PONTIAC FIERO 1988 Service Repair Manual
Manufacturer: PONTIAC, Model Year: 1988, Model line: FIERO, Model: PONTIAC FIERO 1988Pages: 1825, PDF Size: 99.44 MB
Page 301 of 1825
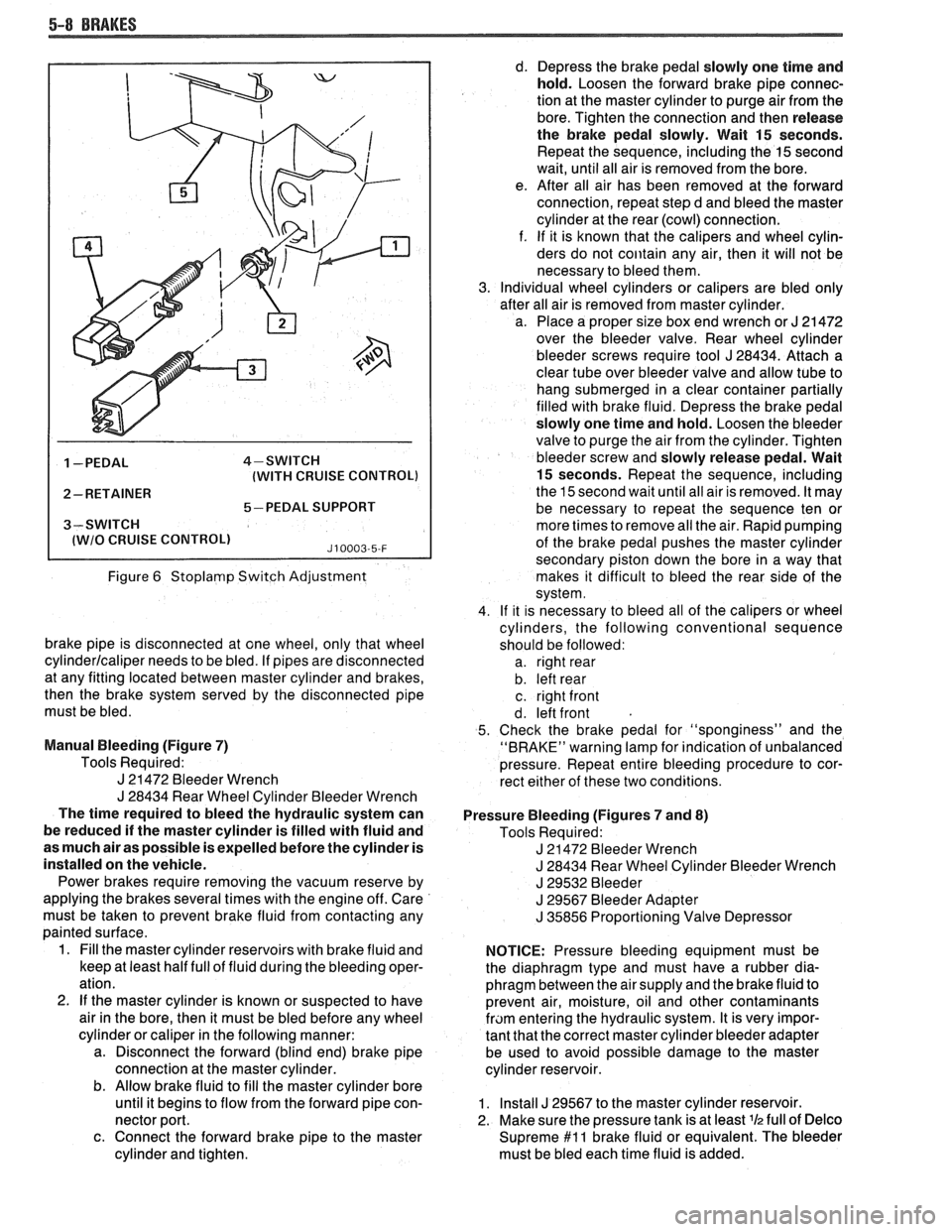
5-8 BRAKES
1 -PEDAL 4-SWITCH
(WITH CRUISE CONTROL)
2- RETAINER
5-PEDAL SUPPORT
3-SWITCH
I lWlO CRUISE CONTROLl J10003-5-F
Figure 6 Stoplamp Switch Adjustment
brake pipe is disconnected at one wheel, only that wheel
cylinderlcaliper needs to be bled. If pipes are disconnected
at any fitting located between master cylinder and brakes,
then the brake system served by the disconnected pipe
must be bled.
Manual Bleeding (Figure
7)
Tools Required:
J 21472 Bleeder Wrench
J 28434 Rear Wheel Cylinder Bleeder Wrench
The time required to bleed the hydraulic system can
be reduced if the master cylinder is filled with fluid and
as much air as possible is expelled before the cylinder is
installed on the vehicle.
Power brakes require removing the vacuum reserve by
applying the brakes several times with the engine off. Care
must be taken to prevent brake fluid from contacting any
painted surface.
1. Fill the master cylinder reservoirs with brake fluid and
keep at least half full of fluid during the bleeding oper-
ation.
2.
If the master cylinder is known or suspected to have
air in the bore, then it must be bled before any wheel
cylinder or caliper in the following manner:
a. Disconnect the forward (blind end) brake pipe
connection at the master cylinder.
b. Allow brake fluid to fill the master cylinder bore
until it begins to flow from the forward pipe con-
nector port.
c. Connect the forward brake pipe to the master
cylinder and tighten. d.
Depress the brake pedal slowly one time and
hold. Loosen the forward brake pipe connec-
tion at the master cylinder to purge air from the
bore. Tighten the connection and then release
the brake pedal slowly. Wait
15 seconds.
Repeat the sequence, including the
15 second
wait, until all air is removed from the bore.
e. After all air has been removed at the forward
connection, repeat step d and bleed the master
cylinder at the rear (cowl) connection.
f. If it is known that the calipers and wheel cylin-
ders do not
coiitain any air, then it will not be
necessary to bleed them.
Individual wheel cylinders or calipers are bled only
after all air is removed from master cylinder.
a. Place a proper size box end wrench or
J 21 472
over the bleeder valve. Rear wheel cylinder
bleeder screws require tool
J 28434. Attach a
clear tube over bleeder valve and allow tube to
hang submerged in a clear container partially
filled with brake fluid. Depress the brake pedal
slowly one time and hold. Loosen the bleeder
valve to purge the air from the cylinder. Tighten
bleeder screw and slowly release pedal. Wait
15 seconds. Repeat the sequence, including
the 15 second wait until all air is removed. It may
be necessary to repeat the sequence ten or
more times to remove all the air. Rapid pumping
of the brake pedal pushes the master cylinder
secondary piston down the bore in a way that
makes it difficult to bleed the rear side of the
system.
If it is necessary to bleed all of the calipers or wheel
cylinders, the following conventional sequence
should be followed: a. right rear
b. left rear
c. right front
d. left front
Check the brake pedal for "sponginess" and the
"BRAKE" warning lamp for indication of unbalanced
pressure. Repeat entire bleeding procedure to cor-
rect either of these two conditions.
Pressure Bleeding (Figures
7 and 8)
Tools Required:
J 21472 Bleeder Wrench
J 28434 Rear Wheel Cylinder Bleeder Wrench
J 29532 Bleeder
J 29567 Bleeder Adapter
J 35856 Proportioning Valve Depressor
NOTICE: Pressure bleeding equipment must be
the diaphragm type and must have a rubber dia-
phragm between the air supply and the brake fluid to
prevent air, moisture, oil and other contaminants
fram entering the hydraulic system. It is very impor-
tant that the correct master cylinder bleeder adapter
be used to avoid possible damage to the master
cylinder reservoir.
1. Install J 29567 to the master cylinder reservoir.
2. Make sure the pressure tank is at least
lh full of Delco
Supreme $1 1 brake fluid or equivalent. The bleeder
must be bled each time fluid is added.
