engine JAGUAR XJ6 1994 2.G Repair Manual
[x] Cancel search | Manufacturer: JAGUAR, Model Year: 1994, Model line: XJ6, Model: JAGUAR XJ6 1994 2.GPages: 521, PDF Size: 17.35 MB
Page 78 of 521
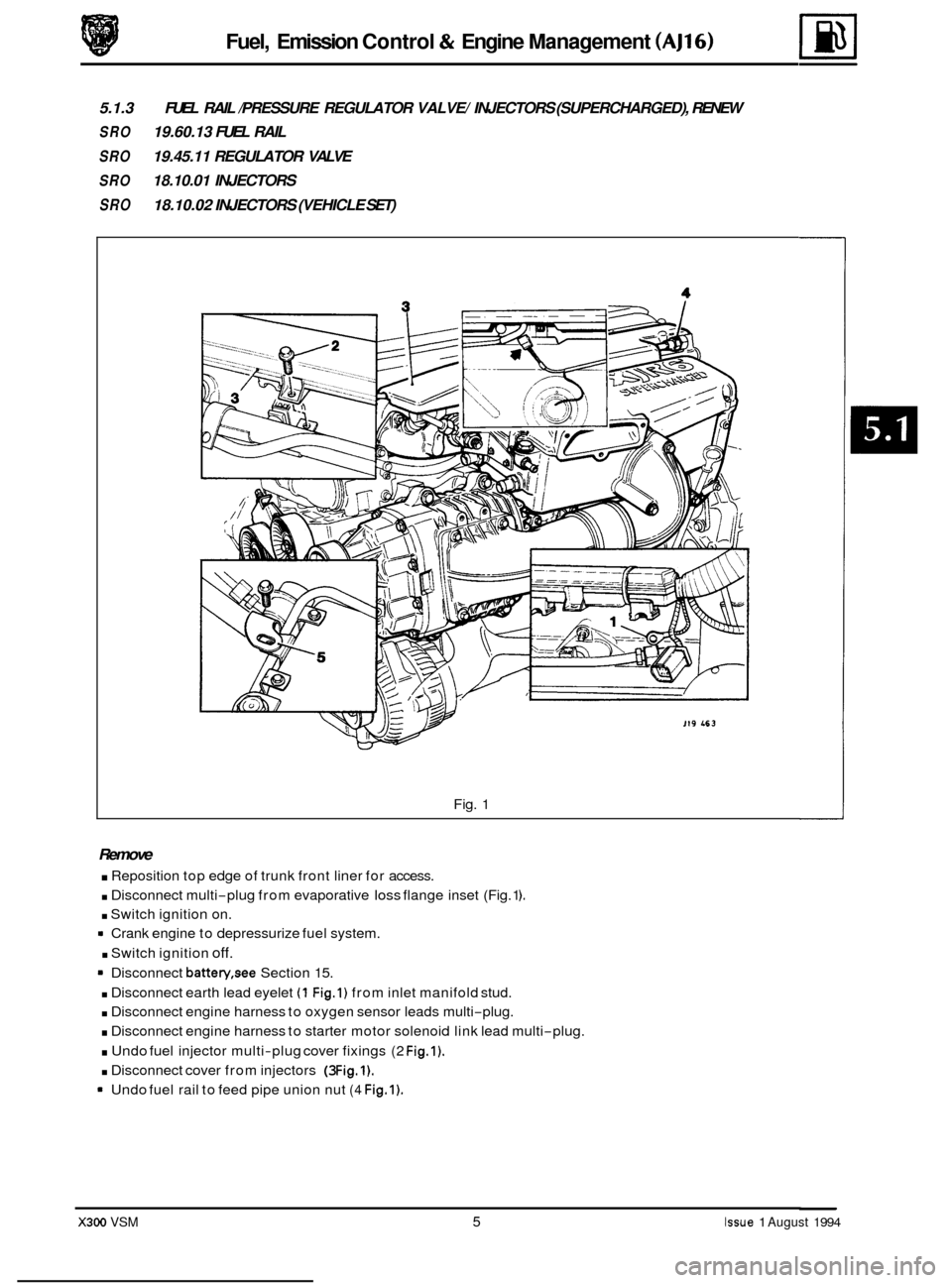
Fuel, Emission Control & Engine Management (AJ16)
5.1.3
SRO 19.60.13 FUEL RAIL
SRO 19.45.11 REGULATOR VALVE
SRO 18.10.01 INJECTORS
SRO 18.10.02 INJECTORS (VEHICLE SET)
FUEL
RAIL /PRESSURE REGULATOR VALVE/ INJECTORS (SUPERCHARGED), RENEW
Fig. 1
Remove
. Reposition top edge of trunk front liner for access.
. Disconnect multi-plug from evaporative loss flange inset (Fig. 1 ).
. Switch ignition on.
. Switch ignition off.
. Disconnect earth lead eyelet (1 Fig.1) from inlet manifold stud.
. Disconnect engine harness to oxygen sensor leads multi-plug.
. Disconnect engine harness to starter motor solenoid link lead multi-plug.
. Undo fuel injector multi-plug cover fixings (2 Fig.1).
. Disconnect cover from injectors (3 Fig.1).
Crank engine to depressurize fuel system.
Disconnect
battery,see Section 15.
Undo fuel rail to feed pipe union nut
(4 Fig.1).
