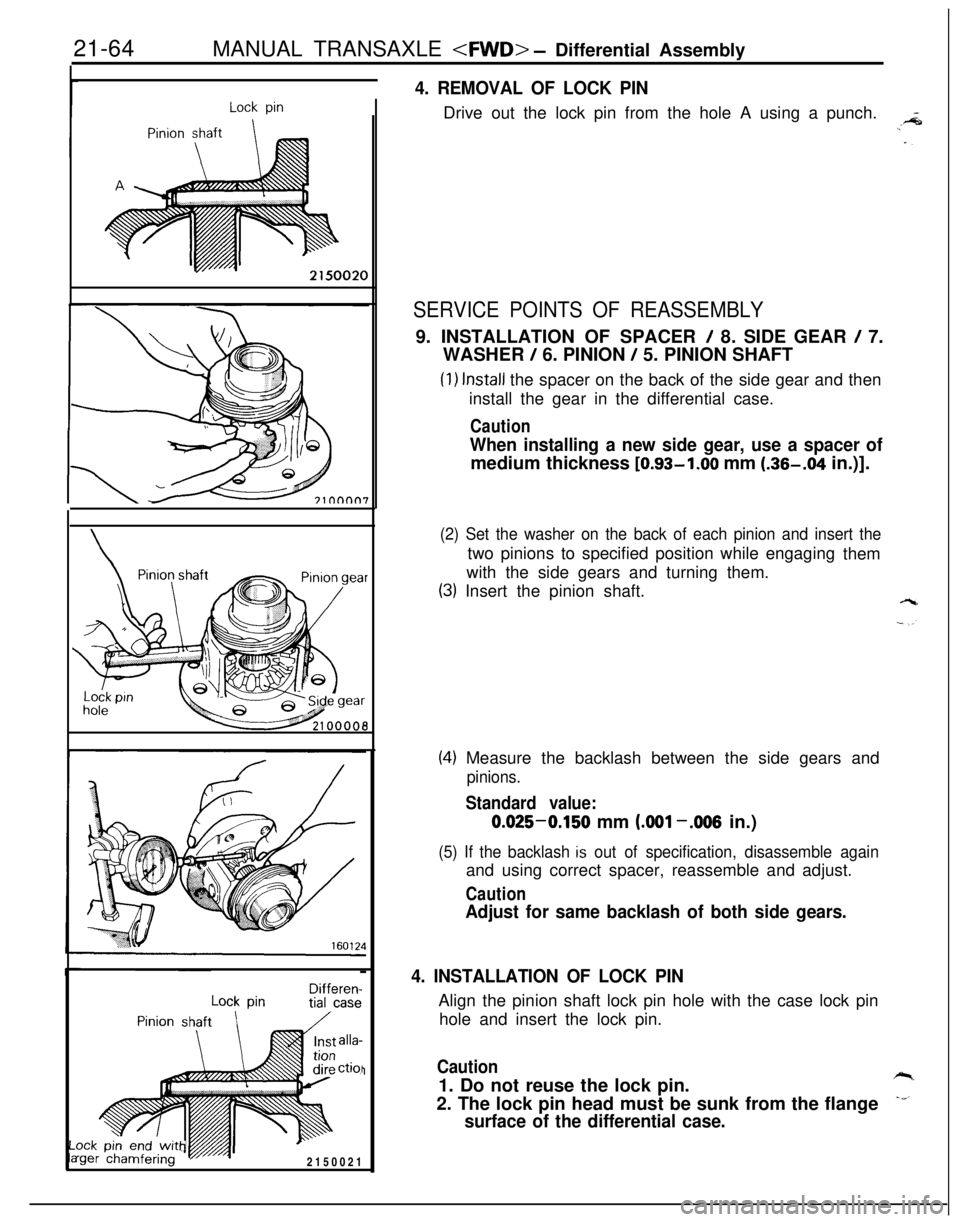
21-64MANUAL TRANSAXLE
Lock pin
Llla
Lock pinDifferen-tial case
alla-ctiol
ock pinendwith2150021
4. REMOVAL OF LOCK PINDrive out the lock pin from the hole A using a punch.
SERVICE POINTS OF REASSEMBLY9. INSTALLATION OF SPACER
/ 8. SIDE GEAR / 7.
WASHER
/ 6. PINION / 5. PINION SHAFT
(1) Install the spacer on the back of the side gear and then
install the gear in the differential case.
Caution
When installing a new side gear, use a spacer ofmedium thickness [0.93-1.00 mm (.36-.04 in.)].
