MITSUBISHI SPYDER 1990 Service Repair Manual
Manufacturer: MITSUBISHI, Model Year: 1990, Model line: SPYDER, Model: MITSUBISHI SPYDER 1990Pages: 2103, PDF Size: 68.98 MB
Page 661 of 2103
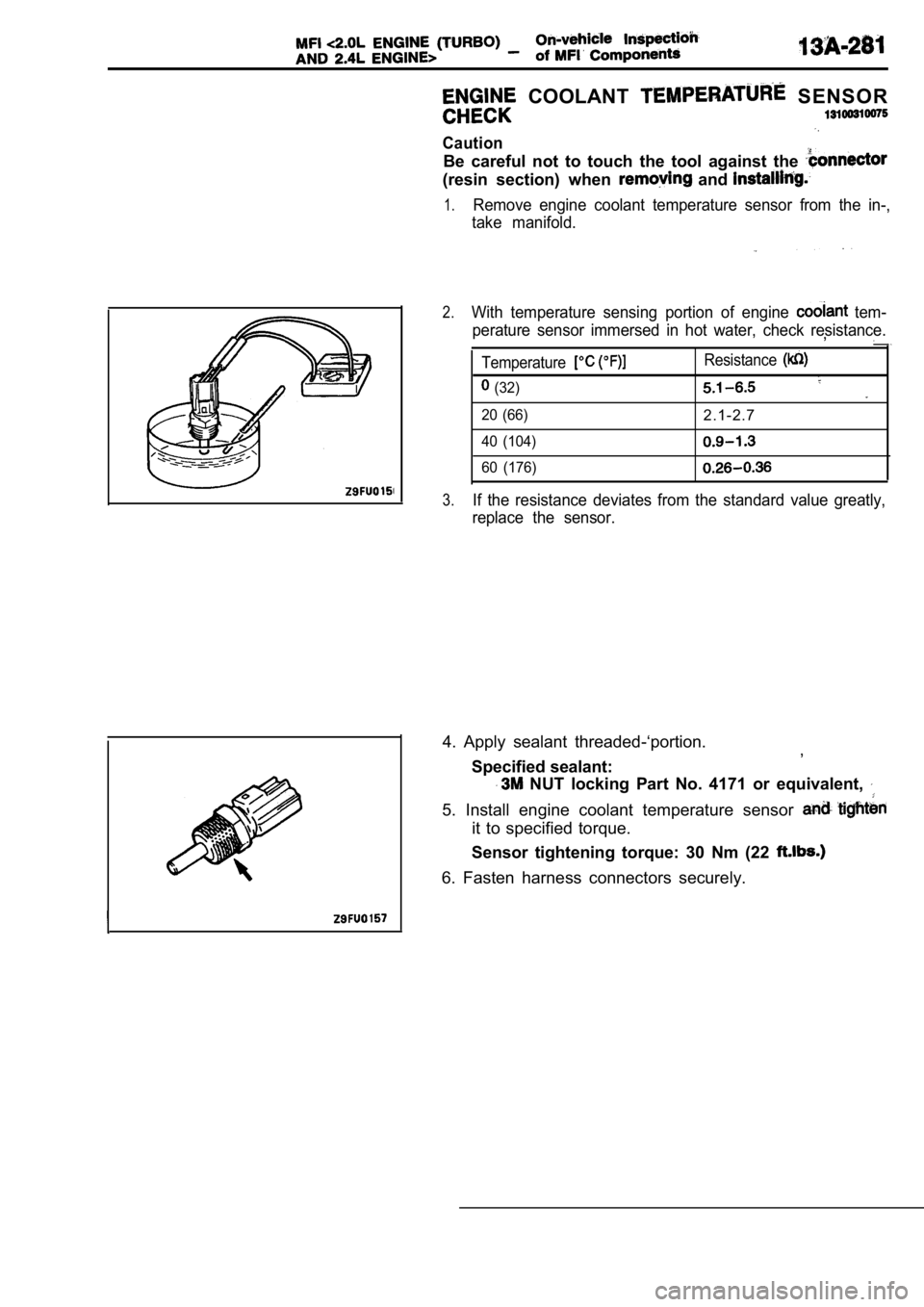
COOLANT SENSOR
Caution
Be careful not to touch the tool against the
(resin section) when and
1.Remove engine coolant temperature sensor from the in-,
take manifold.
2.With temperature sensing portion of engine tem-
perature sensor immersed in hot water, check resist ance.
,
Temperature
(32)
20 (66)
40 (104)
60 (176)
Resistance
2.1-2.7
3.If the resistance deviates from the standard value greatly,
replace the sensor.
4. Apply sealant threaded-‘portion. ,
Specified sealant:
NUT locking Part No. 4171 or equivalent,
5. Install engine coolant temperature sensor
it to specified torque.
