DATSUN 210 1979 Service Manual
Manufacturer: DATSUN, Model Year: 1979, Model line: 210, Model: DATSUN 210 1979Pages: 548, PDF Size: 28.66 MB
Page 221 of 548
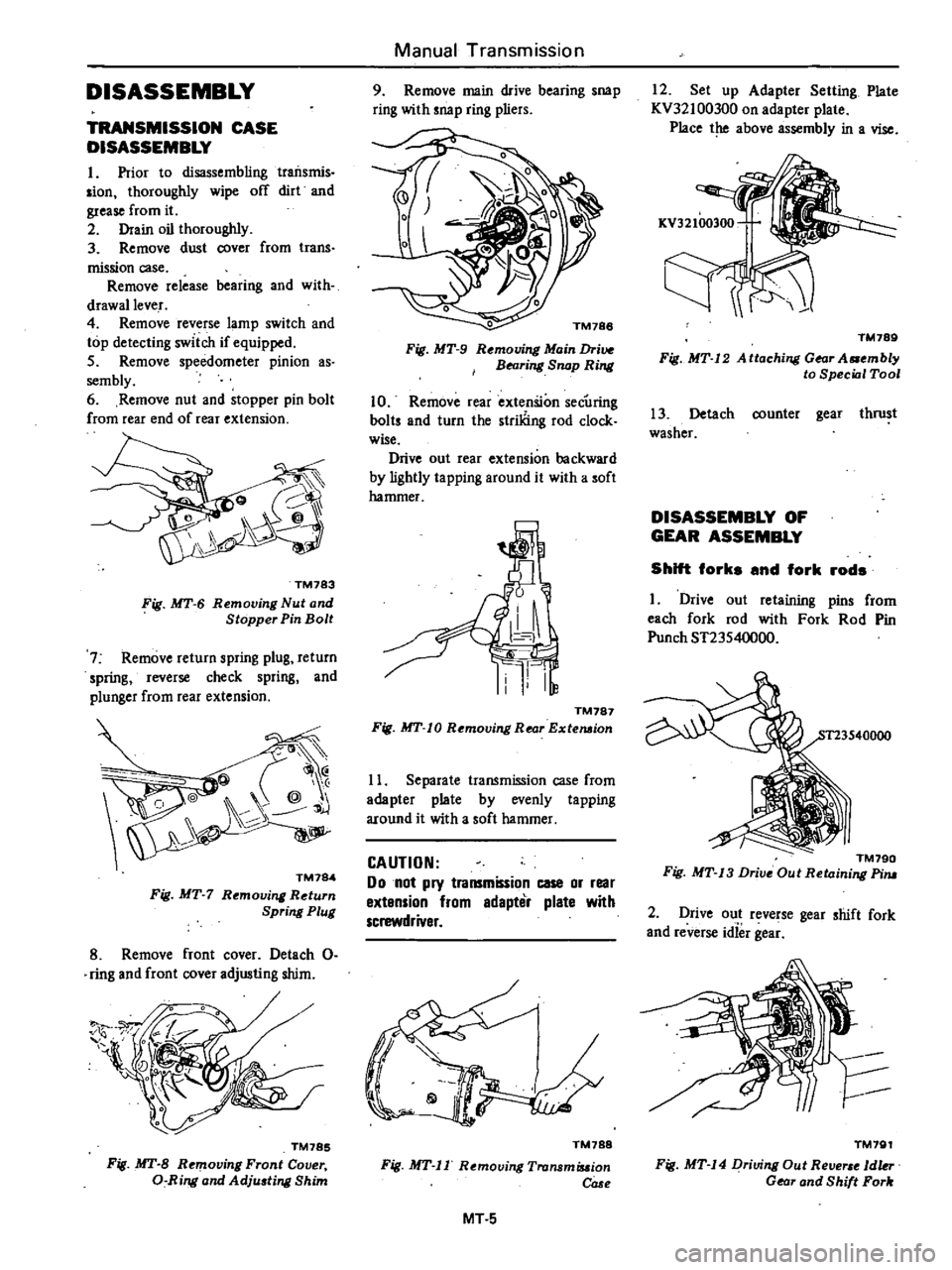
DISASSEMBLY
TRANSMISSION
CASE
DISASSEMBLY
I
Prior
to
disassembling
traiIsmis
sian
thoroughly
wipe
off
dirt
and
grease
from
it
2
Drain
oil
thoroughly
3
Remove
dust
cover
from
trans
mission
case
Remove
release
bearing
and
with
drawallever
4
Remove
reverse
lamp
switch
and
top
detecting
switch
if
equipped
5
Remove
speedometer
pinion
as
sembly
6
Remove
nut
and
stopper
pin
bolt
from
rear
end
of
rear
extension
TM783
Fig
MT
6
Removing
Nut
and
Stopper
Pin
Bolt
7
Remove
return
spring
plug
return
spring
reverse
check
spring
and
plunger
from
rear
extension
@
@
j
TM784
Fig
MT
7
Rt
moving
Return
Spring
Plug
8
Remove
front
cover
Detach
0
ring
and
front
cover
adjusting
shim
TM785
Fig
MT
B
Removing
Front
Cover
a
Ring
and
Adju
ting
Shim
Manual
Transmission
9
Remove
main
drive
bearing
snap
ring
with
snap
ring
pliers
o
TM188
Fig
MT
9
Rt
mouing
Main
Drive
BNring
Snap
Ring
10
Remove
rear
extenSion
secUring
baits
and
turn
the
striliing
rod
clock
wise
Drive
out
rear
extension
backward
by
lightly
ta
pping
around
it
with
a
soft
hammer
TM787
Fig
MT
10
Removing
Rear
Extemion
11
Separate
transmission
case
from
adapter
plate
by
evenly
tapping
around
it
with
a
soft
hammer
CAUTION
Do
not
pry
transmission
case
or
rear
extension
from
edapter
plate
with
screwdriver
TM788
Fig
MT
II
Removing
Tronsmiuion
COSf
MT
5
12
Set
up
Adapter
Setting
Plate
KV32100300
on
adapter
plate
Place
the
above
assembly
in
a
vise
TM789
Fig
MT
12
A
ttaching
Gear
A
mbly
to
Special
Tool
13
Detach
counter
gear
thrust
washer
DISASSEMBLY
OF
GEAR
ASSEMBLY
Shift
forks
and
fork
rods
I
Drive
out
retaining
pins
from
each
fork
rod
with
Fork
Rod
Pin
Punch
ST23540000
TM790
Fig
MT
13
Drive
Out
Retaining
Pim
2
Drive
out
reverse
gear
shift
fork
and
reverse
idief
gea
TM791
Fig
MT
14
Driving
Out
Re
1dkr
Gear
and
Shift
Fork
Page 222 of 548
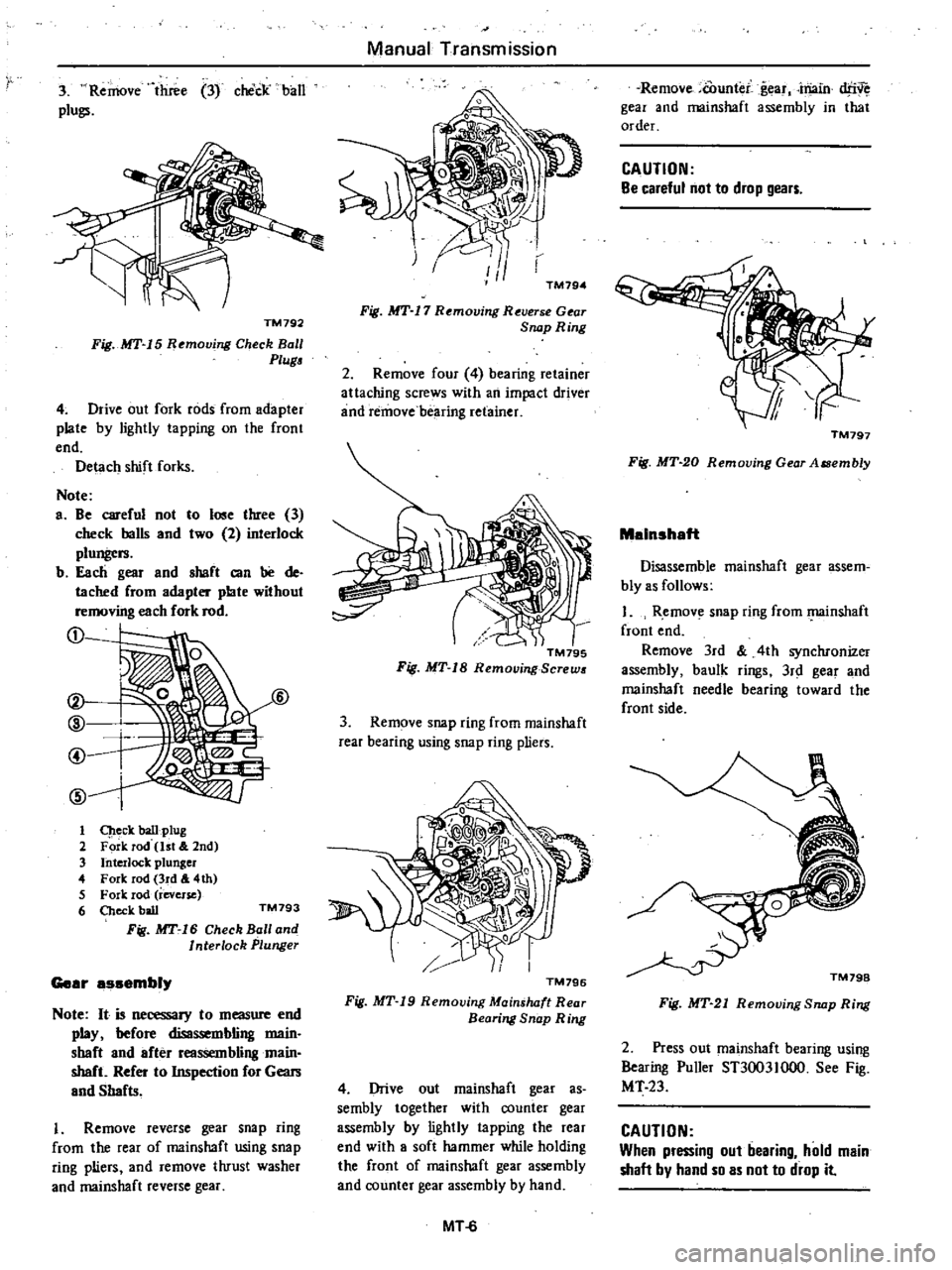
3
Remove
three
3
chick
ball
plugs
TM792
Fig
MT
15
Removing
Check
Ball
Plug
4
Drive
out
fork
rods
from
adapter
plate
by
lightly
tapping
on
the
front
end
Detach
shift
forks
Note
a
Be
careful
not
to
lose
three
3
check
balls
and
two
2
interlock
pluDgl
rs
b
Each
gear
and
sbaft
can
be
de
tached
from
adapter
plate
without
removing
each
fork
rod
D
t
@
@
6
@
1
q
eck
ball
ptug
2
Fork
Tod
1st
2nd
3
InterJock
plunger
4
Fork
rod
3rd
4th
5
Fork
rod
reverse
6
Check
ball
TM793
Fig
MT
16
Check
Ball
and
Interlock
Plunger
Gear
assembly
Note
It
is
necessary
to