(2) Set the washer on the back of each pinion and insert thetwo pinions to specified position while engaging
them
with the side gears and turning them.
(3) Insert the pinion shaft.
(4) Measure the backlash between the side gears and
pinions.
Standard value:0.025-0.150 mm
LOO1 -.006 in.)
(5) If the backlash is out of specification, disassemble againand using correct spacer, reassemble and adjust.
Caution
Adjust for same backlash of both side gears.
4. INSTALLATION OF LOCK PINAlign the pinion shaft lock pin hole with the case lock pin
hole and insert the lock pin.
Caution1. Do not reuse the lock pin.
2. The lock pin head must be sunk from the flange
surface of the differential case.
Page 759 of 1216
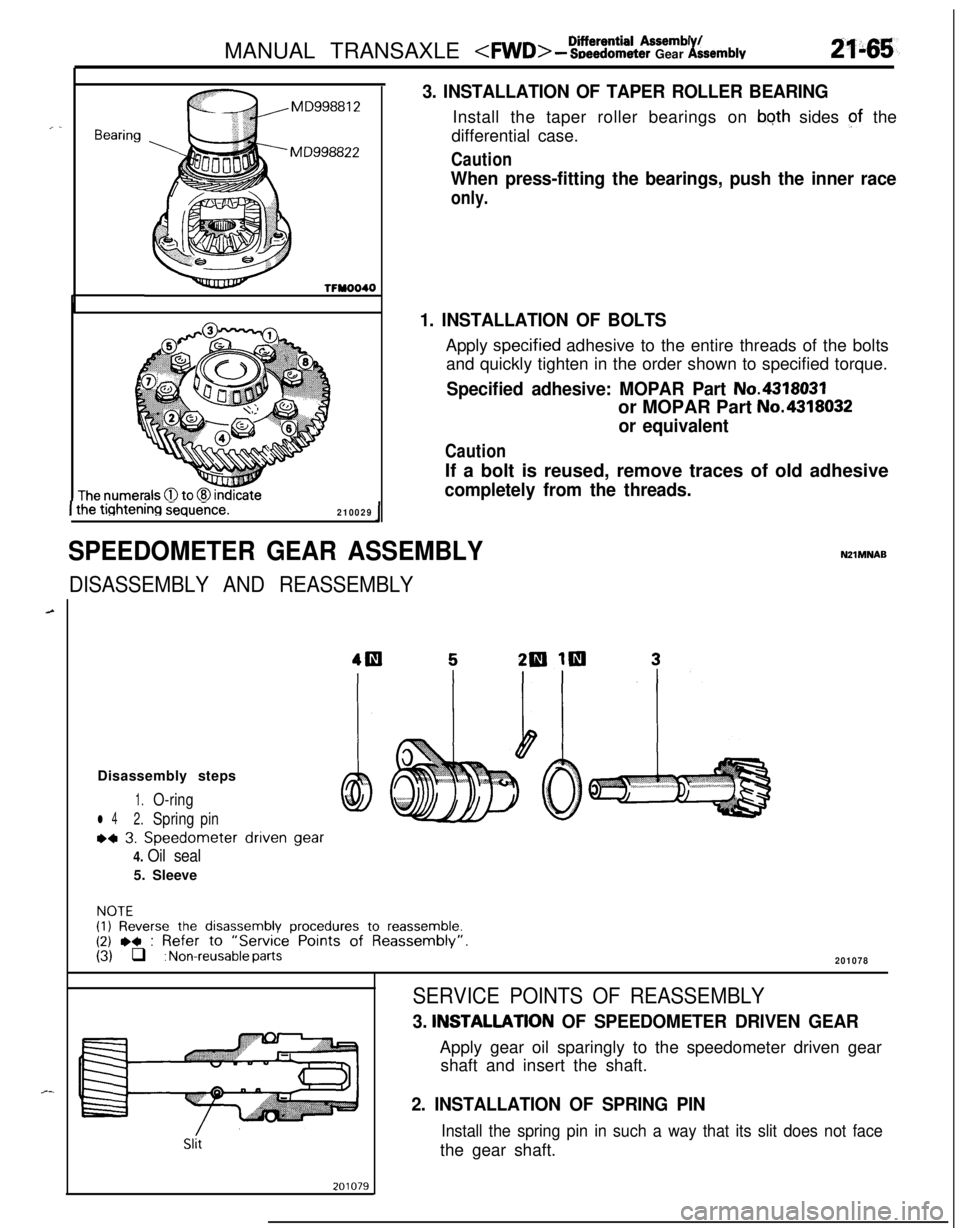
bierential Assembl /MANUAL TRANSAXLE
, .Bearing
TFYOOIO
The numerals 0 to (8 indicate1 the tiqhtening Gequeice.210029I
SPEEDOMETER GEAR ASSEMBLY
3. INSTALLATION OF TAPER ROLLER BEARINGInstall the taper roller bearings on
bqth sides of the
differential case.
