MAZDA 626 1987 Workshop Manual
Manufacturer: MAZDA, Model Year: 1987, Model line: 626, Model: MAZDA 626 1987Pages: 1865, PDF Size: 94.35 MB
Page 511 of 1865
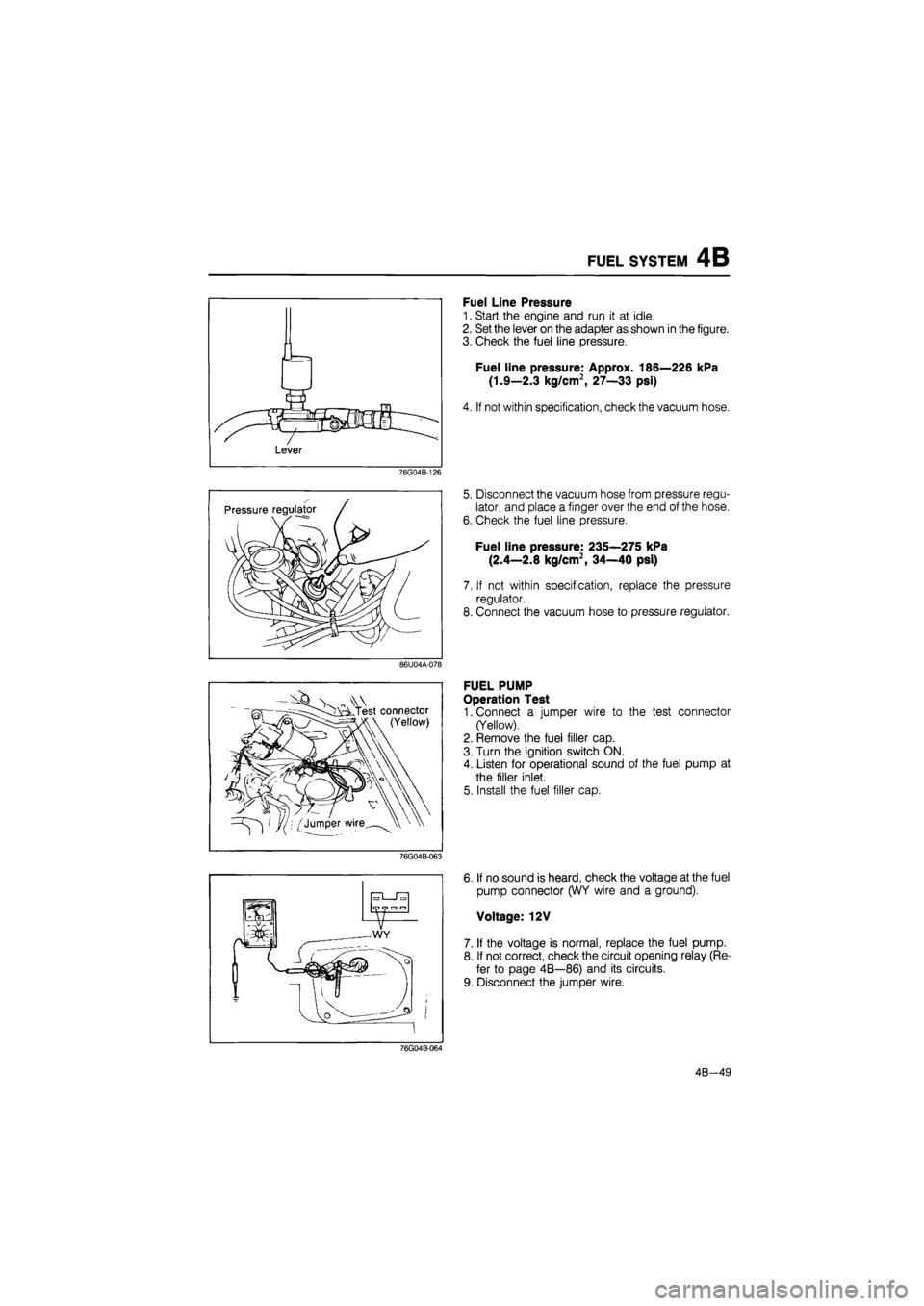
FUEL SYSTEM 4B
76G04B-126
86U04A-078
V^AN.
- Test connector
(Yellow)
76G04B-063
Fuel Line Pressure
1. Start the engine and run it at idle.
2. Set the lever on the adapter as shown in the figure.
3. Check the fuel line pressure.
Fuel line pressure: Approx. 186—226 kPa
(1.9—2.3 kg/cm2, 27—33 psi)
4. If not within specification, check the vacuum hose.
5. Disconnect the vacuum hose from pressure regu-
lator, and place a finger over the end of the hose.
6. Check the fuel line pressure.
Fuel line pressure: 235—275 kPa
(2.4—2.8 kg/cm2, 34—40 psi)
7. If not within specification, replace the pressure
regulator.
8. Connect the vacuum hose to pressure regulator.
FUEL PUMP
Operation Test
1. Connect a jumper wire to the test connector
(Yellow).
2. Remove the fuel filler cap.
3. Turn the ignition switch ON.
4. Listen for operational sound of the fuel pump at
the filler inlet.
5. Install the fuel filler cap.
6. If no sound is heard, check the voltage at the fuel
pump connector (WY wire and a ground).
Voltage: 12V
7. If the voltage is normal, replace the fuel pump.
8. If not correct, check the circuit opening relay (Re-
fer to page 4B—86) and its circuits.
