MITSUBISHI ECLIPSE 1990 Owner's Manual
Manufacturer: MITSUBISHI, Model Year: 1990, Model line: ECLIPSE, Model: MITSUBISHI ECLIPSE 1990Pages: 391, PDF Size: 15.27 MB
Page 21 of 391
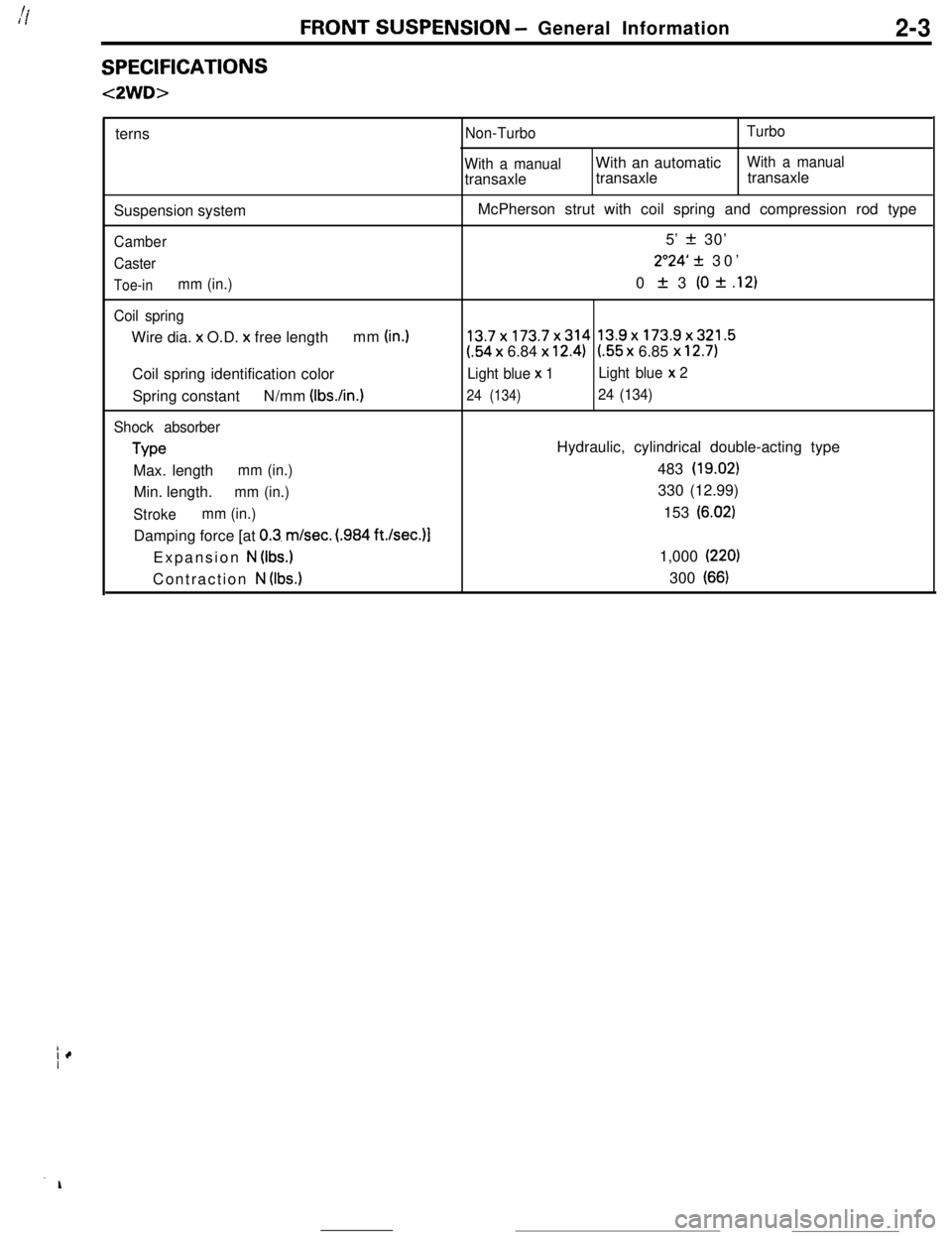
FRONT SUSPENSION - General Information2-3
SPECIFICATIONS
<2WD>terns
Suspension system
Camber
Caster
Toe-inmm (in.)
Coil springWire dia. x O.D.
x free lengthmm (in.)Coil spring identification color
Spring constantN/mm (IbsAn.)
Shock absorber
TypeMax. length
mm (in.)Min. length.
mm (in.)
Strokemm (in.)Damping force [at
0.3. m/set. (.984 ft./sec.)l
Expansion
N (Ibs.)Contraction
N (Ibs.)