Page 302 of 1825
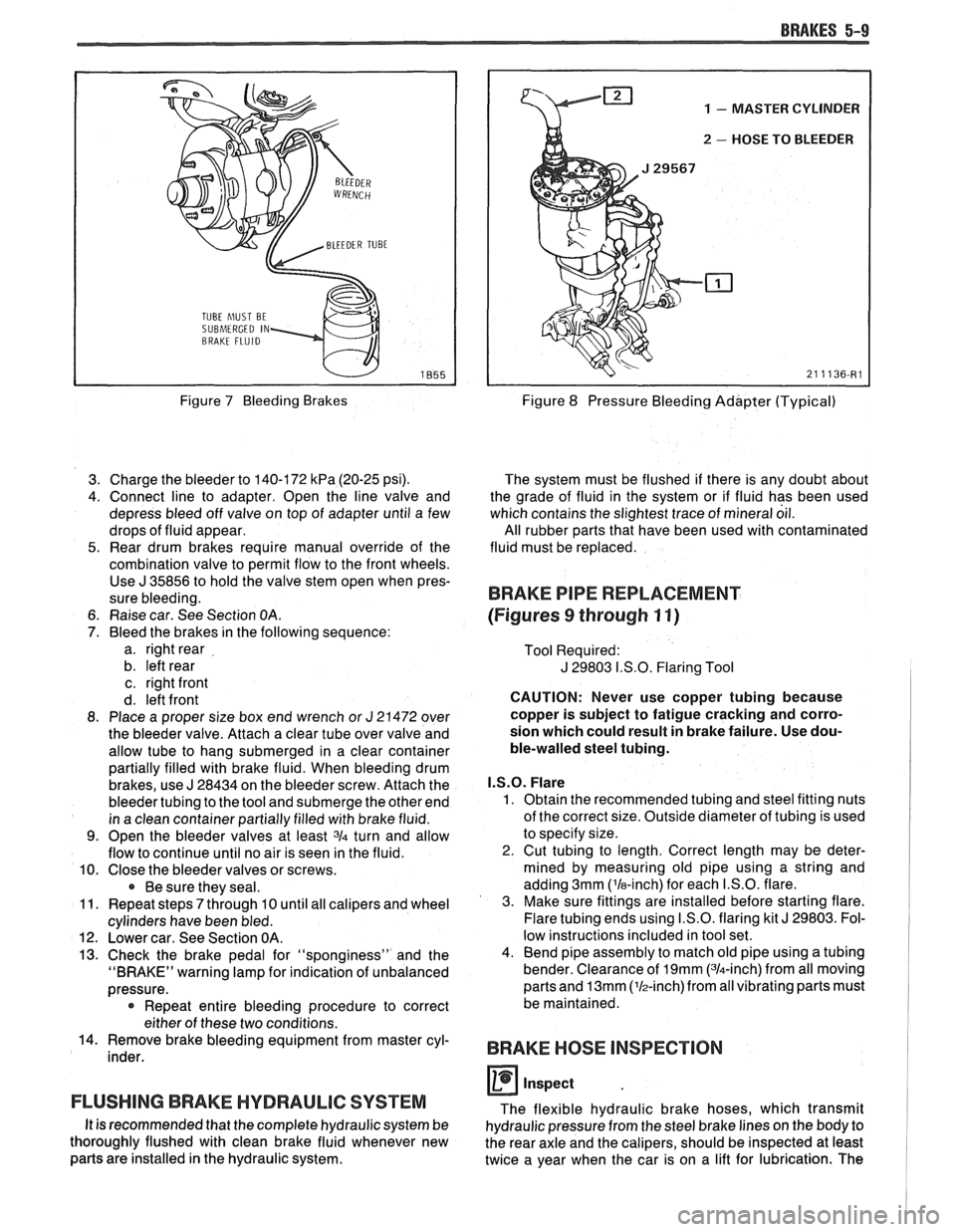
BRAKES 5-9
TUBE hlUST BE
SUBMERGED IN
Figure 7 Bleeding Brakes
3. Charge the bleeder to 140-172
kPa (20-25 psi).
4. Connect line to adapter. Open the line valve and
depress bleed off valve on top of adapter until a few
drops of fluid appear.
5. Rear drum brakes require manual override of the
combination valve to permit flow to the front wheels. Use
J 35856 to hold the valve stem open when pres-
sure bleeding.
6. Raise car. See Section
OA.
7. Bleed the brakes in the following sequence:
a. right rear
b. left rear
c. right front
d. left front
8. Place a proper size box end wrench or
J 21472 over
the bleeder valve. Attach a clear tube over valve and
allow tube to hang submerged in a clear container
partially filled with brake fluid. When bleeding drum
brakes, use
J 28434 on the bleeder screw. Attach the
bleeder tubing to the tool and submerge the other end
in a clean container partially filled with brake fluid.
9. Open the bleeder valves at least 3/4 turn and allow
flow to continue until no air is seen in the fluid.
10. Close the bleeder valves or screws.
Be sure they seal.
11. Repeat steps
7 through 10 until all calipers and wheel
cylinders have been bled.
12. Lower car. See Section OA.
13. Check the brake pedal for "sponginess" and the
"BRAKE" warning lamp for indication of unbalanced
pressure.
* Repeat entire bleeding procedure to correct
either of these two conditions.
14. Remove brake bleeding equipment from master cyl-
inder.
FLUSHING BRAKE HYDRAULIC SYSTEM
It is recommended that the complete hydraulic system be
thoroughly flushed with clean brake fluid whenever new
parts are installed in the hydraulic system.
1 - MASTER CYLINDER
u 2 - HOSE TO BLEEDER
Figure 8 Pressure Bleeding Adapter (Typical)
The system must be flushed if there is any doubt about
the grade of fluid in the system or if fluid has been used
which contains the slightest trace of mineral oil.
All rubber parts that have been used with contaminated
fluid must be replaced.
BRAKE PIPE REPLACEMENT
(Figures
9 through 11)
Tool Required:
J 29803 I.S.O. Flaring Tool
CAUTION: Never use copper tubing because
copper is subject to fatigue cracking and corro-
sion which could result in brake failure. Use dou-
ble-walled steel tubing.
I.S.O. Flare
1. Obtain the recommended tubing and steel fitting nuts
of the correct size. Outside diameter of tubing is used
to specify size.
2. Cut tubing to length. Correct length may be deter-
mined by measuring old pipe using a string and
adding 3mm ('la-inch) for each I.S.O. flare.
3. Make sure fittings are installed before starting flare.
Flare tubing ends using I.S.O. flaring kit
J 29803. Fol-
low instructions included in tool set.
4. Bend pipe assembly to match old pipe using a tubing
bender. Clearance of
19mm (314-inch) from all moving
parts and
13mm (lh-inch)from all vibrating parts must
be maintained.
