NISSAN PULSAR 1987 Workshop Manual
Manufacturer: NISSAN, Model Year: 1987, Model line: PULSAR, Model: NISSAN PULSAR 1987Pages: 238, PDF Size: 28.91 MB
Page 191 of 238
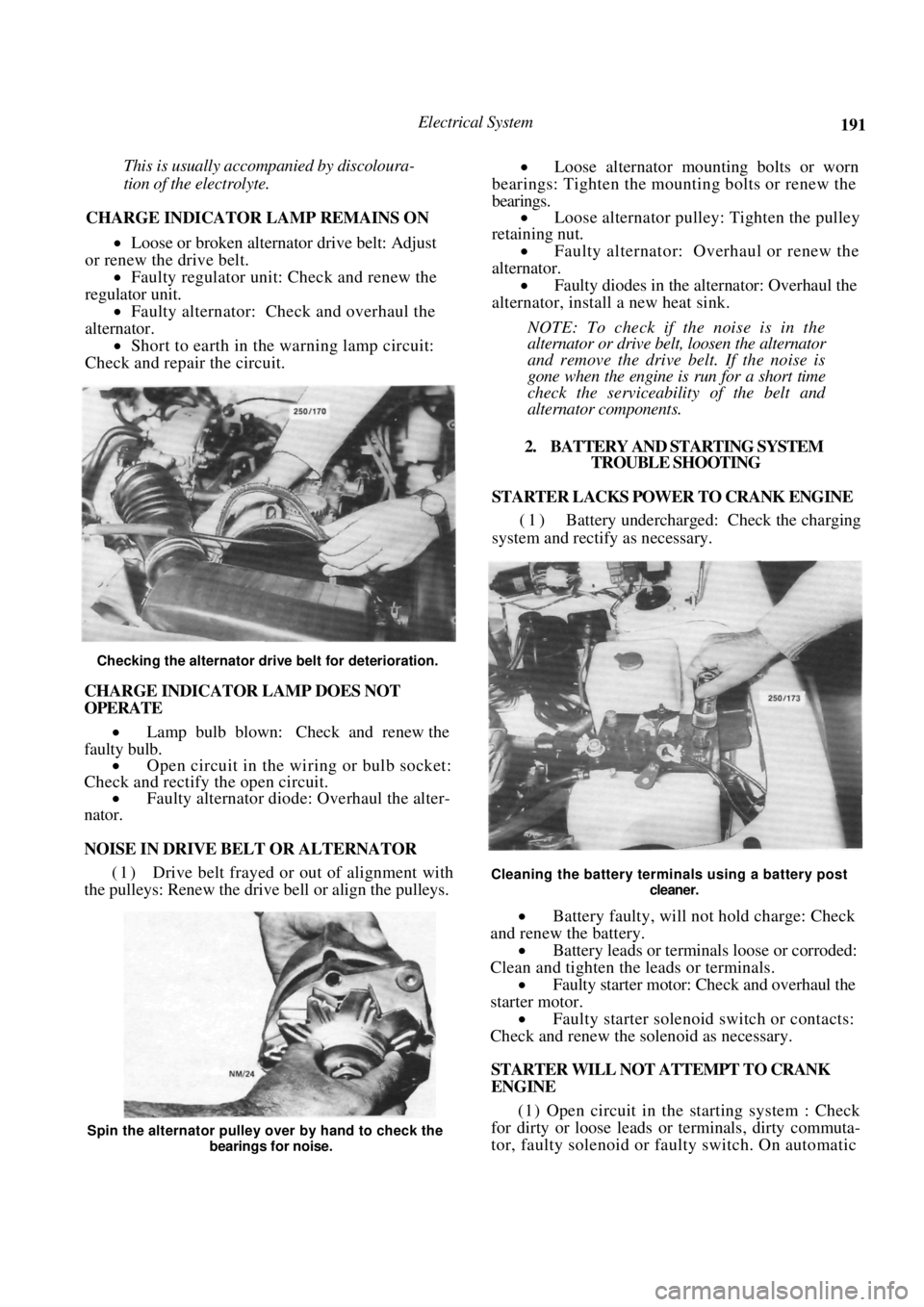
Electrical System 191
This is usually accompanied by discoloura-
tion of the electrolyte.
CHARGE INDICATOR LAMP REMAINS ON
• Loose or broken alternator drive belt: Adjust
or renew the drive belt.
• Faulty regulator unit: Check and renew the
regulator unit. • Faulty alternator: Check and overhaul the
alternator. • Short to earth in the warning lamp circuit:
Check and repair the circuit.
Checking the alternator drive belt for deterioration.
CHARGE INDICATOR LAMP DOES NOT
OPERATE
• Lamp bulb blown: Check and renew the
faulty bulb. • Open circuit in the wi ring or bulb socket:
Check and rectify the open circuit. • Faulty alternator diode: Overhaul the alter-
nator.
NOISE IN DRIVE BELT OR ALTERNATOR
(1) Drive belt frayed or out of alignment with
the pulleys: Renew the drive bell or align the pulleys.
• Loose alternator moun ting bolts or worn
bearings: Tighten the mounting bolts or renew the
bearings. • Loose alternator pulley: Tighten the pulley
retaining nut.
• Faulty alternator: Overhaul or renew the
alternator. • Faulty diodes in the alternator: Overhaul the
alternator, install a new heat sink.
NOTE: To check if the noise is in the
alternator or drive belt, loosen the alternator
and remove the drive belt. If the noise is
gone when the engine is run for a short time
check the serviceability of the belt and
alternator components.
2. BATTERY AND STARTING SYSTEM TROUBLE SHOOTING
STARTER LACKS POWER TO CRANK ENGINE
(1) Battery undercharged: Check the charging
system and rectify as necessary.
Cleaning the battery terminals using a battery post
cleaner.
• Battery faulty, will not hold charge: Check
and renew the battery. • Battery leads or terminals loose or corroded:
Clean and tighten the leads or terminals.
• Faulty starter motor: Check and overhaul the
starter motor. • Faulty starter solenoid switch or contacts:
Check and renew the solenoid as necessary.
STARTER WILL NOT ATTEMPT TO CRANK
ENGINE
(1 ) Open circuit in the starting system : Check
for dirty or loose leads or terminals, dirty commuta-
tor, faulty solenoid or faulty switch. On automatic
Spin the alternator pulley over by hand to check the
bearings for noise.