9. Disconnect the jumper wire.
76G04B-064
4B—49
Page 512 of 1865
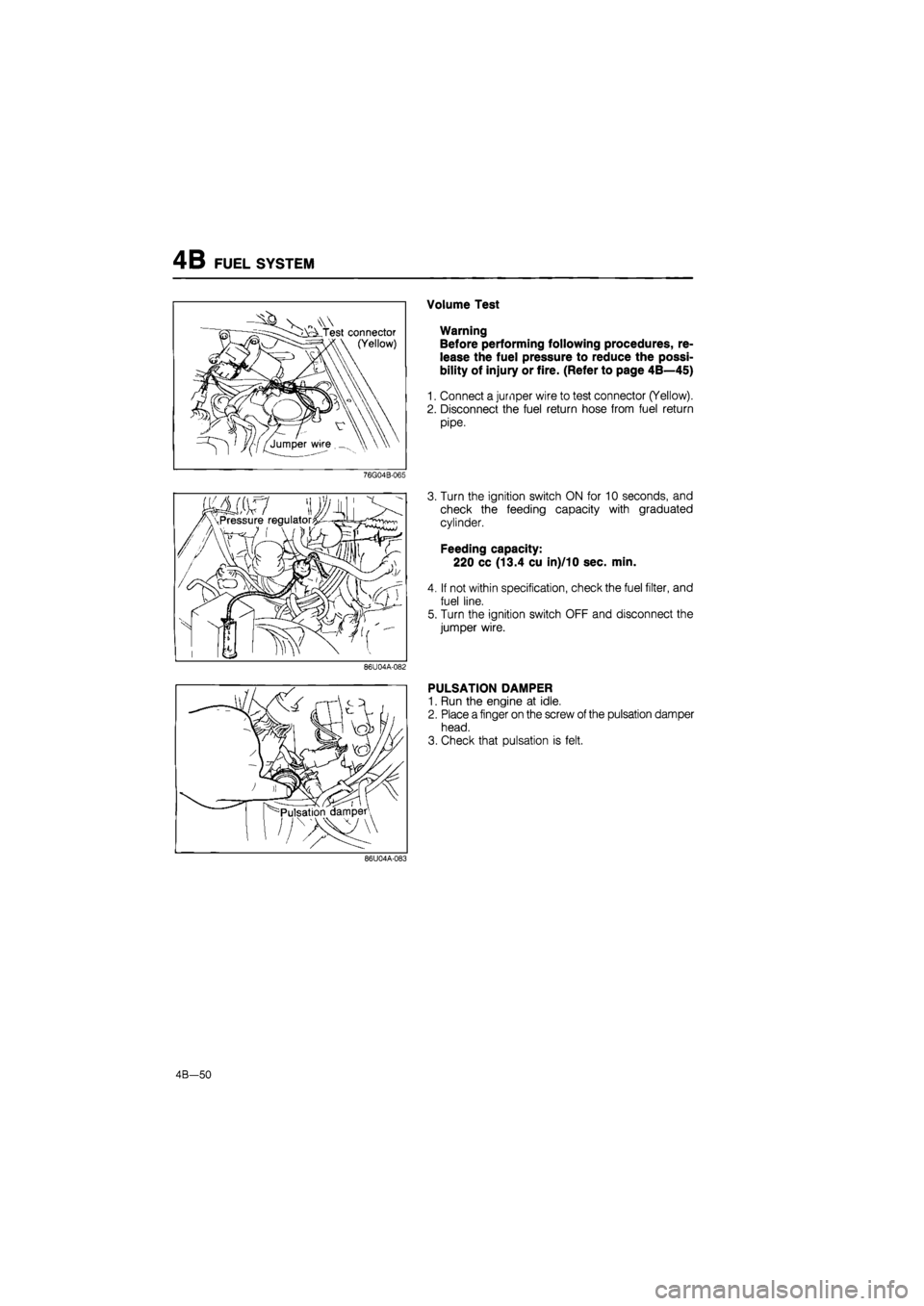
4B FUEL SYSTEM
Volume Test
Warning
Before performing following procedures, re-
lease the fuel pressure to reduce the possi-
bility of injury or fire. (Refer to page 4B—45)
1. Connect a jumper wire to test connector (Yellow).
2. Disconnect the fuel return hose from fuel return
pipe.
76G04B-065
3. Turn the ignition switch ON for 10 seconds, and
check the feeding capacity with graduated
cylinder.
Feeding capacity:
220 cc (13.4 cu in)/10 sec. min.
4. If not within specification, check the fuel filter, and
fuel line.
5. Turn the ignition switch OFF and disconnect the
jumper wire.
86U04A-082
PULSATION DAMPER
1. Run the engine at idle.
2. Place a finger on the screw of the pulsation damper
head.
3. Check that pulsation is felt.
86U04A-083
4B—50
Page 513 of 1865
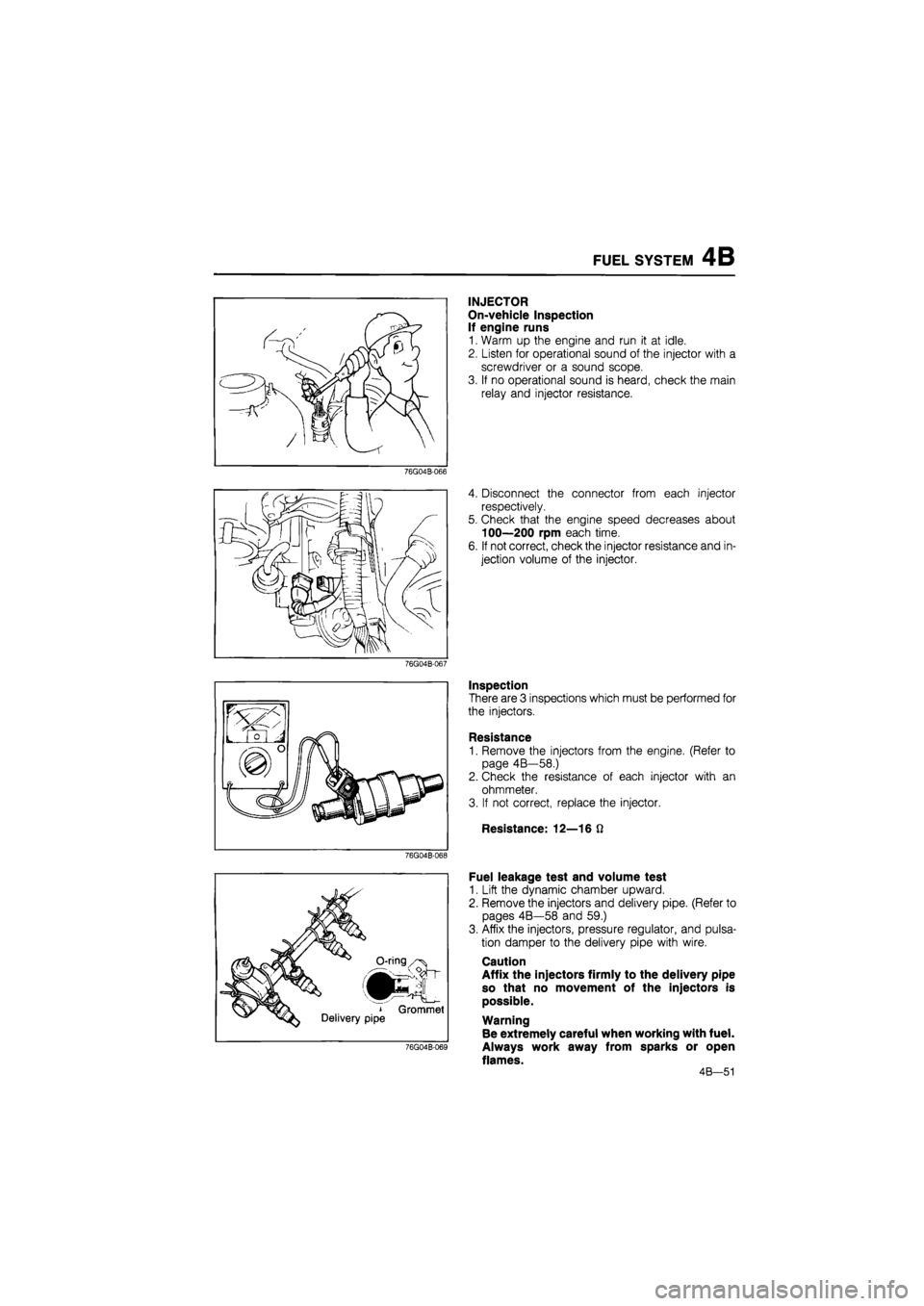
FUEL SYSTEM 4B
INJECTOR
On-vehicle Inspection
If engine runs
1. Warm up the engine and run it at idle.
2. Listen for operational sound of the injector with a
screwdriver or a sound scope.
3. If no operational sound is heard, check the main
relay and injector resistance.
76G04B-066