Non-TurboTurbo
With a manualWith an automatic
With a manualtransaxletransaxletransaxle
McPherson strut with coil spring and compression rod type
5’
z!z 30’
2”24’ 31 30’
0
It 3 (0 * .12)
13.7x173.7x314 13.9x173.9x321.5
(.54 x 6.84 x 12.4)l.55 x 6.85 x 12.7)
Light blue x 1Light blue x 2
24 (134)24 (134)Hydraulic, cylindrical double-acting type
483
(19.02)330 (12.99)
153
(6.02)1,000
(220)300
(66)
Page 22 of 391
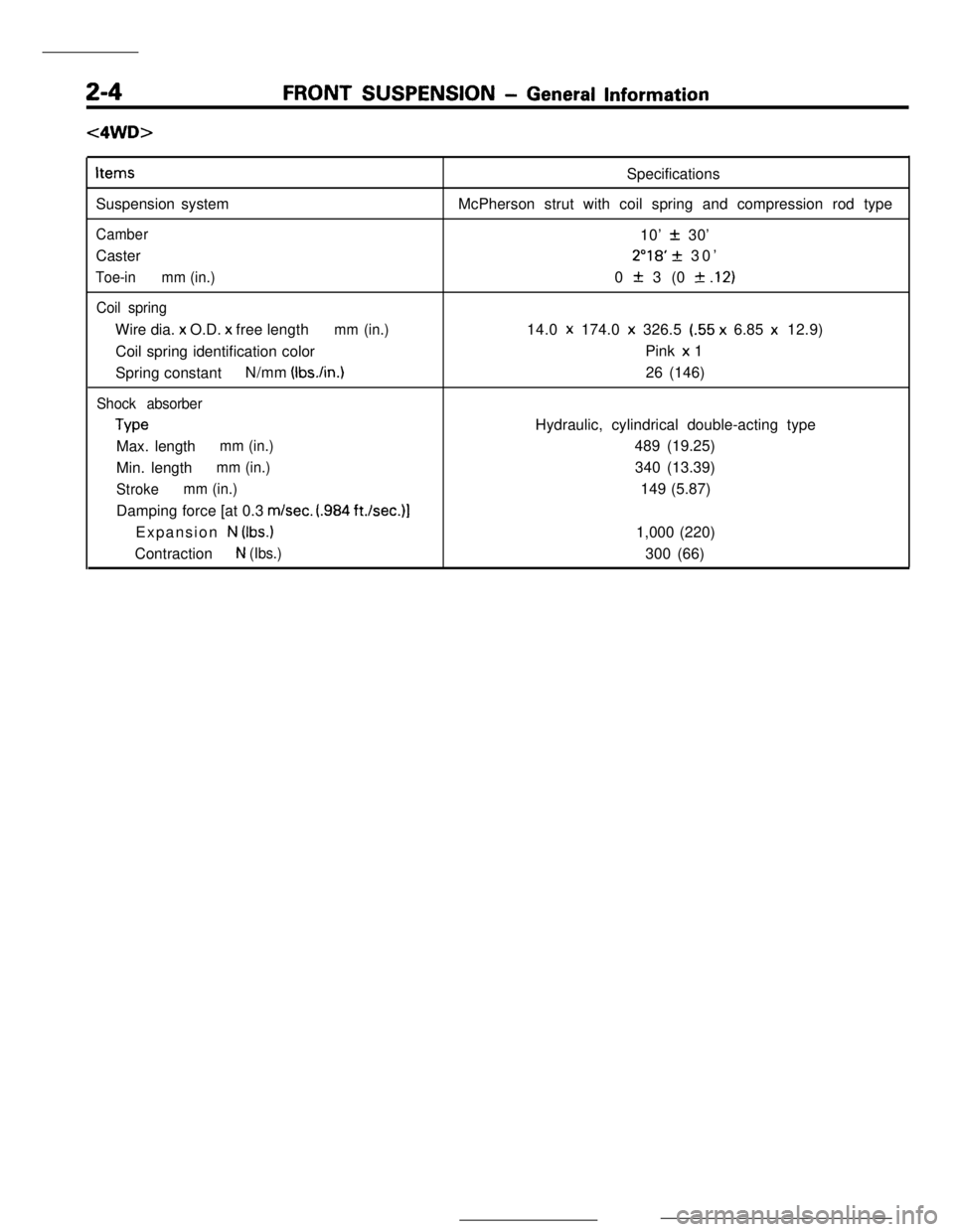
FRONT SUSPENSION - General Information
c4WD>Items
Suspension system
CamberCaster
Toe-inmm (in.)
Coil springWire dia. x O.D. x free length
mm (in.)Coil spring identification color
Spring constantN/mm
(Ibs./in.)
Shock absorber
TypeMax. length
mm (in.)Min. length
mm (in.)
Strokemm (in.)Damping force [at 0.3
m/set. (.984 ft./set.)]Expansion
N (Ibs.)Contraction
N (Ibs.)Specifications
McPherson strut with coil spring and compression rod type
10’
+- 30’
2”18’ + 30’
0
zk 3 (0 f .l2)14.0 x 174.0
x 326.5 (.55 x 6.85 x 12.9)
Pink x 1
26 (146)
Hydraulic, cylindrical double-acting type
489 (19.25)
340 (13.39)
149 (5.87)
1,000 (220)
300 (66)
Page 23 of 391
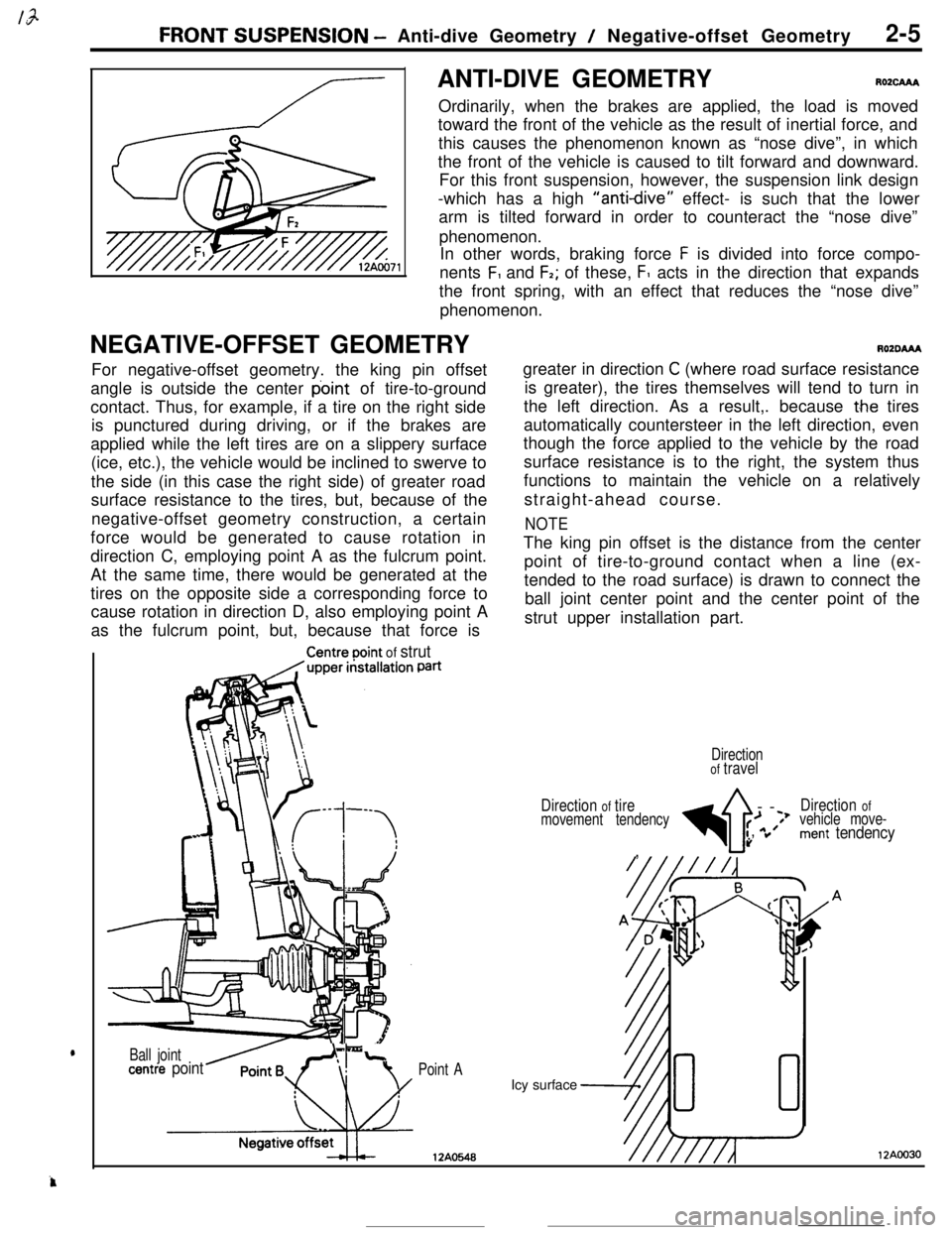
FRONT SUSPENSION - Anti-dive Geometry / Negative-offset Geometry2-5ANTI-DIVE GEOMETRY
RO2cAAAOrdinarily, when the brakes are applied, the load is moved
toward the front of the vehicle as the result of inertial force, and
this causes the phenomenon known as “nose dive”, in which
the front of the vehicle is caused to tilt forward and downward.