BRAKE HOSE INSPECTION
0 inspect
The flexible hydraulic brake hoses, which transmit
hydraulic pressure from the steel brake lines on the body to
the rear axle and the calipers, should be inspected at least
twice a year when the car is on a lift for lubrication. The
Page 303 of 1825
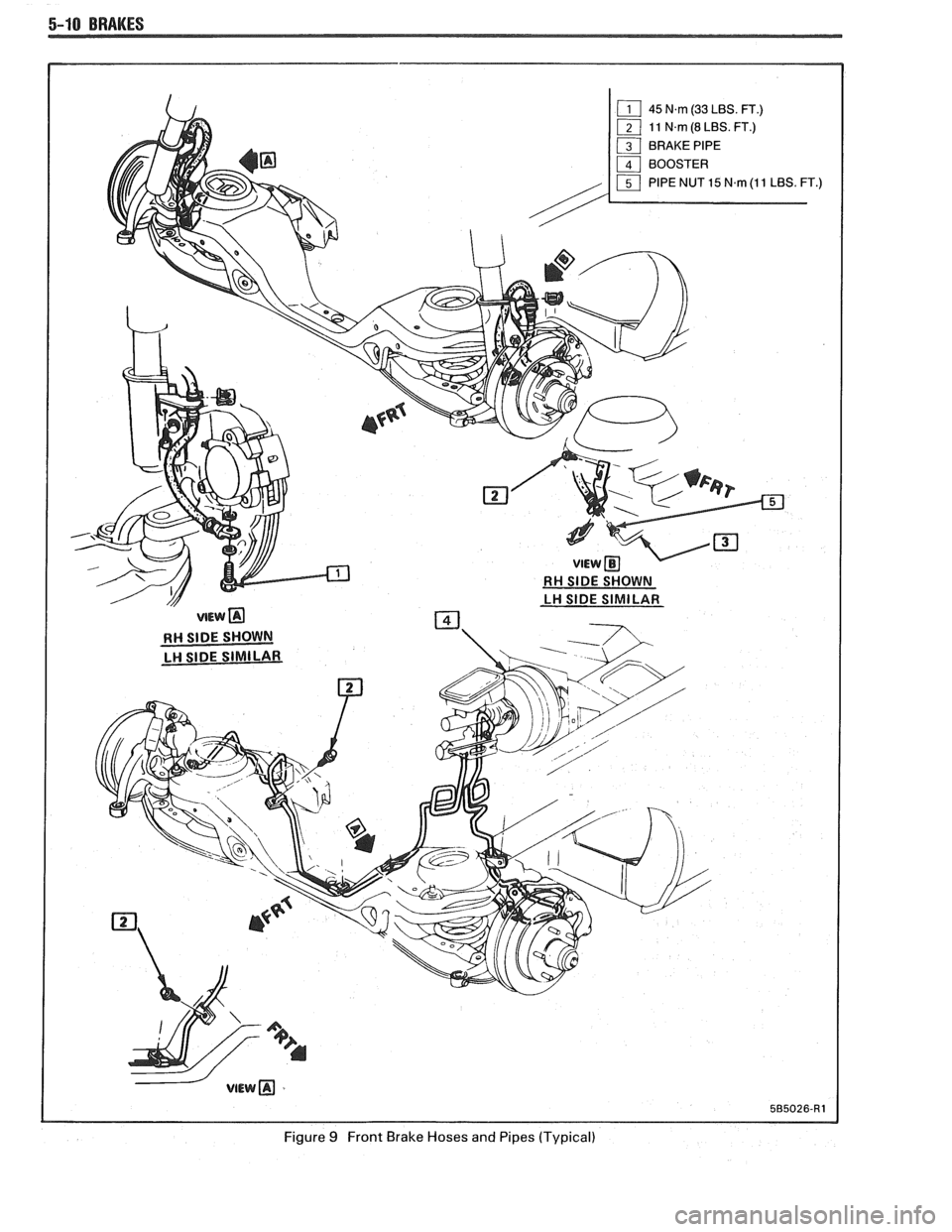
5-10 BRAKES
-
Figure 9 Front Brake Hoses and Pipes (Typical)
Page 304 of 1825
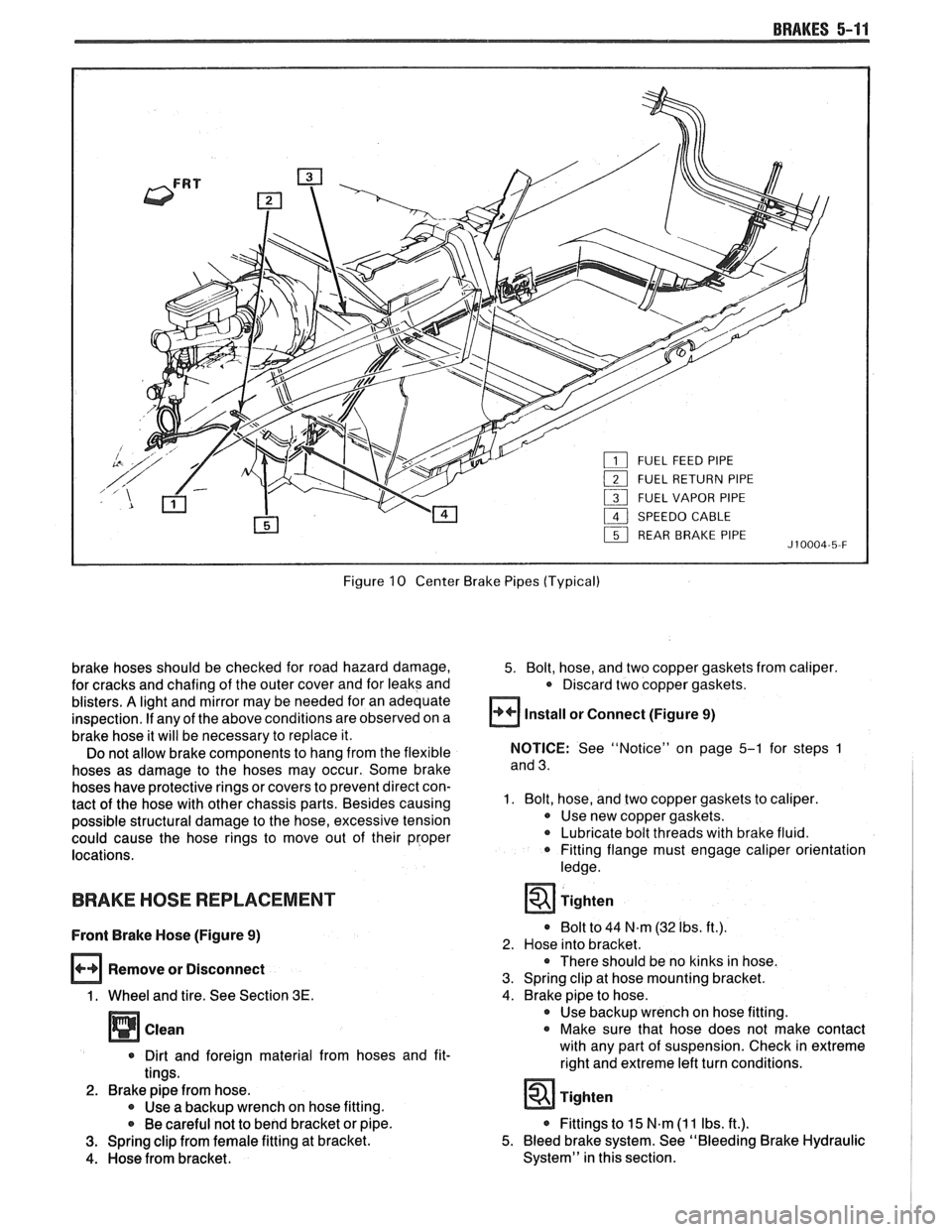
BRAKES 5-11
Figure 10 Center Brake Pipes (Typical)
brake hoses should be checked for road hazard damage,
for cracks and chafing of the outer cover and for leaks and
blisters.
A light and mirror may be needed for an adequate
inspection.
If any of the above conditions are observed on a
brake hose it will be necessary to replace it.
Do not allow brake components to hang from the flexible
hoses as damage to the hoses may occur. Some brake
hoses have protective rings or covers to prevent direct con-
tact of the hose with other chassis parts. Besides causing
possible structural damage to the hose, excessive tension
could cause the hose rings to move out of their proper
locations.
BRAKE HOSE REPLACEMENT
Front Brake Hose (Figure 9)
Remove or Disconnect
1. Wheel and tire. See Section 3E.
Clean
* Dirt and foreign material from hoses and fit-
tings.
2. Brake pipe from hose. 0 Use a backup wrench on hose fitting.
* Be careful not to bend bracket or pipe.
3. Spring clip from female fitting at bracket.
4. Hose from bracket.
5. Bolt, hose, and two copper gaskets from caliper.
* Discard two copper gaskets.
Install or Connect (Figure 9)
NOTICE: See "Notice" on page 5-1 for steps 1
and 3.
1. Bolt, hose, and two copper gaskets to caliper.
0 Use new copper gaskets.
Lubricate bolt threads with brake fluid.
