torque HONDA INTEGRA 1998 4.G Owner's Manual
[x] Cancel search | Manufacturer: HONDA, Model Year: 1998, Model line: INTEGRA, Model: HONDA INTEGRA 1998 4.GPages: 1681, PDF Size: 54.22 MB
Page 441 of 1681
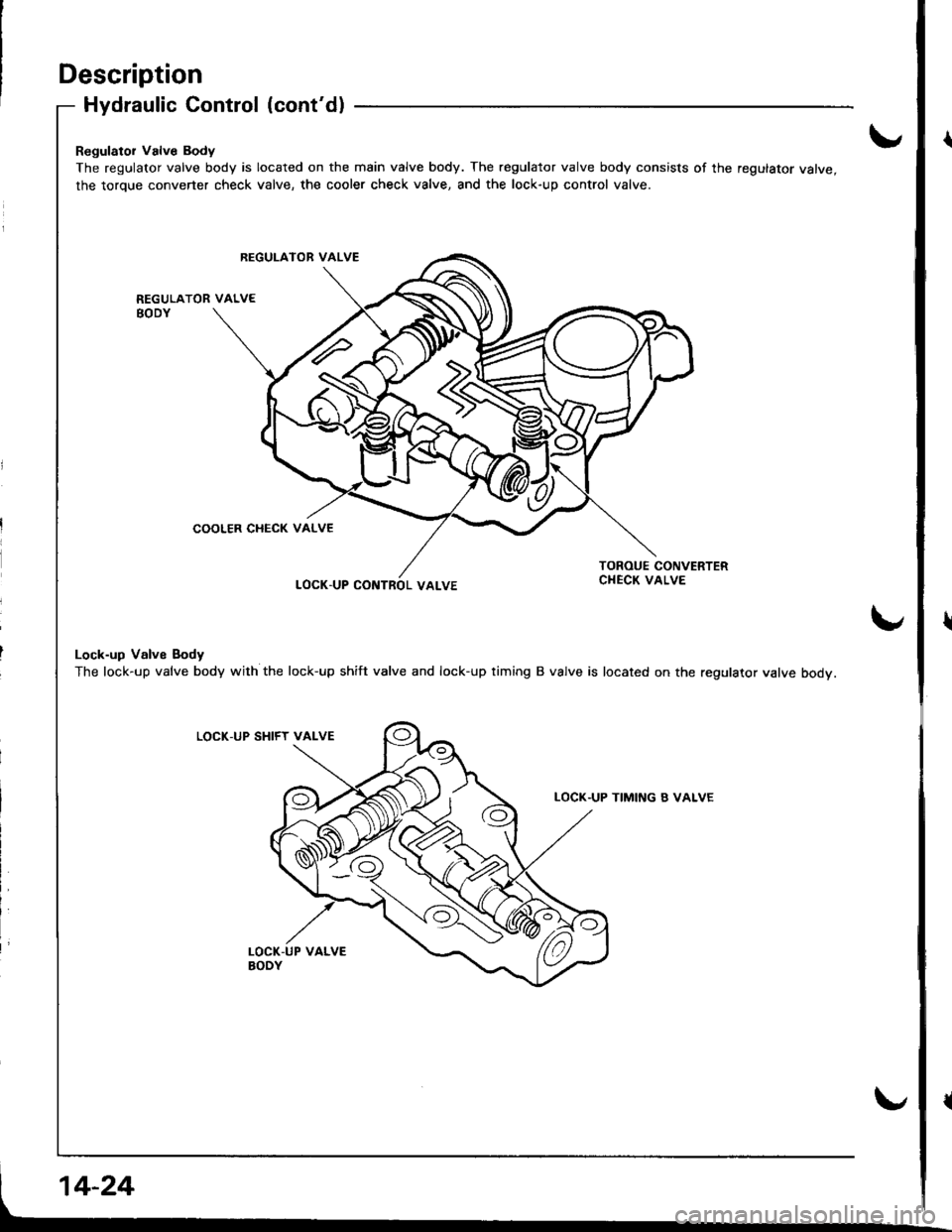
Description
Hydraulic Control (cont'd)
Regulator Valve Body
The regulator valve body is located on the main valve body. The regulator valve body consists of the regulator valve,
the torque converter check valve, the cooler check valve, and the lock-up control valve.
LOCK.UP CONTROL VALVE
Lock-up Valve Body
The lock-up valve body with the lock-up shift valve and lock-up timing B valve is located on the regulator valve body.
