OPEL GT-R 1973 Workshop Manual
Manufacturer: OPEL, Model Year: 1973, Model line: GT-R, Model: OPEL GT-R 1973Pages: 625, PDF Size: 17.22 MB
Page 51 of 625
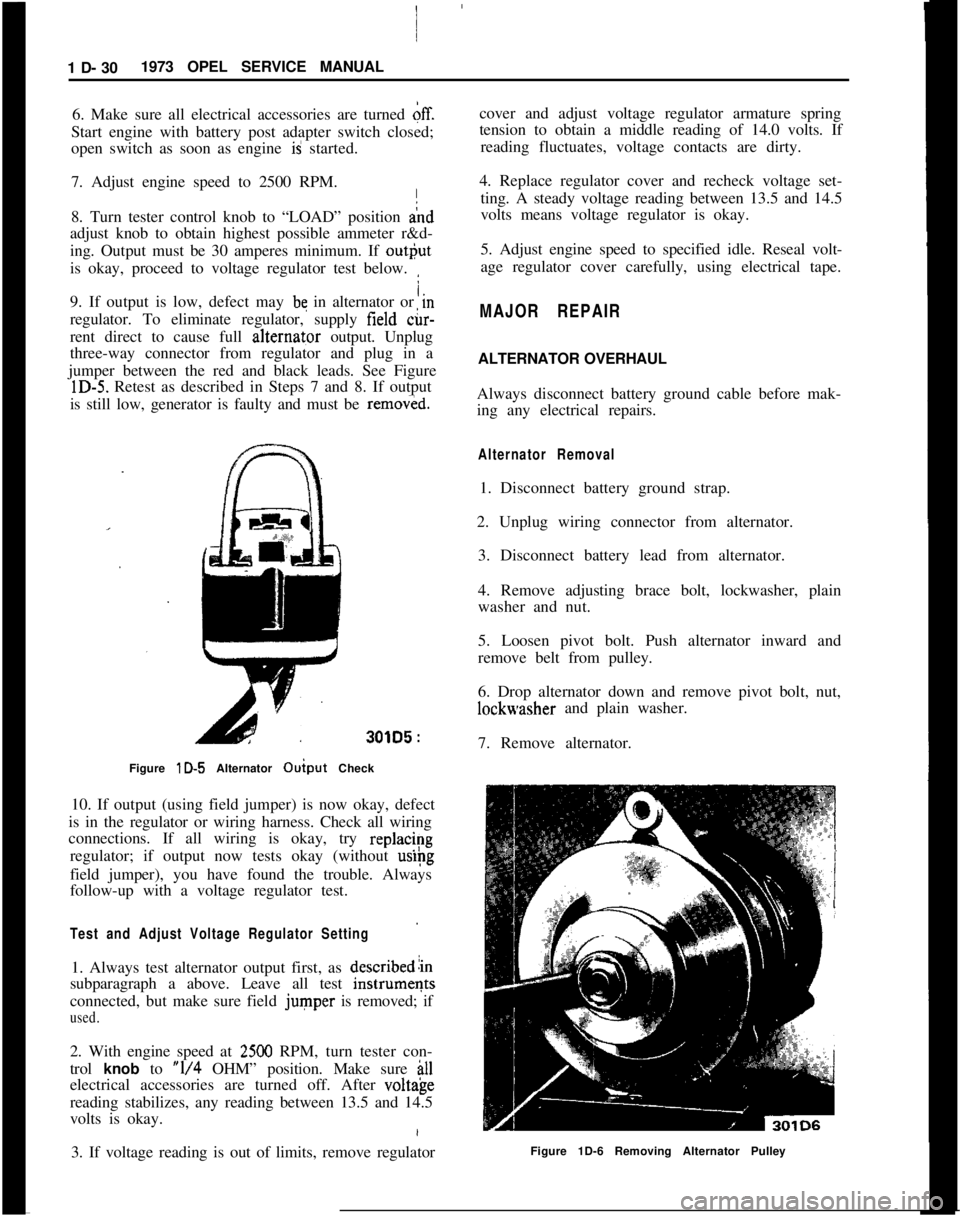
i
1 D- 301973 OPEL SERVICE MANUAL
6. Make sure all electrical accessories are turned (lff.
Start engine with battery post adapter switch closed;
open switch as soon as engine
iS: started.
7. Adjust engine speed to 2500 RPM.
8. Turn tester control knob to “LOAD” position
aid
adjust knob to obtain highest possible ammeter r&d-
ing. Output must be 30 amperes minimum. If
outcut
is okay, proceed to voltage regulator test below. j
/.9. If output is low, defect may be in alternator or m
regulator. To eliminate regulator, supply field &-
rent direct to cause full alternat,or output. Unplug
three-way connector from regulator and plug in a
jumper between the red and black leads. See Figure
lD-5. Retest as described in Steps 7 and 8. If output
is still low, generator is faulty and must be
remov&d.
301D5 :
Figure lD-5 Alternator Ouiput Check I
10. If output (using field jumper) is now okay, defect
is in the regulator or wiring harness. Check all wiring
connections. If all wiring is okay, try
replac/~g
regulator; if output now tests okay (without
uslpg
field jumper), you have found the trouble. Always
follow-up with a voltage regulator test.
Test and Adjust Voltage Regulator Setting
1. Always test alternator output first, as describedlin
subparagraph a above. Leave all test
instrumeqts
connected, but make sure field
jumper is removed; if
used.
2. With engine speed at 2500 RPM, turn tester con-
trol
knob to “l/4 OHM” position. Make sure ill
electrical accessories are turned off. After volt&e
reading stabilizes, any reading between 13.5 and 14.5
volts is okay.
3. If voltage reading is out of limits, remove regulator cover and adjust voltage regulator armature spring
tension to obtain a middle reading of 14.0 volts. If
reading fluctuates, voltage contacts are dirty.
4. Replace regulator cover and recheck voltage set- ting. A steady voltage reading between 13.5 and 14.5
volts means voltage regulator is okay.
5. Adjust engine speed to specified idle. Reseal volt-
age regulator cover carefully, using electrical tape.
MAJOR REPAIR
ALTERNATOR OVERHAUL
Always disconnect battery ground cable before mak-
ing any electrical repairs.
Alternator Removal
1. Disconnect battery ground strap.
2. Unplug wiring connector from alternator. 3. Disconnect battery lead from alternator.
4. Remove adjusting brace bolt, lockwasher, plain
washer and nut.
5. Loosen pivot bolt. Push alternator inward and
remove belt from pulley.
6. Drop alternator down and remove pivot bolt, nut,
lockwasher and plain washer.
