OPEL GT-R 1973 Service Manual
Manufacturer: OPEL, Model Year: 1973, Model line: GT-R, Model: OPEL GT-R 1973Pages: 625, PDF Size: 17.22 MB
Page 241 of 625
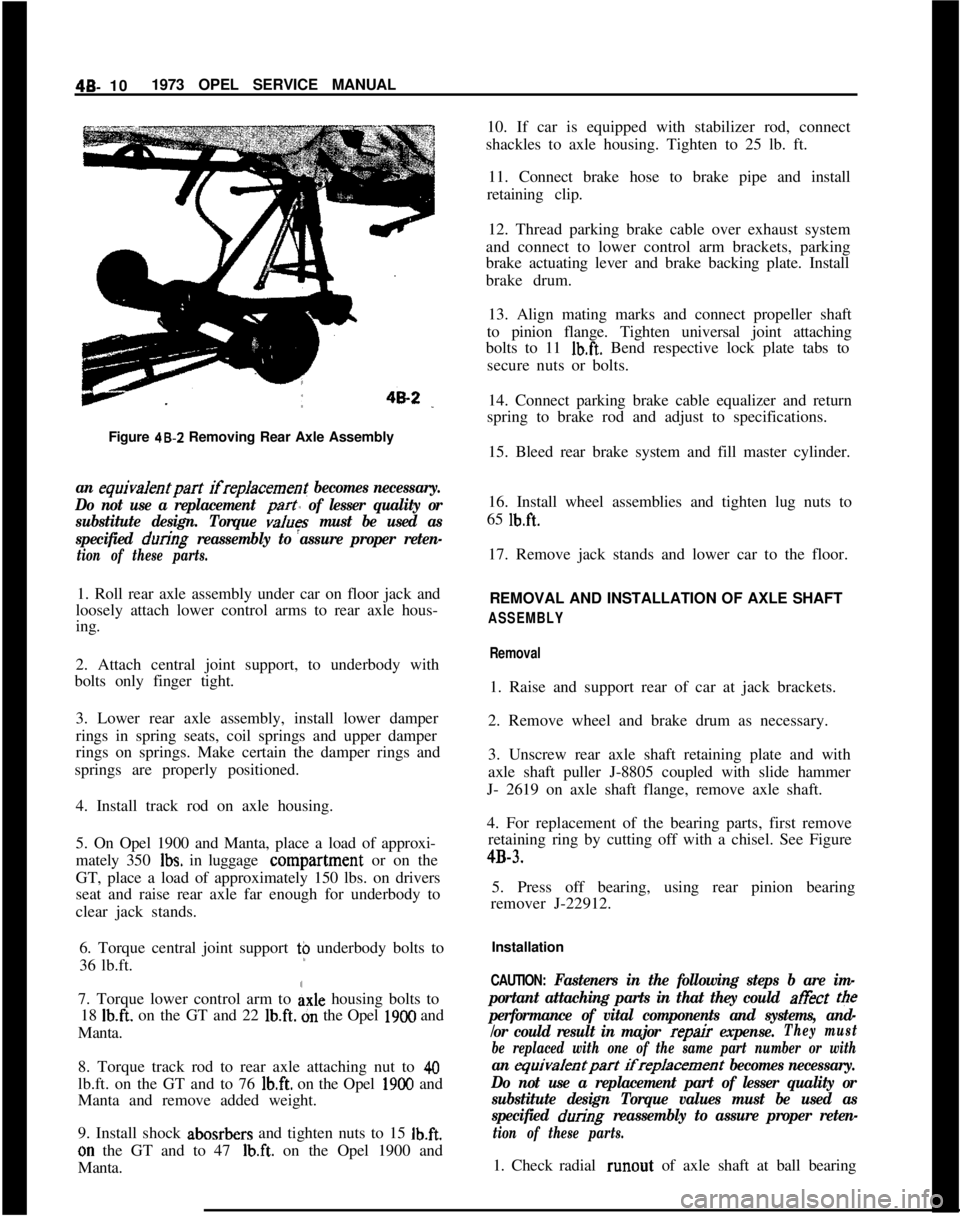
4B- 101973 OPEL SERVICE MANUAL
Figure 48-Z Removing Rear Axle Assemblyan equiva/entpart ifreplacement becomes necessary.
Do not use a replacement
part of lesser quality or
substitute design. Torque
values must be used as
specified
during reassembly to assure proper reten-
tion of these parts.1. Roll rear axle assembly under car on floor jack and
loosely attach lower control arms to rear axle hous-
ing.
2. Attach central joint support, to underbody with
bolts only finger tight.
3. Lower rear axle assembly, install lower damper
rings in spring seats, coil springs and upper damper
rings on springs. Make certain the damper rings and
springs are properly positioned.
4. Install track rod on axle housing.
5. On Opel 1900 and Manta, place a load of approxi-
mately 350
Ibs. in luggage conipartment or on the
GT, place a load of approximately 150 lbs. on drivers
seat and raise rear axle far enough for underbody to
clear jack stands.
6. Torque central joint support t$ underbody bolts to
36 lb.ft.
7. Torque lower control arm to
Axle housing bolts to
18
Ib.ft. on the GT and 22 lb.ft. dn the Opel 1900 and
Manta.
8. Torque track rod to rear axle attaching nut to
40lb.ft. on the GT and to 76
lb.ft. on the Opel 1900 and
Manta and remove added weight.
9. Install shock abosrbers and tighten nuts to 15
Ib.ft.on the GT and to 47
Ib.ft. on the Opel 1900 and
Manta.10. If car is equipped with stabilizer rod, connect
shackles to axle housing. Tighten to 25 lb. ft.
11. Connect brake hose to brake pipe and install
retaining clip.
12. Thread parking brake cable over exhaust system
and connect to lower control arm brackets, parking
brake actuating lever and brake backing plate. Install
brake drum.
13. Align mating marks and connect propeller shaft
to pinion flange. Tighten universal joint attaching
bolts to 11
Ib.ft. Bend respective lock plate tabs to
secure nuts or bolts.
14. Connect parking brake cable equalizer and return
spring to brake rod and adjust to specifications.
15. Bleed rear brake system and fill master cylinder.
16. Install wheel assemblies and tighten lug nuts to
65
lb.ft.17. Remove jack stands and lower car to the floor.
REMOVAL AND INSTALLATION OF AXLE SHAFT
ASSEMBLY
Removal1. Raise and support rear of car at jack brackets.
2. Remove wheel and brake drum as necessary.
3. Unscrew rear axle shaft retaining plate and with
axle shaft puller J-8805 coupled with slide hammer
J- 2619 on axle shaft flange, remove axle shaft.
4. For replacement of the bearing parts, first remove
retaining ring by cutting off with a chisel. See Figure4B-3.
5. Press off bearing, using rear pinion bearing
remover J-22912.
Installation
CAUTION: Fasteners in the following steps b are im-
portant attaching parts in that they could at&t
tee
performance of vital components and systems, and-
/or could result in major
repair expense.They must
be replaced with one of the same part number or with
an equivalentpart ifreplacement becomes necessary.
