service DATSUN PICK-UP 1977 Workshop Manual
[x] Cancel search | Manufacturer: DATSUN, Model Year: 1977, Model line: PICK-UP, Model: DATSUN PICK-UP 1977Pages: 537, PDF Size: 35.48 MB
Page 298 of 537
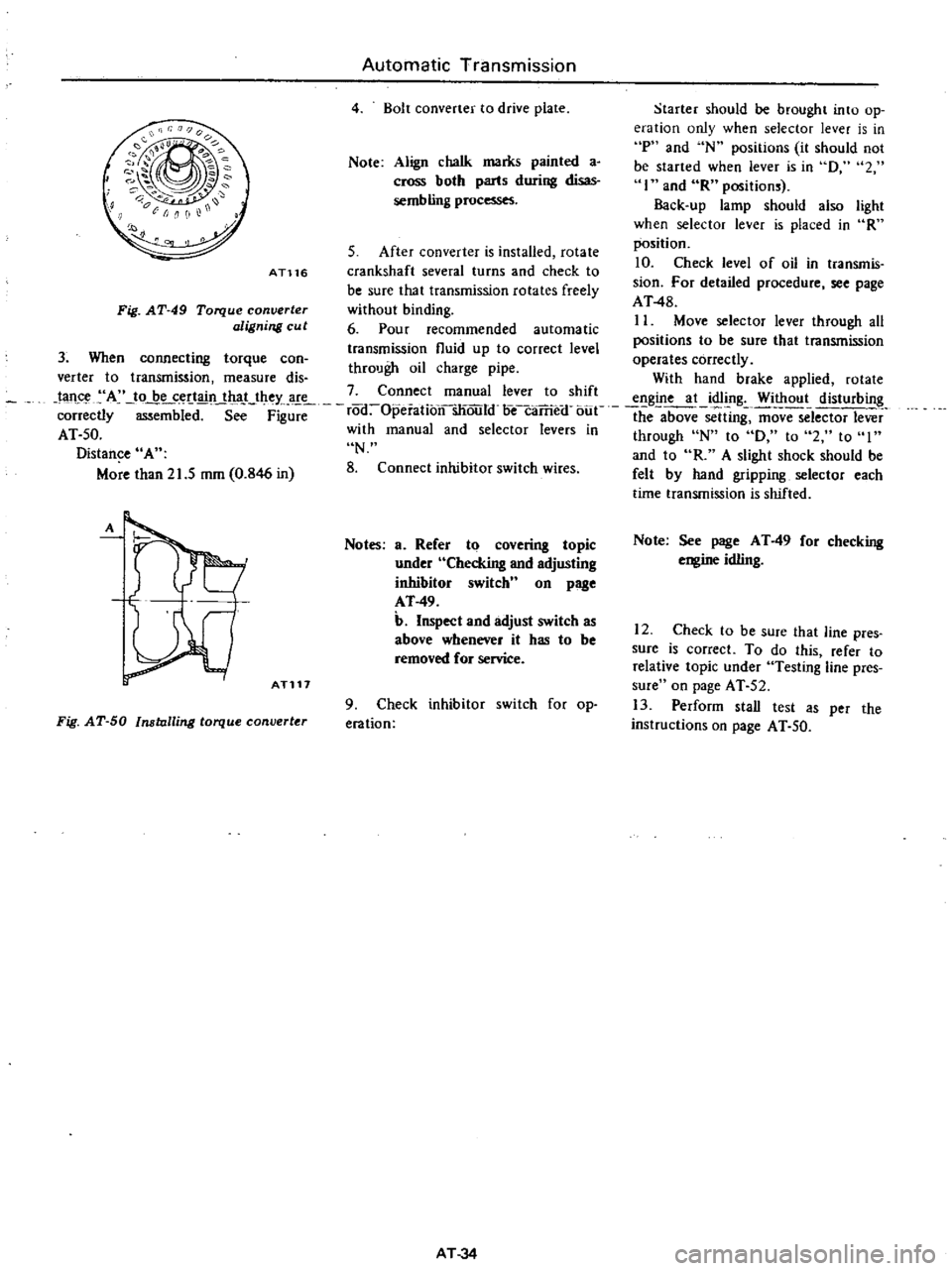
Starter
should
be
brought
into
op
eration
only
when
selector
lever
is
in
P
and
N
positions
it
should
not
be
started
when
lever
is
in
D
2
I
and
R
positions
Back
up
lamp
should
also
light
when
selector
lever
is
placed
in
R
position
S
After
converter
is
installed
rotate
10
Check
level
of
oil
in
transmis
crankshaft
several
turns
and
check
to
be
sure
that
transmission
rotates
freely
sion
For
detailed
procedure
see
page
AT48
without
binding
6
Pour
recommended
automatic
II
Move
selector
lever
through
aU
positions
to
be
sure
that
transmission
transmission
fluid
up
to
correct
level
operates
correctly
through
oil
charge
pipe
verter
to
transmission
measure
dis
With
hand
brake
applied
rotate
tan
A
to
be
certain
that
they
are
7
Connect
manual
lever
to
shift
engine
at
idling
Without
disturbing
correctly
mbi
d
S
F
rod
Opeiationsliould
oecaTrie
f
bue
the
above
sclUng
ffiovTSelector
lever
AT
50
with
manual
and
selector
levers
in
through
N
to
D
to
2
to
I
Distance
A
N
and
to
R
A
slight
shock
should
be
More
than
21
5
mm
0
846
in
8
Connect
inhibitor
switch
wires
felt
by
hand
gripping
selector
each
time
transmission
is
shifted
Automatic
Transmission
4
Bolt
converter
to
drive
plate
Note
Align
chalk
marks
painted
a
cross
both
parts
during
disas
sembling
processes
AT116
Fig
AT
49
Torque
converter
aligning
cu
t
3
When
connecting
torque
can
A
ATl17
Notes
a
Refer
to
covering
topic
under
Checking
and
adjusting
inhibitor
switch
n
on
page
AT
49
b
Inspect
and
adjust
switch
as
above
whenever
it
has
to
be
removed
for
service
Fig
AT
50
Installing
torque
converter
9
Check
inhibitor
switch
for
op
eration
AT
34
Note
See
page
AT
49
for
checking
engine
idling
12
Check
to
be
sure
that
line
pres
sure
is
correct
To
do
this
refer
to
relative
topic
under
Testing
line
pres
sure
on
page
AT
52
13
Perform
stall
test
as
per
the
instructions
on
page
AT
50
Page 300 of 537
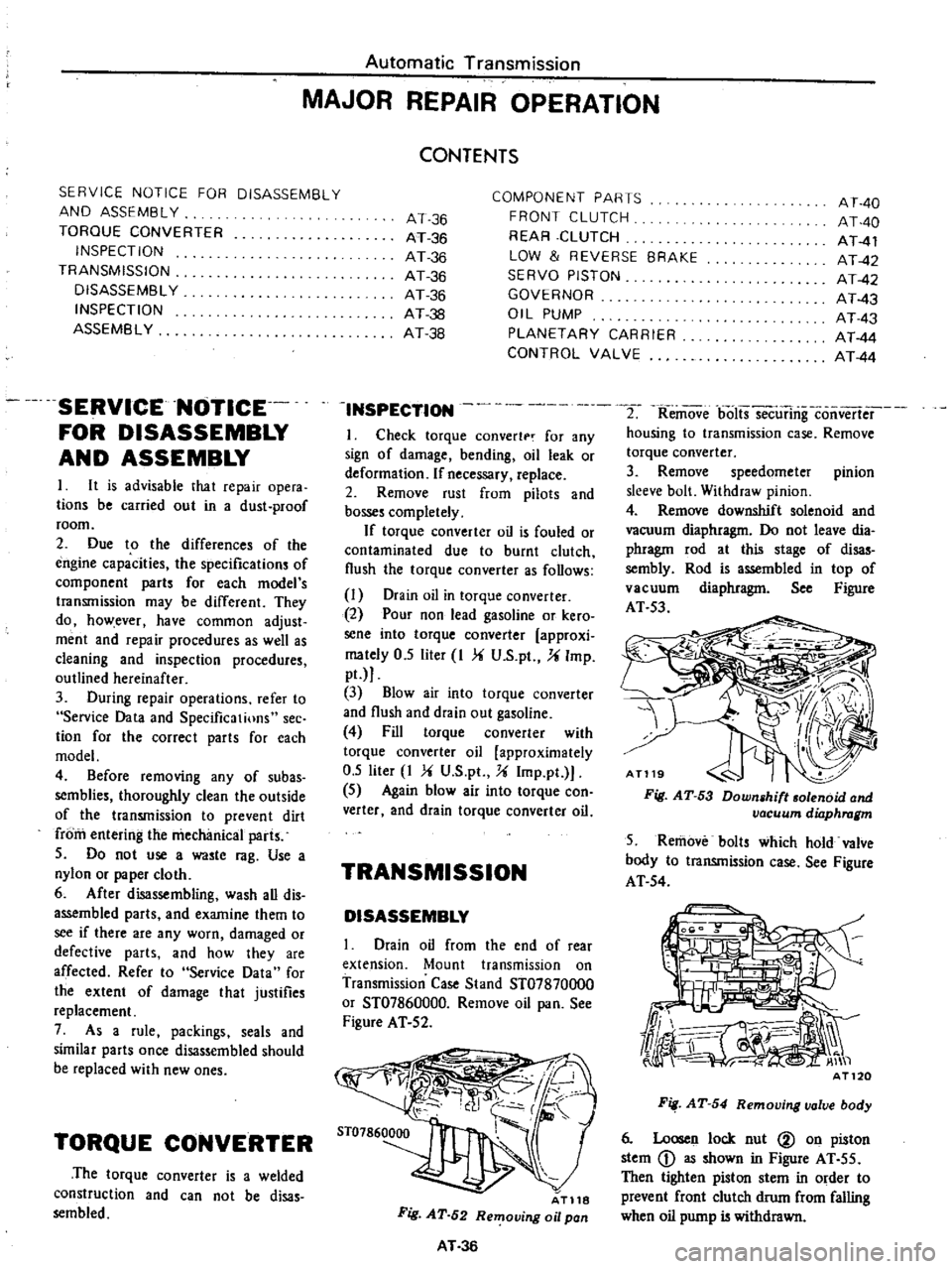
Automatic
Transmission
MAJOR
REPAIR
OPERATION
SERVICE
NOTICE
FOR
DISASSEMBLY
AND
ASSEMBLY
TORQUE
CONVERTER
INSPECTION
TRANSMISSION
DISASSEMBL
Y
INSPECTION
ASSEMBL
Y
SERVICE
NOTICE
FOR
DISASSEMBLY
AND