4. Disconnect the connector from each injector
respectively.
5. Check that the engine speed decreases about
100—200 rpm each time.
6. If not correct, check the injector resistance and in-
jection volume of the injector.
76G04B-067
Inspection
There are 3 inspections which must be performed for
the injectors.
Resistance
1. Remove the injectors from the engine. (Refer to
page 4B—58.)
2. Check the resistance of each injector with an
ohmmeter.
3. If not correct, replace the injector.
Resistance: 12—16 ft
76G04B-068
' Grommet Delivery pipe
76G04B-069
Fuel leakage test and volume test
1. Lift the dynamic chamber upward.
2. Remove the injectors and delivery pipe. (Refer to
pages 4B—58 and 59.)
3. Affix the injectors, pressure regulator, and pulsa-
tion damper to the delivery pipe with wire.
Caution
Affix the injectors firmly to the delivery pipe
so that no movement of the injectors is
possible.
Warning
Be extremely careful when working with fuel.
Always work away from sparks or open
flames.
4B—51
Page 514 of 1865
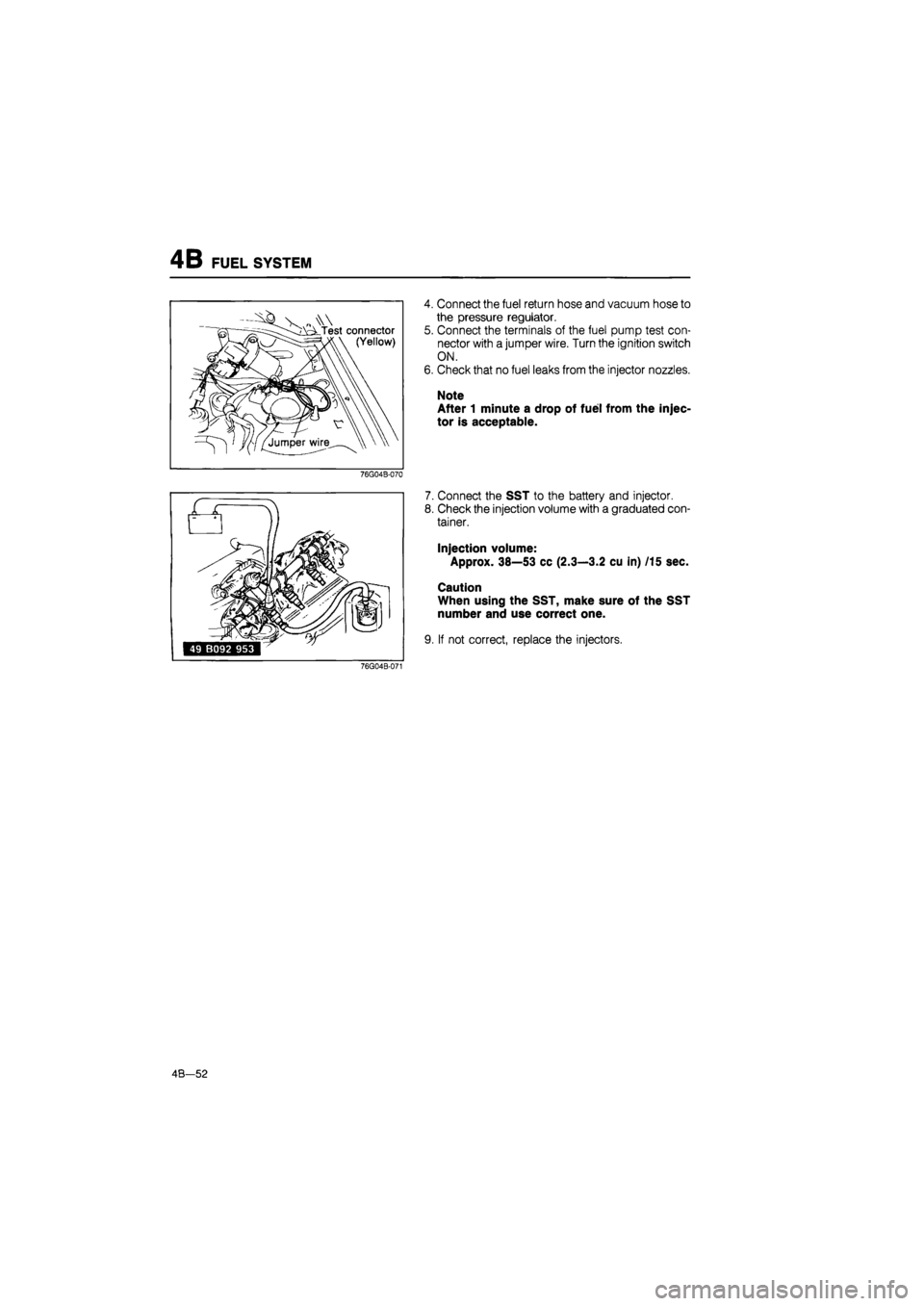
4B FUEL SYSTEM
v - \\N . Test connector
VW^^^^^^AX (Yellow)
76G04B-070
4. Connect the fuel return hose and vacuum hose to
the pressure regulator.
