PONTIAC FIERO 1988 Service Repair Manual
Manufacturer: PONTIAC, Model Year: 1988, Model line: FIERO, Model: PONTIAC FIERO 1988Pages: 1825, PDF Size: 99.44 MB
Page 331 of 1825
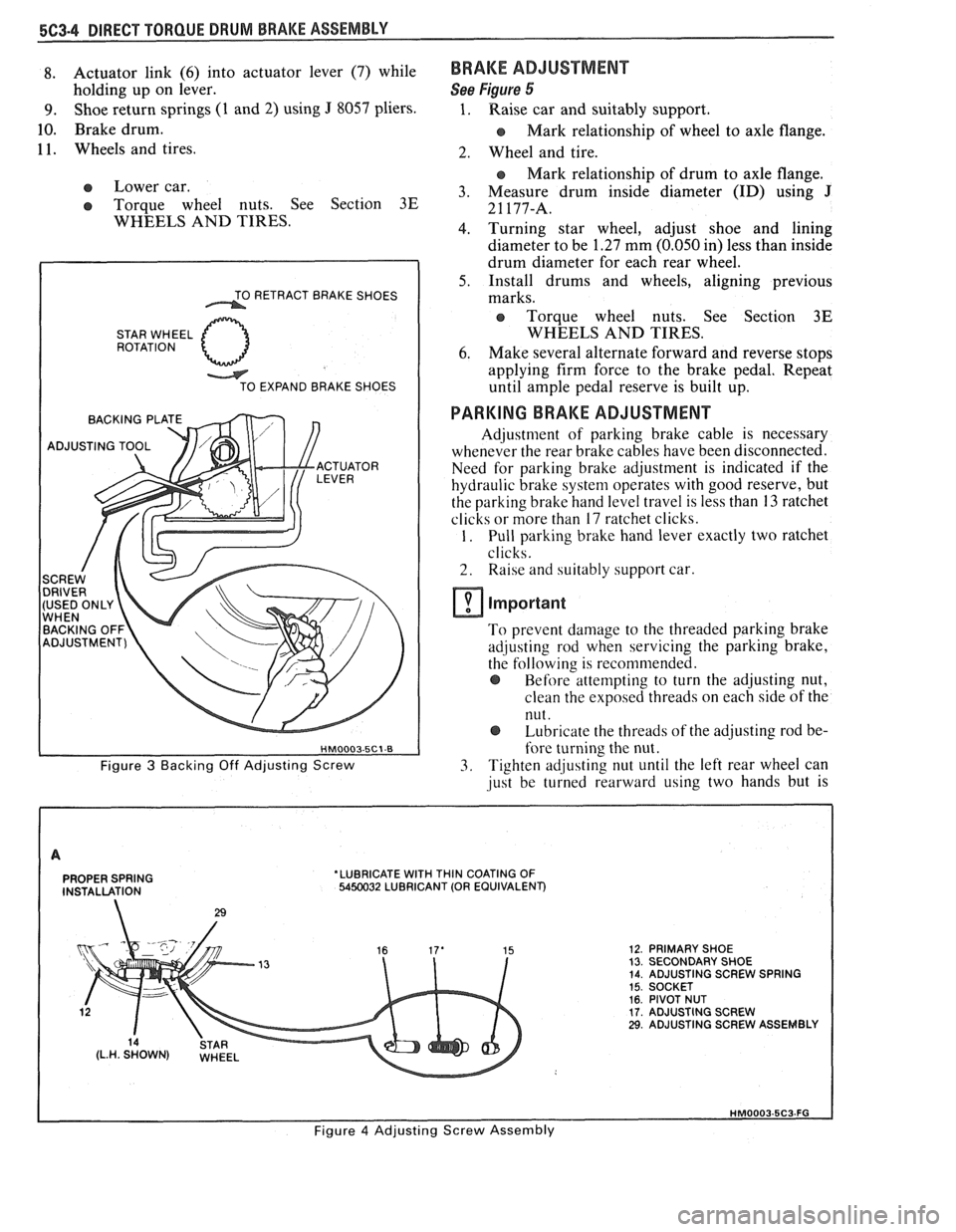
8. Actuator link (6) into actuator lever (7) while
holding up on lever.
9. Shoe return springs (1 and 2) using J 8057 pliers.
10. Brake drum.
1 1. Wheels and tires.
Lower car.
Torque wheel nuts. See Section 3E
WHEELS AND TIRES.
BRAKE ADJUSTMENT
See Figure 5
1. Raise car and suitably support.
Mark relationship of wheel to axle flange.
2. Wheel and tire.
o Mark relationship of drum to axle flange.
3. Measure drum inside diameter (ID) using J
21 177-A.
4. Turning star wheel, adjust shoe and lining
diameter to be 1.27 mm (0.050 in) less than inside
drum diameter for each rear wheel.
5. Install drums and wheels, aligning previous
marks.
s Torque wheel nuts. See Section 3E
WHEELS AND TIRES.
6. Make several alternate forward and reverse stops
applying firm force to the brake pedal. Repeat
until ample pedal reserve is built up.
TO RETRACT BRAKE SHOES
STAR WHEEL ROTATION
TO
EXPAND BRAKE SHOES
PARKING BRAKE ADJUSTMENT
Adjustment of parking brake cable is necessary
whenever the rear brake cables have been disconnected.
Need for parking brake adjustment is indicated if the
hydraulic brake system operates with good reserve, but
the parking brake hand level travel is less than 13 ratchet
clicks or more than 17 ratchet clicks.
1. Pull parking brake hand lever exactly two ratchet
clicks.
2. Raise and suitably support car.
important
To prevent damage to the threaded parking brake
adjusting rod when servicing the parking brake,
the following is recommended.
@ Before attempting to turn the adjusting nut,
clean the exposed threads on each side of the
nut.
@ Lubricate the threads of the adjusting rod be-
fore turning the nut.