Sensor tightening torque: 30 Nm (22
6. Fasten harness connectors securely.
Page 662 of 2103
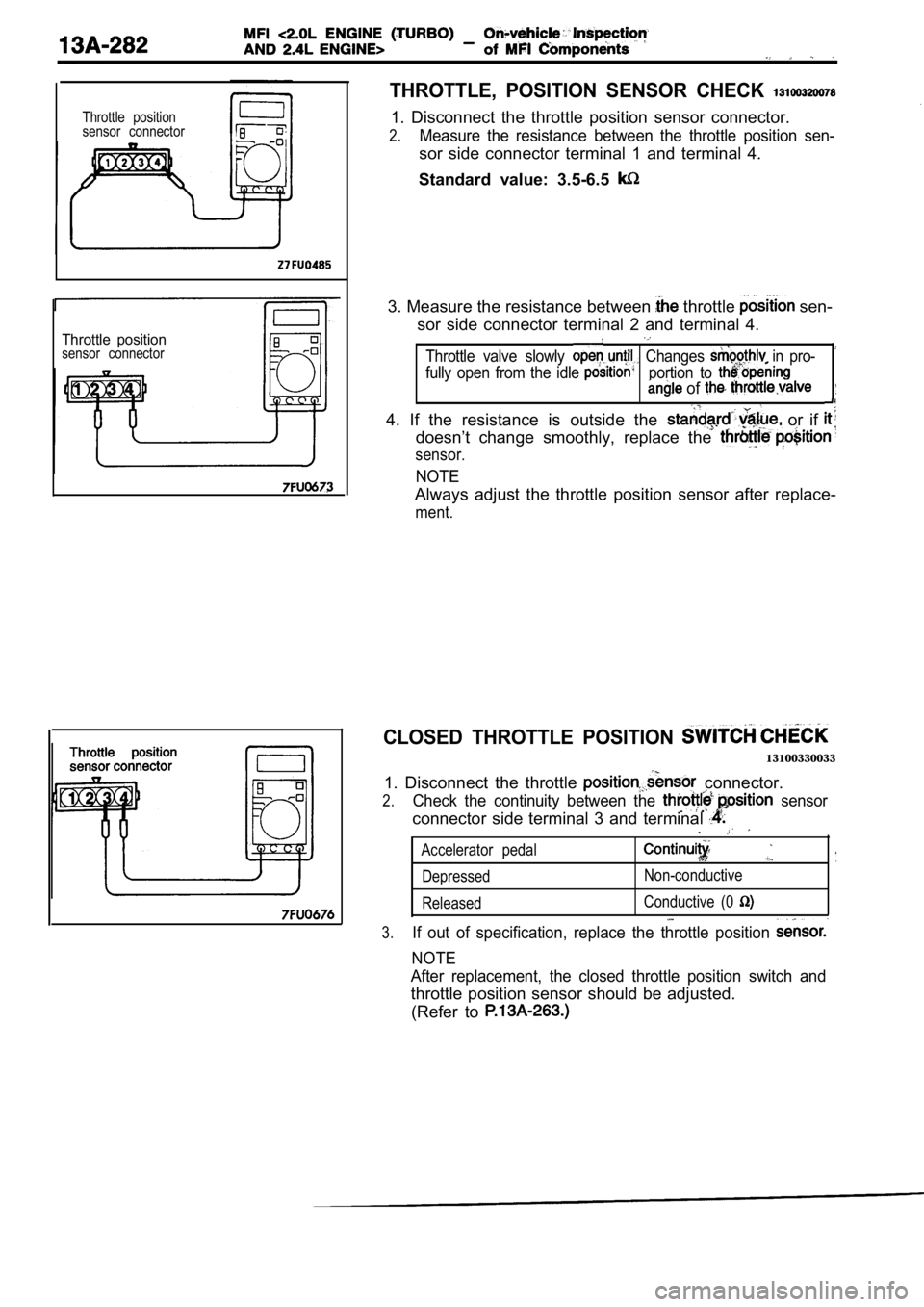
Throttle position
sensor connector
Throttle positionsensor connector
THROTTLE, POSITION SENSOR CHECK
1. Disconnect the throttle position sensor connector.
2.Measure the resistance between the throttle position sen-
sor side connector terminal 1 and terminal 4.
Standard value: 3.5-6.5
3. Measure the resistance between throttle sen-
sor side connector terminal 2 and terminal 4.
Throttle valve slowly Changes in pro-
fully open from the idle portion to
of .
4. If the resistance is outside the or if
doesn’t change smoothly, replace the
sensor.
NOTE
Always adjust the throttle position sensor after re place-
ment.
CLOSED THROTTLE POSITION
13100330033
1. Disconnect the throttle connector.
2.Check the continuity between the sensor
connector side terminal 3 and terminal .
Accelerator pedal
DepressedNon-conductive
Released Conductive (0
3.If out of specification, replace the throttle posit
ion
NOTE
After replacement, the closed throttle position swi tch and
throttle position sensor should be adjusted.
(Refer to
Page 663 of 2103
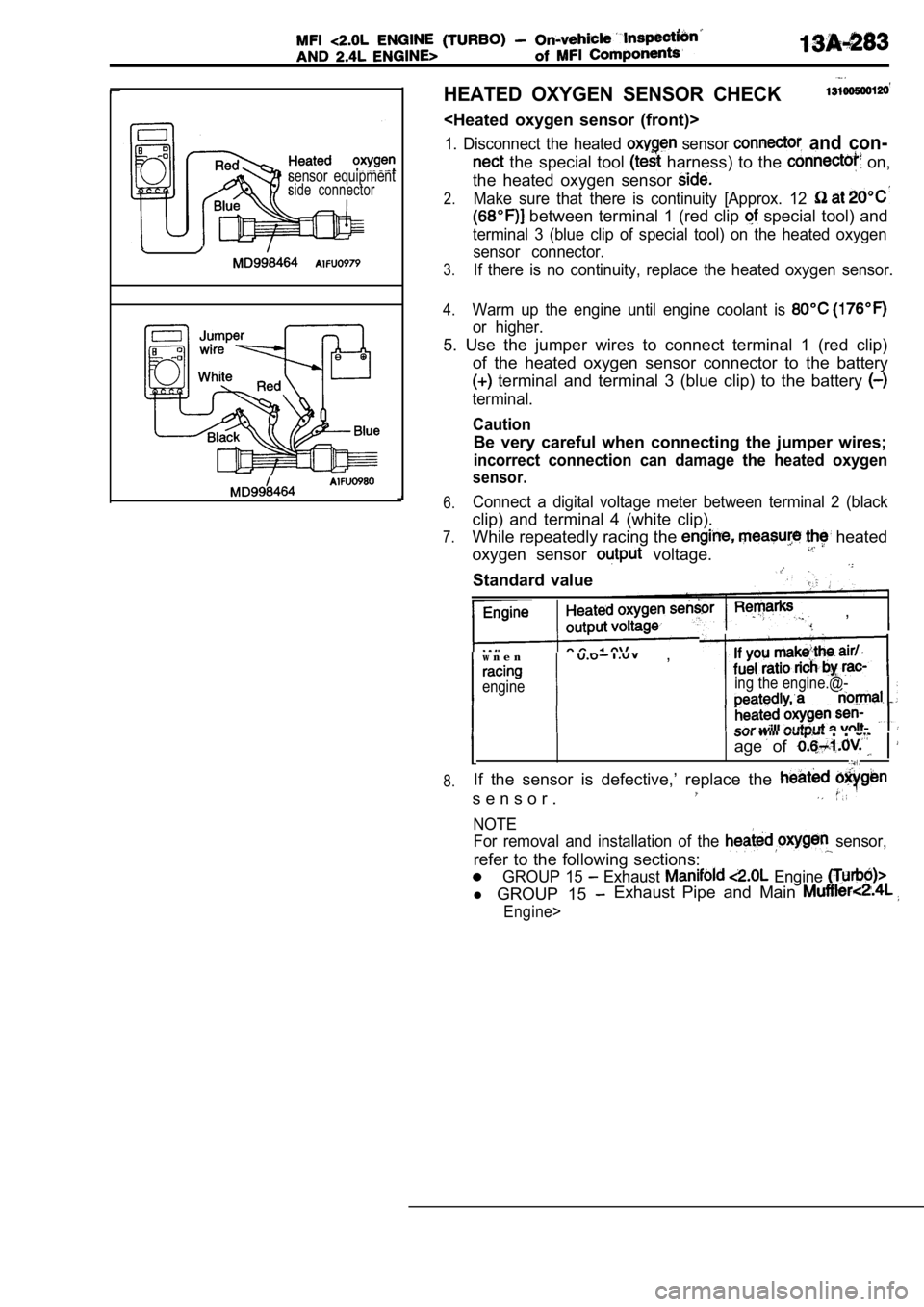
sensor equipmentside connector
HEATED OXYGEN SENSOR CHECK
1. Disconnect the heated sensor and con-
the special tool harness) to the on,
the heated oxygen sensor
2.Make sure that there is continuity [Approx. 12
between terminal 1 (red clip special tool) and
terminal 3 (blue clip of special tool) on the heate d oxygen
sensor connector.