ASSEMBLY
I
It
is
advisable
that
repair
opera
tions
be
carried
out
in
a
dust
proof
room
2
Due
to
the
differences
of
the
engine
capacities
the
specifications
of
component
parts
for
each
model
s
transmission
may
be
different
They
do
however
have
common
adjust
ment
and
repair
procedures
as
well
as
cleaning
and
inspection
procedures
outlined
hereinafter
3
During
repair
operations
refer
to
Service
Data
and
Specifications
see
tion
for
the
correct
parts
for
each
model
4
Before
removing
any
of
subas
semblies
thoroughly
clean
the
outside
of
the
transmission
to
prevent
dirt
from
entering
the
mechanical
parts
5
Do
not
use
a
waste
rag
Use
a
nylon
or
paper
cloth
6
After
disassembling
wash
all
dis
assembled
parts
and
examine
them
to
see
if
there
are
any
worn
damaged
or
defective
parts
and
how
they
are
affected
Refer
to
Service
Data
for
the
extent
of
damage
that
justifies
replacement
7
As
a
rule
packings
seals
and
similar
parts
once
disassembled
should
be
replaced
with
new
ones
TORQUE
CONVERTER
The
torque
converter
is
a
welded
construction
and
can
not
be
disas
sembled
CONTENTS
AT
36
AT
36
AT
36
AT
36
AT
36
AT
38
AT
38
COMPONENT
PARTS
FRONT
CLUTCH
REAR
CLUTCH
LOW
REVERSE
BRAKE
SERVO
PISTON
GOVERNOR
OIL
PUMP
PLANETARY
CARRIER
CONTROL
VALVE
AT
40
AT
40
AT
41
AT
42
AT
42
AT
43
AT
43
AT
44
AT
44
INSPECTION
2
Remove
bolts
securing
converter
1
Check
torque
convertf
for
any
housing
to
transmission
case
Remove
sign
of
damage
bending
oil
leak
or
torque
converter
deformation
If
necessary
replace
3
Remove
speedometer
pinion
2
Remove
rust
from
pilots
and
sleeve
bolt
Withdraw
pinion
bosses
completely
4
Remove
downshift
solenoid
and
If
torque
converter
oil
is
fouled
or
vacuum
diaphragm
Do
not
leave
dia
contaminated
due
to
burnt
clutch
phragm
rod
at
this
stage
of
disas
flush
the
torque
converter
as
follows
sembly
Rod
is
assembled
in
top
of
vacuum
diaphragm
See
Figure
I
Drain
oil
in
torque
converter
AT
53
2
Pour
non
lead
gasoline
or
kero
sene
into
torque
converter
approxi
mately
0
5
liter
I
U
S
pt
U
Imp
pt
3
Blow
air
into
torque
converter
and
flush
and
drain
out
gasoline
4
Fill
torque
converter
with
torque
converter
oil
approximately
0
5
liter
I
V
S
pt
U
Imp
pt
5
Again
blow
air
into
torque
con
verter
and
drain
torque
converter
oil
TRANSMISSION
DISASSEMBLY
I
Drain
oil
from
the
end
of
rear
extension
Mount
transmission
on
Transmission