7. Remove alternator.
Figure 1D-6 Removing Alternator Pulley
Page 52 of 625
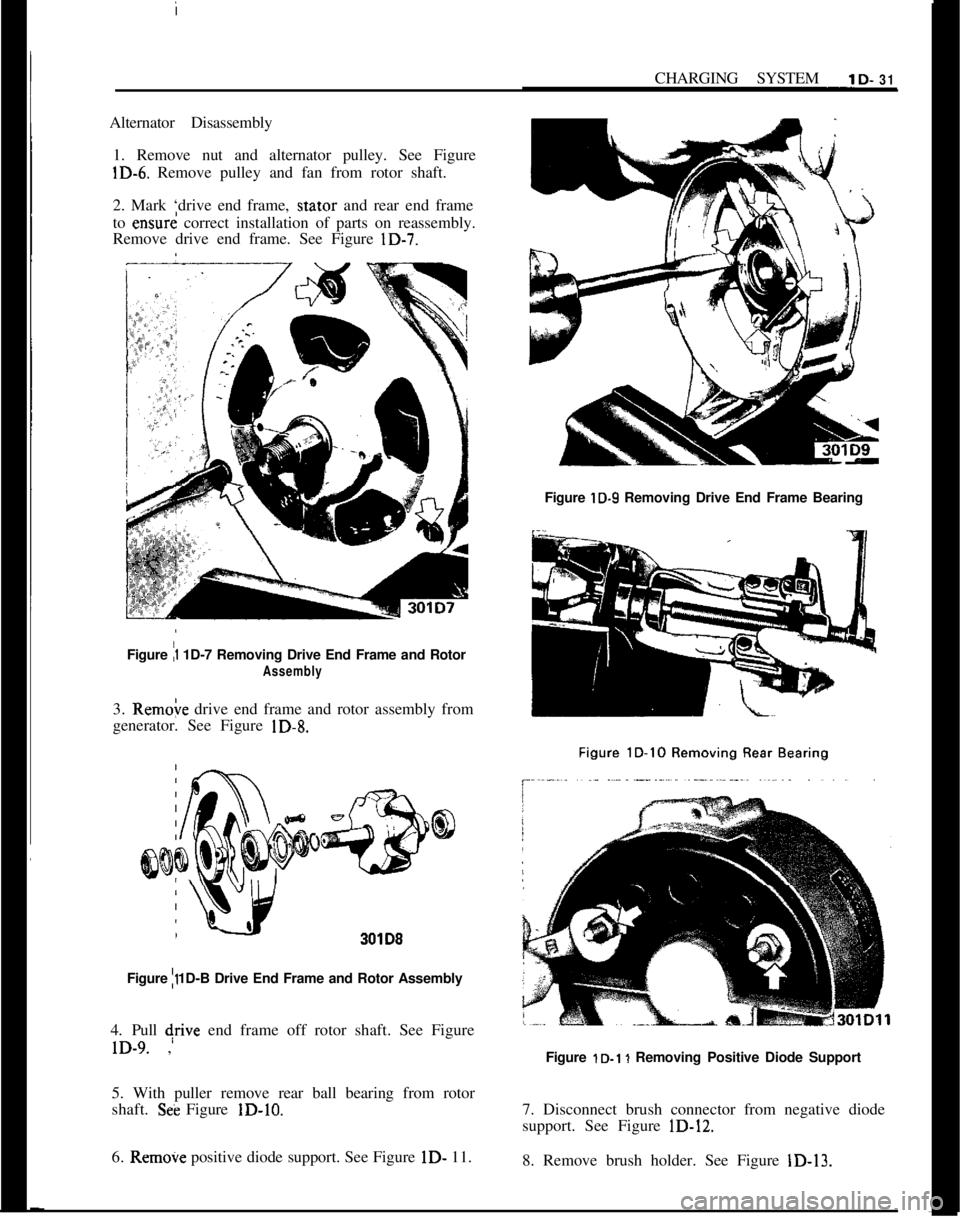
CHARGING SYSTEMlD- 31
Alternator Disassembly1. Remove nut and alternator pulley. See Figure
lD-6. Remove pulley and fan from rotor shaft.
2. Mark ‘drive end frame,
stator and rear end frame
to
ensurd correct installation of parts on reassembly.
Remove drive end frame. See Figure
lD-7.
Figure lD-9 Removing Drive End Frame Bearing
Figure
/l 1D-7 Removing Drive End Frame and Rotor
Assembly
3. Remoie drive end frame and rotor assembly from
generator. See Figure
lD-8.
/
301D8
Figure I11D-B Drive End Frame and Rotor Assembly
4. Pull +ve end frame off rotor shaft. See Figure
lD-9. ,
5. With puller remove rear ball bearing from rotor
shaft.
S& Figure lD-10.
6.
Remove positive diode support. See Figure lD- 11.
Figure 1D-l 1 Removing Positive Diode Support
7. Disconnect brush connector from negative diode
support. See Figure
lD-12.
8. Remove brush holder. See Figure
lD-13.
Page 53 of 625
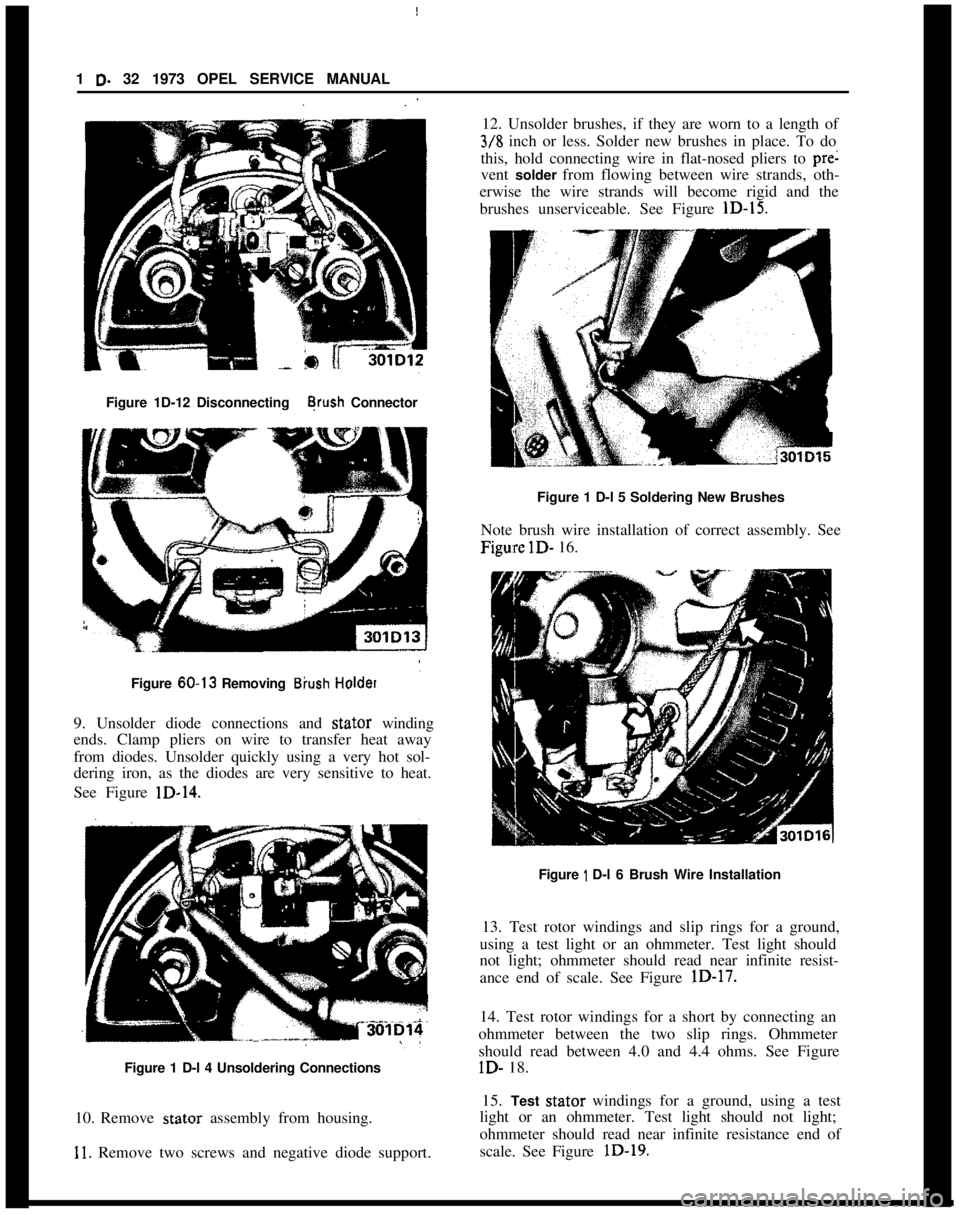
1 D- 32 1973 OPEL SERVICE MANUAL
12. Unsolder brushes, if they are worn to a length of
3/8 inch or less. Solder new brushes in place. To do
this, hold connecting wire in flat-nosed pliers to
pre:
vent
solder from flowing between wire strands, oth-
erwise the wire strands will become rigid and the
brushes unserviceable. See Figure
lD-15.
