RENAULT KANGOO 1997 KC / 1.G Sheet Metal Work User Guide
Manufacturer: RENAULT, Model Year: 1997, Model line: KANGOO, Model: RENAULT KANGOO 1997 KC / 1.GPages: 255
Page 11 of 255
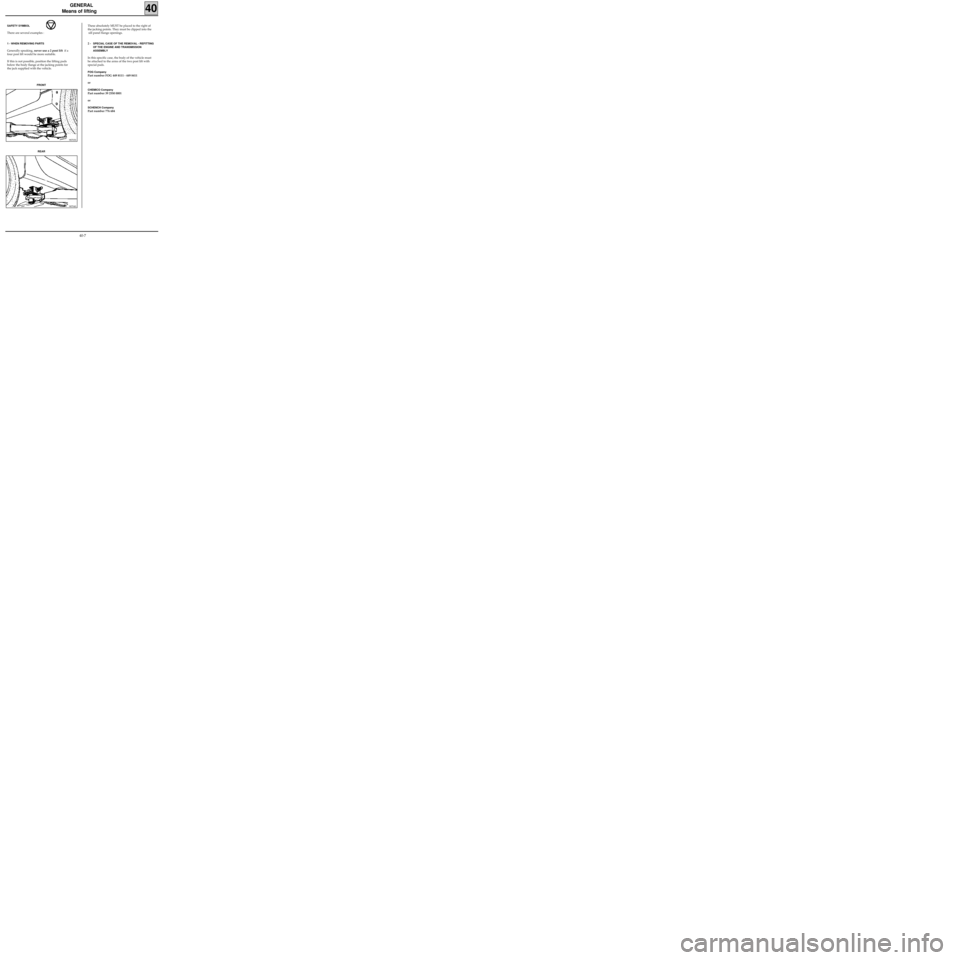
GENERAL
Means of lifting
40
SAFETY SYMBOL
There are several examples :
1 - WHEN REMOVING PARTS
Generally speaking, never use a 2 post lift if a
four post lift would be more suitable.
If this is not possible, position the lifting pads
below the body flange at the jacking points for
the jack supplied with the vehicle.
98703S
FRONT
98704S
REAR
These absolutely MUST be placed to the right of
the jacking points. They must be clipped into the
sill panel flange openings.
2 -
SPECIAL CASE OF THE REMOVAL - REFITTING
OF THE ENGINE AND TRANSMISSION
ASSEMBLY
In this specific case, the body of the vehicle must
be attached to the arms of the two post lift with
special pads.
