TOYOTA RAV4 2006 Service Repair Manual
Manufacturer: TOYOTA, Model Year: 2006, Model line: RAV4, Model: TOYOTA RAV4 2006Pages: 2000, PDF Size: 45.84 MB
Page 1931 of 2000
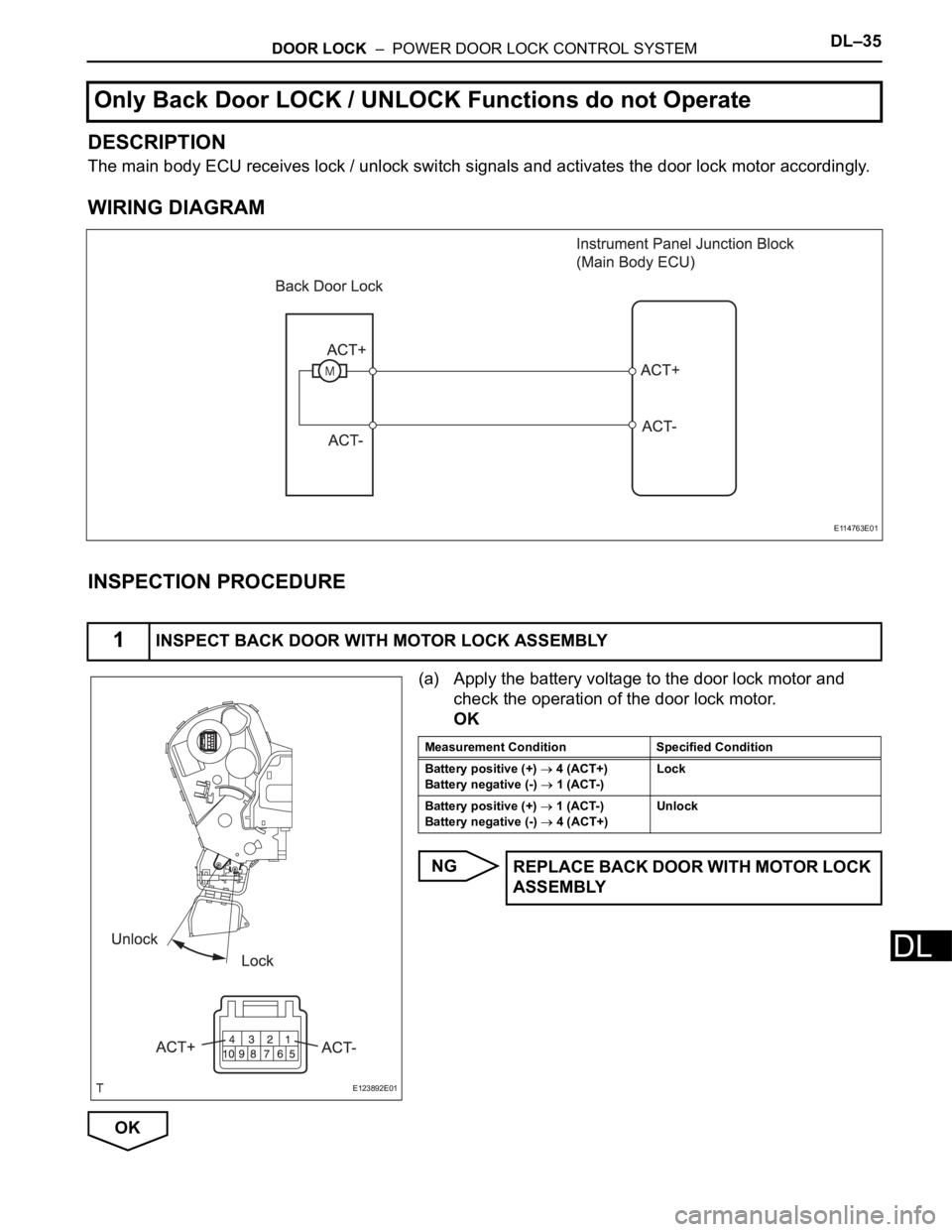
DOOR LOCK – POWER DOOR LOCK CONTROL SYSTEMDL–35
DL
DESCRIPTION
The main body ECU receives lock / unlock switch signals and activates the door lock motor accordingly.
WIRING DIAGRAM
INSPECTION PROCEDURE
(a) Apply the battery voltage to the door lock motor and
check the operation of the door lock motor.
OK
NG
OK
Only Back Door LOCK / UNLOCK Functions do not Operate
1INSPECT BACK DOOR WITH MOTOR LOCK ASSEMBLY
E114763E01
E123892E01
Measurement Condition Specified Condition
Battery positive (+)
4 (ACT+)
Battery negative (-)
1 (ACT-)Lock
Battery positive (+)
1 (ACT-)
Battery negative (-)
4 (ACT+)Unlock
REPLACE BACK DOOR WITH MOTOR LOCK
ASSEMBLY
Page 1932 of 2000
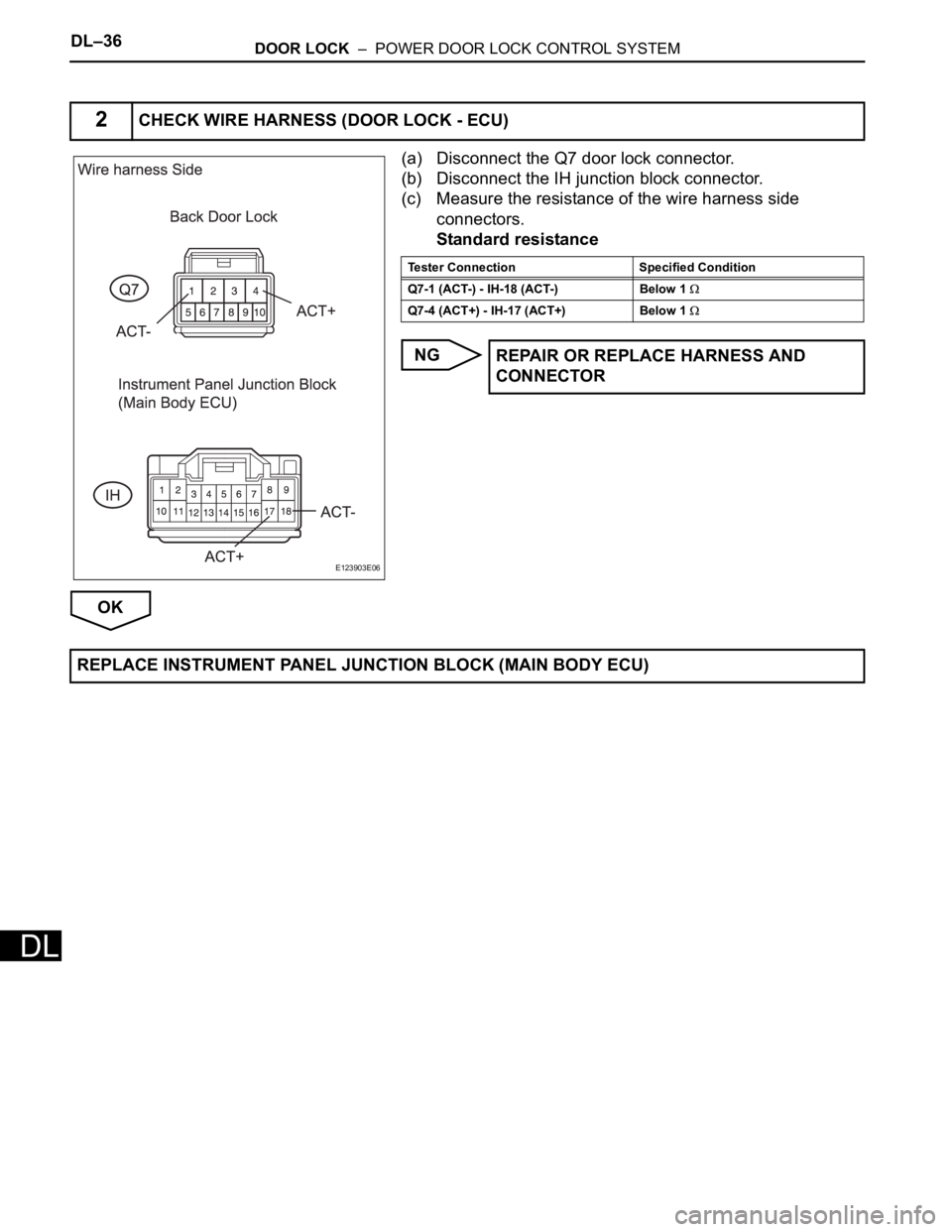
DL–36DOOR LOCK – POWER DOOR LOCK CONTROL SYSTEM
DL
(a) Disconnect the Q7 door lock connector.