For this front suspension, however, the suspension link design
-which has a high
“anti-dive” effect- is such that the lower
arm is tilted forward in order to counteract the “nose dive”
phenomenon.
In other words, braking force
F is divided into force compo-
nents
F, and F2; of these, F1 acts in the direction that expands
the front spring, with an effect that reduces the “nose dive”
phenomenon.
NEGATIVE-OFFSET GEOMETRY
AOZDAAAFor negative-offset geometry. the king pin offset
angle is outside the center point of tire-to-ground
contact. Thus, for example, if a tire on the right side
is punctured during driving, or if the brakes are
applied while the left tires are on a slippery surface
(ice, etc.), the vehicle would be inclined to swerve to
the side (in this case the right side) of greater road
surface resistance to the tires, but, because of the
negative-offset geometry construction, a certain
force would be generated to cause rotation in
direction C, employing point A as the fulcrum point.
At the same time, there would be generated at the
tires on the opposite side a corresponding force to
cause rotation in direction D, also employing point A
as the fulcrum point, but, because that force is
Centreooint of strutPatigreater in direction
C (where road surface resistance
is greater), the tires themselves will tend to turn in
the left direction. As a result,. because
t.he tires
automatically countersteer in the left direction, even
though the force applied to the vehicle by the road
surface resistance is to the right, the system thus
functions to maintain the vehicle on a relatively
straight-ahead course.
NOTEThe king pin offset is the distance from the center
point of tire-to-ground contact when a line (ex-
tended to the road surface) is drawn to connect the
ball joint center point and the center point of the
