check engine ISUZU KB P190 2007 Workshop Repair Manual
[x] Cancel search | Manufacturer: ISUZU, Model Year: 2007, Model line: KB P190, Model: ISUZU KB P190 2007Pages: 6020, PDF Size: 70.23 MB
Page 3544 of 6020
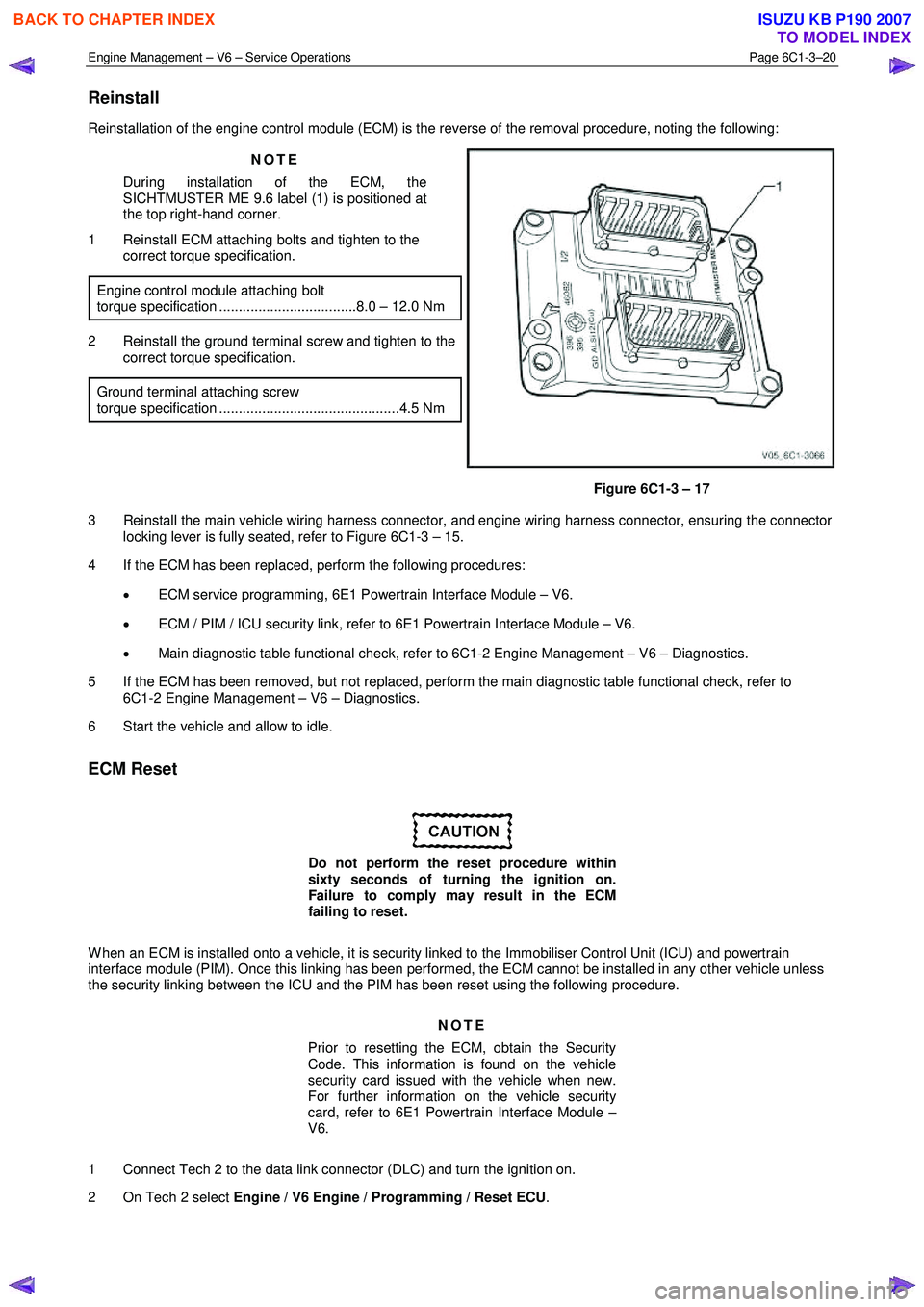
Engine Management – V6 – Service Operations Page 6C1-3–20
Reinstall
Reinstallation of the engine control module (ECM) is the reverse of the removal procedure, noting the following:
NOTE
During installation of the ECM, the
SICHTMUSTER ME 9.6 label (1) is positioned at
the top right-hand corner.
1 Reinstall ECM attaching bolts and tighten to the correct torque specification.
Engine control module attaching bolt
torque specification ...................................8.0 – 12.0 Nm
2 Reinstall the ground terminal screw and tighten to the correct torque specification.
Ground terminal attaching screw
torque specification ..............................................4.5 Nm
Figure 6C1-3 – 17
3 Reinstall the main vehicle wiring harness connector, and engine wiring harness connector, ensuring the connector locking lever is fully seated, refer to Figure 6C1-3 – 15.
4 If the ECM has been replaced, perform the following procedures:
• ECM service programming, 6E1 Powertrain Interface Module – V6.
• ECM / PIM / ICU security link, refer to 6E1 Powertrain Interface Module – V6.
• Main diagnostic table functional check, refer to 6C1-2 Engine Management – V6 – Diagnostics.
5 If the ECM has been removed, but not replaced, perform the main diagnostic table functional check, refer to 6C1-2 Engine Management – V6 – Diagnostics.
6 Start the vehicle and allow to idle.
ECM Reset
Do not perform the reset procedure within
sixty seconds of turning the ignition on.
Failure to comply may result in the ECM
failing to reset.
W hen an ECM is installed onto a vehicle, it is security linked to the Immobiliser Control Unit (ICU) and powertrain
interface module (PIM). Once this linking has been performed, the ECM cannot be installed in any other vehicle unless
the security linking between the ICU and the PIM has been reset using the following procedure.
NOTE
Prior to resetting the ECM, obtain the Security
Code. This information is found on the vehicle
security card issued with the vehicle when new.
For further information on the vehicle security
card, refer to 6E1 Powertrain Interface Module –
V6.
