OPEL GT-R 1973 Service Manual
Manufacturer: OPEL, Model Year: 1973, Model line: GT-R, Model: OPEL GT-R 1973Pages: 625, PDF Size: 17.22 MB
Page 231 of 625
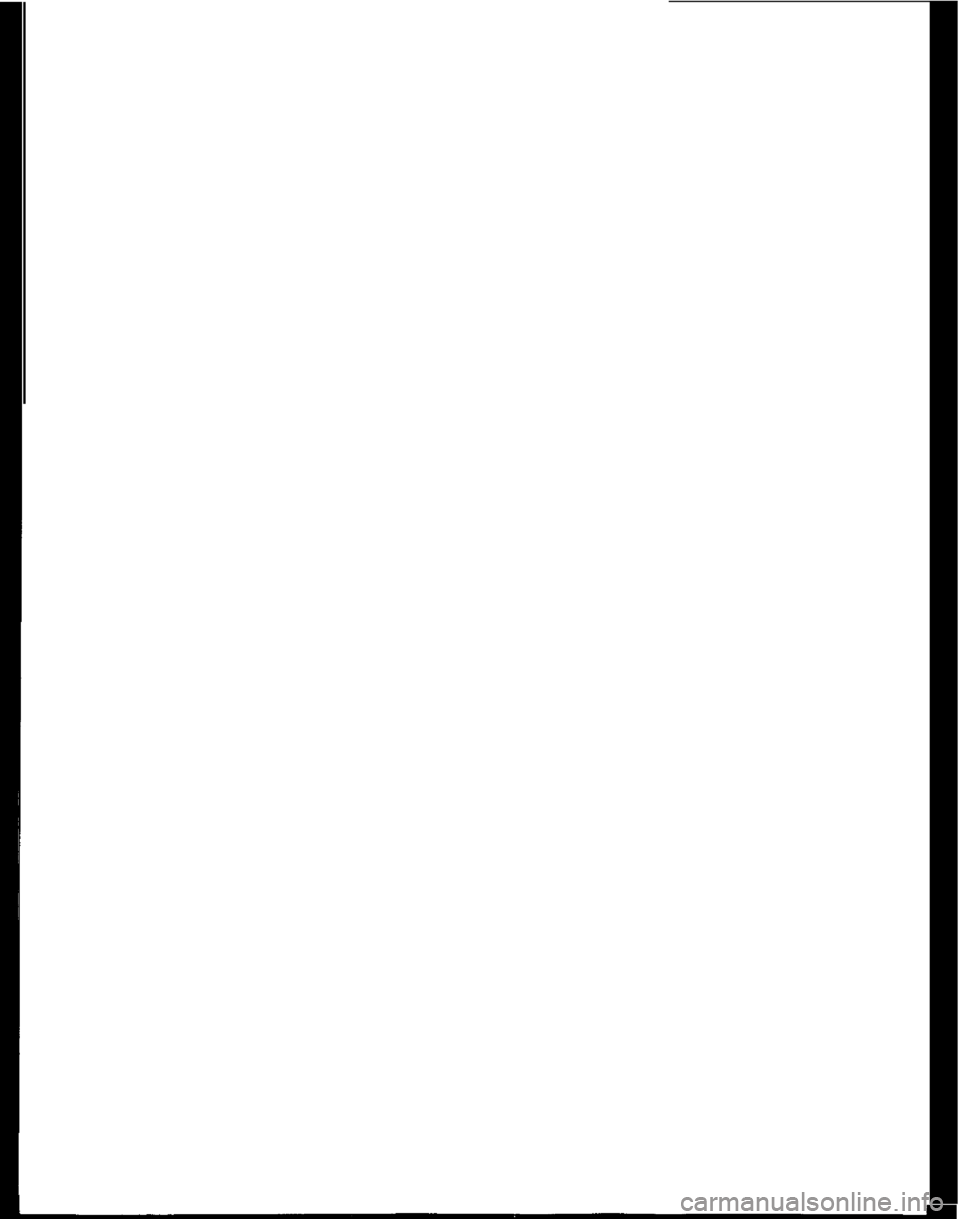
Page 232 of 625

GROUP 4
PROPELLER SHAFT
AND DIFFERENTIALTitlePage No.Propeller Shaft and
CentralJoint. . . . . . . . . . . . . . .4A-2
RearAxle. . . . . . . . . . . . . . . . . . . .4B-7
Page 233 of 625
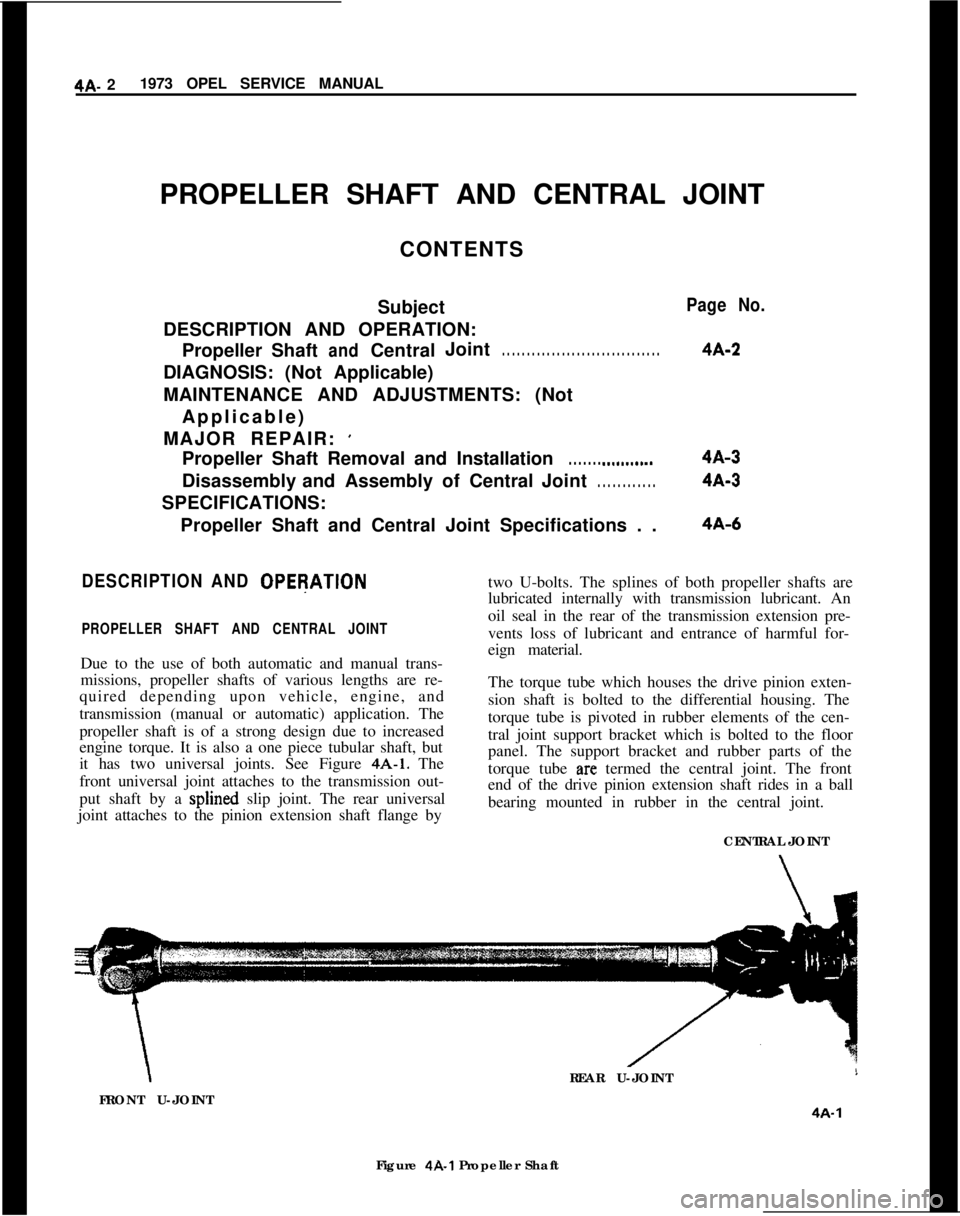
4A- 21973 OPEL SERVICE MANUAL
PROPELLER SHAFT AND CENTRAL JOINT
CONTENTS
Subject
DESCRIPTION AND OPERATION:
PropellerShaftandCentralJoint. . . . . . . . . . . . . . . . . . . . . . . . . . . . . . . .DIAGNOSIS: (Not Applicable)
MAINTENANCE AND ADJUSTMENTS: (Not
Applicable)
MAJOR REPAIR:
’Propeller Shaft Removal andInstallation
. . . . . . . ..-....Disassembly andAssembly of CentralJoint
. . . . . . . . . . . .SPECIFICATIONS:
Propeller Shaft and Central Joint Specifications . .
DESCRIPTION AND OPEqATlON
PROPELLER SHAFT AND CENTRAL JOINTDue to the use of both automatic and manual trans-
missions, propeller shafts of various lengths are re-
quired depending upon vehicle, engine, and
transmission (manual or automatic) application. The
propeller shaft is of a strong design due to increased
engine torque. It is also a one piece tubular shaft, but
it has two universal joints. See Figure 4A-1. The
front universal joint attaches to the transmission out-
put shaft by a splined slip joint. The rear universal
joint attaches to the pinion extension shaft flange by
Page No.
4A-2
4A-3
4A-3
4A-6two U-bolts. The splines of both propeller shafts are
lubricated internally with transmission lubricant. An
oil seal in the rear of the transmission extension pre-