Figure 1D-12 Disconnecting Brush Connector
Figure 1 D-l 5 Soldering New Brushes
Note brush wire installation of correct assembly. See
Figwe lD- 16.
Figure 60.13 Removing Biush Holder
9. Unsolder diode connections and stator winding
ends. Clamp pliers on wire to transfer heat away
from diodes. Unsolder quickly using a very hot sol-
dering iron, as the diodes are very sensitive to heat.
See Figure
lD-14.
Figure 1 D-l 6 Brush Wire Installation
Figure 1 D-l 4 Unsoldering Connections
10. Remove stator assembly from housing.
Il. Remove two screws and negative diode support. 13. Test rotor windings and slip rings for a ground,
using a test light or an ohmmeter. Test light should
not light; ohmmeter should read near infinite resist-
ance end of scale. See Figure
lD-17.
14. Test rotor windings for a short by connecting an
ohmmeter between the two slip rings. Ohmmeter
should read between 4.0 and 4.4 ohms. See Figure
lD- 18.
15.
Test stator windings for a ground, using a test
light or an ohmmeter. Test light should not light;
ohmmeter should read near infinite resistance end of
scale. See Figure
lD-19.
Page 54 of 625
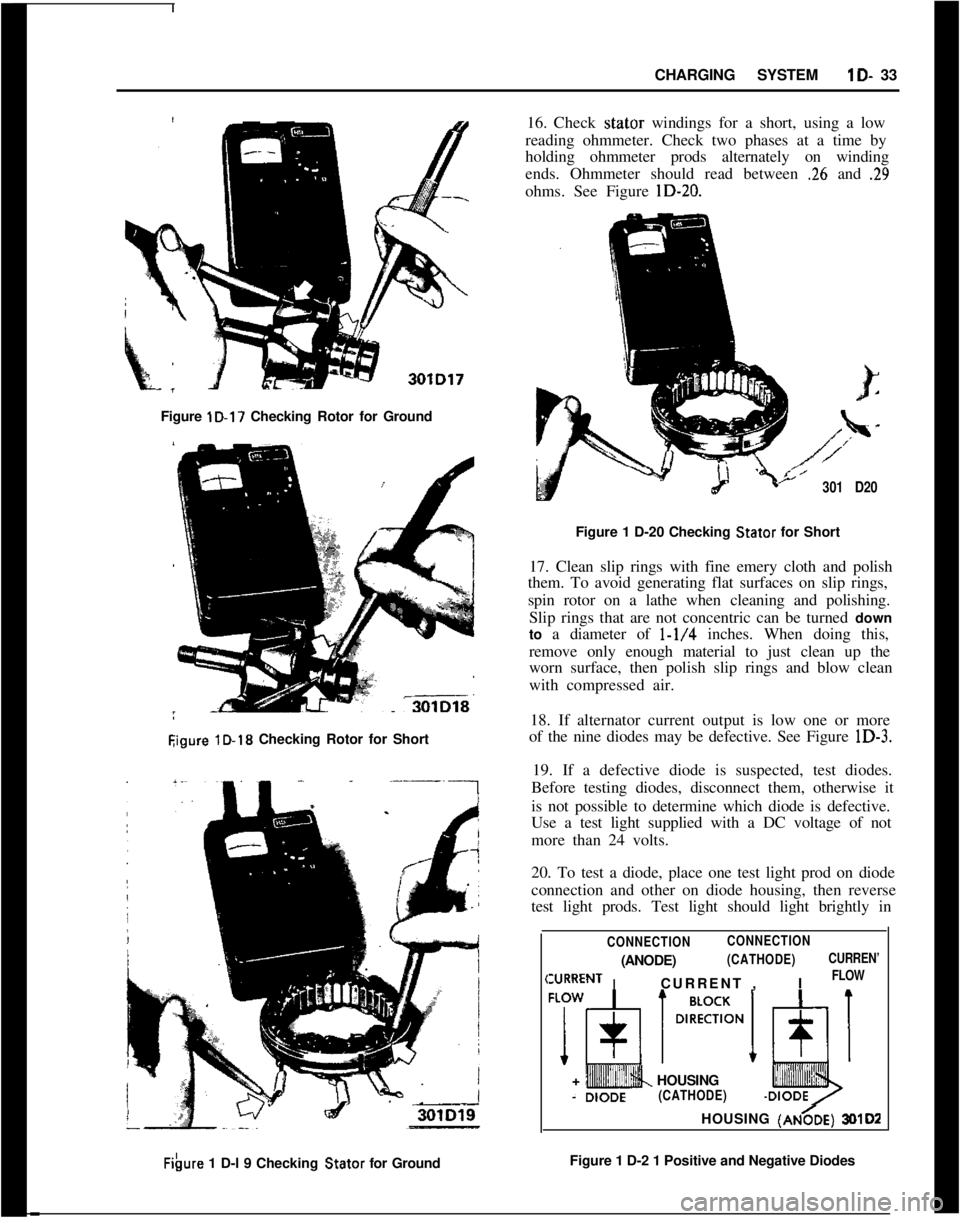
CHARGING SYSTEMlD- 33
Figure lD-17 Checking Rotor for Ground
Eigure lD-18 Checking Rotor for ShortFibwe 1 D-l 9 Checking Stator for Ground16. Check stator windings for a short, using a low
reading ohmmeter. Check two phases at a time by
holding ohmmeter prods alternately on winding
ends. Ohmmeter should read between
.26 and .29ohms. See Figure lD-20.
301 D20Figure 1 D-20 Checking Stator for Short
17. Clean slip rings with fine emery cloth and polish
them. To avoid generating flat surfaces on slip rings,
spin rotor on a lathe when cleaning and polishing.