1 Connect Tech 2 to the data link connector (DLC) and turn the ignition on.
2 On Tech 2 select Engine / V6 Engine / Programming / Reset ECU .
BACK TO CHAPTER INDEX
TO MODEL INDEX
ISUZU KB P190 2007
Page 3545 of 6020
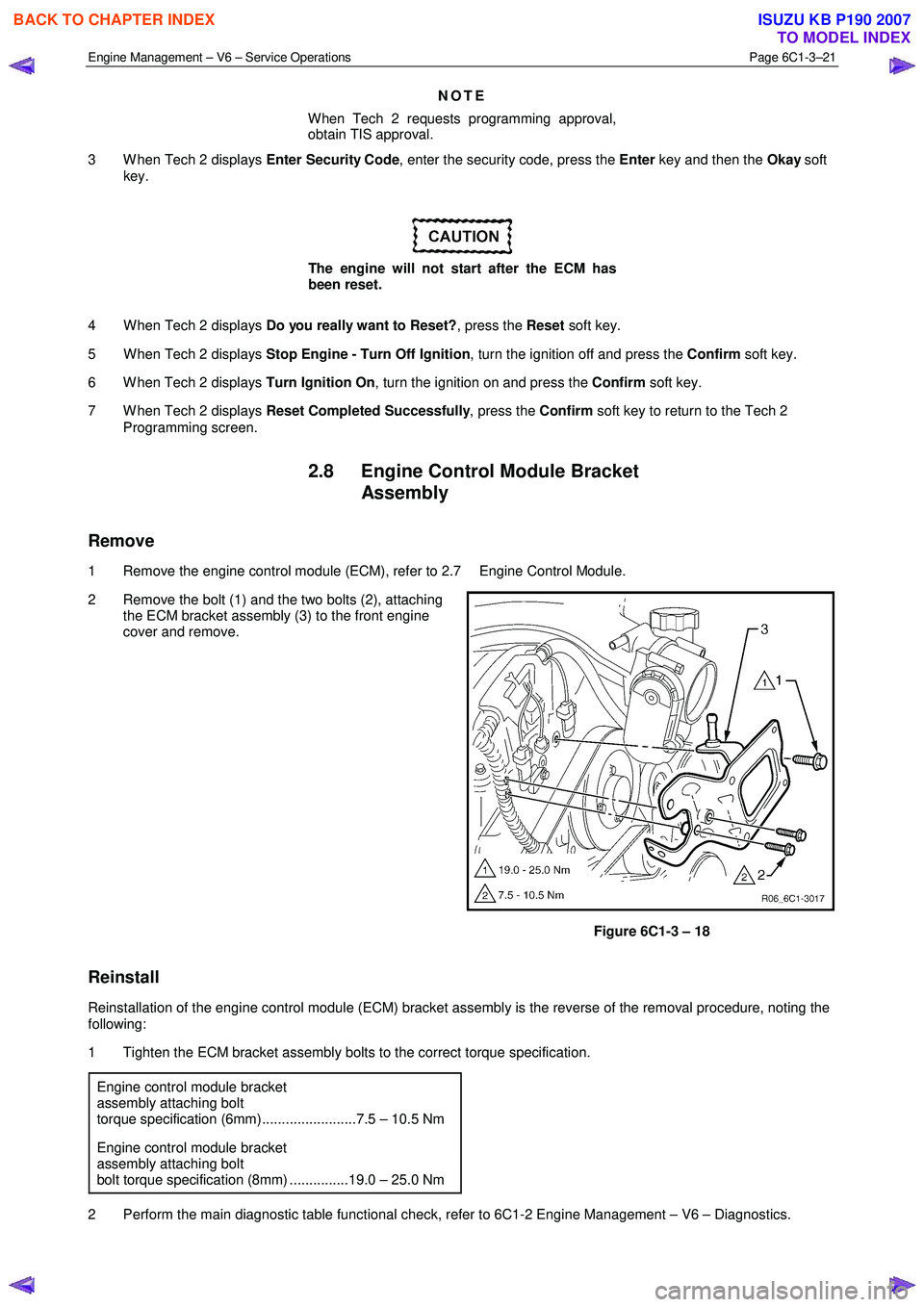
Engine Management – V6 – Service Operations Page 6C1-3–21
NOTE
When Tech 2 requests programming approval,
obtain TIS approval.
3 W hen Tech 2 displays Enter Security Code, enter the security code, press the Enter key and then the Okay soft
key.
The engine will not start after the ECM has
been reset.
4 W hen Tech 2 displays Do you really want to Reset? , press the Reset soft key.
5 W hen Tech 2 displays Stop Engine - Turn Off Ignition , turn the ignition off and press the Confirm soft key.
6 W hen Tech 2 displays Turn Ignition On, turn the ignition on and press the Confirm soft key.
7 W hen Tech 2 displays Reset Completed Successfully , press the Confirm soft key to return to the Tech 2
Programming screen.
2.8 Engine Control Module Bracket Assembly
Remove
1 Remove the engine control module (ECM), refer to 2.7 Engine Control Module.
2 Remove the bolt (1) and the two bolts (2), attaching the ECM bracket assembly (3) to the front engine
cover and remove.
Figure 6C1-3 – 18
Reinstall
Reinstallation of the engine control module (ECM) bracket assembly is the reverse of the removal procedure, noting the
following:
1 Tighten the ECM bracket assembly bolts to the correct torque specification.
Engine control module bracket
assembly attaching bolt
torque specification (6mm)........................7.5 – 10.5 Nm
Engine control module bracket
assembly attaching bolt
bolt torque specification (8mm) ...............19.0 – 25.0 Nm
2 Perform the main diagnostic table functional check, refer to 6C1-2 Engine Management – V6 – Diagnostics.
BACK TO CHAPTER INDEX
TO MODEL INDEX
ISUZU KB P190 2007
Page 3546 of 6020
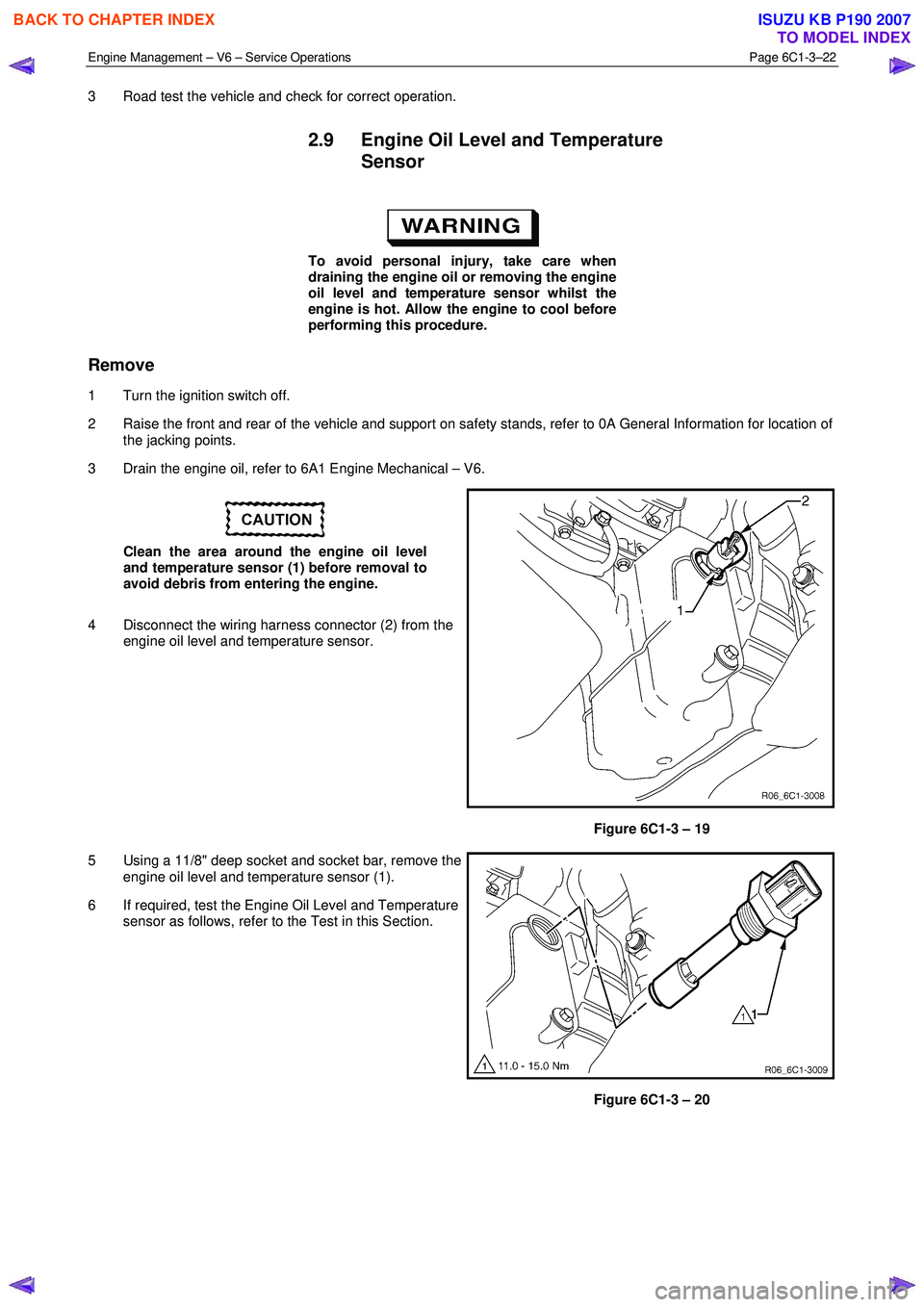
Engine Management – V6 – Service Operations Page 6C1-3–22
3 Road test the vehicle and check for correct operation.
2.9 Engine Oil Level and Temperature
Sensor
To avoid personal injury, take care when
draining the engine oil or removing the engine
oil level and temperature sensor whilst the
engine is hot. Allow the engine to cool before
performing this procedure.
Remove
1 Turn the ignition switch off.
2 Raise the front and rear of the vehicle and support on safety stands, refer to 0A General Information for location of the jacking points.
3 Drain the engine oil, refer to 6A1 Engine Mechanical – V6.
Clean the area around the engine oil level
and temperature sensor (1) before removal to
avoid debris from entering the engine.
4 Disconnect the wiring harness connector (2) from the engine oil level and temperature sensor.
Figure 6C1-3 – 19
5 Using a 11/8" deep socket and socket bar, remove the engine oil level and temperature sensor (1).
6 If required, test the Engine Oil Level and Temperature sensor as follows, refer to the Test in this Section.
Figure 6C1-3 – 20
BACK TO CHAPTER INDEX
TO MODEL INDEX
ISUZU KB P190 2007
Page 3547 of 6020
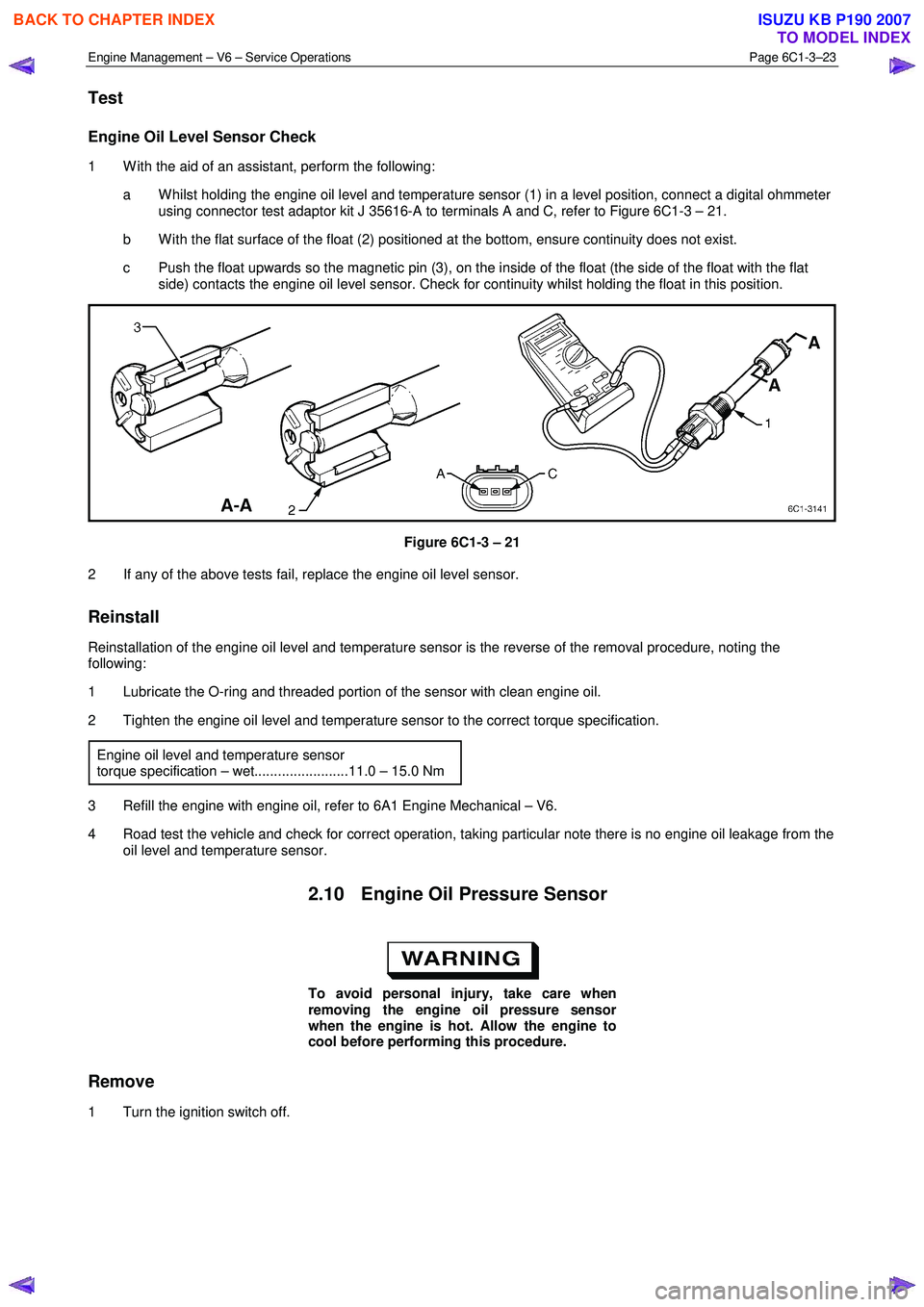
Engine Management – V6 – Service Operations Page 6C1-3–23
Test
Engine Oil Level Sensor Check
1 W ith the aid of an assistant, perform the following:
a W hilst holding the engine oil level and temperature sensor (1) in a level position, connect a digital ohmmeter using connector test adaptor kit J 35616-A to terminals A and C, refer to Figure 6C1-3 – 21.