strut upper installation part.
Point AIcy surface
12AO548
Ball jointLcentre point
t
Directionof travel
Direction
of tire
4--
Direction ofmovement tendency>f;’*Jvehicle move-:’
”ment tendency,
12AOO30
Page 24 of 391
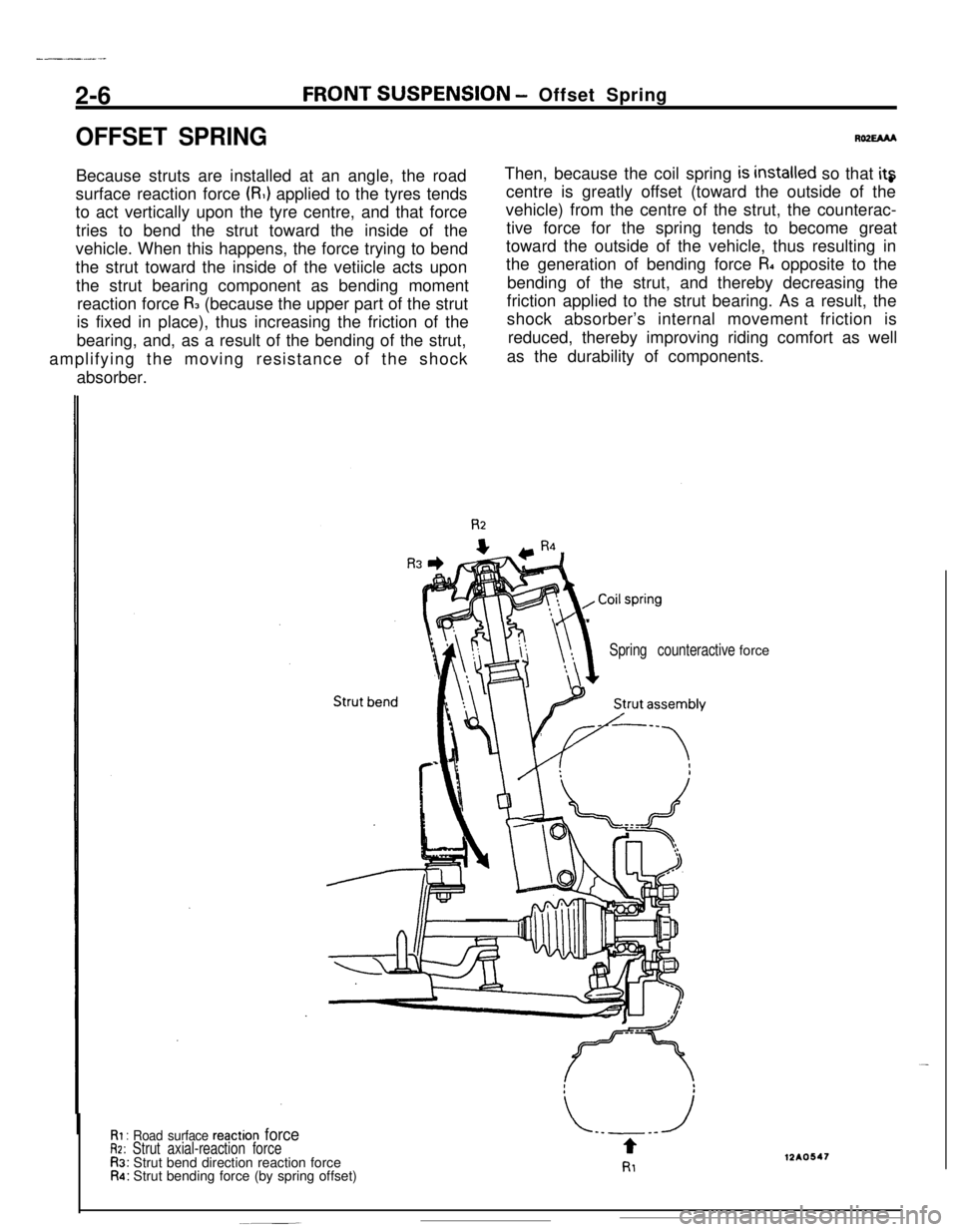
----2-6
FRONT SUSPENSION - Offset Spring
OFFSET SPRINGBecause struts are installed at an angle, the road
surface reaction force
(RI) applied to the tyres tends
to act vertically upon the tyre centre, and that force
tries to bend the strut toward the inside of the
vehicle. When this happens, the force trying to bend
the strut toward the inside of the vetiicle acts upon
the strut bearing component as bending moment
reaction force
FL (because the upper part of the strut
is fixed in place), thus increasing the friction of the
bearing, and, as a result of the bending of the strut,
amplifying the moving resistance of the shock
absorber.Ro2EMA
Then, because the coil spring
is installed so that itscentre is greatly offset (toward the outside of the
vehicle) from the centre of the strut, the counterac-
tive force for the spring tends to become great
toward the outside of the vehicle, thus resulting in
the generation of bending force
FL opposite to the
bending of the strut, and thereby decreasing the
friction applied to the strut bearing. As a result, the
shock absorber’s internal movement friction is
reduced, thereby improving riding comfort as well
as the durability of components.
Spring counteractiveforce
RI : Road surface reaction forceR2: Strut axial-reaction forceR3: Strut bend direction reaction forceR4: Strut bending force (by spring offset)
Page 25 of 391
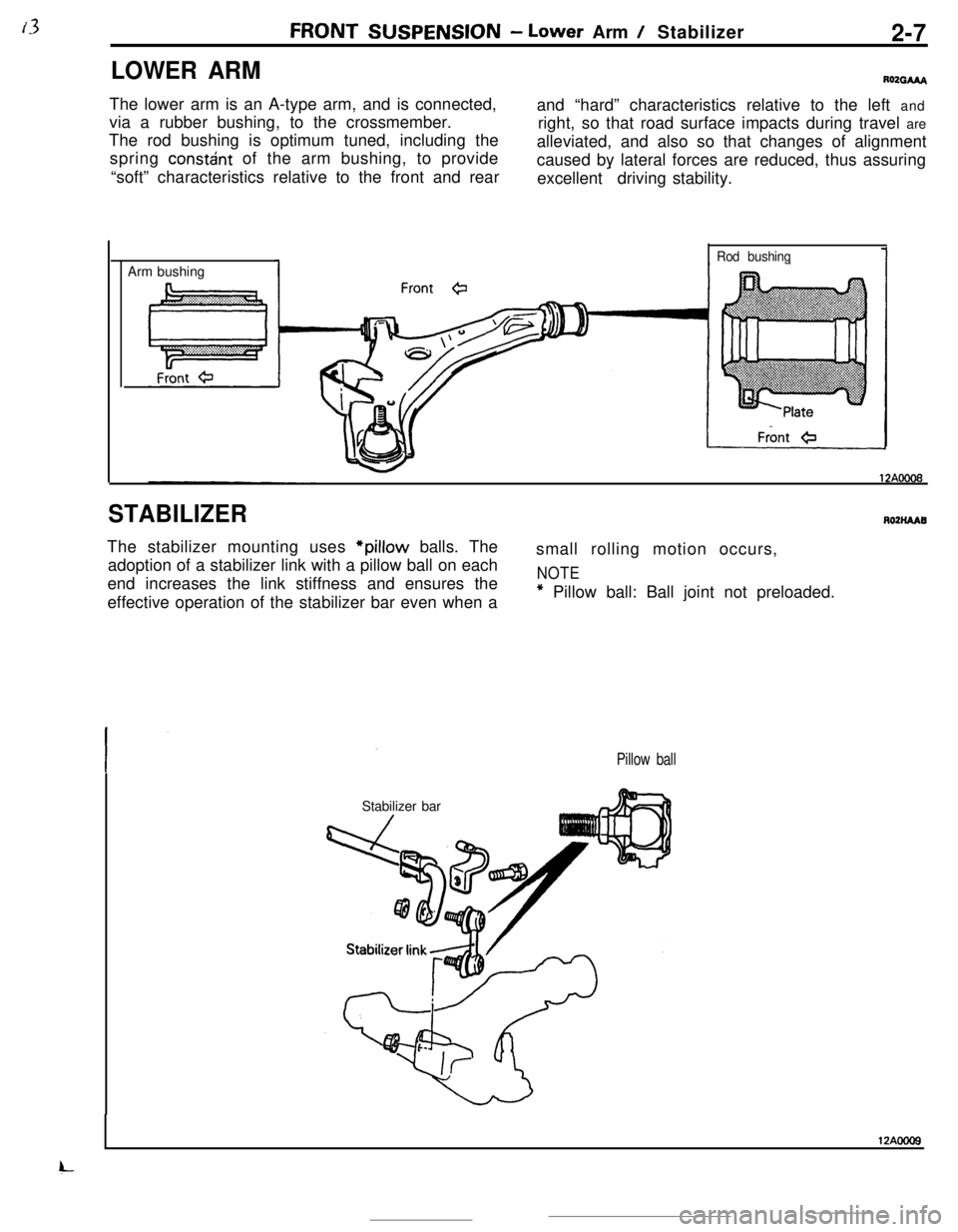
FRONT SUSPENSION- Lower Arm / Stabilizer2-7
LOWER ARM
ROZGAAAThe lower arm is an A-type arm, and is connected,
via a rubber bushing, to the crossmember.