Slip rings that are not concentric can be turned down
to a diameter of
l-1/4 inches. When doing this,
remove only enough material to just clean up the
worn surface, then polish slip rings and blow clean
with compressed air.
18. If alternator current output is low one or more
of the nine diodes may be defective. See Figure lD-3.
19. If a defective diode is suspected, test diodes.
Before testing diodes, disconnect them, otherwise it
is not possible to determine which diode is defective.
Use a test light supplied with a DC voltage of not
more than 24 volts.
20. To test a diode, place one test light prod on diode
connection and other on diode housing, then reverse
test light prods. Test light should light brightly in
,
CONNECTIONCONNECTION
I(ANODE)
(CATHODE)
IURRENTCURRENT ,I
CURREN’
FLOW+
+ HOUSING(CATHODE)HOUSING
(AN&E) 3lMD2Figure 1 D-2 1 Positive and Negative Diodes
Page 55 of 625
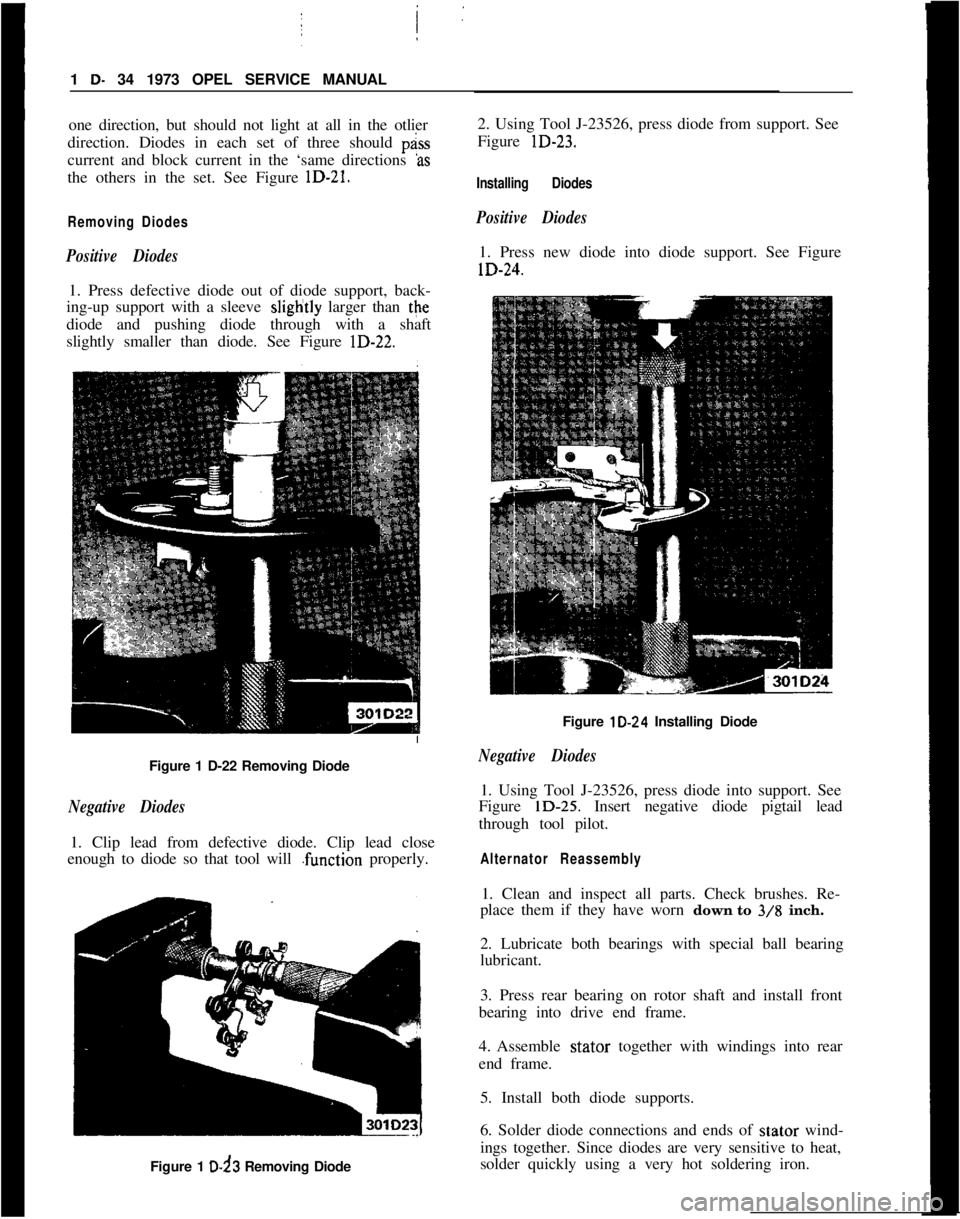
1 D- 34 1973 OPEL SERVICE MANUAL!
I
one direction, but should not light at all in the otlier
direction. Diodes in each set of three should p&s
current and block current in the ‘same directions
Asthe others in the set. See Figure lD-21.
Removing Diodes/
Positive Diodes1. Press defective diode out of diode support, back-
ing-up support with a sleeve sliglitly larger than the
diode and pushing diode through with a shaft
slightly smaller than diode. See Figure lD-22.;
Figure 1 D-22 Removing Diode
Negative Diodes1. Clip lead from defective diode. Clip lead close
enough to diode so that tool will .function properly.
Figure 1 D-d3 Removing Diode2. Using Tool J-23526, press diode from support. See
Figure lD-23.
Installing Diodes
Positive Diodes1. Press new diode into diode support. See FigurelD-24.
Figure lD-24 Installing Diode
Negative Diodes1. Using Tool J-23526, press diode into support. See
Figure lD-25. Insert negative diode pigtail lead
through tool pilot.
Alternator Reassembly1. Clean and inspect all parts. Check brushes. Re-
place them if they have worn down to
3/8 inch.
2. Lubricate both bearings with special ball bearing
lubricant.
3. Press rear bearing on rotor shaft and install front
bearing into drive end frame.
4. Assemble stator together with windings into rear
end frame.
5. Install both diode supports.
6. Solder diode connections and ends of stator wind-
ings together. Since diodes are very sensitive to heat,
solder quickly using a very hot soldering iron.