5. Connect the terminals of the fuel pump test con-
nector with a jumper wire. Turn the ignition switch
ON.
6. Check that no fuel leaks from the injector nozzles.
Note
After 1 minute a drop of fuel from the injec-
tor is acceptable.
7. Connect the SST to the battery and injector.
8. Check the injection volume with a graduated con-
tainer.
Injection volume:
Approx. 38—53 cc (2.3—3.2 cu in) /15 sec.
Caution
When using the SST, make sure of the SST
number and use correct one.
9. If not correct, replace the injectors.
76G04B-071
4B-52
Page 515 of 1865
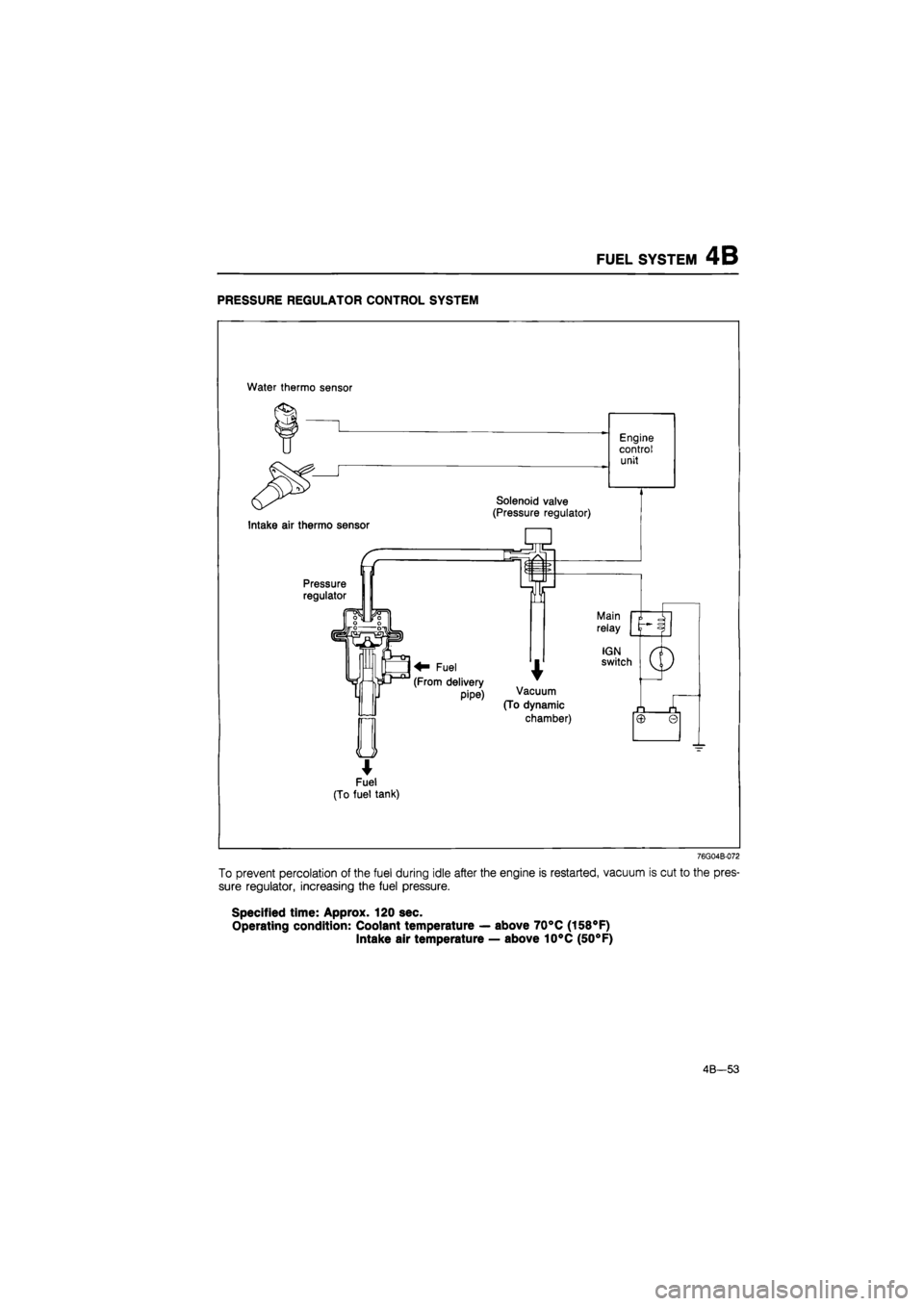
FUEL SYSTEM 4B
PRESSURE REGULATOR CONTROL SYSTEM
Water thermo sensor
*
Fuel
(To fuel tank)
76G04B-072
To prevent percolation of the fuel during idle after the engine is restarted, vacuum is cut to the pres-
sure regulator, increasing the fuel pressure.
