DODGE NEON 1999 Service Repair Manual
Manufacturer: DODGE, Model Year: 1999, Model line: NEON, Model: DODGE NEON 1999Pages: 1200, PDF Size: 35.29 MB
Page 951 of 1200
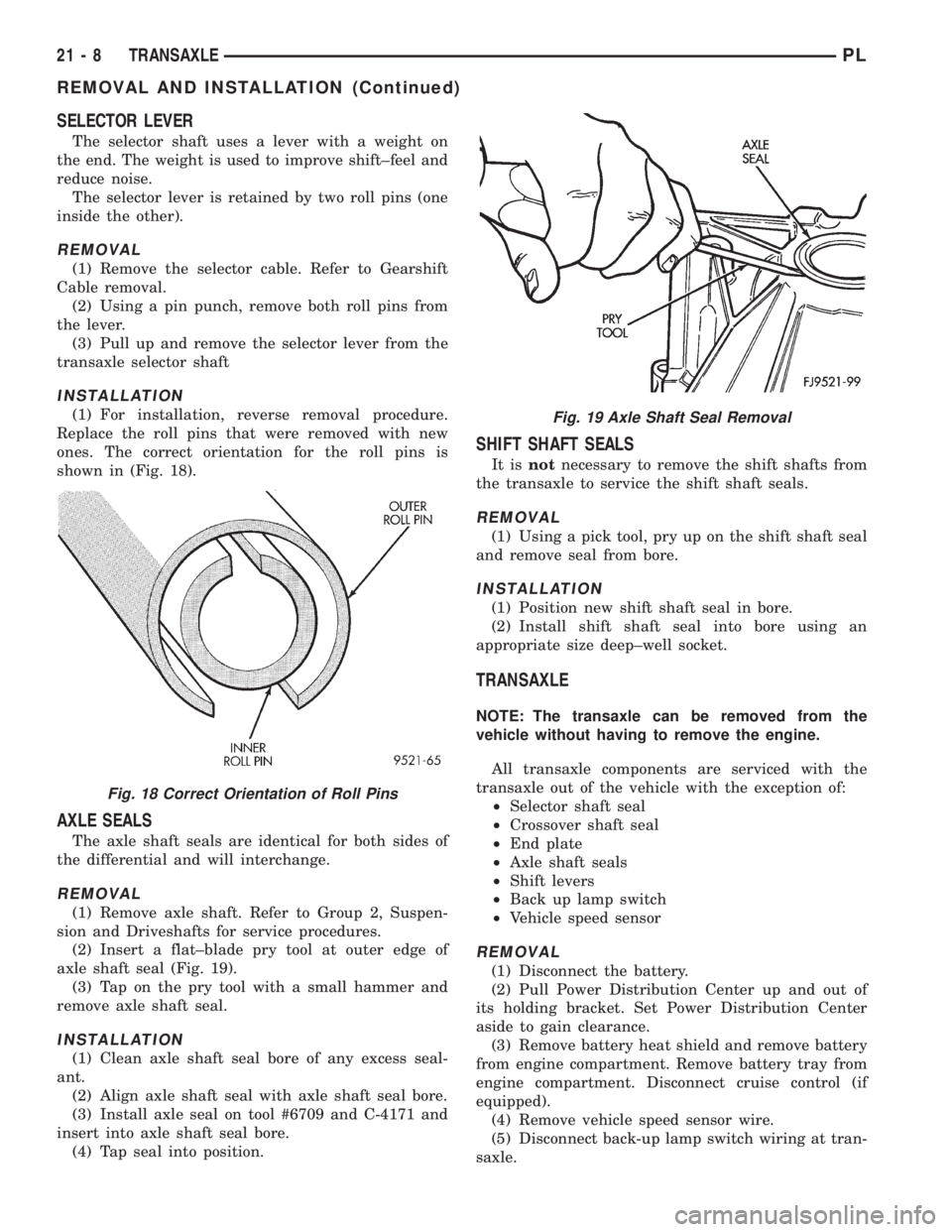
SELECTOR LEVER
The selector shaft uses a lever with a weight on
the end. The weight is used to improve shift±feel and
reduce noise.
The selector lever is retained by two roll pins (one
inside the other).
REMOVAL
(1) Remove the selector cable. Refer to Gearshift
Cable removal.
(2) Using a pin punch, remove both roll pins from
the lever.
(3) Pull up and remove the selector lever from the
transaxle selector shaft
INSTALLATION
(1) For installation, reverse removal procedure.
Replace the roll pins that were removed with new
ones. The correct orientation for the roll pins is
shown in (Fig. 18).
AXLE SEALS
The axle shaft seals are identical for both sides of
the differential and will interchange.
REMOVAL
(1) Remove axle shaft. Refer to Group 2, Suspen-
sion and Driveshafts for service procedures.
(2) Insert a flat±blade pry tool at outer edge of
axle shaft seal (Fig. 19).
(3) Tap on the pry tool with a small hammer and
remove axle shaft seal.
INSTALLATION
(1) Clean axle shaft seal bore of any excess seal-
ant.
(2) Align axle shaft seal with axle shaft seal bore.
(3) Install axle seal on tool #6709 and C-4171 and
insert into axle shaft seal bore.
(4) Tap seal into position.
SHIFT SHAFT SEALS
It isnotnecessary to remove the shift shafts from
the transaxle to service the shift shaft seals.
REMOVAL
(1) Using a pick tool, pry up on the shift shaft seal
and remove seal from bore.
INSTALLATION
(1) Position new shift shaft seal in bore.
(2) Install shift shaft seal into bore using an
appropriate size deep±well socket.
TRANSAXLE
NOTE: The transaxle can be removed from the
vehicle without having to remove the engine.
All transaxle components are serviced with the
transaxle out of the vehicle with the exception of:
²Selector shaft seal
²Crossover shaft seal
²End plate
²Axle shaft seals
²Shift levers
²Back up lamp switch
²Vehicle speed sensor
REMOVAL
(1) Disconnect the battery.
(2) Pull Power Distribution Center up and out of
its holding bracket. Set Power Distribution Center
aside to gain clearance.
(3) Remove battery heat shield and remove battery
from engine compartment. Remove battery tray from
engine compartment. Disconnect cruise control (if
equipped).
(4) Remove vehicle speed sensor wire.