X300 VSM 5 Issue 1 August 1994
Page 79 of 521
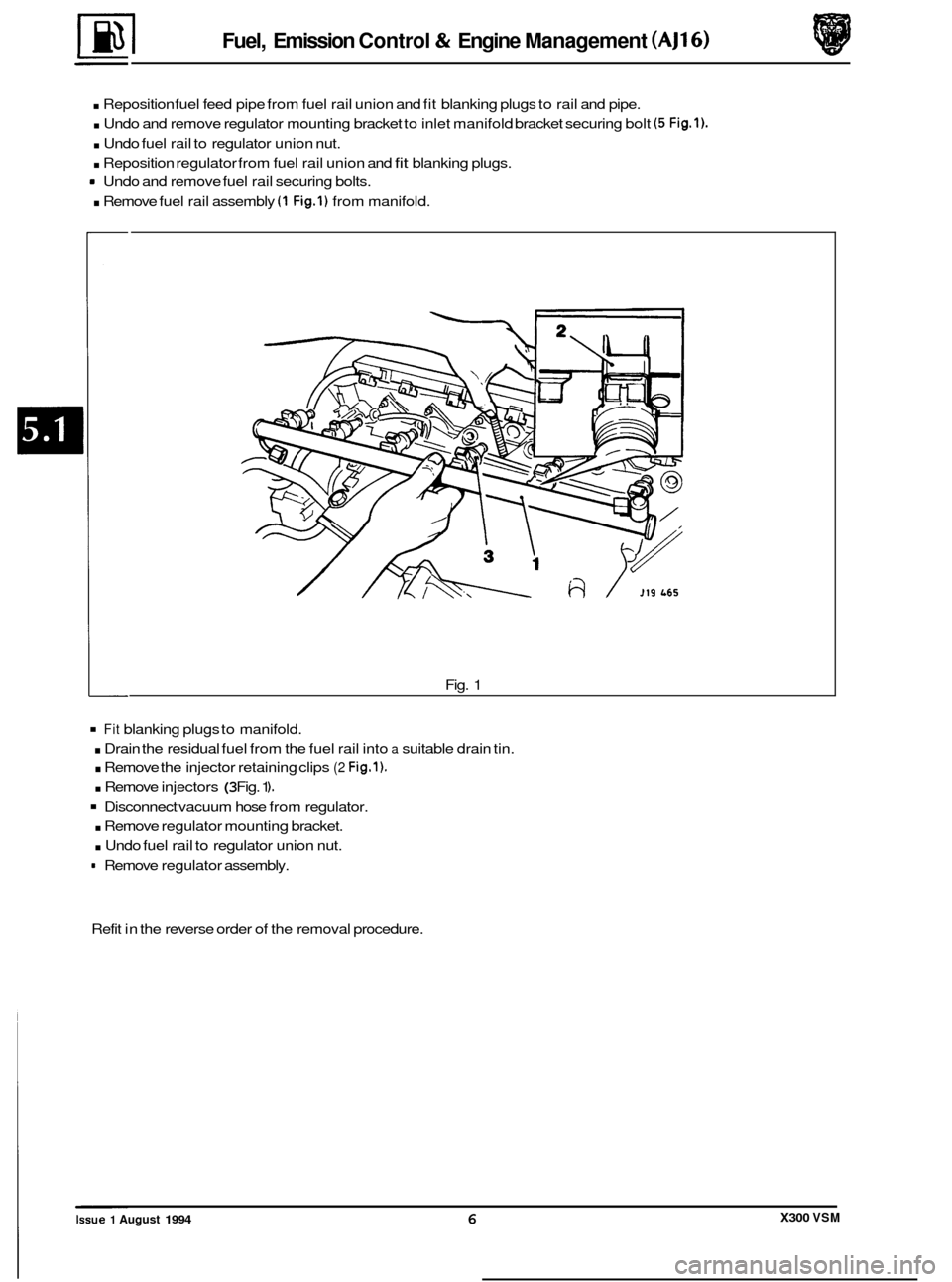
Fuel, Emission Control & Engine Management (AJ16)
. Reposition fuel feed pipe from fuel rail union and fit blanking plugs to rail and pipe.
. Undo and remove regulator mounting bracket to inlet manifold bracket securing bolt (5 Fig.1).
. Undo fuel rail to regulator union nut.
. Reposition regulator from fuel rail union and fit blanking plugs.
. Remove fuel rail assembly (1 Fig.1) from manifold.
Undo
and remove fuel rail securing bolts.
Fig. 1
Fit blanking plugs to manifold.
. Drain the residual fuel from the fuel rail into a suitable drain tin.
. Remove the injector retaining clips (2 Fig.1).
. Remove injectors (3 Fig. 1 ).
Disconnect vacuum hose from regulator.
. Remove regulator mounting bracket.
. Undo fuel rail to regulator union nut.
= Remove regulator assembly.
Refit in the reverse order of the removal procedure.
X300 VSM Issue 1 August 1994 6
Page 80 of 521
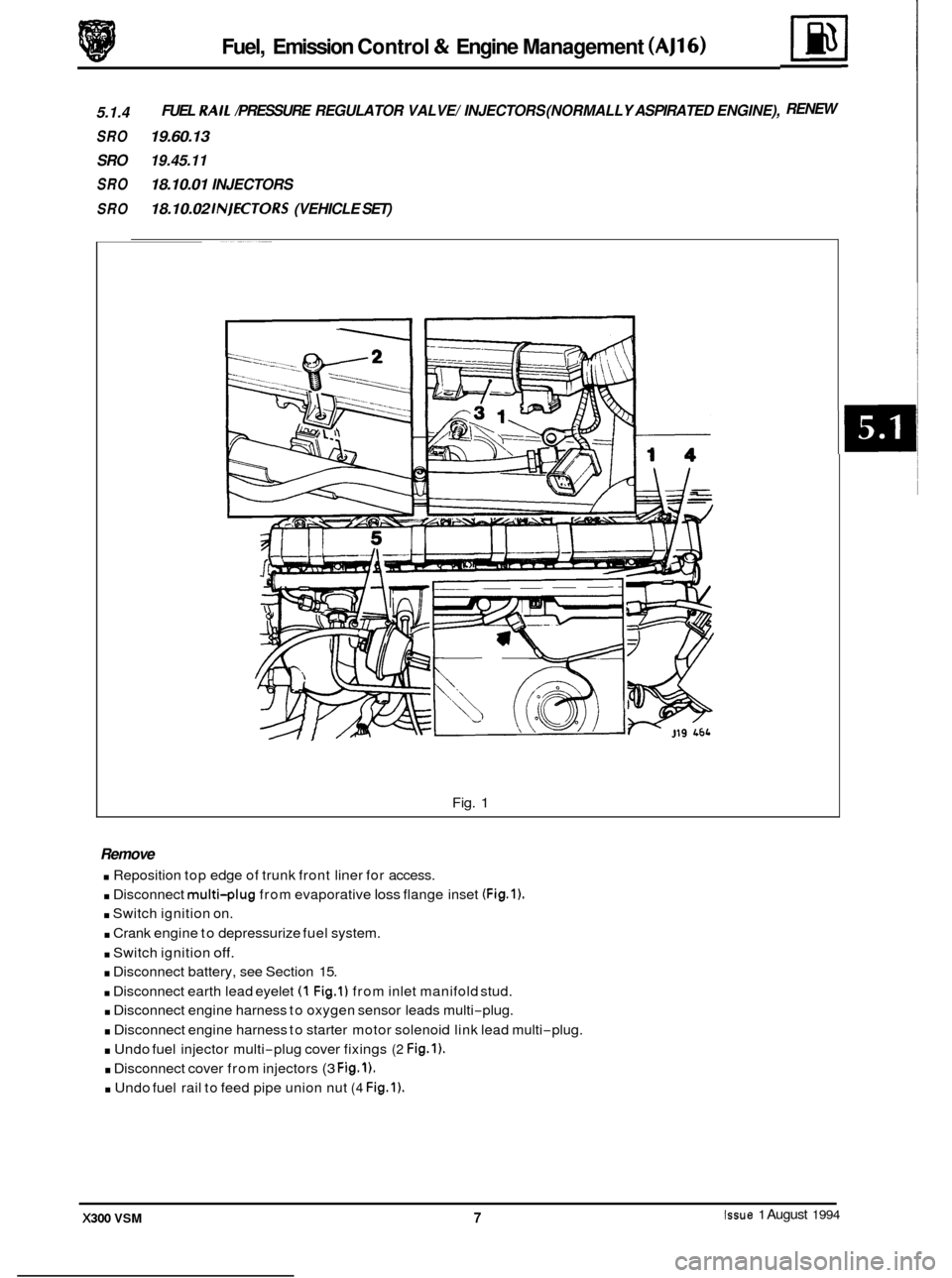
Fuel, Emission Control & Engine Management (AJ16)
5.1.4
SRO 19.60.13
FUEL RAIL /PRESSURE REGULATOR VALVE/ INJECTORS (NORMALLY ASPIRATED ENGINE),
SRO 19.45.11
SRO 18.10.01 INJECTORS
SRO 18.10.02 INIECTORS (VEHICLE SET)
IB
RENEW
Fig. 1
Remove
. Reposition top edge of trunk front liner for access.
