PONTIAC FIERO 1988 Service Repair Manual
Manufacturer: PONTIAC, Model Year: 1988, Model line: FIERO, Model: PONTIAC FIERO 1988Pages: 1825, PDF Size: 99.44 MB
Page 191 of 1825
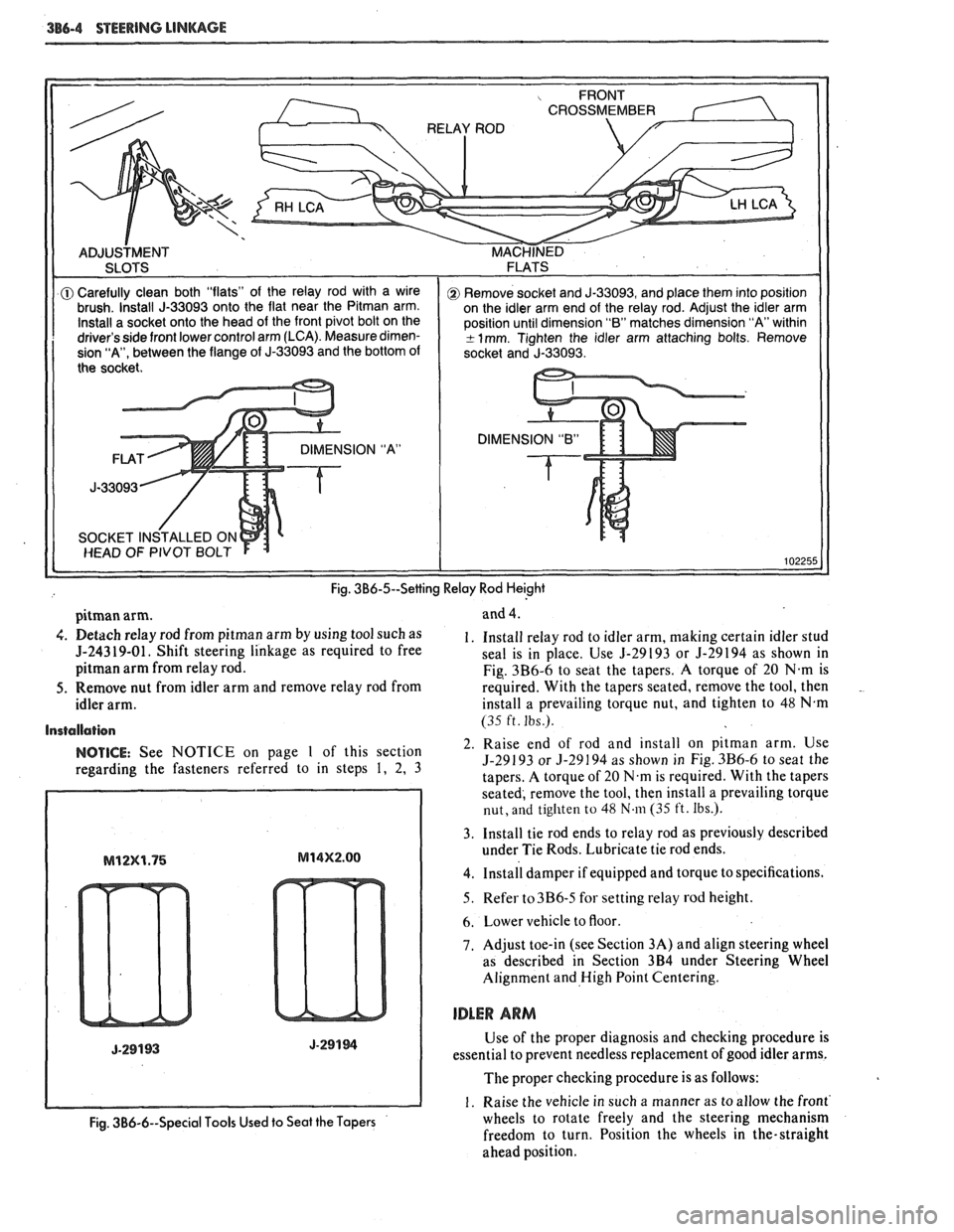
386-4 STEERING LINKAGE
DIMENSION "B"
Fig. 3B6-5--Setting Relay Rod Heighi
pitman arm.
4. Detach relay rod from pitman arm by using tool such as
5-24319-01. Shift steering linkage as required to free
pitman arm from relay rod.
5. Remove nut from idler arm and remove relay rod from
idler arm.
Installation
NOTICE: See NOTICE on page 1 of this section
regarding the fasteners referred to in steps
1, 2, 3 and
4.
1. Install relay
rod to idler arm, making certain idler stud
seal is in place. Use
5-29193 or 5-29194 as shown in
Fig. 3B6-6 to seat the tapers. A torque of
20 N.m is
required. With the tapers seated, remove the tool, then
.
install a prevailing torque nut, and tighten to 48 N.m
(35 ft. Ibs.).
2. Raise end of rod and install on pitman arm. Use
5-29193 or 3-29194 as shown in Fig. 3B6-6 to seat the
tapers. A torque of
20 N.m is required. With the tapers
seated, remove the tool, then install a prevailing torque
nut, and tighten to 48 N.111 (35 ft. Ibs.).
3. Install tie rod ends to relay rod as previously described
under Tie Rods. Lubricate tie rod ends.
4. ~nstall damper if equipped and torque to specifications.
5. Refer to3B6-5 for setting relay rod height.
6. Lower vehicle to floor
7. Adjust toe-in (see Section 3A) and align steering wheel
as described in Section
3B4 under Steering Wheel
Alignment and High Point Centering.
IDLER ARM
Use of the proper diagnosis and checking procedure is
essential to prevent needless replacement of good idler arms.
The proper checking procedure is as follows:
1. Raise the vehicle in such a manner as to allow the front'
Fig. 3B6-6--Special Tools Used to Seat the Tapers wheels to rotate freely and the steering mechanism
freedom to turn. Position the wheels in the-straight
ahead position.