(5) Disconnect back-up lamp switch wiring at tran-
saxle.
Fig. 18 Correct Orientation of Roll Pins
Fig. 19 Axle Shaft Seal Removal
21 - 8 TRANSAXLEPL
REMOVAL AND INSTALLATION (Continued)
Page 952 of 1200
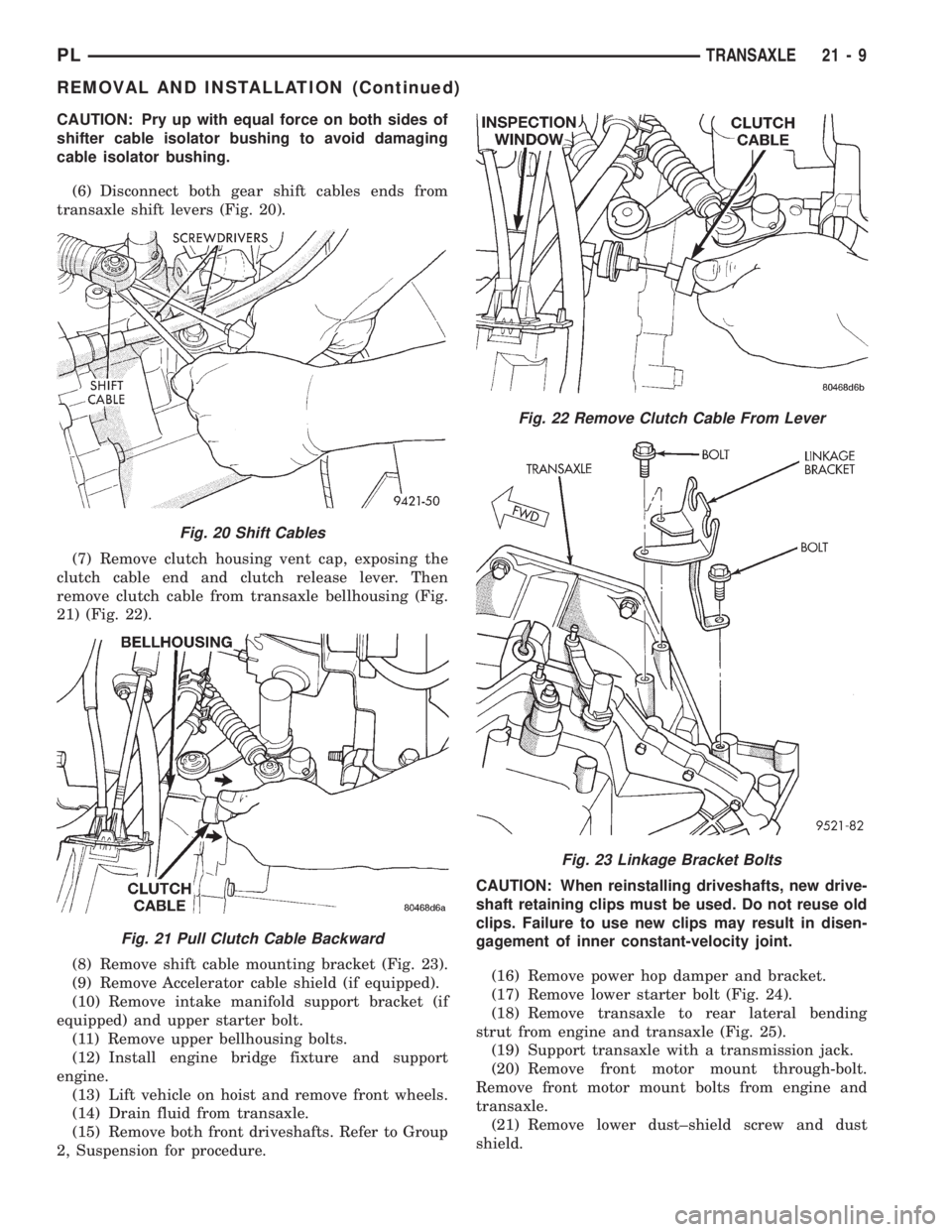
CAUTION: Pry up with equal force on both sides of
shifter cable isolator bushing to avoid damaging
cable isolator bushing.
(6) Disconnect both gear shift cables ends from
transaxle shift levers (Fig. 20).
(7) Remove clutch housing vent cap, exposing the
clutch cable end and clutch release lever. Then
remove clutch cable from transaxle bellhousing (Fig.
21) (Fig. 22).
(8) Remove shift cable mounting bracket (Fig. 23).
(9) Remove Accelerator cable shield (if equipped).
(10) Remove intake manifold support bracket (if
equipped) and upper starter bolt.
(11) Remove upper bellhousing bolts.
(12) Install engine bridge fixture and support
engine.
(13) Lift vehicle on hoist and remove front wheels.
(14) Drain fluid from transaxle.
(15) Remove both front driveshafts. Refer to Group
2, Suspension for procedure.CAUTION: When reinstalling driveshafts, new drive-
shaft retaining clips must be used. Do not reuse old
clips. Failure to use new clips may result in disen-
gagement of inner constant-velocity joint.
(16) Remove power hop damper and bracket.
(17) Remove lower starter bolt (Fig. 24).
(18) Remove transaxle to rear lateral bending
strut from engine and transaxle (Fig. 25).
(19) Support transaxle with a transmission jack.
(20) Remove front motor mount through-bolt.
Remove front motor mount bolts from engine and
transaxle.
(21) Remove lower dust±shield screw and dust
shield.
