PONTIAC FIERO 1988 Service Repair Manual
Manufacturer: PONTIAC, Model Year: 1988, Model line: FIERO, Model: PONTIAC FIERO 1988Pages: 1825, PDF Size: 99.44 MB
Page 101 of 1825
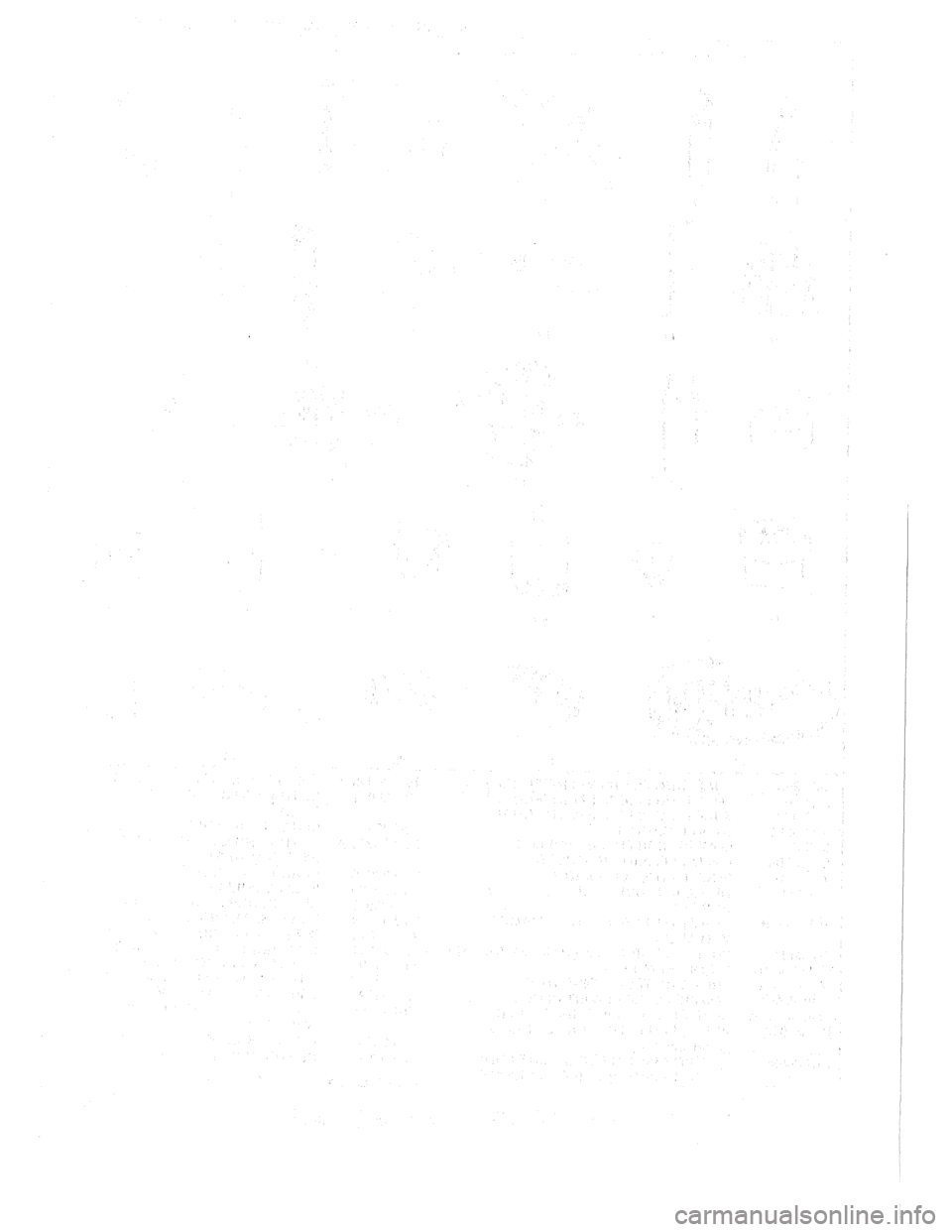
Page 102 of 1825
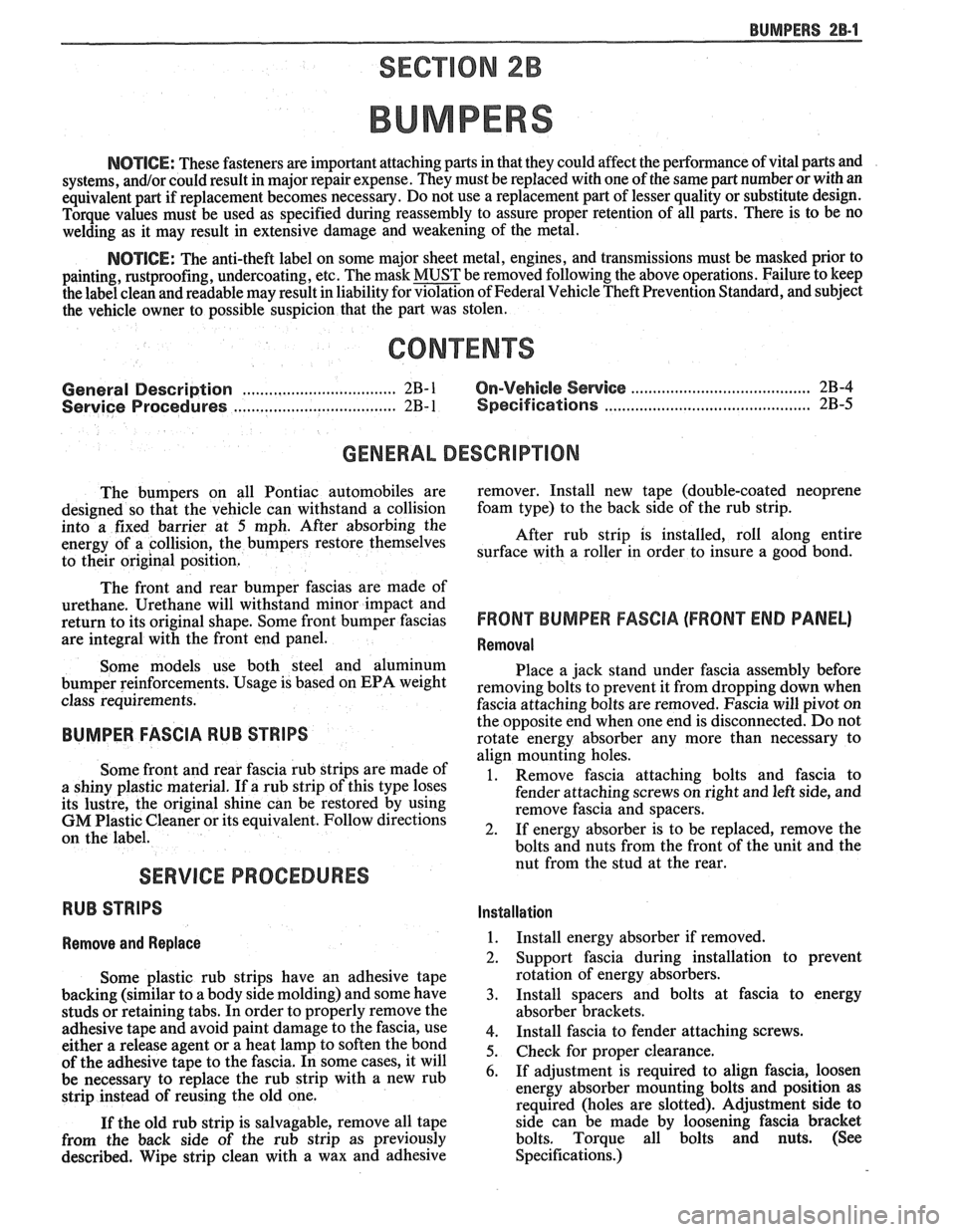
BUMPERS 28-1
SECTION 2B
BUMPERS
NOTICE: These fasteners are important attaching parts in that they could affect the performance of vital parts and
systems,
andlor could result in major repair expense. They must be replaced with one of the same part number or with an
equivalent
part if replacement becomes necessary. Do not use a replacement part of lesser quality or substitute design.