b W ith the flat surface of the float (2) positioned at the bottom, ensure continuity does not exist.
c Push the float upwards so the magnetic pin (3), on the inside of the float (the side of the float with the flat side) contacts the engine oil level sensor. Check for continuity whilst holding the float in this position.
Figure 6C1-3 – 21
2 If any of the above tests fail, replace the engine oil level sensor.
Reinstall
Reinstallation of the engine oil level and temperature sensor is the reverse of the removal procedure, noting the
following:
1 Lubricate the O-ring and threaded portion of the sensor with clean engine oil.
2 Tighten the engine oil level and temperature sensor to the correct torque specification.
Engine oil level and temperature sensor
torque specification – wet........................11.0 – 15.0 Nm
3 Refill the engine with engine oil, refer to 6A1 Engine Mechanical – V6.
4 Road test the vehicle and check for correct operation, taking particular note there is no engine oil leakage from the oil level and temperature sensor.
2.10 Engine Oil Pressure Sensor
To avoid personal injury, take care when
removing the engine oil pressure sensor
when the engine is hot. Allow the engine to
cool before performing this procedure.
Remove
1 Turn the ignition switch off.
BACK TO CHAPTER INDEX
TO MODEL INDEX
ISUZU KB P190 2007
Page 3548 of 6020
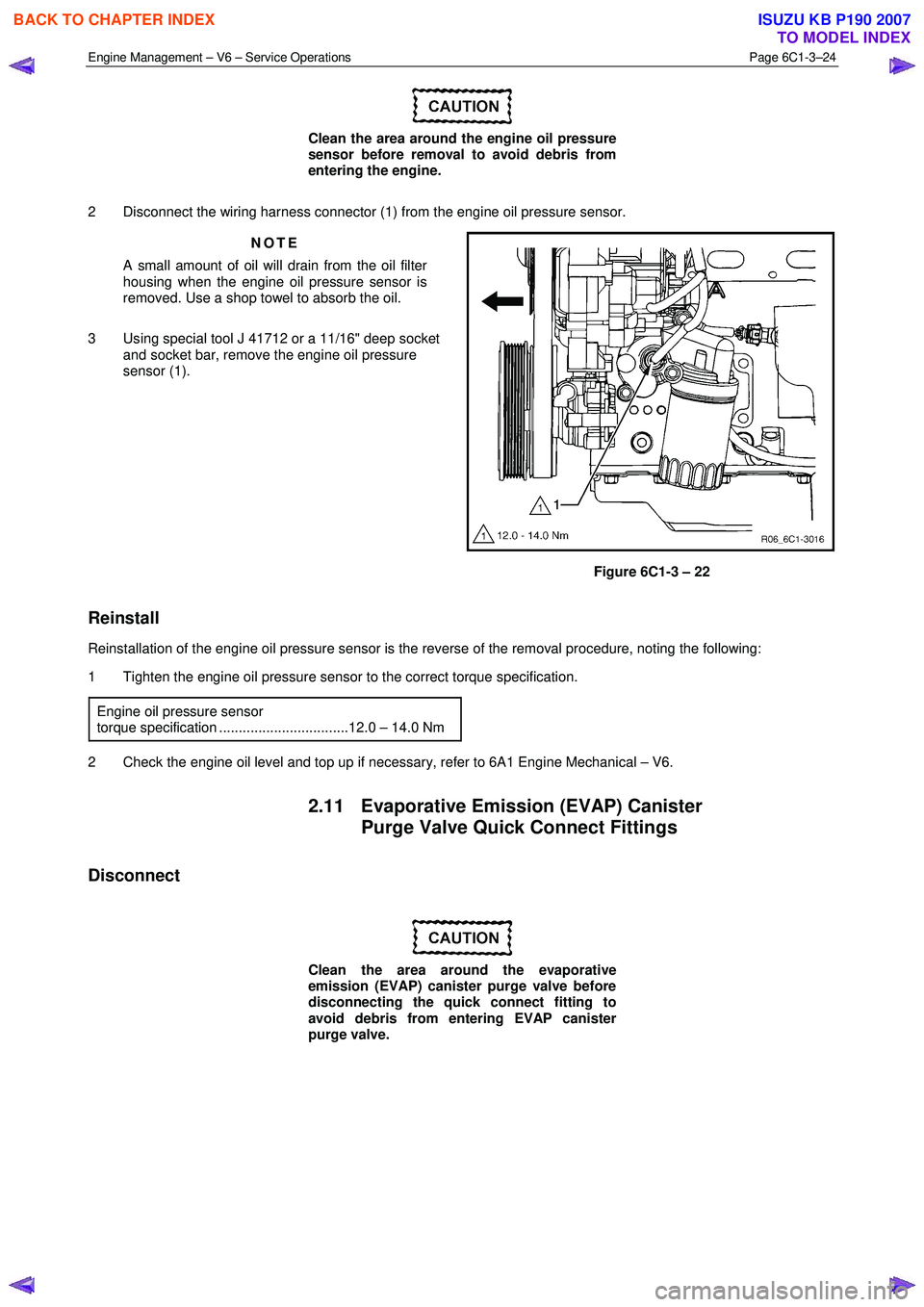
Engine Management – V6 – Service Operations Page 6C1-3–24
Clean the area around the engine oil pressure
sensor before removal to avoid debris from
entering the engine.
2 Disconnect the wiring harness connector (1) from the engine oil pressure sensor. NOTE
A small amount of oil will drain from the oil filter
housing when the engine oil pressure sensor is
removed. Use a shop towel to absorb the oil.
3 Using special tool J 41712 or a 11/16" deep socket and socket bar, remove the engine oil pressure
sensor (1).