Page 56 of 625
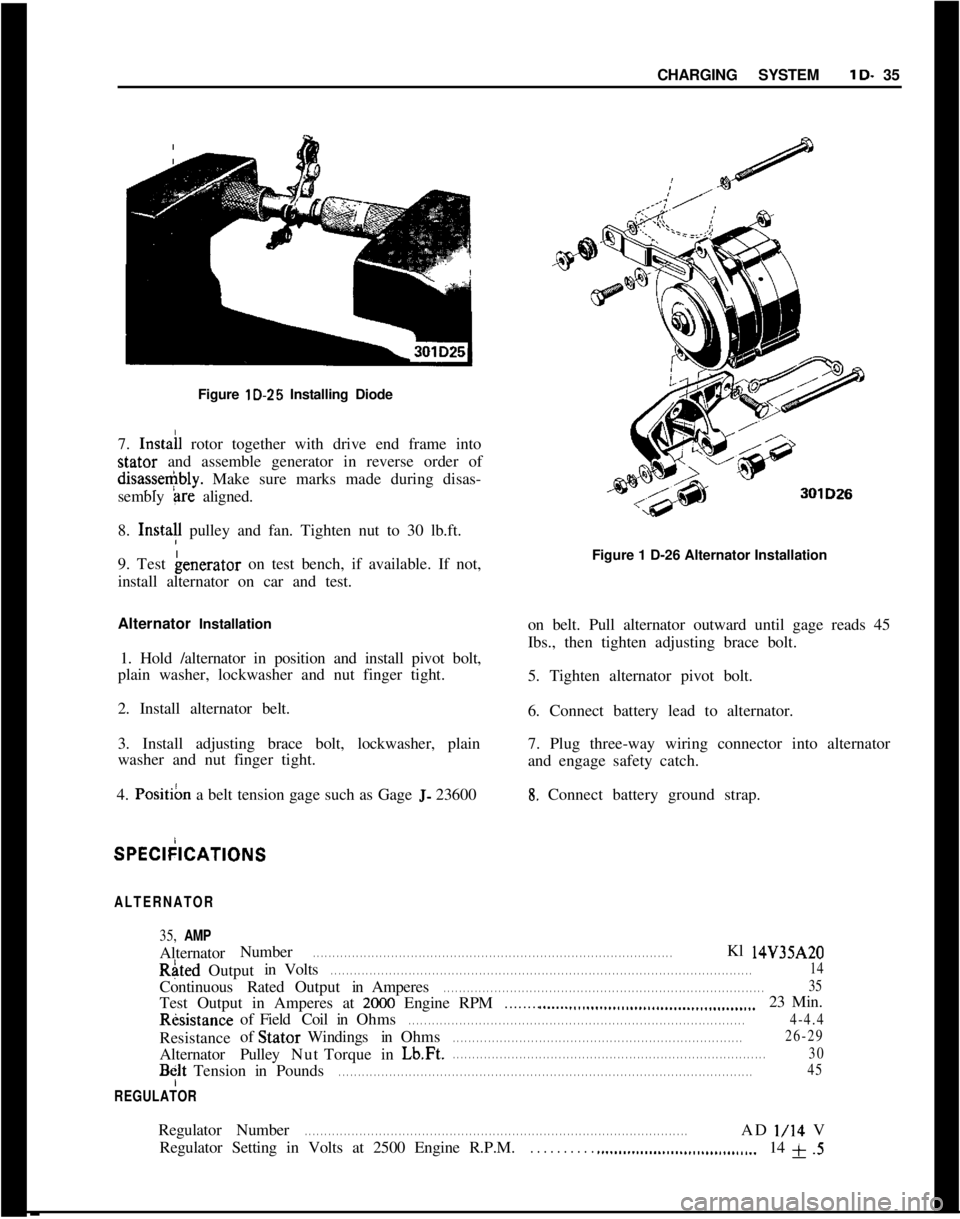
CHARGING SYSTEMlD- 35
’Figure lD-25 Installing Diode
I
7. Instail rotor together with drive end frame intostator and assemble generator in reverse order ofdisasse+bly. Make sure marks made during disas-
sembly
+-ire aligned.
8. Insta!l pulley and fan. Tighten nut to 30 lb.ft.
9. Test benerator on test bench, if available. If not,
install alternator on car and test.
Alternator Installation
1. Hold /alternator in position and install pivot bolt,
plain washer, lockwasher and nut finger tight.
2. Install alternator belt.
3. Install adjusting brace bolt, lockwasher, plain
washer and nut finger tight.
4.
Posit& a belt tension gage such as Gage J- 23600Figure 1 D-26 Alternator Installation
on belt. Pull alternator outward until gage reads 45
Ibs., then tighten adjusting brace bolt.
5. Tighten alternator pivot bolt.
6. Connect battery lead to alternator.
7. Plug three-way wiring connector into alternator
and engage safety catch.8. Connect battery ground strap.SPECkICATIONS
ALTERNATOR
35, AMPAlternatorNumberRated
. . . . . . . . . . . . . . . . . . . . . . . . . . . . . . . . . . . . . . . . . . . . . . . . . . . . . . . . . . . . . . . . . . . . . . . . . . . . . . . . . . . . . . . . . . . .Kl 14V35AZOOutputinVolts
. . . . . . . . . . . . . . . . . . . . . . . . . . . . . . . . . . . . . . . . . . . . . . . . . . . . . . . . . . . . . . . . . . . . . . . . . . . . . . . . . . . . . . . . . . . . . . . . . . . . . . . . . . . .14ContinuousRatedOutputinAmperes
. . . . . . . . . . . . . . . . . . . . . . . . . . . . . . . . . . . . . . . . . . . . . . . . . . . . . . . . . . . . . . . . . . . . . . . . . . . . . . . . . .35Test Output in Amperes at
2000 Engine RPM. . . . . . . . ..__.._...........................................23 Min.RksistanceofFieldCoilinOhms
. . . . . . . . . . . . . . . . . . . . . . . . . . . . . . . . . . . . . . . . . . . . . . . . . . . . . . . . . . . . . . . . . . . . . . . . . . . . . . . . . . . . . .4-4.4Resistanceof StatorWindingsinOhms
. . . . . . . . . . . . . . . . . . . . . . . . . . . . . . . . . . . . . . . . . . . . . . . . . . . . . . . . . . . . . . . . . . . . . . . . . .26-29AlternatorPulleyNutTorqueinLb.Ft.
. . . . . . . . . . . . . . . . . . . . . . . . . . . . . . . . . . . . . . . . . . . . . . . . . . . . . . . . . . . . . . . . . . . . . . . . . . . . . . . .30
BfltTensioninPounds. . . . . . . . . . . . . . . . . . . . . . . . . . . . . . . . . . . . . . . . . . . . . . . . . . . . . . . . . . . . . . . . . . . . . . . . . . . . . . . . . . . . . . . . . . . . . . . . . . . . . . . . . .45
REGULATORRegulatorNumber
. . . . . . . . . . . . . . . . . . . . . . . . . . . . . . . . . . . . . . . . . . . . . . . . . . . . . . . . . . . . . . . . . . . . . . . . . . . . . . . . . . . . . . . . . . . . . . . . . .ADl/14V
Regulator Setting in Volts at 2500 Engine R.P.M.
