PONTIAC FIERO 1988 Service Repair Manual
Manufacturer: PONTIAC, Model Year: 1988, Model line: FIERO, Model: PONTIAC FIERO 1988Pages: 1825, PDF Size: 99.44 MB
Page 311 of 1825
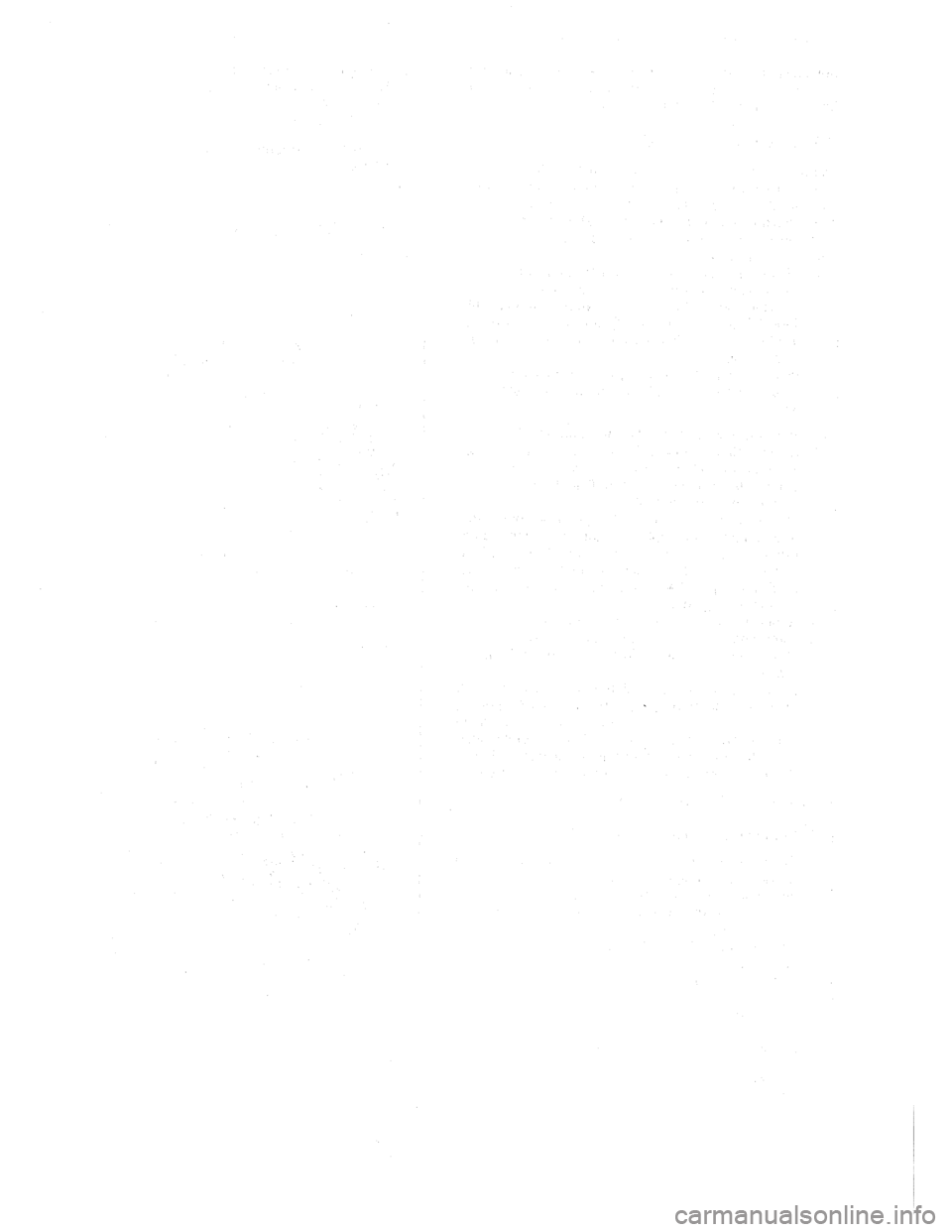
Page 312 of 1825
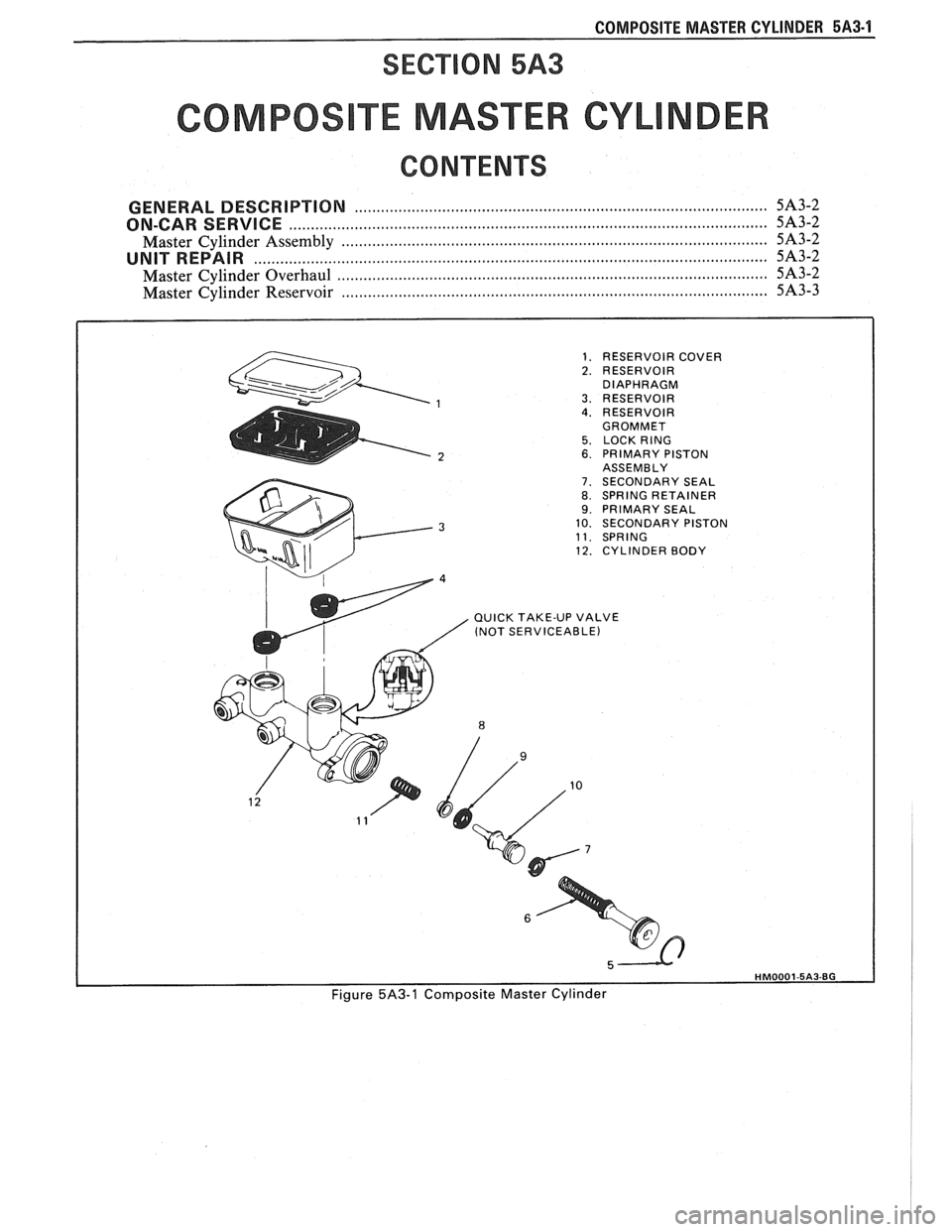
COMPOSITE MASTER CYLINDER 5A3-1
SECTION 5A3
COMPOS TE MASTER CYL
CONTENTS
GENERAL DESCRIPTION .............................................................................................. 5A3-2
ON-CAR SERVICE ..................... .. ............................................................................... 5A3-2
Master Cylinder Assembly ..................... .. ..................................................................... 5A3-2
................... UNIT REPAIR ....... .............................................................................. 5A3-2
Master Cylinder Overhaul ............................................................................................... 5A3-2