Figure 3 Backing Off Adjusting Screw 3. Tighten adjusting nut until the left rear wheel can
just be turned rearward using two hands but is
PROPER SPRING 'LUBRICATE WITH THIN COATING OF 5450032 LUBRICANT (OR EQUIVALENT)
29
12. PRIMARY SHOE 13. SECONDARY SHOE 14. ADJUSTING SCREW SPRING 15. SOCKET 16. PIVOT NUT 17. ADJUSTING SCREW 29. ADJUSTING SCREW ASSEMBLY
Figure 4 Adjusting Screw Assembly
Page 332 of 1825
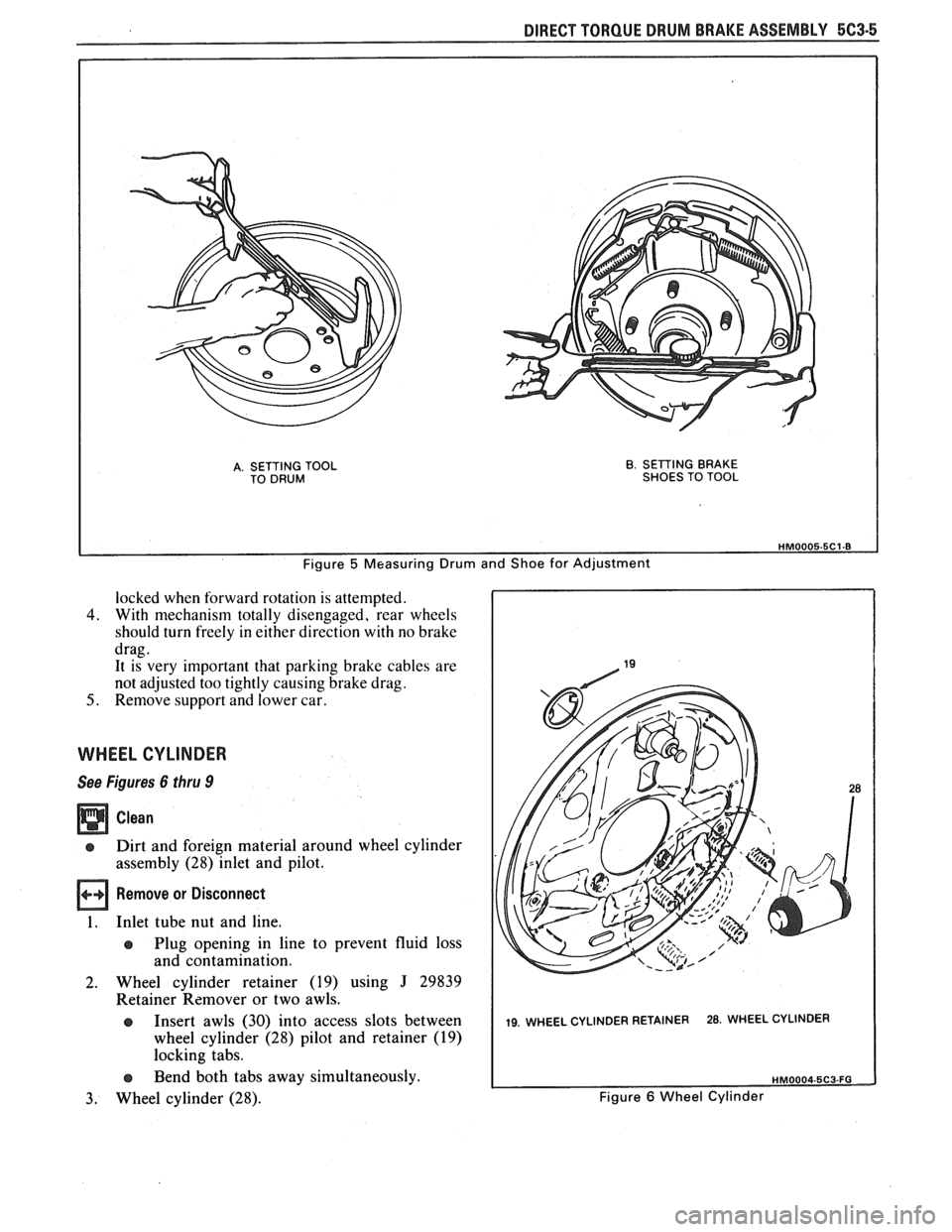
DIRECT TORQUE DRUM BRAKE ASSEMBLY 5C3-5
A. SETTING TOOL TO DRUM B. SETTING BRAKE
SHOES TO TOOL
Figure 5 Measuring Drum and Shoe for Adjustment
locked when forward rotation is attempted.
4. With mechanism totally disengaged, rear wheels
should turn freely in either direction with no brake
drag. It is very important that parking brake cables are
not adjusted too tightly causing brake drag.
5. Remove support and lower car.
WHEEL CYLINDER
See Figures 6 thru 9
Clean
s Dirt and foreign material around wheel cylinder
assembly
(28) inlet and pilot.
Remove or Disconnect
1. Inlet tube nut and line.
Plug opening in line to prevent fluid loss
and contamination.
2. Wheel cylinder retainer (19) using J 29839
Retainer Remover or two awls.
s Insert awls (30) into access slots between
wheel cylinder
(28) pilot and retainer (19)
locking tabs.
s Bend both tabs away simultaneously.