0 Fitting flange must engage caliper orientation
ledge.
Tighten
0 Bolt to 44 N.m (32 Ibs. ft.).
2. Hose into bracket.
There should be no kinks in hose.
3. Spring clip at hose mounting bracket.
4. Brake pipe to hose. 0 Use backup wrench on hose fitting.
0 Make sure that hose does not make contact
with any part of suspension. Check in extreme
right and extreme left turn conditions.
* Fittings to 15 N.m (1 1 Ibs. ft.).
5. Bleed brake system. See "Bleeding Brake Hydraulic
System" in this section.
Page 305 of 1825
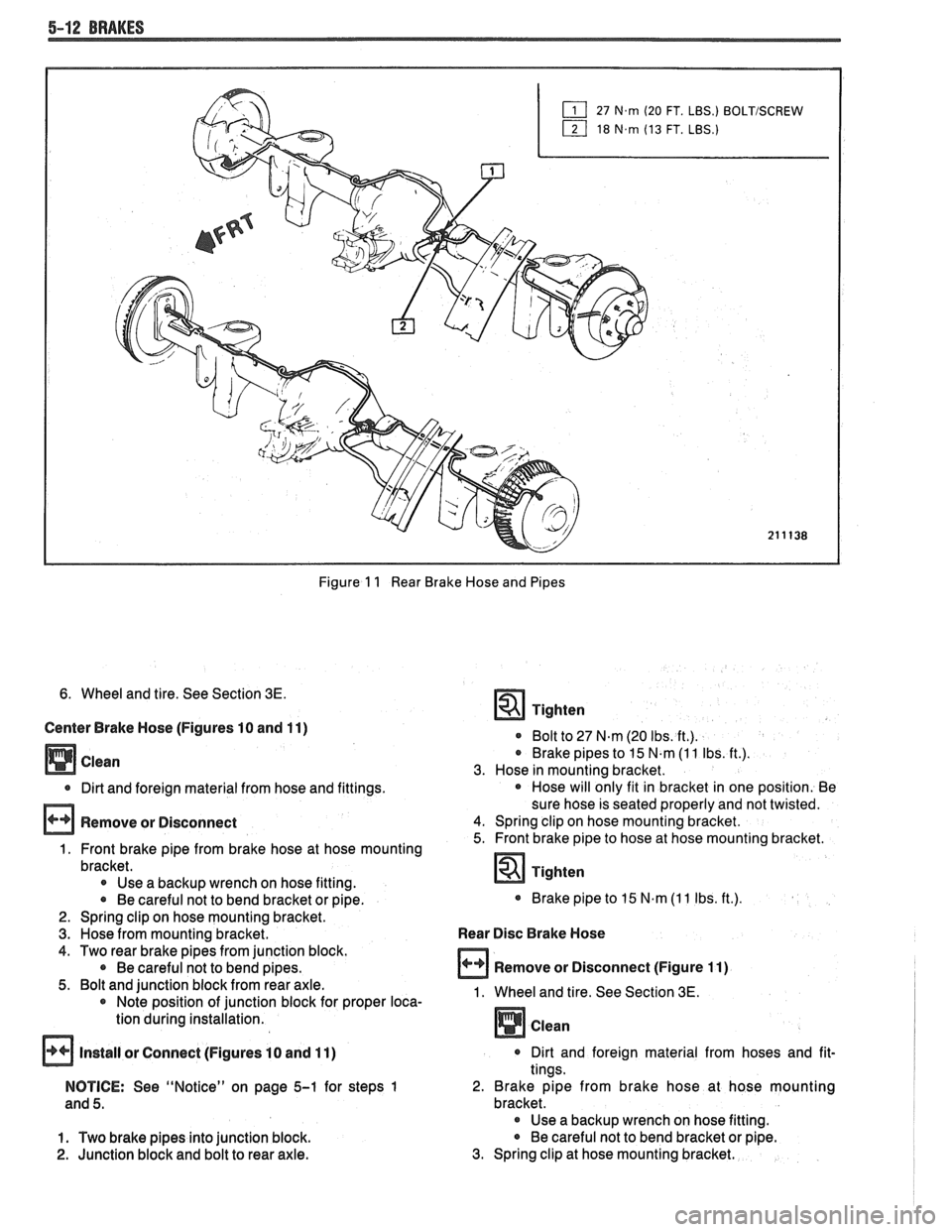
5-12 BRAKES
27 27.m (20 FT. LBS.) BOLTISCREW
1 18 18.m (13 FT. LBS.)
Figure 1 1 Rear Brake Hose and Pipes
6. Wheel and tire. See Section 3E.
Center Brake Hose (Figures 10 and 11)
0 Dirt and foreign material from hose and fittings.
Remove or Disconnect
1. Front brake pipe from brake hose at hose mounting
bracket.
* Use a backup wrench on hose fitting.
0 Be careful not to bend bracket or pipe.
2. Spring clip on hose mounting bracket.
3. Hose from mounting bracket.
4. Two rear brake pipes from junction block. 0 Be careful not to bend pipes.
5. Bolt and junction block from rear axle.
Note position of junction block for proper loca-
tion during installation.
* Bolt to 27 N.m (20 Ibs. ft,).
0 Brake pipes to 15 N.m (1 1 Ibs. ft.).
3. Hose in mounting bracket.
Hose will only fit in bracket in one position. Be
sure hose is seated properly and not twisted.
4. Spring clip on hose mounting bracket.
5. Front brake pipe to hose at hose mounting bracket.
Tighten
0 Brake pipe to 15 N.m (1 1 Ibs. ft.).
Rear Disc Brake Hose
Remove or Disconnect (Figure
11)
1. Wheel and tire. See Section 3E.
Install or Connect (Figures 10 and 11) 0 Dirt and foreign material from hoses and fit-
tings.
NOTICE: See "Notice" on page
5-1 for steps 1 2. Brake pipe from brake hose at hose mounting
and
5. bracket. Use a backup wrench on hose fitting.
1. Two brake pipes into junction block. Be
careful not to bend bracket or pipe.
