MITSUBISHI SPYDER 1990 Service Repair Manual
Manufacturer: MITSUBISHI, Model Year: 1990, Model line: SPYDER, Model: MITSUBISHI SPYDER 1990Pages: 2103, PDF Size: 68.98 MB
Page 181 of 2103
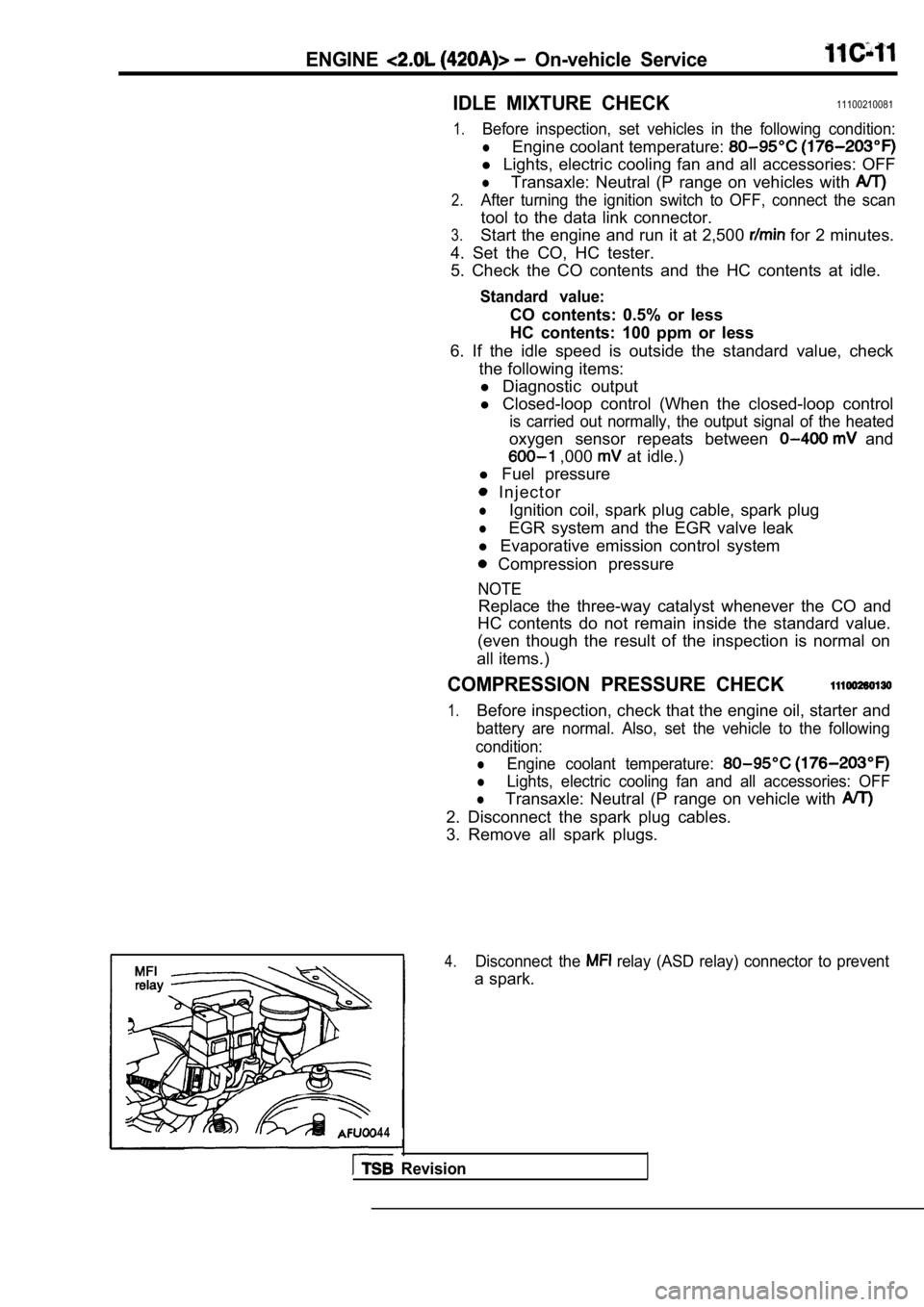
ENGINE On-vehicle Service
IDLE MIXTURE CHECK
11100210081
1.Before inspection, set vehicles in the following co ndition:
lEngine coolant temperature:
l Lights, electric cooling fan and all accessories: O FF
lTransaxle: Neutral (P range on vehicles with
2.After turning the ignition switch to OFF, connect t he scan
tool to the data link connector.
3.Start the engine and run it at 2,500 for 2 minutes.
4. Set the CO, HC tester.
5. Check the CO contents and the HC contents at idl e.
Standard value:
CO contents: 0.5% or less
HC contents: 100 ppm or less
6. If the idle speed is outside the standard value, check
the following items: l Diagnostic output
l Closed-loop control (When the closed-loop control
is carried out normally, the output signal of the h eated
oxygen sensor repeats between and
,000 at idle.)
l Fuel pressure
I n j e c t o r
lIgnition coil, spark plug cable, spark plug
lEGR system and the EGR valve leak
l Evaporative emission control system
Compression pressure
NOTE
Replace the three-way catalyst whenever the CO and
HC contents do not remain inside the standard value .
(even though the result of the inspection is normal on
all items.)
COMPRESSION PRESSURE CHECK
1.Before inspection, check that the engine oil, start er and
battery are normal. Also, set the vehicle to the fo llowing
condition:
lEngine coolant temperature:
lLights, electric cooling fan and all accessories: O FF
lTransaxle: Neutral (P range on vehicle with
2. Disconnect the spark plug cables.
3. Remove all spark plugs.
4.Disconnect the relay (ASD relay) connector to prevent
a spark.