3. Wheel cylinder (28).
19. WHEEL CYLINDER RETAINER 28. WHEEL CYLINDER
Figure 6 Wheel Cylinder
Page 333 of 1825
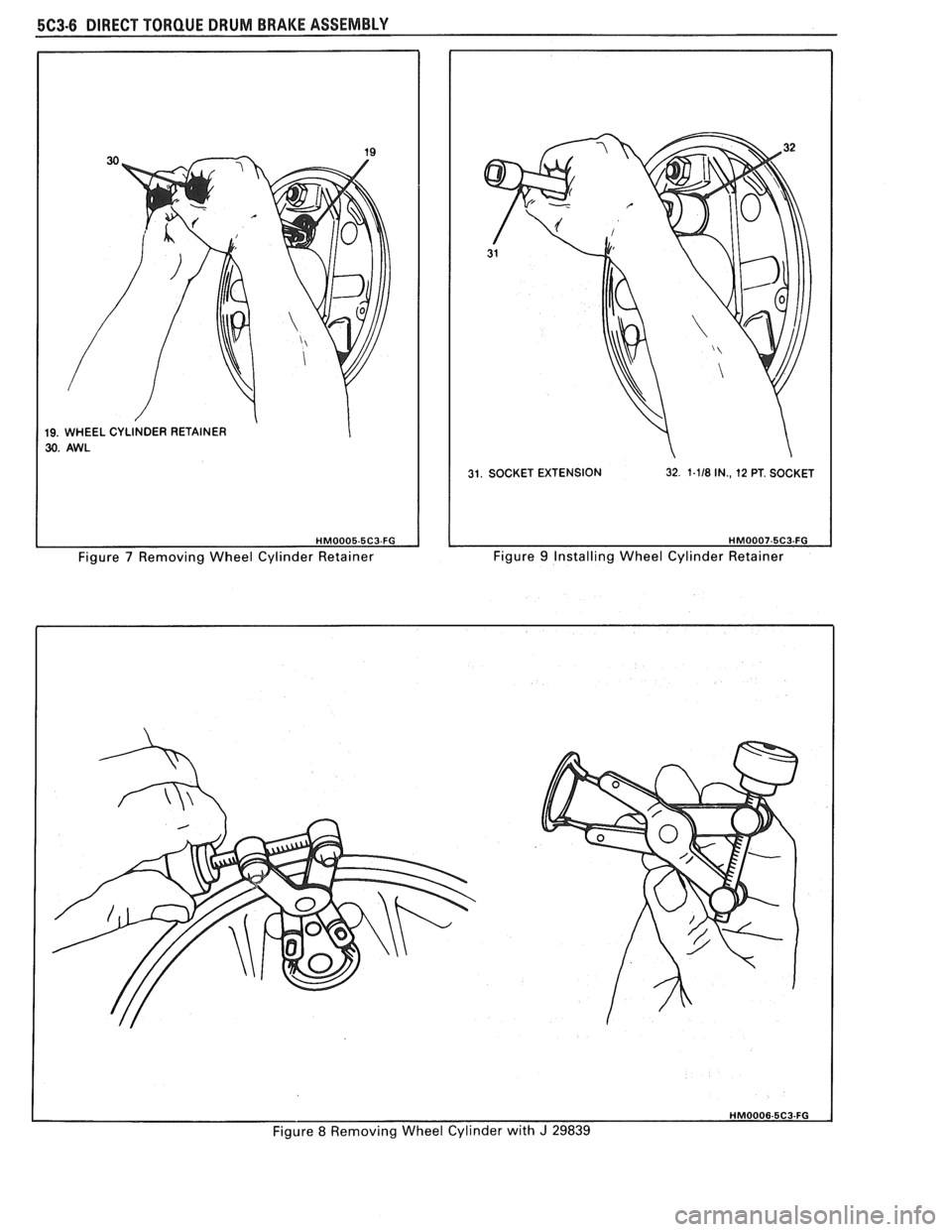
5C3-6 DIRECT TORQUE DRUM BRAKE ASSEMBLY
19. WHEEL CYLINDER RETAINER
30. AWL
Figure 7 Removing Wheel Cylinder Retainer
31. SOCKET EXTENSION 32. 1-118 IN., 12 PT. SOCKET
1 HM0007-5C3-FG Figure 9 Installing Wheel Cylinder Retainer
Figure 8 Removing Wheel Cylinder with
J 29839
Page 334 of 1825
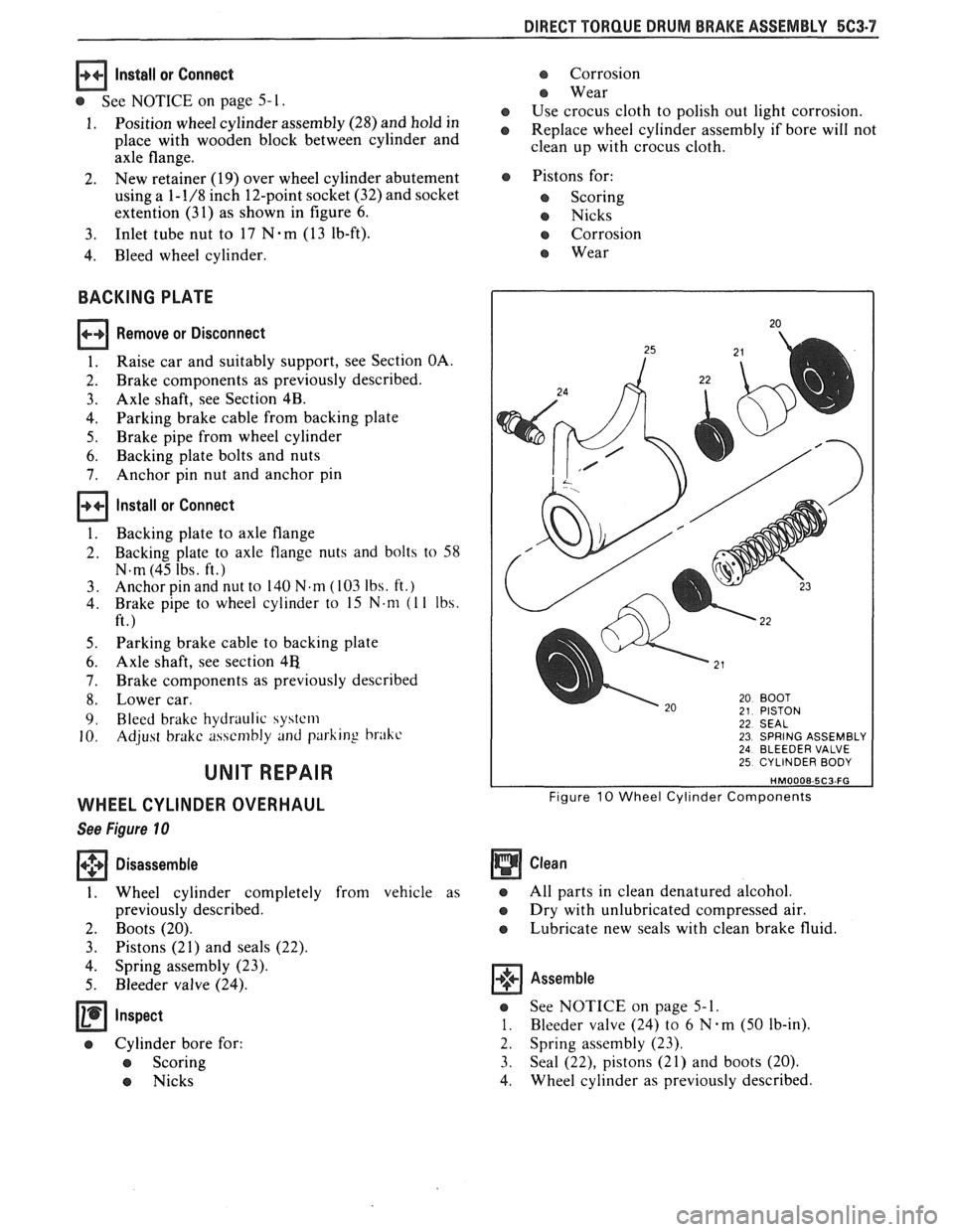
DIRECT TORQUE DRUM BRAKE ASSEMBLY 5C3-7
Install or Connect
See NOTICE on page 5- 1.