(b) Disconnect the IH junction block connector.
(c) Measure the resistance of the wire harness side
connectors.
Standard resistance
NG
OK
2CHECK WIRE HARNESS (DOOR LOCK - ECU)
E123903E06
Tester Connection Specified Condition
Q7-1 (ACT-) - IH-18 (ACT-) Below 1
Q7-4 (ACT+) - IH-17 (ACT+) Below 1
REPAIR OR REPLACE HARNESS AND
CONNECTOR
REPLACE INSTRUMENT PANEL JUNCTION BLOCK (MAIN BODY ECU)
Page 1933 of 2000
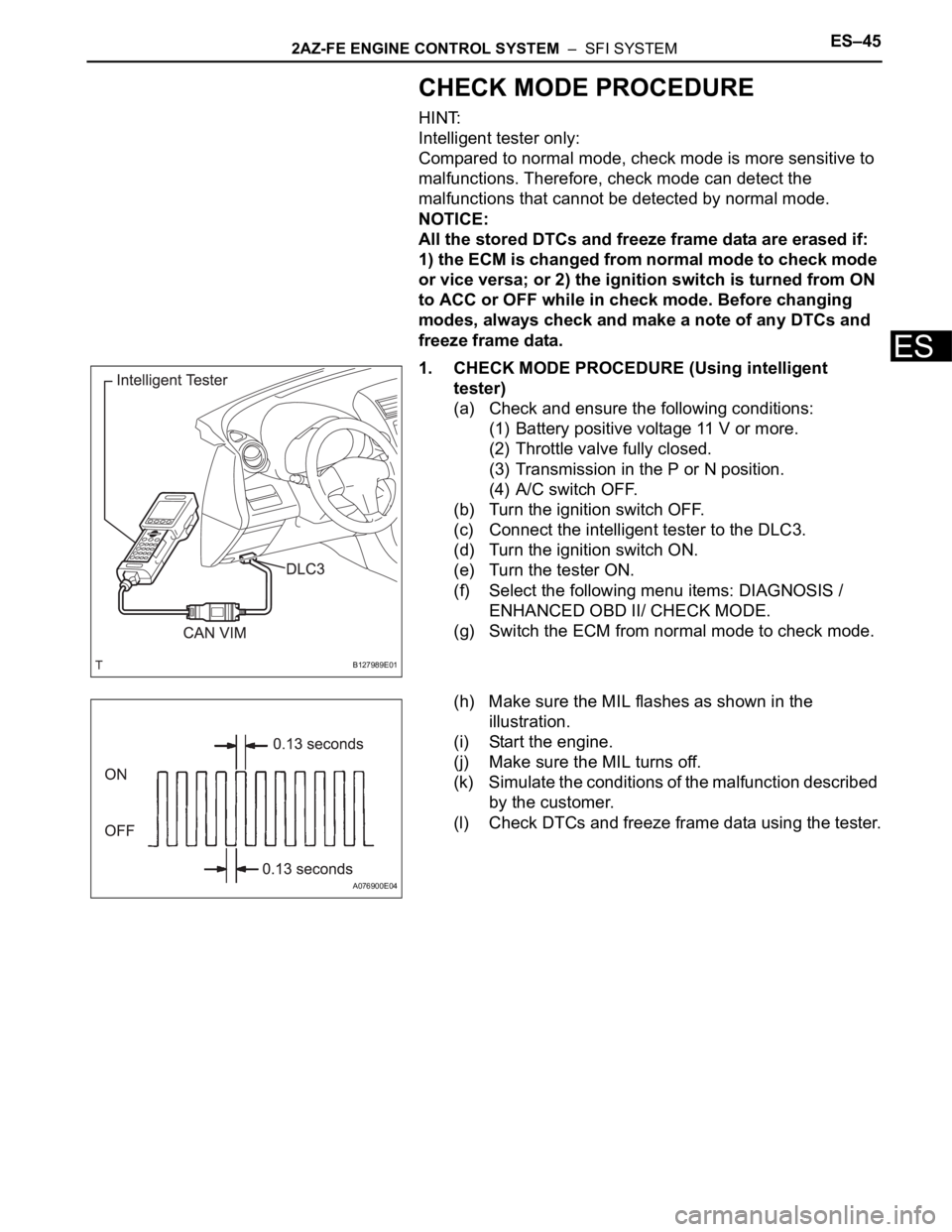
2AZ-FE ENGINE CONTROL SYSTEM – SFI SYSTEMES–45
ES
CHECK MODE PROCEDURE
HINT:
Intelligent tester only:
Compared to normal mode, check mode is more sensitive to
malfunctions. Therefore, check mode can detect the
malfunctions that cannot be detected by normal mode.
NOTICE:
All the stored DTCs and freeze frame data are erased if:
1) the ECM is changed from normal mode to check mode
or vice versa; or 2) the ignition switch is turned from ON
to ACC or OFF while in check mode. Before changing
modes, always check and make a note of any DTCs and
freeze frame data.
1. CHECK MODE PROCEDURE (Using intelligent
tester)
(a) Check and ensure the following conditions:
(1) Battery positive voltage 11 V or more.
(2) Throttle valve fully closed.
(3) Transmission in the P or N position.
(4) A/C switch OFF.
(b) Turn the ignition switch OFF.
(c) Connect the intelligent tester to the DLC3.
(d) Turn the ignition switch ON.
(e) Turn the tester ON.
(f) Select the following menu items: DIAGNOSIS /
ENHANCED OBD II/ CHECK MODE.
(g) Switch the ECM from normal mode to check mode.
(h) Make sure the MIL flashes as shown in the
illustration.
(i) Start the engine.
(j) Make sure the MIL turns off.
(k) Simulate the conditions of the malfunction described
by the customer.
(l) Check DTCs and freeze frame data using the tester.