LOCK-UP SHIFY VALVE
TIMI[\'G B VALVE
REGUI-ATOR VALVE
COOLER CHECK VALVE
Page 442 of 1681
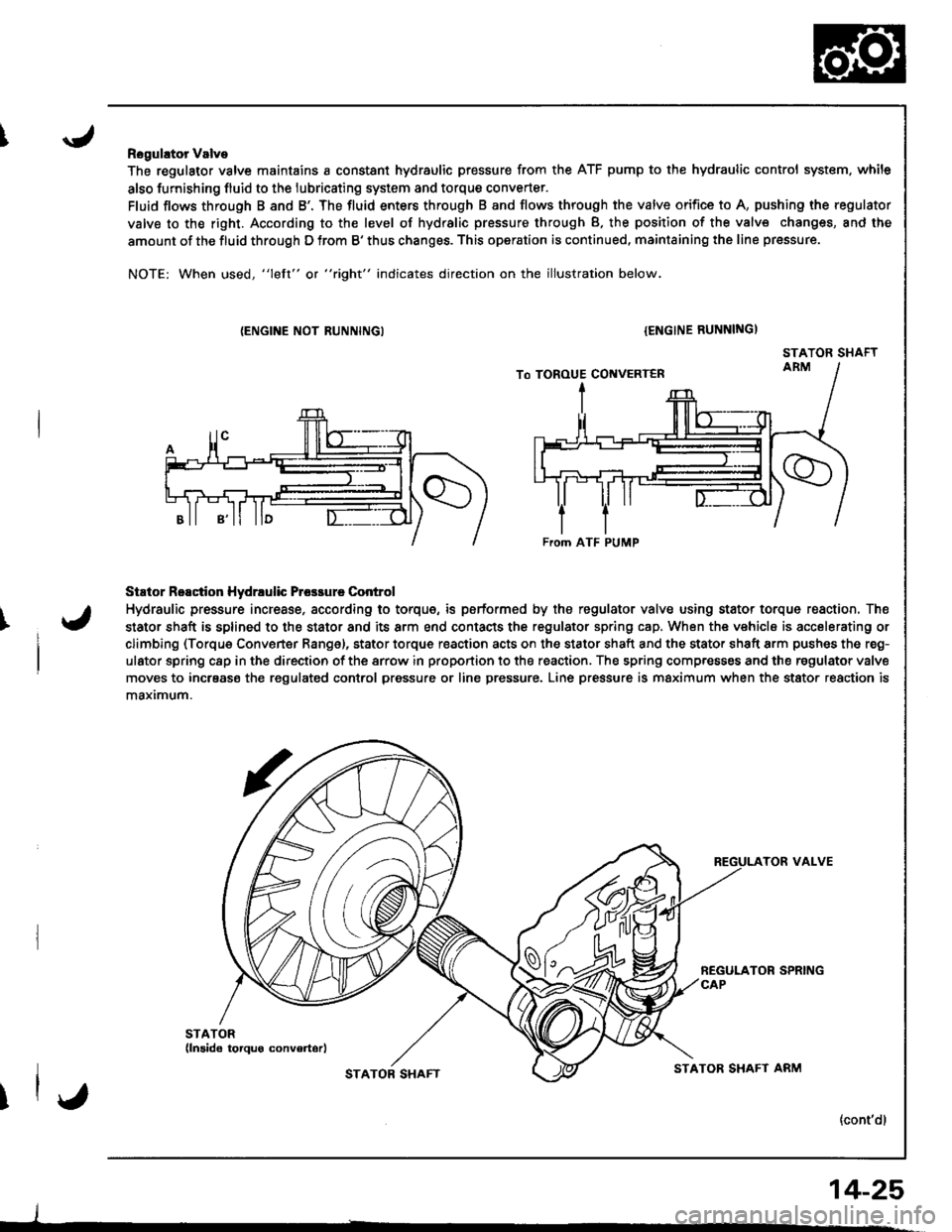
I
I
Rogulator Valve
The regulator valve maintains a constant hydraulic pressure from the ATF pump to the hydraulic control system. while
also furnishing fluid to the lubricating system and torque converter.
Fluid flows through B and B'. The fluid enters through B and flows through the valve orifice to A, pushing the regulator
valve to the right. According to the level of hydralic pressure through B. the position of the valv€ changes, and the
amount of the fluid through D from B' thus changes. This operation is continued, maintaining the line pressure.
NOTE: When used, "left" or "right" indicates direction on the illustration below.
{ENGINE NOT RUNNINGI{ENGINE RUNNINGI
STATOR SHAFT
Stator Reactior Hydrrulic Prcsrure Control
Hydraulic pressure incresse, according to torque, is performed by the regulator valve using stator torque reaction. The
stator shaft is splined to the stator and its arm end contacts the regulator spring cap. When the vehicle is accelerating or
climbing (Torque Converter Range), stator torque reaction acts on the stator shaft and the stator shaft arm pushes the reg-
ulator spring c8p in the direction of the srrow in proportion to the reaction. The spring compresses and the regulator valve
moves to incrsase the regulated conlrol pressure or line pressure. Line pressure is maximum when the stator reaction is
maximum.