. . . . . . . . . . ..___................................14 f .5
Page 57 of 625
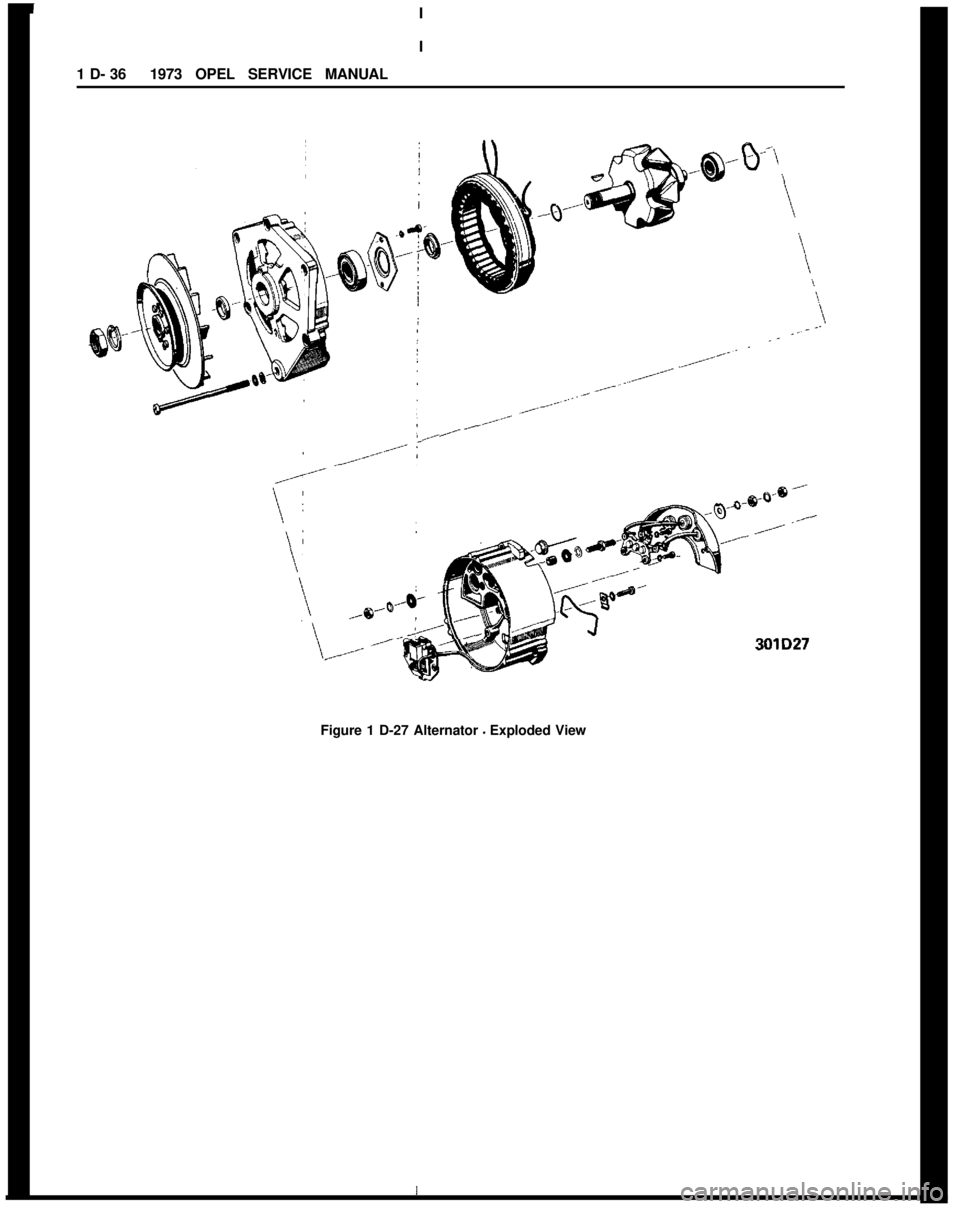
I
;
I
1 D- 361973 OPEL SERVICE MANUALI‘\
Figure 1 D-27 Alternator - Exploded View301D27
Page 58 of 625
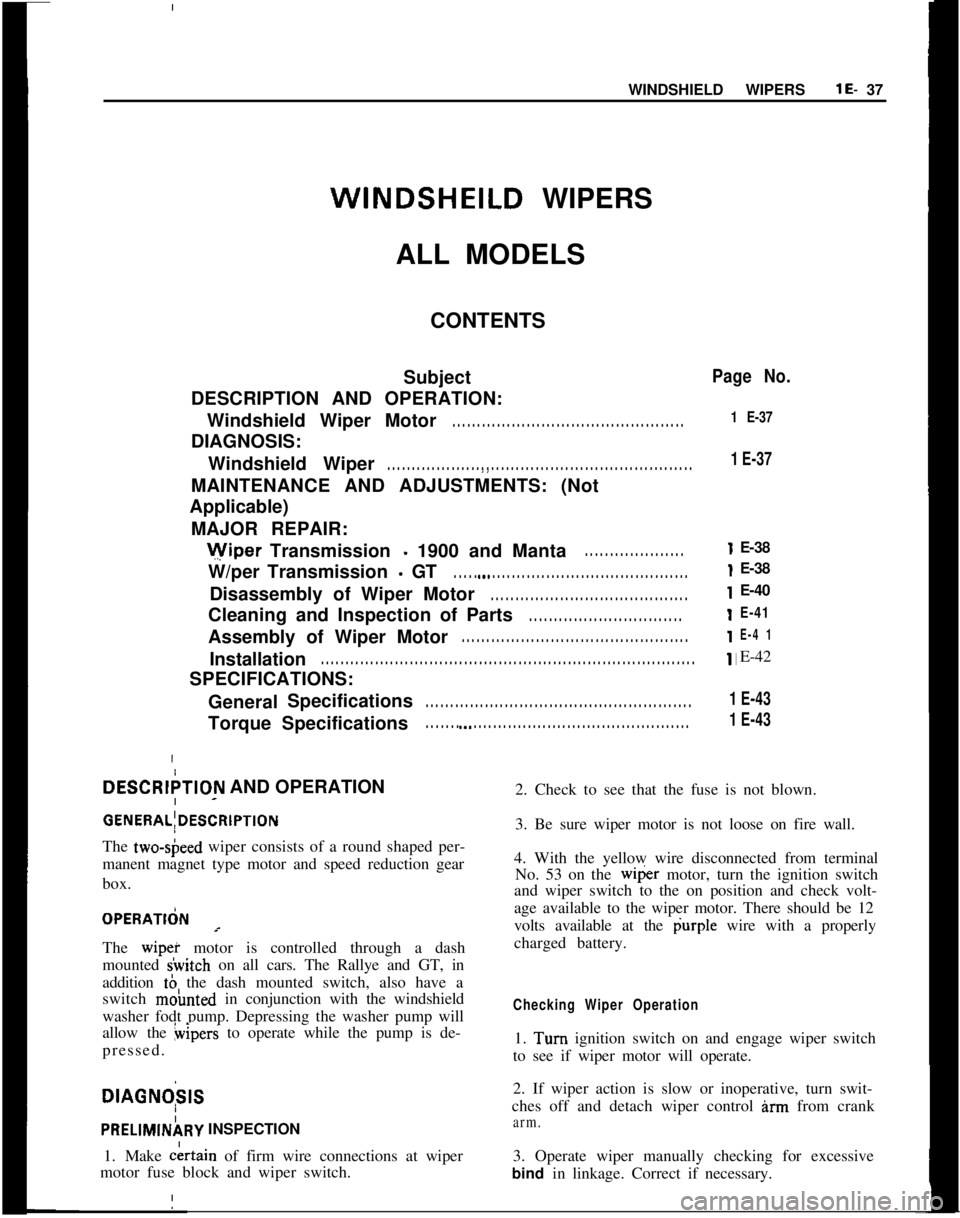
WINDSHIELD WIPERSlE- 37WINDSHEILD WIPERS
ALL MODELS
CONTENTS
Subject
DESCRIPTION AND OPERATION:
Windshield Wiper Motor. . . . . . . . . . . . . . . . . . . . . . . . . . . . . . . . . . . . . . . . . . . . . . .DIAGNOSIS:
Windshield Wiper
. . . . . . . . . . . . . . . . . . . , , . . . . . . . . . . . . . . . . . . . . . . . . . . . . . . . . . . . . . . . . .MAINTENANCE AND ADJUSTMENTS: (Not
Applicable)
MAJOR REPAIR:Wiper Transmission
- 1900 and Manta. . . . . . . . . . . . . . . . . . . .W/per Transmission
- GT. . . . . a.* . . . . . . . . . . . . . . . . . . . . . . . . . . . . . . . . . . . . . . . .Disassembly of Wiper Motor
. . . . . . . . . . . . . . . . . . . . . . . . . . . . . . . . . . . . . . . .Cleaning and Inspection of Parts
. . . . . . . . . . . . . . . . . . . . . . . . . . . . . . .Assembly of Wiper Motor
. . . . . . . . . . . . . . . . . . . . . . . . . . . . . . . . . . . . . . . . . . . . . .Installation
. . . . . . . . . . . . . . . . . . . . . . . . . . . . . . . . . . . . . . . . . . . . . . . . . . . . . . . . . . . . . . . . . . . . . . . . . . . .SPECIFICATIONS:
GeneralSpecifications
. . . . . . . . . . . . . . . . . . . . . . . . . . . . . . . . . . . . . . . . . . . . . . . . . . . . . .Torque Specifications
. . . . . . . a.. . . . . . . . . . . . . . . . . . . . . . . . . . . . . . . . . . . . . . . . . . . . .