Case
Stand
ST07870000
or
ST07860000
Remove
oil
pan
See
Figure
AT
52
AT118
Fig
AT
52
Removing
oil
pan
AT
36
Fig
AT
53
Down
hilt
olenoid
and
vacuum
dilJphragm
5
Remove
bolts
which
hold
valve
body
to
transmission
case
See
Figure
AT
54
Fig
AT
54
Removing
valve
body
6
Loosen
lock
nut
@
on
piston
stem
D
as
shown
in
Figure
AT
55
Then
tighten
piston
stem
in
order
to
prevent
front
clutch
drum
from
falling
when
oil
pump
is
withdrawn
Page 305 of 537
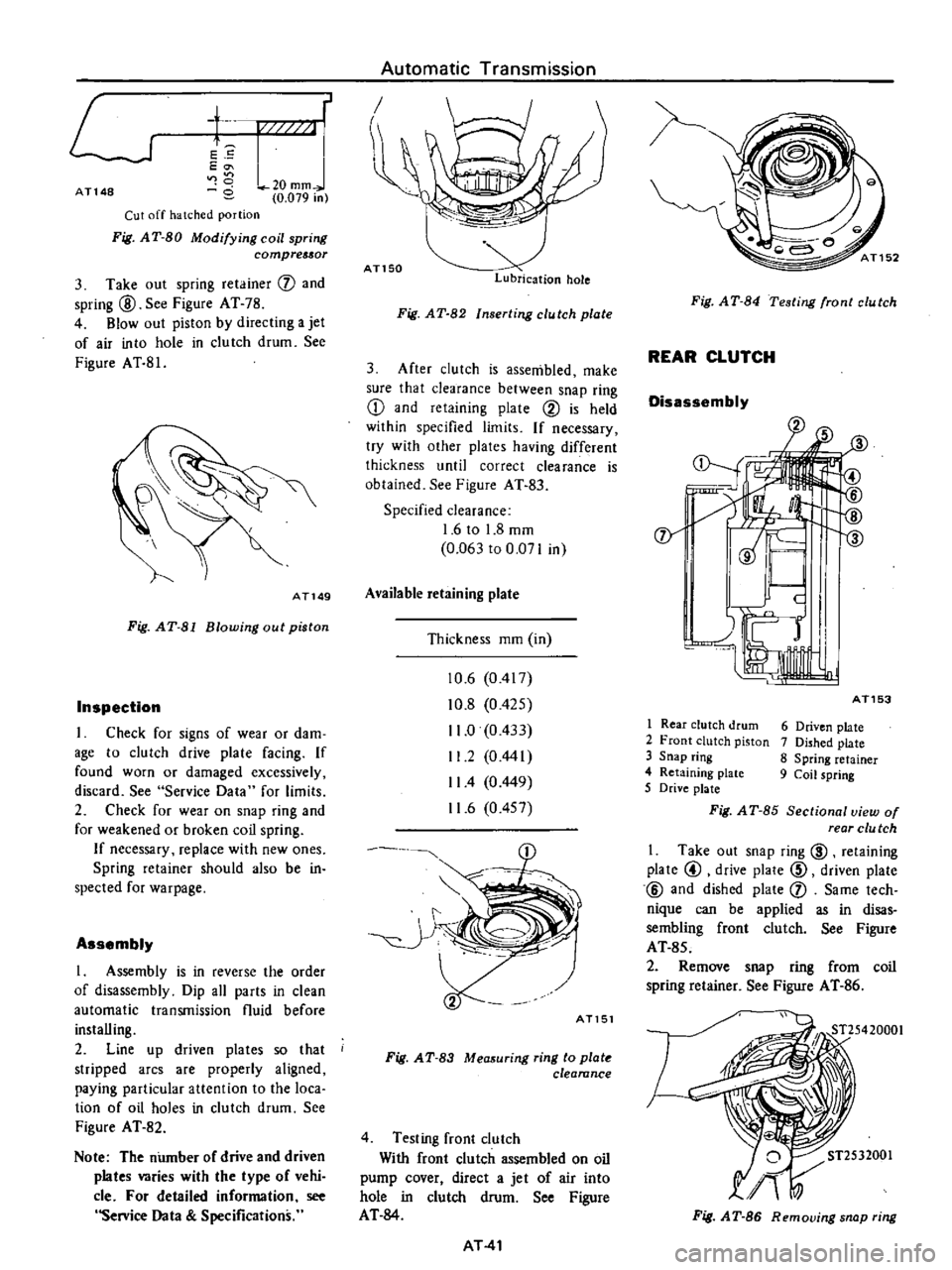
Automatic
Transmission
L
1
r
E
5
Eo
1
20
mm
l
AT148
3
0
079
in
Cut
off
hatched
portion
Fig
AT
SO
Modifying
coil
spring
compres
or
3
Take
out
spring
retainer
f
and
spring
@
See
Figure
AT
78
4
Blowout
piston
by
directing
a
jet
of
air
inlO
hole
in
clutch
drum
See
Figure
A
T
8l
AT149
Fig
AT
81
Blowing
out
piston
Inspection
I
Check
for
signs
of
wear
or
dam
age
to
clutch
drive
plate
facing
If
found
worn
or
damaged
excessively
discard
See
Service
Data
for
limits
2
Check
for
wear
on
snap
ring
and
for
weakened
or
broken
coil
spring
If
necessary
replace
with
new
ones
Spring
retainer
should
also
be
in
spected
for
warpage
Assembly
I
Assembly
is
in
reverse
the
order
of
disassembly
Dip
all
parts
in
clean
automatic
transmission
fluid
before
installing
2
Line
up
driven
plates
so
that
stripped
arcs
are
properly
aligned
paying
particular
attention
to
the
loca
tion
of
oil
holes
in
clutch
drum
See
Figure
AT
82
Note
The
number
of
drive
and
driven
plates
varies
with
the
type
of
vehi
cle
For
detailed
information
see
Service
Data
Specifications
AT150
Lub
ication
hole
Fig
AT
82
Inserting
clutch
plate
3
After
clutch
is
assembled
make
sure
that
clearance
between
snap
ring
CD
and
retaining
plate
@
is
held
within
specified
limits
If
necessary
try
with
other
plates
having
different
thickness
until
correct
clearance
is
obtained
See
Figure
AT
83
Specified
clearance
I
6
to
1
8
mm
0
063
to
0
071
in
Available
retaining
plate
Thickness
mm
in
10
6
0417
10
8
0425
11
0
0
433
11
2
0441
II
4
0
449
11
6
0457
AT151
Fig
AT
83
Measuring
ring
to
plate
clearance
4
Testing
front
clutch
With
front
clutch
assembled
on
oil
pump
cover
direct
a
jet
of
air
into
hole
in
clutch
drum
See
Figure
AT
84
AT
41
Fig
AT
B4
Testing
front
clutch
REAR
CLUTCH
Disassembly
AT153
1
Rear
clutch
drum
2
Front
clutch
piston
3
Snap
ring
4
Retaining
plate
5
Drive
plate
Fig
A
T
85
Sectional
view