B127989E01
A076900E04
Page 1934 of 2000
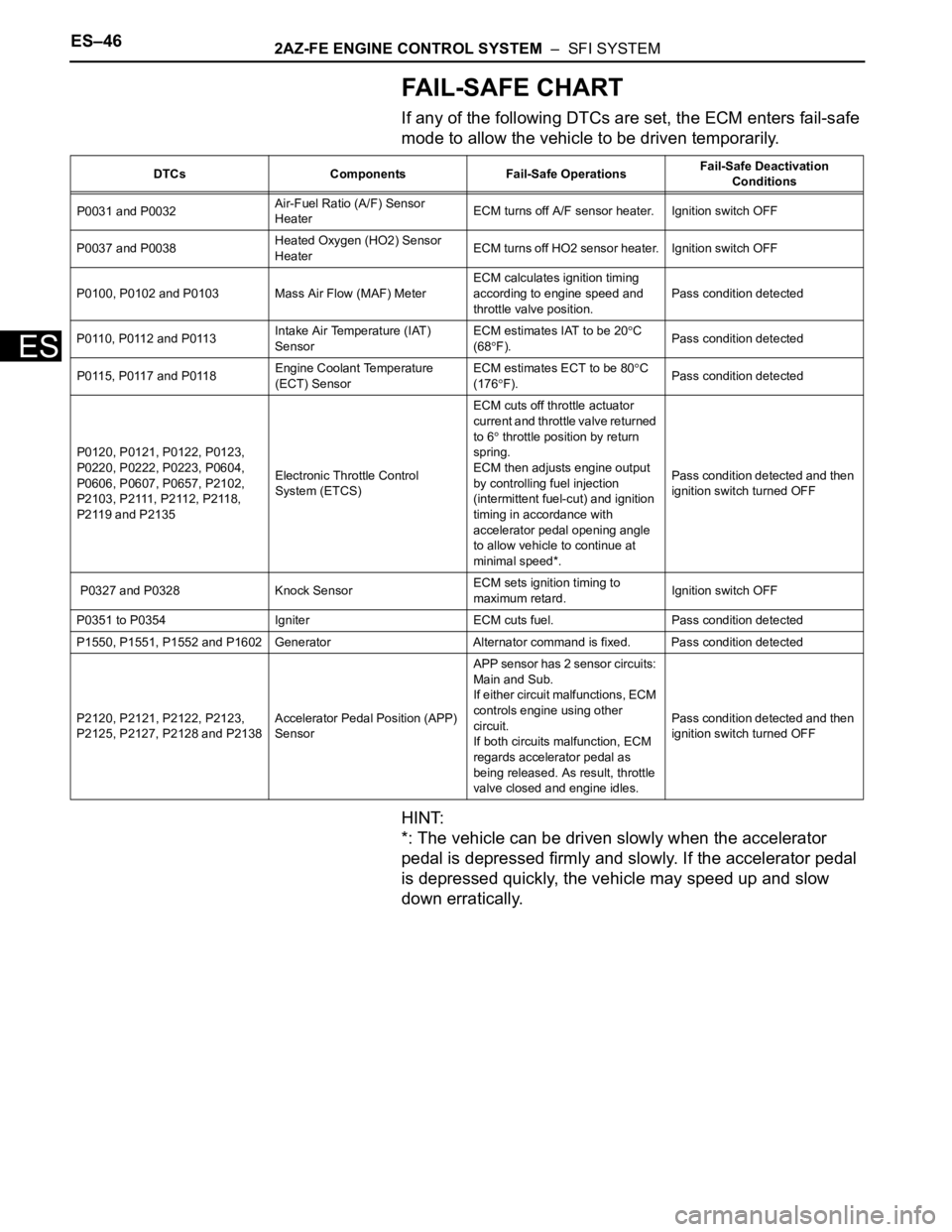
ES–462AZ-FE ENGINE CONTROL SYSTEM – SFI SYSTEM
ES
FAIL-SAFE CHART
If any of the following DTCs are set, the ECM enters fail-safe
mode to allow the vehicle to be driven temporarily.
HINT:
*: The vehicle can be driven slowly when the accelerator
pedal is depressed firmly and slowly. If the accelerator pedal
is depressed quickly, the vehicle may speed up and slow
down erratically.
DTCs Components Fail-Safe OperationsFail-Safe Deactivation
Conditions
P0031 and P0032Air-Fuel Ratio (A/F) Sensor
HeaterECM turns off A/F sensor heater. Ignition switch OFF
P0037 and P0038Heated Oxygen (HO2) Sensor
HeaterECM turns off HO2 sensor heater. Ignition switch OFF
P0100, P0102 and P0103 Mass Air Flow (MAF) MeterECM calculates ignition timing
according to engine speed and
throttle valve position.Pass condition detected
P0110, P0112 and P0113Intake Air Temperature (IAT)
SensorECM estimates IAT to be 20
C
(68
F).Pass condition detected
P0115, P0117 and P0118Engine Coolant Temperature
(ECT) SensorECM estimates ECT to be 80
C
(176
F).Pass condition detected
P0120, P0121, P0122, P0123,
P0220, P0222, P0223, P0604,
P0606, P0607, P0657, P2102,
P2103, P2111, P2112, P2118,
P2119 and P2135Electronic Throttle Control
System (ETCS)ECM cuts off throttle actuator
current and throttle valve returned
to 6
throttle position by return
spring.
ECM then adjusts engine output
by controlling fuel injection
(intermittent fuel-cut) and ignition
timing in accordance with
accelerator pedal opening angle
to allow vehicle to continue at
minimal speed*.Pass condition detected and then
ignition switch turned OFF
P0327 and P0328 Knock SensorECM sets ignition timing to
maximum retard.Ignition switch OFF
P0351 to P0354 Igniter ECM cuts fuel. Pass condition detected
P1550, P1551, P1552 and P1602 Generator Alternator command is fixed. Pass condition detected
P2120, P2121, P2122, P2123,
P2125, P2127, P2128 and P2138Accelerator Pedal Position (APP)
SensorAPP sensor has 2 sensor circuits:
Main and Sub.
If either circuit malfunctions, ECM
controls engine using other
circuit.
If both circuits malfunction, ECM
regards accelerator pedal as
being released. As result, throttle
valve closed and engine idles.Pass condition detected and then
ignition switch turned OFF
Page 1935 of 2000
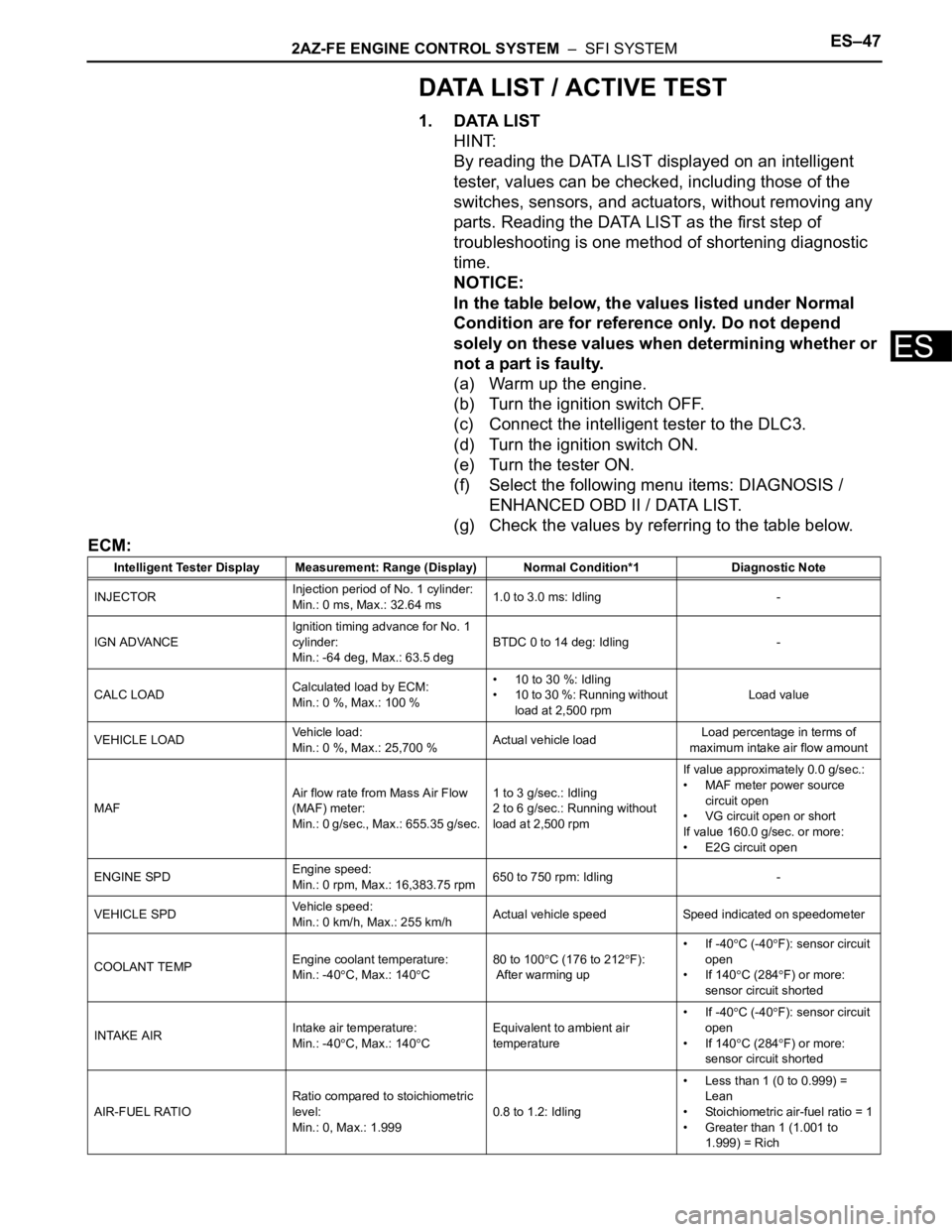
2AZ-FE ENGINE CONTROL SYSTEM – SFI SYSTEMES–47
ES
DATA LIST / ACTIVE TEST
1. DATA LIST
HINT:
By reading the DATA LIST displayed on an intelligent
tester, values can be checked, including those of the
switches, sensors, and actuators, without removing any
parts. Reading the DATA LIST as the first step of
troubleshooting is one method of shortening diagnostic
time.