DESCRIPTIOfV AND OPERATION
GENERAL;DESCRlPTlDNThe two-sbeed wiper consists of a round shaped per-
manent magnet type motor and speed reduction gear
box. IOPERATldN
=The wipei motor is controlled through a dash
mounted &itch on all cars. The Rallye and GT, in
addition tb the dash mounted switch, also have a
switch moimted in conjunction with the windshield
washer fodt pump. Depressing the washer pump will
allow the bipers to operate while the pump is de-
pressed. i
DIAGNO;SIS
PRELIMINj9RY INSPECTION
1. Make
c&in of firm wire connections at wiper
motor fuse block and wiper switch.
Page No.
1 E-37
1 E-37E-38
E-38
E-40
E-41
E-4 1E-42
1 E-43
1 E-432. Check to see that the fuse is not blown.
3. Be sure wiper motor is not loose on fire wall.
4. With the yellow wire disconnected from terminal
No. 53 on the
wi@er motor, turn the ignition switch
and wiper switch to the on position and check volt-
age available to the wiper motor. There should be 12
volts available at the durple wire with a properly
charged battery.
Checking Wiper Operation1. Turn ignition switch on and engage wiper switch
to see if wiper motor will operate.
2. If wiper action is slow or inoperative, turn swit-
ches off and detach wiper control
inn from crank
arm.3. Operate wiper manually checking for excessive
bind in linkage. Correct if necessary.
Page 59 of 625
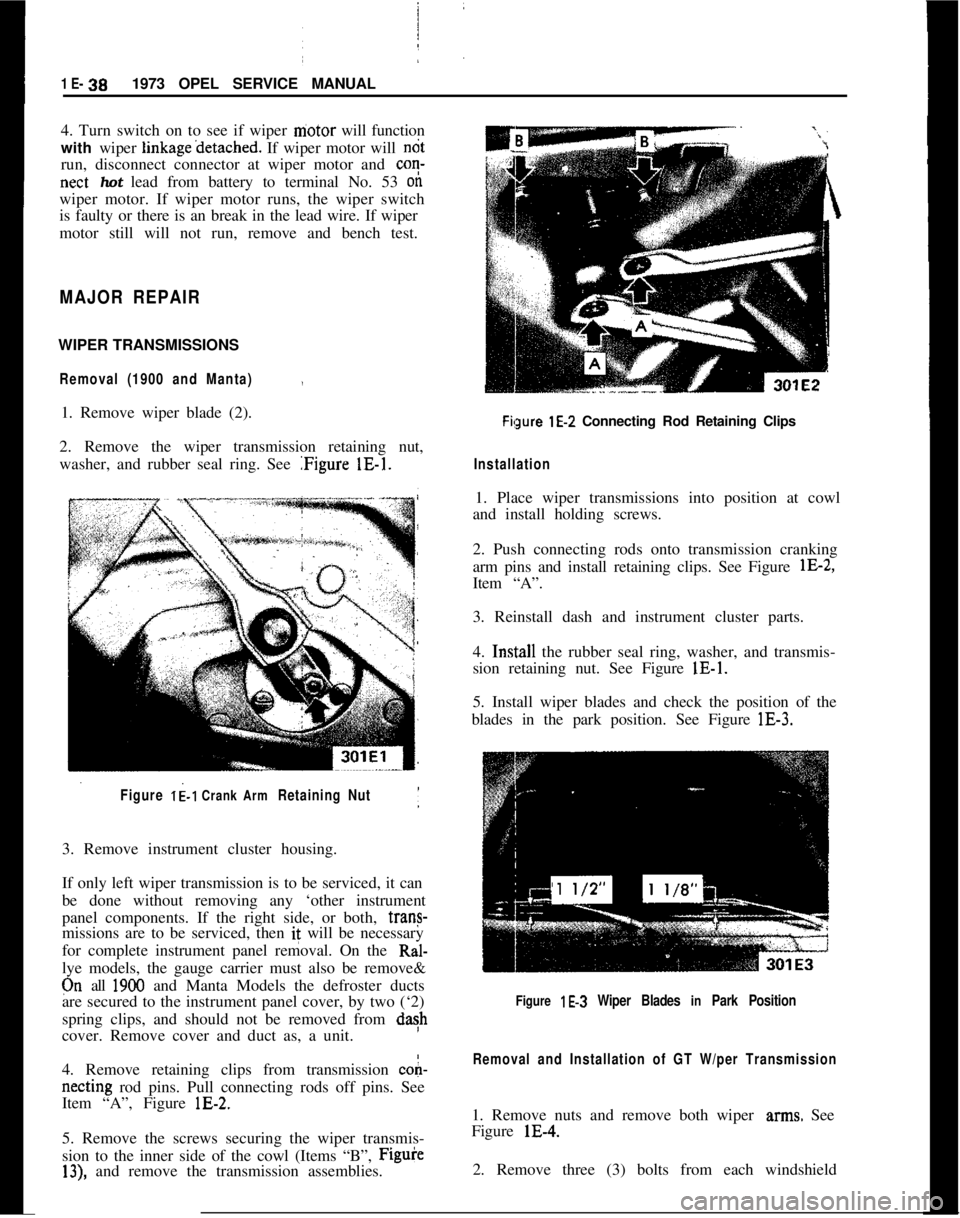
1 E- 381973 OPEL SERVICE MANUAL
4. Turn switch on to see if wiper niotor will function
with wiper linkage’detached. If wiper motor will ndt
run, disconnect connector at wiper motor and co?-
nect hot lead from battery to terminal No. 53 onwiper motor. If wiper motor runs, the wiper switch
is faulty or there is an break in the lead wire. If wiper
motor still will not run, remove and bench test.