Page 192 of 238
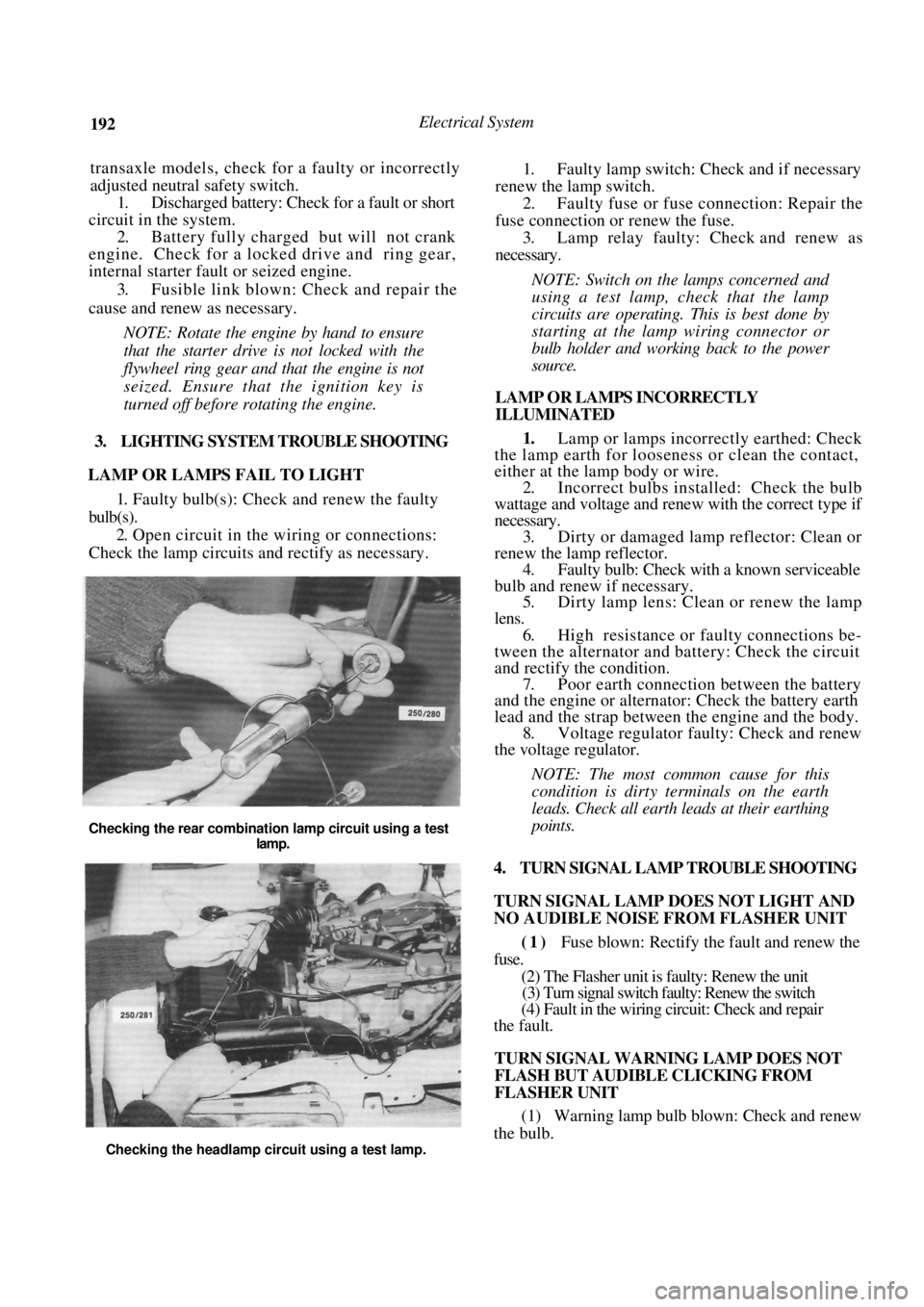
192 Electrical System
transaxle models, check for a faulty or incorrectly
adjusted neutral safety switch.
1. Discharged battery: Check for a fault or short
circuit in the system. 2. Battery fully charged but will not crank
engine. Check for a locked drive and ring gear,
internal starter faul t or seized engine.
3. Fusible link blown: Check and repair the
cause and renew as necessary.
NOTE: Rotate the engine by hand to ensure
that the starter drive is not locked with the
flywheel ring gear and t hat the engine is not
seized. Ensure that the ignition key is
turned off before rotating the engine.
3. LIGHTING SYSTEM TROUBLE SHOOTING
LAMP OR LAMPS FAIL TO LIGHT
1. Faulty bulb(s): Check and renew the faulty
bulb(s). 2. Open circuit in the wiring or connections:
Check the lamp circuits and rectify as necessary.
1. Faulty lamp switch: Check and if necessary
renew the lamp switch. 2. Faulty fuse or fuse connection: Repair the
fuse connection or renew the fuse. 3. Lamp relay faulty: Check and renew as
necessary.
NOTE: Switch on the lamps concerned and
using a test lamp, check that the lamp
circuits are operating. This is best done by
starting at the lamp wiring connector or
bulb holder and work ing back to the power
source.
LAMP OR LAMPS INCORRECTLY
ILLUMINATED
1. Lamp or lamps incorrectly earthed: Check
the lamp earth for loosene ss or clean the contact,
either at the lamp body or wire.
2. Incorrect bulbs installe d: Check the bulb
wattage and voltage and renew with the correct type if
necessary. 3. Dirty or damaged lamp reflector: Clean or
renew the lamp reflector. 4. Faulty bulb: Check with a known serviceable
bulb and renew if necessary. 5. Dirty lamp lens: Clean or renew the lamp
lens. 6. High resistance or faulty connections be-
tween the alternator and battery: Check the circuit
and rectify th e condition.
7. Poor earth connection between the battery
and the engine or alternat or: Check the battery earth
lead and the strap between the engine and the body. 8. Voltage regulator faulty: Check and renew
the voltage regulator.
NOTE: The most common cause for this
condition is dirty t erminals on the earth
leads. Check all earth leads at their earthing
points.
4. TURN SIGNAL LAMP TROUBLE SHOOTING
TURN SIGNAL LAMP DOES NOT LIGHT AND
NO AUDIBLE NOISE FROM FLASHER UNIT
(1) Fuse blown: Rectify the fault and renew the
fuse.
(2) The Flasher unit is faulty: Renew the unit
(3) Turn signal switch faulty: Renew the switch
(4) Fault in the wiring circuit: Check and repair
the fault.
TURN SIGNAL WARNING LAMP DOES NOT
FLASH BUT AUDIBLE CLICKING FROM
FLASHER UNIT
(1) Warning lamp bulb blown: Check and renew
the bulb.
Checking the rear combination lamp circuit using a test
lamp.
Checking the headlamp circuit using a test lamp.
Page 193 of 238
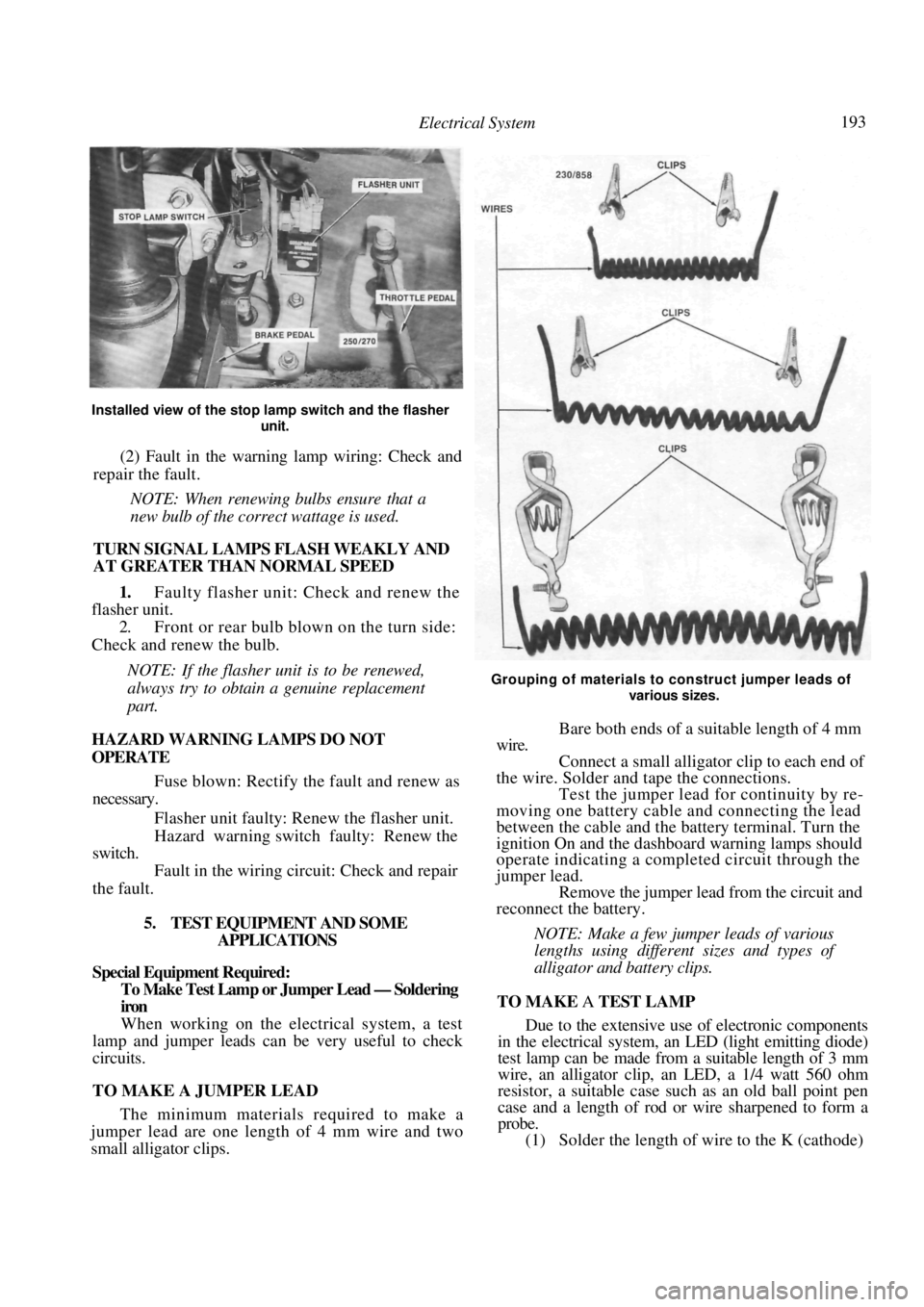
Electrical System 193
Installed view of the stop lamp switch and the flasher
unit.
