RENAULT KANGOO 1997 KC / 1.G Engine And Peripherals Repair Manual
Manufacturer: RENAULT, Model Year: 1997, Model line: KANGOO, Model: RENAULT KANGOO 1997 KC / 1.GPages: 208
Page 61 of 208
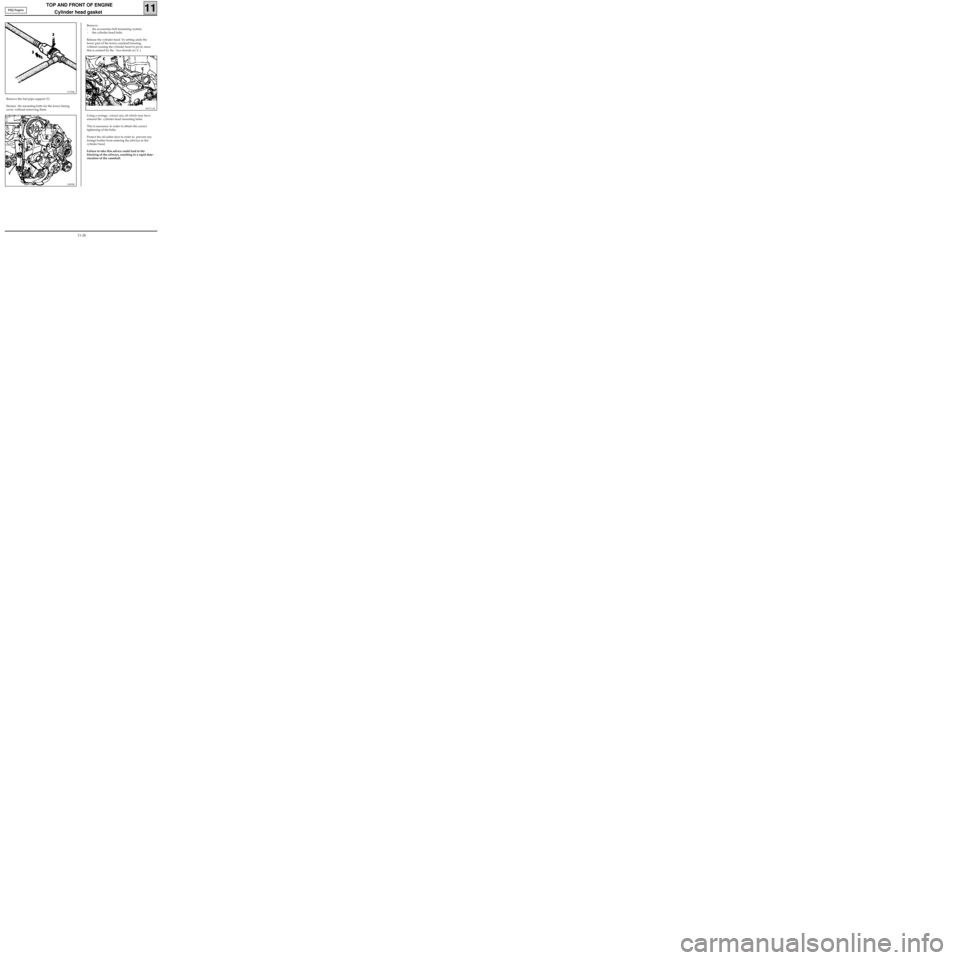
TOP AND FRONT OF ENGINE
Cylinder head gasket
11
11733R
Remove the fuel pipe support (7).
Slacken the mounting bolts for the lower timing
cover, without removing them.
99173-1R
13093R
Remove :
- the accessories belt tensioning system,
- the cylinder head bolts.
Release the cylinder head by setting aside the
lower part of the lower camshaft housing,
without causing the cylinder head to pivot, since
this is centred by the two dowels at ( C ).
Using a syringe, extract any oil which may have
entered the cylinder head mounting holes .
This is necessary in order to obtain the correct
tightening of the bolts.
Protect the oil outlet duct in order to prevent any
foreign bodies from entering the oilways in the
cylinder head.