Master Cylinder Reservoir ................................... .... .......................................................... 5A3-3
1. RESERVOIR COVER 2. RESERVOIR
DIAPHRAGM
3. RESERVOIR 4. RESERVOIR
GROMMET
5. LOCK RING 6. PRIMARY PISTON
ASSEMBLY
7. SECONDARY SEAL 8. SPRING RETAINER 9. PRIMARY SEAL 10. SECONDARY PISTON 11. SPRING 12. CYLINDER BODY
QUICK TAKE-UP VALVE
(NOT SERVICEABLE)
Figure 5A3-1 Composite Master Cylinder
Page 313 of 1825
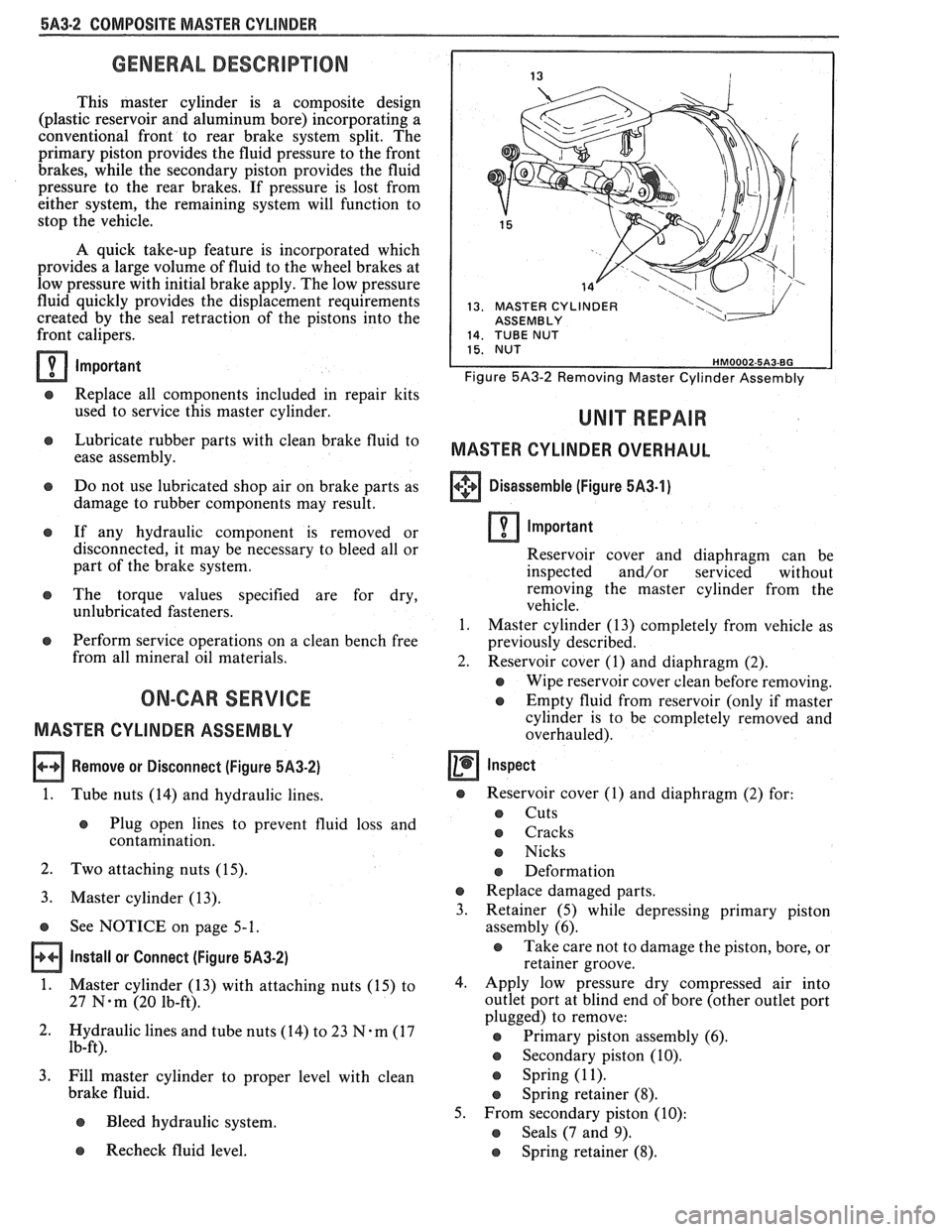
5A3-2 COMPOSlf E MASTER CYLINDER
GENERAL DESCRIPTION
This master cylinder is a composite design
(plastic reservoir and aluminum bore) incorporating
a
conventional front to rear brake system split. The
primary piston provides the fluid pressure to the front
brakes, while the secondary piston provides the fluid
pressure to the rear brakes. If pressure is lost from
either system, the remaining system will function to
stop the vehicle.