(2) Fault in the warning lamp wiring: Check and
repair the fault.
NOTE: When renewing bulbs ensure that a
new bulb of the correct wattage is used.
TURN SIGNAL LAMPS FLASH WEAKLY AND
AT GREATER THAN NORMAL SPEED
1. Faulty flasher unit: Check and renew the
flasher unit.
2. Front or rear bulb blown on the turn side:
Check and renew the bulb.
NOTE: If the flasher unit is to be renewed,
always try to obtain a genuine replacement
part.
HAZARD WARNING LAMPS DO NOT
OPERATE
Fuse blown: Rectify the fault and renew as
necessary.
Flasher unit faulty: Re new the flasher unit.
Hazard warning switch faulty: Renew the
switch.
Fault in the wiring circuit: Check and repair
the fault.
5. TEST EQUIPMENT AND SOME APPLICATIONS
Special Equipment Required:
To Make Test Lamp or Jumper Lead — Soldering
iron
When working on the electrical system, a test
lamp and jumper leads can be very useful to check
circuits.
TO MAKE A JUMPER LEAD
The minimum materials required to make a
jumper lead are one length of 4 mm wire and two
small alligator clips.
Grouping of materials to construct jumper leads of
various sizes.
Bare both ends of a suitable length of 4 mm
wire. Connect a small alligato r clip to each end of
the wire. Solder and tape the connections. Test the jumper lead for continuity by re-
moving one battery cable and connecting the lead
between the cable and the battery terminal. Turn the
ignition On and the dashboard warning lamps should
operate indicating a completed circuit through the
jumper lead. Remove the jumper lead from the circuit and
reconnect the battery.
NOTE: Make a few jumper leads of various
lengths using different sizes and types of
alligator and battery clips.
TO MAKE A TEST LAMP
Due to the extensive use of electronic components
in the electrical system, an LED (light emitting diode)
test lamp can be made from a suitable length of 3 mm
wire, an alligator clip, an LED, a 1/4 watt 560 ohm
resistor, a suitable case such as an old ball point pen
case and a length of rod or wire sharpened to form a
probe.
(1) Solder the length of wire to the K (cathode)
Page 194 of 238

194 Electrical System
Schematic of LED test lamp. Ensure that the connec-
tions to the K (cathode) lead and A (anode) lead of the LED are as illustrated.
lead of the LED. The K lead is the shorter of the two
leads and is adjacent to the flat on the LED.
Solder the 560 ohm resister to the A (anode)
lead of the LED. Solder a short length of wire to the other lead
of the resistor and to the probe. Drill a hole in the side of the case to accept
the wire attached to the K lead of the LED. Mount the probe in the case. If using a pen
case, push the probe through the lower end of the pen
after removing the refill. Push the lead attached to the K lead of the
LED through the hole made in the side of the case and
solder the alligator clip to the lead.
Mount the LED to the case. If using a pen
case, the LED may be mounted in the plug at the top
of the pen after drilling the plug to accept the LED. Suitably attach the probe to the case using
adhesive or tape.
TO TEST SWITCHES
Disconnect the wires from the switch.
Using a test lamp, test each wire to locate the
power wire. It may be nec essary to turn the ignition
On as the switch may be wired through the ignition
circuit. Disconnect the test lamp and connect a jumper lead between the power wire and the wire
from the other side of the switch.
If the circuit functions, the switch can be consid-
ered faulty and should be renewed. Refer to the
heading Switches and Controls.
TO TEST BULBS
Remove the bulb from the bulb holder.
Connect a jumper lead between the positive
terminal of a battery a nd the base of the bulb.
Connect another jumper lead between the
negative battery terminal and the contact on the base
of the bulb. The bulb should illuminate. If the bulb has two filaments, connect the jumper
lead to the second contact on the base of the bulb. The
second filament should illuminate.
If the bulb fails to illuminate, it should be
renewed with a bulb of the correct voltage and
wattage.
TO TEST CIRCUITS
Turn the circuit switch On.
Using a test lamp, check for power at one of
the circuit connections. A fuse is a good starting point.
If power is available, reconnect the connector and
continue checking towards the motor or bulb end of
the circuit.
If power is not available, continue checking
towards the battery or switch end of the circuit.
6. BATTERY
Special Equipment Required: To Test — Hydrometer
To Charge — Battery charger
TO REMOVE AND INSTAL
(1) Disconnect the negative and positive battery
terminals.
Installed view of the battery.