Do not use a replacement part of lesser quality or
substitute design Torque values must be used as
specified
during reassembly to assure proper reten-
tion of these parts.1. Check radial runout of axle shaft at ball bearing
Page 242 of 625
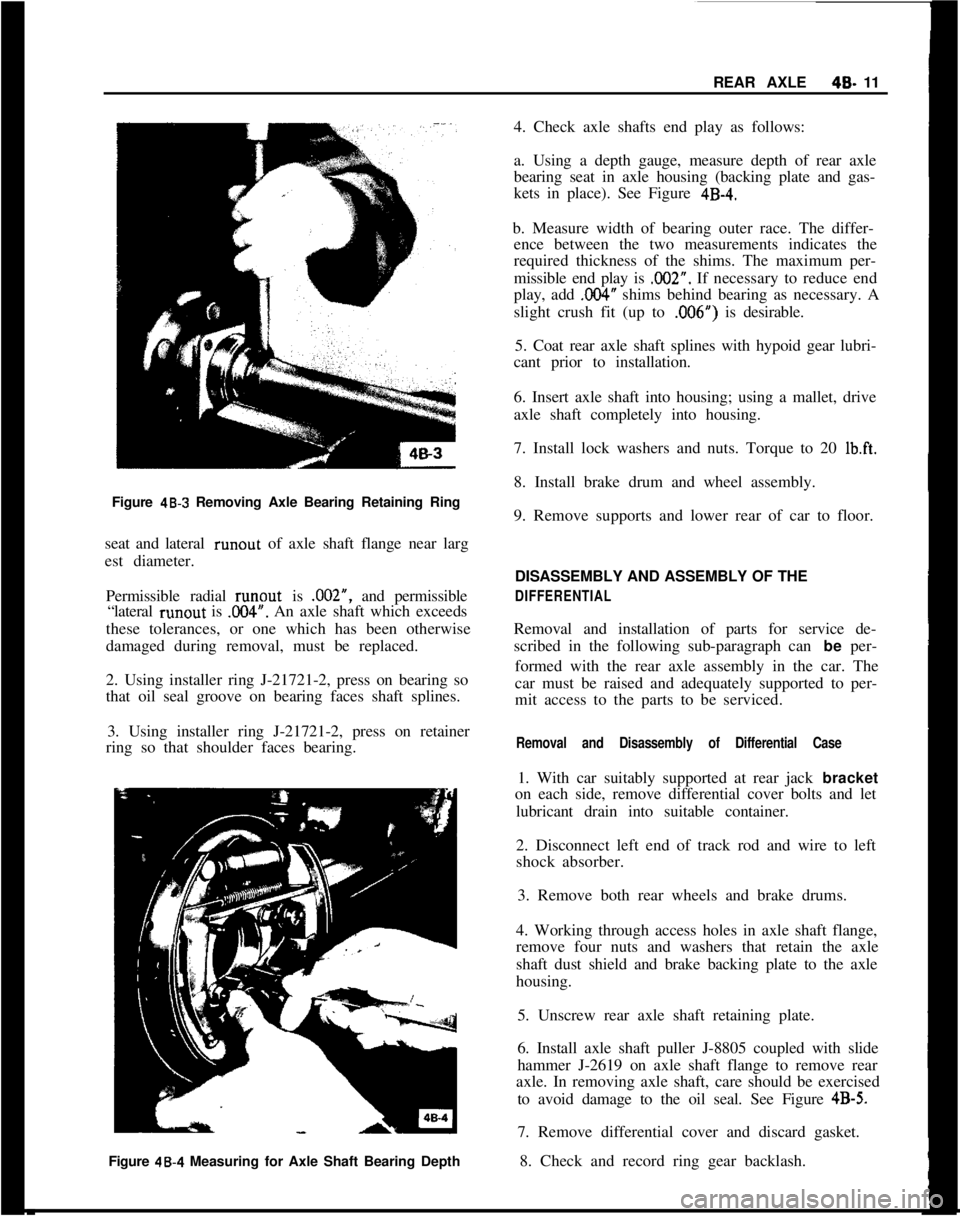
REAR AXLE40- 11
Figure
48-3 Removing Axle Bearing Retaining Ring
seat and lateral runout of axle shaft flange near larg
est diameter.
Permissible radial runout is .002”, and permissible
“lateral runout is
.OO4”. An axle shaft which exceeds
these tolerances, or one which has been otherwise
damaged during removal, must be replaced.
2. Using installer ring J-21721-2, press on bearing so
that oil seal groove on bearing faces shaft splines.
3. Using installer ring J-21721-2, press on retainer
ring so that shoulder faces bearing.
Figure 48.4 Measuring for Axle Shaft Bearing Depth4. Check axle shafts end play as follows:
a. Using a depth gauge, measure depth of rear axle
bearing seat in axle housing (backing plate and gas-
kets in place). See Figure
4B-4.b. Measure width of bearing outer race. The differ-
ence between the two measurements indicates the
required thickness of the shims. The maximum per-
missible end play is .002”. If necessary to reduce end
play, add
,004” shims behind bearing as necessary. A
slight crush fit (up to ,006”) is desirable.
5. Coat rear axle shaft splines with hypoid gear lubri-
cant prior to installation.
6. Insert axle shaft into housing; using a mallet, drive
axle shaft completely into housing.
7. Install lock washers and nuts. Torque to 20
Ib.ft.8. Install brake drum and wheel assembly.
9. Remove supports and lower rear of car to floor.
DISASSEMBLY AND ASSEMBLY OF THE
DIFFERENTIALRemoval and installation of parts for service de-
scribed in the following sub-paragraph can be per-
formed with the rear axle assembly in the car. The
car must be raised and adequately supported to per-
mit access to the parts to be serviced.
Removal and Disassembly of Differential Case1. With car suitably supported at rear jack bracket
on each side, remove differential cover bolts and let
lubricant drain into suitable container.
2. Disconnect left end of track rod and wire to left
shock absorber.
3. Remove both rear wheels and brake drums.
4. Working through access holes in axle shaft flange,
remove four nuts and washers that retain the axle
shaft dust shield and brake backing plate to the axle
housing.
5. Unscrew rear axle shaft retaining plate.
6. Install axle shaft puller J-8805 coupled with slide
hammer J-2619 on axle shaft flange to remove rear
axle. In removing axle shaft, care should be exercised
to avoid damage to the oil seal. See Figure
4B-5.7. Remove differential cover and discard gasket.