Failure to take this advice could lead to the
blocking of the oilways, resulting in a rapid dete-
rioration of the camshaft. F8Q Engine
11-26
Page 62 of 208
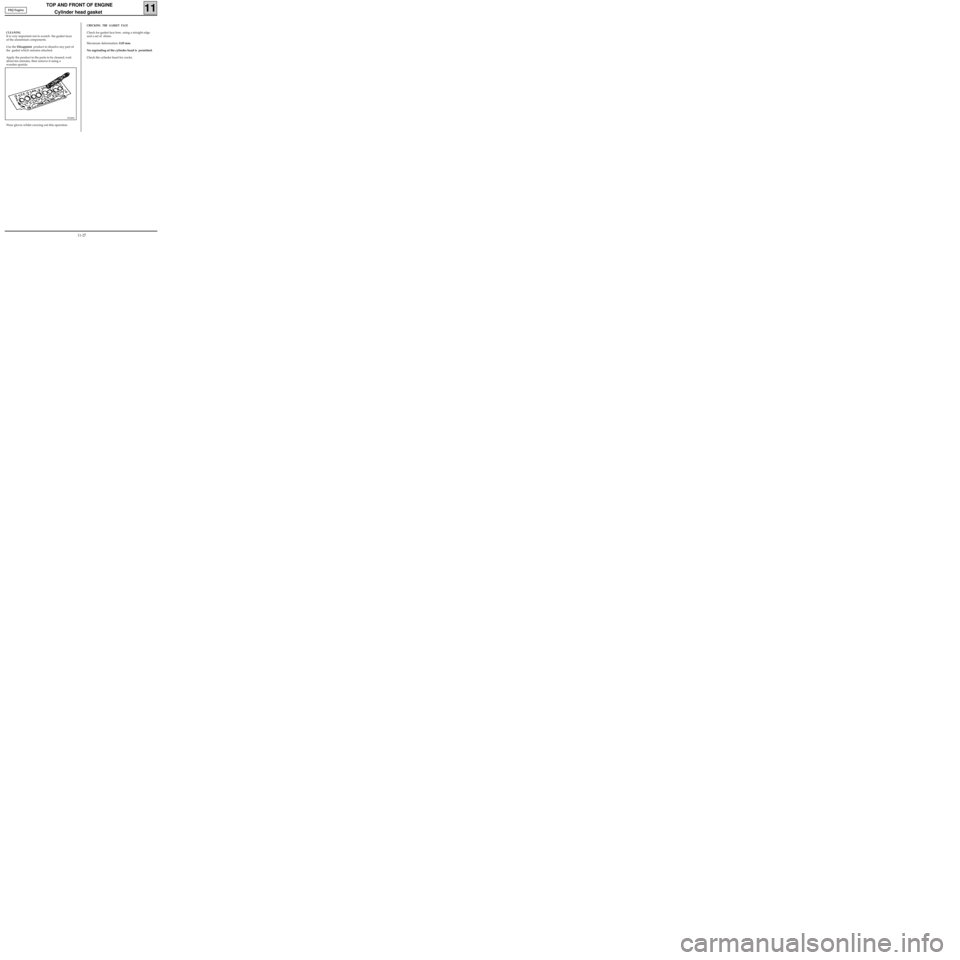
TOP AND FRONT OF ENGINE
Cylinder head gasket
11
Wear gloves whilst carrying out this operation.
99180S
CHECKING THE GASKET FACE
Check for gasket face bow, using a straight edge
and a set of shims.
Maximum deformation: 0.05 mm.
No regrinding of the cylinder head is permitted.
Check the cylinder head for cracks.
F8Q Engine
CLEANING
It is very important not to scratch the gasket faces
of the aluminium components.
Use the Décapjoint product to dissolve any part of
the gasket which remains attached.
Apply the product to the parts to be cleaned; wait
about ten minutes, then remove it using a
wooden spatula.
11-27
Page 63 of 208
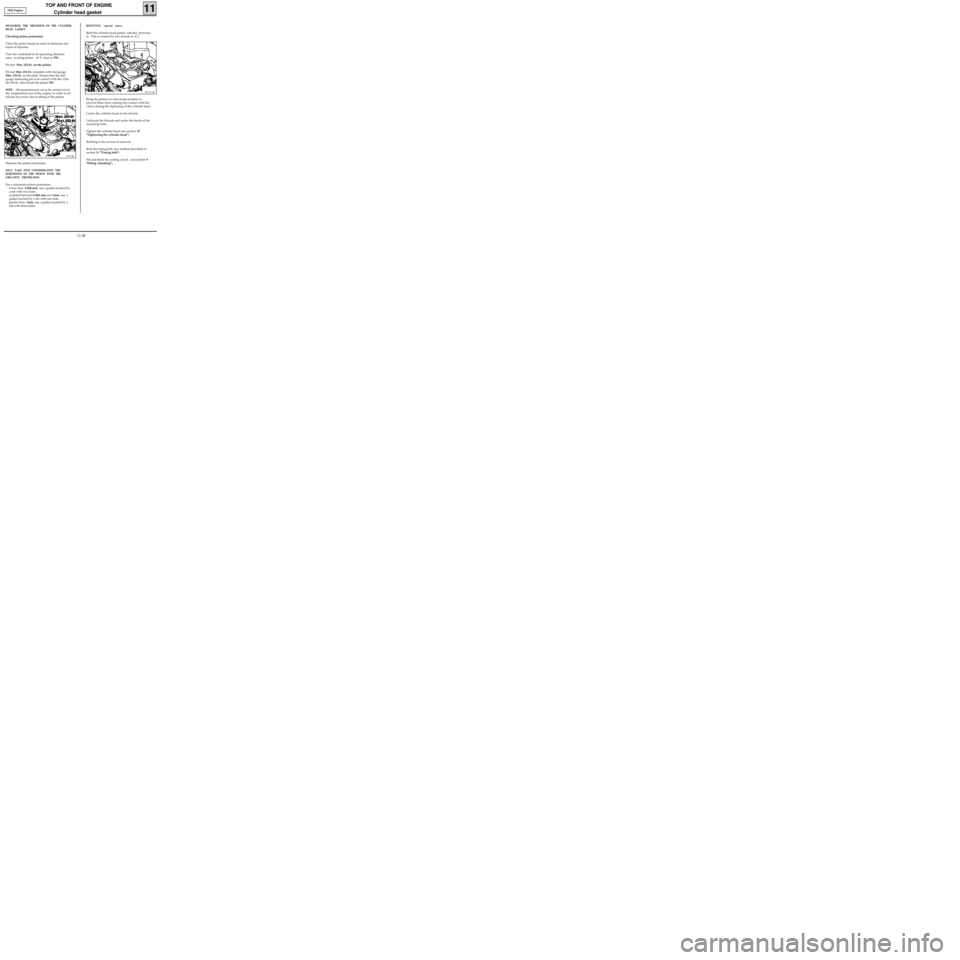
TOP AND FRONT OF ENGINE
Cylinder head gasket
11
REFITTING (special notes)
Refit the cylinder head gasket selected previous-
ly. This is centred by two dowels at (C).