measure
end
play
before
disassembling
main
sbaft
and
after
reassembling
main
shaft
Refer
to
Inspection
for
Gears
and
Shafts
1
Remove
reverse
gear
snap
ring
from
the
rear
of
mainshaft
using
snap
ring
pliers
and
remove
thrust
washer
and
mainshaft
reverse
gear
Manual
Transmission
TM794
Fig
MT
17
R
molJing
Reuerse
Gear
SfUJpRing
2
Remove
four
4
bearing
retainer
attaching
screws
with
an
impact
driver
and
remove
bearing
retainer
TM79S
Fif
MT
18
RemouingBcrews
3
Remove
snap
ring
from
mainshaft
rear
bearing
using
snap
ring
pliers
TM796
Fig
MT
19
Removing
Mainshaft
Rear
Bearing
Snap
Ring
4
Drive
out
mainshaft
gear
as
sembly
together
with
counter
gear
assembly
by
lightly
tapping
the
rea
end
with
a
soft
hammer
while
holding
the
front
of
mainshaft
gear
assembly
and
counter
gear
assembly
by
hand
MT
6
Remove
counter
g
ar
main
dfN
gear
and
mainshaft
assembly
in
that
order
CAUTION
Be
careful
not
to
drop
gears
TM797
Fig
MT
20
Removing
Gear
AlSembly
Malnshaft
Disassemble
mainsltaft
gear
assem
bly
as
follows
1
R
emove
snap
ring
from
l
l
Iinshaft
front
end
Remove
3rd
4th
synchronizer
assembly
baulk
rings
3r
gear
and
mainshaft
needle
bearing
toward
the
front
side
Fig
MT
21
Removing
Snap
Ring
2
Press
out
mainsltaft
bearing
using
Bearing
Puller
ST3003Iooo
See
Fig
MT
23
CAUTION
When
pressing
out
bearing
hold
main
shaft
by
hand
so
as
not
to
drop
it
Page 223 of 548
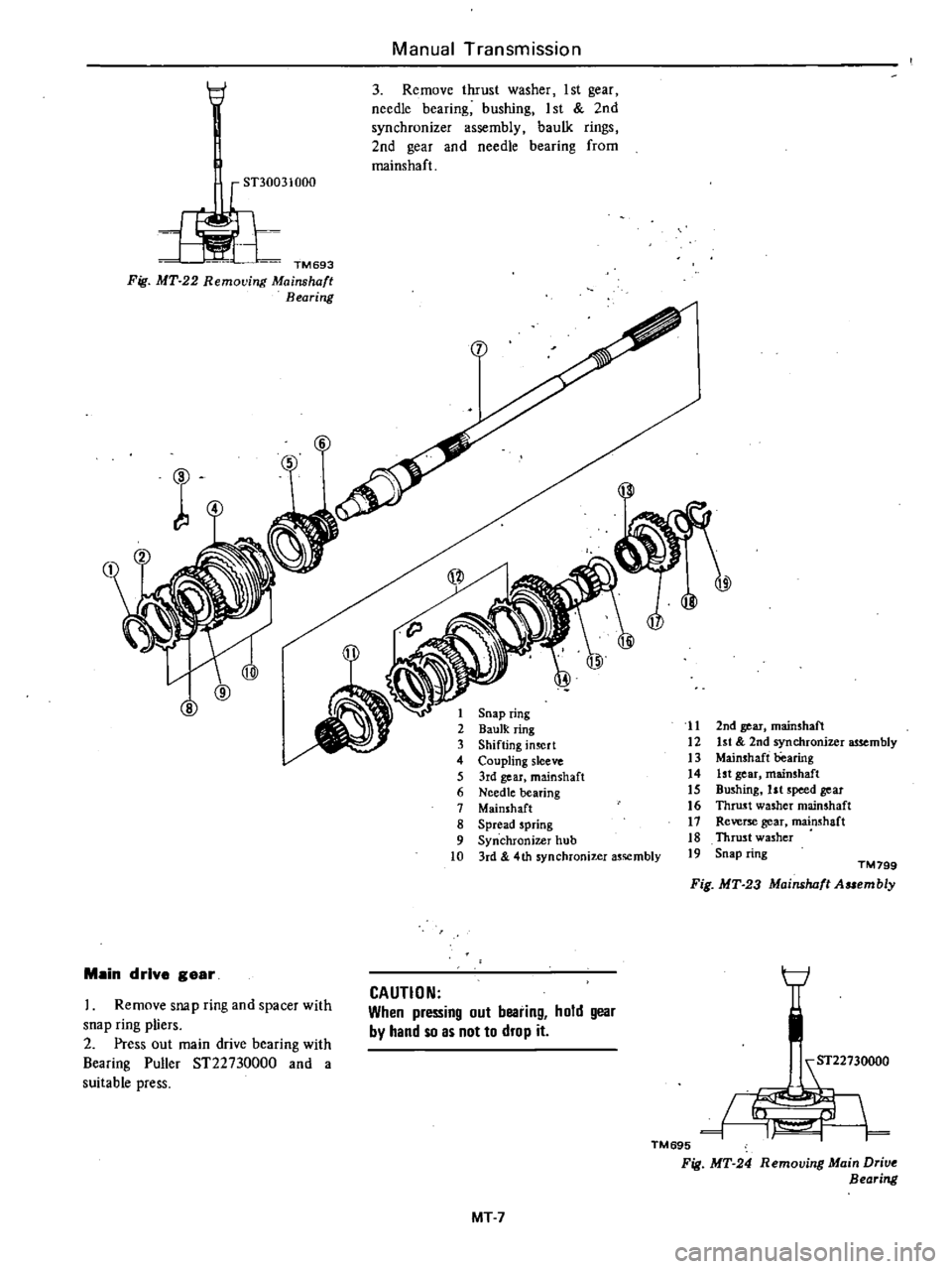
Manual
Transmission
3
Remove
thrust
washer
1
st
gear
needle
bearing
bushing
1st
2nd
synchronizer
assembly
baulk
rings
2nd
gear
and
needle
bearing
from
mains
haft
ST30031000
l
l
TM693
Fig
MT
22
RemotJing
Mainshaft
Bearing
fJ
I
@
00
1
Snap
ring
2
Baulk
ring
3
Shifting
imcrt
4
Coupling
sleeve
5
3rd
gear
mainshaft
6
Needle
bearing
7
Mainshaft
8
Spread
spring
9
Synchronil
er
hub
10
3rd
4th
synchroniz
er
assembly
II
2nd
gear
mainshat
t
12
ht
2nd
synchronizer
assembly
13
Mainshaft
bearing
14
1st
gear
mainshaft
15
Bushing
ht
speed
gear
16
Thrust
washer
mainshaft
11
Reverse
gear
mainshaCt
18
Thrust
washer
19
Snap
ring
TM799
Fig
MT
23
Mainshaft
A
mbly
Remove
sna
p
ring
and
spacer
with
snap
ring
pliers
2
Press
out
main
drive
bearing
with
Bearing
Puller
ST22730000
and
a
suitable
press
CAUTION
When
pressing
oul
bearing
hold
gear
by
hand
so
as
not
to
drop
it
1
Mein
drive
geer
ST22730000
TM
695
Fig
MT
24
Removing
Main
Drive
Bearing
MT7
Page 224 of 548
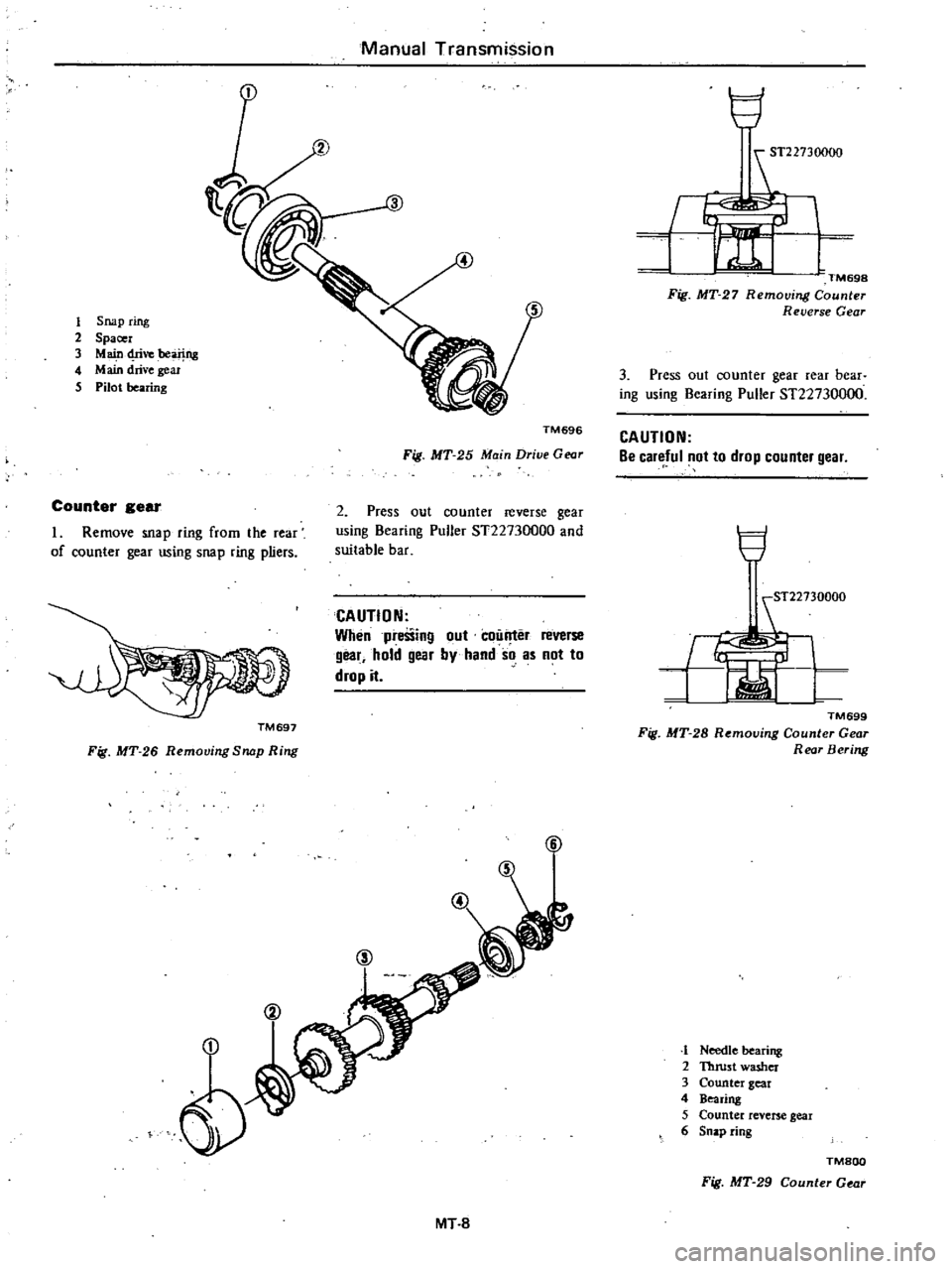
Manual
Transmission
1
Snap
ring
2
Spacer
3
MaiJl4rive
be
ng
4
Main
drive
gear
5
Pilot
bearing
TM696
Fig
MT
25
Main
Drive
Gear
Counter
gear
1
Remove
snap
ring
from
the
rear
of
counter
gear