8. Check and record ring gear backlash.
Page 243 of 625
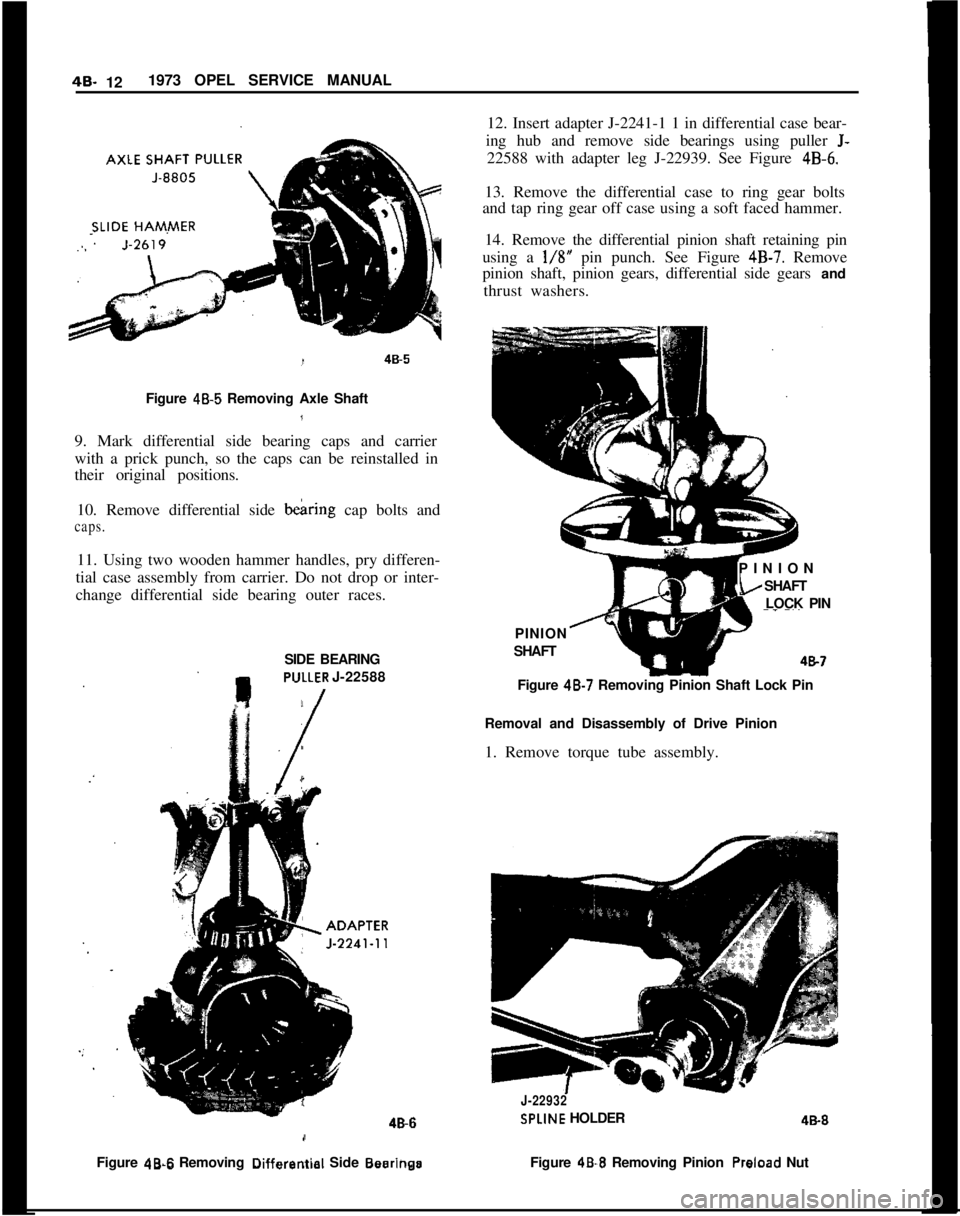
4S- 121973 OPEL SERVICE MANUAL
12. Insert adapter J-2241-1 1 in differential case bear-
ing hub and remove side bearings using puller J-22588 with adapter leg J-22939. See Figure
4B-6.13. Remove the differential case to ring gear bolts
and tap ring gear off case using a soft faced hammer.
14. Remove the differential pinion shaft retaining pin
using a
l/8” pin punch. See Figure 4B-7. Remove
pinion shaft, pinion gears, differential side gears and
thrust washers.
Figure 46.5 Removing Axle Shaft18
9. Mark differential side bearing caps and carrier
with a prick punch, so the caps can be reinstalled in
their original positions.
10. Remove differential side bearing cap bolts and
caps.11. Using two wooden hammer handles, pry differen-
tial case assembly from carrier. Do not drop or inter-
change differential side bearing outer races.
SIDE BEARING
PVLLER J-2258846.6
/NFigure
48-S Removing Differentiel Side BesrlngaPINION
SHAFTPINION
kSHAFT
LOCK PIN487
Figure 48-7 Removing Pinion Shaft Lock Pin
Removal and Disassembly of Drive Pinion
1. Remove torque tube assembly.
J-22932
SPLINE HOLDER4&8
Figure
48-E Removing Pinion Preload Nut
Page 244 of 625
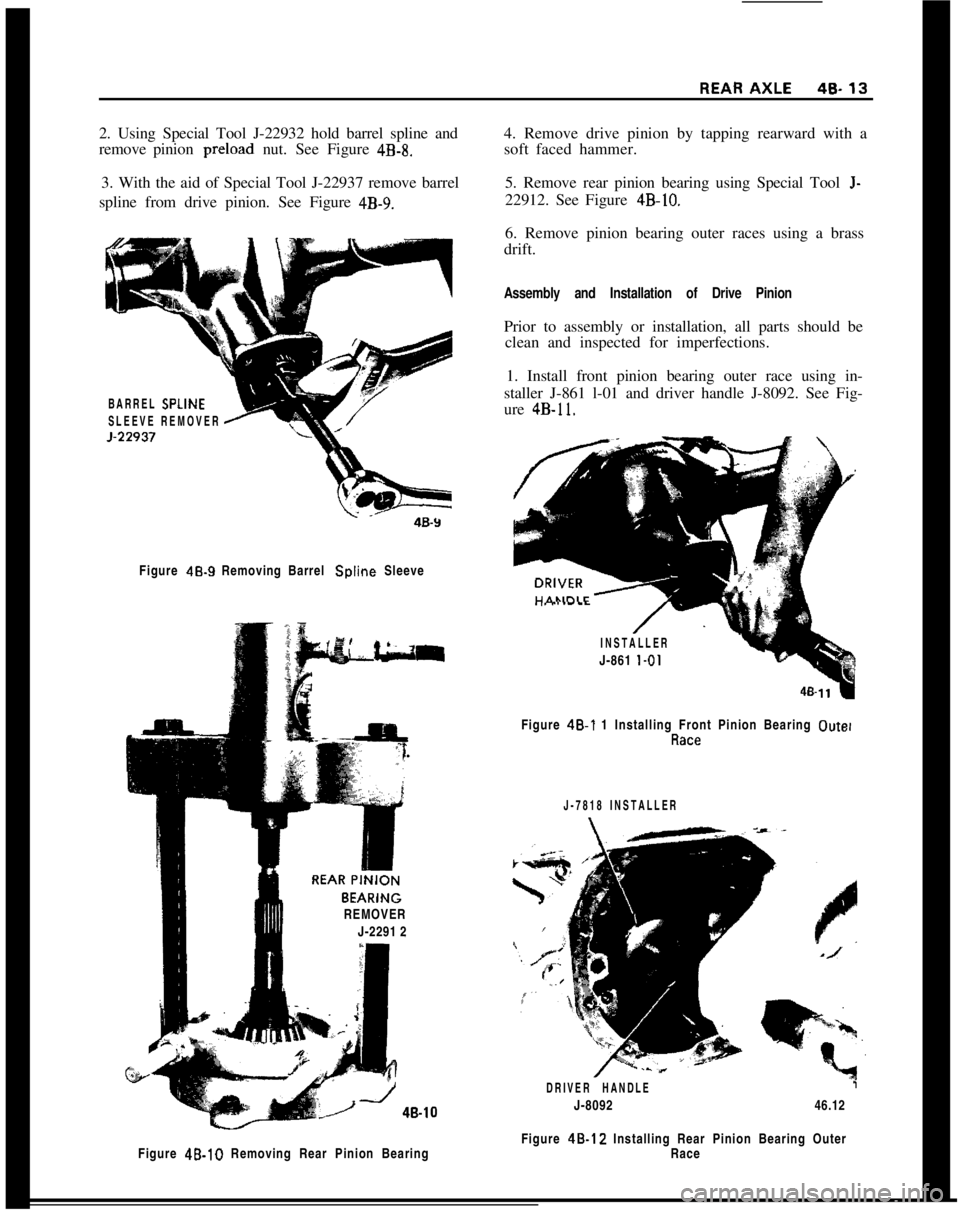
2. Using Special Tool J-22932 hold barrel spline and
remove pinion preload nut. See Figure 4B-8.4. Remove drive pinion by tapping rearward with a
soft faced hammer.