99173-1R
Bring the pistons to mid-stroke position to
prevent them from coming into contact with the
valves during the tightening of the cylinder head .
Centre the cylinder head on the dowels.
Lubricate the threads and under the heads of the
mounting bolts.
Tighten the cylinder head (see section 07
"Tightening the cylinder head").
Refitting is the reverse of removal.
Refit the timing belt, (see method described in
section 11 "Timing belt").
Fill and bleed the cooling circuit , (see section 9
"Filling -bleeding").
MEASURING THE THICKNESS OF THE CYLINDER
HEAD GASKET
Checking piston protrusion
Clean the piston heads in order to eliminate any
traces of deposits.
Turn the crankshaft in its operating direction
once, to bring piston n° 1 close to
TDC .
Fit tool Mot. 252-01 on the piston.
Fit tool Mot. 251-01, complete with dial gauge
Mot. 252-01. on the plate Ensure that the dial
gauge measuring pin is in contact with the cylin-
der block; then locate the piston
TDC.
NOTE
: All measurements are to be carried out in
the longitudinal axis of the engine, in order to eli-
minate any errors due to tilting of the piston.
99173R
Measure the piston protrusion.
ONLY TAKE INTO CONSIDERATION THE
DIMENSIONS OF THE PISTON WITH THE
GREATEST PROTRUSION.
For a maximum piston protrusion:
- lower than 0.868 mm, use a gasket marked by
a tab with two holes ,
- included between 0.868 mm and 1mm, use a
gasket marked by a tab with one hole,
- greater than 1mm, use a gasket marked by a
tab with three holes. F8Q Engine
11-28
Page 64 of 208
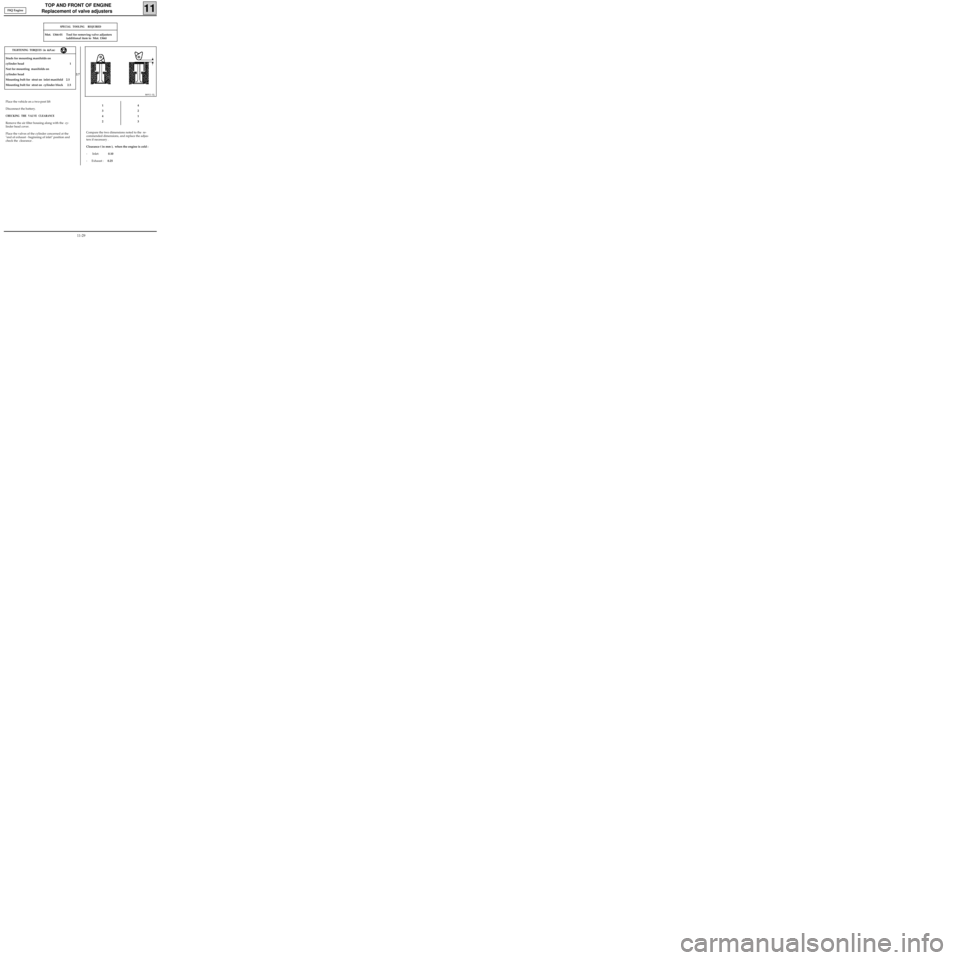
TOP AND FRONT OF ENGINE
Replacement of valve adjusters
11
SPECIAL TOOLING REQUIRED
Mot. 1366-01 Tool for removing valve adjusters
(additional item to Mot. 1366)
TIGHTENING TORQUES (in daN.m)
Studs for mounting manifolds on
cylinder head 1
Nut for mounting manifolds on
cylinder head 2.7
Mounting bolt for strut on inlet manifold 2.5
Mounting bolt for strut on cylinder block 2.5
Place the vehicle on a two-post lift
Disconnect the battery.
