CHEVROLET CAMARO 1982 Repair Guide
Manufacturer: CHEVROLET, Model Year: 1982, Model line: CAMARO, Model: CHEVROLET CAMARO 1982Pages: 875, PDF Size: 88.64 MB
Page 301 of 875
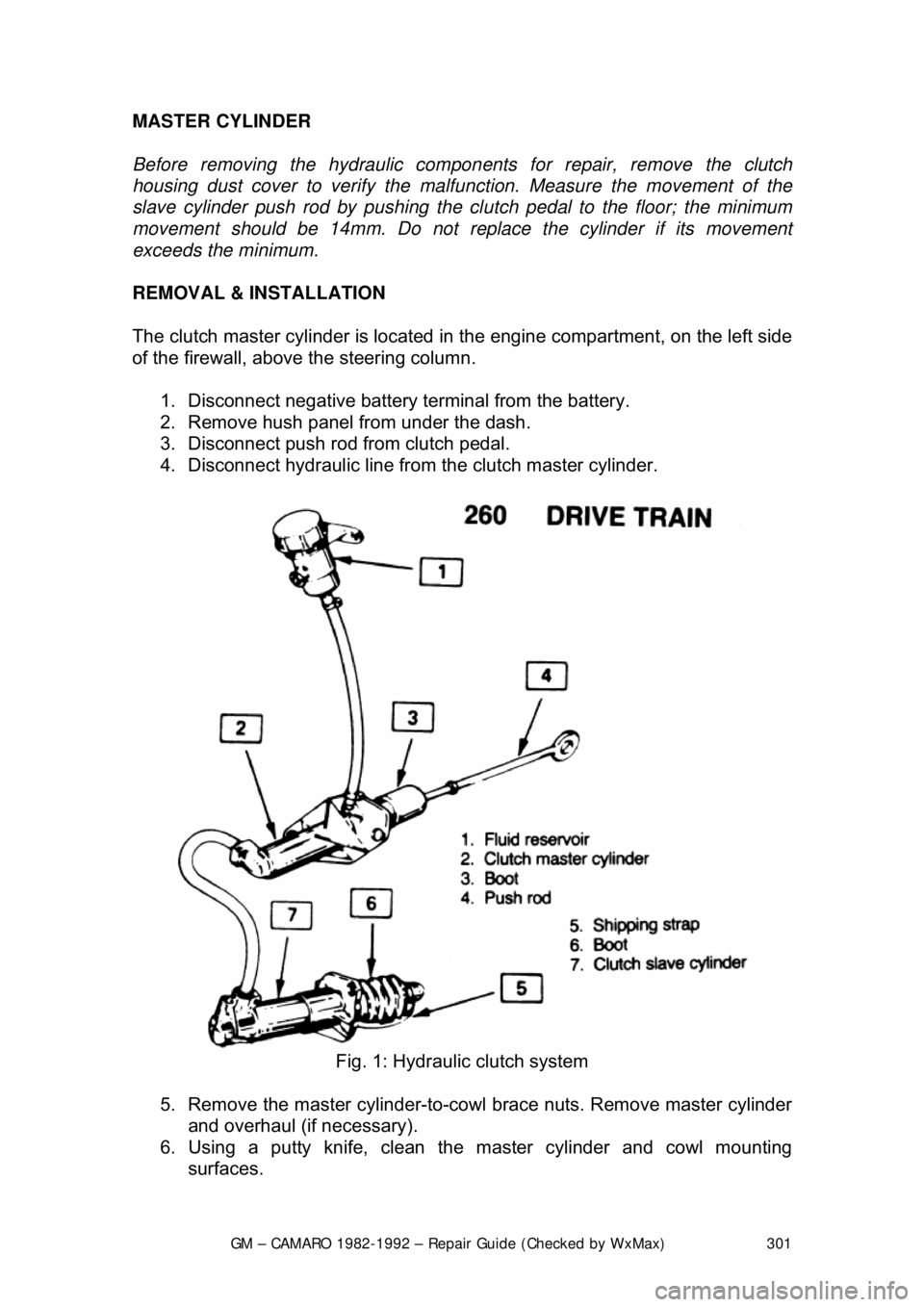
GM – CAMARO 1982-1992 – Repair Guide (Checked by WxMax) 301
MASTER CYLINDER
Before removing the hydraulic compon
ents for repair, remove the clutch
housing dust cover to verify the malf unction. Measure the movement of the
slave cylinder push rod by pushing the cl utch pedal to the floor; the minimum
movement should be 14mm. Do not r eplace the cylinder if its movement
exceeds the minimum.
REMOVAL & INSTALLATION
The clutch master cylinder is located in the engine compartment, on the left side
of the firewall, above the steering column.
1. Disconnect negative battery terminal from the battery.
2. Remove hush panel from under the dash.
3. Disconnect push rod from clutch pedal.
4. Disconnect hydraulic line from the clutch master cylinder.
Fig. 1: Hydraulic clutch system
5. Remove the master cylinder-to-cowl brace nuts. Remove master cylinder
and overhaul (if necessary).
6. Using a putty knife, clean th e master cylinder and cowl mounting
surfaces.