Fig. 20 Shift Cables
Fig. 21 Pull Clutch Cable Backward
Fig. 22 Remove Clutch Cable From Lever
Fig. 23 Linkage Bracket Bolts
PLTRANSAXLE 21 - 9
REMOVAL AND INSTALLATION (Continued)
Page 953 of 1200
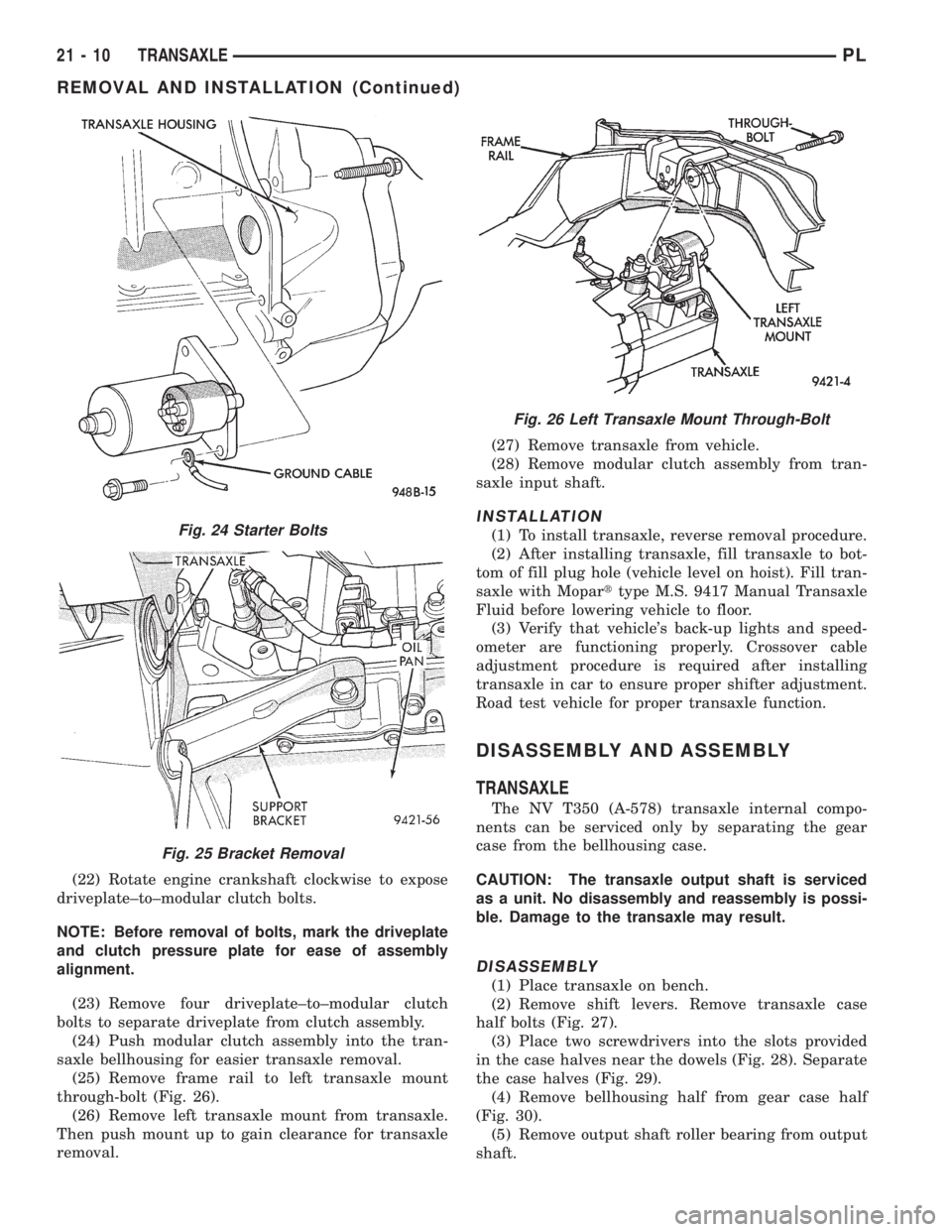
(22) Rotate engine crankshaft clockwise to expose
driveplate±to±modular clutch bolts.
NOTE: Before removal of bolts, mark the driveplate
and clutch pressure plate for ease of assembly
alignment.
(23) Remove four driveplate±to±modular clutch
bolts to separate driveplate from clutch assembly.
(24) Push modular clutch assembly into the tran-
saxle bellhousing for easier transaxle removal.
(25) Remove frame rail to left transaxle mount
through-bolt (Fig. 26).
(26) Remove left transaxle mount from transaxle.
Then push mount up to gain clearance for transaxle
removal.(27) Remove transaxle from vehicle.
(28) Remove modular clutch assembly from tran-
saxle input shaft.
INSTALLATION
(1) To install transaxle, reverse removal procedure.
(2) After installing transaxle, fill transaxle to bot-
tom of fill plug hole (vehicle level on hoist). Fill tran-
saxle with Moparttype M.S. 9417 Manual Transaxle
Fluid before lowering vehicle to floor.
(3) Verify that vehicle's back-up lights and speed-
ometer are functioning properly. Crossover cable
adjustment procedure is required after installing
transaxle in car to ensure proper shifter adjustment.
Road test vehicle for proper transaxle function.
DISASSEMBLY AND ASSEMBLY
TRANSAXLE
The NV T350 (A-578) transaxle internal compo-
nents can be serviced only by separating the gear
case from the bellhousing case.
CAUTION: The transaxle output shaft is serviced
as a unit. No disassembly and reassembly is possi-
ble. Damage to the transaxle may result.
DISASSEMBLY
(1) Place transaxle on bench.
(2) Remove shift levers. Remove transaxle case
half bolts (Fig. 27).
(3) Place two screwdrivers into the slots provided
in the case halves near the dowels (Fig. 28). Separate
the case halves (Fig. 29).
(4) Remove bellhousing half from gear case half
(Fig. 30).
(5) Remove output shaft roller bearing from output
shaft.