vents loss of lubricant and entrance of harmful for-
eign material.
The torque tube which houses the drive pinion exten-
sion shaft is bolted to the differential housing. The
torque tube is pivoted in rubber elements of the cen-
tral joint support bracket which is bolted to the floor
panel. The support bracket and rubber parts of the
torque tube
arc termed the central joint. The front
end of the drive pinion extension shaft rides in a ball
bearing mounted in rubber in the central joint.
CENTRAL JOINT\REAR U-JOINT
FRONT U-JOINT
4A-1Figure 4R1 Propeller Shaft
Page 234 of 625
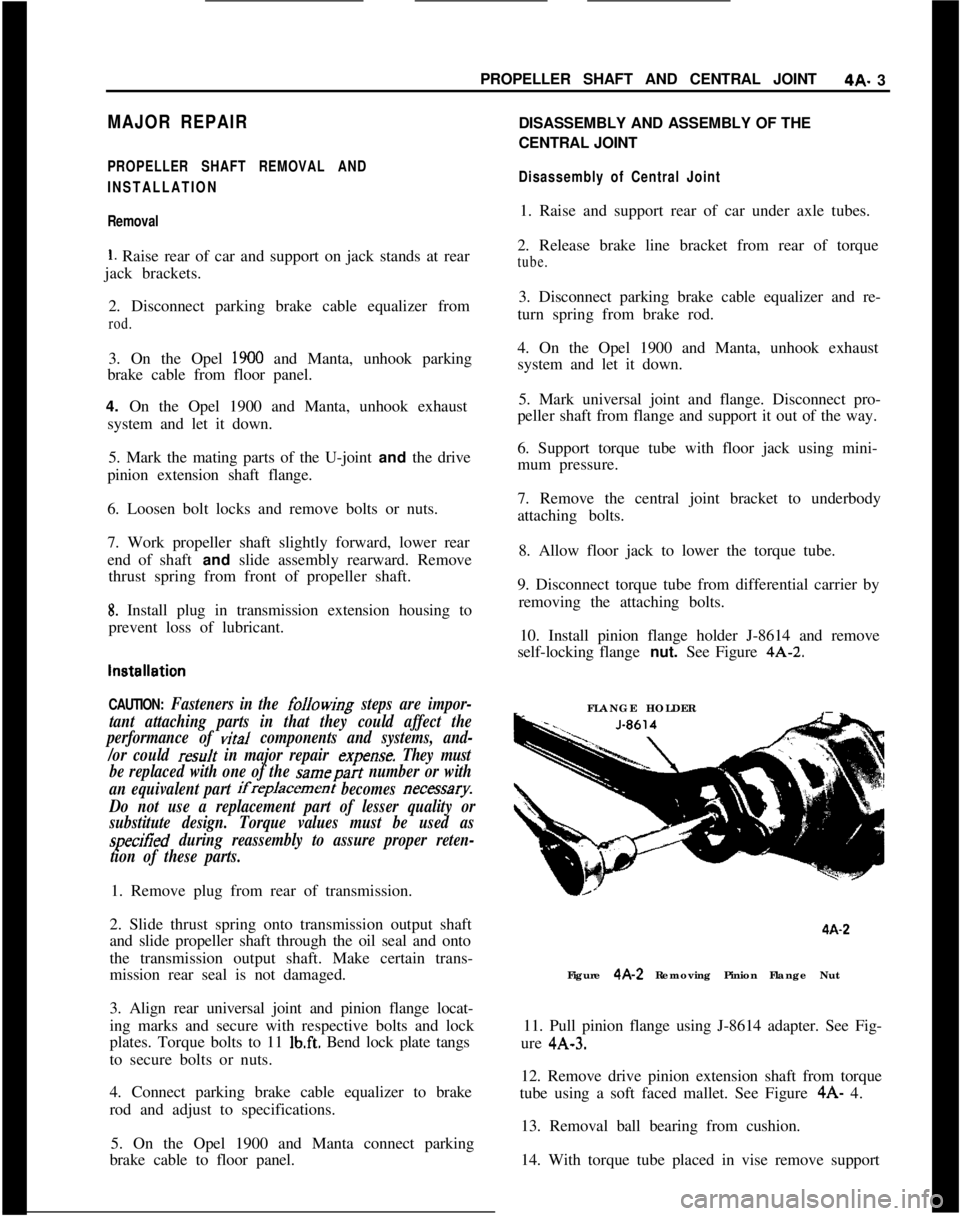
PROPELLER SHAFT AND CENTRAL JOINT4A- 3MAJOR REPAIR
PROPELLER SHAFT REMOVAL AND
INSTALLATION
Removal
1. Raise rear of car and support on jack stands at rear
jack brackets.
2. Disconnect parking brake cable equalizer from
rod.3. On the Opel
1900 and Manta, unhook parking
brake cable from floor panel.
4. On the Opel 1900 and Manta, unhook exhaust
system and let it down.
5. Mark the mating parts of the U-joint and the drive
pinion extension shaft flange.
6. Loosen bolt locks and remove bolts or nuts.
7. Work propeller shaft slightly forward, lower rear
end of shaft and slide assembly rearward. Remove
thrust spring from front of propeller shaft.
S. Install plug in transmission extension housing to
prevent loss of lubricant.
installation
CAUTION:
Fasteners in the foJlowing steps are impor-
tant attaching parts in that they could affect the
performance of
vital components and systems, and-
/or could
result in major repair expense. They must
be replaced with one of the
samepart number or with
an equivalent part
ifreplacement becomes oecessary.
Do not use a replacement part of lesser quality or