of
rear
clu
tch
6
Driven
plate
7
Dished
plate
8
Spring
retainer
9
Coil
spring
I
Take
out
snap
ring
@
retaining
plate
@
drive
plate
@
driven
plate
@
and
dished
plate
f
Same
tech
nique
can
be
applied
as
in
disas
sembling
front
clutch
See
Figure
AT
85
2
Remove
snap
ring
from
coil
spring
retainer
See
Figure
AT
86
ST2532001
Xf
Fig
AT
86
Remolling
snap
ring
Page 306 of 537
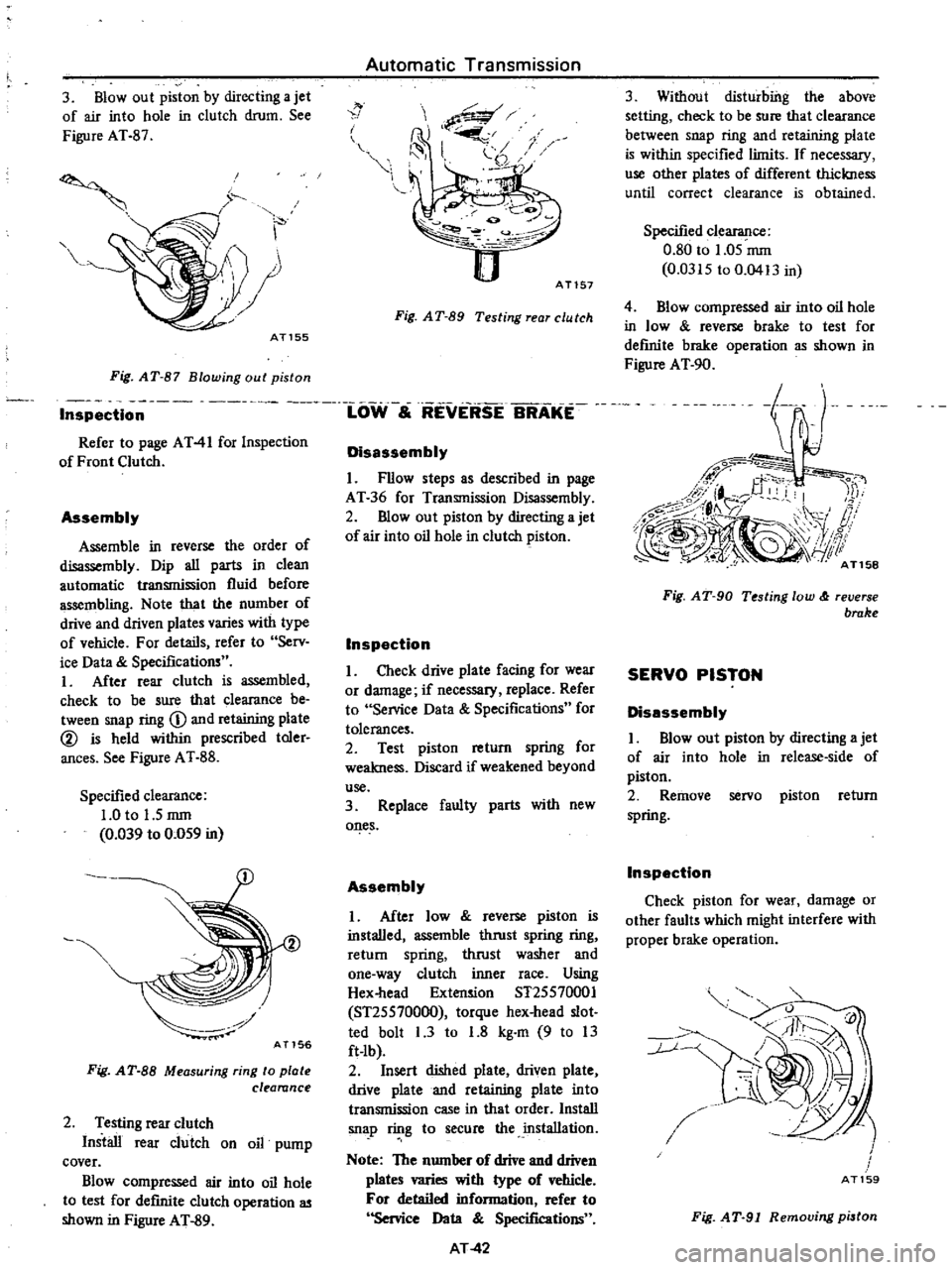
3
Blowout
piston
by
directing
a
jet
of
air
into
hole
in
clutch
drum
See
Figure
AT
87
AT155
V
i
J
i
j
Fig
AT
87
Blowing
out
piston
Automatic
Transmission
1
w
Ai
I
i
1
i
3
j
P2
0
AT157
Fig
A
T
89
Testing
rear
C
U
tch
Inspectl
ioW
S
REVERSE
BRAKE
Refer
to
page
AT41
for
Inspection
of
Front
Clutch
Assembly
Assemble
in
reverse
the
order
of
disassembly
Dip
all
parts
in
clean
automatic
transmission
fluid
before
assembling
Note
that
the
number
of
drive
and
driven
plates
varies
with
type
of
vehicle
F
or
details
refer
to
Serv
ice
Data
Specifications
I
After
rear
clutch
is
assembled
check
to
be
sure
that
clearance
be
tween
snap
ring
D
and
retaining
plate
l
is
held
within
prescribed
toler
ances
See
Figure
AT
88
Specified
clearance
1
0
to
1
5
rom
0
039
to
0
059
in
AT156
Fig
AT
SS
Measuring
ring
to
plate
clearance
2
Testing
rear
clutch
Install
rear
clutch
on
oil
pump
cover
Blow
compressed
air
into
oil
hole
to
test
for
defInite
clutch
operation
as
shown
in
Figure
AT
89
Disassembly
1
Fllow
steps
as
described
in
page
AT
36
for
Transmission
Disassembly
2
mow
out
piston
by
directing
a
jet
of
air
into
oil
hole
in
clutch
piston
Inspection
I
Check
drive
plate
facing
for
wear
or
damage
if
necessary
replace
Refer
to
Service
Data
Specifications
for
tolerances
2
Test
piston
return
spring
for
weakness
Discard
if
weakened
beyond
use
3
Replace
faulty
parts
with
new
ones
Assembly
I
After
low
reverse
piston
is
installed
assemble
thrust
spring
ring
retum
spring
thrust
washer
and
one
way
clutch
inner
race
Using
Hex
head
Extension
ST25570001
ST25570000
torque
hex
head
slot
ted
bolt
I
3
to
1
8
kg
m
9
to
13
ft
lb
2
Insert
dished
plate
driven
plate
drive
plate
and
retaining
plate
into
transmission
case
in
that
order
Install
sn
p
ring
to
secure
the
installation
Note
The
number
of
drive
and
driven
plates
wries
with
type
of
vehicle
For
detailed
information
refer
to
Service
Data
Specifications
AT42
3
Without
disturbiilg
the
above