Fig. 24 Starter Bolts
Fig. 25 Bracket Removal
Fig. 26 Left Transaxle Mount Through-Bolt
21 - 10 TRANSAXLEPL
REMOVAL AND INSTALLATION (Continued)
Page 954 of 1200
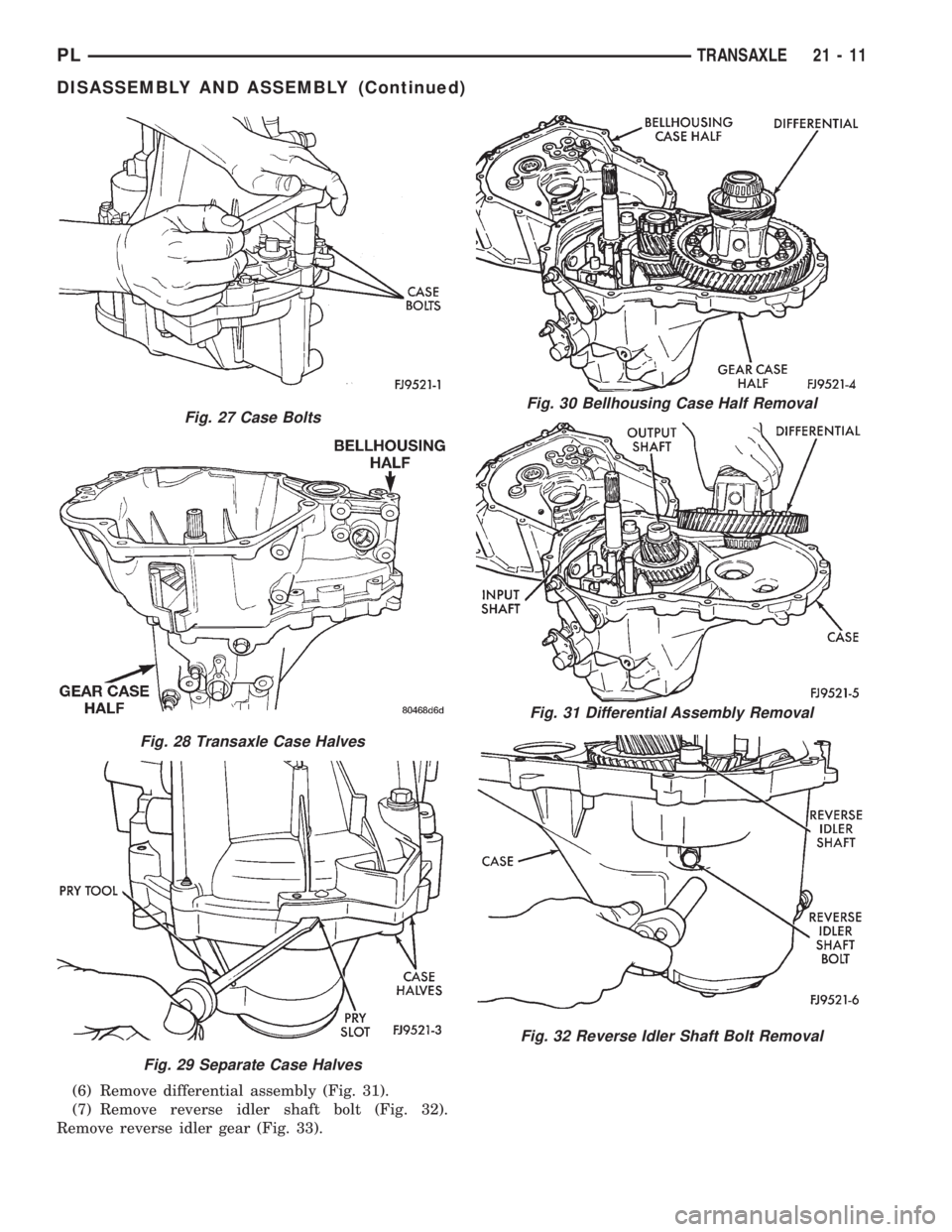
(6) Remove differential assembly (Fig. 31).
(7) Remove reverse idler shaft bolt (Fig. 32).
Remove reverse idler gear (Fig. 33).
Fig. 27 Case Bolts
Fig. 28 Transaxle Case Halves
Fig. 29 Separate Case Halves
Fig. 30 Bellhousing Case Half Removal
Fig. 31 Differential Assembly Removal
Fig. 32 Reverse Idler Shaft Bolt Removal
PLTRANSAXLE 21 - 11
DISASSEMBLY AND ASSEMBLY (Continued)
Page 955 of 1200
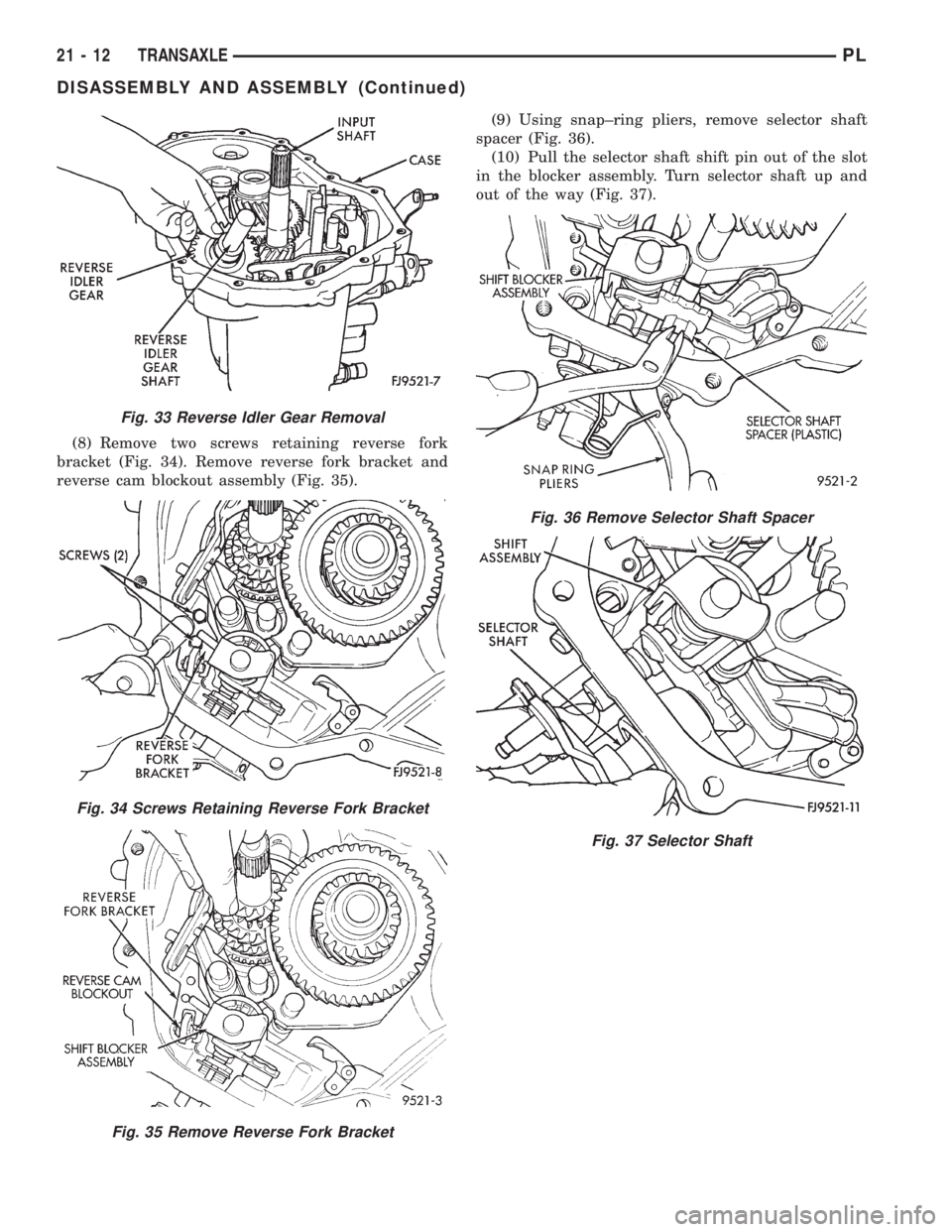
(8) Remove two screws retaining reverse fork
bracket (Fig. 34). Remove reverse fork bracket and
reverse cam blockout assembly (Fig. 35).(9) Using snap±ring pliers, remove selector shaft
spacer (Fig. 36).