3. With the aid of Special Tool J-22937 remove barrel
spline from drive pinion. See Figure
4B-9.5. Remove rear pinion bearing using Special Tool
J-22912. See Figure
4B-10.6. Remove pinion bearing outer races using a brass
drift.
BARREL SPLINE
SLEEVE REMOVERFigure
48.9 Removing Barrel Spline Sleeve
REMOVER
J-2291 2
748-10Figure
48-10 Removing Rear Pinion Bearing
Assembly and Installation of Drive PinionPrior to assembly or installation, all parts should be
clean and inspected for imperfections.
1. Install front pinion bearing outer race using in-
staller J-861 l-01 and driver handle J-8092. See Fig-
ure
4B-11.
.‘.---/- .INSTALLERJ-861
l-01T748.
Figure
48-l 1 Installing Front Pinion Bearing OuretRace
J-7818 INSTALLER
/U.-‘“.
DRIVER HANDLEJ-809246.12
Figure
4B-12 Installing Rear Pinion Bearing Outer
Race
Page 245 of 625
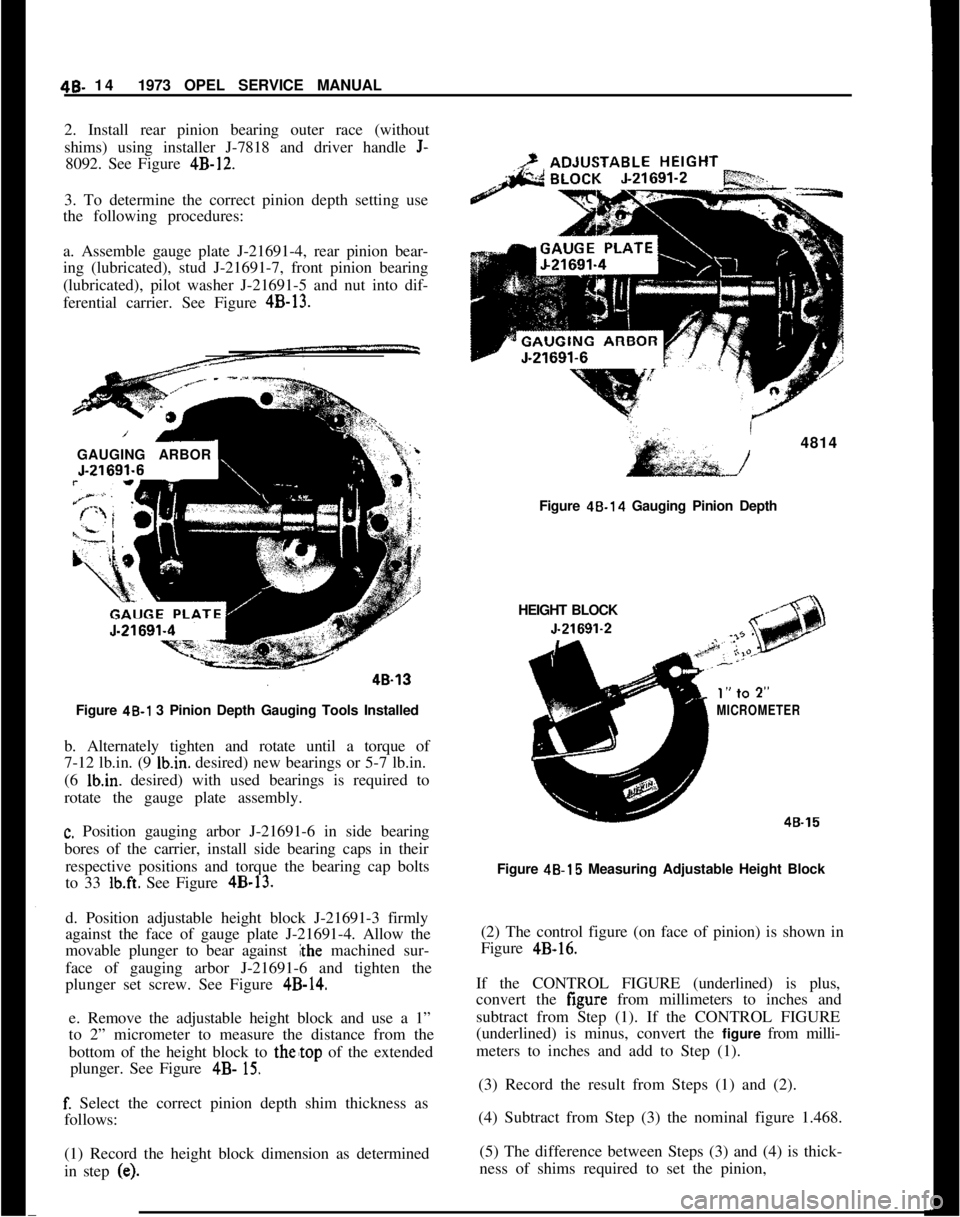
46. 141973 OPEL SERVICE MANUAL
2. Install rear pinion bearing outer race (without
shims) using installer J-7818 and driver handle
J-8092. See Figure 4B-12.
3. To determine the correct pinion depth setting use
the following procedures:
a. Assemble gauge plate J-21691-4, rear pinion bear-
ing (lubricated), stud J-21691-7, front pinion bearing
(lubricated), pilot washer J-21691-5 and nut into dif-
ferential carrier. See Figure 4B-13.
‘1GAUGING ARBOR
Figure 48-l 3 Pinion Depth Gauging Tools Installed
b. Alternately tighten and rotate until a torque of
7-12 lb.in. (9 Ibin. desired) new bearings or 5-7 lb.in.