setting
check
to
be
sure
that
clearance
between
snap
ring
and
retaining
plate
is
within
specified
limits
If
necessary
use
other
plates
of
different
thickness
until
correct
clearance
is
obtained
Specified
clearance
0
80
to
1
05
rom
0
0315
to
0
0413
in
4
Blow
compressed
air
into
oil
hole
in
low
reverse
brake
to
test
for
definite
brake
operation
as
shown
in
Figure
AT
90
Fig
AT
90
Testing
low
reverse
brake
SERVO
PISTON
Disassembly
I
Blowout
piston
by
directing
a
jet
of
air
into
hole
in
release
side
of
piston
2
Remove
servo
piston
return
spring
Inspection
Check
piston
for
wear
damage
or
other
faults
which
might
interfere
with
proper
brake
operation
v
r
0
111
Ll
7
J
I
AT159
Fig
AT
91
Removing
pi3ton
Page 308 of 537
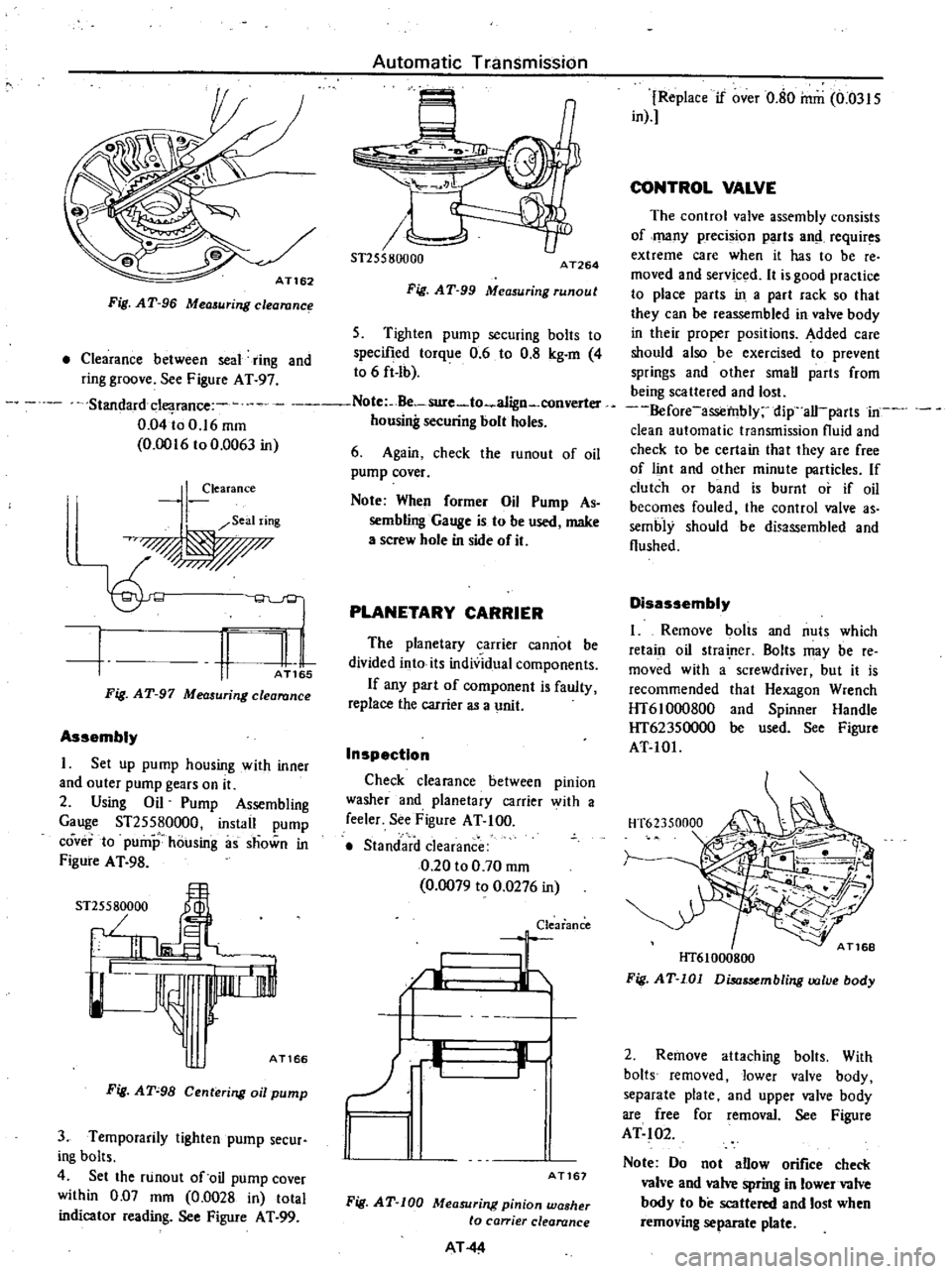
Fig
AT
96
Measuring
clearanc
Automatic
Transmission
6
u
ST255801JOO
AT264
Fig
AT
99
Measuring
runout
5
Tighten
pump
securing
bolts
to
specified
torque
0
6
to
0
8
kg
m
4
to
6
ft
Ib
Clearance
between
seal
ring
and
ring
groove
See
Figure
AT
97
Standarddearance
Note
Be
sure
to
a1ign
converter
0
04
io
0
16
mm
housing
securing
bolt
holes
0
0016
to
0
0063
in
6
Again
check
the
runout
of
oil
pump
cover
I
learance
Seal
ring
q
I
n
l
1
AT
5
Fig
AT
97
Measuring
clearance
Assembly
I
Set
up
pump
housing
with
inner
and
outer
pump
gears
on
it
2
Using
Oil
Pump
Assembling
Gauge
ST25580000
instail
pump
coverta
pump
housing
as
shown
in
Figure
A
T
98
ST
5
000
J
I
I
JL
AT166
Fig
AT
98
Centering
oil
pump
3
Temporarily
lighten
pump
secur
ing
bolts
4
Set
the
runout
of
oil
pump
cover
within
0
D7
mm
0
0028
in
total
indicator
reading
See
Figure
AT
99
Note
When
former
Oil
Pump
As
sembling
Gauge
is
to
be
used
make
a
screw
hole
in
side
of
it
PLANETARY
CARRIER
The
planetary
carrier
cannot
be
divided
into
its
individual
components
If
any
part
of
component
is
faulty
replace
the
carrier
as
a
unit
Inspection
Check
clearance
between
pinion
washer
and
planetary
carrier
with
a
feeler
See
Figure
AT
100
Standard
clearance
0
20
to
0
70
mm
0
0079
to
0
0276
in
Clearance
I
Jr
I
1
11
r
AT167
Fig
AT
100
Measuring
pinion
washer
to
ca
ier
clearance
AT
44
Replace
if
over
0
80
mm
0
0315
in
CONTROL
VALVE
The
control
valve
assembly
consists
of
many
preci
ion
parts
and
requir
s
extreme
care
when
it
has
to
be
reo
moved
and
serviced
It
is
good
practice
to
place
parts
in
a
part
rack
so
that
they
can
be
reassembled