(10) Pull the selector shaft shift pin out of the slot
in the blocker assembly. Turn selector shaft up and
out of the way (Fig. 37).
Fig. 33 Reverse Idler Gear Removal
Fig. 34 Screws Retaining Reverse Fork Bracket
Fig. 35 Remove Reverse Fork Bracket
Fig. 36 Remove Selector Shaft Spacer
Fig. 37 Selector Shaft
21 - 12 TRANSAXLEPL
DISASSEMBLY AND ASSEMBLY (Continued)
Page 956 of 1200
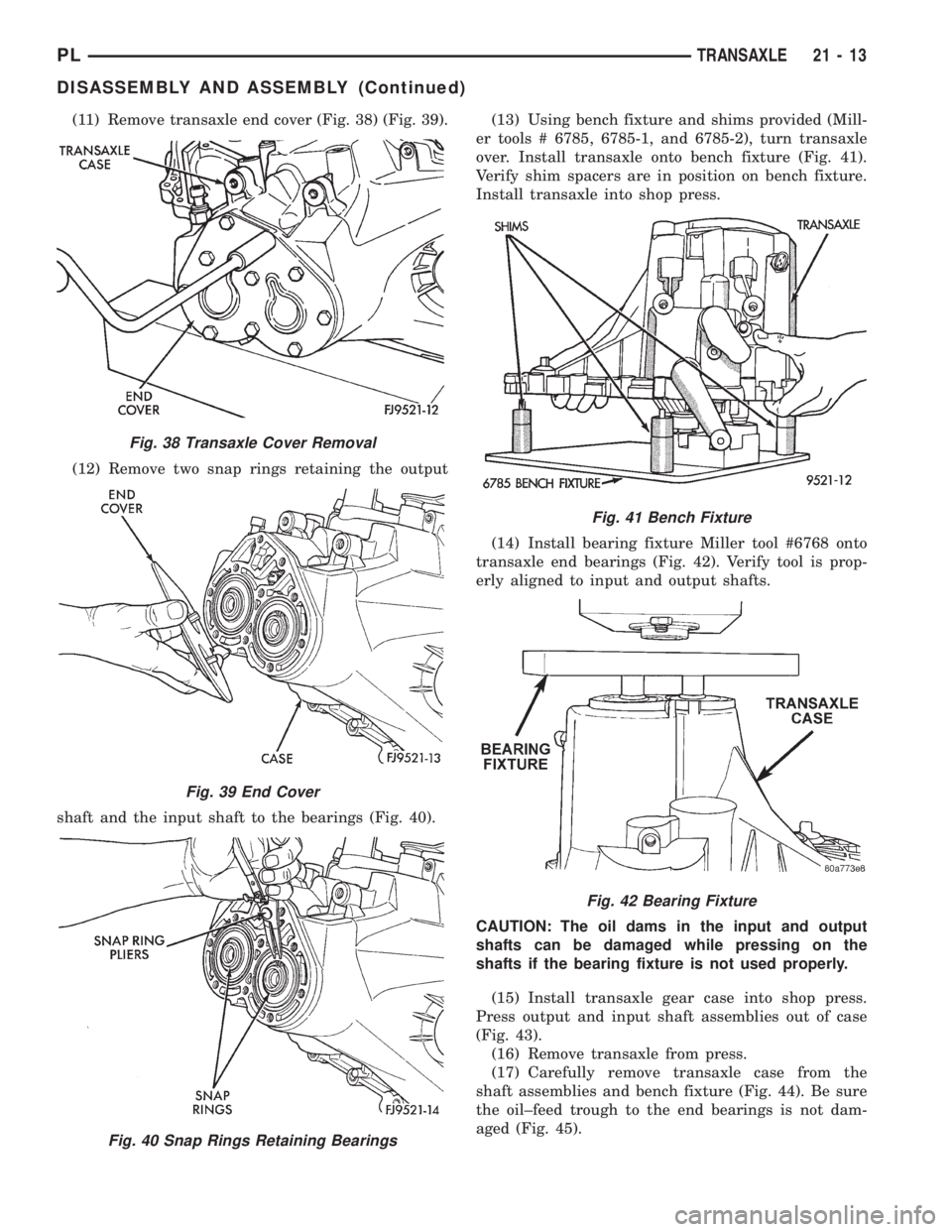
(11) Remove transaxle end cover (Fig. 38) (Fig. 39).
(12) Remove two snap rings retaining the output
shaft and the input shaft to the bearings (Fig. 40).(13) Using bench fixture and shims provided (Mill-
er tools # 6785, 6785-1, and 6785-2), turn transaxle
over. Install transaxle onto bench fixture (Fig. 41).
Verify shim spacers are in position on bench fixture.
Install transaxle into shop press.
(14) Install bearing fixture Miller tool #6768 onto
transaxle end bearings (Fig. 42). Verify tool is prop-
erly aligned to input and output shafts.
CAUTION: The oil dams in the input and output
shafts can be damaged while pressing on the
shafts if the bearing fixture is not used properly.
(15) Install transaxle gear case into shop press.
Press output and input shaft assemblies out of case
(Fig. 43).
(16) Remove transaxle from press.
(17) Carefully remove transaxle case from the
shaft assemblies and bench fixture (Fig. 44). Be sure
the oil±feed trough to the end bearings is not dam-
aged (Fig. 45).