(6 lb.in. desired) with used bearings is required to
rotate the gauge plate assembly.
c. Position gauging arbor J-21691-6 in side bearing
bores of the carrier, install side bearing caps in their
respective positions and torque the bearing cap bolts
to 33
lb.ft. See Figure 4B-13.
d. Position adjustable height block J-21691-3 firmly
against the face of gauge plate J-21691-4. Allow the
movable plunger to bear against
#the machined sur-
face of gauging arbor J-21691-6 and tighten the
plunger set screw. See Figure
4B-14.e. Remove the adjustable height block and use a 1”
to 2” micrometer to measure the distance from the
bottom of the height block to
thetop of the extended
plunger. See Figure
4B- 15.
f. Select the correct pinion depth shim thickness as
follows:
(1) Record the height block dimension as determined
in step
(e).
I4814
/Figure 48.14 Gauging Pinion Depth
HEIGHT BLOCK
MICROMETER
48-15Figure 4B-15 Measuring Adjustable Height Block
(2) The control figure (on face of pinion) is shown in
Figure
4B-16.If the CONTROL FIGURE (underlined) is plus,
convert the figure from millimeters to inches and
subtract from Step (1). If the CONTROL FIGURE
(underlined) is minus, convert the figure from milli-
meters to inches and add to Step (1).
(3) Record the result from Steps (1) and (2).
(4) Subtract from Step (3) the nominal figure 1.468.
(5) The difference between Steps (3) and (4) is thick-
ness of shims required to set the pinion,
Page 246 of 625
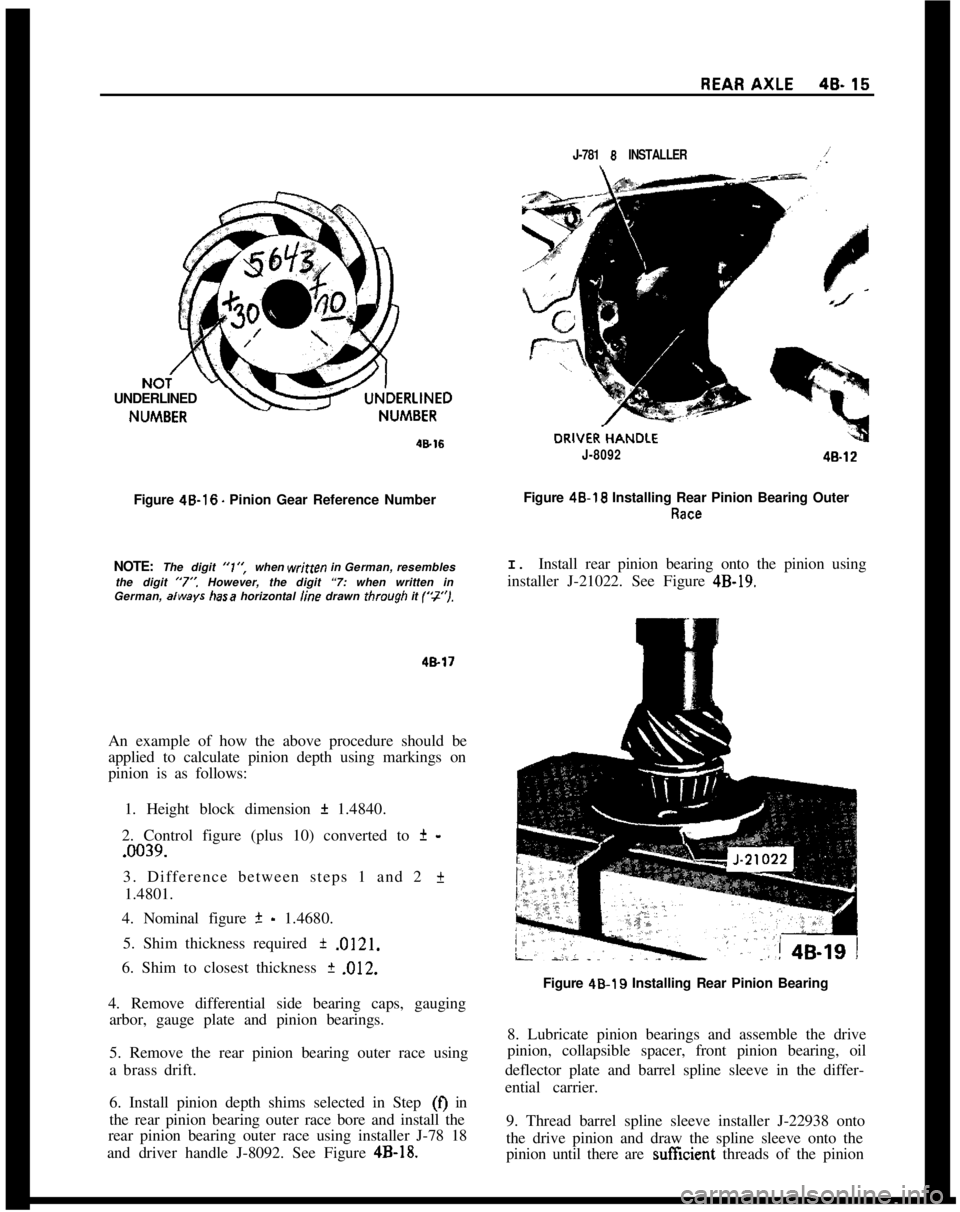
J-781 B INSTALLERiUNDERLINED
4B16Figure 46-16
- Pinion Gear Reference Number
NOTE: The digit “1’:when written in German, resembles
the digit
“7, However, the digit “7: when written in
German, always hasa horizontal line drawn rhrough it ,‘Z”).
4&17An example of how the above procedure should be
applied to calculate pinion depth using markings on
pinion is as follows:
1. Height block dimension
+ 1.4840.
2. Control figure (plus 10) converted to
f -.0039.
3. Difference between steps 1 and 2 it
1.4801.
4. Nominal figure
2 - 1.4680.
5. Shim thickness required
?r .0121.
6. Shim to closest thickness
+ .012.
4. Remove differential side bearing caps, gauging
arbor, gauge plate and pinion bearings.
5. Remove the rear pinion bearing outer race using
a brass drift.
6. Install pinion depth shims selected in Step
(f) in
the rear pinion bearing outer race bore and install the
rear pinion bearing outer race using installer J-78 18
and driver handle J-8092. See Figure 4B-18.
DRIVER.HANDLE
J-8092
48-12Figure 48.18 Installing Rear Pinion Bearing Outer
RaceI. Install rear pinion bearing onto the pinion using
installer J-21022. See Figure
4B-19.Figure 4B-19 Installing Rear Pinion Bearing
8. Lubricate pinion bearings and assemble the drive
pinion, collapsible spacer, front pinion bearing, oil
deflector plate and barrel spline sleeve in the differ-
ential carrier.