. Disconnect multi-plug from evaporative loss flange inset (Fig.1).
. Switch ignition on.
. Crank engine to depressurize fuel system.
. Switch ignition off.
. Disconnect battery, see Section 15.
. Disconnect earth lead eyelet (1 Fig.1) from inlet manifold stud.
. Disconnect engine harness to oxygen sensor leads multi-plug.
. Disconnect engine harness to starter motor solenoid link lead multi-plug.
. Undo fuel injector multi-plug cover fixings (2 Fig.1).
. Disconnect cover from injectors (3 Fig.1).
. Undo fuel rail to feed pipe union nut (4 Fig.1).
Issue 1 August 1994 X300 VSM 7
Page 81 of 521
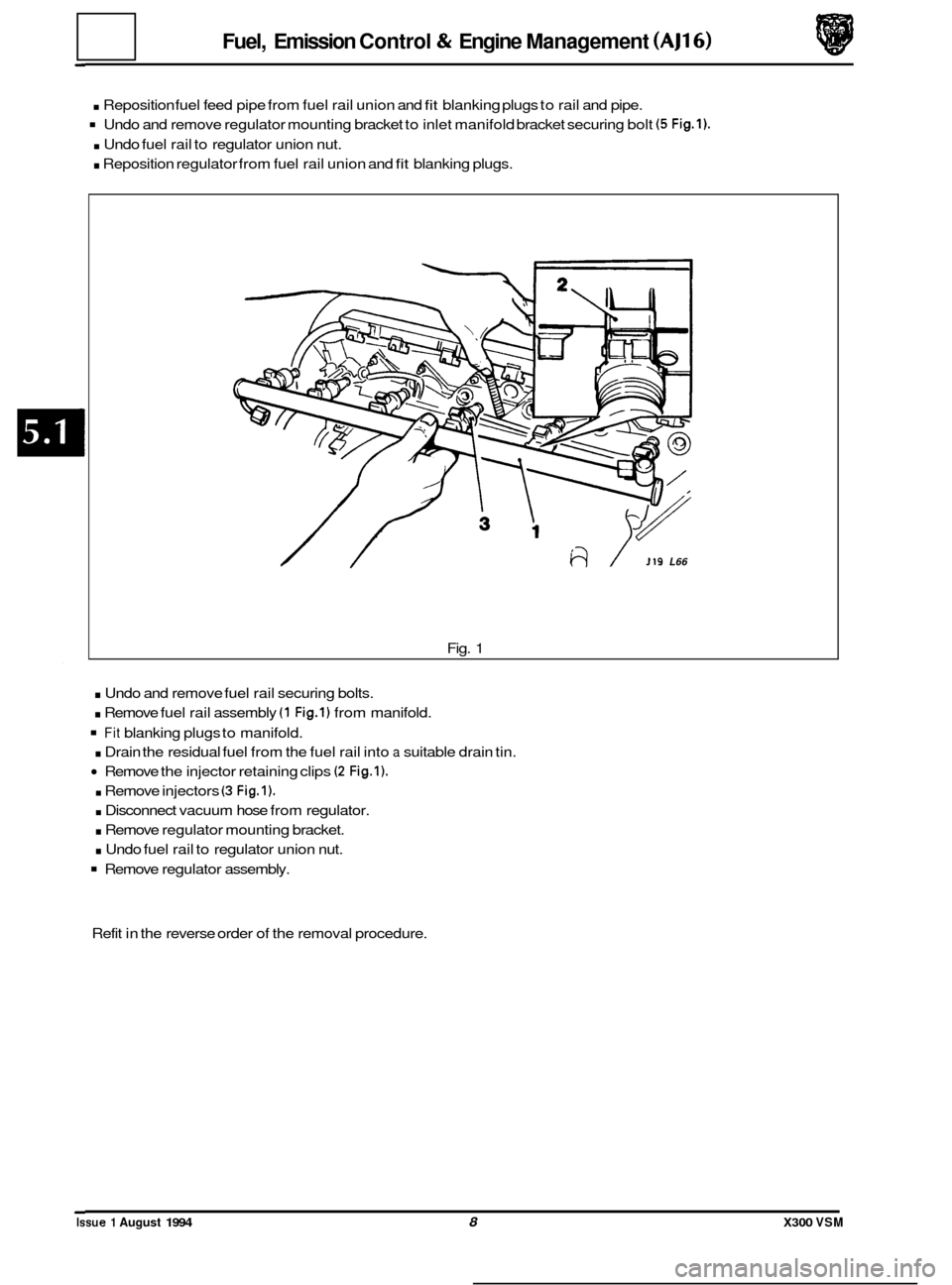
Fuel, Emission Control & Engine Management (AJ16)
. Reposition fuel feed pipe from fuel rail union and fit blanking plugs to rail and pipe.
Undo and remove regulator mounting bracket to inlet manifold bracket securing bolt (5 Fig.1).
. Undo fuel rail to regulator union nut.
. Reposition regulator from fuel rail union and fit blanking plugs.
/ 119 L66
Fig. 1
. Undo and remove fuel rail securing bolts.
. Remove fuel rail assembly (1 Fig.1) from manifold.
Fit blanking plugs to manifold.
. Drain the residual fuel from the fuel rail into a suitable drain tin.