using
snap
ring
pliers
2
Press
out
counter
reverse
gear
using
Bearing
Puller
ST22730000
and
suitable
bar
CAUTION
When
pressing
out
coiinter
reverse
gear
hold
gear
by
hand
so
as
not
to
drop
it
TM697
Fig
MT
26
Removing
Snap
Ring
@
5
i
MT
8
H
J
TM698
Fig
MT
27
Removing
Counter
Reverse
Gear
3
Press
out
counter
gear
rear
bear
ing
using
Bearing
Puller
ST22730000
CAUTION
Be
careful
01
to
drop
counter
gear
9
iL
TM699
Fig
MT
28
Removing
Counter
Gear
Rear
Bering
1
Needle
bearing
2
Thrust
washer
3
Counter
gear
4
Bearing
5
Counter
reverse
gear
6
Snap
ring
TM800
Fig
MT
29
Counter
Gear
Page 225 of 548
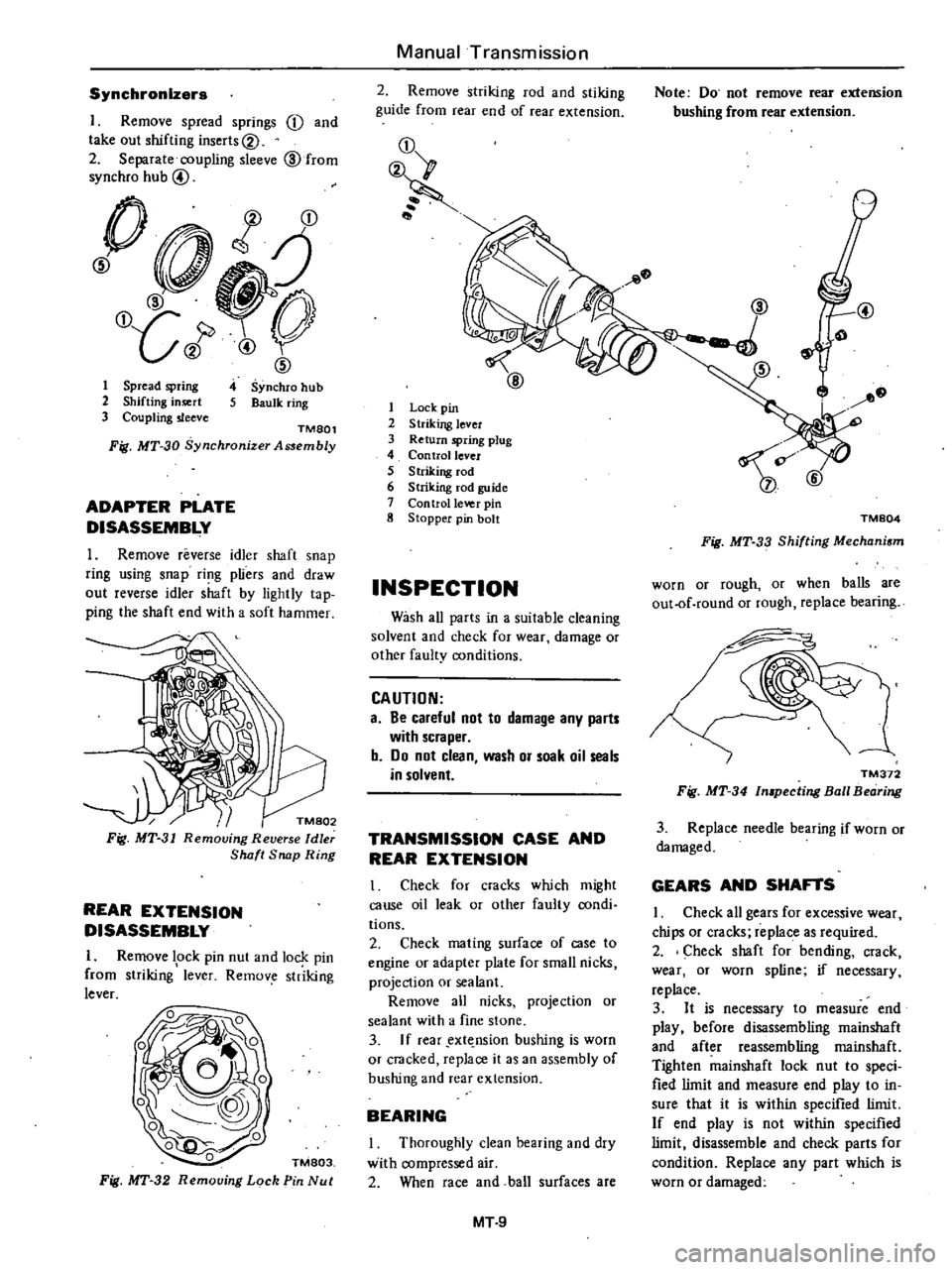
Synchronizers
I
Remove
spread
springs
j
and
take
out
shifting
inserts@
2
Separate
coupling
sleeve
@
from
synchro
hub
@
0
t
j
@
O
LJ
J
1
ID
4
Synchro
hub
S
Baulk
ring
1
Spread
spring
2
Shifting
insert
3
Coupling
sleeve
TMSOl
Fig
MT
30
Synchronjzer
Assembly
ADAPTER
PLATE
DISASSEMBLY
1
Remove
reverse
idler
shaft
snap
ring
using
snap
ri
1g
pliers
and
draw
out
reverse
idler
shaft
by
lightly
tap
ping
the
shaft
end
with
a
soft
hammer
k
Fig
MT
31
Removing
Reverse
Idler
Shaft
Snap
Ring
REAR
EXTENSION
DISASSEMBLY
I
Remove
lock
pin
nut
and
lock
pin
from
striking
1
lever
Remov
str
iking
lever
TM803
Fig
MT
32
Removing
Lock
Pin
Nut
Manual
Transmission
2
Remove
striking
rod
and
stiking
guide
from
rear
end
of
rear
extension
j
1
Lock
pin
2
Striking
lever
3
Return
spring
plug
4
Con
trollevcr
5
Striking
rod
6
Striking
fod
guide
7
Control
Ie
o
eI
pin
8
Stopper
pin
bolt
INSPECTION
Wash
all
parts
in
a
suitable
cleaning
solvent
and
check
for
wear
damage
or
other
faulty
conditions
CAUTION
a
Be
careful
not
to
damage
any
parts
with
scraper
b
Do
not
clean
wash
or
soak
oil
seals
in
solvent
TRANSMISSION
CASE
AND
REAR
EXTENSION
I
Check
for
cracks
which
might
cause
oil
leak
or
other
faulty
condi
tions
2
Check
mating
surface
of
case
to
engine
or
adapter
plate
for
small
nicks
projection
or
sealant
Remove
all
nicks
projection
or
sealant
with
a
fine
stone
3
If
rear
ext
nsion
bushing
is
worn
or
cracked
replace
it
as
an
assembly
of
bushing
and
rear
extension
BEARING
Thoroughly
clean
bearing
and
dry
with
compressed
air
2
When
race
and
ball
surfaces
are
MT
9
Note
Do
not
remove
rear
extension
bushing
from
rear
extension
@
TM804
Fig
MT
33
Shifting
Mechanism
worn
or
rough
or
when
balls
are
out
of
round
or
rough
replace
bearing
TM372
Fig
MT
34
In
pecting
Ball
Bearing
3
Replace
needle
bearing
if
worn
or
damaged
GEARS
AND
SHAFTS
I
Check
all
gears
for
excessive
wear
chips
or
cracks
replace
as
required
2
Check
shaft
for
bending
crack
wear
or
worn
spline
if