TOR VALVE
{cont'dl
From ATF PUMP
I
STATOB SHAFTSTATOR SHAFT ARM
14-25
Page 445 of 1681
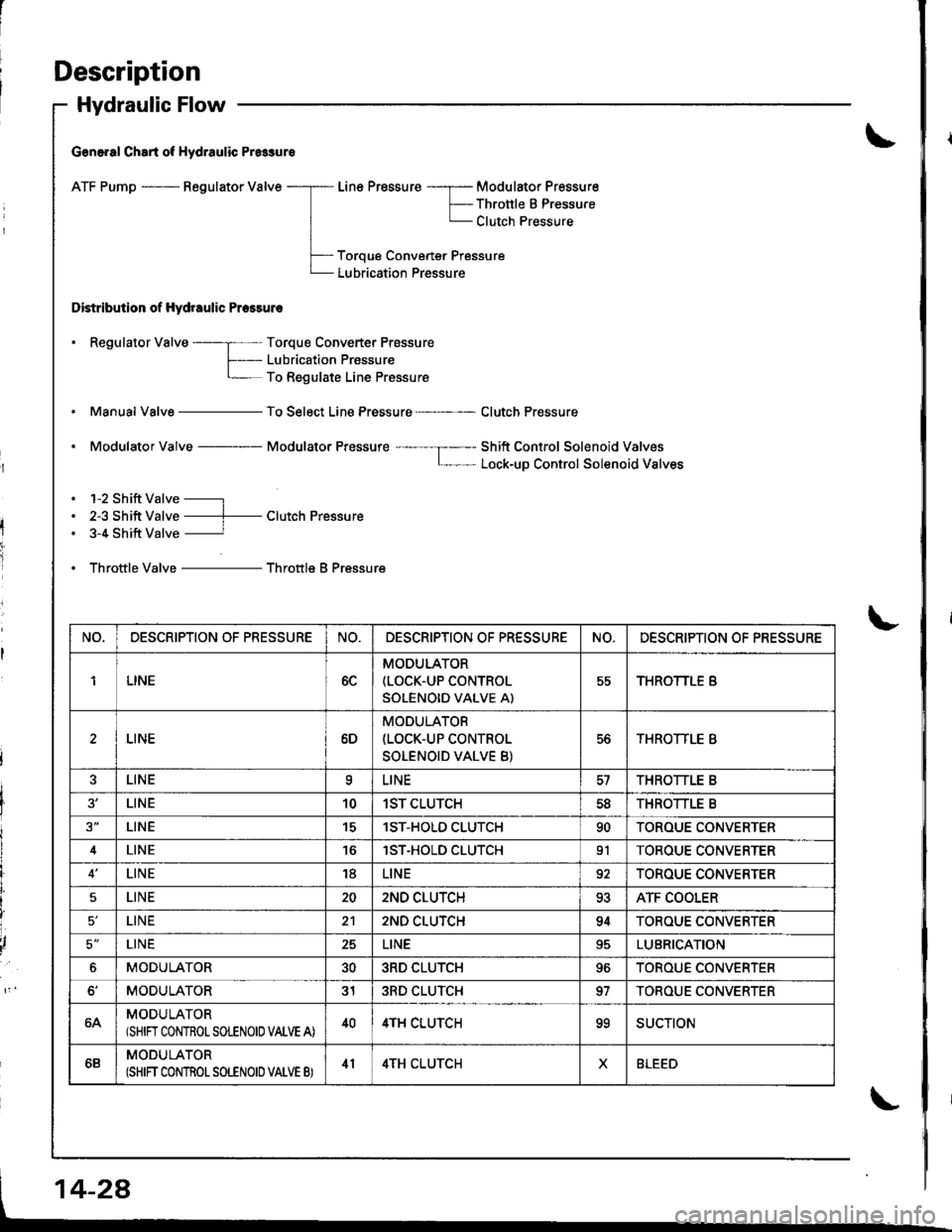
Description
Hydraulic Flow
G€n6.al Chart of Hydraulic Pr6sure
ATF Pump - Regulator Valve
Distribution of Hydraulic Pressuro
Line Pressure -----r- Modulator Pressure
F-- Thronle B PressureL Clutch Pressure
Toroue Convener Pressure
Lubrication Pressure
. Regulator Valve ----; Torque Converter Prossure
f- Lubricaiion PrassureL To Regulate Line Pressure
Manual Valve - To Select Line Pressure - Clutch Pressure
. Modulator Valve Modulator Pressure ---- --I----- Shift Control Solenoid ValvosL- Lock-uD Control Solenoid Valves
. 1-2 Shift Valve -----l
. 2-3 Shift Valve ----f- Clutch Pressure. 3-4 Shift Valve ----------r
. Throttle Valve - Throttle B Pressure
NO,DESCRIPTION OF PRESSURENO.DESCRIPTION OF PR€SSURENO.DESCRIPTION OF PRESSURE
1LINE6C
MODULATOR(LOCK.UP CONTROL
SOLENOID VALVE A)
55THROTTLE B
LINE6D
MODULATOR(LOCK-UP CONTROL
SOLENOID VALVE B)
56THROTTLE B
LINEaLINETHROTTLE B
LINE101ST CLUTCH5dTHROTTLE B
LINE151ST-HOLD CLUTCH90TOROUE CONVERTER
4LINElST.HOLD CLUTCH91TOROUE CONVERTER
LINE18LINE92TOROUE CONVERTER
5LINE202ND CLUTCH93ATF COOLER