CHECKING THE VALVE CLEARANCE
Remove the air filter housing along with the cy-
linder head cover.
Place the valves of the cylinder concerned at the
"end of exhaust - beginning of inlet" position and
check the clearance .
86911-1S
1
3
4
24
2
1
3
Compare the two dimensions noted to the re-
commended dimensions, and replace the adjus-
ters if necessary .
Clearance ( in mm ), when the engine is cold :
- Inlet: 0.10
- Exhaust :0.25 F8Q Engine
11-29
Page 65 of 208
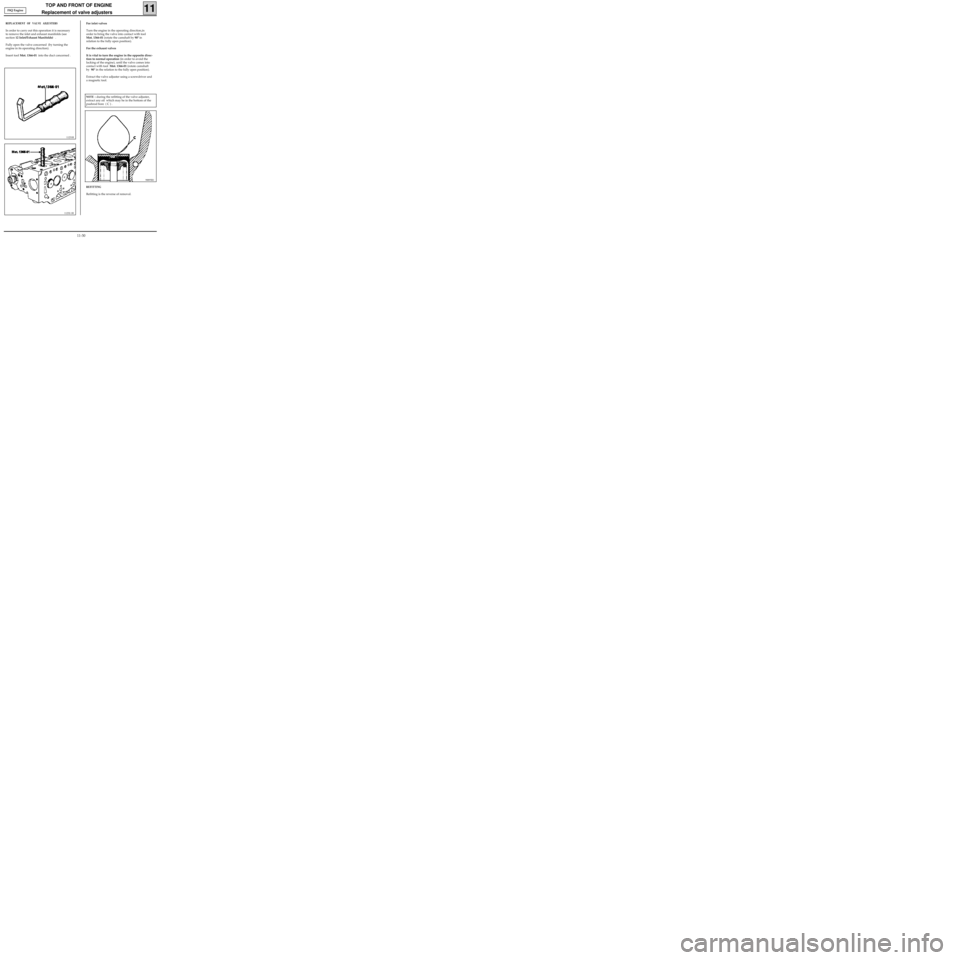
TOP AND FRONT OF ENGINE
Replacement of valve adjusters
11
REPLACEMENT OF VALVE ADJUSTERS
In order to carry out this operation it is necessary
to remove the inlet and exhaust manifolds (see
section 12 Inlet/Exhaust Manifolds) .
Fully open the valve concerned (by turning the
engine in its operating direction).
Insert tool Mot. 1366-01 into the duct concerned .
11231R
For inlet valves
Turn the engine in the operating direction,in
order to bring the valve into contact with tool
Mot. 1366-01 (rotate the camshaft by 90° in
relation to the fully open position).
For the exhaust valves
It is vital to turn the engine in the opposite direc-
tion to normal operation (in order to avoid the
locking of the engine), until the valve comes into
contact with tool Mot. 1366-01 (rotate camshaft
by 90° in the relation to the fully open position).
Extract the valve adjuster using a screwdriver and
a magnetic tool.
11232-1R
NOTE : during the refitting of the valve adjuster,
extract any oil which may be in the bottom of the
pushrod bore ( C ) .