substitute design. Torque values must be used as
specirid during reassembly to assure proper reten-
tion of these parts.1. Remove plug from rear of transmission.
2. Slide thrust spring onto transmission output shaft
and slide propeller shaft through the oil seal and onto
the transmission output shaft. Make certain trans-
mission rear seal is not damaged.
3. Align rear universal joint and pinion flange locat-
ing marks and secure with respective bolts and lock
plates. Torque bolts to 11
lb.ft. Bend lock plate tangs
to secure bolts or nuts.
4. Connect parking brake cable equalizer to brake
rod and adjust to specifications.
5. On the Opel 1900 and Manta connect parking
brake cable to floor panel.DISASSEMBLY AND ASSEMBLY OF THE
CENTRAL JOINT
Disassembly of Central Joint1. Raise and support rear of car under axle tubes.
2. Release brake line bracket from rear of torque
tube.3. Disconnect parking brake cable equalizer and re-
turn spring from brake rod.
4. On the Opel 1900 and Manta, unhook exhaust
system and let it down.
5. Mark universal joint and flange. Disconnect pro-
peller shaft from flange and support it out of the way.
6. Support torque tube with floor jack using mini-
mum pressure.
7. Remove the central joint bracket to underbody
attaching bolts.
8. Allow floor jack to lower the torque tube.
9. Disconnect torque tube from differential carrier by
removing the attaching bolts.
10. Install pinion flange holder J-8614 and remove
self-locking flange nut. See Figure 4A-2.
FLANGE HOLDER4A-2
Figure 4A-2 Removing Pinion Flange Nut
11. Pull pinion flange using J-8614 adapter. See Fig-
ure 4A-3.
12. Remove drive pinion extension shaft from torque
tube using a soft faced mallet. See Figure 4A- 4.