3.If there is no continuity, replace the heated oxyge n sensor.
4.Warm up the engine until engine coolant is
or higher.
5. Use the jumper wires to connect terminal 1 (red clip)
of the heated oxygen sensor connector to the batter y
terminal and terminal 3 (blue clip) to the battery
terminal.
Caution
Be very careful when connecting the jumper wires;
incorrect connection can damage the heated oxygen
sensor.
6.
7.
8.Connect a digital voltage meter between terminal 2 (black
clip) and terminal 4 (white clip).
While repeatedly racing the
heated
oxygen sensor
voltage.
Standard value
,
w n e n ,
engineing the engine.@-
. .
age of
If the sensor is defective,’ replace the
s e n s o r .
NOTEFor removal and installation of the
sensor,
refer to the following sections:
GROUP 15 Exhaust Engine
l GROUP 15 Exhaust Pipe and Main
Engine>
Page 664 of 2103
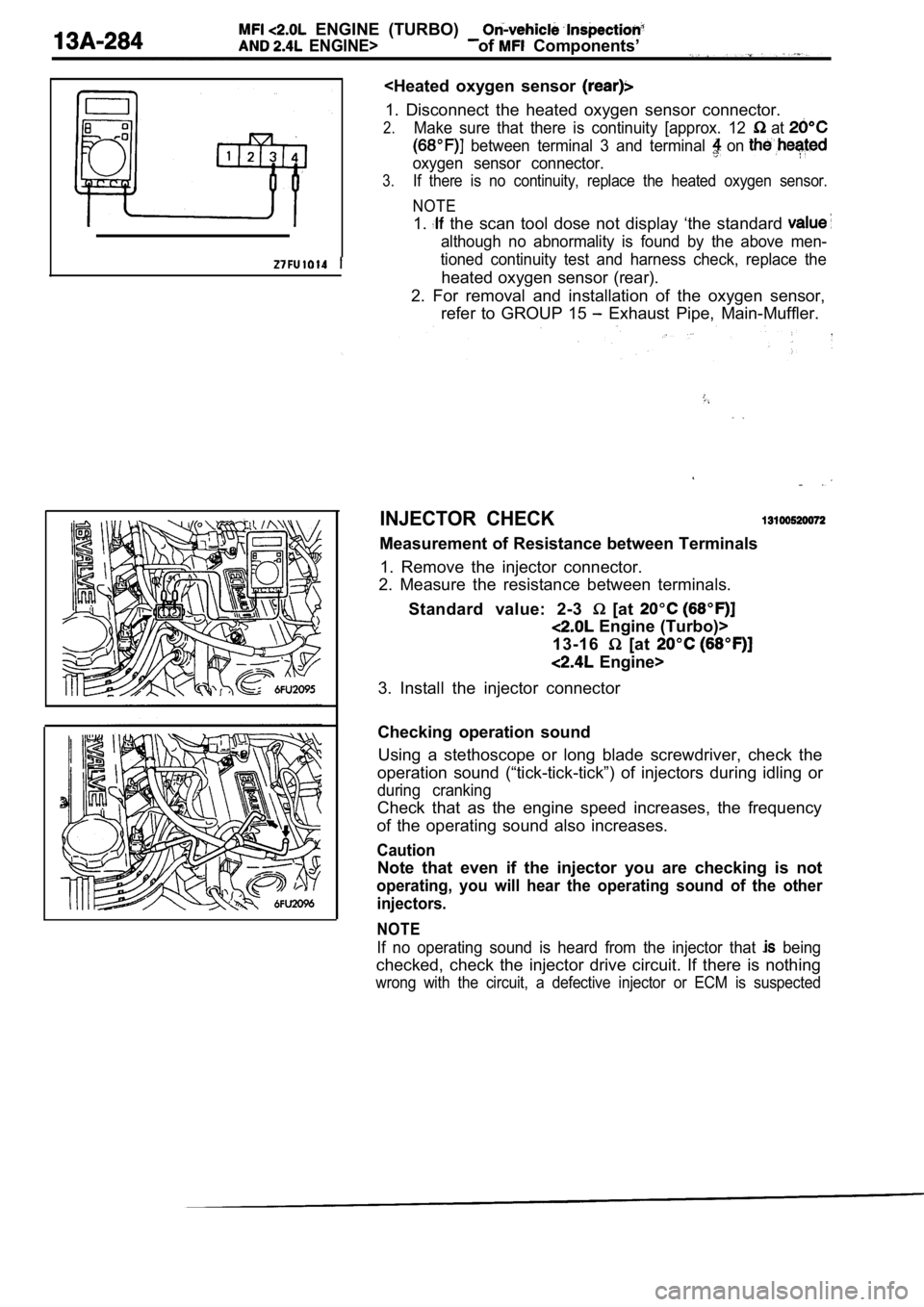
ENGINE (TURBO)
ENGINE>of Components’
2.Make sure that there is continuity [approx. 12 at
between terminal 3 and terminal on
oxygen sensor connector.