A quick take-up feature is incorporated which
provides a large volume of fluid to the wheel brakes at
low pressure with initial brake apply. The low pressure
fluid quickly provides the displacement requirements
created by the seal retraction of the pistons into the
front calipers.
Important
e Replace all components included in repair kits
used to service this master cylinder.
e Lubricate rubber parts with clean brake fluid to
ease assembly.
a Do not use lubricated shop air on brake parts as
damage to rubber components may result.
e If any hydraulic component is removed or
disconnected, it may be necessary to bleed all or
part of the brake system.
e The torque values specified are for dry,
unlubricated fasteners.
a Perform service operations on a clean bench free
from all mineral oil materials.
ON-CAR SERVICE
MASTER CYLINDER ASSEMBLY
Remove or Disconnect (Figure 5,432)
1.
Tube nuts (14) and hydraulic lines.
e Plug open lines to prevent fluid loss and
contamination.
2. Two attaching nuts (15).
3. Master cylinder (13).
s See NOTICE on page 5-1.
Install or Connect (Figure 5A3-2)
1.
Master cylinder (13) with attaching nuts (15) to
27
N-m (20 lb-ft).
2. Hydraulic lines and tube nuts
(14) to 23 7%-m (17
lb-ft).
3. Fill master cylinder to proper level with clean
brake fluid.
e Bleed hydraulic system.
13. MASTER CYLINDER I ASSEMBLY
Figure 5A3-2 Removing Master Cylinder Assembly
MASTER CYLINDER OVERHAUL
+++ Disassemble (Figure 5A3-1) [I]
Important
Reservoir cover and diaphragm can be
inspected and/or serviced without
removing the master cylinder from the
vehicle.
1. Master cylinder (13) completely from vehicle as
previously described.
2. Reservoir cover (1) and diaphragm (2).
e Wipe reservoir cover clean before removing.
e Empty fluid from reservoir (only if master
cylinder is to be completely removed and
overhauled).
Inspect
s Reservoir cover (I) and diaphragm (2) for:
s Cuts
o Cracks
e Nicks
e Deformation
e Replace damaged parts.
3. Retainer
(5) while depressing primary piston
assembly (6).
e Take care not to damage the piston, bore, or
retainer groove.
4. Apply low pressure dry compressed air into
outlet port at blind end of bore (other outlet port
plugged) to remove:
@ Primary piston assembly (6).
s Secondary piston (10).
s Spring (1 1).
e Spring retainer (8).
5. From secondary piston (10):
e Seals (7 and 9).
Recheck fluid level. e Spring retainer (8).
Page 314 of 1825

Inspect
s Master cylinder bore for scoring or corrosion.
e If noted, replace master cylinder.
e No abrasives should be used in bore.
All parts in clean, denatured alcohol.
e Dry with unlubricated compressed air.
Assemble (Figure 5A3-1)
s See NOTICE on page 5-1.
1. Lubricated
seals
(7 and 9) and spring retainer (8)
onto secondary piston (10).
2. Spring (1
I), and
secondary piston assembly (7
thru 10) into cylinder bore.
a To ease reassembly, lubricate with clean
brake fluid.
3. Lubricated primary piston assembly (6) into
cylinder bore.
4. Retainer
(5) while depressing primary piston
assembly (6).
5. Diaphragm
(2) into reservoir cover (1) and install
on reservoir (3).
6. Master cylinder (13) as previously described.
Figure 5A3-3 Removing Reservoir
COMPOSITE MASTER CYLINDER 5A3-3
3. RESERVO 4. GROMMET 12. CYLINDER BODY
Figure 5A3-4 Installing Reservoir
MASTER CYLINDER RESERVOIR
Disassemble (Figures 5A3-3,5A3-4)
1. Remove and disassemble master cylinder as
previously described.
2. Clamp flange of master cylinder body (12) in vise.
Important
s Do not clamp on master cylinder body (12).
e Do not remove quick take-up valve from body.
Valve is not serviceable separately.
3. Reservoir (3) using a pry bar
(16).
4. Reservoir grommets (4).
Inspect
s Reservoir for cracks or deformation.
e Replace if found.
s Reservoir with clean denatured alcohol.
a Dry with unlubricated compressed air.
Assemble (Figure 5A3.4)
e See NOTICE on page 5-1.
@ Lubricate new grommets (4) and reservoir
bayonets with clean brake fluid.
1. Grommets (4) into master cylinder body (12).
a Make sure grommets are properly seated.
2. Reservoir (3) into master cylinder body (12) using
rocking motion.
3. Reassemble master cylinder and install as
previously described.