The rod bushing is optimum tuned, including the
spring constant of the arm bushing, to provideand “hard” characteristics relative to the left and
right, so that road surface impacts during travel are
alleviated, and also so that changes of alignment
caused by lateral forces are reduced, thus assuring
“soft” characteristics relative to the front and rear
excellent
I driving stability.
Arm bushing
,m
Rod bushing
STABILIZERROZHAABThe stabilizer mounting uses
*pillow balls. The
adoption of a stabilizer link with a pillow ball on each
end increases the link stiffness and ensures the
effective operation of the stabilizer bar even when asmall rolling motion occurs,
NOTE* Pillow ball: Ball joint not preloaded.
Pillow ballStabilizer bar
12AOOOS
4--
Page 26 of 391
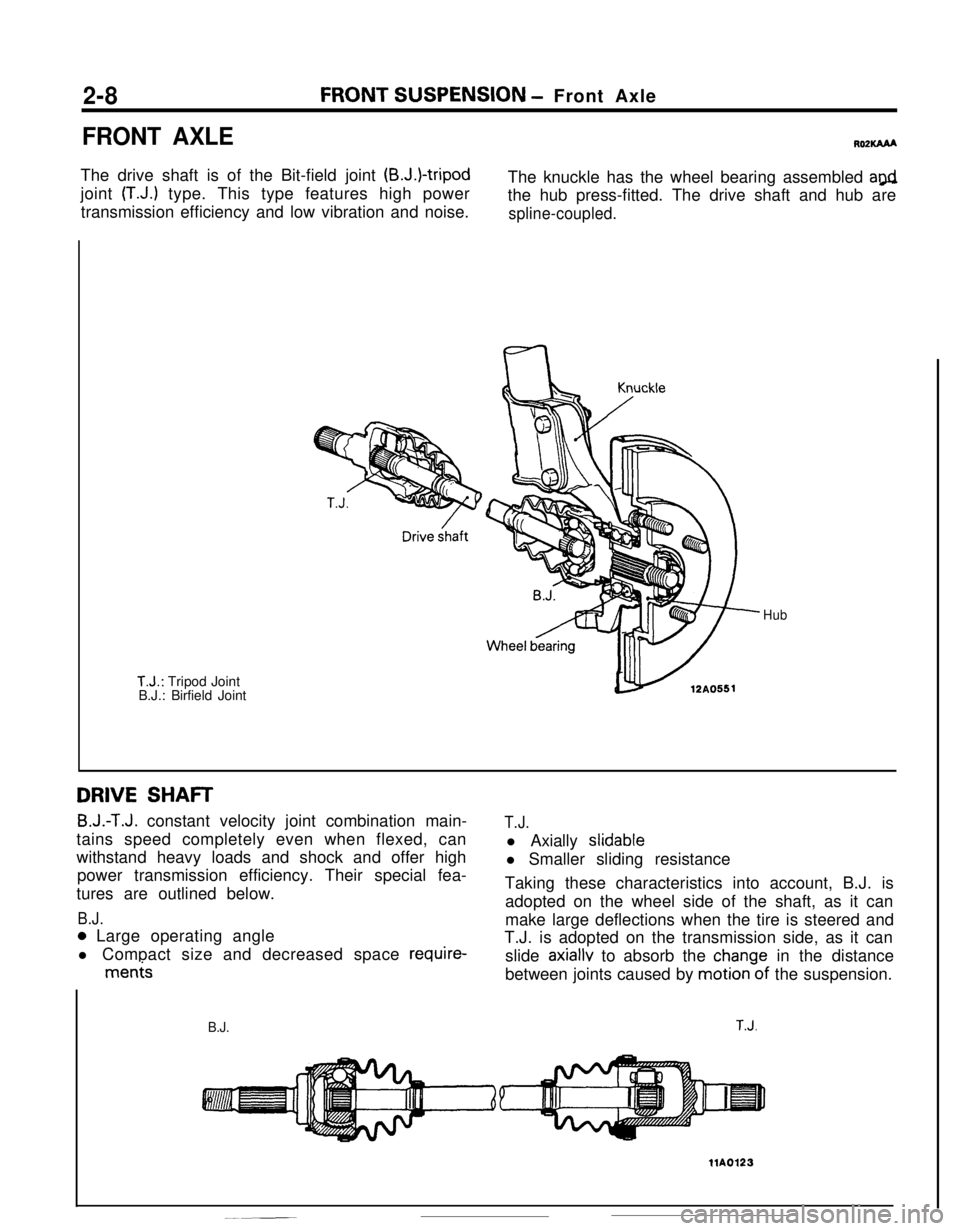
2-8FRONT SUSPENSION - Front Axle
FRONT AXLEROPKAAAThe drive shaft is of the Bit-field joint
(B.J.)-tripodjoint
(T.J.) type. This type features high power
transmission efficiency and low vibration and noise.The knuckle has the wheel bearing assembled
a@the hub press-fitted. The drive shaft and hub are
spline-coupled.
T.J.: Tripod Joint
B.J.: Birfield Joint
Hub
DRIVE SHAFT
B.J.-T.J. constant velocity joint combination main-
tains speed completely even when flexed, can
withstand heavy loads and shock and offer high
power transmission efficiency. Their special fea-
tures are outlined below.
B.J.T.J.l Axially
slidablel Smaller sliding resistance
0 Large operating angle
l Compact size and decreased space
require-
me&Taking these characteristics into account, B.J. is
adopted on the wheel side of the shaft, as it can
make large deflections when the tire is steered and
T.J. is adopted on the transmission side, as it can
slide
axiallv to absorb the chanae in the distance
between joints caused by
motionWof the suspension.