Remove the injector retaining clips (2 Fig.1).
. Remove injectors (3 Fig.1).
. Disconnect vacuum hose from regulator.
. Remove regulator mounting bracket.
. Undo fuel rail to regulator union nut.
Remove regulator assembly.
Refit in the reverse order of the removal procedure.
0
0
0
0
Issue 1 August 1994 8 X300 VSM
Page 83 of 521
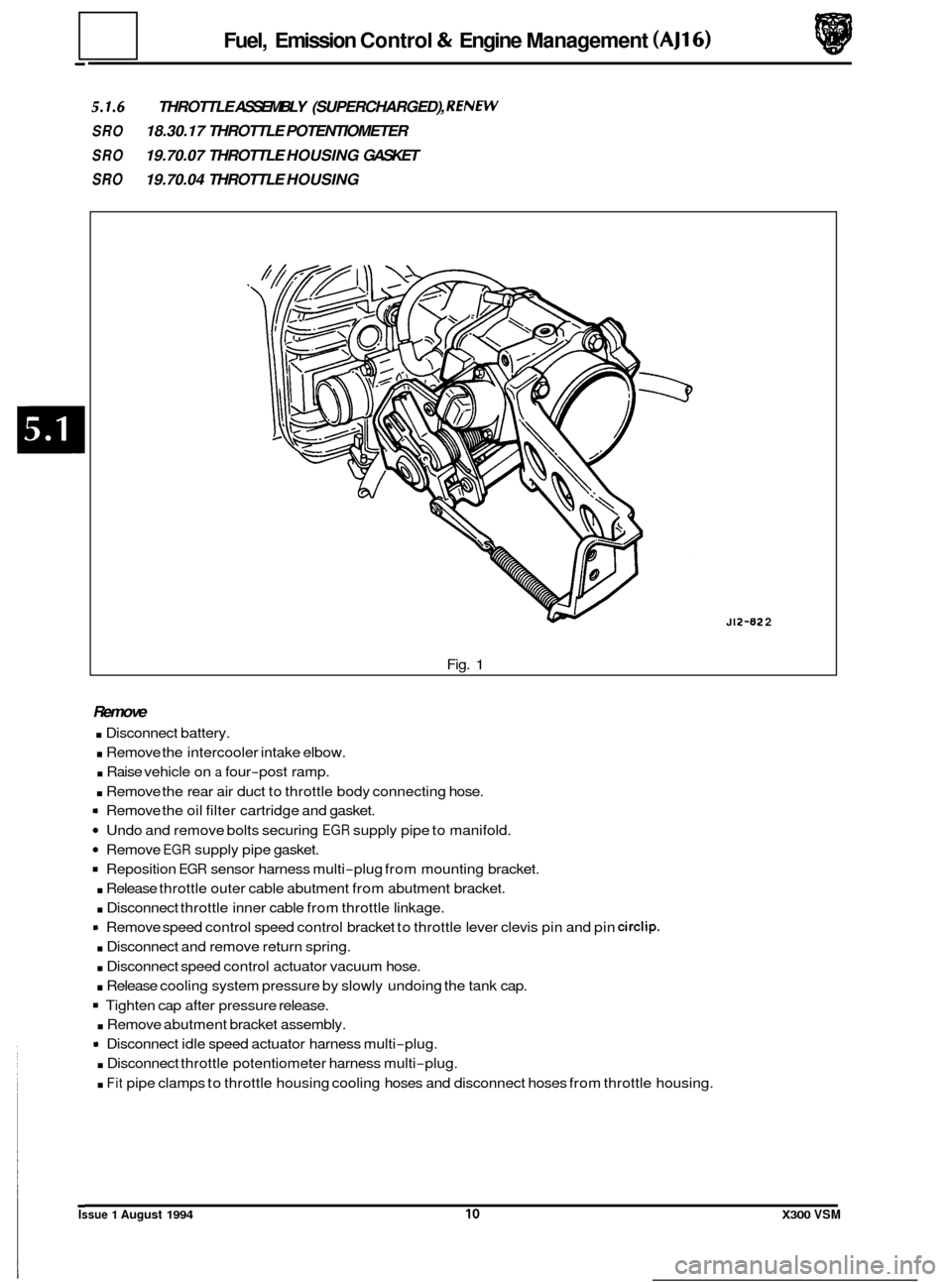
Fuel, Emission Control & Engine Management (AJ16)
5.1.6 THROTTLE ASSEMBLY (SUPERCHARGED), RENEW
SRO 18.30.17 THROTTLE POTENTIOMETER
SRO 19.70.07 THROTTLE HOUSING GASKET
SRO 19.70.04 THROTTLE HOUSING
J 12-62 2
Fig. 1
Remove
. Disconnect battery.
. Remove the intercooler intake elbow.
. Raise vehicle on a four-post ramp.
. Remove the rear air duct to throttle body connecting hose.
Undo and remove bolts securing EGR supply pipe to manifold.
Remove EGR supply pipe gasket.
Reposition EGR sensor harness multi-plug from mounting bracket.
. Release throttle outer cable abutment from abutment bracket.
. Disconnect throttle inner cable from throttle linkage.
. Disconnect and remove return spring.
. Disconnect speed control actuator vacuum hose.
. Release cooling system pressure by slowly undoing the tank cap.
Tighten cap after pressure release.
. Remove abutment bracket assembly.
Disconnect idle speed actuator harness multi
-plug.
. Disconnect throttle potentiometer harness multi-plug.
. Fit pipe clamps to throttle housing cooling hoses and disconnect hoses from throttle housing.
Remove
the oil filter cartridge and gasket.
Remove speed control speed control bracket to throttle lever clevis pin and pin
circlip.