NOTICE:
In the table below, the values listed under Normal
Condition are for reference only. Do not depend
solely on these values when determining whether or
not a part is faulty.
(a) Warm up the engine.
(b) Turn the ignition switch OFF.
(c) Connect the intelligent tester to the DLC3.
(d) Turn the ignition switch ON.
(e) Turn the tester ON.
(f) Select the following menu items: DIAGNOSIS /
ENHANCED OBD II / DATA LIST.
(g) Check the values by referring to the table below.
ECM:
Intelligent Tester Display Measurement: Range (Display) Normal Condition*1 Diagnostic Note
INJECTORInjection period of No. 1 cylinder:
Min.: 0 ms, Max.: 32.64 ms1.0 to 3.0 ms: Idling -
IGN ADVANCE Ignition timing advance for No. 1
cylinder:
Min.: -64 deg, Max.: 63.5 degBTDC 0 to 14 deg: Idling -
CALC LOADCalculated load by ECM:
Min.: 0 %, Max.: 100 %• 10 to 30 %: Idling
• 10 to 30 %: Running without
load at 2,500 rpmLoad value
VEHICLE LOADVehicle load:
Min.: 0 %, Max.: 25,700 %Actual vehicle loadLoad percentage in terms of
maximum intake air flow amount
MAFAir flow rate from Mass Air Flow
(MAF) meter:
Min.: 0 g/sec., Max.: 655.35 g/sec.1 to 3 g/sec.: Idling
2 to 6 g/sec.: Running without
load at 2,500 rpmIf value approximately 0.0 g/sec.:
• MAF meter power source
circuit open
• VG circuit open or short
If value 160.0 g/sec. or more:
• E2G circuit open
ENGINE SPDEngine speed:
Min.: 0 rpm, Max.: 16,383.75 rpm650 to 750 rpm: Idling -
VEHICLE SPDVehicle speed:
Min.: 0 km/h, Max.: 255 km/hActual vehicle speed Speed indicated on speedometer
COOLANT TEMPEngine coolant temperature:
Min.: -40
C, Max.: 140C80 to 100C (176 to 212F):
After warming up• If -40
C (-40F): sensor circuit
open
• If 140
C (284F) or more:
sensor circuit shorted
INTAKE AIRIntake air temperature:
Min.: -40
C, Max.: 140CEquivalent to ambient air
temperature• If -40
C (-40F): sensor circuit
open
• If 140
C (284F) or more:
sensor circuit shorted
AIR-FUEL RATIORatio compared to stoichiometric
level:
Min.: 0, Max.: 1.9990.8 to 1.2: Idling• Less than 1 (0 to 0.999) =
Lean
• Stoichiometric air-fuel ratio = 1
• Greater than 1 (1.001 to
1.999) = Rich
Page 1936 of 2000
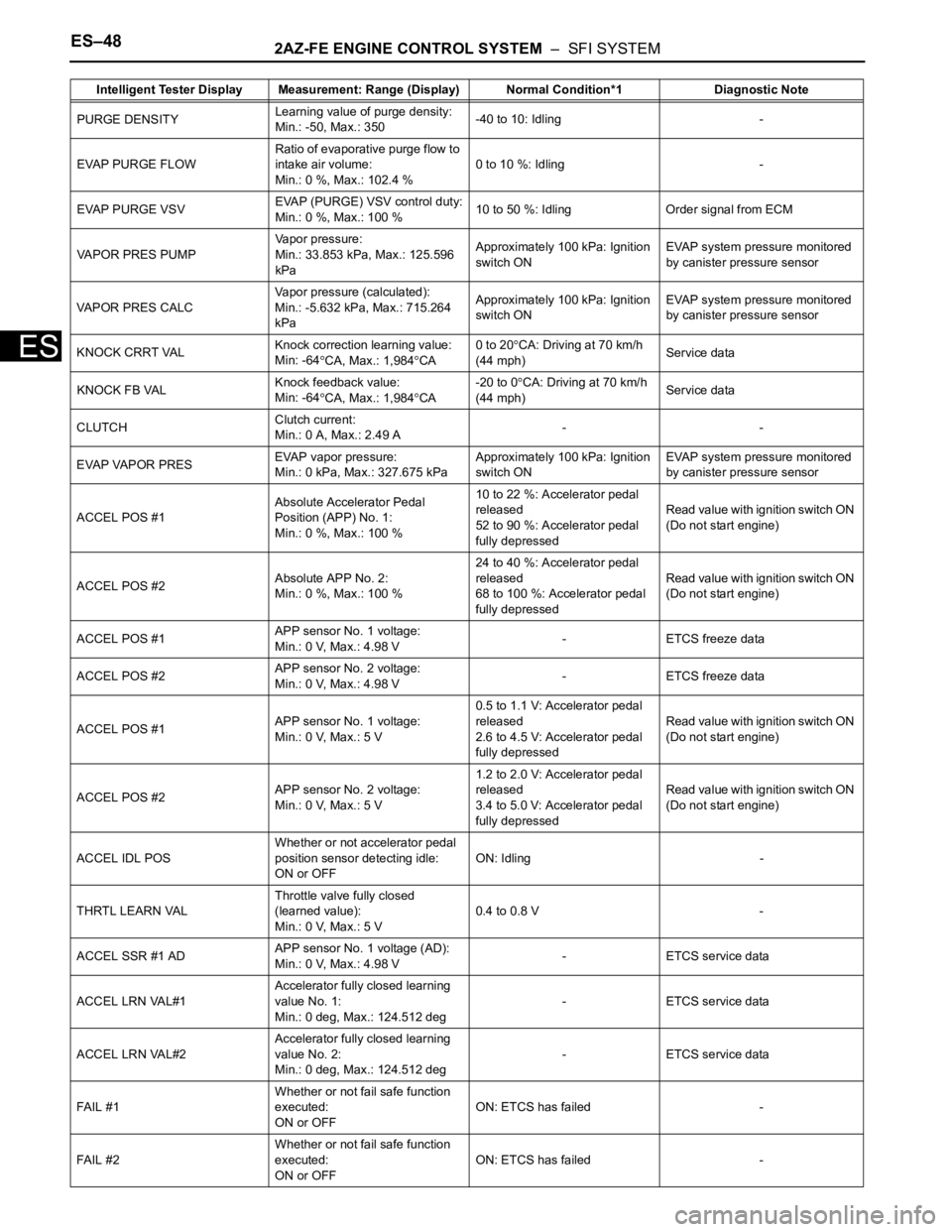
ES–482AZ-FE ENGINE CONTROL SYSTEM – SFI SYSTEM
ES
PURGE DENSITY Learning value of purge density:
Min.: -50, Max.: 350-40 to 10: Idling -
EVAP PURGE FLOWRatio of evaporative purge flow to
intake air volume:
Min.: 0 %, Max.: 102.4 %0 to 10 %: Idling -
EVAP PURGE VSVEVAP (PURGE) VSV control duty:
Min.: 0 %, Max.: 100 %10 to 50 %: Idling Order signal from ECM
VAPOR PRES PUMPVapor pressure:
Min.: 33.853 kPa, Max.: 125.596
kPaApproximately 100 kPa: Ignition
switch ONEVAP system pressure monitored
by canister pressure sensor
VAPOR PRES CALCVapor pressure (calculated):
Min.: -5.632 kPa, Max.: 715.264
kPaApproximately 100 kPa: Ignition
switch ONEVAP system pressure monitored
by canister pressure sensor
KNOCK CRRT VALKnock correction learning value:
Min: -64
CA, Max.: 1,984CA0 to 20
CA: Driving at 70 km/h
(44 mph)Service data
KNOCK FB VALKnock feedback value:
Min: -64
CA, Max.: 1,984CA-20 to 0
CA: Driving at 70 km/h
(44 mph)Service data
CLUTCHClutch current:
Min.: 0 A, Max.: 2.49 A--