3.If there is no continuity, replace the heated oxyge n sensor.
NOTE
1. the scan tool dose not display ‘the standard
although no abnormality is found by the above men-
tioned continuity test and harness check, replace t he
heated oxygen sensor (rear).
2. For removal and installation of the oxygen senso r,
refer to GROUP 15
Exhaust Pipe, Main-Muffler.
INJECTOR CHECK
Measurement of Resistance between Terminals
1. Remove the injector connector.
2. Measure the resistance between terminals.
Standard value: 2-3
[at
Engine (Turbo)>
13-16
[at
Engine>
3. Install the injector connector
Checking operation sound Using a stethoscope or long blade screwdriver, chec k the
operation sound (“tick-tick-tick”) of injectors dur ing idling or
during cranking
Check that as the engine speed increases, the frequ ency
of the operating sound also increases.
Caution
Note that even if the injector you are checking is not
operating, you will hear the operating sound of the other
injectors.
NOTE
If no operating sound is heard from the injector th at being
checked, check the injector drive circuit. If there is nothing
wrong with the circuit, a defective injector or ECM is suspected
Page 665 of 2103
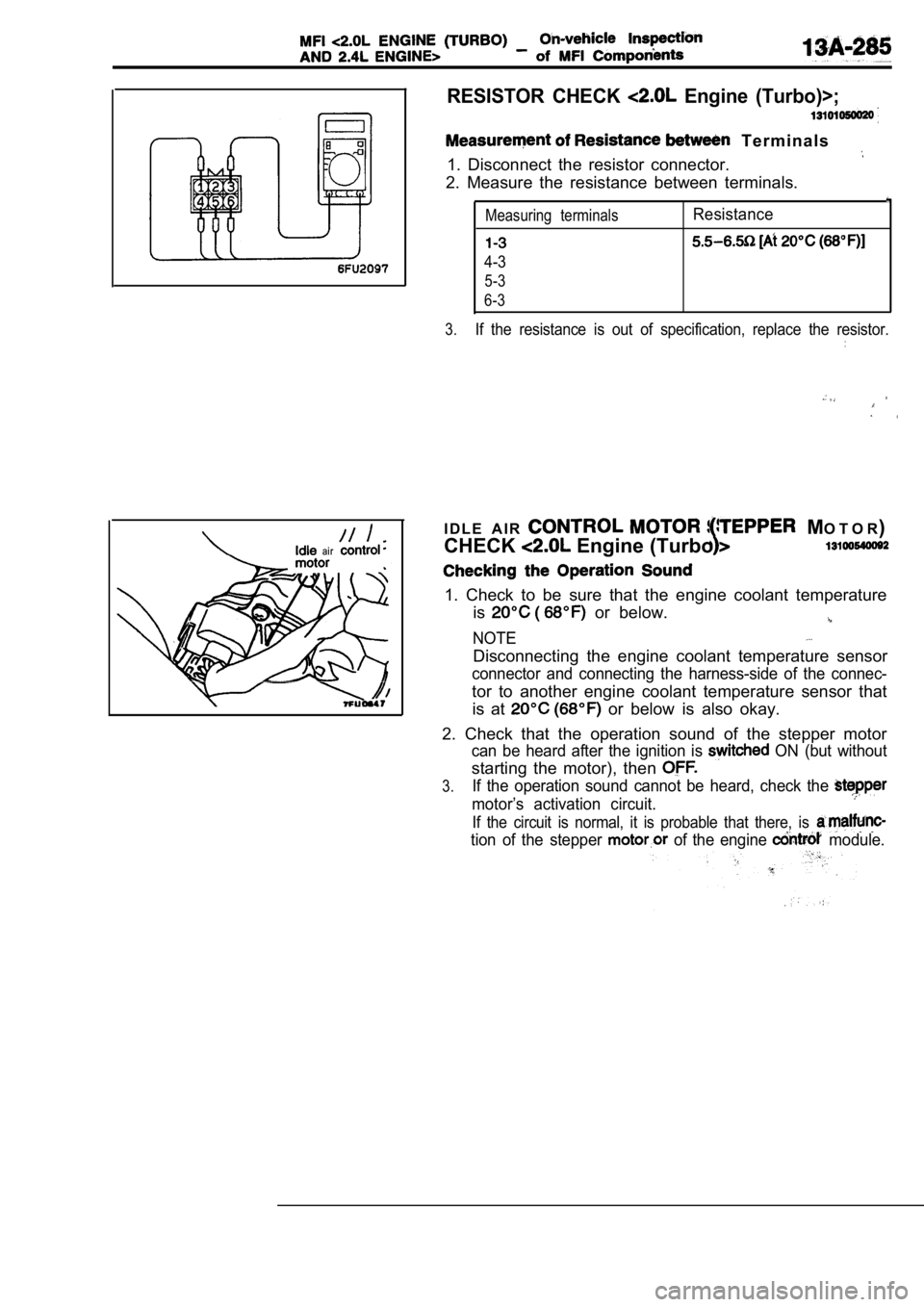
RESISTOR CHECK Engine (Turbo)>;
T e r m i n a l s
1. Disconnect the resistor connector.
2. Measure the resistance between terminals.
Measuring terminalsResistance
4-3
5-3
6-3
3.
If the resistance is out of specification, replace the resistor.
ai r
I D L E A I R MO T O R )
CHECK Engine (Turbo
1. Check to be sure that the engine coolant tempera ture
is
or below.