Specified time: Approx. 120 sec.
Operating condition: Coolant temperature — above 70°C (158°F)
Intake air temperature — above 10°C (50°F)
4B—53
Page 516 of 1865
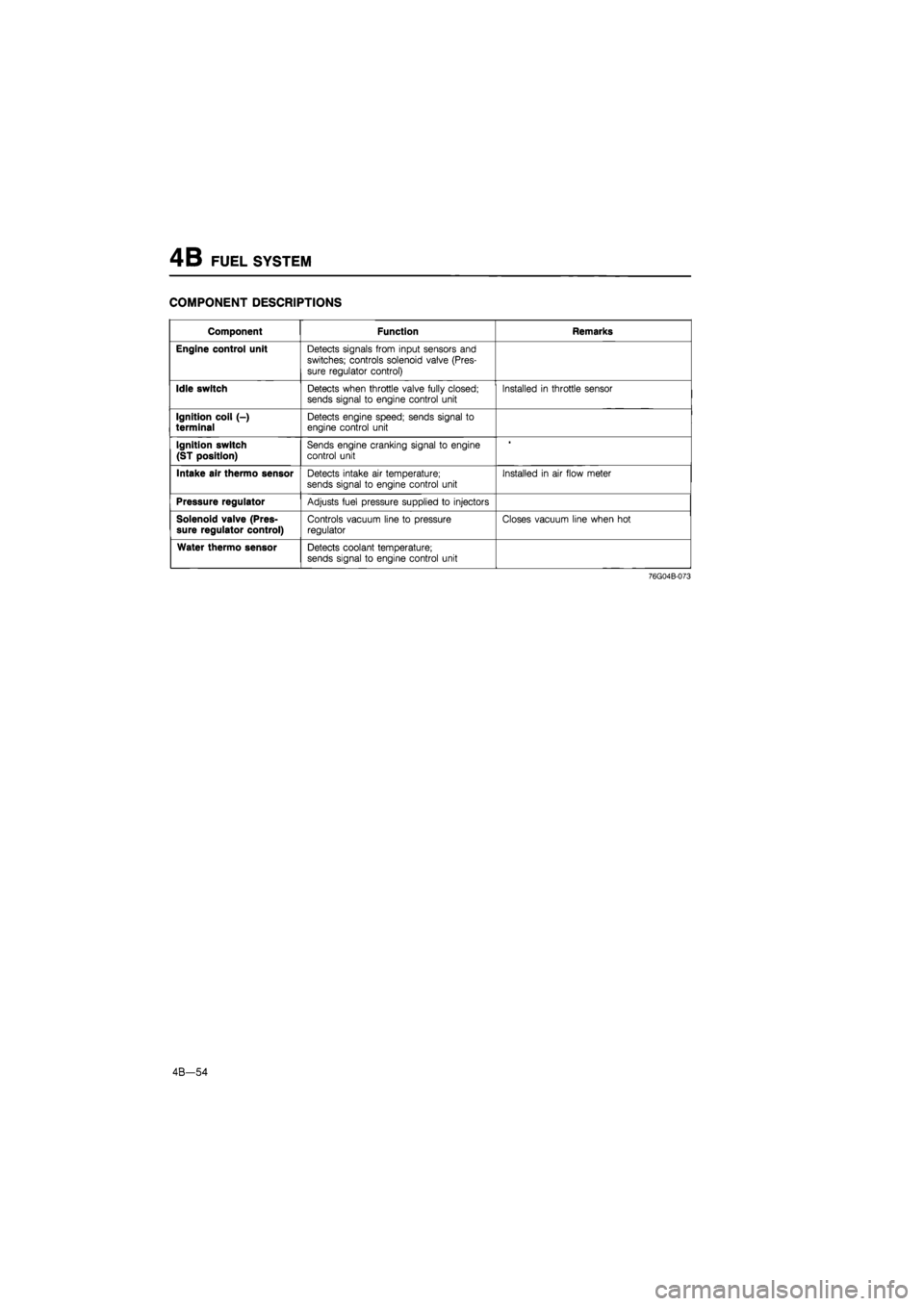
4B FUEL SYSTEM
COMPONENT DESCRIPTIONS
Component Function Remarks
Engine control unit Detects signals from input sensors and
switches; controls solenoid valve (Pres-
sure regulator control)
Idle switch Detects when throttle valve fully closed; sends signal to engine control unit Installed in throttle sensor
Ignition coil (-) terminal Detects engine speed; sends signal to engine control unit
Ignition switch
(ST position)
Sends engine cranking signal to engine control unit
Intake air thermo sensor Detects intake air temperature; sends signal to engine control unit
Installed in air flow meter
Pressure regulator Adjusts fuel pressure supplied to injectors
Solenoid valve (Pres-sure regulator control) Controls vacuum line to pressure regulator Closes vacuum line when hot
Water thermo sensor Detects coolant temperature; sends signal to engine control unit
76G04B-073
4B—54
Page 517 of 1865