Figure 6C1-3 – 22
Reinstall
Reinstallation of the engine oil pressure sensor is the reverse of the removal procedure, noting the following:
1 Tighten the engine oil pressure sensor to the correct torque specification.
Engine oil pressure sensor
torque specification .................................12.0 – 14.0 Nm
2 Check the engine oil level and top up if necessary, refer to 6A1 Engine Mechanical – V6.
2.11 Evaporative Emission (EVAP) Canister Purge Valve Quick Connect Fittings
Disconnect
Clean the area around the evaporative
emission (EVAP) canister purge valve before
disconnecting the quick connect fitting to
avoid debris from entering EVAP canister
purge valve.
BACK TO CHAPTER INDEX
TO MODEL INDEX
ISUZU KB P190 2007
Page 3550 of 6020
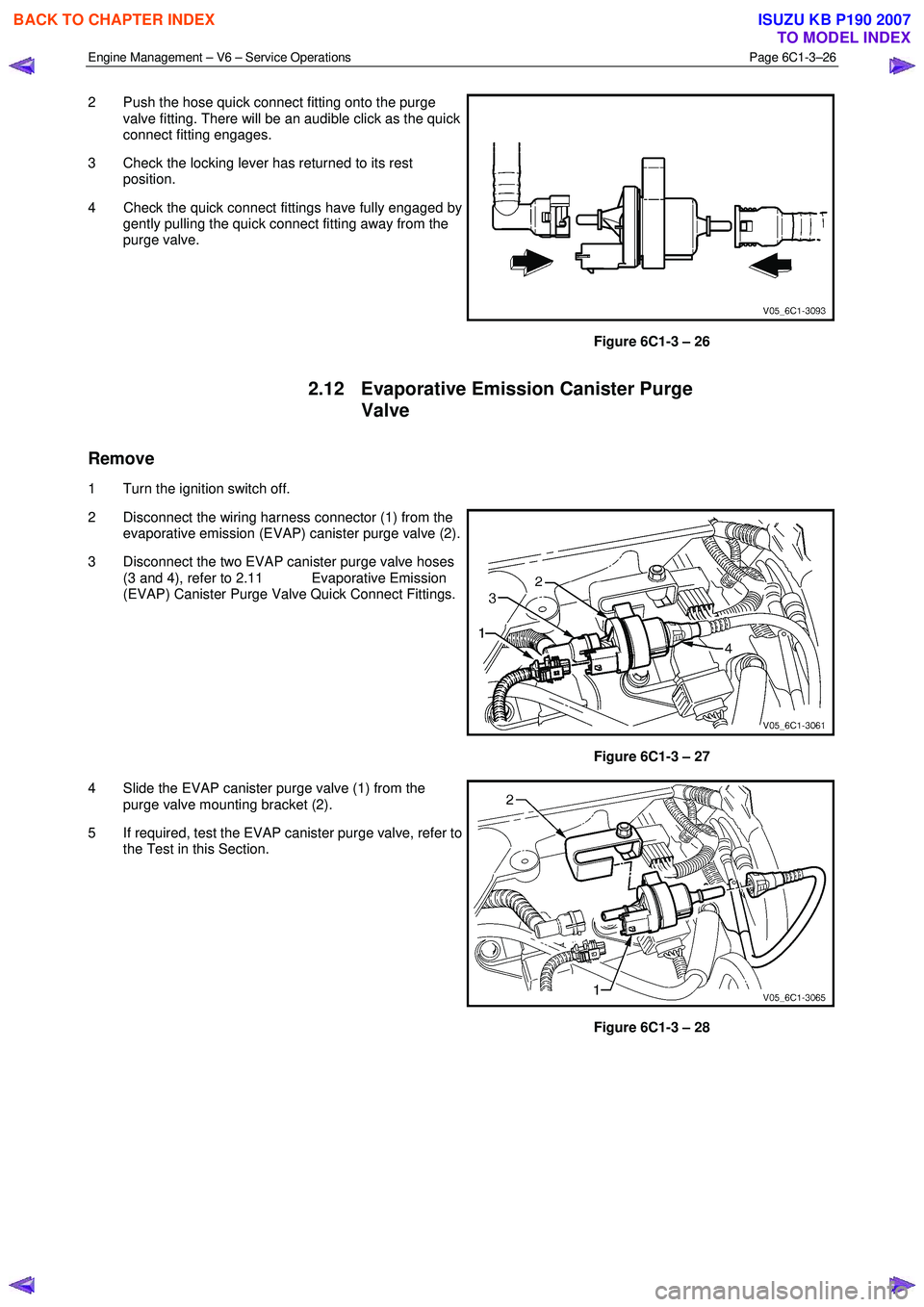
Engine Management – V6 – Service Operations Page 6C1-3–26
2 Push the hose quick connect fitting onto the purge
valve fitting. There will be an audible click as the quick
connect fitting engages.
3 Check the locking lever has returned to its rest position.
4 Check the quick connect fittings have fully engaged by gently pulling the quick connect fitting away from the
purge valve.
Figure 6C1-3 – 26
2.12 Evaporative Emission Canister Purge
Valve
Remove
1 Turn the ignition switch off.
2 Disconnect the wiring harness connector (1) from the evaporative emission (EVAP) canister purge valve (2).
3 Disconnect the two EVAP canister purge valve hoses (3 and 4), refer to 2.11 Evaporative Emission
(EVAP) Canister Purge Valve Quick Connect Fittings.