Page 192 of 1825
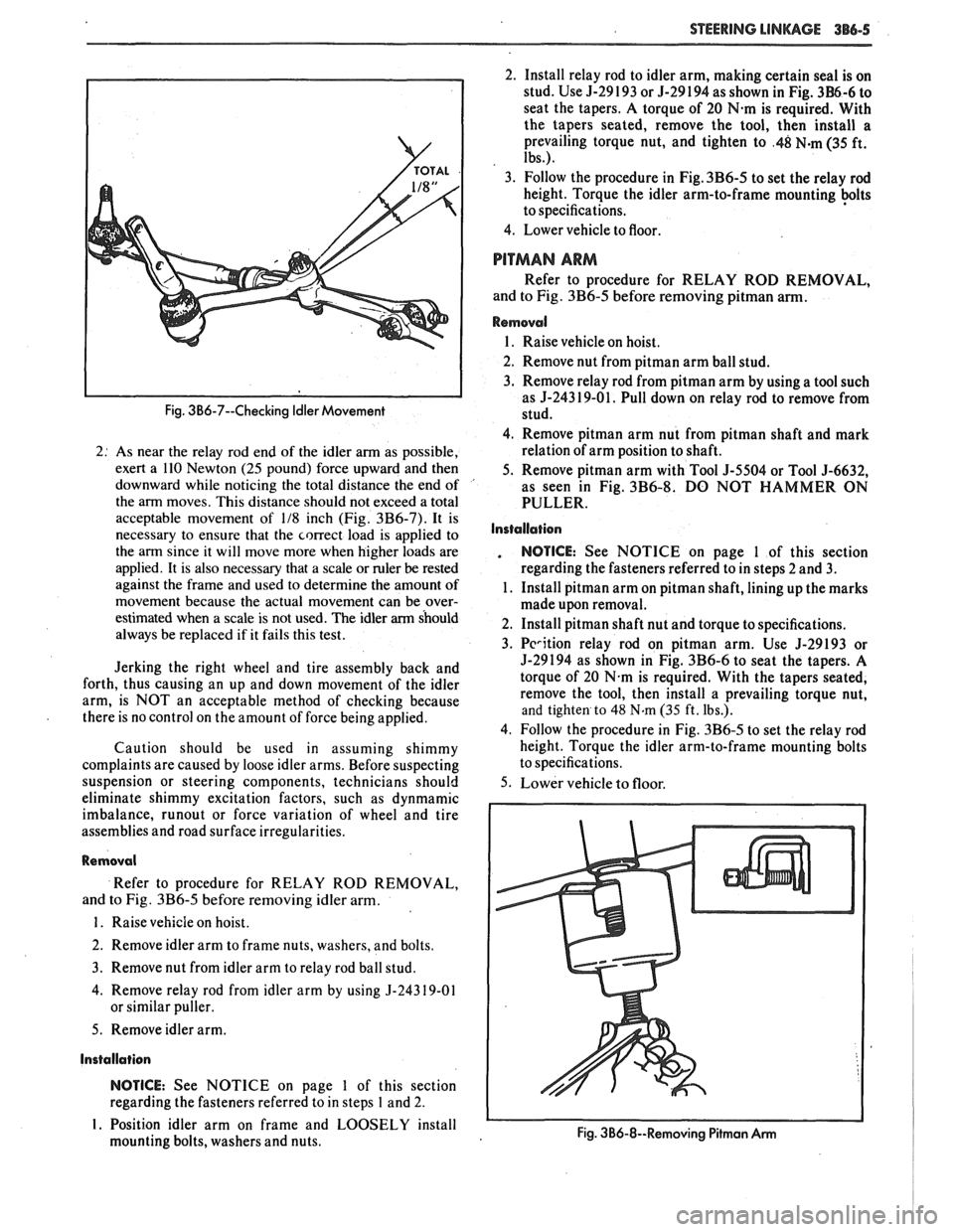
STEERING LINKAGE 386-5
Fig. 3B6-7--Checking Idler Movement
2: As near the relay rod end of the idler arm as possible,
exert a 110 Newton
(25 pound) force upward and then
downward while noticing the total distance the end of '
the arm moves. This distance should not exceed a total
acceptable movement of
118 inch (Fig. 3B6-7). It is
necessary to ensure that the correct load is applied to
the arm since it will move more when higher loads are
applied. It is also necessary that a scale or ruler
be rested
against the frame and used to determine the amount of
movement because the actual movement can be over-
estimated when a scale is not used. The idler
arm should
always be replaced if it fails this test.
Jerking the right wheel and tire assembly back and
forth, thus causing an up and down movement of the idler
arm, is NOT an acceptable method of checking because
there is no control on the amount of force being applied.
Caution should be used in assuming shimmy
complaints are caused by loose idler arms. Before suspecting
suspension or steering components, technicians should
eliminate shimmy excitation factors, such as dynmamic
imbalance,
runout or force variation of wheel and tire
assemblies and road surface irregularities.
Removal
Refer to procedure for RELAY ROD REMOVAL,
and to Fig.
3B6-5 before removing idler arm.
1. Raise vehicle on hoist.
2. Remove idler arm to frame nuts, washers, and bolts.
3. Remove nut from idler arm to relay rod ball stud.
4. Remove relay rod from idler arm by using
5-24319-01
or similar puller.
5. Remove idler arm.
Installation
NOTICE: See NOTICE on page 1 of this section
regarding the fasteners referred to in steps
1 and 2.
I. Position idler arm on frame and LOOSELY install
mounting bolts, washers and nuts. 2.
Install relay rod to idler arm, making certain seal is on
stud. Use 5-29 193 or 5-29 194 as shown in Fig.
3B6-6 to
seat the tapers. A torque of 20
N.m is required. With
the tapers seated, remove the tool, then install a
prevailing torque nut, and tighten to
.48 N-m (35 ft.
Ibs.).
3. Follow the procedure in Fig. 3B6-5 to set the relay rod
height. Torque the idler arm-to-frame mounting
+Its
to specifications.
4. Lower vehicle to floor.
PITMAN ARM
Refer to procedure for RELAY ROD REMOVAL,
and to Fig.
3B6-5 before removing pitman arm.
Removal
1. Raise vehicle on hoist.
2. Remove nut from
pitman arm ball stud.
3. Remove relay rod from pitman arm by using a tool such
as
5-243 19-01. Pull down on relay rod to remove from
stud.
4. Remove pitman arm nut from pitman shaft and mark
relation of arm position to shaft.
5. Remove
pitman arm with Tool 5-5504 or Tool 5-6632,
as seen in Fig.
3B6-8. DO NOT HAMMER ON
PULLER.
Installation
. NOTICE: See NOTICE on page 1 of this section
regarding the fasteners referred to in steps 2 and
3.
1. Install pitman arm on pitman shaft, lining up the marks
made upon removal.
2. Install pitman shaft nut and torque to specifications.
3.
Pcrition relay rod on pitman arm. Use 5-29193 or
5-29194 as shown in Fig. 3B6-6 to seat the tapers. A
torque of 20
N.m is required. With the tapers seated,
remove the tool, then install a prevailing torque nut,
and tighten to 48 N.m (35 ft. Ibs.).
4. Follow the procedure in Fig.
3B6-5 to set the relay rod
height. Torque the idler arm-to-frame mounting bolts
to specifications.