LINE212ND CLUTCH94TOROUE CONVERTER
5'LINE25LINELUBRICATION
6MODULATOR303RD CLUTCH96TOROUE CONVERTER
MODULATOR313RD CLUTCH97TOBOUE CONVERTER
64MODULATOR(SHIN CONTROLSOLENOIO VALVE A)404TH CLUTCHooSUCTION
6BMODULATOR(SHIFT CONTROT SOLENOID VATVE B)414TH CLUTCHXBLEED
Page 446 of 1681
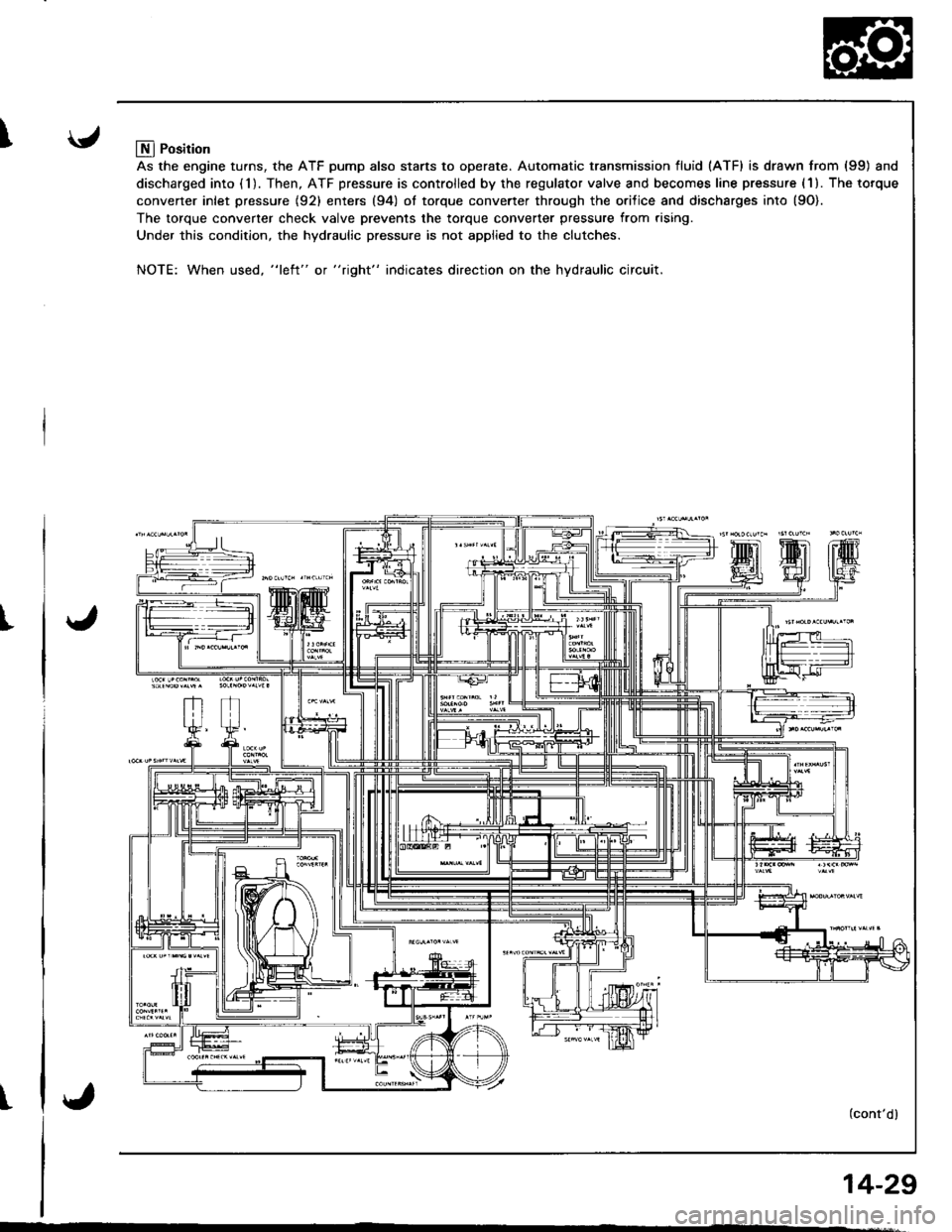
I
I
I
Llfl Position
As the engine turns, the ATF pump also starts to operate. Automatic transmission fluid (ATF) is drawn from (99) and
discharged into (1). Then, ATF pressure is controlled by the regulator valve and becomes line pressure (1). The torque
converter inlet pressure {92} enters (94) ol torque converter through the orilice and discharges into {9O).
The torque converter check valve prevents the torque converter pressure from rising.
Under this condition, the hydraulic pressure is not applied to the clutches.
NOTE: When used, "l€ft" or "right" indicates direction on the hydraulic circuit.
(cont'dl
14-29
Page 449 of 1681
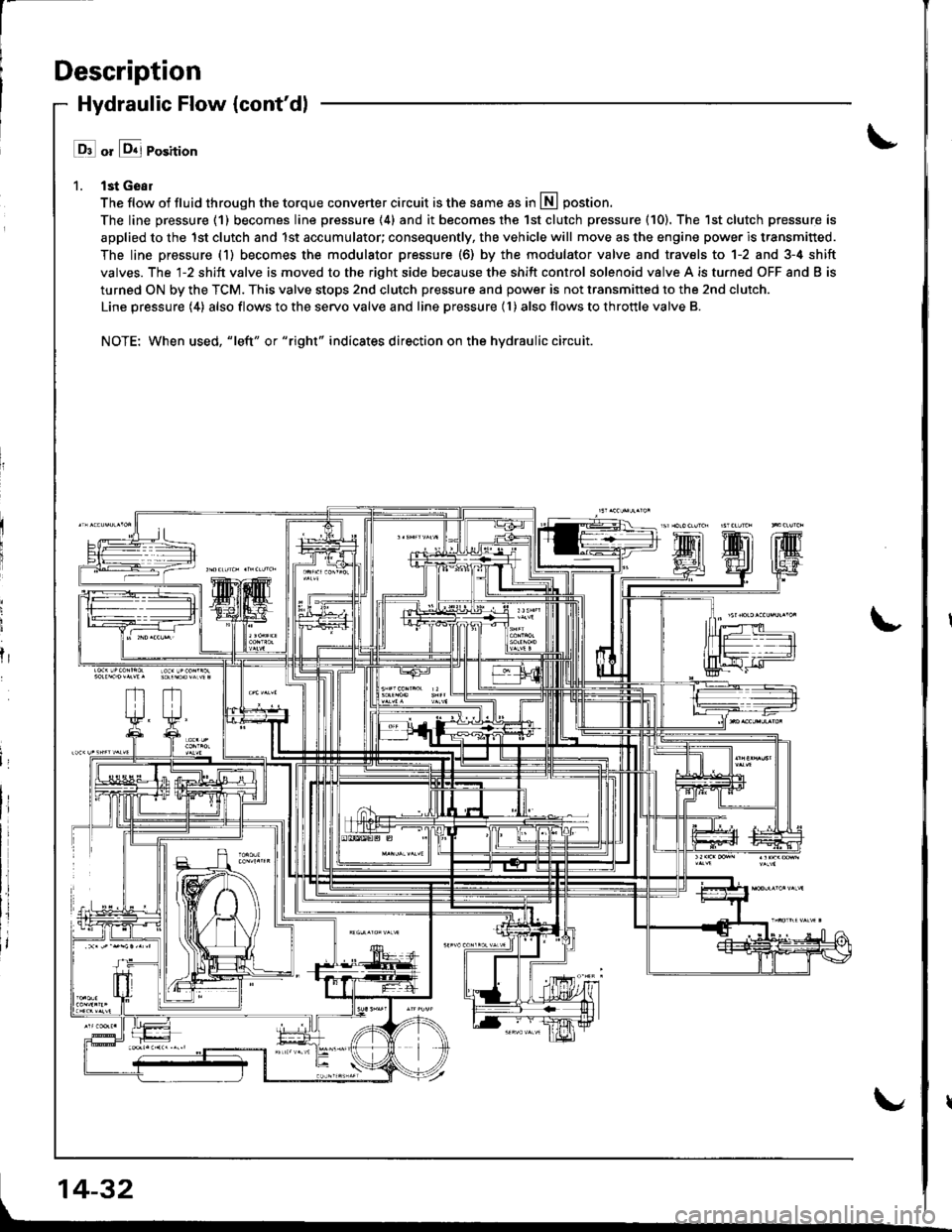
Description
Hydraulic Flow {cont'dl
l ll or &j Position
1. lst Geal
The flow of fluid through the torque converter circuit is the same as in lll postion.