Figure 6C1-3 – 27
4 Slide the EVAP canister purge valve (1) from the purge valve mounting bracket (2).
5 If required, test the EVAP canister purge valve, refer to the Test in this Section.
Figure 6C1-3 – 28
BACK TO CHAPTER INDEX
TO MODEL INDEX
ISUZU KB P190 2007
Page 3551 of 6020
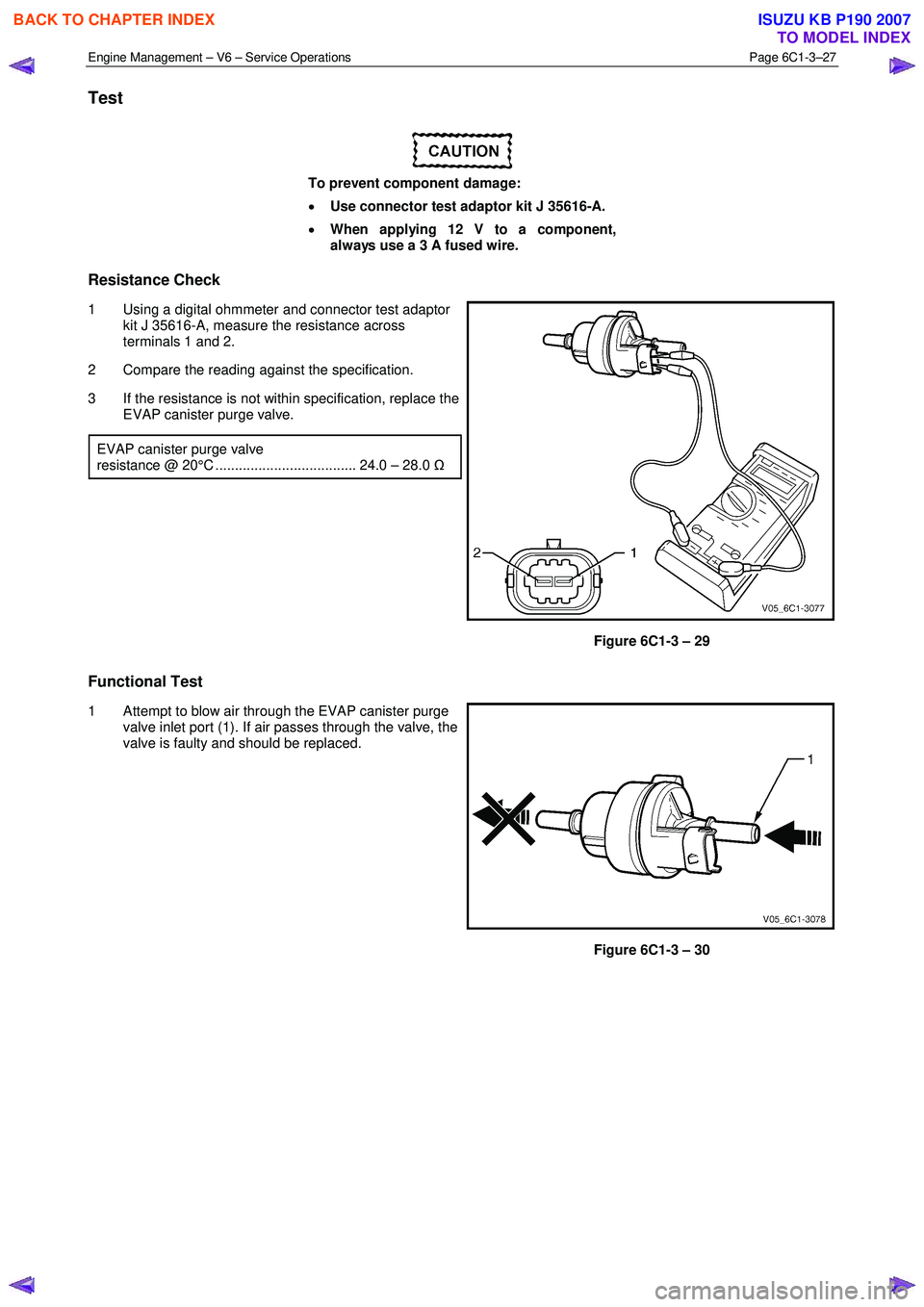
Engine Management – V6 – Service Operations Page 6C1-3–27
Test
To prevent component damage:
• Use connector test adaptor kit J 35616-A.
• When applying 12 V to a component,
always use a 3 A fused wire.
Resistance Check
1 Using a digital ohmmeter and connector test adaptor
kit J 35616-A, measure the resistance across
terminals 1 and 2.
2 Compare the reading against the specification.
3 If the resistance is not within specification, replace the EVAP canister purge valve.
EVAP canister purge valve
resistance @ 20°C .................................... 24.0 – 28.0 Ω
Figure 6C1-3 – 29
Functional Test
1 Attempt to blow air through the EVAP canister purge
valve inlet port (1). If air passes through the valve, the
valve is faulty and should be replaced.
Figure 6C1-3 – 30
BACK TO CHAPTER INDEX
TO MODEL INDEX
ISUZU KB P190 2007
Page 3552 of 6020
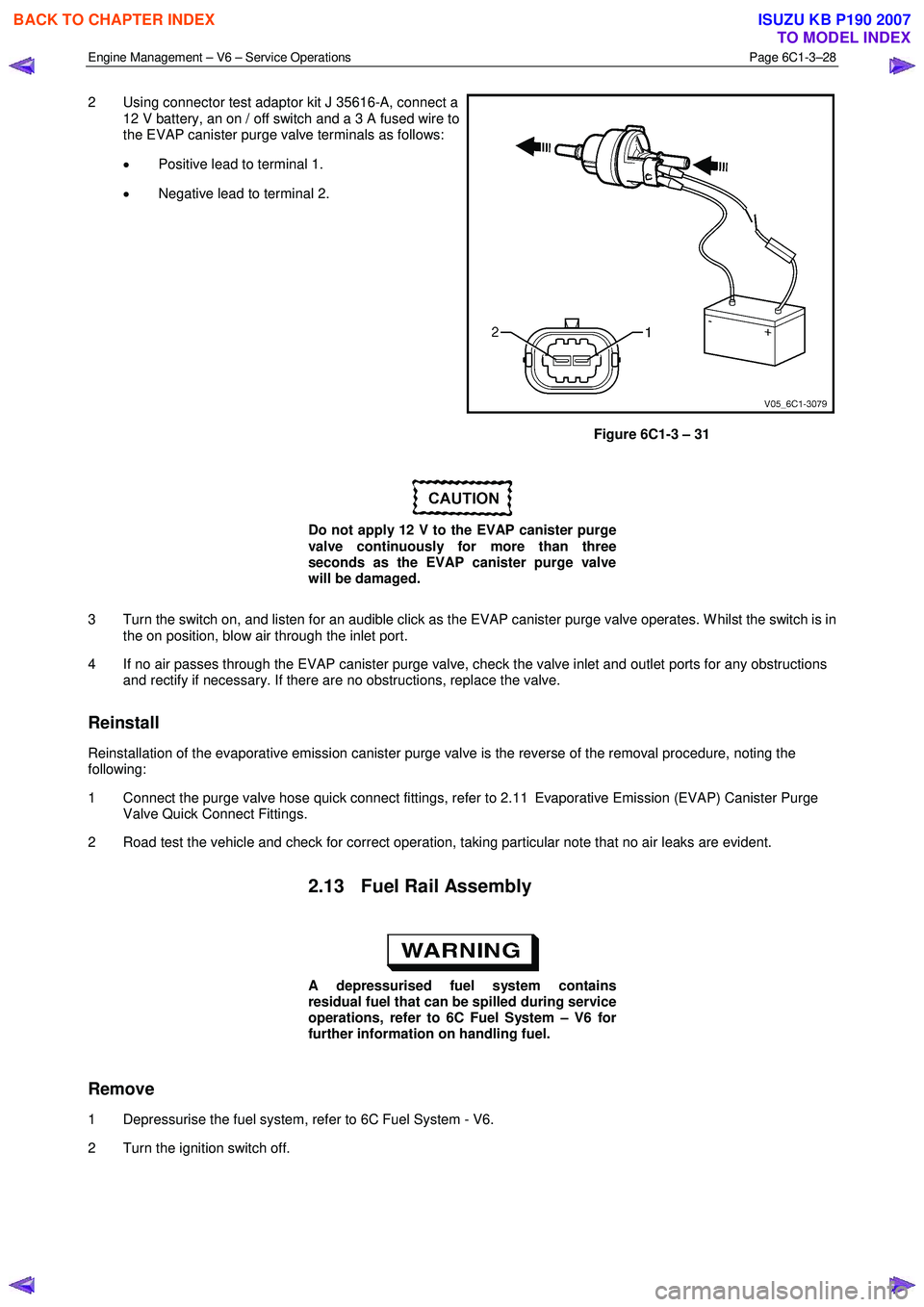
Engine Management – V6 – Service Operations Page 6C1-3–28
2 Using connector test adaptor kit J 35616-A, connect a
12 V battery, an on / off switch and a 3 A fused wire to
the EVAP canister purge valve terminals as follows:
• Positive lead to terminal 1.