5. Lower vehicle to floor.
Fig. 3B6-8--Removing Pitmon Arm I I
Page 193 of 1825
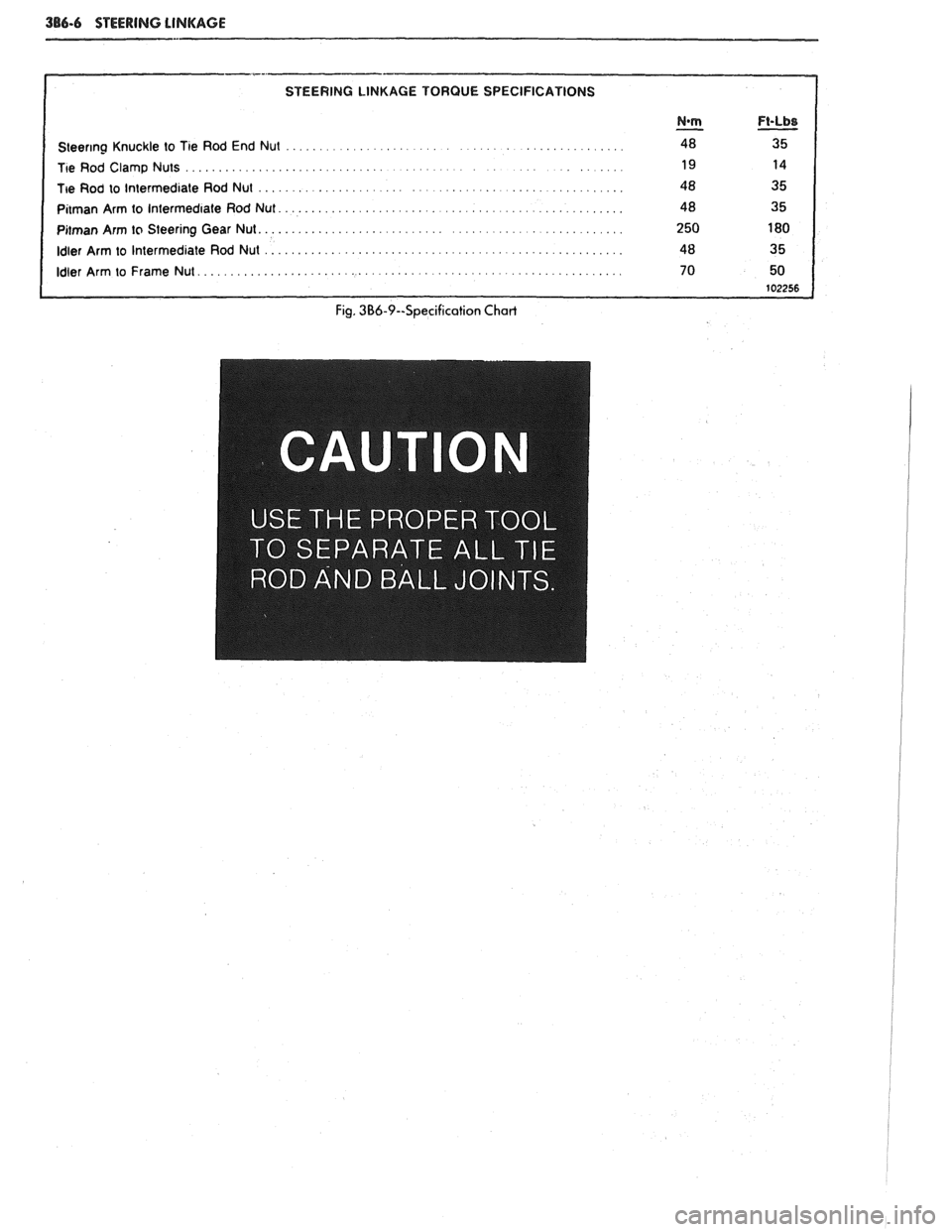
386-6 STEERING LINKAGE
Steering Knuckle to Tie Rod End Nut ............................................
Tie Rod Clamp Nuts ............................................. ....
Tie Rod to Intermediate Rod Nut ..................................................
Pitman Arm to lntermed~ate Rod Nut.. .................................................
Pitman Arm to Steering Gear Nut.. ..................................................
Idler Arm to Intermediate Rod Nut ......................................................
Page 194 of 1825
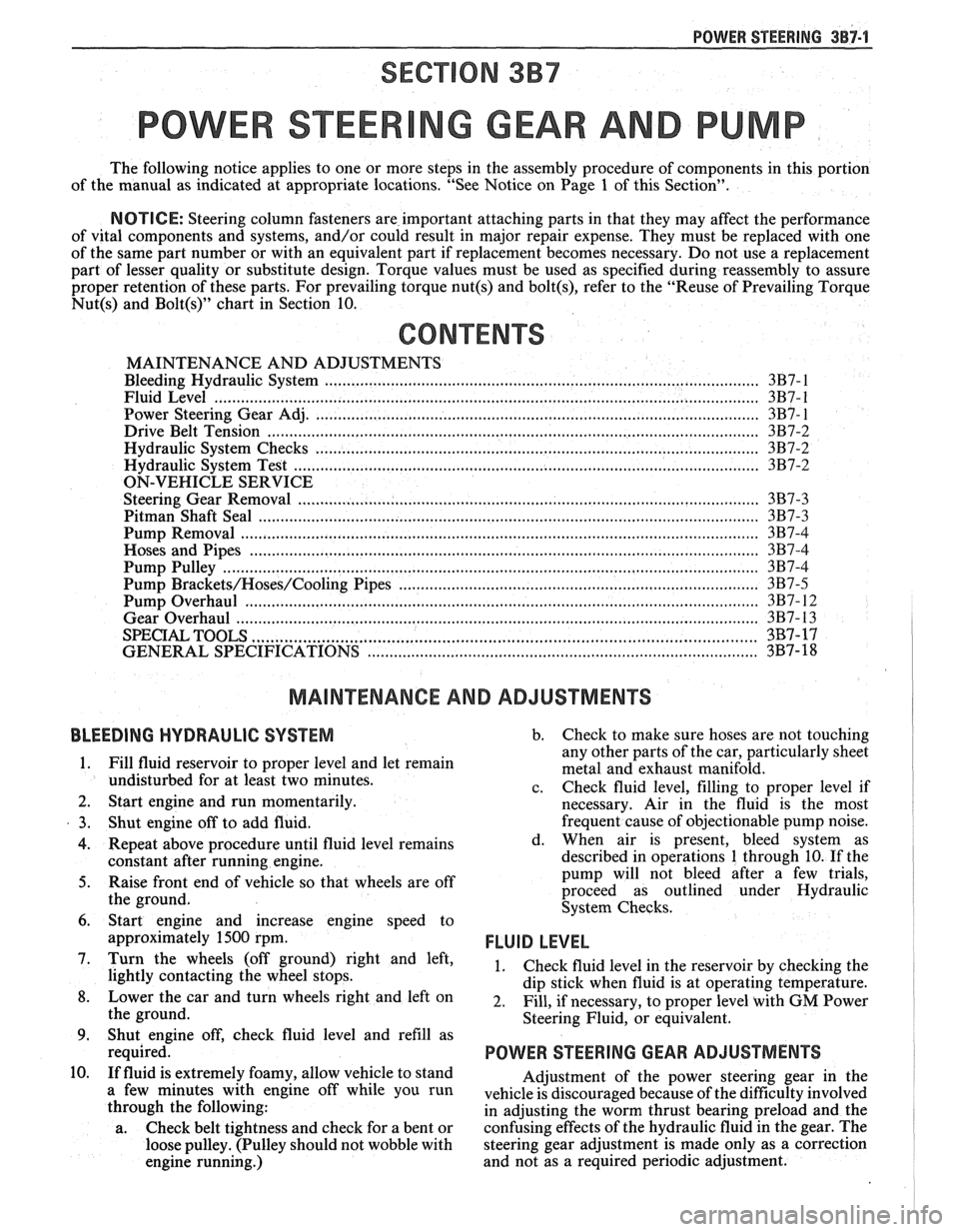
POWER Sf EERING 387-1
SECTION 3B7
POWER STEER NG GEAR AND PUMP
The following notice applies to one or more steps in the assembly procedure of components in this portion
of the manual as indicated at appropriate locations. "See Notice on Page
1 of this Section".
NOTICE: Steering column fasteners are important attaching parts in that they may affect the performance
of vital components and systems, and/or could result in major repair expense. They must be replaced with one
of the same part number or with an equivalent part if replacement becomes necessary. Do not use a replacement
part of lesser quality or substitute design. Torque values must be used as specified during reassembly to assure
proper retention of these parts. For prevailing torque
nut(s) and bolt(s), refer to the "Reuse of Prevailing Torque
Nut(s) and Bolt(s)" chart in Section 10.