Page 195 of 238
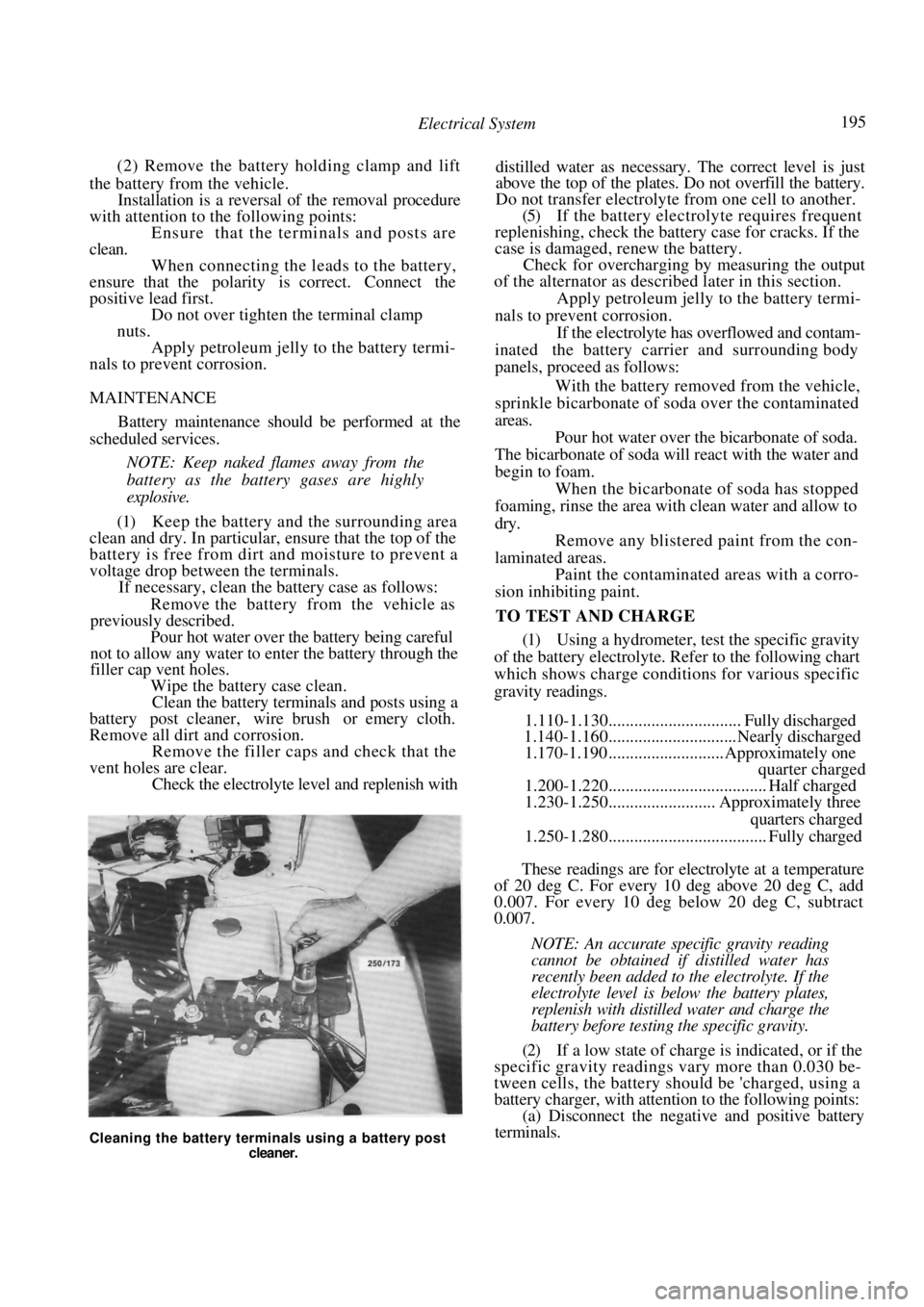
Electrical System 195
(2) Remove the battery holding clamp and lift
the battery from the vehicle.
Installation is a reversal of the removal procedure
with attention to the following points:
Ensure that the terminals and posts are
clean. When connecting the l eads to the battery,
ensure that the polarity is correct. Connect the
positive lead first. Do not over tighten the terminal clamp
nuts.
Apply petroleum jelly to the battery termi-
nals to prevent corrosion.
MAINTENANCE
Battery maintenance should be performed at the
scheduled services.
NOTE: Keep naked flames away from the
battery as the battery gases are highly
explosive.
(1) Keep the battery and the surrounding area
clean and dry. In particular, ensure that the top of the
battery is free from dirt and moisture to prevent a
voltage drop between the terminals.
If necessary, clean the battery case as follows:
Remove the battery from the vehicle as
previously described.
Pour hot water over the battery being careful
not to allow any water to enter the battery through the
filler cap vent holes. Wipe the battery case clean.
Clean the battery terminals and posts using a
battery post cleaner, wire brush or emery cloth.
Remove all dirt and corrosion.
Remove the filler caps and check that the
vent holes are clear. Check the electrolyte le vel and replenish with distilled water as necessary. The correct level is just
above the top of the plates. Do not overfill the battery.
Do not transfer electrolyte from one cell to another.
(5) If the battery electrolyte requires frequent
replenishing, check the batt ery case for cracks. If the
case is damaged, renew the battery.
Check for overcharging by measuring the output
of the alternator as described later in this section.
Apply petroleum jelly to the battery termi-
nals to prevent corrosion. If the electrolyte has overflowed and contam-
inated the battery carrier and surrounding body
panels, proceed as follows:
With the battery removed from the vehicle,
sprinkle bicarbonate of soda over the contaminated
areas.
Pour hot water over the bicarbonate of soda.
The bicarbonate of soda will react with the water and
begin to foam. When the bicarbonate of soda has stopped
foaming, rinse the area with clean water and allow to
dry. Remove any blistered paint from the con-
laminated areas. Paint the contaminated areas with a corro-
sion inhibiting paint.
TO TEST AND CHARGE
(1) Using a hydrometer, test the specific gravity
of the battery electrolyte. Refer to the following chart
which shows charge conditi ons for various specific
gravity readings.
1.110-1.130............................... Fully discharged
1.140-1.160..............................Nearly discharged
1.170-1.190 ........................... Approximately one
quarter charged
1.200-1.220..................................... Half charged
1.230-1.250......................... Approximately three
quarters charged
1.250-1.280..................................... Fully charged
These readings are for electrolyte at a temperature
of 20 deg C. For every 10 deg above 20 deg C, add
0.007. For every 10 deg below 20 deg C, subtract
0.007.
NOTE: An accurate specific gravity reading
cannot be obtained if distilled water has
recently been added to the electrolyte. If the
electrolyte level is below the battery plates,
replenish with distilled water and charge the
battery before testing the specific gravity.
(2) If a low state of charge is indicated, or if the
specific gravity readings vary more than 0.030 be-
tween cells, the battery s hould be 'charged, using a
battery charger, with attention to the following points:
(a) Disconnect the negati ve and positive battery
terminals.
Cleaning the battery terminals using a battery post
cleaner.
Page 196 of 238
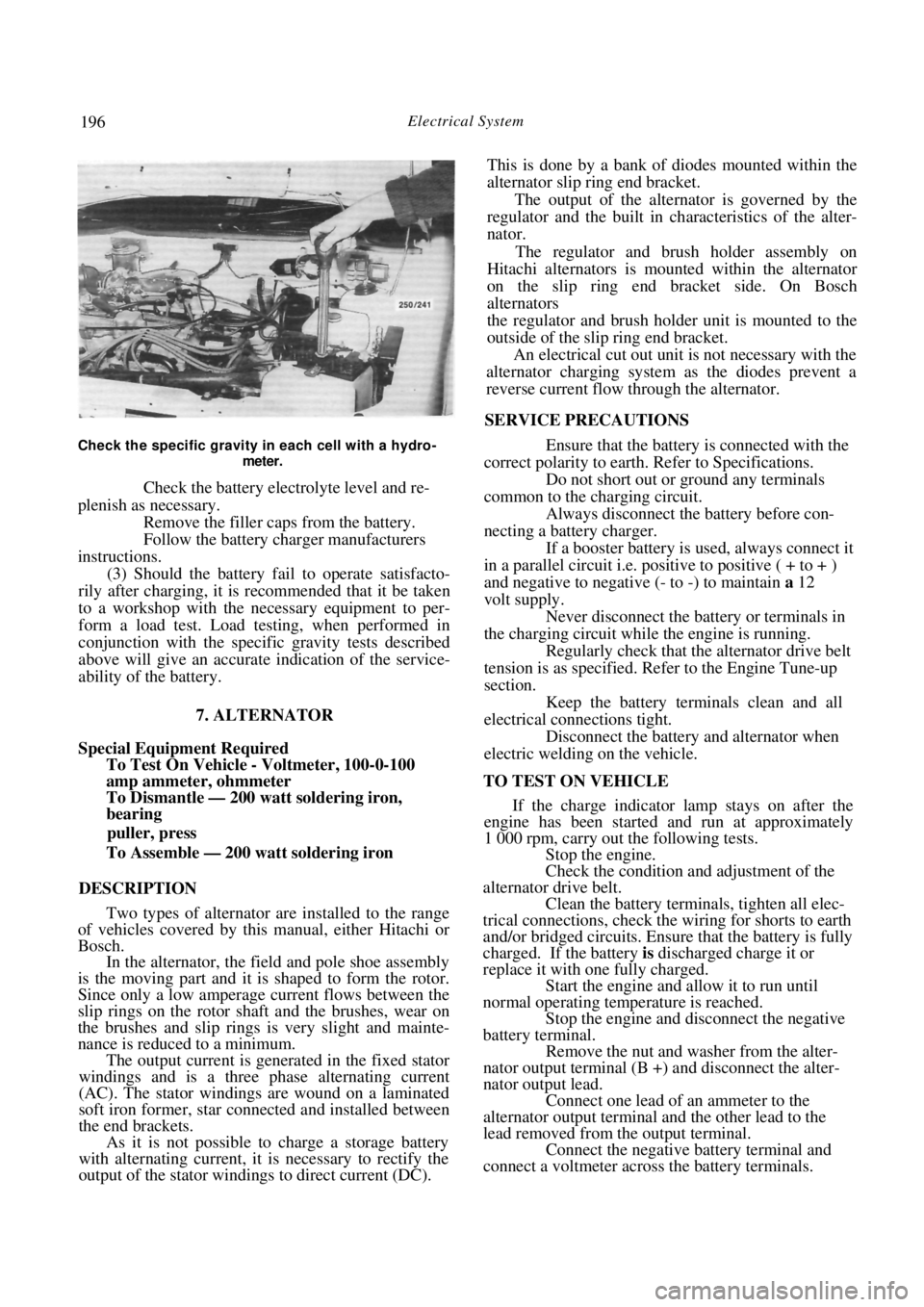
196 Electrical System
Check the specific gravity in each cell with a hydro-
meter.