The line pressure (1) becomes line pressure (4) and it becomes the 1st clutch pressure (10). The 1st clutch pressure is
applied to the 1st clutch and 1st accumulator; consequently, the vehicle will move as the engine power is transmitted.
The line pressure (1) becomes the modulator pressure (6) by the modulator valve and travels to 1-2 and 3-4 shift
valves. The l-2 shift valve is moved to the right side because the shift control solenoid valve A is turned OFF and B is
turned ON by the TCM. This valve stops 2nd clutch pressure and power is not transmitted to the 2nd clutch.
Line pressure (4) also flows to the servo valve and line pressure (l ) also flows to throttle valve B.
NOTE: When used, "|eft" or "right" indicates direction on the hydraulic circuit.
fr
14-32
Page 453 of 1681
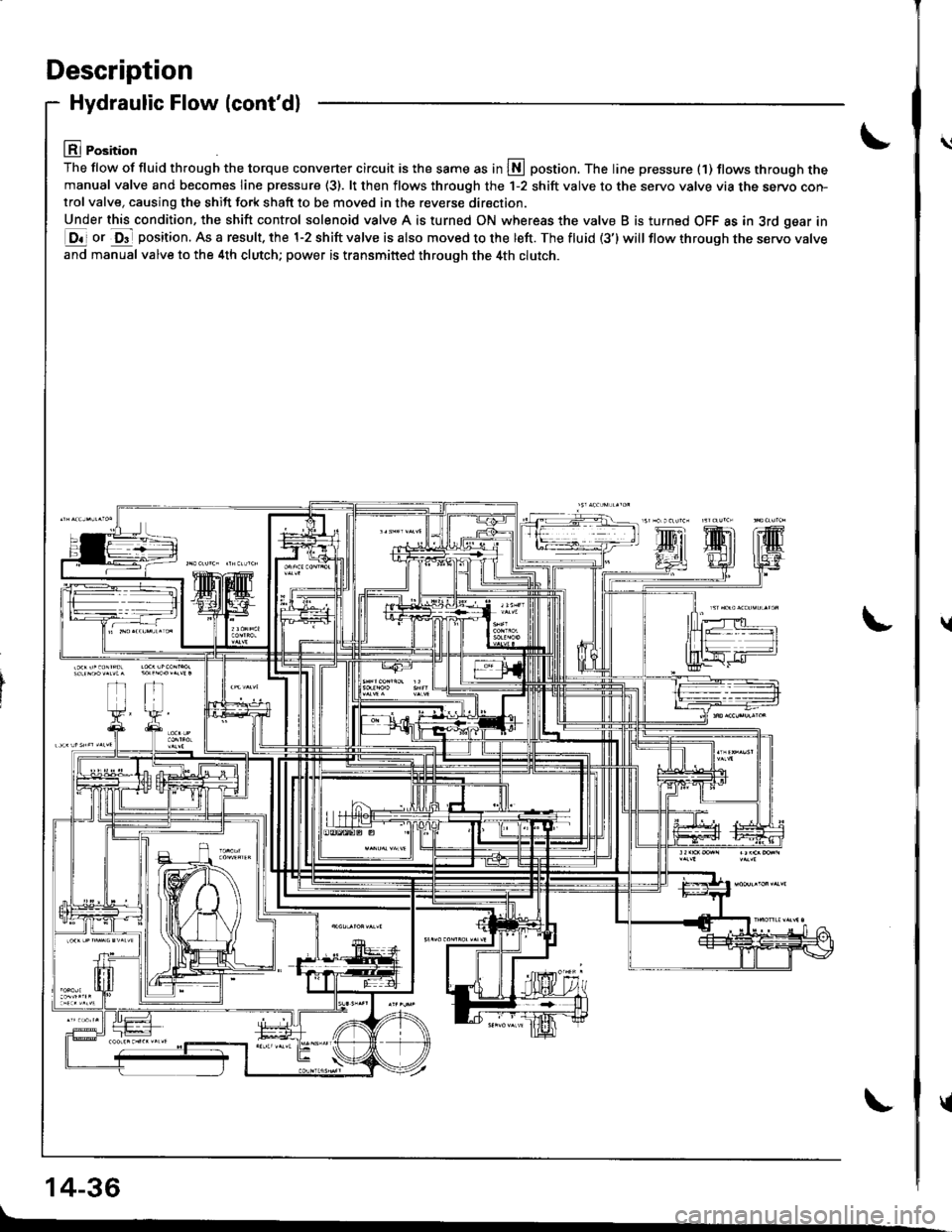
Description
Hydraulic Flow (cont'dl
lll Position
The flow of fluid th.ough the torque converter circuit is the same as in S postion. The line pressure (1) tlows through themanual valve and becomes line pressure (3). lt then flows through the 1-2 shift valve to the servo valve via the servo con-trol valve, causing the shift fork shaft to be moved in the reverse direction.