4 4
Revision
Page 182 of 2103
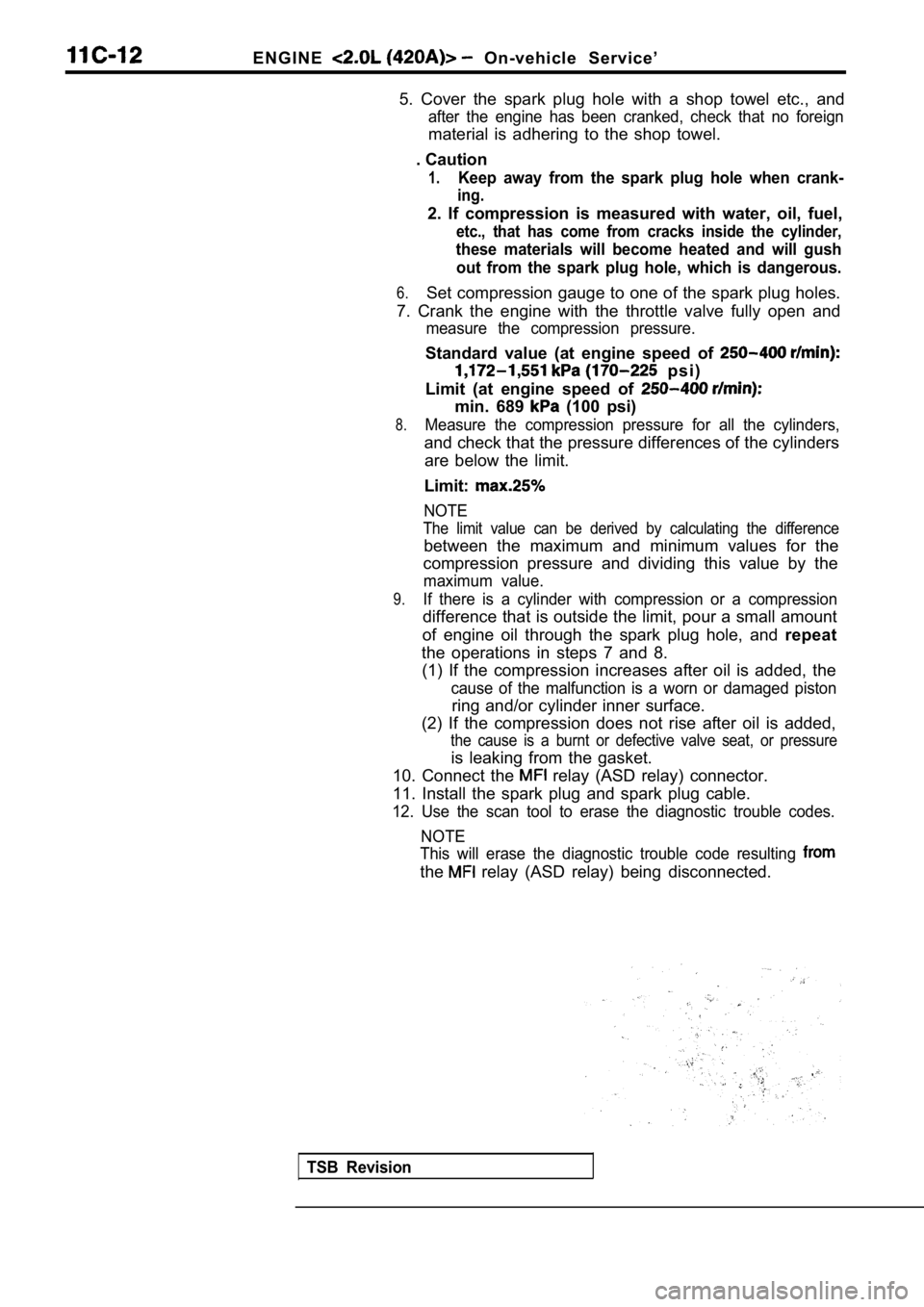
E N G I N E On-vehicle Service’
5. Cover the spark plug hole with a shop towel etc. , and
after the engine has been cranked, check that no foreign
material is adhering to the shop towel.
. Caution
1.Keep away from the spark plug hole when crank-
ing.
2. If compression is measured with water, oil, fuel ,
etc., that has come from cracks inside the cylinder ,
these materials will become heated and will gush
out from the spark plug hole, which is dangerous.
6.Set compression gauge to one of the spark plug hole s.
7. Crank the engine with the throttle valve fully o pen and
measure the compression pressure.
Standard value (at engine speed of
p s i )
Limit (at engine speed of
min. 689 (100 psi)
8.Measure the compression pressure for all the cylind ers,
and check that the pressure differences of the cylinders
are below the limit.
Limit:
NOTE
The limit value can be derived by calculating the d ifference
between the maximum and minimum values for the
compression pressure and dividing this value by the
maximum value.
9.If there is a cylinder with compression or a compre ssion
difference that is outside the limit, pour a small amount
of engine oil through the spark plug hole, and repeat
the operations in steps 7 and 8. (1) If the compression increases after oil is added , the
cause of the malfunction is a worn or damaged pisto n
ring and/or cylinder inner surface.
(2) If the compression does not rise after oil is a dded,
the cause is a burnt or defective valve seat, or pr essure
is leaking from the gasket.
10. Connect the
relay (ASD relay) connector.
11. Install the spark plug and spark plug cable.
12. Use the scan tool to erase the diagnostic troub le codes.
NOTE
This will erase the diagnostic trouble code resulti ng
the relay (ASD relay) being disconnected.