• Negative lead to terminal 2.
Figure 6C1-3 – 31
Do not apply 12 V to the EVAP canister purge
valve continuously for more than three
seconds as the EVAP canister purge valve
will be damaged.
3 Turn the switch on, and listen for an audible click as the EVAP canister purge valve operates. W hilst the switch is in the on position, blow air through the inlet port.
4 If no air passes through the EVAP canister purge valve, check the valve inlet and outlet ports for any obstructions and rectify if necessary. If there are no obstructions, replace the valve.
Reinstall
Reinstallation of the evaporative emission canister purge valve is the reverse of the removal procedure, noting the
following:
1 Connect the purge valve hose quick connect fittings, refer to 2.11 Evaporative Emission (EVAP) Canister Purge Valve Quick Connect Fittings.
2 Road test the vehicle and check for correct operation, taking particular note that no air leaks are evident.
2.13 Fuel Rail Assembly
A depressurised fuel system contains
residual fuel that can be spilled during service
operations, refer to 6C Fuel System – V6 for
further information on handling fuel.
Remove
1 Depressurise the fuel system, refer to 6C Fuel System - V6.
2 Turn the ignition switch off.
BACK TO CHAPTER INDEX
TO MODEL INDEX
ISUZU KB P190 2007
Page 3557 of 6020
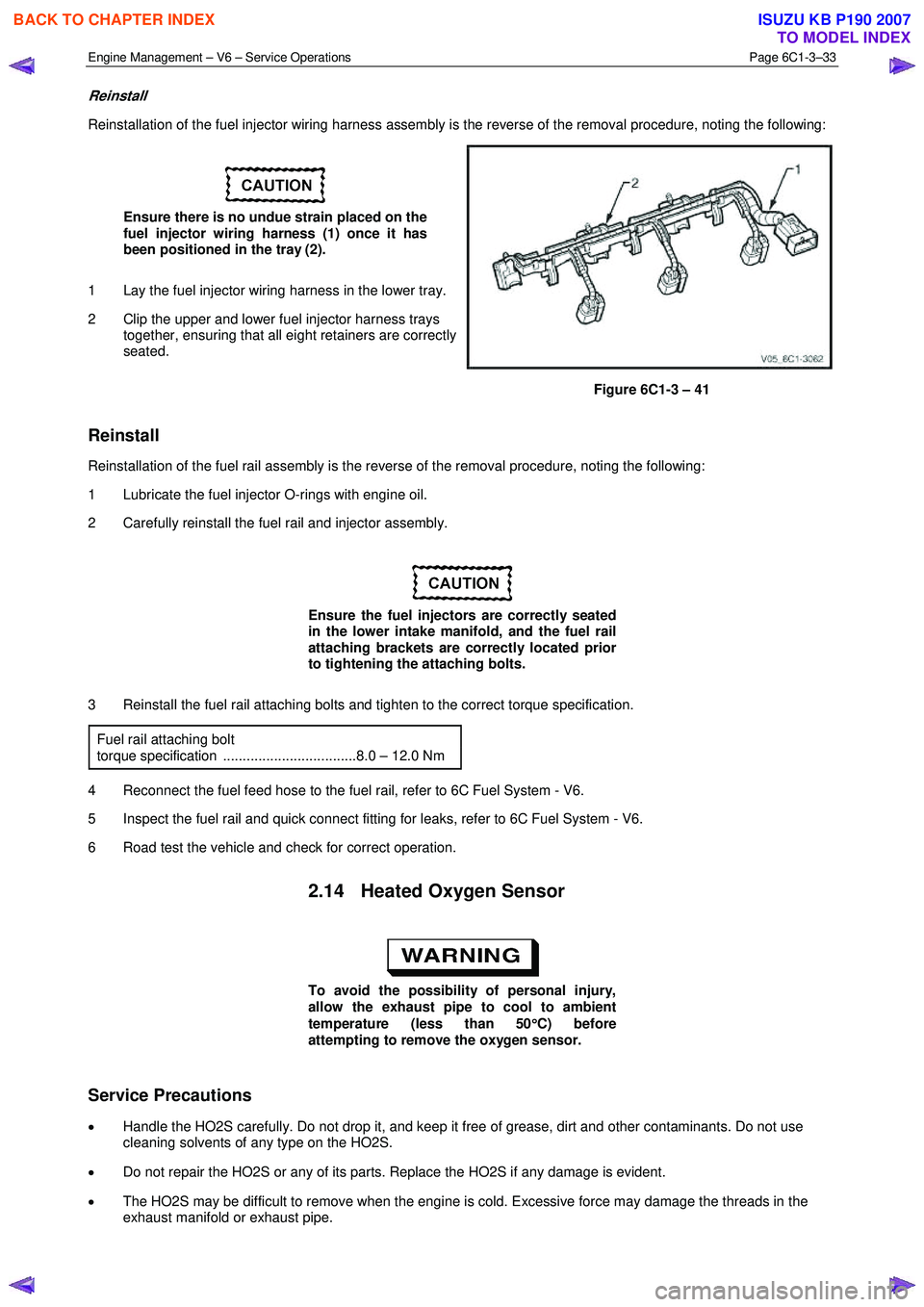
Engine Management – V6 – Service Operations Page 6C1-3–33
Reinstall
Reinstallation of the fuel injector wiring harness assembly is the reverse of the removal procedure, noting the following:
Ensure there is no undue strain placed on the
fuel injector wiring harness (1) once it has
been positioned in the tray (2).
1 Lay the fuel injector wiring harness in the lower tray.
2 Clip the upper and lower fuel injector harness trays together, ensuring that all eight retainers are correctly
seated.