Caution
When press-fitting the bearings, push the inner race
only.
1. INSTALLATION OF BOLTSApply
spec.ified adhesive to the entire threads of the bolts
and quickly tighten in the order shown to specified torque.
Specified adhesive: MOPAR Part No.4318031or MOPAR Part
No.4318032
or equivalent
CautionIf a bolt is reused, remove traces of old adhesive
completely from the threads.
DISASSEMBLY AND REASSEMBLY
NZlMNABDisassembly steps
1.O-ring
l 42.Springpin
~4 3. Speedometer driven gear
4. Oil seal5. Sleeve
NOTE(1) Reverse the disassembly procedures to reassemble.(2) ,+ : Refer to “Service Points of Reassembly”.(3) q : Non-reusable parts201078
Slit
SERVICE POINTS OF REASSEMBLY
3. INSTALLATlON OF SPEEDOMETER DRIVEN GEARApply gear oil sparingly to the speedometer driven gear
shaft and insert the shaft.
2. INSTALLATION OF SPRING PIN
Install the spring pin in such a way that its slit does not facethe gear shaft.
Page 762 of 1216
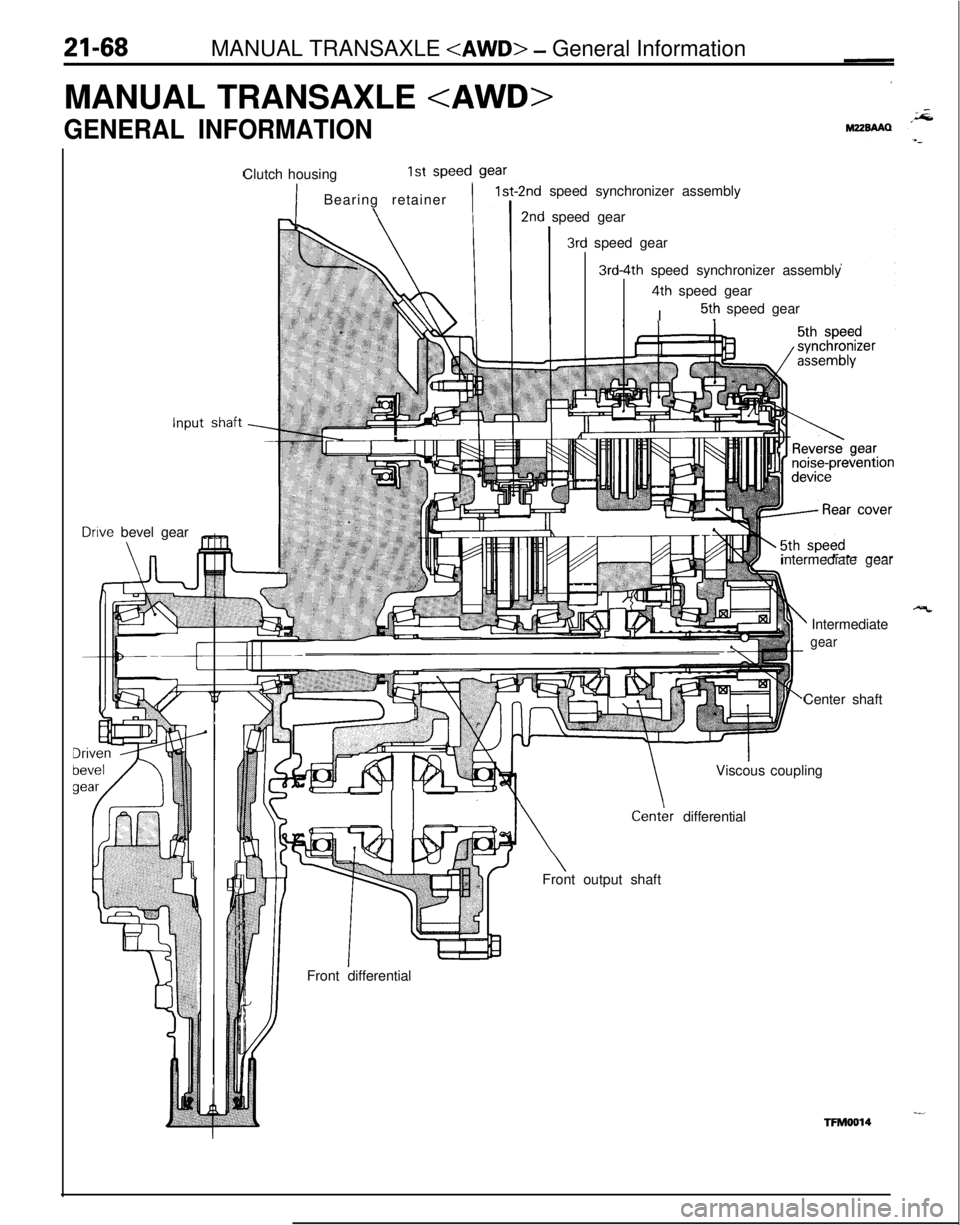
21-68MANUAL TRANSAXLE
MANUAL TRANSAXLE
GENERAL INFORMATION
lnpu