13. Removal ball bearing from cushion.
14. With torque tube placed in vise remove support
Page 235 of 625
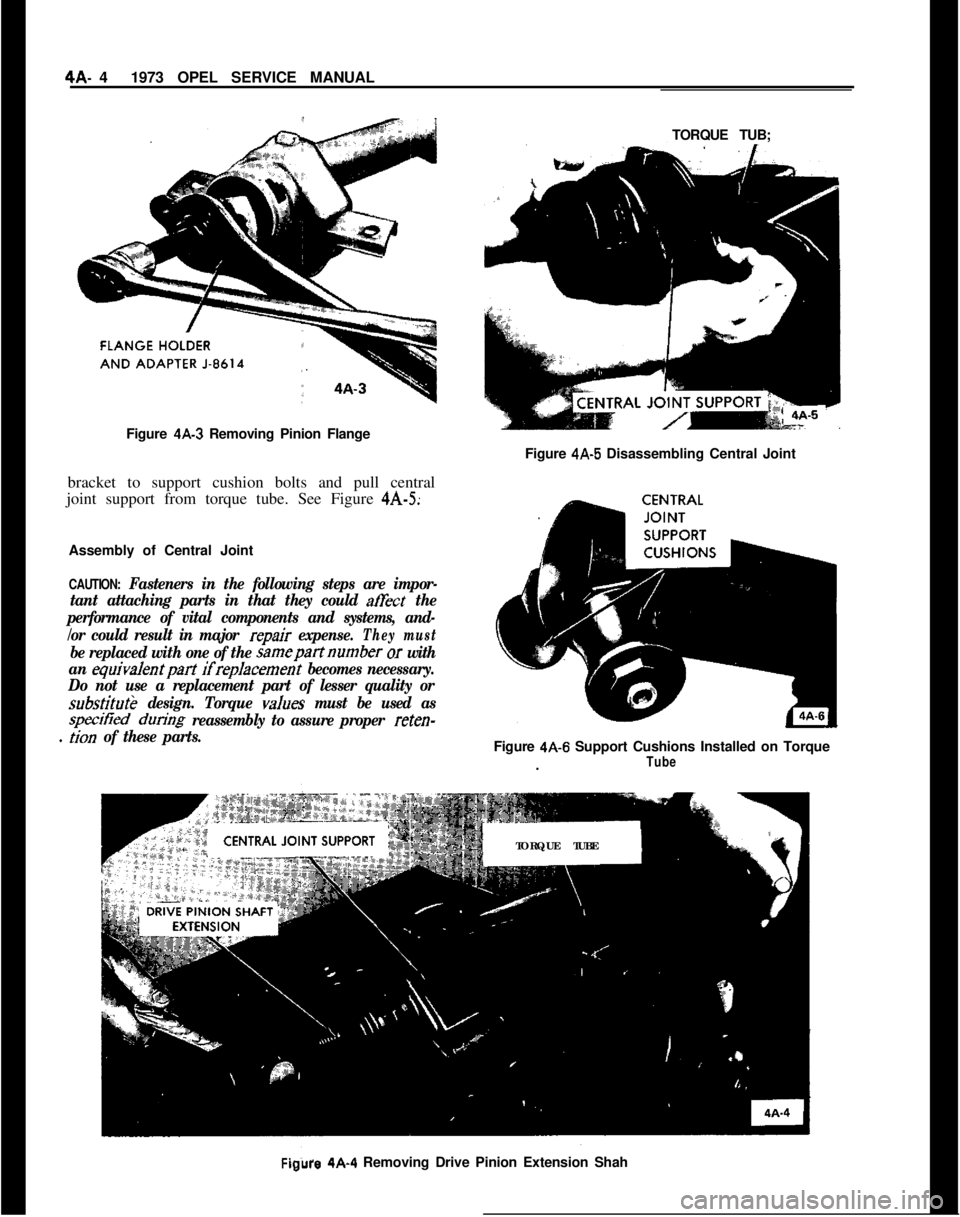
4A- 41973 OPEL SERVICE MANUAL
Figure 4A-3 Removing Pinion Flange
bracket to support cushion bolts and pull central
joint support from torque tube. See Figure 4A-5;
Assembly of Central Joint
CAUTION: Fasteners in the following steps are impor-
tant attaching parts in that they could
ah&t the
performance of vital components and systems, and-
/or could result in major
repair expense.They must
be replaced with one of the samepartnumber or with
an
equivalentpart ifreplacement becomes necessary.
Do not use a replacement part of lesser quality or
substitutk design. Torque vah~es must be used as
specitied dun’ng reassembly to assure proper reten-
. lion of these parts.TORQUE TUB;
Figure
4A-5 Disassembling Central Joint
Figure
4A-6 Support Cushions Installed on Torque
.TubeTORQUE TUBE
Figure 4A-4 Removing Drive Pinion Extension Shah
Page 236 of 625
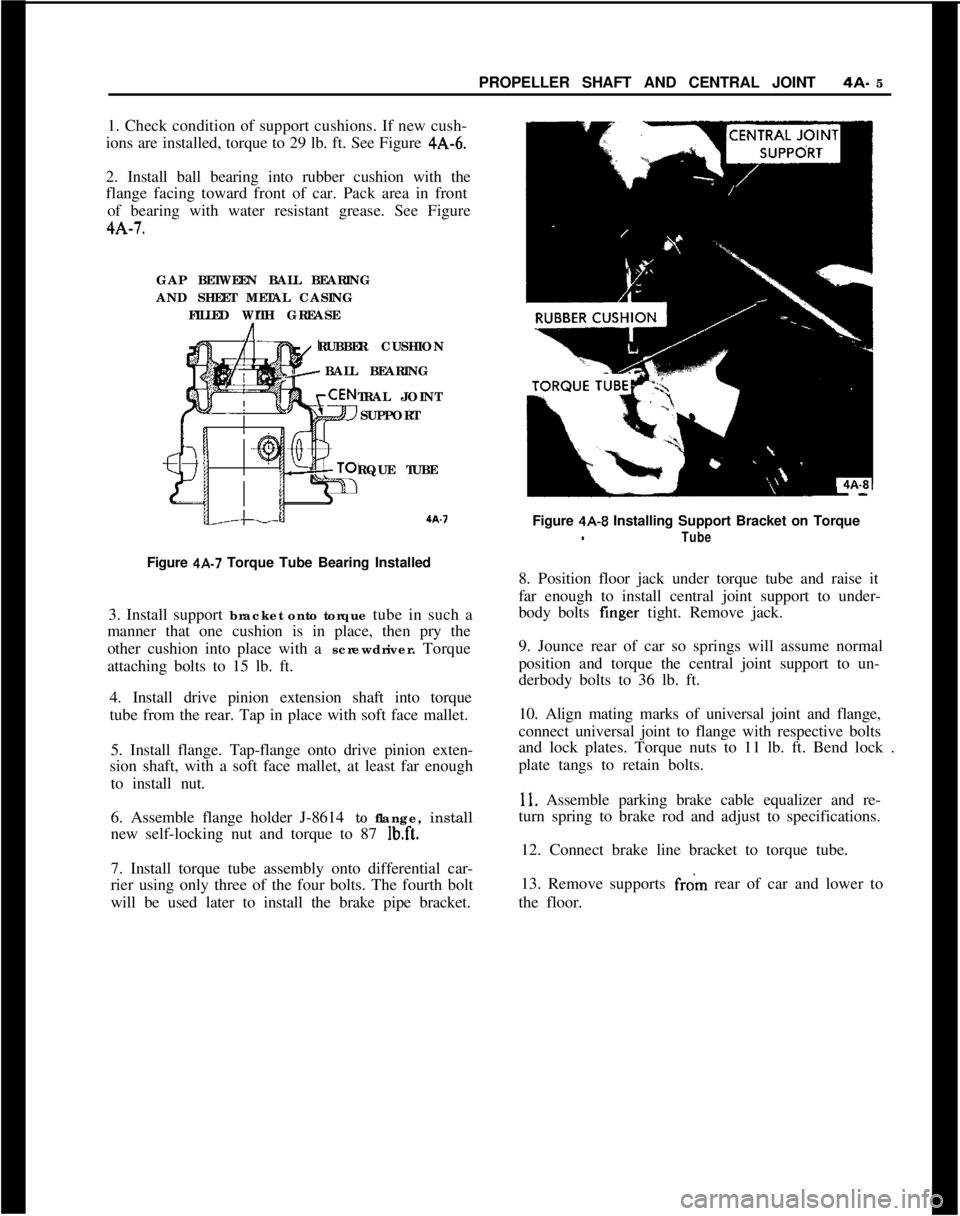
PROPELLER SHAFT AND CENTRAL JOINT4A- 5
1. Check condition of support cushions. If new cush-
ions are installed, torque to 29 lb. ft. See Figure 4A-6.