Check the battery electrolyte level and re-
plenish as necessary. Remove the filler cap s from the battery.
Follow the battery charger manufacturers
instructions. (3) Should the battery fail to operate satisfacto-
rily after charging, it is recommended that it be taken
to a workshop with the necessary equipment to per-
form a load test. Load testing, when performed in
conjunction with the specific gravity tests described
above will give an accurate indication of the service-
ability of the battery.
7. ALTERNATOR
Special Equipment Required
To Test On Vehicle - Voltmeter, 100-0-100
amp ammeter, ohmmeter
To Dismantle — 200 watt soldering iron,
bearing
puller, press
To Assemble — 200 watt soldering iron
DESCRIPTION
Two types of alternator are installed to the range
of vehicles covered by this manual, either Hitachi or
Bosch. In the alternator, the field and pole shoe assembly
is the moving part and it is shaped to form the rotor.
Since only a low amperage current flows between the
slip rings on the rotor shaft and the brushes, wear on
the brushes and slip rings is very slight and mainte-
nance is reduced to a minimum. The output current is generated in the fixed stator
windings and is a three phase alternating current
(AC). The stator windings are wound on a laminated
soft iron former, star connected and installed between
the end brackets. As it is not possible to charge a storage battery
with alternating current, it is necessary to rectify the
output of the stator windings to direct current (DC). This is done by a bank of diodes mounted within the
alternator slip ring end bracket.
The output of the alternator is governed by the
regulator and the built in ch aracteristics of the alter-
nator.
The regulator and brush holder assembly on
Hitachi alternators is mounted within the alternator
on the slip ring end bracket side. On Bosch
alternators
the regulator and brush holder unit is mounted to the
outside of the slip ring end bracket. An electrical cut out unit is not necessary with the
alternator charging system as the diodes prevent a
reverse current flow through the alternator.
SERVICE PRECAUTIONS
Ensure that the battery is connected with the
correct polarity to earth. Refer to Specifications.
Do not short out or ground any terminals
common to the charging circuit. Always disconnect the battery before con-
necting a battery charger.
If a booster battery is used, always connect it
in a parallel circuit i.e. positive to positive ( + to + )
and negative to negative (- to -) to maintain a 12
volt supply. Never disconnect the battery or terminals in
the charging circuit while the engine is running. Regularly check that the alternator drive belt
tension is as specified. Refer to the Engine Tune-up
section.
Keep the battery terminals clean and all
electrical connections tight. Disconnect the battery and alternator when
electric welding on the vehicle.
TO TEST ON VEHICLE If the charge indicator lamp stays on after the
engine has been started and run at approximately
1 000 rpm, carry out the following tests. Stop the engine.
Check the condition and adjustment of the
alternator drive belt. Clean the battery terminals, tighten all elec-
trical connections, check the wiring for shorts to earth
and/or bridged circuits. Ensure that the battery is fully
charged. If the battery is discharged charge it or
replace it with one fully charged. Start the engine and allow it to run until
normal operating temperature is reached.
Stop the engine and disconnect the negative
battery terminal.
Remove the nut and washer from the alter-
nator output terminal (B +) and disconnect the alter-
nator output lead. Connect one lead of an ammeter to the
alternator output terminal and the other lead to the
lead removed from the output terminal. Connect the negative battery terminal and
connect a voltmeter across the battery terminals.
Page 197 of 238
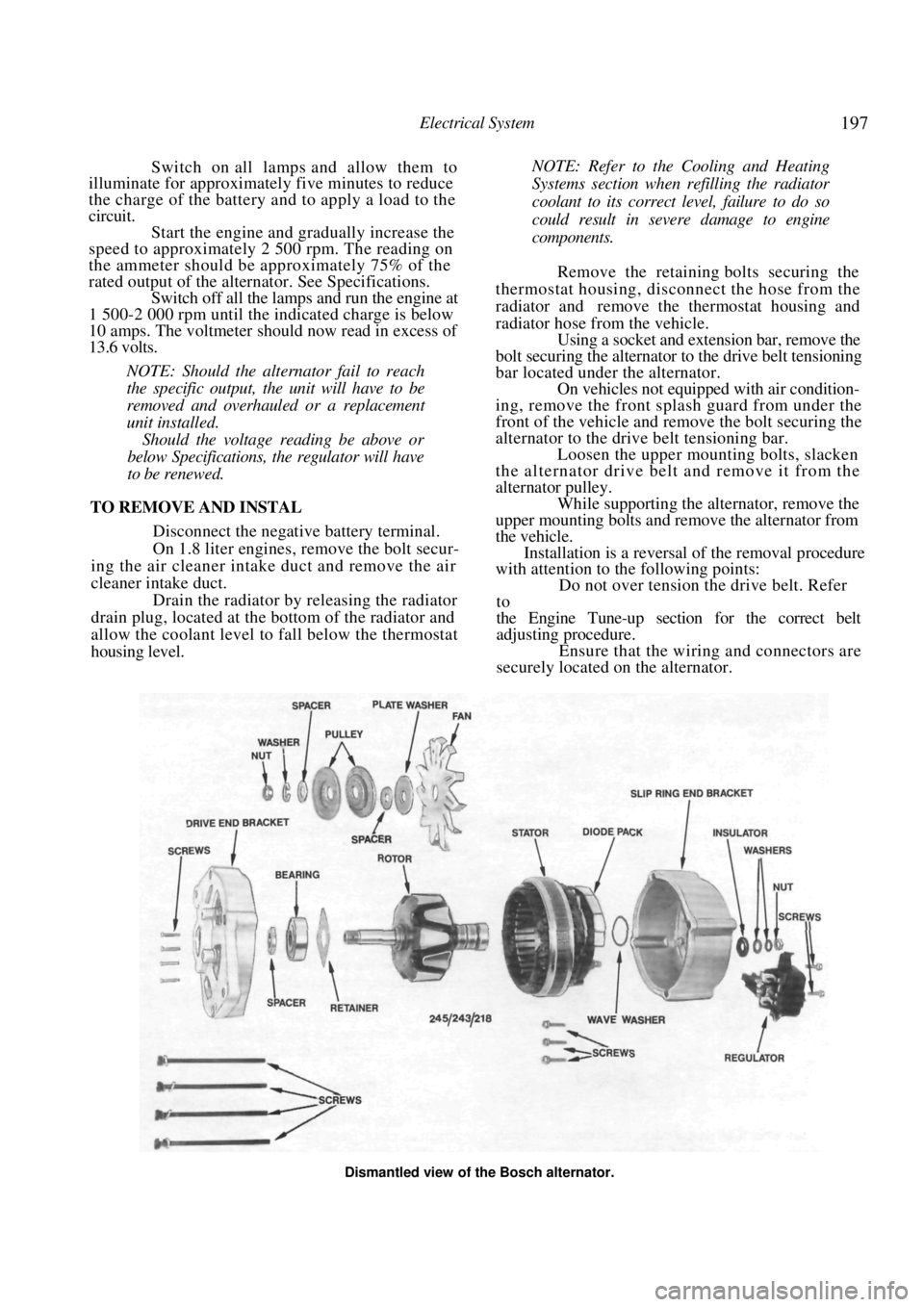
Electrical System 197
Switch on all lamps and allow them to
illuminate for approximately five minutes to reduce
the charge of the battery and to apply a load to the
circuit.