TSB Revision
Page 183 of 2103
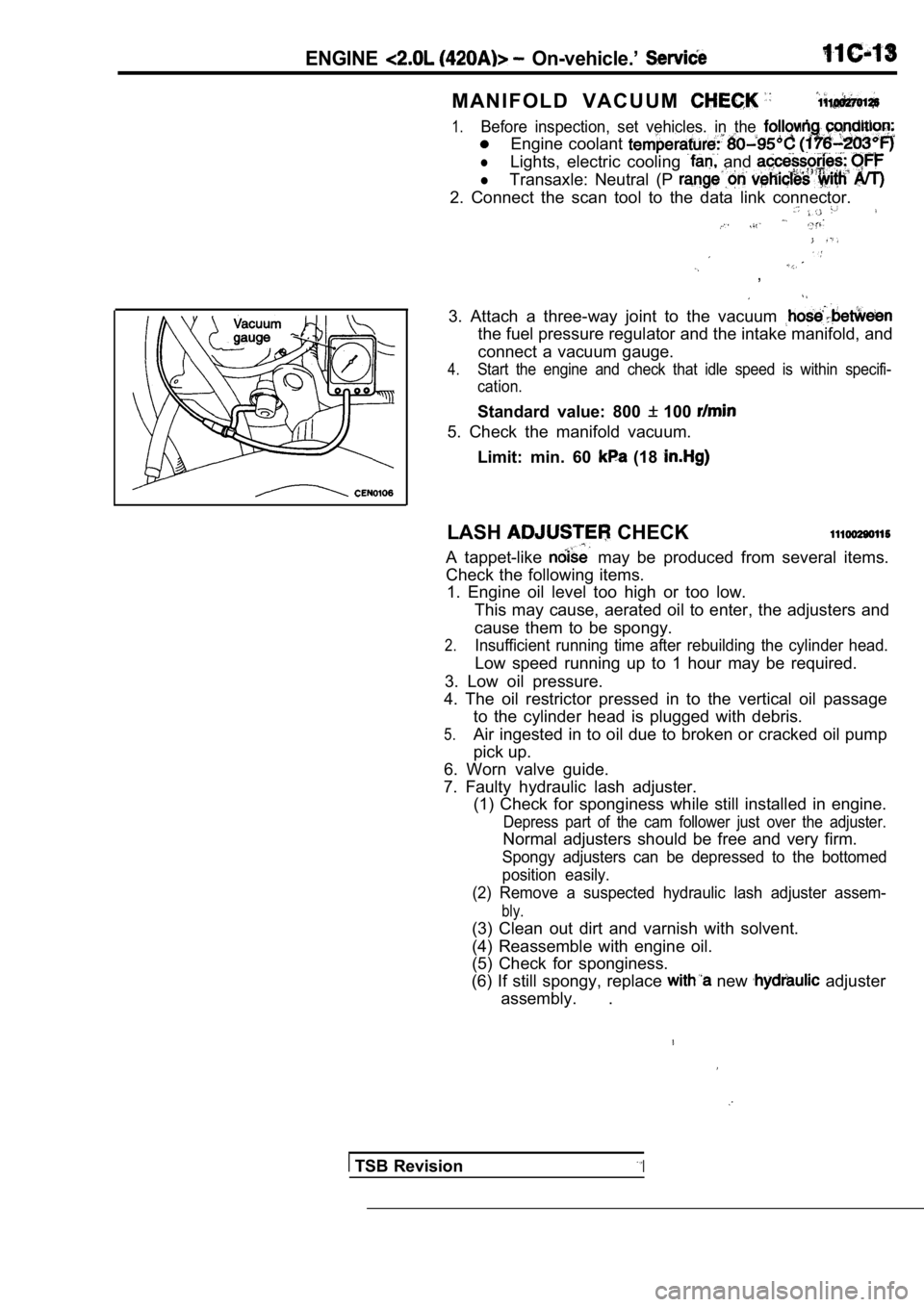
ENGINE On-vehicle.’
M A N I F O L D V A C U U M
1.Before inspection, set vehicles. in the condition:
Engine coolant
lLights, electric cooling and
lTransaxle: Neutral (P
2. Connect the scan tool to the data link connector.
,
3. Attach a three-way joint to the vacuum
the fuel pressure regulator and the intake manifold, and
connect a vacuum gauge.
4.Start the engine and check that idle speed is withi n specifi-
cation.
Standard value: 800 100
5. Check the manifold vacuum.
Limit: min. 60
(18
LASH CHECK
A tappet-like may be produced from several items.
Check the following items. 1. Engine oil level too high or too low.
This may cause, aerated oil to enter, the adjusters and
cause them to be spongy.
2.Insufficient running time after rebuilding the cyli nder head.
Low speed running up to 1 hour may be required.
3. Low oil pressure.
4. The oil restrictor pressed in to the vertical oi l passage
to the cylinder head is plugged with debris.
5.Air ingested in to oil due to broken or cracked oil pump
pick up.
6. Worn valve guide.
7. Faulty hydraulic lash adjuster. (1) Check for sponginess while still installed in e ngine.
Depress part of the cam follower just over the adju ster.
Normal adjusters should be free and very firm.
Spongy adjusters can be depressed to the bottomed
position easily.
(2) Remove a suspected hydraulic lash adjuster asse m-
bly.
(3) Clean out dirt and varnish with solvent.
(4) Reassemble with engine oil.
(5) Check for sponginess.
(6) If still spongy, replace
new adjuster
assembly. .