CONTENTS
MAINTENANCE AND ADJUSTMENTS
Bleeding Hydraulic System
................................................................................................. 3B7- 1
Fluid Level ......................................................................................................................... 3B7- 1
Power Steering Gear Adj. ..................................................................................................... 3B7- 1
Drive Belt Tension .............................................................................................................. 3B7-2
Hydraulic System Checks .................................................................................................. 3B7-2
Hydraulic System Test ......................................................................................................... 3B7-2
ON-VEHICLE SERVICE
Steering Gear Removal
...................................................................................................... 3B7-3
Pitman Shaft Seal .................................................................................................................. 3B7-3
Pump Removal ..... , ................................................................................................................ 3B7-4
................................................................................................................... Hoses and Pipes 3B7-4
Pump Pulley ....................................................................................................................... 3B7-4
.................................................................................. Pump Brackets/Hoses/Cooling Pipes 3B7-5
........................................................................................ Pump Overhaul .................... ..... 3B7- 12
Gear Overhaul .................................................................................................................... 3B7- 13
SPECIAL TOOLS ............................................................................................................ 3B7-17 ......................... .......................................................... GENERAL SPECIFICATIONS .. 3B7- 18
MAlNKNANGE AND ADJUSTMENTS
BLEEDING HYDRAULIC SYSTEM
Fill fluid reservoir to proper level and let remain
undisturbed for at least two minutes.
Start engine and run momentarily.
Shut engine off to add fluid.
Repeat above procedure until fluid level remains
constant after running engine.
Raise front end of vehicle so that wheels are off
the ground.
Start engine and increase engine speed to
approximately
1500 rpm.
Turn the wheels (off ground) right and left,
lightly contacting the wheel stops.
Lower the car and turn wheels right and left on
the ground.
Shut engine off, check fluid level and refill as
required.
If fluid is extremely foamy, allow vehicle to stand
a few minutes with engine off while you run
through the following:
a. Check belt
tightness and check for a bent or
loose pulley. (Pulley should not wobble with
engine running.) b.
Check
to make sure hoses are not touching
any other parts of the car, particularly sheet
metal and exhaust manifold.
c. Check fluid
level, filling to proper level if
necessary. Air in the fluid is the most
frequent cause of objectionable pump noise.
d. When air is present, bleed system as
described in operations 1 through 10. If the
pump will not bleed after a few trials,
proceed as outlined under Hydraulic
System Checks. FLUID LEVEL
1. Check fluid level in the reservoir by checking the
dip stick when fluid is at operating temperature.
2. Fill, if necessary, to proper level with GM Power
Steering Fluid, or equivalent.
POWER STEERING GEAR ADJUSTMENTS
Adjustment of the power steering gear in the
vehicle is discouraged because of the difficulty involved
in adjusting the worm thrust bearing preload and the
confusing effects of the hydraulic fluid in the gear. The
steering gear adjustment is made only as a correction
and not as a required periodic adjustment.
Page 195 of 1825
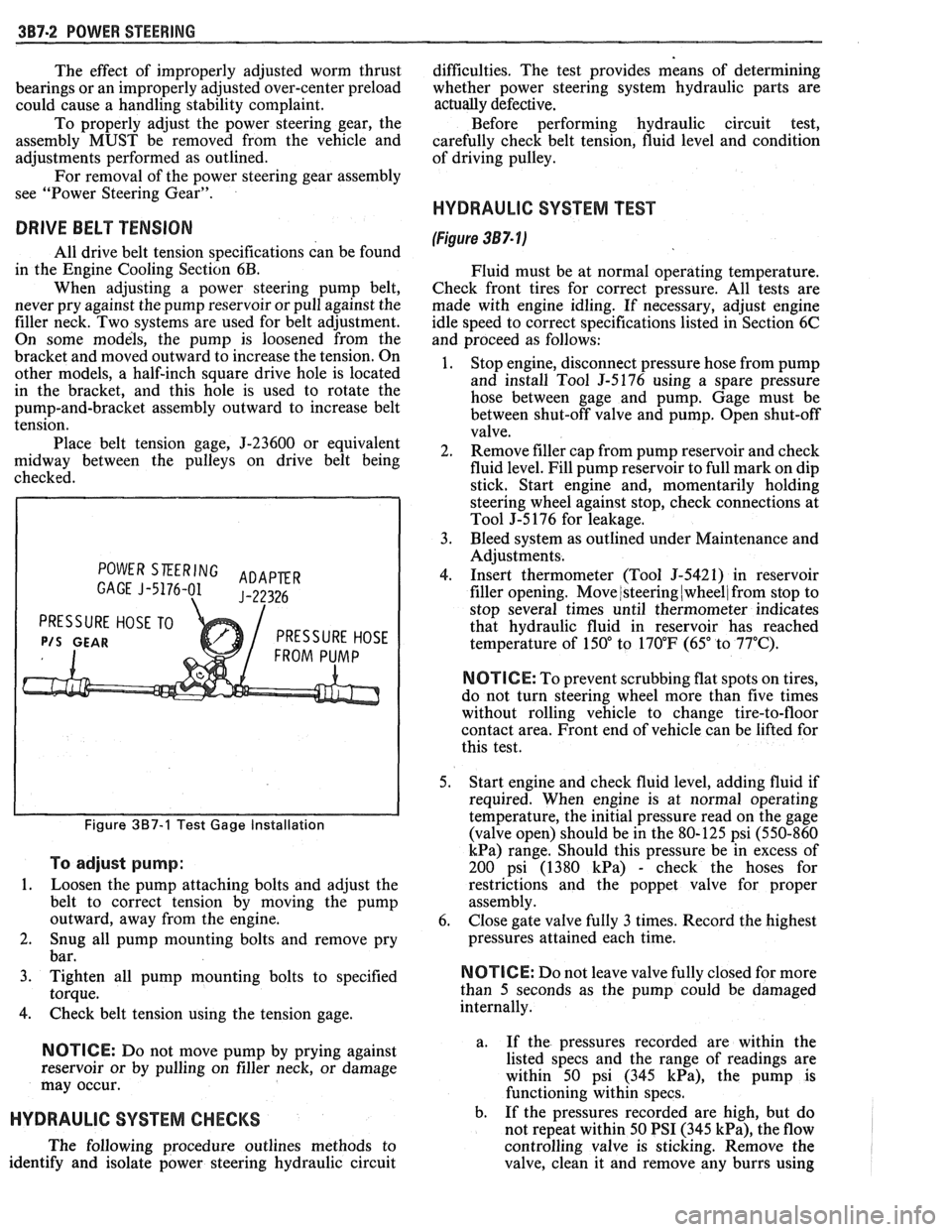
387-2 POWER STEERING
The effect of improperly adjusted worm thrust
bearings or an improperly adjusted over-center preload
could cause a handling stability complaint.
To properly adjust the power steering gear, the
assembly MUST be removed from the vehicle and
adjustments performed as outlined.
For removal of the power steering gear assembly
see "Power Steering Gear".
DRIVE BELT TENSION
All drive belt tension specifications can be found
in the Engine Cooling Section 6B.
When adjusting a power steering pump belt,
never pry against the pump reservoir or pull against the
filler neck. Two systems are used for belt adjustment.