EVAP VAPOR PRESEVAP vapor pressure:
Min.: 0 kPa, Max.: 327.675 kPaApproximately 100 kPa: Ignition
switch ONEVAP system pressure monitored
by canister pressure sensor
ACCEL POS #1Absolute Accelerator Pedal
Position (APP) No. 1:
Min.: 0 %, Max.: 100 %10 to 22 %: Accelerator pedal
released
52 to 90 %: Accelerator pedal
fully depressedRead value with ignition switch ON
(Do not start engine)
ACCEL POS #2Absolute APP No. 2:
Min.: 0 %, Max.: 100 %24 to 40 %: Accelerator pedal
released
68 to 100 %: Accelerator pedal
fully depressedRead value with ignition switch ON
(Do not start engine)
ACCEL POS #1APP sensor No. 1 voltage:
Min.: 0 V, Max.: 4.98 V- ETCS freeze data
ACCEL POS #2APP sensor No. 2 voltage:
Min.: 0 V, Max.: 4.98 V- ETCS freeze data
ACCEL POS #1APP sensor No. 1 voltage:
Min.: 0 V, Max.: 5 V0.5 to 1.1 V: Accelerator pedal
released
2.6 to 4.5 V: Accelerator pedal
fully depressedRead value with ignition switch ON
(Do not start engine)
ACCEL POS #2APP sensor No. 2 voltage:
Min.: 0 V, Max.: 5 V1.2 to 2.0 V: Accelerator pedal
released
3.4 to 5.0 V: Accelerator pedal
fully depressedRead value with ignition switch ON
(Do not start engine)
ACCEL IDL POSWhether or not accelerator pedal
position sensor detecting idle:
ON or OFFON: Idling -
THRTL LEARN VALThrottle valve fully closed
(learned value):
Min.: 0 V, Max.: 5 V0.4 to 0.8 V -
ACCEL SSR #1 ADAPP sensor No. 1 voltage (AD):
Min.: 0 V, Max.: 4.98 V-ETCS service data
ACCEL LRN VAL#1 Accelerator fully closed learning
value No. 1:
Min.: 0 deg, Max.: 124.512 deg-ETCS service data
ACCEL LRN VAL#2Accelerator fully closed learning
value No. 2:
Min.: 0 deg, Max.: 124.512 deg-ETCS service data
FAIL #1 Whether or not fail safe function
executed:
ON or OFFON: ETCS has failed -
FAIL #2 Whether or not fail safe function
executed:
ON or OFFON: ETCS has failed - Intelligent Tester Display Measurement: Range (Display) Normal Condition*1 Diagnostic Note
Page 1937 of 2000
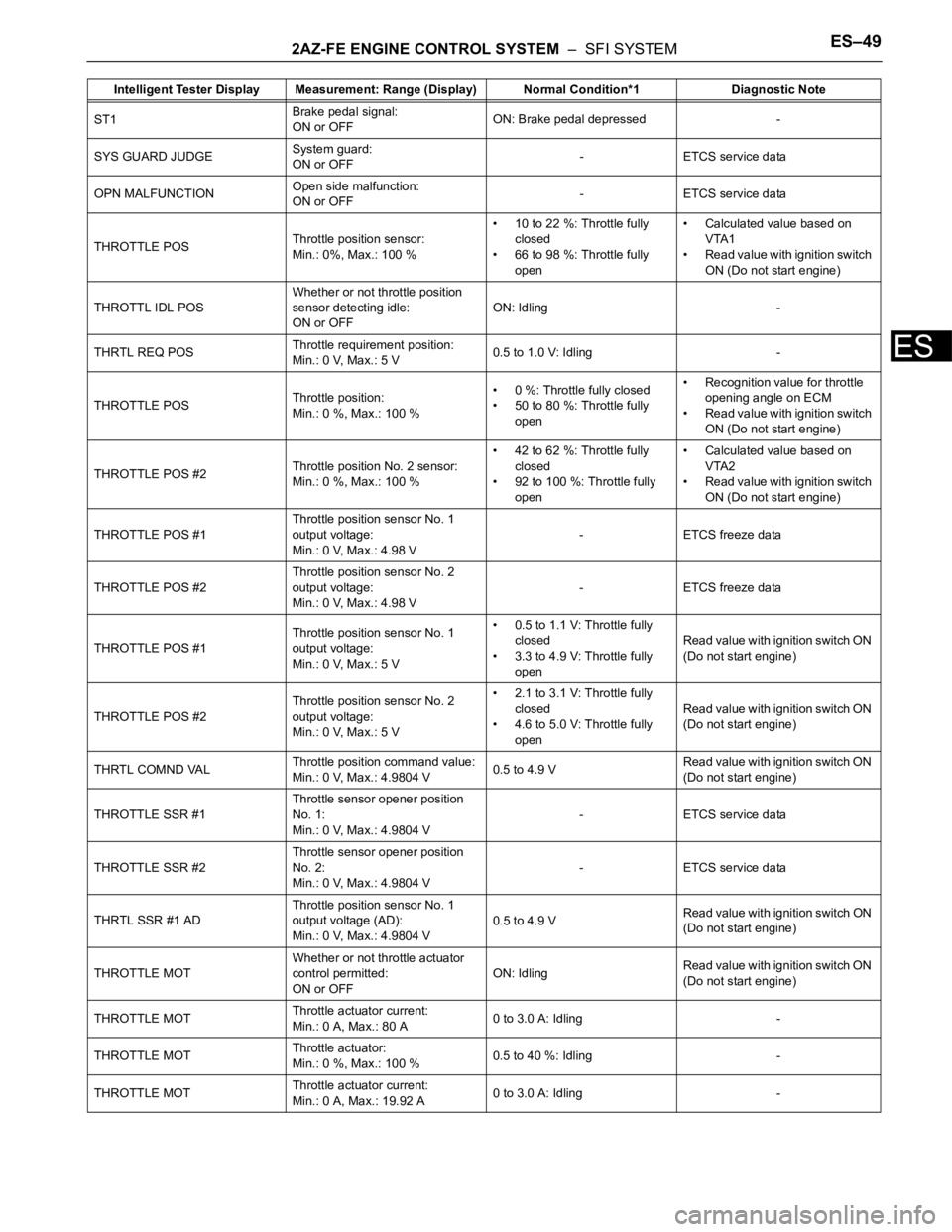
2AZ-FE ENGINE CONTROL SYSTEM – SFI SYSTEMES–49
ES
ST1Brake pedal signal:
ON or OFFON: Brake pedal depressed -
SYS GUARD JUDGESystem guard:
ON or OFF-ETCS service data
OPN MALFUNCTIONOpen side malfunction:
ON or OFF-ETCS service data
THROTTLE POSThrottle position sensor:
Min.: 0%, Max.: 100 %• 10 to 22 %: Throttle fully
closed
• 66 to 98 %: Throttle fully
open• Calculated value based on
VTA1
• Read value with ignition switch
ON (Do not start engine)
THROTTL IDL POSWhether or not throttle position
sensor detecting idle:
ON or OFFON: Idling -
THRTL REQ POSThrottle requirement position:
Min.: 0 V, Max.: 5 V0.5 to 1.0 V: Idling -
THROTTLE POSThrottle position:
Min.: 0 %, Max.: 100 %• 0 %: Throttle fully closed
• 50 to 80 %: Throttle fully
open• Recognition value for throttle
opening angle on ECM
• Read value with ignition switch
ON (Do not start engine)
THROTTLE POS #2Throttle position No. 2 sensor:
Min.: 0 %, Max.: 100 %• 42 to 62 %: Throttle fully
closed
• 92 to 100 %: Throttle fully
open• Calculated value based on
VTA2
• Read value with ignition switch
ON (Do not start engine)
THROTTLE POS #1Throttle position sensor No. 1
output voltage:
Min.: 0 V, Max.: 4.98 V- ETCS freeze data
THROTTLE POS #2Throttle position sensor No. 2
output voltage:
Min.: 0 V, Max.: 4.98 V- ETCS freeze data
THROTTLE POS #1Throttle position sensor No. 1
output voltage:
Min.: 0 V, Max.: 5 V• 0.5 to 1.1 V: Throttle fully
closed
• 3.3 to 4.9 V: Throttle fully
openRead value with ignition switch ON
(Do not start engine)
THROTTLE POS #2Throttle position sensor No. 2
output voltage:
Min.: 0 V, Max.: 5 V• 2.1 to 3.1 V: Throttle fully
closed
• 4.6 to 5.0 V: Throttle fully
openRead value with ignition switch ON
(Do not start engine)
THRTL COMND VALThrottle position command value:
Min.: 0 V, Max.: 4.9804 V0.5 to 4.9 VRead value with ignition switch ON
(Do not start engine)
THROTTLE SSR #1Throttle sensor opener position
No. 1:
Min.: 0 V, Max.: 4.9804 V-ETCS service data
THROTTLE SSR #2Throttle sensor opener position
No. 2:
Min.: 0 V, Max.: 4.9804 V-ETCS service data
THRTL SSR #1 ADThrottle position sensor No. 1
output voltage (AD):
Min.: 0 V, Max.: 4.9804 V0.5 to 4.9 VRead value with ignition switch ON
(Do not start engine)
THROTTLE MOTWhether or not throttle actuator
control permitted:
ON or OFFON: IdlingRead value with ignition switch ON
(Do not start engine)
THROTTLE MOTThrottle actuator current:
Min.: 0 A, Max.: 80 A0 to 3.0 A: Idling -
THROTTLE MOTThrottle actuator:
Min.: 0 %, Max.: 100 %0.5 to 40 %: Idling -
THROTTLE MOT Throttle actuator current:
Min.: 0 A, Max.: 19.92 A0 to 3.0 A: Idling - Intelligent Tester Display Measurement: Range (Display) Normal Condition*1 Diagnostic Note
Page 1938 of 2000
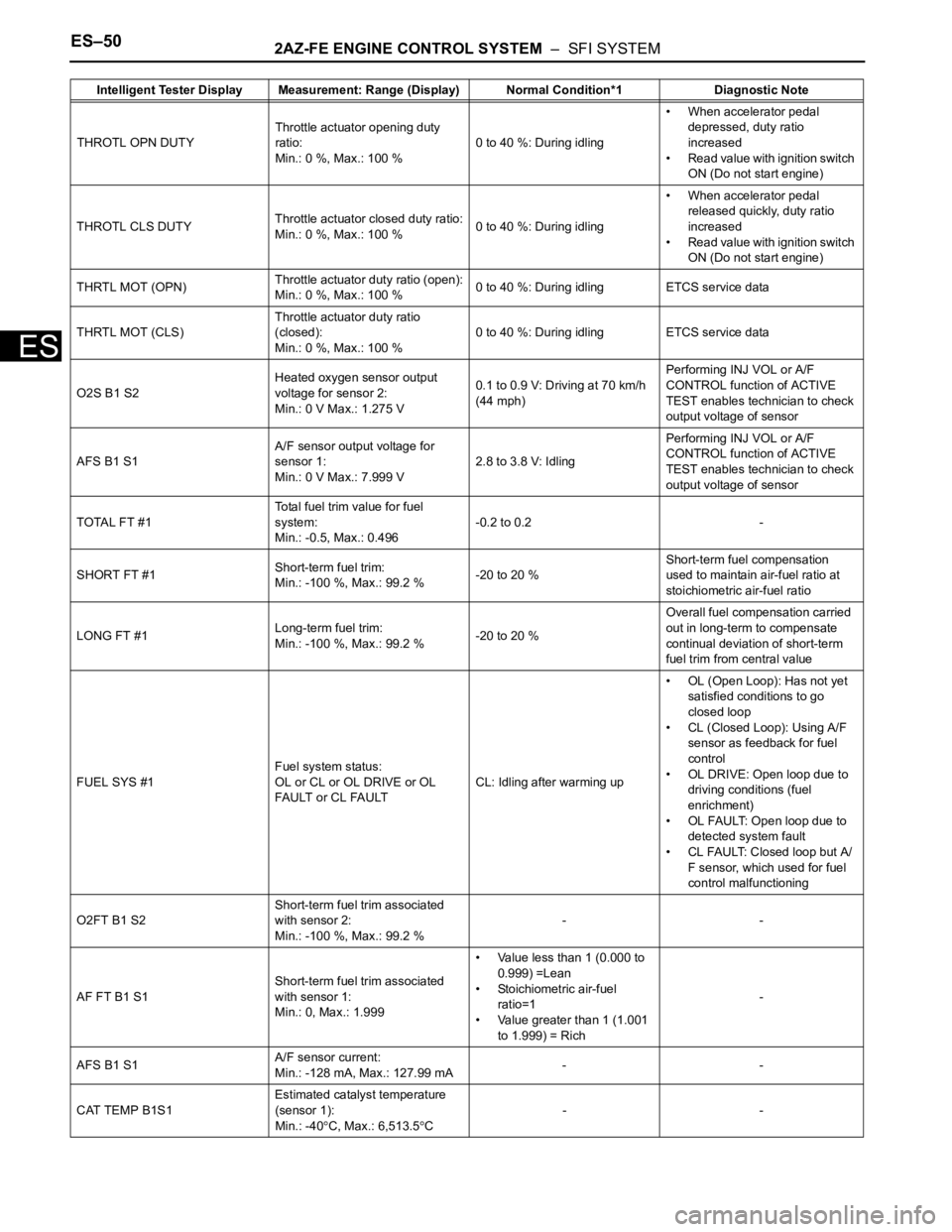
ES–502AZ-FE ENGINE CONTROL SYSTEM – SFI SYSTEM
ES
THROTL OPN DUTYThrottle actuator opening duty
ratio:
Min.: 0 %, Max.: 100 %0 to 40 %: During idling• When accelerator pedal
depressed, duty ratio
increased
• Read value with ignition switch
ON (Do not start engine)
THROTL CLS DUTYThrottle actuator closed duty ratio:
Min.: 0 %, Max.: 100 %0 to 40 %: During idling• When accelerator pedal
released quickly, duty ratio
increased
• Read value with ignition switch
ON (Do not start engine)
THRTL MOT (OPN)Throttle actuator duty ratio (open):
Min.: 0 %, Max.: 100 %0 to 40 %: During idling ETCS service data
THRTL MOT (CLS)Throttle actuator duty ratio
(closed):
Min.: 0 %, Max.: 100 %0 to 40 %: During idling ETCS service data
O2S B1 S2Heated oxygen sensor output
voltage for sensor 2:
Min.: 0 V Max.: 1.275 V0.1 to 0.9 V: Driving at 70 km/h
(44 mph)Performing INJ VOL or A/F
CONTROL function of ACTIVE
TEST enables technician to check
output voltage of sensor
AFS B1 S1A/F sensor output voltage for
sensor 1:
Min.: 0 V Max.: 7.999 V2.8 to 3.8 V: IdlingPerforming INJ VOL or A/F
CONTROL function of ACTIVE
TEST enables technician to check
output voltage of sensor
TOTAL FT #1Total fuel trim value for fuel
system:
Min.: -0.5, Max.: 0.496-0.2 to 0.2 -
SHORT FT #1Short-term fuel trim:
Min.: -100 %, Max.: 99.2 %-20 to 20 %Short-term fuel compensation
used to maintain air-fuel ratio at
stoichiometric air-fuel ratio
LONG FT #1Long-term fuel trim:
Min.: -100 %, Max.: 99.2 %-20 to 20 %Overall fuel compensation carried
out in long-term to compensate