Under this condition, the shift control solenoid valve A is turned ON whereas the valve B is turned OFF as in 3rd gear in
E ot O"- position. As a result. the 1-2 shift valve is also moved to the left. The fluid (3') will flow through tne servo varve
and manual valve to the 4th clutch; power is transmitted through the 4th clutch.
14-36
\l
\
{
{
Page 454 of 1681
![HONDA INTEGRA 1998 4.G Owners Manual E Position
The flow of tluid through the torque converter circuit is the same as in L\l]position. The line pressure (1) becomes line
pressure (3) as it passes through the manual valve. Then line press HONDA INTEGRA 1998 4.G Owners Manual E Position
The flow of tluid through the torque converter circuit is the same as in L\l]position. The line pressure (1) becomes line
pressure (3) as it passes through the manual valve. Then line press](/img/13/6069/w960_6069-453.png)
E Position
The flow of tluid through the torque converter circuit is the same as in L\l]position. The line pressure (1) becomes line
pressure (3) as it passes through the manual valve. Then line pressure (3) flows through the 1-2 shift valve to the servo
valve via the servo control valve, causing the shift fork shaft to be moved to the reverse position as in @ position.
However, the hydraulic pressure is not supplied to the clutches. Power is not transmitted.
NOTE: When used, "left" or "right" indicates direction on the hydraulic circuit.
14-37
Page 455 of 1681
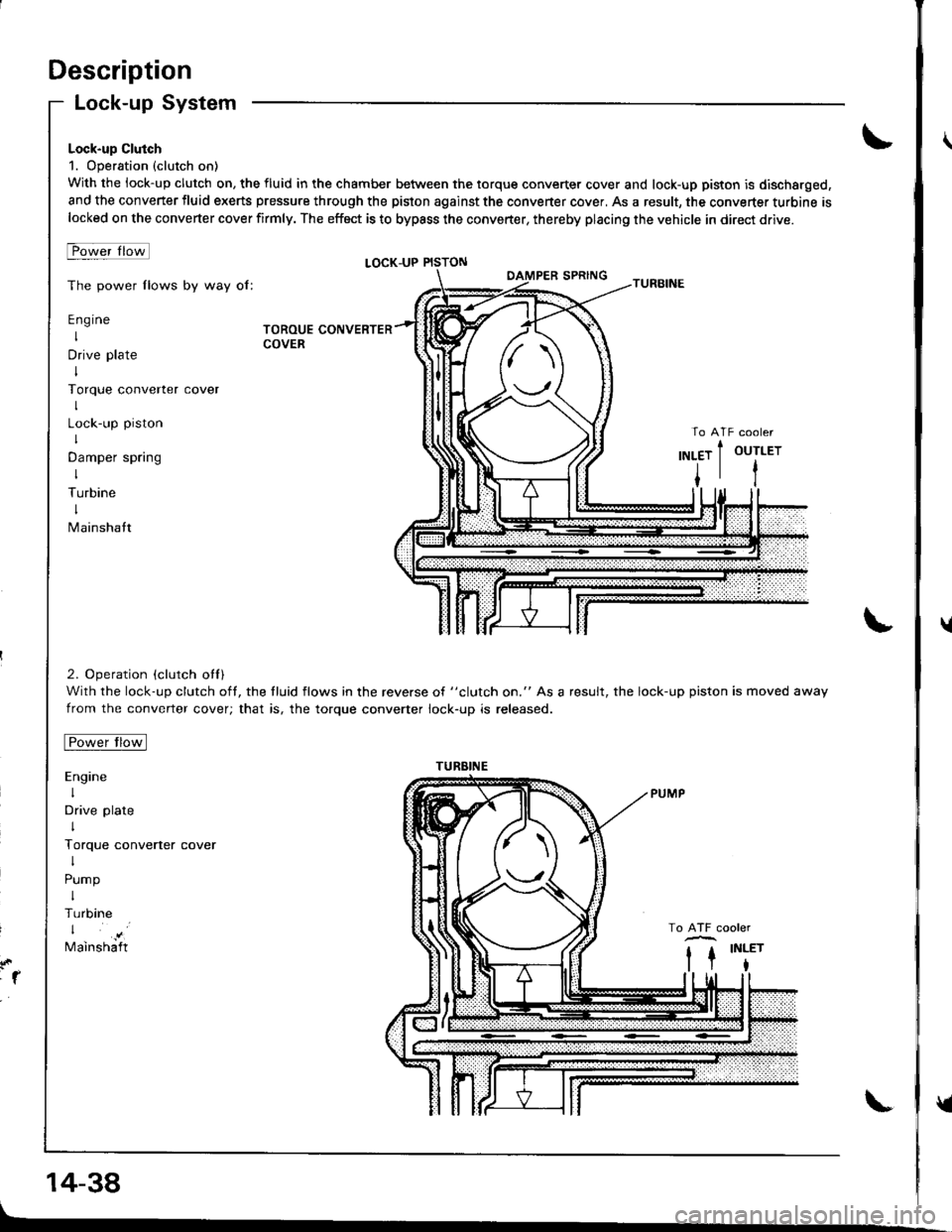
Description
Lock-up System
Lock-up Clutch
1. Operation (clutch on)
With the lock-up clutch on, the fluid in the chamber between the torque converter cover and lock-up piston is discharged,
and the converter fluid exerts pressure through the piston against the converter cover, As a result, the converter turbine islocked on the converter cover firmly. The effoct is to bypass the converter, thereby placing the vehicle in direct drive.