Start the engine and gradually increase the
speed to approximately 2 500 rpm. The reading on
the ammeter should be approximately 75% of the
rated output of the altern ator. See Specifications.
Switch off all the lamps and run the engine at
1 500-2 000 rpm until the indicated charge is below
10 amps. The voltmeter should now read in excess of
13.6 volts.
NOTE: Should the alternator fail to reach
the specific output, the unit will have to be
removed and overhauled or a replacement
unit installed.
Should the voltage reading be above or
below Specifications, the regulator will have
to be renewed.
TO REMOVE AND INSTAL
Disconnect the negative battery terminal.
On 1.8 liter engines, remove the bolt secur-
ing the air cleaner intake duct and remove the air
cleaner intake duct. Drain the radiator by releasing the radiator
drain plug, located at the bottom of the radiator and
allow the coolant level to fall below the thermostat
housing level. NOTE: Refer to the Cooling and Heating
Systems section when refilling the radiator
coolant to its correct l
evel, failure to do so
could result in severe damage to engine
components.
Remove the retaining bolts securing the
thermostat housing, disconnect the hose from the
radiator and remove the thermostat housing and
radiator hose from the vehicle. Using a socket and extension bar, remove the
bolt securing the alternator to the drive belt tensioning
bar located under the alternator. On vehicles not equipped with air condition-
ing, remove the front splash guard from under the
front of the vehicle and remove the bolt securing the
alternator to the drive belt tensioning bar. Loosen the upper mounting bolts, slacken
the alternator drive belt and remove it from the
alternator pulley.
While supporting the alternator, remove the
upper mounting bolts and remove the alternator from
the vehicle. Installation is a reversal of the removal procedure
with attention to the following points:
Do not over tension the drive belt. Refer
to
the Engine Tune-up section for the correct belt
adjusting procedure. Ensure that the wiring and connectors are
securely located on the alternator.
Dismantled view of the Bosch alternator.
Page 198 of 238
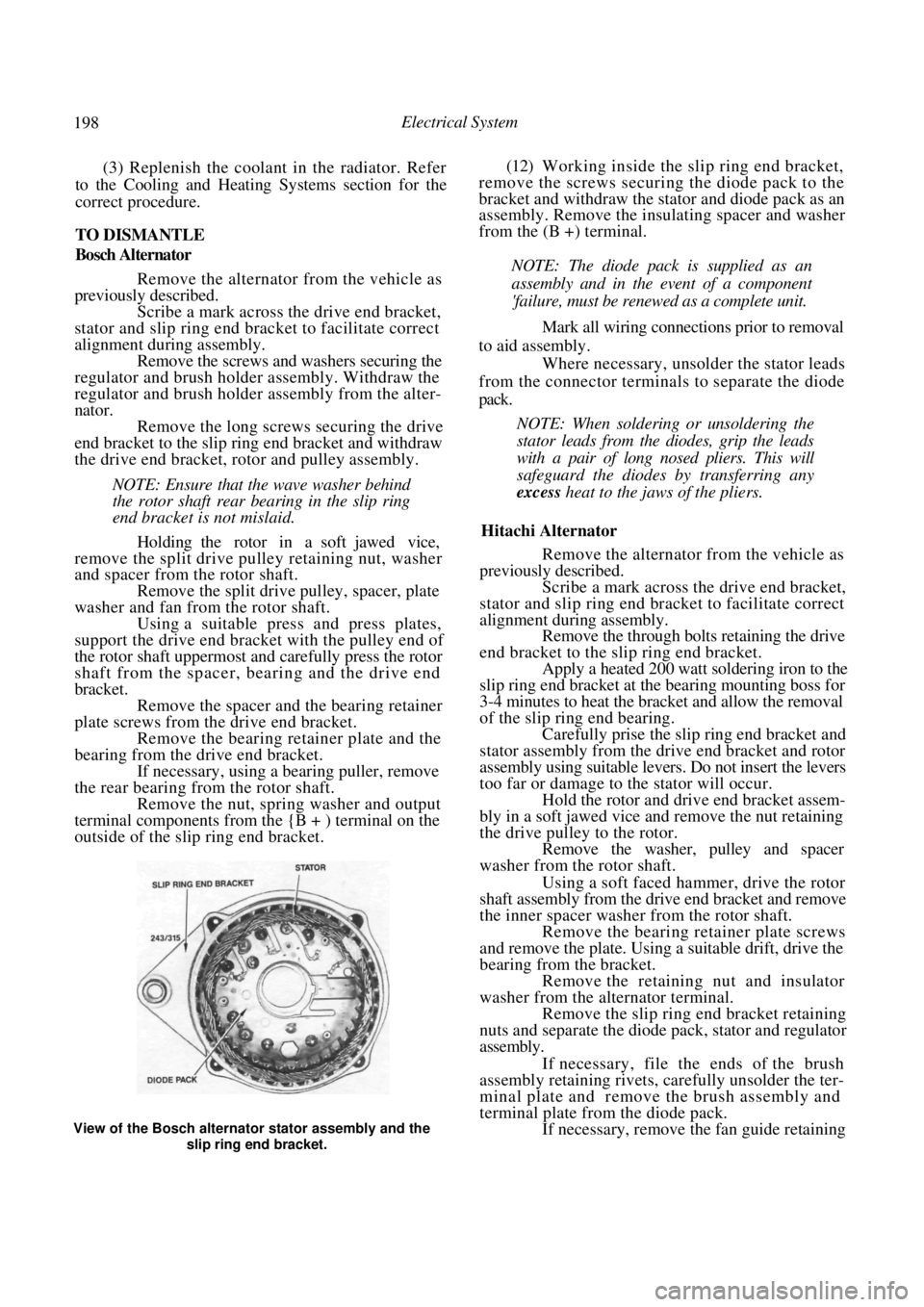
198 Electrical System
(3) Replenish the coolant in the radiator. Refer
to the Cooling and Heating Systems section for the
correct procedure.
TO DISMANTLE
Bosch Alternator
Remove the alternator from the vehicle as
previously described.
Scribe a mark across the drive end bracket,
stator and slip ring end bracket to facilitate correct
alignment during assembly. Remove the screws and washers securing the
regulator and brush holder assembly. Withdraw the
regulator and brush holder assembly from the alter-
nator. Remove the long screws securing the drive
end bracket to the slip ring end bracket and withdraw
the drive end bracket, rotor and pulley assembly.
NOTE: Ensure that the wave washer behind
the rotor shaft rear bearing in the slip ring
end bracket is not mislaid.