Dnve bevel gearIClutch housing
1st speecBearing retainer
\
gear
;t-2ndspeed synchronizer assembly
2nd speed gear
3rd speed gear
3rd-4th speed synchronizer assembly
4th speed gear
I .
5th speed gear
intermediate gear
ii\IntermediategearCenter shaft
Viscous coupling
Front differential
\Cent& differential
Front output shaft
,&
--
APLTFM0014
Page 763 of 1216
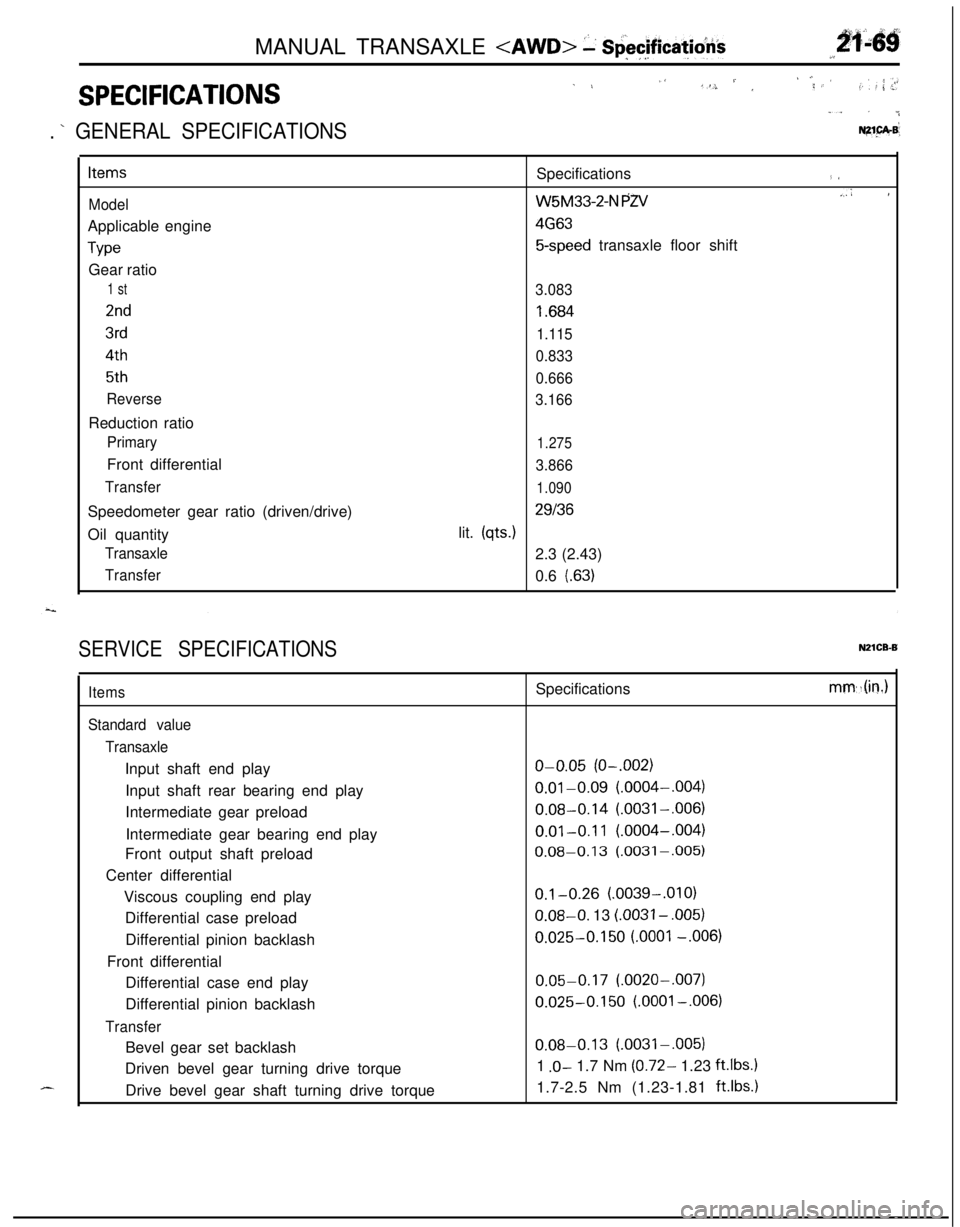
MANUAL TRANSAXLE
2f.46g
\ ,...,
,,, .,
SPECIFICATIONS
1 L,‘S. / ,‘; ,< ’,f. : ,: ; .>r
“. . ..&
. ’ GENERAL SPECIFICATIONSNZ1.pA.B’
Items
ModelApplicable engine
TypeGear ratio
1 st
2nd
3rd
4th
5th
ReverseReduction ratio
PrimaryFront differential
TransferSpeedometer gear ratio (driven/drive)
Oil quantity
Transaxle
TransferSpecifications
(I
W5M33-2-N PZV.,A I
4G63
5-speed transaxle floor shift
3.083
I .684
1.115
0.833
0.666
3.166
1.275
3.866
1.090
29136lit.
(qts.)2.3 (2.43)
0.6
l.63)
SERVICE SPECIFICATIONSN21CB-B
d-...
Items
Standard value
TransaxleInput shaft end play
Input shaft rear bearing end play
Intermediate gear preload
Intermediate gear bearing end play