FOG Company
Part number FOG 449 8111 - 449 8411
or
CHEMICO Company
Part number 39 2550 0001
or
SCHENCH Company
Part number 776 684
40-7
Page 12 of 255
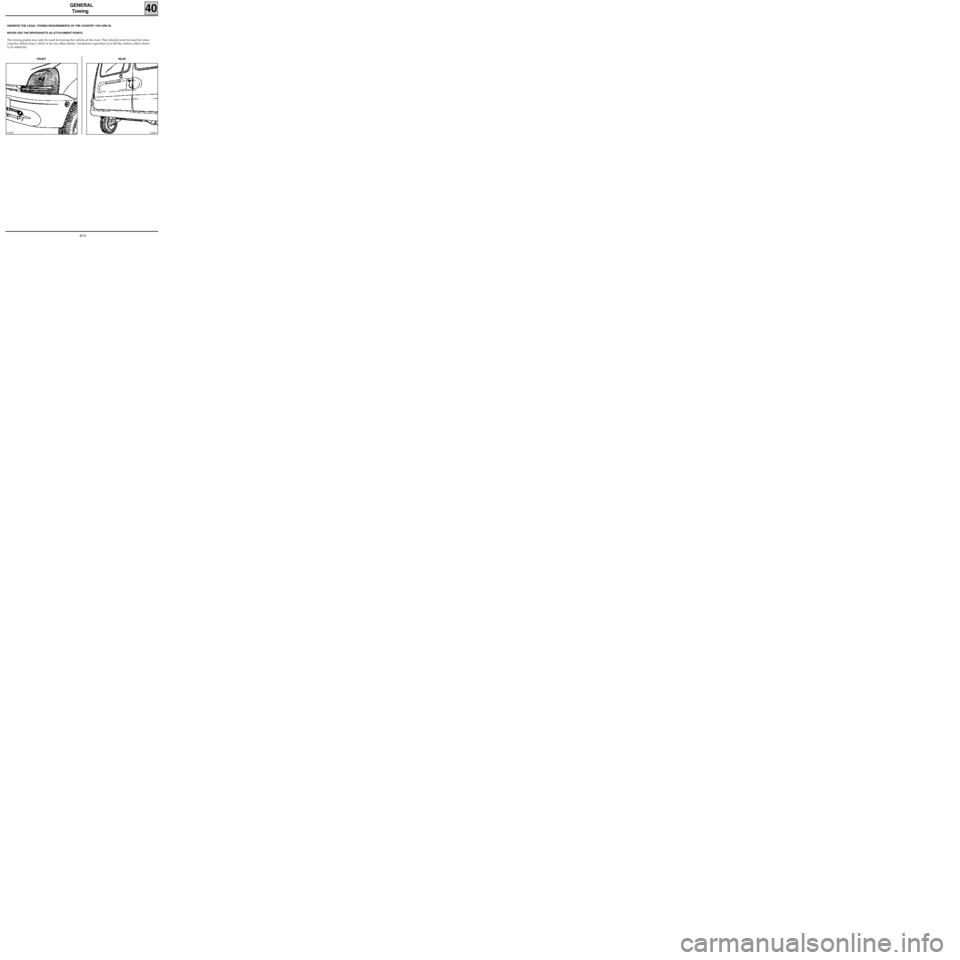
GENERAL
Towing
40
FRONT OBSERVE THE LEGAL TOWING REQUIREMENTS OF THE COUNTRY YOU ARE IN.
NEVER USE THE DRIVESHAFTS AS ATTACHMENT POINTS.
The towing points may only be used for towing the vehicle on the road. They should never be used for remo-
ving the vehicle from a ditch or for any other similar breakdown operation or to lift the vehicle, either direct-
ly or indirectly.