TSB RevisionI
Page 184 of 2103
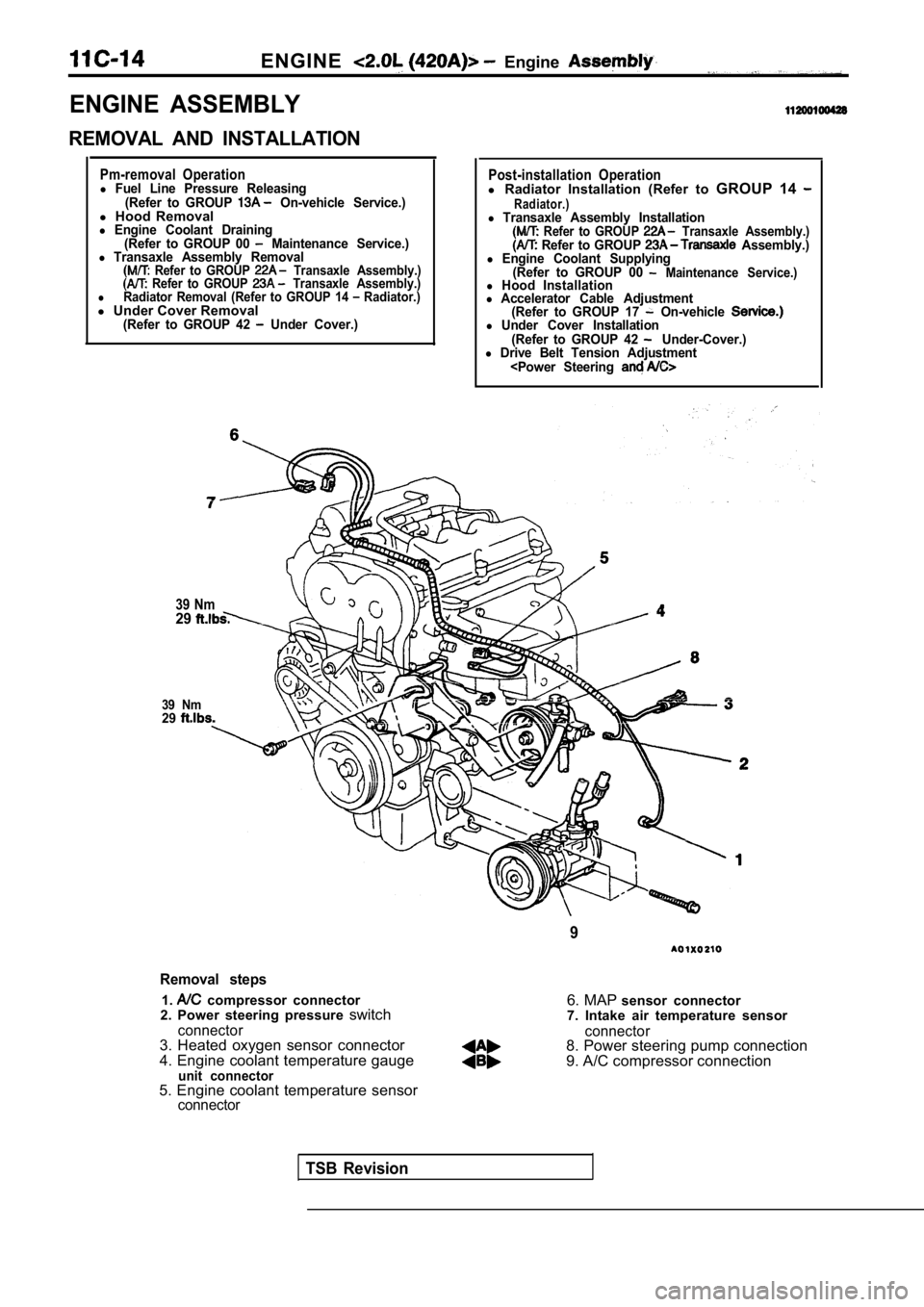
ENGINE Engine
ENGINE ASSEMBLY
REMOVAL AND INSTALLATION
Pm-removal Operationl Fuel Line Pressure Releasing(Refer to GROUP On-vehicle Service.)l Hood Removall Engine Coolant Draining
(Refer to GROUP 00 Maintenance Service.)l Transaxle Assembly Removal Refer to GROUP Transaxle Assembly.) Refer to GROUP Transaxle Assembly.)lRadiator Removal (Refer to GROUP 14 Radiator.)l Under Cover Removal(Refer to GROUP 42 Under Cover.)
39 Nm29
39 Nm29
Post-installation Operationl Radiator Installation (Refer to GROUP 14 Radiator.)l Transaxle Assembly Installation Refer to GROUP Transaxle Assembly.) Refer to GROUP Assembly.)l Engine Coolant Supplying
(Refer to GROUP 00 Maintenance Service.)l Hood Installationl Accelerator Cable Adjustment(Refer to GROUP 17 On-vehicle l Under Cover Installation
(Refer to GROUP 42 Under-Cover.)l Drive Belt Tension Adjustment
Removal steps
1. compressor connector
2. Power steering pressure switch
connector3. Heated oxygen sensor connector
4. Engine coolant temperature gauge
unit connector
6. MAP sensor connector