e
0
0
0
Issue 1 August 1994 10 X300 VSM
Page 85 of 521
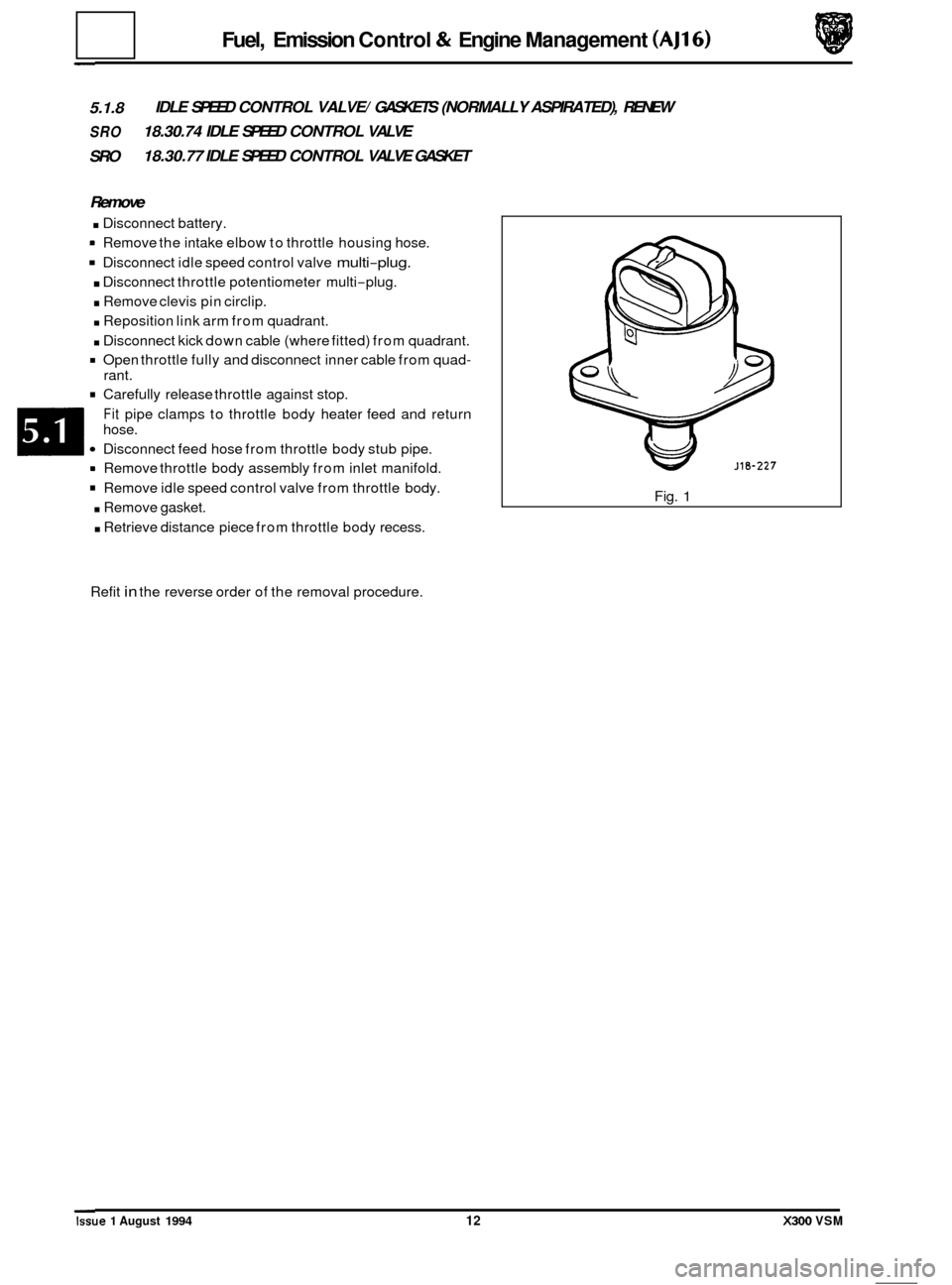
Fuel, Emission Control & Engine Management (AJ16)
5.1.8
SRO
SRO IDLE
SPEED CONTROL VALVE/ GASKETS (NORMALLY ASPIRATED), RENEW
18.30.74 IDLE SPEED CONTROL VALVE
18.30.77 IDLE SPEED CONTROL VALVE GASKET
Remove
. Disconnect battery.
9 Remove the intake elbow to throttle housing hose.
Disconnect idle speed control valve multi-plug.
. Disconnect throttle potentiometer multi-plug.
. Remove clevis pin circlip.
. Reposition link arm from quadrant.
. Disconnect kick down cable (where fitted) from quadrant.
Open throttle fully and disconnect inner cable from quad-
Carefully release throttle against stop.
rant.
Fit pipe clamps
to throttle body heater feed and return
hose.
Disconnect feed hose from throttle body stub pipe.
rn Remove throttle body assembly from inlet manifold.
Remove idle speed control valve from throttle body.
. Remove gasket.
. Retrieve distance piece from throttle body recess. Fig.
1
Refit in the
reverse order of the removal procedure.
0
0
0
0
Issue 1 August 1994 12 X300 VSM
Page 92 of 521
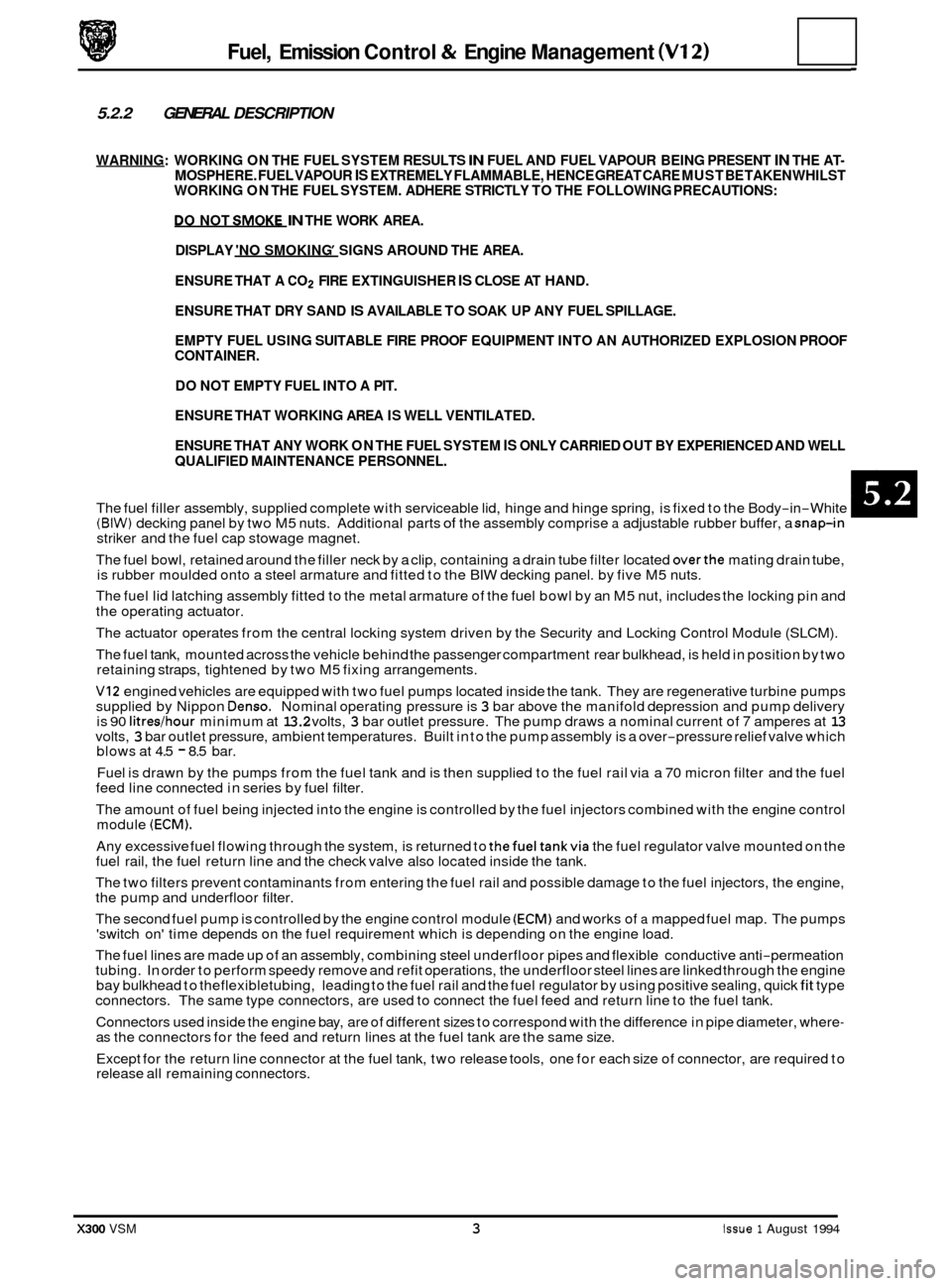
striker and the fuel cap stowage magnet.