B.J.T.J.
llA0123
Page 27 of 391
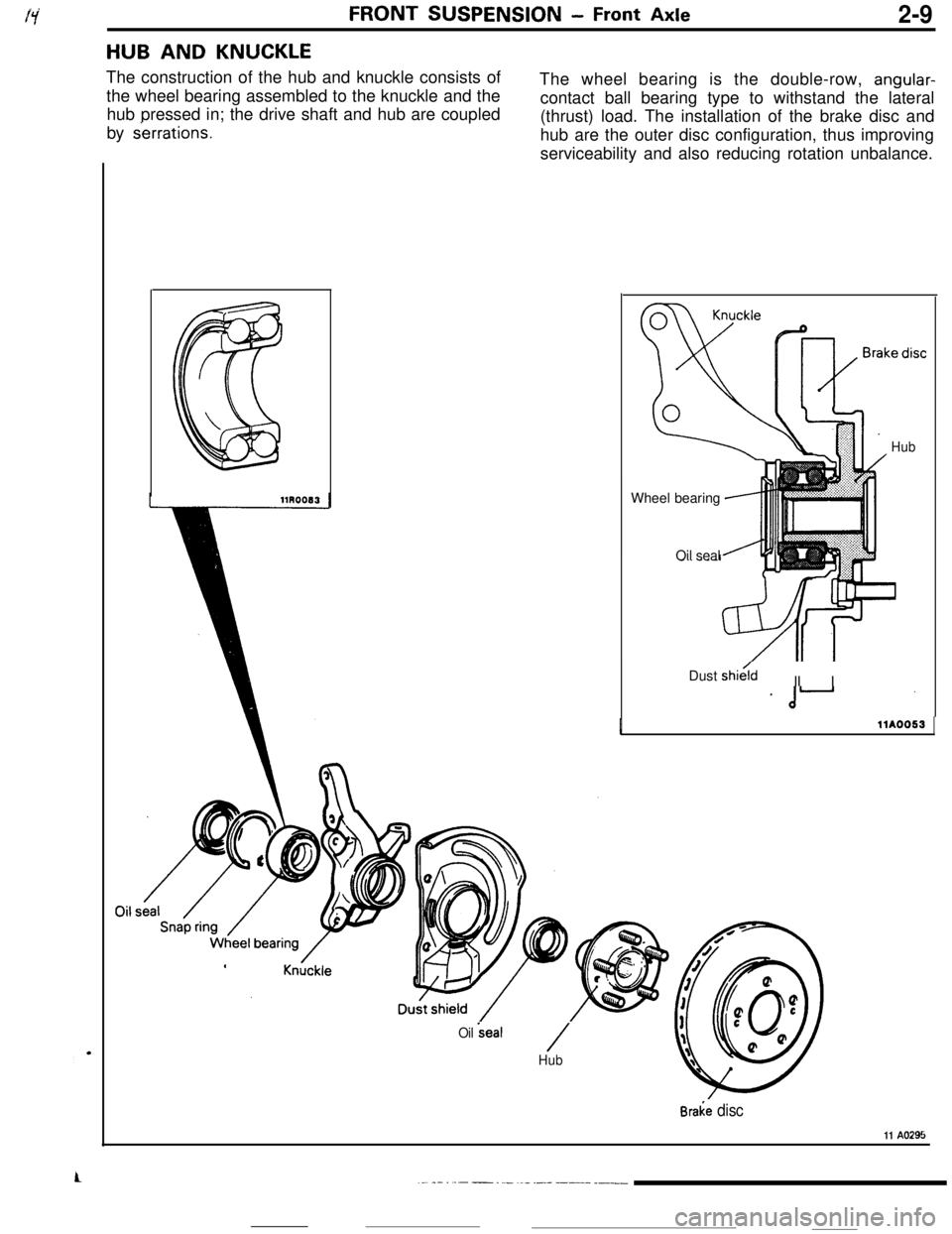
FRONT SUSPENSION - Front Axle2-9
HUB AND KNUCKLEThe construction of the hub and knuckle consists of
The wheel bearing is the double-row,
angular-the wheel bearing assembled to the knuckle and the
contact ball bearing type to withstand the lateral
hub pressed in; the drive shaft and hub are coupled
(thrust) load. The installation of the brake disc and
by
&rations.hub are the outer disc configuration, thus improving
serviceability and also reducing rotation unbalance.