98895R1
REFITTING
Refitting is the reverse of removal. F8Q Engine
11-30
Page 66 of 208
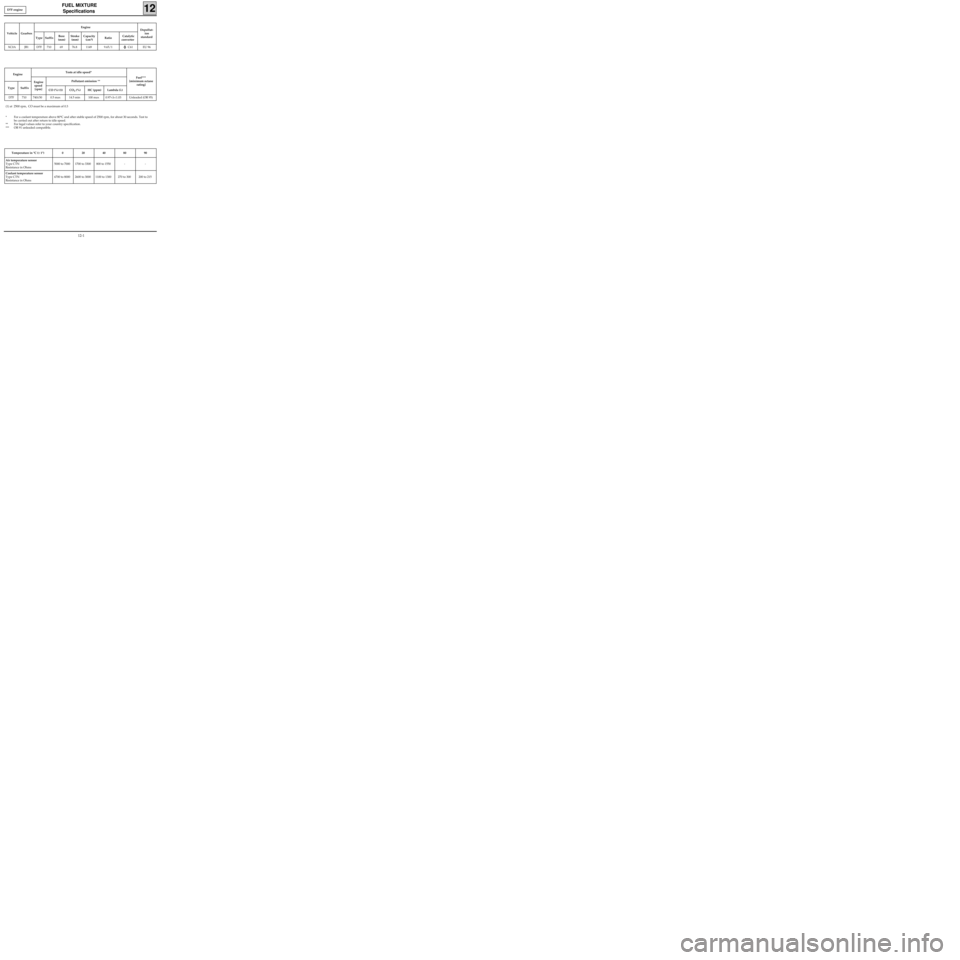
FUEL MIXTURE
Specifications
12
Vehicle GearboxEngine
Type SuffixBore
(mm)Stroke
(mm)Capacity
(cm
3)RatioCatalytic
converterDepollut-
ion
standard
XC0A JB1 D7F 710 69 76.8 1149 9.65/1 C61 EU 96
Temperature in °C (± 1°) 0 20 40 80 90
Air temperature sensor
Type CTN
Resistance in Ohms5000 to 7000 1700 to 3300 800 to 1550 - -
Coolant temperature sensor
Type CTN
Resistance in Ohms6700 to 8000 2600 to 3000 1100 to 1300 270 to 300 200 to 215
Engine
Type SuffixTests at idle speed*
Engine
speed
[rpm]Pollutant emission **
CO (%) (1) CO
2 (%) HC (ppm) Lambda (λ)Fuel***
[minimum octane
rating]
D7F 710 740±50 0.5 max 14.5 min 100 max 0.97<λ<1.03 Unleaded (OR 95)
(1) at 2500 rpm, CO must be a maximum of 0.3
* For a coolant temperature above 80°C and after stable speed of 2500 rpm, for about 30 seconds. Test to
be carried out after return to idle speed.