9. Thread barrel spline sleeve installer J-22938 onto
the drive pinion and draw the spline sleeve onto the
pinion until there are suflicient threads of the pinion
Page 247 of 625
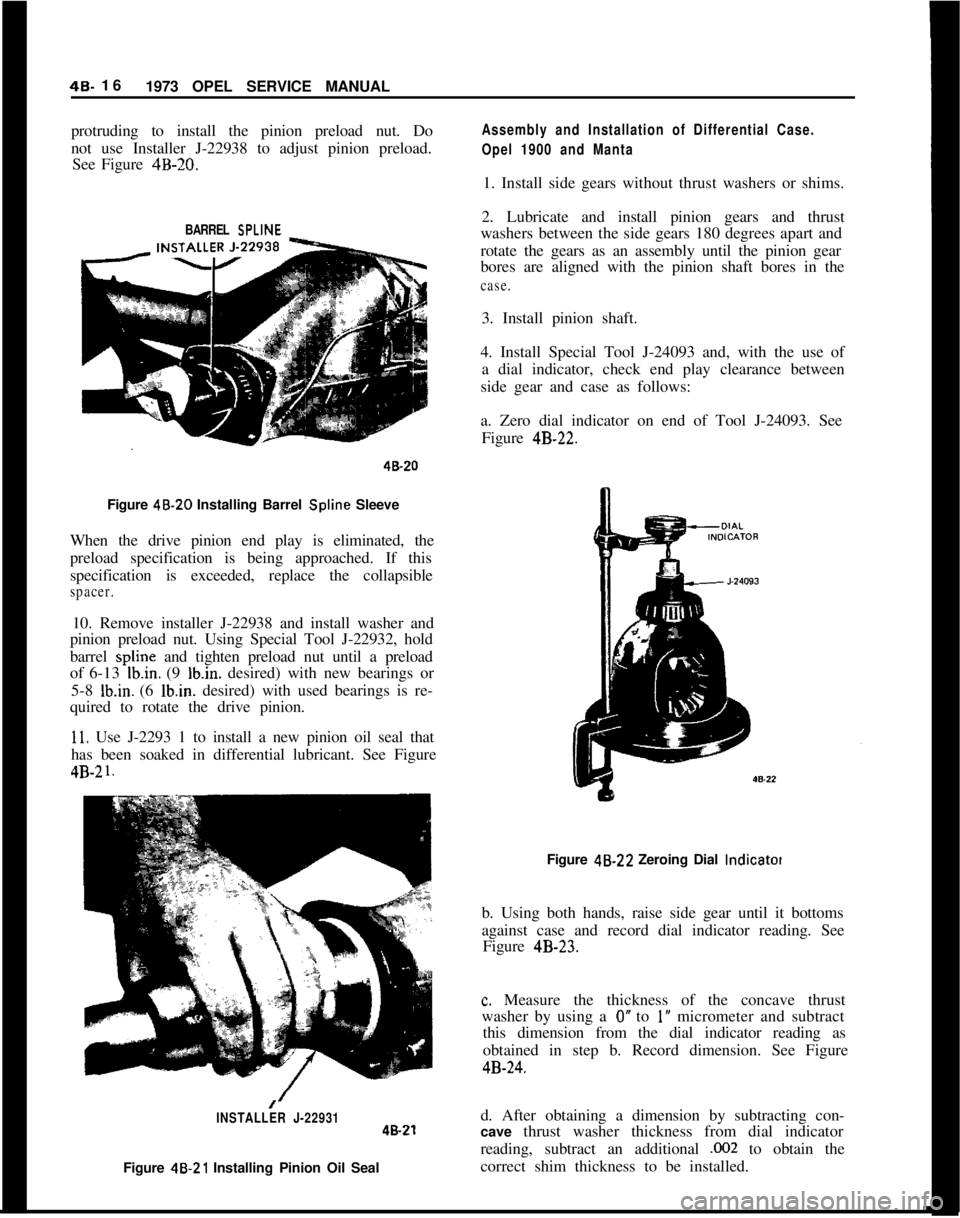
48. 16
1973 OPEL SERVICE MANUAL
protruding to install the pinion preload nut. Do
not use Installer J-22938 to adjust pinion preload.
See Figure 4B-20.
Assembly and Installation of Differential Case.
Opel 1900 and Manta1. Install side gears without thrust washers or shims.
BARREL SPLINE2. Lubricate and install pinion gears and thrust
washers between the side gears 180 degrees apart and
rotate the gears as an assembly until the pinion gear
bores are aligned with the pinion shaft bores in the
case.3. Install pinion shaft.
4. Install Special Tool J-24093 and, with the use of
a dial indicator, check end play clearance between
side gear and case as follows:
40-20a. Zero dial indicator on end of Tool J-24093. See
Figure 4B-22.
Figure 48.20 Installing Barrel Spline Sleeve
When the drive pinion end play is eliminated, the
preload specification is being approached. If this
specification is exceeded, replace the collapsible
spacer.10. Remove installer J-22938 and install washer and
pinion preload nut. Using Special Tool J-22932, hold
barrel spline and tighten preload nut until a preload
of 6-13
Ib.in. (9 Ibin. desired) with new bearings or
5-8
Ib.in. (6 lb.in. desired) with used bearings is re-
quired to rotate the drive pinion.
11. Use J-2293 1 to install a new pinion oil seal that
has been soaked in differential lubricant. See Figure4B-2
1.Figure 48.22 Zeroing Dial
lndicatotb. Using both hands, raise side gear until it bottoms
against case and record dial indicator reading. See
Figure 4B-23.
c. Measure the thickness of the concave thrust
washer by using a
0” to 1’ micrometer and subtract
this dimension from the dial indicator reading as
obtained in step b. Record dimension. See Figure
4B-24.
/INSTALLER J-22931d. After obtaining a dimension by subtracting con-48-21cave thrust washer thickness from dial indicator
reading, subtract an additional
,002 to obtain the
Figure 46.21 Installing Pinion Oil Sealcorrect shim thickness to be installed.