continual deviation of short-term
fuel trim from central value
FUEL SYS #1Fuel system status:
OL or CL or OL DRIVE or OL
FAULT or CL FAULTCL: Idling after warming up• OL (Open Loop): Has not yet
satisfied conditions to go
closed loop
• CL (Closed Loop): Using A/F
sensor as feedback for fuel
control
• OL DRIVE: Open loop due to
driving conditions (fuel
enrichment)
• OL FAULT: Open loop due to
detected system fault
• CL FAULT: Closed loop but A/
F sensor, which used for fuel
control malfunctioning
O2FT B1 S2Short-term fuel trim associated
with sensor 2:
Min.: -100 %, Max.: 99.2 %--
AF FT B1 S1Short-term fuel trim associated
with sensor 1:
Min.: 0, Max.: 1.999• Value less than 1 (0.000 to
0.999) =Lean
• Stoichiometric air-fuel
ratio=1
• Value greater than 1 (1.001
to 1.999) = Rich-
AFS B1 S1A/F sensor current:
Min.: -128 mA, Max.: 127.99 mA--
CAT TEMP B1S1Estimated catalyst temperature
(sensor 1):
Min.: -40
C, Max.: 6,513.5C-- Intelligent Tester Display Measurement: Range (Display) Normal Condition*1 Diagnostic Note
Page 1939 of 2000
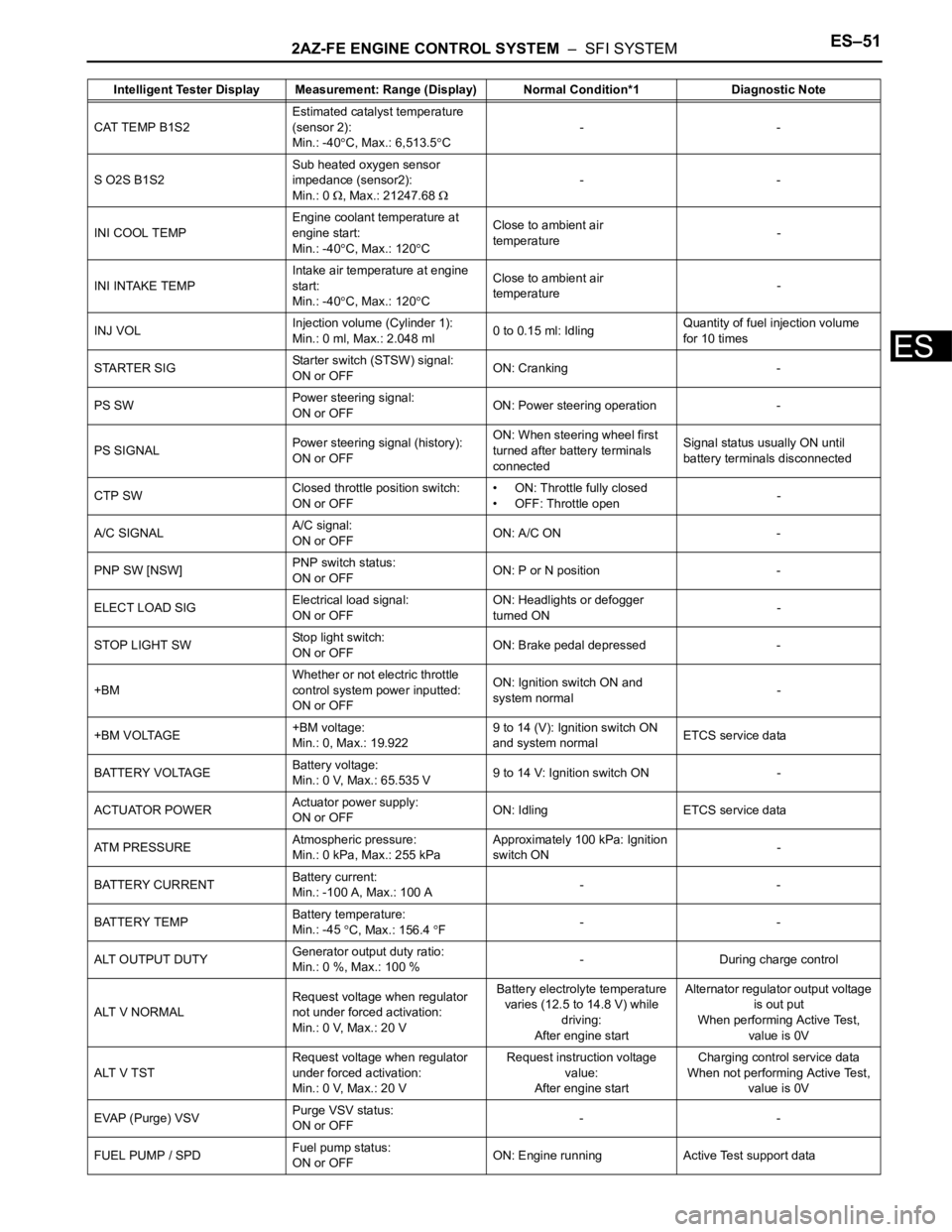
2AZ-FE ENGINE CONTROL SYSTEM – SFI SYSTEMES–51
ES
CAT TEMP B1S2Estimated catalyst temperature
(sensor 2):
Min.: -40C, Max.: 6,513.5C--
S O2S B1S2Sub heated oxygen sensor
impedance (sensor2):
Min.: 0
, Max.: 21247.68
--
INI COOL TEMPEngine coolant temperature at
engine start:
Min.: -40
C, Max.: 120CClose to ambient air
temperature-
INI INTAKE TEMPIntake air temperature at engine
start:
Min.: -40
C, Max.: 120CClose to ambient air
temperature-
INJ VOLInjection volume (Cylinder 1):
Min.: 0 ml, Max.: 2.048 ml0 to 0.15 ml: IdlingQuantity of fuel injection volume
for 10 times
STARTER SIGStarter switch (STSW) signal:
ON or OFFON: Cranking -
PS SWPower steering signal:
ON or OFFON: Power steering operation -
PS SIGNALPower steering signal (history):
ON or OFFON: When steering wheel first
turned after battery terminals
connectedSignal status usually ON until
battery terminals disconnected
CTP SWClosed throttle position switch:
ON or OFF• ON: Throttle fully closed
• OFF: Throttle open-
A/C SIGNALA/C signal:
ON or OFFON: A/C ON -
PNP SW [NSW]PNP switch status:
ON or OFFON: P or N position -
ELECT LOAD SIGElectrical load signal:
ON or OFFON: Headlights or defogger
turned ON-
STOP LIGHT SWStop light switch:
ON or OFFON: Brake pedal depressed -
+BMWhether or not electric throttle
control system power inputted:
ON or OFFON: Ignition switch ON and
system normal-
+BM VOLTAGE+BM voltage:
Min.: 0, Max.: 19.9229 to 14 (V): Ignition switch ON
and system normalETCS service data
BATTERY VOLTAGEBattery voltage:
Min.: 0 V, Max.: 65.535 V9 to 14 V: Ignition switch ON -
ACTUATOR POWERActuator power supply:
ON or OFFON: Idling ETCS service data
ATM PRESSUREAtmospheric pressure:
Min.: 0 kPa, Max.: 255 kPaApproximately 100 kPa: Ignition
switch ON-
BATTERY CURRENTBattery current:
Min.: -100 A, Max.: 100 A--
BATTERY TEMPBattery temperature:
Min.: -45
C, Max.: 156.4 F--
ALT OUTPUT DUTYGenerator output duty ratio:
Min.: 0 %, Max.: 100 %- During charge control
ALT V NORMALRequest voltage when regulator
not under forced activation:
Min.: 0 V, Max.: 20 VBattery electrolyte temperature