2. Junction block and bolt to rear axle. 3. Spring clip at hose mounting bracket.
Page 306 of 1825
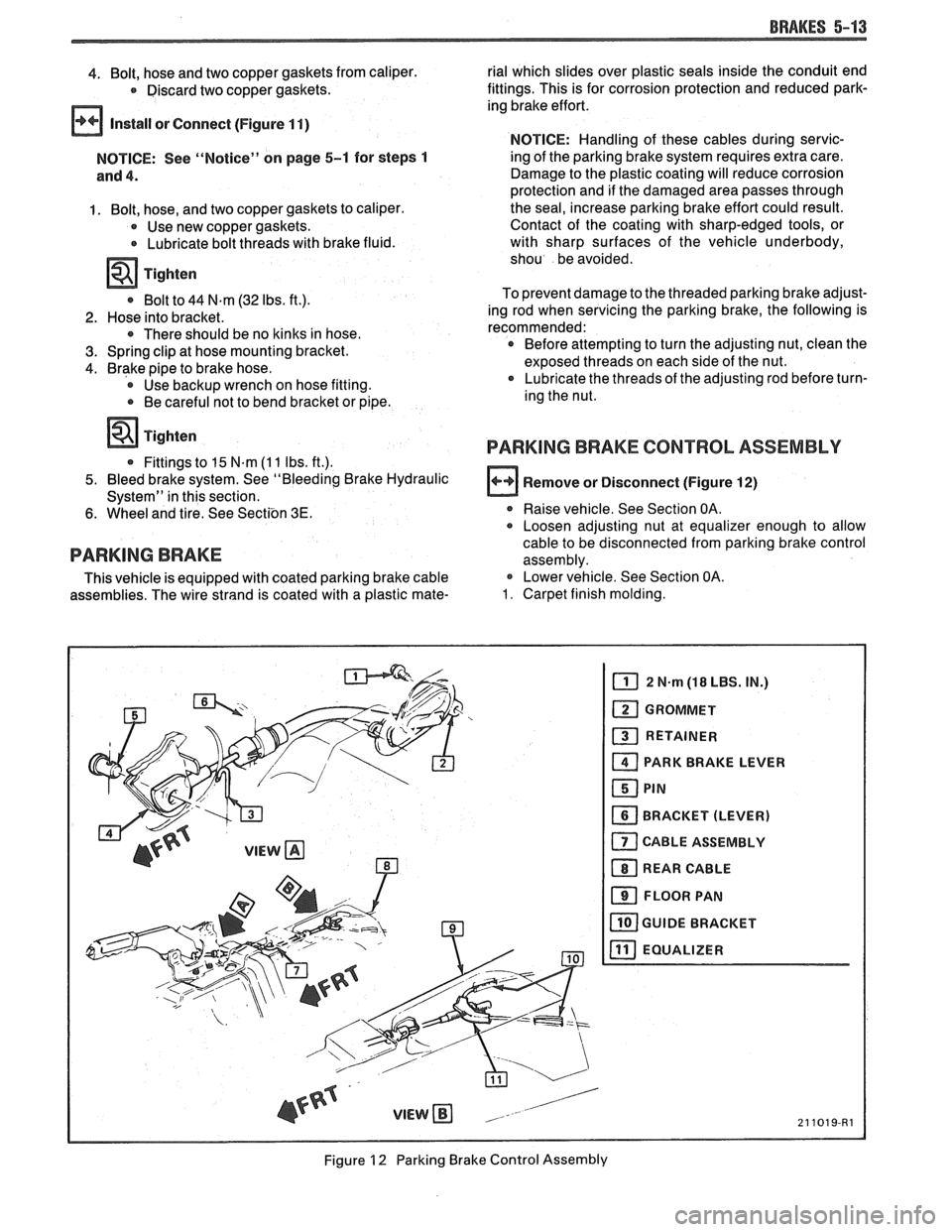
BRAKES 5-13
4. Bolt, hose and two copper gaskets from caliper.
Discard two copper gaskets.
Install or Connect (Figure 1 1)
NOTICE: See "Notice" on page 5-1 for steps 1
and 4.
1. Bolt, hose, and two copper gaskets to caliper.
0 Use new copper gaskets. 0 Lubricate bolt threads with brake fluid.
0 Bolt to 44 N.m (32 Ibs. ft.).
2. Hose into bracket. r There should be no kinks in hose.
3. Spring clip at hose mounting bracket.
4. Brake pipe to brake hose.
Use backup wrench on hose fitting.
0 Be careful not to bend bracket or pipe.
Tighten
Fittings to 15 N.m (1 1 Ibs. ft.).
5. Bleed brake system. See "Bleeding Brake Hydraulic
System" in this section.
6. Wheel and tire. See Sectbn 3E.
PARKING BRAKE
This vehicle is equipped with coated parking brake cable
assemblies. The wire strand is coated with a plastic mate- rial which slides over plastic seals inside
the conduit end
fittings. This is for corrosion protection and reduced park-
ing brake effort.
NOTICE: Handling of these cables during servic-
ing of the parking brake system requires extra care.
Damage to the plastic coating will reduce corrosion
protection and if the damaged area passes through
the seal, increase parking brake effort could result.
Contact of the coating with sharp-edged tools, or
with sharp surfaces of the vehicle underbody,
shou be avoided.
To prevent damage to the threaded parking brake adjust-
ing rod when servicing the parking brake, the following is
recommended:
r Before attempting to turn the adjusting nut, clean the
exposed threads on each side of the nut.
Lubricate the threads of the adjusting rod before turn-
ing the nut.
PARKlNG BRAKE CONTROL ASSEMBLY
Remove or Disconnect (Figure 12)
Raise vehicle. See Section OA.
@ Loosen adjusting nut at equalizer enough to allow
cable to be disconnected from parking brake control
assembly. Lower vehicle. See Section OA.
1. Carpet finish molding.
2 N-m (18 LBS. IN.)
a PARK BRAKE LEVER
BRACKET (LEVER)
CABLE ASSEMBLY
Figure 12 Parking Brake Control Assembly
Page 307 of 1825
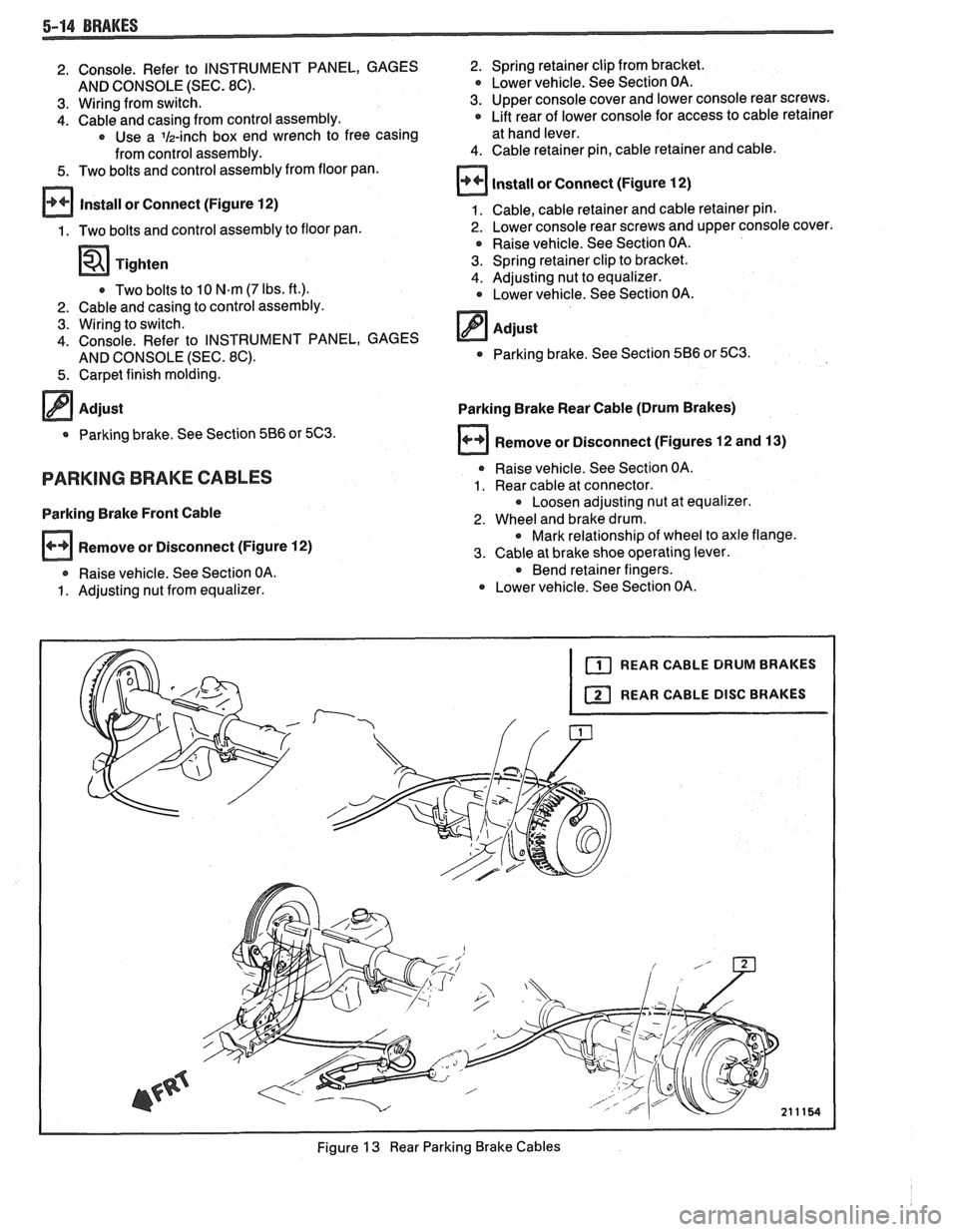
2. Console. Refer to INSTRUMENT PANEL, GAGES
AND CONSOLE (SEC.