Fig. 38 Transaxle Cover Removal
Fig. 39 End Cover
Fig. 40 Snap Rings Retaining Bearings
Fig. 41 Bench Fixture
Fig. 42 Bearing Fixture
PLTRANSAXLE 21 - 13
DISASSEMBLY AND ASSEMBLY (Continued)
Page 957 of 1200
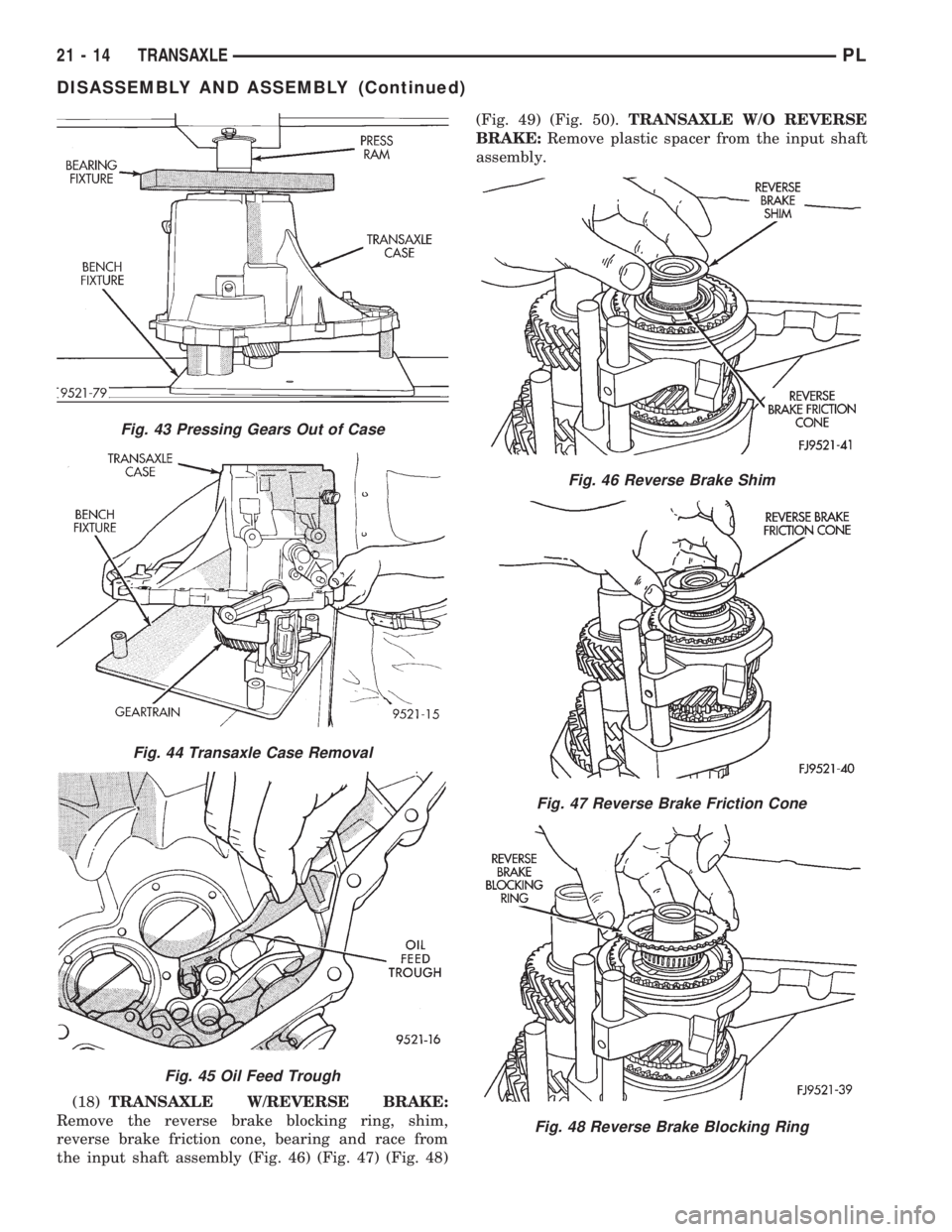
(18)TRANSAXLE W/REVERSE BRAKE:
Remove the reverse brake blocking ring, shim,
reverse brake friction cone, bearing and race from
the input shaft assembly (Fig. 46) (Fig. 47) (Fig. 48)(Fig. 49) (Fig. 50).TRANSAXLE W/O REVERSE
BRAKE:Remove plastic spacer from the input shaft
assembly.