varies (12.5 to 14.8 V) while
driving:
After engine startAlternator regulator output voltage
is out put
When performing Active Test,
value is 0V
ALT V TSTRequest voltage when regulator
under forced activation:
Min.: 0 V, Max.: 20 VRequest instruction voltage
value:
After engine startCharging control service data
When not performing Active Test,
value is 0V
EVAP (Purge) VSVPurge VSV status:
ON or OFF--
FUEL PUMP / SPDFuel pump status:
ON or OFFON: Engine running Active Test support data Intelligent Tester Display Measurement: Range (Display) Normal Condition*1 Diagnostic Note
Page 1940 of 2000
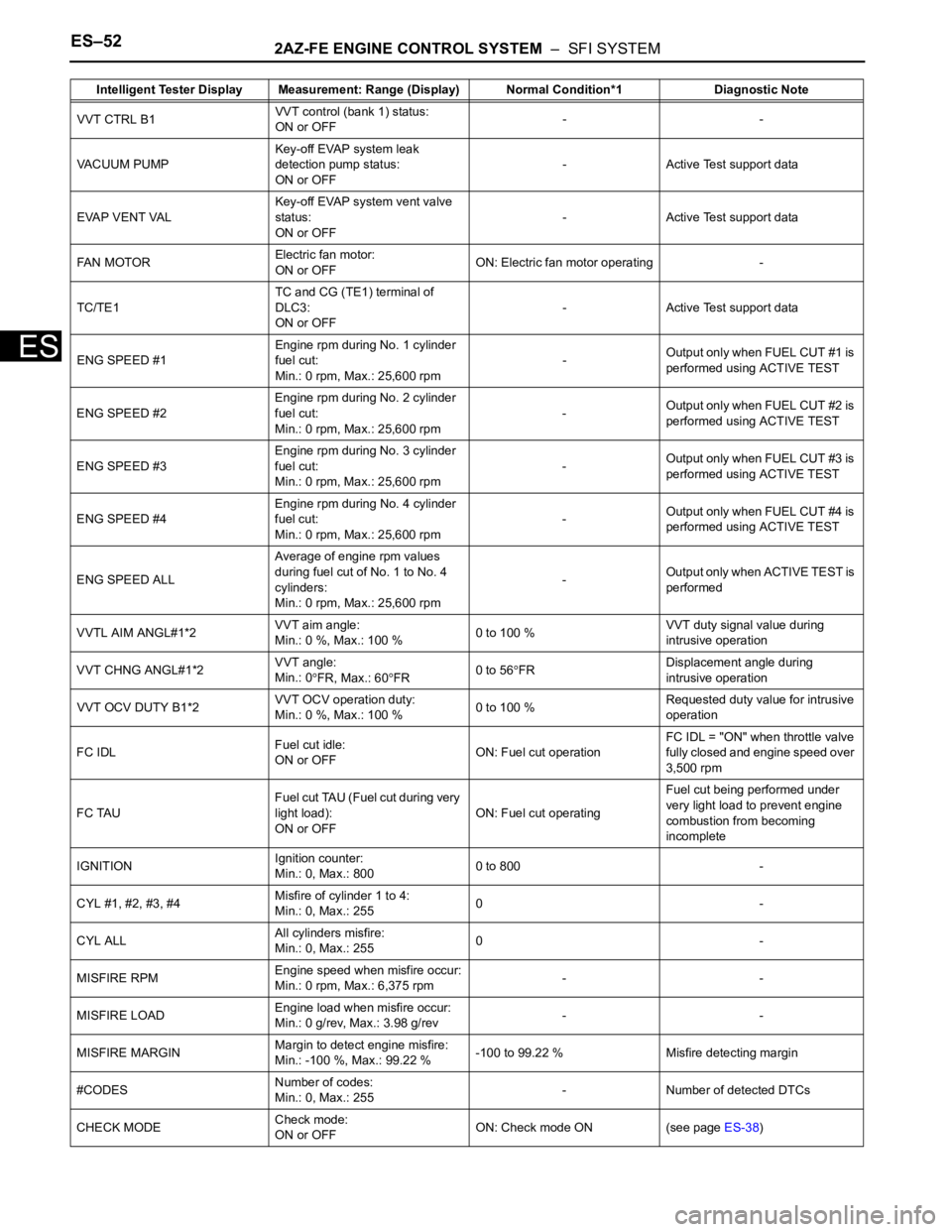
ES–522AZ-FE ENGINE CONTROL SYSTEM – SFI SYSTEM
ES
VVT CTRL B1VVT control (bank 1) status:
ON or OFF--
VACUUM PUMPKey-off EVAP system leak
detection pump status:
ON or OFF- Active Test support data
EVAP VENT VALKey-off EVAP system vent valve
status:
ON or OFF- Active Test support data
FA N M O TO RElectric fan motor:
ON or OFFON: Electric fan motor operating -
TC/TE1TC and CG (TE1) terminal of
DLC3:
ON or OFF- Active Test support data
ENG SPEED #1Engine rpm during No. 1 cylinder
fuel cut:
Min.: 0 rpm, Max.: 25,600 rpm-Output only when FUEL CUT #1 is
performed using ACTIVE TEST
ENG SPEED #2Engine rpm during No. 2 cylinder
fuel cut:
Min.: 0 rpm, Max.: 25,600 rpm-Output only when FUEL CUT #2 is
performed using ACTIVE TEST
ENG SPEED #3Engine rpm during No. 3 cylinder
fuel cut:
Min.: 0 rpm, Max.: 25,600 rpm-Output only when FUEL CUT #3 is
performed using ACTIVE TEST
ENG SPEED #4Engine rpm during No. 4 cylinder
fuel cut:
Min.: 0 rpm, Max.: 25,600 rpm-Output only when FUEL CUT #4 is
performed using ACTIVE TEST
ENG SPEED ALLAverage of engine rpm values
during fuel cut of No. 1 to No. 4
cylinders:
Min.: 0 rpm, Max.: 25,600 rpm-Output only when ACTIVE TEST is
performed
VVTL AIM ANGL#1*2VVT aim angle:
Min.: 0 %, Max.: 100 %0 to 100 %VVT duty signal value during
intrusive operation
VVT CHNG ANGL#1*2VVT angle:
Min.: 0
FR, Max.: 60FR0 to 56FRDisplacement angle during
intrusive operation
VVT OCV DUTY B1*2VVT OCV operation duty:
Min.: 0 %, Max.: 100 %0 to 100 %Requested duty value for intrusive
operation
FC IDLFuel cut idle:
ON or OFFON: Fuel cut operationFC IDL = "ON" when throttle valve
fully closed and engine speed over
3,500 rpm
FC TAUFuel cut TAU (Fuel cut during very
light load):
ON or OFFON: Fuel cut operatingFuel cut being performed under
very light load to prevent engine
combustion from becoming
incomplete
IGNITIONIgnition counter:
Min.: 0, Max.: 8000 to 800 -
CYL #1, #2, #3, #4Misfire of cylinder 1 to 4:
Min.: 0, Max.: 2550-
CYL ALLAll cylinders misfire:
Min.: 0, Max.: 2550-
MISFIRE RPMEngine speed when misfire occur:
Min.: 0 rpm, Max.: 6,375 rpm--
MISFIRE LOADEngine load when misfire occur:
Min.: 0 g/rev, Max.: 3.98 g/rev--
MISFIRE MARGINMargin to detect engine misfire:
Min.: -100 %, Max.: 99.22 %-100 to 99.22 % Misfire detecting margin
#CODESNumber of codes:
Min.: 0, Max.: 255- Number of detected DTCs
CHECK MODECheck mode:
ON or OFFON: Check mode ON (see page ES-38) Intelligent Tester Display Measurement: Range (Display) Normal Condition*1 Diagnostic Note