** For legal values refer to your country specification.
*** OR 91 unleaded compatible.D7F engine
12-1
Page 67 of 208
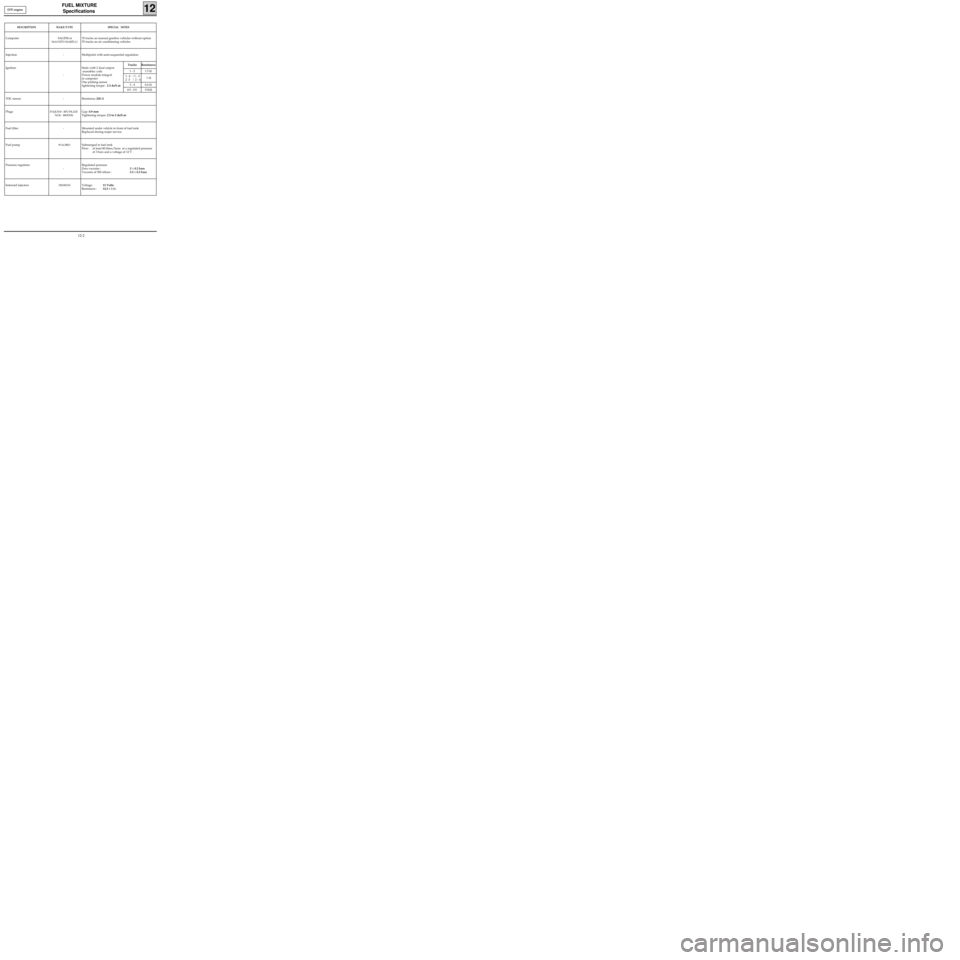
FUEL MIXTURE
Specifications
12
DESCRIPTIONMAKE/TYPESPECIAL NOTES
Computer SAGEM or
MAGNÉTI MARÉLLI
35 tracks on manual gearbox vehicles without option
55 tracks on air conditioning vehicles
Injection - Multipoint with semi-sequential regulation
Ignition
-Static with 2 dual output
monobloc coils
Power module integral
in computer
One pinking sensor
tightening torque : 2.5 daN.m
TDC sensor - Resistance 220 Ω
Plugs
EYQUEM : RFC50LZ2E
NGK : BKR5EKGap: 0.9 mm
Tightening torque: 2.5 to 3 daN.m
Fuel filter - Mounted under vehicle in front of fuel tank
Replaced during major service
Fuel pump
WALBROSubmerged in fuel tank
Flow: at least 80 litres/hour at a regulated pressure
of 3 bars and a voltage of 12 V
Pressure regulator
-Regulated pressure
Zero vacuum :3 ± 0.2 bars
Vacuum of 500 mbars :2.5 ± 0.2 bars
Solenoid injectors
SIEMENSVoltage:12 Volts
Resistance :14.5 ± 1 Ω
Tracks Resistance
1 - 2 1.5 Ω
1
- 4 |1 - 3
2 -3 | 2 - 41 Ω
3 - 4 0.6 Ω
HT - HT8 KΩ
D7F engine
12-2
Page 68 of 208
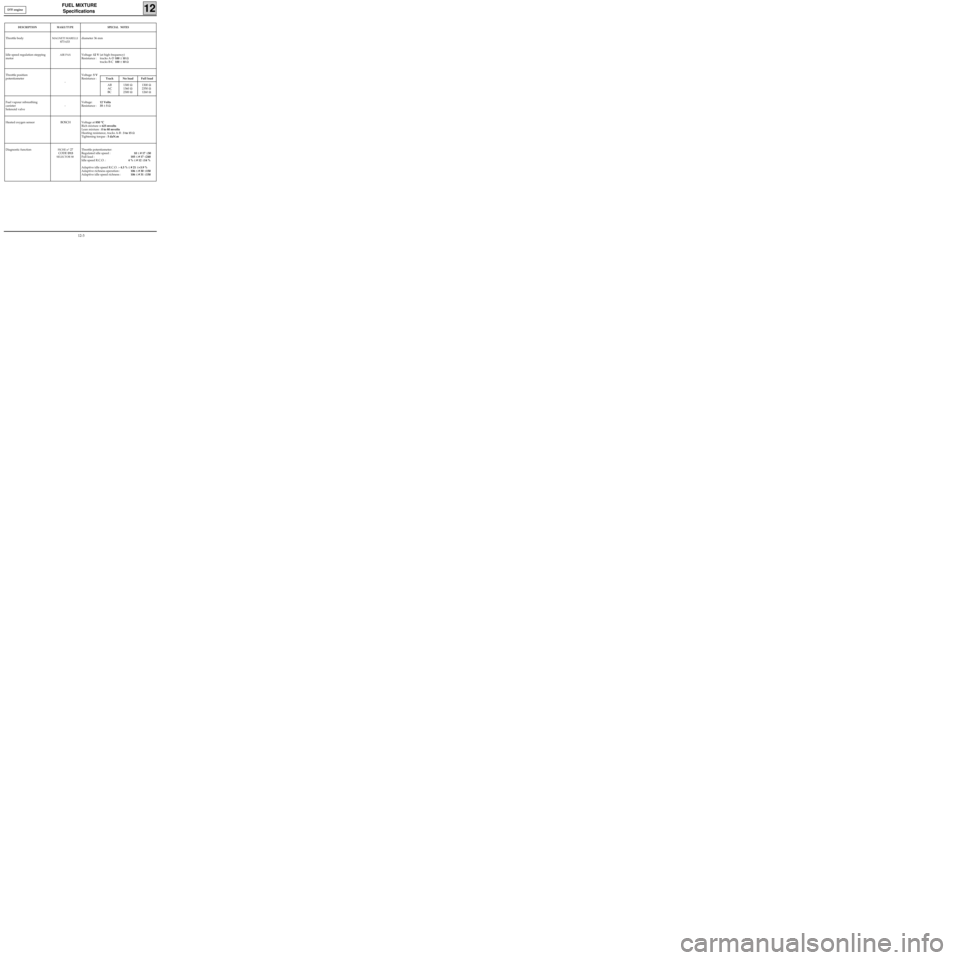
FUEL MIXTURE
Specifications
12
DESCRIPTIONMAKE/TYPESPECIAL NOTES
Throttle bodyMAGNETI MARELLI
873 633diameter 36 mm
Idle speed regulation stepping
motor
AIR PAXVoltage: 12 V (at high frequency)
Resistance : tracks A-D100 ± 10 Ω
tracks B-C100 ± 10 Ω
Throttle position
potentiometer
-Voltage: 5 V
Resistance :
Fuel vapour rebreathing
canister