1. Position wheel cylinder assembly (28) and hold in
place with wooden block between cylinder and
axle flange.
2. New retainer (19) over wheel cylinder abutement
using a 1-
1/8 inch 12-point socket (32) and socket
extention (31) as shown in figure
6.
3. Inlet tube nut to 17 N-m (13 1b-ft).
4. Bleed wheel cylinder.
BACKING PLATE
Remove or Disconnect
1. Raise
car and suitably support, see Section OA.
2. Brake
components as previously described.
3. Axle shaft, see Section 4B.
4. Parking brake
cable from backing plate
5. Brake pipe from wheel cylinder
6. Backing plate bolts and nuts
7. Anchor
pin nut and anchor pin
Install or Connect
1. Backing plate to axle flange
2. Backing plate to axle flange nuts and bolts to 58
N.m (45 lbs. ft.)
3. Anchor
in and nut to 140 N.m ( 103 Ibs. ft.)
4. Brake
pipe to
wheel cylinder to 15 N.nl (I l Ibs.
ft.)
5. Parking brake cable to backing plate
6. Axle shaft, see section 48
7. Brake
components as previously described
8. Lower car.
9. Bleed brake hydraulic syatcm
10. Adjust brake asscnlbly and parking brakc
UNIT REPAIR
WHEEL
CYLINDER OVERHAUL
See Figure 10
+++ Disassemble [I]
1. Wheel cylinder completely from vehicle as
previously described.
2. Boots (20).
3. Pistons (21) and seals (22).
4. Spring assembly (23).
5. Bleeder valve (24).
e Cylinder bore for:
e Scoring
e Nicks
e Corrosion
e Wear
e Use crocus cloth to polish out light corrosion.
e Replace wheel cylinder assembly if bore will not
clean up with crocus cloth.
e Pistons for:
e Scoring
e Nicks
e Corrosion
e Wear
22 SEAL 23 SPRING ASSEMBLY 24 BLEEDER VALVE 25 CYLINDER BODY
Figure 10 Wheel Cylinder Components
Clean
e All parts in clean denatured alcohol.
e Dry with unlubricated compressed air.
e Lubricate new seals with clean brake fluid.
Assemble
e See NOTICE on page 5-1.
1. Bleeder valve (24) to 6 N.m (50 lb-in).
2. Spring assembly (23).
3. Seal
(22), pistons (21) and boots (20).
4. Wheel
cylinder as previously described,
Page 335 of 1825
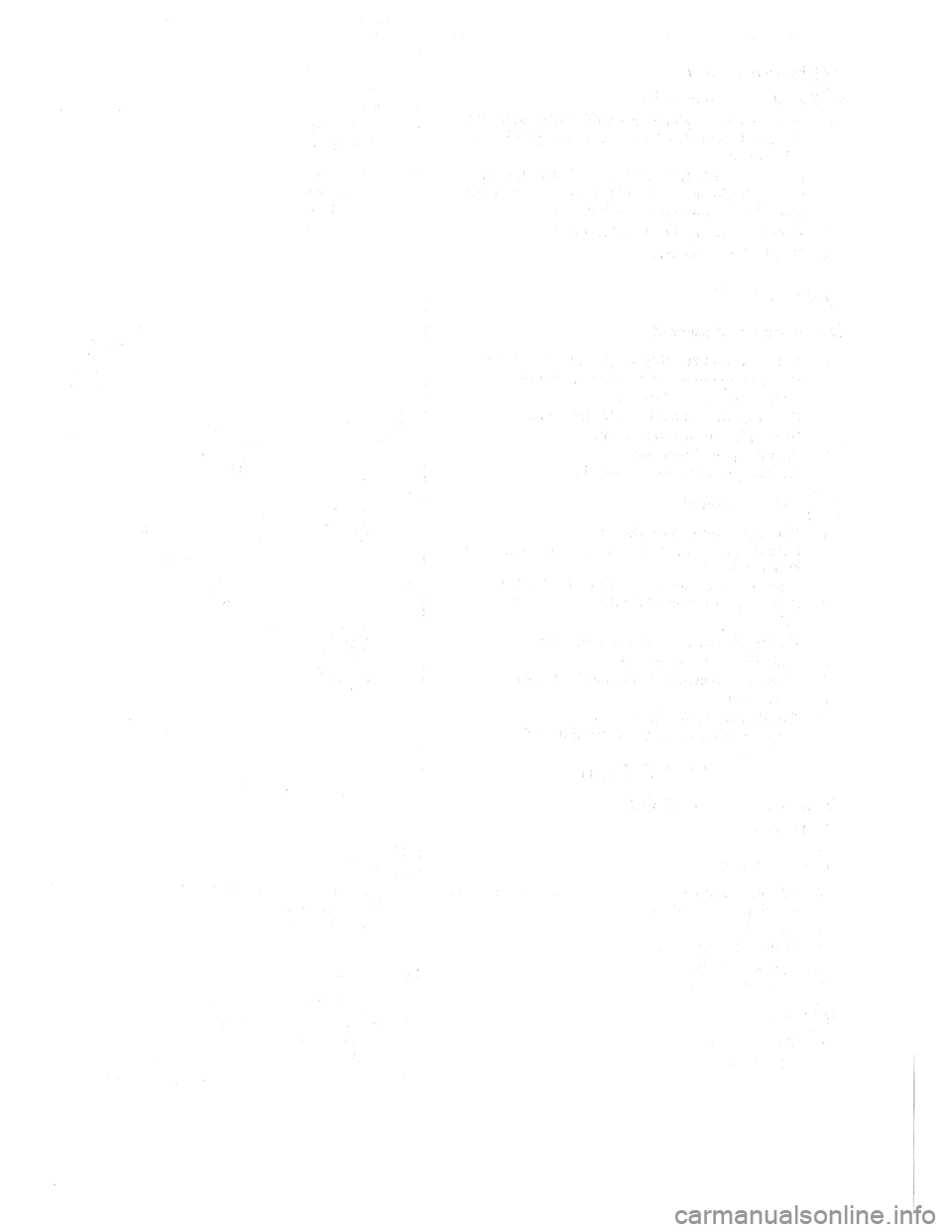
Page 336 of 1825
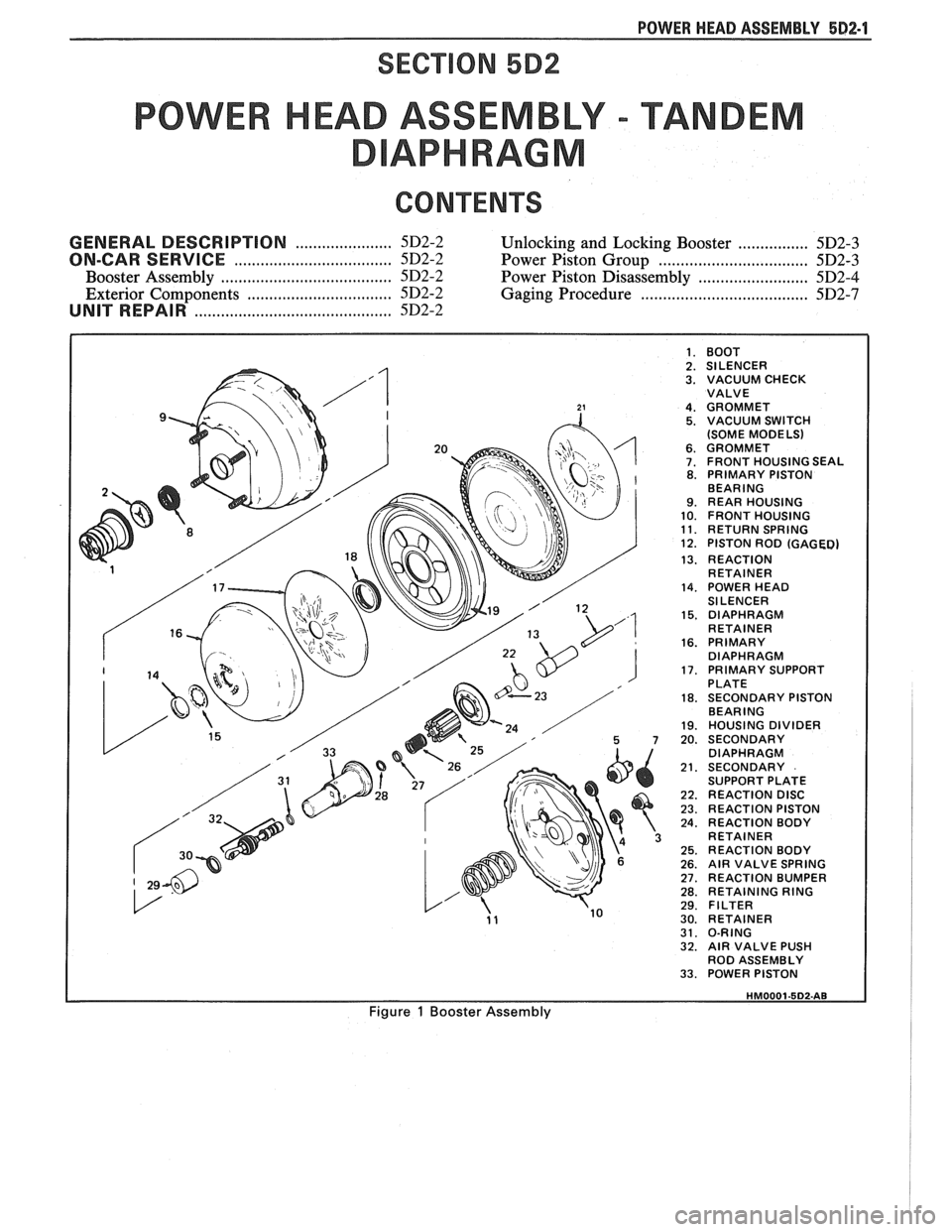
POWER HEAD ASSEMBLY 582-1
SECTION 582