in
valve
body
in
their
proper
positions
Added
care
should
also
be
exercised
to
prevent
springs
and
other
small
parts
from
being
scattered
and
lo
t
Before
assembly
dip
all
parts
in
clean
automatic
transmission
fluid
and
check
to
be
certain
that
they
are
free
of
lint
and
other
minute
particles
If
clutch
or
band
is
burnt
or
if
oil
becomes
fouled
the
control
valve
as
sembly
should
be
di
ssembled
and
flushed
Disassembly
I
Remove
bolts
and
nuts
which
retain
oil
trainer
Bolts
may
be
re
moved
with
a
screwdriver
but
it
is
recommended
that
Hexagon
Wrench
HT610oo800
and
Spinner
Handle
HT62350000
be
used
See
Figure
AT
101
HT61000800
Fig
AT
101
Disassembling
valve
body
2
Remove
attaching
bolts
With
bolts
removed
lower
valve
body
separate
plate
and
upper
valve
body
are
free
for
removal
See
Figure
AT
102
Note
Do
not
allow
orifice
check
vah
e
and
valve
spring
in
lower
valve
body
to
be
scattered
and
lost
when
removing
separate
plate
Page 323 of 537
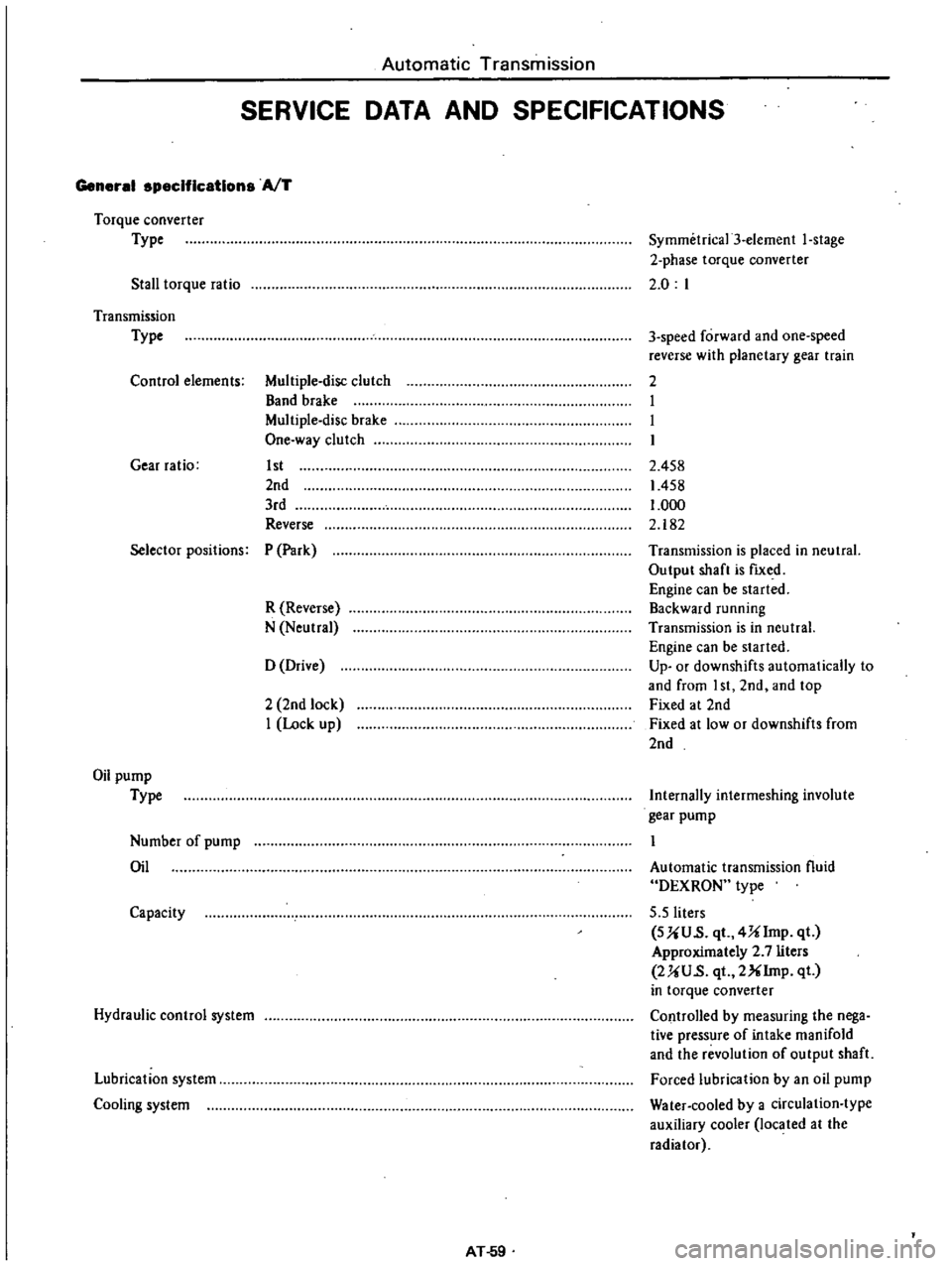
Automatic
Transmission
SERVICE
DATA
AND
SPECIFICATIONS
General
specifications
AfT
Torque
converter
Type
Stall
torque
ratio
Symmetrica13
element
I
stage
2
phase
torque
converter
2
0
I
Transmission
Type
Control
elements
Multiple
disc
clutch
Band
brake
Multiple
disc
brake
One
way
clutch
Gear
ratio
1st
2nd
3rd
Reverse
3
speed
forward
and
one
speed
reverse
with
planetary
gear
train
2
I
I
I
2
458
1458
1
000
2
182
Selector
positions
P
Park
R
Reverse
N
Neutral
Transmission
is
placed
in
neutral
Output
shaft
is
fIXed
Engine
can
be
started
Backward
running
Transmission
is
in
neutral
Engine
can
be
started
Up
or
downshifts
automatically
to
and
from
I
st
2nd
and
top
Fixed
at
2nd
Fixed
at
low
or
downshifts
from
2nd
o
Drive
2
2nd
lock
I
Lock
up
Oil
pump
Type
Internally
intermeshing
involute
gear
pump
Number
of
pump
Oil
Automatic
transmission
fluid
DEXRON
type
5
5
liters
SUU
s
qt
4Ulmp
qt
Approximately
2
7
liters
2UU
s
qt
2XIrnp
qt
in
torque
converter
Controlled
by
measuring
the
nega
tive
pressure
of
intake
manifold
and
the
revolution
of
output
shaft
Forced
lubrication
by
an
oil
pump
Water
cooled
by
a
circulation
type
auxiliary
cooler
located
at
the
radiator
Capacity
Hydraulic
control
system
Lubrication
system
Cooling
system
AT
59
Page 326 of 537
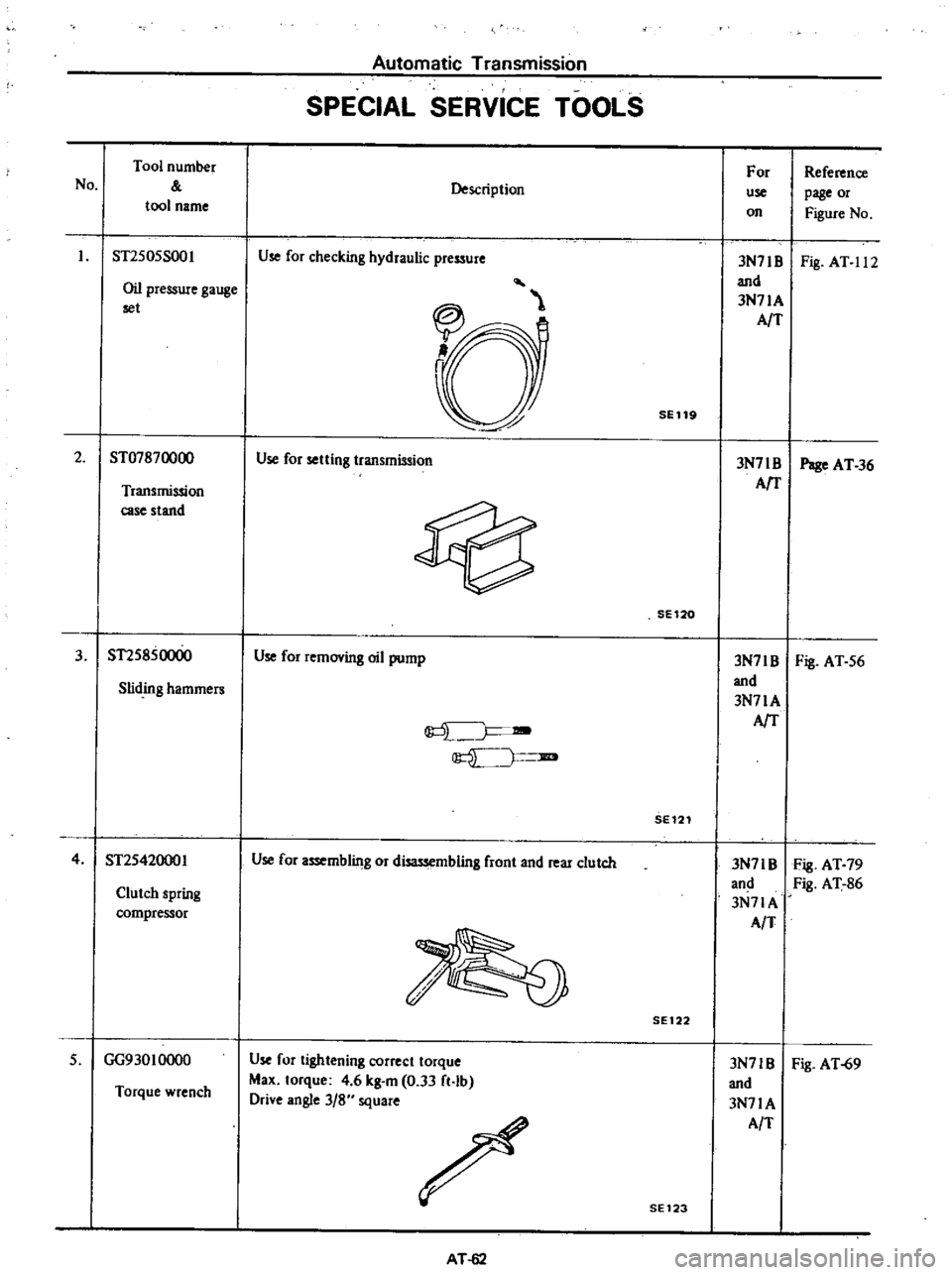
Automatic
Transmission
SPECIAL
SERVICE
TOOLS
No
Tool