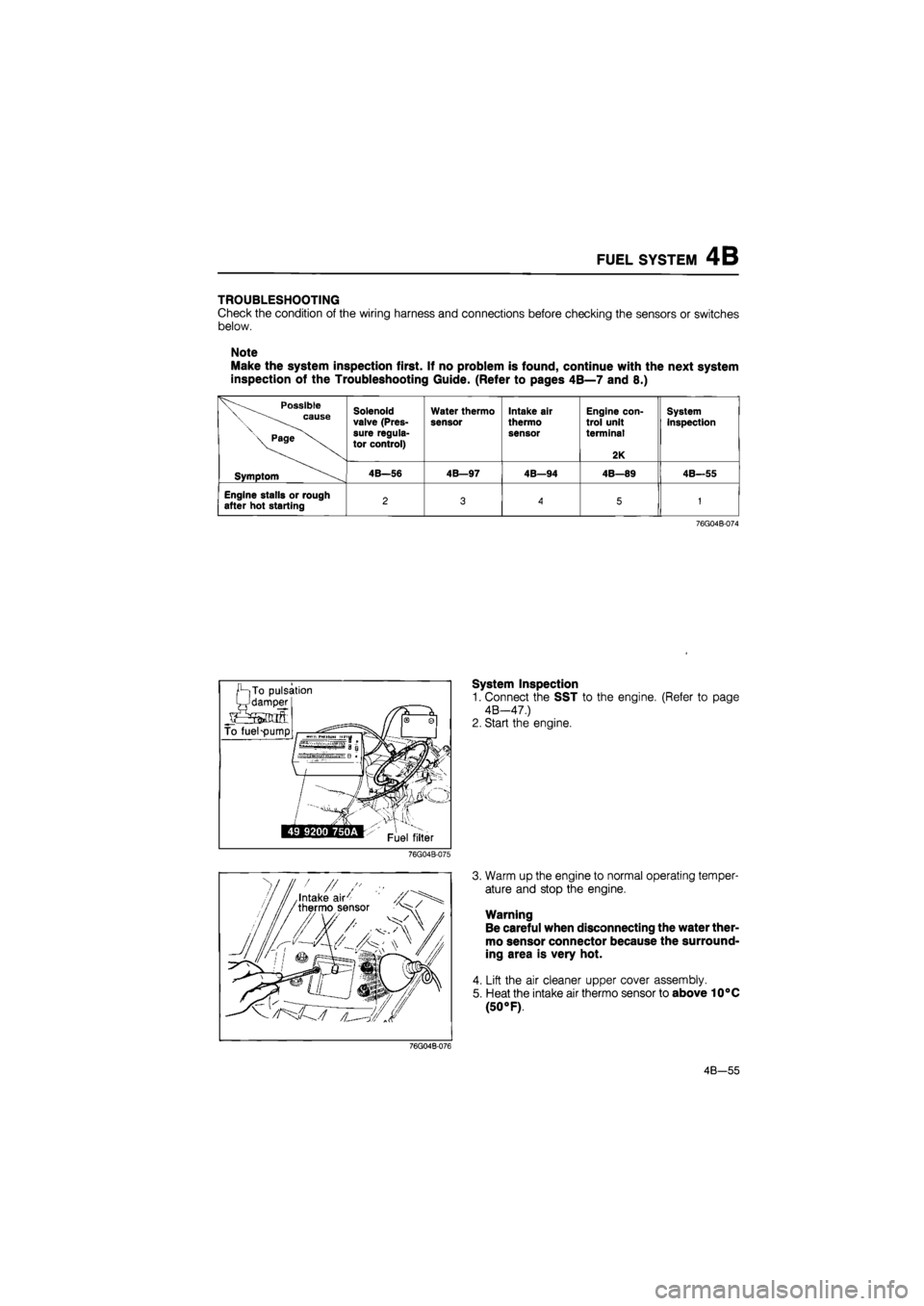
FUEL SYSTEM 4B
TROUBLESHOOTING
Check the condition of the wiring harness and connections before checking the sensors or switches
below.
Note
Make the system inspection first. If no problem is found, continue with the next system
inspection of the Troubleshooting Guide. (Refer to pages 4B—7 and 8.)
Possible \ cause
\ Page
Solenoid valve (Pres-sure regula-tor control)
Water thermo
sensor Intake air
thermo sensor
Engine con-trol unit terminal
2K
System inspection
Symptom 4B—56 4B—97 4B—94 4B—89 4B—55
Engine stalls or rough after hot starting 2 3
A
5 1
76G04B-074
System Inspection
1. Connect the SST to the engine. (Refer to page
4B—47.)
2. Start the engine.
76G04B-075
3. Warm up the engine to normal operating temper-
ature and stop the engine.
Warning
Be careful when disconnecting the water ther-
mo sensor connector because the surround-
ing area is very hot.
4. Lift the air cleaner upper cover assembly.
5. Heat the intake air thermo sensor to above 10°C
(50 °F).
76G04B-076
4B—55
Page 518 of 1865
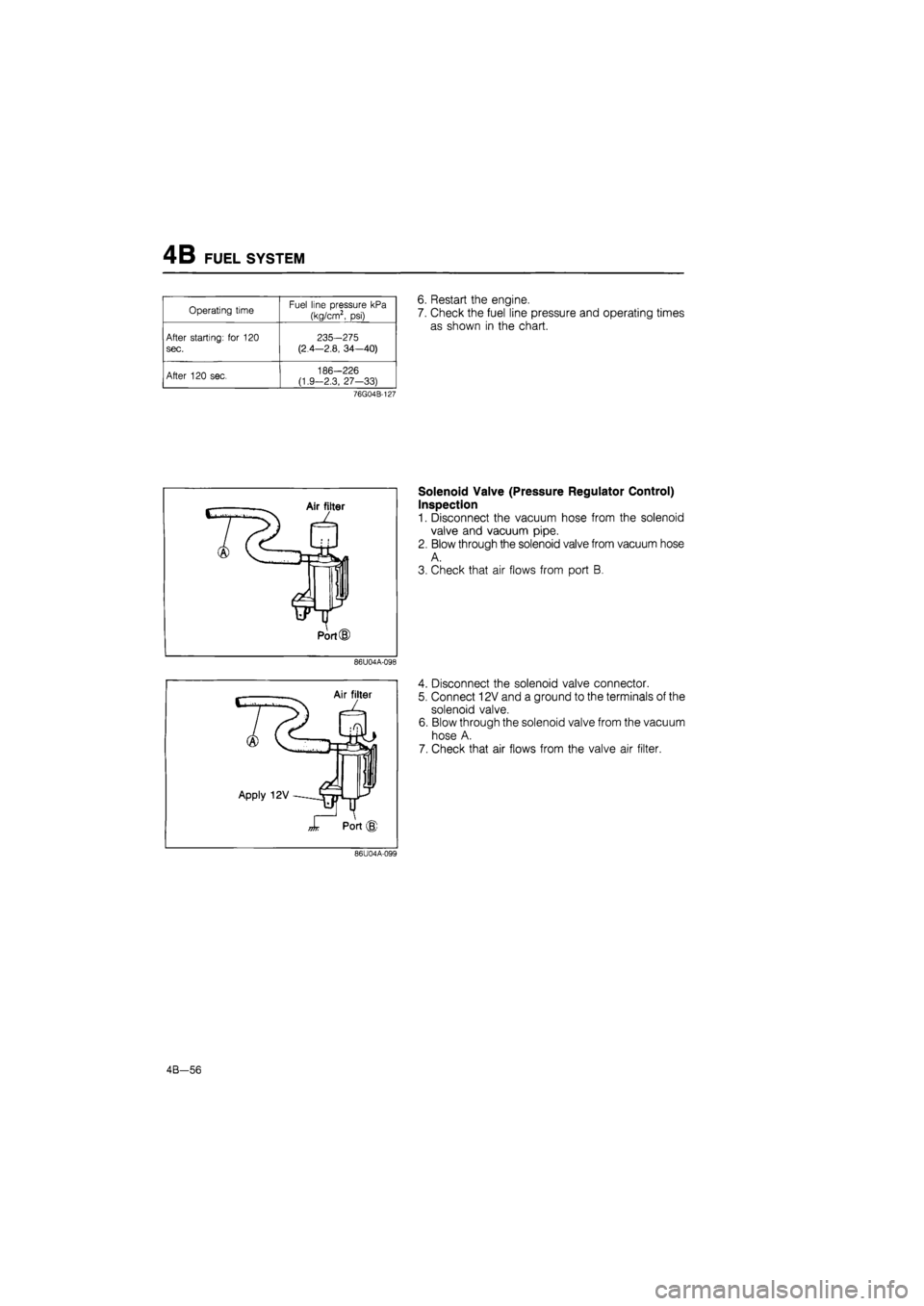
4B FUEL SYSTEM