Holding the rotor in a soft jawed vice,
remove the split drive pulley retaining nut, washer
and spacer from the rotor shaft. Remove the split driv e pulley, spacer, plate
washer and fan from the rotor shaft. Using a suitable pres s and press plates,
support the drive end bracket with the pulley end of
the rotor shaft uppermost a nd carefully press the rotor
shaft from the spacer, bearing and the drive end
bracket.
Remove the spacer and the bearing retainer
plate screws from the drive end bracket. Remove the bearing retainer plate and the
bearing from the drive end bracket. If necessary, using a bearing puller, remove
the rear bearing from the rotor shaft. Remove the nut, spring washer and output
terminal components from the {B + ) terminal on the
outside of the slip ring end bracket.
(12) Working inside the slip ring end bracket,
remove the screws securing the diode pack to the
bracket and withdraw the stator and diode pack as an
assembly. Remove the insulating spacer and washer
from the (B +) terminal.
NOTE: The diode pack is supplied as an
assembly and in the event of a component
'failure, must be renewed as a complete unit.
Mark all wiring connections prior to removal
to aid assembly. Where necessary, unsolder the stator leads
from the connector terminals to separate the diode
pack.
NOTE: When soldering or unsoldering the
stator leads from the diodes, grip the leads
with a pair of long nosed pliers. This will
safeguard the diodes by transferring any
excess heat to the jaws of the pliers.
Hitachi Alternator
Remove the alternator from the vehicle as
previously described.
Scribe a mark across the drive end bracket,
stator and slip ring end bracket to facilitate correct
alignment during assembly. Remove the through bolts retaining the drive
end bracket to the slip ring end bracket. Apply a heated 200 watt soldering iron to the
slip ring end bracket at the bearing mounting boss for
3-4 minutes to heat the bracket and allow the removal
of the slip ring end bearing. Carefully prise the slip ring end bracket and
stator assembly from the drive end bracket and rotor
assembly using suitable levers. Do not insert the levers
too far or damage to the stator will occur.
Hold the rotor and driv e end bracket assem-
bly in a soft jawed vice and remove the nut retaining
the drive pulley to the rotor. Remove the washer, pulley and spacer
washer from the rotor shaft.
Using a soft faced hammer, drive the rotor
shaft assembly from the drive end bracket and remove
the inner spacer washer from the rotor shaft.
Remove the bearing retainer plate screws
and remove the plate. Using a suitable drift, drive the
bearing from the bracket. Remove the retaining nut and insulator
washer from the alternator terminal. Remove the slip ring end bracket retaining
nuts and separate the diode pack, stator and regulator
assembly.
If necessary, file the ends of the brush
assembly retaining rivets, caref ully unsolder the ter-
minal plate and remove the brush assembly and
terminal plate from the diode pack. If necessary, remove the fan guide retaining
View of the Bosch alternator stator assembly and the
slip ring end bracket.
Page 199 of 238
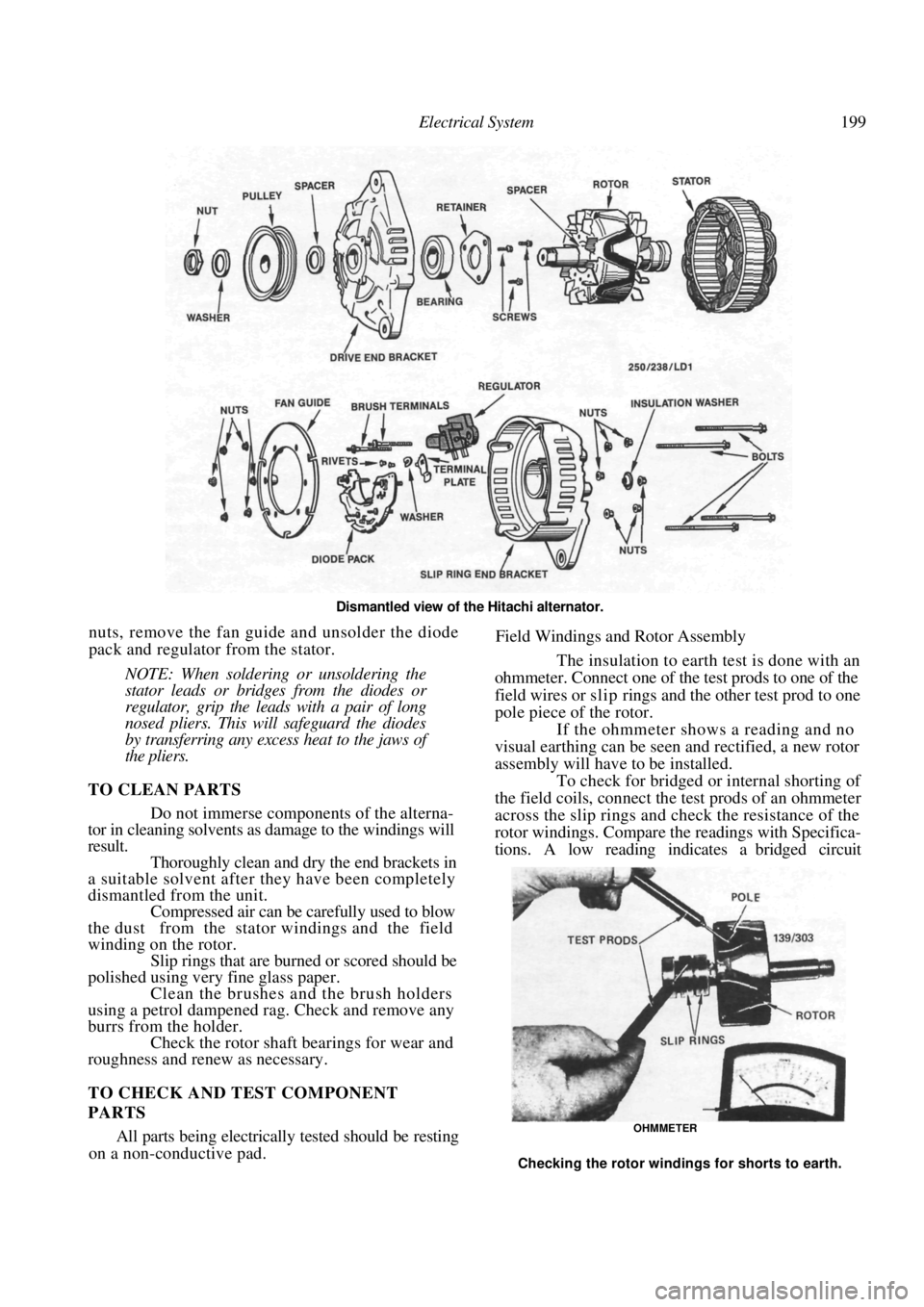
Electrical System 199
Dismantled view of the Hitachi alternator.
nuts, remove the fan guide and unsolder the diode
pack and regulator from the stator.
NOTE: When soldering or unsoldering the
stator leads or bridges from the diodes or
regulator, grip the leads with a pair of long
nosed pliers. This will safeguard the diodes
by transferring any excess heat to the jaws of
the pliers.
TO CLEAN PARTS
Do not immerse components of the alterna-
tor in cleaning solvents as damage to the windings will
result. Thoroughly clean and dry the end brackets in
a suitable solvent after they have been completely
dismantled from the unit. Compressed air can be carefully used to blow
the dust from the stator windings and the field
winding on the rotor. Slip rings that are burned or scored should be
polished using very fine glass paper. Clean the brushes and the brush holders
using a petrol dampened rag. Check and remove any
burrs from the holder. Check the rotor shaft bearings for wear and
roughness and renew as necessary.
TO CHECK AND TEST COMPONENT
PARTS
All parts being electrically tested should be resting
on a non-conductive pad.