The fuel bowl, retained around the filler neck by a clip, containing a drain tube filter located
overthe mating drain tube,
is rubber moulded onto a steel armature and fitted to the BIW decking panel. by five M5 nuts.
The fuel lid latching assembly fitted to the metal armature of the fuel bowl by an M5 nut, includes the locking pin and
the operating actuator.
The actuator operates from the central locking system driven by the Security and Locking Control Module (SLCM).
The fuel tank, mounted across the vehicle behind the passenger compartment rear bulkhead, is held in position by two
retaining straps, tightened by two M5 fixing arrangements.
VI2 engined vehicles are equipped with two fuel pumps located inside the tank. They are regenerative turbine pumps
supplied by Nippon Denso. Nominal operating pressure is 3 bar above the manifold depression and pump delivery
is 90 litres/hour minimum at 13.2 volts, 3 bar outlet pressure. The pump draws a nominal current of 7 amperes at 13 volts, 3 bar outlet pressure, ambient temperatures. Built in to the pump assembly is a over-pressure relief valve which
blows at 4.5 - 8.5 bar.
Fuel is drawn by the pumps from the fuel tank and is then supplied to the fuel rail via a
70 micron filter and the fuel
feed line connected in series by fuel filter.
The amount of fuel being injected into the engine is controlled by the fuel injectors combined with the engine control
module (ECM).
Any excessive fuel flowing through the system, is returned to thefuel tankvia the fuel regulator valve mounted on the
fuel rail, the fuel return line and the check valve also located inside the tank.
The two filters prevent contaminants from entering the fuel rail and possible damage to the fuel injectors, the engine,
the pump and underfloor filter.
The second fuel pump is controlled by the engine control module
(ECM) and works of a mapped fuel map. The pumps
'switch on' time depends on the fuel requirement which is depending on the engine load.
The fuel lines are made up of an assembly, combining steel underfloor pipes and flexible conductive anti
-permeation
tubing. In order to perform speedy remove and refit operations, the underfloor steel lines are linked through the engine
bay bulkhead to theflexibletubing, leading to the fuel rail and the fuel regulator by using positive sealing, quick
fit type
connectors. The same type connectors, are used to connect the fuel feed and return line to the fuel tank.
Connectors used inside the engine bay, are of different sizes to correspond with the difference in pipe diameter, where
- as the connectors for the feed and return lines at the fuel tank are the same size.
Except for the return line connector at the fuel tank, two release tools, one for each size of connector, are required to
release all remaining connectors.
Fuel, Emission Control & Engine Management (V12)
5.2.2 GENERAL DESCRIPTION
WARNING: WORKING ON THE FUEL SYSTEM RESULTS IN FUEL AND FUEL VAPOUR BEING PRESENT IN THE AT- MOSPHERE. FUEL VAPOUR IS EXTREMELY FLAMMABLE, HENCE GREAT CARE MUST BE TAKEN WHILST
WORKING ON THE FUEL SYSTEM. ADHERE STRICTLY TO THE FOLLOWING PRECAUTIONS:
PO NOT SMOKF, IN THE WORK AREA.
DISPLAY 'NO SMOKING
' SIGNS AROUND THE AREA.
ENSURE THAT A
CO2 FIRE EXTINGUISHER IS CLOSE AT HAND.
ENSURE THAT DRY SAND
IS AVAILABLE TO SOAK UP ANY FUEL SPILLAGE.
EMPTY FUEL USING SUITABLE FIRE PROOF EQUIPMENT INTO AN AUTHORIZED EXPLOSION PROOF
CONTAINER.
DO NOT EMPTY FUEL INTO A PIT.
ENSURE THAT WORKING AREA IS WELL VENTILATED.
ENSURE THAT ANY WORK ON THE FUEL SYSTEM
IS ONLY CARRIED OUT BY EXPERIENCED AND WELL
QUALIFIED MAINTENANCE PERSONNEL.