Solenoid valve-Voltage:12 Volts
Resistance :35 ± 5 Ω
Heated oxygen sensor BOSCH Voltage at 850 °C
Rich mixture > 625 mvolts
Lean mixture : 0 to 80 mvolts
Heating resistance, tracks A-B : 3 to 15 Ω
Tightening torque : 5 daN.m
Diagnostic function
FICHE n° 27
CODE D13
SELECTOR S8
Throttle potentiometer:
Regulated idle speed :10 ≤ # 17 ≤50
Full load :185 ≤ # 17 ≤240
Idle speed R.C.O. :4 % ≤ # 12 ≤14 %
Adaptive idle speed R.C.O. :- 4.3 % ≤ # 21 ≤+3.9 %
Adaptive richness operation
:106 ≤ # 30 ≤150
Adaptive idle speed richness :106 ≤ # 31 ≤150
Track No load Full load
AB
AC
BC1300 Ω
1360 Ω
2300 Ω1300 Ω
2350 Ω
1260 Ω
D7F engine
12-3
Page 69 of 208
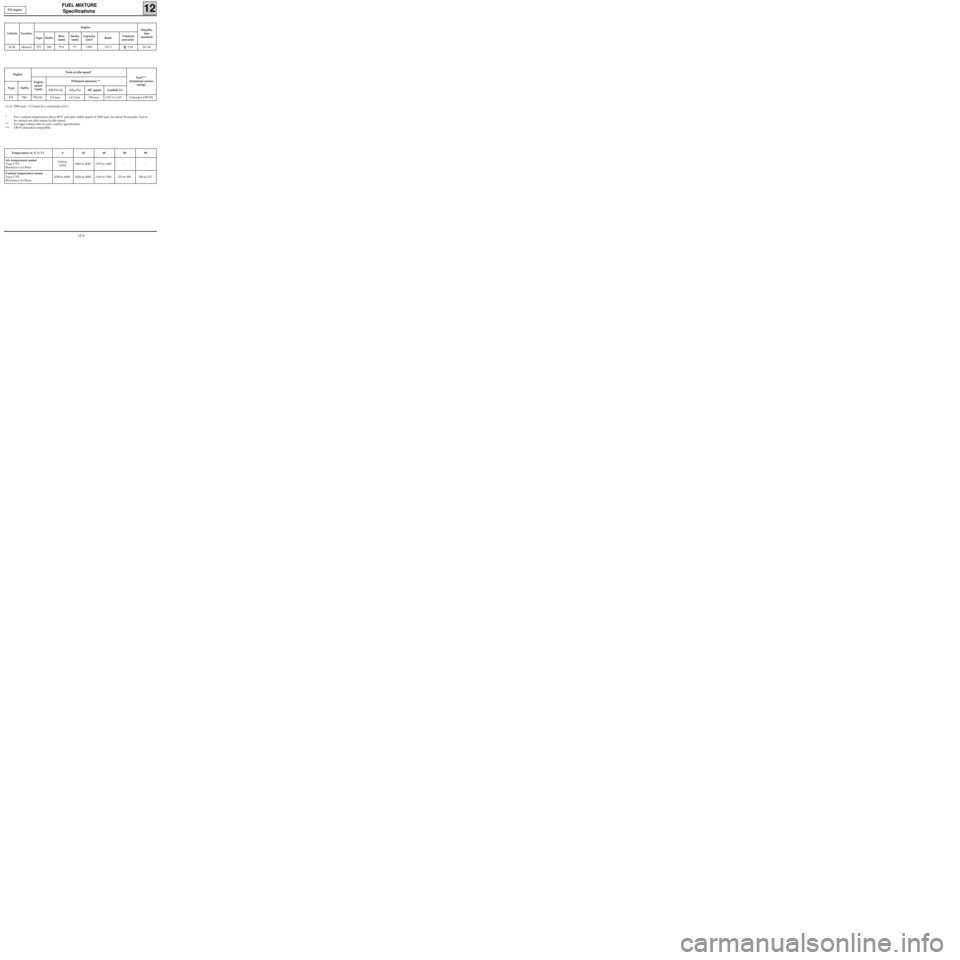
FUEL MIXTURE
Specifications
12
Vehicle GearboxEngine
Type SuffixBore
(mm)Stroke
(mm)Capacity
(cm
3)RatioCatalytic
converterDepollu-
tion
standard
XC0C Manual E7J 780 75.8 77 1390 9.5/1 C63 EU 96
Temperature in °C (± 1°) 0 20 40 80 90
Air temperature sensor
Type CTN
Resistance in Ohms7470 to
119703060 to 4045 1315 to 1600 - -
Coolant temperature sensor
Type CTN
Resistance in Ohms6700 to 8000 2600 to 3000 1100 to 1300 270 to 300 200 to 215
Engine
Type SuffixTests at idle speed*
Engine
speed
[rpm]Pollutant emission **
CO (%) (1) CO
2 (%) HC (ppm) Lambda (λ)Fuel***
(minimum octane
rating)
E7J 780 750±50 0.5 max 14.5 min 100 max 0.97<λ<1.03 Unleaded (OR 95)
(1) at 2500 rpm, CO must be a maximum of 0.3
* For a coolant temperature above 80°C and after stable speed of 2500 rpm, for about 30 seconds. Test to
be carried out after return to idle speed.