2. Install ball bearing into rubber cushion with the
flange facing toward front of car. Pack area in front
of bearing with water resistant grease. See Figure4A-7.
GAP BETWEEN BALL BEARING
AND SHEET METAL CASING
FILLED WITH GREASE
RUBBER CUSHION
BALL BEARING
TRAL JOINT
SUPPORT
RQUE TUBEa.7
Figure 4A-7 Torque Tube Bearing Installed
3. Install support bracket onto torque tube in such a
manner that one cushion is in place, then pry the
other cushion into place with a screwdriver. Torque
attaching bolts to 15 lb. ft.
4. Install drive pinion extension shaft into torque
tube from the rear. Tap in place with soft face mallet.
5. Install flange. Tap-flange onto drive pinion exten-
sion shaft, with a soft face mallet, at least far enough
to install nut.
6. Assemble flange holder J-8614 to flange, install
new self-locking nut and torque to 87
lb.ft.7. Install torque tube assembly onto differential car-
rier using only three of the four bolts. The fourth bolt
will be used later to install the brake pipe bracket.Figure
4A-8 Installing Support Bracket on TorquelTube8. Position floor jack under torque tube and raise it
far enough to install central joint support to under-
body bolts finger tight. Remove jack.
9. Jounce rear of car so springs will assume normal
position and torque the central joint support to un-
derbody bolts to 36 lb. ft.
10. Align mating marks of universal joint and flange,
connect universal joint to flange with respective bolts
and lock plates. Torque nuts to 11 lb. ft. Bend lock .
plate tangs to retain bolts.
11. Assemble parking brake cable equalizer and re-
turn spring to brake rod and adjust to specifications.
12. Connect brake line bracket to torque tube.
13. Remove supports
f&n rear of car and lower to
the floor.
Page 237 of 625
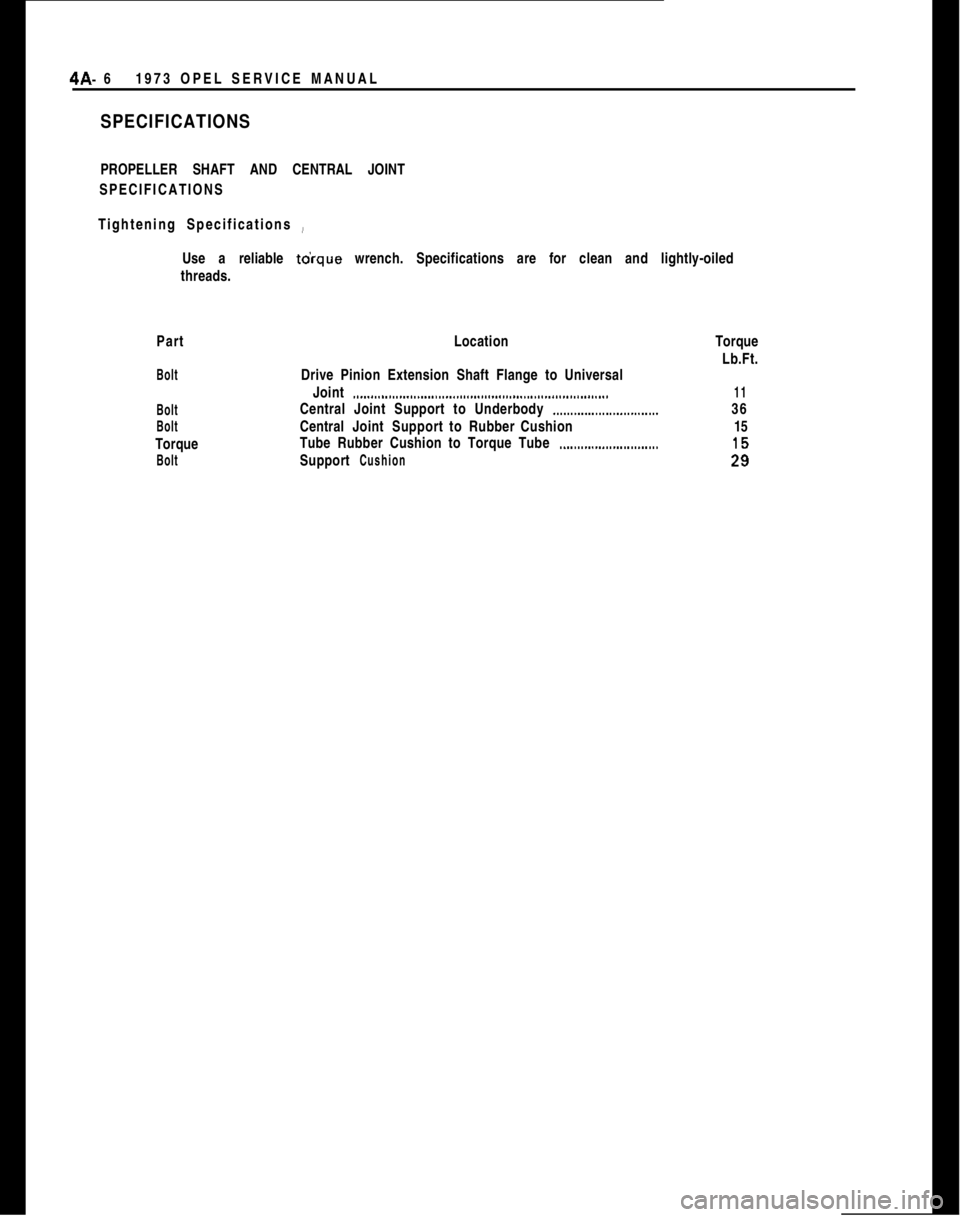
4A- 61973 OPEL SERVICE MANUAL
SPECIFICATIONSPROPELLER SHAFT AND CENTRAL JOINT
SPECIFICATIONS
Tightening Specifications ~
Use a reliable to’rque wrench. Specifications are for clean and lightly-oiled
threads.