Operating time Fuel line pressure kPa
(kg/cm2, psi)
After starting: for 120
sec.
235-275
(2.4—2.8, 34—40)
After 120 sec, 186-226 (1.9-2.3, 27-33)
6. Restart the engine.
7. Check the fuel line pressure and operating times
as shown in the chart.
76G04B-127
Solenoid Valve (Pressure Regulator Control)
Inspection
1. Disconnect the vacuum hose from the solenoid
valve and vacuum pipe.
2. Blow through the solenoid valve from vacuum hose
A.
3. Check that air flows from port B.
86U04A-098
Air filter
Apply 12V
Port (J)
4. Disconnect the solenoid valve connector.
5. Connect 12V and a ground to the terminals of the
solenoid valve.
6. Blow through the solenoid valve from the vacuum
hose A.
7. Check that air flows from the valve air filter.
86U04A-099
4B-56
Page 519 of 1865
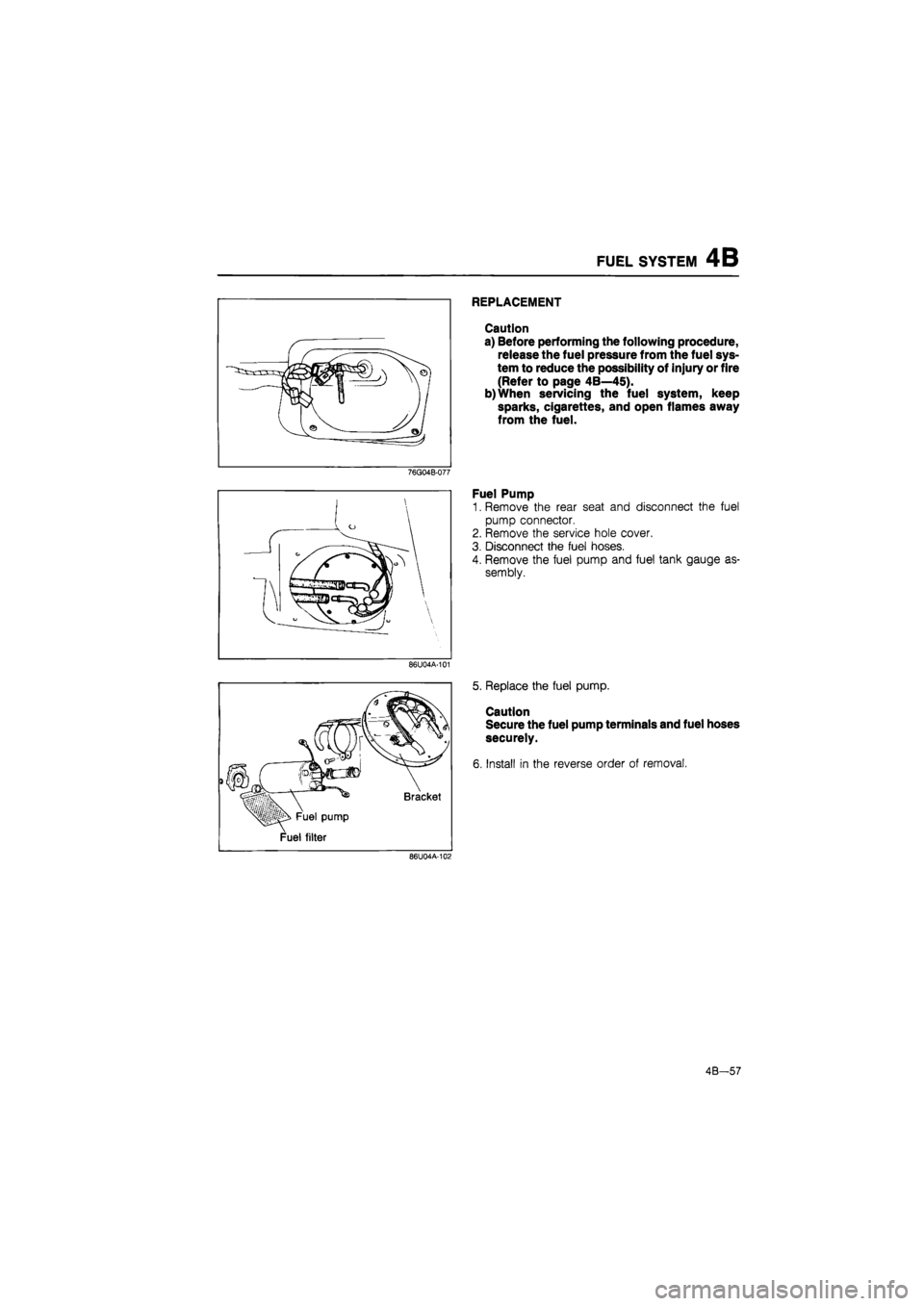
FUEL SYSTEM 4B
REPLACEMENT
Caution
a) Before performing the following procedure,
release the fuel pressure from the fuel sys-
tem to reduce the possibility of injury or fire
(Refer to page 4B—45).
b)When servicing the fuel system, keep
sparks, cigarettes, and open flames away
from the fuel.