NOTE
Disconnecting the engine coolant temperature sensor
connector and connecting the harness-side of the co nnec-
tor to another engine coolant temperature sensor th at
is at
or below is also okay.
2. Check that the operation sound of the stepper mo tor
can be heard after the ignition is ON (but without
starting the motor), then
3.If the operation sound cannot be heard, check the
motor’s activation circuit.
If the circuit is normal, it is probable that there, is
tion of the stepper of the engine module.
Page 666 of 2103
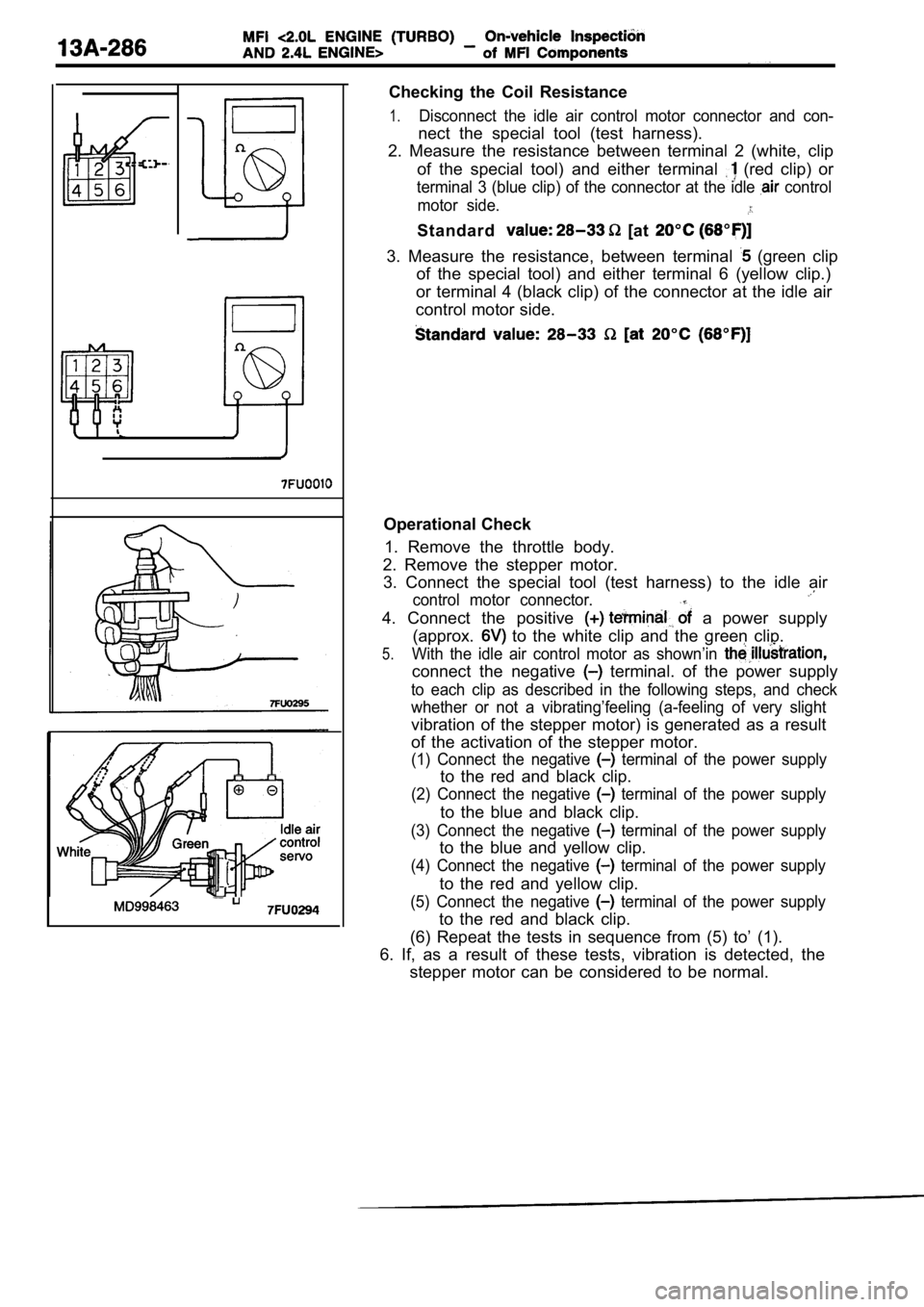
Checking the Coil Resistance
1.Disconnect the idle air control motor connector and con-
nect the special tool (test harness).
2. Measure the resistance between terminal 2 (white , clip
of the special tool) and either terminal
(red clip) or
terminal 3 (blue clip) of the connector at the idle control
motor side.
Standard [at
3. Measure the resistance, between terminal (green clip
of the special tool) and either terminal 6 (yellow clip.)
or terminal 4 (black clip) of the connector at the idle air
control motor side.
Operational Check
1. Remove the throttle body.
2. Remove the stepper motor. 3. Connect the special tool (test harness) to the i dle air
control motor connector.
4. Connect the positive a power supply
(approx.
to the white clip and the green clip.
5.With the idle air control motor as shown’in
connect the negative terminal. of the power supply
to each clip as described in the following steps, a nd check
whether or not a vibrating’feeling (a-feeling of ve ry slight
vibration of the stepper motor) is generated as a r esult
of the activation of the stepper motor.
(1) Connect the negative terminal of the power supply
to the red and black clip.
(2) Connect the negative terminal of the power supply
to the blue and black clip.
(3) Connect the negative terminal of the power supply
to the blue and yellow clip.
(4) Connect the negative terminal of the power supply
to the red and yellow clip.
(5) Connect the negative terminal of the power supply
to the red and black clip.
(6) Repeat the tests in sequence from (5) to’ (1).
6. If, as a result of these tests, vibration is det ected, the
stepper motor can be considered to be normal.