The fuel filler assembly, supplied complete with serviceable lid, hinge and hinge spring, is fixed to the Body-in-White (BIW) decking panel by two M5 nuts. Additional parts of the assembly comprise a adjustable rubber buffer, a snap-in
X300 VSM 3 Issue 1 August 1994
Page 93 of 521
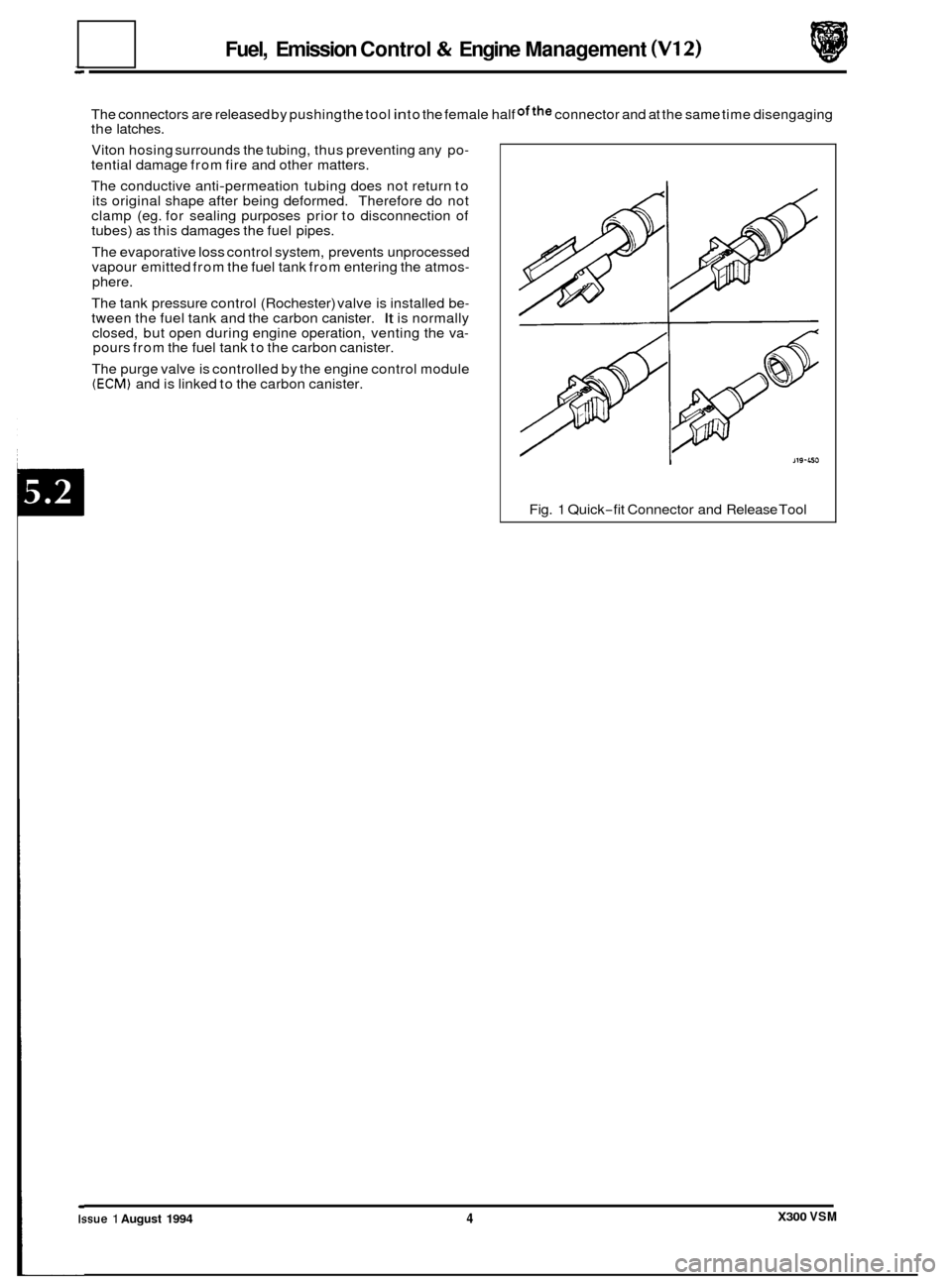
Fuel, Emission Control 8t Engine Management (V12)
The connectors are released by pushing the tool in to the female half ofthe connector and at the same time disengaging
the latches.
Viton hosing surrounds the tubing, thus preventing any po
- tential damage from fire and other matters.
The conductive anti
-permeation tubing does not return to
its original shape after being deformed. Therefore do not
clamp (eg. for sealing purposes prior to disconnection of
tubes) as this damages the fuel pipes.
The evaporative
loss control system, prevents unprocessed
vapour emitted from the fuel tank from entering the atmos- phere.
The tank pressure control (Rochester) valve is installed be
- tween the fuel tank and the carbon canister. lt is normally
closed, but open during engine operation, venting the va- pours from the fuel tank to the carbon canister.
The purge valve is controlled by the engine control module
(ECM) and is linked to the carbon canister.
Fig.
1 Quick-fit Connector and Release Tool
X300 VSM Issue 1 August 1994 4
Page 95 of 521
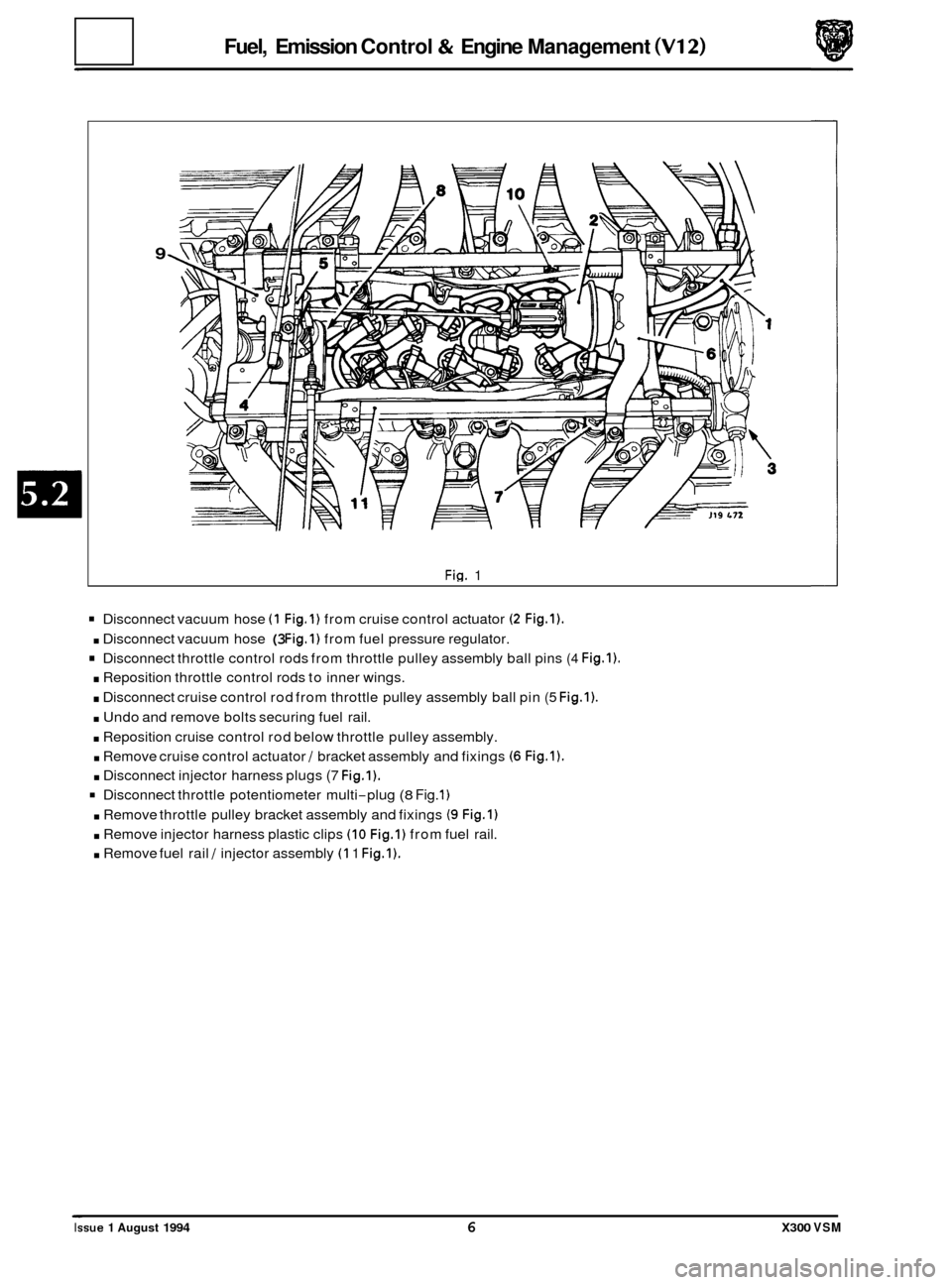
Fuel, Emission Control & Engine Management (V12)
9
Fig. 1
Disconnect vacuum hose (1 Fig.1) from cruise control actuator (2 Fig.1).