On some
models, the pump is loosened from the
bracket and moved outward to increase the tension. On
other models, a half-inch square drive hole is located
in the bracket, and this hole is used to rotate the
pump-and-bracket assembly outward to increase belt
tension.
Place belt tension gage, J-23600 or equivalent
midway between the pulleys on drive belt being
checked.
POWER SKERING ADAPER GAGE J-5176-01 J-22326
PRESSURE HOSE TO
P/S GEAR PRESSURE HOSE
Figure 387-1 Test Gage Installation
To adjust pump:
1.
Loosen the pump attaching bolts and adjust the
belt to correct tension by moving the pump
outward, away from the engine.
2. Snug all pump mounting bolts and remove pry
bar.
3. Tighten all pump mounting bolts to specified
torque.
4. Check belt tension using the tension gage.
NOTICE: Do not move pump by prying against
reservoir or by pulling on filler neck, or damage
may occur.
HYDRAULIC SYSTEM CHECKS
The following procedure outlines methods to
identify and isolate power steering hydraulic circuit difficulties.
The test provides means of determining
whether power steering system hydraulic parts are
actually
defective.
Before performing hydraulic circuit test,
carefully check belt tension, fluid level and condition
of driving pulley.
HYDRAULIC SYSTEM TEST
(Figure 387- lj
Fluid must be at normal operating temperature.
Check front tires for correct pressure. All tests are
made with engine idling. If necessary, adjust engine
idle speed to correct specifications listed in Section 6C
and proceed as follows:
1. Stop engine, disconnect pressure hose from pump
and install Tool
5-5176 using a spare pressure
hose between gage and pump. Gage must be
between shut-off valve and pump. Open shut-off
valve.
2. Remove filler cap from pump reservoir and check
fluid level. Fill pump reservoir to full mark on dip
stick. Start engine and, momentarily holding
steering wheel against stop, check connections at
Tool J-5 176 for leakage.
3. Bleed system as outlined under Maintenance and
Adjustments.
4. Insert thermometer (Tool J-5421) in reservoir
filler opening. Move
/steering (wheel/ from stop to
stop several times until thermometer indicates
that hydraulic fluid in reservoir has reached
temperature of
150" to 170°F (65" to 77°C).
N OTI G E: To prevent scrubbing flat spots on tires,
do not turn steering wheel more than five times
without rolling vehicle to change tire-to-floor
contact area. Front end of vehicle can be lifted for
this test.
5. Start engine and check fluid level, adding fluid if
required. When engine is at normal operating
temperature, the initial pressure read on the gage
(valve open) should be in the 80-125 psi (550-860
kPa) range. Should this pressure be in excess of
200 psi (1380
kPa) - check the hoses for
restrictions and the poppet valve for proper
assembly.
6. Close gate valve fully
3 times. Record the highest
pressures attained each time.
N OTI C E: Do not leave valve fully closed for more
than
5 seconds as the pump could be damaged
internally.
a. If
the pressures recorded are within the
listed specs and the range of readings are
within 50 psi (345
kPa), the pump is
functioning within specs.
b. If the pressures recorded are high, but do
not repeat within 50 PSI (345
kPa), the flow
controlling valve is sticking. Remove the
valve, clean it and remove any burrs using
Page 196 of 1825
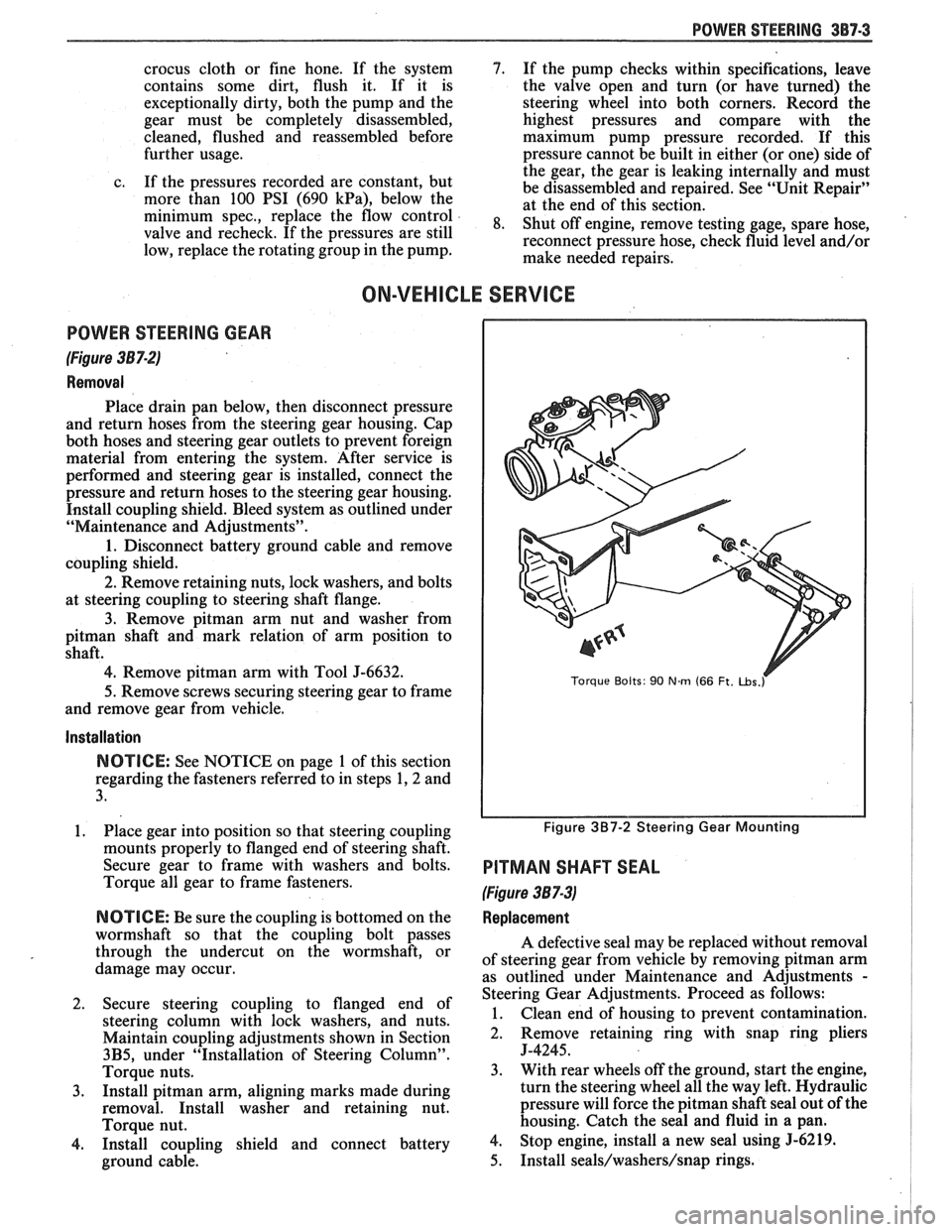
POWER STEERING 387-3
crocus cloth or fine hone. If the system 4. If the pump checks within specifications, leave
contains some dirt, flush it. If it is the valve open and turn (or have turned) the
exceptionally dirty, both the pump and the steering wheel into both corners. Record the
gear must be completely disassembled, highest pressures and compare with the
cleaned, flushed and reassembled before maximum pump pressure recorded. If this
further usage. pressure cannot be built in either (or one) side of
- the gear, the gear is leaking internally and must
c. If
the pressures recorded are constant, but
be disassembled and repaired. See "Unit Repair"
more than
100 PSI (690 kPa), below the
at the end of this section.
spec.9 rep1ace the flow 8. Shut off engine, remove testing gage, spare hose,
valve and recheck. If the pressures are still
low, replace the rotating group in the pump. reconnect pressure hose, check fluid
level and/or
make needed repairs.