Torque values must be used as specified during reassembly to assure proper retention of all parts. There is to be no
welding as it may result in extensive damage and weakening of the metal.
NOTICE: The anti-theft label on some major sheet metal, engines, and transmissions must be masked prior to
painting, rustproofing, undercoating, etc. The mask MUST be removed following the above operations. Failure to keep
the label clean and readable may result in liability for violation of Federal Vehicle Theft Prevention Standard, and subject
the vehicle owner to possible suspicion that the part was stolen.
CONTENTS
General Description ................................ 2B-1 On-Vehicle Service ..................................... 2B-4
........................................... ..................... Service Procedures .. ........... 2B- 1 Specifications 2B-5
GENERAL DESCRIPWIBN
The bumpers on all Pontiac automobiles are remover.
Install new tape (double-coated neoprene
designed so that the vehicle can withstand a collision foam type)
to the back side of the rub strip.
into a fixed barrier at
5 mph. After absorbing the
energy of a collision, the bumpers restore themselves After
rub strip is installed, roll along entire
to their original position. surface with a roller
in order to insure a good bond.
The front and rear bumper fascias are made of
urethane. Urethane will withstand minor impact and
return to its original shape. Some front bumper fascias
are integral with the front end panel.
Some models use both steel and aluminum
bumper reinforcements. Usage is based on
EPA weight
class requirements.
BUMPER FASCIA RUB STRIPS
Some front and rear fascia rub strips are made of
a shiny plastic material. If a rub strip of this type loses
its lustre, the original shine can be restored by using
GM Plastic Cleaner or its equivalent. Follow directions
on the label.
SERVICE PROCEDURES
RUB STRIPS
Remove and Replace
Some plastic rub strips have an adhesive tape
backing (similar to a body side molding) and some have
studs or retaining tabs. In order to properly remove the
adhesive tape and avoid paint damage to the fascia, use
either a release agent or a heat lamp to soften the bond
of the adhesive tape to the fascia. In some cases, it will
be necessary to replace the rub strip with a new rub
strip instead of reusing the old one.
If the old rub strip is salvagable, remove all tape
from the back side of the rub strip as previously
described. Wipe strip clean with a wax and adhesive
FRONT BUMPER FASCIA (FRONT END PANEL)
Removal
Place a jack stand under fascia assembly before
removing bolts to prevent it from dropping down when
fascia attaching bolts are removed. Fascia will pivot on
the opposite end when one end is disconnected. Do not
rotate energy absorber any more than necessary to
align mounting holes.
1. Remove fascia attaching bolts and fascia to
fender attaching screws on right and left side, and
remove fascia and spacers.
2. If energy absorber is to be replaced, remove the
bolts and nuts from the front of the unit and the
nut from the stud at the rear.
Installation
1. Install energy absorber if removed.
2. Support fascia during installation to prevent
rotation of energy absorbers.
3. Install spacers and bolts at fascia to energy
absorber brackets.
4. Install fascia to fender attaching screws.
5. Check for proper clearance.
6. If adjustment is required to align fascia, loosen
energy absorber mounting bolts and position as
required (holes are slotted). Adjustment side to
side can be made by loosening fascia bracket
bolts. Torque all bolts and nuts. (See
Specifications.)
Page 103 of 1825
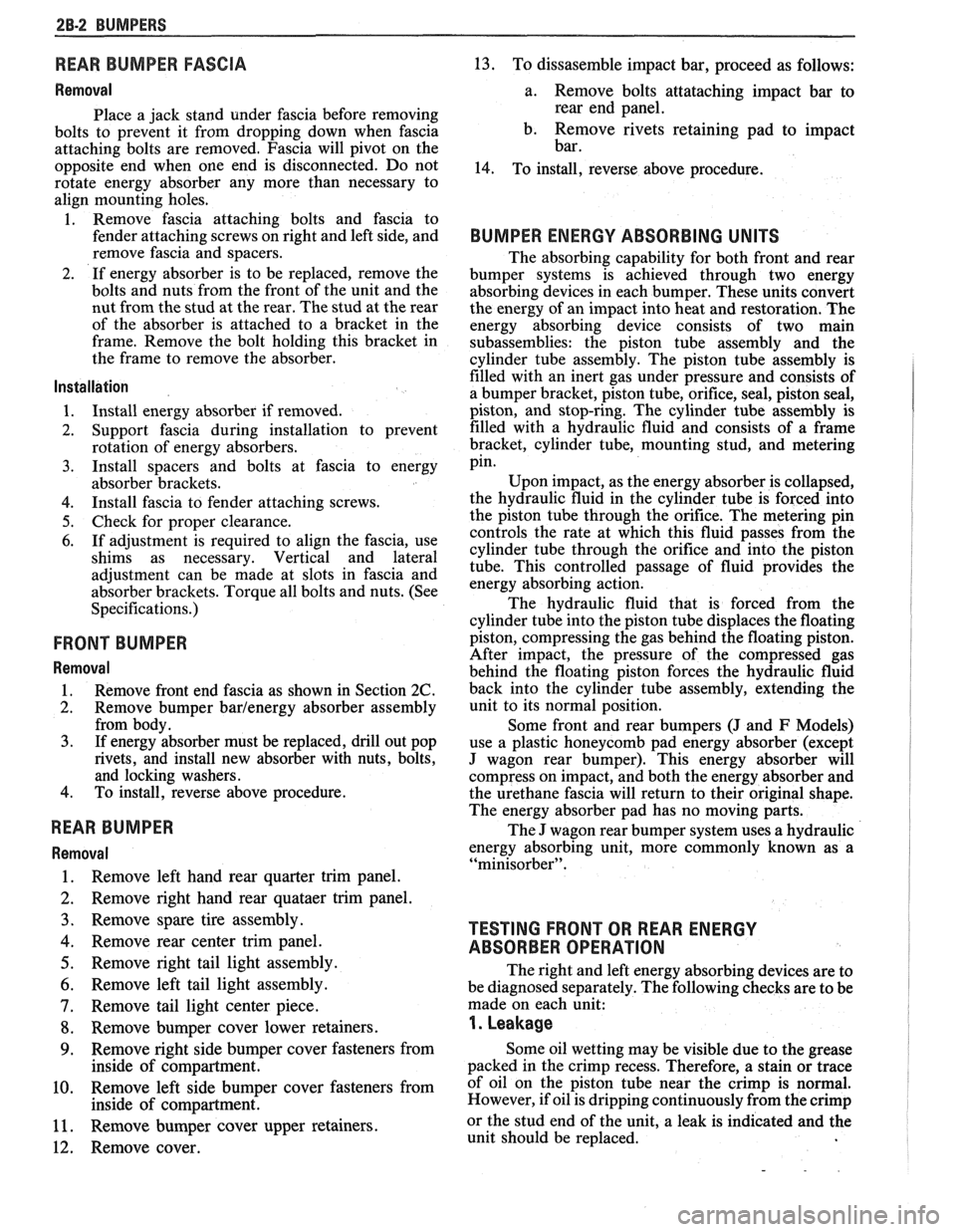
2B-2 BUMPERS
REAR BUMPER FASCIA
Removal
Place a jack stand under fascia before removing
bolts to prevent it from dropping down when fascia
attaching bolts are removed. Fascia will pivot on the
opposite end when one end is disconnected. Do not
rotate energy absorber any more than necessary to
align mounting holes.