number
tool
name
Description
For
use
on
Reference
page
or
Figure
No
Oil
pressure
gauge
set
3N71B
Fig
AT
11
2
and
3N71A
AfT
ST2S0SS001
Use
for
checking
hydraulic
pressure
SE119
2
ST07870000
Use
for
setting
transmission
3N71
B
Page
AT
36
AfT
Transmission
case
stand
SE120
3
ST2S850000
Use
for
removing
oil
pump
3N7IB
Fig
AT
S6
and
Sliding
hammers
3N71A
J
AfT
JIB
SE121
4
ST2S42000I
Use
for
assemblilJg
or
disassembling
front
and
rear
clutch
3N71B
Fig
AT
79
and
Fig
AT
86
Clutch
spring
3N7lA
compressor
AIT
SE
122
3N71B
Fig
AT
69
and
3N71A
AlT
Torque
wrench
Use
for
tightening
correct
torque
Max
torque
4
6
kg
m
0
33
ft
lb
Drive
angle
3
8
square
S
GG93010000
SE123
AT
62
Page 329 of 537
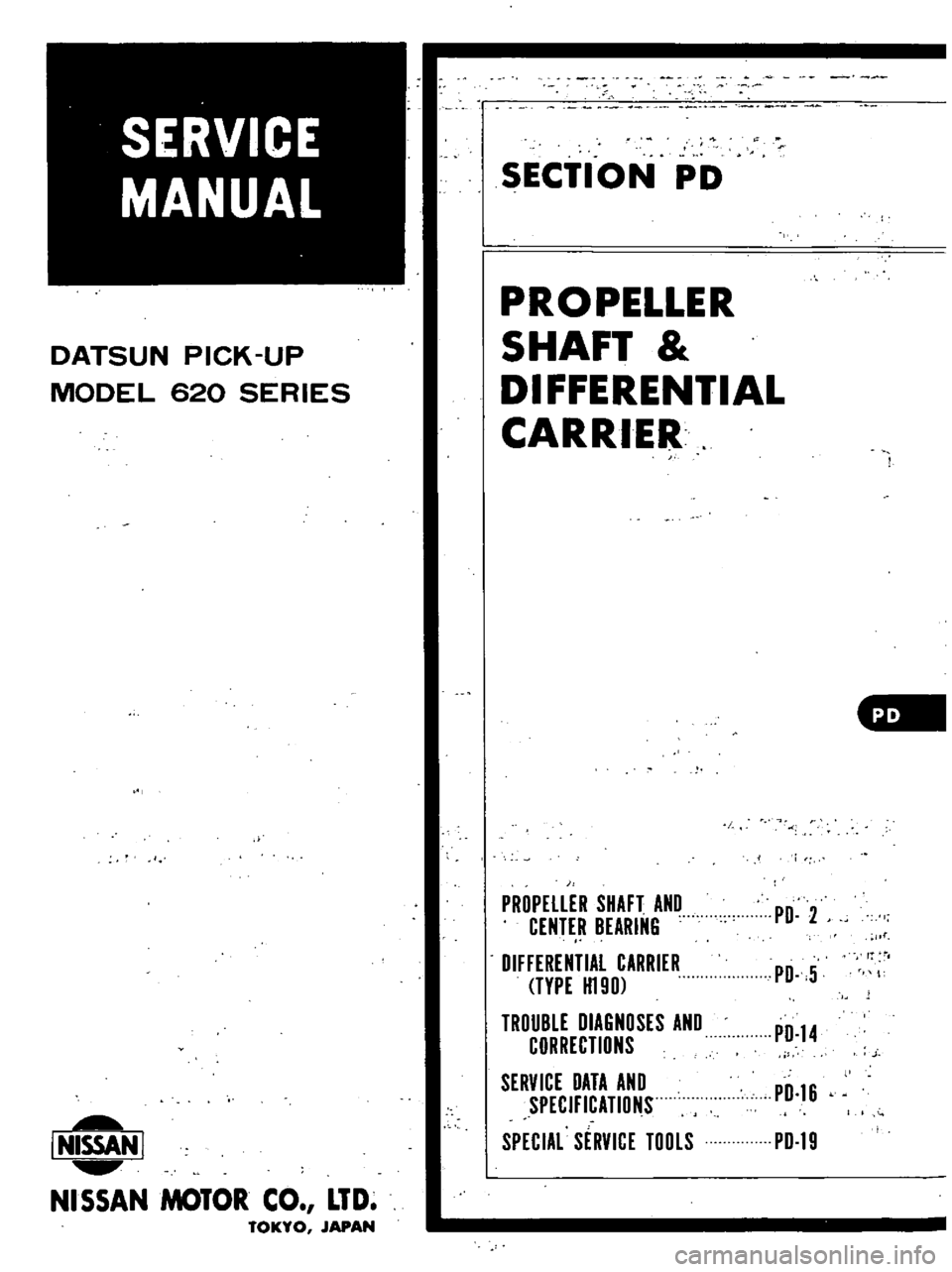
DATSUN
PICK
UP
MODEL
620
SERIES
I
NISSAN
I
NISSAN
MOTOR
CO
LTD
TOKYO
JAPAN
0
SECTION
PD
PROPELLER
SHAFT
DIFFERENTIAL
CARRIER
PROPELLER
SHAFT
AND
CENTER
BEARING
DIFFERENTIAL
CARRIER
TYPE
H19D
TROUBLE
DIAGNOSES
AND
CORRECTIONS
SERVICE
DATA
AND
I
SPECiFiCATIONS
PD
16
SPECIAL
SERVICE
TOOLS
PD
19
PD
2
f
PD
5
PD
14
Page 330 of 537
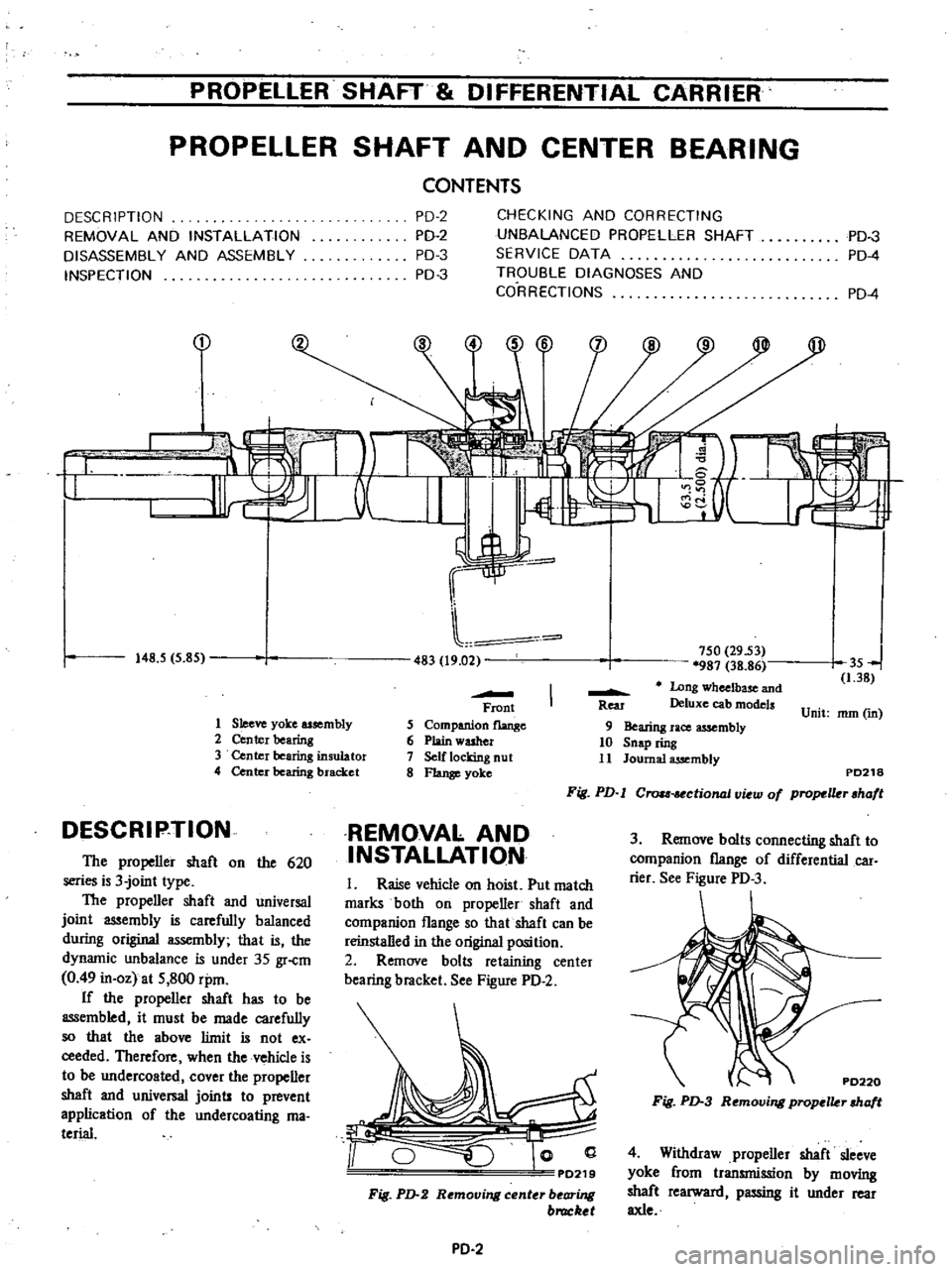
PROPElLER
SHAFT
DIFFERENTIAL
CARRIER
PROPELLER
SHAFT
AND
CENTER
BEARING
CONTENTS
DESCRIPTION
REMOVAL
AND
INSTALLATION
DISASSEMBLY
AND
ASSEMBLY
INSPECTION
i
t
I
tl
J
I
O
148
5
5
85
PD
2
PD
2
PD
3
PD
3
CHECKING
AND
CORRECTING
UNBALANCED
PROPELLER
SHAFT
SERVICE
DATA
TROUBLE
DIAGNOSES
AND
CORRECTIONS
PD
4
PD
3
PD
4
2
483
19
02
750
29
53
987
38
86
Long
wheelbase
and
Deluxe
cab
models
Unit
mm
in
35
1
38
Front
5
Companion
flange
6
Plain
washer
7
Self
locking
nut
8
Flange
yoke
Rea
1
Sleeve
yoke
assembly
2
Center
bearing
3
Center
bearing
insulator
4
Center
bearing
bracket
DESCRIP
TION
The
propeller
shaft
on
the
620
series
is
3
joint
type
The
propeller
shaft
and
universal
joint
assembly
is
carefully
balanced
during
original
assembly
that
is
the
dynamic
unbalance
is
under
35
gr
cm
0
49
in
oz
at
S
800
rpm
If
the
propeller
shaft
has
to
be
assembled
it
must
be
made
carefully
so
that
the
above
limit
is
not
ex
ceeded
Therefore
when
the
vehicle
is
to
be
undercoated
cover
the
propeller
shaft
and
universal
joints
to
prevent
application
of
the
undercoating
ma
terial
9
Bearing
race
assembly
10
Snap
ring
11
Journal
assembly
PD218
Fig
PD
l
Crou
ctional
v
w
of
propelkr
hafl
REMOVAL
AND
INSTALLATION
3
Remove
bolts
connecting
shaft
to
companion
flange