Page 315 of 1825
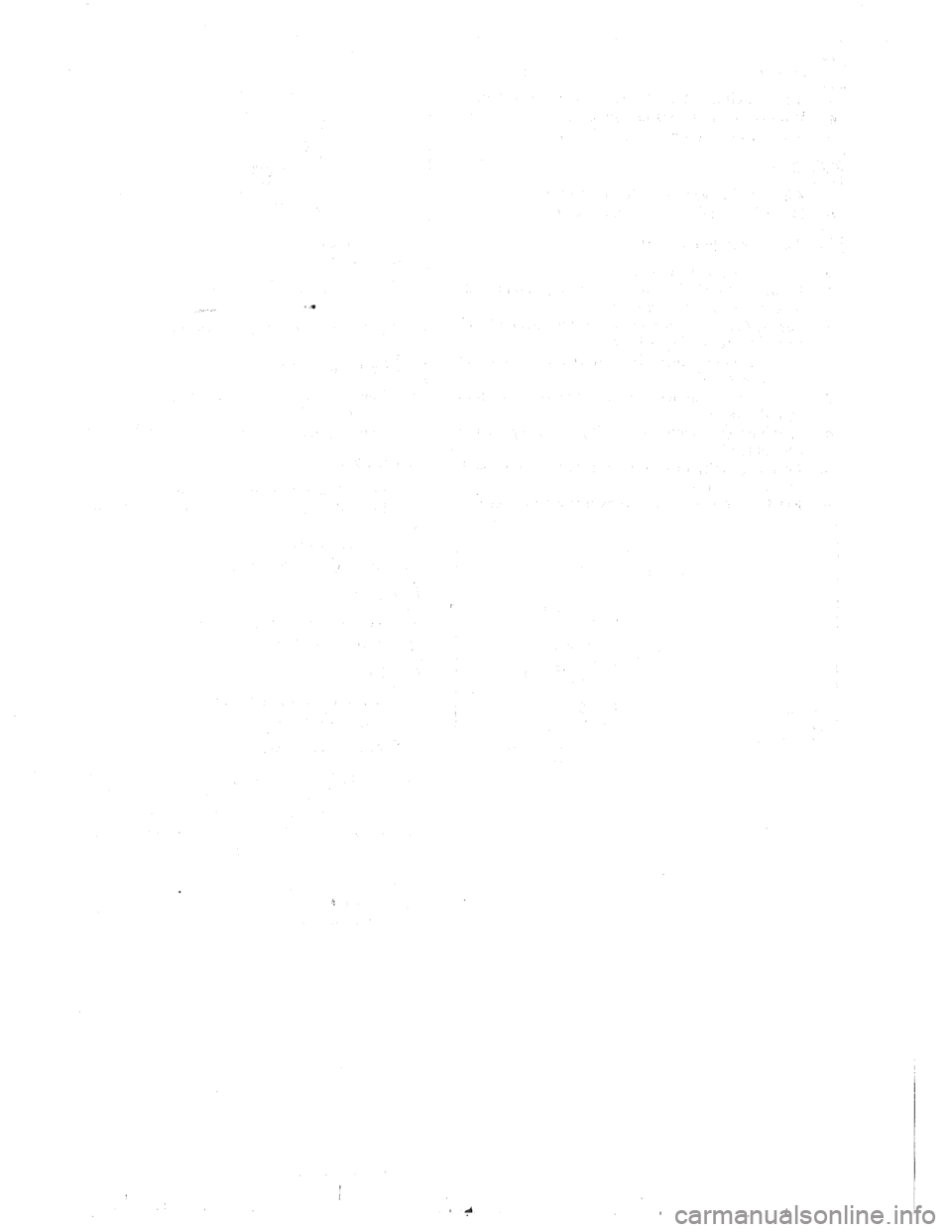
Page 316 of 1825
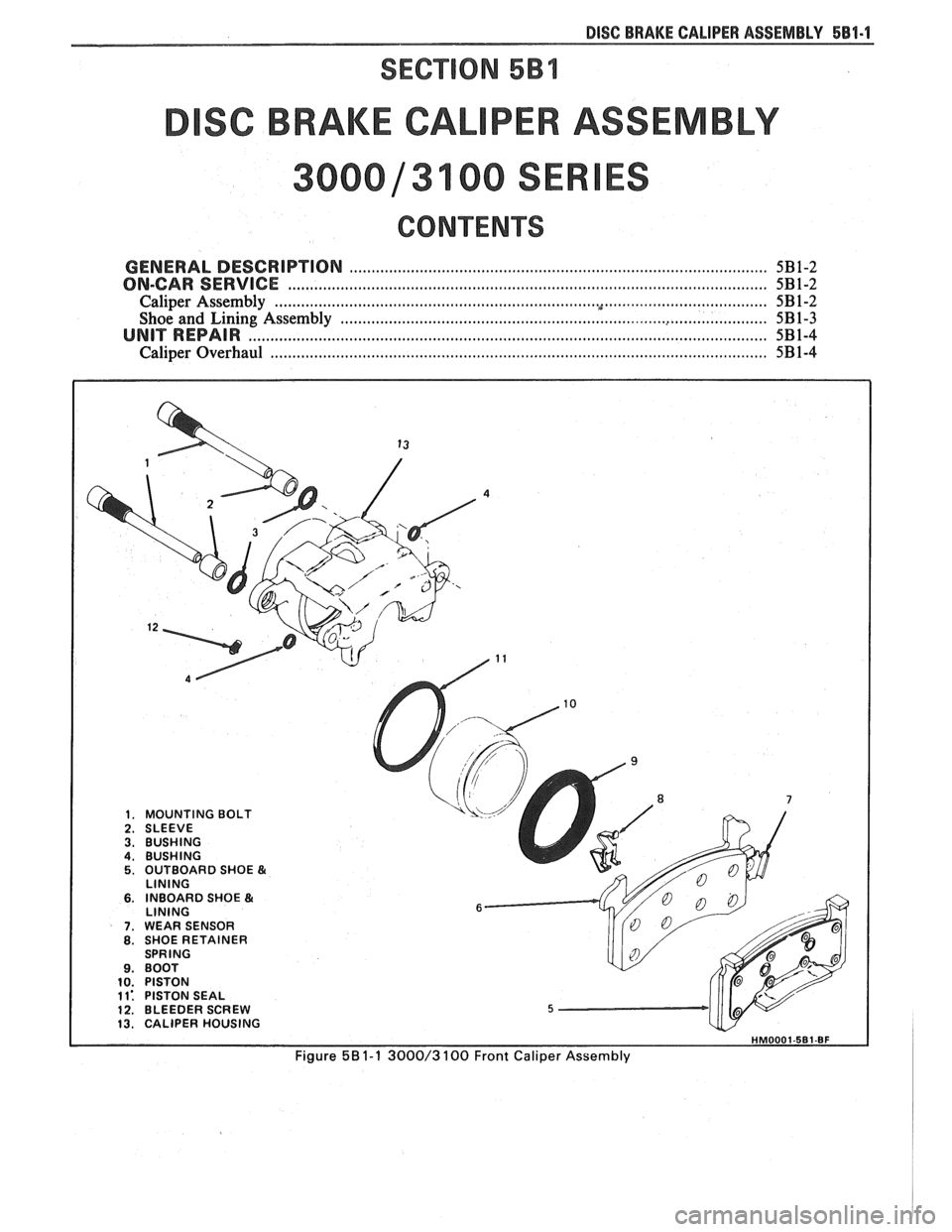
DISC BRAKE CALIPER ASSEMBLY 581.1
SC BRAKE CAL PER ASSEMBLY
3100 SER
CONTENTS
GENERAL DESCRIPTION ........................................................................................ 5B1-2
ON-CAR SERVICE .......................... . ...... .................. ............. 5B1-2
Caliper Assembly . . . .... .. . .... . .. . . ... ... ... . . .... . . . , . . . . . . . . .. . . . . . . . . . . . . . . . . . . . . . . . . . . . . . . . . . . . . . . . . .. . . . . . . . . 5B 1-2
Shoe and Lining Assembly .. . .... . . .. . ... . .. . . ... . . .. . . . . .. . . . .. . .. . . . . . . . . . . . . . . . . . . . . . . . . . . . . . . . . . . . . . . , , ,. . , , . 5B 1-3
UNIT REPAIR ................ . .... .... .... ............. . ........... . . . 5B1-4
Caliper Overhaul .. . . .. . . .. . . ... . .. . .. . . ... . .. . .. . . .. . . , , . . , , , . . , . . , . . . . . . . . . . . . . . . . . . . . . . . . . . . . . . . . . . . . . . . . , . . . , , . . , , . 5B 1-4
Page 317 of 1825
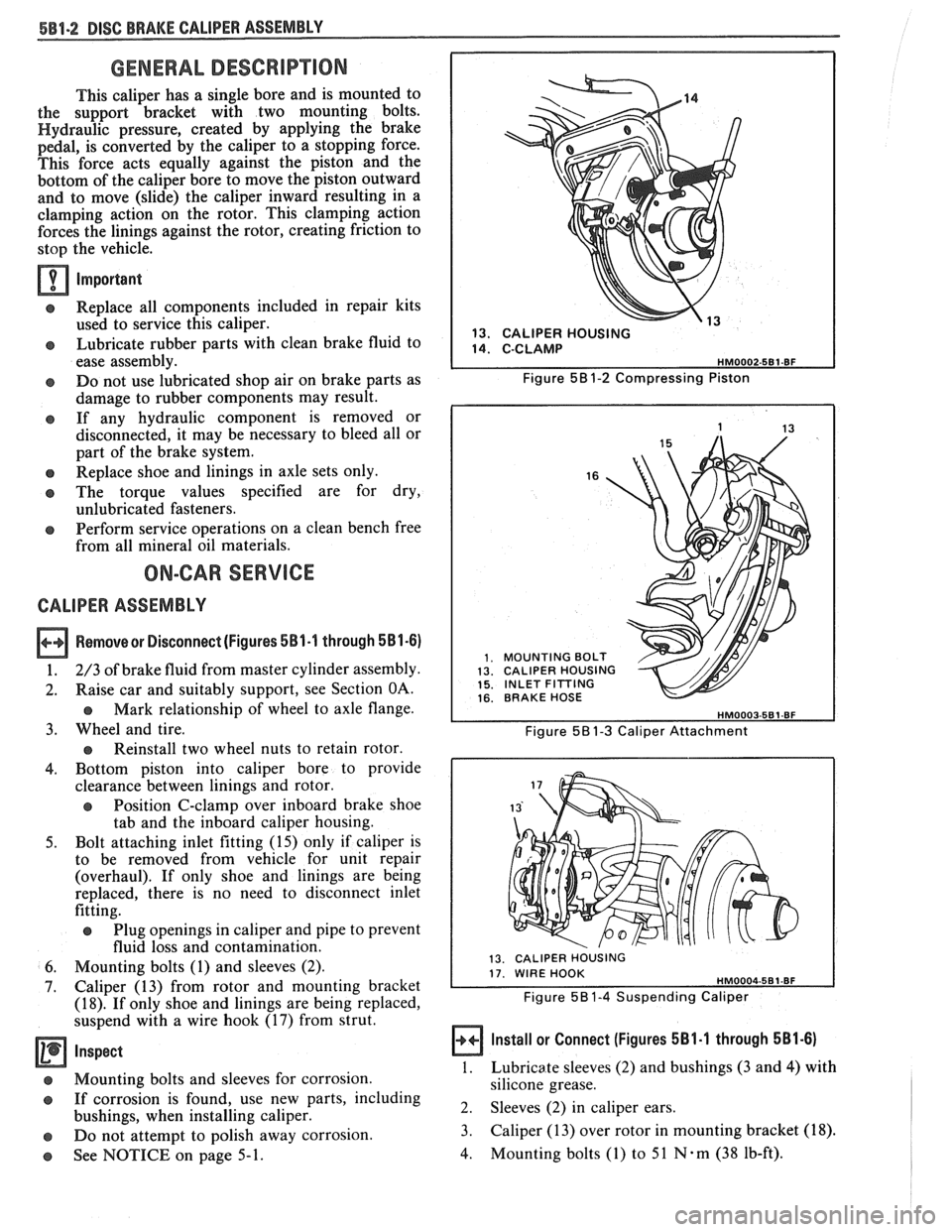
SBO-2 DISC BRAKE CALIPER ASSEMBLY
GENERAL DESCRIP"F0N
This caliper has a single bore and is mounted to
the support bracket with two mounting bolts.
Hydraulic pressure, created by applying the brake
pedal, is converted by the caliper to a stopping force.
This force acts equally against the piston and the
bottom of the caliper bore to move the piston outward
and to move (slide) the caliper inward resulting in a
clamping action on the rotor. This clamping action
forces the linings against the rotor, creating friction to
stop the vehicle.
Important
e Replace all components included in repair kits
used to service this caliper.
Lubricate rubber parts with clean brake fluid to
ease assembly.
e Do not use lubricated shop air on brake parts as
damage to rubber components may result.
e If any hydraulic component is removed or
disconnected, it may be necessary to bleed all or
part of the brake system.
Replace shoe and linings in axle sets only.
e The torque values specified are for dry,
unlubricated fasteners.
s Perform service operations on a clean bench free
from all mineral oil materials.
ON-GAR SERVICE
CALIPER ASSEMBLY
Removesr Disconnect (Figures 581-1 through 581-6)
1. 2/3 of brake fluid from master cylinder assembly.