1. Remove fascia attaching bolts and fascia to
fender attaching screws on right and left side, and
remove fascia and spacers.
2. If energy absorber is to be replaced, remove the
bolts and nuts from the front of the unit and the
nut from the stud at the rear. The stud at the rear
of the absorber is attached to a bracket in the
frame. Remove the bolt holding this bracket in
the frame to remove the absorber.
Installation
1. Install energy absorber if removed.
2. Support fascia during installation to prevent
rotation of energy absorbers.
3. Install spacers and bolts at fascia to energy
absorber brackets.
4. Install fascia to fender attaching screws.
5. Check for proper clearance.
6. If adjustment is required to align the fascia, use
shims as necessary. Vertical and lateral
adjustment can be made at slots in fascia and
absorber brackets. Torque all bolts and nuts. (See
Specifications.)
FRONT BUMPER
Removal
1. Remove
front end fascia as shown in Section 2C.
2. Remove bumper barlenergy absorber assembly
from body.
3. If energy absorber must be replaced, drill out pop
rivets, and install new absorber with nuts, bolts,
and locking washers.
4. To install, reverse above procedure.
REAR BUMPER
Removal
1. Remove left hand rear quarter trim panel.
2. Remove right hand rear quataer trim panel.
3. Remove spare tire assembly.
4. Remove rear center trim panel.
5. Remove right tail light assembly.
6. Remove left tail light assembly.
7. Remove tail light center piece.
8. Remove bumper cover lower retainers.
9. Remove right-side bumper cover fasteners from
inside of compartment.
10. Remove left side bumper cover fasteners from
inside of compartment.
11. Remove bumper cover upper retainers.
12. Remove cover.
13. To dissasemble impact bar, proceed as follows:
a. Remove bolts attataching impact bar to
rear end panel.
b. Remove rivets retaining pad to impact
bar.
14. To install, reverse above procedure.
BUMPER ENERGY ABSORBING UNITS
The absorbing capability for both front and rear
bumper systems is achieved through two energy
absorbing devices in each bumper. These units convert
the energy of an impact into heat and restoration. The
energy absorbing device consists of two main
subassemblies: the piston tube assembly and the
cylinder tube assembly. The piston tube assembly is
filled with an inert gas under pressure and consists of
a bumper bracket, piston tube, orifice, seal, piston seal,
piston, and stop-ring. The cylinder tube assembly is
filled with a hydraulic fluid and consists of a frame
bracket, cylinder tube, mounting stud, and metering
pin.
Upon impact, as the energy absorber is collapsed,
the hydraulic fluid in the cylinder tube is forced into
the piston tube through the orifice. The metering pin
controls the rate at which this fluid passes from the
cylinder tube through the orifice and into the piston
tube. This controlled passage of fluid provides the
energy absorbing action.
The hydraulic fluid that is forced from the
cylinder tube into the piston tube displaces the floating
piston, compressing the gas behind the floating piston.
After impact, the pressure of the compressed gas
behind the floating piston forces the hydraulic fluid
back into the cylinder tube assembly, extending the
unit to its normal position.
Some front and rear bumpers (J and
F Models)
use a plastic honeycomb pad energy absorber (except
J wagon rear bumper). This energy absorber will
compress on impact, and both the energy absorber and
the urethane fascia will return to their original shape.
The energy absorber pad has no moving parts.
The J wagon rear bumper system uses a hydraulic
energy absorbing unit, more commonly known as a
"minisorber".
TESTING FRONT OR REAR ENERGY
ABSORBER OPERATION
The right and left energy absorbing devices are to
be diagnosed separately. The following checks are to be
made on each unit:
1. Leakage
Some oil wetting may be visible due to the grease
packed in the crimp recess. Therefore, a stain or trace
of oil on the piston tube near the crimp is normal.
However, if oil is dripping continuously from the crimp
or the stud end of the unit, a leak is indicated and the
unit should be replaced.
Page 104 of 1825
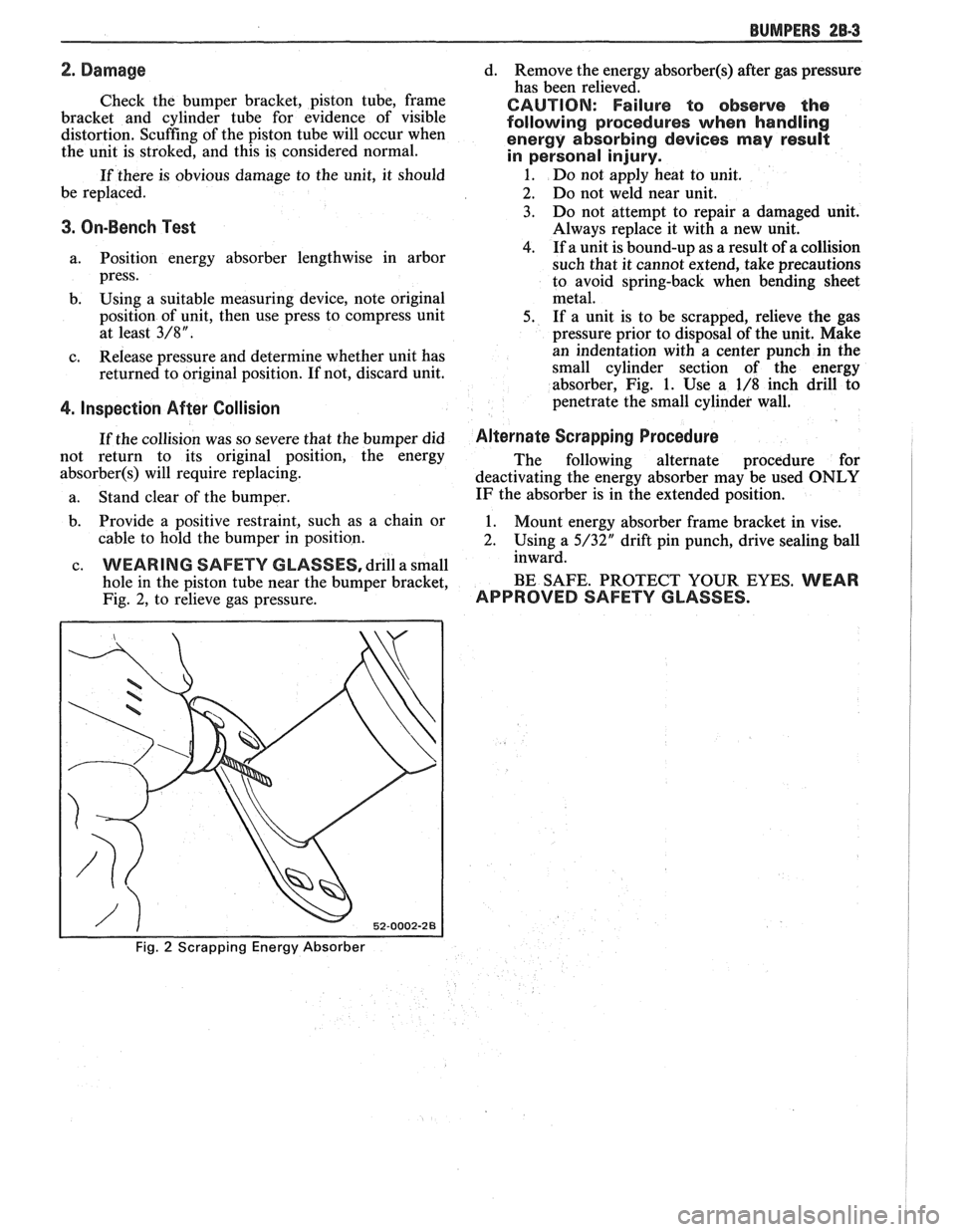
BUMPERS 28-3
Check the bumper bracket, piston tube, frame
bracket and cylinder tube for evidence of visible
distortion. Scuffing of the piston tube will occur when
the unit is stroked, and this is considered normal.