Page 302 of 875
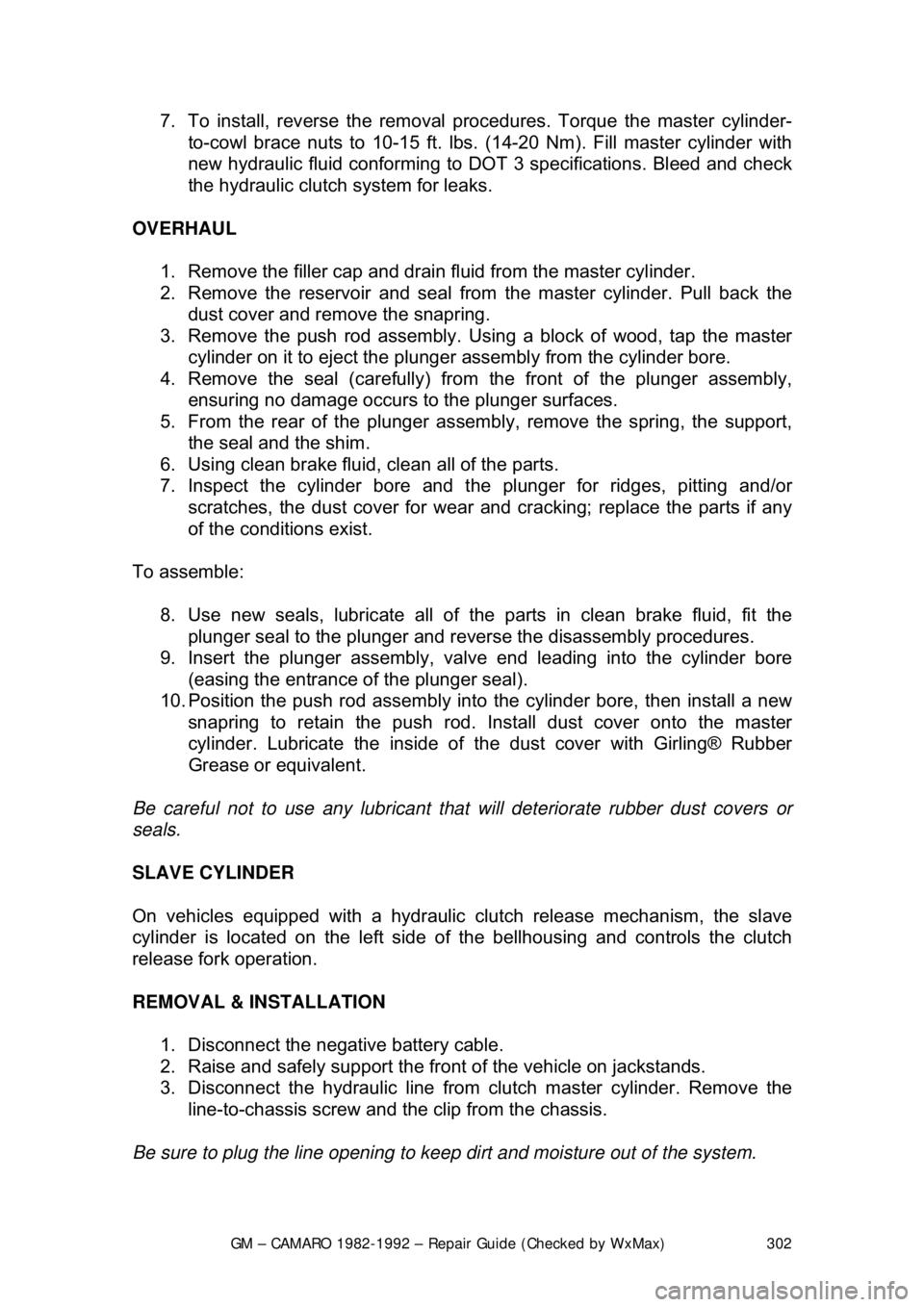
GM – CAMARO 1982-1992 – Repair Guide (Checked by WxMax) 302
7. To install, reverse the removal
procedures. Torque the master cylinder-
to-cowl brace nuts to 10-15 ft. lbs. (14-20 Nm). Fill master cylinder with
new hydraulic fluid conforming to DO T 3 specifications. Bleed and check
the hydraulic clutch system for leaks.
OVERHAUL 1. Remove the filler cap and drain fl uid from the master cylinder.
2. Remove the reservoir and seal from the master cylinder. Pull back the
dust cover and remove the snapring.
3. Remove the push rod assembly. Usi ng a block of wood, tap the master
cylinder on it to eject the plunger a ssembly from the cylinder bore.
4. Remove the seal (carefully) from the front of the plunger assembly,
ensuring no damage occurs to the plunger surfaces.
5. From the rear of t he plunger assembly, remove the spring, the support,
the seal and the shim.
6. Using clean brake fluid, clean all of the parts.
7. Inspect the cylinder bore and t he plunger for ridges, pitting and/or
scratches, the dust cover for wear and cracking; replace the parts if any
of the conditions exist.
To assemble: 8. Use new seals, lubric ate all of the parts in clean brake fluid, fit the
plunger seal to the plunger and reve rse the disassembly procedures.
9. Insert the plunger assembly, va lve end leading into the cylinder bore
(easing the entrance of the plunger seal).
10. Position the push rod assembly into the cylinder bore, then install a new
snapring to retain the push rod. Install dust cover onto the master
cylinder. Lubricate the inside of t he dust cover with Girling® Rubber
Grease or equivalent.
Be careful not to use any lubricant that will deteriorate rubber dust covers or
seals.
SLAVE CYLINDER
On vehicles equipped with a hydraulic clutch release mechanism, the slave
cylinder is located on the left side of the bellhousing and controls the clutch
release fork operation.
REMOVAL & INSTALLATION
1. Disconnect the negative battery cable.
2. Raise and safely support the front of the vehicle on jackstands.
3. Disconnect the hydraulic line from clutch master cylinder. Remove the
line-to-chassis screw and the c lip from the chassis.
Be sure to plug the line opening to k eep dirt and moisture out of the system.
Page 303 of 875
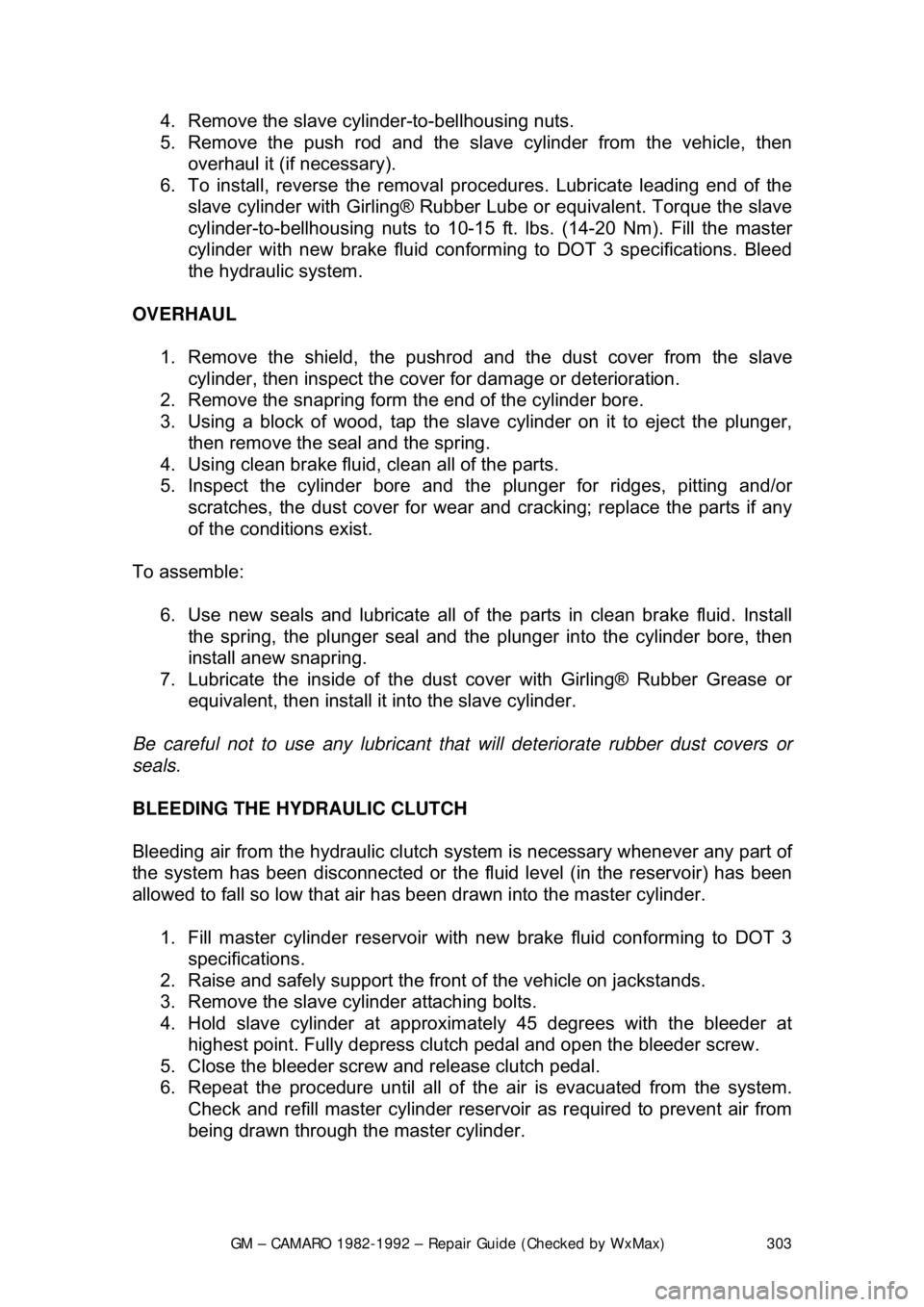
GM – CAMARO 1982-1992 – Repair Guide (Checked by WxMax) 303
4. Remove the slave cyli
nder-to-bellhousing nuts.