7. Intake air temperature sensor
connector8. Power steering pump connection
9. A/C compressor connection
5. Engine coolant temperature sensor
connector
TSB Revision
Page 185 of 2103
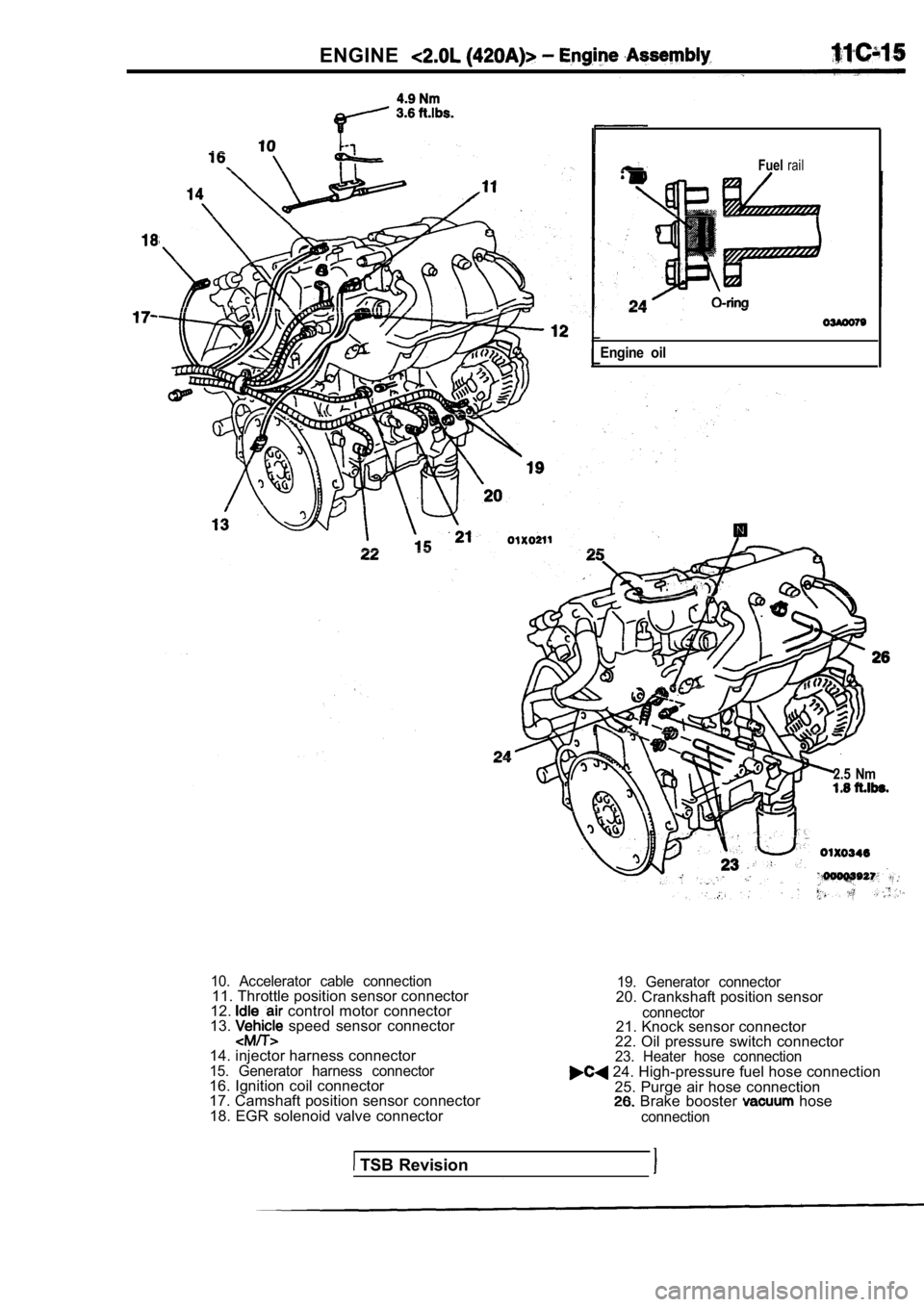
ENGINE
Fuelrail
Engine oil
2.5 Nm
10. Accelerator cable connection11. Throttle position sensor connector
12. control motor connector
13. speed sensor connector
14. injector harness connector
15. Generator harness connector16. Ignition coil connector
17. Camshaft position sensor connector 18. EGR solenoid valve connector
19. Generator connector20. Crankshaft position sensor
connector21. Knock sensor connector
22. Oil pressure switch connector
23. Heater hose connection 24. High-pressure fuel hose connection
25. Purge air hose connection
Brake booster hose
connection
TSB Revision
Page 186 of 2103
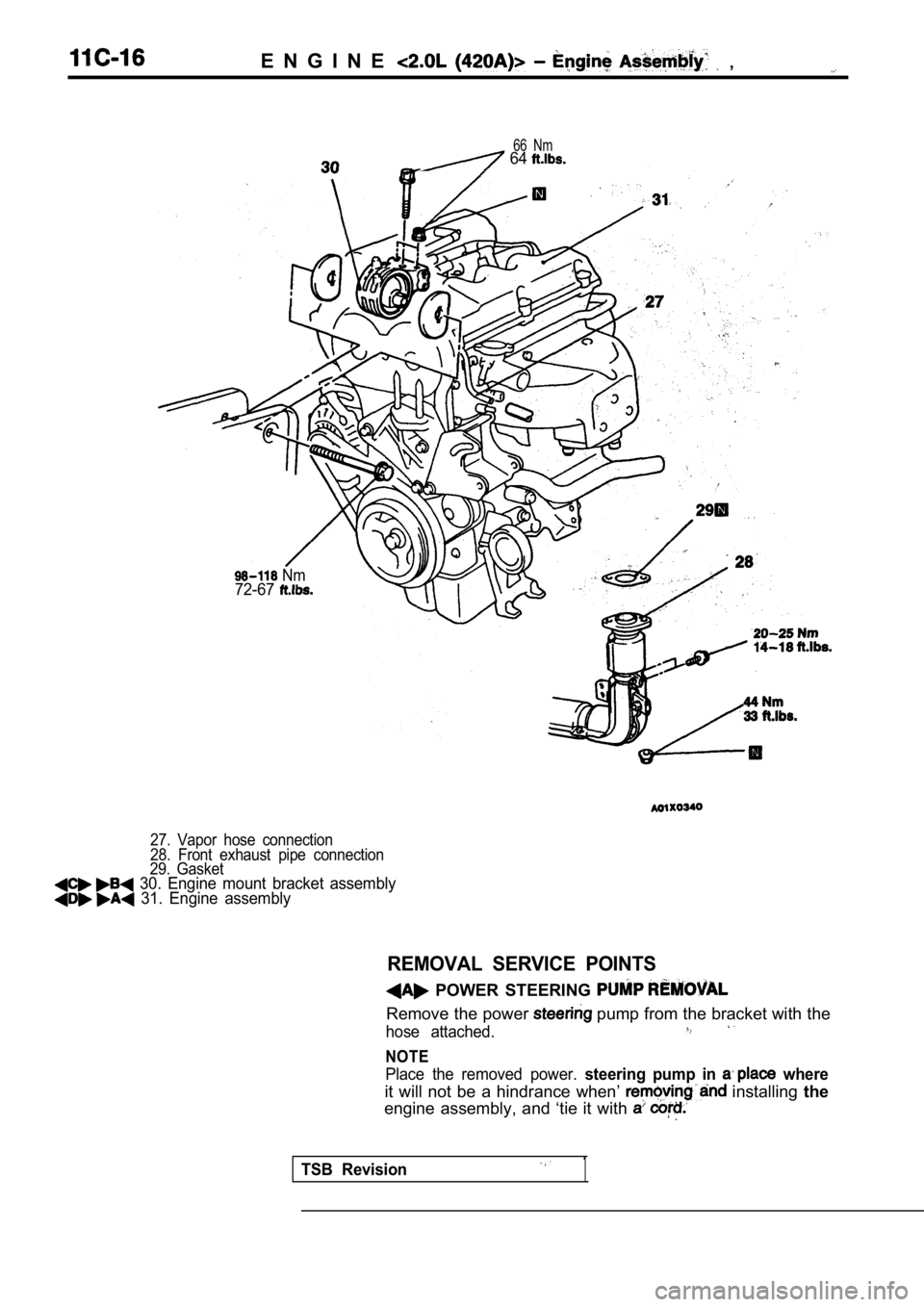
E N G I N E ,
66 Nm 64
Nm72-67
27. Vapor hose connection
28. Front exhaust pipe connection
29. Gasket
30. Engine mount bracket assembly 31. Engine assembly
REMOVAL SERVICE POINTS
POWER STEERING
Remove the power pump from the bracket with the
hose attached.