8C).
3. Wiring from switch.
4. Cable and casing from control assembly. * Use a lh-inch box end wrench to free casing
from control assembly.
5. Two bolts and control assembly from floor pan.
Install or Connect (Figure 12)
1. Two bolts and control assembly to floor pan.
Two bolts to 10
N.m (7 Ibs. ft.).
2. Cable and casing to control assembly.
3. Wiring to switch.
4. Console. Refer to INSTRUMENT PANEL, GAGES
AND CONSOLE (SEC.
8C).
5. Carpet finish molding.
@ Parking brake. See Section 566 or 5C3.
PARKING BRAKE CABLES
Parking Brake Front Cable
Remove or Disconnect (Figure 12)
@ Raise vehicle. See Section OA.
1. Adjusting nut from equalizer.
2. Spring retainer clip from bracket. * Lower vehicle. See Section OA.
3. Upper console cover and lower console rear screws.
@ Lift rear of lower console for access to cable retainer
at hand lever.
4. Cable retainer pin, cable retainer and cable.
Install or Connect (Figure 12)
1. Cable, cable retainer and cable retainer pin.
2. Lower console rear screws and upper console cover.
Raise vehicle. See Section OA.
3. Spring retainer clip to bracket.
4. Adjusting nut to equalizer.
Lower vehicle. See Section OA.
Adjust
Parking brake. See Section 586 or 5C3.
Parking Brake Rear Cable (Drum Brakes)
Remove or Disconnect (Figures 12 and
13)
* Raise vehicle. See Section OA.
1. Rear cable at connector.
Loosen adjusting nut at equalizer.
2. Wheel and brake drum. * Mark relationship of wheel to axle flange.
3. Cable at brake shoe operating lever.
* Bend retainer fingers.
Lower vehicle. See Section OA.
Figure
13 Rear Parking Brake Cables
Page 308 of 1825
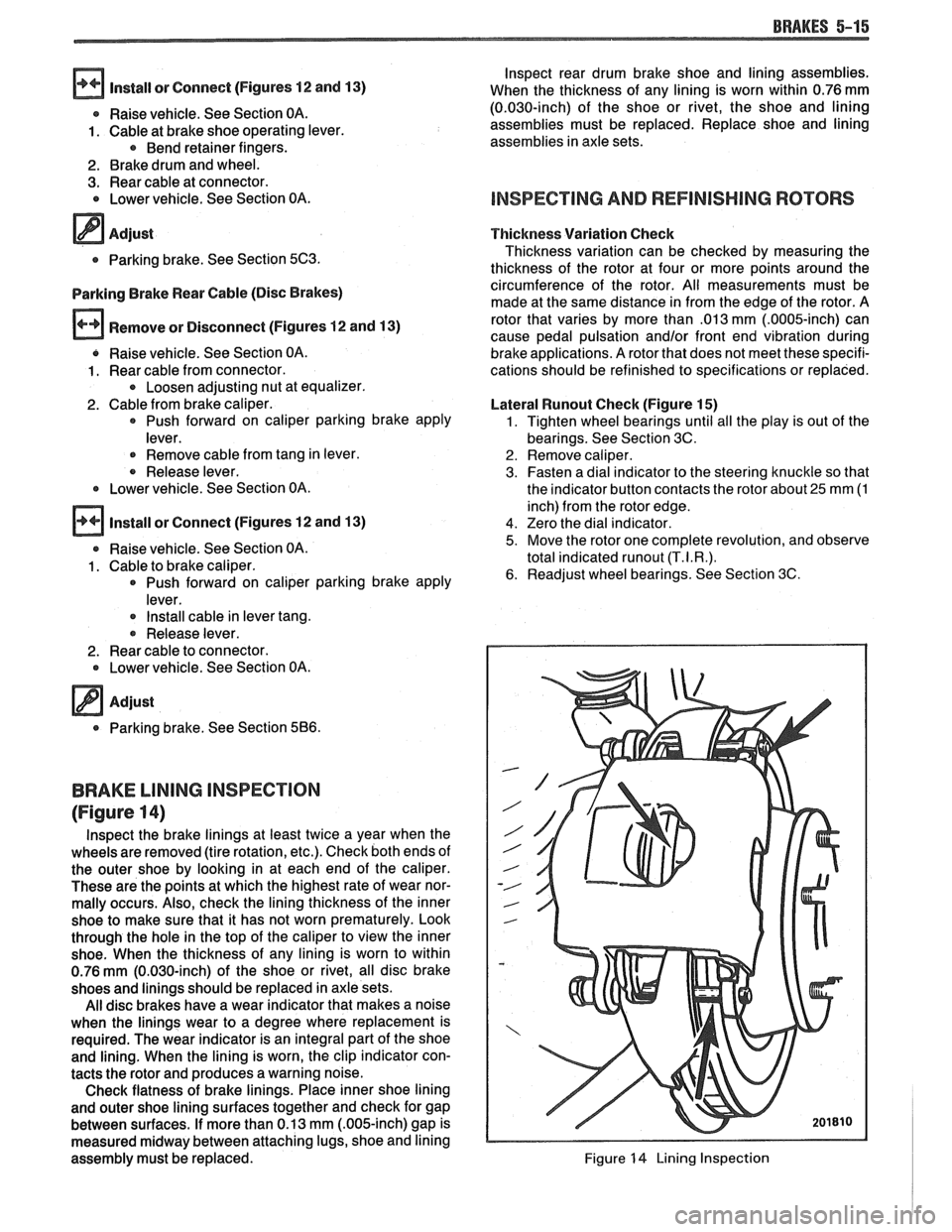
BRAKES 5-15
lnspect rear drum brake shoe and lining assemblies.
Install or Connect (Figures 12 and 13)
When the thickness of any lining is worn within 0.76 mm
Raise vehicle. See Section OA. (0.030-inch)
of the shoe or rivet, the shoe and lining
1. Cable at brake shoe operating lever. assemblies must
be replaced. Replace shoe and lining
Bend retainer fingers. assemblies
in axle sets.
2. Brake drum and wheel.
3. Rear cable at connector.
0 Lower vehicle. See Section oA. INSPECTING AND REFINISHING ROTORS
Adjust
0 Parking brake. See Section 5C3.
Parking Brake Rear Cable (Disc Brakes)
Remove or Disconnect (Figures
12 and 13)
0 Raise vehicle. See Section OA.
1. Rear cable from connector.
0 Loosen adjusting nut at equalizer.
2. Cable from brake caliper.
Push forward on caliper parking brake apply
lever.
@ Remove cable from tang in lever.
Release lever.
Lower vehicle. See Section OA.
Install or Connect (Figures 12 and
13)
Raise vehicle. See Section OA.
1. Cable to brake caliper.
0 Push forward on caliper parking brake apply
lever.
0 Install cable in lever tang.
Release lever.
2. Rear cable to connector. 0 Lower vehicle. See Section OA.
0 Parking brake. See Section 586.
BRAKE LINING INSPECTION
(Figure 14)
lnspect the brake linings at least twice a year when the
wheels are removed (tire rotation, etc.). Check both ends of
the outer shoe by looking in at each end of the caliper.
These are the points at which the highest rate of wear nor-
mally occurs. Also, check the lining thickness of the inner
shoe to make sure that it has not worn prematurely. Look
through the hole in the top of the caliper to view the inner
shoe. When the thickness of any lining is worn to within
0.76
mm (0.030-inch) of the shoe or rivet, all disc brake
shoes and linings should be replaced in axle sets.
All disc brakes have a wear indicator that makes a noise
when the linings wear to a degree where replacement is
required. The wear indicator is an integral part of the shoe
and lining. When the lining is worn, the clip indicator con-
tacts the rotor and produces a warning noise.