POWER HEAD ASSEMBLY - TANDEM
APHRAGM
CONTENTS
...................... GENERAL DESCRIPTION 5D2-2 Unlocking and Locking Booster ................ 5D2-3
................................. ON-CAR SERVICE 5D2-2 Power Piston Group ................................. 5D2-3
..................................... Booster Assembly 5D2-2 Power Piston Disassembly ......................... 5D2-4
................................. Exterior Components 5D2-2 Gaging Procedure ...................................... 5D2-7
......................................... UNIT REPAIR 5D2-2
I 1. BOOT I 2. SILENCER 3. VACUUM CHECK
VALVE
4. GROMMET 5. VACUUM SWITCH
(SOME MODELS)
6. GROMMET 7. FRONT HOUSING SEAL 8. PRIMARY PISTON
BEARING
9. REAR HOUSING 10. FRONT HOUSING 11. RETURN SPRING 12. PISTON ROD (GAGED)
13. REACTION
RETAINER
14. POWER HEAD
SILENCER
15. DIAPHRAGM
RETAINER
16. PRIMARY
DIAPHRAGM
17. PRIMARY SUPPORT
PLATE
18. SECONDARY PISTON
BEARING
19. HOUSING DIVIDER 20. SECONDARY
DIAPHRAGM
21. SECONDARY
SUPPORT PLATE
22. REACTION DISC 23. REACTION PISTON 24. REACTION BODY
RETAINER
25. REACTION BODY 26. AIR VALVE SPRING 27. REACTION BUMPER 28. RETAINING RING 29. FILTER 30. RETAINER 31. O-RING 32. AIR VALVE PUSH
ROD ASSEMBLY
33. POWER PISTON
Figure 1 Booster Assembly
Page 337 of 1825
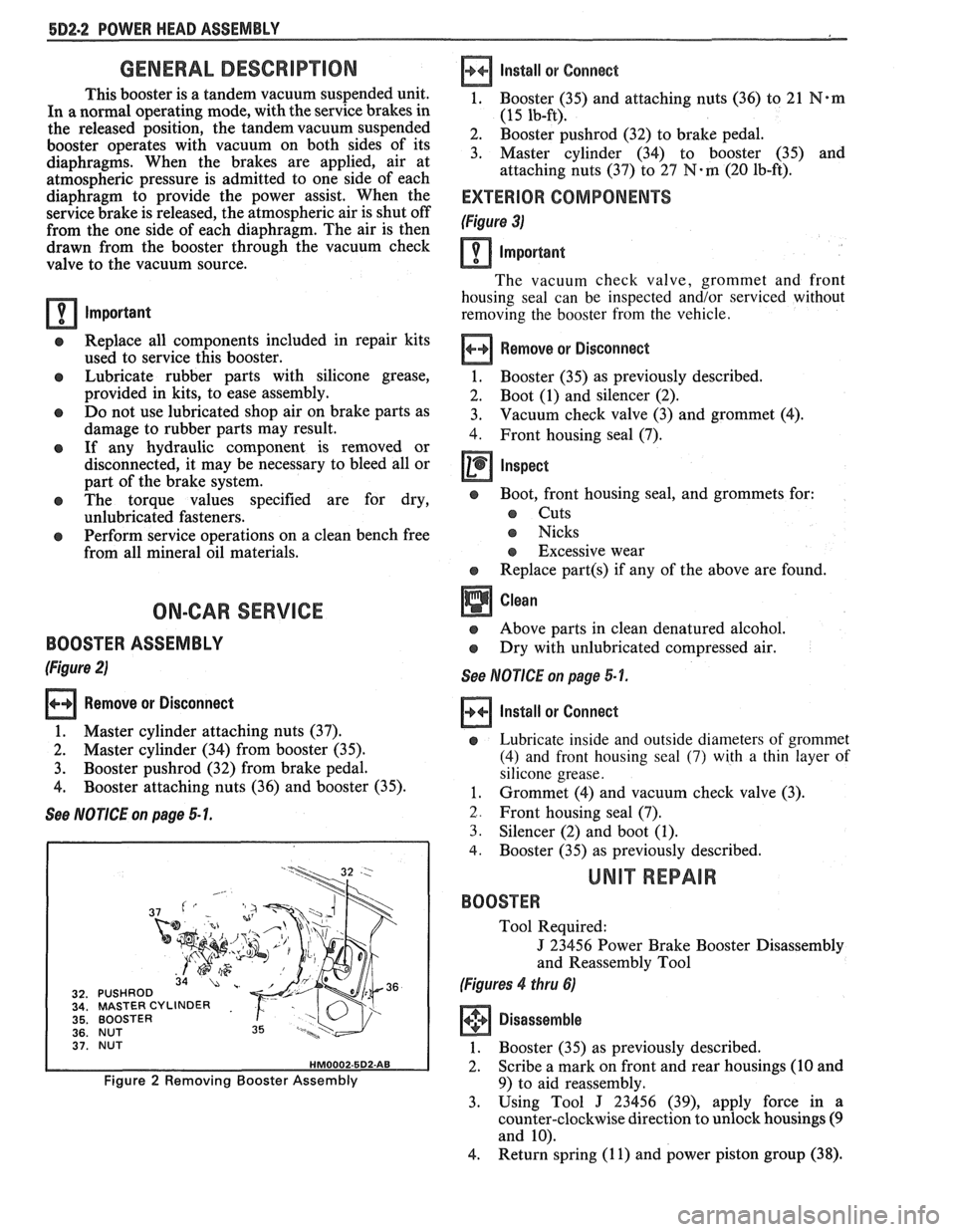
582.2 POWER HEAD ASSEMBLY
GENERAL DESCRIPTION
This booster is a tandem vacuum suspended unit.
In a normal operating mode, with the service brakes in
the released position, the tandem vacuum suspended
booster operates with vacuum on both sides of its
diaphragms. When the brakes are applied, air at
atmospheric pressure is admitted to one side of each
diaphragm to provide the power assist. When the
service brake is released, the atmospheric air is shut off
from the one side of each diaphragm. The air is then
drawn from the booster through the vacuum check
valve to the vacuum source.
important
e Replace all components included in repair kits
used to service this booster.
e Lubricate rubber parts with silicone grease,
provided in kits, to ease assembly.
o Do not use lubricated shop air on brake parts as