Front output shaft preload
Center differential
Viscous coupling end play
Differential case preload
Differential pinion backlash
Front differential
Differential case end play
Differential pinion backlash
TransferBevel gear set backlash
Driven bevel gear turning drive torque
Drive bevel gear shaft turning drive torqueSpecifications
o-0.05 (O-.002)
0.01-0.09 (.0004-,004)
0.08-0.14 (.0031-,006)
0.01-0.11 (.0004-,004)
0.08-0.13 (.0031-,005)
0.1-0.26 (.0039-.OlO)0.08-O. 13
LOO31 - ,005)
0.025-0.150 LOO01 -.006)
0.05-0.17 (.0020-,007)
0.025-0.150 (.OOOl-,006)
0.08-0.13 (.0031-.005)
1
.O- 1.7 Nm (0.72- 1.23 ft.lbs.11.7-2.5 Nm (1.23-1.81
ft.lbs.1
mm,.(in.)
Page 765 of 1216
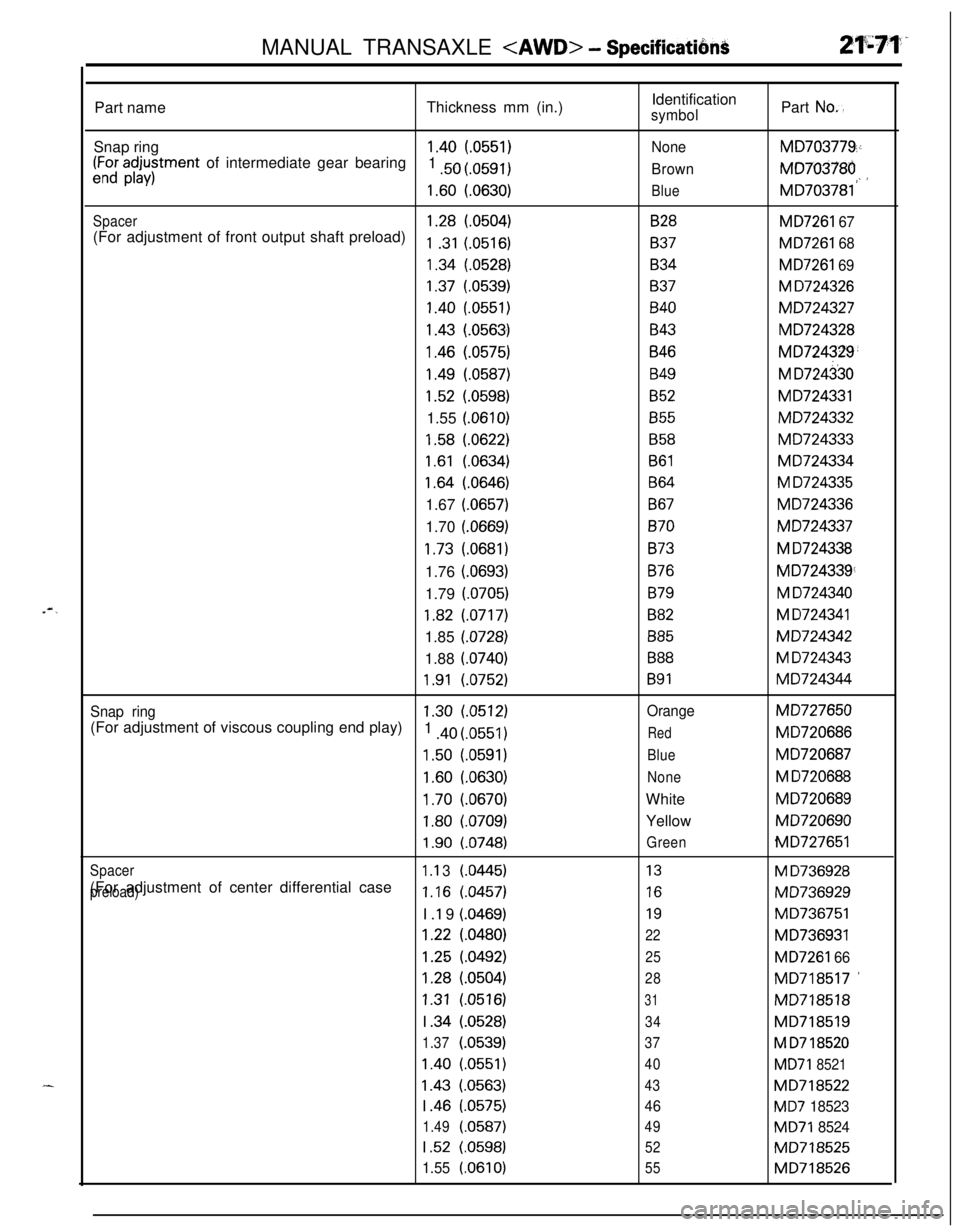
MANUAL TRANSAXLE
symbolPart No.,Snap ring
1.40 (0551)NoneMD703779,:
(Fo; x&tment of intermediate gear bearing
1 .50 (6591)BrownMD703786,.r
1.60 (.0630)BlueMD703781
Spacer1.28(0504)B28MD7261 67(For adjustment of front output shaft preload)1 .31 (.05I6)B37MD7261 68
1.34(0528)B34MD7261 69
1.37 (.0539)B37M D724326
1.40 (0551)B40MD724327