REAR
13366S13189S
40-8
Page 13 of 255
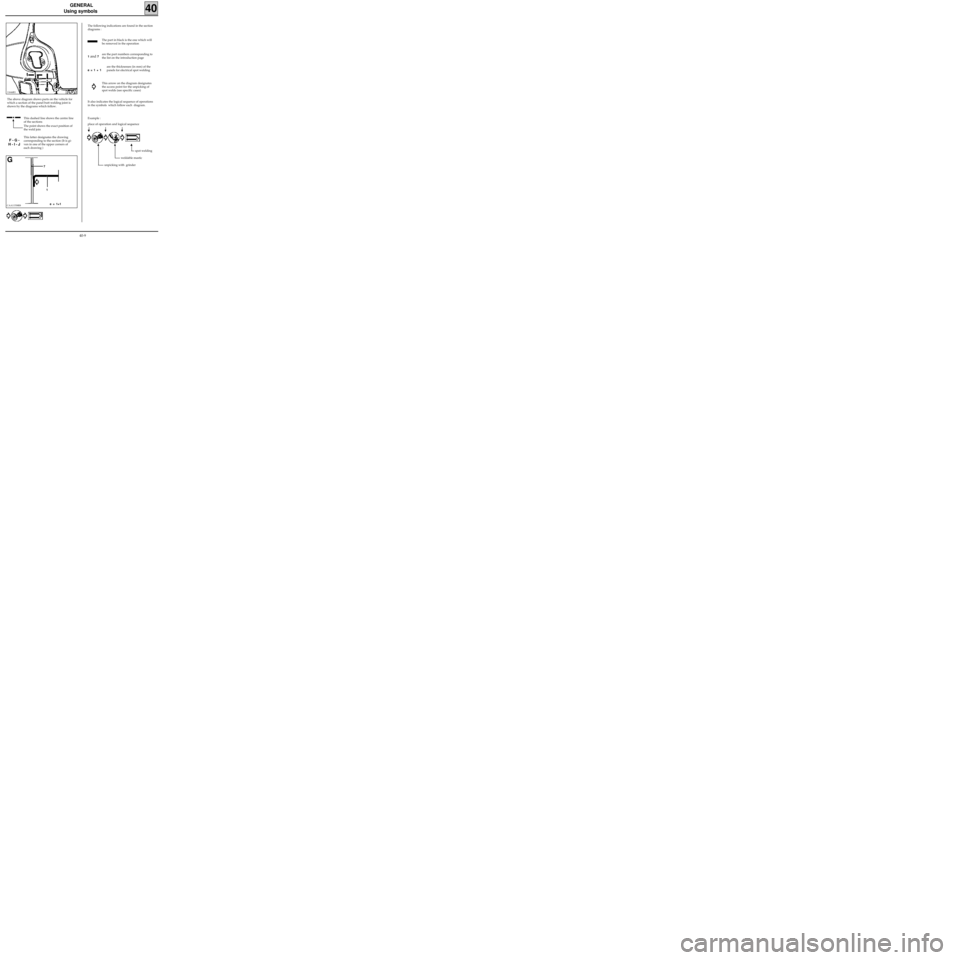
GENERAL
Using symbols
40
11644R1
The above diagram shows parts on the vehicle for
which a section of the panel butt welding joint is
shown by the diagrams which follow.
This dashed line shows the centre line
of the sections
The point shows the exact position of
the weld join
This letter designates the drawing
corresponding to the section (It is gi-
ven in one of the upper corners of
each drawing )
F - G -
H - I - J
CAA11538R8
G
1
e = 1+1 7The following indications are found in the section
diagrams :
The part in black is the one which will
be removed in the operation
are the part numbers corresponding to
the list on the introduction page 1
and 7
e = 1 + 1are the thicknesses (in mm) of the
panels for electrical spot welding
This arrow on the diagram designates
the access point for the unpicking of
spot welds (see specific cases)
It also indicates the logical sequence of operations
in the symbols which follow each diagram.