5. Remove the push rod and the slav e cylinder from the vehicle, then
overhaul it (if necessary).
6. To install, reverse the removal pr ocedures. Lubricate leading end of the
slave cylinder with Girli ng® Rubber Lube or equiva lent. Torque the slave
cylinder-to-bellhousing nuts to 10-15 ft. lbs. (14-20 Nm). Fill the master
cylinder with new brake fluid conformi ng to DOT 3 specifications. Bleed
the hydraulic system.
OVERHAUL 1. Remove the shield, the pushrod and the dust cover from the slave cylinder, then inspect the cover for damage or deterioration.
2. Remove the snapring form t he end of the cylinder bore.
3. Using a block of wood, tap the slave cylinder on it to eject the plunger,
then remove the seal and the spring.
4. Using clean brake fluid, clean all of the parts.
5. Inspect the cylinder bore and the plunger for ridges, pitting and/or
scratches, the dust cover for wear and cracking; replace the parts if any
of the conditions exist.
To assemble: 6. Use new seals and lubricat e all of the parts in clean brake fluid. Install
the spring, the plunger seal and the plunger into the cylinder bore, then
install anew snapring.
7. Lubricate the inside of the dust co ver with Girling® Rubber Grease or
equivalent, then install it into the slave cylinder.
Be careful not to use any lubricant that will deteriorate rubber dust covers or
seals.
BLEEDING THE HYDRAULIC CLUTCH
Bleeding air from the hydrau lic clutch system is necessary whenever any part of
the system has been disconnect ed or the fluid level (in the reservoir) has been
allowed to fall so low that air has been drawn into the master cylinder.
1. Fill master cylinder reservoir wit h new brake fluid conforming to DOT 3
specifications.
2. Raise and safely support the front of the vehicle on jackstands.
3. Remove the slave cylinder attaching bolts.
4. Hold slave cylinder at approximatel y 45 degrees with the bleeder at
highest point. Fully depress clutch pedal and open the bleeder screw.
5. Close the bleeder screw and release clutch pedal.
6. Repeat the procedure until all of t he air is evacuated from the system.
Check and refill master cylinder reserv oir as required to prevent air from
being drawn through the master cylinder.
Page 304 of 875
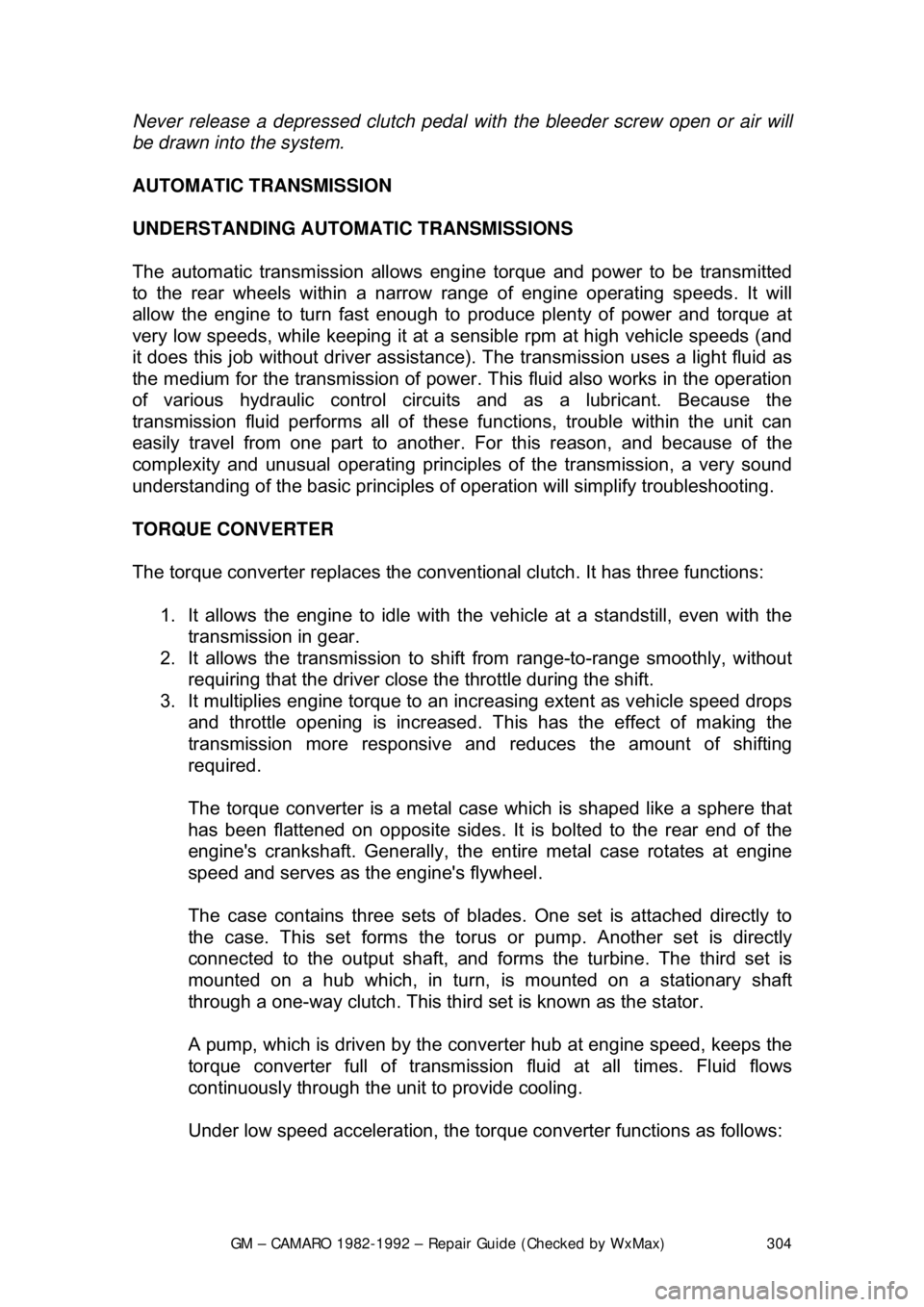
GM – CAMARO 1982-1992 – Repair Guide (Checked by WxMax) 304
Never release a depressed clutch pedal
with the bleeder screw open or air will
be drawn into the system.