If there is obvious damage to the unit, it should
be replaced.
3. On-Bench Test
a. Position energy absorber lengthwise in arbor
press.
b. Using
a suitable measuring device, note original
position of unit, then use press to compress unit
at least
3/8".
c. Release pressure and determine whether unit has
returned to original position.
If not, discard unit.
4. Inspection After Collision
If the collision was so severe that the bumper did
not return to its original position, the energy
absorber(s) will require replacing.
a. Stand clear
of the bumper.
b. Provide
a positive restraint, such as a chain or
cable to hold the bumper in position.
c.
WEARING SAFETY GLASSES, drill a small
hole in the piston tube near the bumper bracket,
Fig.
2, to relieve gas pressure.
Fig. 2 Scrapping Energy Absorber
d. Remove the energy absorber(§) after gas pressure
has been relieved.
CAUTION: Failure to observe the
following procedures when handling
energy absorbing devices
nnay result
in personal injury.
1. Do not apply heat to unit.
2. Do not weld near unit.
3. Do not attempt to repair a damaged unit.
Always replace it with a new unit.
4. If a unit is bound-up as a result of a collision
such that it cannot extend, take precautions
to avoid spring-back when bending sheet
metal.
5. If
a unit is to be scrapped, relieve the gas
pressure prior to disposal of the unit. Make
an indentation with a center punch in the
small cylinder section of the energy
absorber, Fig.
1. Use a 1/8 inch drill to
penetrate the small cylinder wall.
Alternate Scrapping Procedure
The following alternate procedure for
deactivating the energy absorber may be used
ONLY
IF the absorber is in the extended position.
1. Mount energy absorber frame bracket in vise.
2. Using a 5/32" drift pin punch, drive sealing ball
inward.
BE SAFE. PROTECT YOUR EYES.
WEAR
APPROVED SAFETY GLASSES.
Page 105 of 1825
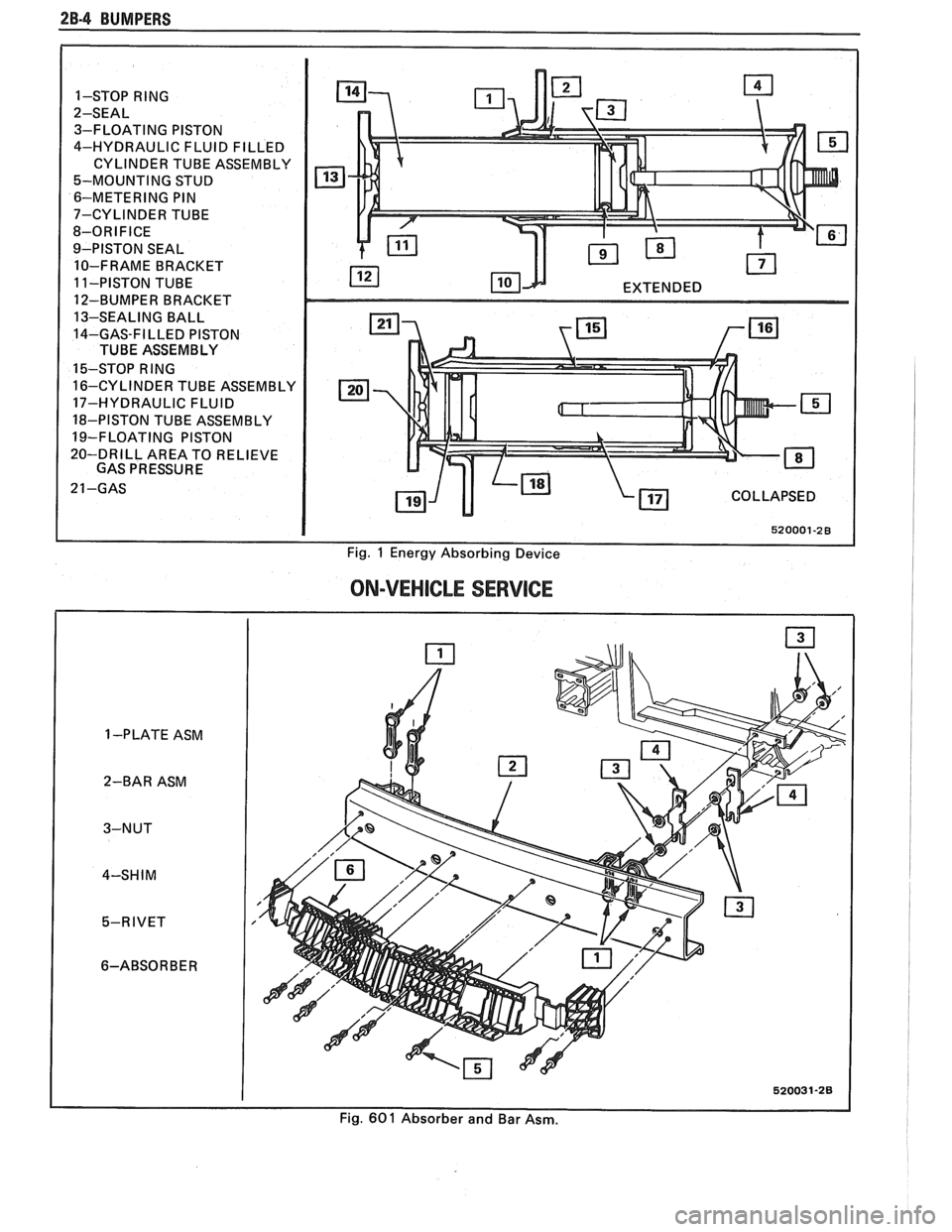
28-4 BUMPERS
1-STOP RlNG
2-SEAL 3-FLOATING PISTON
4-HYDRAULIC FLUID FILLED
CYLINDER TUBE ASSEMBLY
5-MOUNTING STUD
6-METERING PIN
7-CYLINDER TUBE
8-ORIFICE
9-PISTON SEAL
10-FRAME BRACKET
11-PISTON TUBE
12-BUMPER BRACKET
13-SEALING BALL
14-GAS-FILLED PISTON
TUBE ASSEMBLY
15-STOP RlNG
16-CYLINDER TUBE ASSEMBLY
17-HYDRAULIC FLUID
18-PISTON TUBE ASSEMBLY
19-FLOATING PISTON
20-DRILL AREA TO RELIEVE
GAS PRESSURE
21 -GAS m
COLLAPSED
Fig. 1 Energy Absorbing Device
ON-VEHICLE SERVICE
1 -PLATE ASM
2-BAR ASM
3-NUT
4-SH
I M
5-RIVET
6-ABSORBER
Fig.