Page 248 of 625
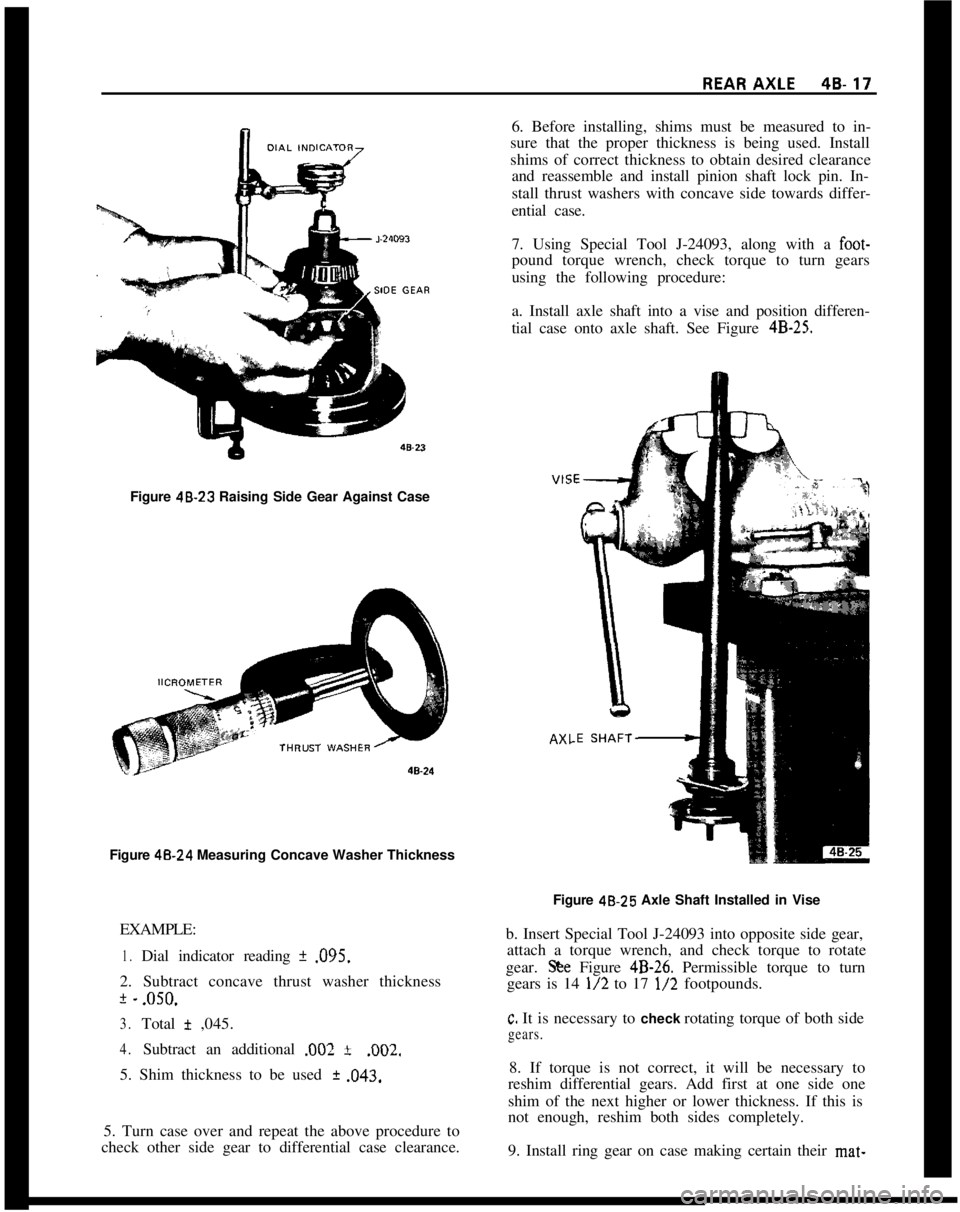
6. Before installing, shims must be measured to in-
sure that the proper thickness is being used. Install
shims of correct thickness to obtain desired clearance
and reassemble and install pinion shaft lock pin. In-
stall thrust washers with concave side towards differ-
ential case.
7. Using Special Tool J-24093, along with a foot-pound torque wrench, check torque to turn gears
using the following procedure:
a. Install axle shaft into a vise and position differen-
tial case onto axle shaft. See Figure
4B-25.Figure 48-23 Raising Side Gear Against Case
Figure 48.24 Measuring Concave Washer Thickness
AX,EXAMPLE:
1.Dial indicator reading * .095.
2. Subtract concave thrust washer thickness
+ -.oso.
3.Total + ,045.
4.Subtract an additional .002 *.002.
5. Shim thickness to be used
+ .043.
5. Turn case over and repeat the above procedure to
check other side gear to differential case clearance.Figure 48.25 Axle Shaft Installed in Vise
b. Insert Special Tool J-24093 into opposite side gear,
attach a torque wrench, and check torque to rotate
gear. S& Figure
4B-26. Permissible torque to turn
gears is 14
l/2 to 17 l/2 footpounds.
c. It is necessary to check rotating torque of both side
gears.8. If torque is not correct, it will be necessary to
reshim differential gears. Add first at one side one
shim of the next higher or lower thickness. If this is
not enough, reshim both sides completely.
9. Install ring gear on case making certain their mat-
Page 249 of 625
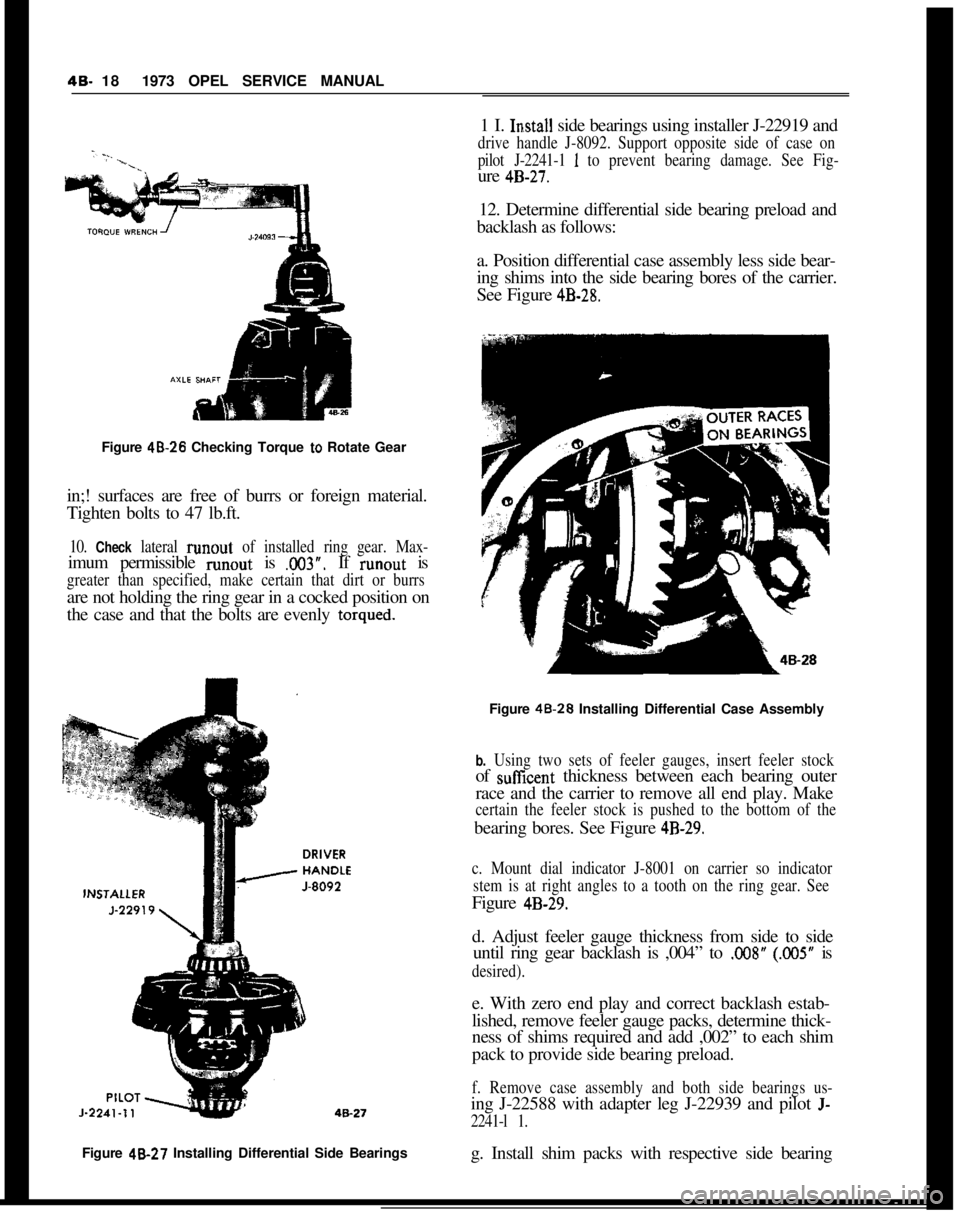
48. 181973 OPEL SERVICE MANUAL
Figure 48.26 Checking Torque
to Rotate Gear
in;! surfaces are free of burrs or foreign material.