necessary
replace
3
It
is
necessary
to
measure
end
play
before
disassembling
mainshaft
and
after
reassembling
rnainshaft
Tighten
mainshaft
lock
nut
to
speci
fied
limit
and
measure
end
play
to
in
sure
that
it
is
within
specified
limit
If
end
play
is
not
within
specified
limit
disassemble
and
check
parts
for
condition
Replace
any
part
which
is
worn
or
damaged
Page 226 of 548
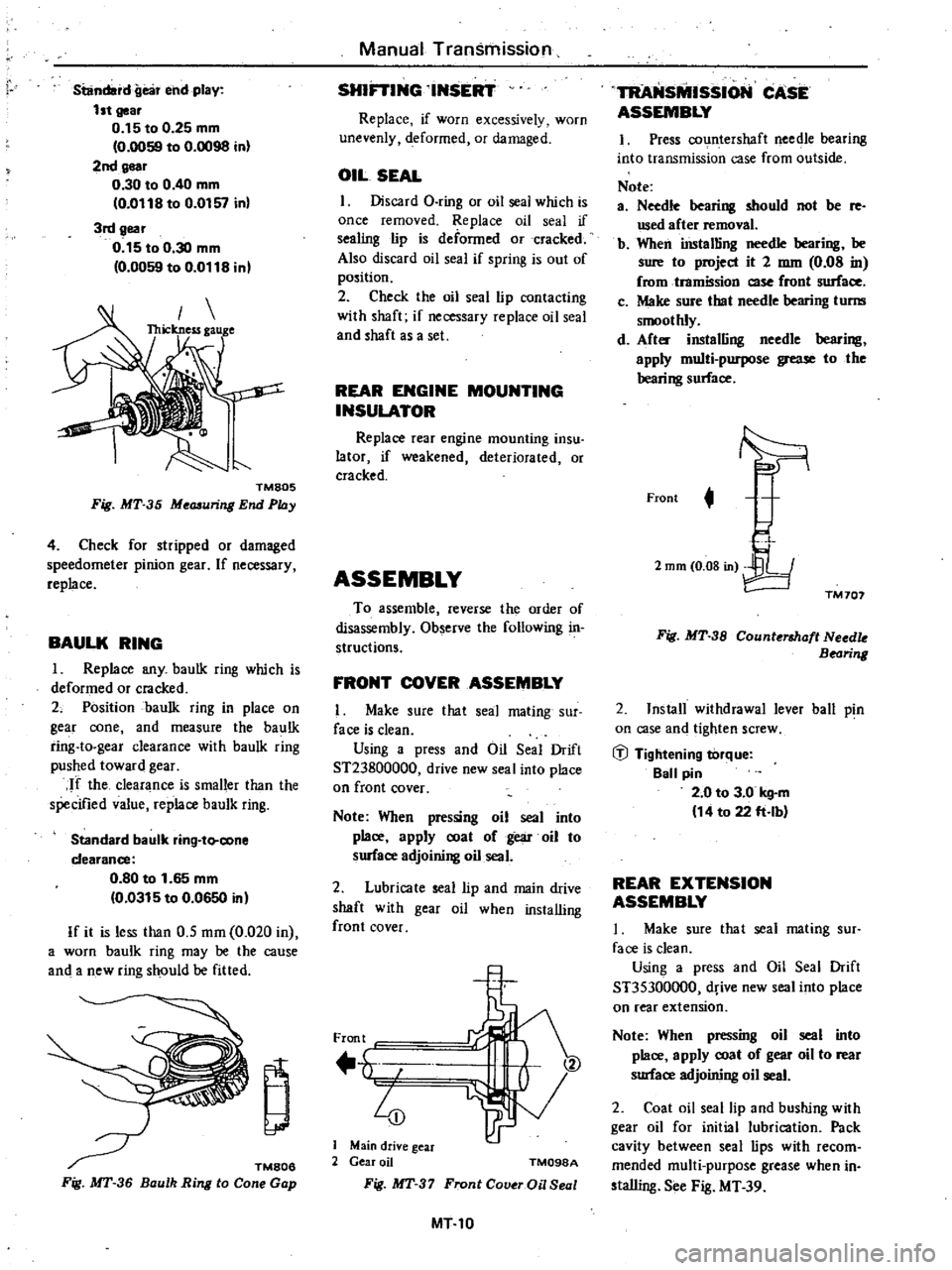
standard
gea
end
play
1st
gear
0
15
to
0
25
mm
0
0059
to
0
0098
inl
2nd
gear
0
30
to
0
40
mm
0
0118
to
0
0157
in
3rd
gear
0
15
to
0
30
mm
0
0059
to
0
0118
in
TMB05
Fig
MT
35
Me
uring
End
Phly
4
Check
for
stripped
or
damaged
speedometer
pinion
gear
If
necessary
replace
BAULK
RING
1
Replace
any
baulk
ring
which
is
deformed
or
cracked
2
Position
baulk
ring
in
place
on
gear
cone
and
measure
the
baulk
ring
to
gear
clearance
with
baulk
ring
pushed
toward
gear
If
the
clearance
is
smaller
than
the
specified
value
replace
baulk
ring
Standard
baulk
ring
to
cone
clearance
0
80
to
1
65
mm
0
0315
to
0
0650
inl
If
it
is
less
than
0
5
mm
0
020
in
a
worn
baulk
ring
may
be
the
cause
and
a
new
ring
should
be
fitted
TM806
Fig
MT
36
Baulh
Ring
10
Cone
Gap
Manual
Transmission
SHlFTING
INSERT
Replace
if
worn
excessively
worn
unevenly
deformed
or
damaged
OIL
SEAL
I
Discard
a
ring
or
oil
seal
which
is
once
removed
Replace
oil
seal
if
sealing
lip
is
deformed
Or
cracked
Also
discard
oil
seal
if
spring
is
out
of
position
2
Check
the
oil
seal
lip
contacting
with
shaft
if
necessary
replace
oil
seal
and
shaft
as
a
set
REAR
ENGINE
MOUNTING
INSULATOR
Replace
rear
engine
mounting
insu
lator
if
weakened
deteriorated
or
cracked
ASSEMBLY
To
assemble
reverse
the
order
of
disassembly
Observe
the
following
in
structions
FRONT
COVER
ASSEMBLY
I
Make
sure
that
seal
mating
sur
face
is
clean
Using
a
press
and
Oil
Seal
Drift
ST23800000
drive
new
seal
into
place
on
front
cover
Note
When
pressing
oil
seal
into
place
apply
coat
of
gear
oil
to
surface
adjoining
oil
seal
2
Lubricate
seal
lip
and
main
drive
shaft
with
gear
oil
when
installing
front
cover
Front
4
Main
drive
gear
2
Gear
oil
TM098A
Fig
MT
37
Fronl
Cover
Oil
Seal
MT10
TRANsMISSION
CASE
ASSEMBLY
1
Press
countershaft
needle
bearing
into
transmission
case
from
outside
Note
a
Needle
bearing
should
not
be
fe
used
after
removal
b
When
iDstalling
needle
bearing
be
sure
to
project
it
2
mm
0
08
in
fromtramission
so
front
surface
c
Make
sure
that
needle
bearing
turm
smoothly
d
After
installing
needle
bearing
apply
multi
purpose
grease
to
the
bearing
surface
Front
t
2
mm
0
08
in
TM
707
Fig
MT
38
Counterlhaft
Needk
Bearing
2