2. Raise car and suitably support, see Section OA.
Mark relationship of wheel to axle flange.
3. Wheel and tire.
Reinstall two wheel nuts to retain rotor.
4. Bottom piston into caliper bore to provide
clearance between linings and rotor.
e Position C-clamp over inboard brake shoe
tab and the inboard caliper housing.
5. Bolt attaching inlet fitting (15) only if caliper is
to be removed from vehicle for unit repair
(overhaul). If only shoe and linings are being
replaced, there is no need to disconnect inlet
fitting.
e Plug openings in caliper and pipe to prevent
fluid loss and contamination.
6. Mounting bolts (1) and sleeves (2).
7. Caliper (13) from rotor and mounting bracket
(18). If only shoe and linings are being replaced,
suspend with a wire hook (17) from strut.
Inspect
@ Mounting bolts and sleeves for corrosion.
@ If corrosion is found, use new parts, including
bushings, when installing caliper.
e Do not attempt to polish away corrosion.
See NOTICE on page 5-1.
," 13. CALIPER HOUSING
Figure
58 1-2 Compressing Piston
16
MOUNTING BOLT CALIPER HOUSING INLET FITTING BRAKE HOSE
Figure 58 1-3 Caliper Attachment
13. CALIPER HOUSING
Figure 5B1-4 Suspending Caliper
Install or Connect (Figures 581.1 through 581-6)
1.
Lubricate sleeves (2) and bushings (3 and 4) with
silicone grease.
2. Sleeves (2) in caliper ears.
3. Caliper (13) over rotor in mounting bracket
(18).
4. Mounting bolts (1) to 51 N-m (38 lb-ft).
Page 318 of 1825
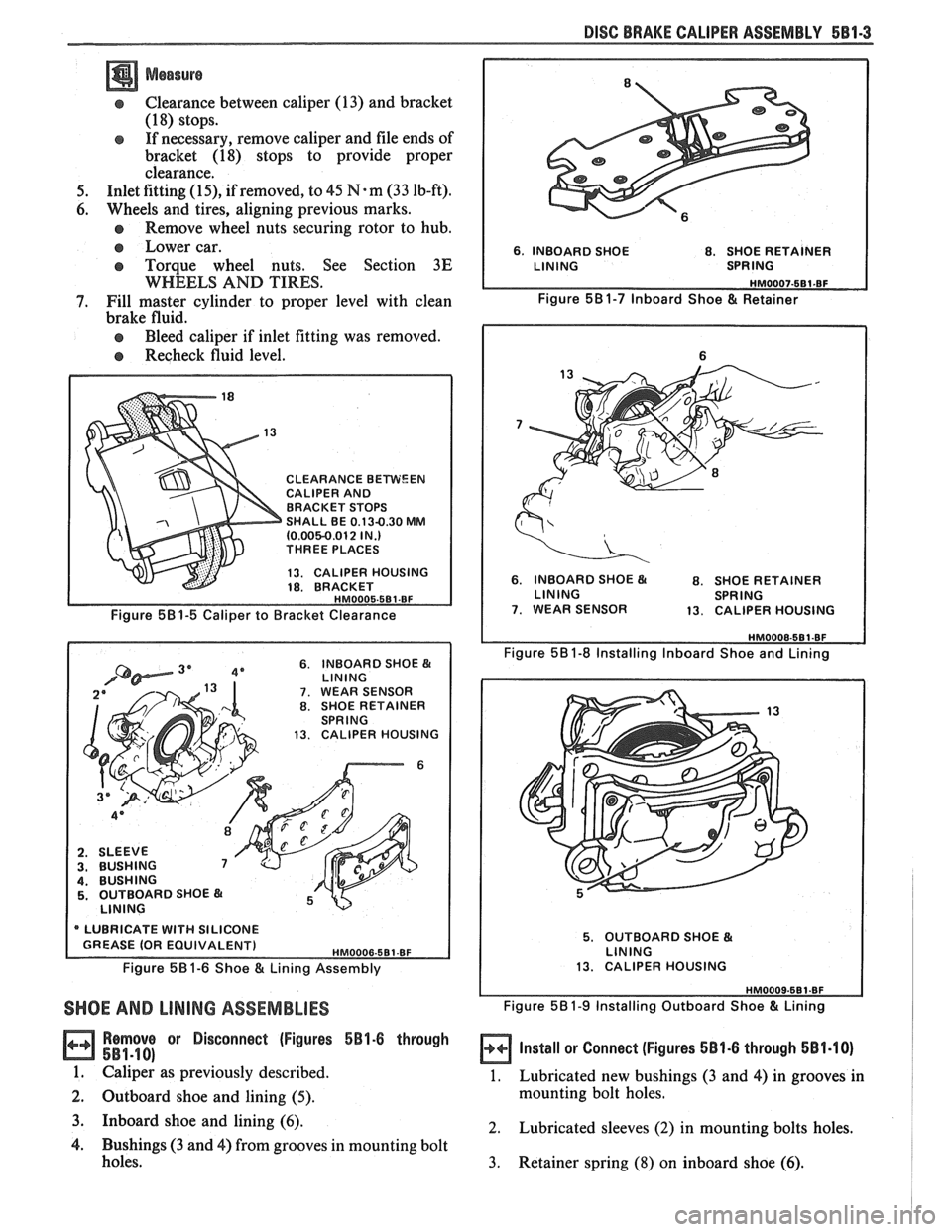
DISC BRAKE CALIPER ASSEMBLY 581-3
a Measure
Clearance between caliper (13) and bracket
(1 8) stops.
If necessary, remove caliper and file ends of
bracket
(18) stops to provide proper
clearance.
5. Inlet fitting (15), if removed, to 45 N-m (33 lb-ft).
6. Wheels and tires, aligning previous marks.
Remove wheel nuts securing rotor to hub.
e Lower car.
e Torque wheel nuts. See Section 3E
WHEELS AND TIRES.
7. Fill master cylinder to proper level with clean
brake fluid.
Bleed caliper if inlet fitting was removed.
Recheck fluid level.