NOTE
Place the removed power. steering pump in where
it will not be a hindrance when’ installing the
engine assembly, and ‘tie it with
TSB Revision1
Page 187 of 2103
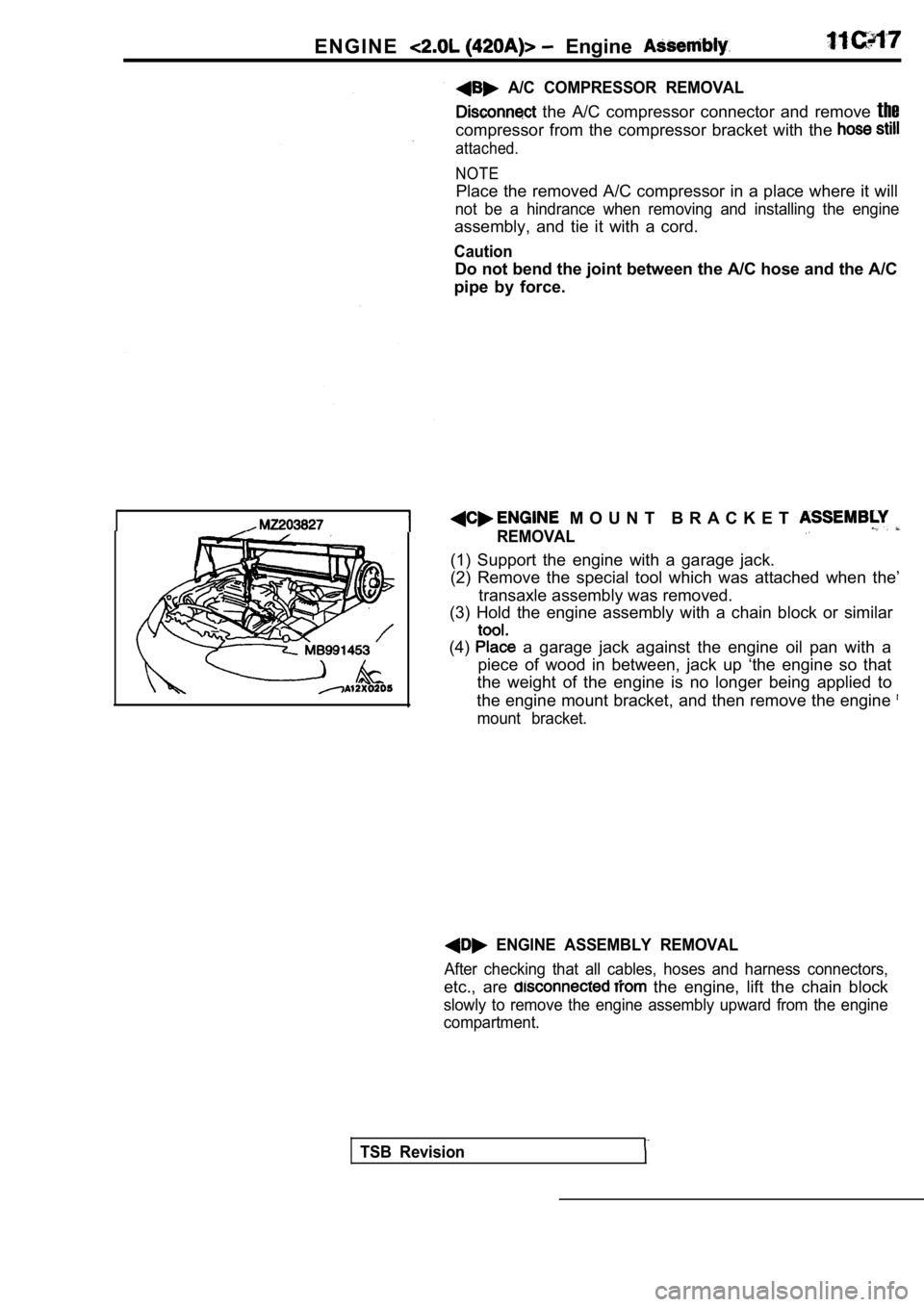
E N G I N E Engine
A/C COMPRESSOR REMOVAL
the A/C compressor connector and remove the
compressor from the compressor bracket with the
attached.
NOTE
Place the removed A/C compressor in a place where i t will
not be a hindrance when removing and installing the engine
assembly, and tie it with a cord.
Caution
Do not bend the joint between the A/C hose and the A/C
pipe by force.
M O U N T B R A C K E T
REMOVAL
(1) Support the engine with a garage jack.
(2) Remove the special tool which was attached when the’
transaxle assembly was removed.
(3) Hold the engine assembly with a chain block or similar
(4) a garage jack against the engine oil pan with a
piece of wood in between, jack up ‘the engine so th at
the weight of the engine is no longer being applied to
the engine mount bracket, and then remove the engin e
mount bracket.
ENGINE ASSEMBLY REMOVAL
After checking that all cables, hoses and harness connectors,. ..etc., are the engine, lift the chain block
slowly to remove the engine assembly upward from th e engine
compartment.