AUTOMATIC TRANSMISSION
UNDERSTANDING AUTOMATIC TRANSMISSIONS
The automatic transmission allows eng ine torque and power to be transmitted
to the rear wheels within a narrow range of engine operating speeds. It will
allow the engine to turn fast enough to produce plenty of power and torque at
very low speeds, while keeping it at a s ensible rpm at high vehicle speeds (and
it does this job without driv er assistance). The transmission uses a light fluid as
the medium for the transmission of power. This fluid also works in the operation
of various hydraulic control circui ts and as a lubricant. Because the
transmission fluid performs all of thes e functions, trouble within the unit can
easily travel from one part to another. For this reason, and because of the
complexity and unusual oper ating principles of the transmission, a very sound
understanding of the basic principles of operation will simplify troubleshooting.
TORQUE CONVERTER
The torque converter replaces the convent ional clutch. It has three functions:
1. It allows the engine to idle with t he vehicle at a standstill, even with the
transmission in gear.
2. It allows the transmission to shi ft from range-to-range smoothly, without
requiring that the driver close the throttle during the shift.
3. It multiplies engine torque to an incr easing extent as vehicle speed drops
and throttle opening is increased. This has the effect of making the
transmission more responsive and redu ces the amount of shifting
required.
The torque converter is a metal case which is shaped like a sphere that
has been flattened on opposite sides. It is bolted to the rear end of the
engine's crankshaft. Generally, the ent ire metal case rotates at engine
speed and serves as the engine's flywheel.
The case contains three sets of bl ades. One set is attached directly to
the case. This set forms the torus or pump. Another set is directly
connected to the output shaft, and forms the turbine. The third set is
mounted on a hub which, in turn, is mounted on a stationary shaft
through a one-way clutch. This third set is known as the stator.
A pump, which is driven by the conv erter hub at engine speed, keeps the
torque converter full of transmission fluid at all times. Fluid flows
continuously through the unit to provide cooling.
Under low speed acceleration, the tor que converter functions as follows:
Page 305 of 875
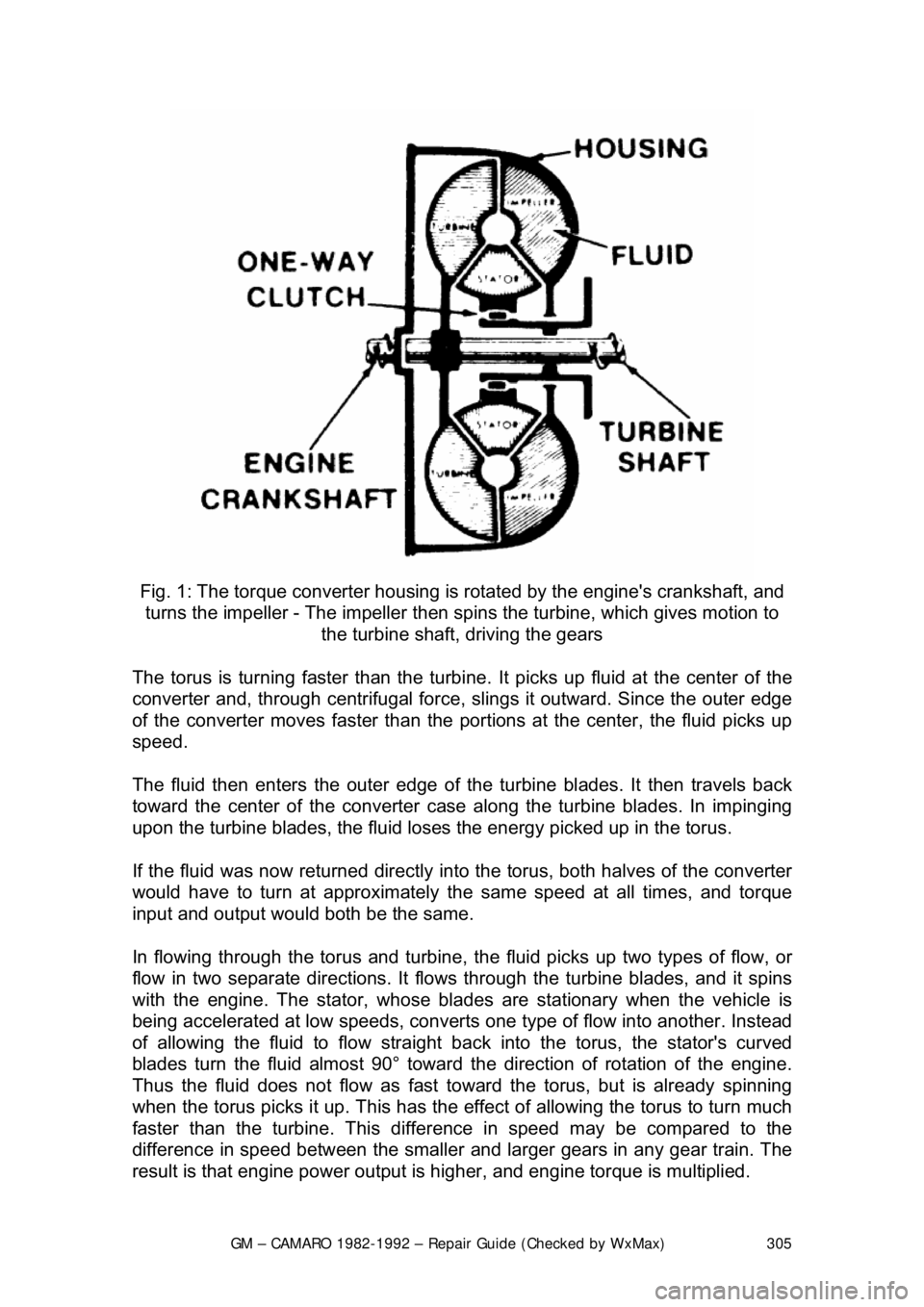
GM – CAMARO 1982-1992 – Repair Guide (Checked by WxMax) 305
Fig. 1: The torque converter housing is rotated by the engine's crankshaft, and
turns the impeller - The impeller then spin s the turbine, which gives motion to
the turbine shaft, driving the gears
The torus is turning faster than the turbi ne. It picks up fluid at the center of the
converter and, through centrifugal force, slings it outward. Since the outer edge
of the converter moves faster than the portions at the center, the fluid picks up
speed.