place of operation and logical sequence
spot welding
weldable mastic
unpicking with grinder
Example :
40-9
Page 14 of 255
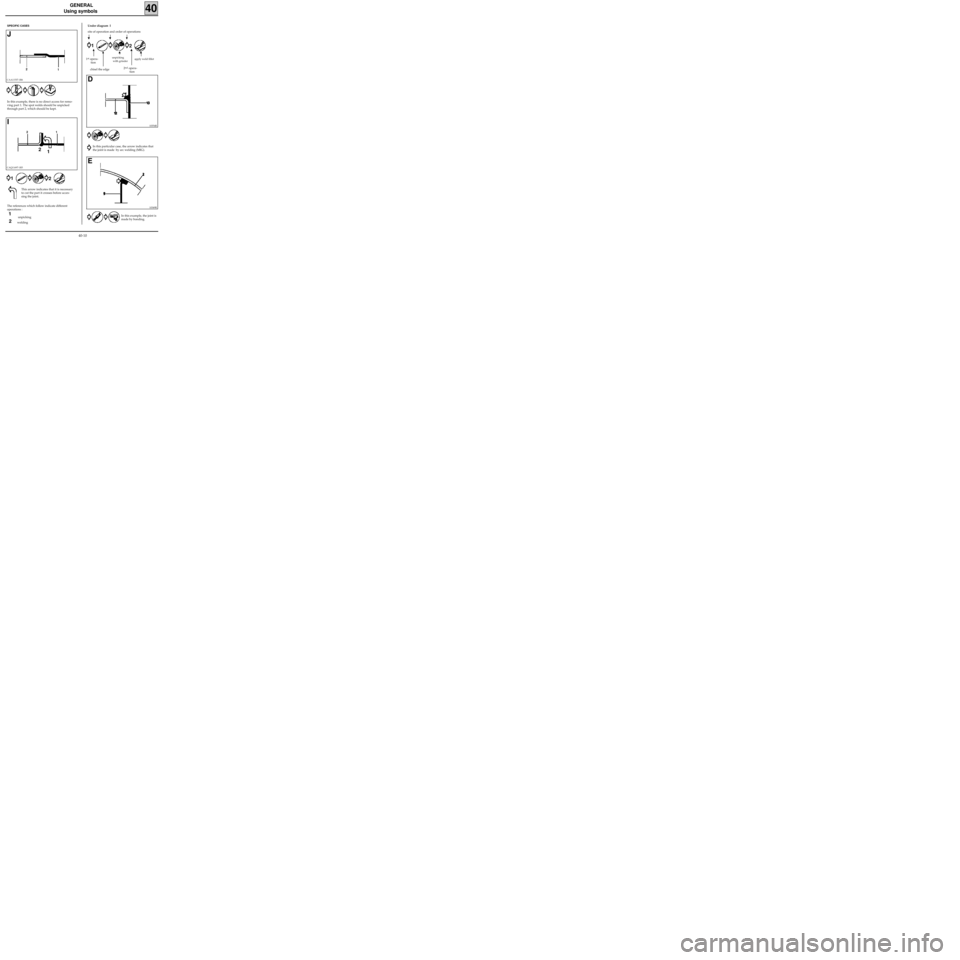
GENERAL
Using symbols
40
The references which follow indicate different
operations :
unpicking
welding
SPECIFIC CASES
CAA11537-1R6
J
1 2
In this example, there is no direct access for remo-
ving part 1. The spot welds should be unpicked
through part 2, which should be kept.
CAQ11697-1R5
I
1 2
1
2
This arrow indicates that it is necessary
to cut the part it crosses before acces-
sing the joint
.
Under diagram I
1
2
unpicking
with grinderapply weld fillet1st opera-
tion
site of operation and order of operations
10354R
D
In this particular case, the arrow indicates that
the joint is made by arc welding (MIG).
10349R
E
In this example, the joint is
made by bonding.
chisel the edge2nd opera-
tion
1 2
1
2
40-10
Page 15 of 255
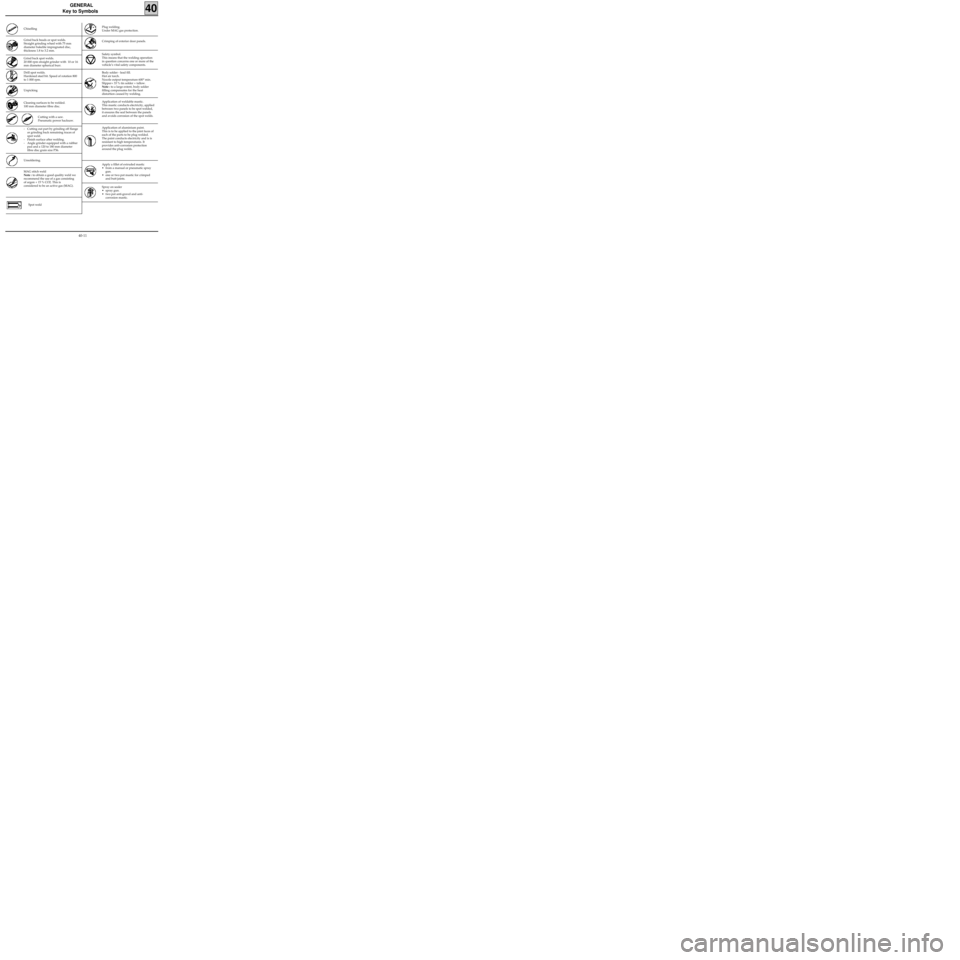
GENERAL
Key to Symbols
40
- Cutting out part by grinding off flange
or grinding back remaining traces of
spot weld.