damage to rubber parts may result.
o If any hydraulic component is removed or
disconnected, it may be necessary to bleed all or
part of the brake system.
e The torque values specified are for dry,
unlubricated fasteners.
Perform service operations on a clean bench free
from all mineral oil materials.
ON-CAR SERVICE
BOOSTER ASSEMBLY
(Figure 2)
Remove or Disconnect
1. Master cylinder attaching nuts (37).
2. Master cylinder (34) from booster (35).
3. Booster pushrod (32) from brake pedal.
4. Booster attaching nuts (36) and booster (35).
See NOTICE on page 5 1.
MASTER CYLINDER
BOOSTER
NUT
BOOSTER
Figure 2 Removing Booster Assembly
Install
or Connect
1, Booster (35) and attaching nuts (36) to 21 N*m
(15 lb-ft).
2. Booster pushrod (32) to brake pedal.
3. Master cylinder (34) to booster (35) and
attaching nuts (37) to
27 N-m (20 lb-ft).
EXTERIOR COMPONENTS
(Figure 3)
Important
The vacuum check valve, grommet and front
housing seal can be inspected and/or serviced without
removing the booster from the vehicle.
Remove or Disconnect
1. Booster (35)
as previously described.
2. Boot (1) and silencer (2).
3. Vacuum check
valve (3) and grommet (4).
4. Front housing seal (7).
Inspect
e Boot, front housing seal, and grommets for:
s Cuts
s Nicks
s Excessive wear
e Replace part(s) if any of the above are found.
Above parts in clean denatured alcohol.
Dry with unlubricated compressed air.
See NOTICE on page 5-1.
Install or Connect
e Lubricate inside and outside diameters of grommet
(4) and front housing seal
(7) with a thin layer of
silicone grease.
1. Grommet (4) and vacuum check valve (3).
2. Front housing seal (7).
3. Silencer (2) and boot (1).
4. Booster (35) as previously described.
UNIT REPAIR
BOOSTER
Tool Required:
J 23456 Power Brake Booster Disassembly
and Reassembly Tool
(Figures 4 thru 6)
Disassemble
1. Booster (35) as previously described.
2. Scribe a mark on front and rear housings (10 and
9) to aid reassembly.
3. Using Tool
J 23456 (39), apply force in a
counter-clockwise direction to unlock housings
(9
and 10).
4. Return spring
(1 1) and power piston group (38).