The fluid then enters the outer edge of th e turbine blades. It then travels back
toward the center of the converter case along the turbine blades. In impinging
upon the turbine blades, the fluid loses the energy picked up in the torus.
If the fluid was now returned directly into the torus, both halves of the converter
would have to turn at approximately t he same speed at all times, and torque
input and output would both be the same.
In flowing through the torus and turbine, the fluid picks up two types of flow, or
flow in two separate directions. It flow s through the turbine blades, and it spins
with the engine. The stator, whose blades are stationary when the vehicle is
being accelerated at low speeds, converts one type of flow into another. Instead
of allowing the fluid to flow straight back into the torus, the stator's curved
blades turn the fluid almost 90° toward the direction of rotation of the engine.
Thus the fluid does not flow as fast to ward the torus, but is already spinning
when the torus picks it up. This has the effe ct of allowing the torus to turn much
faster than the turbine. This differ ence in speed may be compared to the
difference in speed between the smaller and larger gears in any gear train. The
result is that engine powe r output is higher, and engine torque is multiplied.
Page 306 of 875
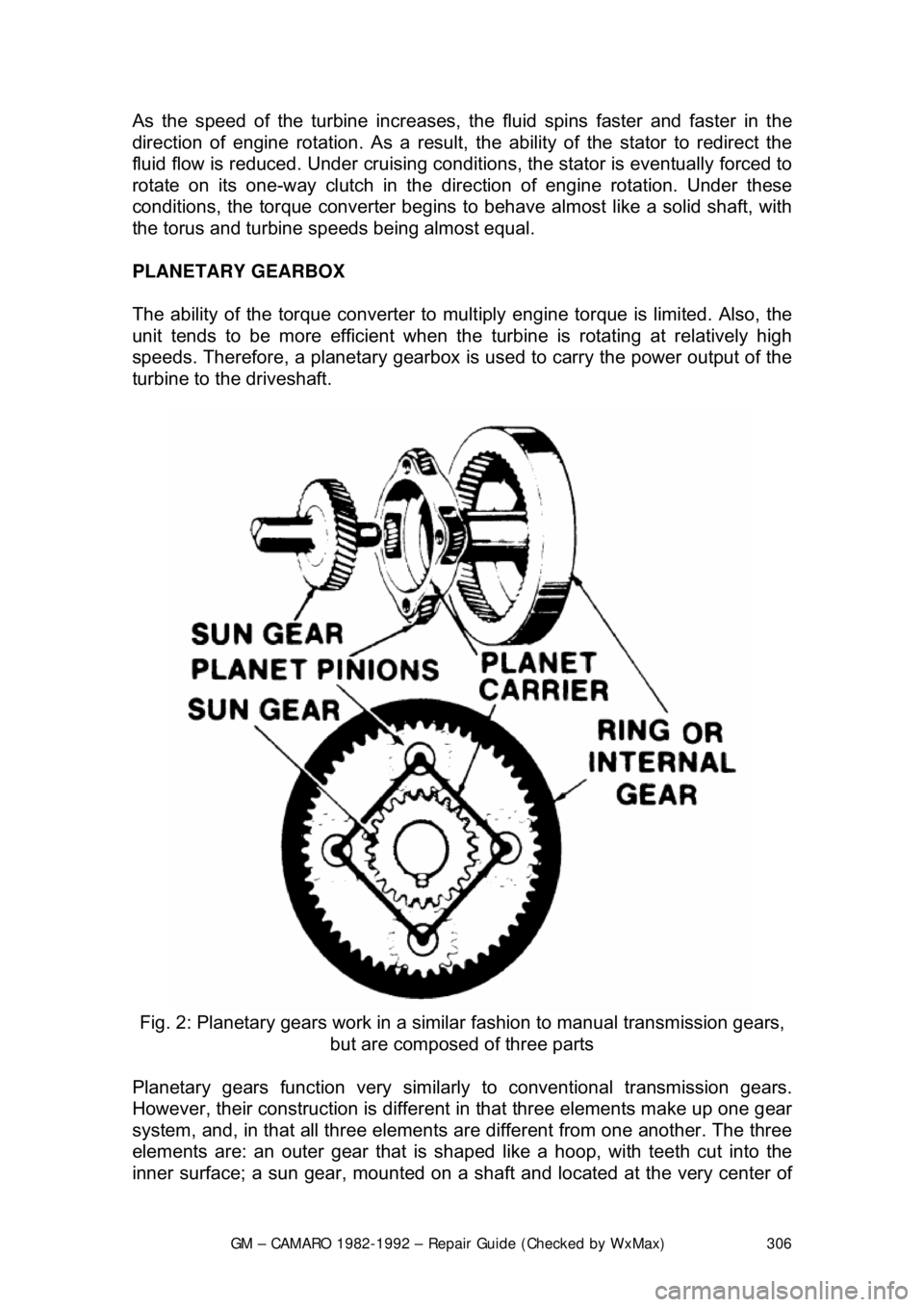
GM – CAMARO 1982-1992 – Repair Guide (Checked by WxMax) 306
As the speed of the turbine increases, th
e fluid spins faster and faster in the
direction of engine rotation. As a result, t he ability of the stator to redirect the
fluid flow is reduced. Under cruising conditions, the stator is eventually forced to
rotate on its one-way clutch in the dire ction of engine rotation. Under these
conditions, the torque converter begins to behave almost like a solid shaft, with
the torus and turbine speeds being almost equal.