Fig. 43 Pressing Gears Out of Case
Fig. 44 Transaxle Case Removal
Fig. 45 Oil Feed Trough
Fig. 46 Reverse Brake Shim
Fig. 47 Reverse Brake Friction Cone
Fig. 48 Reverse Brake Blocking Ring
21 - 14 TRANSAXLEPL
DISASSEMBLY AND ASSEMBLY (Continued)
Page 958 of 1200
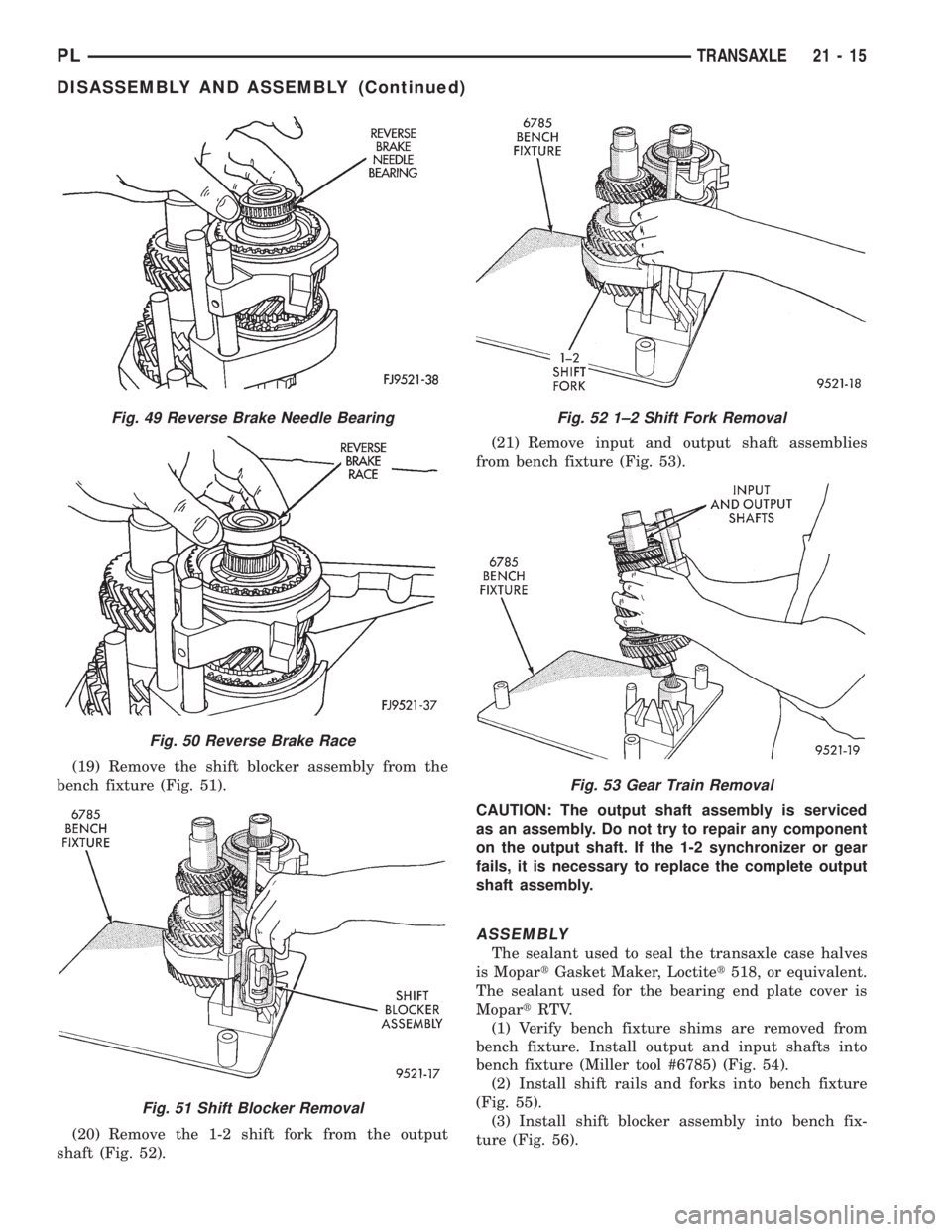
(19) Remove the shift blocker assembly from the
bench fixture (Fig. 51).
(20) Remove the 1-2 shift fork from the output
shaft (Fig. 52).(21) Remove input and output shaft assemblies
from bench fixture (Fig. 53).
CAUTION: The output shaft assembly is serviced
as an assembly. Do not try to repair any component
on the output shaft. If the 1-2 synchronizer or gear
fails, it is necessary to replace the complete output
shaft assembly.
ASSEMBLY
The sealant used to seal the transaxle case halves
is MopartGasket Maker, Loctitet518, or equivalent.
The sealant used for the bearing end plate cover is
MopartRTV.
(1) Verify bench fixture shims are removed from
bench fixture. Install output and input shafts into
bench fixture (Miller tool #6785) (Fig. 54).
(2) Install shift rails and forks into bench fixture
(Fig. 55).
(3) Install shift blocker assembly into bench fix-
ture (Fig. 56).
Fig. 49 Reverse Brake Needle Bearing
Fig. 50 Reverse Brake Race
Fig. 51 Shift Blocker Removal
Fig. 52 1±2 Shift Fork Removal
Fig. 53 Gear Train Removal
PLTRANSAXLE 21 - 15
DISASSEMBLY AND ASSEMBLY (Continued)
Page 959 of 1200
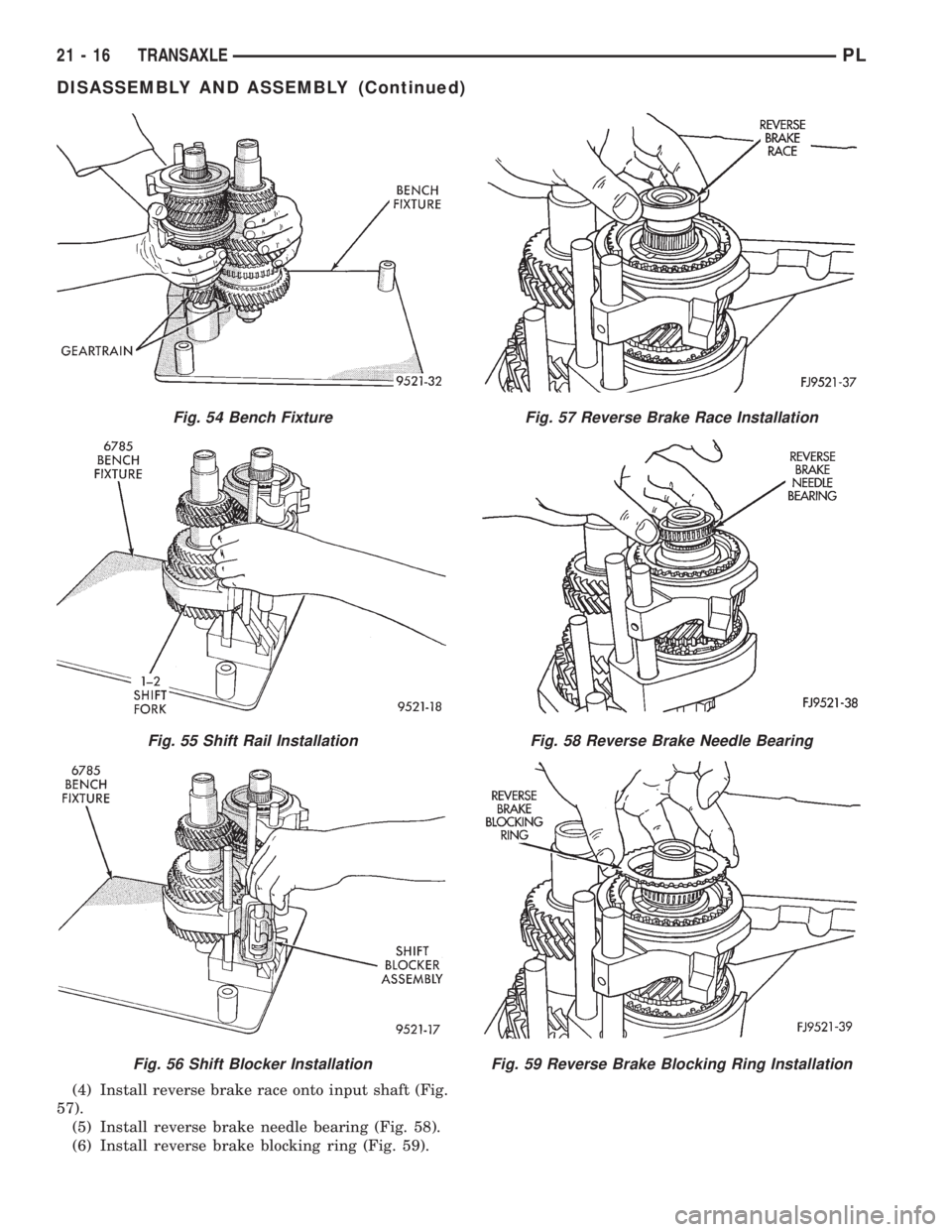
(4) Install reverse brake race onto input shaft (Fig.