Page 667 of 2103
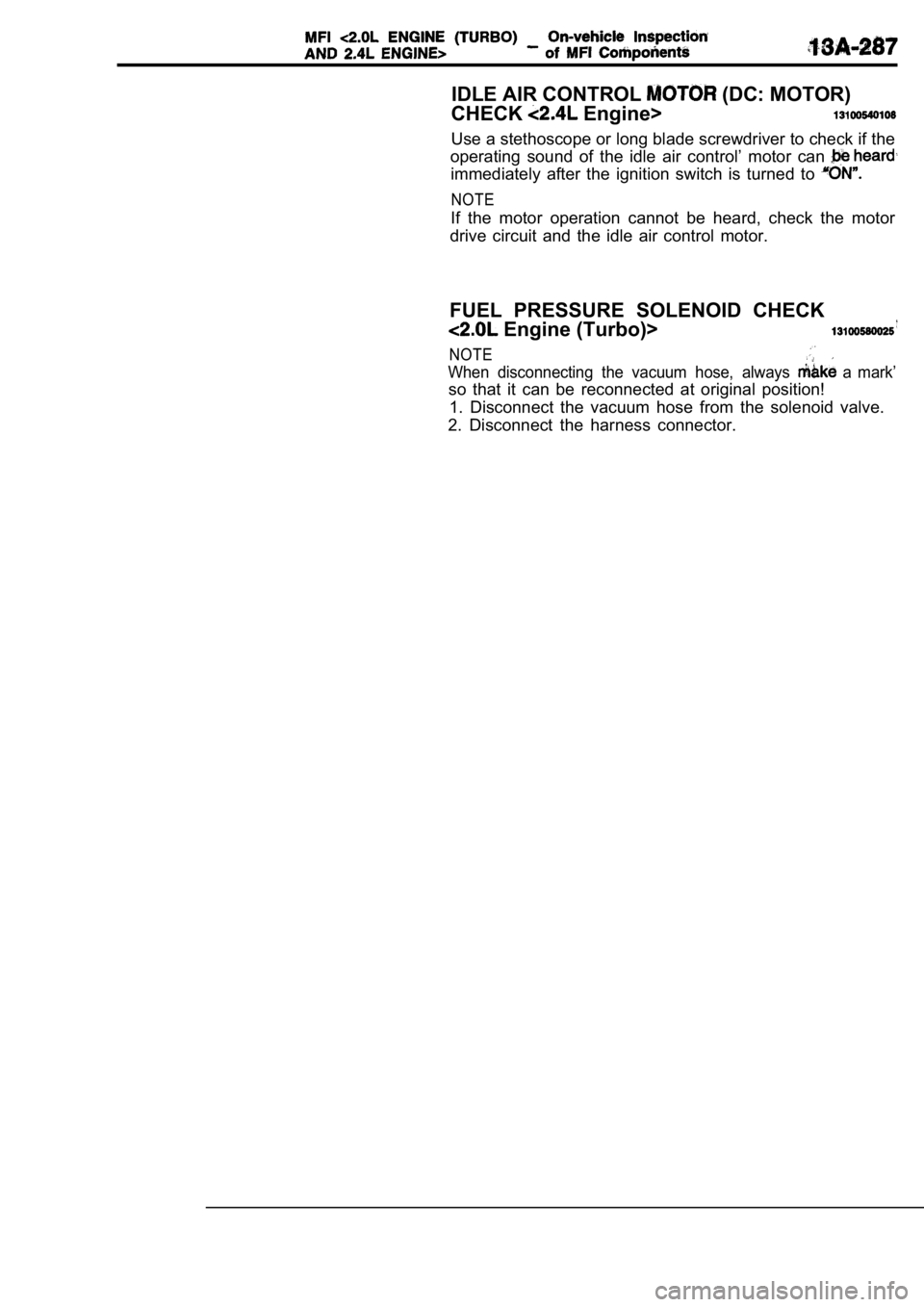
IDLE AIR CONTROL (DC: MOTOR)
CHECK
Engine>
Use a stethoscope or long blade screwdriver to chec k if the
operating sound of the idle air control’ motor can
immediately after the ignition switch is turned to
NOTE
If the motor operation cannot be heard, check the m otor
drive circuit and the idle air control motor.
FUEL PRESSURE SOLENOID CHECK
Engine (Turbo)>
NOTE
When disconnecting the vacuum hose, always a mark’
so that it can be reconnected at original position! 1. Disconnect the vacuum hose from the solenoid val ve.
2. Disconnect the harness connector.
Page 668 of 2103
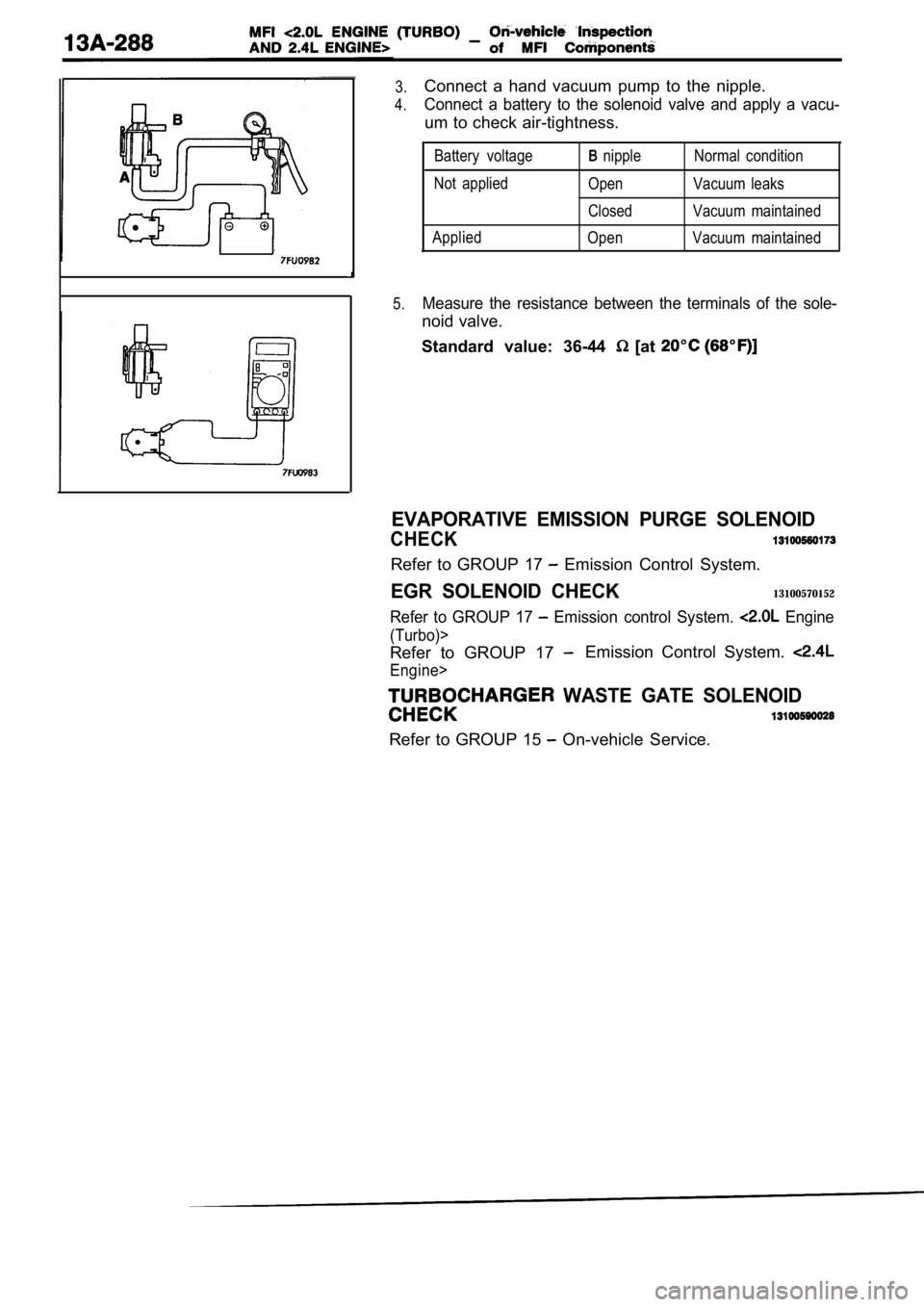
Connect a hand vacuum pump to the nipple.
Connect a battery to the solenoid valve and apply a vacu-
um to check air-tightness.
Battery voltage
Not applied
Applied nipple
Open
Closed
Open Normal condition
Vacuum leaks
Vacuum maintained
Vacuum maintained
Measure the resistance between the terminals of the sole-
noid valve.