PLANETARY GEARBOX
The ability of the torque converter to mult iply engine torque is limited. Also, the
unit tends to be more efficient when the turbine is rotating at relatively high
speeds. Therefore, a planetar y gearbox is used to carry the power output of the
turbine to the driveshaft.
Fig. 2: Planetary gears work in a sim ilar fashion to manual transmission gears,
but are composed of three parts
Planetary gears function very similarly to conventional transmission gears.
However, their construction is different in that three elements make up one gear
system, and, in that all three elements ar e different from one another. The three
elements are: an outer gear that is shaped like a hoop, with teeth cut into the
inner surface; a sun gear, mounted on a sha ft and located at the very center of
Page 307 of 875
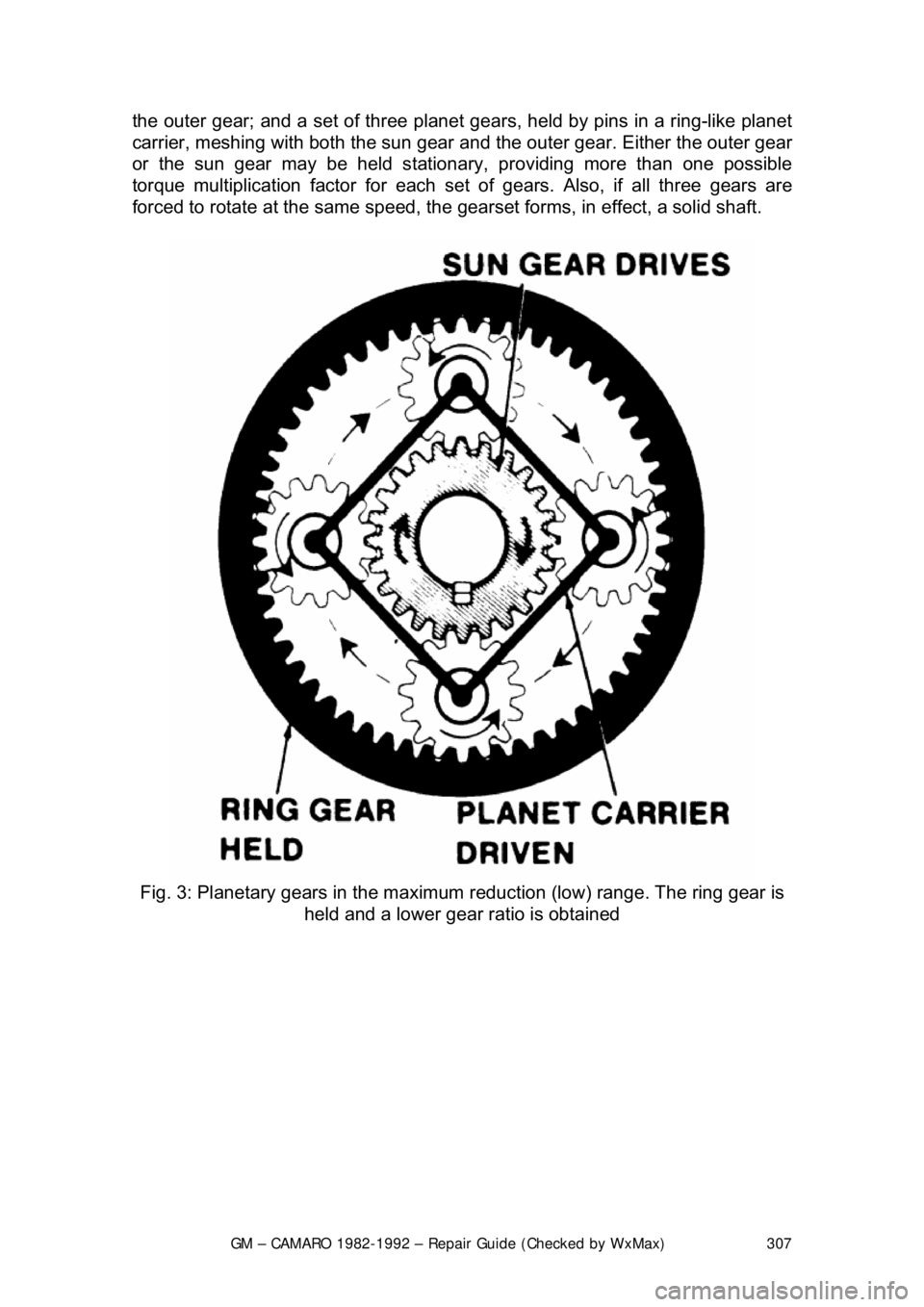
GM – CAMARO 1982-1992 – Repair Guide (Checked by WxMax) 307
the outer gear; and a set of three planet gear
s, held by pins in a ring-like planet
carrier, meshing with both the sun gear and the outer gear. Either the outer gear
or the sun gear may be held stationary, providing more than one possible
torque multiplication factor for each se t of gears. Also, if all three gears are
forced to rotate at the same speed, the gearset forms, in effect, a solid shaft.