Part
Bolt
Bolt
BoltTorque
BoltLocation
Drive Pinion Extension Shaft Flange to Universal
Joint
.._.....................................................................Central Joint Support to Underbody
_.._....._........._..........CentralJointSupport toRubber Cushion
Tube Rubber Cushion to Torque Tube
._.........._...............Support
CushionTorque
Lb.Ft.
1136
15
Page 238 of 625
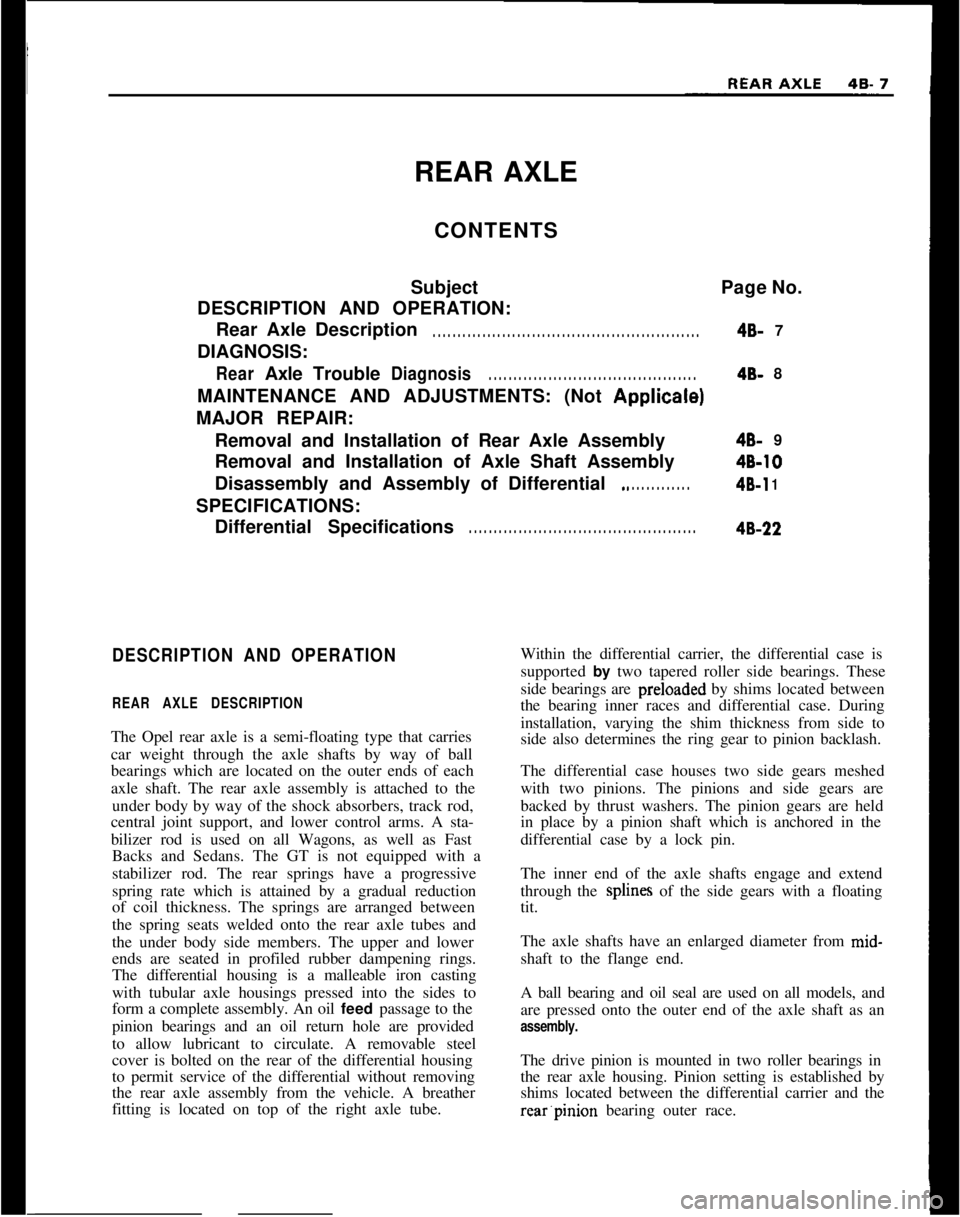
REAR AXLE
CONTENTS
SubjectPage No.
DESCRIPTION AND OPERATION:
Rear Axle Description. . . . . . . . . . . . . . . . . . . . . . . . . . . . . . . . . . . . . . . . . . . . . . . . . . . . . .4B- 7
DIAGNOSIS:
RearAxleTroubleDiagnosis. . . . . . . . . . . . . . . . . . . . . . . . . . . . . . . . . . . . . . . . . .4B- 8
MAINTENANCE AND ADJUSTMENTS: (Not Applicale)
MAJOR REPAIR:
Removal and Installation of Rear Axle Assembly
Removal and Installation of Axle Shaft Assembly
Disassembly and Assembly of Differential
.* . . . . . . . . . . . .SPECIFICATIONS:
DifferentialSpecifications
. . . . . . . . . . . . . . . . . . . . . . . . . . . . . . . . . . . . . . . . . . . . . .4B- 94B-10
48-l 1
4B-22
DESCRIPTION AND OPERATION
REAR AXLE DESCRIPTIONThe Opel rear axle is a semi-floating type that carries
car weight through the axle shafts by way of ball
bearings which are located on the outer ends of each
axle shaft. The rear axle assembly is attached to the
under body by way of the shock absorbers, track rod,
central joint support, and lower control arms. A sta-
bilizer rod is used on all Wagons, as well as Fast
Backs and Sedans. The GT is not equipped with a
stabilizer rod. The rear springs have a progressive
spring rate which is attained by a gradual reduction
of coil thickness. The springs are arranged between
the spring seats welded onto the rear axle tubes and
the under body side members. The upper and lower
ends are seated in profiled rubber dampening rings.