TSB Revision
Page 188 of 2103
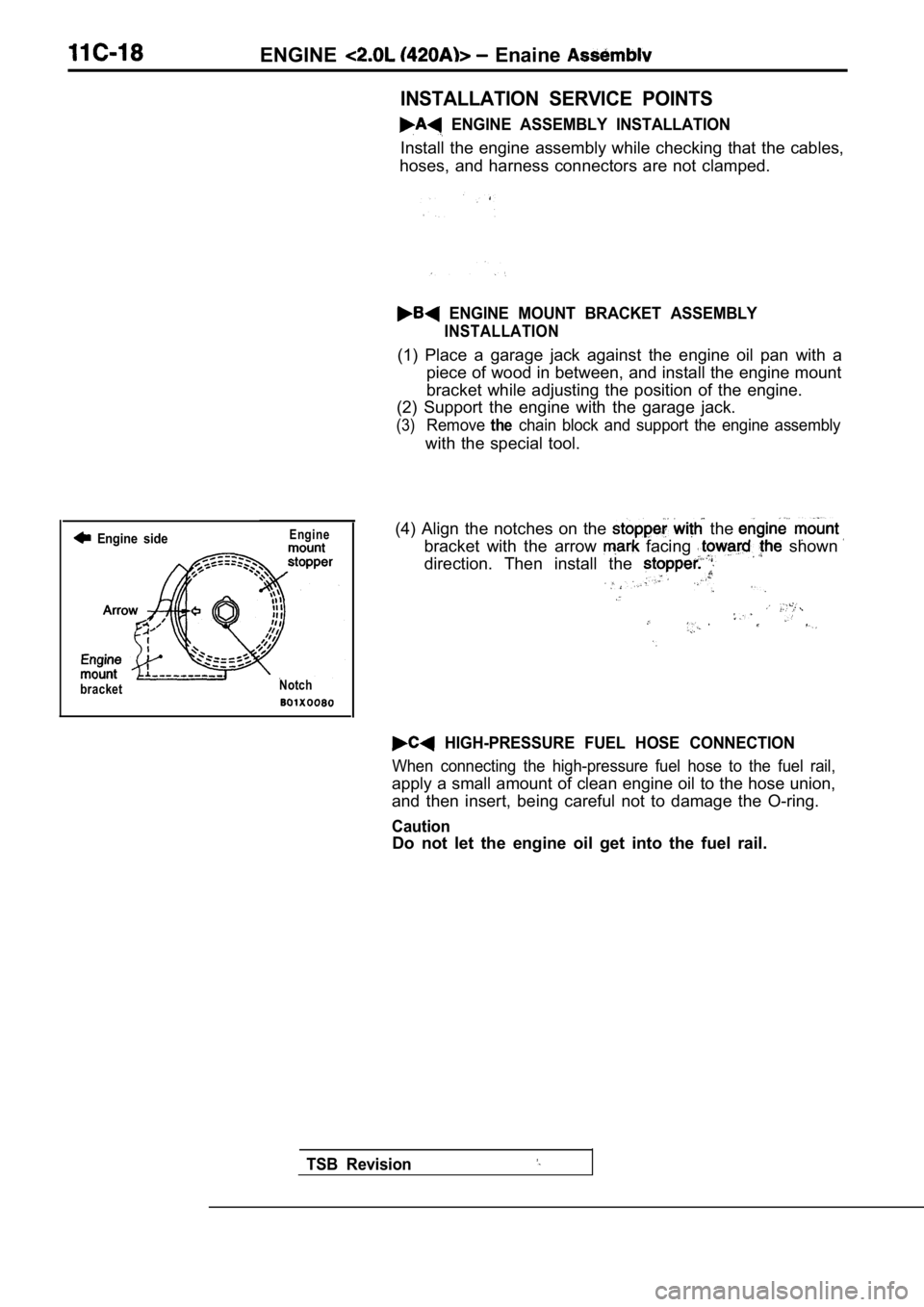
ENGINE Enaine
Engine side
bracketEngine
Notch
INSTALLATION SERVICE POINTS
ENGINE ASSEMBLY INSTALLATION
Install the engine assembly while checking that the cables,
hoses, and harness connectors are not clamped.
ENGINE MOUNT BRACKET ASSEMBLY
INSTALLATION
(1) Place a garage jack against the engine oil pan with a
piece of wood in between, and install the engine mo unt
bracket while adjusting the position of the engine.
(2) Support the engine with the garage jack.
(3)Removethechain block and support the engine assembly
with the special tool.
(4) Align the notches on the
the
bracket with the arrow facing shown
direction. Then install the
HIGH-PRESSURE FUEL HOSE CONNECTION
When connecting the high-pressure fuel hose to the fuel rail,
apply a small amount of clean engine oil to the hose union,
and then insert, being careful not to damage the O- ring.
Caution
Do not let the engine oil get into the fuel rail.
TSB Revision
Page 189 of 2103
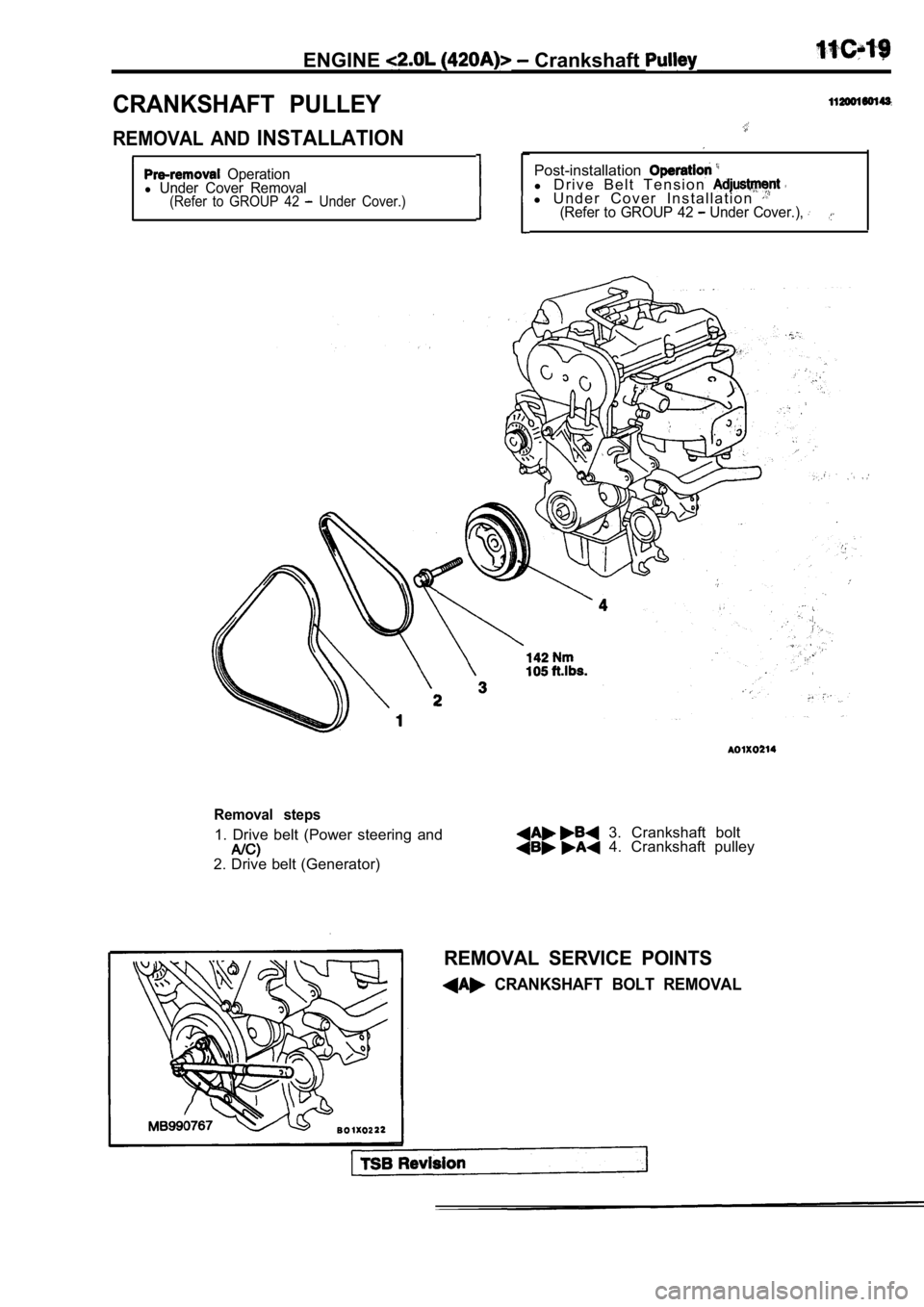
ENGINE Crankshaft
CRANKSHAFT PULLEY
REMOVAL AND INSTALLATION
Operationl Under Cover Removal(Refer to GROUP 42 Under Cover.)