Fig. 3: Planetary gears in the maximum reduction (low) range. The ring gear is
held and a lower gear ratio is obtained
Page 308 of 875
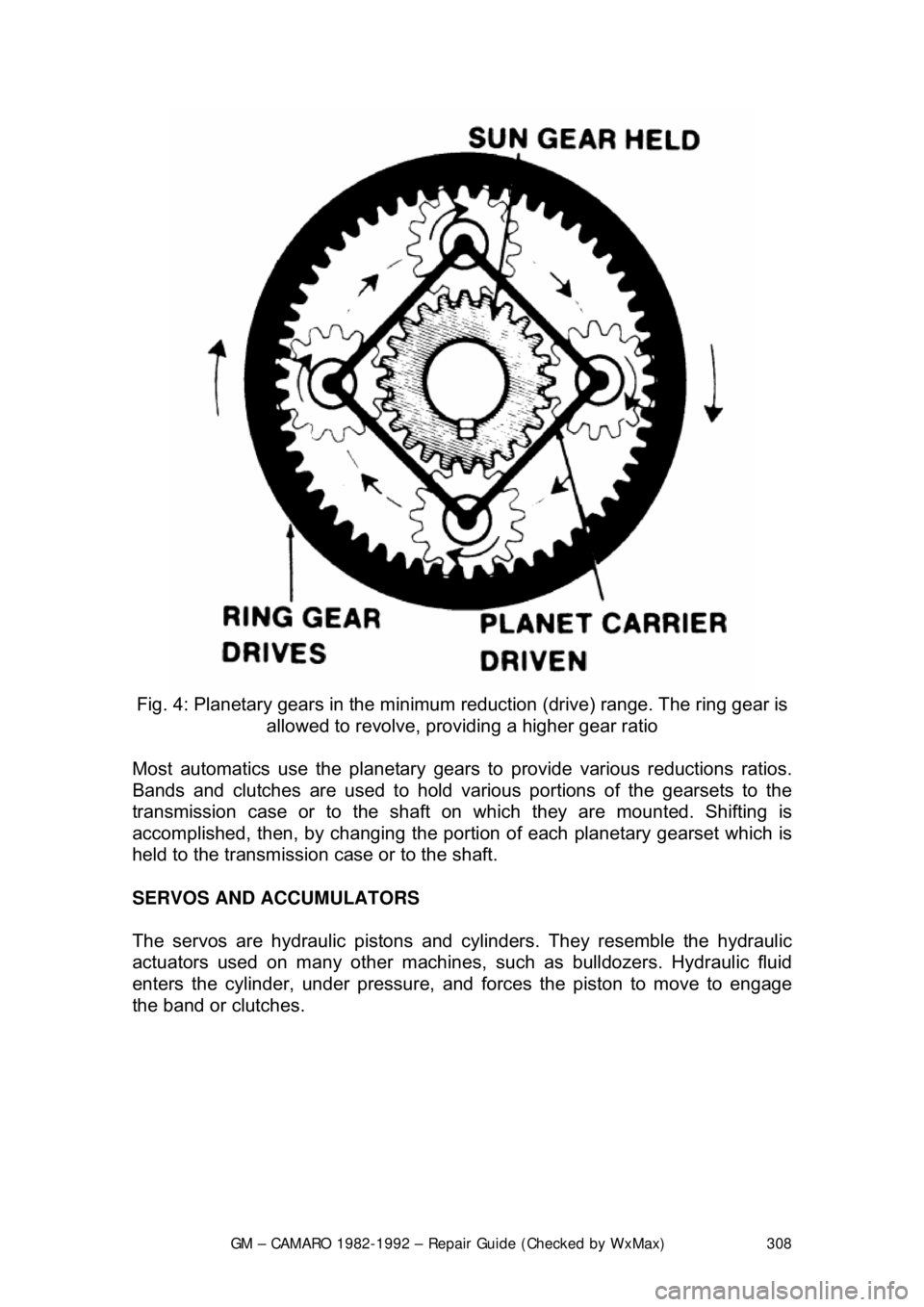
GM – CAMARO 1982-1992 – Repair Guide (Checked by WxMax) 308
Fig. 4: Planetary gears in the minimum reduction (drive) range. The ring gear is
allowed to revolve, providing a higher gear ratio
Most automatics use the pl anetary gears to provide various reductions ratios.
Bands and clutches are used to hold va rious portions of the gearsets to the
transmission case or to the shaft on which they are mounted. Shifting is\
accomplished, then, by c hanging the portion of each planetary gearset which is
held to the transmission case or to the shaft.
SERVOS AND ACCUMULATORS
The servos are hydraulic pistons and cylinders. They resemble the hydrau\
lic
actuators used on many other machines, such as bulldozers. Hydraulic fluid
enters the cylinder, under pressure, and fo rces the piston to move to engage
the band or clutches.
Page 309 of 875
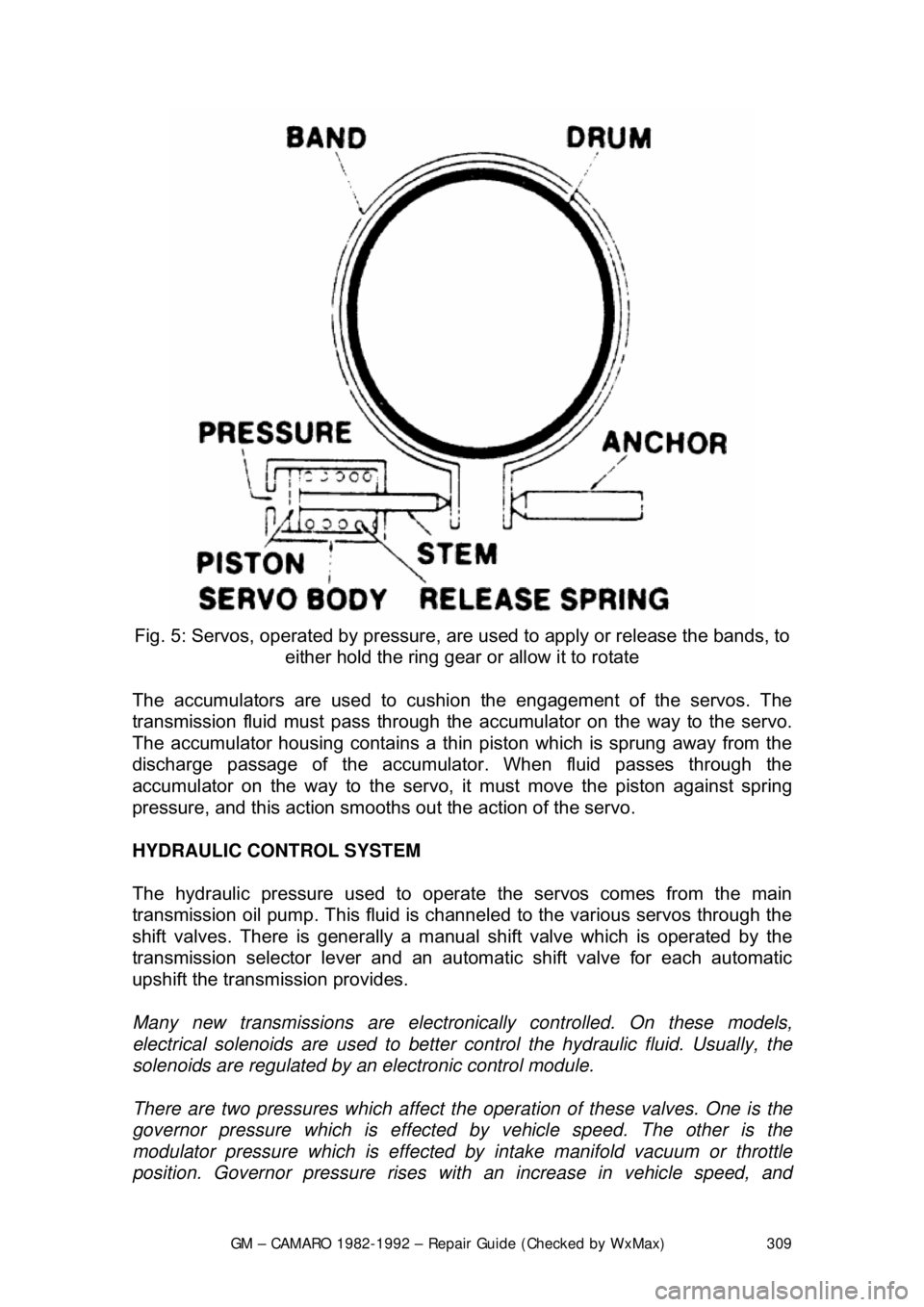
GM – CAMARO 1982-1992 – Repair Guide (Checked by WxMax) 309
Fig. 5: Servos, operated by pressure, ar e used to apply or release the bands, to
either hold the ring gear or allow it to rotate
The accumulators are used to cushi on the engagement of the servos. The
transmission fluid must pass through the ac cumulator on the way to the servo.