. Disconnect vacuum hose (3 Fig.1) from fuel pressure regulator.
Disconnect throttle control rods from throttle pulley assembly ball pins (4 Fig.1).
. Reposition throttle control rods to inner wings.
. Disconnect cruise control rod from throttle pulley assembly ball pin (5 Fig.1).
. Undo and remove bolts securing fuel rail.
. Reposition cruise control rod below throttle pulley assembly.
. Remove cruise control actuator / bracket assembly and fixings (6 Fig.1).
. Disconnect injector harness plugs (7 Fig.1).
Disconnect throttle potentiometer multi-plug (8 Fig. 1)
. Remove throttle pulley bracket assembly and fixings (9 Fig.1)
. Remove injector harness plastic clips (IO Fig.1) from fuel rail.
. Remove fuel rail / injector assembly (1 1 Fig.1).
Issue 1 August 1994 6 X300 VSM
Page 96 of 521
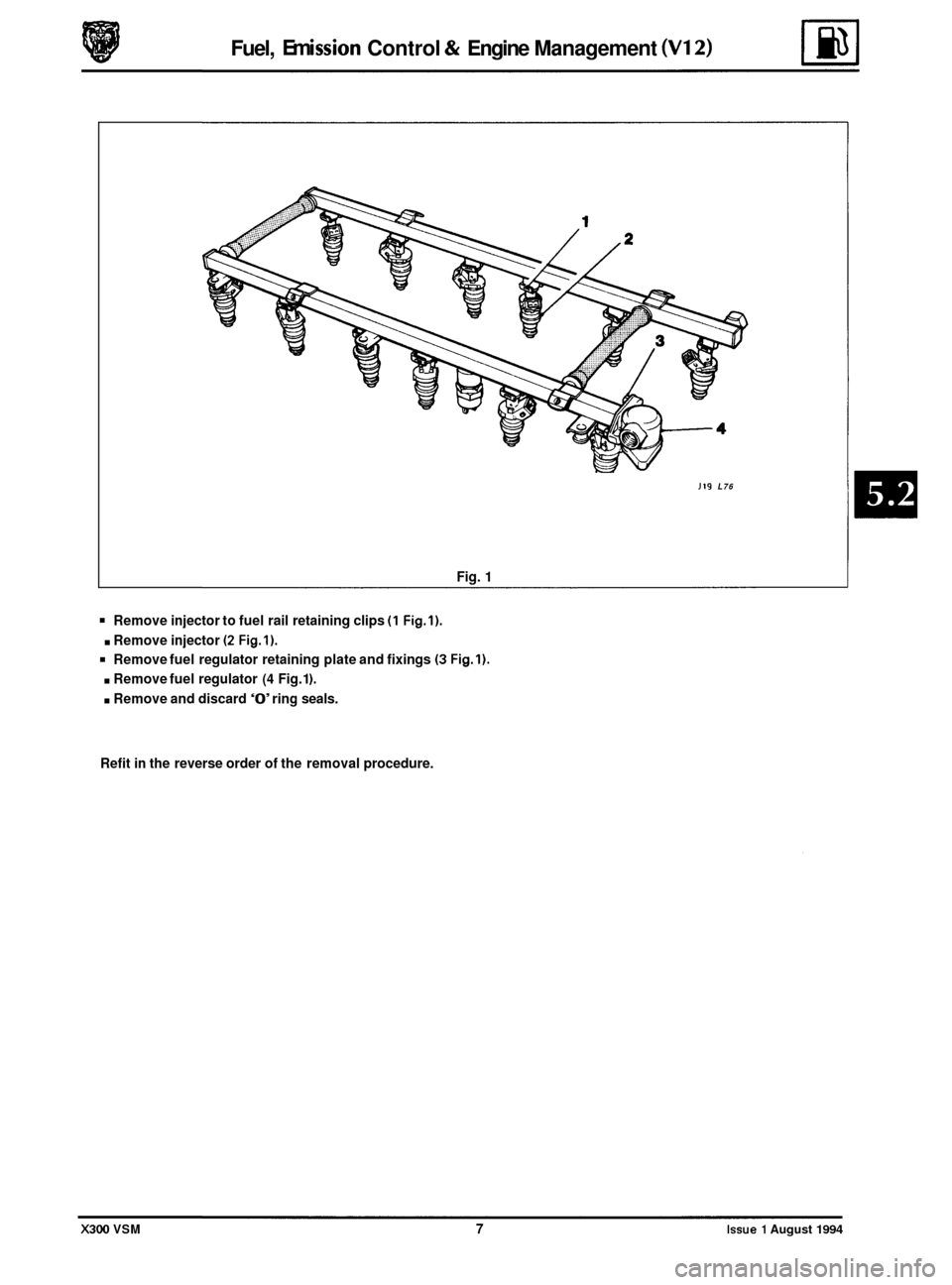
Fuel, Em i ssion Control & Engine
Management
J19 L76
Fig. 1
Remove injector to fuel rail retaining clips (1 Fig.1).
. Remove injector (2 Fig.1).
Remove fuel regulator retaining plate and fixings (3 Fig.1).
. Remove fuel regulator (4 Fig. 1 ).
. Remove and discard ‘0’ ring seals.
Refit in the reverse order of the removal procedure.
X300 VSM 7 Issue 1 August 1994