60 1 Absorber and Bar Asm.
Page 106 of 1825
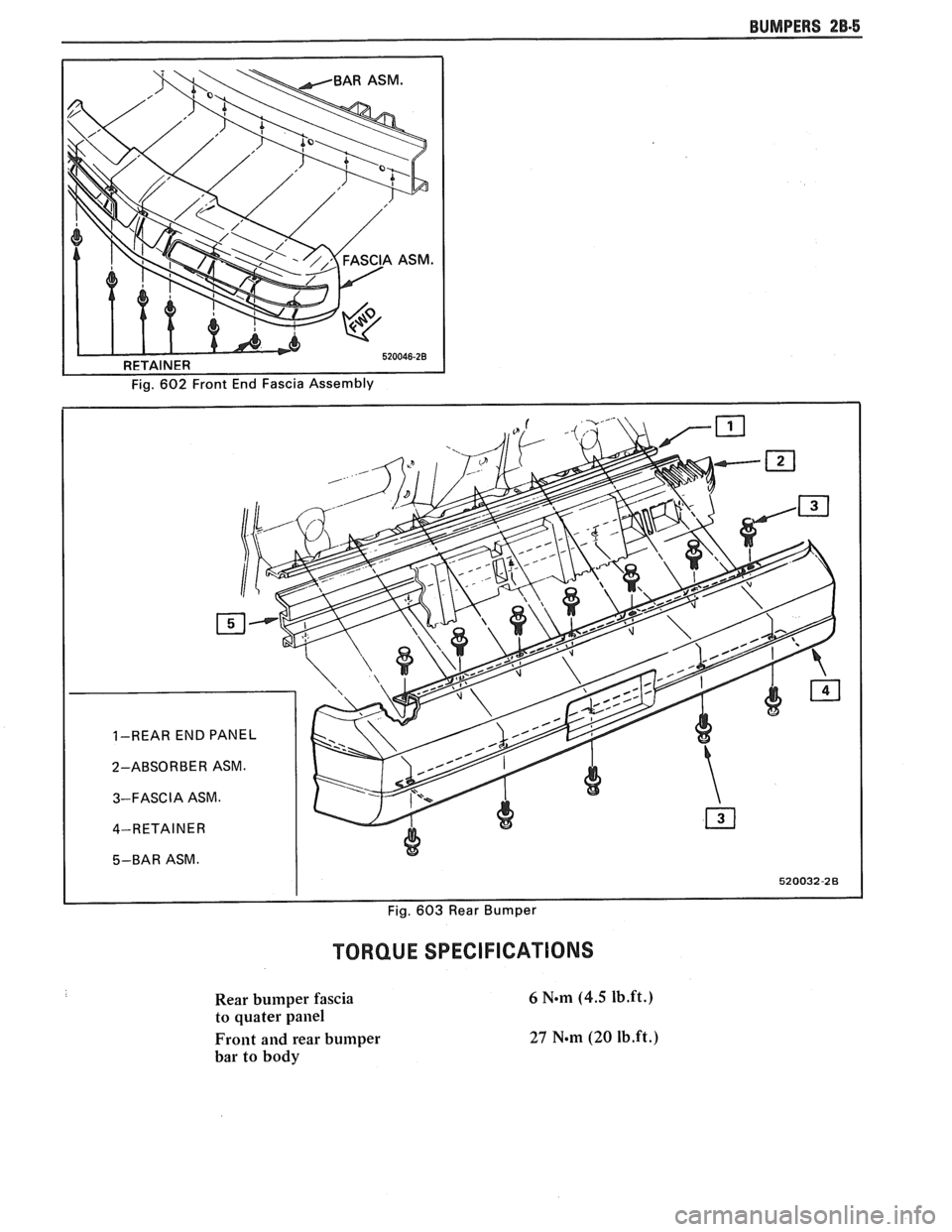
BUMPERS 28.5
TORQUE SPECIFICATIONS
Rear bumper fascia
to quater
pailel
Front and rear bumper
bar to body
Page 107 of 1825
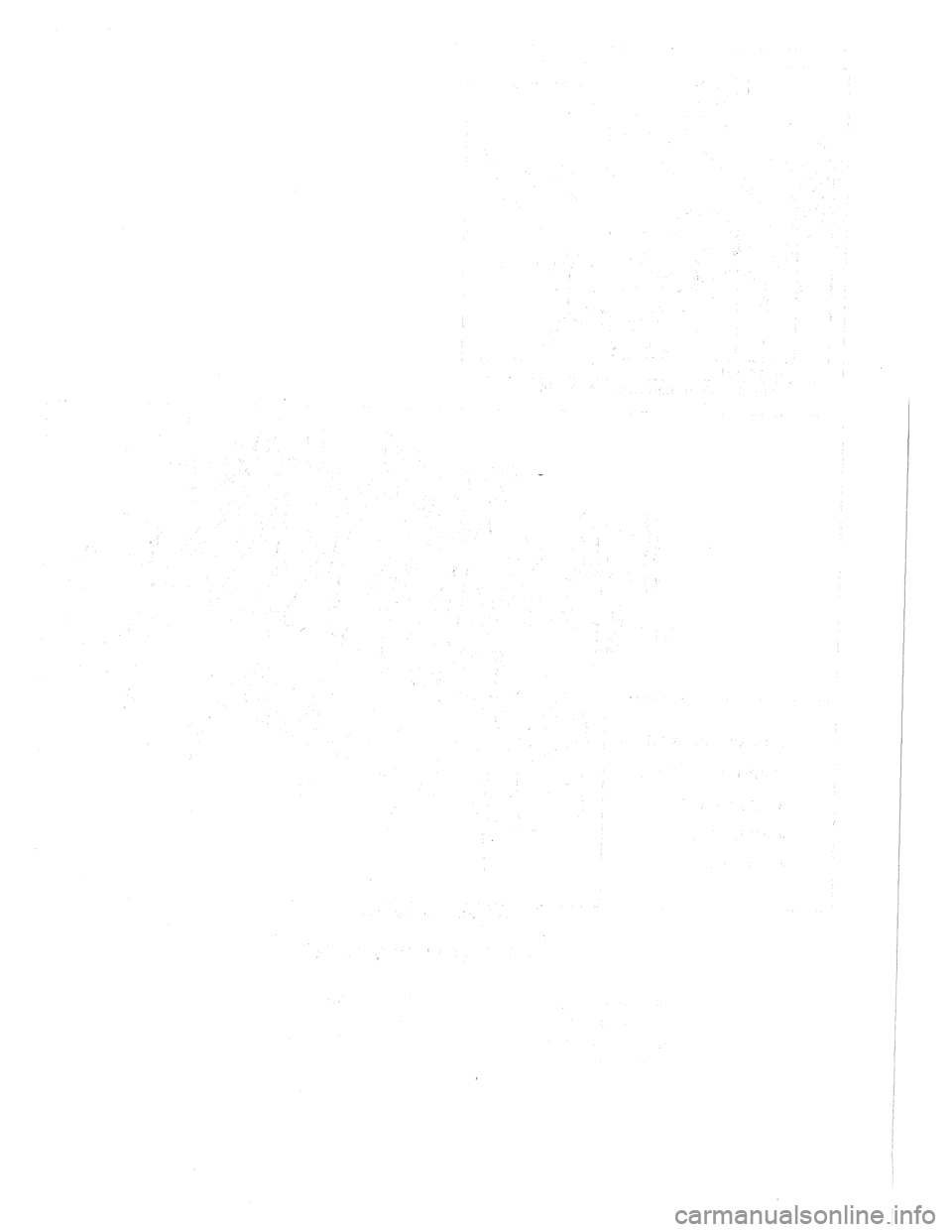
Page 108 of 1825
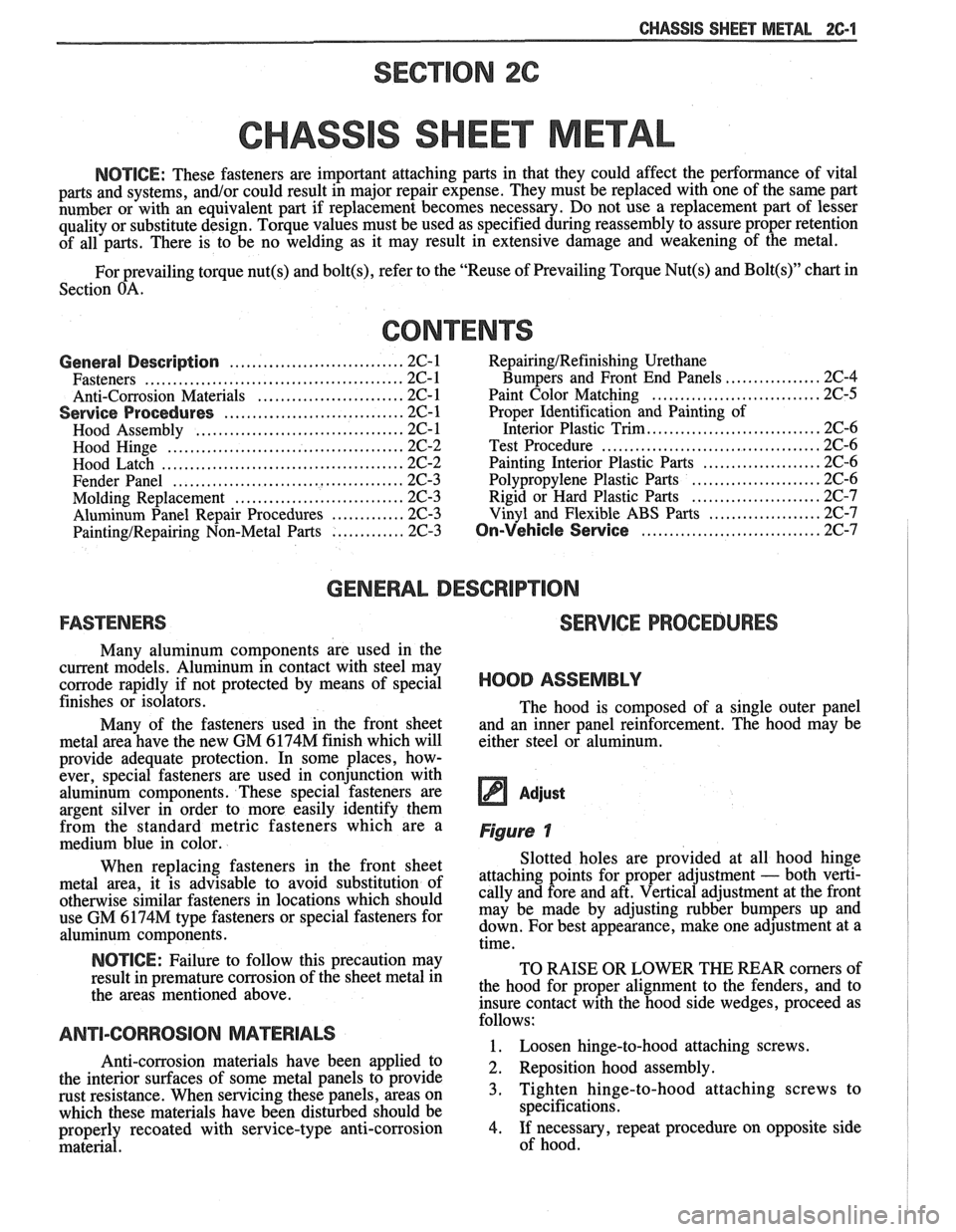
CHASSIS SHEET METAL 2C-1
SECTION %C
CHASS S SHEET METAL
NOTICE: These fasteners are important attaching parts in that they could affect the performance of vital
parts and systems,
andlor could result in major repair expense. They must be replaced with one of the same part
number or with an equivalent part if replacement becomes necessary. Do not use a replacement part of lesser
quality or substitute design. Torque values must be used as specified during reassembly to assure proper retention
of all parts. There is to be no welding as it may result in extensive damage and weakening of the metal.
For prevailing torque
nut(s) and bolt(s), refer to the "Reuse of Prevailing Torque Nut(s) and Bolt(s)" chart in
Section OA.
CONTENTS
............................... General Description 2C-1
.............................................. Fasteners 2C- I
.......................... Anti-Corrosion Materials 2C- 1
................................ Service Procedures 2C-1
..................................... Hood Assembly 2C-1
.......................................... Hood Hinge 2C-2
........................................... Hood Latch 2C-2
......................................... Fender Panel 2C-3
.............................. Molding Replacement 2C-3
Aluminum Panel Repair Procedures
............. 2C-3
PaintingIRepairing Non-Metal Parts ............. 2C-3
RepairingIRefinishing Urethane
Bumpers and Front End Panels
................. 2C-4
.............................. Paint Color Matching 2C-5
Proper Identification and Painting of
............................. Interior Plastic Trim.. 2C-6
....................................... Test Procedure 2C-6