The accumulator housing contains a thin piston which is sprung away from the
discharge passage of the accumulato r. When fluid passes through the
accumulator on the way to the servo, it must move the piston against spring
pressure, and this action smooths out the action of the servo.
HYDRAULIC CONTROL SYSTEM
The hydraulic pressure used to operat e the servos comes from the main
transmission oil pump. This fluid is channel ed to the various servos through the
shift valves. There is generally a manual shift valve which is operated by the
transmission selector lever and an automat ic shift valve for each automatic
upshift the transmission provides.
Many new transmissions are electroni cally controlled. On these models,
electrical solenoids are used to better control the hydraulic fluid. Usually, the
solenoids are regulated by an electronic control module.
There are two pressures which affect t he operation of these valves. One is the
governor pressure which is effected by vehicle speed. The other is the
modulator pressure which is effected by intake manifold vacuum or throttle
position. Governor pressure rises wit h an increase in vehicle speed, and
Page 310 of 875
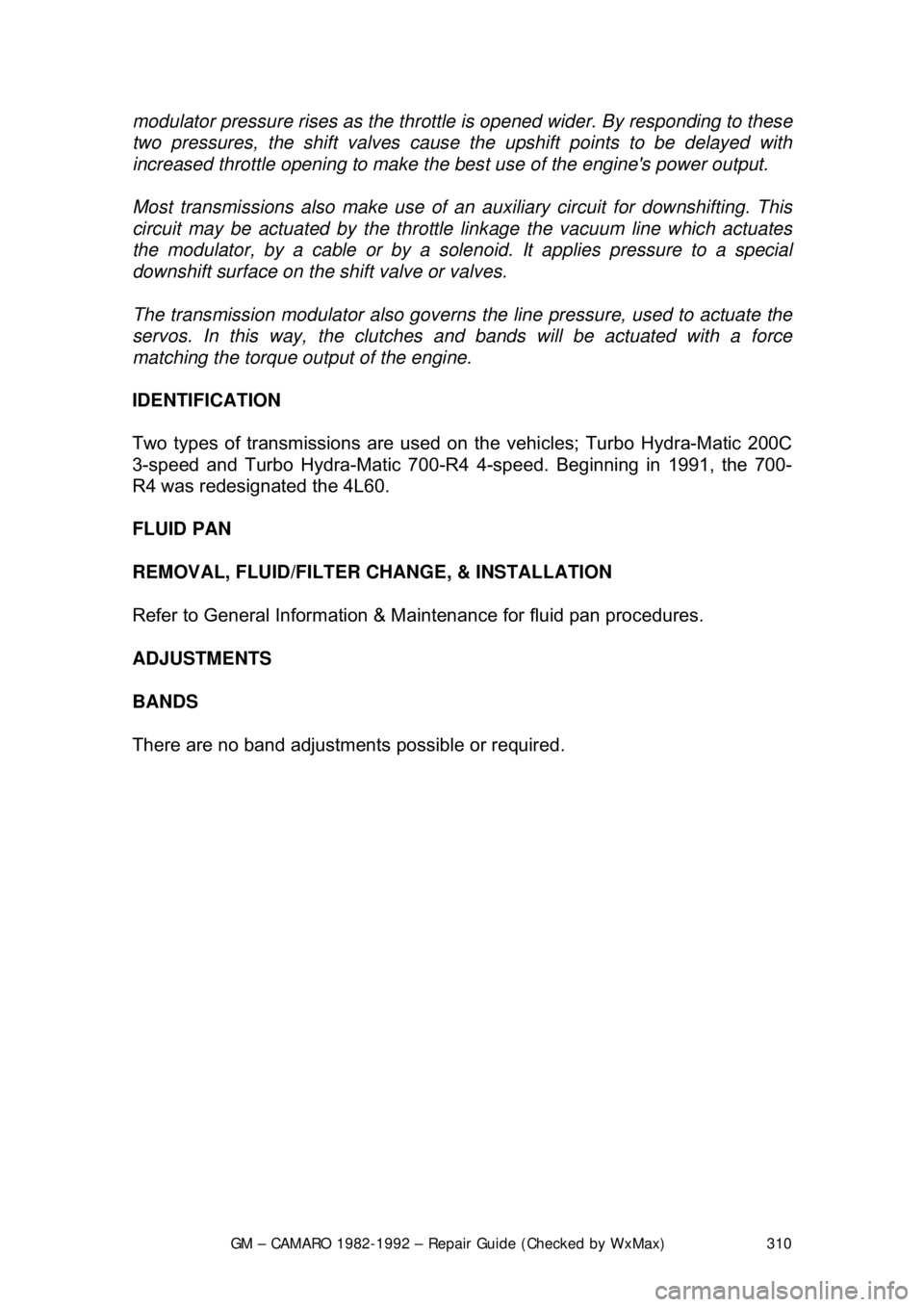
GM – CAMARO 1982-1992 – Repair Guide (Checked by WxMax) 310
modulator pressure rises as the thro
ttle is opened wider. By responding to these
two pressures, the shift valves caus e the upshift points to be delayed with
increased throttle opening to make the bes t use of the engine's power output.
Most transmissions also make use of an auxiliary circuit for downshifting. This
circuit may be actuated by the throttle linkage the vacuum line which actuates
the modulator, by a cable or by a solenoid. It applies pressure to a special
downshift surface on the shift valve or valves.
The transmission modulator also governs the line pressure, used to actuate the
servos. In this way, the clutches and bands will be actuated with a force
matching the torque output of the engine.
IDENTIFICATION
Two types of transmissions are used on th e vehicles; Turbo Hydra-Matic 200C
3-speed and Turbo Hydra-Matic 700-R4 4-speed. Beginning in 1991, the 700-
R4 was redesignated the 4L60.
FLUID PAN
REMOVAL, FLUID/FILTER CH ANGE, & INSTALLATION
Refer to General Information & Ma intenance for fluid pan procedures.
ADJUSTMENTS
BANDS
There are no band adjustments possible or required.