Check flatness of brake linings. Place inner shoe lining
and outer shoe lining surfaces together and check for gap
between surfaces. If more than 0.13 mm
(.OO&inch) gap is
measured midway between attaching lugs, shoe and lining
assembly must be replaced. Thickness
Variation Check
Thickness variation can be checked by measuring the
thickness of the rotor at four or more points around the
circumference of the rotor. All measu'rements must be
made at the same distance in from the edge of the rotor. A
rotor that varies by more than
.013 mm (.0005-inch) can
cause pedal pulsation
and/or front end vibration during
brake applications. A rotor that does not meet these specifi-
cations should be refinished to specifications or replaced.
Lateral
Wunout Check (Figure 15)
1. Tighten wheel bearings until all the play is out of the
bearings. See Section 3C.
2. Remove caliper.
3. Fasten a dial indicator to the steering knuckle so that
the indicator button contacts the rotor about
25 mm (1
inch) from the rotor edge.
4. Zero the dial indicator.
5. Move the rotor one complete revolution, and observe
total indicated
runout (T.I.R.).
6. Readjust wheel bearings. See Section 3C.
Figure 14 Lining Inspection
Page 309 of 1825
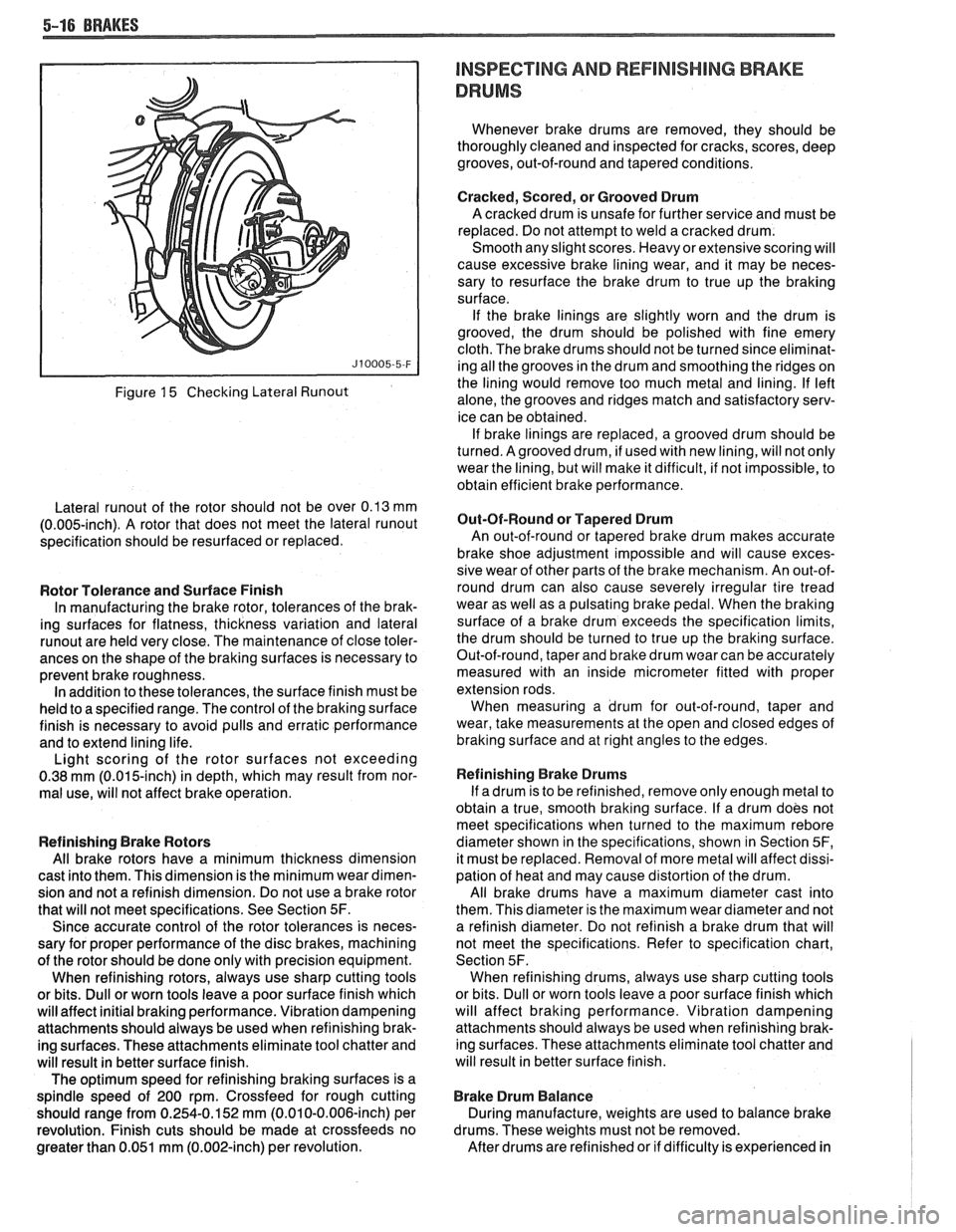
5-16 BRAKES
Figure 15 Checking Lateral Runout
Lateral runout of the rotor should not be over 0.13 mm
(0.005-inch). A rotor that does not meet the lateral runout
specification should be resurfaced or replaced.
Rotor Tolerance and Surface Finish
In manufacturing the brake rotor, tolerances of the brak-
ing surfaces for flatness, thickness variation and lateral
runout are held very close. The maintenance of close toler-
ances on the shape of the braking surfaces is necessary to
prevent brake roughness. In addition to these tolerances, the surface finish must be
held to a specified range. The control of the braking surface
finish is necessary to avoid pulls and erratic performance
and to extend lining life.
Light scoring of the rotor surfaces not exceeding
0.38
mrn (0.015-inch) in depth, which may result from nor-
mal use, will not affect brake operation.
Refinishing Brake Rotors
All brake rotors have a minimum thickness dimension
cast into them. This dimension is the minimum wear dimen-
sion and not a refinish dimension. Do not use a brake rotor
that will not meet specifications. See Section
5F.
Since accurate control of the rotor tolerances is neces-
sary for proper performance of the disc brakes, machining
of the rotor should be done only with precision equipment.
When refinishing rotors, always use sharp cutting tools
or bits. Dull or worn tools leave a poor surface finish which
will affect initial braking performance. Vibration dampening
attachments should always be used when refinishing brak-
ing surfaces. These attachments eliminate tool chatter and
will result in better surface finish.
The optimum speed for refinishing braking surfaces is a
spindle speed of 200 rpm. Crossfeed for rough cutting
should range from 0.254-0.152 mm (0.010-0.006-inch) per
revolution. Finish cuts should be made at crossfeeds no
greater than 0.051 mm (0.002-inch) per revolution.
INSPECTING AND REFlNlSHlMG BRAKE
DRUMS
Whenever brake drums are removed, they should be
thoroughly cleaned and inspected for cracks, scores, deep
grooves, out-of-round and tapered conditions.
Cracked, Scored, or Grooved Drum
A cracked drum is unsafe for further service and must be
replaced. Do not attempt to weld a cracked drum.
Smooth any slight scores. Heavy or extensive scoring will
cause excessive brake lining wear, and it may be neces-
sary to resurface the brake drum to true up the braking
surface.
If the brake linings are slightly worn and the drum is
grooved, the drum should be polished with fine emery
cloth. The brake drums should not be turned since eliminat-
ing all the grooves in the drum and smoothing the ridges on
the lining would remove too much metal and lining. If left
alone, the grooves and ridges match and satisfactory serv-
ice can be obtained. If brake linings are replaced, a grooved drum should be
turned. Agrooved drum, if used with new lining, will not only
wear the lining, but will make it difficult, if not impossible, to
obtain efficient brake performance.
But-Of-Round or Tapered Drum
An out-of-round or tapered brake drum makes accurate
brake shoe adjustment impossible and will cause exces-
sive wear of other parts of the brake mechanism. An out-of-
round drum can also cause severely irregular tire tread
wear as well as a pulsating brake pedal. When the braking
surface of a brake drum exceeds the specification limits,
the drum should be turned to true up the braking surface.