Tighten bolts to 47 lb.ft.
10. Check lateral runout of installed ring gear. Max-imum permissible runout is
.003”. If runout is
greater than specified, make certain that dirt or burrsare not holding the ring gear in a cocked position on
the case and that the bolts are evenly
torqued.Figure 48-27 Installing Differential Side Bearings
g. Install shim packs with respective side bearing1 I.
In.stall side bearings using installer J-22919 and
drive handle J-8092. Support opposite side of case on
pilot J-2241-1
1 to prevent bearing damage. See Fig-ure
4B-27.12. Determine differential side bearing preload and
backlash as follows:
a. Position differential case assembly less side bear-
ing shims into the side bearing bores of the carrier.
See Figure
4B-28.Figure 48.28 Installing Differential Case Assembly
b. Using two sets of feeler gauges, insert feeler stockof suffcent thickness between each bearing outer
race and the carrier to remove all end play. Make
certain the feeler stock is pushed to the bottom of thebearing bores. See Figure
4B-29.
c. Mount dial indicator J-8001 on carrier so indicator
stem is at right angles to a tooth on the ring gear. SeeFigure
4B-29.d. Adjust feeler gauge thickness from side to side
until ring gear backlash is ,004” to
.OO8” (.005” is
desired).e. With zero end play and correct backlash estab-
lished, remove feeler gauge packs, determine thick-
ness of shims required and add ,002” to each shim
pack to provide side bearing preload.
f. Remove case assembly and both side bearings us-ing J-22588 with adapter leg J-22939 and pilot
J-
2241-l 1.
Page 250 of 625
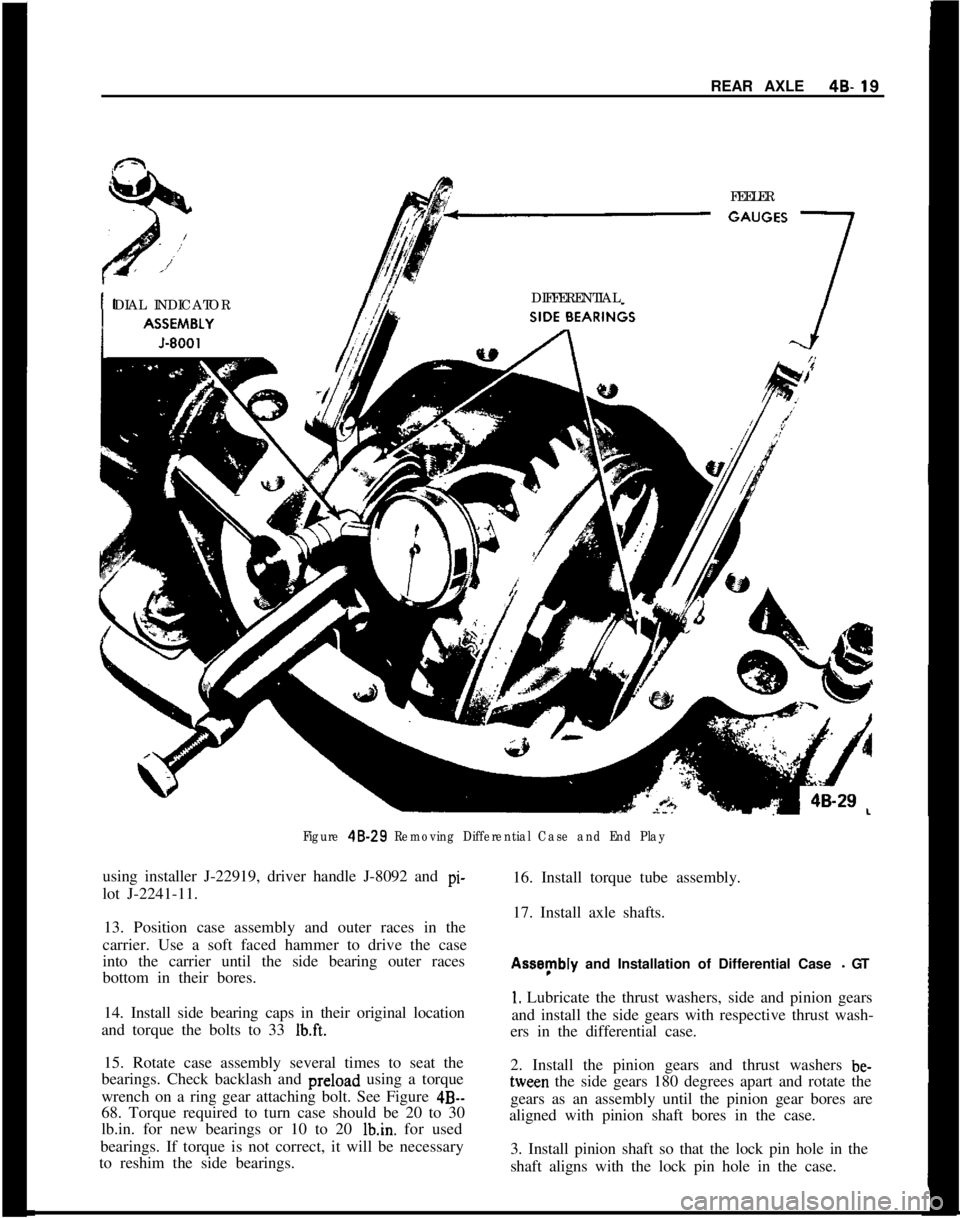
REAR AXLE48.19FEELER
DIAL INDICATORDIFFERENTIAL
Figure 48.29 Removing Differential Case and End Playusing installer J-22919, driver handle J-8092 and pi-
lot J-2241-11.16. Install torque tube assembly.
17. Install axle shafts.
13. Position case assembly and outer races in the
carrier. Use a soft faced hammer to drive the case
into the carrier until the side bearing outer races
bottom in their bores.Assynbly and Installation of Differential Case
- GT
14. Install side bearing caps in their original location
and torque the bolts to 33
Ib.ft.
1. Lubricate the thrust washers, side and pinion gears
and install the side gears with respective thrust wash-
ers in the differential case.
15. Rotate case assembly several times to seat the
bearings. Check backlash and preload using a torque
wrench on a ring gear attaching bolt. See Figure
4B--68. Torque required to turn case should be 20 to 30
lb.in. for new bearings or 10 to 20 Ibin. for used
bearings. If torque is not correct, it will be necessary
to reshim the side bearings.2. Install the pinion gears and thrust washers be-tween the side gears 180 degrees apart and rotate the
gears as an assembly until the pinion gear bores are
aligned with pinion shaft bores in the case.
3. Install pinion shaft so that the lock pin hole in the
shaft aligns with the lock pin hole in the case.