MAJOR REPAIRWIPER TRANSMISSIONS
Removal (1900 and Manta)1. Remove wiper blade (2).
2. Remove the wiper transmission retaining nut,
washer, and rubber seal ring. See .Figure lE-1.
Figure lE-1 Crank Arm Retaining Nut3. Remove instrument cluster housing.
If only left wiper transmission is to be serviced, it can
be done without removing any ‘other instrument
panel components. If the right side, or both, trans-
missions are to be serviced, then
it will be necessary
for complete instrument panel removal. On the Ral-
lye models, the gauge carrier must also be remove&Qn all
1900 and Manta Models the defroster ducts
are secured to the instrument panel cover, by two (‘2)
spring clips, and should not be removed from
dayhcover. Remove cover and duct as, a unit.
4. Remove retaining clips from transmission co;-netting rod pins. Pull connecting rods off pins. See
Item “A”, Figure lE-2.
5. Remove the screws securing the wiper transmis-
sion to the inner side of the cowl (Items “B”, Figuie
13), and remove the transmission assemblies.I
Figure lE-2 Connecting Rod Retaining Clips
Installation1. Place wiper transmissions into position at cowl
and install holding screws.
2. Push connecting rods onto transmission cranking
arm pins and install retaining clips. See Figure lE-2,
Item “A”.
3. Reinstall dash and instrument cluster parts.
4.
1nst:all the rubber seal ring, washer, and transmis-
sion retaining nut. See Figure IE-1.
5. Install wiper blades and check the position of the
blades in the park position. See Figure lE-3.
Figure lE-3 Wiper Blades in Park Position
Removal and Installation of GT W/per Transmission1. Remove nuts and remove both wiper
arms. See
Figure lE-4.
2. Remove three (3) bolts from each windshield
Page 60 of 625
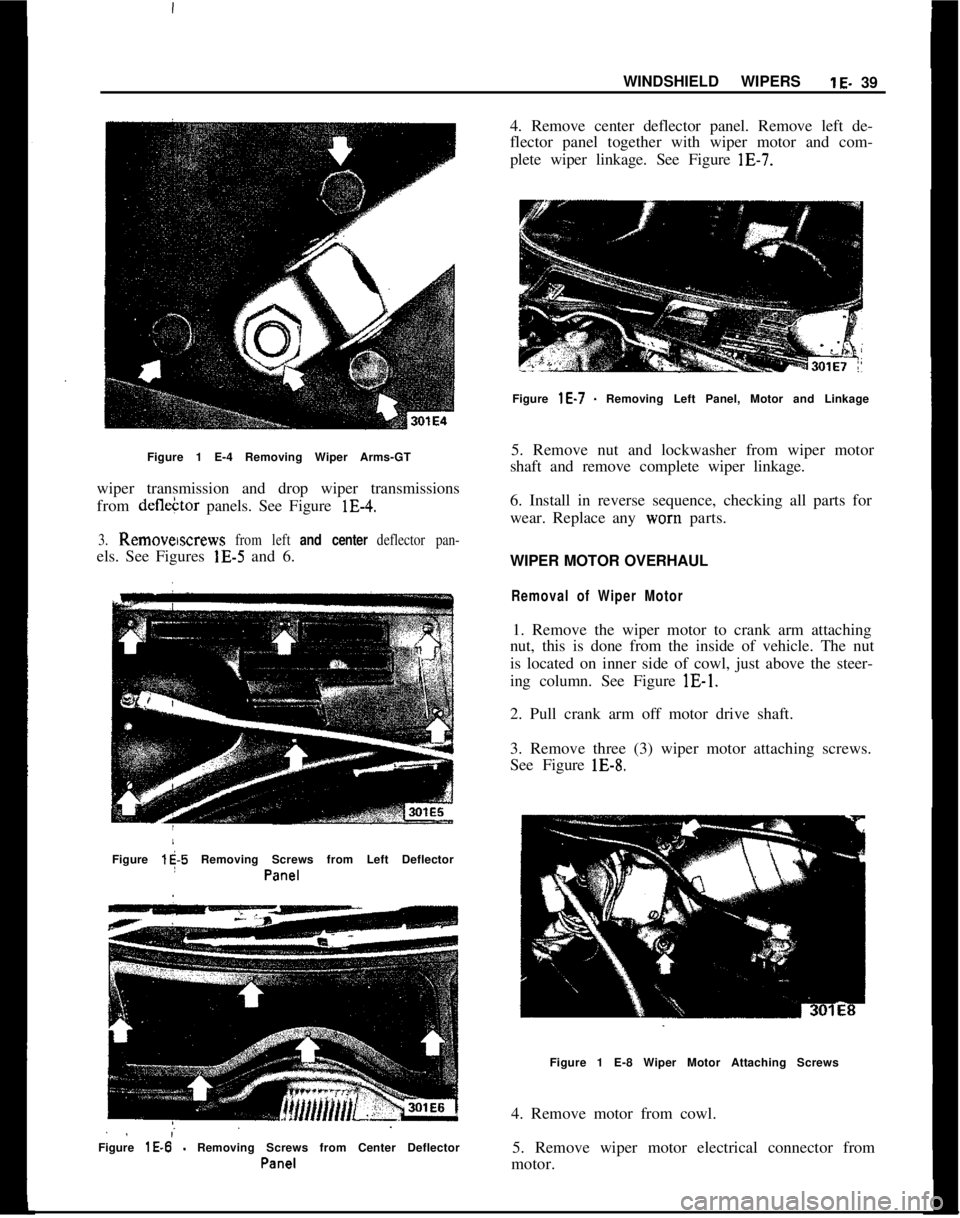
WINDSHIELD WIPERSlE- 39
Figure 1 E-4 Removing Wiper Arms-GT
wiper transmission and drop wiper transmissions
from defleCtor panels. See Figure lE-4.3. Remowscrews from left and center deflector pan-els. See Figures lE-5 and 6.
Figure
l$-5 Removing Screws from Left Deflector
I
Pa%?1
. .;Figure
lE-6 - Removing Screws from Center Deflector
Pall-Z!14. Remove center deflector panel. Remove left de-
flector panel together with wiper motor and com-
plete wiper linkage. See Figure lE-7.
Figure
lE-7 - Removing Left Panel, Motor and Linkage
5. Remove nut and lockwasher from wiper motor
shaft and remove complete wiper linkage.
6. Install in reverse sequence, checking all parts for
wear. Replace any worn parts.
WIPER MOTOR OVERHAUL
Removal of Wiper Motor1. Remove the wiper motor to crank arm attaching
nut, this is done from the inside of vehicle. The nut
is located on inner side of cowl, just above the steer-
ing column. See Figure lE-1.
2. Pull crank arm off motor drive shaft.
3. Remove three (3) wiper motor attaching screws.
See Figure lE-8.
Figure 1 E-8 Wiper Motor Attaching Screws
4. Remove motor from cowl.
5. Remove wiper motor electrical connector from
motor.