Painting Interior Plastic Parts
..................... 2C-6
...................... Polypropylene Plastic Parts .2C-6
Rigid or Hard Plastic Parts ....................... 2C-7
Vinyl and Flexible ABS Parts
.................... 2C-7
On-Vehicle Sewice ................................ 2C-7
GENERAL DESCRIPTION
FASTENERS SERVICE PROCEDURES
Many aluminum components are used in the
current models. Aluminum in contact with steel may
corrode rapidly if not protected by means of special
finishes or isolators.
Many of the fasteners used in the front sheet
metal area have the new GM
6174M finish which will
provide adequate protection. In some places, how-
ever, special fasteners are used in conjunction with
aluminum components. These special fasteners are
argent silver in order to more easily identify them
from the standard metric fasteners which are a
medium blue in color.
When replacing fasteners in the front sheet
metal area, it is advisable to avoid substitution of
otherwise similar fasteners in locations which should
use GM
6174M type fasteners or special fasteners for
aluminum components.
NOTICE: Failure to follow this precaution may
result in premature corrosion of the sheet metal in
the areas mentioned above.
ANTI-CORROSION MATERIALS
Anti-corrosion materials have been applied to
the interior surfaces of some metal panels to provide
rust resistance. When servicing these panels, areas on
which these materials have been disturbed should be
properly
recoated with service-type anti-corrosion
material.
HOOD ASSEMBLY
The hood is composed of a single outer panel
and an inner panel reinforcement. The hood may be
either steel or aluminum.
Adjust
Figure 1
Slotted holes are provided at all hood hinge
attaching points for proper adjustment
- both verti-
cally and fore and aft. Vertical adjustment at the front
may be made by adjusting rubber bumpers up and
down. For best appearance, make one adjustment at a
time.