** For legal values refer to your country specification.
*** OR 91 unleaded compatible.E7J engine
12-4
Page 70 of 208
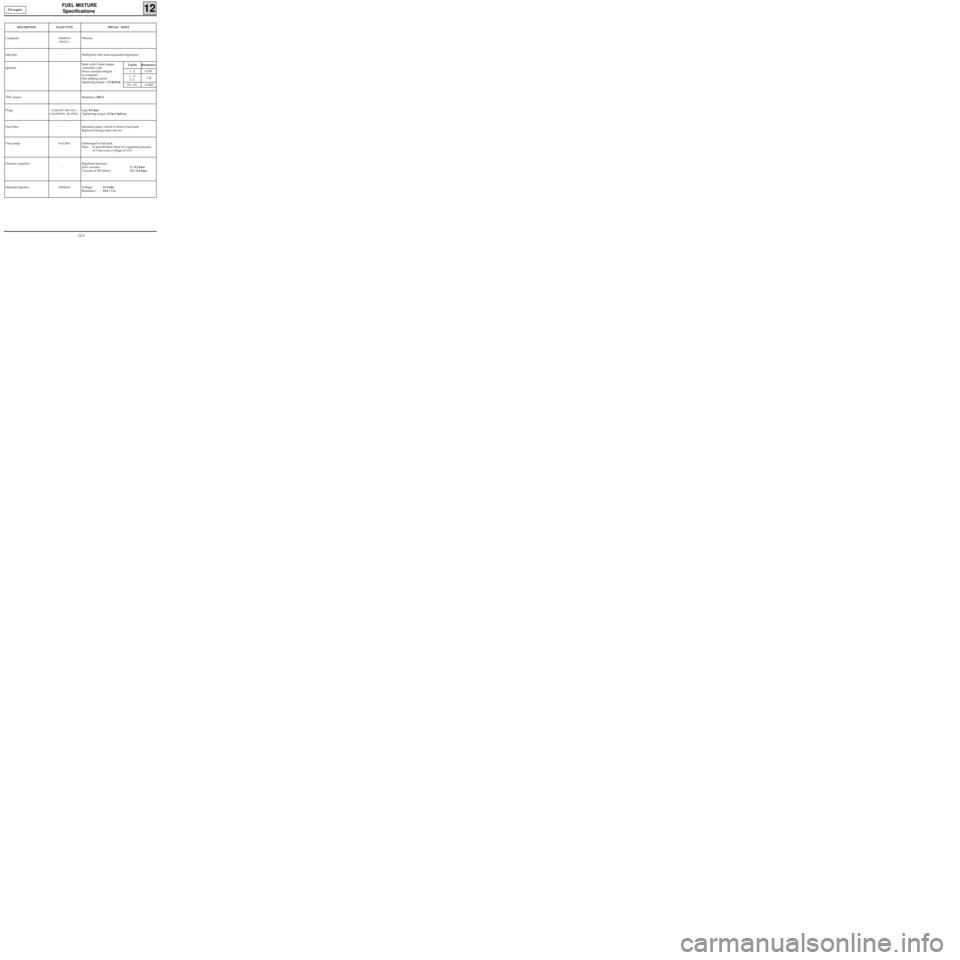
FUEL MIXTURE
Specifications
12
DESCRIPTIONMAKE/TYPESPECIAL NOTES
ComputerSIEMENS
FENIX 555tracks
Injection - Multipoint with semi-sequential regulation
Ignition
-Static with 2 dual output
monobloc coils
Power module integral
in computer
One pinking sensor
tightening torque : 2.5 daN.m
TDC sensor - Resistance 220 Ω
Plugs
EYQUEM : RFC52LS
CHAMPION
: RC10PYC
Gap: 0.9 mm
Tightening torque: 2.5 to 3 daN.m
Fuel filter - Mounted under vehicle in front of fuel tank
Replaced during major service
Fuel pump
WALBROSubmerged in fuel tank
Flow: at least 80 litres/hour at a regulated pressure
of 3 bars and a voltage of 12 V
Pressure regulator
-
Regulated pressure
Zero vacuum :3 ± 0.2 bars
Vacuum of 500 mbars :2.5 ± 0.2 bars
Solenoid injectors
SIEMENSVoltage:12 Volts
Resistance :14.5 ± 1 Ω
Tracks Resistance
1 - 2 0.5 Ω
1 - 3
2 -31 Ω
HT - HT10 KΩ
E7J engine
12-5