Install
withdrawal
lever
ball
pin
on
case
and
tighten
screw
iJ
Tightening
torque
Ball
pin
2
0
to
3
0
kg
m
14
to
22
ft
lb
REAR
EXTENSION
ASSEMBLY
I
Make
sure
that
seal
mating
sur
face
is
clean
Using
a
press
and
Oil
Seal
Drift
ST35300000
drive
new
seal
into
place
on
rear
extension
Note
When
pressing
oil
seal
into
place
apply
coat
of
gear
oil
to
rear
smace
adjoining
oil
seal
2
Coat
oil
seal
lip
and
bushing
with
gear
oil
for
initial
lubri
tion
Pack
cavity
between
seal
lips
with
recom
mended
multi
purpose
grease
when
in
sta1ling
See
Fig
MT
39
Page 227 of 548
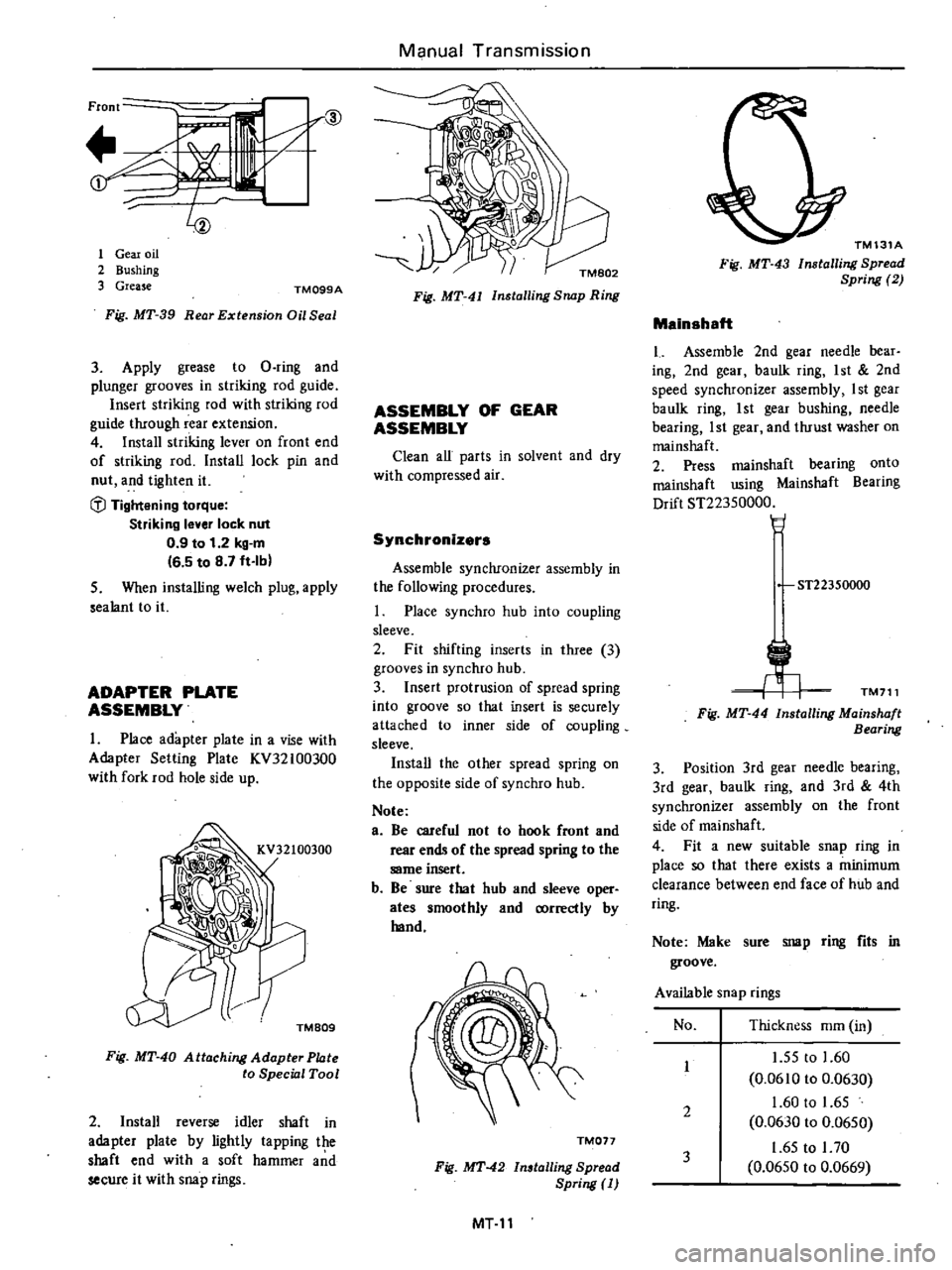
Front
if
r@
t
1
1
Gear
oil
2
Bushing
3
Grease
TM099A
Fig
MT
39
Rear
Extension
Oil
Seal
3
Apply
grease
to
D
ring
and
plunger
grooves
in
striking
rod
guide
Insert
striking
rod
with
striking
rod
guide
through
rear
extension
4
Install
striking
lever
on
front
end
of
striking
rod
Install
lock
pin
and
nut
and
tighten
it
fl
Tightening
torque
Striking
lever
lock
nut
0
9
to
1
2
kg
m
16
5
to
8
7
ft
Ib
5
When
installing
welch
plug
apply
sealant
to
it
ADAPTER
PLATE
ASSEMBLY
1
Place
adapter
plate
in
a
vise
with
Adaptet
Selling
Plate
KV32100300
with
fork
rod
hole
side
up
TMB09
Fig
MT
40
Attaching
Adapter
Phlte
to
Special
Tool
2
Install
reverse
idler
shaft
in
adapter
plate
by
lightly
tapping
the
shaft
end
with
a
soft
hammer
a
d
secure
it
with
snap
rings
Manual
Transmission
Fig
MT
4J
Installing
Snap
Ring
ASSEMBLY
OF
GEAR
ASSEMBLY
Clean
all
parts
in
solvent
and
dry
with
compressed
air
Synchronizers
Assemble
synchronizer
assembly
in
the
following
procedures
Place
synchro
hub
into
coupling
sleeve
2
Fit
shifting
inserts
in
three
3
grooves
in
synchro
hub
3
Insert
protrusion
of
spread
spring
into
groove
so
that
insert
is
securely
attached
to
inner
side
of
coupling
sleeve
Install
the
other
spread
spring
on
the
opposite
side
of
synchro
hub
Note
e
Be
careful
not
to
hook
front
and
rear
ends
of
the
spread
spring
to
the
same
insert
b
Be
sure
that
hub
and
sleeve
oper
ates
smoothly
and
correctly
by
hand
TM017
Fig
MT
42
Installing
Spread
Spring
MT
11
TM131A
Fig
MT
43
Installing
Spread
Spring
2
Mainshaft
Assemble
2nd
gear
needle
bear
ing
2nd
gear
baulk
ting
1
st
2nd
speed
synchronizer
assembly
I
st
gear
baulk
ring
1st
gear
bushing
needle
bearing
1st
gear
and
thrust
washer
on
mainshaft
2
Press
mainshaft
bearing
onto
mainshaft
using
Mainshaft
Bearing
Drift
ST22350000
H
ST22350000
TM711
Fig
MT
44
Installing
Mainshaft
Bearing
3
Position
3rd
gear
needle
bearing
3rd
gear
baulk
ring
and
3rd
4th
synchronizer
assembly
on
the
front
side
of
mainshaft
4
Fit
a
new
suitable
snap
ring
in
place
so