ON-VEHICLE SERVICE
POWER STEERING GEAR
(Figure 387-2)
Removal
Place drain pan below, then disconnect pressure
and return hoses from the steering gear housing. Cap
both hoses and steering gear outlets to prevent foreign
material from entering the system. After service is
performed and steering gear is installed, connect the
pressure and return hoses to the steering gear housing.
Install coupling shield. Bleed system as outlined under
"Maintenance and Adjustments".
1. Disconnect battery ground cable and remove
coupling shield.
2. Remove retaining nuts, lock washers, and bolts
at steering coupling to steering shaft flange.
3. Remove pitman arm nut and washer from
pitman shaft and mark relation of arm position to
shaft.
4. Remove pitman arm with Tool J-6632.
5.
Remove screws securing steering gear to frame
and remove gear from vehicle.
Installation
NOTICE: See NOTICE on page 1 of this section
regarding the fasteners referred to in steps 1,2 and
3.
1. Place gear into position so that steering coupling
mounts properly to flanged end of steering shaft.
Secure gear to frame with washers and bolts.
Torque all gear to frame fasteners.
NOTICE: Be sure the coupling is bottomed on the
wormshaft so that the coupling bolt passes
through the undercut on the wormshaft, or
damage may occur.
2. Secure steering coupling to flanged end of
steering column with lock washers, and nuts.
Maintain coupling adjustments shown in Section
3B5, under "Installation of Steering Column".
Torque nuts.
3. Install pitman arm, aligning marks made during
removal. Install washer and retaining nut.
Torque nut.
4. Install coupling shield and connect battery
ground cable.
Torque Bolts: 90 Nm (66 Ft. ~bs.r
Figure 3B7-2 Steering Gear Mounting
PITMAN SHAFT SEAL
(Figure 387-3)
Replacement
A defective seal may be replaced without removal
of steering gear from vehicle by removing
pitman arm
as outlined under Maintenance and Adjustments
-
Steering Gear Adjustments. Proceed as follows:
1. Clean end of housing to prevent contamination.
2. Remove retaining
ring with snap ring pliers
J-4245.
3. With rear wheels off the ground, start the engine,
turn the steering wheel all the way left. Hydraulic
pressure will force the
pitman shaft seal out of the
housing. Catch the seal and fluid in a pan.
4. Stop engine, install a new seal using 5-6219.
5. Install seals/washers/snap rings.
Page 197 of 1825
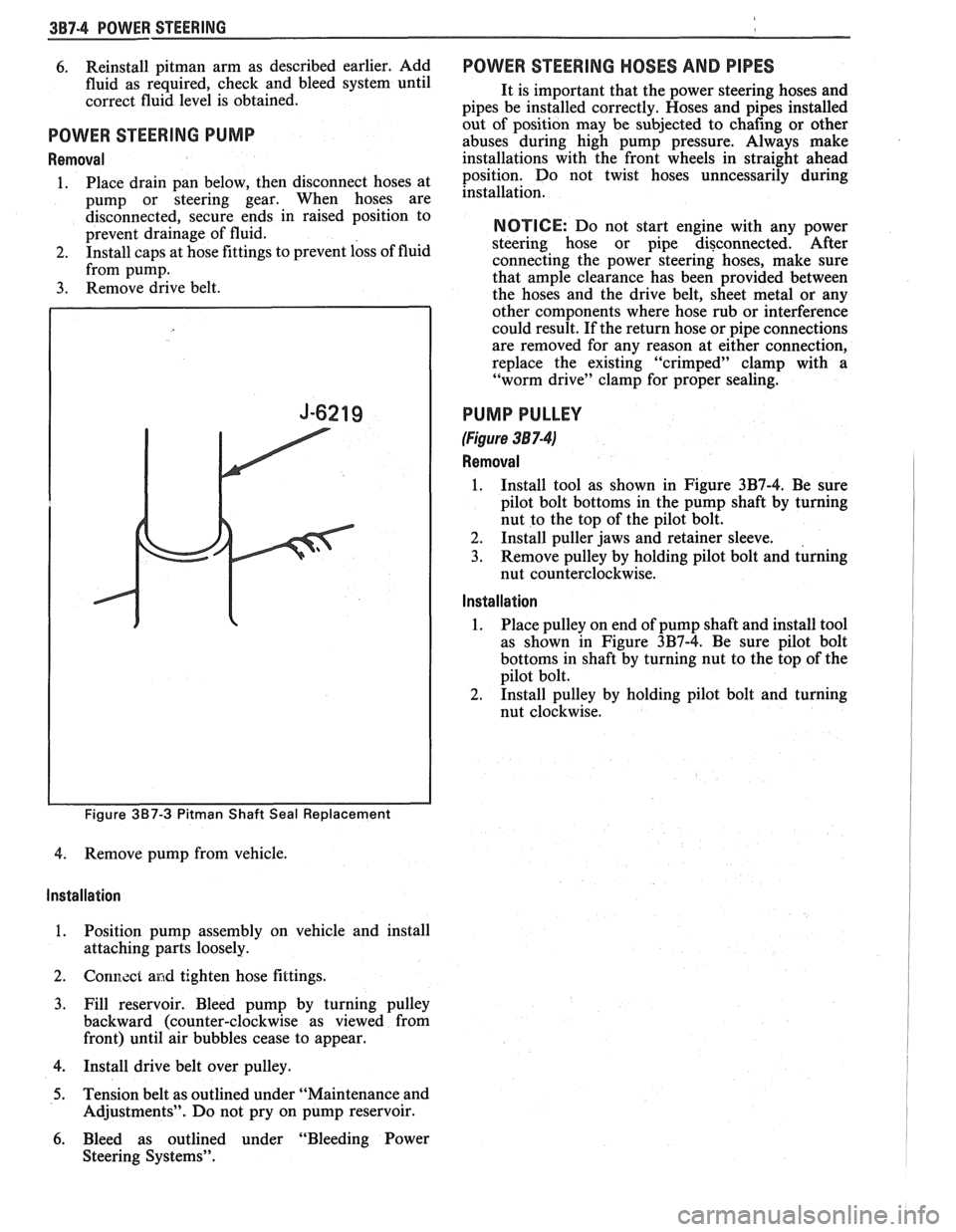
3B7-4 POWER STEERING
6. Reinstall pitman arm as described earlier, Add
fluid as required, check and bleed system until
correct fluid level is obtained.
POWER STEERING PUMP
Removal
1. Place drain pan below, then disconnect hoses at
pump or steering gear. When hoses are
disconnected, secure ends in raised position to
prevent drainage of fluid.
2. Install caps at hose fittings to prevent loss of fluid
from pump.
3. Remove drive belt.
Figure 3B7-3 Pitman Shaft Seal Replacement
4. Remove pump from vehicle.
Installation
1. Position pump assembly on vehicle and install
attaching parts loosely.
2. Gonl7.zct and tighten hose fittings.
3. Fill reservoir. Bleed pump by turning pulley
backward (counter-clockwise as viewed from
front) until air bubbles cease to appear.