TO RAISE OR LOWER THE REAR comers of
the hood for proper alignment to the fenders, and to
insure contact with the hood side wedges, proceed as
follows:
1. Loosen hinge-to-hood attaching screws.
2. Reposition hood assembly.
3. Tighten hinge-to-hood attaching screws to
specifications.
4. If necessary, repeat procedure on opposite side
of hood.
Page 109 of 1825
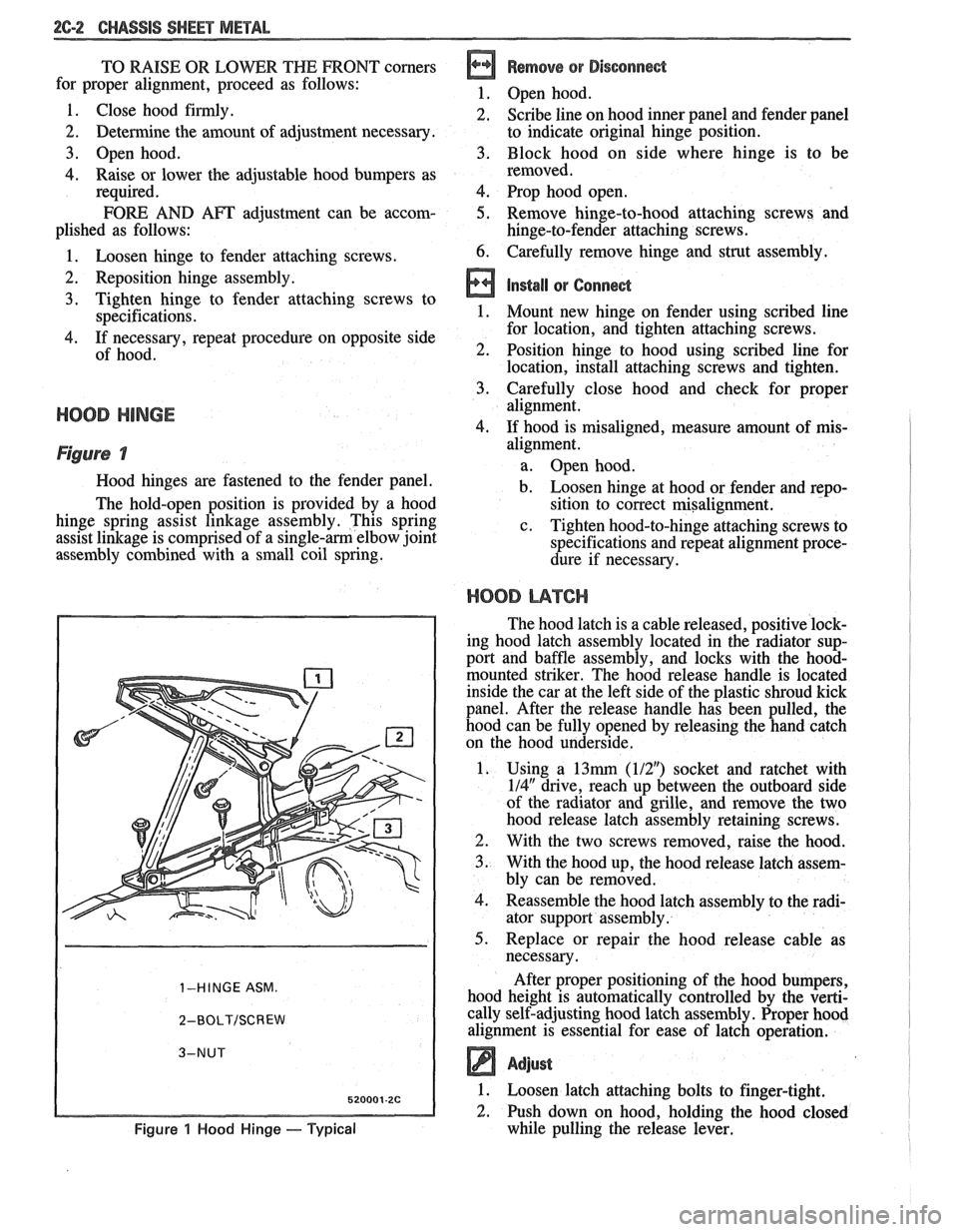
26-2 CHASSIS SHEET METAL
TO RAISE OR LOWER THE FRONT comers
for proper alignment, proceed as follows:
1. Close hood firmly.
2. Determine the amount of adjustment necessary.
3. Open hood.
4. Raise or lower the adjustable hood bumpers as
required.
FORE AND APT adjustment can be accom-
plished as follows:
1. Loosen hinge to fender attaching screws.
Remove or Disconnect
Open hood.
Scribe line on hood inner panel and fender panel
to indicate original hinge position.
Block hood on side where hinge is to be
removed.
Prop hood open.
Remove hinge-to-hood attaching screws and
hinge-to-fender attaching screws.
Carefully remove hinge and strut assembly.
- -
2. Reposition hinge assembly. install or Conned 3. Tighten hinge to fender attaching screws to
specifications. 1. Mount new hinge on fender using scribed line
4. If necessary, repeat procedure on opposite side for location,
and tighten attaching screws.
of hood. 2.
Position hinge to hood using scribed line for
location, install attaching screws and tighten.
3. Carefully close hood and check for proper
- - alignment.
4. If hood is misaligned, measure amount of
mis-
Figure 7
Hood hinges are fastened to the fender panel.
The hold-open position is provided by a hood
hinge spring assist linkage assembly. This spring
assist linkage is comprised of a
single-am elbow joint
assembly combined with a small coil spring.
1-HINGE ASM.
2-BOLT/SCREW
Figure 1 Hood Hinge - Typical
alignment.
a. Open hood.
b. Loosen hinge at hood or fender and repo-
sition to correct misalignment.
c. Tighten hood-to-hinge attaching screws to
specifications and repeat alignment proce-
dure if necessary.
HOOD L14TCI-I
The hood latch is a cable released, positive lock-
ing hood latch assembly located in the radiator sup-
port and baffle assembly, and locks with the
hood-
mounted striker. The hood release handle is located
inside the car at the left side of the plastic shroud kick
panel. After the release handle has been pulled, the
hood can be fully opened by releasing the hand catch
on the hood underside.
1. Using a
13mrn (112") socket and ratchet with
114" drive, reach up between the outboard side
of the radiator and grille, and remove the two
hood release latch assembly retaining screws.
2. With the two screws removed, raise the hood.
3. With the hood up, the hood release latch assem-
bly can be removed.
4. Reassemble the hood latch assembly to the radi-
ator support assembly.
5. Replace or repair the hood release cable as
necessary.
After proper positioning of the hood bumpers,
hood height is automatically controlled by the verti-
cally self-adjusting hood latch assembly. Proper hood
alignment is essential for ease of latch operation.
Adjust
1. Loosen latch attaching bolts to finger-tight.
2. Push down on hood, holding the hood closed
while pulling the release lever.