57).
(5) Install reverse brake needle bearing (Fig. 58).
(6) Install reverse brake blocking ring (Fig. 59).
Fig. 54 Bench Fixture
Fig. 55 Shift Rail Installation
Fig. 56 Shift Blocker Installation
Fig. 57 Reverse Brake Race Installation
Fig. 58 Reverse Brake Needle Bearing
Fig. 59 Reverse Brake Blocking Ring Installation
21 - 16 TRANSAXLEPL
DISASSEMBLY AND ASSEMBLY (Continued)
Page 960 of 1200
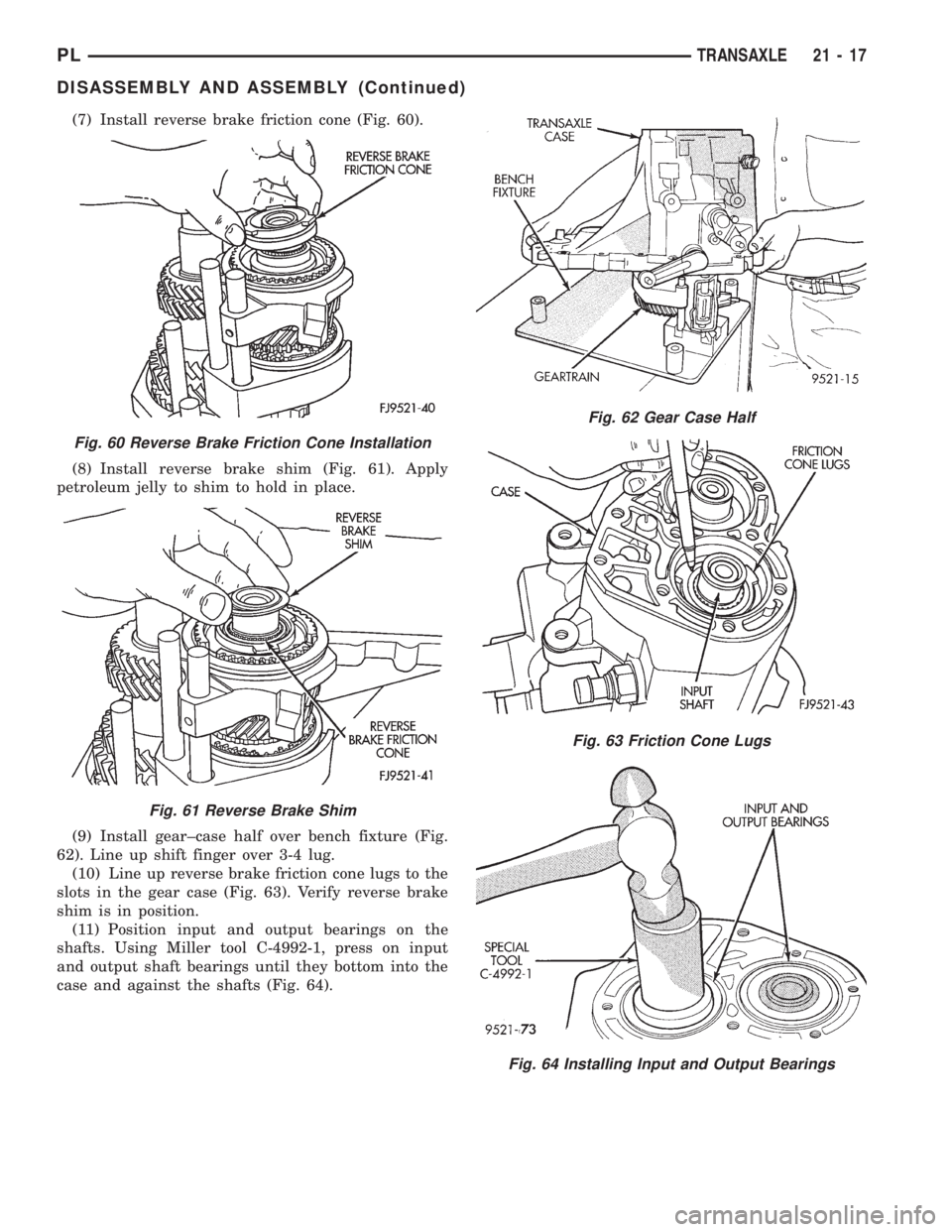
(7) Install reverse brake friction cone (Fig. 60).
(8) Install reverse brake shim (Fig. 61). Apply
petroleum jelly to shim to hold in place.
(9) Install gear±case half over bench fixture (Fig.
62). Line up shift finger over 3-4 lug.
(10) Line up reverse brake friction cone lugs to the
slots in the gear case (Fig. 63). Verify reverse brake
shim is in position.
(11) Position input and output bearings on the
shafts. Using Miller tool C-4992-1, press on input
and output shaft bearings until they bottom into the
case and against the shafts (Fig. 64).
Fig. 60 Reverse Brake Friction Cone Installation
Fig. 61 Reverse Brake Shim
Fig. 62 Gear Case Half
Fig. 63 Friction Cone Lugs
Fig. 64 Installing Input and Output Bearings
PLTRANSAXLE 21 - 17
DISASSEMBLY AND ASSEMBLY (Continued)