1.43 (.0563)B43MD724328
1.46 (0575)B46MD724329,:,1.49 (.0587)B49M D724330
1.52 (.0598)B52MD7243311.55 (0610)
B55MD724332
1.58 (.0622)B58MD724333
1.61 (.0634)B61MD724334
1.64 (.0646)B64M D7243351.67
(.0657)B67MD7243361.70
(.0669)B70MD724337
1.73 (0681)B73M D7243381.76
(.0693)B76MD724339:1.79
(.0705)B79M D724340
1.82 (0717)B82M D7243411.85 (0728)
B85MD7243421.88 (0740)
B88M D724343
1.91 (0752)B91MD724344
Snap ring
1.30 (0512)OrangeMD727650(For adjustment of viscous coupling end play)
1
.40 (,055~)RedMD720686
1.50 (.0591)BlueMD720687
1.60 (0630)NoneM D720688
1.70 (.0670)WhiteMD720689
1.80 (.0709)YellowMD720690
1.90 (.0748)GreenMD727651
Spacer1 .I 3(.0445)13M D736928(For adjustment of center differential case
preload)I. 16(0457)16MD736929I
.I 9 (.0469)I9MD736751
1.22(0480)22MD736931
1.25(.0492)25MD7261 66
1.28(.0504)28MD718517’
1.31(.0516)31MD718518I
.34(.0528)34MD718519
1.37(.0539)37M D7 18520
1.40(.0551)40MD71 8521
1.43(.0563)43MD718522I
.46(.0575)46MD7 18523
1.49(.0587)49MD71 8524I
.52(.0598)52MD718525
1.55
(.0610)55MD718526