4. Install drive belt over pulley.
5. Tension belt as outlined under "Maintenance and
Adjustments". Do not pry on pump reservoir.
6. Bleed as outlined under "Bleeding Power
Steering Systems".
POWER STEERING HOSES AND PIPES
It is important that the power steering hoses and
pipes be installed correctly. Hoses and pipes installed
out of position may be subjected to chafing or other
abuses during high pump pressure. Always make
installations with the front wheels in straight ahead
position. Do not twist hoses unncessarily during
installation.
NOTICE: Do not start engine with any power
steering hose or pipe disconnected. After
connecting the power steering hoses, make sure
that ample clearance has been provided between
the hoses and the drive belt, sheet metal or any
other components where hose rub or interference
could result. If the return hose or pipe connections
are removed for any reason at either connection,
replace the existing "crimped" clamp with a
"worm drive" clamp for proper sealing.
PUMP PULLEY
(Figure 38 7-41
Removal
1. Install tool as shown in Figure 3B7-4. Be sure
pilot bolt bottoms in the pump shaft by turning
nut to the top of the pilot bolt.
2. Install puller jaws and retainer sleeve.
3. Remove pulley by holding pilot bolt and turning
nut counterclockwise.
Installation
1. Place
pulley on end of pump shaft and install tool
as shown in Figure 3B7-4. Be sure pilot bolt
bottoms in shaft by turning nut to the top of the
pilot bolt.
2. Install pulley by holding pilot bolt and turning
nut clockwise.
Page 198 of 1825
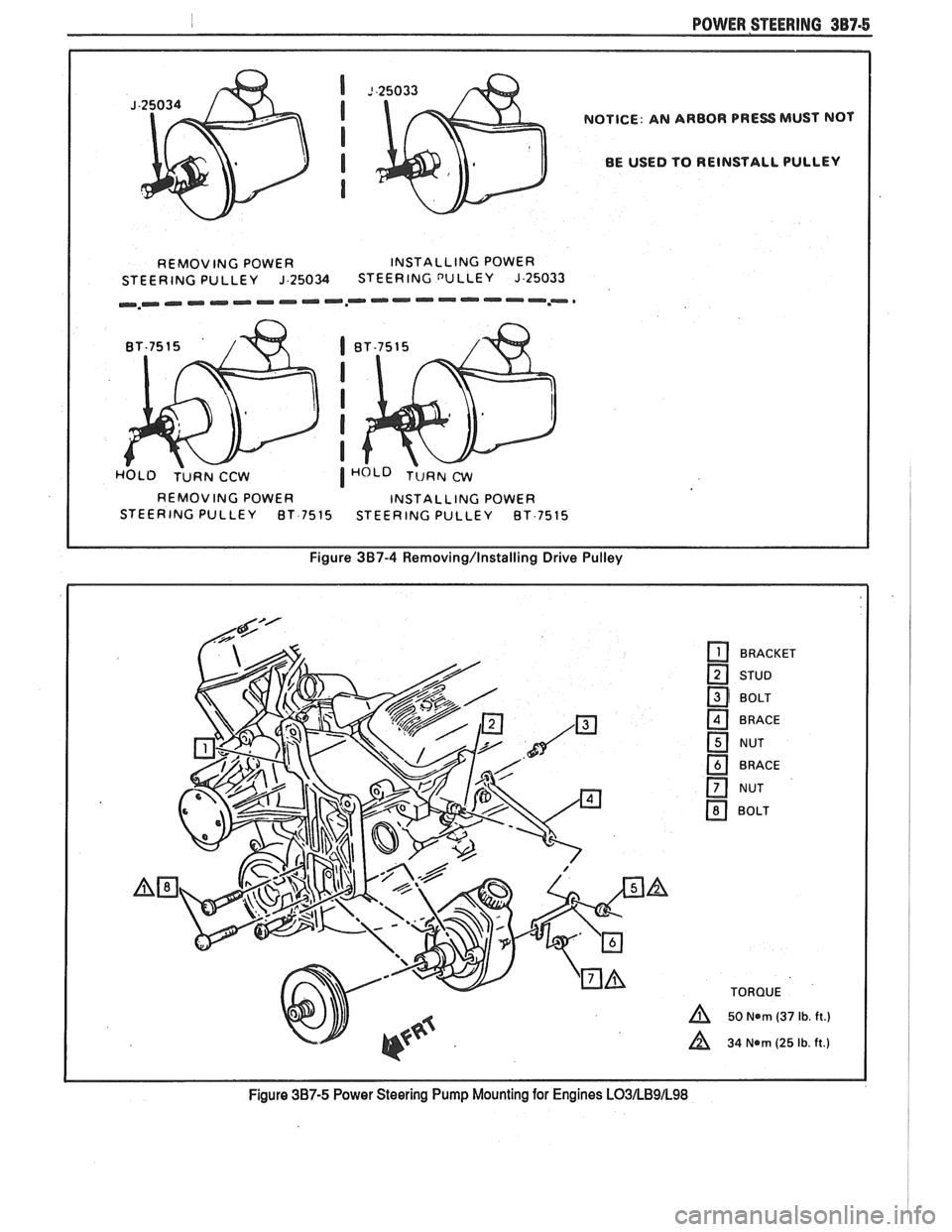
I POWER STEERING 387-5
NOTICE: AN ARBOR PRESS MUST NOT
BE USED TO REINSTALL PULLEY
REMOVING POWER INSTALLING POWER
STEERING PULLEY
J.25034 STEERING DULLEY J.25033
~,w~,~III.rw-Ilr-.-lll.l.l.---llll--.~.