Post-installationl D r i v e B e l t T e n s i o n l U n d e r C o v e r I n s t a l l a t i o n (Refer to GROUP 42 Under Cover.),
Removal steps
1. Drive belt (Power steering and
2. Drive belt (Generator)
3. Crankshaft bolt 4. Crankshaft pulley
REMOVAL SERVICE POINTS
CRANKSHAFT BOLT REMOVAL
Page 190 of 2103
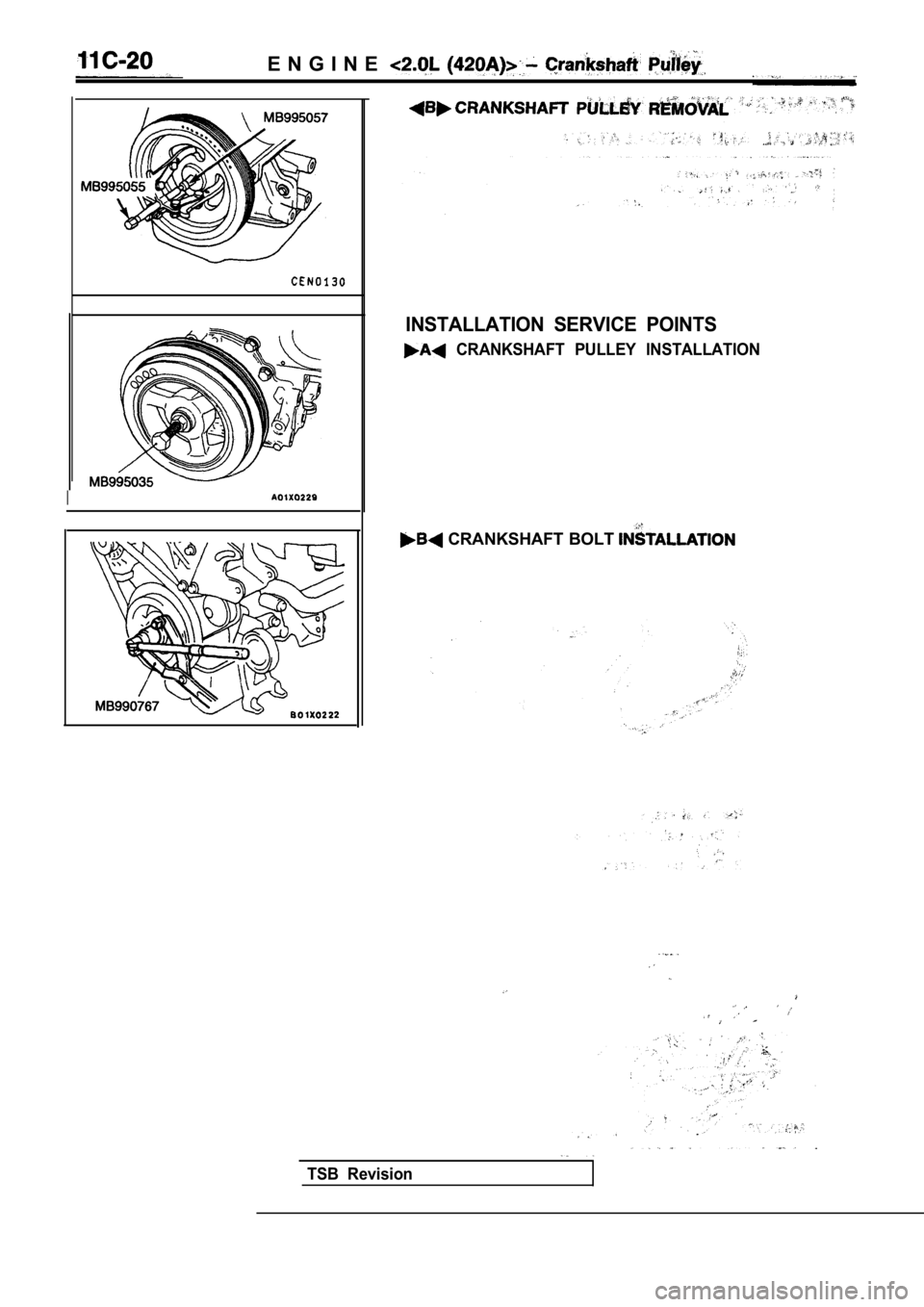
E N G I N E
I
INSTALLATION SERVICE POINTS
CRANKSHAFT PULLEY INSTALLATION
CRANKSHAFT BOLT
TSB Revision