The differential housing is a malleable iron casting
with tubular axle housings pressed into the sides to
form a complete assembly. An oil feed passage to the
pinion bearings and an oil return hole are provided
to allow lubricant to circulate. A removable steel
cover is bolted on the rear of the differential housing
to permit service of the differential without removing
the rear axle assembly from the vehicle. A breather
fitting is located on top of the right axle tube.Within the differential carrier, the differential case is
supported by two tapered roller side bearings. These
side bearings are preloaded by shims located between
the bearing inner races and differential case. During
installation, varying the shim thickness from side to
side also determines the ring gear to pinion backlash.
The differential case houses two side gears meshed
with two pinions. The pinions and side gears are
backed by thrust washers. The pinion gears are held
in place by a pinion shaft which is anchored in the
differential case by a lock pin.
The inner end of the axle shafts engage and extend
through the splines of the side gears with a floating
tit.
The axle shafts have an enlarged diameter from mid-
shaft to the flange end.
A ball bearing and oil seal are used on all models, and
are pressed onto the outer end of the axle shaft as an
assembly.The drive pinion is mounted in two roller bearings in
the rear axle housing. Pinion setting is established by
shims located between the differential carrier and therear’pinion bearing outer race.
Page 239 of 625
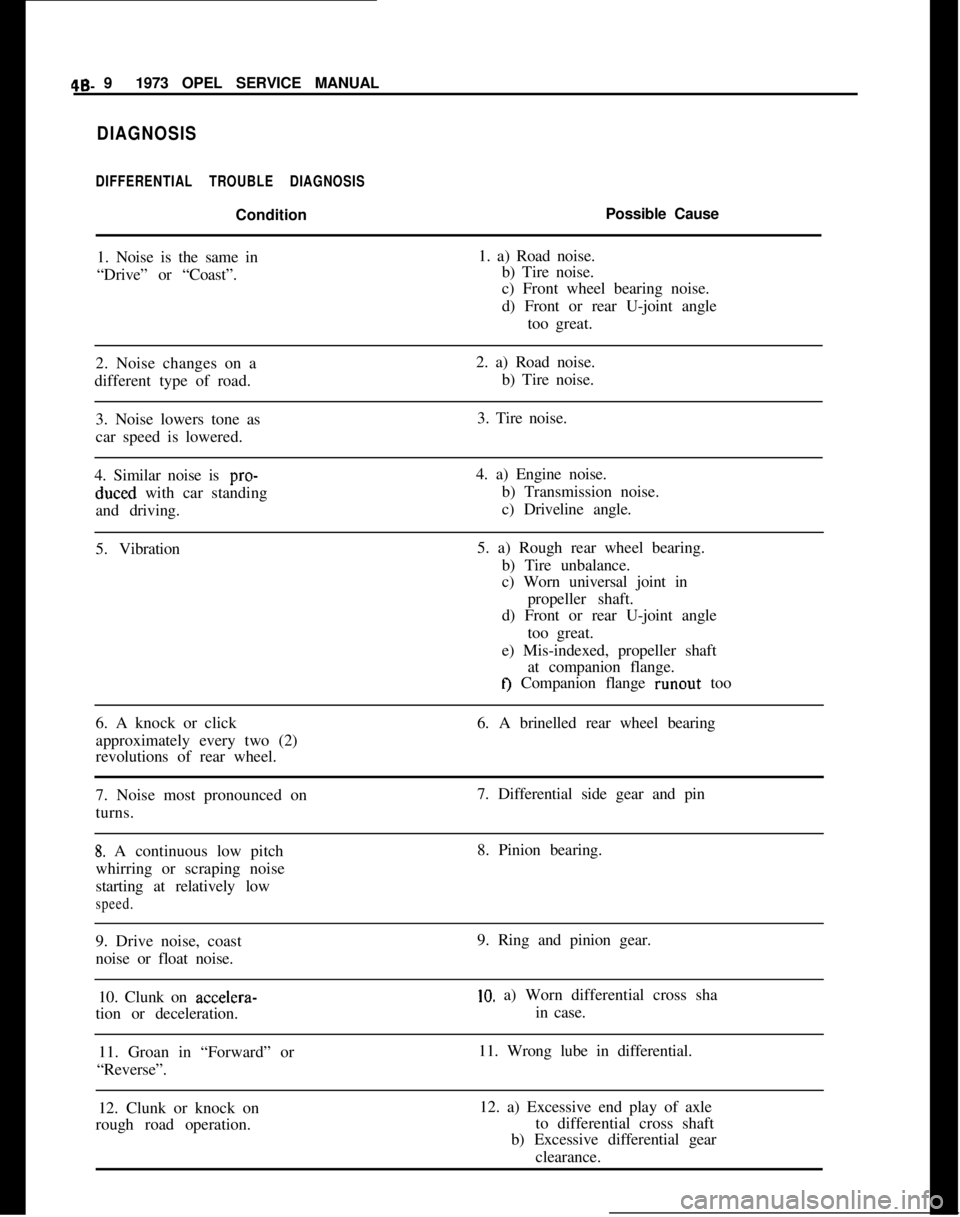
4S- 91973 OPEL SERVICE MANUAL
DIAGNOSIS
DIFFERENTIAL TROUBLE DIAGNOSISConditionPossible Cause
1. Noise is the same in1. a) Road noise.
“Drive” or “Coast”.b) Tire noise.
c) Front wheel bearing noise.
d) Front or rear U-joint angle
too great.
2. Noise changes on a2. a) Road noise.
different type of road.b) Tire noise.
3. Noise lowers tone as3. Tire noise.
car speed is lowered.
4. Similar noise is pro-4. a) Engine noise.duced with car standingb) Transmission noise.
and driving.c) Driveline angle.