t-owerlrotl
The power flows by way of:
Engine
I
Drive plate
I
Torque converter
I
Lock-up piston
I
Damper spring
I
Turbine
I
Mainshatt
2. Operation (clutch otl)
With the lock-up clutch oft, the tluid flows in the reverse of "clutch on." As a result, the lock-up piston is moved away
from the converter cover; that is, the torque converter lock-up is released.
tro-wt rrotl
Engine
I
Drive plate
I
Torque converter cover
I
Pump
I
Turbine
Mainshaft
LOCK-UP PISTON
TOROUE CONVERTERCOVER
:1
14-38
TURBINE
tl
u
v
Page 456 of 1681
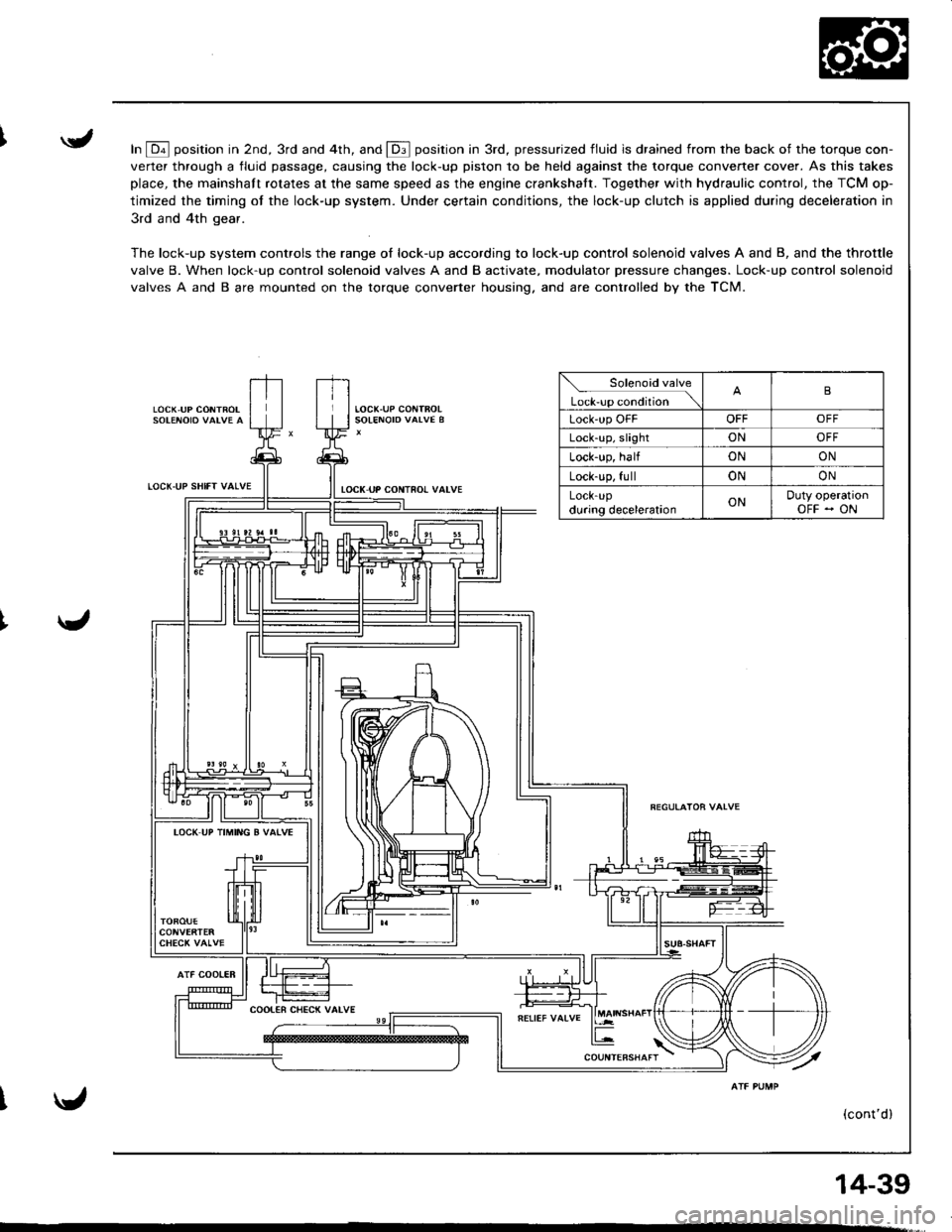
In E position in 2nd, 3rd and 4th, and E position in 3rd, pressurized fluid is drained from rhe back of the torque con-
verter through a fluid passage, causing the lock-up piston to be held against the torque converter cover. As this takes
place, the mainshaft rotates at the same speed as the engine crankshatt. Together with hydraulic control, the TCM op-
timized the timing of the lock-up system. Under certain conditions, the lock-up clutch is applied during deceleration in
3rd and 4th gear.