- Finish surface after welding.
- Angle grinder equipped with a rubber
pad and a 120 to 180 mm diameter
fibre disc grain size P36. Chiselling
Grind back beads or spot welds.
Straight grinding wheel with 75 mm
diameter bakelite impregnated disc,
thickness 1.8 to 3.2 mm.
Grind back spot welds.
20 000 rpm straight grinder with 10 or 16
mm diameter spherical burr.
Drill spot welds.
Hardened steel bit. Speed of rotation 800
to 1 000 rpm.
Unpicking
Cleaning surfaces to be welded.
100 mm diameter fibre disc.
Cutting with a saw.
Pneumatic power hacksaw.
Unsoldering.
Plug welding.
Under MAG gas protection.
Crimping of exterior door panels.
Safety symbol.
This means that the welding operation
in question concerns one or more of the
vehicle’s vital safety components.
Body solder - lead fill.
Hot air torch.
Nozzle output temperature 600° min.
Slipper+ 33 % tin solder + tallow.
Note : to a large extent, body solder
filling compensates for the heat
distortion caused by welding.
Application of weldable mastic.
This mastic conducts electricity, applied
between two panels to be spot welded,
it ensures the seal between the panels
and avoids corrosion of the spot welds.
Application of aluminium paint.
This is to be applied to the joint faces of
each of the parts to be plug welded.
The paint conducts electricity and is is
resistant to high temperatures. It
provides anti-corrosion protection
around the plug welds.
Apply a fillet of extruded mastic
• from a manual or pneumatic spray
gun.
• one or two pot mastic for crimped
and butt joints.
Spray on sealer
• spray gun.
• two pot anti-gravel and anti-
corrosion mastic.
MAG stitch weld
Note : to obtain a good quality weld we
recommend the use of a gas consisting
of argon + 15 % CO2. This is
considered to be an active gas (MAG).
Spot weld
40-11
Page 16 of 255
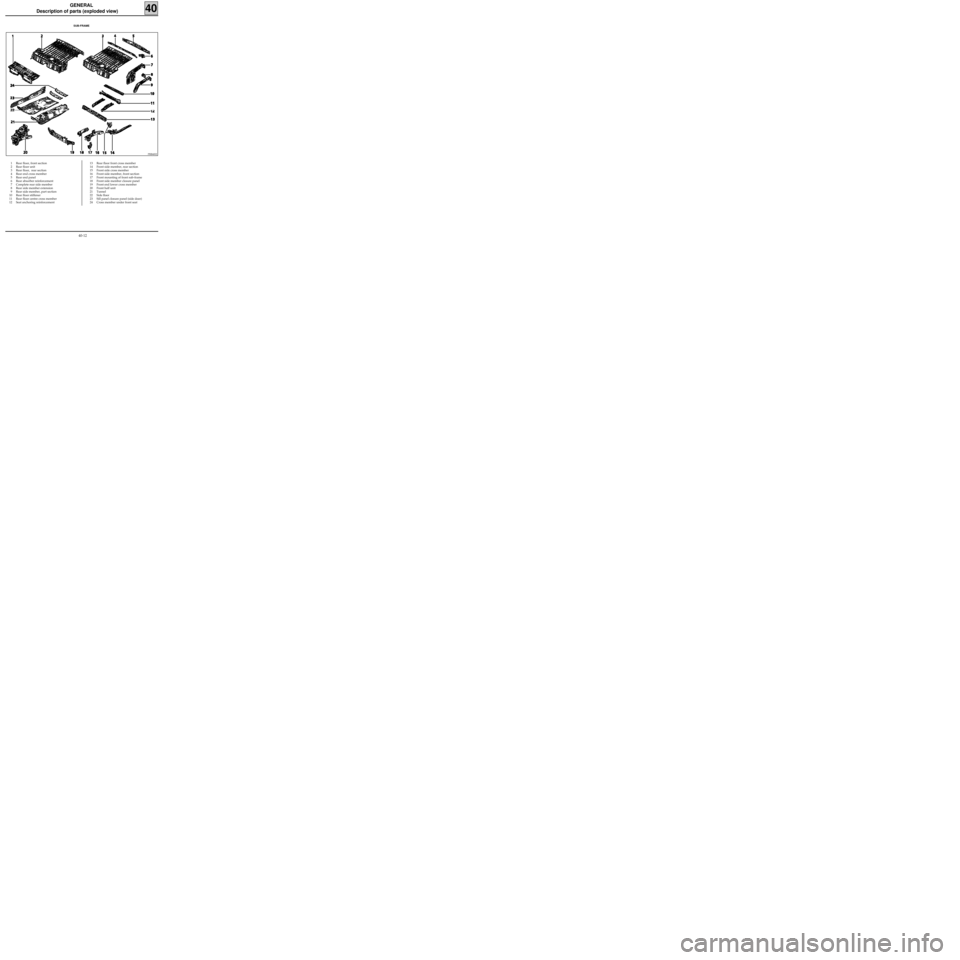
GENERAL
Description of parts (exploded view)
40
PRB4002
1 Rear floor, front section
2 Rear floor unit
3 Rear floor, rear section
4 Rear end cross member
5 Rear end panel
6 Rear absorber reinforcement
7 Complete rear side member
8 Rear side member extension
9 Rear side member, part section
10 Rear floor stiffener