76G04B-077
86U04A-101
M Fuel pump
Fuel filter
Bracket
86U04A-102
Fuel Pump
1. Remove the rear seat and disconnect the fuel
pump connector.
2. Remove the service hole cover.
3. Disconnect the fuel hoses.
4. Remove the fuel pump and fuel tank gauge as-
sembly.
5. Replace the fuel pump.
Caution
Secure the fuel pump terminals and fuel hoses
securely.
6. Install in the reverse order of removal.
4B—57
Page 520 of 1865
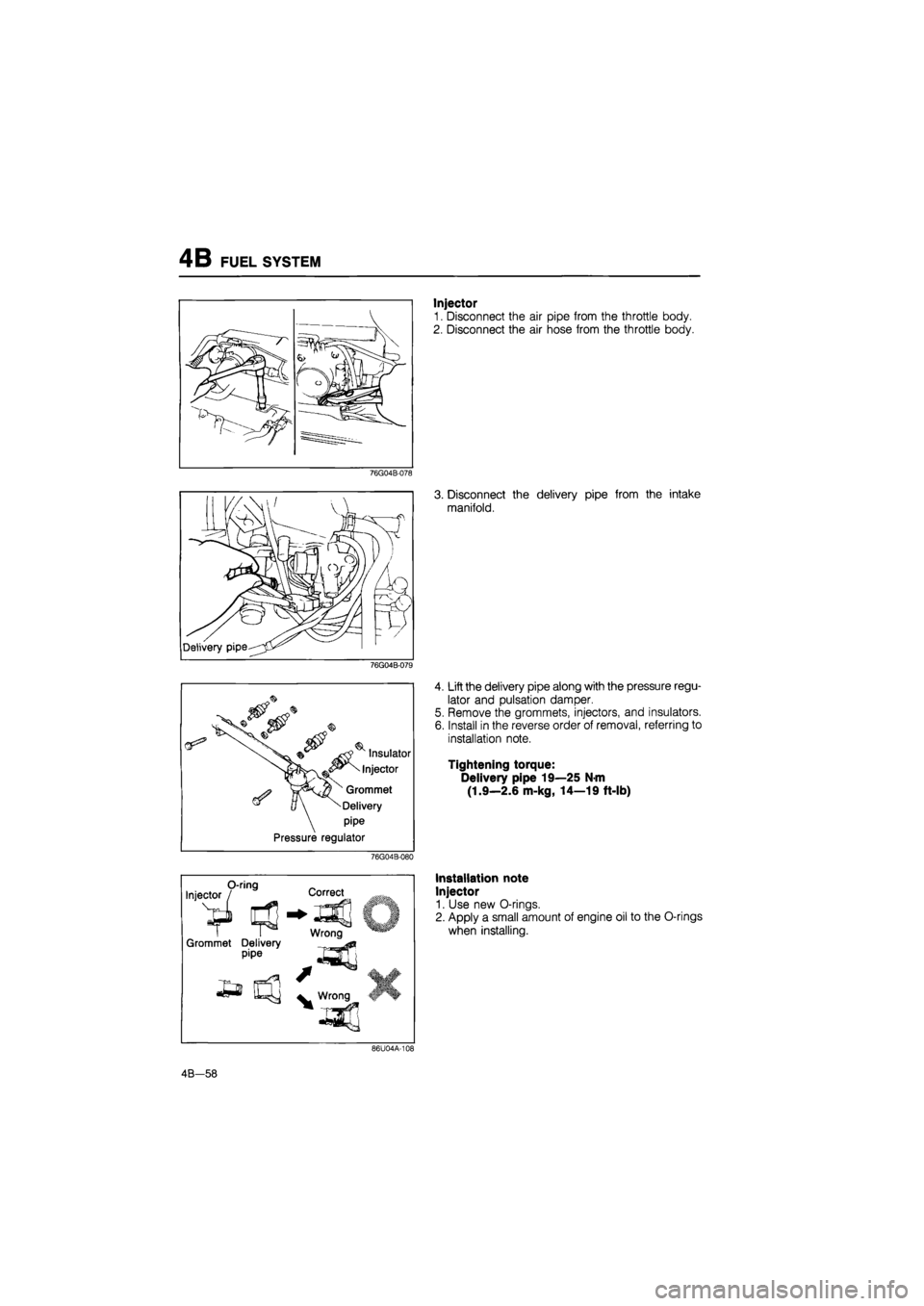
4B FUEL SYSTEM
76G04B-078
76G04B-079
Insulator
Injector
Grommet
Delivery
pipe
Pressure regulator
76G04B-080
Injector O-ring Correct
1 #J
Grommet Delivery pipe
Wrong
£a
/
^ Wrong IF
Injector
1. Disconnect the air pipe from the throttle body.
2. Disconnect the air hose from the throttle body.
3. Disconnect the delivery pipe from the intake
manifold.
4. Lift the delivery pipe along with the pressure regu-
lator and pulsation damper.
5. Remove the grommets, injectors, and insulators.
6. Install in the reverse order of removal, referring to
installation note.
Tightening torque:
Delivery pipe 19—25 N-m
(1.9—2.6 m-kg, 14—19 ft-lb)
Installation note
Injector
1. Use new O-rings.
2. Apply a small amount of engine oil to the O-rings
when installing.
86U04A-108
4B-58