CLEARANCE BEWEEN CALIPER AND
BRACKET STOPS
SHALL BE
0.13-0.30 MM (0.0050.012 IN.) THREE PLACES
13. CALIPER HOUSING
18. BRACKET
Figure 581-5 Caliper to Bracket Clearance
6. INBOARD SHOE B( LlNlNG 7. WEAR SENSOR 8. SHOE RETAINER
SPRING
13. CALIPER HOUSING
6
2. SLEEVE 3. BUSHING 4. BUSHING 5. OUTBOARD SHOE
LlNlNG
* LUBRICATE WITH SILICONE
Figure 58 1-6 Shoe & Lining Assembly
SHOE AND LINING ASSEMBLIES
Remove or Disconnect (Figures 5B1-6 through
581-18)
1. Calipe; as previously described.
2. Outboard shoe and lining
(5).
6, INBOARD SHOE 8. SHOE RETAINER
Figure 581-7 lnboard Shoe & Retainer
6. INBOARD SHOE B( 8. SHOE RETAINER
LINING SPRING
7. WEAR SENSOR 13. CALIPER HOUSING
Figure 581-8 Installing lnboard Shoe and Lining
5. OUTBOARD SHOE & LINING
13. CALIPER HOUSING
Figure 581-9 Installing Outboard Shoe & Lining
Install or Connect (Figures 581.6 through 581.10)
1. Lubricated new bushings (3 and 4) in grooves in
mounting bolt holes.
3. Inboard shoe and lining (6). 2. Lubricated sleeves (2) in mounting bolts holes.
4. Bushings (3 and 4) from grooves in mounting bolt
holes.
3. Retainer spring (8) on inboard shoe (6).
Page 319 of 1825
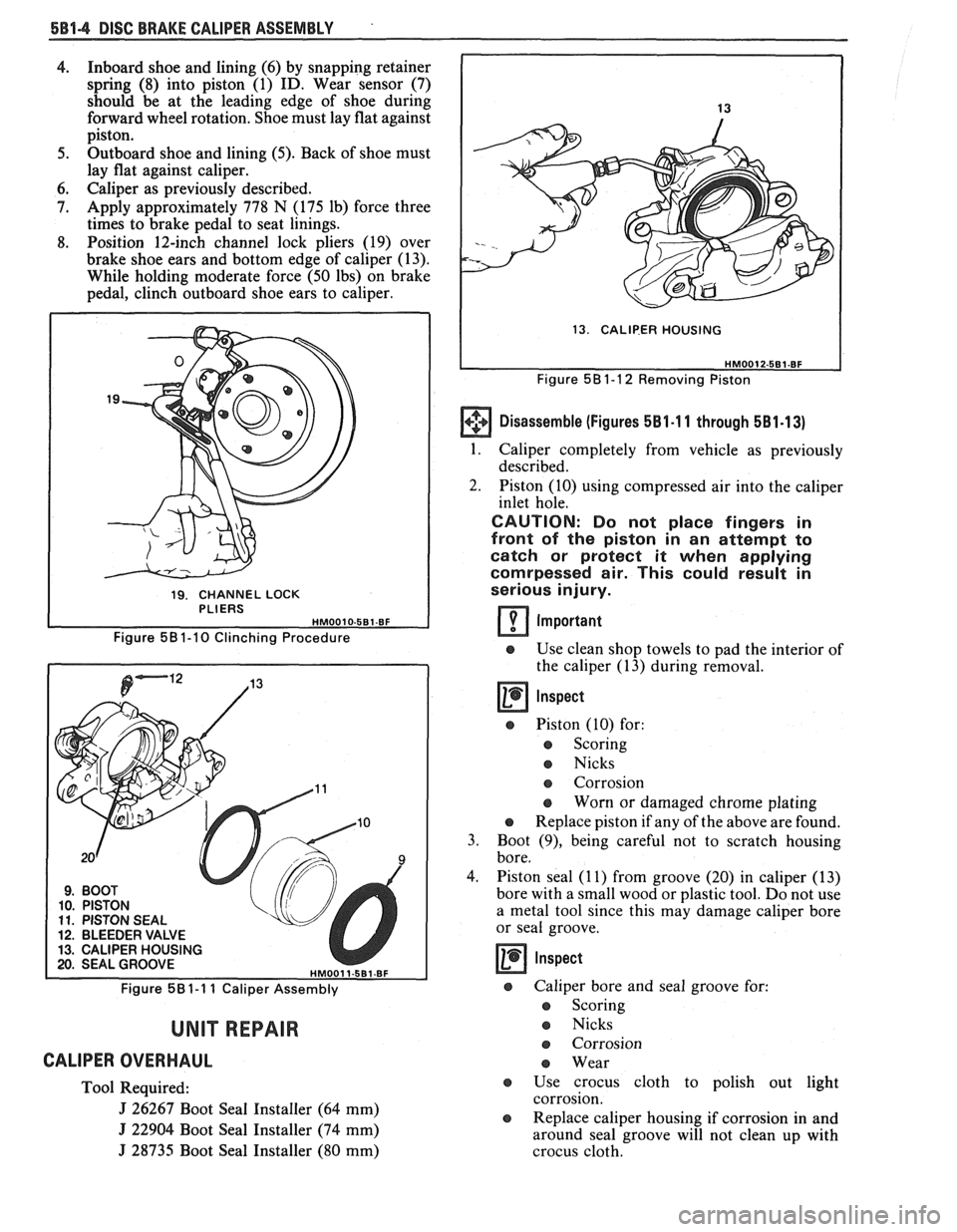
5814 DISC BRAKE CALIPER ASSEMBLY .
4. Inboard shoe and lining (6) by snapping retainer
spring (8) into piston (1) ID. Wear sensor (7)
should be at the leading edge of shoe during
forward wheel rotation. Shoe must lay flat against
piston.
5. Outboard
shoe and lining (5). Back of shoe must
lay flat against caliper.
6. Caliper as previously described.
7. Apply approximately
778
N (175 lb) force three
times to brake pedal to seat linings.
8. Position 12-inch channel lock pliers (19) over
brake shoe ears and bottom edge of caliper (13).
While holding moderate force (50 Ibs) on brake
pedal, clinch outboard shoe ears to caliper.