Page 338 of 1825
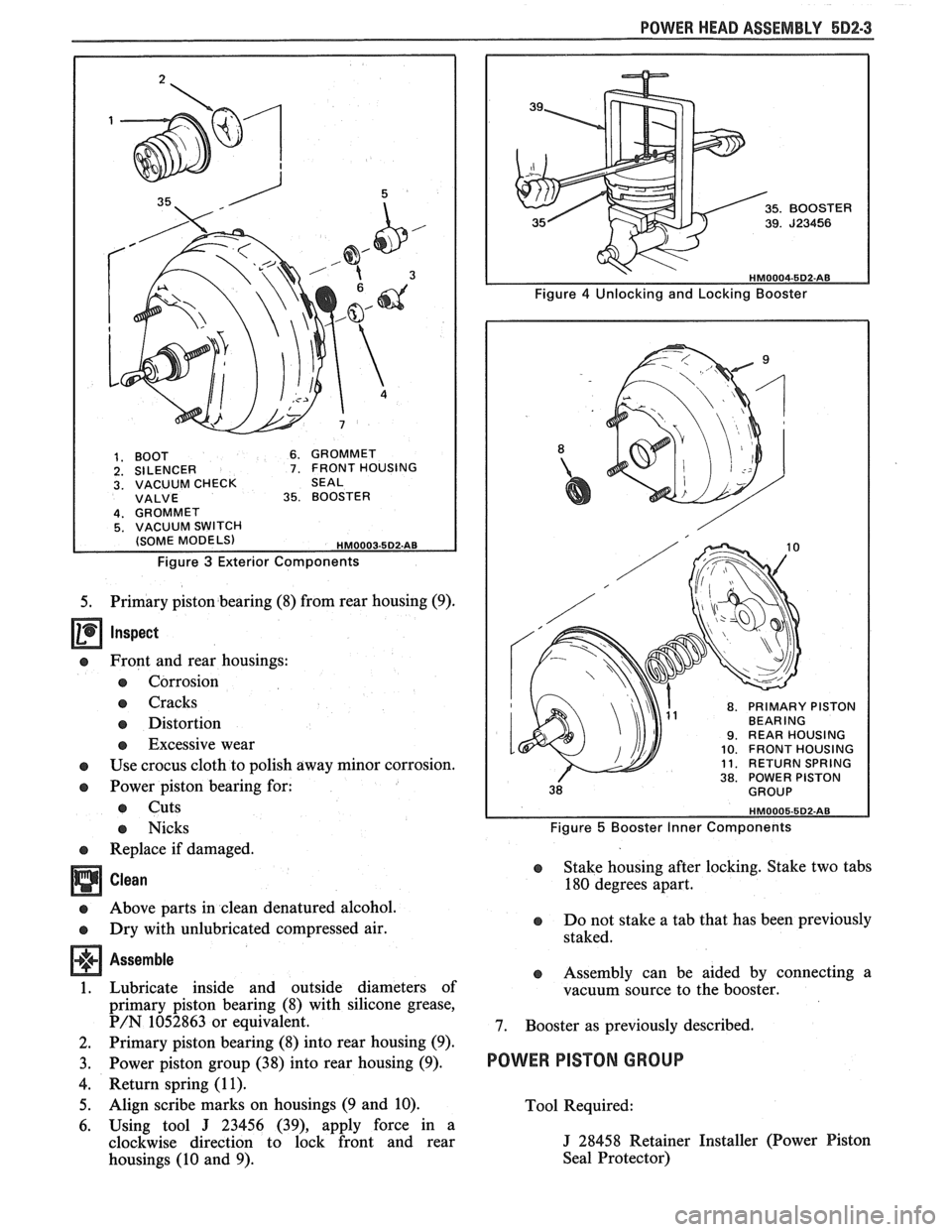
POWER HEAD ASSEMBLY 5D2-3
1. BOOT 6. GROMMET 2. SILENCER 7. FRONT HOUSING 3. VACUUM CHECK SEAL VALVE 35. BOOSTER
Figure 3 Exterior Components
5. Primary piston bearing (8) from rear housing (9).
Inspect
e Front and rear housings:
e Corrosion
e Cracks
e Distortion
e Excessive wear
e Use crocus cloth to polish away minor corrosion.
e Power piston bearing for:
e Cuts
e Nicks
e Replace if damaged.
Clean
e Above parts in clean denatured alcohol.
e Dry with unlubricated compressed air.
Assemble
1. Lubricate inside and outside diameters of
primary piston bearing (8) with silicone grease,
P/N 1052863 or equivalent.
2. Primary piston bearing (8) into rear housing (9).
3. Power piston group (38) into rear housing (9).
4. Return spring (1 1).
5. Align scribe marks on housings (9 and 10).
6. Using tool
J 23456 (39), apply force in a
clockwise direction to lock front and rear
housings (10 and 9).
8. PRIMARY PISTON BEARING 9. REAR HOUSING 10. FRONT HOUSING 11. RETURN SPRING 38. POWER PISTON
Figure 5 Booster Inner Components
e Stake housing after locking. Stake two tabs
180 degrees apart.
e Do not stake a tab that has been previously
staked.
e Assembly can be aided by connecting a
vacuum source to the booster.
7. Booster as previously described.
POWER PISTON GROUP
Tool Required:
J 28458 Retainer Installer (Power Piston
Seal Protector)
Page 339 of 1825
![PONTIAC FIERO 1988 Service Repair Manual
6D2-4 POWER HEAD ASSEMBLY
STAKE
I STAKING TAB SOCKET WITH SCREWDRIVER
Figure 6 Staking Procedure
(Figures 7 thru 1 1)
(.+g Disassemble [I]
1.
Remove booster (35) and disconnect housings (9
PONTIAC FIERO 1988 Service Repair Manual
6D2-4 POWER HEAD ASSEMBLY
STAKE
I STAKING TAB SOCKET WITH SCREWDRIVER
Figure 6 Staking Procedure
(Figures 7 thru 1 1)
(.+g Disassemble [I]
1.
Remove booster (35) and disconnect housings (9](/img/50/57415/w960_57415-338.png)
6D2-4 POWER HEAD ASSEMBLY
STAKE
I STAKING TAB SOCKET WITH SCREWDRIVER
Figure 6 Staking Procedure
(Figures 7 thru 1 1)
(.+g Disassemble [I]
1.
Remove booster (35) and disconnect housings (9
and 10) as previously described.
2. Piston rod
(12), reaction retainer (13) and power
head silencer (14).
3. Power piston assembly (41) along with pushrod
(32).
e Grasp assemby at outside edge of housing
divider (19) and diaphragms (16 and 20).
e Hold with pushrod (32) down against a
hard surface.
e Use a slight force or impact to dislodge
diaphragm retainer (15).
4. Primary diaphragm (16) and primary support
plate (17) from housing divider (19).
5. Primary diaphragm (16) from primary support
plate (17).
6. Secondary diaphragm (20) and secondary
support plate (21) from housing divider (19).
7. Secondary piston bearing (18) from housing
divider (19).
8. Secondary diaphragm (20) from secondary
support plate
(2 1).
e Parts for:
e Corrosion
e Nicks
e Cracks
e Cuts
e Scoring
e Distortion
e Excessive wear
e Use crocus cloth to polish away minor corrosion
to diaphragm supports, or housing divider.