11 Rear floor centre cross member
12 Seat anchoring reinforcement13 Rear floor front cross member
14 Front side member, rear section
15 Front side cross member
16 Front side member, front section
17 Front mounting of front sub-frame
18 Front side member closure panel
19 Front end lower cross member
20 Front half unit
21 Tunnel
22 Side floor
23 Sill panel closure panel (side door)
24 Cross member under front seat
SUB-FRAME
40-12
Page 17 of 255
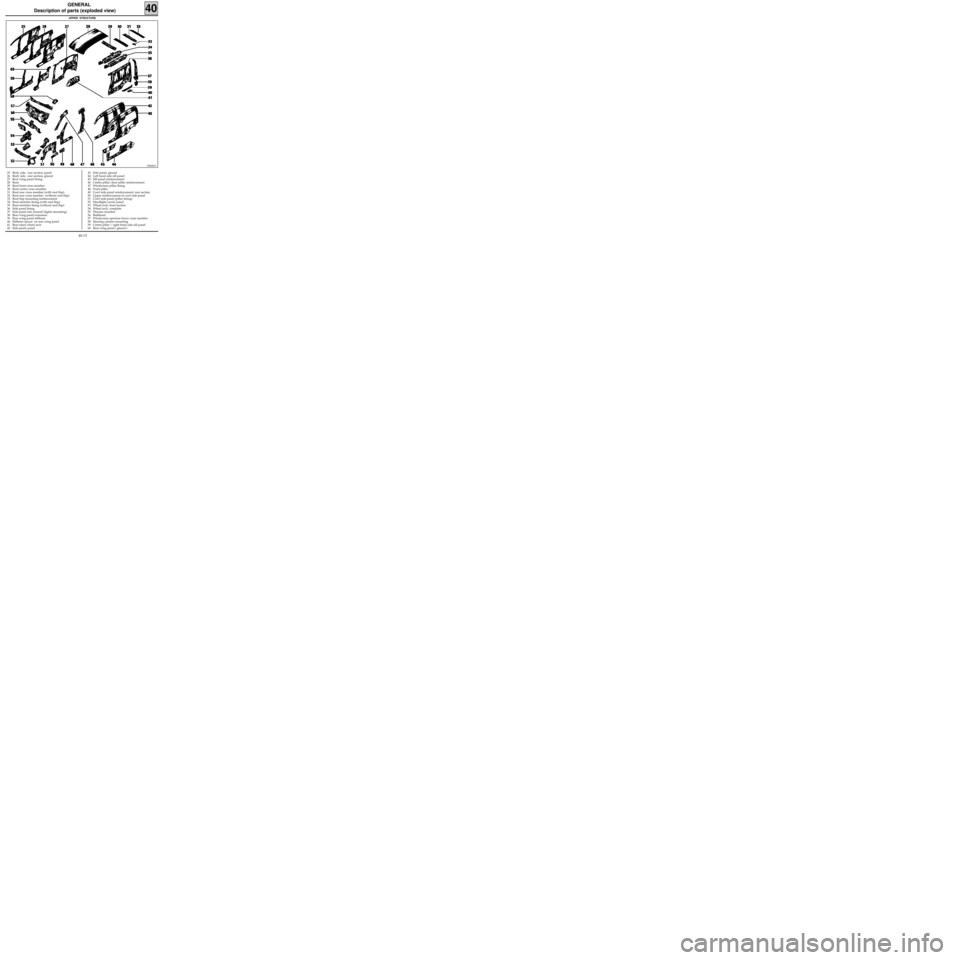
GENERAL
Description of parts (exploded view)
40
PRB4003
UPPER STRUCTURE
25 Body side, rear section, panel
26 Body side , rear section, glazed
27 Rear wing panel lining
28 Roof
29 Roof front cross member
30 Roof centre cross member
31 Roof rear cross member (with roof flap)
32 Roof rear cross member (without roof flap)
33 Roof flap mounting reinforcement
34 Roof stretcher lining (with roof flap)
35 Roof stretcher lining (without roof flap)
36 Side panel lining
37 Side panel rain channel (lights mounting)
38 Rear wing panel extension
39 Rear wing panel stiffener
40 Stiffener spacer on rear wing panel
41 Rear inner wheel arch