Figure 6C1-3 – 41
Reinstall
Reinstallation of the fuel rail assembly is the reverse of the removal procedure, noting the following:
1 Lubricate the fuel injector O-rings with engine oil.
2 Carefully reinstall the fuel rail and injector assembly.
Ensure the fuel injectors are correctly seated
in the lower intake manifold, and the fuel rail
attaching brackets are correctly located prior
to tightening the attaching bolts.
3 Reinstall the fuel rail attaching bolts and tighten to the correct torque specification. Fuel rail attaching bolt
torque specification ..................................8.0 – 12.0 Nm
4 Reconnect the fuel feed hose to the fuel rail, refer to 6C Fuel System - V6.
5 Inspect the fuel rail and quick connect fitting for leaks, refer to 6C Fuel System - V6.
6 Road test the vehicle and check for correct operation.
2.14 Heated Oxygen Sensor
To avoid the possibility of personal injury,
allow the exhaust pipe to cool to ambient
temperature (less than 50 °
°°
°
C) before
attempting to remove the oxygen sensor.
Service Precautions
• Handle the HO2S carefully. Do not drop it, and keep it free of grease, dirt and other contaminants. Do not use
cleaning solvents of any type on the HO2S.
• Do not repair the HO2S or any of its parts. Replace the HO2S if any damage is evident.
• The HO2S may be difficult to remove when the engine is cold. Excessive force may damage the threads in the
exhaust manifold or exhaust pipe.
BACK TO CHAPTER INDEX
TO MODEL INDEX
ISUZU KB P190 2007
Page 3559 of 6020
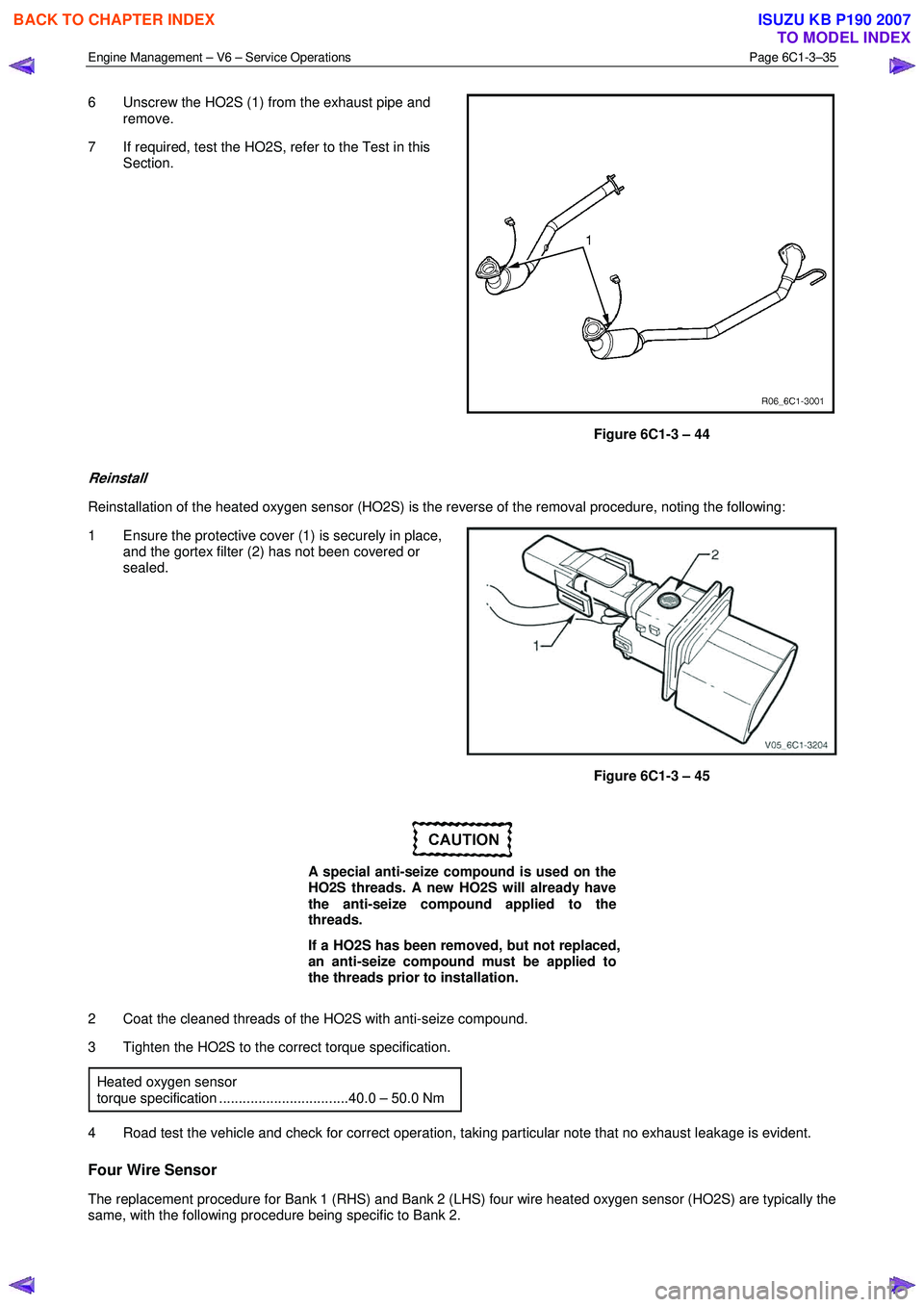
Engine Management – V6 – Service Operations Page 6C1-3–35
6 Unscrew the HO2S (1) from the exhaust pipe and
remove.
7 If required, test the HO2S, refer to the Test in this Section.
Figure 6C1-3 – 44
Reinstall
Reinstallation of the heated oxygen sensor (HO2S) is the reverse of the removal procedure, noting the following:
1 Ensure the protective cover (1) is securely in place, and the gortex filter (2) has not been covered or
sealed.
Figure 6C1-3 – 45
A special anti-seize compound is used on the
HO2S threads. A new HO2S will already have
the anti-seize compound applied to the
threads.
If a HO2S has been removed, but not replaced,
an anti-seize compound must be applied to
the threads prior to installation.
2 Coat the cleaned threads of the HO2S with anti-seize compound.
3 Tighten the HO2S to the correct torque specification.
Heated oxygen sensor
torque specification .................................40.0 – 50.0 Nm
4 Road test the vehicle and check for correct operation, taking particular note that no exhaust leakage is evident.
Four Wire Sensor
The replacement procedure for Bank 1 (RHS) and Bank 2 (LHS) four wire heated oxygen sensor (HO2S) are typically the
same, with the following procedure being specific to Bank 2.
BACK TO CHAPTER INDEX
TO MODEL INDEX
ISUZU KB P190 2007