19. CHANNEL LOCK
PLIERS
Figure 58 1-1 0 Clinching Procedure
9. BOOT 10. PISTON 11. PISTON SEAL 12. BLEEDER VALVE 13. CALIPER HOUSING 20. SEAL GROOVE HMO01 1-5B1-BF
Figure 581-1 1 Caliper Assembly
UNIT REPAIR
CALIPER OVERHAUL
Tool Required:
J 26267 Boot Seal Installer (64 mm)
J 22904 Boot Seal Installer (74 mm)
J 28735 Boot Seal Installer (80 mm)
I
13. CALlP-ER HOUSING
I
Figure 58 1-1 2 Removing Piston
Disassemble (Figures 581-1 1 through 5B1-13)
1. Caliper completely from vehicle as previously
described.
2. Piston (10) using compressed air into the caliper
inlet hole.
CAUTION: Do not place fingers in
front of the piston in an attempt to
catch or protect it when applying
comrpessed air. This could result in
serious injury.
Important
e Use clean shop towels to pad the interior of
the caliper (13) during removal.
@ Piston (10) for:
e Scoring
Nicks
e Corrosion
e Worn or damaged chrome plating
e Replace piston if any of the above are found.
3. Boot (9), being careful not to scratch housing
bore,
4. Piston seal
(1 1) from groove (20) in caliper (13)
bore with a small wood or plastic tool. Do not use
a metal tool since this may damage caliper bore
or seal groove.
Inspect
@ Caliper bore and seal groove for:
e Scoring
e Nicks
e Corrosion
Wear
e Use crocus cloth to polish out light
corrosion.
@ Replace caliper housing if corrosion in and
around seal groove will not clean up with
crocus cloth.
Page 320 of 1825
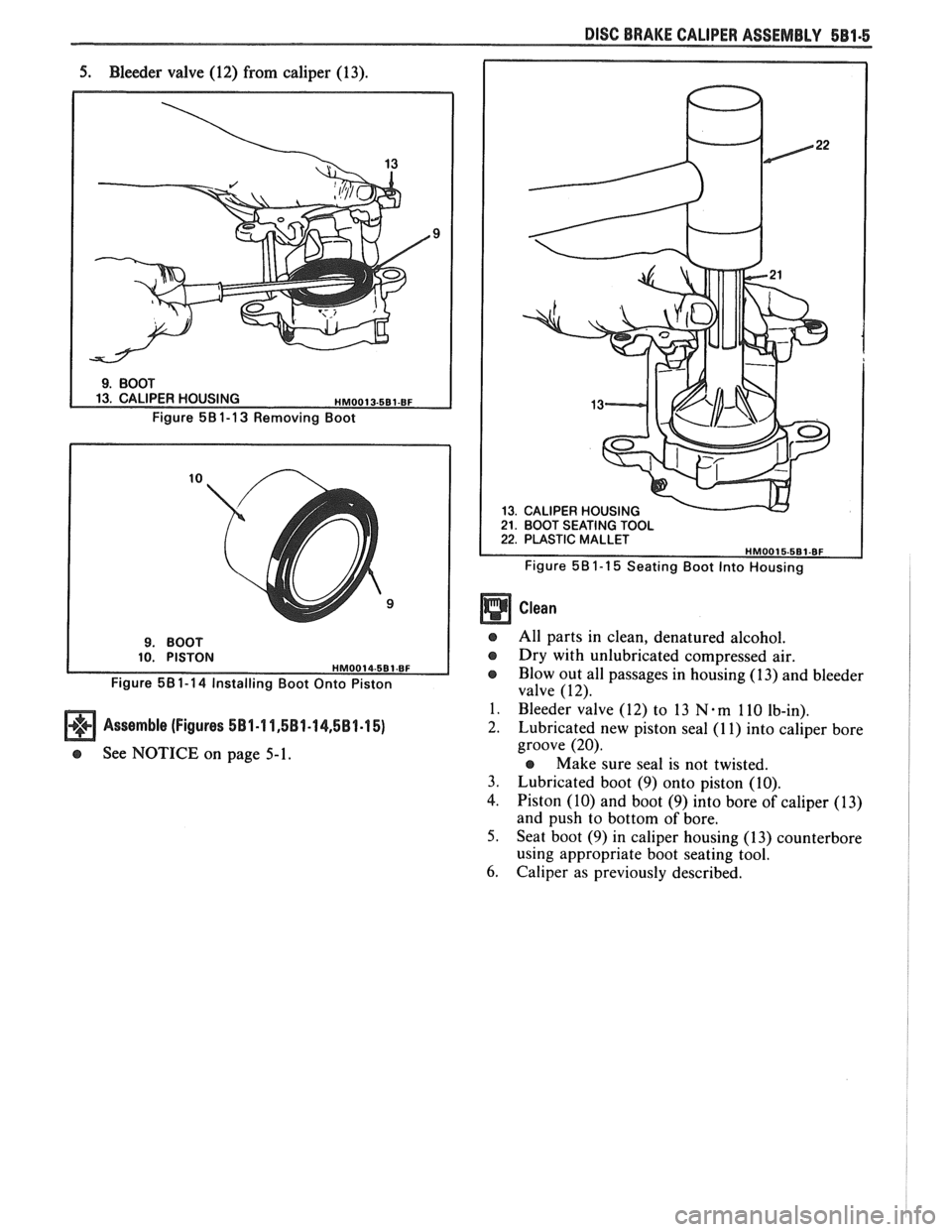
DISC BRAKE CALIPER ASSEMBLY 581-5
5. Bleeder valve (12) from caliper (13).
Figure 581-13 Removing Boot
Figure
58 1-1 4 Installing Boot Onto Piston
Assemble (Figures 581-1 1,581-14,581.15)
@ See NOTICE on page 5-1.
Figure 58 1-1 5 Seating Boot Into Housing
e All parts in clean, denatured alcohol.
@ Dry with unlubricated compressed air.
e Blow out all passages in housing (1 3) and bleeder
valve (12).
Bleeder valve (12) to 13
N-m 1 10 Ib-in).
Lubricated new piston seal
(1 1) into caliper bore
groove (20).
@ Make sure seal is not twisted.
Lubricated boot
(9) onto piston (10).
Piston (10) and boot
(9) into bore of caliper (13)
and push to bottom of bore.
Seat boot
(9) in caliper housing (13) counterbore
using appropriate boot seating tool.
Caliper as previously described.