42 Side panel, panel43 Side panel, glazed
44 Left hand side sill panel
45 Sill panel reinforcement
46 Centre pillar/door pillar reinforcement
47 Windscreen pillar lining
48 Front pillar
49 Cowl side panel reinforcement, rear section
50 Upper reinforcement of cowl side panel
51 Cowl side panel (pillar lining)
52 Headlight carrier panel
53 Wheel arch, front section
54 Wheel arch, complete
55 Plenum chamber
56 Bulkhead
57 Windscreen aperture lower cross member
58 Steering column mounting
59 Centre pillar / right hand side sill panel
60 Rear wing panel ( glazed )
40-13
Page 18 of 255

GENERAL
Description of parts (exploded view)
40
PRB4004
61 Hinged roof flap
62 Tailgate
63 Rear opening door, right hand side
64 Rear opening door, left hand side
65 Front door panel
66 Front door
67 Front wing
68 Bonnet
69 Side door
70 Side door panel
REMOVABLE COMPONENTS
40-14
Page 19 of 255
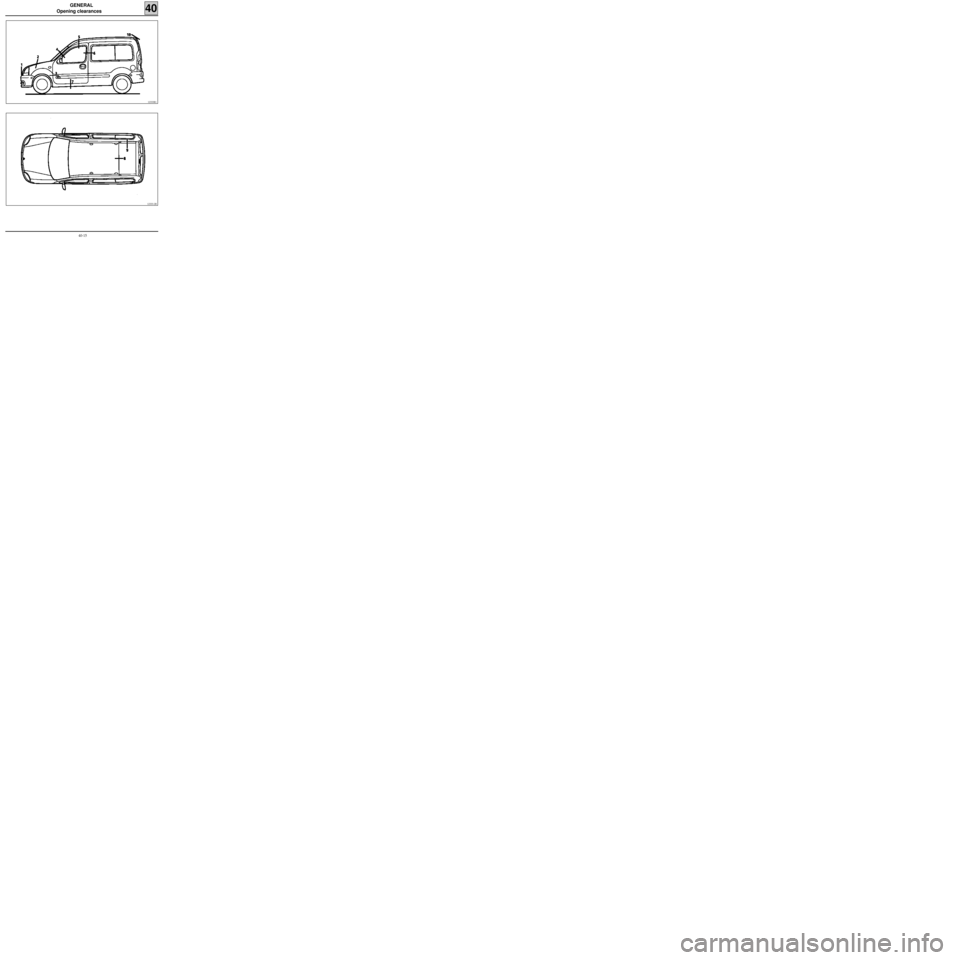
GENERAL
Opening clearances
40
12333-2R
12333R1
40-15
Page 20 of 255
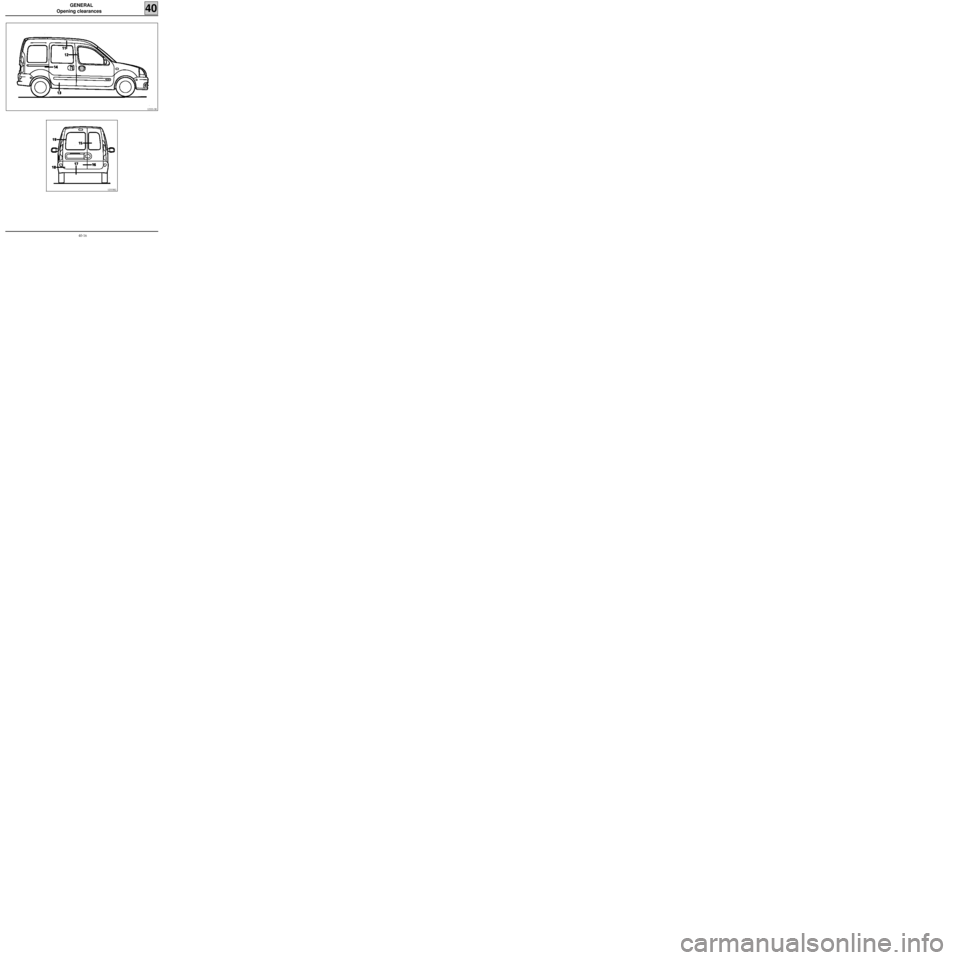
GENERAL
Opening clearances
40
12333R2
12333-3R
40-16