5. Vibration5. a) Rough rear wheel bearing.
b) Tire unbalance.
c) Worn universal joint in
propeller shaft.
d) Front or rear U-joint angle
too great.
e) Mis-indexed, propeller shaft
at companion flange.
tJ Companion flange runout too
6. A knock or click6. A brinelled rear wheel bearing
approximately every two (2)
revolutions of rear wheel.
7. Noise most pronounced on7. Differential side gear and pin
turns.
8. A continuous low pitch8. Pinion bearing.
whirring or scraping noise
starting at relatively low
speed.9. Drive noise, coast9. Ring and pinion gear.
noise or float noise.
10. Clunk on accelera-
10. a) Worn differential cross sha
tion or deceleration.in case.
11. Groan in “Forward” or11. Wrong lube in differential.
“Reverse”.
12. Clunk or knock on12. a) Excessive end play of axle
rough road operation.to differential cross shaft
b) Excessive differential gear
clearance.
Page 240 of 625
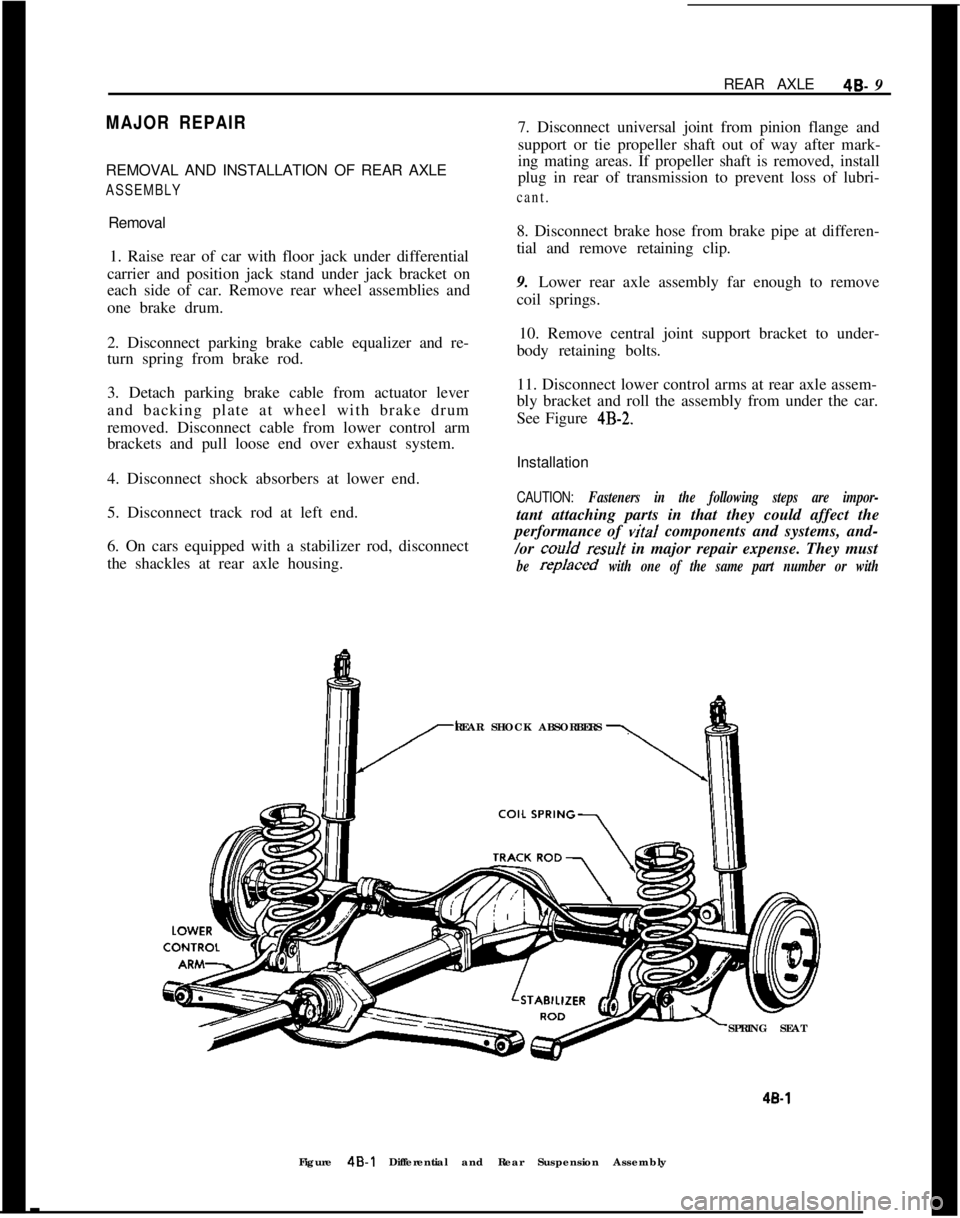
REAR AXLE48. 9
MAJOR REPAIRREMOVAL AND INSTALLATION OF REAR AXLE
ASSEMBLYRemoval
1. Raise rear of car with floor jack under differential
carrier and position jack stand under jack bracket on
each side of car. Remove rear wheel assemblies and
one brake drum.
2. Disconnect parking brake cable equalizer and re-
turn spring from brake rod.
3. Detach parking brake cable from actuator lever
and backing plate at wheel with brake drum
removed. Disconnect cable from lower control arm
brackets and pull loose end over exhaust system.
4. Disconnect shock absorbers at lower end.
5. Disconnect track rod at left end.
6. On cars equipped with a stabilizer rod, disconnect
the shackles at rear axle housing.7. Disconnect universal joint from pinion flange and
support or tie propeller shaft out of way after mark-
ing mating areas. If propeller shaft is removed, install
plug in rear of transmission to prevent loss of lubri-cant.8. Disconnect brake hose from brake pipe at differen-
tial and remove retaining clip.
9. Lower rear axle assembly far enough to remove
coil springs.
10. Remove central joint support bracket to under-
body retaining bolts.
11. Disconnect lower control arms at rear axle assem-
bly bracket and roll the assembly from under the car.
See Figure
4B-2.Installation
CAUTION: Fasteners in the following steps are impor-tant attaching parts in that they could affect the
performance of vital components and systems, and-
/or coo/d
resuJt in major repair expense. They must
be rep/aced with one of the same part number or withREAR SHOCK ABSORBERS
SPRING SEAT
4B-1Figure
4B-l Differential and Rear Suspension Assembly