Page 110 of 1825
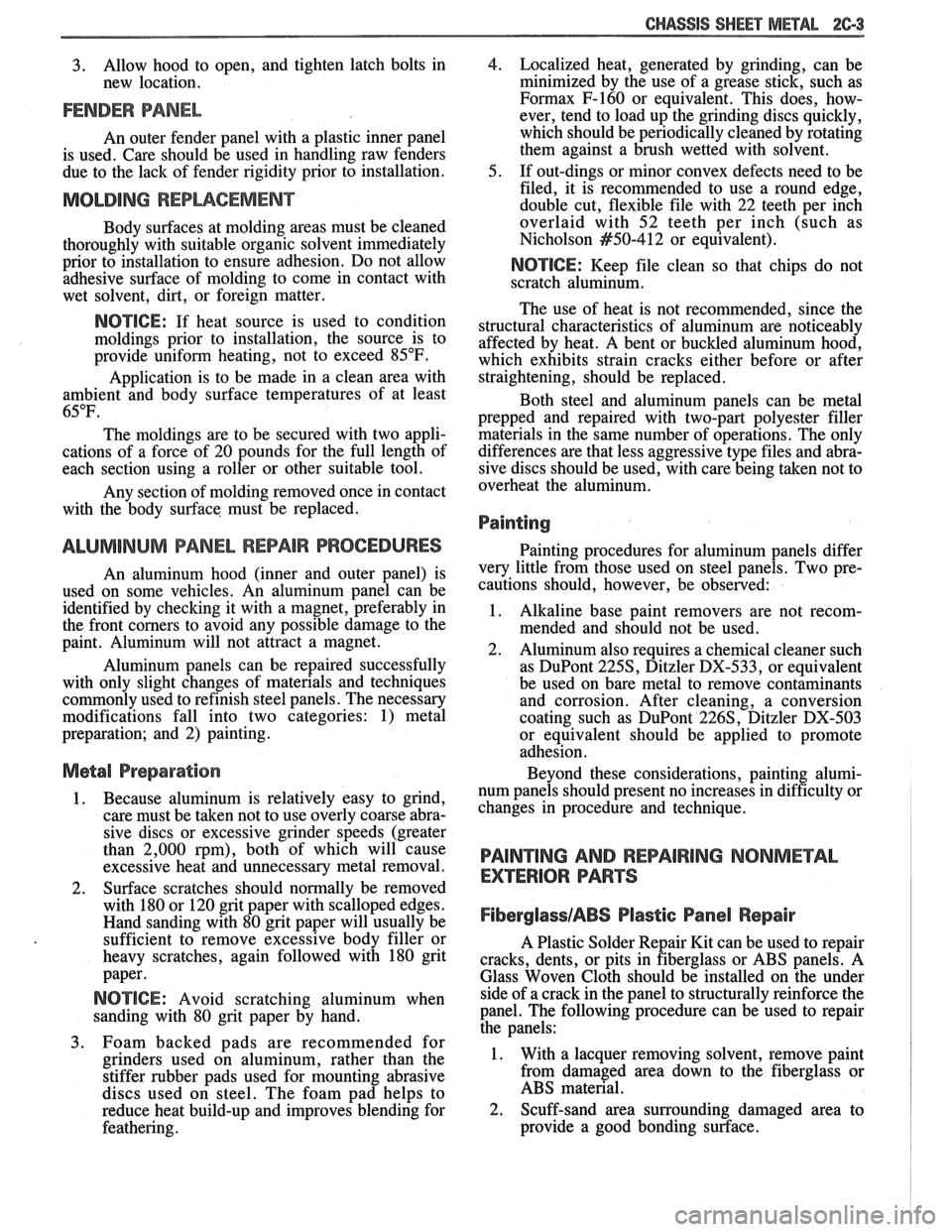
CHASSIS SHEET METAL 2C-3
3. Allow hood to open, and tighten latch bolts in
new location.
FENDER PANEL
An outer fender panel with a plastic inner panel
is used. Care should be used in handling raw fenders
due to the lack of fender rigidity prior to installation.
Body surfaces at molding areas must be cleaned
thoroughly with suitable organic solvent immediately
prior to installation to ensure adhesion. Do not allow
adhesive surface of molding to come in contact with
wet solvent, dirt, or foreign matter.
NO"FICE: If heat source is used to condition
moldings prior to installation, the source is to
provide
uniform heating, not to exceed 85°F.
Application is to be made in a clean area with
ambient and body surface temperatures of at least
65°F.
The moldings are to be secured with two appli-
cations of a force of 20 pounds for the full length of
each section using a roller or other suitable tool.
Any section of molding removed once in contact
with the body surface must be replaced.
ALUMINUM PANEL REPAIR PROCEDURES
An aluminum hood (inner and outer panel) is
used on some vehicles. An aluminum panel can be
identified by checking it with a magnet, preferably in
the front corners to avoid any possible damage to the
paint. Aluminum will not attract a magnet.
Aluminum panels can be repaired successfully
with only slight changes of materials and techniques
commonly used to refinish steel panels. The necessary
modifications fall into two categories: 1) metal
preparation; and 2) painting.
Metal Preparation
1. Because aluminum is relatively easy to grind,
care must be taken not to use overly coarse abra-
sive discs or excessive grinder speeds (greater
than 2,000 rpm), both of which will cause
excessive heat and unnecessary metal removal.
2. Surface scratches should normally be removed
with 180 or 120 grit paper with scalloped edges.
Hand sanding with 80 grit paper will usually be
sufficient to remove excessive body filler or
heavy scratches, again followed with 180 grit
paper.
NOTICE: Avoid scratching aluminum when
sanding with 80 grit paper by hand.
3. Foam backed pads are recommended for
grinders used on aluminum, rather than the
stiffer rubber pads used for mounting abrasive
discs used on steel. The foam pad helps to
reduce heat build-up and improves blending for
feathering.
4. Localized heat, generated by grinding, can be
minimized by the use of a grease stick, such as
Formax F-160 or equivalent. This does, how-
ever, tend to load up the grinding discs quickly,
which should be periodically cleaned by rotating
them against a brush wetted with solvent.
5. If out-dings or minor convex defects need to be
filed, it is recommended to use a round edge,
double cut, flexible file with 22 teeth per inch
overlaid with 52 teeth per inch (such as
Nicholson
#50-412 or equivalent).
NOTICE: Keep file clean so that chips do not
scratch aluminum.
The use of heat is not recommended, since the
structural characteristics of aluminum are noticeably
affected by heat. A bent or buckled aluminum hood,
which exhibits strain cracks either before or after
straightening, should be replaced.
Both steel and aluminum panels can be metal
prepped and repaired with two-part polyester filler
materials in the same number of operations. The only
differences are that less aggressive type files and abra- sive discs should be used, with care being taken not to
overheat the aluminum.
Painting
Painting procedures for aluminum panels differ
very little from those used on steel panels. Two pre-
cautions should, however, be observed:
1. Alkaline base paint removers are not recom-
mended and should not be used.
2. Aluminum also requires a chemical cleaner such
as
DuPont 2253, Ditzler DX-533, or equivalent
be used on bare metal to remove contaminants
and corrosion. After cleaning, a conversion
coating such as DuPont
226S, Ditzler DX-503
or equivalent should be applied to promote
adhesion.
Beyond these considerations, painting alumi-
num panels should present no increases in difficulty or
changes in procedure and technique.
PAINTING AND REPAIRING NONMETAL
EXTERIOR PARTS 1
FiberglassIABS Plastic Panel Repair ~
A Plastic Solder Repair Kit can be used to repair
cracks, dents, or pits in fiberglass or ABS panels. A
Glass Woven Cloth should be installed on the under
side of a crack in the panel to structurally reinforce the
panel. The following procedure can be used to repair
the panels:
1. With a lacquer removing solvent, remove paint
from damaged area down to the fiberglass or
, ABS material. I
2. Scuff-sand area surrounding damaged area to
provide a good bonding surface.