Out-of-round, taper and brake drum wear can be accurately
measured with an inside micrometer fitted with proper
extension rods. When measuring a drum for out-of-round, taper and
wear, take measurements at the open and closed edges of
braking surface and at right angles to the edges.
Refinishing Brake Drums
If adrum is to be refinished, remove only enough metal to
obtain a true, smooth braking surface. If a drum does not
meet specifications when turned to the maximum
rebore
diameter shown in the specifications, shown in Section 5F,
it must be replaced. Removal of more metal will affect dissi-
pation of heat and may cause distortion of the drum.
All brake drums have a maximum diameter cast into
them. This diameter is the maximum wear diameter and not
a refinish diameter. Do not refinish a brake drum that will
not meet the specifications. Refer to specification chart,
Section 5F. When refinishing drums, always use sharp cutting tools
or bits. Dull or worn tools leave a poor surface finish which
will affect braking performance. Vibration dampening
attachments should always be used when refinishing brak-
ing surfaces. These attachments eliminate tool chatter and
will result in better surface finish.
Brake Drum Balance
During manufacture, weights are used to balance brake
drums. These weights must not be removed.
After drums are refinished or if difficulty is experienced in
Page 310 of 1825
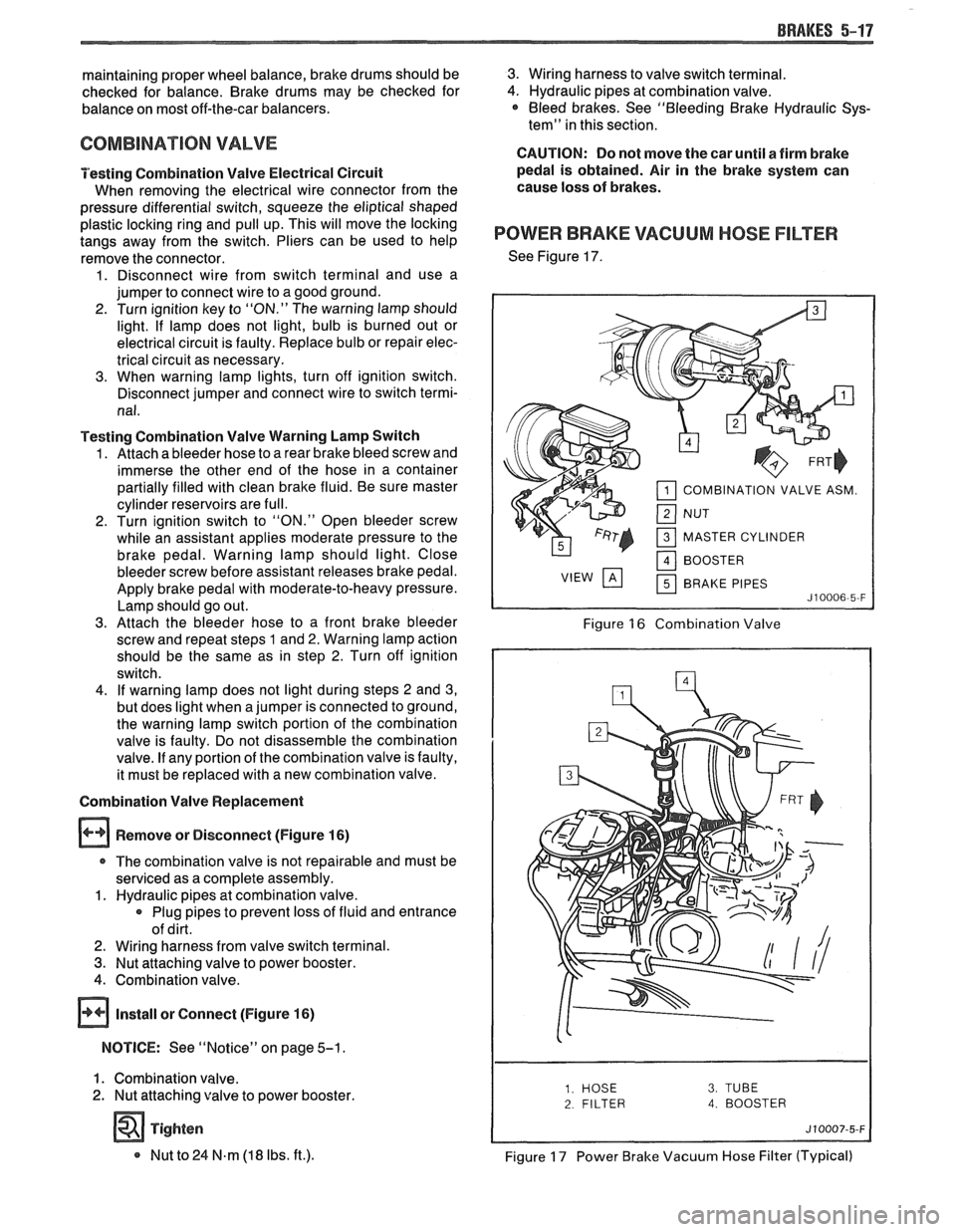
BRAKES 5-17
maintaining proper wheel balance, brake drums should be
checked for balance. Brake drums may be checked for
balance on most off-the-car balancers.
COMBINATION VALVE
Testing Combination Valve Electrical Circuit
When removing the electrical wire connector from the
pressure differential switch, squeeze the
eliptical shaped
plastic locking ring and pull up. This will move the locking
tangs away from the switch. Pliers can be used to help
remove the connector.
1. Disconnect wire from switch terminal and use a
jumper to connect wire to a good ground.
2. Turn ignition key to "ON." The warning lamp should
light. If lamp does not light, bulb is burned out or
electrical circuit is faulty. Replace bulb or repair elec-
trical circuit as necessary.
3. When warning lamp lights, turn off ignition switch.
Disconnect jumper and connect wire to switch termi-
nal.
Testing Combination Valve Warning Lamp Switch
1. Attach a bleeder hose to a rear brake bleed screw and
immerse the other end of the hose in a container
partially filled with clean brake fluid. Be sure master
cylinder reservoirs are full.
2. Turn ignition switch to "ON." Open bleeder screw
while an assistant applies moderate pressure to the
brake pedal. Warning lamp should light. Close
bleeder screw before assistant releases brake pedal.
Apply brake pedal with moderate-to-heavy pressure.
Lamp should go out.
3. Attach the bleeder hose to a front brake bleeder
screw and repeat steps
1 and 2. Warning lamp action
should be the same as in step
2. Turn off ignition
switch.
4. If warning lamp does not light during steps 2 and 3,
but does light when a jumper is connected to ground,
the warning lamp switch portion of the combination
valve is faulty. Do not disassemble the combination
valve.
If any portion of the combination valve is faulty,
it must be replaced with a new combination valve.
Combination Valve Replacement
Remove or Disconnect (Figure
16)
r The combination valve is not repairable and must be
serviced as a complete assembly.
1. Hydraulic pipes at combination valve.
Plug pipes to prevent loss of fluid and entrance
of dirt.
2. Wiring harness from valve switch terminal.
3. Nut attaching valve to power booster.
4. Combination valve.
@ Install or Connect (Figure 16)
NOTICE: See "Notice" on page 5-1.
1. Combination valve.
2. Nut attaching valve to power booster.
Tighten
* Nut to 24 N.m (18 Ibs. ft.).
3. Wiring harness to valve switch terminal.
4. Hydraulic pipes at combination valve. * Bleed brakes. See "Bleeding Brake Hydraulic Sys-
tem" in this section.
CAUTION: Do not move the car until a firm brake
pedal is obtained. Air in the brake system can
cause loss of brakes.
POWER BRAKE VACUUM HOSE FILTER
See Figure 17.
COMBINATION VALVE ASM.
MASTER CYLINDER BRAKE PIPES
Figure 16 Combination Valve
2 FILTER 4. BOOSTER
Figure 17 Power Brake Vacuum Hose Filter (Typical)