Field Windings and Rotor Assembly
The insulation to earth test is done with an
ohmmeter. Connect one of the test prods to one of the
field wires or s l i p rings and the other test prod to one
pole piece of the rotor. If the ohmmeter shows a reading and no
visual earthing can be seen and rectified, a new rotor
assembly will have to be installed. To check for bridged or internal shorting of
the field coils, connect the te st prods of an ohmmeter
across the slip rings and check the resistance of the
rotor windings. Compare the readings with Specifica-
tions. A low reading i ndicates a bridged circuit
OHMMETER
Checking the rotor windings for shorts to earth.
Page 200 of 238
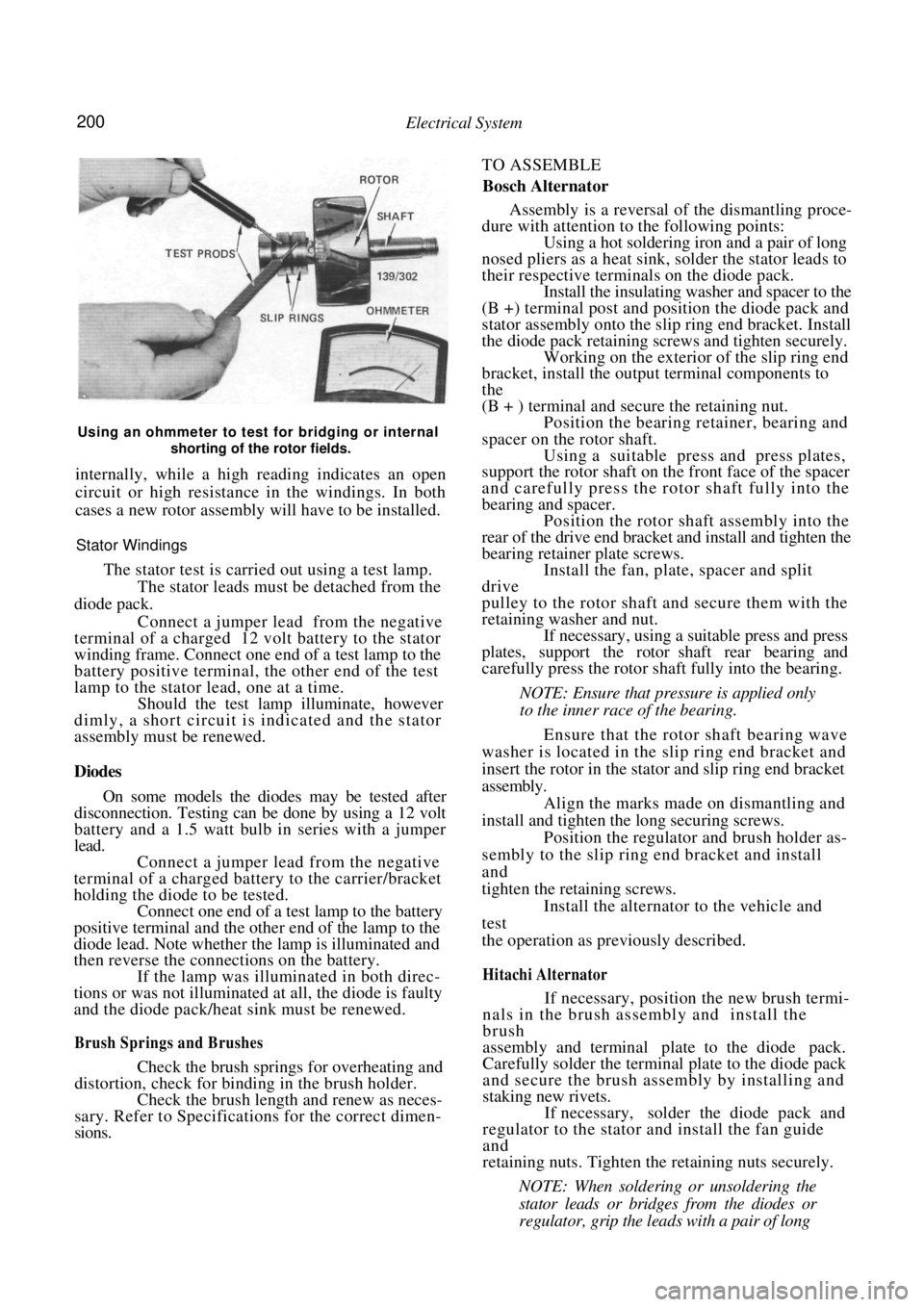
200 Electrical System
Using an ohmmeter to test for bridging or internal shorting of the rotor fields.
internally, while a high reading indicates an open
circuit or high resistance in the windings. In both
cases a new rotor assembly will have to be installed.
Stator Windings
The stator test is carried out using a test lamp.
The stator leads must be detached from the
diode pack.
Connect a jumper lead from the negative
terminal of a charged 12 volt battery to the stator
winding frame. Connect one en d of a test lamp to the
battery positive terminal, the other end of the test
lamp to the stator lead, one at a time. Should the test lamp illuminate, however
dimly, a short circuit is indicated and the stator
assembly must be renewed.
Diodes
On some models the diod es may be tested after
disconnection. Testing can be done by using a 12 volt
battery and a 1.5 watt bulb in series with a jumper
lead.
Connect a jumper lead from the negative
terminal of a charged battery to the carrier/bracket
holding the diode to be tested. Connect one end of a test lamp to the battery
positive terminal and the other end of the lamp to the
diode lead. Note whether the lamp is illuminated and
then reverse the connections on the battery. If the lamp was illuminated in both direc-
tions or was not illuminated at all, the diode is faulty
and the diode pack/heat sink must be renewed.
Brush Springs and Brushes
Check the brush spring s for overheating and
distortion, check for binding in the brush holder.
Check the brush length and renew as neces-
sary. Refer to Specifications for the correct dimen-
sions. TO ASSEMBLE
Bosch Alternator
Assembly is a reversal of the dismantling proce-
dure with attention to the following points:
Using a hot soldering iron and a pair of long
nosed pliers as a heat sink, solder the stator leads to
their respective terminals on the diode pack. Install the insulating washer and spacer to the
(B +) terminal post and position the diode pack and
stator assembly onto the slip ring end bracket. Install
the diode pack retaining screws and tighten securely. Working on the exterior of the slip ring end
bracket, install the output terminal components to
the
(B + ) terminal and secure the retaining nut.
Position the bearing retainer, bearing and
spacer on the rotor shaft. Using a suitable press and press plates,
support the rotor sh aft on the front face of the spacer
and carefully press the rotor shaft fully into the
bearing and spacer. Position the rotor shaft assembly into the
rear of the drive end bracket and install and tighten the
bearing retainer plate screws. Install the fan, plate, spacer and split
drive
pulley to the rotor shaft and secure them with the
retaining washer and nut. If necessary, using a suitable press and press
plates, support the rotor shaft rear bearing and
carefully press the rotor shaft fully into the bearing.
NOTE: Ensure that pressure is applied only
to the inner race of the bearing.
Ensure that the rotor shaft bearing wave
washer is located in the slip ring end bracket and
insert the rotor in the stator and slip ring end bracket
assembly. Align the marks made on dismantling and
install and tighten the long securing screws.
Position the regulator and brush holder as-
sembly to the slip ring end bracket and install
and
tighten the retaining screws. Install the alternator to the vehicle and
test
the operation as prev iously described.
Hitachi Alternator
If necessary, position the new brush termi-
nals in the brush assembly and install the
brush
assembly and terminal plate to the diode pack.
Carefully solder the terminal plate to the diode pack
and secure the brush assembly by installing and
staking new rivets.
If necessary, solder the diode pack and
regulator to the stator and install the fan guide
and
retaining nuts. Tighten the retaining nuts securely.
NOTE: When soldering or unsoldering the
stator leads or bridges from the diodes or
regulator, grip the leads with a pair of long