that
there
exists
a
minimum
clearance
between
end
face
of
hub
and
ring
Note
Make
sure
snap
ring
fits
in
groove
Available
snap
rings
No
Thickness
mm
in
1
55
to
1
60
0
0610
to
0
0630
1
60
to
1
65
0
0630
to
0
0650
1
65
to
I
70
0
0650
to
0
0669
1
2
3
Page 228 of 548
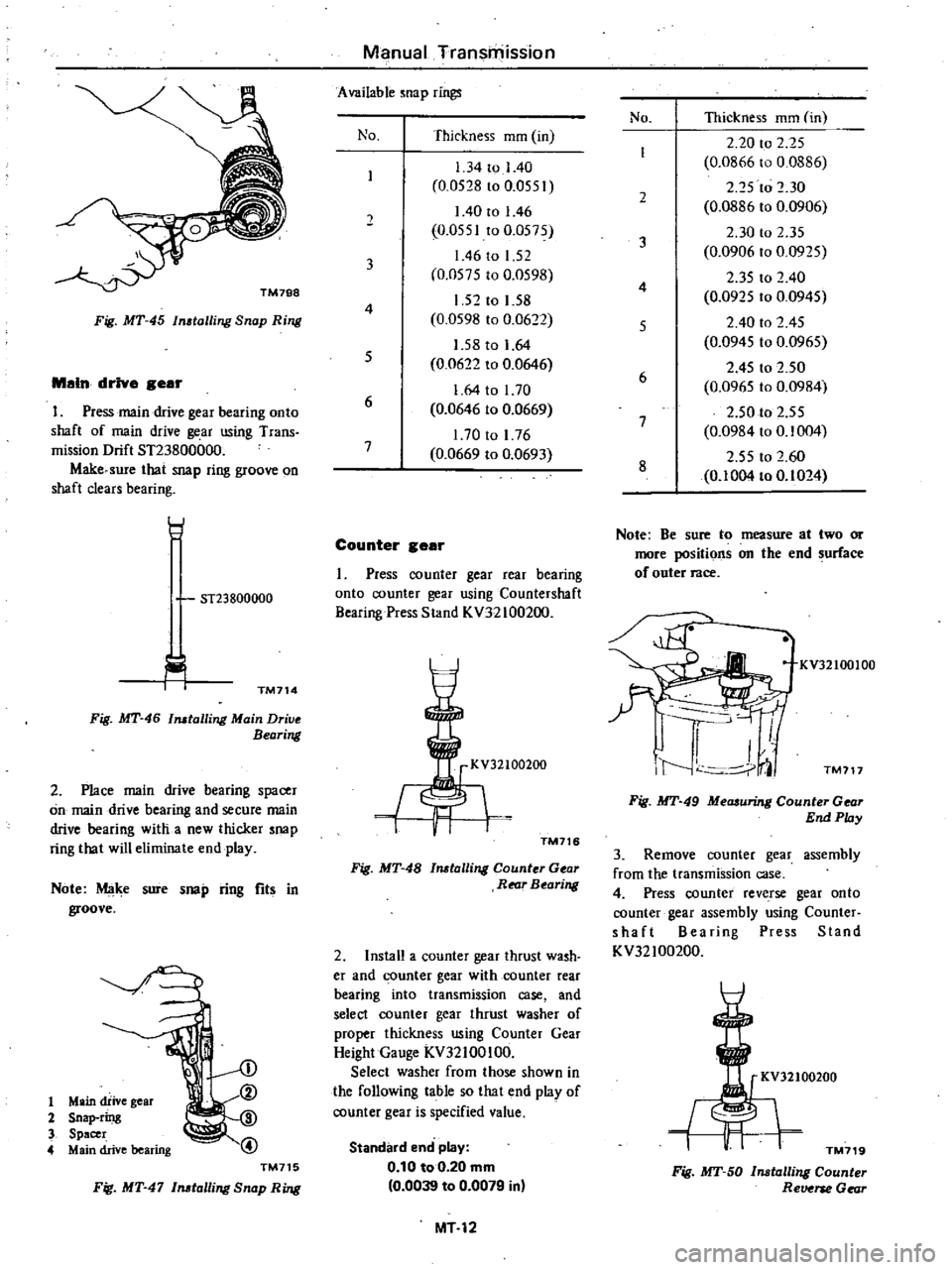
TM798
Fig
MT
45
In
talling
Snap
Ring
Main
drive
Bear
I
Press
main
drive
gear
bearing
onto
shaft
of
main
drive
gear
using
Trans
mission
Drift
ST23800000
Make
sure
that
snap
ring
groove
00
shaft
clears
bearing
L
i
ST23800000
TM714
Fig
MT
46
Imtalling
Main
Drive
Bearing
2
Place
main
drive
bearing
spacer
on
main
drive
bearing
and
secure
main
drive
bearing
with
a
new
thicker
soap
ring
that
will
eliminate
end
play
Note
Mlike
sure
soap
ring
fits
in
groove
1
Main
d
ive
gear
2
Snap
ring
3
Spacer
4
Main
drive
bearing
TM715
Fig
MT
47
Irutalling
Snap
Ring
Manual
Transmission
Available
nap
rings
No
Thickness
mm
in
No
Thickness
mm
in
2
20
to
2
25
1
34
to
1
40
0
0866
to
0
0886
0
0528
to
0
0551
2
25
to
2
30
2
0
0886
to
0
0906
140rol46
2
0
0551
to
0
0575
2
30
to
2
35
3
146
to
1
52
0
0906
to
0
0925
3
0
0575
to
0
0598
2
35
to
2
40
4
1
52
to
1
58
0
0925
to
0
0945
4
0
0598
to
0
0622
2
40
to
2
45
5
1
58
to
1
64
0
0945
to
0
0965
5
0
0622
to
0
0646
2
45
to
2
50
6
0
0965
to
0
0984
1
64
to
1
70
6
0
0646
to
0
0669
2
50
to
2
55
7
1
70
to
I
76
0
0984
to
0
1004
7
0
0669
to
0
0693
2
55
to
2
60
8
0
1004100
1024
Counter
Beer
Note
Be
sure
to
measure
at
two
or
more
positions
on
the
end
urface
of
outer
race
1
Press
counter
gear
rear
bearing
onto
counter
gear
usingCountershaft
Bearing
Press
Stand
KV32
100200
KV32100100
r
I
J
I
1
T
II
I
TM117
Fig
MT
49
Mecuuring
Counter
Gear
End
Phly
TM716
Fig
MT
48
Installing
Counter
Gear
Rear
Bearing
3
Remove
counter
gear
assembly
from
the
transmission
case
4
Press
counter
reverse
gear
onto
counter
gear
assembly
using
Counter
shaft
Bearing
Press
Stand
KV32
100200
2
Install
a
counter
gear
thrust
wash
er
and
unter
gear
with
counter
rear
bearing
into
transmission
case
and
select
counter
gear
thrust
washer
of
proper
thickness
using
Counter
Gear
Height
Gauge
KV32
100
100
Select
washer
from
those
shown
in
the
following
table
so
that
end
play
of
counter
gear
is
specified
value
KV32100200
Standard
end
play
0
10
to
0
20
mm
0
0039
to
0
0079
in
TM719
Fig
MT
50
Installing
Counter
Revene
Gear
MT12
Page 229 of 548
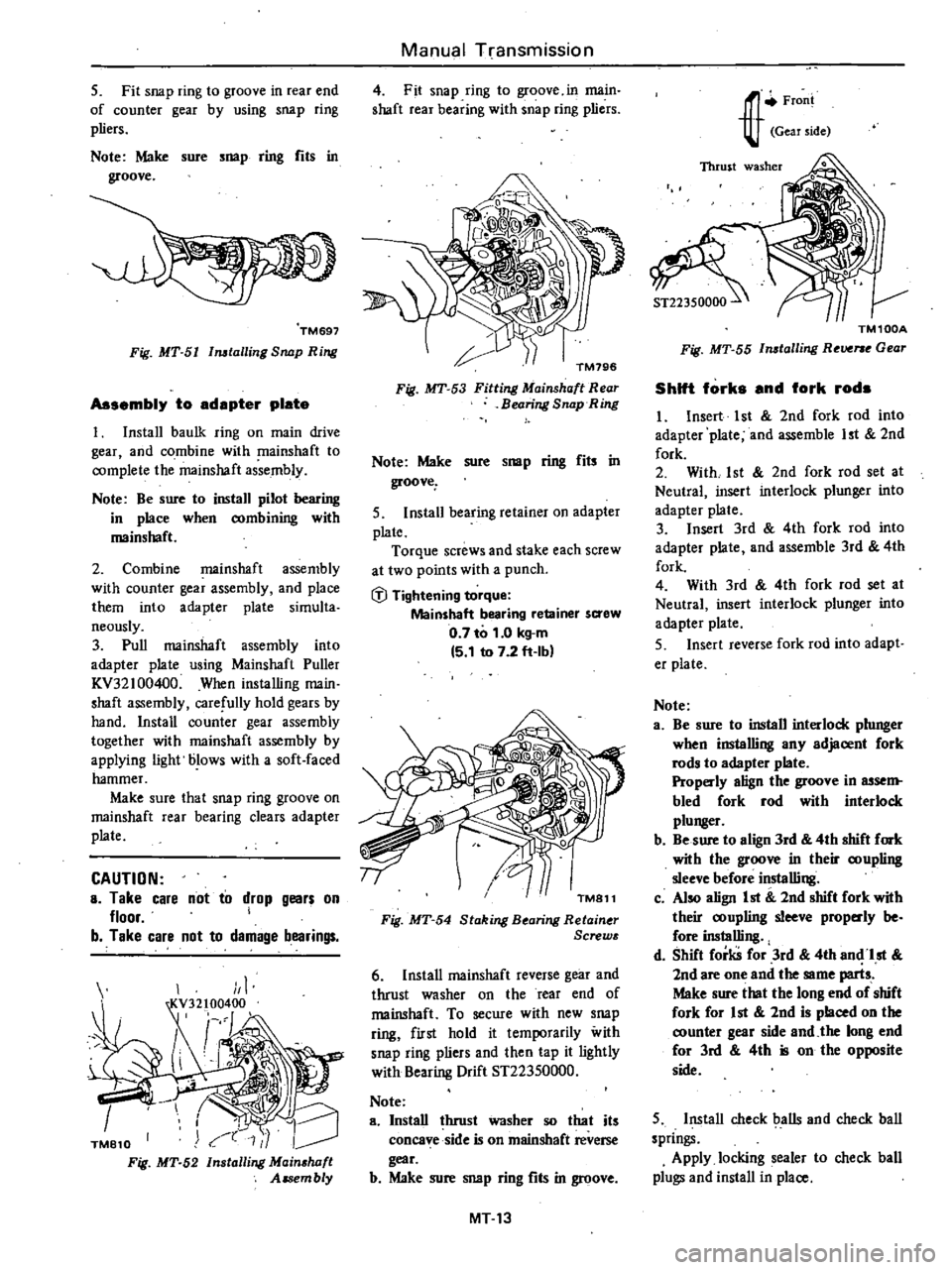
5
Fit
snap
ring
to
groove
in
rear
end
of
counter
gear
by
using
snap
ring
pliers
Note
Maire
sure
snap
ring
fits
in
groove
TM697
Fig
MT
5I
Imtalling
Snap
Ring
Assembly
to
adapter
plate
t
Install
baulk