@ All parts in clean denatured alcohol.
e Do not immerse power piston and pushrod
assembly in alcohol, rather wipe clean with an
alcohol dampened cloth.
e Dry with unlubricated compressed air.
Assemble
1. Lubricate inside diameter of secondary
diaphragm (20) lip, inside diameter of primary
diaphragm (16) lip and secondary piston bearing
(18) with a thin layer of silicone grease.
2. Secondary diaphragm (20) into secondary
support plate (21).
3. Secondary diaphragm (20) and support plate (21)
over power piston assembly (41) and
pushrod
(32). Use J 28458 as a guide to protect the power
piston.
4. Secondary piston bearing (18) into housing
divider (19) with flat surface of bearing on same
side as six raised lugs on divider.
5. Secondary piston bearing (18) and housing
divider (19) over power piston assembly (41) and
pushrod (32). Use J 28458 as a guide.
6. Primary diaphragm (16) into primary support
plate (17).
7. Fold primary diaphragm (16) up, away from
primary support plate (17).
8. Primary diaphragm (16) and support plate (17)
over power piston assembly (41) and
pushrod
(32).
9. Fold primary diaphragm (16) back into position
and pull diaphragm
OD over formed flange of
housing divider (19).
e Check that beads on secondary diaphragm
(20) are seated evenly around complete
circumference.
10. New diaphragm retainer (15) and seat using
J
28458 Retainer Installer.
11. Silencer
(14), reaction retainer (13) and piston
rod (12).
12. Reassemble booster as previously described.
POWER PISTON OVERHAUL
Tools Required:
J 29282 Air Valve Push Rod Retainer
Installer
(Figures 12 thru 14)
+++ Disassemble GI
1. Reaction body retainer (24).
2. Reaction body (25).
Page 340 of 1825
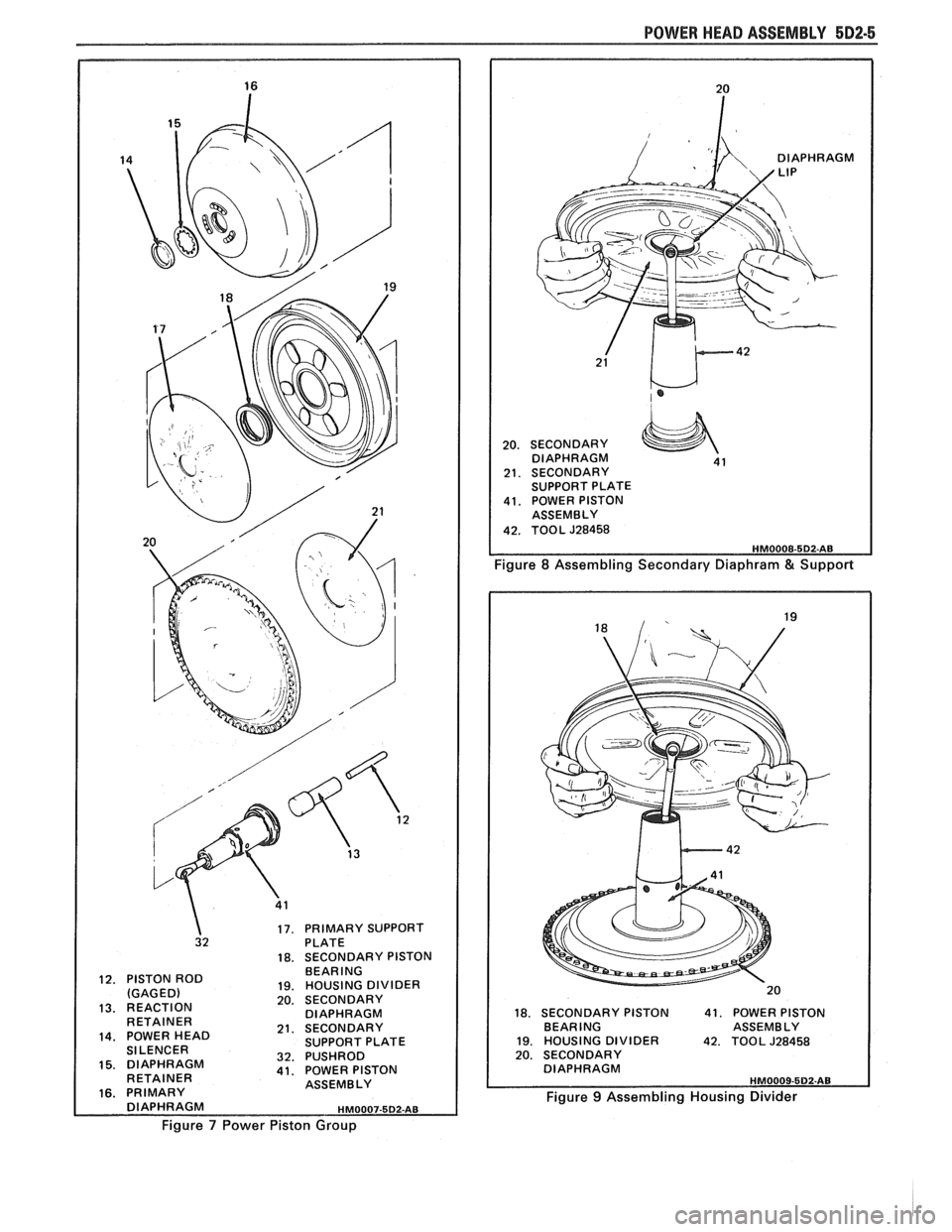
POWER HEAD ASSEMBLY 5D2-5
17. PRIMARY SUPPORT 32 PLATE 18. SECONDARY PISTON
12. PISTON ROD
(GAGED)
13. REACTION
RETAINER
14. POWER HEAD Sl LENCER 15. DIAPHRAGM
RETAINER
16. PRIMARY BEARING
19. HOUSING
DIVIDER 20. SECONDARY
DIAPHRAGM
21. SECONDARY
SUPPORT PLATE
32. PUSHROD 41. POWER PISTON
ASSEMBLY
DIAPHRAGM
HM0007-5D2-AB
Figure 7 Power Piston Group
DIAPHRAGM
20. SECONDARY
DIAPHRAGM 4 1 21. SECONDARY
SUPPORT PLATE
41. POWER PISTON
ASSEMBLY
42. TOOL J28458
Figure 8 Assembling Secondary Diaphram & Support
18. SECONDARY PISTON 41. POWER PISTON
BEARING ASSEMBLY
19. HOUSING DIVIDER 42. TOOL J28458 20. SECONDARY
Figure 9 Assembling Housing Divider