Wheel bearing
Oil seal
HubDust shi&d
II I
IllA0053
Oil seal/HubBraie
disc
11 A0295
..~ -- . ..- - . .._ ~._ __.- ----_ .__
Page 28 of 391
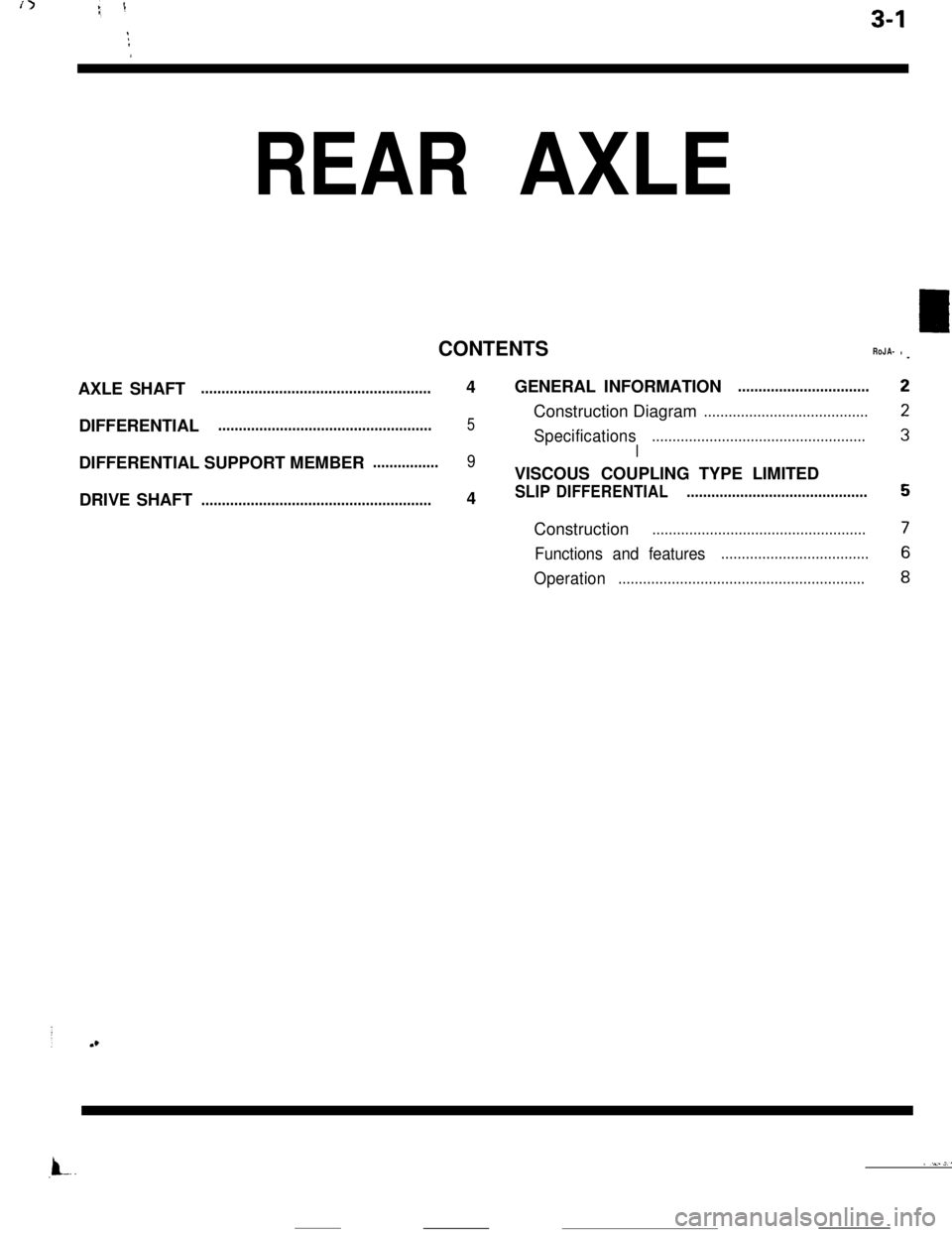
3-1
REAR
.L..,,....
Page 29 of 391
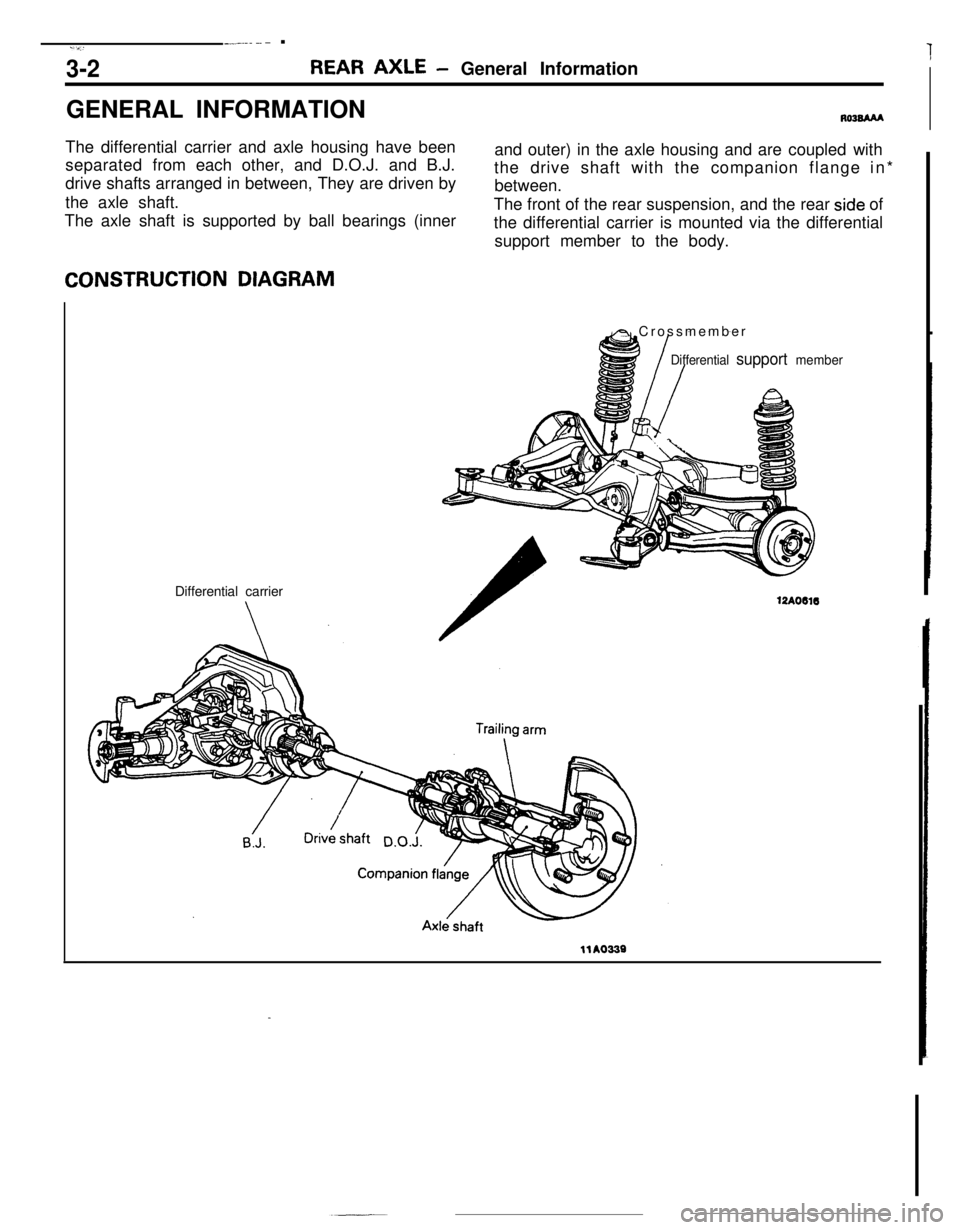
-.-...- ..v:T
3-2REAR AXLE- General Information
GENERAL INFORMATION
RO3BAAAThe differential carrier and axle housing have been
separated from each other, and D.O.J. and B.J.
drive shafts arranged in between, They are driven by
the axle shaft.