ring
on
main
drive
gear
and
combine
with
mainshaft
to
complete
the
mainshaft
assembly
Note
Be
sure
to
install
pilot
bearing
in
place
when
combining
with
mainshaft
2
Combine
mainshaft
assembly
with
counter
gear
assembly
and
place
them
into
adapter
plate
simulta
neously
3
Pull
mainshaft
assembly
into
adapter
plate
using
Mainshaft
Puller
KV32
100400
When
installing
main
shaft
assembly
carefully
hold
gears
by
hand
Install
counter
gear
assembly
together
with
mainshaft
assembly
by
applying
light
blows
with
a
soft
faced
hammer
Make
sure
that
snap
ring
groove
on
mainshaft
rear
bearing
clears
adapter
plate
CAUTION
a
Take
care
not
to
drop
gears
on
floor
I
b
Take
care
not
to
damage
bearings
TM810
Fig
MT
52
1
Installing
Mainshaft
Assembly
Manual
Transmission
4
Fit
snap
ring
to
groove
in
main
shaft
rear
bearing
with
snap
ring
pliers
TM796
Fig
MT
53
Fitting
Mainshaft
Rear
Bearing
Snap
Ring
Note
Make
sure
snap
ring
fils
in
groove
5
Install
bearing
retainer
on
adapter
plate
Torque
screws
and
stake
each
screw
at
two
points
with
a
punch
fj
Tightening
torque
Mainshaft
bearing
retainer
saew
0
7
to
1
0
kg
m
15
1
to
7
2
ft
Ibl
TM811
Fig
MT
54
Staking
B
aring
Retain
r
Screw
6
Install
mainshaft
reverse
gear
and
thrust
washer
on
the
rear
end
of
mainshaft
To
secure
with
new
snap
ring
first
hold
it
temporarily
with
snap
ring
pliers
and
then
tap
it
lightly
with
Bearing
Drift
ST22350000
Note
a
Install
lhrust
washer
so
that
its
concave
side
is
on
mainshaet
reverse
gear
b
Make
sure
snap
ring
fits
in
groove
MT
13
J
r
Froni
Gear
side
TM100A
Fig
MT
55
Imtalling
R
Vf
e
Gear
Shift
forks
and
fork
rods
I
Insert
1st
2nd
fork
rod
into
adapter
plate
and
assemble
1st
2nd
fork
2
With
1st
2nd
fork
rod
set
at
Neutral
insert
interlock
plunger
into
adapter
plate
3
Insert
3rd
4th
fork
rod
into
adapter
plate
and
assemble
3rd
4th
fork
4
With
3rd
4th
fork
rod
set
at
Neutral
insert
interlock
plunger
into
adapter
plate
S
Insert
reverse
fork
rod
into
adapt
er
plate
Nole
a
Be
sure
to
install
interlock
plunger
when
installing
any
adjacent
fork
rods
to
adapter
plate
Properly
align
the
groove
in
assem
bled
fork
rod
with
interlock
plunger
b
Be
sure
to
align
3rd
4th
shift
fork
wilh
the
groove
in
their
coupling
sleeve
before
installing
c
Also
align
1st
2nd
shift
fork
with
their
coupling
sleeve
prop
dy
be
fore
inslalling
d
Shift
forks
for
3rd
4th
an
1st
2nd
are
one
and
the
same
parts
Make
sure
that
the
long
end
of
shift
fork
for
1st
2nd
is
placed
on
the
counter
gear
side
and
the
long
end
for
3rd
4th
is
on
the
opposite
side
5
Install
check
balls
and
check
ball
springs
Apply
locking
sealer
to
check