HOLD TURNCCW 1 TORN CW
REMOVING POWER INSTALLING POWER
STEERING PULLEY
BT 7515 STEERING PULLEY BT-7515
Figure 387-4 Removing/lnstalling Drive Pulley
Figure 387-5 Power Steering Pump Mounting for Engines L03/LB9/L98
Page 199 of 1825
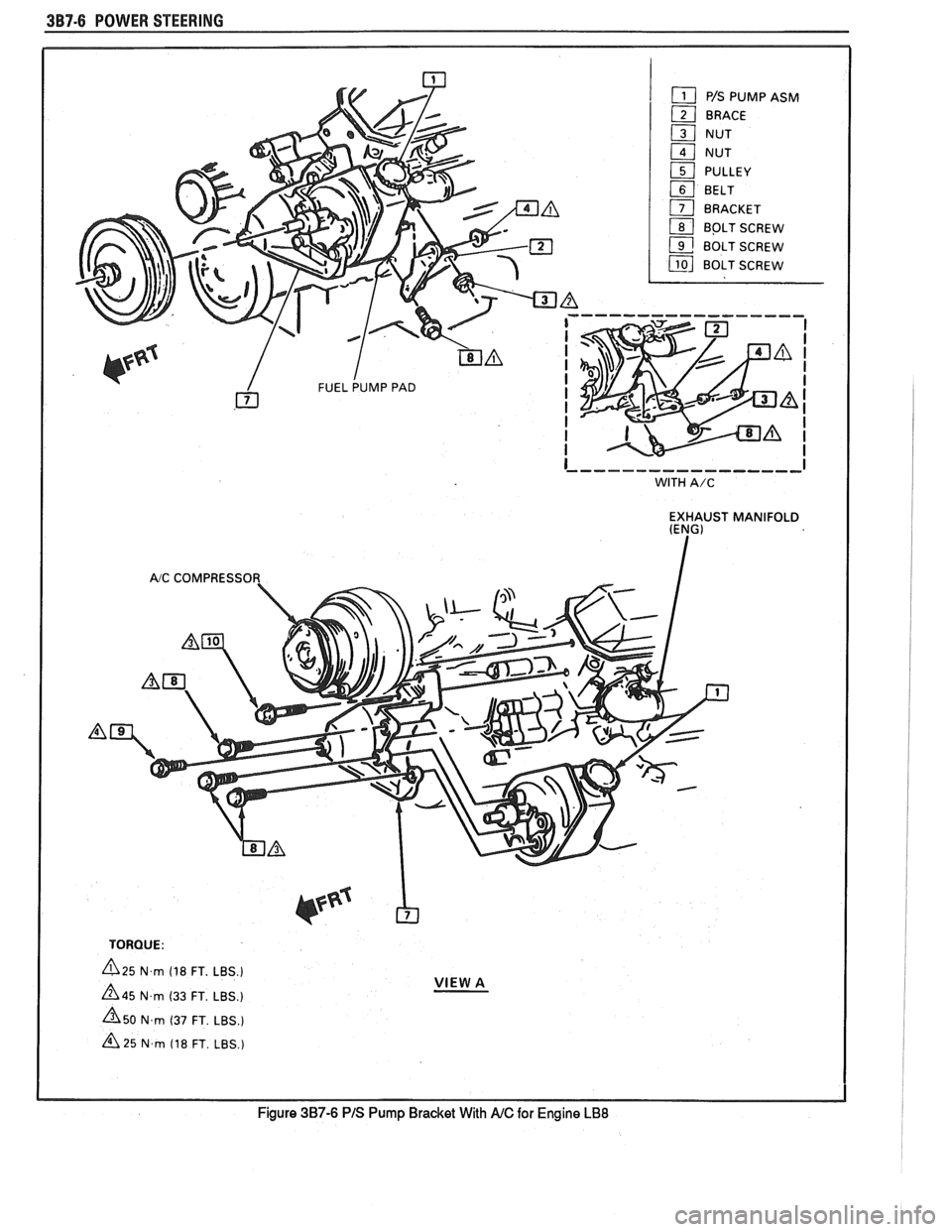
3B7-6 POWER STEERING
L,,,_,---..--..,~-,,- I WITH A/C
EXHAUST MANIFOLD
TORQUE:
425 N.rn (18 FT. LBS.) VIEW A A45 N.rn (33 FT. LBS.)
A50 N,rn (37 FT. LBS.)
A 25 N,rn (18 FT. LBS.)
Figure 3B7-6 PIS Pump Bracket With A/C for Engine LB8
Page 200 of 1825
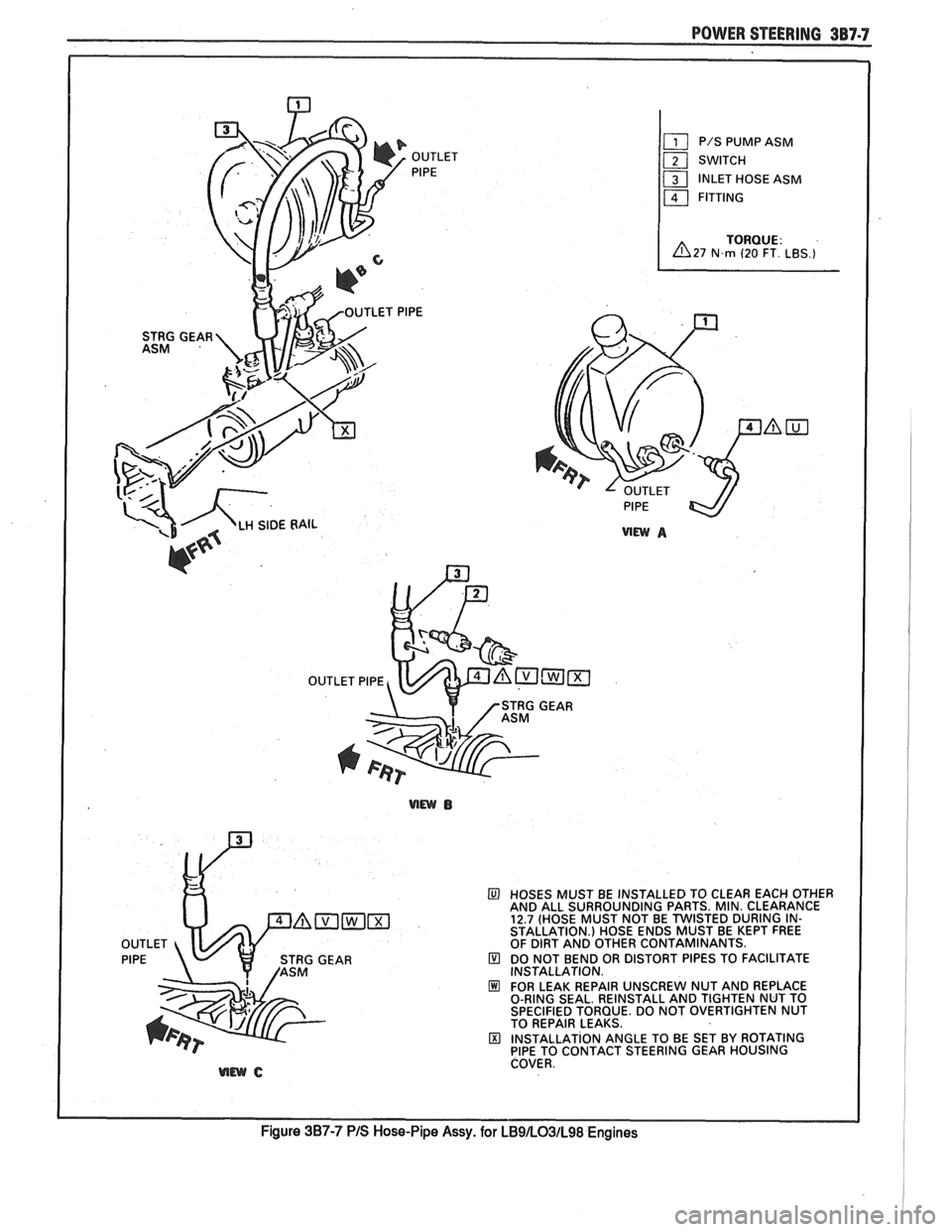
POWER STEERING 3B7-7
HOSES MUST BE INSTALLED TO CLEAR EACH OTHER
AND ALL SURROUNDING PARTS. MIN. CLEARANCE
12.7 (HOSE MUST NOT BE TWISTED DURING IN-
STALLATION.) HOSE ENDS MUST BE KEPT FREE
OF
DIRT AND OTHER CONTAMINANTS. DO NOT BEND OR DISTORT PIPES TO FACILITATE
INSTALLATION.
l?d FOR LEAK REPAIR UNSCREW NUT AND REPLACE
O-RING SEAL. REINSTALL AND TIGHTEN NUT TO
SPECIFIED TORQUE. DO NOT OVERTIGHTEN NUT
TOREPAIR LEAKS.
INSTALLATION ANGLE TO BE SET BY ROTATING PIPE TO CONTACT STEERING GEAR HOUSING
COVER.
Figure 387-7 PIS Hose-Pipe Assy. for LB9A03IL98 Engines