The axle shaft is supported by ball bearings (innerand outer) in the axle housing and are coupled with
the drive shaft with the companion flange in*
between.
The front of the rear suspension, and the rear
side of
the differential carrier is mounted via the differential
support member to the body.CONSTRUCTION DIAGRAM
Differential carrier
A Crossmember
Differential support member
12AO616
llA0339
Page 30 of 391
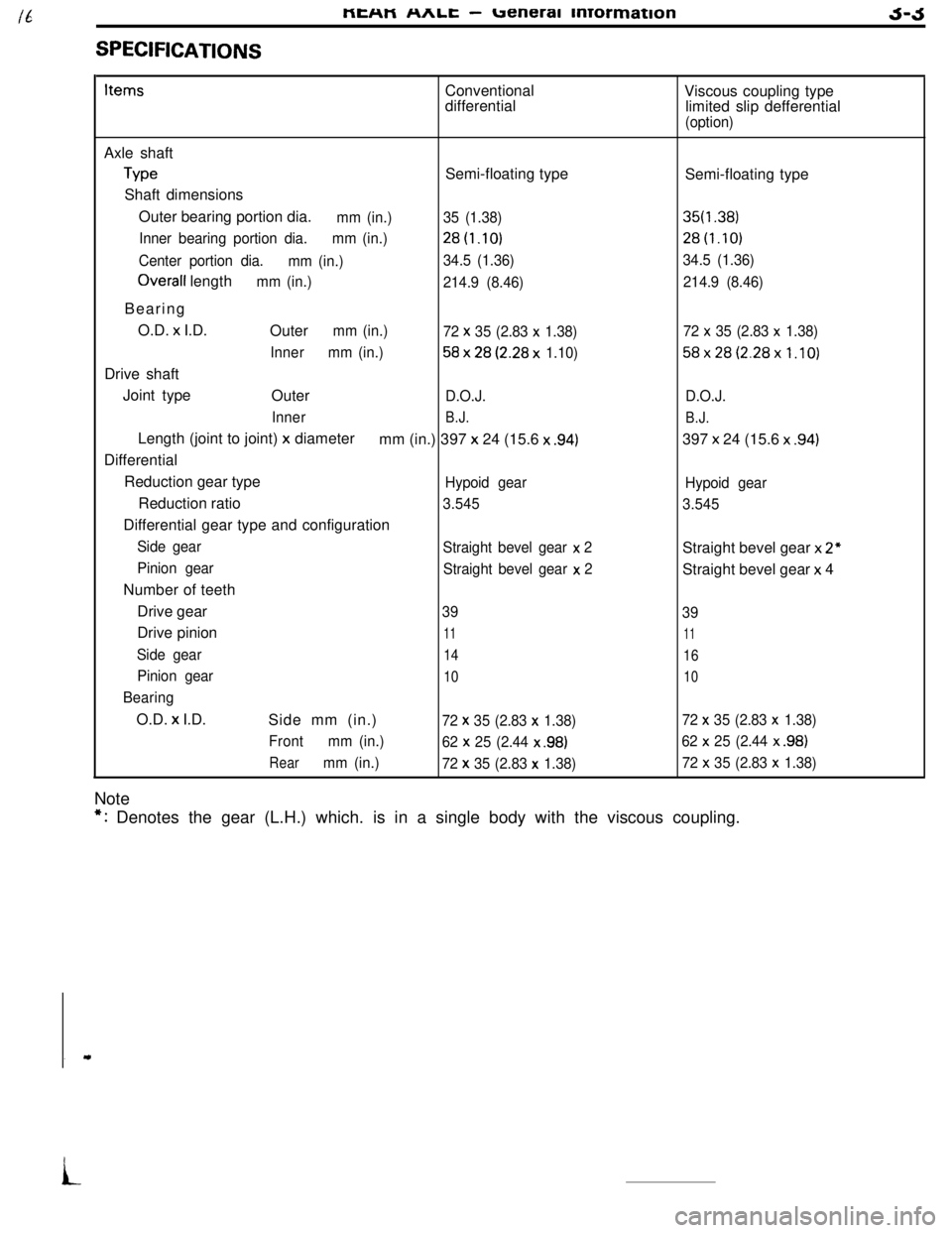
SPECIFICATIONSMEHM
nnlL -ueneral mrormationJ-JItemsConventional
differentialViscous coupling type
limited slip defferential
(option)Axle shaft
TypeSemi-floating type
Shaft dimensions
Outer bearing portion dia.
mm (in.)35 (1.38)
Inner bearing portion dia.mm (in.)28t1.10)
Center portion dia.
mm (in.)34.5 (1.36)
Overall lengthmm (in.)
214.9 (8.46)Bearing
O.D. x I.D.
Outer
mm (in.)
72 x 35 (2.83 x 1.38)
Innermm (in.)
58x28(2.28x 1.10)Drive shaft
Joint type
Outer
D.O.J.
Inner
B.J.Length (joint to joint)
x diameter
mm (in.) 397 x 24 (15.6 x .94)Differential
Reduction gear type
Hypoid gearReduction ratio
3.545Differential gear type and configuration
Side gear
Straight bevel gear x 2
Pinion gear
Straight bevel gear x
2Number of teeth
Drive gear
39Drive pinion
11
Side gear14
Pinion gear10
BearingO.D.
x I.D.
Side mm (in.)72 x 35 (2.83 x 1.38)
Frontmm (in.)
62 x
25 (2.44 x .98)
Rearmm (in.)
72 x 35 (2.83 x 1.38)NoteSemi-floating type
35f1.38)28t1.10)
34.5 (1.36)
214.9 (8.46)
72
x 35 (2.83 x 1.38)
58x28(2.28x1.10)
D.O.J.
B.J.397 x 24 (15.6 x
.94)
Hypoid gear
3.545Straight bevel gear x
2”Straight bevel gear x 4
39
11
16
10
72 x 35 (2.83 x 1.38)
62
x 25 (2.44 x .98)
72 x 35 (2.83 x 1.38)
*: Denotes the gear (L.H.) which. is in a single body with the viscous coupling.
i