ball
plugs
and
install
in
place
Page 230 of 548
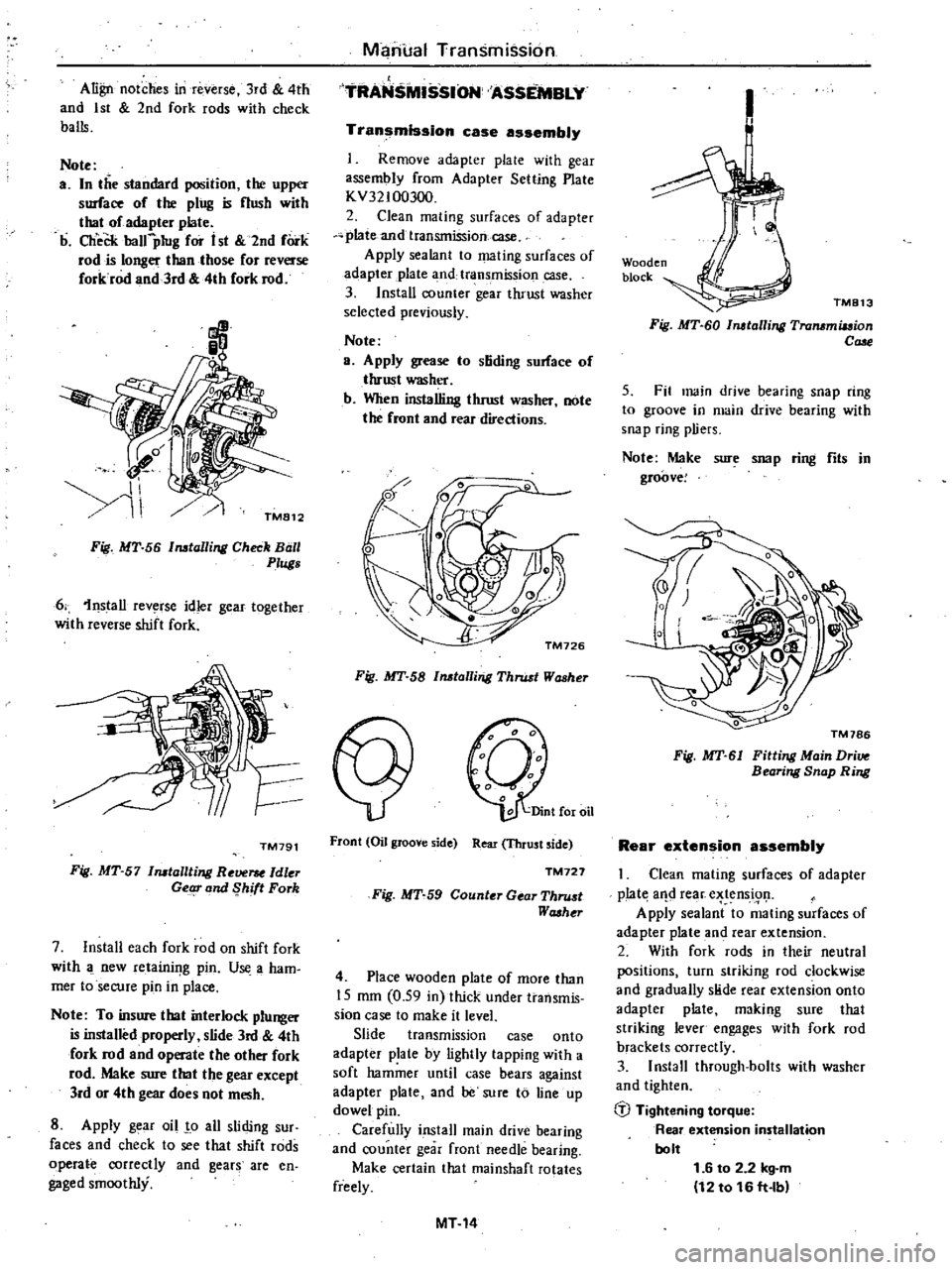
Align
notches
in
reverse
3rd
4th
and
1st
2nd
fork
rods
with
check
balls
Note
a
In
the
standard
position
the
upper
surface
of
the
ping
is
nush
with
thaI
of
adapter
plate
b
CheCk
balfpIug
for
i
st
2nd
fork
rod
is
longer
than
those
for
reverse
forkrod
and
3rd
4th
fork
rod
Manual
Transmission
TRANS
SSION
ASSEMBLY
Transmission
case
assembly
Remove
adapter
plale
with
gear
assembly
from
Adapter
Setting
Plate
KV32100300
2
Clean
mating
surfaces
of
adapter
plate
and
transmission
case
Apply
sealant
to
mating
surfaces
of
adapter
plate
3
nd
transmission
case
3
Install
counter
gear
thrust
washer
selected
previously
Note
a
Apply
grease
to
stiding
sorface
of
thrust
washer
b
When
installing
thrust
washer
note
the
front
and
rear
directions
Fig
MT
56
Installing
Check
Ball
0
Plugs
6
1nstall
rev
rse
idler
gear
together
with
reverse
shift
fork
TM791
Fig
MT
57
Installting
Re
ldler
Getg
and
Shift
Fork
7
Install
each
fork
rod
on
shift
fork
with
new
retainif
g
pin
U
a
ham
mer
toseCUfe
pin
in
place
Note
To
insure
that
interlock
plunger
is
installed
properly
slide
3rd
4th
fork
rod
and
operate
the
other
fork
rod
Make
sure
that
the
gear
except
lrd
or
4th
gear
does
not
mesh
8
Apply
g
ar
oil
o
all
sliding
sur
faces
and
check
to
see
that
shift
rods
operate
correctly
and
gears
are
en
gaged
smoothly
Fig
MT
58
Installing
Thrust
Washer
Front
Oil
groove
side
Rear
Thrust
side
TM727
Fig
MT
59
Counter
Gear
Thru
t
Washt
r
4
Place
wooden
plate
of
more
than
15
mm
0
59
in
thick
under
transmis
sion
case
to
make
it
level
Slide
transmission
case
onto
adapter
plate
by
lightly
tapping
with
a
soft
hammer
until
case
bears
against
adapter
plate
and
be
sure
to
line
up
dowel
pin
Carefully
install
main
drive
bearing
and
counter
gear
front
needle
bearing
Make
certain
that
rnainshaft
rotates
freely
MT14
1
Wooden
block
TM813
Fig
MT
60
Installing
Transmiuion
Cale
5
Fit
main
drive
bearing
snap
ring
to
groove
in
main
drive
bearing
with
snap
ring
pliers
Note
Make
sure
snap
ring
fits
in
groove
Fig
MT
61
Fitting
Main
Dri
Bearing
Snap
Ring
Rear
extension
assembly
Clean
mating
surfaces
of
adapter
p
Iat
aIld
rear
e
tens
i91
Apply
sealant
to
mating
surfaces
of
adapter
plate
and
rear
extension
2
With
fork
rods
in
their
neutral
positions
turn
striking
rod
clockwise
and
gradually
slide
rear
extension
onto
adapter
plate
making
sure
that
striking
lever
engages
with
fork
rod
brackets
correctly
3
Install
through
bolts
with
washer
and
tighten
b
Tightening
torque
Rear
extension
installation
bolt
1
6
to
2
2
kg
m
12
to
16
ft
lb