of
differential
car
rier
See
Figure
PD
3
I
Raise
vehicle
on
hoist
Put
match
marks
both
on
propeller
shaft
and
companion
flange
so
that
shaft
can
be
reinstalled
in
the
original
position
2
Remove
bolts
retaining
center
bearing
bracket
See
Figure
PD
2
PD220
Fig
PD
3
Removing
propclkr
cha
t
PD219
Fig
PD
2
Removing
center
bearing
bruckel
4
Withdraw
propeller
shaft
sleeve
yoke
from
transmission
by
moving
shaft
rearward
passing
it
under
rear
axle
PD
2
Page 332 of 537
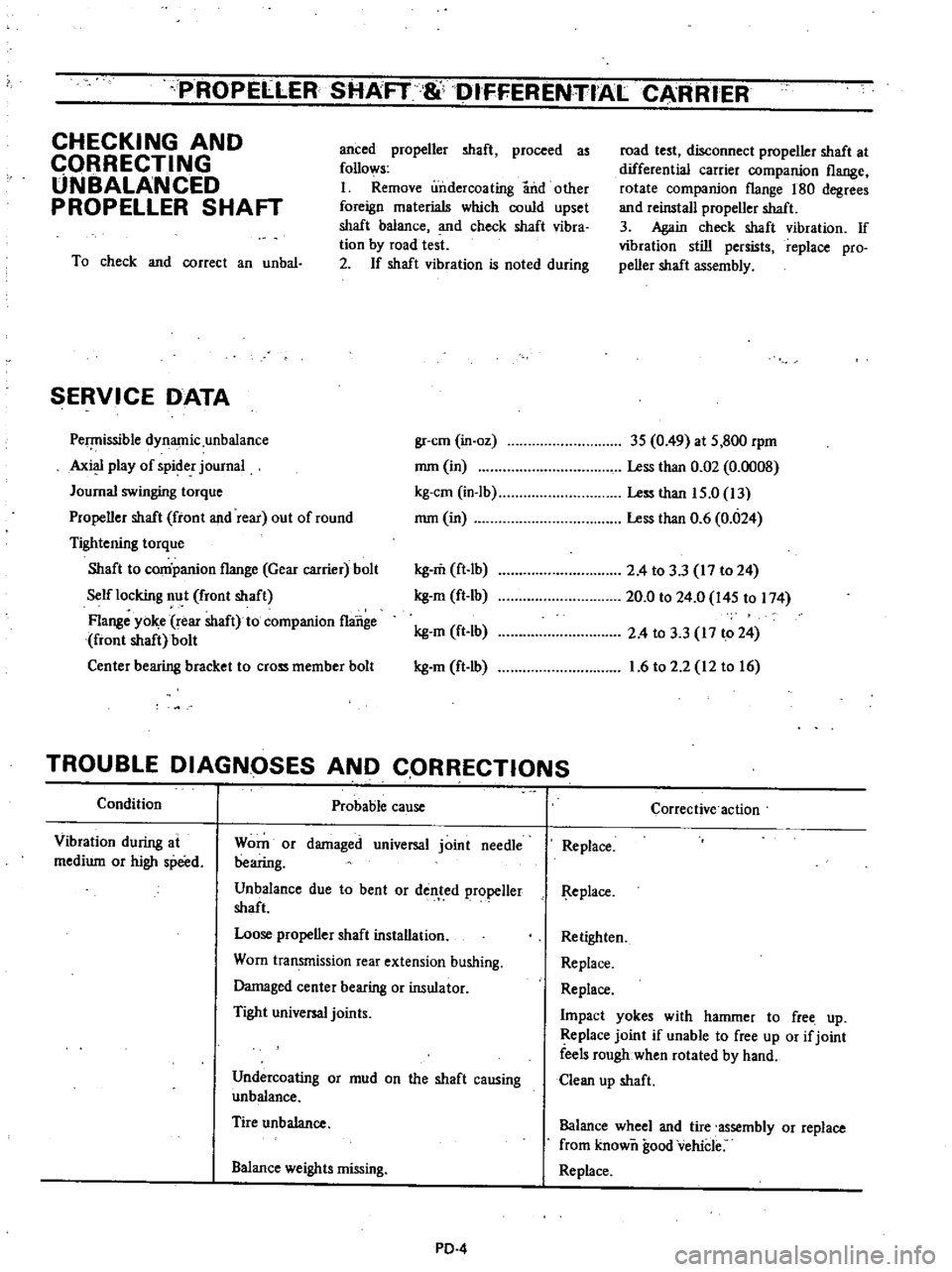
PROPELLER
SHAFT
8l
DIFFERENTIALCAAR
ER
CHECKING
AND
CQRRECTING
UNBALANCED
PROPELLER
SHAFT
anced
propeller
shaft
proceed
as
follows
I
Remove
undercoating
and
other
foreign
materials
which
could
upset
shaft
balance
and
check
shaft
vibra
tion
by
road
test
2
If
shaft
vibration
is
noted
during
To
check
and
correct
an
unbal
SERVICE
DATA
Pe
issible
dynamic
unbalance
Axi
play
of
spider
journal
Journal
swinging
torque
Propeller
shaft
front
and
rear
out
of
round
Tightening
torque
Shaft
to
conipanion
flange
Gear
carrier
bolt
Self
locking
nut
front
shaft
Flange
yo
e
rear
shaft
to
companion
flange
front
shaft
bolt
Center
bearing
bracket
to
cross
member
bolt
road
test
disconnect
propeller
shaft
at
differential
carrier
companion
flange
rotate
companion
flange
180
degrees
and
reinstall
propeller
shaft
3
Again
check
shaft
vibration
If
vibration
still
persists
replace
pro
peller
shaft
assembly
gr
cm
in
oz
3S
0
49
at
S
800
rpm
mm
in
Less
than
0
02
0
0008
kg
em
in
Ib
Less
than
IS
O
13
mm
in
Less
than
0
6
0
024
kg
m
ft
lb
kg
m
ft
Ib
kg
m
ft
lb
kg
m
ft
lb
2
4
to
3
3
17
to
24
20
0
to
24
0
l4S
to
174
2
4
to
3
3
17
to
24
1
6
to
2
2
12
to
16
TROUBLE
DIAGNOSES
AND
CQRRECTIONS
Condition
Probable
cause
Vibration
during
at
medium
or
high
speed
Worn
or
damaged
universal
joint
needle
bearing
Unbalance
due
to
bent
or
dented
propeller
shaft
Loose
propeller
shaft
installation
Worn
transmission
rear
extension
bushing
Damaged
center
bearing
or
insulator
Tight
universal
joints
Undercoating
or
mud
on
the
shaft
causing
unbalance
Tire
unbalance
Balance
weights
missing
PD
4
Corrective
action
Replace
I
l
eplace
Retighten
Replace
Replace
Impact
yokes
with
hammer
to
free
up
Replace
joint
if
unable
to
free
up
or
if
joint
feels
rough
when
rotated
by
hand
Clean
up
shaft
Balance
wheel
and
tire
assembly
or
replace
from
known
good
vehicle
Replace