The lock-up system controls the range of lock-up according to lock-up control solenoid valves A and B, and the throttle
valve B. When lock-up control solenoid valves A and B activate, modulator pressure changes. Lock-up control solenoid
valves A and B are mounted on the torque converter housing. and are controlled by the TCM.
LOCK,UP CONTROL
LOCT.UP SHIfT VALVE
AlF COOIER
tocK uP coNTno! valvE
Solenoid valve
L*r""r "o.Jtio" \B
Lock'up OFFOFFOFF
Lock-up, slightONOFF
Lock-up, halfONON
Lock-up, fullONON
LOCK-Updu.ing decelerationONDuty operationOFF - ON
IOCK UP TIMING B VATVE
(cont'd)
14-39
Page 457 of 1681
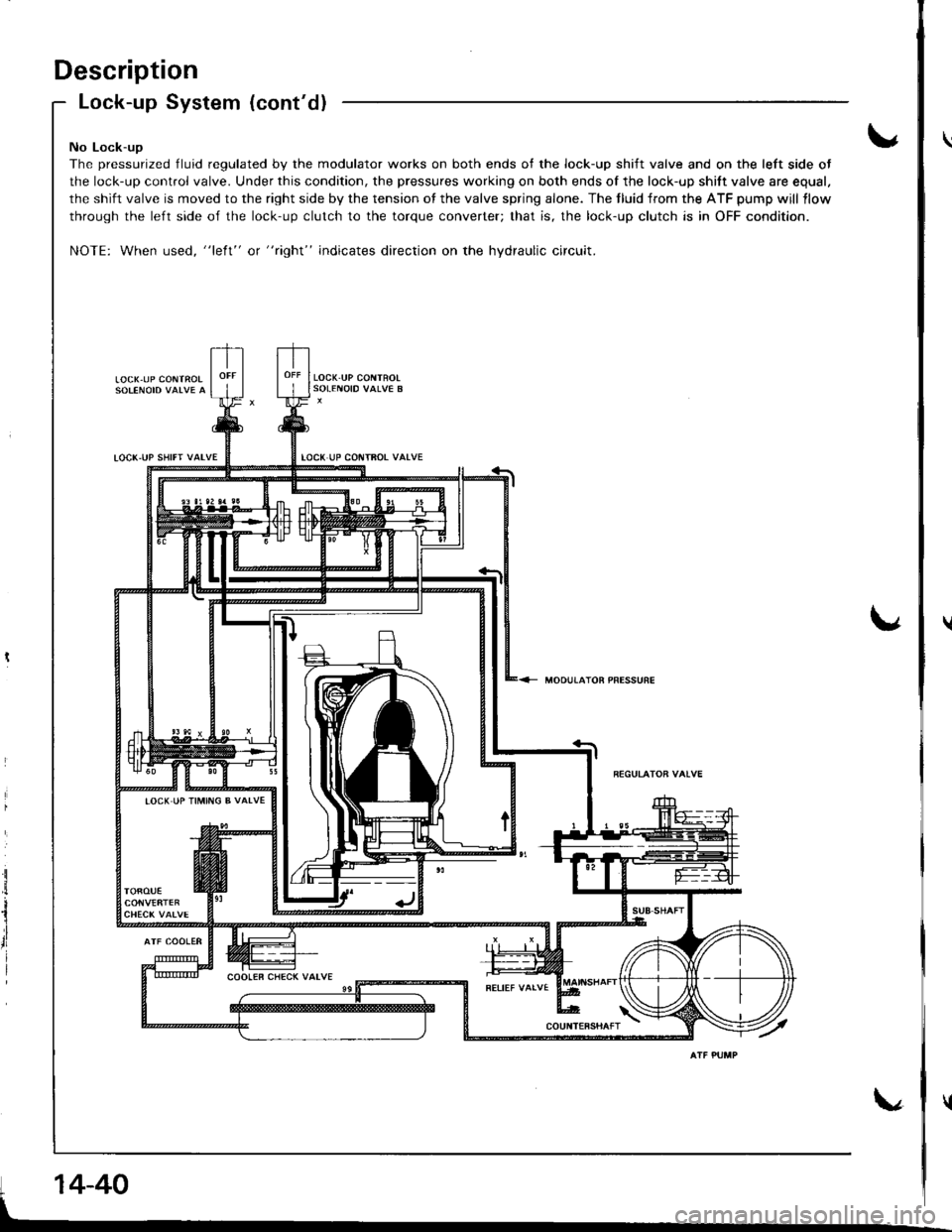
Description
LOC(,UP SlllFT VATVE
Lock-up System (cont'd)
No Lock-ug
The pressurized fluid regulated by the modulator works on both ends of the lock-up shift valve and on the left side ot
the lock-up control valve. Under this condition, the pressures working on both ends of the lock-up shift valve are equal.
the shift valve is moved to the right side by the tension of the valve spring alone. The tluid from the ATF pump will llow
through the left side of the lock-up clutch to the torque converter; that is, the lock-up clutch is in OFF condition.
NOTE: When used, "left" or "right" indicates direction on the hydraulic circuit.
LOCX.UP CONTROI
LOCK.UP COITTFOT VATVE
MOOUTATOR PRESSURE
i
il
rl
I
IOCK IJP TIMING B VALVE
14-40