Standard value: 36-44
[at
3.
4.
5.
EVAPORATIVE EMISSION PURGE SOLENOID
CHECK
Refer to GROUP 17 Emission Control System.
EGR SOLENOID CHECK13100570152
Refer to GROUP 17 Emission control System. Engine
(Turbo)>
Refer to GROUP 17 Emission Control System.
Engine>
WASTE GATE SOLENOID
Refer to GROUP 15 On-vehicle Service.
Page 669 of 2103
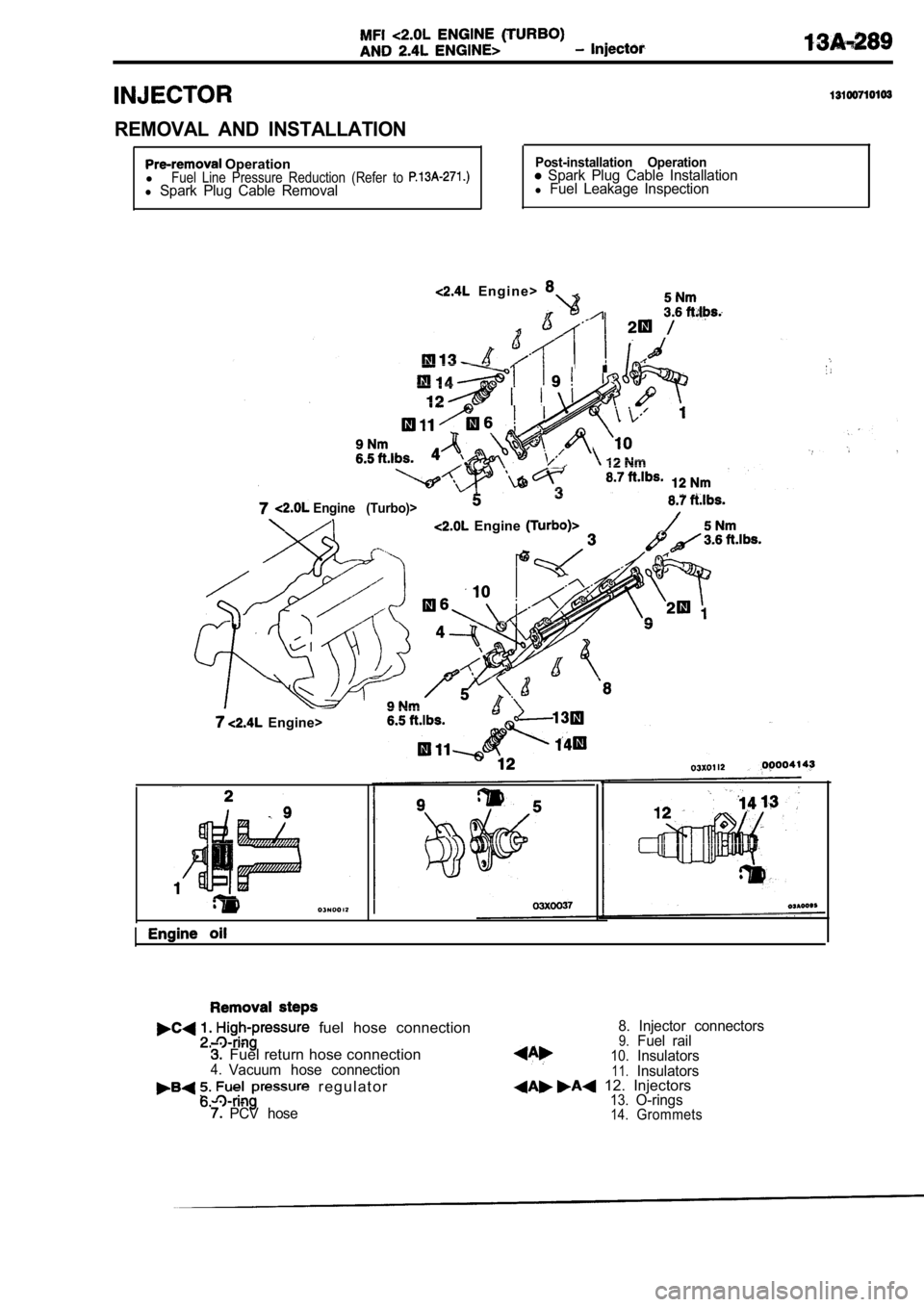
REMOVAL AND INSTALLATION
Operation
lFuel Line Pressure Reduction (Refer to l Spark Plug Cable Removal
Post-installation Operation Spark Plug Cable Installationl Fuel Leakage Inspection
E n g i n e >
Engine (Turbo)>
I:
Engine
Engine>
fuel hose connection
Fuel return hose connection4.Vacuum hose connection
r e g u l a t o r
PCV hose 8. Injector connectors
9.Fuel rail10.Insulators11.Insulators 12. Injectors13.O-rings14.Grommets
Page 670 of 2103
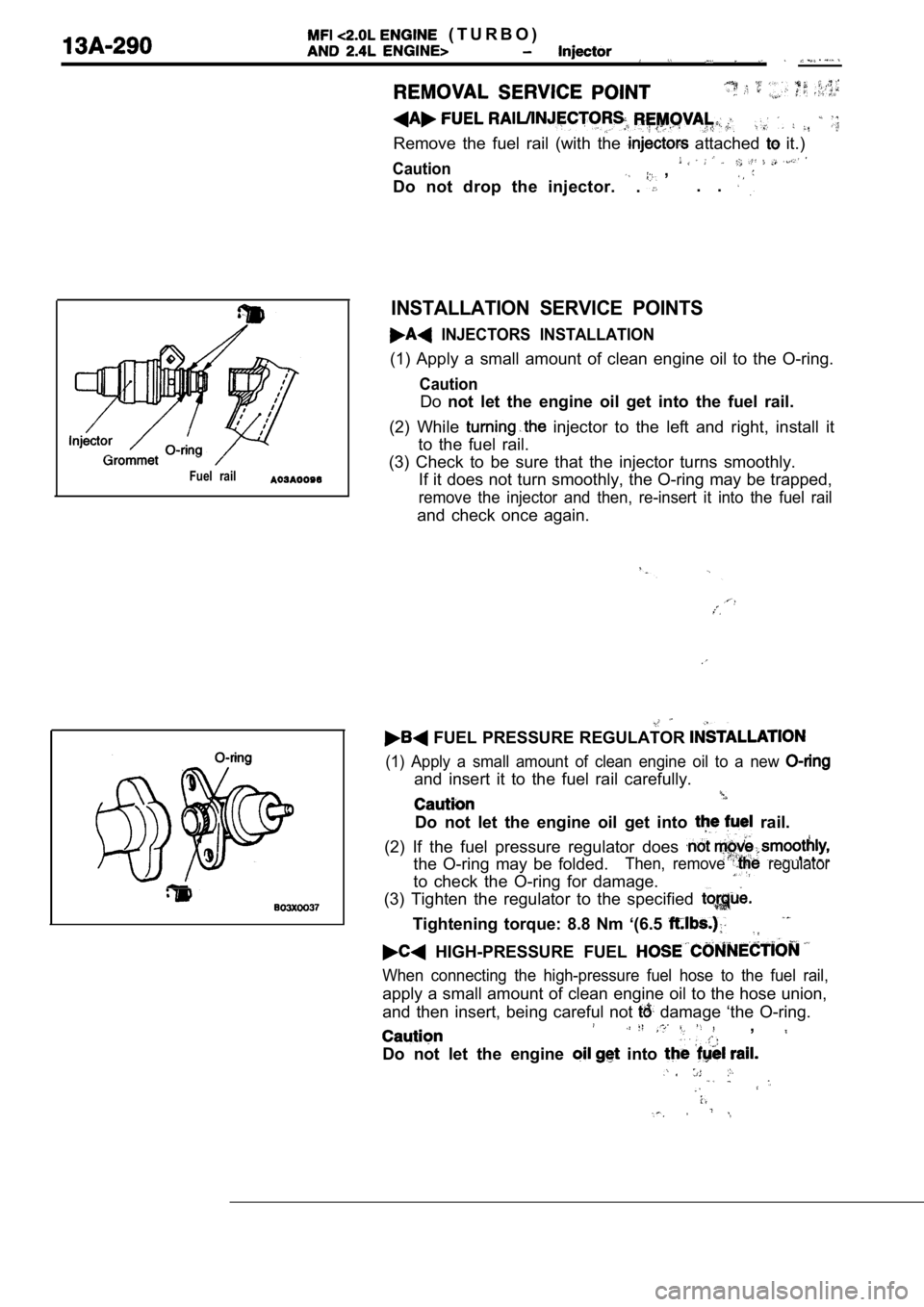
( T U R B O )
Remove the fuel rail (with the attached it.)
Caution ,
Do not drop the injector.
. . .
Fuel rail
INSTALLATION SERVICE POINTS
INJECTORS INSTALLATION
(1) Apply a small amount of clean engine oil to the O-ring.
Caution
Donot let the engine oil get into the fuel rail.
(2) While
injector to the left and right, install it
to the fuel rail.
(3) Check to be sure that the injector turns smooth ly.
If it does not turn smoothly, the O-ring may be tra pped,
remove the injector and then, re-insert it into the fuel rail
and check once again.
FUEL PRESSURE REGULATOR
(1) Apply a small amount of clean engine oil to a n ew
and insert it to the fuel rail carefully.
Do not let the engine oil get into rail.
(2) If the fuel pressure regulator does
the O-ring may be folded.Then, remove regulator
to check the O-ring for damage.
(3) Tighten the regulator to the specified
Tightening torque: 8.8 Nm ‘(6.5
HIGH-PRESSURE FUEL
When connecting the high-pressure fuel hose to the fuel rail,
apply a small amount of clean engine oil to the hose union,
and then insert, being careful not
damage ‘the O-ring.,
Do not let the engine into
,